65Г сталь свойства: характеристики и применение, сталь 65Г – зарубежные аналоги
alexxlab | 18.07.2019 | 0 | Разное
Сталь 65Г. Состав и свойства ~ БЛОГ О ЗАТОЧКЕ
Сталь марки 65Г – конструкционная, рессорно-пружинная сталь производства Украины. Твердость от обычных 45-47HRC до редких 61HRC, в зависимости от температуры отпуска. Традиционно в промышленности применяется для изготовления пружин, рессор, шестерней, фланцев, корпусов подшипников и т.д. Легко поддается коррозии. Сталь плохо выдерживает ударные нагрузки, при уровне магния выше 1% склонна к отпускной хрупкости. При закалке до 47-50HRC сталь 65Г имеет приличную ударную вязкость и стать неплохим вариантом для метательных ножей и турнирных мечей. При изготовлении ножей и закалке до 58-61HRC считается довольно износоустойчивой сталью с хорошей упругостью.
Похожие аналоги: ?
Состав стали 65Г, % | |||||||||
---|---|---|---|---|---|---|---|---|---|
C | Cr | Mn | Mo | Ni | P | Si | S | V | Другое |
0.62-0.7 | 0.25 | 0.9-1.2 | – | 0.25 | 0.35 | 0.17-0.37 | 0.035 | – | 0.2/Cu |
=
СВОЙСТВА ЭЛЕМЕНТОВ СТАЛИ:
Углерод (C, Carbon): улучшает удержание кромки и повышает вязкость; увеличивает твердость и сопротивление износу; уменьшает пластичность; в больших значениях понижает коррозионную стойкость.
Хром (Cr, Chromium): повышает твердость, сопротивление растяжению и плотность; повышают устойчивость к коррозии (>11% делает сплав нержавеющим).
Марганец (Mn, Manganese): повышает прокаливаемость, износостойкость и вязкость; используется как раскислитель и дегазатор для удаления кислорода при плавке металла; в больших % увеличивает твердость и хрупкость.
Молибден (Mo, Molybdenum): увеличивает твердость, прочность, прокаливаемость и плотность; улучшает обрабатываемость и устойчивость к коррозии.
Никель (Ni, Nickel): добавляет ударную вязкость; улучшает коррозионную стойкость; уменьшает твердость.
Фосфор (P, Phosphorus): считается вредной примесью. Растворяется в феррите, за счет этого повышается прочность, но снижается пластичность и ударная вязкость с увеличением склонности стали к хрупкости. В низколегированных сталях с углеродом около 0.1% фосфор повышает прочность и сопротивление атмосферной коррозии. Считается вредной примесью.
Кремний (Si, Silicon): увеличивает прочность; используется как раскислитель и дегазатор для удаления кислорода при плавке металла.
Сера (S, Sulfur): обычно считается вредной примесью влияющей на пластичность, ударную вязкость, свариваемость, коррозионные свойства, качество поверхности стали и т.д. Вредное влияние серы уменьшает присутствие в стали марганца. Содержание же серы в качественных сталях не превышает 0.02-0.03%.
Ванадий (V, Vanadium): увеличивает прочность, износостойкость, повышает плотность и вязкость; повышает коррозионную стойкость, увеличивая оксидную пленку; карбидные включения ванадия очень твердые.
Вольфрам (W, Tungsten): добавляет прочности, вязкости и улучшает прокаливаемость; сохраняет твердость при высоких температурах.
Кобальт (Co, Cobalt): увеличивает прочность и твердость, позволяет закалку при более высоких температурах; усиливает эффекты других элементах в сложных сталях.
Ниобий (Nb, Niobium): ограничивает рост карбидов; ограничивает обрабатываемость; создает самые твердые карбиды.
Азот (N, Nitrogen): используется вместо углерода в стальной матрице (атомы азота функционируют аналогично атомам углерода, но обладают преимуществами в коррозионной стойкости)…
ZAT (Днепр, Украина)
http://www.zat24.com/
Создана 01.02.18, посл.обновление – 26.04.19
Лист сталь 65Г холоднокатный в наличии
Сталь 65Г – конструкционная рессорно-пружинная легированная сталь.
Марка 65Г обладает высокой износостойкостью, поэтому широко применяется в машиностроении. Из стали 65Г изготавливаются пружины и рессоры, фланцы, шайбы, шестерни, тормозные диски и ленты, подающие и зажимные цанги и другие элементы конструкций.
Лист или полоса 65Г зачастую применяется для изготовления ножей, поскольку сталь 65Г обладает хорошими режущими свойствами и поддается оксидированию (воронению, чернению). Сталь 65Г одна из самых дешевых марок сталей, используемых для изготовления ножей. Похожие механические и физические свойства позволяют использовать лист марки 65Г вместо стали 60С2А, 70, 55С2, 9ХС и У8А.
ЛИСТОВОЙ ПРОКАТ ИЗ РЕССОРНО-ПРУЖИННОЙ
ЛЕГИРОВАННОЙ СТАЛИ 65Г
Марка и химический состав стали 65Гпо плавочному анализу
соответствуют нормам, указанным в таблице 1:
Таблица 1
Прокат из качественной стали 65Г может быть изготовлен с массовой долей серы не более 0,035 % и фосфора не более 0,035%
Твердость проката марки 65Г для термически необработанного составляет не более 285 HB, диаметр отпечатка не менее 3,6 мм. Для термически обработанного проката 65Г твердость не более 241 HB, диаметр отпечатка не менее 3,9 мм.
Механические свойства проката категорий 3, 3А, 3Б, 3В, 3Г, 4, 4А, 4Б, определяемые на термически обработанных продольных образцах, должны соответствовать нормам, указанным в таблице 2.
Таблица 2
Светлый лист должен иметь поверхность металлического цвета от светло-серого до темно-серого оттенков.
На светлом листе с цветами побежалости допускается окисленная поверхность с неоднородными цветами побежалости различных оттенков.
Цвет поверхности темного листа не регламентируется. На поверхности темного листа допускаются пятна загрязнения.
На поверхности листа допускается наличие единичных плен, а также отдельных мелких царапин, рисок, отпечатков, рябизны, величина которых не превышает:
для светлых и светлых с цветами побежалости листов – половины предельных отклонений по толщине;
для темных листов – предельного отклонения по толщине.
Параметр шероховатости поверхности светлого листа не более Ra 1,25 мкм.
Таблица 3
Ширина листов холоднокатаных марки 65Г, предлагаемых нами, от 350 до 480 мм, длина листов 2000 мм.
Лист 65Г хранится на крытом складе, что позволяет нам сохранить его в первозданном виде, без коррозии. Для приобретения листа марки 65Г холоднокатаного обращайтесь к нам по телефону +7 (343) 202-00-77, либо отправляйте Ваш запрос на e-mail: [email protected].
Температура закалки, °С
Температура отпуска, °С
Предел текучести
Ơт, Н/мм2
(кгс/мм2)
Временное сопротивление Ơв, Н/мм2
(кгс/мм2)
Относительное удлинение
δ5, %
Относительное сужение
φ, %
Закалочная среда
Механические свойства, не менее
Режим термической обработки
(ориентировочный)
Сталь 65Г.

Классификация: cталь конструкционная рессорно-пружинная
Применение: пружины, рессоры, упорные шайбы, тормозные ленты, фрикционные диски, шестерни, фланцы, корпусы подшипников, зажимные и подающие цанги и другие детали, к которым предъявляются требования повышенной износостойкости, и детали, работающие без ударных нагрузок.
Химический состав в % материала 65Г (ГОСТ 14959 – 79)
C | Si | Mn | Ni | S | P | Cr | Cu |
0,62-0,7 | 0,17-0,37 | 0,9-1,2 | до 0,25 | до 0,035 | до 0,035 | до 0,25 | до 0,2 |
Зарубежные аналоги материала 65Г (указаны как точные, так и ближайшие аналоги)
США | Германия | Англия | Китай | Болгария | Польша |
– | DIN,WNr | BS | GB | BDS | PN |
1066 1566 G15660 |
66Mn4 Ck67 |
080A67 | 65Mn | 65G | 65G |
Большой популярностью пружинная сталь 65Г пользуется при производстве всевозможных пружин.
Сталь 65Г, как и любая пружинно-рессорная сталь, обладает хорошими режущими свойствами и поддается оксидированию — воронению и чернению. Полоса или лист 65Г успешно применяются для изготовления ножей. В основном из этой стали изготавливают метательные ножи, где больше важна прочность и износостойкость, чем твердость. При этом закалка проводится до твердости 45-47 ед. HRC.
Осуществляется доставка по всем регионам Российской Федерации: Московская область, Самара, Челябинская область, Свердловская область (Екатеринбург), Уфа (Республика Башкортостан), Республика Татарстан, Курганская область, Тюменская область, Пермский край, Оренбургская область, Краснодарский край, Удмуртская Республика и далее – все регионы России.
Наши менеджеры будут рады предоставить вам всю необходимую информацию.
Вся информация на сайте носит справочный характер и не является публичной офертой, определяемой положениями Статьи 437 Гражданского кодекса Российской Федерации. Технические параметры (спецификация) и комплект поставки товара могут быть изменены производителем.
Магазин Златоустовских украшенных изделий. Ножи Златоуста, Украшенное оружие, украшенная посуда. Часы, часы водолазные, секундомеры. © 2021 mybestbuy.ru
Сталь 65Г
Рессорно-пружинная сталь 65Г получила достаточно широкое распространение в современном промышленном производстве. Основное свое применение этот материал нашел в машиностроении. Благодаря своей прочности и износостойкости сталь 65г стала лидером в своей отрасли, также стоит отметить приемлемую цену данного изделия по сравнению с конкурентами. Все перечисленные преимущества позволяют использовать ее в производстве ряда деталей и конструкций (в том числе и для медицины – изготовление износостойких деталей для протезирования), к примеру, таких как: металлические уголки и швеллера, которые применяются при сооружении различных видов заборов, шайб, пружин, корпусов подшипников, тормозных лент, фланцев и шестерен.
Также хотелось бы поговорить о механических свойствах стали 65г. Данный материал имеет повышенную отпускную хрупкость, потому не должен применяться в конструкциях с ударной нагрузкой, иначе это приведет к поломке изделия.
Стоит упомянуть, что сталь 65г выпускается в следующих разновидностях: сортовой прокат, шлифованный или калиброванный пруток, лента, лист 65г, полоса, проволока, кованые заготовки. За всеми видами закреплены соответствующие ГОСТы, что еще раз дает возможность убедиться в качестве данной продукции.
Важным его свойством является неприменимость материала для изготовления сварных конструкций. Сваривание возможно, но для этого следует соблюсти ряд условий: во-первых, для получения качественных сварных соединений требуется подогрев: перед сваркой до 200-300 градусов, во-вторых, после сварки необходима термообработка, а именно – отжиг.
Еще стоит отметить, что сталь имеет прекрасные режущие свойства и отлично поддается оксидированию, что позволяет применять ее в производстве ножей. Опять же цена играет важную роль, так как этот вид стали, пожалуй, самый дешевый для данного производства.
Свойства конструкции изделия позволили заменить многие другие виды стали, а именно: 55С2 и 60С2, 70 и 70Г, У8А и 9Хс. Это можно считать еще одним выигрышным экономическим показателем.
Область применения стали 65Г — ООО ЭнТехМет
В процессе выбора металлопроката важно знать маркировку продукции. Именно эти знания помогут в дальнейшем сделать правильный выбор в соответствии с дальнейшим предназначением. Дело в том, что на маркировке опытные специалисты смогут распознать все основные свойства и особенности металлопродукции и спланировать грамотное ее использование. Буквенное обозначение, которое определено ГОСТ указывает на эти свойства.
Сталь 65г купить означает приобретение низколегированной стали. В состав металла включен такой химический элемент как марганец. Двухзначное число (в данном случае – 65) указывает на процентное содержание углерода.
Некоторые свойства.
Одна из основных особенностей этого металла, которая обусловлена вхождением в состав ряда химических элементов – достаточно высокий предел текучести. Благодаря этому свойству сплав включен в категорию рессорно-пружинных сталей со всеми вытекающими из данного определения направлениями дальнейшего применения. При изготовлении данного сплава соблюдается специально разработанная технология термической обработки. Для придания заготовкам необходимых характеристик в соответствии с предназначением, используется технология закалки и отпуска. Применяется температурный режим в пределах: от 350 до 600 градусов. За счет проведения подобной обработки заготовки приобретают улучшенные физико-механические характеристики, такие как:
— повышенная упругость,
— существенное увеличение предела стойкости,
— длительная стойкость к продолжительным статическим нагрузкам и возвращение в исходное положение с сохранением заданных показателей,
— минимальная пластичность при увеличенной устойчивости к износу.
Отсутствие пластической деформации – важнейшая характеристика металла, основное назначение которого – сохранение заданного производителем показателя.
Область использования.
Применение стали данной марки – это рессоры и пружины, о чем можно догадаться из самого наименования металла. Наибольшее распространение сплав получил при изготовлении различных узлов и агрегатов, деталей машиностроения. Все эти детали способны выдерживать существенные механические нагрузки и сохранять первоначальную прочность, упругости, износостойкость при высоких температурных и механических нагрузках.
конструкционный рессорно-пружинный сплав.
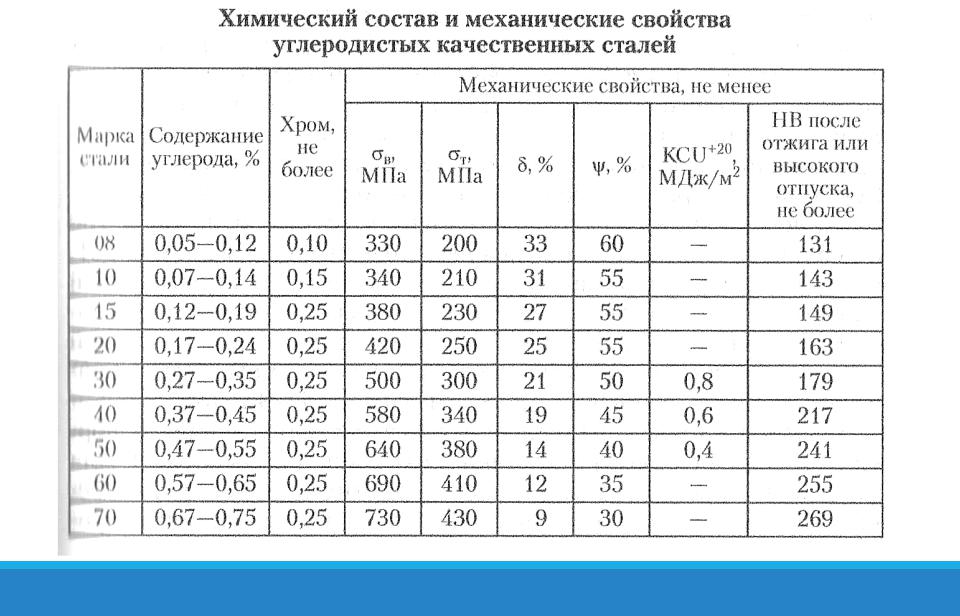
Этот сплав специально разработан для производства спиральных пружин и рессор. Сталь 65г является одной из самых распространенных пружинно-рессорных сталей, для которых свойственна простота обработки. Также для неё характерны прекрасные режущие свойства и возможность оксидирования (декоративного чернения и воронения).
Помимо относительно высокого среднего содержания углерода в данном материале присутствуют другие, не менее важные элементы, определяющие высокие эксплуатационные свойства металла:
- Mn (марганец) – 0,90-1,20%
- Si (кремний) – 0,17-0,37%
- Cr (хром) – до 0,25%
- Ni (никель) – до 0,25%
- Cu (медь) – до 0,20%
- P (фосфор) – до 0,035%
- S (сера) – до 0,035%
Лучшей характеристикой для данного сплава можно считать отзывы производителей боевых ножей: они называют сталь марки 65г идеальным балансом упругости и твердости металла. При этом добавляется, что такой материал режет ничуть не хуже популярных кованых многослойных сталей.
Физические и механические свойства стали 65г
Основные свойства данного сплава представлены в следующих таблицах:
Поставляется сталь 65г в виде сортового и фасонного проката согласно ГОСТам 14959-79, 2590-2006, 2591-2006, 2879-2006, 7419.0-78 и 7419.8-78. Это конструкционный рессорно-пружинный сплав поступает на производственные предприятия в виде (в соответствии с ГОСТами):
- ГОСТы 1051-73, 8559-75, 8560-78, 14959-79, 7417-75, – калиброванного прутка
- ГОСТы 14955-77, 7419.8-78 и 7419.0-78 – шлифованного прутка и серебрянки
- ГОСТ 1577-93 – толстого листа
- ГОСТы 2283-79, 21997-76, 10234-77, 19039-73, 1530-78, 21996-76 – ленты
- ГОСТы 4405-75 и 103-2006 – полосы
- ГОСТ 1133-71 – кованых заготовок и поковок
- ГОСТ 11850-72 – проволоки пружинной
Сталь 65г: сферы применения
Этот сплав довольно популярен в промышленности, поскольку идет на изготовление рессор, пружин, тормозных лент, упорных шайб, шестерен и фрикционных дисков. Данный материал является оптимальным для отливки корпусов подшипников, фланцев, подающих и зажимных цанг – словом, большого спектра деталей и узлов, для которых должна быть гарантирована высокая износостойкость. При всём этом такие детали не могут подвергаться ударным нагрузкам.
Еще одна популярная область применения стали 65г – изготовление ножей. Материал часто идет на серийное производство недорогого бытового режущего инструмента, а также специальных «метательных» ножей. Сталь 65г является недорогой, поэтому такие недостатки, как сильная подверженность коррозии или слабая стойкость к нагрузкам, считаются незначительными. Впрочем, по-настоящему проблемным будет лишь тот сплав 65г, который недокалён, т.е. сильно отпущен.
65 | ГОСТ 14959 – 79 | Feот 97.4%C0.62-0.7%Mn0.5-0.8%Si0.17-0.3%… |
70 | ГОСТ 14959 – 79 | Feот 97.4%C0.67-0.7%Mn0.5-0.8%Si0.17-0.3%… |
75 | ГОСТ 14959 – 79 | Feот 97.3%C0.72-0.8%Mn0.5-0.8%Si0.17-0.3%… |
80 | ГОСТ 14959 – 79 | Feот 97.3%C0.77-0.8%Mn0.5-0.8%Si0.17-0.3%… |
85 | ГОСТ 14959 – 79 | Feот 97.2%C0.82-0.9%Mn0.5-0.8%Si0.17-0.3%… |
3К-7 | ГОСТ 9389 – 75 | Feот 98%C0.68-0.7%Mn0.5-0.8%Si0.17-0.3%… |
50ХГ | ГОСТ 14959 – 79 | Feот 96.5%Cr0.9-1.2%Mn0.7-1%C0.46-0.5%Si0.17-0.3%… |
50ХГА | ГОСТ 14959 – 79 | Feот 96.5%Cr0.95-1.2%Mn0.8-1%C0.47-0.5%Si0.17-0.3%… |
50ХГФА | ГОСТ 14959 – 79 | Feот 96.3%Cr0.95-1.2%Mn0.8-1%C0.48-0.5%Si0.17-0.3%V0.15-0.2%… |
50ХСА | Feот 96.1%Cr0.9-1.2%Si0.8-1.2%C0.45-0.5%Mn0.3-0.5%… | |
50ХФА | ГОСТ 14959 – 79 | Feот 96.6%Cr0.8-1.1%Mn0.5-0.8%C0.46-0.5%Si0.17-0.3%V0.1-0.2%… |
51ХФА | ГОСТ 14959 – 79 | Feот 96.![]() |
55С2 | ГОСТ 14959 – 79 | Feот 95.7%Si1.5-2%Mn0.6-0.9%C0.52-0.6%… |
55С2А | ГОСТ 14959 – 79 | Feот 95.8%Si1.5-2%Mn0.6-0.9%C0.53-0.5%… |
55С2ГФ | ГОСТ 14959 – 79 | Feот 95.2%Si1.5-2%Mn0.95-1.2%C0.52-0.6%V0.1-0.15%… |
55ХГР | ГОСТ 14959 – 79 | Feот 96.2%Cr0.9-1.2%Mn0.9-1.2%C0.52-0.6%Si0.17-0.3%B0.001-0.003%… |
60Г | ГОСТ 14959 – 79 | Feот 97.3%Mn0.7-1%C0.57-0.6%Si0.17-0.3%… |
60С2 | ГОСТ 14959 – 79 | Feот 95.7%Si1.5-2%Mn0.6-0.9%C0.57-0.6%… |
60С2А | ГОСТ 14959 – 79 | Feот 95.7%Si1.6-2%Mn0.6-0.9%C0.58-0.6%… |
60С2Г | ГОСТ 14959 – 79 | Feот 95.4%Si1.8-2.2%Mn0.7-1%C0.55-0.6%… |
60С2Н2А | ГОСТ 14959 – 79 | Feот 94.7%Si1.4-1.8%Ni1.4-1.7%C0.56-0.6%Mn0.4-0.7%… |
60С2ХА | ГОСТ 14959 – 79 | Feот 95.4%Si1.4-1.8%Cr0.7-1%C0.56-0.6%Mn0.4-0.7%… |
60С2ХФА | ГОСТ 14959 – 79 | Feот 95%Si1.4-1.8%Cr0.9-1.2%C0.56-0.6%Mn0.4-0.7%V0.1-0.2%… |
65Г | ГОСТ 14959 – 79 | Feот 97%Mn0.9-1.2%C0.62-0.7%Si0.17-0.3%… |
65ГА | ГОСТ 1071 – 81 | Feот 97.3%Mn0.7-1%C0.65-0.7%Si0.15-0.3%… |
65С2ВА | ГОСТ 14959 – 79 | Feот 94.4%Si1.5-2%W0.8-1.2%Mn0.7-1%C0.61-0.6%… |
68А | ГОСТ 1071 – 81 | Feот 98%C0.65-0.7%Mn0.4-0.55%Si0.15-0.2%… |
68ГА | ГОСТ 1071 – 81 | Feот 97.5%Mn0.7-1%C0.65-0.7%Si0.15-0.2%… |
70Г | ГОСТ 14959 – 79 | Feот 97%Mn0.9-1.2%C0.67-0.7%Si0.17-0.3%… |
70Г2 | ГОСТ 17152 – 89 | Feот 96.2%Mn1.4-1.8%C0.65-0.7%Si0.![]() |
70С2ХА | ГОСТ 14959 – 79 | Feот 96.1%Si1.4-1.7%C0.65-0.7%Mn0.4-0.6%Cr0.2-0.4%… |
70С3А | ГОСТ 14959 – 79 | Feот 94.8%Si2.4-2.8%C0.66-0.7%Mn0.6-0.9%… |
70ХГФА | ГОСТ 1071 – 81 | Feот 97%Mn0.5-0.8%Cr0.3-0.5%Si0.15-0.3%V0.1-0.2%C0.065-0.72%… |
SH | ГОСТ Р 50567 – 93 | Feот 97.1%C0.46-1%Mn0.24-1.5%Si0.07-0.3%… |
SL | ГОСТ Р 50567 – 93 | Feот 97.3%C0.36-0.8%Mn0.24-1.5%Si0.07-0.3%… |
SM | ГОСТ Р 50567 – 93 | Feот 97.3%C0.36-0.8%Mn0.24-1.5%Si0.07-0.3%… |
ДМ | ГОСТ Р 50567 – 93 | Feот 97.1%C0.46-1%Mn0.24-1.5%Si0.07-0.3%… |
ДН | ГОСТ Р 50567 – 93 | Feот 97.1%C0.46-1%Mn0.24-1.5%Si0.07-0.3%… |
КТ-2 | ГОСТ 9389 – 75 | Feот 98.2%C0.86-0.9%Mn0.2-0.4%Si0.17-0.3%… |
Сталь 65Г: характеристики, свойства, аналоги
Сталь65Г отличается высокой эластичностью и прочностью, соответствует стандартам ГОСТ 14959, ГОСТ 1577, ДСТУ 8429.
Классификация: Конструкционная пружинная сталь.
Продукция: Прокат, включая фасонный и листовой.
Химический состав стали 65Г,%
Si | млн | пол | ю | Кр | Cu | |
0.17-0,37 | ≤0,9–1,2 | ≤0,035 | ≤0,035 | ≤0,25 | ≤0,2 |
Механические свойства стали 65Г
Термическая обработка | Минимальный предел текучести, (МПа) | Минимальное временное сопротивление, (МПа) | Минимальный коэффициент удлинения,% | Минимальная степень усадки,% |
Закалка от 830 ° С в масле, отпуск при 470 ° С | 785 | 980 | 8 | 30 |
Аналог стали 65Г
США | 1066, 1566, G15660 |
Германия | 66Mn4, Ck67 |
Великобритания | 080A67 |
Китай | 65 млн |
Болгария | 65 г |
Польша | 65 г |
Приложение
В качестве пружинной стали 65G широко используется в шайбах и пружинных кольцах, различных типах пружин (плоских и круглых), зажимных и подающих цангах, упорных шайбах, дисках сцепления, стопорных кольцах и других компонентах с пружинным управлением, которые должны быть очень эластичными. и прочный.
Сварка
Сталь65Г не применяется для сварных конструкций. Допускается неограниченное применение контактной стыковой сварки.
Сталь 65G / Auremo
Описание
Сталь 65Г
Сталь 65Г : марка сталей и сплавов. Ниже представлена систематизированная информация о назначении, химическом составе, видах материалов, заменителях, температуре критических точек, физико-механических, технологических и литейных свойствах для марки – характеристики стали 65г.
Сталь общего назначения 65Г
Заменяющая марка |
сталь: 70, У8А, 70Г, 60С2А, 9Хс, 50ХФА, 60С2, 55С2. |
Вид поставки |
Лист 65г, лента 65г, круг 65г, проволока 65г, полоса 65г, сортовой прокат, в том числе фасонный: ГОСТ 14959-79, ГОСТ 2590-71, ГОСТ 2591-71, ГОСТ 2879-69 , ГОСТ 7419.0-78 – ГОСТ 7419.8-78. Пруток калиброванный ГОСТ 14959-79, ГОСТ 7417-75, ГОСТ 8559-75, ГОСТ 8560-78, ГОСТ 1051-73. Пруток шлифованный и пруток серебряный ГОСТ 14955-77, ГОСТ 7419.0−78 – ГОСТ 7419.8−78. Лист толстый ГОСТ 1577-81. Лента по ГОСТ 1530-78, ГОСТ 2283-79, ГОСТ 21996-76, ГОСТ 21997-76, ГОСТ 10234-77, ГОСТ 19039-73. Лента ГОСТ 103-76, ГОСТ 4405-75. Проволока ГОСТ 11850-72. Поковки и поковки ГОСТ 1133-71. |
Применение |
пружины, пружины, упорные шайбы, тормозные ленты, фрикционные диски, шестерни, фланцы, корпуса подшипников, зажимные и подающие цанги и другие детали, требующие повышенной износостойкости, и детали, работающие без ударных нагрузок. |
Химический состав стали 65Г
Химический элемент | % |
Кремний (Si) | 0,17−0,37 |
Марганец (Mn) | 0,90−1,20 |
Медь (Cu), не более | 0,20 |
Никель (Ni), не более | 0,25 |
Сера (S), не более | 0,035 |
Углерод (C) | 0.![]() |
Фосфор (P), не более | 0,035 |
Хром (Cr), не более | 0,25 |
Механические свойства стали 65Г
Механические свойства
Термическая обработка, состояние при поставке | Сечение, мм | σ 0,2 , МПа | σ B , МПа | δ 5 ,% | ψ,% | HRC e |
Категории стали: 3.3A, 3B, 3V, 3G, 4.4A, 4B. Закалка 830 ° С, масло, отпуск 470 ° С. | Образцы | 785 | 980 | 8 | тридцать | |
Лист нормализованный и горячекатаный | 80 | 730 | 12 | |||
Закалка 800-820 ° С, масло. Отпуск 340−380 ° С, воздух. | 20 | 1220 | 1470 | пять | десять | 44-49 |
Закалка 790-820 ° С, масло.Отпуск 550-580 ° С, воздух. | 60 | 690 | 880 | 8 | тридцать | 30-35 |
Механические свойства при повышенных температурах
испытание t, ° С | σ 0,2 , МПа | σ B , МПа | δ 5 ,% | ψ,% | ||||||||||
Закалка 830 ° С, масло. Отпуск 350 ° C. | ||||||||||||||
200 | 1370 | 1670 | пятнадцать | 44 | ||||||||||
300 | 1220 | 1370 | 19 | 52 | ||||||||||
400 | 980 | 1000 | 20 | 70 |
Механические свойства в зависимости от температуры отпуска
отпуск t, ° С | σ 0.2 , МПа | σ B , МПа | δ 5 ,% | ψ,% | KCU, Дж / м 2 | HRC e | ||||||||
Закалка 830 ° С, масло.![]() | ||||||||||||||
200 | 1790 | 2200 | 4 | тридцать | пять | 61 | ||||||||
400 | 1450 | 1670 | 8 | 48 | 29 | 46 | ||||||||
600 | 850 | 880 | пятнадцать | 51 | 76 | тридцать |
Технологические свойства стали 65Г
Температура ковки |
Начало 1250, конец 780-760.Охлаждение заготовок сечением до 100 мм осуществляется на воздухе, сечением от 101 до 300 мм – в форме. |
Свариваемость |
не применяется для сварных конструкций. КТС – без ограничений. |
Обрабатываемость резанием |
В закаленном и отпущенном состоянии при HB 240 и σ B = 820 МПа K υ тв.спл. = 0,85, K υ b.st. = 0,80. |
Способность к высвобождению |
склонность при содержании Mn> = 1% |
Чувствительность к флоку |
нечувствительность |
Температура критических точек стали 65G
Критическая точка | ° С |
Ас1 | 721 |
Ac3 | 745 |
Ar3 | 720 |
Ar1 | 670 |
Мн | 270 |
Ударная вязкость стали 65Г
Ударная вязкость, KCU, Дж / см 2
Состояние поставки, термообработка | +20 | 0 | -20 | -тридцать | -70 |
Закалка 830 C.Отпуск 480 C. | 110 | 69 | 27 | 23 | 12 |
Предел выносливости стали 65Г
σ -1 , МПа | τ -1 , МПа | σ B , МПа | σ 0,2 , МПа | Термическая обработка, состояние стали |
725 | 431 | Закалка 810 С, масло.![]() | ||
480 | 284 | Закалка 810 С, масло. Отпуск 500 с. | ||
578 | 1470 | 1220 | HB 393-454 | |
647 | 1420 | 1280 | НВ 420 | |
725 | 1690 | 1440 | HB 450 |
Прокаливаемость стали 65Г
Закалка 800 ° С.
Расстояние от торца, мм / HRC e | |||||||||||
1,5 | 3 | 4,5 | 6 | девять | 12 | пятнадцать | восемнадцать | 27 | 39 | ||
58,5-66 | 56,5-65 | 53-64 | 49,5–62,5 | 41,5−56 | 38,5−51,5 | 35,5–50,5 | 34,5–49,5 | 35−47,5 | 31-45 |
Количество мартенсита,% | Crit.Диам. в воде, мм | Crit. Диам. в масле, мм | Крит. твердость, HRCэ |
50 | 30−57 | 10−31 | 52−54 |
90 | до 38 | до 16 | 59−61 |
Физические свойства стали 65Г
Температура испытания, ° С | 20 | 100 | 200 | 300 | 400 | 500 | 600 | 700 | 800 | 900 |
Нормальный модуль упругости, E, ГПа | 215 | 213 | 207 | 200 | 180 | 170 | 154 | 136 | 128 | |
Модуль упругости при сдвиге G, ГПа | 84 | 83 | 80 | 77 | 70 | 65 | 58 | 51 | 48 | |
Плотность стали, pn, кг / м 3 | 7850 | 7830 | 7800 | 7730 | ||||||
Коэффициент теплопроводности Вт / (м ° С) | 37 | 36 | 35 | 34 | 32 | 31 | тридцать | 29 | 28 | |
Температура испытания, ° С | 20−100 | 20−200 | 20−300 | 20-400 | 20−500 | 20-600 | 20-700 | 20-800 | 20−900 | 20-1000 |
Коэффициент линейного расширения (a, 10-6 1 / ° С) | 11.![]() | 12,6 | 13,2 | 13,6 | 14,1 | 14,6 | 14,5 | 11,8 | ||
Удельная теплоемкость (C, Дж / (кг ° C)) | 490 | 510 | 525 | 560 | 575 | 590 | 625 | 705 |
Источник: Марка сталей и сплавов
Источник: www.manual-steel.ru / 65G.html
Металлы -> Конструкционная сталь -> Пружинная конструкционная сталь Характеристики материала 65Г (65Г, 65).
Химический состав в% материала 65G (65G, 65).
Температура критических точек марки 65G (65G, 65).
Механические свойства под = 20 o материала 65G (65G, 65).
Физические свойства материала 65Г (65Г, 65).
Технологические свойства материала 65Г (65Г, 65).
Спецификация:
База данных сталей и сплавов (Марочник) содержит информацию о химическом составе и свойствах 1500 сталей и сплавов (нержавеющая сталь, легированная сталь, углеродистая сталь, конструкционная сталь, инструментальная сталь, чугун, алюминиевый сплав, титановый сплав, медный сплав, никелевый сплав. ![]() Полезно для специалистов в области материаловедения, инженеров-конструкторов, инженеров-механиков, металлургов и металлоторговцев Топ
|
65Mn4, 1.1240, 66Mn4, 1.1260, 65Г
65G, 65Mn4, 66Mn4, 1.1240, 1.1260 – Конструкционная сталь из марганцево-пружинного сплава согласно PN-74 / H-84032
Стандарт | Марка стали | ||||||||
---|---|---|---|---|---|---|---|---|---|
Химический состав% | |||||||||
C: | Mn: | Si : | P: | S: | Cr: | Ni: | Al: | Cu: | |
PN | 65G | ||||||||
0,90 – 1,20 | 0,15 – 0,40 | <0,04 | <0,04 | <0,3 | <0,3 | – | <0,25 | ||
DIN | 66Mn4 – 66 Mn 4 – 1,1260 | ||||||||
0,60 – 0,71 | 0,85 – 1,15 | 0,15 – 0,30 | <0,035 | <0,035 | – | – | – | – | |
DIN | 65Mn4 – 65 Mn 4-1.1240 | ||||||||
0,60 – 0,70 | 0,90 – 1,20 | 0,25 – 0,50 | <0,035 | <0,035 | – | – | – | – | |
ISO | 920 920 56Mn4 – 56 Mn 4 – 1,1233|||||||||
0,52 – 0,60 | 0,90 – 1,20 | <0,40 | <0,025 | <0,03 | – | – | <0.![]() | <0,3 | |
ГОСТ | 65G – 65Г | ||||||||
0,62 – 0,70 | 0,90 – 1,20 | 0,17 – 0,37 | <0,035 | <0,035 | <0,035 | <0,25 | – | – | |
ГОСТ | 65GA – 65ГА | ||||||||
0,65 – 0.70 | 0,7 – 1,0 | 0,15 – 0,30 | <0,025 | <0,025 | <0,15 | <0,2 | <0,08 | <0,2 | |
STAS | 65MN10 – 65 Mn 10 | ||||||||
0,62 – 0,70 | 0,90 – 1,20 | 0,17 – 0,37 | <0,035 | <0,035 | <0,3 | <0.3 | – | <0,3 | |
ČSN / STN | ČSN 13 180 – ČSN 13180 | ||||||||
0,70 – 0,80 | 0,90 – 1,20 | 0,15 – 0,35 900 | <0,04 | <0,3 | <0,4 | – | <0,3 | ||
SAE | AISI C1062 – 1062 | ||||||||
0.54 – 0,65 | 0,85 – 1,15 | – | <0,04 | <0,05 | – | – | – | – | |
UNS | AISI 1066 – AISI20 1566 | ||||||||
0,60 – 0,71 | 0,85 – 1,15 | – | <0,04 | <0,05 | – | – | – | – |
Сталь 65G – спецификация и применение
65G – Сталь для листовых рессор и пружин с низкой закалкой, требующих повышенной устойчивости к истиранию, для колец, пружин клапанов, плоских, витков и пружинных шайб с небольшими поперечными сечениями и нагрузками. Сталь для закалки в масле, нечувствительная к отпускной хрупкости. Сталь не проявляет стойкости к агрессивным средам.
Механические и физические свойства стали 65Г
- Предел прочности, Rm ≥ 980 МПа
- Предел текучести, Re ≥ 780 МПа
- Усадка, Z ≥ 30%
- Удлинение, A ≥ 8%
- Твердость после размягчение ≤ 241 HB
- Твердость в исходном состоянии: ≤ 262 HB
- Твердость после закалки и отпуска при темп.380-520 ℃ = 42 – 47 HRC
- Твердость после закалки и отпуска при 400 – 550 ℃ = 310 – 350 HB
- Плотность ρ = ~ 7,83 кг / дм3
- Теплопроводность λ20 ℃ = ~ 46,2 Вт м-1 K-1
- Тепловая мощность cp20-100 ℃ = ~ 481 Дж кг-1 K-1
- Коэффициент линейного расширения α20-100 ℃ = ~ 11,35 10-6 K-1
В описываемой марке компания предоставляет:
Перечень аналогов и другие обозначения стали 65Г:
66Mn4, 66 Mn 4, 1.1260, 65Mn4, 65 Mn 4, 1.1240, 56Mn4, 56 Mn 4, 1.1233, 65Г, 65GA, 65ГА, 65MN10, 65 Mn 10, ČSN 13 180, ČSN 13180, AISI C1062, 1062, AISI 1066, AISI 1566
Y1Cr18Ni9 | Улучшить обрабатываемость, сопротивление абляции. Подходит для производства болтов и гаек на токарных автоматах. | ||
1Cr18Ni9 | Высокая прочность после холодной штамповки, но относительное удлинение несколько хуже, чем у 1 cr17ni7.Используется в деталях архитектурного декора | ||
1Cr18Mn10Ni5Mo3N | Мочевина с хорошей коррозионной стойкостью, может вызывать коррозию оборудования мочевиной. | ||
1Cr17Ni7 | Высокая прочность после холодной штамповки. Используется в железнодорожном транспорте, конвейерной ленте, болте и гайке и т. | ||
Y1Cr18Ni9Se | Улучшить обрабатываемость, сопротивление абляции.Подходит для токарного автомата производства заклепок, винтов . | ||
0Cr18Ni9 | Трубы бесшовные из нержавеющей стали для котла и теплообменника | ||
00Cr19Ni10 | Сталь с содержанием углерода ниже 0Cr19ni9, отличная стойкость к межкристаллитной коррозии, используется для сварки после необработанных деталей класса | ||
1Cr17Mn6Ni5N | Никелевая марка стали вместо Cr17ni7 №1 и магнетизм после холодной обработки, применяемая в железнодорожном транспорте и т. Д. | ||
1Cr18Mn8Ni5N | Сталь никелевая вместо 1кр18ни9 | ||
0Cr19Ni9N | На базе 0cr19ni9 plus N, прочность увеличивается, а пластик не проседает.Уменьшите толщину материала. Как конструкция с элементами прочности | ||
0Cr19Ni10NbN | На основе нулевого cr19ni9 плюс N и Nb, со свойствами выше 0 cr19ni9 и ИСПОЛЬЗУЕТ | ||
00Cr18Ni10N | В 00cr19ni10 с добавлением N на основе вышеуказанных марок также используется то же, что и в 0 cr19ni9n, но с лучшей стойкостью к межкристаллитной коррозии. | ||
1Cr18Ni12 | По сравнению с 0 cr19ni9, низкая закаливаемость при обработке.Применяется для прядильной обработки, специального волочения, холодная позиция . | ||
0Cr23Ni13 | Коррозионная стойкость и термостойкость лучше, чем 0cr19ni9 | ||
0Cr25Ni20 | Стойкость к окислению лучше, чем у 0cr23ni13. | ||
0Cr17Ni12Mo2 | Трубы бесшовные из нержавеющей стали для котла и теплообменника | ||
1Cr18Ni12Mo2Ti | Трубы бесшовные из нержавеющей стали для котла и теплообменника | ||
0Cr18Ni12Mo2Ti | Трубы бесшовные из нержавеющей стали для котла и теплообменника | ||
А-29 1025 | Пруток из углеродистой стали общего назначения | ||
1025 | Эти продукты обычно используются для изготовления фитингов, но не ограничиваются такими применениями.Эти продукты обычно не используются для операций глубокой формовки или купирования. |
Магнитные и электромагнитные методы контроля износостойкости металлопродукции
Твердость, механические свойства и другие характеристики, определенные стандартными методами, не могут рассматриваться как надежные критерии износостойкости металлов. Известно, что износостойкость зависит от ряда факторов, например структура и состав материала, параметры трения и др., а оценка износостойкости стальных изделий – актуальная задача для промышленных предприятий. В статье предлагается использовать высокочувствительные магнитные и электромагнитные методы для оценки и прогнозирования абразивной износостойкости мартенситных сталей. Неразрушающая оценка износостойкости оказалась возможной после установления корреляции между износостойкостью стальных деталей, с одной стороны, и коэрцитивной силой H C и показаниями вихретоковой единицы a (~), с другой стороны, a в зависимости от начальной магнитной проницаемости м ri и удельное электрическое сопротивление r . Измерения выполнены на 8 товарных марках стали. Образцы вырезаны из сталей марок У8 (0,83 мас. % С), 80М2 (0,82 мас.% С; 1,86 мас.% Мо), 80Ф1 (0,83 мас.% С; 1,21 мас. % V), 80Г2 (0,83 мас.% C; 2,0 мас.% Mn), 80S2 (0,83 мас.% C; 1,66 мас.% Si), 9ХС (0,89 мас.% C; 1,43 мас.% Si, 1,08 мас.% Cr) и ШХ25 (1,0 мас.% C; 1,42 мас.% Cr) закалили в воде от 810-1220 ° С.
C [1,2], затем они были подвергнуты отрицательной обработке при -196 °
C для получения высокоуглеродистой (~ 0,7 мас.% C) мартенситной структуры с содержанием не более 5-10 об.% остаточного аустенита и окончательный отпуск при 75-700 °
В. Образцы из стали марки 20ХН3А (0,20 мас.% С; 0,68 мас.% Cr; 2,90 мас.% Ni; 0,14 мас.% Мо) науглерожены и закалены в масле от 790 ° С.
C. Испытания на износостойкость проводились путем скольжения образцов по закрепленному абразивному материалу (корунд), а также путем сухого скольжения образцов попарно с помощью сферического индентора из твердого сплава. Параметры вихретокового измерения измерялись с помощью прилагаемого преобразователя диам. 5 мм, частота f от 2,4 до 72 кГц.
Рис.1: Твердость HRC, сопротивление абразивному износу e, коэрцитивная сила H C и показания вихретоковой единицы a (f = 2,4 кГц) как функция температуры отпуска T для сталей марок U8 (1), 80M2 (2 ), 80Ф1 (3), 80Г2 (4), 80С2 (5), 9ХС (6) и ШХ25 (7), подвергнутые закалке с последующей минусовой обработкой при -196 ° С. |
Рис 2: Сопротивление абразивному износу e против.коэрцитивная сила H C и показания вихретоковой единицы a для стали марки У8 после закалки и 2-часового отпуска. Цифры в точках обозначают температуру отпуска. |
При повышении температуры отпуска до 250 °
C наблюдается относительно небольшое изменение твердости сталей, однако оно сопровождается резким снижением абразивной износостойкости e
, коэрцитивная сила H C и показания вихретоковой единицы a
(Рисунок. 1) за счет выделения углерода из мартенситной решетки. Предыдущие исследования показали линейную зависимость как H C , так и a
при содержании углерода для низко отпущенного мартенсита в стали марок У8 и 65Г (0,63 мас.% C; 0,92 мас.% Mn) [1]. Физическая основа для разработки как коэрцитиметрических, так и вихретоковых методов неразрушающей оценки износостойкости мартенситных сталей с низким отпуском основана на том факте, что соотношение между содержанием углерода в мартенсите и его износостойкостью очень похоже на соотношение между содержанием углерода в мартенсите и его износостойкостью. содержание углерода и параметры вихревых токов [1,2].На рис. 2 показана корреляция между абразивной износостойкостью низкотемпературной стали У8 и ее коэрцитивной силой и показаниями вихретоковой единицы. Вихретоковый метод позволяет определять износостойкость стальных изделий, подвергнутых объемной закалке и поверхностной закалке, например лазерное лечение [1]. Сохранение пластичного сердечника в стальных деталях после лазерной закалки тонкого поверхностного слоя позволяет избежать дополнительного отпуска, тем не менее, последующий нагрев, связанный со сваркой, шлифованием, работой при повышенных температурах, а также нагрев из-за трения может привести к значительному снижению в износостойкости.
Дополнительное легирование высокоуглеродистых сталей 1-2% Mo, V, Mn, Si и Cr не влияет ни на установленное соотношение между низкой температурой отпуска и e. , H C и а
, а также характер корреляции между абразивной износостойкостью, магнитными и электромагнитными характеристиками [2]. Однако легирование неоднозначно влияет на абсолютные значения вышеупомянутых параметров, таким образом, корреляция между износостойкостью и H C или
следует устанавливать для каждой конкретной марки стали [2].Легирование кремнием (например, стали марок 80С2 и 9ХС) существенно тормозит снижение абразивной износостойкости высокоуглеродистых сталей при средних температурах отпуска, а легирование ванадием (80F1) и молибденом (80M2) улучшает износостойкость после высокого отпуска (600 ° С). C) из-за дисперсионного твердения, вызванного карбидами VC и Mo 2 C (рис. 1). Коэрцитивная сила 80С2 и 9ХС неуклонно снижается с увеличением температуры отпуска до 400 °.
C (рис. 1б, кривые 5,6) из-за тормозящего влияния кремния на эволюцию структуры при среднем отпуске.Остальные исследованные стали демонстрируют интенсивное снижение коэрцитивной силы только при температурах ниже 250 ° С.
C. Как и в случае с H C , показания вихретоковых единиц неуклонно уменьшаются до минимума при повышении температуры отпуска до 250-400 ° C.
C, причем конкретные значения определяются маркой стали. Заметное снижение
объясняется интенсивным ростом начальной магнитной проницаемости m ri , что приводит к снижению удельного электрического сопротивления r
в ходе вышеупомянутых режимов отпуска.Однако дальнейшее повышение температуры отпуска сопровождается значительным ростом температуры отпуска.
за счет одновременного уменьшения м ri и r
, коэрцитивная сила демонстрирует лишь незначительные изменения в диапазоне температур (рис. 1). Поскольку в исследуемых сталях наблюдается сложная корреляция между e
и H C после среднего и высокого отпуска (рис. 2), надежная оценка их износостойкости коэрцитиметрическим методом очень затруднена.Поскольку вихретоковый метод, в отличие от коэрцитиметрического, очень чувствителен к изменению микроструктуры в процессе среднего и высокого отпуска, этот метод также может быть применен для испытаний стальных изделий, подвергнутых как низкому отпуску, так и отпуску выше 250-400 °
C – температура отпуска, зависящая от химического состава конкретной легированной стали (рис. 1,2).
Особое внимание уделено исследованию стали марки 20ХН3А, поскольку поверхностный слой с переменным содержанием углерода и остаточным аустенитом в количестве 25-30% отличает сталь от вышеуказанных.Рис. 3 показывает возможность использования метода вихревых токов для проверки износостойкости стальных деталей, подверженных абразивному износу и трению скольжения. Обработка ниже нуля снижает содержание аустенита в науглероженном слое до 5-10% и увеличивает твердость на 2-3 HRC, тем не менее износостойкость стали остается неизменной (рис. 3а) из-за превращения остаточного аустенита в высокую прочность. деформационный мартенсит, возникающий при трении. Повышенное количество метастабильного аустенита, присутствующего в закаленной стали, предотвращает резкое увеличение интенсивности абразивного износа и снижает потерю массы при трении скольжения после небольшого отпуска.Обработка при отрицательных температурах приводит к значительному снижению показаний вихретокового блока.
(рис. 3а) из-за разложения немагнитного газа
-фаза и соответствующее увеличение магнитной проницаемости, что приводит к снижению электрического сопротивления стали. Исследование науглероженной стали и подшипниковой стали марки ШХ25 после объемной и поверхностной лазерной закалки показало, что чувствительность как вихретоковых (рис. 3б), так и коэрцитиметрических методов контроля износостойкости значительно возрастает, если содержание остаточного аустенита в низкотемпературная сталь составляет 25-40%.
Рис.3: Твердость HRC, средняя интенсивность абразивного износа Ih для поверхностного слоя глубиной ~ 0,5 мм, потеря массы образца D P, вызванное трением скольжения и показаниями вихретоковых единиц a (f = 72 кГц) в зависимости от температуры отпуска T (a) и корреляции между Ih, D P и a б) для науглероженной стали марки 20ХН3А, подвергнутой закалке (I) и подвергнутой закалке с последующей холодной обработкой до -196 ° С (II).Цифры в точках обозначают температуру 2-часового отпуска |
Недавно разработанный вихретоковый блок для контроля структуры и коэрцитиметры со специально разработанными присоединенными преобразователями позволяют проверять износостойкость стальных деталей прямо в рабочих условиях и позволяют снимать показания непосредственно с локальных участков, подверженных трению.
Руководство по наиболее часто используемым сталям для топоров
Прежде чем мы перейдем к этому, давайте рассмотрим несколько вещей, которые вы должны знать, прежде чем искать подходящую для вас сталь.Прежде всего, какова основная цель этого инструмента? Будете ли вы использовать топор для кемпинга, охоты или рубки леса?
Будет ли он использоваться для раскопок, взлома или других тактических целей? Какой износ он выдержит? Будет ли это экспонат или предмет коллекционирования? Все эти факторы имеют решающее значение для определения того, какой тип стали вам подходит.
Изучение основ
Из чего состоит сталь?
Вообще говоря, сталь – это металл, содержащий смесь железа и углерода.Когда в состав не входят другие элементы, она называется простой углеродистой сталью. Сталь, содержащая другие элементы, такие как сера, марганец, хром, никель и т.п., называется легированной сталью. Нержавеющая сталь – это легированная сталь с содержанием хрома не менее 12%.
Распространенные сплавы и их свойства включают:
- Углерод – Не сплав, но поскольку углерод присутствует во всей стали, он является наиболее важным ингредиентом во всем производстве стали.Он необходим для упрочнения, но в больших количествах может снизить ударную вязкость.
- Хром – Этот элемент отлично сопротивляется коррозии, хотя в больших количествах он может снизить ударную вязкость материала. Для получения нержавеющей стали уровень хрома должен составлять не менее 12%.
- Кобальт – Придает клинку повышенную прочность.
- Медь – Повышает коррозионную стойкость.
- Марганец – Этот элемент увеличивает твердость материала.Однако слишком много марганца может увеличить хрупкость.
- Молибден – помогает стали сохранять прочность при воздействии высоких температур.
- Никель – Повышает ударную вязкость, сопротивляется коррозии и улучшает прокаливаемость.
- Азот – Этот элемент иногда используется как заменитель углерода.
- Phosphorus – Эта добавка этого элемента помогает увеличить прочность лезвия.
- Кремний – Помогает удалять кислород из металла в процессе формирования. Добавление его в сталь также может увеличить ее прочность.
- Сера – Этот элемент увеличивает способность стали использоваться в машинах, но также снижает ударную вязкость.
- Вольфрам – Повышает долговечность и защищает от износа.
- Ванадий – Упрочняет лезвие и обеспечивает повышенную коррозионную стойкость.
Важные качества стали
Важно понимать свойства и качество каждого вида стали или сплава. Это необходимо для понимания того, как лучше всего использовать каждый из них и чего можно ожидать от топора, выкованного из особой комбинации стали. Вот некоторые важные свойства, на которые следует обратить внимание при покупке топоров и оружия.
- Твердость: Способность стали противостоять короблению и деформации после использования.Это рассчитывается по шкале Роквелла (поясняется ниже).
- Прокаливаемость: Показатель способности стали закаливаться в процессе термообработки.
- Прочность: Насколько хорошо лезвие выдерживает нагрузку и силу.
- Пластичность: Мера гибкости стали.
- Прочность: Способность стали поглощать удары.
- Начальная резкость: Насколько острое лезвие поступает прямо с завода.
- Удержание кромки: Насколько хорошо лезвие сохраняет свою кромку без переточки.
- Drop Forged: Процесс термической обработки металла и стратегического забивания его в конкретную литейную форму. Этот процесс используется для производства высококачественного оружия и изделий, требующих повышенной прочности и долговечности.
- Устойчивость к износу: Способность стали бороться с коррозией.
- Износостойкость: Насколько хорошо топор выдерживает основной износ с течением времени.
Что такое шкала твердости по Роквеллу?
Эта шкала используется для измерения твердости стали и различных других металлов. Измерение обычно отображается как RCxx или xx HRC. Например, он может отображаться как RC55 или HRC 55. Числовая шкала измеряет твердость или мягкость конкретного металла. Более высокие числа соответствуют более твердым материалам, а чем меньше число, тем мягче сталь.
Если материал слишком твердый или имеет высокий уровень твердости по Роквеллу, его может быть трудно затачивать или он станет хрупким после длительного использования. И наоборот, когда сталь слишком мягкая, она может быть подвержена изгибу и деформации и, вероятно, не будет хорошо удерживать кромку. Идеально найти топор, который имеет средний уровень твердости.
Мы составили таблицу ниже, которая легко показывает некоторые из наиболее распространенных характеристик стали для инструментов и лезвий с точки зрения твердости кромки, коррозионной стойкости и заточки.
Виды стали
Как вы понимаете, существует множество различных типов стали, и каждый может использоваться для различных целей. Когда дело доходит до создания качественных топоров и томагавков, есть несколько популярных вариантов, которые используются многими известными производителями топоров на рынке. Это руководство поможет вам понять качества, свойства и идеальное использование каждого вида стали.
Я собираюсь объяснить различия в различных типах популярных сталей.При желании в нестандартных изделиях можно использовать специальные стали, но здесь мы сосредоточимся только на наиболее широко используемых типах.
У каждого типа стали есть свои плюсы и минусы, а также области, в которых он наиболее эффективен. Важно помнить, что если топор используется по основному назначению, он должен работать безупречно. При этом, когда инструментом злоупотребляют или используют ненадлежащим образом, маловероятно, что вы увидите положительные результаты независимо от качества стали. Убедитесь, что вы точно знаете, для чего собираетесь использовать свой топор.
Нержавеющая сталь часто лучше подходит для использования на открытом воздухе, поскольку она дольше выдерживает износ, но углерод может быть лучше, если вы планируете выполнять тяжелую работу. Кроме того, сталь не работает с топорами, топорами и более крупными инструментами так же, как с ножами. Некоторые желаемые свойства ножей считаются нежелательными или ненужными для топоров.
Углеродистая сталь (1050-1090, 5150, 5160)
Обычная углеродистая сталь – один из самых популярных материалов, используемых при ковке топоров.Легко затачивается и устойчив к коррозии. Она тверже, чем другие стали, например, нержавеющая, поэтому лучше сохраняет кромку при контакте с закаленными материалами. Конечно, во всей стали есть немного углерода.
Однако простые углеродистые стали содержат в основном смесь углерода и стали, в то время как другие типы стали содержат соединения различных других сплавов и составов. Углерод является наиболее важным упрочняющим элементом во всех типах стали и может помочь продлить срок службы вашего лезвия, хотя слишком много может снизить ударную вязкость материала, делая его более восприимчивым к ударам и повреждениям.
Углерод можно разделить на три подкатегории: низкий, средний и высокий уровень углерода. Средний и высокий – это то, что вы чаще всего найдете во многих топорах. Углерод со средним уровнем содержания углерода составляет от 0,4 до 0,6%, а углерод с высоким уровнем – от 0,7 до 0,8% и выше. В соответствии с системой наименования, разработанной SAE (Обществом инженеров автомобильной промышленности), обычная углеродистая сталь включена в серию номеров 10xx.
Последние две цифры указывают процент углерода, включенного в сталь.В большинстве топоров используется среднеуглеродистая сталь, чаще всего около 1050-1060. Это потому, что эта сталь лучше всего подходит для хонингованного холодного оружия, и ее закаляют при высокой температуре, чтобы уменьшить риск поломки и раскола.
Иногда используется высокоуглеродистый 1070 или выше. Высококачественная сталь, которую вы можете приобрести, – это углеродистая сталь 1080 или ее японский аналог SK5. Металлы в этих материалах высокого качества, закалены с уровнем RC до 65. Лезвия из этого материала являются подходящим выбором для тяжелых, грубых работ, хотя они требуют немного большей осторожности, так как лезвие требует заточки чаще, чем другие материалы.Однако из-за их качественного макияжа их легко затачивать, а уход дешевле.
Другим популярным типом углеродистой стали является 5150 и 5160. Группа стали 50xx классифицируется как легированная сталь в SAE, а последние две цифры определяют процентное содержание углерода, как указано выше. При 0,5% и 0,6% это углерод среднего уровня с достаточным количеством хрома, чтобы значительно повысить его общие характеристики, но недостаточно, чтобы считать его нержавеющей сталью.
Благодаря столь же низкому содержанию углерода эта сталь имеет повышенную ударную вязкость, способность к закалке и ударопрочность по сравнению с другими материалами.Одна из самых прочных и ударопрочных сталей, благодаря своей исключительной прочности и твердости, она лучше всего подходит для больших лезвий и делает ее отличным лезвием для метательного топора.
Нержавеющая сталь (серия 400, 2Cr13, 3Cr13)
Нержавеющая сталь – еще один очень популярный и широко используемый материал, поскольку за ним легко ухаживать и он эффективно противостоит коррозии. Основным ингредиентом этого материала является хром, и, чтобы его можно было считать нержавеющей сталью, должно присутствовать не менее 12% его.На этом уровне хром окисляется, придавая стали ее основные свойства, в том числе повышенную стойкость к износу и истиранию.
Тем не менее, поскольку нержавеющая сталь, как известно, является особенно мягким металлом, для ее закалки, она может содержать ограниченное количество хрома, что снижает ее устойчивость к коррозии. Нержавеющая сталь используется в широком спектре продуктов и инструментов, доступных на различных рынках, таких как столовые приборы, хирургические инструменты, ювелирные изделия и многое другое. Обычно это недорогая и дешевая сталь, но ее регулярно комбинируют с такими качественными материалами, как никель, для повышения ее эффективности.
Самым популярным типом этой стали среди топоров и топоров является нержавеющая сталь 420. Твердее, чем 410, но мягче, чем 440 (как следует из порядкового номера), этот материал содержит только около 0,3% – 0,4% углерода, что означает, что это довольно мягкая сталь и имеет умеренное удержание кромки.
И наоборот, он невероятно устойчив к коррозии и хорошо противостоит погодным условиям, что делает его идеальным для инструментов, которые часто подвергаются воздействию воды или незначительных химических веществ. После закалки он имеет пластичность выше средней и может достигать RC53.Нержавеющая сталь 2Cr13 и 3Cr13 является китайским эквивалентом нержавеющей стали 420.
Они достигают уровней RC50 и RC52 соответственно. Эта сталь идеально подходит для рабочих нагрузок от умеренных до средних, требующих длительного воздействия воды, снега, химикатов, грязи и т. Д. Их легко полировать и обслуживать, а заточка – это короткая, выполнимая задача.
Другой широко используемый тип нержавеющей стали серии 400, который используется при ковке головок топоров, – это 420HC, которая представляет собой высокоуглеродистую нержавеющую сталь 420, и ее не следует путать с вышеупомянутой 420.Благодаря более высокому содержанию углерода, он имеет повышенную твердость и устойчивость кромки, что дает ему значительный прирост прочности по сравнению с его аналогом.
Этот вариант стали сочетает в себе стойкость кромок, износостойкость высокоуглеродистых сталей с антикоррозийными свойствами хромовых сплавов. Она считается качественной сталью, поскольку сочетает в себе прекрасное сочетание желаемых характеристик и идеально подходит для инструментов, которые, как вы ожидаете, будут часто использоваться.
Нержавеющая сталь (AUS 6, 8, 10)
AUS-6, AUS-8 и AUS-10, также известные в этом порядке как 6A, 8A и 10A, представляют собой нержавеющие стали, производимые японским производителем стали Aichi Steel Corporation.Их содержание углерода можно сравнить со сталями, такими как 440A, 440B и 440C соответственно. 6A имеет в среднем 0,65% углерода и обычно конкурирует со сталями, такими как нержавеющая сталь 420, когда дело доходит до изготовления оружия. 8A имеет содержание углерода около 0,75% и считается умеренно прочной сталью среднего класса. 10A имеет содержание углерода около 1,10%. Его часто сравнивают с 440C, хотя их самая большая разница – небольшое уменьшение содержания хрома в 10A.
Лезвия, изготовленные из стали AUS, обычно закалены до RC 55–58 по шкале Роквелла.Эта нержавеющая сталь имеет острый и острый край. Однако из-за его способности удерживать более острую и тонкую кромку возникает необходимость в более частой заточке, так что это своего рода компромисс. Заточка позволит легко и точно получить острую как бритву кромку, но вам придется часто ремонтировать лезвие.
Самым большим отличием и основным преимуществом серии AUS является добавление ванадия.