Большая металлургия: МЕТАЛЛУРГИЯ • Большая российская энциклопедия
alexxlab | 17.08.2020 | 0 | Разное
Иранская черная металлургия — состояние и проблемы
№1(20), 2012
Экономика зарубежных стран
В статье исследуется история и современное состояние иранской черной металлургии, а также ее перспективы
Ключевые слова: Иран, черная металлургия
N.Mamedova. Iran’s non-ferrous metallurgy: situation and prospects
Article focuses on history and modern situation in Iran’s non-ferrous metallurgy as well its prospects
Key words: Iran, non-ferrous metallurgy
С давних времен, когда нефть еще не стала главным богатством Ирана, он славился высоким уровнем изготовления не только ковров, но и различных металлических изделий — из железа, меди, серебра, бронзы, свинца и других металлов. Европейские путешественники отмечали в 17в. высокое качество стали, которая производилась в районе оз. Нейриз [1], клинков, которые изготовлялись в Куме, в русских работах часто упоминались кызылбашские сабли с высоким качеством стали и красотой отделки.
В настоящее время экономика страны зависит, главным образом, от состояния ее нефтегазового сектора. Но эта зависимость от экспорта энергоресурсов делает актуальным развитие других отраслей. Одной из наиболее перспективных для Ирана направлений развития промышленности, которая не только бы обеспечила потребность растущего внутреннего рынка, но и стала бы экспортной отраслью, является основная, или черная, металлургия.
Деятельность металлургических предприятий в Иране находится в ведении Министерства горнорудных дел и металлургии. После исламской революции 1979г. практически все металлургические заводы, шахты и рудники были переданы в руки государства. После перехода с 1990г. к политике либерализации и создания рыночной экономики Министерство горнодобывающей промышленности и металлургии через свои организации приступило к проведению программы приватизации. Уже в 1995г. правительство Ирана приняло решении о приватизации более чем 1000 предприятий горнодобывающей промышленности, оставив в государственной собственности треть наиболее крупных рудников и шахт, требующих значительных затрат на модернизацию.
Хотя кустарная выплавка железа и стали, как было сказано выше, возникла в древности, современная черная металлургия появилась в Иране сравнительно недавно- во второй половине ХХ века. Еще в 1937г. Иран заключил соглашение с одной из немецких компаний о строительстве в Кередже (под Тегераном) металлургического завода мощностью 100 тыс.тонн железа в год. Сырьевой базой для него должны были стать железная руда из Семнана и каменный уголь из Альборзких гор.[3] Однако Вторая мировая война прервала реализацию этого проекта. Стремление Ирана организовать собственное металлургическое производство в 60-70ые годы наталкивалось на упорное противодействие этому со стороны западных государств. Построенные в 60-е годы предприятия — государственные и частные- работали на импортном металлоломе. Первенец черной металлургии — Исфаганский металлургический комбинат с полным циклом производства был построен в 1973г. с помощью СССР. Советский Союз не только построил этот завод, но и, по-существу, обустроил всю сырьевую базу. С его участием были пущены в эксплуатацию рудники по добыче железной руды и каменноугольные шахты, обслуживавшие потребности комбината. Однако строительство этого комбината не решило проблему с обеспечением внутреннего рынка.
Однако после исламской революции 1979г. программа была прервана, и к ее реализации приступили после окончания ирано-иракской войны. Первыми стали сталелитейные заводы в Мобареке и Мияне, что превратило провинцию (остан) Исфаган в центр иранской металлургии. Первая очередь Мобарекского металлургического комбината вступила в строй в 1991г. Мобарекский комбинат является и по сегодняшний день одним из самых современных заводов в мире. Внедрению технологий по прямому восстановлению железа благоприятствует наличие огромных запасов газа и его дешевизна (государство субсидирует поставки газа для промышленных предприятий). В результате Иран уже к середине 2000-х годов занял одно из ведущих мест в мире по производству DRI-прямовосстановленного железа, этого перспективнейшего металлургического сырья. Установки прямого восстановления (по технологии Midrex, Xyl III, Purofer) в Иране имеют тенденцию к росту. Если в 2005г. их общая мощность составляла 7 млн.тонн, в т.ч. на Мобарекском заводе — 3,2 млн.т, Хузестанском комплексе- около 2 млн.т),[4] то в 2009г. возросла до 8,9 млн.т[5]. Развитие этого направления металлургии, с одной стороны, снижает зависимость от поставок металлолома, но с другой- требует руды с высоким содержанием железа, низким содержанием примесей и малой склонностью к разрушению во время восстановления, а потребность в такой руде не покрывается собственной добычей. Если импорт металлических руд в 2004г. не превышал 46 млн.долл, то в 2007г. составил уже 321, в 2008г.-227 млн.долл.[6] При этом Иран увеличивал экспорт металлических руд, отвечающим требованиям для доменных производств. С 2005/6г.
В пятилетних планах социально-экономического развития (срок действия Пятого плана заканчивается в марте 2016г.) металлургическая отрасль определяется как одна из наиболее приоритетных. Планы выпуска металлов, если и корректировались, то только в сторону увеличения. Так, согласно программе по увеличению выпуска продукции основной металлургии, разработанной в начале 2000-х годов, предполагалось довести производство стали до 18-20млн. т к 2014г., а пятый пятилетний план поставил цель довести этот показатель к 2016г. до 42-45 млн.т[8], что позволит войти в первую десятку мировых производителей черного металла.
Проекты строительства металлургических комбинатов разного профиля с участием различных иностранных компаний, включая германские, японские, испанские, китайские и индийские, осуществляются по всей стране. В последние пять лет в строй постоянно вводятся новые объекты и модернизируются действующие предприятия.

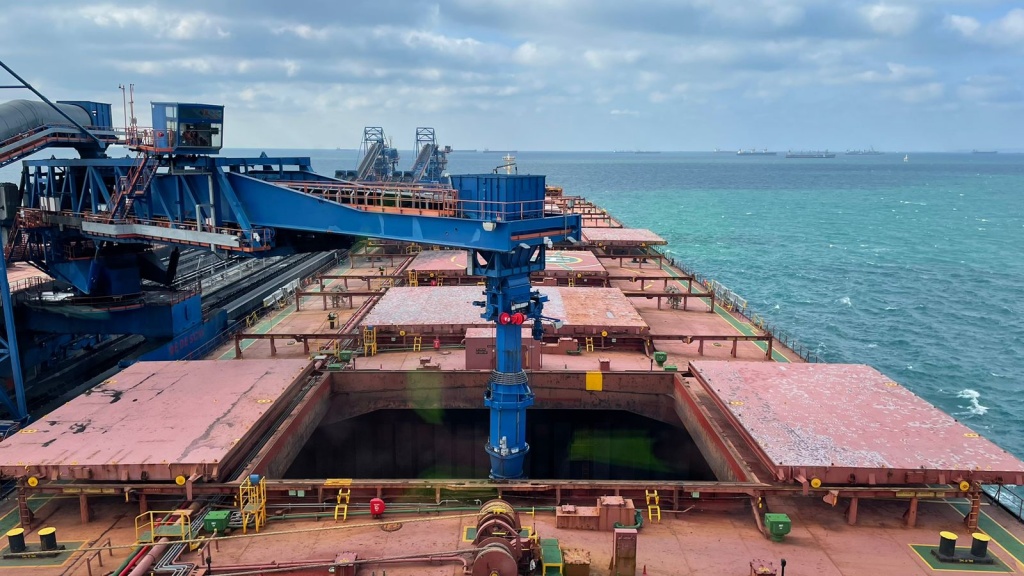
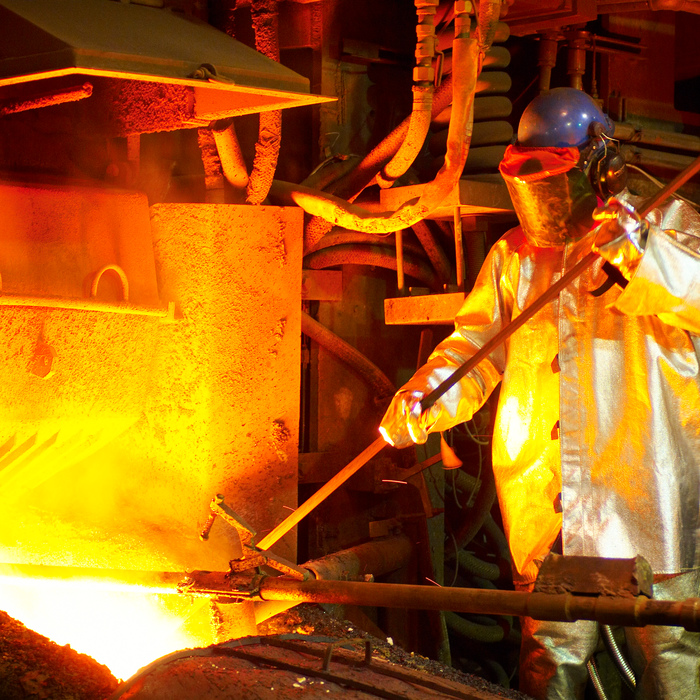
Согласно промышленным переписям за 1997/8г. и 2005/6г.[17] общее число металлургических предприятий (основная металлургия) увеличилось с 352 до 572. Из этих 572 предприятий 97 составляли крупные заводы с числом занятых свыше 100человек, 85- с числом занятых от 50 до 99 человек, а занятость на остальных 390 предприятиях не превышала 50 человек. Наиболее значительный рост произошел в группе средних предприятий (с 30 до 85), прирост мелких предприятий составил 50%,крупных-56%. Хотя в структуре металлургических предприятий доля наиболее крупных составляет менее 20%, именно они определяют лицо иранской металлургии, т. к. на их долю приходится более 96% продукции отрасли.[18] В общей сумме инвестиций капиталовложения в металлургию не опускались в 2000-е годы ниже 20%, при этом в 2005г. они превысили 33%, а в 2006г. достигли почти 42% от всей суммы капиталовложений.[19]
Введение в строй новых предприятий позволило Ирану уже в 1995г. начать экспорт стали (1,5 млн. тонн), а металлургия наряду с нефтехимией стала становиться экспортной отраслью. В 2005/6г. было экспортировано уже 2,55 млн.т. на 1,1 млрд.долл.[20] Однако в связи с быстрым ростом потребности внутреннего рынка в металле, особенно со стороны строительной, автомобильной и оборонной промышленности, экспорт металла стал сокращаться, и по состоянию на 2009г. Иран являлся чистым нетто-импортером стали. Он вошел в 2009г. в число крупнейших импортеров стали, закупив в 2008/9г. 10,2 млн.т (13 место), в 2009/10г., по оценкам Центрального банка Ирана,- 12,1 млн.т, а экспорт- не превысил и десятой части экспорта. Уже в 2007/8г. экспорт стали снизился до 1,5 млн. т, в 2008/9г.- до 0,9 млн.т, в 2009/10г. ввод новых предприятий позволит увеличить экспорт до 1,4 млн.т. (около 1 млрд. долл).[21] Часть первичного импортируемого металла используется в качестве сырья для прокатных и металлургических заводов страны. Так как внутренний рынок металла не сбалансирован и до сих пор спрос на высококачественные сорта стали не покрывается, часть импорта идет на удовлетворение потребностей других отраслей. Не хватает плоского проката — горячекатаных полос, полос с покрытием, тонких полос, белой жести. Не полностью удовлетворяется спрос на такие виды сортового проката как арматура, легкие профили.[22]
При этом общее производство металла росло быстрыми темпами. Если в 1992г. в Иране было выплавлено 3,0млн. т стали, то в 2000г. — уже 6,6 млн.т. По данным World Steel Association производство стали в Иране в 2009г. составило 10,9 млн.т,[23] в 2010г.-12 млн.т, что позволило ему стать вторым после Турции крупнейшим производителем стали на Ближнем и Среднем Востоке. [24] C 2003г. Активно работает Тегеранская биржа металлов. В 2009/10г. через нее было продано 7,4 млн.т металла, что на 11,4% превысило оборот биржи в 2008/9г. Число трейдеров, занимавшихся продажей металла через Тегеранскую биржу металлов, в 2009/10г. достигло восьми. Подавляющая часть операций и по количеству и по стоимости пришлась на сделки со сталью.[25]
До настоящего времени в иранской металлургии преобладает государственный сектор, но доля частного сектора постоянно увеличивается, т.к. государство оказывает значительную кредитную поддержку частным предпринимателям, работающим в этой отрасли. В 2009г. на долю частных предприятий пришлось не более 15% выпуска стали.[26] Большая часть программ по развитию металлургии и предприятий горнодобывающей промышленности, обслуживающих потребности металлургического производства, реализуется под управлением образованной в 2002г. Организации рудников и промышленности (IMIDRO- Iran mines and Mining Industries and Renovation Organisation). Она контролирует производство, включая добычу железной руды, реализацию, импорт и экспорт металла, в сфере ее деятельности находятся и некоторые частные компании. Часть металлургических предприятий работает под контролем Организации оборонной промышленности, других государственных организаций или являются независимыми компаниями.
Ассортимент металлопродукции металлургических предприятий разнообразен и включает горячекатаную и холоднокатаную полосу, тонкую полосу, трубы, проволоку, сортовой прокат, легкие и тяжелые профили и в небольших объемах жесть с металлическим покрытием. Более 70% производства составляет электросталь.
Центрами основной металлургии в Иране являются останы Исфаган, Хузестан и Йезд. В них расположены наиболее крупные предприятия отрасли, а также тяготеющие к ним более мелкие предприятия. Основная доля производимой в стране металлопродукции приходится на 10-12 предприятий. На иранском рынке металла по состоянию на 2011г., по данным Министерства горной и металлургической промышленности, на долю Мобаракского комплекса приходилось приблизительно 47%, Хузестанского комплекса — около 23%, Исфаганского металлургического комбината — около 20%, Иранской национальной сталелитейной группы (Ахваз)–около 10%. [27]
Первым предприятием с полным металлургическим циклом стал Исфаганский комбинат, построенный, как было сказано выше, с помощью СССР. Производительность комбината (после завершения работ по третьей очереди увеличения мощности в 2006г.) — до 5 млн. т в год, включая первичный металл и металлопрокат.
В Исфагане находится также крупнейший на сегодняшний день в Иране металлургический комбинат «Мобареке», который является предприятием с полным циклом, и имеет установки по прямому восстановлению железа. На «Мобараке» освоены технологии производства стали для судостроения, с 2003г. введен цех по производству оцинкованного стального листа. Вступивший в Мобареке в 2003г. в строй новый металлургический завод «Саба»(проектная мощность 700 тыс. т. горячекатаного стального листа, предполагается увеличить мощность до 1,6 млн.т) в настоящее время включен в Мобарекский комплекс. К Мобарекскому комплексу в марте 2011г. был присоединен металлургический завод прямого восстановления железа «Хормозган», расположенный в специальной зоне на побережье Персидского залива, мощность которого предполагается увеличить с 1,5 до 3,0 млн. т.[28] Для его строительства был создан консорциум с участием немецких компаний.
В остане Исфаган в г. Натанзе в июле 2010г. состоялась торжественная церемония начала строительства крупного завода по производству стального бруса мощностью 800-1000тыс.т и общим объемом инвестиций 320 млн.долл., как часть развития сталелитейной компании Натанза[29]. Не исключено, что часть продукции этого завода предназначена для нужд атомной промышленности.
На ряде заводов Хузестанской металлургической компании, которая была образована в 1994г. путем слияния Ахвазского сталелитейного и трубопрокатного завода и завода Кавиан по выпуску бронированной стали, в последние годы проведены работы по модернизации производства, налажено производство горячекатаного стального листа категории А, который используется в судостроении и на которую получен международный сертификат качества. Основная продукция завода- листовая сталь толщиной от 5 до 150мм. Ахвазский сталелитейный комплекс(2,5 млн.т губчатого железа, 1,5 млн. т литых заготовок и слябов) работает по технологии прямого восстановления железа.В Хузестане в свободной экономической зоне «Эрвенд» строится новый металлургический завод.
Металлургический комплекс в Хорасане, выпускающий прокатную сталь, с 2004г. расширяет производство за счет дополнительных мощностей по прямому восстановлению железа. В 2008г. выпустил около 0,5 млн.т первичного металла и более 0,6 млн.т металлопроката.
Становление Йезда как одного из центров иранской металлургии началось со строительства завода специальных сплавов, пущенного в эксплуатацию в 1994г. (Компания « Iran Alloy Steel Company»). Модернизация завода позволила увеличить первоначальную мощность (140тыс.т стали в год), вдвое. Продукция завода идет на нужды медицины, автомобильной, нефтехимической, оборонной промышленности. Это один из самых крупных заводов на Среднем Востоке, выпускающих легированную сталь.[30] В остане Йезд работает металлургический завод «Мейбад», который в 2008г. произвел более 200 тыс. т металла.[31] Хотя строительство запланированных нескольких заводов в Йезде было признано ошибочным из-за напряженного водного баланса в этой провинции, тем не менее, близость к запасам железных руд и возможность получения высокообогащенного концентрата, вероятно, сделают завершение работ реальным.
Для развития металлургической промышленности Иран располагает достаточно надежной собственной сырьевой базой, которая по мере увеличения геолого-поисковых работ, постоянно расширяется.
Прогнозные запасы железной руды оцениваются в 3226 млн.тонн, подтвержденные- в 2540 млн.т, с содержанием железа- 39-64%. Большая часть месторождений железных руд сосредоточена в центральных районах страны. Наиболее крупные месторождения железной руды относятся к Бафкскому железнорудному району, где они оцениваются в 1843,3 млн.т (останы Керман и Йезд).[32] Железорудный концентрат и агломерат получают на рудниках «Чадормалу» с запасами в 378 млн.т и «Чогарт» с запасами 115 млн.т, относящимися к Бафкскому району. До 90% запасов Чадормалу составляют богатые руды со средним содержанием железа 58,9%. Месторождение «Чогарт» находится вблизи г.Йезд. Рудники «Чогарта» обеспечивают основные потребности Исфаганского комбината, «Чадеромлу» и месторождение «Голегохар» Сирджанского рудного района ориентированы на заводы по прямому восстановлению железа в Мобареке и Ахвазе. Вблизи «Голегохар» с его запасами св.1 млрд.т, и дающего в настоящее время до 2,5 млн.т железнорудного концентрата, планируется построить с помощью иностранных инвесторов мощный горно-металлургический комплекс ( на 10 млн. т стали).[33]
В стадии освоения находятся такие крупные месторождения железной руды как «Се-Чахун» (относится к Бафкскому рудному району, содержит высокофосфористые руды), находящееся недалеко от «Чогарта» и месторождение «Санган» (запасы — 1200млн.т в Хорасане), которое ориентировано на потребности запроектированного к строительству металлургического завода в Нишапуре. Все указанные крупные месторождения и работающие на них рудники находятся в государственной собственности, кроме того, около 50 мелких месторождений железной руды разного качества находятся в частной собственности. Добыча железной руды постоянно растет, увеличившись за последние пятнадцать лет более, чем в 10 раз и составляя в настоящее время до 20 млн.т товарной руды. Полностью удовлетворяются потребности Исфаганского металлургического комбината, Мобарекского комплекса и некоторых других заводов. Однако вывод на полную мощность новых заводов по прямому восстановлению железа требуют ускорения работ по обустройству новых месторождений. Можно предположить, что возможности для расширения сырьевой базы есть, т.к. за последние сорок лет выявлено более 38 аномалий (с запасами в 7,1 млрд.т), но достоверных данных о проведении геолого-разведочных работ на железорудное сырье в последние несколько лет нет.[34] Запасы и добыча в Иране хрома и марганца также являются фактором получения высококачественного металла.
Однако освоение новых месторождений требует больших средств и времени. В настоящее время, когда развитие металлургии находится в стадии роста и резкого увеличения спроса на сырье для предприятий прямого восстановления железа, выявилась несбалансированность не только с точки зрения ассортимента выпускаемой металлургическими предприятиями продукции, но и с точки зрения обеспечения их сырьем. Иран превратился не только в чистого импортера металла, но и импортера железных руд (до 10% от всей добычи). Потребность в металле на иранском рынке была столь велика, что в середине 2000-х гг. импортные пошлины на металл были практически нулевыми. Одним из крупных поставщиков металла в Иран стала Россия, что поддержало российские компании в условиях разворачивавшегося мирового кризиса, но снизило рентабельность иранских предприятий, выпускающих первичный металл. К этому добавилось и усиление санкционного режима против Ирана, введенного большинством стран во второй половине 2010г, что затормозило реализацию некоторых проектов. С 2010г. импортные пошлины на металл были повышены, большинство иранских металлургических компаний уже в 2011г. показало устойчивую тенденцию к росту.
Но к настоящему времени, несмотря на рост выпуска стали, Иран по-прежнему остается страной с высоким импортным потенциалом. Металлургический рынок Ирана перспективен и с точки зрения поставок на него готового металла и рудных концентратов, и с точки зрения участия в инвестиционных проектах. В условиях санкционного режима, когда многие зарубежные компании ограничили свои контакты с Ираном, металлургическая отрасль, не попадающая под санкции, может стать привлекательной для российских инвесторов. При этом России необходимо учитывать, что уже в ближайшей перспективе Иран может превратиться не только в крупного регионального производителя стали, но и его экспортера, в первую очередь, экспортера прямовосстановленного железа (DRI).
- в г. Нейриз в настоящее время работает металлургический завод «Нейриз стил».
- Рассчитано по данным « The Central Bank of Iran. Economic Report and Balance Sheet 2007/08». Tehran. 2010.P.202.
- Мориди, Сиявуш. Китабе Иран. Эктесад.(Книги Ирана.Экономика).Техран,2002. С.116.
- «Исламский вариант» металлургии». Металлургический бюллетень.21.10.2011.
- Steel Statistical Yearbook 2010.P.
- The Central Bank of Iran. Economic Report and Balance Sheet 2007/08. Tehran. 2010.P.190.
- The Central Bank of Iran.
Annual Review. 1388 (2009/10).P58-59.
- Iran steel production surging upward. Iron and Steel. 11.08.2010. www.metalsnews.ir
- www.intl.mim,gov.ir (сайт Министерства горной промышленности и металлургии).
- Там же. 02.2011.
- Там же.30.05.2011.
- Там же.17.05.2011.
- Иран: перспективы строительства металлургических предприятий. www.ukrbuild.dp.ua. 28.08.28. 2011.
- Leading Industrial and Mining Projects to Launch. 10.08.2010. www.metalsnews.ir
- В.И.Сажин. Иран :июль — август 2011. Экономическая ситуация. www.iimes.ru/stat/2011/20-10-11c.htm
- Металлургический бюллетень. Информационно-аналитический журнал. 04 ноября 2011г.
- В Иране год начинается с 21 марта.
- Сальнаме-йе амарие кешвар(статистический годовой отчет) 1377(1998/99), С.276-280. Табл.7.4.7.16, Сальнаме-йе амарие кешвар 1385(2006/07).Табл.7.4.
- Подсчитано по данным: «The Central Bank of Iran.
Economic Report and Balance Sheet 2007/08». Tehran. 2010.P.157.
- The Central Bank of Iran. Annual Review. 1388 (2009/10).P..58-59.
- Там же. P.59-60.
- Р.Сафаров. Металлургическая промышленность Ирана. www.Iran.ru. 19.11.2009.
- Steel Statistical Yearbook 2010. Brussels.P.4.
- Иран: перспективы строительства металлургических предприятий. www.ukrbulild.dp.ua/2011/08/28/iran-perspectivy-stroitelstva-metallurgicheskix-pred…
- Annual Report.1388. (2009/10). P.26.
- Ali Forouzan. Iran:Steel Industry Overview. www.steelmaking.wordpress.com. 28.01.2010.
- .www.intl.mim,gov.ir (сайт Министерства горной промышленности и металлургии).02.05.2011.
- www.mobarakeh-steel.ir/index.aspx?id=41&ln=en (сайт Мобарекского комплекса).
- Iran inaugurates Middle East’s largest steel rod production plant. www.metalsnews.ir. 15.07.2011
- Сайт компании- www.iranalloysteel.
com.
- С.М.Задонский. Общая характеристика основных отраслей обрабатывающей промышленности Ирана. www.iimes.ru. 12/05/2009/
- www.mineral.ru/ Facts/world/116/140/index/html
- Там же
- Там же.
Металлургия Германии
Впервые немецкие промышленники от металлургии заявили о себе в 1890 году. 19 марта большая встреча хозяев предприятий состоялась в Берлине, где в ассоциацию вошли представители других территорий, на которых активно развивалась металлургия. Созданное более 125 лет назад сообщество металлургов Германии долгие годы позволяло крупным фирмам поддерживая корпоративную солидарность развивать производство, не растрачивая силы на конкурентную борьбу. К 1914 году в стране существовали около тысячи картелей — монополий. Со временем создания в Европе в 1834 году Таможенного союза во главе с Пруссией и появления единого экономического пространства связывают начало промышленного переворота в Германии.
Центр металлургии Германии
Самые благоприятные условия для развития металлургической промышленности Германии сложились в Руре: достаточная сырьевая база, транспортные развязки, наличие рабочей силы. Близко находился и рынок сбыта. В конце 19 века в Руре на 50 предприятиях черной и цветной металлургии работало более 3 тысяч человек. Самой крупной была компания «Фридрих Крупп АГ». Создание Германской империи в 1871 году укрепило экономическую ситуацию и совершило значительный экономический рывок.
С 70-х годов 19 века и до начала первой мировой войны Германия была в числе самых значимых европейских стран, производящих металл. Центром тяжелой промышленности стал Рурский угольный бассейн. Почти 40 % металла выплавлялось в Германии.
Переживая подъемы и спады, в 1933 году немецкая промышленность выпустила 22 млн. тонн металла. Во время подготовки руководства страны к войне, производимые фирмой “Круппа” броня, вооружение были востребованы, что давало предпосылки к новому развитию черной металлургии.
Потрясения второй мировой были преодолены, и в 20 веке модернизированная промышленность Германии была в состоянии стабильности. Объемы производства чугуна составляли более 30, а стали более 40 млн. тонн.
Черная металлургия Германии, сегодня
Проводя исследования, немецкие экономисты приходят к выводу, что, несмотря на сокращение производства черных металлов в 2013 – 2015 годах и потерю статуса ведущей отрасли, черная металлургия находится на хорошем уровне. В связи с развитием строительной отрасли ожидается повышения спроса на металл.
Сами же металлургические компании, такие как «Объединение немецких производителей стали» считают, что трудно выдерживать конкуренцию, работая на привозном сырье в условиях избытка производственных мощностей. С конца 20 века концерны Германии, производящие металл, ведут работу по переориентации рынков сбыта и меняют приоритеты в пользу производства машин и оборудования, а не просто металла.
Цветная металлургия
Для цветной металлургии характерны различные принципы размещения производств: сырьевой или энергетический (как в производстве алюминия). Цветная металлургия страны находится в более выгодном положении, хотя так же работает на импортируемом сырье. Объемы здесь меньше, и потому доставка на заводы Германии морским транспортом обходится дешевле, учитывая, что центры цветной металлургии располагаются на побережье.
Сегодня при производстве цветных металлов в большом количестве используется лом, который есть внутри страны. Производимая медь подразделяется на черновую, которую выплавляют в Гамбурге, и на рафинированную, потребители которой расположены достаточно близко.
Успешной можно назвать работу производителей алюминия. В этой отрасли наблюдается стабильный рост объемов выпущенной продукции. С 2014 года производство алюминиевых сплавов выросло на 2,2 % и составило около 2,5 млн. тонн.
Bell Copper Reports Big Sandy Metallurgy
Ванкувер, Британская Колумбия — (Newsfile Corp. — 21 июля 2022 г.) — Bell Copper Corporation (TSXV: BCU) (OTCQB: BCUFF) («Bell Copper» или «Компания “) сообщает, что получила предварительный отчет о металлургических испытаниях наиболее богатого медью интервала скважины БС-3 на своем проекте Биг-Сэнди в Аризоне. Big Sandy представляет собой крупную медно-молибденовую медно-порфировую цель, расположенную на северо-западе Аризоны, примерно в 30 км к югу от аналогичного проекта Perseverance компании.
Скважина BS-3 прошла 200 метров от 1302 метров до 1502 метров, содержание меди 0,42% (8,4 фунта меди/ст) и 2,4 грамма серебра на тонну в виде супергенного халькоцита, заключенного в сильно пиритном серицитизированном порфире. Отверстие было завершено сильно пиритным, серицитизированным порфиром на наклонной глубине 2026,33 метра, когда были достигнуты механические пределы бурения.
Сводная проба крупных отходов анализа из халькоцитоносного (меденосного) интервала 1302-1502 м была отправлена в компанию SGS Canada Inc. (площадка Лейкфилд, Онтарио) [SGS] для банка предварительных металлургических исследований. Халькозин испытывали на способность к извлечению как пенной флотацией, так и кислотным выщелачиванием. Молибденит был испытан на его способность концентрироваться пенной флотацией и на содержание в нем стратегического элемента рения. Содержание составного образца, полученного SGS, составляло 0,41 % Cu, 0,005 % Mo, 2,3 г/т Ag и 4 % S. Концентрации вредных элементов As, Pb, Sb и Zn были менее 50 частей на млн.
Основные моменты испытаний включают:
Минералогически 75% меди в образце составлял халькоцит, еще 15% составлял борнит, а остальная часть состояла из других сульфидных минералов меди. Оксидные минералы меди были незначительны.
Примерно 8% пробы приходится на долю пирита. Кварц с содержанием 52% и мусковит с содержанием 34% были преобладающими несульфидными разновидностями. Карбонатные минералы составили 0,1 % пробы.
Традиционный метод пенной флотации оказался успешным при извлечении и обогащении ценных минералов. Было достигнуто извлечение меди при периодическом испытании 82-84% в концентрат с содержанием меди 25%.
При содержании меди в концентрате 25 % меди содержание серебра составляло приблизительно 130 г/т, а степень извлечения составляла приблизительно 68 %.
Серебро, казалось, сопровождалось медью.
Низкое содержание молибдена в исходном материале затрудняло получение молибденового концентрата, но в лучшем случае был получен более чистый молибденовый концентрат с содержанием молибдена 20,7%. Для улучшения результатов по молибдену необходимы дальнейшие испытания на большем количестве образцов.
Содержание рения было исследовано в молибденовом концентрате более низкого качества, и при наличии следов молибдена рений оценивается в концентрации приблизительно 1700 г/т Re в молибденовом концентрате с содержанием молибдена 50%.
Выщелачивание железа Серная кислота с концентрацией 30 г/л оценивалась на измельченной цельной руде до P 80 размером 120 мкм. Руда поддавалась выщелачиванию с извлечением меди в пределах 96%. Пирит, присущий образцу, внес дополнительную свободную кислоту в ходе экспериментов по выщелачиванию.
Как только окончательный отчет будет получен от SGS, он будет размещен на веб-сайте компании.
Металлургические испытания
На одном этапе испытаний халькозин (сульфид меди) извлекали пенной флотацией с использованием стандартных реагентов, используемых на действующих медеплавильных заводах. Цель этого испытания состояла в том, чтобы 1) определить процентное содержание меди, которое может быть извлечено с использованием этого общего метода, 2) определить содержание меди в полученном концентрате и 3) оценить концентрацию побочных металлов и вредных элементов в концентрате.
Достигнуто извлечение меди при периодическом испытании 82-84% в концентрат с содержанием меди 25%. Существуют возможности для повышения качества концентрата за счет подавления чистого пирита. При содержании меди в концентрате 25 % перечистной массы содержание серебра составляло примерно 130 г/т Ag, а степень извлечения составляла примерно 68 %. Серебро, казалось, сопровождалось медью. Ожидается окончательный многоэлементный анализ концентрата. Медный концентрат, полученный в результате опытно-промышленных работ, теперь доступен для обсуждения с медеплавильными компаниями.
Образец халькоцита BS-3 был также подвергнут кислотному выщелачиванию, чтобы определить, может ли халькоцит Биг-Сэнди поддаваться добыче раствором. Это тестирование не предназначено для оценки того, возможно ли извлечение меди путем добычи на месте, а скорее для того, чтобы определить на этой ранней стадии оценки, не препятствуют ли этому какие-либо минералогические факторы. Эта тестовая работа показала, что возможно извлечение меди в диапазоне от 96% из измельченной цельной руды до P 80 размером 120 мкм. Испытания также показали положительный эффект, заключающийся в том, что вместо того, чтобы потреблять дорогостоящую кислоту, в процессе тестового выщелачивания образуется свободная кислота в ходе экспериментов по выщелачиванию из-за окисления пирита, присущего образцу.
При содержании молибденита 0,005% Мо интервал проб не содержал большого количества молибденита, хотя было желательно проверить его способность к пенной флотации и отделяемость от медного концентрата. Низкое содержание молибденита затруднило проведение испытаний, но в лучшем случае был получен более чистый концентрат молибдена с содержанием молибдена 20,7%. Для улучшения результатов по молибдену необходимы дальнейшие испытания.
Кроме того, было определено содержание рения в лучшем молибденитовом концентрате, полученном в результате испытаний, для оценки потенциала получения кредита на Биг-Сэнди из этого стратегического металла. Молибденит из скважины БС-1, расположенной в 1,2 км к востоку от БС-3, был геохронологически датирован в лаборатории Эйри Колорадского государственного университета с использованием рениево-осмиевой методики датирования. Это датирование выявило необычно высокое содержание рения в молибдените Big Sandy BS-1: от 8713 ± 17 ppm до 9319 ± 25 м.д. Содержание рения было определено в молибденовом концентрате с более низким содержанием молибдена, и, учитывая присутствие в нем молибдена, рений оценивается в концентрации примерно до 1700 г/т Re в молибденовом концентрате с содержанием молибдена 50%. Молибденит BS-1 и молибденит BS-3, расстояние между которыми составляет 1,2 км, позволяют предположить, что повышенное содержание рения является характерной чертой порфировой системы Биг-Сэнди.
В заключительном отчете технология высокого разрешения TIMA-X будет использоваться для визуализации материала BS-3 и определения идентичности, размера и микроскопической текстуры минералов, содержащих целевые металлы. Эти изображения помогут оптимизировать размер помола, выбор реагентов, повышение качества концентрата и поведение любых потенциальных побочных продуктов или вредных элементов.
Рисунок A. Керн из скважины BS-3 (1304 м), показывающий вкрапленный халькоцит (ярко-белый) в сильно измененных кварц-серицитом порфирах.
Для просмотра расширенной версии рисунка А посетите:
https://images.newsfilecorp.com/files/2825/131572_df39f925148039c5_001full.jpg
Рисунок Б.1 (керн из 6БС-3) показаны темные прожилки халькоцит-борнита, секущие прожилки крупнозернистого пирита в кварц-серицит-измененных порфирах.
Чтобы просмотреть расширенную версию рисунка B, посетите:
https://images.newsfilecorp.com/files/2825/131572_df39f925148039c5_002full.jpg
Тим Марш, президент и главный исполнительный директор Bell, а также уполномоченное лицо, как определено по NI43-101, сказал ,
«Первый взгляд на металлургические характеристики порфира Биг-Сэнди предполагает, что Bell должна рассмотреть несколько альтернатив извлечения, поскольку мы преследуем это захватывающее, продолжающееся открытие. Эта работа показывает, что либо обычная пенная флотация или выщелачивание является потенциальным методом извлечения медного оруденения, обнаруженного в БС-3. Существуют возможности для тонкой настройки процессов, но первоначальные усилия по получению 25-процентного медного концентрата с извлечением 82-84 % дали продукт, привлекательный для Если будущие инженерные исследования покажут, что добыча посредством подземной добычи неблагоприятна, то исследования по выщелачиванию предполагают, что добыча на месте может быть возможной альтернативой. тив. И во второй раз в первые дни этой истории открытия повышенное содержание рения в молибдените в металлургическом образце БС-3, как и высокое содержание рения в молибдените, возраст которого был определен на расстоянии 1200 метров в скважине БС-1, позволяет предположить, что высокое содержание стратегического металла рения является отличительной чертой порфировой системы Биг-Сэнди».0090
Отбор проб и контроль качества
Единая 100-килограммовая составная проба халькоцитового пересечения BS-3 (1302–1502 м) была получена путем комбинирования отбракованного материала, возвращенного из первоначальной кампании по анализу в Skyline Laboratories в Тусоне, штат Аризона. . Три восьмых разделения через разделитель типа Джонса каждого исходного образца для анализа объединяли для получения составного образца. Работа по композитингу проводилась под непосредственным контролем Уполномоченного лица Компании. Три ведра со 100-килограммовым образцом были отправлены в лабораторию SGS Lakefield Lab в Онтарио, где сотрудники SGS Lakefield смешали три ведра в однородный образец перед разделением на аликвоты для металлургических испытаний.
О компании Bell Copper
Bell Copper занимается разведкой полезных ископаемых, занимаясь выявлением, разведкой и открытием крупных месторождений меди, расположенных в Аризоне. Bell Copper изучает свой 100%-ный проект Big Sandy Porphyry Copper и проект Perseverance Porphyry Copper, который находится в рамках совместного предприятия – Earn In.
Квалифицированное лицо
Техническое содержание этого выпуска было проверено и одобрено Тимоти Маршем, доктором философии, инженером, генеральным директором и президентом компании. Минеральные ресурсы на проекте «Большой песчаный» пока не обнаружены. Нет никакой уверенности в том, что нынешние усилия по разведке приведут к выявлению полезных ископаемых или что любые полезные ископаемые, которые могут быть обнаружены, окажутся экономически извлекаемыми.
От имени Совета директоров
Bell Copper Corporation
“Тимоти Марш”
Тимоти Марш, президент, генеральный директор и директор
Тел. 418 8250
Электронная почта: [email protected]
Ни венчурная биржа TSX, ни ее поставщик услуг по регулированию (согласно определению этого термина в политике венчурной биржи TSX) не несут ответственности за адекватность или точность данного выпуска.
Прогнозные заявления
Этот пресс-релиз включает «прогнозные заявления» и «прогнозную информацию» по смыслу канадского законодательства о ценных бумагах. Все заявления, включенные в этот пресс-релиз, за исключением заявлений об исторических фактах, являются заявлениями прогнозного характера. Заявления о перспективах включают предположения, прогнозы и прогнозы и часто, но не всегда, обозначаются использованием таких слов, как «предполагать», «полагать», «планировать», «оценивать», «ожидать», «потенциальный», «цель», «бюджет» и «намерение», а также заявления о том, что событие или результат «может», «будет», «должен», «может» или «может» произойти или быть достигнутым, и другие подобные выражения, включая их отрицания .
Заявления прогнозного характера основаны на ряде предположений и оценок, которые, хотя и считаются разумными руководством с учетом бизнеса и рынков, на которых работает Bell Copper, по своей сути подвержены значительным операционным, экономическим и конкурентным факторам неопределенности, рискам и непредвиденным обстоятельствам . Не может быть никакой гарантии, что такие заявления окажутся точными и действительными результатами, и будущие события могут существенно отличаться от ожидаемых в таких заявлениях. Важные факторы, которые могут привести к существенному отличию фактических результатов от ожиданий Компании, включают фактические результаты разведки, интерпретацию металлургических характеристик минерализации, изменения параметров проекта по мере уточнения планов, будущие цены на металлы, наличие капитала и финансирования на приемлемых условиях. , общие экономические, рыночные или деловые условия, незастрахованные риски, нормативные изменения, задержки или невозможность получения необходимых разрешений, а также другие разведочные или другие риски, подробно описанные здесь и время от времени в документах, подаваемых Компанией в органы регулирования ценных бумаг, в том числе описанные в последнем поданном Компанией MD&A. Компания не обязуется обновлять или пересматривать какие-либо прогнозные заявления, кроме как в соответствии с применимым законодательством.
Для просмотра исходной версии этого пресс-релиза посетите сайт https://www.newsfilecorp.com/release/131572
Маленький шаг для металлургии, большой шаг для аддитивного производства | by Aerosint
Мы можем продемонстрировать полезность лазерного сплавления нескольких металлов в порошковом слое с помощью «простых» комбинаций материалов с немедленным промышленным применением.
Брэм Нейринк, доктор философии. старший инженер по исследованиям и разработкам @ Aerosint; с помощью редактирования Кевина Экеса
Неудивительно, что аксиома бесплатно так часто используется при обсуждении преимуществ аддитивного производства (АП). Действительно, сама природа этой новой отрасли производства позволяет дизайнерам использовать беспрецедентную геометрическую свободу, что, в свою очередь, позволяет настраивать свойства конечных продуктов. Этот новый подход к изготовлению компонентов уже имел далеко идущие последствия в облегченной конструкции, обеспечении функциональной совместимости и оптимизации температурных характеристик деталей, таких как пресс-формы для литья под давлением. Возможность беспрепятственного изменения материалов в одной детали выводит эту свободу проектирования на новый уровень.
В настоящее время дизайнеры продуктов уже имеют некоторые инструменты для объединения различных свойств в одном элементе. Один из способов заключается в соединении различных материалов в одну деталь путем склеивания, сварки, пайки, скрепления или комбинирования во время самого производственного процесса. Типичными примерами являются эластомеры, наплавленные на жесткие полимерные конструкции для улучшения сцепления и ощущения, пластины из твердого металла, припаянные к режущим инструментам, и тефлоновые или латунные втулки на поверхностях скольжения, вставленные в точки трения. Помимо необходимых дополнительных шагов, недостатком этого подхода является то, что часто сустав является слабым местом, подверженным поломке и возможной потере функциональности.
Другим способом является локальное изменение химического состава или микроструктуры материала с пространственной градацией. Подумайте о цементации стали, селективной термообработке и ионной бомбардировке функциональных полимеров. Несмотря на их кажущуюся более сложную природу, эти методы широко распространены в промышленности, и некоторые из них применялись на протяжении столетий.
Локальные постепенные изменения в химическом составе материалов являются целью исследований функционально-градиентных материалов (FGM), которые являются основной целью для методов AM с несколькими материалами. В этой области материаловедения уже выявлено огромное количество потенциально полезных комбинаций материалов. Что кажется упущенным из виду, так это то, что изрядное количество комбинаций металлов должно быть легким плодом для технологии AM, способной работать с несколькими материалами.
Те, кто занимается разработкой материалов и параметров в мире аддитивного производства, понимают, что материалы одного класса можно обрабатывать с очень похожими или одинаковыми параметрами без реальной потери качества. Даже сплавы с явно разным составом часто можно обрабатывать лазерным сплавлением в порошковом слое (LPBF) с теми же параметрами лазера и стратегией сканирования, если они имеют схожие термические свойства. Типичными примерами являются нержавеющие стали и кобальт-хромовые сплавы или вольфрам и тантал. Эти материалы могут быть легко сплавлены вместе в процессе многокомпонентного порошкового слоя без необходимости изменять параметры мощности лазера на лету в каждом слое или даже без прерывания векторов сканирования. Тем не менее, свойства конечных материалов достаточно различны, что позволяет оптимизировать функциональность.
Ниже приведен неисчерпывающий список потенциально «простых» комбинаций металлов и сплавов, которые можно использовать в мультиматериальных LPBF.
С селективным порошковым осаждением, применяемым для распыления связующего AM, этот список может быть расширен. Существуют материалы, которые в настоящее время несовместимы с лазерной обработкой из-за проблем с микроструктурой и растрескивания. Если бы можно было использовать струйное распыление связующего из нескольких материалов для формирования неспеченных деталей, содержащих два материала, которые спекаются при одинаковых температурах и с одинаковой скоростью, вероятно, возможно полное удаление связующего и сплавление во время термического цикла. Кроме того, естественным образом образуется зона диффузии, увеличивающая прочность соединения. Чтобы компенсировать разницу в температуре спекания, скорость спекания можно регулировать, изменяя распределение частиц по размерам, поскольку более мелкие частицы имеют тенденцию спекаться быстрее благодаря большему отношению площади поверхности к объему, чем более крупные частицы.
В сочетании с LPBF или распылением связующего селективное напыление порошка может способствовать дальнейшему созреванию металла AM за счет обработки нескольких материалов. Необходимо провести множество исследований, чтобы определить, какие комбинации металлов можно успешно обрабатывать совместно, но при таком огромном разнообразии доступных сплавов вполне вероятно, что по крайней мере несколько из них окажутся осуществимыми и практичными.