Большая металлургия – МЕТАЛЛУРГИЯ • Большая российская энциклопедия
alexxlab | 13.10.2020 | 0 | Разное
Металлургия
Слово «металлургия» свои истоки берет из древнегреческого языка, там «μεταλλουργέω» означает в буквальном смысле «добывать руду» или «обрабатывать металлы». Это некая область науки и техники, которая описывает процессы получения металла из руд или различных материалов. Кроме этого, в процессе обработки изменяется химический состав веществ их структура и свойства. Сегодня этими словами называют отрасль промышленности, но раньше это было искусство по извлечению металла из руды.Современное понятие металлургии обширное, к ней можно отнести:
• производство металлов на основе сырья (руды) и других материалов;
• производство сплавов;
• горячая и холодная обработка металлов;
• сварка;
• область науки, которая занимается изучением физических и химических свойств металлов и сплавов;
• производство оборудования и машин для металлургической промышленности.
Коксохимическая промышленность и производство огнеупоров являются отраслями металлургии.
Виды металлургии
Изначально металлургия, по сырьевому признаку, делится на: черную и цветную. К первому виду относят железо и его сплавы, сюда входит: добыча черной руды, обогащение, производство и прокат ферросплавов, стали и чугуна.
Ко второму виду относят, соответственно, цветные металлы: их добычу, обогащение руд, производство металлов и сплавов. Цветные металлы бывают тяжелые (Cu, Zn, Pb, Ni, Sn) и легкие (Al, Ti, Mg).
Кроме сырьевого признака, металлургию можно разделить по технологическому процессу:
1. Пирометаллургия – это такие процессы как обжиг или плавка, которые протекают при высоких температурах. К подвиду подобной металлургии относят плазменную.
2. Гидрометаллургия – абсолютно противоположный процесс, при котором из руд извлекают металл с помощью воды или химических реактивов на ее основе, такой процесс называется «выщелачивание».
Научный прогресс не стоит на месте, в мировой практике в металлургии применяют даже микроорганизмы, биотехнологии. К таким процессам можно отнести: биовыщелачивание, биоокисление и другие. На сегодня таким способом извлекают некоторые цветные металлы (Cu, Au, Zn, Ni, U). Однако, наиболее важным применением биотехнологий является процесс очищения сточных вод на производстве.
Производство металлов и их потребление
Области применения
Немногие ценные металлы содержатся в земной коре в достаточном количестве. Например: Al – 8,9 %, Fe – 4,65 %, Mg – 2,1 %, Ti – 0,63 %. Можно заметить, что чем благороднее металл, тем его меньше содержится в природе.
Потребность и производство металлов с каждым годом растет. Если рассматривать период 20-ти прошедших лет, можно заметить, что потребление (около 0,8 млрд. тонн) и металлофонд (восемь млрд. тон) увеличились.
Конструкции из металла стали наиболее популярными, сферы потребления расширились потому, что данный материал обладает хорошими свойствами, а производство экономически выгодно. 72 – 74 % ВНП многих государств составляет производство, основанное на применение черных и цветных металлов.
750 млн. тонн из 800 млн. тонн, что соответствует 90 % ежегодного потребления металлов, приходится на сталь. Значительно меньше потребляется алюминия – 3 %, меди – 1,5 %, цинка- около 5,5 тонн, свинца – около 4,5 тонн.
США, Китай, Россия, Великобритания, Германия, Украина, Франция, Италия производят и потребляют львиную долю всех металлов.
Различные металлы обладают индивидуальным набором физических свойств, характерных только им. Благодаря таким свойствам, как твердость, плотность, электропроводность, температура плавления, внешний вид и другие, область их применения достаточно широка.
• Высокой твердостью и прочностью обладает железо, в строительной сфере это незаменимые и ценные показатели.
• Из алюминия легко сковать нужную вещь, он отлично проводит тепло и при низкой температуре сохраняет высокую прочность. Поэтому его широко применяют для производства посуды, фольги, даже в самолетостроении.
• Такой дорогой материал, как золото и серебро обладает хорошей тягучестью, вязкостью и инертностью, что помимо ювелирного дела, позволяет применять его при изготовлении неокисляемых электрических соединений.
Применение сплавов
Металлы редко применяют в чистом виде, чаще всего используют сплавы, которые обладают лучшими показателями и характерными свойствами. В производстве популярными являются следующие сплавы: хромовые, алюминиевые, железные, медные, магниевые, никелевые, титановые, цинковые. Если необходимо использовать дешевый материал, с высоким показателем прочности, то применяют углеродистую сталь.
Нержавеющая сталь или оцинковка оказывают сопротивление коррозионному процессу. Если необходим прочный и легкий материал, тогда используют сплавы алюминия и магния.
Сплав из двух металлов: меди и никеля применяют в средах агрессивных к коррозии, для производства ненамагничиваемых изделий. Существуют и так называемые «суперсплавы», изготавливаются на основе никеля. Их особенность – устойчивость к высокой температуре, поэтому они нашли применение в турбонагревателях, теплообменниках и так далее.
Исторические факты
Человечество стало добывать металлы еще в далеком прошлом, об этом свидетельствуют археологические находки и исследования. Медь начали плавить еще в VII—VI тысячелетием до н. э., доказательства этому факту были обнаружены в ходе исследований Малой Азии в 1950-1960 гг. В Сербии были обнаружены следы первой металлургии. Там был найдено множество предметов, одним из которых является топор из меди, дотирующийся 5500 лет до н. э.. Подобные находки были найдены и в Болгарии, Португалии (в Палмеле), Испании, Великобритании (в Стоунхендджи). Находки очень древние и точный возраст предметов не получается определить.
Кроме меди, древние люди применяли: серебреные изделия, оловянные и метеоритное железо. Это позволило развивать металлообработку, особенно наши предки ценили метеорное изделие. Они создавали прочные кинжалы с 3 тысячелетия до н. э. В честь появившегося применения бронзы, был назван целый век – Бронзовый. Это произошло после того как человек стал добывать медь и олово и попробовал сплавить их. Соединение им понравилось и бронзу в 3300 годы до н.э. стали применять повсеместно.
Изготавливалась бронза не сложно, из олова и меди, в результате получался древнейший сплав – оловянная бронза. Из нее делали различные предметы быта и оружия труда.
Чуть позже в это соединение стали добавлять и другие металлы: алюминий, бериллий, кремний, никель. Бронзу изготавливали и без олова, а из меди и цинка, получалась латунь. Сперва из сплавов делали только орудия труда и не значительного оружия. Затем из бронзы стали делать колокола, пушки и прочее. Современная бронза состоит из сплава 5-12% алюминия и железа, марганца, никеля. Сегодня ее называют алюминиевой.
Научившись использовать медь, человечество перешло к изучению железа. О существовании трех веков развития человечества (каменный, бронзовый и железный) упомянуто в общих чертах в античном мире (Тит Лукреций Кар). В середине XIX века датский археолог К. Томсеном ввел в науку понятие «железный век».
Вслед за медью человек стал использовать железо.
Начало железного века положено в в 1200 году до н. э. Считается что сложная технология извлечения железа из руды, а далее выплавка придумана хеттами. Этот факт доказывает найденное упоминание о металле «упавшем с неба» в хеттских текстах XIX века до н. э. Поэтому их считают основателями сложной технологии. Они хранили этот секретный процесс, так как это позволяла держать могущества филистимлян.
Железная колонна в Дели (Кутубская колонна)
История считает, что первое железо было метеоритное, этот факт основан на названии железа, в переводе с древнего языка египтян и греков, дословно «небесное тело», «звезда». «Небесной медью» было названо железо «шумерами. Добывать железо мог не каждый, те, кто это умел и занимался – были на особом месте почета и уважения. Секрет добычи и переработки хранился в строжайшем секрете, некоторые боялись их. На древних фресках их изображали колдунами и магами.
В Европу железный век пришел в X—V веков до н. э., и называется он Гальштатская культура. Название было выбрано не случайно, в Австралии в городишке Гальштат были найдены предметы утвари из железа. Чуть позже в V—II веков до н. э. протекал «Второй железный век» или Латенская культура. Название по местечку в Швейцарии, там было найдено большое количество предметов из железа. Этот период истории тесно связан с кельтами. Они считались мастерами по изготовлению любого железных орудий. ВV веке до н. э. кельты начали переселяться, так применение железа распространилось на территории Западной Европы. Культы называли железо «изарнон», немецы «айзен», а англичане «айрон»..
До Закавказья железо добралось в конце II тысячелетия до н. э.. А в Северном Причерноморье – в VII—I веках до н. э.. здесь проживали скифы, они сформировали развитую культуру получения и применения железа в России и Украине.
Первые монеты, хранившиеся в царских сокровищницах, были изготовлены из железа. Оно было очень дорогим и ценилось. Затем перешли на производство орудий труда и оружия. В «Илиаде» Гомера впервые упоминается об этом. Там сказано, что Ахилл победителей дискобола награждал победителей железным диском. В конструкции храма Артемиды было уже использовано железо. Греки скрепляли мраморные колонные барабаны мраморных колонн. Соединение было при помощи железных штырей, длина которых составляла 130 мм, ширина – 90 мм, а толщина- 15 мм.
Когда в Европу пришли народы с Востока, то металлургия получила новый толчок в развитии. Существует предание, что в Алтайских горах залежи богатых руд, это все богатство монголов и туркменов. Они боготворили ремесленников, работающих с железом. Кочевники из Средней Азии были воинственными, их доспехи и оружие изготавливались из железа. Этот исторический факт свидетельствует об их знаниях в области металлургии.
Знаменитая Кутубская колонна, расположена в Дели является подтверждением факта развития металлургии в древней Индии. Высота 7,5 м, диаметр – 40 см, колонна стоит ровно в вертикальном положении, масса составляет 6 тонн. На колонне имеется надпись, что она изготовлена в 380—330 годах до н. э.. Исследователи древних памятников провели ряд анализов, и был установлен факт: колонна сооружена из отдельных криц, а на кузнечном горне их уже сварили в целое изделие. До сих пор на колонне нет не единого следа ржавчины. Кроме этого памятника истории, о знаниях в области металлургии свидетельствует и оружие, найденное в захоронениях. Его изготовили еще в середине первого тысячелетия до н. э..
Все эти факты истории свидетельствуют о знаниях в области черной металлургии еще в древности, ее развитии. Следы применения железа присутствуют практически в каждой культуре и цивилизации древнего мира. Это и: Империи Востока (Северного и Ближнего), древнего Египта и Турции (в древности Анатолия), Карфаген, Европы, Китая, Индии, Японии и другие древние королевства, средневековые государства. Стоит отметить, что изобретателем различных методов обработки, технологии и оборудование по изготовлению железа были разработаны в древнем Китае, и оттуда ремесленники Европы осваивали такое мастерство как металлургия. К оборудованию и технологиям древней металлургии и разработкам китайцев относят: доменные печи, плавление чугуна, получение стали,гидромолоты и прочее. Однако современные раскопки доказывают, римляне оказались первыми в металлургии и их оборудование и технологии были более продуманными и продвинутыми. Особое мастерство они достигли при добычи руд и ковки.
Добывающая металлургия
Основная суть в добывающей металлургии – это извлечение чистого металла из руд, путем переплавке добытого сырья. Для этого применяют физические, химические или электролитические способы, тогда оксид или сульфат металла превращается в ценный металл, отделившись от руды. Масштабы производства и добычи руды колоссальные. Только в бывшем СССР ежегодно извлекали из земных недр более 1 млрд. тонн руды, это данные за 1980-1990 гг. Сегодня эта цифра значительно выше.
Металлургия включает в себя основные компоненты, с которыми работают металлурги: сырье, концентрат, отходы. К концентрату относят оксид или сульфат, ценный для металла. Руду добывают, а затем измельчают до малейших частиц. Это необходимо, чтобы отделить каждую частицу, так как часть их – это ценный концентрат, или отход.
Есть и другой способ получения ценного металла, если есть условия для проведения выщелачивания. Согласно данному способу, технология следующая: минерал растворяют, в результате получают раствор, обогащенный им.
Чаще всего в руде содержится сразу несколько металлов, тогда производство протекает несколькими этапами. В этом случае, отходы отделенные от руды будут сырьем для другого процесса производства.
Чёрная металлургия
Оксид Fe3O4, Fe2O3, гидроксида Fe2O3*H2O, карбонатов FeCO3 и так далее – в таком виде железо находится в руде. Для того, чтобы получить железо или сплав на его основе, существует производственный процесс, включающий несколько стадий производства (в том числе производство стали и чугуна).
Доменное производство чугуна
Этапы производства:
1. Сплав, содержащий железо высвобождают из руды в специальных доменных печах. Температура при этом процессе более 1000 градусов Цельсия, в это же время происходит выплавка чугуна. От хода процесса зависят и свойства будущего чугуна, и соответственно его вид: передельный чугун и литейный.
2. Из первого в дальнейшем производят выплавку стали, а из второго уже изготавливают отливки. Все эти процессы контролируются доменной печью и могут выставляться при ее настройке.
Производство стали
Как было отмечено ранее, сталь производят из передельного чугуна. Соединив железо с углеродом и легирующим элементом, получают сталь. По своим свойствам, чугун менее прочный сплав, сталь чаще всего применяют в строительных конструкциях, при производстве деталей в машиностроении. Чтобы выплавить сталь, необходима сталеплавильная печь, в ней металл в жидком виде.
Получить сталь можно несколькими способами. Для применения того или иного метода, требуется специальное оборудование: для кислородно-конверторного способа – конвертеры, мартеновского – мартеновские печи, электроплавильного – индукционные печи, дуговые. Это наиболее распространенные методы производства стали.
Кислородно-конвертерный процесс
Данный способ придумал в 1856-1860 гг. англичанин Г. Бессемер. Это был первый способ массового получения стали в жидком состоянии, в результате бессемеровского процесса.
Для этого способа требуется конвертер с кислой футеровкой.
С.Томас в 1878 году разработал процесс схожий со способом Бессемера, однако он применил основную футеровку. В честь основателя способ назван томасовский процесс.
Конвертерный процесс заключается на основе воздушного дутья, в конвертер, так называемый плавильный агрегат, заливают чугун. Его продувают снизу, и кислород окисляет чугунные примеси, превращая их в сталь. В результате томасовского процесса, в основном шлаке удаляют фосфор и серу. Процесс окисления кислородом, нагревает сталь, в результате выделения тепла. Сталь достигает 1600 градусов Цельсия.
Мартеновский процесс
В пламенной отражающей печи находятся регенераторы, они предварительно подогревают воздух или газ. Сущность мартеновского процесса заключается в ведении плавки на поду данной печи. Данный способ разрабатывался многими ученными, загвоздка заключалась в том, что температуры факела была недостаточной. В то время в качестве топлива использовали генераторный газ. Реомюр еще 1722 году упоминал об этой недоработке, он, как и все, искал способ получения жидкой стали. Благодаря предложению братьев Сименсов в 1856 году, Пьер Мартен смог довести данный процесс до конца. Суть идеи братьев заключалась в том, что они предложили использовать тепло отходящих газов, установив в печь генераторы. Газы обеспечивали подогрев воздушных потоков до необходимой температуры плавления. С 8 апреля 1864 года П. Мартен на заводе во Франции внедрил данную печь в производство, получив первую плавку. Эту дату можно считать началом мартеновского процесса.
В печь помещают шихту, которая состоит из металлического лома, чугуна и других компонентов. Тепло, выделяющееся при сжигании топлива, плавит шихту. Далее, добавляют специальные добавки, в результате чего получают металл, необходимого состава и при требуемой температуре. Из печи готовый металл попадает в ковшом, откуда его и разливают. Мартеновскую сталь широко применяют, она обладает хорошими качествами и низкой себестоимостью. На данный способ получения стали, с начала XX века, приходится 50 % от всего производства стали в мире.
В России основателем применения мартеновской печи считают Ивано-Сергеевский железоделательный завод. С.И. Мальцева в 1866-1867 гг. внедрил данную технологию, завод расположен в Калужской губернии. В 1870 г. металлурги Сормовского завода А. А. Износков и Н. Н. Кузнецов увеличили объем печи, она стала вмещать до 2,5 тонн. Это было толчком к дальнейшему развитию металлургии в России, на основе данной печи, русские металлурги, стали изготавливать аналоги и на других заводах.
Мартеновские печи и процесс в целом сыграли большую роль в развитии российской металлургии, в том числе в годы ВОВ. Впервые в мире, советские металлурги в годы войны, на Магнитогорском комбинате и Кузнецовском, удвоили садку стали. Сделав сталь высококачественной для производства брони, подшипников и прочего, на основе мартеновских печей, без особой переналадки. На сегодня большее развитие получили конвертерные и электросталеплавильные способы производства стали, мартеновские печи уходят в прошлое.
По своей сути мартеновские печи универсальны, они позволяют плавить чугун или скрап. При этом содержание и состав сырья не имеет значение, а получать сталь, хорошего качества и необходимого состава. Исключение лишь высоколегированная сталь и сплавы, их можно получить только в электропечах. Необходимый состав металлической шихты находится в прямой зависимости от составляющих компонентов чугуна и скрапа, от соотношения требуемого чугуна к стали, а это зависит от целого ряда условий.
Электросталеплавильное производство
Дуговая сталеплавильная печь
На сегодня для выплавки стали массового производства используют дуговую сталеплавильную электропечь. Работает она за счет переменного тока, в последнее время развитие получили печи индукционные, дуговые, питающиеся постоянным током. Однако их доля, в общем производстве незначительна.
Сталь электропечного сортамента выплавляют в дуговой электропечи переменного тока. Ее преимуществом является возможность выплавки высококачественной легированной и высоколегированной стали. В последние десятилетие это наиболее популярный способ получения подобной стали. В конвертерах и мартеновских печах выплавить легированную сталь затруднительно или невозможно вообще. Это возможно в силу того, что в дуговой печи, есть возможность быстрого нагрева металла, затем можно добавлять легирующие добавки в большом количестве, в это время в печи поддерживается восстановительная атмосфера и безокислительные шлаки. Это и позволяет медленное плавление вводимых элементов. Дополнительным преимуществом, можно считать, то что металл раскисляется более полно, в результате металл содержит меньше оксидных неметаллических добавок. Сталь содержит серы в меньшем количестве, чем при получении ее обычным способом. Электрические дуговые печи позволяют контролировать и изменять температуру металла равномерно, задавая точный температурный режим.
Легирование стали
Когда требуется изменить или добавить свойств стали проводят процесс легирования. В ходе данного процесса, в состав сплава вводят определенные дополнительные элементы в требуемой концентрации, за счет этого изменяется состав стали и его свойства. На свойства стали в процессе легирования, могут повлиять следующие компоненты: хромовые (Cr), никелевые (Ni), марганцевые (Mn), кремниевые (Si), молибденовые (Mo), ванадиевые (V), боровые (B), вольфрамовые (W), титановые (Ti), алюминиевые (Al), медные (Cu), ниобий (Nb), кобальтовые (Co). Такое разнообразие дополнительных веществ и возможность влияния на свойства стали их концентрацией, позволяют производить сталь различных марок с определенным составом легирующих элементов.
Порошковая металлургия
Кардинально отличается от предшествующих выше способов производства – порошковая металлурги. Основная идея заключается в том, что металл используют в виде порошка, размер частиц 0,1 – 0,5 мкм. Частицы черных металлов спрессовывают между собой, и после этого спекают. Таким образом, образуется плотная однородная масса.
Цветная металлургия
Для цветной металлургии характерны разнообразные способы производства. Основных два:
1. Пирометаллургический, он более распространенный в получении многих металлов. Проводится он за счет плавки металлов, восстановительной или окислительной. В данном процессе источник тепла – сера, которая содержится в самой руде. Ее же используют и как химический реактив.
2. Гидрометаллургический, основан на процессе выщелачивания, путем перевода их в растворимые соединения.
Кроме этих двух видов, применяют электролитические процессы. За основу берут водные растворы или расплавленные среды.
Реже применяется металлотермический процесс. В ходе данного способа используют другие металлы, которые в большей степени схожи с кислородом, и на их основе восстанавливают необходимый металл. Существует и ряд других способов, но они не столь распространены: химико-термические, цианирование, хлорид-возгонка.
Как производят медь
Существует 2 способа получения меди, ее получают из руды и концентратов:
1. Гидрометаллургический, малораспространенный способ. В исключительных случаях его применяют, например, если требуется переработать окисленные или самородные руды. Недостатком этого метода является отсутствие возможности попутно извлекать драгоценные металлы.
2. Пирометаллургический, наоборот, делает эту операцию доступной, поэтому его применение более целесообразно. 85-90 % меди производят именно этим способом, получая медь из сульфидной руды. Это довольно сложный процесс, он включает в себя несколько стадий. Основными являются следующие: подготовительный этап, плавка или выплавка медного штейна, получение черной меди за счет конвертирования штейна, рафинирование, производство металла. в первоначальный подготовительный этап входит: обогащение и если требуется обжиг металла. Рафинирование проходит в 2 этапа, первый – огневой, второй – электролитический.
Электролизные ванны на норвежском алюминиевом заводе в городе Мушёэн компании Алкоа
Алюминиевая промышленность
Электролитическим способом получает алюминий, есть и другие способы, но на сегодня он является более современным.
Состоит из двух этапов:
1. Получают глинозем (Аl2O3), основным сырьем является руда,
2. Получают жидкий алюминий. Полученный на первом этапе глинозем путем электролиза выдает в результате – жидкий алюминий.
В мире глинозем на основании способа Байера, получают из бокситов. Байер – австрийский инженер, работал в России. Кроме этого способа, есть и другой способ – получение глинозема из бокситов и нефелинов, то есть способ спекания. Это щелочные методы, за счет которых выделяют глинозем. Дальше растворяют его в электролите и путем электролиза получают алюминий. Электролит состоит из нескольких компонентов, основной – криолит. В идеале Na3AlF6 (3NaF • AlF3) в соотношение с NaF: AlF3 равно 3:1. На электроэнергии можно сэкономить, так как для данного процесса достаточно соотношения 2,6-2,8:1. Для получения такой пропорции, к криолиту добавляется алюминий. Можно также понизить температуру плавления, достаточно в электролит добавлять в небольших количествах CaF2, MgF2 и NaCl. Для промышленного электролита основные компоненты должны быть следующими: Na3AlF6 – 75-90 %; AlF3 – 5-12 %; MgF2 – 2-5 %; CaF2 – 2-4 %; Al2O3 – 2-10 %. При несоблюдении данного соотношения меняются свойства электролита, например, Аl2О3 повысили на более 10 %, сразу же увеличится тугоплавкость. Если снизить содержание ниже 1,3 %, то автоматически режим электролиза нарушается.
Когда из электронной ванны извлекается алюминий, то его называют алюминием-сырцом. Такой элемент содержит в себе металлические и неметаллические примеси, газы. К последним относят: водород, азот, серный и прочие газы. Металлический состав алюминием-сырцом состоит из: Fe, Si, Cu, Zn и прочее. Глинозем, частички футеровок, электролиты, при увлечении их частиц механически, будут относиться к неметаллическим смесям. Могут подвергнуть алюминий и хлорированию, это необходимо для очистки. Очищать металл необходимо от газов Na, Ca, Mg, примесей.
После всех процедур алюминий заливается в электрические печи, которые так же выполняют функцию миксера. Возможно помещение в отражательные печи, алюминий отстаивается 30-45 минут. После данной процедуры, произойдет полная очистка металла от газовых, неметаллических составляющих. Разлитый в разные ванны алюминий соединяют. После этого его разольют на конвейер, получится чушка. На некоторых производствах стоят установки непрерывного литья, тогда алюминий сливают в слитки и получают прокатки. Чистота подобного алюминия выше 99,8 %.
Какими способами производят другие цветные металлы
К другим цветным металлам можно отнести: свинца, олова, цинка, вольфрама и молибдена. Для их производства используют некоторые вышеуказанные способы и методы производства. В целом суть процесса сохраняется, различны реагенты и агрегаты, существуют особенности производства.
metallplace.ru
Металлургия Википедия
Металлу́ргия и металлурги́я[1] (от др.-греч. μεταλλουργέω — добываю руду, обрабатываю металлы) — область науки и техники, охватывающая процессы получения металлов из руд или других видов сырья, а также процессы, связанные с изменением химического состава, структуры и свойств металлических сплавов и производством разнообразных металлических изделий из них. В первоначальном, узком значении — искусство извлечения металлов из руд[2][3]. В настоящее время металлургия является также отраслью промышленности[4][5].
Нужно отметить, что структурные свойства металлических материалов в зависимости от их состава и способов обработки изучаются в рамках металловедения[3]. К металлургии относятся:
К металлургии примыкает разработка, производство и эксплуатация машин, аппаратов, агрегатов, используемых в металлургической промышленности. На условной границе между металлургией и горным делом находятся процессы окускования (подготовка обогащённого сырья к дальнейшей пирометаллургической переработке). С точки зрения академической науки их относят к металлургическим дисциплинам. С металлургией тесно связаны коксохимия, производство огнеупорных материалов, и химия (когда речь идёт о металлургии редкоземельных металлов, например).
Обобщённое название лиц, занятых в металлургии — металлург.
На металлургическом предприятииРазновидности металлургии[ | ]
В мировой практике исторически сложилось деление металлов на чёрные (железо и сплавы на его основе) и все остальные — нечерные (англ.
ru-wiki.ru
БОЛЬШАЯ МЕТАЛЛУРГИЯ. Бардин
БОЛЬШАЯ МЕТАЛЛУРГИЯ
Декабрьской ночью 1934 года Ивана Павловича разбудил телефонный звонок. Его, беспартийного специалиста, приглашали в Москву на заседание Политбюро Центрального Комитета партии, посвященное встрече с металлургами. Он выехал в столицу в то же утро.
Снова, как и пять лет назад, когда он ехал впервые в Кузнецк, мелькали в вагонном окне заснеженные сибирские пейзажи. И вспомнилось академику, как тогда он размечтался о будущем этого края и доказывал своему спутнику:
«Наступление на этот занесенный снегом край мы начнем с запада. Кузнецкий промышленный комплекс явится главнейшим опорным пунктом Урало-Кузнецкого комбината. Одновременно он будет центром тяжелой промышленности в южной части Западной Сибири. Это не прожектерство. Доказательства следующие: Кузнецк — это величайшая в СССР каменноугольная база, железная руда находится здесь на расстоянии ста-трехсот километров. В самом ближайшем будущем надо ожидать открытия новых железорудных месторождений.
На Алтае, в Хакасии и в Горной Шории есть золото, серебро, медь, цинк, свинец; в южной части Западной Сибири есть все необходимое для металлургии, машиностроения и промышленности строительных материалов. Все эти богатства царское правительство, как гоголевский Плюшкин, держало в ледяных подвалах Сибири, обрекая на голод и холод миллионы людей. Теперь все это уже в прошлом. В Сибирь идут большевики. Мощные водяные артерии превратятся в неисчерпаемые источники электроэнергии; лесные массивы вдоль сплавных рек дадут древесину для топлива и лесохимической промышленности.
Сибирский край будет исчерчен стальными линиями железнодорожных путей. Будущий Кузнецкий металлургический завод даст стране столько металла, сколько давали все заводы царской России. В тайге вырастут города. Уголь, металл и вода дадут жизнь краю. К услугам людей появятся новые средства сообщения. В городе заговорит радио, световые рекламы сообщат о театральных постановках и новых фильмах. Металлургический завод, рассчитанный на пятьдесят лет работы, потребует школ и университетов для детей рабочих; здесь будут больницы и дома отдыха, фабрики, здесь расцветет мощный индустриальный край…»
Так писал Бардин в книге «Жизнь инженера».
Да, все, о чем тогда мечтал «академик в полушубке», сбылось! Наша современная действительность уже опередила его мечты. А тогда, в вагоне, Иван Павлович думал еще о том, как быстро изменяется жизнь в стране освобожденного труда. Перед его взором проходили год за годом все семнадцать лет Советской власти. Его, инженера-практика, всегда убеждали факты. А факты жизни были поразительны. Вот они, годы его работы: восстановление разрушенных войной заводов, их реконструкция, затем — пятилетка, строительство Кузнецка — как все преобразилось вокруг!
Летом 1934 года газета «Правда» писала:
«Новокузнецк… — город, фантастически созданный за четыре каких-нибудь года на безотрадном пустыре, где торчали одинокие чахлые кустики. Это город, один из самых младших «октябренков» нашей революции, творение энтузиазма народных масс, создающих свое богатство, свою несокрушимую мощь…»
И в создание всего этого, в сооружение огромного металлургического завода и города в бывшей сибирской глуши вложена доля энтузиазма и труда, частица души и разума академика Ивана Павловича Бардина, бессменного главного инженера Кузнецкстроя.
…К 1936 году Кузнецкий металлургический завод был уже на полном ходу. Были освоены и местные угли, и местные руды. Домны — главная забота Бардина — работали спокойно. Расширялись рудники, продолжал строиться и завод.
Иван Павлович получил высшую награду — увидел воочию результаты своего труда, дело своих рук и разума. На сибирской земле поднялись могучие доменные печи, встали стройные шеренги кауперов, как бы возглавляя цехи — мартеновский, прокатный, коксовый… И все это жило полной жизнью, дышало воздухом, крепко настоянным на сибирском морозе, двигалось, гудело — и давало металл стране, много металла, столь нужного для мирных строек пятилетки и обороны. На Западе и на Дальнем Востоке сгущались тучи новой мировой бойни.
Бардин хорошо ощущал это нарастающее напряжение. И он с еще большей энергией окунался в работу. Быстрее, лучше развивать металлургию, больше дать Родине металла!
В феврале 1936 года он участвовал в конференции металлургов. На ней шел горячий разговор, как улучшить работу домен. Участники конференции говорили о том, что надо уменьшить количество пыли, добиться более ровного хода печей.
Бардин и раньше считал, что подготовка сырья в металлургии — одна из важнейших ее проблем. А теперь он все более и более убеждается, что невозможно успешно развивать производство черных металлов без подготовки сырьевых баз и топлива. Причем особое внимание, считал он, надо обращать на усреднение, дробление, сортировку и окускование железных руд и на обогащение углей для коксования. Но при этом не забывал и о другом: а как развивается металлургия за границей, каких рубежей достигла, что еще можно сделать для повышения производительности наших заводов?
Деятельному и пытливому специалисту недостаточно напечатанных монографий и технических журналов — ему необходимо все увидеть самому, собственными глазами, пощупать руками. И он просит командировать его в США для ознакомления с металлургическими заводами.
Пассажирский лайнер «Бенгалия» доставил Ивана Павловича к тому же берегу, на который он уже высаживался двадцать шесть лет тому назад. Тогда это был бедный искатель счастья. Теперь сюда приехал крупнейший советский металлург, действительный член Академии наук СССР. Приехал знакомиться с передовым техническим опытом, чтобы лучше осуществить свою заветную мечту: советские производственные показатели должны стать значительно выше, чем на заводах Европы и США.
Американские консультанты из «Фрейна», когда уезжали из Советского Союза, обещали Бардину многое. Но теперь они всячески увиливали, и лишь Кениг, бывший когда-то наименее любезным и симпатичным, вдруг помог ему посетить ряд заводов.
В Буффало Иван Павлович познакомился с только что пущенным непрерывным тонколистовым станом и прокаткой жести, а также с другим интересным заводом, на котором в доменном процессе применялась тщательная подготовка и сортировка руд.
Затем он отправился в большую поездку по Штатам. В Чикаго ему удалось посмотреть завод, на котором он когда-то работал. Внешне предприятие мало изменилось, но мощность его значительно возросла, Затем как в калейдоскопе замелькали дорожные впечатления: строительство грандиозной плотины в Колорадо, Сан-Франциско, Лос-Анджелесе, с Технологическим институтом неподалеку. Миннесота, где находилась очень интересная лаборатория по изучению металлургических процессов и обогащению руд. Снова Чикаго, завод «Гэри». А потом — металлургический Питтсбург и юг страны.
В августе 1936 года Бардин возвращался домой на гигантском лайнере — знаменитой «Куин Мери». И первый визит в Москве — к командарму тяжелой промышленности Серго Орджоникидзе. Нарком долго беседовал с Бардиным у себя в кабинете, детально расспрашивал об американских заводах, о работе отдельных цехов и агрегатов. Больше всего его интересовали вопросы производительности труда: почему американцы ухитряются работать с меньшим количеством людей и какие мероприятия нужно провести, чтобы наши заводы укладывались в такие же нормативы. А потом Серго пригласил Ивана Павловича к себе на дачу.
«Приветливо улыбаясь, широко и гостеприимно протягивая обе руки, он встретил меня у себя на даче, — вспоминал впоследствии Бардин. — Он требовал от меня подробного отчета о работе всех заводов, на которых мне удалось побывать в Америке. «Лучше или хуже, чем наши, оборудованы американские заводы, — спрашивал Серго, — чище ли эти заводы, какое количество людей работает на том или ином предприятии, как расставлены люди у агрегатов, какова организация труда, каково качество металла?» Его интересовало все. При упоминании о том, что наши заводы оборудованы не хуже американских, по блеску его глаз было видно, что это ему приятно. Но те же глаза выражали неудовольствие, загорались гневом, когда он узнавал, что некоторые наши заводы грязнее американских, завалены ненужным хламом, загромождены, что очень часто материалы валяются no,v ногами, а в Америке все то, что не относится к работе — весь хлам, мусор, скрап, — убрано в нужное место.
У Серго было горячее желание, чтобы советские заводы были во всех отношениях не только не хуже, а лучше заграничных, чтобы все, что мы строим, было построено красивей, изящней, лучше. Он не мог допустить, чтобы советские заводы были построены хуже заграничных».
С этим был целиком согласен Иван Павлович. И не только согласен — он был горячим поборником и пропагандистом технического прогресса в нашей стране, активным борцом за его осуществление. После встречи с Орджоникидзе он отправился в Днепропетровск и Днепродзержинск, где сделал доклады о своих заграничных впечатлениях. Затем такой же доклад — в Кузнецке и статьи по этому вопросу. Металлурги страны должны знать все лучшее из зарубежного опыта и быстрее внедрять его у себя!
В то время Иван Павлович начинает чувствовать, что рамки главного инженера Кузнецкого завода становятся ему уже тесноваты. Его опыт, знания, его организаторские способности могут принести значительно больше пользы стране, если будут использованы в более широких масштабах. Но он продолжает трудиться на Кузнецком заводе, мечтает о его расширении и совершенствовании. К этому периоду относятся и его первые наметки об интенсификации металлургических процессов, об их ускорении.
В 1937 году Бардина вызывают в Москву и назначают главным инженером ГУМПа (Главного управления металлургической промышленности) Наркомтяжпрома. Иван Павлович с удовлетворением принял новое назначение. Оно открывало перед ним заманчивую перспективу — применить свои технические идеи в масштабе всей страны.
С первых же шагов он активно принимается за решение сложных вопросов, например, участвует в заседаниях по проблеме изготовления специальных сталей и лучшего использования ванадиевых и титано-магнетитовых руд. Многое здесь Иван Павлович почерпнул из знакомства с научно-исследовательскими работами, которые велись по этим процессам. Уже тогда он почувствовал и понял, как необходимы нашей металлургий крупные научно-исследовательские центры. Без серьезных, хорошо спланированных и организованных исследовательских работ двигаться дальше нельзя.
Это было тем более необходимо, что, по мнению Бардина, наша металлургия в то время несколько замедлила темпы своего развития, особенно до наращиванию мощностей и по обеспечению производства сырьем и топливом. Особое внимание главному инженеру главка приходилось уделять рудникам — тут было еще много незавершенных работ, реконструкция и расширение велись медленно. Вот почему в конце 1937 года Иван Павлович решил съездить в Кривой Рог, чтобы самому познакомиться с положением дел.
Последний раз в Кривом Роге Иван Павлович был чуть ли не в 1910 году, еще в студенческие годы. Сейчас ян увидел вполне современный рудничный район с крупными механизированными шахтами, оборудованными сортировочными устройствами и бункерами. Но тут же его опытный глаз отметил, что склады руды очень небольшие, достаточных запасов нет, а добыча ведется в обрез. Все, как говорится, бралось с колес. Вот, значит, почему постоянно лихорадит заводы — нехватка запасов сырья! К тому же руды бедны и неоднородны из-за того, что нет запасов и нет времени подбирать и складывать их по сортам. Да, думал Иван Павлович, надо решительно кончать с этой старой привычкой работать «с колес».
Тут же, в Кривом Роге, Бардин отметил очень интересное начинание, которое должно было помочь наладить работу рудников, — организацию института по обогащению бедных кварцитов. Иван Павлович одобрил это нужное дело и в дальнейшем всемерно поддерживал его. К сожалению, война помешала завершить исследования.
После Кривого Рога Бардин заглянул на свой родной завод имени Дзержинского. И здесь все изменилось — выросли еще две мощные домны, давали кокс коксовые батареи, начиналось строительство большого коксового и азотнотукового заводов, появились новые мартены и универсальный прокатный стан. Вид старого детища значительно поднял настроение главного инженера главка.
Дел в новой должности было очень много. Надо было продумать доклад правительству о состоянии металлургической промышленности и о том, что надо делать для ее улучшения. Надо убеждать в важности и необходимости листопрокатки и в том, что строительство корпусов железнодорожных вагонов из фасонного металла — отсталая техника. Необходимо пересмотреть проекты заводов.
При этом Иван Павлович очень решительно отстаивал свою точку зрения: когда строится комплексный металлургический комбинат, он должен обязательно быть привязан к строительству машиностроительных заводов.
А затем снова поездка. На этот раз — в Магнитогорск для наладки производства проволоки. Заодно Иван Павлович посетил и многие другие уральские заводы в Нижнем Тагиле, Чусовой, Сатке, Серове… Знакомство с уральской металлургией на этот раз было капитальным. Оно очень помогло Бардину в руководстве Уральским филиалом Академии наук СССР и впоследствии, в годы Великой Отечественной войны, когда он работал в Комиссии по мобилизации ресурсов Урала на нужды обороны.
Настройка проволочного стана на Магнитке оказалась делом длительным и трудным. Это был новый скоростной непрерывный стан, который требовал совершенно новых приемов в работе. Его часто приходилось останавливать, и Иван Павлович в это время летал на самолете в Свердловск, где осматривал близлежащие заводы и занимался Уральским филиалом Академии наук, одним из организаторов и председателем которого он был. В филиале была создана отличная лаборатория по металлургии, и Бардин имел возможность исследовать здесь многие важные для уральцев (да и не только для них) проблемы.
Один такой полет чуть было не закончился трагически. Маленький самолет в тумане сделал вынужденную посадку. Иван Павлович получил сильные ушибы. Пришлось несколько дней отлеживаться. Однако дела не ждали, и Бардин снова до позднего вечера находится в цехе, следит за наладкой стана, дает советы, что-то предлагает, изменяет. Наконец новый стан начинает ритмично выдавать продукцию, и академик может уехать.
Сколько в его жизни было таких случаев, когда он сам непосредственно руководил вводом в действие крупнейших металлургических агрегатов — домен, мартенов, станов, цехов и заводов! Многие (если не большинство) металлургические предприятия нашей страны видели в своих цехах Бардина. Его хорошо знали, глубоко уважали и рабочие, и инженеры, и ученые. Шли к нему за советами, консультацией. Он ехал в Сибирь, на Урал, в Донбасс, дневал и ночевал в жарких цехах, у горячего металла.
В конце 1938 года в жизни академика произошло очень важное событие: его выдвинули кандидатом в депутаты Верховного Совета СССР от Томского сельского избирательного округа. По своей обычной скромности Иван Павлович никак не ожидал, что ему окажут такое огромное доверие. Он по-прежнему считал себя только инженером-металлургом, хотя стал, по существу, техническим руководителем советской металлургии и вел огромную научную работу в академии. Советские люди к тому же знали его как прославленного строителя Кузнецкого гиганта.
По-прежнему главное внимание Ивана Павловича занимают вопросы производительности металлургических заводов, интенсификация всех процессов. С этим связано и дальнейшее наращивание мощностей в металлургии. Бардин принимает активное участие в разработке третьего пятилетнего плана по разделу черной металлургии, причем особое внимание уделяет изготовлению специальных сталей. Это направление вполне понятно. В Европе и на Дальнем Востоке в это время уже бушевало пламя второй мировой войны. Страна наша все наращивала темпы, готовилась к обороне. А для военной техники нужны в первую очередь специальные стали.
В тот год в Харькове было созвано совещание сталеплавильщиков. Основной вопрос: как ускорить плавки, дать больше металла? Группа работников из Днепропетровска предлагала увеличить подачу горючего и глубину ванн в мартенах и, таким образом, получать больше стали с квадратного метра пода печи в час. Им возражали многие металлурги.
Для Бардина было ясно одно: необходимо достигнуть на мартенах наивысшей производительности. А для этого хороши все средства, включая и такое, как увеличение подачи горючего в рабочую камеру печи и наилучшее ее использование. Вот почему он согласился на предложение днепропетровцев. С точки зрения старых теорий это ухудшало металл, удлиняло плавку. Но Иван Павлович считал, что это неверно. Главная беда неудовлетворительной работы мартенов, по его мнению, заключалась в другом: в плохих огнеупорах, в недостаточных калорийности газов и подаче воздуха, в слабой автоматизации. И действительно, когда все это устранялось, глубина ванны, установленная по решению Бардина, оказывалась вполне пригодной.
Дел у Ивана Павловича теперь заметно прибавилось: нужно было участвовать в предвыборных собраниях, познакомиться с избирателями и представиться им. И он снова едет в Сибирь. По дороге побывал на Кузнецком заводе, в сельских районах Западной Сибири и, наконец, на Петровско-Забайкальском заводе. Там и застали его выборы.
Итак, он стал членом Советского парламента. Чувство гордости за оказанное ему доверие охватило Бардина. С чего он начинал и к чему пришел? Сын скромного сельского ремесленника, рабочий с дипломом инженера на американском заводе, главный инженер одного из крупнейших металлургических заводов Юга в царской России, в условиях засилья иностранцев, борьба за оживление замерзших в гражданскую войну предприятий, строительство металлургического гиганта в глухом сибирском углу, академик и крупнейший инженер-металлург. А теперь вот — народный избранник!
С этого времени Бардин заседал в верховном органе власти Советской страны. Больше двадцати лет он так же добросовестно, внимательно выполнял свои депутатские обязанности, как трудился в металлургии. Не жалел сил, чтобы оправдать доверие избравшего его народа.
…В 1939 году был создан Народный комиссариат черной металлургии СССР. Бардин назначается заместителем наркома. На его попечении и здесь — техническая политика в металлургии, но теперь уже в значительно возросших масштабах.
В это время Иван Павлович особое внимание уделяет научной работе. Он всегда считал, что нельзя развивать металлургию, не имея твердого научного обоснования процессов. Вообще одним из методов его работы всегда было тщательное изучение какого-либо вопроса, научное исследование его, поиски теоретических основ. И только после того, как он был глубоко убежден в чем-то, Бардин принимал окончательное решение. И одним из первых его шагов была организация лабораторий для исследований.
Так и теперь: он ясно видел, что развивать дальше металлургию страны без научной базы нельзя. Невозможно улучшать производство, не применяя в металлургических процессах достижений физики и химии. Жизнь настоятельно требовала, чтобы на основе физико-химических и термодинамических исследований реакций между металлом и шлаком революционизировать процессы выплавки стали. Надо было разрабатывать новые, более совершенные методы контроля металла и интенсифицировать технологические процессы.
Высококачественные сплавы — база развития новейшей техники. Но нельзя было получить качественные сплавы только в результате множества проводимых вслепую экспериментов. Необходимо разработать их теоретические основы, для чего надо изучать механизм упрочнения сплавов, теории деформации, дислокации и скольжения. Короче говоря, надо создавать теорию металлургических процессов — металлургическую науку.
Такова была основная, ведущая идея деятельности И. П. Бардина, начиная с того времени. И, как всегда уверившись, что эта идея плодотворна и необходима, он тут же приступил к ее практическому осуществлению. По его инициативе и под его руководством организуется Институт металлургии Академии наук СССР (впоследствии ему было присвоено имя известного металлурга академика А. А. Байкова). Одновременно, как заместитель наркома и директор института, Иван Павлович руководил и Центральным научно-исследовательским институтом черной металлургии (теперь — имени И. П. Бардина).
Он был убежден, что научные исследования вызываются практическими потребностями производства. Но в то же время постоянно подчеркивал, что невозможно добиться революционных сдвигов в технике без глубокого проникновения в тайны природы. Отсюда и те конкретные задачи, которые он всегда ставил перед руководимыми им научными учреждениями.
Бардин считал, что металлургия как наука должна встать в один ряд с другими теоретическими областями знания. «Для того чтобы новейшая физика и химия раздвинули горизонты металлургии, — писал он впоследствии, — необходима большая научно-исследовательская работа по приложению данных современных физических теорий к наукам о металлах и сплавах. Физика должна быть переработана в физику металлов, химия — в химию металлов, теория твердого тела — в науку о пластической деформации металла и т. д. Лишь после этого создадутся контакты: линии переходов от теоретической физики и химии к практической металлургии. Этот мост должны создавать институты технических наук в системе Академии наук (металлургия берется здесь лишь как пример). Итоги их работы должны далее усваиваться и применяться к решению производственных задач в многочисленных отраслевых научно-исследовательских институтах, заводских лабораториях или институтах при крупных заводах».
Это было написано через 20 лет после организации им научной базы металлургии. Но и тогда, в 1939 году, он уже придерживался этих положений. При этом он считал еще, что институты технических наук должны заниматься также разработкой новых технологических процессов и первичным исследованием новых сырьевых материалов, а затем активно участвовать в промышленной проверке и доработке этих процессов. Кроме того, «в небольшой степени они (эти институты) должны заниматься также и совершенствованием существующих технологических процессов в порядке применения возникающих на базе теоретического анализа идей к существующим процессам. Но эта сторона дела является как бы и побочным производством в работе академических институтов технических наук».
И перед теоретическими и перед отраслевыми институтами Бардин всегда стремился поставить четко разграниченные, но достаточно глубокие задачи. При этом он прекрасно понимал, какое значение в комплексе исследовательских работ имеет хорошая организация, координация, руководство делом и оснащенность оборудованием.
«Весь комплекс научно-исследовательских институтов и заводских лабораторий в целом, — говорил он, — представляет производственный организм, работа которого зависит, с одной стороны, от того, как им руководят, а с другой стороны, как он вооружен и как он работает.
Используя исследовательские институты и заводские лаборатории, нужно знать, что следует передать для разработки институту, что дать заводской лаборатории и что следует решать в техническом отделе министерства, предприятия или в проектной организации.
Если к организации научных и технических работ подходить без соответствующего правильного разграничения их задач, то мы будем иметь слабую производительность институтов в целом и научных сил, которые обслуживают институты, в частности».
Таковы в весьма общих чертах те взгляды и установки в организации научных работ, которыми руководствовался в своей деятельности И. П. Бардин еще тогда, в 1939 году, и впоследствии, когда стал вице-президентом Академии наук, одним из организаторов и руководителей советской науки.
Не забывал он в то время и о своих обязанностях в Уральском филиале Академии. Ведь «без филиалов, — считал всегда Бардин, — Академия наук будет иметь неполное представление о том, где и что должно быть предпринято в первую очередь для освоения природных ресурсов нашей Родины. Филиалы это разведчики наших богатств на необозримой территории Советского Союза». И он всю деятельность филиала направил на выявление природных ресурсов Урала. Достаточно вспомнить такие его работы этого периода, как «Важнейшие проблемы Урала», «К общей постановке проблемы» в книге «Орско-Халиловская проблема», «Задачи черной металлургии Урала», чтобы понять, сколько внимания и сил Иван Павлович уделял Уралу.
О широте его научных интересов, об огромном диапазоне работы свидетельствуют и другие труды академика в это время. Он занимался сложнейшей проблемой низколегированных, антикоррозийных сталей и другими вопросами качественной металлургии (его работы: «Черная металлургия», «Низколегированные, антикоррозийные стали», «Основные вопросы качественной металлургии» и др.), организацией и планированием общих проблем металлургии («Черная металлургия в третьем пятилетии». «Пути советской металлургии», «Металлургия СССР в третьей пятилетке великих работ», «Новая технология черной металлургии в третьей пятилетке»), организацией металлургической науки и техники («Упорядочить дело стандартизации и нормализации», «Расширить исследовательские работы заводских лабораторий черной металлургии» и др.).
И при всем этом, при своей огромной занятости в Наркомате, в Академии наук, в институтах Бардин находил время для популяризации знаний среди молодежи, для того, чтобы поделиться с ней своим огромным опытов. Он написал книгу «Жизнь инженера» для «Молодой гвардии», статью «Металл» в журнале «Техника — молодежи», предисловие к вышедшей в серии «Жизнь замечательных людей» книге о Курако.
К этому особенно наполненному разнообразной кипучей деятельностью периоду жизни Ивана Павловича относится и событие, которое началось очень буднично, развивалось сначала незаметно, а потом под руководством и при участии Бардина выросло в крупнейшую проблему металлургии.
Как-то к заместителю наркома пришел на прием инженер Мозговой.
— Мы с вами, Иван Павлович, — сказал он, — учились у одного и того же профессора — Василия Петровича Ижевского.
— Да, — ответил Бардин, — Василий Петрович был моим учителем.
— А я пришел к вам с одной идеей, — продолжал Мозговой, — продувать жидкий чугун технически чистым кислородом для получения стали. Я уже проводил опыты на заводе…
Бардин внимательно выслушал, в чем заключаются опыты, и решил заняться этим вопросом. В 1940 году эта работа проводилась в Экспериментальном научно-исследовательском институте металлорежущих станков (ЭНИМСе). Установка была примитивная, но для Ивана Павловича несомненно было одно: металл получается, и притом высокого качества.
При Бардине было проведено две плавки, на основании чего он написал два письма в правительство, в которых говорил о перспективах этого метода и просил разрешения на строительство экспериментального завода. Затем, видя, что Мозговой ведет работу один, Иван Павлович рекомендовал ему в помощь своего старого сотрудника, опытного инженера Голдобина.
Начавшаяся война заставила экспериментаторов продолжить свои работы на Урале. Но там не хватало кислорода. И лишь впоследствии появилась возможность построить достаточно мощную кислородную станцию. В 1945 году Иван Павлович возглавил работы по применению кислорода в черной металлургии. Но возвратимся к 1940 году.
В этом году Ивана Павловича ждала новая работа. Как крупнейшего специалиста, его пригласили быть советником правительства членом совета по металлургии и химии Совнаркома.
Первый вопрос, который был задан новому члену совета: почему в металлургии темпы снижаются? Бардин достаточно хорошо знал положение дел и ответил: из-за отсутствия хорошо подготовленного сырья, неоднородности материалов на складах заводов и рудников и из-за неотрегулированной системы зарплаты. В результате были проведены мероприятия по накоплению запасов сырья и изменена система оплаты работников заводов.
Со второй половины сорокового года дела в металлургии пошли лучше. Иван Павлович в это время занялся вопросами энергетики для металлургии. Изучая подбор топлива, обеспеченность нефтью, он также составил различные предложения по подготовке руд и обстоятельные записки о строительстве агломерационных машин на заводах (агломерация — спекание мелкой руды в куски для последующей плавки).
Часто Бардин включался в работу Наркомата черной металлургии, помогал решать практические задачи на заводах. Одновременно продолжал вести научную работу, особенно по подготовке сырья.
К этому времени относится начало еще одной выдающейся научной работы И. П. Бардина. В его кабинете проходили первые совещания по непрерывной разливке стали. Идея эта давно занимала Ивана Павловича, и вот в 1940 году он собрал специалистов, чтобы посоветоваться, какой метод и как применять.
Так трудился Иван Павлович в самый канун войны. Он отдал много сил, чтобы развить нашу металлургию, вывести ее на передовые рубежи технического прогресса, создать для нее научную базу. И в том, что советские металлурги сумели в годы кровавой битвы с фашизмом обеспечить наших воинов металлом, есть немалая заслуга Ивана Павловича Бардина. Это и строительство Кузнецкого завода, который в войну стал одной из основных баз снабжения металлом, это и изучение природных ресурсов Урала, и внедрение в металлургию новой технологии, и создание ее научной базы, и деятельность его как заместителя наркома…
Многие важнейшие начинания Ивана Павловича — такие, как кислородная проблема, непрерывная разливка стали, — были задержаны войной. Но впоследствии они получили свое дальнейшее плодотворное развитие.
Поделитесь на страничкеСледующая глава >
biography.wikireading.ru
Главные страны производители черной и цветной металлургии
Производство черных и цветных металлов издавна занимало одну из главных промышленных областей. Благодаря металлургии люди обеспечены материалами, служащими для сооружения различных конструкций во многих технологических сферах. До 70-х годов прошлого столетия металлургическая промышленность развивалась с ускоренными темпами, но затем наступило некоторое снижение активности, связанное с уменьшением производственных металлоемкостей. На сегодняшний день металлургия взяла курс развития в следующих направлениях:
- нацеленность на потребительские запросы;
- повышенный интерес в развитии транспортных путей вместо экспорта сырья.
- предпочтение развитию предприятий с малыми и средними мощностями;
- уклон на развитие отрасли в развивающихся государствах.
Металлургическая отрасль подразделяется на производство черных и цветных металлов.
Развитие чёрной металлургии в мире
Черная металлургия подразумевает следующие этапы:
- разработка рудных месторождений;
- сырьевая подготовка;
- выплавка таких материалов, как чугун, сталь, прокат и ферросплавы.
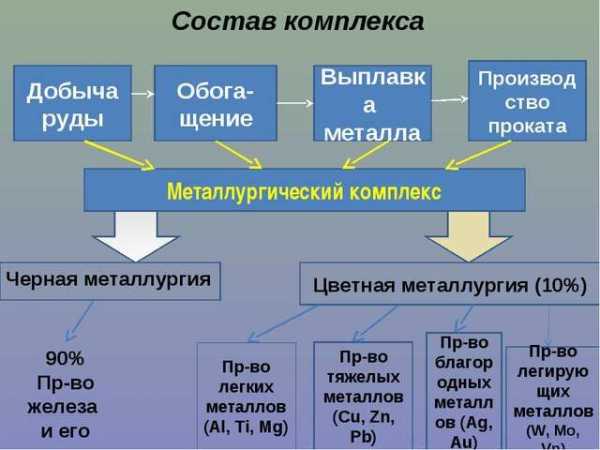
Этапы черной металлургии
Черная металлургия использует в качестве базового исходного сырья руду с содержанием таких металлов как железо, хром и марганец. Помимо этого, многие предприятия работают со вторсырьем, таким как амортизационный лом и отходы металлургии.
Использование лома позволяет значительно удешевить производство, поскольку пропускается этап литья чугуна, и сразу идет процесс получения стали. В качестве топлива для чугунного производства используется коксующийся уголь.
Черная металлургия полного цикла в каждой стадии выпускает свой продукт. В зависимости от этого существует несколько видов предприятий, таких как:
- заводы малых мощностей;
- предприятия передельной металлургии;
- полноцикличные комбинаты;
- предприятия по получению ферросплавов;
- электросталеплавильные заводы.
В соответствии с расположением каменноугольных или железорудных бассейнов черная металлургия зачастую была непостоянна в своей локализации. В нынешний период научно-технического прорыва ориентиры сместились в сторону топливно-сырьевых грузопотоков.
Благодаря этому размеры строящихся предприятий уменьшаются, а их географическое расположение не зависит от месторождений. Например, металлургические комбинаты западноевропейских стран и Японии теперь располагаются в районах с выходом в морской порт.
Главные страны в добыче железной руды
Месторождения разрабатывают разные страны, лидеры по производству, тем не менее, далеко не все. До 40-х годов прошлого столетия основные разработки железорудных месторождений проводились Германией, Францией, США, Великобританией и Швецией. В послевоенные годы эти страны уступили свое первенство ЮАР, Австралии, Канаде и СССР. Сегодня ситуация несколько поменялась, и в этой области лидируют следующие страны:
- Китай;
- Бразилия;
- Индия;
- СНГ;
- Австралия.
Больше 40 государств в мире занимаются разработкой месторождений руды, а общее количество добытого полезного ископаемого составляет почти 1 млрд т. Примерно 70% от общей добытой руды приходится на такие государства, как Китай (23%), Бразилия (17%), Австралия (13%), Россия (9%), Индия (8%).
Несмотря на внушительные объемы, далеко не все из этих стран экспортируют данный вид сырья. Австралия и Бразилия — важнейшие экспортеры, которые обеспечивают больше половины мирового экспорта.
Некоторые государства, экспортирующие железорудные ресурсы, занимаются и ее импортом. К таким странам относятся Китай, США, Италия и Великобритания, поскольку на их территории находятся полноцикличные предприятия, отличающиеся повышенной производственной материалоемкостью.
В этом случае расход используемого сырья и топлива превосходит количество полученного чугуна в 4–5 раз по массе. Особенно значительны затраты на железную руды по сравнению с коксующимся углем.
По этой причине самым экономически выгодным местом расположения полноцикличных комбинатов являются территории, богатые сырьем и топливом одновременно. Представителями таких государств являются Украина, Индия, Китай, Австралия. В остальных случаях центры черной металлургии возникли рядом с железорудными или каменноугольными месторождениями.
Локализация металлургических центров в приморских зонах дает альтернативу в качестве морских поставок угля и железной руды. Порой эксплуатация импортного сырья и топлива является более прибыльной, чем разработка собственных месторождений.
В частности, Индия и Латинская Америка перевозят по морю железорудное сырье на прибрежные заводы Японии, а Австралия и КНР — энергетическое сырье. В государства ЕС уголь поставляется таким же образом из США, а руда поставляется Бразилией и ЮАР.
Производство чугуна
Основной промежуточный продукт в процессе производства черных металлов — чугун, посредством которого получают 50% общей стали в мире. В последнее время объемы чугунной промышленности медленно снижаются, поскольку это экономически невыгодно и загрязняет атмосферу. С начала 90-х годов прошлого столетия лидирующую позицию в чугунном производстве занимает Китай, до этого первенство было у СССР.
Лидирующие в производстве стали
Сталеплавильное производство считается важным процессом в черной металлургии.
Обычно чугун поставляется в роли первичного сырья для получения стали, но все чаще доменное производство заменяется на использование вторсырья в виде металлического лома. Благодаря научно-технической революции современные технологии практически вытеснили прежние способы получения стали.
Электротермический и кислородно-конвертный способы затрачивают меньше ресурсов, сокращают энергозатраты и длительность выплавки. Новая методика получения стали путем переработки металлизированных окатышей позволила отказаться от классического чугунного производства и сооружать сталеплавильные заводы вне зависимости от расположения железорудных месторождений.
Главными странами-производителями черной металлургии являются:
- КНР;
- Япония;
- США;
- Российская Федерация;
- Германия;
- Южная Корея;
- Бразилия;
- Индия;
- Италия.
Прокатное производство
Самым востребованным товаром в производстве черных металлов является прокат, представляющий конечный продукт полного цикла. Сталь стоит в несколько раз меньше проката, из которого производится около 30 тыс. видов изделий в смежных промышленных областях.
Перечень государств, выпускающих качественный прокат:
- Япония;
- США;
- страны ЕС.
Лидирующие в производстве цветных металлов страны
Цветная металлургия подразделяется на две крупные отрасли: тяжелую (производство Pb, Cu, Zn, Sn, Ni) и легкую (производство Al, Mg, Co, Ti, Li, Be и других металлов). По своим производственным масштабам металлургия черных металлов превосходит цветные приблизительно в 20 раз.
Обычно комбинаты цветной металлургии сооружаются в зависимости от локализации месторождений, поскольку количество ценного металла в руде незначительное.
Другие факторы, влияющие на локализацию заводов цветной металлургии:
- энергетический;
- потребительский;
- транспортный.
Начальные производственные стадии меди, подразумевающие добычу и обогащение руды, локализованы в странах третьего мира. Государства, не обладающие большими медными запасами, ориентированы на окончательные продукты производственного цикла.
Лидирующие позиции в получении меди занимают следующие страны:
- Чили;
- США;
- Индонезия;
- Канада;
- Россия.
Перевозка алюминиевой руды более рентабельна, чем сырья для тяжелых металлов, поскольку содержание алюминия в бокситах составляет около 50%. Суммарное расстояние транспортировки бокситов по морю составляет больше 7 тыс. км, поскольку основные их месторождения расположены в регионах с тропическим и субтропическим климатом.
Государства, добывающие самые большие объемы алюминиевой руды:
- Австралия;
- Гвинея;
- Ямайка;
- Бразилия.
В алюминиевом производстве первенство занимают США, Германия, Япония, Норвегия, Россия, Канада.
Видео по теме:
Металлургическая промышленность
promzn.ru
МЕТАЛЛУРГИЯ – это… Что такое МЕТАЛЛУРГИЯ?
МЕТАЛЛУРГИЯ — греч., от metallon, металл, и ergon, труд. Наука о способах добывания и обработки металлов. Объяснение 25000 иностранных слов, вошедших в употребление в русский язык, с означением их корней. Михельсон А.Д., 1865. МЕТАЛЛУРГИЯ наука о способах… … Словарь иностранных слов русского языка
МЕТАЛЛУРГИЯ — (от греч. metallurgeo добываю руду обрабатываю металлы), область науки и техники и отрасль промышленности, охватывающие процессы получения металлов из руд или др. материалов, изменения химического состава, структуры и свойств металлических… … Большой Энциклопедический словарь
Металлургия — отрасль тяжелой промышленности, охватывающая процессы получения (выплавки) металлов из руд и других материалов, производства сплавов, придания нужной формы металлическим заготовкам путем обработки их давлением. Традиционно металлургия… … Финансовый словарь
металлургия — Наука о металлах и сплавах. Металлургия процессов имеет отношение к извлечению металлов из их руд и их очистке. Физическая металлургия работает с физическими и механическими свойствами металлов в соответствии с их соединением, обработкой и… … Справочник технического переводчика
МЕТАЛЛУРГИЯ — МЕТАЛЛУРГИЯ, область науки и техники, а также отрасль промышленности, занимающаяся МЕТАЛЛАМИ. Металлургия включает изучение методов выделения металлов из их РУД; физических и химических свойств металлов; производство СПЛАВОВ; закалку и упрочнение … Научно-технический энциклопедический словарь
МЕТАЛЛУРГИЯ — МЕТАЛЛУРГИЯ, и и МЕТАЛЛУРГИЯ, и, жен. 1. Наука о промышленных способах производства металлов и сплавов и их первичной обработке. 2. Промышленное производство металлов и сплавов, их механическая и химическая обработка. М. сплавов. Порошковая м.… … Толковый словарь Ожегова
МЕТАЛЛУРГИЯ — МЕТАЛЛУРГИЯ, и и МЕТАЛЛУРГИЯ, и, жен. 1. Наука о промышленных способах производства металлов и сплавов и их первичной обработке. 2. Промышленное производство металлов и сплавов, их механическая и химическая обработка. М. сплавов. Порошковая м.… … Толковый словарь Ожегова
металлургия — (горячий, огненный) цех Словарь русских синонимов. металлургия сущ., кол во синонимов: 5 • гидрометаллургия (1) • … Словарь синонимов
металлургия — и металлургия … Словарь трудностей произношения и ударения в современном русском языке
металлургия — комбинаты. Металл өндіретін және өңдейтін комбинат. Айталық, Қарағанды мен Теміртаудың м е т а л л у р г и я к о м б и н а т т а р ы н а н шыққан ақаба су Нұраға осы жолмен табысады (Қаз. әдеб., 18.03.1988, 3). Металлургия отаны. п е р и ф р.… … Қазақ тілінің түсіндірме сөздігі
big_medicine.academic.ru
Чёрная металлургия – это… Что такое Чёрная металлургия?
Чёрная металлургия служит основой развития машиностроения (одна треть отлитого металла из доменной печи идёт в машиностроение) и строительства (1/4 металла идёт в строительство). Основным исходным сырьем для получения черных металлов являются железная руда, марганец, коксующиеся угли и руды легирующих металлов.
Состав
В состав чёрной металлургии входят следующие основные подотрасли:
Металлургический цикл
Собственно металлургическим циклом является производство
1) чугунно-доменное производство, 2) стали (мартеновское, кислородноконвертерное и электросталеплавильное), (непрерывная разливка, МНЛЗ),
− − 3) проката (прокатное производство).
− − Предприятия, выпускающие чугун, углеродистую сталь и прокат, относятся к металлургическим предприятиям полного цикла.
− − Предприятия без выплавки чугуна относят к так называемой передельной металлургии. «Малая металлургия» представляет собой выпуск стали и проката на машиностроительных заводах. Основным типом предприятий чёрной металлургии являются комбинаты.
− − В размещении чёрной металлургии полного цикла большую роль играет сырьё и топливо, особенно велика роль сочетаний железных руд и коксующихся углей.
Размещение предприятий отрасли в Российской Федерации
Особенность промышленности России заключается в больших расстояниях между производствами различных циклов. Металлургические комбинаты, производящие чугун и сталь из руды, традиционно располагались около месторождений железных руд в районах, богатых лесом, так как для восстановления железа использовали древесный уголь. И в настоящее время металлургические комбинаты металлургической отрасли России расположены вблизи месторождений железной руды: Новолипецкий и Оскольский — около месторождений центральной России, Череповецкий («Северсталь») — около Карельского и Костомукшского, Магнитогорский — около горы Магнитная (уже выработанное месторождение) и в 300 км от Соколовско-Сарбайского в Казахстане, бывший Орско-Халиловский комбинат (в настоящее время «Уральская сталь») около месторождений природнолегированных руд, Нижнетагильский — вблизи Качканарского ГОКа, Новокузнецкий и Западно-Сибирский — около месторождений Кузбасса. Все комбинаты России расположены в местах, где ещё в XVIII веке и ранее существовало производство железа и изделий из него с использованием древесного угля. Месторождения коксующегося угля расположены чаще всего вдали от комбинатов именно по этой причине. Только НКМК и Запсиб расположены непосредственно на месторождениях каменного угля Кузбасса. «Северсталь» снабжается углём, добываемым в Печорском угольном бассейне.
В центральной части России большая часть железорудного сырья добывается в районе Курской аномалии. В промышленных масштабах железорудное сырьё производится также в Карелии и на Урале, а также в Сибири (добыча ведётся в Кузбассе, Красноярском крае, Хакасии и близких им районах). Большие запасы железной руды в Восточной Сибири практически не осваиваются из-за отсутствия инфраструктуры (железных дорог для вывоза сырья).
Два основных района производства коксующегося угля в России — Печорский (Воркута) и Кузнецкий бассейн (Кузбасс). Крупные угольные поля есть также в Восточной Сибири; они отчасти разрабатываются, однако промышленное их освоение упирается в отсутствие транспортной инфраструктуры.
Центральная часть России, в частности Орел, Белгород, Воронеж, Тула не богаты металлами, поэтому в основном для внутренних нужд все сырье привозится из других регионов. Крупнейшими поставщиками металла в центральный регион являются общероссийские компании, такие как Импром, и местные, такие как ПРОТЭК и Союзметаллкомплект.
При строительстве всех крупных металлургических комбинатов России (в советское время) одновременно велось и строительство ориентированного на каждый завод горно-обогатительного комбината. Однако после развала СССР некоторые комплексы оказались разбросанными по территории СНГ. Например, Соколовско-Сарбайское ГПО, поставщик руды на Магнитогорский меткомбинат, теперь находится в Казахстане. Железорудные предприятия Сибири ориентированы на Западно-Сибирский и Новокузнецкий меткомбинаты. Качканарский ГОК «Ванадий» поставляет руду на Нижнетагильский меткомбинат. «Карельский Окатыш» поставляет руду в основном на Череповецкий металлургический комбинат («Северсталь») в Череповце.
При размещении предприятий учитывалось также обеспечение водой, электроэнергией, природным газом.
В России созданы три металлургические базы:
См. также
В этой статье не хватает ссылок на источники информации. Информация должна быть проверяема, иначе она может быть поставлена под сомнение и удалена. Вы можете отредактировать эту статью, добавив ссылки на авторитетные источники. Эта отметка установлена 15 мая 2011. |
Ссылки
dic.academic.ru