Алюминиевые отливки: Алюминиевые отливки – серийное изготовление | Завод “Алюмлит”
alexxlab | 14.12.1986 | 0 | Разное
Алюминиевые отливки – zavod-litja.ru
«Zavod-Litja.ru» выполняет алюминиевые отливки, с помощью метода отлива в землю, также мы льем цветной металл в кокиля. Такой вид цветных отливок очень часто используется в строительстве. Алюминий хороший материал, он не поддается влиянию влаги, и соответственно устойчив к коррозии. Долго сохраняет свой первоначальный вид и начальные характеристики металла.
Высокое качество изделий из металла
Качественное изготовление детали из цветного литья долго сохраняет свои природные свойства. «Zavod-Litja.ru» гарантирует качественное литье и готов привезти уже готовую продукцию по заданному адресу по всей России и СНГ. Также цветное алюминиевое литье широко используется в запчастях для машин, изготовлении шестеренок, мебельных деталей и изделий для строительства.
Пришлите ваши чертежи или эскизы на [email protected]
Либо звоните 8-800-250-88-72. Доставка по России и СНГ!!!
Алюминиевые отливки
Цветное центробежное литье, цветное литье в форму кокиля, а также способ укладывания в форму из песка и глины. Один из этих способов литья есть центробежный способ. Он очень эффективен, поскольку при его использовании отсутствуют отходы производства. С помощью этого метода можно осуществить все виды литья из черных и цветных металлов от 1кг.
Когда используют кокильный метод, с помощью гравитации жидкий горячий металл укладывается в специальную форму для литья. Благодаря такому методу цветного литья можно производить большое количество готовой продукции за счет многоразового использования формы.
После проделанной работы отливки подвергаются дополнительному воздействию механической обработки для придания завершенности готового изделия или определенной конфигурации и вида. Отливки, которые изготавливаются из цветного металла, идут в ход в автотранспорте, а также в железнодорожном транспорте.
Это могут быть поршневые кольца, подшипники для электрических двигателей тепловозов и электровозов, а также их запчасти для дизельных двигателей. Подземное оборудование тоже использует их для венцов редуктора на лифтах и подъемных кранах.
Художественное литье
Цветное литье стало модно использовать при художественном дизайне. Дизайнеры очень часто применяют подобные эффекты декора в ландшафтных проектах и при литье алюминиевых отливок. Для художественного литья применяют такие металлы, как:
- бронза,
- чугун,
- латунь.
Из этих цветных металлов производят изделия для дизайнерского оформления:
- заборы,
- ограждения,
- решетки,
- фонтаны.
«Zavod-Litja.ru» выполняет и эти работы с легкостью и тонкостью изделий. А также предоставит аккуратный привоз таких изделий по России и в любую страну СНГ.
Применение алюминия
Существует много разновидностей литья. В частности цветного литья алюминия. Есть способ отлива алюминия в форму кокиля, и литье под давлением. Также алюминиевые сплавы эффективно очищают. Делают это с помощью фильтров из пенокерамики, а также флюсов.
В такой промышленности как машиностроение, алюминий имеет довольно популярное применение, в особенности применяют его с другими сплавами из разных металлов. На механические свойства самого алюминиевого сплава действует и также может изменять эти свойства химический состав сплава, обработка высокими температурами отливок и сам способ литья. Мы предлагаем литье алюминия в пенопласт по выгодным ценам и условиям дальнейшего сотрудничества.
Каждый сплав алюминия можно разделить на несколько видов групп.
- Первая. Сплавы АЛ 9, АЛ 4, АЛ 2 – это алюминий с кремнием.
- Второй. АЛ 13 и АЛ 8 – это алюминий и магний.
- Третий. АЛ 12 и АЛ 7- это алюминий и медь.
- Четвертый. АЛ 10, АЛ 6, АЛ 5, АЛ 3 – это сплав меди, кремния и алюминия.
- Пятый. Это сложные сплавы АЛ 11 и АЛ 1.
Используемые дополнительные сплавы
Так называемые силумины, сплавы алюминия и кремния, имеют хорошее свойство для литья. Сюда входит линейная усадка и растекаемость материала. При литье определенных форм и конфигураций изделия образуются резкие перепады и переходы, а благодаря выше перечисленным свойствам плотность отливок значительно выше.
Пришлите ваши чертежи или эскизы на [email protected]
Либо звоните 8-800-250-88-72. Доставка по России и СНГ!!!
Еще для того, чтобы повысить прочность, используют различные добавки меди, либо магния и других металлов. Улучшить механические характеристики сплава можно при помощи процесса модификации, то есть добавления в алюминий, при жидком состоянии, разумеется, натрия 0,1%, либо смесь из солей фтора и хлора натрия в процессе литья алюминиевых отливок.
Такой метод значительно влияет на силумин с 5% добавления кремния, который не подвергают модификации. А при сплаве в 9% кремния, при применении данного способа можно лить сплавы в модифицированном состоянии.
Если добавить в эти сплавы 0,2-0,3% магния, тогда можно будет их упрочнить. А вот если в сплавах находится значительное количество магния или железа, пластические характеристики значительно снижаются. Сплав АЛ 9, хорош в применении отливки изделий, когда конфигурация самого вида изделия усложнена. Этот сплав имеет хорошие линейные свойства, механические и технологические качества. Если выбирать из разновидностей сплавов, то самыми лучшими механическими, а также пластическими качествами обладают сплавы с добавлением в алюминий магния и других металлов. Также им присущ маленький удельный вес и стойкость к коррозии. Все хорошо в этих сплавах, кроме того, что при литье могут появиться трещины там, где разная толщина стенок. Еще они неустойчивы к окислению и имеют плохую растекаемость при плавлении. Вот из-за этих отрицательных качеств данных сплавов, применяют плавление с помощью флюса, если магния в этих сплавах больше 8%.
Очень плохо влияют добавки железа и окислы на сплавы алюминия, в которых присутствует магний. Эти сплавы становятся чувствительными и теряют свои механические свойства. Но вот стоит добавить немного титана или бериллия, как механические характеристики алюминия с магнием снова повышаются, причем также повышается сопротивляемость к коррозии. Предел прочности при центробежном литье алюминия становится значительно выше, до 40кг/мкВ – это при растяжении, и удлиняется на двадцать процентов.
Все благодаря добавлению в двойной алюминиевый сплав, сотых долей титана или бериллия. А вот если вашему предприятию понадобятся детали с высоким уровнем нагрузок, тогда применяют сплавы марки АЛ 8.
Существует два вида алюминиевого сплава: первый – это литейный сплав. Детали производятся с помощью литья из светлых металлов. А второй вид – это деформационный вид сплава. Такой вид используется при изготовлении полуфабрикатов – профиля, листы, проволока, фольга.
Методы литья у нас
Самый популярный способ цветного литья — это способ отлива под постоянным давлением. А менее распространёнными способами являются литье в кокиль, либо в глинисто-песчаную заготовку.
Вот такие существуют способы цветных отливок алюминия. Довольно просто и удобно использовать гипсовые формы для цветного литья, если заказанная партия изделий не слишком велика. Также можно применить способ литья и по моделям, которые выплавляются заранее. Линейные алюминиевые сплавы часто используются в производстве роторов в электромоторах, а также для литых деталей в самолетах и вертолетах.
Для бамперов машин, деталей интерьера и различного декора, для панелей кузовов и много другого применяется деформированный алюминиевый сплав. Такой сплав, который получают при цветном плавлении алюминия, еще используют в летательных машинах и строительстве, и прочих сферах промышленности.
В строительстве очень широко применяют алюминий и все виды деталей из этого материала. Сюда входят рамы и оконные блоки, двери, металлические кабеля и облицовочные плиты. Алюминиевые отливки вырабатываются благодаря цветному литью, имеет популярность в строительной отрасли.
Пришлите ваши чертежи или эскизы на [email protected]
Либо звоните 8-800-250-88-72. Доставка по России и СНГ!!!
Так как этот материал редко подвергается коррозии и любому влажному воздействию, на стройке он идет вход практически везде. При соприкосновении с бетоном, использовании штукатурки и любых растворов, он выдержит повышенную влажность и устоит коррозии. Другое дело, если изделие из алюминиевого сплава находится под постоянным воздействием влажности или любого намокания, тогда коррозии не избежать. Но только тогда, если не была произведена специальная обработка, когда производилось цветное литье. В случае не выполнения обработки, изделие из цветного алюминиевого сплава может потемнеть. Если же в воздухе имеется повышенное содержание окислителя, изделия из подобного сплава даже чернеют.
Алюминиевые отливки в Новосибирске
Алюминиевые отливки (заготовки) – один из самых востребованных видов продукции, которую производят на специально разработанном оборудовании для литья алюминия. Способ технологии производства зависит от требований к качеству, необходимых характеристик и размеров изделия.
Алюминий- известнейший материал, имеющий малую плотность и низкую температуру плавления. Высокая пластичность алюминия позволяет существенно облегчить его прокатку, ковку, волочение и другую обработку. Кроме того, он обладает высокой тепло и электропроводностью , коррозионной стойкостью.
Свойства этого металла позволяют создавать сложные по конфигурации заготовки.
На сегодняшний день алюминиевые литейные сплавы широко применяются во всех отраслях промышленности.
Наиболее популярными способами производства являются кокильное литьё или литьё под давлением, также используется метод жидкой штамповки.
Литье алюминия под давлением
Технология производства
Литье алюминия под давлением осуществляется в литьевых машинах с использованием поршня и пресс-форм.
Процесс отливки происходит по отработанной технологии: расплавленный до 600 градусов Цельсия и выше, металл подается в разъемную пресс-форму под давлением (при помощи сжатого воздуха или поршня). Поршневая машина оснащена прессовочной камерой (холодного или горячего прессования). Через некоторое время готовая деталь извлекается.
Преимущества
Литье алюминия под давлением обеспечивает максимально точное соответствие по размерам отливки и готовой детали, а качество выполнения исключает в дальнейшем использование шлифовки или полировки изделия.
Литье алюминия под давлением позволяет изготавливать большого партию отливок за один рабочий цикл.
Экологичность данного метода обеспечивается отсутствием необходимости использовать формовочные смеси в ходе процесса.
Применение
Литье алюминия под давлением применяется для изготовления заготовок с точными геометрическими формами и отличными физико-механическими свойствами. Эта технология позволяет выполнять изделия различных конфигураций с минимально тонкими гладкими стенками.
Литье алюминия в кокиль
Литье алюминия в кокиль осуществляется при помощи разборной отливочной формы многоразового использования – кокиля.
Кокили бывают разъемные (с различной геометрией разъема) и неразъемные. При помощи кокильного литья получают отливки малых и средних размеров разной конфигурации с использованием сплавов.
Технология производства
Перед началом процесса кокиль нагревают до температуры 150-280 градусов, покрывают огнеупорной краской и после этого разогревают его до рабочей температуры.
Преимущества метода
Практически все операции производства могут быть выполнены механизмами автоматической установки, помогающими механизировать процесс.
При литье в кокиль, одну и ту же форму можно использовать многократно, что также повышает производительность труда.
Точность отливки варьируется от 5 до 9 класса, при шероховатости от 4 до 6 класса. Это позволяет существенно экономить исходное сырье. Метод литья алюминия в кокиль можно отнести к уменьшающим вредное воздействие на окружающую среду.
Применение
Этот способ производства экономически целесообразно применять для серийного (массового) выпуска продукции.
Жидкая штамповка алюминия
Жидкая штамповка алюминия представляет собой технологический процесс получения изделия , при котором кристаллизация жидкого металла , залитого в полость штампа, происходит под высоким давлением.
Технология производства
Технология жидкой штамповки сочетает в себе, с одной стороны, технологию литья под давлением, с другой – процесс горячей штамповки. Жидкий металл подается в матрицу штампа и подвергается давлению пуансона. Окончательное формообразование изделия происходит в момент, когда металл находится в полужидком состоянии, а затем в твердом.
Преимущества метода
Этот метод позволяет получать отливки высококачественного исполнения с высокой плотностью металла и повышенными механическими свойствами, возможностью получения толстостенных заготовок (не менее 4 мм), почти не имеющих воздушно-газовой пористости, экономии металла за счет отсутствия литниковой системы.
Применение
Метод жидкой штамповки широко используется в машино и приборостроении.
Магниевые и литейные алюминиевые сплавы
Разработка магниевых и литейных алюминиевых сплавов, технологий изготовления из них отливок и полуфабрикатов, а также нормативной документации на производственно-технологические процессы изготовления отливок, полуфабрикатов и поставку продукции.
Авторское сопровождение изготовления отливок и полуфабрикатов из магниевых и литейных алюминиевых сплавов в условиях металлургического производства.
Осуществление 3D-моделирования литейных процессов получения фасонных отливок из магниевых и алюминиевых сплавов, а также разработка и проектирование модельной оснастки для литья в песчаные формы, холоднотвердеющие смеси (ХТС) и по выплавляемым моделям.
В НИЦ «Курчатовский институт» – ВИАМ создано малотоннажное производство противопригарных присадочных материалов и флюсов, используемых в магниевом литье, а также отливок из серийных и новых литейных магниевых и алюминиевых сплавов, изготавливающихся по полному технологическому циклу – начиная с разработки чертежа отливки и оснастки, заканчивая получением готовой отливки с защитным покрытием.
Литейные магниевые сплавы
- разработка литейных магниевых сплавов, соответствующих современным требованиям эксплуатации в авиакосмической, машиностроительной и других отраслях;
- разработка коррозионностойких, высокопрочных и жаропрочных магниевых сплавов, значительно превосходящих по характеристикам серийно применяемые сплавы;
- разработка энергосберегающих нетоксичных технологий плавки и литья;
- отработка существующих технологий изготовления отливок из магниевых сплавов и их внедрение на металлургических предприятиях;
- разработка и внедрение технологий герметизации путем пропитки отливок современными пропиточными составами отечественного производства в целях устранения негерметичности литья из алюминиевых и магниевых сплавов;
- анализ качества продукции на наличие внутренних дефектов рентгеновским просвечиванием в соответствии с разработанными регламентом и типовыми эталонами рентгенограмм плотности отливок из магниевых сплавов (МЛ5, МЛ5п.
ч., МЛ9, МЛ10, МЛ19).
Деформируемые магниевые сплавы
- разработка магниевых деформируемых сплавов, а также технологий их плавки, литья и изготовления деформированных полуфабрикатов;
- разработка высокопрочных, жаропрочных, гранулированных деформируемых магниевых сплавов, превосходящих по характеристикам серийно применяемые сплавы;
- исследование влияния структуры, фазового состава и морфологии на основные свойства магниевых сплавов совместно с ИЦ НИЦ «Курчатовский институт» – ВИАМ .
Литейные алюминиевые сплавы
- разработка литейных высокопрочных, коррозионностойких, герметичных и жаропрочных алюминиевых сплавов, превосходящих по своим характеристикам серийно применяемые сплавы, и технологических процессов их производства.
Специалистами института разработаны и производятся:
- противопригарные присадочные материалы для защиты магниевых расплавов от окисления при литье в сырые песчано-глинистые смеси;
- отливки из серийных и новых магниевых и алюминиевых сплавов.
Алюминиевые деформируемые сплавы
Разработка деформируемых алюминиевых и алюминий-литиевых сплавов, слоистых алюмостеклопастиков и гибридных материалов на их основе, бериллийсодержащих сплавов, порошковых композиций на основе алюминия для аддитивного производства.
Отработка промышленных технологий изготовления и термической обработки различных видов полуфабрикатов из новых и серийных деформируемых алюминиевых сплавов на металлургических предприятиях, разработка нормативной документации на изготовление и поставку.
Авторское сопровождение изготовления полуфабрикатов из деформируемых алюминиевых сплавов, слоистых гибридных материалов и конструкций из них в условиях промышленного производства на металлургических и авиастроительных предприятиях.
Алюминий-литиевые сплавы
- разработка современных высокоресурсных и высокопрочных коррозионностойких свариваемых алюминий-литиевых сплавов и технологий изготовления из них различных видов полуфабрикатов на металлургических предприятиях;
- разработка технологий многоступенчатой упрочняющей термической обработки в целях обеспечения наилучшего сочетания прочности и вязкости разрушения;
- разработка технологий изготовления деталей из полуфабрикатов алюминий-литиевых сплавов.
Слоистые алюмостеклопластики и гибридные материалы на их основе
- разработка металлополимерных композиционных материалов на основе алюминиевых, алюминий-литиевых листов и стеклопластиков различного назначения, в том числе:
– высокопрочных слоистых алюмостеклопластиков применительно к обшивкам фюзеляжа;
– слоистых гибридных панелей для обшивок крыла на базе листов из алюминий-литиевых сплавов 1441 и В-1469;
– огнестойких алюмостеклопластиков для противопожарных перегородок, обеспечивающих отсутствие сквозного прогорания материала при температуре 1100°С в течение 15 мин;
- разработка технологий соединения слоистых алюмостеклопластиков, в том числе методом сращивания, для создания крупногабаритных конструкций;
- разработка технологий автоклавного формообразования конструктивно-подобных образцов, элементов и деталей из слоистых гибридных материалов применительно к авиационным конструкциям;
- разработка технологий получения бериллийсодержащих сплавов на основе алюминия, меди, железа и никеля;
- разработка технологий соединения радиационно-прозрачной бериллиевой фольги толщиной 0,01–0,15 мм с конструкционными материалами (медь, монель, нержавеющая сталь и др.
).
Высокопрочные конструкционные алюминиевые сплавы
- разработка современных высокопрочных алюминиевых конструкционных сплавов системы Al–Zn–Mg–Cu с повышенной вязкостью разрушения для различных отраслей промышленности, в частности авиационно-космической;
- разработка технологий изготовления полуфабрикатов из высокопрочных алюминиевых конструкционных сплавов с повышенной вязкостью разрушения на металлургических предприятиях;
- разработка многоступенчатых режимов термической обработки полуфабрикатов из высокопрочных сплавов системы Al–Zn–Mg–Cu.
Ковочные алюминиевые сплавы
- разработка технологий изготовления полуфабрикатов из высокопрочных алюминиевых деформируемых сплавов с пониженным уровнем остаточных напряжений;
- разработка новых сплавов, ресурсо- и энергосберегающих технологий изготовления точных штамповок методами изотермической деформации и тиксоформирования с использованием компьютерного моделирования и экспериментального исследования технологических режимов тиксоформирования для получения точных штамповок для авиационно-космической отрасли;
- разработка технологий изготовления точных штамповок из алюминий-литиевых сплавов методом изотермической деформации.
Алюминиевые сплавы на основе систем Al–Cu, Al–Cu–Mg и Al–Mg–Si
- разработка современных высокоресурсных, высокотехнологичных, свариваемых, коррозионностойких, жаропрочных сплавов и сплавов, не упрочняемых термической обработкой, различного назначения;
- разработка технологий изготовления полуфабрикатов из них на металлургических предприятиях;
- разработка металлопорошковых композиций на основе алюминия для аддитивных технологий.
Алюминий в заготовках, отливках, поковках
Другие товары категории
|
Минимальная толщина стенок отливки из алюминиевых сплавов, мм.
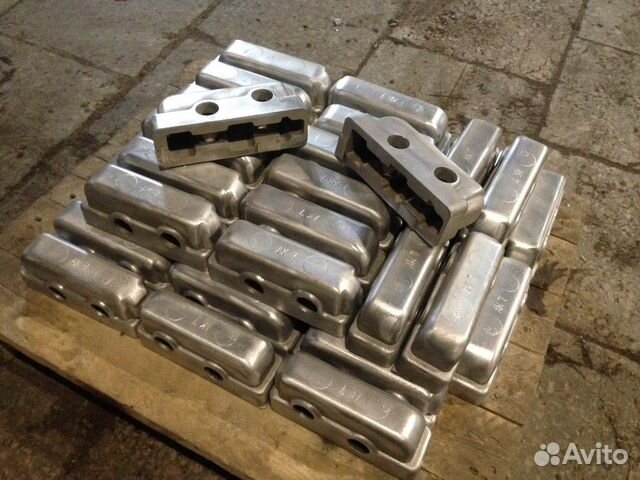
Площадь стенки, см2 | АЛ2 | ЛЛ9, АЛ 11 | АЛ8, АЛ13 |
100 – 250 250 – 900 Св. 900 | 2,2 2,5 3,5 | 3,0 3,5 4,0 | 4,0 4,5 5 |
Таблица 3.9
Диаметры отверстий в отливках и их глубина
Сплавы | Минимальный
диаметр, мм. | Максимальная глубина отверстий, мм. | |
глухих | сквозных | ||
Алюминиевые, магниевые и цинковые Медные | 8 10 | 16 15 | 24 20 |
Таблица 3.10
Минимальная толщина стенок отливок (литье по выплавляемым моделям)
Сплавы | Размеры отливки, мм. | ||||
10 – 50 | 50 – 100 | 100 – 200 | 200 – 350 | Св. | |
Сталь углеродистая Чугун Алюминиевые Магниевые Медные Цинковые | 1,0 1,5 1,0 | 1,5 2,0 1,5 | 2,5 2,0 2,5 2,5 2,5 2,0 | 3,0 2,5 3,0 3,0 3,0 2,5 | 4,0 3,5 3,5 3,5 3,5 3,0 |
Таблица
3. 11
Наименьшая толщина стенок отливок при литье в оболочковую форму
Сплавы | Наибольший габаритный размер отливок мм. | ||||
50 – 100 | 100 – 200 | 200 – 350 | 350 – 500 | До 1500 | |
Чугун Сталь Алюминиевые Магниевые Цинковые Медные Бронзы оловянные | 2,5 – 3,5 2,5 – 4,0 2,5 – 4,0 2,5 – 4,0 2,0 – 4,0 2,5 – 4,0 1,5 – 2,0 | 2,5 – 4,0 3,0 – 3,5 3,0 – 5,0 3,0 – 4,0 2,5 – 3,5 3,0 – 4,0 2,0 – 3,0 | 3,0 – 4,5 3,5 – 6,0 4,0 – 6,0 3,5 – 5,0 3,0 – 4,0 3,5
– 5. 2,5 – 3,5 | 4,0 – 5,0 5,0 – 7,0 4,0 – 7,0 4,0 – 6,0 3,5 – 5,0 4,0 – 6,0 3,0 – 4,0 | 8,0 – 10,0 8,0 – 12,0 7,0 – 10,0 5,0 – 7,0 4,0 – 6,0 |
При
конструировании отливок учитывают
следующие их особенности. Наименьшая
толщина стенок отливок по выплавляемым
моделям, которая может быть выполнена
без применения специальных условий
заливки (вакуумное всасывание, центробежное
литье, литье под низким давлением), 1 – 2
мм. Наиболее распространена толщина
стенки отливки 2 – 5 мм. Тонкие стенки
могут выполняться только при определенной
площади их поверхности (не более 75 х 75
мм), так как в противном случае происходит
коробление стенок формы. Толщину стенок
отливок, получаемых литьем по выплавляемым
моделям из различных сплавов, выбирают
с учетом минимально допустимых ее
значений (табл. 3.10).
В длинных плоских стенках, имеющих площадь более 100 см2, следует предусматривать технологические отверстия диаметром 10 – 20 мм. При конструировании пазов в отливках необходимо, чтобы расстояние между выступами или ребрами, образующими ширину и глубину паза, для цветных сплавов было не менее 1 мм, а для стали – не менее 2,5 мм. Необходимо избегать внутренних полостей, усложняющих изготовление моделей и требующих изготовления стержней. Внутренняя полость отливки должна иметь выходные отверстия, достаточные для того, чтобы прочно соединять внешние и внутренние стенки формы.
В
рациональном варианте конструкции
отливки внутренние полости соединены
и образуют общую полость, что обеспечивает
необходимую устойчивую связь внутренней
стенки формы с наружной. Внутренние
полости должны иметь выходные отверстия
для удаления остатков формы при очистке
отливок. Выполнение резьбы литьем по
выплавляемым моделям представляет
большие трудности, особенно при мелком
шаге (усложняется изготовление моделей,
а на отливках в углублениях резьб
возникают дефекты в виде металлических
приливов).
При литье по выплавляемым моделям желательно, чтобы деталь имела одни и те же базовые плоскости для изготовления и проверки пресс-форм и для механической обработки детали. Базовые поверхности должны образовываться минимальным числом элементов пресс-формы, желательно – одним элементом, например, в случае, если они расположены в одной плоскости пресс-формы.
3.6.4 Литье в оболочковую форму.
При
этом способе литья заливку металла
производят в оболочковые песчано-смоляные
формы, которые позволяют устранить
недостатки, свойственные толстостенным
песчаным формам (большой расход
формовочных материалов, низкая скорость
затвердевания). Эти формы имеют небольшую
толщину стенок (6
– 8 мм), высокое значение временного
сопротивления (до 6 МПа), что объясняется
использованием в качестве связующего
материала термореактивных смол, которые
в процессе нагрева при изготовлении
формы полимеризуются и прочно связывают
кварцевый песок.
При литье в оболочковую форму припуски на механическую обработку назначают меньшими, чем при литье в песчаную форму, что способствует значительной экономии металла. Разъем формы должен быть плоским, а поверхности отливок по возможности плоскими или цилиндрическими. Следует избегать конструирования отливок большой длины при малой ширине или толщине, так как это ведет к их короблению при охлаждении в форме и при термической обработке.
Толщину стенок отливок предпочтительно выполнять одинаковой, чтобы обеспечить равномерную кристаллизацию металла. Выбирают ее с учетом минимально допустимых значений, приведенных в табл. 3.11. При малой толщине стенок отливок отверстия можно выполнять без стержней по модели.
Алюминиевые сплавы, обладающие улучшенным качеством поверхности отливок, и способ их получения
Изобретение относится к составам алюминиевых сплавов, а именно к улучшенному качеству поверхности алюминиевых болванок. Способ получения литых алюминиевых сплавов с улучшенными поверхностными свойствами включает стадии: приготовление расплавленного алюминиевого сплава из 7ххх группы зарегистрированных Aluminium Association сплавов, практически не содержащего Be; добавление к расплавленному алюминиевому сплаву приблизительно от 0,0005 до 0,5 мас. % Са и измельчающей зерно добавки, выбранной из группы, состоящей из, мас.%: 3Тi-1В-Al, 3Ti-0,15C-Al; и отливка алюминиевого сплава с образованием болванки. Предложен также алюминиевый сплав и болванка, отлитая из него. Техническим результатом изобретения является улучшение поверхностных свойств болванки, отлитой из алюминиевого сплава. 3 н. и 8 з.п. ф-лы, 8 ил., 2 табл.
Область техники
Изобретение относится в основном к составам алюминиевых сплавов и, более конкретно, к улучшенному качеству поверхности алюминиевых болванок, полученных из этих сплавов в строго регулируемых условиях плавления, что улучшает последующую переработку и выходы.
Предшествующий уровень техники
В практике алюминиевого литья хорошо известно, что различные дефекты поверхности, такие как раковины, вертикальные складки, оксидные лоскуты и т.п., которые образуются при отливке болванки, в процессе отливки или последующей переработки могут превратиться в трещины. Трещина в болванке или плите развивается, например при последующей прокатке, приводя к необходимости дорогостоящей повторной восстановительной обработки или полной отбраковки растрескавшегося материала. Поверхностные дефекты у отлитых алюминиевых болванок продолжают оставаться проблемой в практике производства сплавов.
Обработка предполагает различные, хорошо известные в металлургической практике операции, в числе которых могут быть, например, названы горячая прокатка, холодная прокатка, экструзия, ковка, протяжка, вытяжка с утонением, горячая обработка, дисперсионное твердение, формовка и вытягивание. При обработке или формовке сплава к обрабатываемому объекту подводят энергию, но эта энергия не всегда распределяется равномерно.
Отливка сплавов может быть осуществлена с помощью множества известных специалистам способов, таких как бесслитковое литье (БСЛ), электромагнитное литье (ЭМЛ), горизонтальное бесслитковое литье (ГБСЛ), утепленное литье сверху, непрерывное литье, полунепрерывное литье, литье под давлением, литье через валки и литье в песчаные формы. Каждый из этих способов литья имеет ряд присущих ему проблем, но при этом общей проблемой для каждого из этих способов продолжают оставаться поверхностные дефекты. Одним их механических средств для удаления поверхностных дефектов с болванки алюминиевого сплава является удаление поверхностного слоя. Удаление поверхностного слоя заключается в механической обработке поверхности поверхностного слоя по боковым поверхностям болванки после того, как она затвердеет.
Алюминиевыми сплавами могут быть любые сплавы, зарегистрированные ассоциацией Aluminum Association (“AA”), такие как серии сплавов 1xxx, 2xxx, 3ххх, 4ххх, 5ххх, 6ххх, 7ххх и 8ххх. Некоторые сплавы, такие как 7050 и другие сплавы 7ххх, так же, как 5182 и 5083, особенно предрасположены к поверхностным дефектам и растрескиванию. В прошлом для предотвращения поверхностных дефектов к некоторым из этих сталей добавляли бериллий, обычно в количествах порядка 1 части на миллион (ч./млн.). Однако бериллий был исключен из алюминиевых изделий, используемых для упаковки пищевых продуктов и напитков. Кроме того, существовало большое опасение относительно опасности для здоровья заводских рабочих, имеющих дело с бериллием и содержащими его изделиями. В результате этого, несмотря на эффективность бериллия в отношении предотвращения поверхностных дефектов у болванок из алюминиевого литья, бериллий нуждается в адекватной замене.
В патенте US 5469911, выданном на имя Parker, раскрывается способ улучшения качества поверхности отлитых электромагнитным методом болванок алюминиевого сплава, который включает добавление от 0,01 до 0,04 мас.% кальция в приемную горловину изложницы. Эти количества кальция значительно выше измеряемых в ч./млн., уровней, используемых для бериллия. Такое высокое содержание кальция может неблагоприятно повлиять на свойства сплава.
В патенте US 4377425 на имя Otani et al. раскрывается применение кальция для полученных с помощью бесслиткового литья болванок из алюминиевого сплава с высоким содержанием железа с целью сведения к минимуму дендритных, или так называемых «елочных», кристаллических структур с размером зерна меньше 150 мкм. Этот способ оказался особенно успешным для алюминиевых сплавов серий АА1000 и АА5000. Влияние (если таковое имеется) кальция на качество производимых болванок Otani et al. раскрыто не было.
В историческом аспекте кальций так же, как и натрий, рассматривались как нежелательные элементы для выплавленных или отлитых алюминиевых сплавов из-за проблем, связанных с краевым растрескиванием. Эти элементы обычно удаляли из расплава с помощью газообразного хлора, вводимого перед отливкой болванки.
Сохраняется потребность в эффективной альтернативе бериллию для предотвращения образования при отливке алюминиевой болванки поверхностных дефектов, таких как вертикальные складки, раковины, оксидные лоскуты и т.п. Такой альтернативой мог бы быть инструментальный способ предотвращения трещин, которые могут образоваться при отливке или развиться при последующей обработке. Наконец, способ не должен оказывать неблагоприятного влияния на свойства сплава.
Раскрытие сущности изобретения
Целью настоящего изобретения является добавление к алюминиевому сплаву малых количеств кальция для улучшения поверхностных свойств болванки отлитого алюминия. Кальций и до 0,25% измельчающих зерно добавок, таких как борид титана, вместе с щелочно-земельными металлами, переходными металлами, редкоземельными металлами и/или другими элементами добавляют к расплавленному алюминиевому сплаву. В результате этого добавления улучшается внешний вид поверхности свежеотлитого металла, значительно уменьшаются поверхностные дефекты и/или значительно снижается окисление поверхности отлитого слиткового алюминия и алюминиевых сплавов. Неожиданным образом было обнаружено, что введение малых количеств названных добавок в значительной степени устраняет вертикальные складки, раковины и растрескивание болванки в не менее чем двух способах отливки болванок. Добавки улучшают также внешний вид болванок, включая их отражательную способность. Благодаря этому болванки могут быть обжаты или в существенной степени обработаны непосредственно по завершении операции отливки без предварительного кондиционирования поверхности, например удаления ее поверхностного слоя.
Алюминиевый сплав настоящего изобретения содержит от 5 до 1000 ч. /млн. кальция, до 0,25% измельчающих зерно добавок и практически не содержит Be. Сплав может содержать менее 0,2% Fe. Кроме того алюминиевый сплав может содержать щелочно-земельные металлы, переходные металлы, редкоземельные металлы и/или другие элементы, необходимые для обеспечения желаемых свойств.
Нами было также обнаружено, что для удаления поверхностных дефектов требуется значительно меньшее количество Са в сочетании с измельчающей зерно добавкой Ti-C, чем в сочетании с измельчающей зерно добавкой Ti-B.
Целью изобретения является также способ улучшения поверхностных свойств и предупреждения поверхностных дефектов и растрескивания отлитых алюминиевых сплавов. Этот способ включает стадии добавления кальция к расплавленному алюминиевому сплаву, практически не содержащему бериллия, и отливки алюминиевого сплава с использованием обычно применяемых способов.
Эти и другие преимущества настоящего изобретения будут освещены в описании предпочтительных вариантов изобретения вместе с приложенными чертежами, на которых одни и те же ссылочные цифры всюду обозначают одни и те же элементы.
Фиг.1 представляет (фотографию) свежеотлитую болванку алюминиевого сплава, к которому не было добавлено ни бериллия, ни кальция.
Фиг.2 представляет фотографию, показывающую крупным планом поверхностную часть болванки алюминиевого сплава фиг.1, демонстрируя участок зарождения трещины.
Фиг.3 представляет (фотографию) свежеотлитую болванку алюминиевого сплава, к которому было добавлено 12 ч./млн. Be.
Фиг.4 представляет (фотографию) свежеотлитую болванку алюминиевого сплава, к которому было добавлено 240 ч./млн. (0,024%) Са в соответствии с изобретением.
Фиг.5 представляет (фотографию) свежеотлитую болванку алюминиевого сплава, к которому было добавлено 53 ч./млн. (0,0053%) Са в соответствии с изобретением.
Фиг.6а и фиг.6b представляют гистограммы, показывающие взаимоотношение между содержанием Са в алюминиевом сплаве и развитием поверхностных трещин.
Фиг.7 представляет фотографию, показывающую взаимоотношение между составом алюминиевого сплава серии 7ххх и окислением поверхности.
Исключая примеры выполнения операций или те случаи, когда оговорено особо, все числа или выражения, относящиеся к количествам ингредиентов, условиям реакции и т.д., использованных в детальных описаниях или в пунктах формулы изобретения, следует принимать во всех случаях как изменяемые термином «приблизительно».
Алюминиевый сплав настоящего изобретения содержит от 5 до 1000, предпочтительно от 10 до 750 и, наиболее предпочтительно, от 15 до 500 ч./млн. кальция; до 0,25, предпочтительно от 0,001 до 0,25% и, наиболее предпочтительно, от 0,1 до 0,25% измельчающих зерно добавок; менее 0.2, преимущественно менее 0,19 и, наиболее предпочтительно, от 0,001 до 0,19% Fe; практически без Be – остальное составляют алюминий и неизбежные примеси. Алюминиевый сплав может также содержать щелочно-земельные металлы, переходные металлы, редкоземельные металлы и/или другие элементы, необходимые для обеспечения желаемых свойств.
Количество кальция в составе алюминиевого сплава настоящего изобретения может быть любым количеством, которое обеспечило бы улучшение свойств поверхности и предотвратило поверхностные дефекты и растрескивание отливок алюминиевого сплава. Необходимое количество кальция может составлять от 8 до 15, or 15 до 300, от 20 до 250, от 25 до 200 или от 25 до 150 ч./млн. в зависимости от отлитого алюминиевого сплава.
Возможно, и при этом предпочтительно, включение в состав алюминиевого сплава настоящего изобретения одной или более измельчающих зерно добавок. К числу агентов, способствующих измельчению зерна алюминия, принадлежат переходные металлы, такие как Ti и Zr, металлы, такие как Sr и неметаллы, такие как В и С, которые добавляют к расплавленному металлу. Предпочтительными измельчителями зерна являются Ti, Zr, В и С.
В настоящем тексте принято, что термин «измельчающая зерно добавка» относится к хорошо известным досплавным материалам, обычно в форме стержня или проволоки, которые непрерывно вводят в поток литья или расплавленного алюминиевого сплава для достижения желаемой дисперсности зерна в затвердевшей болванке. К типичным системам измельчающих зерно добавок относятся Ti-B или Ti-C, вплавленные в алюминий в форме стержня с диаметром 3/8 дюйм. Обычно используемыми системами измельчителей зерна являются 3% Ti – 1% В – баланс Al; 3% Ti – 0,15% С – баланс Al; 5% Ti – 1% В – баланс Al; 5% Ti – 0,2% В – баланс Al и 6% Ti – 0,02% С – баланс Al. Содержание Ti, В и С в затвердевшем алюминиевом сплаве после отливки с использованием названных выше измельчающих зерно материалов является следующим (в мас.%):
Ti Широкий диапазон | 0,0002-0,20 |
Ti Предпочтительный диапазон | 0,0003-0,10 |
В Широкий диапазон | 0,0001-0,03 |
В Средний диапазон | 0,0001-0,01 |
В Предпочтительный диапазон | 0,0003-0,005 |
С Широкий диапазон | 0,00001-0,001 |
С Предпочтительный диапазон | 0,000015-0,0004 |
Алюминиевый сплав настоящего изобретения включает в себя все зарегистрированные Aluminum Association сплавы такие как серии сплавов 1xxx, 2xxx, 3ххх, 4ххх, 5ххх, 6ххх, 7ххх и 8ххх. Предпочтительными сплавами являются АА2ххх, АА3ххх, АА5ххх и АА7ххх. Более предпочтительными сплавами являются АА5ххх и АА7ххх. Наиболее предпочтительными сплавами являются АА5182, АА5083, АА7050 и АА7055. Естественно, что и другие, не зарегистрированные АА сплавы, также могут быть подходящими для настоящего изобретения.
Нами было также обнаружено, что добавление к расплавленному алюминиевому сплаву кальция приводит к меньшему образованию оксидов на поверхности отлитой болванки алюминиевого сплава. Значение ослабления образования некоторых поверхностных дефектов у болванки состоит в том, что это позволяет удалять поверхностный слой на меньшую глубину или, возможно, не удалять его вообще. Настоящее изобретение уменьшает, таким образом, количество отходов от болванки благодаря меньшей потребности или отсутствию потребности в удалении поверхностного слоя.
Целью настоящего изобретения является также способ улучшения поверхностных свойств сразу же после отливки и предотвращения поверхностных дефектов и растрескивания болванки отлитых алюминиевых сплавов. Этот способ включает предварительное добавление к практически не содержащему Be расплавленному алюминию от 5 до 5000, предпочтительно от 5 до 1000, более предпочтительно от 10 до 750 и, наиболее предпочтительно, от 15 до 500 ч./млн. кальция. В случае использования измельчающей зерно добавки Ti-B для устранения поверхностных дефектов эффективны 25-30 ч./млн. Са, а в случае использования измельчающей зерно добавки Ti-C эффективны приблизительно 8-14 ч./млн. Са. Алюминиевый сплав может содержать менее 0,2% Fe, преимущественно менее 0,19% и, наиболее предпочтительно, от 0,001 до 0,19% Fe. Алюминиевый сплав предпочтительно включает также до 0,25, предпочтительно от 0,001 до 0,25 и, наиболее предпочтительно, от 0,1 до 0,25% одной или более измельчающих зерно добавок. Кроме того, алюминиевый сплав может содержать щелочноземельные металлы, переходные металлы, редкоземельные металлы и/или другие элементы, необходимые для обеспечения желаемых свойств и состава сплава в соответствии со стандартом Aluminum Association.
Вторая стадия способа изобретения включает отливку алюминиевого сплава с использованием какого-либо из обычно применяемых видов литья. Такие обычно применяемые виды литья включают бесслитковое литье (БСЛ), электромагнитное литье (ЭМЛ), горизонтальное бесслитковое литье (ГБСЛ), утепленное литье сверху, непрерывное литье, полунепрерывное литье, литье под давлением, литье через валки, литье в песчаные формы и другие известные специалистам способы литья.
В случае необходимости отлитая болванка алюминиевого сплава может быть обработана. Обработка состоит из различных известных в практике сплавов послеотливочных операций, включающих горячую прокатку, холодную прокатку, экструзию, ковку, протяжку, вытяжку с утонением, горячую обработку, дисперсионное твердение, формовку, вытягивание, удаление поверхностного слоя и другие известные специалистам операции.
Способ настоящего изобретения особенно эффективен для улучшения свойств поверхности и предупреждения поверхностных дефектов и растрескивания отлитых алюминиевых сплавов, относящихся к зарегистрированным сплавам Aluminum Association 1xxx, 2ххх, 3ххх, 4ххх, 5ххх, 6ххх, 7ххх и 8ххх. Предпочтительными сплавами, которые могут быть получены в виде болванок с использованием настоящего способа, являются АА2ххх, АА3ххх, АА5ххх и АА7ххх. Более предпочтительными сплавами являются АА5ххх и АА7ххх. Наиболее предпочтительными сплавами являются АА7050, АА5182, АА5083 и АА7055.
Сведение к минимуму окисления расплавленных сплавов и поверхностных дефектов в получаемых болванках повышает степень извлечения алюминиевого сплава на разных стадиях процесса. Повышенная степень извлечения снижает производственные расходы и повышает производительность производственного оборудования. В частности, уменьшенное окисление приводит к уменьшенным потерям расплава, представляющим собой потери, которые имеют место при плавлении, выдержке и отливке.
ПРИМЕРЫ 1-5
Болванки сечением 16 дюйм х 50 дюйм были вертикально отлиты с использованием способа бесслиткового литья (БСЛ). Болванки отливали до длины 180 дюйм. Расплавленный алюминиевый сплав протекал в изложницу из раздаточной печи через одноступенчатую поточную дегазационную установку, фильтр для расплавленного металла и сливное отверстие. Алюминиевый сплав обладал составом серии АА7000. Болванки описаны в Таблице 1.
В таблице 1 «отсутствие трещин» предполагает, что на поверхности болванки не было видимых раковин, складок или трещин. В примерах 1 и 2 степень растрескивания была такова, что болванки были не пригодными для использования. На фиг.1-5 показаны болванки, соответствующие приведенным выше примерам. Эти примеры демонстрируют, что добавление кальция к алюминиевому сплаву АА7ххх предотвращает растрескивание в той же степени, что и бериллий. Очень малая добавка кальция – 53 ч./млн., или 0,0053 мас.%, в сочетании со стандартным количеством измельчающей зерно добавки 3% Ti-0,15% С (пример 5) оказалась неожиданным образом эффективной в отношении устранения с поверхности болванки трещин, раковин или складок.
ПРИМЕРЫ 6-10
Примеры 6-10 были выполнены как указано выше. Алюминиевый сплав АА7050 включал стандартные количества измельчающей зерно добавки 3% Ti-1% В и варьируемые количества кальция с целью определения его содержания, необходимого для предотвращения поверхностных дефектов. Полученные в этих примерах данные представлены в виде гистограммы на фиг.6а.
Эти данные указывают на то, что при содержании кальция выше приблизительно 25 ч./млн. трещины не наблюдались.
ПРИМЕРЫ 5, 8-25
Примеры 5,8-25 были выполнены так же, как и примеры 6-10, с использованием алюминиевого сплава АА7050, но с измельчающей зерно добавкой 3% Ti-0,15% С. Данные этих примеров представлены в виде гистограммы на фиг.6b для разных количеств Са: Пример 5 – 53 ч./млн.Са, Пример 18 – 14 ч./млн. Са, Пример 19 – 4 ч./млн. Са, Пример 20 – 3 ч./млн. Са, Пример 21 – 2 ч./млн. Са, Пример 22 – 3 ч./млн. Са, Пример 23 – 8 ч./млн. Са, Пример 24 – 4 ч./млн. Са и Пример 25 – 96 ч./млн. Са. Эти данные указывают на то, что содержание Са между приблизительно 10 и 50 ч/млн, или выше до 100 ч/млн, оказывается эффективным с измельчающей зерно добавкой 3% Ti-0,15% С в отношении устранения поверхностных дефектов.
ПРИМЕРЫ 11-17
Примеры 11-17 (см. таблицу 2) представляют собой измерение окисления на расплавленном сплаве Al-5Мg. Графики (Фиг.7). Графики временной зависимости (Фиг.7) показывают обусловленный окислением привес для разных примеров. Графики демонстрируют значительное снижение окисления в том случае, когда в сплав введены 300 ч./млн., или 0,03% кальция (Пример 17), по сравнению со сплавом без добавок (Примеры 11 и 12) и измельчающими зерно добавками 3% Ti-1% В (Пример 13), 6% Ti-0,02% С (Пример14), 3% Ti-0,15% С (Пример 15) и 6% Ti (Пример 16).
Таблица 2 | |
Пример | Добавка(и), м.д. мас |
11 | Отсутствует |
12 | Отсутствует |
13 | 3% Ti, 1% В |
14 | 6% Ti, 0,02% С |
15 | 3% Ti, 0,15% С |
16 | 6% Ti |
17 | 300 ч/млн. (0,03%) Са |
Все вышесказанное предполагает, что изобретение построено таким образом, что оно включает все такие модификации и изменения, если они не выходят за рамки приложенных пунктов формулы изобретения или их эквивалентов.
1. Способ получения литых алюминиевых сплавов с улучшенными поверхностными свойствами, включающий стадии:
a) приготовление расплавленного алюминиевого сплава из 7ххх группы зарегистрированных Aluminium Association сплавов, практически не содержащего Be;
b) добавление к расплавленному алюминиевому сплаву приблизительно от 0,0005 до 0,5 мас.% (от 5 до 5000 ч./млн) Са и измельчающей зерно добавки, выбранной из группы, состоящей из, мас.%: 3Ti-1B-Al, 3Ti-0,15C-Al; и
c) отливка алюминиевого сплава с образованием болванки.
2. Способ по п.1, отличающийся тем, что алюминиевый сплав содержит менее 0,2 мас.% Fe.
3. Способ по п.1, отличающийся тем, что получают алюминиевый сплав, содержащий до 0,25 мас.% измельчающих зерно добавок.
4. Способ по п.1, отличающийся тем, что литье отливки из алюминиевого сплава осуществляют бесслитковым литьем или электромагнитным литьем, или горизонтальным бесслитковым литьем, или утепленным литьем сверху, или непрерывным литьем, или полунепрерывным литьем, или литьем под давлением, или литьем через валки, или литьем в песчаные формы.
5. Способ по п.1, отличающийся тем, что дополнительно обрабатывают болванку.
6. Способ по п.1, отличающийся тем, что к расплаву добавляют от 0,0008 до 0,0015 мас.% (от 8 до 15 ч./млн) Са и используют измельчающую зерно добавку, содержащую следующие компоненты, мас.%: 3Ti-0,15C-Al.
7. Способ по п.5, отличающийся тем, что стадия обработки состоит из одной или более операций, выбранных из группы, состоящей из горячей прокатки, холодной прокатки, экструзии, ковки, протяжки, вытяжки с утонением, горячей обработки, дисперсионного твердения, формовки и вытягивания.
8. Алюминиевый сплав из 7ххх группы зарегистрированных Aluminium Association сплавов, отличающийся тем, что практически не содержит Be и содержит от 0,0005 до 0,1 мас.% (от 5 до 1000 ч./млн) Са и до 0,25 мас.% измельчающих зерно добавок, выбранных из группы, состоящей из, мас.%: 3Ti-1B-Al, 3Ti-0,15C-Al.
9. Алюминиевый сплав по п.8, отличающийся тем, что он содержит менее 0,2 мас.% Fe.
10. Алюминиевый сплав по п. 8, отличающийся тем, что он содержит от 8 до 30 ч./млн Са.
11. Болванка, отлитая из алюминиевого сплава, отличающаяся тем, что она отлита из сплава по п.8.
Поставщики алюминиевого литья | Литейный завод по алюминиевому литью
Главная > Алюминиевое литье
Запросить предложение
Компания Le Sueur Incorporated уникальна тем, что мы предлагаем несколько процессов литья алюминия, включая постоянные формы, литье в песчаные формы и литье под давлением. Предложение всех трех процессов позволяет нам давать беспристрастные рекомендации при оказании помощи нашим клиентам. Мы используем наш опыт в нюансах каждого метода, чтобы выбрать лучший процесс литья, сплавы и процессы отделки для достижения конкретных требований к продукту.
Эксперты по алюминиевому литью предлагают индивидуальные решения
Раннее вовлечение в процесс LSI специализированного инженерного персонала имеет важное значение для достижения взаимного успеха проекта. Эти инженеры-профессионалы помогают нашим клиентам в процессе разработки продукта, используя наиболее выгодные инструменты и методы литья алюминия. Наши инженеры являются экспертами в различных процессах литья. Инструментарий создается для каждого уникального сценария. Вместе с нашими клиентами разрабатывается конструкция продукта для выбранных процессов литья и производства, чтобы производить наиболее экономичную и надежную деталь.
Соображения по выбору наилучшего процесса литья алюминия
Литье алюминия — это широко используемый процесс, который включает заливку или впрыскивание расплавленного алюминия в форму для многократного создания сложных и детализированных деталей. Существует много типов процессов литья. В каждом производственном процессе используются разные типы форм для производства отливки, и для заполнения формы расплавленным алюминиевым сплавом используется либо давление, либо сила тяжести.
Существует несколько соображений при выборе правильного процесса литья алюминия для вашего применения. Ознакомьтесь с приведенными ниже соображениями, чтобы узнать больше, или свяжитесь с нашими экспертами, чтобы обсудить любые вопросы, касающиеся того, какой процесс литья алюминия лучше всего подходит для вашего применения.
Рассмотрение кастинга | Литье в песчаные формы | Литье под давлением | Постоянная форма |
---|---|---|---|
Поверхность | Низкий | Высокий | Средний |
Литье | Низкий | Высокий | Средний |
Стоимость инструмента | Низкий | Высокий | Средний |
Производство | Высокий | Низкий | Средний |
Производство | Низкий | Высокий | Средний |
Механические | Средний | Средний | Высокий |
Структура | Высокий | Средний | Высокий |
Давление | Средний | Высокий* | Высокий |
Внутренний | Средний | Низкий | Высокий |
Рядом с сетью | Низкий | Высокий | Средний |
Легкость | Высокий | Низкий | Средний |
Сложность | Низкий | Высокий | Средний |
Стойкость** | Низкий | Высокий | Средний |
Инструмент | Низкий | Высокий | Высокий |
Производство | Низкий | Средний | Высокий |
* Герметичность литья под давлением улучшена за счет использования технологии Squeeze Pin.
** Стойкость инструмента сильно зависит от типа оснастки, геометрии отливки и требований к чистоте поверхности.
Возможности литья в постоянные формы
Являясь ведущим в отрасли поставщиком алюминиевых отливок и литья пластмасс под давлением, компания Le Sueur Incorporated предлагает услуги полупостоянного и постоянного литья в алюминиевые формы. Наши инженеры имеют опыт в поиске наиболее экономичного и эффективного решения для ваших потребностей в литье в постоянные формы низкого давления и наклонной заливки. Наши возможности включают прецизионную механическую обработку, чистовую обработку и сборку.
Обсудите свой проект алюминиевого литья с LeSueur
Le Sueur Incorporated специализируется на сложных по размерам, герметичных алюминиевых отливках и компонентах, полученных литьем под давлением из термопластов. Мы предлагаем полную прецизионную механическую обработку, чистовую обработку и сборку на месте. Пожалуйста, свяжитесь с нами , чтобы начать свой проект!
Алюминиевые отливки | Алюминиевые сплавы
Алюминий — это легкий материал, известный своей коррозионной стойкостью и легкостью обработки. При упрочнении за счет дополнительного легирования и термической обработки алюминий становится материалом, обеспечивающим прочность, аналогичную мягкой низкоуглеродистой легированной стали, что делает его идеальным для целого ряда применений в алюминиевом литье. Именно из-за этих улучшений физических и механических свойств отливки из алюминиевых сплавов все чаще используются в различных условиях окружающей среды во многих отраслях промышленности.
Свяжитесь с Aero Metals
Получить предложение
Текучесть алюминиевых сплавов позволяет разработчикам компонентов использовать тонкостенные профили, когда это необходимо, и создавать сложные детали. Чтобы максимизировать прочность, можно использовать поддерживающую лямку для обеспечения жесткости в критических зонах. Его низкая температура плавления и быстрая теплопередача также приводят к сокращению циклов литья и сокращению времени производства. Литье алюминиевых сплавов — универсальный процесс, обладающий рядом дополнительных преимуществ, в том числе:
- Высокое соотношение прочности и веса
- Превосходная химическая стабильность
- Превосходная коррозионная стойкость
- Устойчивость к высоким температурам
- Превосходная тепло- и электропроводность
- Гладкая литая поверхность
Литье алюминия по выплавляемым моделям — это универсальное решение, используемое в ряде отраслей, включая военную, аэрокосмическую, медицинскую, автомобильную, грузовую, сельскохозяйственную, огнестрельную и другие. Его можно использовать для многочисленных деталей и компонентов, включая клапаны, медицинские устройства, рычаги, приборы, ручные инструменты, кронштейны, автомобильные детали, компоненты самолетов и машины.
Литье из алюминиевого сплава повышает долговечность деталей и компонентов
Aero Metals Inc. имеет большой опыт в литье из алюминиевого сплава, работая с широким спектром других сплавов черных и цветных металлов . Мы можем производить отливки из алюминиевого сплава с различной геометрией, точностью размеров, исключительной чистотой поверхности, тонкими стенками (0,040 дюйма) и мелкими деталями. Мы проектируем и производим все инструменты на месте и предоставляем услуги по обработке с ЧПУ для завершения ваших алюминиевых отливок.
Все наши алюминиевые отливки по инвестиционным моделям изготавливаются из восковой формы, которая либо передается нам, либо изготавливается в нашем собственном инструментальном цехе и отливается из нашей 600-фунтовой индукционной плавильной печи. Наши опытные инженеры могут производить отливки со сложными деталями, используя творческие методы предварительного и последующего литья.
Наши необработанные алюминиевые литейные материалы сертифицируются перед покупкой, как в случае алюминиевых сплавов аэрокосмического качества, или мы сертифицируем сплав в нашей спектрометрической лаборатории перед использованием. После того, как отливка отлита и очищена, мы можем улучшить прочность, обрабатываемость, коррозионную стойкость и пластичность путем термообработки в соответствии со спецификациями чертежа. Наиболее распространенными марками алюминиевого сплава для литья по выплавляемым моделям, которые мы используем, являются A356 и 356, каждая из которых обеспечивает хорошие характеристики литья и механической обработки.
Свяжитесь с нами, чтобы узнать больше об услугах по литью алюминия по выплавляемым моделям и о нашей приверженности качеству литья, включая проверку и испытания для обеспечения высокого качества деталей и услуг.
Отливки из алюминиевого сплава A356
Aero Metals в основном отливает отливки из алюминиевых сплавов A356 и 356 для аэрокосмических и промышленных применений. Алюминий A356 обеспечивает умеренную прочность, отличную литейность, свариваемость и герметичность и относится к категории литейных алюминиевых сплавов со следующим составом:
Сплав A356 Состав:- 92,05% Алюминий (Al)
- 7,00% Кремний (Si)
- 0,35% Магний (Mg)
- 0,20 % железа (Fe)
- 0,20 % Медь (Cu)
- 0,10% Марганец (Mn)
- 0,10% Цинк (Zn)
Термическая обработка литья из алюминиевого сплава
В зависимости от ваших требований к прочности и пластичности мы можем обеспечить термообработку для дальнейшего повышения прочности, твердости и других механических свойств. Этот процесс осуществляется через одного из наших внешних партнеров.
Отжиг происходит после завершения процесса литья по выплавляемым моделям и включает нагрев алюминиевого сплава в течение до трех часов для рекристаллизации сплава, что облегчает работу с компонентом.
Термическая обработка на твердый раствор аналогична процессу отжига, но включает процесс закалки, который быстро охлаждает литой алюминиевый сплав после нагрева, чтобы помочь сохранить распределение элементов. После охлаждения алюминиевого сплава используется один из трех различных процессов старения, чтобы позволить сплаву вернуться в закаленное состояние. Выбранный тип процесса старения зависит от количества времени, необходимого для обработки материала после термической обработки.
Наша термообработка литья из алюминиевого сплава включает:
- T2 (отжиг): отжиг без каких-либо дополнительных процессов
- T4 (Термообработка раствором и естественное старение): создает практически стабильное состояние и идеально подходит для деталей, которые не будут подвергаться холодной обработке после обработки
- T6 (термическая обработка раствором и искусственное старение): создает механические свойства, на которые не влияет холодная обработка
- T61* (Термообработка раствором, закалка и старение): использует закалку кипящей водой и обеспечивает максимальную прочность на растяжение до 40K PSI для отливок из алюминиевых сплавов.
Свяжитесь с нами, чтобы узнать больше о решениях для литья алюминия по выплавляемым моделям
Aero Metals предоставляет услуги по литью по выплавляемым моделям с использованием различных сплавов. Если вы не видите интересующий вас сплав, у нас есть возможность отлить любой алюминиевый сплав «воздушной плавки» как для мелкосерийного, так и для крупносерийного производства.
Начните свой проект литья по выплавляемым моделям сегодня
Свяжитесь с нами или позвоните нам по телефону 219-326-1976, чтобы наш местный металлург помог в выборе сплава для вашего проекта. Мы можем помочь вам найти правильный сплав, соответствующий вашим конкретным потребностям.
Использование технологической сварки для ремонта алюминиевых отливок
Дэвид Вайс, Майк Гвин и Кит Стургилл
Большинство алюминиевых литейных заводов используют сварку для законных действий, таких как вваривание заглушки в отверстие опоры сердечника, но она также часто используется для устранения дефектов в отливках, чтобы они соответствовали размерным или другим требованиям к качеству. .
Ни заказчики, ни руководство литейного производства не совсем довольны этим, поскольку мантра заключается в том, чтобы сделать все правильно с первого раза. Тем не менее, сложные конструкции, небольшие требования к объему или давление затрат иногда заставляют использовать доработку сварных швов для спасения отливок.
Отливки могут иметь небольшие дефекты поверхности, такие как ямки включения, газовая микропористость, холодные притиры, неправильные кромки или вмятины от повреждений при обработке, которые выглядят непривлекательно или не соответствуют требованиям. Доработка отливок в процессе сварки — это рутинная операция по отделке отливок, которая используется для исправления таких дефектов поверхности отливок почти во всех семействах сплавов и процессах изготовления полостей литейной формы.
Отливка, которая была сварена, смешана и термообработана и прошла все проверки, указанные в чертеже, будет соответствовать требованиям чертежа по размерам, физическим, химическим, металлургическим и структурным параметрам. Поэтому спецификации, ограничивающие или документирующие доработку дефектов поверхности в процессе сварки, редко упоминаются в коммерческих отливках.
Что говорят спецификации
Для военных и аэрокосмических отливок жесткость эксплуатации литых компонентов классифицируется (классы с 1 по 4), а поверхностная и/или внутренняя целостность определяется AMS 2175, классы от A до D. Классы требуют различные уровни неразрушающего контроля и сорта напрямую влияют на допустимое напряжение для циклической жизни. AMS 2175 охватывает почти все процессы литья и весь спектр литейных сплавов, поэтому он также принят в качестве коммерческого стандарта для отливок, критически важных с точки зрения безопасности.
Важно отметить, что в стандарте AMS 2175 ничего не говорится о доработке сварного шва в процессе производства, а указывается только степень несовершенства классов от A до D как «классифицированная» при визуальном, радиографическом, магнитопорошковом или пенетрантном контроле. Это инспекция после завершения всех процессов отливки, включая окончательную термообработку.
По логике вещей, отливки, относящиеся к классам 1 или 2, должны иметь четко определенные спецификации для доработки сварных швов в процессе производства. Такие спецификации и/или примечания к чертежам определяют процессы сварки, присадочные сплавы, подготовку поверхности перед сваркой, квалификацию сварщика, выравнивание поверхности после сварки и термообработку перед сваркой и/или после сварки. Производственная способность этих спецификаций поддерживать характеристики долговечности класса и марки была установлена на основе данных, полученных от OEM-производителей, оборонных предприятий и литейщиков. Некоторые данные были опубликованы, но многие считаются закрытыми и недоступными для широкой публики.
В наиболее ограничивающих спецификациях, обычно AMS-A-21180 и его аналогах ASTM, могут указываться «зоны без сварки» или «в процессе доработки сварного шва только с письменного разрешения покупателя». Могут потребоваться карты с указанием местоположения, размера и глубины сварных швов. Ни один элемент конструкции и, следовательно, никакая конструкционная отливка не подвергается критическим нагрузкам. Этот сценарий, лучше всего представленный спецификацией AMS-A-21180, следует применять только к поверхностям отливок, которые действительно подвергаются критическим нагрузкам.
Другие спецификации дают указания по ремонтной сварке алюминиевых отливок, которые иногда используются. AMS 2694 определяет требования к устранению дефектов в процессе ручной сварки. Несколько спецификаций конкретно относятся к сварке аэрокосмических конструкций, таких как AWS 17.1 и Консультативный циркуляр FAA № 33-6 по ремонту сваркой алюминиевых картеров и цилиндров.
Исследования свойств отливок, отремонтированных сваркой
В раннем исследовании эффективности ремонтной сварки алюминиевой отливки материал A357-T6 и A201-T7, который был приварен на глубину 50% толщины стенки, был повторно термообработаны и испытаны на усталость с надрезом, вязкость разрушения и свойства при растяжении. По сравнению со свойствами основного материала свойства при растяжении сварного материала как A357-T6, так и A201-T7 были очень похожими, а усталость надреза и вязкость разрушения сварного A201-T7 были лучше, чем у основного материала. Усталостные свойства сварного материала A357-T6 показали незначительное ухудшение по сравнению с исходным материалом после 500 000 циклов, а свойства вязкости разрушения сварного материала A357-T6 были аналогичны ударной вязкости основного материала.
Недавнее исследование показало, что правильно выполненная доработка сварных швов в процессе производства практически не повлияла на статические и динамические свойства при растяжении отливок из песчаных форм E357-T6. Эта работа была выполнена с пластиной, отлитой в песчаную форму, с дефектом, обработанным для дублирования полного или частичного ремонта сварного шва. Рисунок 1 иллюстрирует эту концепцию, а в таблице 1 приведены сводные данные по растяжению.
Данные по усталости для трех типов образцов (рис. 1) очень похожи друг на друга. Однако регрессия показывает, что литые (без сварки) образцы немного лучше (более длительный срок службы) при высоких уровнях напряжения, образцы со сплошным сварным швом и без сварки имеют примерно одинаковый срок службы при низких уровнях напряжения, а образцы с половинным сварным швом продемонстрировали самую длительную усталостную прочность. жизнь при низком уровне стресса. Это предполагает либо разницу в микроструктуре, геометрию любых имеющихся пор, либо количество пор, присутствующих в исходной литой структуре металла в зоне сварки. КС
Что происходит во время доработки сварных швов?
Сварка — еще один процесс с расплавленным металлом. Можно определить правильные производственные этапы, а детали будут зависеть от конкретного дефекта. Поставщик, выполняющий операцию, должен выполнить следующие ключевые шаги для получения сварных швов высокого качества
:
- Подготовить зону сварки. Удалите дефект и удалите оксидный слой кистью или растворителем.
- Предварительный нагрев перед сваркой. Предварительный нагрев обычно улучшает результаты сварки. Отливки обычно свариваются в литом состоянии, но иногда дефекты не обнаруживаются до термической обработки, поэтому их сваривают в состоянии Т6 или Т7. Для сплавов серии 200 или для отливок, требующих капитального ремонта, рекомендуется отжигать отливки после отпуска Т6 или Т7 перед сваркой, чтобы избежать растрескивания.
- Используйте сварочный пруток, соответствующий химическому составу отливки, или одобренный заменитель. Химический контроль при сварке так же важен, как и при плавке для литья. Использование стержня общего назначения во всех системах сплавов приведет к уменьшению механических свойств и несоответствию цвета, даже если сварка может быть «легче».
- После сварки шов необходимо зачистить до контура детали. Если ремонт сварного шва заметен при случайном взгляде, ремонт был выполнен неправильно.
- Термическая обработка после сварки. Несмотря на то, что хороший сварной шов будет иметь небольшую пористость и тонкую структуру, механические свойства не будут достигнуты, если отремонтированная отливка не будет подвергнута термической обработке в соответствии со спецификацией.
Термическая обработка также устранит остаточное напряжение, которое могло быть вызвано процессом сварки.
Нажмите здесь , чтобы увидеть эту историю в выпуске Casting Source за март/апрель 2020 года.
алюминиевых сплавов | Алюминиевые отливки
Главная > Металлы и сплавы > Алюминиевые сплавы
Посмотреть галерею
СВЯЗАТЬСЯ С НАМИ
Алюминиевые сплавы — это сплавы, в которых алюминий является преобладающим металлом. Алюминий становится сплавом, когда он сочетается с другими элементами, такими как железо, медь, магний, олово, кремний и цинк. Алюминиевые сплавы доступны в различных формах и классах.
В Deeco Metals мы предлагаем услуги по литью алюминия клиентам в различных отраслях промышленности. Если вам нужна деталь, которая является функциональной, декоративной или и той, и другой, мы можем помочь. Имеем опыт работы с алюминиевыми сплавами всех типов.
Чтобы найти алюминиевый сплав, который вам нужен для вашей детали, обратитесь к таблице ниже. Все еще нужна помощь? Свяжитесь с одним из наших технических торговых представителей. Поговорив с членом нашей команды, вы можете описать свой дизайн и цели вашего проекта. Мы можем помочь вам выбрать алюминиевый сплав, который наилучшим образом удовлетворит ваши потребности.
Типичные алюминиевые сплавы для поковок и штамповок включают, но не ограничиваются:
Формуемость или обрабатываемость | Свариваемость | Механическая обработка | Коррозионная стойкость | Термическая обработка | Прочность | Типичные области применения | |
Сплав 1100 | Отлично | Отлично | Хорошо | Отлично | № | Низкий | Прядение металлов, общее производство |
Сплав 2011 | Хорошо | Бедный | Отлично | Бедный | Да | Высокий | Общая обработка |
Сплав 2024 | Хорошо | Плохо | Ярмарка | Бедный | Да | Высокий | Аэрокосмические приложения |
Сплав 3003 | Отлично | Отлично | Хорошо | Хорошо | № | Средний | Пищевое/химическое оборудование, общее производство |
Сплав 5052 | Хорошо | Хорошо | Ярмарка | Отлично | № | Средний | Морское применение, общее производство |
Сплав 6061 | Хорошо | Хорошо | Хорошо | Отлично | Да | Средний | Применение в строительстве, общее производство |
Сплав 6063 | Хорошо | Хорошо | Ярмарка | Хорошо | Да | Средний | Архитектурные приложения |
Сплав 7075 | Бедный | Бедный | Ярмарка | Средний | Да | Высокий | Аэрокосмические приложения |
Методы литья алюминия
Мы предлагаем различные методы литья, включая:
Литье в песчаные формы
Этот древний метод литья заключается в заливке горячего металла в песчаные формы. Типичные алюминиевые сплавы, используемые для этого метода литья, включают:
- C355.0
- А356.0
- 357,0
- 443,0
- 520,0
- 713,0
Литье по выплавляемым моделям
Литье по выплавляемым моделям происходит при заливке расплавленного металла в расширяемую керамическую форму. Типичные алюминиевые сплавы, используемые для этого метода литья, включают:
- 208,0
- 295,0
- 308,0
- 355,0
- 356,0
- 443,0
- 514,0
- 535,0
- 712,0
Литье под высоким или низким давлением
Этот метод литья включает впрыск жидкого металла в многокомпонентную форму под высоким или низким давлением. Типичные алюминиевые сплавы, используемые для этого метода литья, включают:
- 380,0
- А380.0
- 360,0
- 413,0
- 518,0
Отливки в постоянные формы
Процесс литья в постоянные формы состоит из пяти этапов: подготовка формы, сборка формы, заливка, охлаждение и открытие формы. Типичные алюминиевые сплавы, используемые для этого метода литья, включают:
- 366,0
- 355,0
- С355.0
- А357.0
- 356,0
- А356.0
- B443.0
- 513,0
Алюминиевое литье — эффективный способ изготовления прецизионных деталей. При выборе сплава для алюминиевого литья необходимо учитывать следующие факторы:
- Конструкция литья: Выбор алюминиевого сплава зависит от того, насколько проста или сложна ваша конструкция.
- Предпочтительный процесс литья: Важно выбрать правильный сплав для процесса литья алюминия, который вы собираетесь использовать. Наша команда поможет вам сделать правильный выбор.
- Наличие: Если нужный вам алюминиевый сплав отсутствует, мы можем помочь вам найти сплав с аналогичными свойствами.
- Стоимость: Выбранный вами сплав сильно повлияет на стоимость вашего проекта.
Свяжитесь с Deeco Metals сегодня, чтобы узнать больше о наших доступных сплавах для алюминиевых поковок, алюминиевых экструдированных деталей и алюминиевых отливок.
Посмотреть галерею
Решения для литого алюминия | Прецизионные тепловые компоненты и теплообменники
Cast Aluminium Solutions обслуживает компании по всему миру высокотехнологичными тепловыми продуктами и промышленными компонентами. Наша компания производит продукты, которые помогают спасать жизни, соединять мир, защищать нашу страну и готовить самые популярные блюда в мире.
Наши самые популярные категории продуктов включают проточные нагреватели, циркуляционные нагреватели, нагреватели полупроводниковых плит и вафельных пьедесталов, грили и пароварки для оборудования общественного питания, нагреватели крови и плазмы для медицинских устройств, а также множество нагревателей жидкости высокой чистоты со смачиваемыми поверхностями из нержавеющей стали.
CAS обеспечивает ценность для наших клиентов и партнеров благодаря трем принципам: технический опыт, скорость выхода на рынок и операционное совершенство.
Инженерно-технический опыт является основополагающим компонентом нашего подхода к созданию ценности. Инженерный отдел CAS, состоящий из очень опытной команды инженеров-механиков, инженеров-электриков и теплотехников, использует самые современные технологии проектирования и полностью оборудованную научно-исследовательскую лабораторию для создания первоначальных проектов, проверки их функциональности с помощью компьютерного моделирования. перед изготовлением, а затем, после изготовления опытных образцов, для проверки первых изделий на надежность и работоспособность.
Примеры программного обеспечения для проектирования, используемого нашей командой инженеров, включают приложение для трехмерного автоматизированного проектирования (САПР) Solidworks. Анализ методом конечных элементов (FEA) — еще одно очень важное приложение, используемое инженерами CAS. FEA позволяет инженерам CAS создавать как тепловые, так и структурные модели. Тепловые модели в первую очередь нацелены на (A) обеспечение того, чтобы компонент, изготавливаемый CAS, достиг желаемой целевой температуры (что в конечном итоге гарантирует, что требуемое значение Delta-T или изменение температуры может быть достигнуто, что приводит к надлежащей обработке подложки, жидкости, или рассматриваемый газ), и (B) наши тепловые модели направлены на достижение согласованности по всей поверхности нагретого компонента, который CAS проектирует. Тепловое постоянство, особенно на плоских нагретых поверхностях, может быть так же важно, как и пиковая температура. Инженеры CAS также используют приложения FEA для построения структурных моделей. Структурные модели могут быть связаны с моделированием нагрева, что позволяет техническим специалистам увидеть, как тепло влияет на физические характеристики. Поскольку инженерный отдел CAS стремится к эффективности, у них есть возможность связать свои трехмерные CAD-модели с тепловым и структурным моделированием, поэтому при изменении конструкции они могут автоматически повторно запускать этапы моделирования, связанные с теплопередачей и конструкцией.
.
Основной целью этих обширных этапов моделирования и проектирования является устранение всех и всех конструктивных недостатков до того, как будут созданы прототипы. Некоторые переменные, которые инженеры CAS будут расширять в своих упражнениях по моделированию, включают: форму нагревателя и расходомерной трубки, форму изгиба нагревателя и расходомерной трубки, расположение нагревателя и расходомерной трубки внутри более крупного компонента, мощность нагревателя и рабочую температуру, физическую геометрию нагреваемый компонент и небольшие переменные, такие как рисунок канавок на поверхности, размеры монтажного кронштейна, а также расположение и конструкция любых прикрепленных аксессуаров, термопар, датчиков или электрических корпусов.
Как только наши инженеры прибывают в точку, где тепловая и структурная модели соответствуют желаемым параметрам заказчика, создаются схемы окончательного утверждения и файлы STEP. Если все заинтересованные стороны согласятся со спецификациями проекта, можно будет начать подготовку к созданию прототипов. Это может включать в себя заказ нагревателей, расходомерных трубок, датчиков, компрессионных фитингов и, конечно же, материала подложки. CAS предлагает несколько вариантов подложек, в том числе несколько алюминиевых сплавов, несколько марок нержавеющей стали и специальные металлы, такие как Incalloy, Monel, медь, титан и т. д.
Для литья прототипа CAS предлагает методы литья под наклоном и методы литья под давлением. Оба обеспечивают выдающееся качество продукта, низкую пористость и возможность отливать расходомерные трубки, нагревательные элементы и защитные гильзы в формованный компонент. Варианты литья в песчаные формы также доступны для прототипирования. Если литье для прототипа нежелательно, CAS предлагает нашу запатентованную технологию IFC (конструкция с натягом). С помощью этого метода нагреватели и трубчатые компоненты вставляются в прорезанную канавку на подложке; и IFC может работать с более широким спектром подложек, чем наши процедуры литья.
После успешного изготовления начальных тел для прототипов они могут быть обработаны в одном из многоосевых обрабатывающих центров CAS. Если требуются процедуры сварки или соединения, клиенты могут выбирать из множества вариантов, включая сварку MIG и TIG, вакуумную пайку, электронно-лучевую сварку и многое другое. Если требуется специальная отделка поверхности, CAS также может выполнить это, предложив множество вариантов анодирования, порошкового покрытия и синтетических материалов. Окончательная сборка и очистка обычно идут рука об руку с обработкой поверхности, и они представляют собой последние шаги в создании прототипа.
Когда окончательный прототип будет полностью собран, он будет готов вернуться в руки инженерной группы CAS, и здесь, как и на этапе проектирования, используется ряд передовых технологий. CAS предлагает рентгеновские и ультразвуковые изображения для проверки размещения нагревательных элементов, расходомерных трубок и других компонентов внутри отливки. Расположение расходомерных трубок особенно важно для работы наших циркуляционных нагревателей CAST-X и полупроводниковых пьедесталов, которые могут иметь расходомерные трубки (которые в таких обстоятельствах часто служат для подачи охлаждающей жидкости). Инженеры CAS иногда используют инфракрасные камеры, сопровождаемые обширной регистрацией данных, для проверки термической однородности. Надежность прототипов часто проверяется с помощью нашей испытательной станции жизненного цикла с переменным напряжением. Испытания на утечку гелием также могут быть выполнены в CAS: этот тип испытаний важен для компонентов, устанавливаемых в условиях вакуумной камеры. Для тестирования возможностей нагрева компонентов, предназначенных для установки в вакуумных камерах, лаборатория CAS Research & Development Lab оснащена большой вакуумной камерой, способной вместить полупроводниковые нагреватели и плиты высотой до 450 мм.
Многие задачи, связанные с разработкой и тестированием прототипов, находятся в руках группы разработки новых продуктов CAS. Эта группа включает часть нашего инженерного персонала, а также машинистов, техников и руководителей проектов.
Вторым принципом, который постоянно продвигает CAS вперед, является принцип скорости выхода на рынок. CAS обслуживает ряд высокотехнологичных и экономически динамичных отраслей. В результате наши клиенты, как правило, требуют быстрых оборотов, ускоренной работы и стабильных поставок компонентов следующего поколения в процессе разработки. Одним из основных аспектов бизнеса, которым управляет наша директива о скорости выхода на рынок, является наш производственный отдел, который, по сути, является частью нашего бизнеса, связанной с массовым производством.
Для продуктов, которые находятся в производстве — тех, которые вышли за рамки стадии прототипа и пользуются спросом через заказы от OEM-аккаунтов — очень важно, чтобы продукты разрабатывались, производились, тестировались, упаковывались и отгружались вовремя. Это может показаться простым, но если учесть сложность наших продуктов, множество шагов, необходимых для их создания, и внешние услуги, которые часто вступают в игру, легко понять, что соблюдение сроков требует сложных инструментов отслеживания, отличного управления персоналом. , а также преднамеренное внимание к прогрессу в работе.
Для своевременного выполнения многочисленных этапов сборки и изготовления компания Cast Aluminium Solutions вложила средства в современные машины для литья под давлением, компьютеризированные машины с числовым программным управлением (ЧПУ) и КИМ (координатно-измерительные машины) для размерное тестирование. Эти машины повышают эффективность, скорость и качество нашей работы. В сочетании с нашим хорошо обученным штатом технических специалистов они работают над тем, чтобы наполнить скорость, требуемую нашими клиентами, легендарным качеством, которым славится CAS.
Третьим столпом, на котором стоит CAS, является операционное превосходство. Эта цель может показаться возвышенной, но если ее должным образом претворить в жизнь, она затронет два предыдущих принципа. Операционное совершенство — это и состояние ума, и ряд измеримых шагов, которые необходимо предпринять. Все сотрудники CAS должны придерживаться жесткой программы непрерывного обучения и улучшения процессов. Помимо инвестиций в персонал, мы вложили средства в технологии, улучшающие работу, такие как отслеживание штрих-кодом каждого компонента в инвентаре, система ERP (планирование ресурсов предприятия), которая отслеживает все основные бизнес-функции, облачное управление проектами Smartsheet. система, компьютерные программы, которые связывают инженерные схемы с машинным языком ЧПУ, и элементы управления ПЛК для литейных машин, которые повышают скорость и эффективность нашего основного производственного процесса. Клиенты Cast Aluminium Solutions ожидают этих оперативных услуг, и CAS прилагает все усилия для их предоставления.
Стандартные продукты CAS включают серию циркуляционных нагревателей CAST-X, которая в стандартной версии имеет алюминиевый корпус, и линию циркуляционных нагревателей CAST-X High Temperature с бронзовым корпусом. Другой стандартной линейкой продуктов является наш циркуляционный нагреватель с трубкой из PFA, называемый PUR-X, доступный в двух размерах.
Циркуляционный нагреватель CAST-X представляет собой литой теплообменник шести типоразмеров мощностью от 500 до 60 000 Вт. Циркуляционные нагреватели CAST-X способны нагревать легковоспламеняющиеся жидкости и газы, поскольку вся среда изолирована в расходомерной трубке нагревателя из нержавеющей стали. В циркуляционном нагревателе CAST-X среда никогда не касается нагревательного элемента или любого другого компонента нагревателя. Это важная функция безопасности, но она также является ключевой функцией предотвращения загрязнения. Все расходомерные трубки циркуляционных нагревателей CAST-X также способны работать при высоких рабочих давлениях, что часто имеет значение для систем газового нагрева. Циркуляционные нагреватели CAST-X широко используются на развивающемся рынке природного газа, во многих промышленных приложениях для нагрева газа и криогенных системах фазового перехода жидкость-газ: все эти процессы требуют высокого давления. Общие области применения, ориентированные на жидкости, которые подходят для CAST-X, включают нагревание гликоля, деионизированную воду, различные нефтехимические продукты и растворители для полупроводниковой промышленности.
Cast Aluminium Solutions даже производит вариант CAST-X под названием Universal Solvent Heater, который специально разработан для нагрева растворителей с низкой температурой воспламенения. Для обеспечения безопасного нагрева легковоспламеняющихся сред почти все циркуляционные нагреватели CAST-X доступны во взрывозащищенном электрическом корпусе (NEMA 7 или ATEX), в дополнение к водонепроницаемому (NEMA 4) и корпусу общего назначения (NEMA 1).
Мы обслуживаем множество промышленных и коммерческих секторов, при этом наши основные клиенты находятся в секторе полупроводников и обработки пластин, нефтегазовой промышленности, коммерческом оборудовании для общественного питания, промышленном газовом бизнесе и различных промышленных химических рынках. Циркуляционные нагреватели CAS и встроенные нагреватели, разработанные по индивидуальному заказу, также хорошо подходят для чистки ковров, устройств для мойки деталей, полиграфической и перерабатывающей промышленности, а также для ряда аэрокосмических и оборонных применений. Другие рынки, такие как рынок медицинского оборудования и сектор полупроводников, полагаются на команду разработчиков новых продуктов CAS, которая разрабатывает продукты, отвечающие их потребностям.
Cast Aluminium Solutions обслуживает OEM-производителей и конечных пользователей из нашей штаб-квартиры недалеко от Чикаго и через сеть инженеров по применению, расположенных в Северной Америке, Европе и Азии. Для получения дополнительной информации о Cast Aluminium Solutions (CAS) свяжитесь с нами по электронной почте [email protected] или по телефону 630-879-2696.
В чем разница между экструдированным алюминием и литым алюминием?
Алюминий является чрезвычайно универсальным металлом в том смысле, что он является отличным кандидатом для широкого спектра методов производства, двумя из которых являются экструзия и литье. Вы можете задаться вопросом: «В чем разница между экструзией и литьем алюминия?» Экструзия — это процесс, при котором алюминиевые заготовки продавливают через головку, в результате чего получается желаемое поперечное сечение. Принимая во внимание, что литье – это процесс, при котором расплавленный алюминий заливают в форму, а затем дают затвердеть. Каждый метод изготовления алюминиевых деталей имеет как свои преимущества, так и недостатки, но оба они обеспечивают экономию по сравнению с обработкой детали из твердого тела за счет создания формы, близкой к чистой, и сокращения времени обработки. Независимо от того, считаете ли вы, что вам нужны алюминиевые профили или рассматриваете возможность алюминиевого литья, вы можете рассчитывать на команду Howard Precision Metals, которая укажет вам правильное направление.
Экструзия: экономичный производственный процесс
Экструзия алюминия в целом является конкурентоспособным и экономичным вариантом производства, особенно при работе с очень сложными поперечными сечениями. Новый дизайн алюминиевого профиля нестандартной формы может быть изготовлен всего за 8 недель. Такие формы и элементы, которые могут быть выдавлены, включают в себя: запрессовку и защелку, скользящую посадку, шпунт и паз, отверстия под бобышки для самонарезающих винтов, шарниры, соединения с защелкой, фланцы, резьбовые отверстия, противоскользящие поверхности и многое, многое другое. . Первоначальные затраты на экструзии также привлекательны. Плата за проектирование штампов для новых нестандартных форм намного меньше, чем по сравнению с отливками. Экструдированные алюминиевые профили также производятся с превосходной обработкой поверхности и обычно прочнее по сравнению с ними. Некоторыми продуктами, производимыми методом экструзии, являются радиаторы, оконные и дверные рамы, коллекторы и осветительные приборы. Возможности безграничны. Недостатком экструзии по сравнению с литьем является ограничение по размеру. Алюминиевые профили ограничены как размером заготовки, так и емкостью цилиндра экструзионного пресса.
Отливки не имеют таких ограничений и часто используются для изготовления очень крупных изделий. Даже с учетом ограничений по размеру, присущих экструзии, существует множество областей применения, в которых этот метод производства является предпочтительным.
Литье алюминия
Алюминий можно лить любым доступным методом литья. Некоторыми из этих методов литья являются непрерывное литье, литье по выплавляемым моделям, гипсовое литье, литье в песчаные формы, литье в постоянные формы и литье под давлением. Дополнительные процессы литья, такие как горячее и изостатическое прессование, литье под давлением и литье по выплавляемым моделям, также возможны с расплавленным алюминием. Несмотря на разные названия и методы, все виды литья имеют одну общую черту: расплавленный алюминий заливают в форму, которая образует узор при охлаждении алюминия. По сравнению с экструзией литье — гораздо более медленный процесс. Швы и дефекты формы также могут присутствовать в литых деталях. Для этого часто требуется вторичный процесс, известный как зачистка, для устранения таких дефектов путем резки, шлифовки или шлифования. Тем не менее, литье по-прежнему имеет место в производстве. Литье алюминия является очень распространенным методом производства таких продуктов, как кухонная посуда, компоненты небольших бытовых приборов или декоративные детали. Самый распространенный и крупный рынок алюминиевого литья — автомобильная промышленность. Более половины алюминия, используемого в автомобилях, производится методом литья.
Преимущества и недостатки как литья, так и экструзии алюминия
Процесс литья часто имеет более высокие начальные затраты, чем по сравнению с экструзией. Однако он может быть более экономичным при больших объемах производства или при изготовлении деталей, требующих высокой точности размеров. Это особенно верно, когда формы сложные, например, с неравномерной толщиной. Хотя литье может дать более узкие допуски, экструдированная форма будет прочнее. Кроме того, отливка, скорее всего, будет иметь некоторую пористость, а экструзия ее не имеет. Кроме того, отделка поверхности отливки, вероятно, потребует механической обработки, но поверхность алюминиевого профиля может использоваться в готовой детали при условии, что созданные допуски на размеры соответствуют потребностям детали. Отливки ограничиваются металлами с низкой температурой плавления, такими как алюминий, магний и медь, требуют более высоких первоначальных затрат на оснастку, а срок службы формы может быть коротким. Экструзия является лучшим вариантом при более коротких производственных циклах из-за меньших начальных затрат. Отливки, в отличие от штампованных, не ограничены размерами. Поскольку экструзия может быть такой же большой, как и заготовка, которую может содержать экструзионный пресс, диапазон размеров ограничен. Это не относится к формам для отливок. Фактически, отливки очень часто используются для производства крупных деталей, таких как гребные винты для лодок или детали двигателей.
Для этих продуктов экструзия не подходит из-за ограничений по размеру. Независимо от того, рассматриваете ли вы литье или экструзию, важно учитывать все переменные каждого из них.
Свяжитесь с нами сегодня
С 1928 года команда Howard Precision Metals обеспечивает превосходное обслуживание клиентов в металлургической промышленности. В настоящее время компания Howard Precision Metals является 100% дистрибьютором алюминия и имеет под одной крышей больше пил, чем кто-либо на Среднем Западе, и обладает знаниями и оборудованием, необходимыми для предоставления нашим клиентам самой лучшей доступной продукции. Имея опыт обслуживания широкого спектра отраслей, таких как аэрокосмическая промышленность, машиностроение, производство пневматических и гидравлических цилиндров, наша команда готова выполнить любой запрос на алюминий. Для всех ваших потребностей в алюминии запросите бесплатное предложение на нашем веб-сайте или свяжитесь с нами сегодня по телефону 800.