Фрезерный мини станок своими руками: Фрезерный станок по металлу своими руками
alexxlab | 09.06.2023 | 0 | Фрезерный
Преобразование мини-фрезерного станка в станок с ЧПУ
Если вы думаете о преобразовании существующей ручного мини-станка в ЧПУ или планируете купить новый для преобразования в ЧПУ, вам необходимо знать некоторые вещи.
Преобразование, очевидно, не является простым решением «подключи и работай» с помощью комплекта.
Это включает в себя планирование, навыки и правильные компоненты для успешной трансформации.
В этом руководстве я намерен дать общий обзор этого процесса для начинающих.
Стоит ли переоборудовать обычный станок в станок с ЧПУ?
Прежде чем вы приступите к этому процессу, я хотел бы сказать, что этот процесс займет как минимум неделю усилий и, возможно, месяц, если вы можете работать только по выходным.
Вам также понадобится помощник, особенно из-за необходимости подъема тяжелых деталей.
Также вам потребуется минимальный объем знаний о деталях фрезерного станка. Также очень помогает, если вы построили или эксплуатировали хотя бы небольшой фрезерный станок с ЧПУ.
Тем не менее, при наличии правильного комплекта ЧПУ мини-фрезерного станка и надлежащего плана это преобразование может быть достигнуто.
Вы также можете сохранить общую стоимость, чтобы она была намного ниже цены совершенно нового настольного фрезерного станка с ЧПУ начального уровня.
Имея контроллер на базе GRBL и недорогой фрезерный станок, вы можете собрать ЧПУ менее чем за 2000 долларов.
Этого, конечно, будет недостаточно для любой коммерческой операции, но я бы сказал, что это отличный выбор для любителя, который хочет поиграть с фрезерным станком с ЧПУ в своем гараже.
Однако, если вас пугает преобразование, вы можете выбрать готовый к использованию настольный фрезерный станок с ЧПУ
Какой станок лучше всего подходит для преобразования?
Если вы собираетесь купить новый ручной настольный фрезерный станок для преобразования в фрезерный станок с ЧПУ и вам интересно, какой из них выбрать, я предлагаю Precision Matthews PM-25 MV, который стоит около 2000 долларов.
Я рекомендую это в первую очередь потому, что он поставляется с системой ременного привода, в отличие от системы зубчатого привода, используемой на большинстве других машинах.
Если вы согласны потратить немного больше денег на гораздо большую мощность, я также рекомендую настольную мельницу Precision Matthews PM-833TV.
Для рекомендуемых мною комплектов модернизации настольных фрезерных станков с ЧПУ я перечислил совместимые фрезерные станки с ЧПУ в виде таблицы в следующем разделе.
Комплект для переоборудования фрезерного станка в ЧПУ
Преобразование заключается в установке нового набора механических компонентов и электронных компонентов в вашу фрезер.
Механические компоненты (комплект)
Механические компоненты для преобразования станка в ЧПУМеханическая часть состоит в замене ходовых винтов на шарико-винтовые пары и двойные гайки.
Причина, по которой вам нужна новая механическая система, заключается в том, что ходовые винты в настольных фрезерных станках имеют люфт и на самом деле не предназначены для работы с ЧПУ.
ШВП имеют очень небольшой люфт и являются отличным выбором для привода ЧПУ.
Цена этих комплектов для переоборудования колеблется от 700 до 1200 долларов в зависимости от качества шарико-винтовой пары и размера вала двигателя, который вы выберете.
Ключевым выводом является то, что почти все настольные ЧПУ имеют комплекты для модернизации, доступные для покупки.
Электронные компоненты (комплект)
Электронные компоненты для преобразования станка в ЧПУВторой частью преобразования является электроника для управления ЧПУ.
Вам потребуются драйверы шаговых двигателей, контроллер, концевые выключатели (3), механические щупы для контроля перемещений по осям X, Y и Z.
Для управления шпинделем вы можете купить VFD, если вы хотите управлять оборотами вручную с помощью кнопок.
Если вы хотите выбрать шпиндель для своего ЧПУ, ознакомьтесь с этим руководством.
Конечно, вам нужен компьютер на другом конце контроллера, чтобы управлять программным обеспечением ЧПУ и давать инструкции станку.
В отличие от механического комплекта, здесь есть несколько путей в зависимости от предпочитаемого вами программного обеспечения (например, Mach4, GRBL или LinuxCNC).
Как преобразовать фрезерный станок в ЧПУ?
Точные шаги, как это сделать, будут зависеть от модели вашей машины и вашего выбора электроники. Я только намереваюсь дать общий обзор того, как это сделать.
Механическая модернизация
Для переоборудования необходимо разобрать весь станок. Это не так просто.
Для начала необходимо разобрать каждую ось мельницы и закрепить на каждой оси вместо ходовых винтов ШВП.
Резьбовой вал шарико-винтовой передачи имеет форму спиральных дорожек качения шарикоподшипников внутри специальной гайки.
Вес на оси Z типичного настольного фрезерного станка может быть очень большим, поэтому вам, скорее всего, понадобится подъемник для подъема и перемещения осей.
Ваш станок может быть привинчен к полу с помощью гаек и болтов, и вам придется его снять.
После извлечения каждой оси вам нужно будет добавить к ним компоненты для ЧПУ по отдельности.
Шариковые винты и гайкиВыньте ходовой винт на каждой оси и замените его шариковыми винтами.
Обратите внимание, что при установке шарико-винтовых пар необходимо соблюдать осторожность, чтобы не зацепить маслопроводы.
Затем блок гаек ходового винта необходимо заменить блоком гаек шарико-винтовой передачи.
Если монтажные отверстия в блоке гаек не совпадают, вам понадобится адаптер для крепления блока гаек шарико-винтовой передачи к оси.
Кроме того, вам может понадобиться выполнить ручную шлифовку, чтобы все подошло правильно. Этого следовало ожидать, так как это не решение plug-and-play.
Обратным путем было бы изготовить некоторые детали самостоятельно.
Маслопроводы должны быть снова подключены после того, как вы поместите шариковые винты внутрь оси.
Следующим шагом будет присоединение шаговых двигателей к оси. Убедитесь, что шаговые двигатели могут выдержать большой вес по оси Z.
Я немного расскажу о шаговых двигателях для ЧПУ здесь
Повторите те же действия для двух других осей. Сначала поместите оси X и Y обратно на базу.
Далее вам нужно разместить ось Z или блок колонн. Прежде чем вы сможете управлять станком, вам необходимо убедиться, что ось Z идеально перпендикулярна столу, правильно выровняв ее. Обратите внимание, что на YouTube есть подробные видеоролики о том, как это сделать.
Если вы сверитесь с индикатором и обнаружите, что фреза не прижата, то вам нужно использовать тонкие листы металла под основанием для регулировки наклона. Это называется шиммированием колонн.
Вам нужно будет делать пробы и ошибки с листами разной толщины и каждый раз проверять наклон с помощью индикатора, чтобы увидеть, завершена ли калибровка.
Когда вы закончите установку колонны, вам нужно поставить шпиндель, чтобы убедиться, что он не наклонен. Шпиндель должен располагаться под прямым углом к столу или основанию, на котором установлен станок.
Перемещение шпинделя с индикаторомКак и в случае с колонной, вам нужно использовать индикатор перемещения, чтобы проверить наклон шпинделя. Точный способ сделать это показан в нескольких видеороликах на YouTube. Как только вы найдете наклон, вам нужно постучать по передней бабке в компенсирующем направлении.
Ослабьте гайки и постучите молотком для компенсации наклона. Еще раз, вам нужно снова затянуть болты и проверить с помощью индикатора, чтобы увидеть, исправлено ли оно.
Вам также нужно будет сделать несколько проб и ошибок и сделать его идеально правильным.
Крепление электроники ЧПУ
После того, как механическая часть выполнена, вам нужно настроить электронику для ЧПУ. Обратите внимание, что перед этим необходимо установить шаговые двигатели для каждой оси.
Теперь вам нужно собрать мозг/систему управления для шаговых двигателей, что в конечном итоге делает его управляемой компьютером системой, а не ручным фрезерным станком.
Существует множество вариантов сборки электроники для ЧПУ. Я просто объясню, как сделать базовую систему
Вам понадобятся три концевых выключателя и два датчика, а также нерегулируемый источник питания постоянного тока.
Также вам понадобятся три драйвера шагового двигателя. Для управления шаговыми двигателями NEMA 34 я рекомендую драйверы шаговых двигателей DM860T (до 7 А).
Если вы новичок в драйверах шаговых двигателей, я сделал подробный обзор основных драйверов шаговых двигателей, доступных на рынке.
Вероятно, вы могли бы обойтись шаговыми двигателями NEMA 23 для осей X и Y. Просто проверьте, какой крутящий момент вам нужен, и выберите подходящий шаговый двигатель.
В качестве контроллера вы можете выбрать любой контроллер, работающий на linuxCNC, Mach4 или GRBL .
Если вам нравится программное обеспечение linuxCNC, то Mesa 7I76E — хороший выбор для контроллера.
Блок управления ЧПУ с типичными электронными компонентамиЕсли вы не хотите покупать каждую электронную часть отдельно, я рекомендую комплект электроники для преобразования.
Обратите внимание, что концевые выключатели дают мельнице пространственное представление и не позволяют ей выйти за свои физические пределы.
Датчики предназначены для оценки положения заготовки перед началом фрезерования.
Кроме того, вам обязательно понадобится компьютер, который подключается к контроллеру с помощью кабеля USB/Ethernet/параллельного порта. Это зависит от вашего выбора контроллера.
Далее вам необходимо дооснастить шпиндельную систему. Если шпиндель вашего мини-завода работает на системе шпиндельного двигателя с зубчатым приводом, вам необходимо преобразовать его в систему с ременным приводом.
Для управления шпинделем вам понадобится контроллер двигателя VFD. Вам нужно получить контроллер VFD, который подходит для вашего двигателя шпинделя.
Частотно-регулируемый привод обычно имеет ручные кнопки для уменьшения или увеличения скорости вращения шпинделя. Вы также можете изменить направление вращения шпинделя.
Вы также можете подключить VFD к контроллеру, если хотите управлять скоростью вращения шпинделя с помощью компьютера, а не кнопок вручную.
Программное обеспечение, которое вы используете для управления всем этим с вашего компьютера, будет зависеть от того, какой контроллер у вас есть. Это может быть либо Mach4, либо GRBL, либо LinuxCNC.
Это также может быть что-то еще. Здесь действительно есть масса вариантов. Например контроллер на Arduino.
В заключение, независимо от того, модернизируете ли вы свой существующий станок или покупаете новый для преобразования в ЧПУ, убедитесь, что вы знаете, что вам нужно и как это сделать.
Если все сделано правильно, это может дать вам функционирующий домашний фрезерный станок с ЧПУ по общей стоимости, которая намного ниже, чем новый фрезерный станок с ЧПУ начального уровня от таких брендов, как Tormach или HaaS.
6 в 1 для моделистов
Всем здравствуйте,
Тема инструментов для меня одна из самых любимых при написании обзоров. Через меня уже прошла целая кучка ручных и электрических приспособлений для пиления, сверления, резания, строгания и прочих направлений приложения усилий, когда рукам покоя нет. Однако, станков у меня еще не было и, хотя, с инструментами работают постоянно, последний раз за токарным станком я стоял лет, эдак, 25 назад. Поэтому обзор будет на любительском, лубочно-прикладном уровне простого домашнего мастера. Обзор большой: много фото, видео, гифок, попыток и мыслей, как довести «до ума», как быть с расходкой и небольшой DIY… запасайтесь попкорном 🙂
§1.
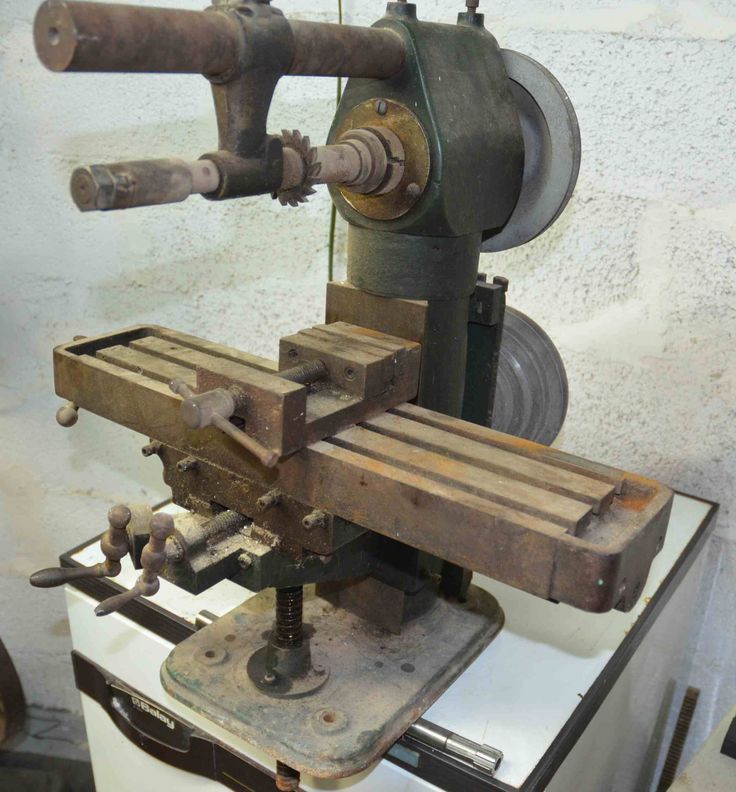
§2. Основные блоки
§3. МИНИЛОБЗИК
§4. ШЛИФОВАЛЬНЫЙ СТАНОК
§5. ВЕРТИКАЛЬНЫЙ СВЕРЛИЛЬНО-ФРЕЗЕРНЫЙ СТАНОК
§6. ГОРИЗОНТАЛЬНЫЙ ФРЕЗЕРНЫЙ СТАНОК
§7. ТОКАРНЫЙ СТАНОК ПО МЕТАЛЛУ
§8. ТОКАРНЫЙ СТАНОК ПО ДЕРЕВУ
§9. Впечатления и итог
Основоположником всех, продающихся подобных станков, считается станок Unimat 1, выпускаемый австрийской компанией «The Cool Tool». Если не ошибаюсь, именно она разработала концепцию и конструкцию мини-модульных станков, которые отлично подходят как для детского творчества, так и для моделистов, да и просто любителей что-то поделать руками, а такую возможность подобные станочки предоставляют с лихвой. Я очень давно хотел «попробовать» такой, но цена, оригинальной версии, прямо скажем, негуманная.
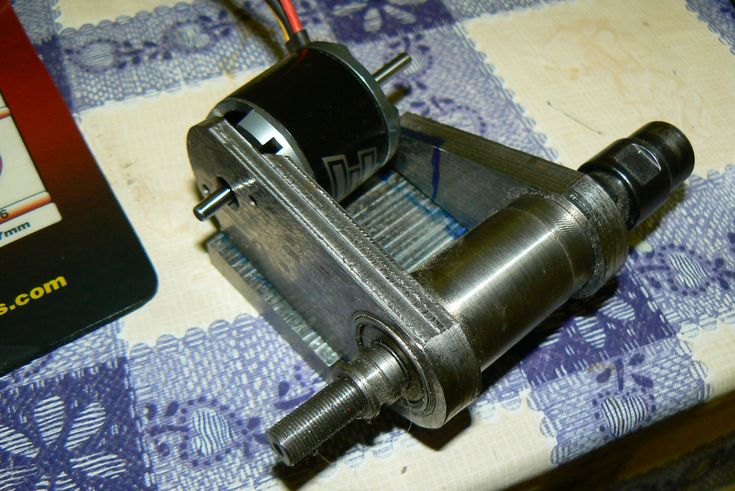
У меня, по-началу, было несколько скептическое отношение к возможностям станочка, поэтому пластиковый вариант я даже не рассматривал. Самое смешное, большинство роликов на Ютубе содержат только общее видео разборки и сборки аналогичных девайсов (иногда даже включения), но без полноценной демонстрации работы, поэтому было действительно интересно пощупать его руками, ведь известно, что «первые 40 лет детства самые сложные в жизни мужчины…» 🙂 Посмотрим, что из этого получилось…
Приехал аппарат в большой коробке:
Если приглядитесь, увидите батарейку АА для сравнения:
Коробка достаточно тяжелая, вес больше 5кг у меня, как назло, измерить оказалось нечем, поэтому по ощущениям тянет примерно на 6-7кг.
Общие технические характеристики:
¤ Материал: алюминий, сплав цинка и алюминия, сталь
¤ Скорость двигателя: 20000 rpm
¤ Питание на входе: AC 100-240V 50/60Hz
¤ Питание на выходе: DC 12V 4A
¤ Мощность: 48W
¤ Варианты собираемых станков: минилобзик, шлифовальный, сверлильный, токарный по дереву, токарный по металлу, фрезерный.
¤ Обрабатываемые материалы: дерево, пластик, мягкие металлы (алюминий, медь, ЗОЛОТО (так и написано!), акрил и др.
Откроем коробку:
У производителя есть даже свой сайт (но малоинформативный):
Убираем комплектную фенерку для опытов:
Поначалу глаза разбегаются даже у опытного рукож… домашнего мастера, привыкшего браться за любую технику без прочтения инструкции:
C рулеткой и батарейкой для сравнения:
Тем более инструкцию, из-за ее размера (брошюрка формата А6!!!) и содержательности, ничем, кроме как издевательством, я назвать не могу. Лупа, как говориться, в помощь. Подробность описания, весьма лаконична, а некоторые моменты вообще не освещены, и требуют самостоятельной компиляции, но это даже интереснее. На самом деле, все достаточно логично собирается.
Инструкция
В общем: «Где наша не пропадала?»
Начну с основных компонентов-модулей из которых, в разных конфигурациях, получаются 6 вариантов станков (а подвариантов и того больше).
«Сердцем» станка является, конечно, 12-ти вольтовый двигатель, мощностью 48Вт:
На первый взгляд, выглядит он, как-то, совсем несерьезно, однако, забегая вперед, скажу, вполне неплохо тянет и отлично работает.
Работает двигатель в связке с редуктором:
Эта связка собирается один раз и работает в неизменном виде во всех вариантах:
Важнейшим компонентом набора, являются соединительные стяжки, которые жестко связывают все конструктивные элементы друг с другом:
Устанавливаются они в профилированные пазы соединяемых элементов, где затягиваются комплектным шестигранником (все необходимые ключи в комплекте есть):
Двигатель и шкив редуктора соединяются ремнем:
Питается все это от комплектного блока питания:
Соединение с двигателем осуществляется с помощью быстро-разъемного коннектора:
Плюс к этому на проводе двигателя есть кнопка выключения (постоянно зацепляющаяся за край стола).
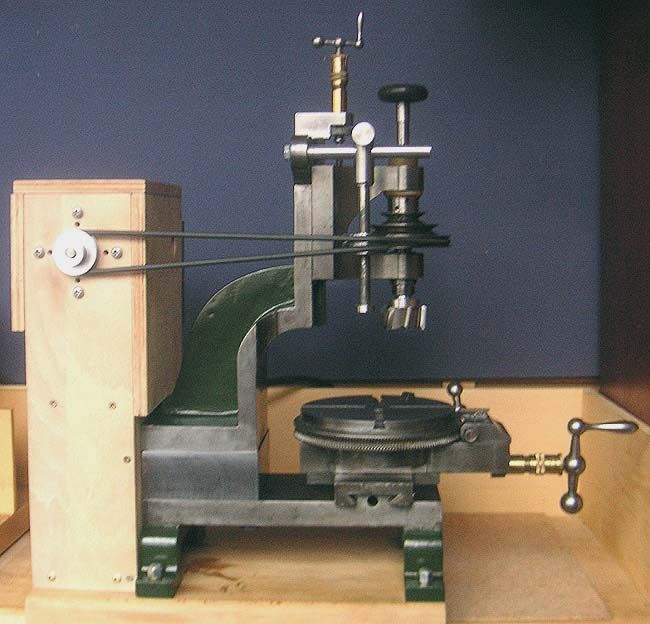
Двигатель и навесные элементы устанавливаются на основные блоки конструкции, образующие раму и выполненные из алюминиевого профиля:
Во все вращающиеся рукоятки вкручиваются втулки (к сожалению, они фиксируются жестко и не имеют независимого вращения):
В комплекте есть все, что нужно для сборки и начала работы: задняя бабка, суппорта, токарный патрон, платформы…
… весь крепеж, небольшой набор расходки, все шестигранники для затяжки крепежа элементов конструкции…
… и даже немного материала для тестирования — фанерка и пара деревянных заготовок:
Другой вопрос, что поначалу глаза «в кучу» от количества всякой мелочевки, а учитывая мелкость и лаконичность инструкции, сборка в первый раз каждого станочка, занимает достаточно длительное время, но потом, наловчившись и зная «что-куда», сборка и переделка из одного варианта в другой занимает не больше 5 минут.
Добавлю, что качество обработки литых компонентов набора средненькое, однако геометрия, посадочные места и соединительные отверстия выдержаны четко — все компоненты друг к другу подходят.
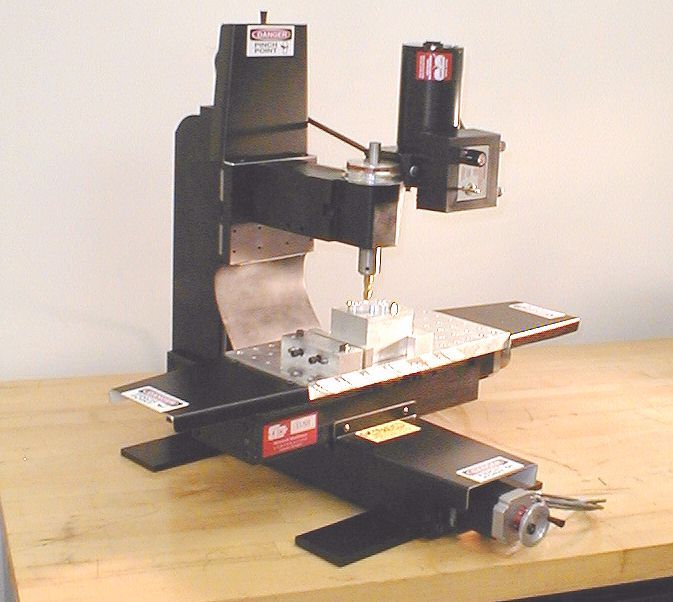
Итак, начинаем собирать станки.
Возможные варианты: минилобзик, шлифовальный, сверлильный, токарный по дереву, токарный по металлу, фрезерный.
к Содержанию ▲
Заявленные характеристики минилобзика:
Рабочая зона: 100 * 100мм
Максимальная толщина материала: 4мм дерево высокой плотности, 7мм средней, 18mm мякгое, 0.5мм алюминий, 2мм оргстекло
Вес станка: 2.4кг
Размеры: 150 * 100 * 140мм
Для станочка используется такой комплект деталей:
и платформа:
Интересным элементом является следующая деталь, в нее вставляется пилка:
желтое желе — смазка, в которой движется эксцентрик, фиксируемый на валу редуктора двигателя:
Для пиления используются мелкие пилки (в комплекте 10 штук):
Устанавливаемые таким образом:
Станок в сборе:
Вес получился, почему-то, меньше заявленного, вероятно считали с блоком питания.
Под рукой была комплектная фанерка толщиной 2.4мм:
Станочек пилит! И при некоторой сноровке выходят, вполне себе, ровные кружки и другие фигуры:
Режет быстро и, несмотря, на отсутствие верхней точки крепления пилки, достаточно ровно (если потренироваться).
Гифка ускорена 🙂
После использования возникает вопрос, где брать расходку (пилки) для станочка? Их всего 10 штук. Все просто, берем пилки от простого ручного лобзика (как оказалось, их сейчас не так-то просто найти в продаже) и отламываем кусочек плоскогубцами:
Стоит комплект из 20 штук сущие копейки, а из каждой обычной пилки получиться штук 5 пилок для станка, хватит на ооочень долго.
Тут же ставим самодельную пилку и проверяем не только на фанерке, но и на ламинате толщиной 8мм. Пилит, хоть и медленнее, чем фанерку, но отлично пилит!
Станок рабочий.
Видео сборки и работы минилобзика
youtube.com/embed/vW0o8ezdGLY?autoplay=0&hl=ru_RU&rel=0″ frameborder=”0″ allowfullscreen=””>к Содержанию ▲
Следующим идет шлифовальный станочек.
Заявленные характеристики:
Рабочее пространство: 120 * 100мм
Обрабатываемые материалы: дерево, пластик, мягкие металлы
Вес: 1.5кг
Размер: 290 * 100 * 100мм
Один станок из другого переделывается достаточно просто, причем, с каждым разом время, сборки сокращается, т.к. уже понимаешь что и как установить, что к чему подогнать и где затянуть.
На вал редуктора накручиваем диск для наждачки, на противоположной стороне вала редуктора предусмотрено отверстия для фиксации вала:
Комплектная расходка состоит, всего лишь, из двух круглых наждачек с клеящим слоем:
В сборе станок выглядит так:
Работает отлично:
Однако, естественно, ситуация с расходкой беспокоит.

Отрываем от шлифовальной насадки накладку из пористого материала с частью «липучки» с крючками.
Вырезаем из оторваной части насадки и наждачки кружки нужного размера, далее часть от насадки клеим на двусторонний скотч на диск станка:
И получаем возможность быстро менять стертые круги:
Немного отодвигаем платформу и продолжаем работать на станке:
Еще шлифовальный станок можно оснастить камнем для заточки металлических лезвий (ножи, ножницы, инструмент итд). В инструкции об этом ни слова, поэтому пришлось самому придумывать, как нужно установить точильный камень.
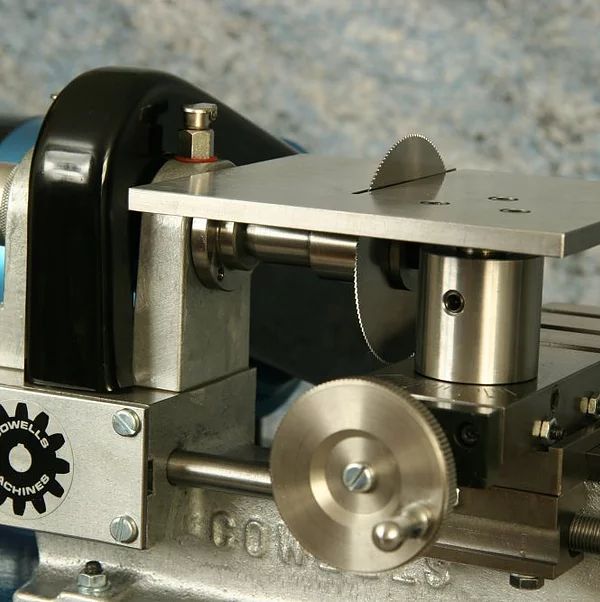
Установил так:
Точит нормально:
Однако, как оказалось установил я не совсем правильно, нашел в интернете такой правильный вариант:
А я то думал зачем эти пластиковые кожухи нужны, но, имхо конечно, мой вариант более удобен 🙂
Видео работы шлифовального станка
к Содержанию ▲
Сверлильный станок требует уже использования в своем устройстве двух поперечных и одни вертикальные салазки:
Заявленные характеристики:
Рабочее пространство: 120 * 100mm
Вертикальный ход свела: 30-50mm
Размер сверла: 1-6mm
Вес: 2.8kg
Размер: 160 * 290 * 150mm
Немного про салазки. Они полностью выполнены из алюминия и имеют, относительно, сложную конструкцию:
Вот эти крепежные элементы отвечают за прижим черной пластиковой пластинки (на фото сверху):
Нужно это для регулировки плавности хода салазок — с одной стороны они должны свободно ходить по направляющим, а с другой — не люфтить и не смещаться от вибрации станка при работе. Понял я это только под конец, и результаты обработки заготовок, которые Вы сможете увидеть ниже, могли бы быть получше 🙂 Как говориться: «Опыт, сын ошибок трудных…»
Собираем станок…
Готово (фотографировал уже правда после использования):
Вес:
В комплекте идут сверло и фрезеровочный бур:
Патрон цанговый, поэтому под каждый размер сверла нужно менять цангу, что не очень удобно:
Для подъема и опускания сверла сбоку вставляется пластиковый шток:
Из салазок убирается винтовое крепление и они становятся простыми направляющими, без фиксации.
Удивило, что подъемный шток пластиковый, деталь то силовая, и должна быть сделана из металла.
Глубина сверления около 15мм (на фото шток поднят в самое верхнее положение, если опустить он на 1мм опуститься в квадратное отверстие):
Станок без проблем сверлит дерево, мягкие металлы:
Кстати, затягивать патрон также не очень удобно, в ручную не получается, приходится прибегать к помощи плоскогубцев:
Если поставить более серьезное сверло (ставил из набора Dewalt), то под силу и сталь (1-2мм):
Кроме этого, в станок можно поставить фрезерный бур:
С помощью него можно проточить мягкие материалы (типа алюминия):
В данном случае, удобнее, когда сверло неподвижно, а фрезеруемая заготовка направляется руками.
В общем, данный станочек тоже работает:
Видео вертикального сверлильно-фрезерного станка
youtube.com/embed/nX6q4GS7WAs?autoplay=0&hl=ru_RU&rel=0″ frameborder=”0″ allowfullscreen=””>к Содержанию ▲
В этой конструкции уже можно достичь определенной точности фрезерования за счет фиксации заготовки и перемещения ее и двигателя с вращающимся буром с помощью направляющих салазок по трем осям.
Используемые детали:
Ход продольных салазок: 50mm
Ход поперечных салазок: 30mm
Диаметр сверла: 1-6mm
Ширина зажимаемой детали max: 25x35mm
Материалы для обработки: дерево, пластик, мягкие металлы
Вес: 2.8kg
Размер: 290 * 160 * 200mm
Станок в сборе:
Вес:
Бур используется тот же самый, что и в вертикальной версии станочка, но еще добавляется фиксатор заготовки (снова пластик):
Максимально раздвинут:
Фрезеровку можно проводить с помощью салазок по трем направлениям: право-лево, вверх-вниз и вглубь детали:
Если потренироваться можно добиться определенного ожидаемого результата. Например, проточить паз в дереве или овальное (относительно 🙂 отверстие в алюминиевой трубке:
Тут прошу сильно не ругать: «Пианист играет, как умеет…»
При определенной тренировке пространственного мышления (как вращать ручки по осям одновременно..) можно даже «вырезать» что-то похожее на буквы:
… но пластиковый фиксатор заготовки, портит картину: деталь, как бы ты не затягивал, постоянно норовить выскочить из него, т.к. нет нужной жесткости и сами губки фиксатора изнутри гладкие (что лечится наклейкой на них абразива типа наждачки). Если приложить большее, чем нужно усилие, его можно вообще сломать.
В общем, станок работает и, даже, неплохо, но на заготовках, с большой площадью контакта с губками фиксатора.
Видео горизонтального фрезерного станка
к Содержанию ▲
Тут слово металл я бы поставил в скобки: медь и алюминий — это максимум, еще пластик, акрил и дерево.
Заявленные характеристики:
Диаметр шпинделя: 50mm
Макс. длина заготовки: 135mm
Обрабатываемые материалы: мягкие металлы (Gold, Silver, Copper, Aluminium, etc.)
Вес: 2.5kg
Размер: 290 * 90 * 220mm
Комплект для сборки:
Добавляется суппорт и задняя бабка:
Длина выдвижения пиноли задней бабки:
Трехкулачковый патрон:
Шпиндель просто накручивается на вал редуктора. Фиксация и затяжка детали в шпинделе осуществляется с помощью двух отверстий, в которые вставляются тонкие отвертки или комплектные шестигранники и тянутся в разные стороны:
Диаметр зажимаемой детали не превышает 25мм:
Если раздвигать кулочки дальше, они просто выскакивают:
Однако, если их перевернуть, можно зафиксировать более крупную деталь подобным образом:
Патрон сделан из силумина. Качество изготовления и фиксации заготовки (особенно гладкой) посредственные.
Высота центра заготовки от нижней основы 25мм, хватает чтобы зажать деталь диаметром 12мм, не более:
В комплекте предусмотрены проставки, поднимающие все элементы конструкции еще на 25мм:
Эти проставки универсальные и подходят, практически для любого станочка, просто в токарных по дереву и металлу, они могут быть наиболее востребованными. Так станок выглядит с ними:
Резец выполнен, по виду и использованию, из закаленной стали, заточка выглядит острой 🙂
Что меня неприятно удивило в конструкции, так это то, что резец фиксируется на поперечных салазках с помощью пластиковых (!) держателей:
Это место подвергается самой большой нагрузке при работе, и естественно пластик тут не уместен. Причем я смотрел на сайте оригинального Unimat 1, там тоже пластик.
Мои опасения подтвердила более менее серьезная нагрузка — пластик треснул:
Но останавливаться на полпути, из-за такой мелочи, я не собирался. Поэтому, из подручных средств и с «лестными» словами в адрес разработчиков, была сделана вот такая конструкция из двух стальных пластин, фиксирующих резец (по жесткости и надежности стало, раз в 10, лучше прежней):
Кстати
запчастей для подобных станочков полно и, несмотря на то, что моя «кустарщина» с держателем вполне жизнеспособна, заказал (недорого) два вот таких металлических крепежных элемента вместо пластиковых:
Едут…
Станок в сборе:
Упомяну, что сзади, любой станок лучше укреплять дополнительными пластинами, для жесткости:
И конструкция заработала. К сожалению, большого количества разнообразных заготовок из пластика или мягкого металла у меня не нашлось, поэтому проверил только на медной трубке от кондиционера и дереве:
Более серьезный металл, тоже попробовал резать, но жесткости конструкции не хватает и резец, часто, «закусывается» под деталь.
Дерево, конечно, лучше обрабатывать на токарном станке по дереву (о нем чуть ниже), но на данном станке удобно «вытачивать» детали типа осей, когда нужна одинаковая толщина по всей заготовке и строго перпендикулярные срезы. Для этого шпиндель заменяем на такой элемент:
Ставим заготовку и потихоньку снимаем материал. Когда закончили с одной стороны и сделали ровный срез, переворачиваем заготовку и делаем с другой:
Дальше, прямо тут, проходим наждачкой:
Как-то так (напоминаю, что автор работал последний раз на токарном станке не один десяток лет назад):
Итог: станок рабочий, но требуется замена пластиковых фиксаторов резца и, думаю, не стоит ждать прецизионной точности обработки деталей.
Видео токарного станка по металлу
к Содержанию ▲
Самое вкусное оставил на последний раздел. Дерево, тот материал, с которым я люблю больше всего работать.
Если до этого был собран токарный станок по металлу, нужно только заменить шпиндель на четырехгранную направляющую и убрать поперечные салазки, поставив вместо них упор для резца:
Макс. диаметр заготовки: 50mm
Макс. длина заготовки: 135mm
Обрабатываемые материалы: дерево, пластик
Вес: 2.0kg
Размер: 290 * 150 * 130mm
Станок в сборе:
Реальная длина обрабатываемой заготовки составляет около 10см (на фото передняя и задняя бабки максимально отодвинуты друг от друга):
Комплектный ручной резец, стальной:
заточен достаточно неплохо.
Реальный максимальный диаметр обрабатываемой детали не превышает 5см (с использованием проставок, о которых я упоминал в описании токарного станка по металлу):
Упомяну еще одну полезную штуку из комплекта к станку, которая позволяет найти центр заготовки. Понятно, что чем лучше мы его нашли, тем меньше биение и проще обработка:
Токарный станочек по дереву «допиливать» не нужно, все работает, главное вспомнить, как пользоваться резцом:
Ну и небольшой DIY в моем исполнении, из сосновых заготовок (не самое подходящее дерево для этого) диаметром 20мм:
Не утерпел, решил потренироваться и изготовить шахматные фигуры. Никаких замеров не проводил, все делал «на глазок», с первого раза:
В итоге получилось вот так, думаю, 4+ (с натяжкой) я бы смог на уроке труда получить 🙂
Отправились в компанию к «гражданину», сделанному несколько ранее, в другом обзоре:
На этом станке мне понравилось работать больше всего, можно сделать достаточно затейливые поверхности вращения.
Мощности для обработки дерева и не только сосны (в комплекте были палочки из более плотной древесины — обрабатывается отлично) хватает.
Видео токарный станок по дереву
youtube.com/embed/9OOLZxMOWFY?autoplay=0&hl=ru_RU&rel=0″ frameborder=”0″ allowfullscreen=””>к Содержанию ▲
Конструктор станков произвел крайне благоприятное впечатление, несмотря на все его недостатки и, кое-где, необходимость довода «до ума». Мощности двигателя, надежности и жесткости конструкции достаточно для выполнения целевых задач на которые рассчитаны станочки. Я бы рассматривал подобный комплект именно в качестве конструктора, т.к. в процессе сборки и использования, можно собирать не только фиксированные конструкции, но и совмещать части от разных станков между собой, получая некоторое количество «не заявленных» модификаций. Кроме этого, легко можно устроить как самостоятельный так и покупной «тюнинг» своего набора, с целью повышения точности обработки материалов, например, поменять двигатель на более мощный (есть модификация на 60Вт), приобрести (или сделать) металлические части вместо пластиковых (чтобы уж стал полностью металлическим) и даже расширить функционал, например, добавив вращающуюся платформу. Да и с запасными частями тоже проблем нет.
Пример дополнительных частей
Основная целевая аудитория, имхо, это подрастающее поколение, хотя, серьезных дяденек-моделистов, кому подобное может понравиться, слава богу, хватает. Я, здоровый дядька, с огромным удовольствием, провозился с ним несколько дней, изучая возможности и собирая материал для обзора. Да если бы мне, во времена моего детства, когда пределом мечтаний были велосипед «Школьник» или фотоаппарат «ФЭД», подарили такой набор, я бы был, наверное, самым счастливым отроком на всей планете. Понятно, что сейчас приоритеты поменялись и, к сожалению, наиболее вожделенными являются компьютеры и гаджеты, но пацаны, по моему глубокому убеждению, должны уметь работать руками и подобный набор неплохой вариант приобщить их к этому. А когда уже начнет что-то получаться… 🙂
Считаю, что малая мощность и «игрушечные» размеры, в данном случае являются плюсом, т.к. сильно снижают риск получения каких-либо травм при использовании. Естественно, технику безопасности никто не отменял и, по меньшей мере, защитные очки, а также контроль со стороны взрослых должны быть обязательно. Кроме этого, желательно, сделать простейшую утяжеляющую платформу (например, из куска толстой доски), к которой можно было бы прикреплять станки, чтобы они не елозили в процессе использования по столу, в крайнем случае прилепить к поверхности на двусторонний скотч 🙂
В общем, игрушка забавная, от которой при желании и определенном приложении сил можно добиться интересных результатов.
к Содержанию ▲
Видео. Полная версия
Сейчас в магазине идет флешсейл на данный комплект (цена $189.99), а, также, на более более бюджетный пластиковый вариант (цена $119.9 9).
На этом все. Надеюсь Вам было интересно 🙂
Всем Добра!
Товар для написания обзора предоставлен магазином. Обзор опубликован в соответствии с п.18 Правил сайта.
Создание недорогого микрофрезерного станка
Говоря о микрообработке, я наткнулся на интересную научную статью о том, как некоторые студенты и преподаватели Университета Северного Иллинойса построили довольно крутую микрофрезерную машину, производительность которой не уступает коммерческим станкам. стоимостью до 100 000 долларов:
Микрофрезерный станок…
Деталь, изготовленная на станке NIU…
чтобы сэкономить на стоимости) и шпиндель. Как видите, его конструкция довольно проста. Несколько сюрпризов для меня из этой статьи:
— Они использовали ходовые винты ACME вместо шариковых винтов, полагаясь на гайки с защитой от люфта, чтобы держать люфт под контролем. Шарико-винтовые пары стали достаточно дешевыми, и я думаю, что в наши дни они являются лучшей заменой.
— Без сервоприводов, только шаговые двигатели. При микрообработке задействованные силы настолько малы, что даже маленьких шаговых двигателей NEMA 17 было достаточно для привода осей.
— Хотя они начали с Mach4, они обнаружили, что он дал неприемлемые результаты — он не мог отслеживать крошечные контуры, необходимые для микрофрезерования. Они предположили, что это связано с тем, что он работал через параллельный порт с ОС не реального времени — Windows. Они перешли на FlashCut, специализированную систему, и их проблемы исчезли. Учитывая, что на базе Windows построено более одной высокопроизводительной системы ЧПУ, я не уверен, насколько виновата Windows. На самом деле, если учесть, что FlashCut также основан на Windows, вам придется в значительной степени отказаться от идеи, что это проблема Windows. Отличие заключается в том, что FlashCut использует аппаратный пошаговый контроллер вместо того, чтобы параллельный порт выполнял всю эту работу. Конечно, у нас есть Smoothstepper, чтобы сделать то же самое для Mach4, и я определенно вижу значительное улучшение по сравнению с моим Smoothstepper по сравнению с параллельным портом.
Вот несколько фотографий этих двоих: лучше увидишь:
Mach4 слева, FlashCut справа. Mach4 оказался неприемлемым для этих микрофрезерованных траекторий…
Окончательные результаты, достигнутые командой на этом маленьком станке, были весьма впечатляющими:
> Общая стоимость материалов: 7000 долларов
> Рабочая зона определенно крошечная, 4″ x 4″ x 4 ″
> Точность чуть больше одной десятой (3 микрона): 0,00012″
> 40 000 об/мин шпиндель — необходим для этих крошечных фрез маленькие моторы. Довольно крутая машинка!
Присоединяйтесь к более чем 100 000 пользователей ЧПУ! Раз в неделю бесплатно получайте наши последние записи в блоге прямо на вашу электронную почту. Кроме того, мы предоставим вам доступ к некоторым замечательным справочным материалам по ЧПУ, включая:
Мини-мельница
Содержание
- Об этой машине
- Полезные ссылки
- Безопасность машины
- Как получить помощь
- Использование этого аппарата
- Настройка
- Эксплуатация
- Крепление
- Замена инструментов
- Установка инструмента
- Удаление инструмента
- Фрезерование
- Попутное фрезерование
- Сверление
- Особенности локации
- болтовня
- Выключение
- Очистка
- Советы и рекомендации
- Как заваривать чай на этой машине
Это HiTorque Mini Mill 3900 от Little Machine Shop.
Этот станок удобен для выполнения точных резов под прямым углом, сверления отверстий и создания плоских поверхностей. Он может работать с такими материалами, как алюминий и мягкая/незакаленная сталь, или любыми более мягкими материалами. (Обратите внимание: если вы обрабатываете сталь, вы должны предоставить свои собственные инструменты. Это необходимо для предотвращения чрезмерного износа лабораторных фрез и сверл.)
Эта фреза имеет ручное управление по трем осям, с циферблатами на X и Y и ограничителем глубины. Оси X и Y имеют значительный люфт, который вам может потребоваться принять во внимание, если вам требуются жесткие допуски.
«Высокий крутящий момент» является относительным. Для мельницы это очень маломоментная машина. Мотор легко заглохнуть на высоких оборотах.
- руководство производителя
- 3900MiniMillSOP
Маленький механический цех-3-осевой ручной-фрезерный станок
- сайт производителя
Безопасность машины
Перед началом эксплуатации мельницы полностью прочтите руководство и настоящую СПД. Помните, что вы несете ответственность за собственную безопасность и безопасность окружающих при эксплуатации мельницы.
- Всегда надевайте защитные очки при выполнении ЛЮБОЙ операции на станках. Ваши очки по рецепту – это защитные очки , а не !
- Убедитесь, что длинные волосы собраны, а свисающая одежда/украшения сняты, включая перчатки.
- Обувь с закрытым носком всегда требуется в зоне станка.
- Никогда не используйте станки, если вы одни в лаборатории.
- Никогда не используйте попутное фрезерование на металлах в EPL.
- Никогда не используйте в EPL глубину резания более 0,040 дюйма.
Фреза будет разбрызгивать острые/зазубренные стружки материала при резке. Это может привести к серьезным травмам глаз.
При сверлении металлов длинные нити материала могут закручиваться вокруг сверла.
Это может вызвать умеренные рваные раны.
На короткое время уменьшите давление сверла, чтобы разорвать эти нити.
Иногда сверла и концевые фрезы могут разбиться и вылететь на большой скорости. Это можно уменьшить, избегая попутного фрезерования и глубоких проходов. Не используйте тупые или поврежденные фрезы. Перед началом операции всегда проверяйте, что инструмент отцентрирован.
Неправильно закрепленные заготовки могут быть захвачены сверлом или концевой фрезой и выброшены на высокой скорости. То, что вы не можете покачивать заготовку, не означает, что станок не сможет этого сделать.
Как получить помощь
Не стесняйтесь обращаться к руководителю лаборатории, если вам нужна помощь. В MCECS также есть специальный механический цех, если вам нужна более подробная помощь или оборудование.
TODO: включите список вводных видеороликов по обработке
В этих разделах описаны стандартные способы использования и типичные ошибки.
Настройка
Опишите, как проверить работоспособность аппарата.
Опишите, как подготовить машину к использованию.
Подтвердите выполнение следующих условий.
- Питание отключено. (красная кнопка слева от шпинделя)
- Скорость установлена на ноль. (циферблат слева от шпинделя)
- Крышка дышла на месте. (черный колпачок над шпинделем)
- Стопорный штифт шпинделя удален из шпинделя.
- В шпинделе уже нет инструмента. (См. раздел «Смена инструментов»)
- Стол чистый и без мусора.
- При наличии тисков
- Тиски чистые и без мусора.
- Тиски надежно закреплены на столе.
- Ключ для тисков снят с тисков.
Эксплуатация
Крепление
Убедитесь, что заготовка надежно закреплена в тисках, чтобы вы могли выполнить намеченную операцию, не перемещая деталь и не забивая инструмент в тиски.
Убедитесь, что заготовка не выходит из тисков дальше, чем на половину ширины губок тисков.
В противном случае деталь может опасно вибрировать во время операций обработки.
Помните, что неподвижная губка и основание тисков являются вашими исходными поверхностями, а это означает, что они должны быть плоскими и квадратными. Если вы хотите убедиться, что тиски перпендикулярны осям стола, обратитесь к руководству.
Пальцевые зажимы — отличный способ зажимать большие заготовки, которые не помещаются в тисках. Пожалуйста, обратитесь к руководству по их использованию.
Замена инструментов
Перед заменой инструментов всегда проверяйте, что питание выключено и скорость установлена на нуле!
Используйте сжатый воздух, полотенца и/или масло для очистки предметов. Воду можно использовать для очистки и охлаждения, однако вы должны высушить ее и протереть тонким слоем масла все затронутые поверхности, когда закончите.
Обратите внимание, что инструменты в США почти исключительно в имперских единицах. Это связано с тем, что по-прежнему дешевле продолжать производство инструментов в имперских единицах, чем переходить на метрические.
Вставка инструмента
Убедитесь, что питание выключено, а скорость равна нулю.
Выберите наименьшую цангу, подходящую для вашего инструмента. Если инструмент не входит в цангу свободно, значит, цанга слишком мала. Использование слишком маленькой или слишком большой цанги для данного инструмента приведет к необратимому повреждению цанги. Убедитесь, что цанга и хвостовик инструмента (гладкий конец инструмента) чистые.
Снимите крышку дышла. Удерживая инструмент в цанге одной рукой, вставьте инструмент в сборе с цангой в шпиндель. Затяните тягу, чтобы втянуть цангу так, чтобы она слегка удерживала инструмент. Вставьте стопорный штифт шпинделя в боковую часть шпинделя. С помощью гаечного ключа затяните тягу, удерживая стопорный штифт шпинделя.
Замените крышку дышла и снимите стопорный штифт шпинделя.
Убедитесь, что инструмент не ослаблен, попробовав пошевелить его вручную.
Если он ослаблен, снимите инструмент и убедитесь, что вы используете правильную цангу. Убедитесь, что инструмент отцентрирован, вращая шпиндель вручную.
Убедитесь, что инструмент снова отцентрирован, включив шпиндель на низкой скорости и проверив колебание.
Если инструмент смещен от центра, снимите его и осмотрите цангу и инструмент на наличие мусора.
Удаление инструмента
Убедитесь, что питание отключено, а скорость равна нулю.
Снимите крышку дышла и вставьте стопорный штифт шпинделя. С помощью гаечного ключа ослабьте тягу, удерживая стопорный штифт шпинделя. Удерживая инструмент и цангу, ослабьте тягу вручную, пока инструмент и цанга не выпадут.
Замените крышку дышла и снимите стопорный штифт шпинделя.
Очистите инструмент и цангу от мусора. Проверьте цангу и инструмент на наличие признаков потускнения или ржавчины. Если найдете, нанесите масло на полотенце и протрите тонким слоем. Верните инструмент и цангу в соответствующие ящики.
Фрезерование
Концевые фрезы — это рабочая лошадка ручного фрезерования. Они бывают разных размеров и форм.
Только две фрезы можно использовать с алюминием и медью. Фрезы с большим количеством канавок забьются и станут непригодными для использования. (Флейты — это спиральные детали сбоку. Сосчитайте их, глядя на конец инструмента.)
Если вы не используете концевую фрезу с центральной режущей кромкой, вам необходимо просверлить направляющее отверстие, прежде чем врезаться концевой фрезой. Дополнительную информацию см. в руководстве.
TODO: сведения о DoC, скоростях и подачах
Попутное фрезерование
Важно обратить внимание на то, используете ли вы обычное или попутное фрезерование. При попутном фрезеровании фреза имеет тенденцию глубже втягиваться в рез. Если ваша установка недостаточно жесткая, это может привести к внезапному и катастрофическому отказу ! Это также может усугубить болтовню. Да, заманчиво сделать разрез «туда-сюда», когда стоишь лицом к поверхности. Сосать его. Если это все еще не очевидно, нельзя использовать попутное фрезерование !
Попутное фрезерование обычно является проблемой только для металлов, но имейте это в виду при обработке пластмасс.
Сверление
Сверла ничем не отличаются от любых других сверл. Храните станочные сверла отдельно от других сверл в лаборатории.
Фиксирующие элементы
Вибрация
Если часть вашей установки недостаточно жесткая, она будет вибрировать во время резки. Это называется болтовня. Это приведет к плохой/неточной обработке поверхности и может привести к поломке инструмента (опасно).
Механическая обработка, естественно, громкий процесс. Однако, если вы заметите очень громкое пение или рычание, исходящие от инструмента или заготовки, вы можете вызвать болтовню.
Обычно вибрацию можно устранить, удерживая инструмент дальше по хвостовику, выбирая инструмент с более коротким соотношением сторон или зажимая заготовку, чтобы уменьшить соотношение размеров любых незажатых областей.
Как правило, незажатые области не должны иметь соотношение сторон более 2:1.
Таким образом, 1-дюймовый стержень не должен выступать из тисков более чем на 2 дюйма без дополнительной поддержки.