Чем обработать подкрылки автомобиля от коррозии: Чем обработать подкрылки автомобиля от коррозии? 🦈 avtoshark.com
alexxlab | 15.02.2023 | 0 | Разное
Как защитить подкрылки от коррозии антикорами 🦈 avtoshark.com
Сами по себе подкрылки не могут обеспечить стопроцентной защиты. Необходимо пользоваться специальными средствами, выбор которых зависит от желания и финансовых возможностей владельца автомобиля.
Российские дороги отличаются агрессивным отношением к внешним деталям машины. Зимой в колесные арки попадает снег с антигололедными реагентами. Летом туда забивается пыль, мелкие камешки и куски асфальтового покрытия. Небольшое повреждение за несколько месяцев приводит к образованию огромной коррозийной поверхности. Машина, выпускаемая с завода, имеет слабую защиту от коррозии, особенно в области подкрылок и днища кузова. Необходимо сразу задуматься, как ее усилить и обработать подкрылки автомобиля от коррозии своими руками.
Что такое подкрылки и зачем их обрабатывать
Подкрылки – это специальные кожухи, устанавливаемые на колесные арки. Представляют собой кусок формованного пластика, выгнутого под определенную модель машины. Они полностью или частично закрывают часть кузова и верхнюю область крыла. Основная их функция – защита от грязи, пыли, снега области, расположенной под днищем кузова и крыльями авто. Они снижают уровень шума и одновременно защищают автомобиль от коррозии. Благодаря им кузовные элементы служат намного дольше.
Что такое подкрылки
Колесные арки – скрытые полости, поэтому коррозийные процессы в них протекают незаметно. В них накапливаются грязь, вода и создаются идеальные условия для появления ржавчины. Для предотвращения этого процесса регулярно обрабатывают подкрылки авто от коррозии и шумоизоляции защитными составами.
Самыми ходовыми считаются пластмассовые подкрылки для авто (как штатные детали для «Лады Приоры»). Они не боятся воды и грязи, но быстро повреждаются камнями и прочими твердыми элементами, вылетающими с дороги. Существуют усовершенствованные детали, изготавливаемые из иглопробивного волокна. Они обладают прекрасной звукоизоляцией, не впитывают грязь и жидкость.
В продаже имеются жидкие аэрозольные составы, которые наносятся своими руками изнутри непосредственно на колесные арки.
Сами по себе подкрылки не могут обеспечить стопроцентной защиты. Необходимо пользоваться специальными средствами, выбор которых зависит от желания и финансовых возможностей владельца автомобиля.
Как часто требуется антикоррозийная обработка
Антикоррозийную обработку машины рекомендуется проводить раз в 2-3 года. Первый раз процедуру делают сразу после покупки новенького авто. Дальнейшая обработка подкрылков автомобиля от коррозии зависит от марки машины. В европейских авто колесные арки начинают покрываться ржавчиной спустя 3-4 года после начала эксплуатации. Китайские, корейские автомобили (например, «Киа») портятся уже в первый год.
Антикоррозийная обработка подкрылков
Немаловажную роль играет и выбор средства, которым предполагается защитить подкрылки машины от коррозии:
- Отработанным маслом их обрабатывают 2-4 раза в год.
- Отечественными средствами на основе моторного масла, антикоррозийных присадок, битума обрабатывают подкрылки раз в год.
Дорогие заграничные средства реже требуют обновления.
Составы для защиты от ржавчины
Существует огромный спектр антикоррозийных средств, чтобы обработать подкрылки автомобиля от коррозии своими руками. Ориентироваться можно по основному компоненту состава.
Битум
Мастики на основе битума – вязкий материал, обладающий хорошей гидроизоляцией. Отличаются морозоустойчивостью, хорошими антикоррозийными и шумоизоляционными свойствами.
Битумные мастики бывают нескольких разновидностей:
- Полимерно-битумные. В их составе имеются полимеры, преобразователи ржавчины, замедлители коррозийных процессов. Отличаются высоким уровнем адгезии. Свойства сохраняет при температурах от -50 до +100 градусов.
- Сланцевые. Мастики на основе битума, пластификатором является минеральное масло. Основным недостатком покрытия считается небольшой разброс рабочих температур.
При -20 состав теряет свои защитные свойства.
- Битумно-каучуковые. Вязкие, густые смеси, которые при высыхании дают большую усадку. Сохраняют свои свойства до -60 градусов.
Битум для обработки подкрылков
Битумные смеси после высыхания образуют своеобразную пленку, напоминающую по фактуре резину. Обработка подкрылков автомобиля от коррозии такими составами защищает от дорожного гравия, камней, грязи, кусков асфальта, песка. Обладают высоким уровнем шумоизоляции.
Эпоксидная смола
Мастики на основе эпоксидки считаются самыми стойкими. Но они при низких температурах раскалываются. Состав наносят прямо на замасленные участки.
Воск
Бесцветные составы с высокой текучестью. Содержат замедлители коррозии, которые действуют, когда восковой состав находится в жидком состоянии. При высыхании средство превращается в пленку и теряет антикоррозийные свойства. Восковой антикор создает защитную пленочку на металле, предохраняя его от воздействия воды, кислорода, агрессивных реагентов.
Читайте также: Как убрать рыжики с кузова автомобиля ВАЗ 2108-2115 своими руками
Средство устойчиво к перепадам температур, но отличается небольшой механической прочностью.
Каучук
Это жидкие составы. Продаются в баллончиках, распыляются по поверхности колесных арок перед установкой обычных подкрылков. Отличаются небольшой шумоизоляцией.
Подкрылки уберегают крылья и часть кузова машины от агрессивного воздействия дорожных покрытий, защищают от посторонних шумов. Но сами они нуждаются в защите, поэтому важно каждому владельцу транспортного средства уметь правильно и своевременно обработать подкрылки автомобиля от коррозии своими руками в домашних условиях, чтобы продлить срок его эксплуатации.
Вы можете использовать наши уникальные ФОТО, при указании активной ссылки – https://avtoshark.com/
антикоррозийная обработкажидкие подкрылкизащита от ржавчиныобработка подкрылков
0
Антикоррозийная обработка и жидкие подкрылки
Коррозия и ржавчина — следствие и причина. Антикоррозийная обработка — устранение следствия и борьба с причиной. С появлением институтов автомобилестроения открылись институты по борьбе с коррозией. Правильная и бережная эксплуатация автомобиля неразрывно связана с защитой кузова, порогов, арок и днища авто от ржавчины и коррозийных процессов.
В недавнем прошлом веке антикоррозийная обработка проводилась собственными силами. Можно было часто наблюдать следующую картину: лето, гараж или дача, разобранный салон автомобиля ВАЗ 2106 или «копейка» и рядом бережливый хозяин с пушечным салом. На тот момент самый эффективный способ консервации кузова. С приходом на рынок ВАЗ 2108, на тот момент – мечта многих автовладельцев, появились целые центры по антикору, где люди в болотных сапогах или костюмах химзащиты наносили антикор на автомобиль с последующей установкой подкрылок.
Время перестройки открыло возможность покупки иномарки. Тут же на свет родился миф о оцинкованных кузовах, неподверженных коррозии. Действительно некоторые производители иномарок оцинковывали кузов и давали гарантию до 12 лет на сквозную коррозию. Мало кто обращал внимание и обращает сейчас на слово – сквозную. Ржавчина или, как еще называют-машина «зацвела» появляется значительно раньше. И способствует этому следующие факторы:
- низкое качество металла, используемого при производстве
- наличие сварочных швов
- агрессивная среда эксплуатации и окружающая атмосфера
- кузовной ремонт, пусть даже самый качественный
- перепады температур и влага, условия хранения авто
Другими словами, коррозийных процессов не избежать, но отсрочить появление ржавчины на годы вперед можно, и лучшее средство антикоррозийная обработка средством Dinitrol от шведского концерна.
Антикор днища и скрытых полостей
Обычно первые «цветы» или следы ржавчины появляются:
- На нижнем шве дверей
- На кромке капота
- На порогах
- На арках
- На местах ремонта кузова
Такие следы ржавчины появляются из-за нарушения проходимости воды в местах для ее слива.
На рамках лобового стекла появляется в следствии нарушения технологического процесса по вклейки стекла и использования некачественных материалов.
Не менее важный этап-защита и обработка днища автомобиля и арок. Кроме антикоррозийных свойств, продукция Динитрол совмещает в себе и функции шумоизоляции.
Многие производители в целях экономии не ставят подкрылки. В этом случае целесообразнее использовать состав Dinitrol — жидкие подкрылки. Вы получаете и подкрылки, и шумоизоляцию, и антикоррозийную обработку.
Цена и стоимость услуг на антикоррозийную обработку и жидкие подкрылки (посмотреть)
Просмотров: 377
Сэкономьте $$$, устраните повреждения от ржавчины дома!
| Практическое руководство — покраска и кузов
Ремонт небольших ржавых участков вашего автомобиля может быть одним из самых простых этапов любой реставрации. Хитрость заключается в том, чтобы найти время, чтобы быть наблюдательным и осторожным во время ремонта. Этот Монте-Карло 1974 года изначально был продан в дилерском центре отца владельца и проехал на нем всего 41 000 миль. Он прожил тяжелую жизнь до того, как его поставили на хранение в 80-х, и ржавое шасси свидетельствовало о том, что дорога была покрыта солью от висконсинских зим. На первый взгляд кузов выглядел не так уж плохо, но как только команда Driven Restorations начала копаться, они обнаружили старый, плохо сделанный ремонт ржавчины. Владелец хотел, чтобы автомобиль был достойным и хорошо выглядящим, чтобы он мог наслаждаться им в летние месяцы, путешествуя со своей семьей.
Молли и Стив Гурски из Driven Restorations, проживающие в заснеженном Рэндольфе, штат Висконсин, слишком хорошо знают, что дорожная соль делает с автомобилем. Они реставрируют классические легковые и грузовые автомобили в течение девяти лет, и они делают полную перекраску с новым виниловым верхом на этом классическом Монте.
Сомнительными областями на Монте-Карло были нижняя передняя часть каждой боковой панели и нижняя задняя часть каждого переднего крыла. Ржавчина скрывалась за широкой отделкой в этих областях, способствуя повреждению, но скрывая его. Вода и дорожная соль скапливаются за этой накладкой и проходят через монтажные отверстия накладки. Затем он накапливается на задней поверхности панелей, ускоряя процесс коррозии.
Правило номер один при ремонте ржавых участков – срезать весь поврежденный материал и тщательно очистить и обработать все заржавевшие поверхности. Продумайте свой путь через ремонт и терпеливо проработайте каждый шаг ремонта. Например, найдите время, чтобы тщательно спроектировать, вырезать и подогнать картонный шаблон для нашивки. Если шаблон не подходит, создайте другой. Одна крошечная оплошность в начале процесса может вызвать большую головную боль позже. Еще одним важным шагом является обеспечение полного охлаждения в процессе сварки.
Прежде чем приступить к работе, Молли измерила площадь поверхности поврежденных ржавчиной участков, а также расстояние между конечным углом каждого участка и рамой автомобиля. Всегда обязательно делайте замеры и фотографии всего ремонтируемого участка со всех сторон, а в некоторых случаях вам может понадобиться нарисовать простой эскиз. Таким образом, после того, как заплатка создана и установлена, вы можете обратиться к ней, поскольку заплата установлена в нужное положение. После прихватки заплаты снова проверьте размеры, так как тепло от сварных швов может тянуть металл и смещать заплату.
На протяжении многих лет люди использовали различные способы охлаждения металла после сварки, чтобы предотвратить его коробление. Некоторые из этих методов включают в себя наложение мокрой тряпки на пораженный участок или охлаждение с помощью пневматического пистолета, но нет ничего лучше, чем подождать, пока он остынет естественным образом. Если металл кажется горячим, отойдите и не сваривайте снова, пока металл не станет прохладным на ощупь. Время, необходимое для остывания металла, означает меньше времени, затрачиваемого на кузовные работы в дальнейшем.
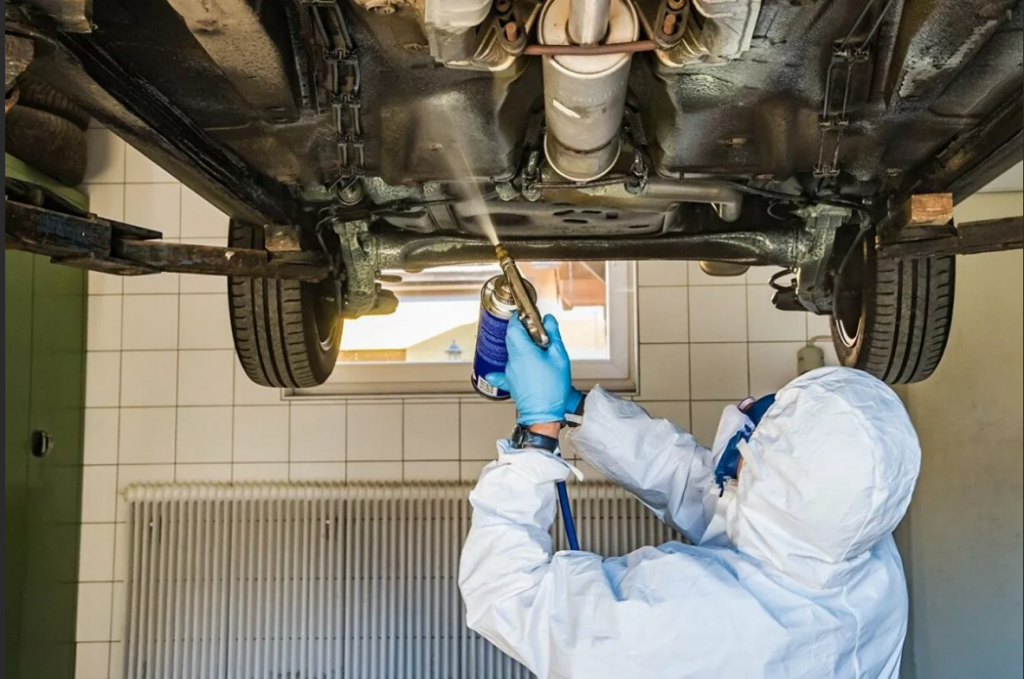
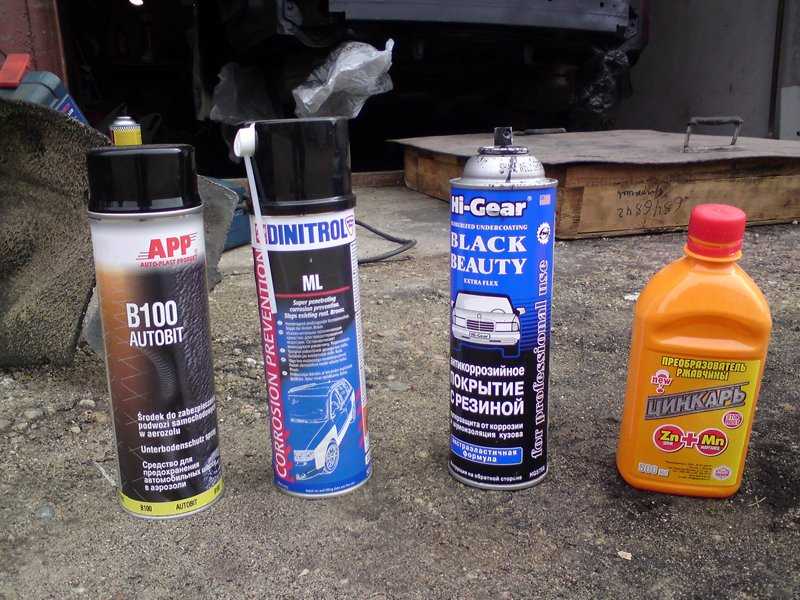

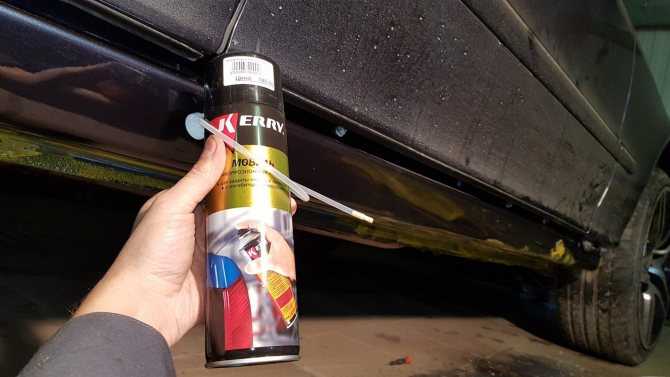
Trending Pages
Может ли Chevrolet Silverado ZR2 «Метеор» убить грузовики-динозавры?
2024 Ford Ranger Raptor: все, что мы знаем о пикапе среднего размера для бездорожья Brother
Мы целый год тестируем Hyundai Ioniq 5, и все может пойти очень плохо
Популярные страницы
Может ли Chevrolet Silverado ZR2 «Метеор» убить грузовики-динозавры?
2024 Ford Ranger Raptor: все, что мы знаем о пикапе среднего размера для бездорожья Brother
Мы целый год тестируем Hyundai Ioniq 5, и все может пойти очень плохо
Ремонт фланцев крыла от ржавчины своими руками
| Практическое руководство — покраска и кузов
Самостоятельный ремонт фланцев крыльев
Вы когда-нибудь замечали, что чем более комфортно вы становитесь в предмете, тем больше вы упускаете. Может быть, именно поэтому мы, казалось бы, упускаем из виду важные вопросы или проблемы, иногда сводя их к минимуму. В конце концов, мы постоянно строим и ремонтируем грузовые и легковые автомобили, поэтому чувствуем уверенность в преодолении любых препятствий. Возможно, именно тогда наше эго и желание конкретного проекта преобладают над нашим мысленным взором в отношении деталей. Если все это было слишком интроспективным, то позвольте мне объяснить, как я упустил из виду проблему, которая стала опытом обучения, и надеялся, что смогу помочь кому-то еще решить подобную проблему.
Просматривая недавний проект реставрации, я заметил небольшую ржавчину в месте соединения крыльев с кузовом. (Этот конкретный предмет был на самом деле автомобилем, но никому не говорите, хорошо?) Я видел немного ржавчины в этой области, но просто не чувствовал, что это нужно, кроме беглого взгляда – черт возьми, почти каждый проект восстановления имеет некоторое количество ржавчины.
Некоторые из инструментов, которые вам понадобятся для работы с металлом, – это хороший сварщик, носилки, термоусадочная машина (экономия времени и труда при ремонте такого типа), а также различные ножницы, ножницы, молотки и тележки. Столкнувшись с этим конкретным ремонтом, я понял, что термоусадка и носилки дадут большие преимущества, поэтому я позвонил дружелюбным и знающим людям из компании Eastwood и заказал пару. Термоусадочная машина собирает материал в набор металлических губок. Челюсти захватывают материал (как черные, так и цветные металлы) и собирают или сжимают его в сжимающем движении. Когда материал собирается, он создает изгиб или кривую в материале. Это позволит пользователю создавать радиусы или изогнутые формы, которые будут напоминать оригинальную панель или фланец, разрушенные ржавчиной или повреждением. Носилки выполняют ту же работу, но в обратном порядке; он захватывает материал и растягивает его, растягивая, чтобы сделать его длиннее. Когда он становится длиннее, он также начинает изгибаться (хотя и в противоположном направлении, чем усадка). Эти два инструмента Eastwood вместе позволят вам сделать эти необходимые патч-панели (среди многих других). Еще один инструмент, который значительно облегчил эту работу, также от Eastwood.
Если вам предстоит масштабный ремонт с использованием новых для вас технологий, помните следующее. По словам моего хорошего друга и наставника Денниса Уэбба (Dennis Webb Designs, Анахайм, Калифорния): «Ни одна работа не будет слишком большой, если ее разбить на множество маленьких шагов». При таком подходе возможно изготовление почти любой панели.
Здесь я проиллюстрирую три различных области патч-панелей, с которыми я столкнулся во время своего проекта. Каждый из них начнет показывать некоторые формы, которые вы можете сделать с помощью этих инструментов. Первый – простой ремонт ржавчины. Инструменты, которые вам понадобятся, это отрезной круг по металлу, проволочная щетка, сварочный аппарат, предпочтительно MIG или TIG (сохраните дуговой сварщик для строительства мостов), и шлифовальный станок.
Второй пример ремонта — тот, о котором я говорил ранее. Когда я снял это крыло, я обнаружил, что большая часть монтажного фланца внутреннего крыла проржавела. Должен признаться, я был удивлен степенью повреждения ржавчиной. Мне потребовалось несколько минут, чтобы прийти в себя и придумать план починки. В этом ремонте мы будем использовать вышеупомянутые термоусадку и растяжку Eastwood.
Последний ремонт панели имеет наибольшую форму. Этот ремонт внутренней заплаты крыла имел несколько контуров. Следуйте вперед и помните, что это всего лишь металл. Если он не выглядит так, как вы хотите, вы всегда можете вырезать его и попробовать еще раз.