40Х13 сталь магнитные свойства: 40Х13 сталь — характеристики, свойства и применение нержавеющей стали
alexxlab | 26.08.2023 | 0 | Разное
Нержавейка магнитится или нет: как определить нержавеющую сталь
- От чего зависят магнитные свойства материалов
- Нержавеющие стали с хорошими магнитными свойствами
- Нержавеющие стали, не обладающие магнитными свойствами
- Как определить, является ли магнитная или немагнитная сталь нержавеющей
Учитывая тот факт, что нержавейка сегодня выпускается в большом разнообразии марок, нельзя однозначно ответить на вопрос о том, магнитится она или нет. Магнитные свойства нержавеющих сталей зависят от химического состава и, соответственно, от внутренней структуры сплавов.
Портативный анализатор металлов позволяет быстро определить содержание химических элементов и сделать заключение о качестве нержавеющей стали
От чего зависят магнитные свойства материалов
Магнитное поле с определенным уровнем своей напряженности (Н) действует на помещенные в него тела таким образом, что намагничивает их. При этом интенсивность такого намагничивания, которая обозначается буквой J, прямо пропорциональна напряженности поля.
В зависимости от значения данного коэффициента все материалы могут входить в одну из трех категорий:
- парамагнетики – коэффициент Ϟ больше нуля;
- диамагнетики – Ϟ равен нулю;
- ферромагнетики – вещества, магнитная восприимчивость которых отличается значительной величиной (такие вещества, к которым, в частности, относятся железо, кобальт, никель и кадмий, способны активно намагничиваться, даже будучи помещенными в слабые магнитные поля).
Направления действия магнитных моментов соседних атомов в веществах различной магнитной природы
Магнитные свойства, которыми обладает нержавейка, связаны еще и с ее внутренней структурой, которая может включать в себя аустенит, феррит и мартенсит, а также их комбинации.
Нержавеющие стали с хорошими магнитными свойствами
Хорошими магнитными свойствами отличается нержавейка, в которой преобладают следующие фазовые составляющие:
- Мартенсит – является ферромагнетиком в чистом виде.
- Феррит – данная фазовая составляющая внутренней структуры нержавейки в зависимости от температуры нагрева может принимать две формы. Ферромагнетиком такая структурная форма становится в том случае, если сталь нагревают до температуры, находящейся ниже точки Кюри. Если же температура нагрева нержавейки находится выше этой точки, то в сплаве начинает преобладать высокотемпературный дельта-феррит, который является выраженным парамагнетиком.
Из всего вышесказанного можно сделать вывод о том, что магнитится та нержавейка, во внутренней структуре которой преобладает мартенсит.Как и обычные углеродистые стали, такие сплавы реагируют на магнит. По данному признаку их и можно отличить от немагнитных.
Способность нержавейки магнитится не влияет на её коррозионную стойкость
Нержавеющие стали, в которых преобладает феррит или его смесь с мартенситом, чаще всего также относятся к ферромагнетикам, но их свойства могут различаться в зависимости от соотношения фазовых составляющих их внутренней структуры.
Нержавейка, магнитные свойства которой могут изменяться, – это преимущественно хромистые и хромоникелевые сплавы, которые могут относиться к одной из нижеприведенных групп.Мартенситные
Стали с мартенситной внутренней структурой, которые, как и обычные углеродистые, могут упрочняться при помощи закалки и отпуска. Такая нержавейка, кроме предприятий общего машиностроения, активно используются в быту (в частности, именно из нее производят столовые приборы и режущие инструменты). К наиболее распространенным маркам таких магнитных сталей, изделия из которых производятся с термообработкой и могут подвергаться финишной шлифовке и полировке, относятся 20Х13, 30Х13, 40Х13.
Сталь марки 30Х13 менее пластична, чем сплав 20Х13, несмотря на сходный состав (нажмите для увеличения)
В данную категорию также входит сплав марки 20Х17Н2, который отличается повышенным содержанием хрома в своем химическом составе, что значительно усиливает его коррозионную устойчивость. Почему такая нержавейка популярна? Дело в том, что, кроме высокой устойчивости к коррозии, она характеризуется отличной обрабатываемостью при помощи холодной и горячей штамповки, методов резания. Кроме того, изделия из такого материала хорошо свариваются.
Распространенной магнитной сталью ферритного типа, которая из-за невысокого содержания углерода в своем химическом составе отличается более высокой мягкостью, чем мартенситные сплавы, является 08Х13, активно используемая в пищевом производстве. Из такой нержавейки изготавливают изделия и оборудование, предназначенные для мойки, сортировки, измельчения, сортировки, а также транспортировки пищевого сырья.
Механические свойства стали 08Х13
Мартенситно-ферритныеПопулярной маркой магнитной нержавейки, внутренняя структура которой состоит из мартенсита и свободного феррита, является 12Х13.
Коррозионная стойкость стали марки 12Х13 (другое название 1Х13)
Нержавеющие стали, не обладающие магнитными свойствами
К нержавеющим сталям, которые не магнитятся, относятся хромоникелевые и хромомарганцевоникелевые. Их принято разделять на несколько групп.
АустенитныеНаиболее популярной маркой таких нержавеющих сталей, которые занимают ведущее место среди немагнитных стальных сплавов, является 08Х18Н10 (международный аналог по классификации AISI 304). Стали данного типа, к которым также относятся 08Х18Н10, 08Х18Н10Т, 12Х18Н10Т, 10Х17Н13М2Т, активно используются в производстве оборудования для пищевой промышленности; кухонной посуды и столовых приборов; сантехнического оснащения; емкостей для пищевых жидкостей; элементов холодильного оборудования; емкостей для пищевых продуктов; предметов медицинского назначения и др.
Состав и применение аустенитных сталей
Большие преимущества такой нержавейки, не обладающей магнитными свойствами, – это ее высокая коррозионная устойчивость, демонстрируемая во многих агрессивных средах, и технологичность.
Аустенитно-ферритныеСтали данной группы, наиболее популярными марками которых являются 08Х22Н6Т, 08Х21Н6М2Т и 12Х21Н5Т, отличаются высоким содержанием хрома, а также пониженным содержанием никеля. Для придания такой нержавейке требуемых характеристик (оптимального сочетания высокой прочности и хорошей пластичности, устойчивости к межкристаллитной коррозии и коррозионному растрескиванию) в ее химический состав вводят такие элементы, как медь, молибден, титан или ниобий.
Химический состав некоторых промышленных марок аустенитно-ферритных сталей (нажмите для увеличения)
Кроме вышеперечисленных, к нержавеющим сталям, которые не магнитятся, относятся сплавы с аустенитно-мартенситной и аустенитно-карбидной структурой.
Как определить, является ли магнитная или немагнитная сталь нержавеющей
Учитывая все вышесказанное, можно сделать следующий вывод: даже если сталь обладает магнитными свойствами, это совершенно не значит, что ее нельзя отнести к сплавам нержавеющего типа. Существует достаточно простой способ, позволяющий проверить, является ли магнитная сталь нержавейкой. Для того чтобы это определить, необходимо зачистить участок поверхности проверяемого изделия до металлического блеска, а затем нанести на этот участок несколько капель концентрированного медного купороса.
На то, что перед вами именно нержавейка, укажет налет красной меди, которым покроется зачищенный участок. Такой несложный способ позволяет очень точно определить, является ли магнитная сталь нержавеющей. А вот проверить (а особенно определить в домашних условиях), относится ли нержавейка к категории пищевых, практически невозможно.
Если вы решили проверить, относится магнитная сталь к нержавеющим или нет, имейте в виду, что такие ее свойства, как способность намагничиваться, нисколько не ухудшают ее коррозионной устойчивости.
Сталь 40Х13 (4Х13) – конструкционная высоколегированная, коррозионно-стойкая, жаростойкая, жаропрочная
Втулки, оси, валы, пружины, рессоры, корпусы, цапфы, лопасти, бандажи паровых турбин, диски, работающие при температуре до 400-450°С, карбюраторные иглы, болты, гайки и другие детали, работающие в коррозионных средах. Сталь данной марки коррозионно-стойкая, мартенситного класса, характеризуется высокой прочностью и износостойкостью. |
Сортовой прокат – ГОСТ 5949-75 Прутки – ГОСТ 18907-73 Лист тонкий – ГОСТ 5582-75 Проволока – ГОСТ 18143-72 |
C | Si | Mn | S | P | Cr |
---|---|---|---|---|---|
0,36-0,45 | ≤0,8 | ≤0,8 | ≤0,025 | ≤0,030 | 12,0-14,0 |
Ас | Ас3 | Ar1 | Ar3 |
---|---|---|---|
820 | 870 | 780 | – |
ГОСТ | Режим термообработки | Сечение мм | σ0,2 | σв | δ | Ψ | KCU | HB | ||
---|---|---|---|---|---|---|---|---|---|---|
Н/мм2 | % | Дж/см2 | ||||||||
Операция | t, ºC | Охлаждающая среда | не менее | |||||||
5582-75 | Отжиг или отпуск | 740-800 | – | 0,7-3,9 | – | 550 | 15 | – | – | – |
5949-75 | Закалка Отпуск |
1000-1050 200-300 |
Масло Воздух или масло |
≤200 | Не определяются | ≥50 (HRC) 143-229 |
||||
18143-72 | В состоянии поставки термообработанная | 1 класс 2 класс |
1,0-6,0 | – | 640-880 | 14 10 |
– | – | – | |
18907-73 | В состоянии поставки термообработанная | 1,0-30,0 | – | 590-810 | 10 | – | – | 143-229 |
Вид коррозии | Среда | t, ºC | Длительность, ч.![]() | Балл стойкости |
---|---|---|---|---|
Общая | Концентрированная H2SO4 | +20 | 720 | 1 |
63% H2SO4 | 40 | 24 | 4 | |
24% аммиак | +20 | 720 | 1 | |
Точечная | Для повышения коррозионной стойкости рекомендуется производить закалку и отпуск при температуре 250-300°С. | |||
Коррозионное растрескивание | ||||
Межкристаллитная | – |
Коэффициент чувствительности к надрезу за 104 ч. | Жаростойкость | |||||
---|---|---|---|---|---|---|
– | Среда | t, °С | Скорость коррозии, мм/год | База испытаний, ч. | ||
Чувствительность к охрупчиванию при старении | Окалиностойкая при длительном сроке службы с температурой до 600°С.![]() |
|||||
Время, ч. | t,°С | KCU, Дж/см2 | ||||
Исходное состояние | 21 | |||||
5000 | 470 | 22 |
Свариваемость | Температурные параметры ковки, °С | Обрабатываемость резанием |
---|---|---|
Не применяется для сварных конструкций. | 1100-800 | В закаленном и отпущенном состоянии при 340 HB и σв ≥ 735 Н/мм2. Kv=0,6 (твердый сплав) Kv=0,4 (быстрорежущая сталь) |
σв | Временное сопротивление (предел прочности при разрыве) | Мк | Температура начала мартенситного превращения |
---|---|---|---|
σвс | Предел прочности при сжатии; | G | Модуль сдвига |
σи | Предел прочности при изгибе | v | Коэффициент Пуассона |
τпч | Предел прочности при кручении | γ | Плотность |
σт | Предел прочности физический (нижний предел текучести) | C | Удельная теплоемкость |
σ0,05 | Условный предел упругости с допуском на остаточную деформацию 0,05% | λ | Теплопроводность |
σ0,2 | Предел текучести условный с допуском на величину пластической деформации при нагружении 0,2% | α | Коэффициент линейного расширения |
δр | Относительное равномерное удлинение | H | Напряженность магнитного поля |
δ | Относительное удлинение после разрыва | μ | Магнитная проницаемость |
ψ | Относительное сужение после разрыва | B | Магнитная индукция |
KCU | Ударная вязкость, определенная на образцах с концентратором вида U | Bs | Индукция насыщения |
KCV | Ударная вязкость, определенная на образцах с концентратором вида V | ΔB | Разброс магнитной индукции вдоль и поперек направления прокатки |
Tk | Критическая температура хрупкости | PB,v0 | Удельные магнитные потери при частоте тока v0и индукции B |
HB | Твердость по Бринеллю | Hc | Коэрцитивная сила |
d10 | Диаметр отпечатка по Бринеллю при диаметре шарика 10 мм и испытательной нагрузке 2943 Н | ρ | Удельное электросопротивление |
HRA | Твердость по Роквеллу (шкала А, конусный наконечник с общей нагрузкой 588,4 Н) | Kp | Красностойкость |
HRB | Твердость по Роквеллу (шкала В, сферический наконечник с общей нагрузкой 980,7 Н) | tпик | Температура полного расплавления металла |
HRC | Твердость по Роквеллу (шкала С, конусный наконечник с общей нагрузкой 1471 Н) | tсол | Температура начала плавления металла |
HV | Твердость по Виккерсу при нагрузке 294,2 Н и времени выдержки 10-15 с | d0 | Начальный диаметр образца |
HSD | Твердость по Шору | l0 | Длина расчетной части образца |
Тз | Заданный ресурс; | V | Скорость деформирования образца |
σtдп,Тз | Условный предел длительной прочности (величина напряжений, вызывающая разрушение при температуре t и заданном ресурсе) | è | Скорость деформации образца |
σ-1 | Предел выносливости при симметричном цикле (растяжение-сжатие) | a | Толщина образца при испытании листов на изгиб |
τ-1 | Предел выносливости при симметричном цикле (кручение) | d | Толщина оправки при испытании листов на изгиб |
σа | Наибольшее положительное значение переменной составляющей цикла напряжений | S | Толщина стенки |
Δε | Размах упруго-пластической деформации цикла при испытании на термическую усталость | Cl’ | Хлор-ион |
N | Число циклов напряжений или деформаций, выдержанных нагруженным объектом до образования усталостной трещины определенной протяженности или до усталостного разрушения | F’ | Фтор-ион |
σ0 | Начальное нормальное напряжение при релаксации | Σ | Коэффициент износостойкости при абразивном износе |
στ | Остаточное нормальное напряжение при релаксации | Σr | Коэффициент износостойкости при гидроабразивном износе |
K1c | Коэффициент интенсивности напряжений | v | Скорость резания |
Ac1 | Температура началаα—>γ превращения при нагреве (нижняя критическая точка) | Kv | Коэффициент относительной обрабатываемости |
Ac3 | Температура конца α—>γ превращения при нагреве (верхняя критическая точка) | T | Время |
Ar1 | Температура конца γ—>αпревращения при охлаждении (нижняя критическая точка) | t | Температура |
Ar3 | Температура начала γ—>αпревращения при охлаждении (верхняя критическая точка) | tотп | Температура отпуска |
Mн | Температура начала мартенситного превращения | tисп | Температура испытания |
РД | Ручная дуговая сварка покрытыми электродами | РАД | Ручная аргонодуговая сварка неплавящимся электродом |
МП | Механизированная сварка плавящимся электродом в среде углекислого газа | АФ | Автоматическая сварка под флюсом |
ЭШ | Электрошлаковая сварка | ЭЛ | Электронолучевая сварка |
КТ | Контактная сварка | Kv | Коэффициент относительной обрабатываемости стали.![]() 1) Для условий точения твердосплавными резцами Kv=v60/145, где v60 – скорость резания, соответствующая 60-ти минутной стойкости резцов при точении данного материала, м/мин; 145 – значение скорости резания при 60-ти минутной стойкости резцов при точении эталонной стали марки 45. 2) Для условий точения резцами из быстрорежущей сталиKv=v60/70, где 70 – значение скорости резания при 60-ти минутной стойкости быстрорежущих резцов при точении эталонной стали марки 45. |
Сталь 40х23 (4Х13) / Auremo
Сталь 10Х18Н5Г9АС4 (ЭП492; ВНС-3) Сталь 10Х32Н4Д (ЭП529) Сталь 10Х17Н5М2 (ЭП405) Сталь 10Х17Н13М3Т (ЭИ432) Сталь 10Х17Н13М2Т (ЭИ448) Сталь 10Х14Г14Н3 (ДИ-6) Сталь 10Х14АГ15 (ДИ-13) Сталь 09Х17Н7Ю1 (0Х17Н7Ю1) Сталь 09Х17Н7Ю (ЭИ973) Сталь 09Х16Н4Б (ЭП56; 1Х16Н4Б) Сталь 09Х15Н8Ю1 (09Х15Н8Ю; ЭИ904) Сталь 08ХГСДП Сталь 08Х22Н6Т (ЭП53) Сталь 08Х21Г11А6 (ВНС-53) Сталь 08Х20Н4АГ10 (НН-3) Сталь 08Х18Т (ДИ-77) Сталь 08Х18Н7Г10АМ3 (08Х18Н7Г10АМ3С2) Сталь 08Х18Н5Г12АБ (ХН-3Б) Сталь 08Х18Н5Г11БАФ (ХН-3БФ) Сталь 08Х18х5Г11АФ (ХН-3Ф) Сталь 08Х18Н12Т (0Х18Н12Т) Сталь 08Х18х22Б (ЭИ402) Сталь 08Х18Г8Н2Т (КО-3) Сталь 08Х17Н6Т (ДИ-21) Сталь 20Х13Н4Г9(ЭИ100) Сталь Х17Н14М3Т Сталь Х17Н14М2Т Сталь 95Х18 (ЭИ229) Сталь 95Х13М3К3Б2Ф (ЭП766) Сталь 65Х13 Сталь 40Х13 (4Х13) Сталь 30Х13 (3Х13) Сталь 26Х14Н2 (ЭП208) Сталь 25Х17х3Б Сталь 25Х17х3 (ЭП407) Сталь 25Х13Н2 (ЭИ474) Сталь 20Х17х3 (2Х17х3) Сталь 08Х17Н15М3Т (ЭИ580) сталь 18Х13х4 Сталь 15Х18Н12С4ТЮ (ЭИ654; 2Х18Н12С4ТЮ) Сталь 15Х17АГ14 (ЭП213) Сталь 13Х18Н10Г3С2М2 (ЗИ98) Сталь 12Х21Н5Т (ЭИ811; 1Х21Н5Т) Сталь 12Х18Н13АМ3 (ЭП878) Сталь 12Х18х20Э (ЭП47) Сталь 12Х17Н8Г2С2МФ (ЗИ126) Сталь 12Х17Г9АН4 (ЭИ878) Сталь 12Х13Г12АС2Н2 (ДИ50) Сталь 11Х13Н3 Сталь 03Х16Н15М3 (ЭИ844) сталь 04Х15СТ Сталь 04Х17х20М2 Сталь 03Х23Н6 (ЗИ68) Сталь 03Х22Н6М2 (ЗИ67) Сталь 03Х21Н25М5ДБ Сталь 03Х21Н21М4ГБ (ЗИ35) Сталь 03Х20Н45М5Б (ЧС32; 03ХН45МБ) Сталь 03Х18Н12Т (000Х18Н12Т) Сталь 03Х18Н12 (000Х18Н12) Сталь 03Х18Н11 (000Х18Н11) Сталь 03Х17Н14М2 Сталь 03Х17АН9 (ЭК177) сталь 04Х17Т Сталь 03Х15Н35Г7М6Б (ЭП855) Сталь 03Х13АГ19 (ЧС36) Сталь 03Х12Н10МТР (ЭП810; ВНС-25) Сталь 03Х12К10М6Н4Т (ЭП927) Сталь 03Х11Н10М2Т2 (ЭП853) Сталь 02Х25Н22АМ2 (ЧС108) Сталь 02Х21Н25М5ДБ (EC5) Сталь 02Х21Н21М4Г2Б (ЗИ69) сталь 02Х18Н11 Сталь 02Х17х24М3 Сталь 015Х16Н15М3 Сталь 06Х14Н6Д2МБТ (ЭП817) Сталь 08Х17Н13М2Т (0Х17Н13М2Т; ЭИ448) Сталь 08Х10Н20Т2 (0Х10Н20Т2) Сталь 08Х10Н16Т2 (0Х10Н16Т2) Сталь 07Х21Г7АН5 (ЭП222) Сталь 07Х18Н10П (ЭП287) Сталь 07Х16Н6 (ЭП288; СН-2А; Х16Н6) Сталь 07Х16Н4Б Сталь 07Х15Н7М2 (ЭП35; СН-4; Х15Н8М2Ю) Сталь 07Х16Н6 Сталь 06Х18х21 (ЭИ684) сталь 06Х15х5ДМ Сталь 08Х17Н5М3 (ЭИ925) сталь 06Х13х5ДМ Сталь 06Х12Н3Д Сталь 06Х12Н3Д (08Х12Н3Д) сталь 05ХГБ Сталь 05Х20Н15АГ6 (ЧС109) Сталь 05Х12Н9М2С3 (ЭП821) Сталь 05Х12Н2К3М2АФ (ВНС-40) Сталь 04Х32Н8 (ЭП535) Сталь 04Х25Н5М2 (ДИ62) Сталь 04Х19МАФТ Сталь 04Х18х20 (ЭИ842)
Обозначение
Наименование | Значение |
---|---|
Обозначение ГОСТ Кириллица | 40Х13 |
Обозначение ГОСТ латинское | 40X13 |
Транслитерация | 40х23 |
Химические элементы | 40Cr13 |
Имя | Значение |
---|---|
Обозначение ГОСТ Кириллица | 4Х13 |
Обозначение ГОСТ латинское | 4X13 |
Транслитерация | 4ч23 |
Химические элементы | 4Cr13 |
Описание
40Х13 сталь применяется: для изготовления режущего, мерительного инструмента, пружин, игл карбюраторов, хозяйственных изделий, клапанных тарелок, компрессоров и других деталей, работающих при температуре до 400-450 °С; детали, работающие в агрессивных средах; различные детали авиастроения (детали с повышенной твердостью, изнашиваемые, работающие при больших механических нагрузках и в условиях релаксации (нержавеющие пружины, болты, пальцы, арматура, оси и подшипники приборов).
Примечание
Сталь хромистая коррозионно-стойкая мартенситного класса. Сталь марки
применяется после закалки и низкого отпуска со шлифованной и полированной поверхностью, имеет высокую твердость.
Из-за склонности стали к самопроизвольному растрескиванию сразу после закалки деталь подвергают отпуску.
Стандарты
Наименование | Код | Стандарты |
---|---|---|
Листы и полосы | В23 | ГОСТ 103-2006 |
Прокат сортовой и фасонный | В22 | ГОСТ 1133-71, ГОСТ 2590-2006, ГОСТ 2591-2006, ГОСТ 2879-2006 |
Проволока из легированной стали | В73 | ГОСТ 18143-72, ТУ 14-173-6-91 |
Листы и полосы | В33 | ГОСТ 4405-75, ГОСТ 5582-75, ТУ 14-1-1422-75, ТУ 14-1-2186-77 |
Классификация, номенклатура и общие нормы | В30 | ГОСТ 5632-72 |
Прокат сортовой и фасонный | В32 | ГОСТ 5949-75, ГОСТ 7417-75, ГОСТ 8559-75, ГОСТ 8560-78, ГОСТ 14955-77, ГОСТ 18907-73, ТУ 14-1-2972-80, ТУ 14-1-377-72, ТУ 14-1-3957-85, ТУ 14-11-245-88 |
Классификация, номенклатура и общие нормы | В20 | ОСТ 1-91 |
Быки.![]() | В21 | ОСТ 1 |
Быки. Бланки. Плиты | В31 | ОСТ 3-1686-90, ОСТ 95-10-72 |
Обработка металлов давлением. Поковки | В03 | ОСТ 5Р.9125-84, ТУ 14-1-1530-75 |
Термическая и термохимическая обработка металлов | В04 | СТП 26.260.484-2004 |
Химический состав
Стандарт | С | С | Р | Мн | Кр | Си | Ni | Фе | Медь | В | Ти | Пн | Вт |
---|---|---|---|---|---|---|---|---|---|---|---|---|---|
ТУ 14-1-2186-77 | 0,35-0,44 | ≤0,025 | ≤0,03 | ≤0,6 | 12-14 | ≤0,6 | ≤0,5 | Остальные | ≤0,3 | ≤0,2 | ≤0,2 | ≤0,3 | ≤0,2 |
ГОСТ 5632-72 | 0,36-0,45 | ≤0,025 | ≤0,03 | ≤0,8 | 12-14 | ≤0,8 | ≤0,6 | Остальные | ≤0,3 | ≤0,2 | ≤0,2 | ≤0,3 | ≤0,2 |
Основа Fe .
По ТУ 14-1-2186-77 для стали, выплавленной с электрошлаковым переплавом, содержание S ≤ 0,015%.
Механические характеристики
Сечение, мм | t отпускания, °С | с Т |с 0,2 , МПа | σ B , МПа | д 5 , % | д 4 | д | г, % | кДж/м 2 , кДж/м 2 | Число твердости по Бринеллю, МПа | HRc |
---|---|---|---|---|---|---|---|---|---|---|
Стальной прокат. Закалка в масло с 1000 °С + Отпуск | ||||||||||
– | 200 | ≥1620 | ≥1840 | ≥1 | – | – | ≥2 | – | – | ≥52 |
Образец деформированный диаметром 6 мм и длиной 30 мм. Скорость деформации 16 мм/мин Скорость деформации 0,009 1/с | ||||||||||
– | – | ≥120 | ≥130 | ≥64 | – | – | ≥96 | – | – | – |
Закалка в масло от 1050 °С до + Отпуск 550 °С (выдержка 10 ч) (при условии температуры и продолжительности теплового воздействия) | ||||||||||
– | – | ≥870 | ≥1080 | ≥11 | – | – | ≥43 | – | – | – |
Градация эксплуатационных свойств готовых термически обработанных деталей по ОСТ 1-91 | ||||||||||
– | – | – | – | – | – | – | – | – | – | 50-56 |
Заготовка (поковки) ОСТ 95-10-72.![]() | ||||||||||
≤200 | – | – | – | – | – | – | – | – | – | 48-56 |
Прокат стальной. Закалка в масло с 1000 °С + Отпуск | ||||||||||
– | 350 | ≥1450 | ≥1710 | ≥11 | – | – | ≥22 | – | – | ≥50 |
Образец деформированный диаметром 6 мм и длиной 30 мм. Скорость деформации 16 мм/мин Скорость деформации 0,009 1/с | ||||||||||
– | – | ≥100 | ≥125 | ≥68 | – | – | ≥92 | – | – | – |
Закалка в масло от 1050 °С до + Отпуск 550 °С (выдержка 10 ч) (при условии температуры и продолжительности теплового воздействия) | ||||||||||
– | – | ≥900 | ≥1080 | ≥13 | – | – | ≥42 | – | – | – |
Прокат стальной.![]() | ||||||||||
– | 500 | ≥1390 | ≥1680 | ≥7 | – | – | ≥9 | – | – | ≥51 |
Образец деформированный диаметром 6 мм и длиной 30 мм. Скорость деформации 16 мм/мин Скорость деформации 0,009 1/с | ||||||||||
– | – | ≥74 | ≥90 | ≥84 | – | – | ≥96 | – | – | – |
Закалка в масло от 1050 °С до + Отпуск 550 °С (выдержка 10 ч) (при условии температуры и продолжительности теплового воздействия) | ||||||||||
– | – | ≥940 | ≥1140 | ≥13 | – | – | ≥48 | – | – | – |
Листовой горячекатаный (1,5-3,9 мм) и холоднокатаный (0,7-3,9 мм) прокат по ГОСТ 5582-75.![]() | ||||||||||
– | – | – | ≥550 | ≥15 | – | – | – | – | – | – |
Образец деформированный диаметром 6 мм и длиной 30 мм. Скорость деформации 16 мм/мин Скорость деформации 0,0091/с | ||||||||||
– | – | ≥51 | ≥75 | ≥70 | – | – | ≥98 | – | – | – |
Прокат стальной. Закалка в масло от 1050 °С до + Отпуск 600 °С (выдержка 3 часа) (при условии температуры и продолжительности теплового воздействия) | ||||||||||
– | – | ≥840 | ≥1000 | ≥13 | – | – | 25-33 | – | – | – |
Образцы для махизматов. Закалка в масло с 1000-1050°С на воздухе + Отпуск при 200-300°С, охлаждение на воздухе или в масле | ||||||||||
– | – | – | – | – | – | – | – | – | – | 52 |
Поковки.![]() | ||||||||||
≤300 | – | – | – | – | – | – | – | – | 269-302 | – |
Образец деформированный диаметром 6 мм и длиной 30 мм. Скорость деформации 16 мм/мин Скорость деформации 0,009 1/с | ||||||||||
– | – | ≥45 | ≥57 | ≥73 | – | – | ≥100 | – | – | – |
Прокат стальной. Закалка в масло от 1050 °С до + Отпуск 600 °С (выдержка 3 часа) (при условии температуры и продолжительности теплового воздействия) | ||||||||||
– | – | ≥820 | ≥1080 | ≥12 | – | – | 28-31 | – | – | – |
Проволока термически обработанная в состоянии поставки по ГОСТ 18143-72 (относительное удлинение, % при номинальной длине образца 100 мм указано для проволоки 1 класса, в скобках – для 2 класса) | ||||||||||
1-6 | – | – | 640-880 | – | – | ≥14 (≥10) | – | – | – | – |
Образец деформированный диаметром 6 мм и длиной 30 мм.![]() | ||||||||||
– | – | ≥43 | ≥53 | ≥60 | – | – | ≥98 | – | – | – |
Прокат стальной. Закалка в масло от 1050 °С до + Отпуск 600 °С (выдержка 3 часа) (при условии температуры и продолжительности теплового воздействия) | ||||||||||
– | – | ≥890 | ≥1120 | ≥13 | – | – | ≥32 | – | – | – |
Аренда в состоянии поставки. Отжиг или отпуск при 740-800 °С | ||||||||||
1-6 | – | – | 590-880 | – | ≥10 | – | – | – | – | – |
Образец деформированный диаметром 6 мм и длиной 30 мм. Скорость деформации 16 мм/мин Скорость деформации 0,009 1/с | ||||||||||
– | – | ≥34 | ≥40 | ≥64 | – | – | ≥100 | – | – | – |
Прокат стальной.![]() | ||||||||||
– | – | ≥880 | ≥1060 | ≥14 | – | – | ≥46 | – | – | – |
Аренда в состоянии поставки. Отжиг или отпуск при 740-800 °С | ||||||||||
5 | – | – | – | – | – | – | – | – | 143-229 | – |
Образец деформированный диаметром 6 мм и длиной 30 мм. Скорость деформации 16 мм/мин Скорость деформации 0,009 1/с | ||||||||||
– | – | ≥27 | ≥35 | ≥60 | – | – | ≥100 | – | – | – |
Прокат стальной. Закалка в масло от 1050 °С до + Отпуск 530 °С (выдержка 6 ч) (при условии температуры и продолжительности теплового воздействия) | ||||||||||
– | – | ≥930 | ≥1100 | ≥13 | – | – | ≥47 | – | – | – |
Прутки шлифованные, обработанные на заданную прочность (ТС) по ГОСТ 18907-73 | ||||||||||
1-30 | – | – | 590-810 | – | – | ≥10 | – | – | – | – |
Прокат стальной.![]() | ||||||||||
– | – | ≥500 | ≥780 | ≥35 | – | – | ≥59 | – | ≥217 | – |
Стальной прокат. Закалка в масло от 1050 °С до + Отпуск 530 °С (выдержка 6 ч) (при условии температуры и продолжительности теплового воздействия) | ||||||||||
– | – | ≥750 | ≥990 | ≥14 | – | – | ≥37 | – | – | – |
Прутки горячекатаные и кованые по СТП 26.260.484-2004. Закалка в масло 1000-1050 °С + Отпуск, охлаждение на воздухе | ||||||||||
250-300 | ≥1500 | ≥1800 | ≥10 | – | – | ≥30 | ≥490 | – | – | |
Прокат стальной.![]() | ||||||||||
– | – | ≥1420 | ≥1670 | ≥6 | – | – | ≥34 | – | – | – |
Прутки горячекатаные и кованые по СТП 26.260.484-2004. Закалка в масло 1000-1050 °С + Отпуск, охлаждение на воздухе | ||||||||||
700-750 | ≥650 | ≥900 | ≥12 | – | – | ≥45 | ≥490 | – | – | |
Прокат стальной. Отжиг на воздухе 1030-1050 °С до + Отпуск при 530 °С (выдержка 2 часа), охлаждение на воздухе | ||||||||||
– | – | ≥1310 | ≥1360 | ≥7 | – | – | ≥36 | – | – | – |
Прокат стальной.![]() | ||||||||||
≤60 | – | ≥960 | ≥1165 | ≥13 | – | – | ≥47,5 | – | – | – |
Стальной прокат. Отжиг на воздухе 1030-1050 °С до + Отпуск при 530 °С (выдержка 2 часа), охлаждение на воздухе | ||||||||||
– | – | ≥960 | ≥1130 | ≥12 | – | – | ≥45 | – | – | – |
Прокат стальной. Отжиг на воздухе 1030-1050 °С + Нагрев до 530 °С (выдержка 2 часа), охлаждение на воздухе | ||||||||||
≤60 | – | ≥1145 | ≥1700 | ≥5,5 | – | – | ≥33,5 | – | – | – |
Прокат стальной.![]() | ||||||||||
– | – | ≥980 | ≥1070 | ≥12 | – | – | ≥49 | – | – | – |
Формовка по ОСТ 1 | ||||||||||
– | – | – | – | – | – | – | – | – | ≥50 | |
Стальной прокат. Отжиг на воздухе 1050 °С + Отпуск при 600 °С (выдержка 3 часа) | ||||||||||
– | – | ≥890 | ≥1120 | ≥13 | – | – | ≥32 | – | – | – |
– | – | ≥810 | ≥940 | ≥11 | – | – | ≥40 | – | – | – |
– | – | ≥710 | ≥900 | ≥10 | – | – | ≥39 | – | – | – |
– | – | ≥670 | ≥780 | ≥12 | – | – | ≥45 | – | – | – |
– | – | ≥470 | ≥520 | ≥20 | – | – | ≥77 | – | – | – |
– | – | ≥255 | ≥300 | ≥21 | – | – | ≥84 | – | – | – |
Прокат стальной.![]() | ||||||||||
– | – | ≥710 | ≥930 | ≥14 | – | – | ≥42 | – | – | – |
– | – | ≥540 | ≥640 | ≥15 | – | – | ≥44 | – | – | – |
– | – | – | ≥540 | ≥18 | – | – | ≥67 | – | – | – |
Описание механических меток
Наименование | Описание |
---|---|
Раздел | Секция |
с Т | с 0,2 | Предел текучести или предел пропорциональности с допуском на остаточную деформацию 0,2% |
о В | Предел кратковременной прочности |
д 5 | Удлинение после разрыва |
д 4 | Удлинение после разрыва |
д | Удлинение после разрыва |
у | Относительное сужение |
кДж/м 2 | Прочность |
HRc | Твердость по Роквеллу (индентор алмазный сфероконический) |
Физические характеристики
Температура | Е, ГПа | р, кг/м3 | л, Вт/(м · °С) | Р, НОМ · м | С, Дж/(кг·°С) | а, 10-6 1/°С |
---|---|---|---|---|---|---|
0 | 214 | 7650 | 25 | – | – | – |
20 | 218 | 7650 | 25 | 590 | 461 | – |
100 | 208 | 7630 | 26 | 786 | – | 107 |
200 | 202 | 7600 | 27 | 830 | – | 115 |
300 | 194 | 7570 | 28 | 890 | – | 119 |
400 | 185 | 7540 | 29 | 950 | – | 122 |
500 | 173 | 7510 | 29 | 998 | – | 125 |
600 | 160 | 7480 | 29 | 1046 | – | 128 |
700 | 148 | 7450 | 28 | 1122 | – | 138 |
800 | 140 | 7420 | 28 | 1180 | – | 13 |
900 | – | – | 29 | 1160 | 666 | – |
1000 | – | – | – | – | – | 132 |
1100 | – | – | – | – | 691 | – |
Описание физических символов
Наименование | Описание |
---|---|
Е | Нормальный модуль упругости |
Г | Модуль упругости при сдвиге и кручении |
р | Плотность |
л | Коэффициент теплопроводности |
Р | УД.![]() |
и | Коэффициент линейного расширения |
С | Удельная теплоемкость |
Технологические свойства
Имя | Значение |
---|---|
Свариваемость | Не относится к сварным конструкциям. |
Температура ковки | Начало – 1200°С, конец – 850°С. сечения до 200 мм подвергают низкотемпературному отжигу. |
Возможность обработки резанием | В закаленном и отпущенном состоянии при нагнетателе СБ 340 и НВ=730 МПа Кн тв.узд.=0,6 Кн б.ст.=0,4. |
Особенности термической обработки | Изделия из стали можно подвергать закалке, отпуску, отжигу. Закалку и отпуск изделий проводят для достижения: а) максимальной коррозионной стойкости; б) заданный уровень механических свойств. Закалку стальных изделий проводят в масле с 1000-1050 °С. Время выдержки при нагреве под закалку для изделий с толщиной стенки или диаметром до 10 мм – 20 мин, свыше 10 мм – 20 мин + 1 мин на 1 мм максимальной толщины.![]() ![]() |
Понимание магнитных свойств нержавеющей стали 304 и 316 • MicroGroup
Опубликовано Николь Беланже 4 апреля 2017 г. должен иметь магнитные свойства или нет. Прежде чем определить это, хорошо бы понять, что делает марку нержавеющей стали магнитной или нет.
Нержавеющие стали представляют собой сплавы на основе железа, особенно известные своей превосходной коррозионной стойкостью. Существует несколько различных типов нержавеющей стали. Двумя основными типами являются аустенитные (изделия MicroGroup: 304х30RW, 304F10250X010SL например) и ферритные (автомобильные приложения, кухонная утварь и промышленное оборудование), каждый из которых имеет различный химический состав. Из-за этой разницы ферритные нержавеющие стали обычно являются магнитными, а аустенитные – нет. Ферритная нержавеющая сталь обязана своим магнетизмом двум факторам: высокой концентрации железа и своей основной структуре.
Ферритные – обычно магнитные Аустенитные – немагнитные
Типовой анализ нержавеющей стали
Превращение немагнитных фаз в магнитные
9000 2 Нержавеющие стали 304 и 316 являются аустенитными, при охлаждении железо остается в форме аустенита (гамма-железа), немагнитной фазы железа.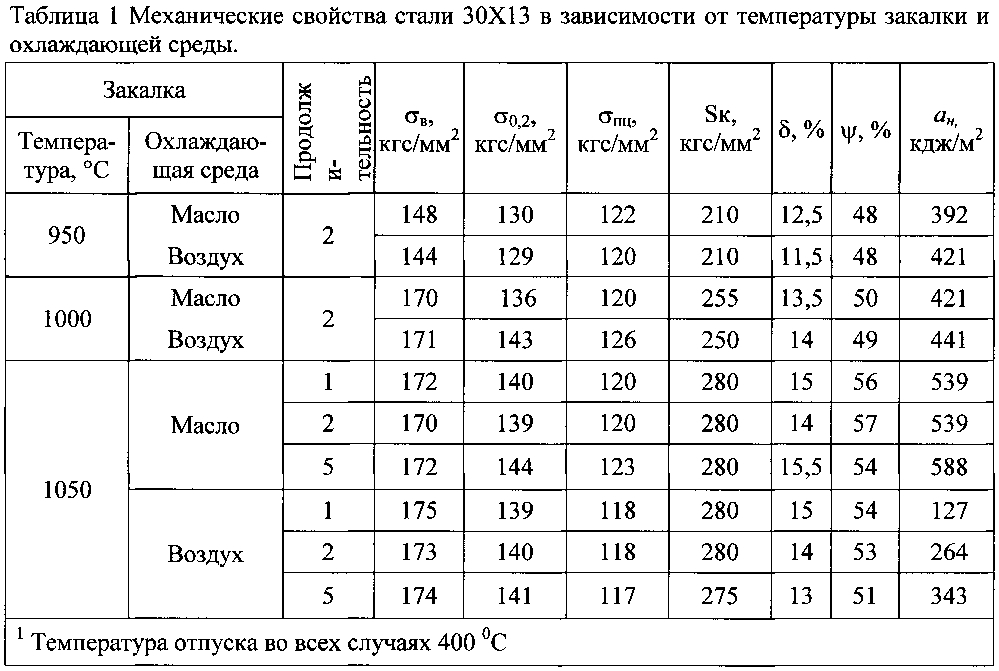
Однако это не означает, что вы должны ожидать измерения такой низкой восприимчивости любого предмета из нержавеющей стали 304 или 316, с которым вы столкнетесь. Любой процесс, который может изменить кристаллическую структуру нержавеющей стали, может привести к превращению аустенита в ферромагнитные мартенситные или ферритные формы железа. Эти процессы включают холодную обработку и сварку. Также возможно самопроизвольное превращение аустенита в мартенсит при низких температурах.