Части токарного станка – основные узлы и назначение, фото, видео
alexxlab | 13.11.2019 | 0 | Разное
основные узлы и назначение, фото, видео
Токарные станки по металлу, в общей своей массе, имеют примерно схожую компоновку — схему расположения узлов. В этой статье мы перечислим и опишем основные узлы, принцип их работы и назначение.
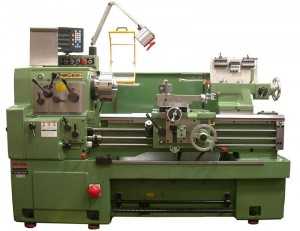
Основными узлами являются:
- станина;
- передняя бабка;
- шпиндель;
- механизм подачи;
- суппорт;
- фартук;
- задняя бабка.
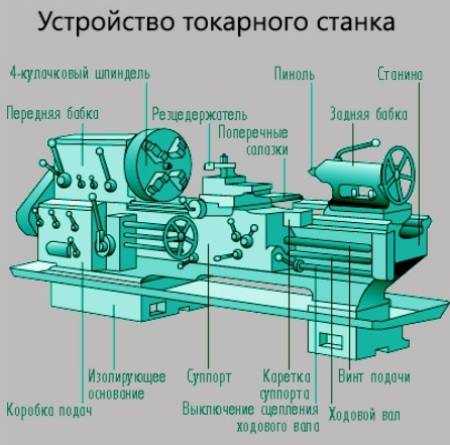
Основные узлы токарного станка по металлу
Видео-урок об устройстве токарных станков по металлу
Станина
Основной неподвижной частью станка является станина, состоящая из 2 вертикальных рёбер. Между ними находятся несколько поперечных перекладин, обеспечивающих жёсткость и неколебимость статора.
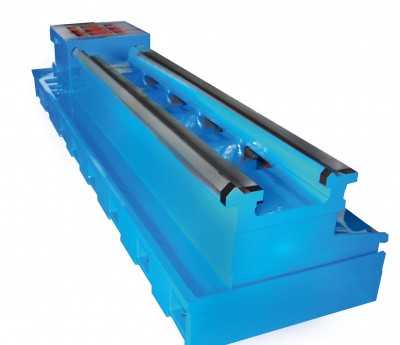
Станина
Станина располагается на ножках, их количество зависит от длины станины. Конструкция ножек-тумб такова, что в них могут храниться необходимые для работы станка инструменты.
Верхние поперечные рейки станины служат направляющими для передвижения по ним суппорта и задней бабки. Сравнивая схемы станков, легко заметить, что в некоторых конструкциях используются направляющие 2 видов:
- призматические для перемещения суппорта;
- плоская направляющая для хода задней бабки. В очень редких случаях её заменяет призматического типа.
Передняя бабка
Детали, расположенные в передней бабке служат для поддержки и вращения заготовки, во время её обработки. Здесь же находятся узлы, регулирующие скорость вращения детали. К ним относятся:
- шпиндель;
- 2 подшипника;
- шкив;
- коробка скоростей, отвечающая за регулировку скорости вращения.
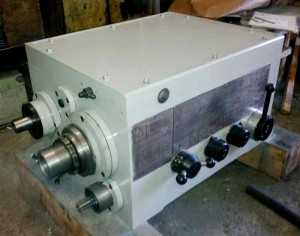
Передняя бабка отдельно от станка
Основная деталь передней бабки в устройстве токарного станка – шпиндель. С правой его стороны, обращённой в сторону задней бабки, есть резьба. К ней крепится патроны, удерживающие обрабатываемую деталь. Сам шпиндель устанавливается на два подшипника. Точность работ, выполняемых на станке, зависит от состояния шпиндельного узла.
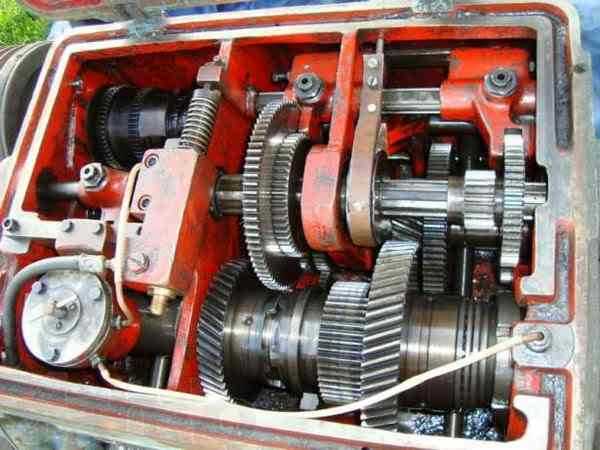
Коробка скоростей вид сверху
В передней бабке находится гитара сменных шестерен, которая предназначается для передачи вращения и крутящего момента с выходного вала коробки скоростей на вал коробки подач для нарезания различных резьб. Наладка подачи суппорта осуществляется путем подбора и перестановки различных зубчатых колес.
Шпиндель
Маловероятно, что ещё можно встретить устройство токарного станка по металлу с монолитным шпинделем. Современные станки имеют полые модели, но это не упрощает требований предъявляемых к ним. Корпус шпинделя должен выдерживать без прогибов:
- детали с большим весом;
- предельное натяжение ремня;
- нажим резца.
Особые требования предъявляются к шейкам, на которые устанавливаются в подшипники. Шлифовка их должна быть правильной и чистой, шероховатость поверхности не более Ra = 0,8.
Шпиндель
В передней части отверстие имеет конусную форму.
Подшипники, шпиндель и ось должны при работе создавать единый механизм, не имеющий возможности создавать лишних биений, которые могут получаться при неправильной расточке отверстия в шпинделе или небрежной шлифовке шеек. Наличие люфта между подвижными частями станка приведут к неточности в обработке заготовки.
Устойчивость шпинделю придают подшипники и механизм регулировки натяга. К правому подшипнику он крепится посредством расточенной, по форме шейки, бронзовой втулки. Снаружи её расточка совпадает с гнездом на корпусе передней бабки. Втулка имеет одно сквозное отверстие и несколько надрезов. Крепится втулка, в гнезде передней бабки гайками, накрученными на её резьбовые концы. Гайки крепления втулки используются для регулировки натяга разрезного подшипника.
За изменение скорости вращения отвечает коробка скоростей. Справа к шкиву присоединяется зубчатая шестерня, справа от шкива шестерня насажена на шпиндель. За шпинделем имеется валик со свободно вращающейся втулкой с ещё 2 шестернями. Через шейку, закреплённому в кронштейнах валику, передаётся вращательное движение. Разный размер шестерней позволяет варьировать скорость вращения.
Перебор увеличивает количество рабочих скоростей токарного станка вдвое. Строение токарного станка по металлу с использованием перебора позволяет выбрать среднюю скорость между базовыми. Для этого достаточно перекинуть ремень с одной передачи на следующую или установить рычаг в соответствующее положение, в зависимости от конструкции станка.
Шпиндель получает вращение от электродвигателя через ременную передачу и коробку скоростей.
Механизм подачи
Механизм подачи сообщает суппорту необходимое направление движения. Задаётся направление трензелем. Сам трензель находится в корпусе передней бабки. Управление им происходит посредством наружных рукояток. Кроме направления можно изменять и амплитуду движения суппорта при помощи сменных шестерней разного количества зубьев или коробки подач.
В схеме станков с автоматической подачей имеются ходовые винт и валик. При проведении работ высокой точности исполнения используется ходовой винт. В остальных случаях – валик, что позволяет дольше сохранить винт в идеальном состоянии для выполнения сложных элементов.
Суппорт
Верхняя часть суппорта – место крепления резцов и другого токарного инструмента, необходимого для обработки различных деталей. Благодаря подвижности суппорта резец плавно перемещается в направлении, необходимом для обработки заготовки, от места, где суппорт с резцом и располагался в начале работы.
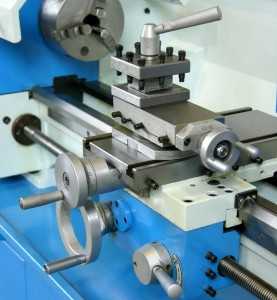
Суппорт
При обработке длинных деталей ход суппорта вдоль горизонтальной линии станка должен совпадать с длиной обрабатываемой заготовки. Такая потребность определяет возможности суппорта передвигаться в 4 направлениях относительно центральной точки станка.
Продольные движения механизма происходят по салазкам – горизонтальным направляющим станины. Поперечная подача резца осуществляется второй частью суппорта, передвигающейся по горизонтальным направляющим.
Поперечные (нижние) салазки служат основой поворотной части суппорта. С помощью поворотной части суппорта задаётся угол расположения заготовки относительно фартука станка.
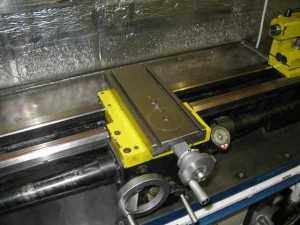
Поперечные салазки
Фартук
Фартук, как и передняя бабка, скрывает за своим корпусом необходимые для приведения в движение механизмов станка узлы, связывающие суппорт с зубчатой рейкой и ходовым винтом. Рукоятки управления механизмами фартука вынесены на корпус, что упрощает регулировку хода суппорта.
Задняя бабка
Задняя бабка подвижная, она используется для закрепления детали на шпинделе. Состоит из 2 частей: нижней – основной плиты и верхней, удерживающей шпиндель.
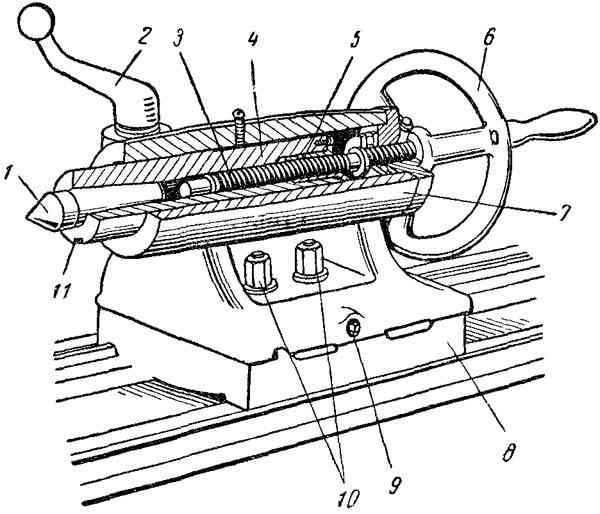
Задняя бабка в разрезе
Подвижная верхняя часть движется по нижней перпендикулярно горизонтальной оси станка. Это необходимо при точении конусообразных деталей. Через стенку бабки проходит вал, он может поворачиваться рычагом на задней панели станка. Крепление бабки к станине производится обычными болтами.
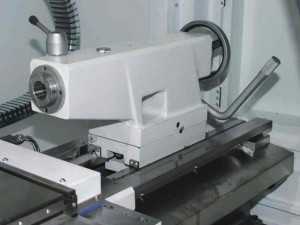
Задняя бабка
Индивидуален по своей компоновке каждый токарный станок, устройство и схема могут несколько отличаться в деталях, но в малых и средних станках такой вариант встречается наиболее часто. Компоновки и схемы тяжёлых больших токарных станков отличается в зависимости от их назначения, они узкоспециализированные.
Если вы нашли ошибку, пожалуйста, выделите фрагмент текста и нажмите Ctrl+Enter.
stankiexpert.ru
Основные части и узлы токарного станка
Основные части и узлы токарного станка
Категория:
Токарное дело
Основные части и узлы токарного станка
Токарный станок, оснащенный специальным устройством для нарезания резьбы, называется токарно-винторезным.
На рис. 1 изображен общий вид токарно-винторезного станка 1К62.
Станина — массивное чугунное основание, на котором смонтированы основные механизмы станка. Верхняя часть станины имеет две плоские и две призматические направляющие, по которым перемещаются суппорт и задняя бабка. Станина установлена на двух тумбах. Передняя бабка — чугунная коробка, внутри которой расположены главный рабочий орган станка — шпиндель и коробка скоростей. Шпиндель представляет собой полый вал. На правом конце шпинделя крепятся приспособления, зажимающие заготовку. Шпиндель получает вращение от расположенного в левой тумбе электродвигателя через клиноременную передачу и систему зубчатых колес и муфт, размещенных внутри передней бабки. Этот механизм называется коробкой скоростей и позволяет изменять частоту вращения (число оборотов в минуту) шпинделя.
Суппорт — устройство для закрепления резца и обеспечения движения подачи, т. е. перемещения резца в различных направлениях. Движение подачи может осуществляться вручную или механически. Механическое движение подачи суппорт получает от ходового вала или ходового винта (при нарезании резьбы).
Суппорт состоит из каретки, которая перемещается по направляющим станины, фартука, в котором расположен механизм преобразования вращательного движения ходового вала и ходового винта в прямолинейное движение суппорта, механизма поперечных салазок, механизма резцовых (верхних) салазок, механизма резцедержателя.
Коробк а подач представляет собой механизм, передающий вращение от шпинделя к ходовому валу или ходовому винту. Она позволяет изменять скорость движения подачи суппорта (величину подачи). Вращательное движение в коробке подач передается от шпинделя через реверсивный механизм и гитару со сменными зубчатыми колесами. Гитара предназначена для настройки станка на требуемую величину подачи или шаг нарезаемой резьбы путем установки соответствующих сменных зубчатых колес. Задняя бабка предназначается для поддержания конца длинных заготовок в процессе обработки, а также для закрепления и подачи стержневых инструментов (сверл, зенкеров, разверток).
1. ОБЩИЙ ВИД ТОКАРНО-ВИНТОРЕЗНОГО СТАНКА 1К62: 1 — передняя бабка с коробкой скоростей, 2 — гитара сменных колес, 3 — коробка подач, 4 — станина, 5 — фартук, 6 — суппорт, 7 — задняя бабка, 8 — шкаф с электрооборудованием
Электрооборудование станка размещено в шкафу. Включение и выключение электродвигателя, пуск и остановка станка, управление коробкой скоростей и коробкой подач, управление механизмом фартука и т. д. производится соответствующими органами управления (рукоятками, кнопками, маховичками). Для закрепления заготовок на токарном станке применяют: патроны, планшайбы, цанги, центры, хомутики, люнеты, оправки. Для контроля точности обработки деталей токарь использует штангенциркули, микрометры, калибры, шаблоны, угломеры и другие измерительные инструменты.
Реклама:
Читать далее:
Понятие о процессе образования стружки
Статьи по теме:
pereosnastka.ru
Основные части и узлы токарного станка
⇐ ПредыдущаяСтр 13 из 16Следующая ⇒Токарные станки предназначены для получения из заготовок различных деталей, имеющих форму тел вращения. Если на станке имеется устройство для нарезания резьбы, то такой станок называется токарно-винторезным. На рис. 3 изображен общий вид то карновинторезного станка модели 1К62, указаны основные части, узлы и органы управления . Станина 4 массивное чугунное основание, на котором смонтированы все основные узлы станка. Верхняя часть станины имеет две плоские и две призматические направляющие, по которым могут перемещаться подвижные узлы стайка. Станина установлена на двух тумбах. Передняя бабка I .-чугунная коробка, внутри которой расположен главный рабочий орган станка шпиндель, представляющий собой полый вал, на правом конце которого крепятся приспособления, зажимающие заготовку, например патрон. Шпиндель получает вращение от расположенного в левой тумбе электродвигателя через клиноременную передачу и систему зубчатых колес и муфт, размещенных внутри передней бабки. Механизм (т. е. система зубчатых колес и муфт), который позволяет изменять числа оборотов шпинделя, называют коробкой скоростей.
Суппорт 6 устройство для закрепления резца, обеспечения движения подачи, т. е. перемещения резца в различных направлениях. Движения подачи могут осуществляться вручную и механически. Механическое движение подачи суппорт получает от ходового винта и ходового вала. Фартук 5 система механизмов, преобразующих вращательное движение ходового винта и ходового вала в прямолинейное движение суппорта. Коробка подач 3 механизм, передающий вращение ходовому винту и ходовому валу и изменяющий величину подачи. Вращательное движение в коробку подач передается от шпинделя с помощью реверсивного механизма и гитары со сменными зубчатыми колесами. Гитара 2 предназначается для настройки станка на требуемую подачу подбором соответствующих сменных зубчатых колес. Задняя бабка 7 предназначена для поддерживания правого конца длинных заготовок в процессе обработки, а также закрепления сверл, зенкеров и разверток. Электропривод станка получает электроэнергию от сети промышленного тока. Общее включение станка производится пакетным выключателем, расположенным на специальном щите. Электрооборудование станка размещается в шкафу 8. Включение и выключение электродвигателя, пуск и остановка станка, управление механизмами станка осуществляют соответствующими кнопками, рукоятками, маховичками. В качестве режущего инструмента при работе на токарно-винторезном станке используют различные типы резцов, а также сверла, зенкеры, развертки, метчики, плашки. При работе на токарном станке применяют различные приспособления для закрепления заготовки: различной конструкции патроны, планшайбы, цанги, центры, хомутики, люнеты, оправки. К станку прилагается комплект ключей и других принадлежностей. Для контроля точности обработки токарь использует штангенциркули, микрометры, предельные калибры, шаблоны, угломеры и другие измерительные инструменты. Более подробные сведения о станке, режущих и измерительных инструментах и приспособлениях приведены в последующих главах книги.
Фрезерование поверхностей заключается в снятии стружки вращающимися многолезвийными инструментами — фрезами, режущие кромки зубьев которых находятся в прерывистом контакте с обрабатываемым материалом.
Различают следующие основные виды фрезерования:
1) осевое цилиндрическое фрезерование цилиндрическими, дисковыми и концевыми фрезами;
2) торцовое фрезерование торцовыми, дисковыми и концевыми фрезами;
3) двустороннее фрезерование дисковыми, концевыми и торцовыми фрезами;
4) трехстороннее фрезерование концевыми и шпоночными фрезами; 5) комбинированное фрезерование наборами фрез;
6) фасонное фрезерование фасонными цилиндрическими и концевыми фрезами.
Фрезерование применяют для обработки поверхностей различных форм (плоскостей, фасонных поверхностей и др.).
Чаще всего фрезерованием обрабатывают плоскости. Для этой цели применяют цилиндрические или торцовые фрезы.
Первые бывают с прямыми (рис. 109, а) или с винтовыми (рис. 109, б) зубьями.
При применении фрез последнего вида фрезерование протекает более плавно и спокойно вследствие постепенного врезания зубьев в металл.
Торцовые фрезы подразделяются на хвостовые и насадные (рис. 109, в). Последние при их значительных размерах делают с вставными зубьями (фрезерные головки, см. рис. 109, г), что позволяет расходовать меньше дорогих инструментальных сталей и заменять, в случае надобности, отдельные зубья фрезы, корпус которой делается из относительно дешевой стали (например, стали 45).Для фрезерования пазов применяют дисковые, а также концевые цилиндрические фрезы. Дисковые фрезы подразделяются на следующие виды: двусторонние, трехсторонние и пазовые (рис. 109, в—ж). Первые имеют зубья на периферии и на одном из торцов; вторые, кроме того, и на втором торце.
Регулируемые трехсторонние фрезы состоят из двух половин, между которыми помещают прокладки для регулировки толщины фрезы, уменьшающейся после ее заточки.
Пазовые фрезы имеют зубья только на периферии. Концевые «пальцевые» цилиндрические фрезы применяют в тех случаях, когда по каким-либо причинам дисковыми фрезами нельзя обрабатывать: фрезерование пазов дисковыми, более жесткими, фрезами производительнее, чем концевыми.
Для фрезерования углублений, канавок, фасонных поверхностей применяют угловые фасонные фрезы, которые могут быть насадными и хвостовыми (рис. 109, е).
Существуют также особые фрезы для нарезания зубчатых профилей, нарезания резьб и др. (рис. 109, ж, з, и).
Для изготовления фрез применяют быстрорежущие стали (Р18, Р9), сталь 9ХС, а также оснащают фрезы пластинками из твердых сплавов.
Геометрическая форма каждого зуба фрезы в принципе сходна с геометрической формой токарного резца, однако условия работы зубьев фрез хуже, чем токарных резцов, вследствие прерывистого контакта зубьев фрезы с обрабатываемой поверхностью. Резание металла при фрезеровании протекает менее спокойно, чем при постоянном контакте режущей кромки резца с обрабатываемой поверхностью, что имеет место при точении. Вместе с тем условия воздействия тепла, возникающего при резании фрезой, на ее зубья меньше, чем при точении, так как каждый зуб несколько охлаждается при выходе из контакта с обрабатываемым металлом.
Геометрические параметры зуба фрезы показаны на рис. 110; здесь передний угол γ = 5 ÷ 15°, задний угол α = 10 ÷ 30° и угол заострения β. У фрез, оснащенных пластинками из твердых сплавов, часто передние углы имеют отрицательное значение, а угол заострения β получается до 90°. Чем больше этот угол, тем прочнее зуб фрезы и лучше условия теплоотвода в тело инструмента. Скорость резания v при фрезеровании равна окружной скорости вращения инструмента. Глубина резания t — это слой металла, снимаемый за один проход (рис. 111).
Рис. 111. Схема фрезерования
Шириной фрезерования В называют длину части поверхности, находящуюся в контакте с режущими элементами фрезы и измеряемую в направлении, перпендикулярном подаче.
Подача — это перемещение обрабатываемой заготовки относительно инструмента или, наоборот, фрезы относительно заготовки. Различают подачу на один зуб фрезы (sz), подачу на один оборот фрезы (sоб) и подачу в минуту (sмин):
sмин=sоб * n =sz * z *n мм/мин,
гдеz — число зубьев фрезы;
n — число оборотов фрезы в минуту;
n = (1000*v) / π*d об/мин;
гдеv — скорость резания в м/мин;
d— диаметр фрезы в мм.
Скорость резания зависит от обрабатываемого материала, условий обработки, глубины резания, подачи, стойкости фрезы и т. д. и назначается по нормативам режима резания или подсчитывается по эмпирическим формулам.
При фрезеровании инструментами с периферическими зубьями стружка имеет вид запятой (рис. 112). Ее толщина не равномерна и изменяется по мере поворота зуба относительно обрабатываемой поверхности.
Рис. 113. Попутное (а) и встречное (б) фрезерование
Различают попутное (по подаче) и встречное (против подачи) фрезерование. В первом случае (рис. 113) направление подачи и вращения фрезы совпадают, во втором они направлены противоположно.
Чаще применяют второй способ, при котором толщина стружки постепенно увеличивается и достигает наибольшего значения при выходе зуба фрезы из контакта с обрабатываемой поверхностью.
Площадь поперечного сечения стружки в каждый момент резания — величина переменная.
Силы резания, действующие на зубья фрезы, имеют различные направления и разную величину в зависимости от направления подачи по отношению к направлению вращения фрезы, т. е. от способа фрезерования (встречное или попутное), а также от рода фрезерования (торцовыми фрезами или фрезами с периферическими зубьями). При встречном фрезеровании цилиндрическими фрезами сила резания Р, действующая на каждый зуб фрезы, может быть разложена на две составляющих: касательную к фрезеPz и радиальную Рy, направленную к центру фрезы. Касательная сила создает крутящий момент M = (Pz* d )/2 кГмм,
где d — диаметр фрезы в мм.
Сверление
Сверление — вид механической обработки материалов резанием, при котором с помощью специального вращающегося режущего инструмента (сверла) получают отверстия различного диаметра и глубины, или многогранные отверстия различного сечения и глубины.
Назначение сверления
Сверление – необходимая операция для получения отверстий в различных материалах при их обработке, целью которой является:
- Изготовление отверстий под нарезание резьбы, зенкерование, развёртывание или растачивание.
- Изготовление отверстий (технологических) для размещения в них электрических кабелей, анкерных болтов, крепёжных элементов и др.
- Отделение (отрезка) заготовок из листов материала.
- Ослабление разрушаемых конструкций.
- Закладка заряда взрывчатого вещества при добыче природного камня.
Сверление цилиндрических отверстий, а также сверление многогранных (треугольных, квадратных, пяти- и шестигранных, овальных) отверстий выполняют с помощью специальных режущих инструментов — свёрл. Свёрла в зависимости от свойств обрабатываемого материала изготавливаются нужных типоразмеров из следующих материалов:
- Углеродистые стали (У8,У9,У10,У12 и др): Сверление и рассверливание дерева, пластмасс, мягких металлов.
- Низколегированные стали (Х,В1,9ХС,9ХВГ и др): Сверление и рассверливание дерева, пластмасс, мягких металлов. Повышенная по сравнению с углеродистыми теплостойкость (до 250 °C) и скорость резания.
- Быстрорежущие стали (Р9,Р18,Р6М5,Р9К5 и др): Сверление всех конструкционных материалов в незакалённом состоянии. Теплостойкость до 650 °C.
- Свёрла, оснащенные твёрдым сплавом, (ВК3,ВК8,Т5К10,Т15К6 и др): Сверление на повышенных скоростях незакалённых сталей и цветных металлов. Теплостойкость до 950 °C. Могут быть цельными, с напайными пластинами, либо со сменными пластинами (крепятся винтами)
- Свёрла, оснащённые боразоном: Сверление закалённых сталей и белого чугуна, стекла, керамики, цветных металлов.
- Свёрла, оснащённые алмазом: Сверление твёрдых материалов, стекла, керамики, камней.
Операции сверления производятся на следующих станках:
- Вертикально-сверлильные станки: Сверление — основная операция.
- Горизонтально-сверлильные станки: Сверление — основная операция.
- Вертикально-расточные станки: Сверление — вспомогательная операция.
- Горизонтально-расточные станки: Сверление — вспомогательная операция.
- Вертикально-фрезерные станки: Сверление — вспомогательная операция.
- Горизонтально-фрезерные станки: Сверление — вспомогательная операция.
- Универсально-фрезерные станки: Сверление — вспомогательная операция.
- Токарные станки: Сверло неподвижно, а обрабатываемая заготовка вращается.
- Токарно-затыловочные станки: Сверление — вспомогательная операция. Сверло неподвижно.
- Токарно-револьверные станки: Сверление — вспомогательная операция. Сверло может быть неподвижно (статический блок) или вращаться (приводной блок)
И на ручном оборудовании:
- Механические дрели: Сверление с использованием мускульной силы человека.
- Электрические дрели: Сверление на монтаже переносным электроинструментом (в том числе ударно-поворотное сверление).
- перфораторы
Для облегчения процессов резания материалов применяют следующие меры:
- Охлаждение: Смазочно-охлаждающие жидкости и газы(вода, эмульсии, олеиновая кислота, углекислый газ, графит и др.)
- Ультразвук: Ультразвуковые вибрации сверла увеличивают производительность и дробление стружки.
- Подогрев: Подогревом ослабляют твёрдость труднообрабатываемых материалов.
- Удар: При ударно-поворотном сверлении (бурении) камня, бетона.
Виды сверления [править]
- Сверление цилиндрических отверстий.
- Сверление многогранных и овальных отверстий.
- Рассверливание цилиндрических отверстий (увеличение диаметра).
- Центровка: высверливание небольшого количества материала для позиционирования другого сверла (например, при глубоком сверлении) или для фиксирования детали задним центром.
- Глубокое сверление: Сверление на глубину 5 и более диаметров отверстия. Часто требует специальных технических решений.
Охлаждение при сверлении [править]
Большой проблемой при сверлении является сильный разогрев сверла и обрабатываемого материала из-за трения. В месте сверления температура может достигать нескольких сотен градусов Цельсия.
При сильном разогреве материал может начать гореть или плавиться. Многие стали при сильном разогреве теряют твердость, в результате режущие кромки стальных свёрл быстрее изнашиваются, из-за чего трение только усиливается, что в итоге приводит к быстрому выходу свёрл из строя и резкому снижению эффективности сверления. Аналогично, при использовании твердосплавного сверла или сверла со сменными пластинами, твердый сплав при перегреве теряет твердость, и начинается пластическая деформация режущей кромки, что является нежелательным типом износа.
Для борьбы с разогревом применяют охлаждение с помощью охлаждающих эмульсий или смазочно-охлаждающих жидкостей (СОЖ). При сверлении на станке часто возможно организовать подачу жидкости непосредственно к месту сверления. Подача охлаждающей жидкости также может осуществляться через каналы в самом сверле, если это позволяет станок. Такие каналы делаются во многих цельных сверлах и во всех корпусных. Внутренняя подача СОЖ необходима при сверлении глубоких отверстий (глубиной 10 и более диаметров). При этом важно не столько охлаждение, сколько удаление стружки. Давление СОЖ вымывает стружку из зоны резания, что позволяет избежать её пакетирования или повторного резания. Если в таком случае невозможно организовать подачу СОЖ, то приходится осуществлять сверление с периодическими выводами сверла для удаления стружки. Такой метод крайне низкопроизводителен.
При сверлении ручным инструментом сверление время от времени прерывают и окунают сверло в емкость с жидкостью.
18) Шлифовáние — механическая или ручная операция по обработке твёрдого материала (металл, стекло, гранит, алмаз и др.). Разновидность абразивной обработки, которая, в свою очередь, является разновидностью резания. Механическое шлифование обычно используется для обработки твёрдых и хрупких материалов в заданный размер с точностью до микрона . А также для достижения наименьшей шероховатости поверхности изделия допустимых ГОСТом. В качестве охлаждения обычно используют смазочно-охлаждающие жидкости (СОЖ).
Типы шлифовального инструмента [править]
- Эльборовые круги на керамических связках применяется для обработки высокоточных деталей из сталей и сплавов твердостью HRC>50, износостойких покрытий.
- Эльборовый инструмент на органических связках, в том числе отрезные круги, применяются, главным образом, на операциях заточки инструмента (свёрла, фрезы, резцы и т. д.) из быстрорежущих сталей, вышлифовки стружечных канавок, отрезки и прорезки пазов.
- Алмазный инструмент на органических связках, в том числе отрезные круги, применяются для заточки режущего инструмента из твёрдых сплавов, деталей из композита и керамики. Алмазные отрезные круги применяются для высокоточной резки твёрдого сплава, технической керамики, цветных металлов, кварцевого стекла, ферритов, кварца.
- Алмазный инструмент на керамических и металлических связках применяется при шлифовании твердосплавных деталей (пуансонов, калибров, валков и др.), для шлифования режущих пластин из композитов, деталей из сочетания стали и твёрдого сплава, а также для правки шлифовальных кругов.
- Алмазные отрезные круги на металлических связках используются для обработки и резки стекла, хрусталя, драгоценных и полудрагоценных камней. Бруски из синтетического алмаза на металлической связке используются для чернового и чистового хонингования деталей из чугуна и стали.
- Специальный абразивный инструмент, в том числе высокопористый, применяют в производстве турбин при шлифовании деталей из вязких, высокопластичных сплавов (жаропрочных, титановых), для бесприжогового производительного шлифования зубчатых колес, а также для шлифования цветных сплавов, полимерных покрытий на валах бумагоделательных машин.
- Шкурка и паста из эльбора и алмаза используются для финишных операций, притирки и полирования, с целью получения поверхностей с минимальной шероховатостью (Ra=0,08-0,02 мкм).
Хонингование — вид абразивной обработки материалов с применением хонинговальных головок (хонов). В основном применяется для обработки внутренних цилиндрических поверхностей путём совмещения вращательного и возвратно-поступательного движения хона с закреплёнными на нём раздвижными абразивными брусками с обильным орошением обрабатываемой поверхности смазочно-охлаждающей жидкостью. Один из видов чистовых и отделочных обработок резанием. Позволяет получить отверстие с отклонением от цилиндричности до 5 мкм и шероховатостью поверхности Ra=0,63÷0,04.
Хонингование наружных поверхностей осуществляется на специализированных станках (горизонтально-хонинговальных) или модернизированных (шлифовальных, горизонтально-расточных), производительность при этом по сравнению с суперфинишированием в 2—4 раза выше вследствие бо́льшего количества брусков и бо́льших давлений.
Области применения хонингования [править]
Обработка отверстий в различных деталях в том числе в деталях двигателя (отверстий блоков цилиндров, гильз цилиндров, отверстий кривошипной и поршневой головок шатунов, отверстий шестерен) и т. д. Хонинговочная сетка является побочным эффектом этого высокоточного метода шлифования. По её характеру можно судить о правильности обработки, точности соблюдения технологии. Особенно это актуально при работе ручным инструментом. Она также способствует лучшему смазыванию при работе пары трения . При обработке хонингованием обеспечивается стабильное получение точных отверстий и требуемых параметров шероховатости обработанной поверхности.
Инструмент для хонингования
При хонинговании используют бруски изготовленный методом прессования на керамической и бакелитовой основе. Абразивным материалом являются белый электрокорунд марок 23А, 24А, 25А и зеленый карбид кремния марок 63С, 64С, а также в качестве абразива используется алмаз и эльбор. Для хонингования используют бруски 2-х типов: БКв – квадратные, БП – плоские. Размеры: длина от 15 до 200 мм ширина и высота от 2 до 80 мм.
1 2 3 1
а) в)
3 1
б) г)
25)
Ковка — это высокотемпературная обработка различных металлов (железо, медь и её сплавы, титан, алюминий и его сплавы), нагретых до ковочной температуры. Для каждого металла существует своя ковочная температура, зависящая от физических (температура плавления, кристаллизация) и химических (наличия легирующих элементов) свойств. Для железа температурный интервал 1250–800 °С, для меди 1000–650 °С, для титана 1600—900 °С, для алюминиевых сплавов 480–400 °С.
Различают:
- ковка на молотах (пневматических, паровых и гидравлических)
- ручная ковка
- штамповка
Изделия и полуфабрикаты, получаемые ковкой, называют поковкой.
При ковке в штампах металл ограничен со всех сторон стенками штампа. При деформации он приобретает форму этой полости (см. Штампование, Ротационная ковка).
При свободной ковке (ручной и машинной) металл не ограничен совсем или же ограничен с одной стороны. При ручной ковке непосредственно на металл или на инструмент воздействуют кувалдой или молотом.
Свободную ковку применяют также для улучшения качества и структуры металла. При проковке металл упрочняется, завариваются так называемые несплошности и размельчаются крупные кристаллы, в результате чего структура становится мелкозернистой, приобретает волокнистое строение.
Машинную ковку выполняют на специальном оборудовании — молотах с массой падающих частей от 40 до 5000 кг или гидравлических прессах, развивающих усилия 2–200 МН (200–20000 тс), а также на ковочных машинах. Изготовляют поковки массой 100 т и более. Для манипулирования тяжёлыми заготовками при ковке используют подъёмные краны грузоподъёмностью до 350 т, кантователи и специальные манипуляторы.
Ковка является одним из экономичных способов получения заготовок деталей. В массовом и крупносерийном производствах преимущественное применение имеет ковка в штампах, а в мелкосерийном и единичном — свободная ковка.
При ковке используют набор кузнечного инструмента, с помощью которого заготовкам придают требуемую форму и размеры.
Основные операции ковки [править]
- осадка
- высадка
- протяжка
- обкатка
- раскатка
- прошивка и др.
Ковка может быть горячей и холодной.
Горячая ковка создаётся методом нагревания металла и придания ему нужной формы.
В то же время холодная ковка создается без нагрева металла. При помощи сгиба либо вручную, либо на специальном станке, также в создании узора участвует болгарка (обрезание концов квадратного либо круглого прута), и сварочный аппарат, который собирает детали узора вместе.
Область применения ковки — мелкосерийное и единичное производство.
Достоинства ковки:
- высокие механические свойства металла по сравнению с литым;
- возможность получения крупных поковок массой 250 и более тонн, длиной 10 и более метров;
- сравнительно невысокие усилия деформирования при изготовлении крупных по массе поковок;
- применение универсальных машин и универсального инструмента приводит к уменьшению затрат при изготовлении различного типа поковок.
Недостатки ковки:
- низкая производительность;
- большие припуски, допуски, напуски, что вызывает большой объем механической обработки.
Горячая объёмная штамповка — это вид обработки металлов давлением, при которой формообразование поковки из нагретой заготовки осуществляют с помощью специального инструмента — штампа. Течение металла ограничивается поверхностями полостей (а также выступов), изготовленных в отдельных частях штампа, так что в конечный момент штамповки они образуют единую замкнутую полость (ручей) по конфигурации поковки. В качестве заготовок для горячей штамповки применяют прокат круглого, квадратного, прямоугольного профилей, а также периодический. При этом прутки разрезают на отдельные (мерные) заготовки, хотя иногда штампуют из прутка с последующим отделением поковки непосредственно на штамповочной машине.
Применение объемной штамповки оправдано при серийном и массовом производстве. При использовании этого способа значительно повышается производительность труда, снижаются отходы металла, обеспечиваются высокие точность формы изделия и качество поверхности. Штамповкой можно получать очень сложные по форме изделия, которые невозможно получить приемами свободной ковки.
Штамповка в открытых штампах характеризуется переменным зазором между подвижной и неподвижной частями штампа. В этот зазор вытекает часть металла – облой, который закрывает выход из полости штампа и заставляет остальной металл заполнить всю полость. В конечный момент деформирования в облой выжимаются излишки металла, находящиеся в полости, что позволяет не предъявлять высокие требования к точности заготовок по массе. Штамповкой в открытых штампах можно получить поковки всех типов.
Штамповка в закрытых штампах характеризуется тем, что полость штампа в процесс деформирования остается закрытой. Зазор между подвижной и неподвижной частями штампа постоянный и небольшой, образование в нем облоя не предусмотрено. Устройство таких штампов зависит от типа машины, на которой штампуют. Например, нижняя половина штампа может иметь полость, а верхняя – выступ (на прессах), или верхняя – полость, а нижняя – выступ (на молотах). Закрытый штамп может иметь две взаимно перпендикулярные плоскости разъема. При штамповке в закрытых штампах необходимо строго соблюдать равенство объемов заготовки и поковки, иначе при недостатке металла не заполняются углы полости штампа, а при избытке размер поковки по высоте будет больше требуемого. Отрезка заготовок должна обеспечивать высокую точность.
Преимущества и недостатки.
Масса слитков составляет от 200 кг до 350т. Наибольшее
распространение имеют слитки массой более 1 т. Для ковки
применяются слитки многогранные (чаще всего шести восьмигранные)
или цилиндрические.
По способу изготовления поковок различают свободную ковку и
горячую объёмную штамповку.
Горячая объёмная штамповка – это вид обработки материалов
давлением, при котором формообразование поковки из нагретой заготовки
осуществляют с помощью специального инструмента – штампа. Течение металла
ограничивается поверхностями плоскостей, изготовленных в отдельных частях
штампа, так что в конечный момент штамповки они образуют единую замкнутую
плоскость (ручей) по конфигурации поковки.
В качестве заготовок для горячей штамповки в подавляющем
большинстве случаев применяют прокат круглого квадратного, прямоугольного
профилей, а также периодический. При этом прутки разрезают на отдельные
заготовки, хотя иногда штампуют и от прутка с последующем отделением
поковки непосредственно на штамповочной машине. Заготовки отрезают от
прутка различными способами: на кривошипных пресс-ножницах, газовой резкой
и т д.
По сравнению с ковкой штамповка имеет ряд преимуществ. Горячей
объёмной штамповкой можно получать без напусков поковки сложной
конфигурации, которые ковкой изготовить без напусков нельзя, при этом
допуски на штамповочную поковку в 3 – 4 раза меньше, чем на кованную. В
следствии этого значительно сокращается объём последующей механической
обработки, штамповочные поковки обрабатывают только в местах сопряжения с
другими деталями, и эта обработка может сводиться только к шлифованию.
Производительность штамповки значительно выше – составляет десятки
и сотни штамповок в час.
В то же время штамповочный инструмент штамп – дорогостоящий
инструмент и является пригодным только для изготовления какой то одной,
конкретной поковки. В связи с этим штамповка экономически целесообразна
лишь при изготовлении достаточно больших партий одинаковых поковок.
Кроме того, для объёмной штамповке поковок требуется гораздо
больше усилий деформирования, чем для ковки таких же поковок. Поковки
массой в несколько сот килограммов для штамповки считается крупными. В
основном штампуют поковки массой 20 – 30 килограмм. Но благодаря созданию
мощных машин в отдельных случаях штампуют поковки массой до трёх тонн.
Горячей объёмной штамповкой изготовляют заготовки для
ответственных деталей автомобилей, тракторов, сельскохозяйственных машин,
самолётов, железнодорожных вагонов, станков и так далее.
Конфигурация поковок чрезвычайно разнообразна, в зависимости от
неё поковки обычно разделяются на группы. Например, штампованные поковки,
можно разделить на 2 группы: удлинённой формы, характеризующиеся большим
отношением длинны к ширине, и круглые или квадратные в плане.
Наличие большого разнообразия форм и размеров штампованных
поковок, а также сплавов, из которых их штампуют, обуславливает
существование различных способов штамповки.
Так как характер течения металла в процессе штамповки определяется
типом штампа, то этот признак можно признать основным для классификации
способов штамповки. В зависимости от типа штампа выделяют штамповку в
открытых штампах и в закрытых штампах.
Штамповка в открытых штампах характеризуется переменным зазором
между подвижным и неподвижным частями штампа. В этот зазор вытекает
заусенец (облой), который закрывает выход из полости штампа и заставляет
металл целиком заполнить всю полость. В конечный момент формирования
заусенец выжимаются излишки металла, находящийся в плоскости, что позволяет
не предъявлять особо высоких требований к точности заготовок по массе.
Заусенец затем обрезается в специальных штампах. Штамповкой в открытых
штампах получают поковки всех типов.
Штамповка в закрытых штампах характеризуется тем, что полость
штампа в процессе деформирования остаётся закрытой. Зазор между подвижной и
не подвижной частями штампа при этом постоянный и большой, так что
образование заусенца в нём не предусматривается. Устройство таких штампов
зависит от типа машины, на которых штампуют. Закрытый штамп может быть с
одной или двумя взаимно перпендикулярными плоскостями разъёма, то есть
состоять из трёх частей.
При штамповке в закрытых штампах надо строго соблюдать равенство
объёмов заготовки и поковки, иначе при недостатке металла не заполняются
углы полости штампа, а при избытке размер поковки по высоте будет больше
нужного. Значит процесс получения заготовки усложняется, поскольку отрезка
заготовок должна сопровождаться высокой точностью. Существенным
преимуществом штамповки в закрытых штампах является уменьшение расхода
металла, поскольку нет отхода заусениц. Поковки полученные в закрытых
штампах имеют более благоприятную микроструктуру, так как волокна обтекают
контур поковки, а не прорезаются в месте выхода металла заусениц. При
штамповке в закрытых штампах металл деформируется в условиях всестороннего
неравномерного сжатия при больших зажимающих напряжениях, чем в открытых
штампах. Это позволяет получить большие степени деформации и штамповать
малопластичные сплавы.
К закрытой штамповке можно отнести штамповку выдавливанием и
прошивкой, так как штамп в этих случаях выполняют по типу закрытого и
отхода металла заусениц не предусматривает. Деформирование металла при
горячей штамповке вдавливанием и прошивкой происходит так же, как при
холодном прямом и обратном выдавливании.
infopedia.su
Основные части и узлы токарного станка — Студопедия.Нет
Токарный станок, оборудованный вспомогательным оборудованием для нарезания резьбы, называют токарно-винторезным станком. На рис. 1 схема общего вида токарно-винторезного станка 1К62.
Станина 4— массивное чугунное основание, где смонтированы основные механизмы станка. Верхняя часть станины состоит из двух призматических и двух плоских направляющих, по которым передвигаются задняя бабка и суппорт. Станина закреплена на двух тумбах.
Передняя бабка 1 — чугунная коробка, в которой находится главный рабочий орган станка — коробка скоростей и шпиндель.
Шпиндель – имеет вид полого вала. Справа на шпинделе крепятся приспособления, зажимающие заготовку. Шпиндель получает вращение от расположенного в левой тумбе электродвигателя через систему зубчатых колес, клиноременную передачу и муфты, которые размещены внутри передней бабки. Этот механизм называется коробкой скоростей и позволяет изменять частоту вращения (число оборотов в минуту) шпинделя. Суппорт 6 — механизм для обеспечения движения подачи и установки резца, т. е. передвижения резца в разные стороны. Движение подачи может производится механически или вручную. Механическое движение подачи к суппорту поступает от ходового винта или ходового вала (во время нарезании резьбы).Суппорт состоит из каретки, которая перемещается по направляющим станины, фартука, в котором расположен механизм преобразования вращательного движения ходового вала и ходового винта в прямолинейное движение суппорта, механизма поперечных салазок, механизма резцовых (верхних) салазок, механизма резцедержателя.Коробка подач 3 – это механизм, которые передает вращение от шпинделя к ходовому винту или ходовому валу. Она позволяет изменять скорость движения подачи суппорта (величину подачи). Вращательное движение в коробке подач передается от шпинделя через реверсивный механизм и гитару со сменными зубчатыми колесами.
51. Узлы консольно-фрезерных станков. Станина служит для крепления всех узлов и механизмов станка. Некоторые узлы станка (коробка скоростей, электродвигатель с ременной передачей, механизм передачи движения к коробке подач и шпиндель станка) расположены внутри станины и не видны. Другие узлы станка (консоль, коробка подач, хобот, стол, насос для подачи охлаждающей жидкости) находятся на наружных поверхностях станины.
Станина имеет коробчатую форму и усилена изнутри ребрами; на передней стенке ее расположены вертикальные направляющие (выполненные в виде «ласточкина хвоста») для консоли, а наверху — горизонтальные направляющие для хобота.
Хобот имеется у горизонтально- и универсально-фрезерных станков и служит для правильной установки и поддержки фрезерной оправки. Хобот установлен в горизонтальных направляющих на верхней части станины и может быть закреплен на любом расстоянии от ее зеркала, т. е. с различным вылетом (см. рис. 88). Для увеличения жесткости при обработке тяжелых деталей и при больших сечениях стружки применяют поддержки, которые связывают хобот с консолью.Консоль представляет собой жесткую чугунную отливку, установленную на вертикальных направляющих станины. Консоль перемещается по вертикальным направляющим станины и несет горизонтальные направляющие для салазок. Она поддерживается стойкой, в которой расположен телескопический винт для подъема и опускания консоли. Салазки являются промежуточным звеном между консолью и столом станка. По верхним направляющим салазок движется стол в продольном направлении, а сами салазки перемещаются в поперечном направлении по верхним направляющим консоли.Стол монтируется на направляющих салазок и перемещается в продольном направлении. Настоле укрепляются заготовки, зажимные и другие приспособления, для чего рабочая поверхность стола имеет продольные Т-образные пазы.Шпиндель. Для вращения режущего инструмента служит шпиндель, который получает движение от коробки скоростей. От точности изготовления шпинделя, от его прочности и жесткости зависит точность вращения оправки с надетой фрезой. Шпиндели фрезерных станков изготовляют из легированной стали марки 40Х и подвергают термической обработке.Консольно-фрезерные станки современной конструкции подобно станку 6Н82Г имеют отдельные электродвигатели для привода коробки скоростей и для привода коробки подач.Коробка скоростей предназначена для передачи вращения от шкива шпинделю и для изменения числа его оборотов при помощи переключения зубчатых колес.Коробка подач служит для изменения величины подач стола в вертикальном, продольном и поперечном направлениях.
.
studopedia.net
Токарный станок – принцип работы, описание :: ТОЧМЕХ
Современные токарные станки и токарные обрабатывающие центры.
Все части токарного станка установлены на прочной основе — станине. Та часть станка, которая держит и вращает деталь, называется передней бабкой. В ее корпусе имеется шпиндель со ступенчатым шкивом на одном конце и патроном — на другом. У мощных скоростных станков, которыми оснащены наши заводы, шкив заменен коробкой скоростей. На другом конце станины находится задняя бабка, которая удерживает правый конец детали при обработке в центрах. В верхней части корпуса задней бабки находится пиноль, двигающаяся влево и вправо с помощью маховичка с винтом и гайки.
В коническое отверстие в передней части пиноли вставляется центр. В случае надобности сюда же можно устанавливать сверла, развертки и другой инструмент. Заднюю бабку можно передвигать по направляющим станины, устанавливая ее на нужное расстояние, в зависимости от размеров обрабатываемой детали.
Между передней и задней бабками помещается суппорт с резцедержателем. Нижняя часть суппорта, называемая кареткой или продольными салазками, скользит по направляющим станины, перемещая резец вдоль обрабатываемой детали. Поперечное движение резца осуществляется с помощью поперечных салазок, в верхней части которых помещается поворотная часть суппорта. Она, как и станина, имеет направляющие, по которым двигаются верхние салазки суппорта с резцедержателем. Резцедержатель может быть устроен по-разному, это зависит от величины нагрузки, действующей на резец.
Для хорошего натяжения ремня у легкого настольного станка можно сделать приспособление, изображенное на рисунке. Ролик удерживает ремень в натянутом состоянии с помощью сильной пружины. Длина шпилек, соединяющих основание приспособления, должна быть несколько больше ширины шкива или равна ей. Ролик с боковинами перемещается по одной из шпилек, как по оси.
Современные токарные станки и токарные обрабатывающие центры
Токарные станки уже много веков являются основным производственным оборудованием. По статистике более 60% всех обрабатываемых деталей проходят через токарные станки. В последнее время эта доля стала еще больше — теперь на токарных станках проводится полная обработка деталей, включая фрезерование, сверление, нарезание резьбы и многое другое (например, гидростатическое накатывание). Таким образом, фактически на рынке начинают доминировать токарные обрабатывающие центры.
Токарные центры предназначены для комплексной обработки современным режущим инструментом с высокой скоростью сложных деталей различного профиля за одну установку: токарная, сверлильная, фрезерная обработка в одной операции. В автоматическом цикле на них можно обрабатывать наружные и внутренние поверхности деталей типа тел вращения со ступенчатым и криволинейным профилем: точение, растачивание конических и фасонных поверхностей, подрезка торцов, точение канавок, нарезание резьбы резцами, метчиками, плашками и др. в деталях типа крышек, фланцев, втулок, валиков, коротких осей, мелких корпусов, стаканов. Кромеобычной токарной обработки позволяют обрабатывать внецентровые отверстия (с продольным и поперечным расположением оси), фрезеровать канавки, лыски, криволинейные поверхности и др.
Основные технологические параметры токарных центров
Для современных токарных центров характерно:
- наибольший диаметр и длина обрабатываемой заготовки;
- наибольший диаметр проката, проходящего через отверстие шпинделя;
- диапазоны регулирования главного привода и подач.
Другие статьи по сходной тематике
tochmeh.ru
Основные части и узлы токарного станка
ТОКАРНОЕ ДЕЛО
7 ВИДЫ ПОВЕРХНОСТЕЙ, ПОЛУЧАЕМЫХ ТОКАРНОЙ ОБРАБОТКОЙ: |
/ — цилиндрическая, 2, 5 — конические, 3 — фасонная, 4 — плоская торцовая, 6— галтель (конструктивный элемент) |
Токарные станки предназначены для получения из заготовок различных деталей, имеющих форму тел вращения. Если на станке имеется устройство для нарезания резьбы, то такой станок называется токарно-винторезным. На рис. 3 изображен общий вид то- карно-винторезного станка модели 1К62, указаны основные части, узлы и органы управления *. Станина 4 — массивное чугунное основание, на котором смонтированы все основные узлы станка. Верхняя часть станины имеет две плоские и две призматические направляющие, по которым могут перемещаться подвижные узлы стайка. Станина установлена на двух тумбах.
Передняя бабка /-.-чугунная коробка, внутри которой расположен главный рабочий орган станка — шпиндель, представляющий собой полый вал, на правом конце которого крепятся приспособления, зажимающие заготовку, например патрон. Шпиндель получает вращение от расположенного в левой тумбе электродвигателя через клиноременную передачу и систему зубчатых колес и муфт, размещенных внутри передней бабки. Механизм (т. е. система зубчатых колес и муфт), который позволяет изменять числа оборотов шпинделя, называют коробкой скоростей. Суппорт 6 — устройство для закрепления резца, обеспечения движения подачи, т. е. перемещения резца в различных направлениях. Движения подачи могут осуществляться вручную и механически. Механическое движение подачи суппорт получает от ходового винта и ходового вала. Фартук 5 — система механизмов, преобразующих вращательное движение ходового винта и ходового вала в прямолинейное движение суппорта. Коробка подач 3 — механизм, передающий вращение ходовому винту и ходовому валу и изменяющий величину подачи. Вращательное движение в коробку подач передается от шпинделя с помощью реверсивного механизма и гитары со сменными зубчатыми колесами.
Гитара 2 предназначается для настройки станка на требуемую подачу подбором соответствующих сменных зубчатых колес.
Задняя бабка 7 предназначена для поддерживания правого конца длинных заготовок в процессе обработки, а также закрепления сверл, зенкеров и разверток.
Электропривод станка получает электроэнергию от сети промышленного тока. Общее включение станка производится пакетным выключателем, расположенным на специальном щите. Электрооборудование станка размещается в шкафу 8.
Включение и выключение электродвигателя, пуск и остановка станка, управление механизмами станка осуществляют соответствующими кнопками, рукоятками, маховичками. В качестве режущего инструмента при работе на токарно-винторезном станке используют различные типы резцов, а также сверла, зенкеры, развертки, метчики, плашки.
При работе на токарном станке применяют различные приспособления для закрепления заготовки: различной конструкции патроны, планшайбы, цанги, центры, хомутики, люнеты, оправки. К станку прилагается комплект ключей и других принадлежностей. Для контроля точности обработки токарь использует штангенциркули, микрометры, предельные калибры, шаблоны, угломеры и другие измерительные инструменты.
Более подробные сведения о станке, режущих и измерительных инструментах и приспособлениях приведены в последующих главах книги.
Долбежный станок
Современные производители станочного оборудования предлагают различные образцы агрегатов, которые находят свое применение в различных отраслях промышленности и производства. Изготовление мебели — сложный процесс, в котором без специальных устройств не обойтись. …
Износ и стойкость резцов
По закону сохранения энергии энергия, затраченная на процесс резания, не может исчезнуть: она превращается в другой вид —в тепловую энергию. В зоне резания возникает теплота резания. В процессе резания больше …
Элементы автоматических устройств
Особенностью современного технического прогресса является автоматизация на базе достижений электронной техники, гидравлики и пневматики. Главными направлениями автоматизации являются применение следящих (копировальных) устройств, автоматизация управления станками и контроля деталей. Автоматическое управление …
msd.com.ua
Токарные станки для обработки металла: модели, устройство, цены
Один из основных типов металлообработки — токарные работы, которые применяются при изготовлении большинства изделий из различных металлов и сплавов. Токарные станки для обработки металла по праву считаются одним из первых типов оборудования (после кузнечного оснащения), которое поспособствовало развитию металлообрабатывающей отрасли.
Конечно, первые появившиеся станки данного типа нельзя сравнивать с современным многофункциональным оборудованием, но именно они положили начало обработке металла резанием.
Составные части и принцип работы токарного станка
Любой токарный станок по металлу (даже современные многофункциональные металлообрабатывающие центры) работает по одному принципу:
- Обрабатываемая заготовка жестко крепится в зажимном шпинделе, который вращается с определенной частотой благодаря приводному механизму.
- Резка (снятие стружки металла небольшой толщины с поверхности заготовки) осуществляется при помощи резца, обладающего повышенной прочностью и заточенного под определенным углом. При этом для обеспечения обработки всей поверхности заготовки, закрепленный в специальном держателе резец перемещается вдоль оси вращения детали.
Обработка металла на токарном станке требует соблюдения определенных условий, так излишняя вибрация оборудования или другие факторы вызывающие даже малейшее изменение во взаимном расположении резца и обрабатываемой детали приводят к браку (отклонению от требуемых технической документацией размеров изделия).
Поэтому устройство токарных станков должно обеспечить не только определенную мощность приводного механизма и устройства продольной подачи, но и должную взаимную статичность заготовки и резца.
Любой промышленный или бытовой токарный станок по металлу (речь не идет о многошпиндельных установках, обеспечивающих выполнение работ в нескольких плоскостях одновременно) состоит из следующих основных узлов:
Станина, являющаяся основанием станка, на ней расположены все остальные части и механизмы. Кроме того на станине установлены направляющие, по которым перемещаются основные рабочие узлы станка.
Передняя бабка — конструктивный узел, в задачу которого входит крепление заготовки в рабочем положении и обеспечение ее вращения с требуемой частотой:
- Фиксация обрабатываемой детали осуществляется многокулачковым шпинделем. На промышленном оборудовании устанавливается устройство с четырьмя кулачками, что позволяет более надежно закрепить заготовку значительного диаметра. А малогабаритные токарные станки по металлу обычно оснащаются шпинделем на 2-3 кулачка, этого вполне достаточно для фиксации незначительных по размеру деталей.
- Вращательное движение шпинделю придается системой электромеханического привода, при этом существует возможность существенной регулировки частоты вращения.
- Задняя бабка предназначена для фиксации второго края заготовки (если она имеет существенную длину). Кроме того, она служит для крепления сверел, метчиков, резцом для выполнения отдельных токарных операций (сверление, нарезка внутренней резьбы, вытачивание полостей в заготовки). Задняя бабка может быть неподвижной, но у большинства промышленного оборудования она перемещается по направляющим.
- Суппорт с резцедержателем — один из самых важных узлов, имеющихся в конструкции. Токарно-винторезный станок по металлу оснащается суппортом, способным обеспечить перемещение резца, закрепленного в резцедержатели, в различных плоскостях по отношению к оси вращения заготовки.
- Каретка (нижняя часть суппорта) перемещается по направляющим, благодаря чему обеспечивается продольное перемещение резца вдоль заготовки при обработке.
- На верхней части каретки установлена другая пара направляющих, по которым двигается резцедержатель с рабочим инструментом. Благодаря этому достигается поперечная подача резца (перпендикулярно оси вращения заготовки).
Механизмы привода и подачи
Обработка металлов на токарных станках при выполнении различных операций требует разных режимов вращения заготовки и скорости подачи резца.
Изменение параметров работы станка обеспечивается специальными электромеханическими устройствами:
- Появление особых видов режущей стали позволило применять высокоскоростные режимы токарной обработки металла. Вращение передается от мощного электрического привода на шпиндель при помощи многоступенчатой коробки скоростей, которая действует по принципу обыкновенного редуктора. Если домашний токарный станок по металлу имеет ограниченное число скоростных режимов, то у серьезного промышленного оборудования данные регулировки существенно расширены.
- Механизм подачи обеспечивает продольное перемещение каретки суппорта на определенное расстояние при каждом обороте шпинделя. Для выполнения различных операций требуется возможность изменять и эти параметры. Современные токарные станки оснащены многоступенчатым механизмом подачи суппорта усовершенствованной конструкции. Регулировка скорости продольного перемещения режущего инструмента осуществляется при помощи изменения частоты вращения ходового вала и ходового винта. Применяемые коробки подач позволяют ступенчато изменять данный параметр работы оборудования.
Бытовые модели токарных станков
Для оснащения небольшой мастерской вполне достаточно приобретения оборудования невысокой мощности. Мини токарный станок по металлу позволяет выполнять основные операции, необходимые для изготовления различных металлических изделий. Конечно, возможности такого оборудования ограничены в части размеров обрабатываемых заготовок, а сам станок имеет достаточно простую конструкцию, которая не предусматривает наличия систем автоматического управления, но установки данного класса имеют целый ряд других преимуществ.
Цена токарного станка по металлу бытового назначения невысока. Благодаря чему окупается такое вложение в оборудование мастерской достаточно быстро.
Небольшие габариты и малая масса установки позволяет отказаться от сложных и дорогостоящих фундаментных конструкций. Невысокая мощность приводного двигателя обеспечивает низкое электропотребление. Такой станок подключается к обычной бытовой электросети (220 В).
Простая конструкция оборудования обусловила его отличную ремонтопригодность. Приобретение даже недорого токарного станка позволит выполнять большинство операций по металлообработке в бытовых условиях.
steelguide.ru