Чертеж станка для холодной ковки своими руками: применение, особенности инструмента, технология ковки. Чертежи для создания своими руками (130 фото)
alexxlab | 23.11.1990 | 0 | Разное
Особенности создания элементов холодной ковки, сборка станка, чертежи
Содержание
- 1 Типы ковки холодным методом
- 1.1 Вытяжка
- 1.2 Кручение
- 1.3 Гнутье
- 2 Особенности производства металлической ковки холодным методом
- 3 Приспособления и станки
- 4 Конструкция станков
- 5 Изготовление станка собственноручно
Владельцы частных домов и дач с удовольствием оборудуют свое жилище коваными изделиями. Такие предметы превосходно смотрятся в интерьере любого стиля. Они подходят для создания элементов декора в каменных, а также деревянных домах. Металлические предметы горячей обработки имеют главный недостаток – высокую цену. Отличной альтернативой является ковка холодная, готовые элементы которой имеют невысокую стоимость и доступную технологию изготовления. При таком процессе нагрев металла отсутствует, а получение необходимой конфигурации производится гибкой с последующим прессованием и выполнением сварки составляющих частей.
Содержание
- Типы ковки холодным методом
- Вытяжка
- Кручение
- Гнутье
- Особенности производства металлической ковки холодным методом
- Приспособления и станки
- Конструкция станков
- Изготовление станка собственноручно
Типы ковки холодным методом
Выполнение операций по обработке металла требует соблюдения мер безопасности. Холодная ковка своими руками, видео основных процессов которой находится в свободном доступе, не требует специальных познаний. Достаточно иметь первоначальное обучение по работе со слесарными приспособлениями. Изготовление декоративных металлоизделий при холодной ковке своими руками выполняется при помощи трех основных типов технологических процессов:
- вытяжка;
- кручение;
- гнутье.
Вытяжка
На этом этапе металлическая заготовка удлиняется с одновременным уменьшением своего сечения. Для данного процесса применяются прессовочные или же раскаточные станки. Проходящая через вальцы заготовка постепенно изменяет свою форму. На валиках могут иметься насечки рельефного типа для придания детали особой текстуры. Таким способом обработки получают декоративные лапки, пики.
Кручение
При этой обработке проводится скручивание стального прута или же полосы. Этим способом можно закручивать несколько заготовок одновременно. При этом один конец металлоизделия крепится в зажиме тисков, а второй проворачивается вдоль оси. При приложении осевого усилия на несколько скрученных прутов получится фигурное утолщение («корзинка» или же красивый «фонарик»).
Гнутье
Это воздействие проводят, используя специальные станки, по заранее заготовленным шаблонам. Металлоизделие подвергается изгибу в разных плоскостях, что предоставляет возможность изготавливать разнообразные декоративные элементы. Предлагаемые производителями станки имеют высокую стоимость, однако их можно соорудить самостоятельно.
Особенности производства металлической ковки холодным методом
Созданные в домашних условиях элементы холодного типа ковки не настолько вычурные, как полученные горячим методом, однако имеют превосходный декоративный вид. Имея под рукой набор специальных приспособлений, инструментов, оборудования, материалов можно создавать великолепные вещи, при этом соблюдая порядок технологического процесса.
Сначала подготавливается эскиз изделия. На первом этапе для работы берутся элементарные вещи. После получения необходимых навыков и овладения приемами работы, можно приступать к изготовлению более сложной продукции. На эскизе изображается общий рисунок, размеры, необходимые составные части. Учтите, что имеющееся в распоряжении оборудование предназначено для определенных операций.
После предварительного эскизного этапа проводится расчет материалов для изготовления металлоизделия. В зависимости от его сложности будет зависеть список материальных компонентов. Для простой подставки можно обойтись металлической трубой и стальными полосами, а для изготовления ворот потребуется более широкий ассортимент материалов.
Перед началом производства повторно проверяются расчеты, от которых будет зависеть конечный вид готового металлоизделия. Этот этап весьма важен, так как исправлять и выполнять подгонку продукции всегда сложнее, чем изготовить новые детали. После этого начинается основной этап создания элементов будущей конструкции. Имея в наличии составные компоненты, проводится их сборка посредством сварки и клепки. На финальном этапе выполняется шлифовка, а также покраска готового металлоизделия.
Используя этот метод, можно получить декоративные компоненты для калиток, ворот, разнообразных заборов, цветочные подставки, обрамления для зеркал и солидных картин. Помимо этого, изготавливаются фигурные ножки для столов, скамеек, стульев, детали козырьков, навесов, перил, оконные решетки, а также прочие декоративные и защитные металлоизделия. Полученные узоры металлоизделий холодной ковки своими руками становятся уникальными авторскими находками.
Приспособления и станки
Домашняя холодная ковка применяет оборудование, сооруженное своими руками, видео с которым покажет основные этапы работы. Специальные станки оснащаются ручным приводом или же электрическим. Спецоборудование для формирования завитков и плоскостных спиралей называется твистерами или закручивателями. Приспособления торсионного типа применяются для винтового кручения металлического прута, деталей из спиралей объемного вида (филаментов): луковиц, фонариков, а также корзинок.
На инерционно-штамповочном оборудовании расплескивают в особые фасонные наконечники концы прутьев, выдавливают рельефную и волновую поверхность, а также штампуют соединительные декоративные хомуты. Станки гибочного типа подразделяются на протяжные, нажимного воздействия и комбинированные. При помощи протяжного оборудования получают завитки, кольца и разнообразные спирали, имеющие широкие ядра. Нажимные приспособления позволяют создавать зигзаги, волны, а комбинированные станки выполняют все вышеперечисленные операции.
Конструкция станков
Выполняемая холодная ковка своими руками, станки, чертежи, видео для которой представлены, позволяет создавать великолепные художественные металлоизделия. Используя основные типы станков, создаются красивые узоры из металлопродукции профильного типа. Упрощенное название гибочного ручного оборудования – гнутики.
Эти приспособления применяются для получения зигзагов и волновых деталей. Для изменения угла зигзага, а также высоты волны и шага заменяется клин или прижимной ролик в центральной части. В качестве материала для этого спецоборудования служит специальная сталь, способная выдерживать повышенные нагрузки.
Твистеры-улитки имеют широкие возможности и простейшую конструкцию. Они подразделяются на улитки с лемехом поворотного типа и воротом, а также рычажные с обводным роликом. На них можно выполнять холодную ковку из профильной трубы и прочих металлических заготовок.
Станки торсионного типа увеличивают производительность, а также качество производимых деталей. Они имеют прочную станину, на которую передается основная нагрузка. Для удержания квадратного прута служат патроны-оправки, имеющие квадратного сечения гнезда. Их крепление в скользящей задней бабке и шпинделе выполняется винтовыми зажимами. Скручивание участков металлических заготовок производится при помощи подвижного ограничителя со специальной вставкой.
Изготовление наконечников на прутьях выполняется на специальном штамповочном приспособлении. Этот специальный станок использует принцип маховика. Вращая грузовую штангу, отводится назад винтовой боек. После этого в специальное гнездо вставляется штамп, и устанавливается заготовка. Раскрученная штанга приводит ударный боек в движение и происходит удар по хвостовику штампа, воздействующего на конец прута.
Для самостоятельного изготовления такого спецоборудования необходимы валки из специальной стали, шестерни, втулки для подшипников и валы.
Изготовление станка собственноручно
Перед тем как сделать холодный ковки станок, определяются с его конструкцией, а также возможностями. Сооруженные своими руками специальные приспособления позволят проводить ковку металлических предметов в практически в домашних условиях. В качестве рабочего места вполне подойдет гараж, хозяйственный блок или сарай. Определившись с ассортиментом будущей продукции, приступают к созданию приспособлений по ее выпуску. Полноценная процедура производства требует наличия всех типов станков по ковке холодным способом. Для ускорения процесса изготовления оборудования следует просмотреть соответствующие видео, где представлены уроки по сборке станков, а также изготовлению металлоизделий. Сделать собственноручно подобный станок можно используя чертежи, схемы, которые можно брать в качестве основы и изучая видеоуроки. Это позволит избежать многочисленных нюансов при создании собственной мехмастерской.
Холодная ковка, оборудование для которой своими руками изготавливается бесплатно при помощи чертежей, позволит изготавливать авторские узоры разнообразных металлоконструкций. К наиболее распространенным станкам относятся улитки, которые предоставляют возможность изготавливать многочисленные кованые холодным способом завитушки из профильной трубы, а также прочего проката. На чертеже представлен классический вариант станка-улитки, который можно соорудить в любом гараже, а ниже приведено описание конструкции.
Для стола используется листовая сталь от 10 мм. В качестве ножки применяется круглая толстостенная труба или же другой подходящий профиль. Конструкция должна иметь прочное основание, так как воспринимает высокие боковые нагрузки при работе. Рычаг изготавливается из трубы квадратного профиля со стенкой порядка 3 мм. Оптимальным считается размер 25×40 мм. Рычаг крепится к ножке посредством подшипникового узла или же другим способом. Подшипник значительно облегчит работу для получения фигурного профиля. Такая конструкция может дополняться собственными идеями по использованию дополнительных станковых приспособлений.
К изготовлению своими руками станков и приспособлений следует подойти весьма ответственно и скрупулезно. От правильности чертежей, а также выполненных расчетов зависит качество станков, а также создаваемых металлоизделий. Получив навыки и сноровку, оборудование можно разнообразить для совершенствования выпускаемой продукции.
Станок для холодной ковки своими руками: видео, фото, чертежи
Сделать станки для холодной ковки можно из подручных материалов.
Так как универсальные приспособления от производителей имеют достаточно высокую стоимость, собственноручно выполненный станок для холодной ковки металла станет отличным решением для людей, занимающихся изготовлением кованых изделий.
Сегодня металлические конструкции с уникальным дизайном и смелыми архитектурными формами применяют для обустройства домов в коттеджных поселках.
Фигурно изогнутые кованые элементы ворот, заборов и калиток вносят непривычный образ в ландшафтный дизайн усадьбы.
На предложенных фото можно увидеть, какой необычный художественный вид создают металлоконструкции.
Какие детали можно выполнить на станке для холодной ковки
Содержание:
- Какие детали можно выполнить на станке для холодной ковки
- Виды оборудования для холодной ковки
- Изготовление станка «Улитка»
- Трубогибочный станок
- Как изготовить станок торсион
Холодная ковка, в отличие от горячей технологии, проста и безопасна. Этот процесс не требует применения раскаленного металла и точного соблюдения рабочей температуры.
Сделать станок для холодной ковки своими руками можно специально для изготовления определенного типа деталей.
Фото:
Также самодельный станок позволит решать самые разнообразные задачи, поэтому он будет просто универсальный.
С помощью самодельного станка удастся добиться идеальной геометрии элементов металла для индивидуальной дизайнерской идеи и сделать самому оригинальные детали с узором.
В процессе холодной декоративной ковки, как правило, применяют мягкий металл — это могут быть никелевые и магниевые сплавы, сталь, медь или латунь.
В остальном ассортимент производимых изделий на станке будет ограничиваться только фантазией и возможностью мастера.
По желанию, своими руками можно сделать ажурные элементы для лестниц, ворот и ограждений.
Использование декоративных деталей позволит украсить камины и мангалы, красиво оформить наружные стены дома и беседку, сделать оригинальные треноги для цветов, как на фото.
Фото:
Виды оборудования для холодной ковки
Существующие виды станков могут эксплуатироваться с участием электрического двигателя или ручной силы.
Первый вариант приспособления дает возможность выполнять работу быстрее, чем ручные станки, но при этом требует от мастера определенных навыков.
Кузнечные станки для ковки разделяют на типы:
- улитка – станок с отдельными снимающимися деталями или цельнолитой — он используется при выполнении спиралевидных отдельных частей;
- универсальное приспособление – применяют для резки, клепки и приданий объема изделию;
- гнутик – с его помощью можно сделать дуговую гибку металла или изгибание деталей под определенным углом;
- приспособление для формирования колец;
- твистер – позволяет выполнить загиб изделия вдоль оси;
- пресс – для образования матричного отпечатка на изделии;
- волна – для получения из металлических прутьев волнообразных элементов.
Изготовление станка «Улитка»
Далее в статье рассмотрим чертежи, фото и видео материалы, с помощью которых станет намного проще сделать в домашних условиях станок для холодной ковки.
Используя нижеприведенный список инструментов и металлических деталей, можно собрать станок цельной улитки.
Видео:
Для работы понадобятся:
- металлические прутья;
- листы и полосы из стали;
- профильная стальная труба;
- сварка, плоскогубцы, болгарка.
Чертежи и пошаговая схема, а также просмотр тематического видео, позволит получить качественное приспособление с нужными параметрами:
- Используя лист бумаги, нанесите на него изображение спирали с тремя витками. Далее сверьте размеры так, чтобы в результате армированный прут с диаметром 10 мм помещался в резьбу;
- С помощью болгарки вырежьте из стального листа две пластины. Первая должна иметь параметры 100х100 мм, вторая – 130х130 мм;
- Возьмите 3-х см прут и три стальные полосы. Края срезов всех используемых деталей нужно зачистить наждаком, чтобы избавиться от заусениц;
- Плоскогубцами выполните изгиб стальных полос по шаблону, в результате у вас появятся три спиральных детали с разной длиной;
- С помощью сварки все элементы станка приваривают по схеме, сварочные работы рекомендуется проводить качественно, так как именно от них будет зависеть срок эксплуатации инструмента;
- Стальная труба приваривается в последнюю очередь снизу в центре станка.
В результате проведенных работ должно получиться оборудование для холодной ковки металла, как на фото.
Трубогибочный станок
Если при оформлении каких-либо элементов интерьера с нарезанием профильных труб трудностей никто не испытывает, то при необходимости выполнить их изгиб, наоборот, все усложняется.
Качественно и быстро провести такую работу позволят специальный гибочные станки для труб, которые заранее можно сделать своими руками.
Чертежи для изготовления данного вида оборудования могут применяться разные, в зависимости от того, какие материалы будут использоваться в работе.
Собрать станок производственного типа для холодной ковки металла, как на фото, на первый взгляд сложно.
Но если мастер, работая с металлом, уже успел набраться опыта, для него нет ничего невозможного. Главное подобрать прочную устойчивую основу под будущую конструкцию.
Например, это может быть массивный металлический стол, выполненный на основе труб или профиля.
Так как сгибание металла будет происходить за счет присутствующих в конструкции валов, необходимо подобрать три таких элемента.
Каждый из них представляет собой металлический цилиндр с толстыми стенками и осью вращения. Два цилиндра фиксируются немного выше стола, а третий – центральный, помещается над ними.
От расстояния двух крайних цилиндров зависит, под каким углом будет осуществляться изгиб трубы.
Чтобы иметь возможность изменять при необходимости положение цилиндров, нужно в чертежи конструкции внести дополнения в виде стопперов и роликов, которые позволят сделать эту часть регулируемой.
После того как цилиндры зафиксированы, необходимо организовать для них систему передачи вращения.
С этой целью используют цепной механизм от старого автомобиля, который можно отыскать на рынке запчастей.
Лучше, если механизм будет укомплектован шестернями, если нет, тогда их придется покупать отдельно.
Шестерни монтируют на два крайних цилиндра и натяжитель, помещенный ниже валов, в центре. Затем один из крайних цилиндров оснащается ручкой, с целью создания вращающего усилия.
Станок для холодной ковки металлических изделий готов. Дополнить вышеизложенный материал подробностями поможет следующее видео.
Видео:
Как изготовить станок торсион
Станок для холодной ковки изделий типа торсион используют для закручивания металлических спиралей в виде змейки.
Вручную работать таким приспособлением тяжело, поэтому, чаще всего для изготовления торсиона применяют чертежи с электрическими вариантами станков.
Для того чтобы правильно собрать торсион, предлагаем просмотреть видео и ознакомиться с нижеизложенным руководством.
Видео:
Инструменты и материалы для сборки станка:
- стальной лист;
- двутавровая балка;
- тиски и крепежные элементы;
- редуктор, электромотор, цепь;
- болгарка;
- сварка.
Схема последовательности действий:
- За основу будет служить двутавровая балка, к одной стороне которой необходимо приварить стальной лист;
- Затем к стали крепят тиски, приваривают и фиксируют болтами с гайками;
- Чтобы при натяжении металлическое изделие не выскакивало из станка, к тискам снизу и сверху крепят пластины;
- Другую сторону двутавровой балки оснащают роликами, на которые, впоследствии, монтируется платформа;
- На поверхность полученной конструкции крепятся другие тиски с подвижными основными элементами.
При этом обе конструкции, расположенные по краям двутавра, должны будут располагаться на одном уровне;
- Далее конструкция оснащается стальной ручкой, выполненной из прута, за счет ее вращения будет загибаться изделие;
- Используя болты, соединяют понижающий редуктор и двигатель. Обод штурвала оснащается цепью;
- Конструкция закрывается стальным кожухом.
В результате проведенных действий получается станок с двумя блоками — подвижным и неподвижным.
Станки холодной ковки. Особенности создания элементов холодной ковки, сборка станка, чертежи
ГлавнаяРазноеСтанки холодной ковки
Станки для холодной ковки Blacksmith: ручные и электрические
Процесс ковки металла применяется людьми очень давно. Стоящая одиноко кузница, дышащий пылом горн, увесистый молот, превращающий в тонкий лист раскаленную заготовку на тяжелой наковальне — такой образ кузнеца известен нам невероятно длительное время. Сегодня мы рассмотрим станки для холодной ковки Blacksmith.
Кузнечное дело
Учиться профессии кузнеца необходимо долгие годы, длительно надо и набираться опыта. Труд кузнеца тяжелый вредный и очень трудоемкий. К тому же кузнечный горн — предмет высочайщей пожарной опасности. Все это мешает нашим мастерам, имеющим желание попробовать свои силы в таком трудном деле, как обработка металла.
Но есть удобный вариант — это процесс холодной ковки, позволяющая придавать заготовкам из прутка или труб необходимую форму и создавать витые и изогнутые элементы самых разных очертаний.
Станки для ковки
Главные преимущества технологии холодной ковки:
- Простой технологический процесс, малое число операций.
- Низкая трудоемкость и себестоимость изделий.
- Высокая повторяемость — изделия одной серии практически идентичны.
Недостатком является ограниченное число базовых элементов ковки, однако при должном мастерстве дизайнера и из них можно создать запоминающееся изделие.
Станки для холодной ковки используют способность металлов к пластической деформации под воздействием механического усилия. Усилие требуется весьма большое, поэтому все устройства оснащаются рычажным, кривошипным или электрическим приводом. Широкое распространение получили несколько типов станков:
- Гнутик – применяется для изгиба заготовки под заданным углом и при заданном радиусе.
- Волна – разновидность гнутика, осуществляющая сразу несколько изгибов, по форме напоминающих бегущую волну.
- Улитка используется для сворачивания конца заготовки в спираль
- Торсион позволяет закручивать заготовку или группы заготовок вокруг продольной оси.
Процесс сгибания Процесс скручивания Приспособление «Гнутик» Волны для выполнения волнообразного изгиба заготовки
Одним из ведущих российских производителей оборудования для холодной ковки является компания BlackSmith
Основные виды станков и их функционал
От недорогих ручных станков для начинающих знакомиться с холодной ковкой до многофункционального гибочного комплекса с ЧПУ — линейка станков для холодной ковки BlackSmith – пожалуй, самая широкая в России.
Ручные станки для ковки BlackSmith выгодно отличаются от китайского ширпотреба высокой точностью изготовления, большим ресурсом и качественной инструментальной сталью, применяемой для изготовления основных узлов. Кроме гнутиков, улиток и торсионов, BlackSmith предлагает широкий спектр оборудования для подготовительных операций — инструмент для резки металла и правки заготовок.
Гнутик M3-G BlackSmith предназначен для сгибания полосы 40*5 и прутка до 12 мм в дуги, изготовления колец радиусом от 80 мм и гибки углов более 60 градусов.
Ручная улитка M3-V1 BlackSmith позволяет гнуть завитки различной формы из полосы до 40*5 мм, круглого и квадратного прутка до 12 мм.
Торсионный станок M04B-KR BlackSmith представляет собой высокофункциональный набор для изготовления корзинок и витых прутков сечением до 16 мм.
Приспособление для обрезки седловин на концах труб TN1-38/50 BlackSmith работает с трубами диаметром 38 и 50 мм позволяет сделать заготовки для сварных объемных трубчатых конструкций
На верхнем конце продуктовой линейки BlackSmith находится топовая модель UNV3-02 универсальный станок для ковки. Этот комбайн выполняет практически все известные операции холодной ковки и способен создавать такие элементы художественной ковки, как завитки, витые прутки, корзинки, кольца, простые , двойные и обратные завитки, дуги и арки больших радиусов, расплющивать конец прутка в «гусиную лапку», двухстороннюю полуволну и «вчистую»
Преимущества станков Blacksmith
Помимо высокого качества и передовой конструкции, станки для холодной ковки BlackSmith обладают следующими преимуществами:
- высокая производительность оборудования;
- надёжность и компактность ручного кузнечного инструмента;
- возможность открыть своё дело в домашних условиях.
- достаточные складские запасы и четко поставленная работа логистики исключают долгое ожидание заказанного покупателем оборудования.
Еще одно немаловажное преимущество- BlackSmith производит действительно все, необходимое для комплектации домашней мастерской и запуска своего дела — не только станки, но и оснастку, вспомогательное оборудование, ручной слесарный инструмент.
Станок BlackSmith
Ваш бизнес может расти вместе с оборудование BlackSmith- достаточно будет по мере роста заходить к ним и докупать необходимое оборудование и более производительные агрегаты.
Если вы нашли ошибку, пожалуйста, выделите фрагмент текста и нажмите Ctrl+Enter.
stankiexpert.ru
оборудование для холодной ковки своими руками
Ковка давно вошла в жизнь современного человека, если множество лет назад, эта технологическая операция применялась практически повсеместно. Ее применяли и для изготовления вооружения (мечи, доспехи), транспорта (обода колес), предметов обихода (засовы, дверные петли, и многое другое.
Ковка на наковальне
Вид горячей ковки
В наши дни ковка, может, и не такой популярный вид обработки металла, но и исключить его из перечня обработки металлов нельзя.Ковку применяют для получения заготовок валов, зубчатых колес. Не менее широко ее применяют и в быту, ее используют для получения декоративных элементов зданий и сооружения, ограждений и пр.
Следует отметить, что, кроме, горячей ковки, широкое распространение получила холодная. Если при первом способе заготовку постоянно подвергали нагреву и обработке ударным воздействием, то при втором методе применяют набор оборудования, позволяющий получать практически такие же детали, как и при горячей ковке.
Разновидности станков для ковки
К несомненным достоинствам холодной ковки металла необходимо отнести то, что исчезает необходимость в сооружении кузни и установки оборудования и приспособлений, без которых работы попросту невозможна (горн, наковальня и пр.).
Самодельный горн для ковки Наковальня для ковки металла
Холодная ковка металла может быть автоматизирована, причем без особых сложностей. Такое решение гарантирует повышение эффективности работы по изготовлению изделий. Даже неавтоматизированное производство позволяет поднять производительность труда, то есть она позволяет производить целые партии деталей по заданному образцу, другими словами, всегда существует возможность организации мелкосерийного и серийного производства. Это особенно выгодно при оформлении больших заказов, например, при изготовлении ограждений, решеток на окна и пр.Для обустройства мастерской холодной ковки нет необходимости в наличии больших площадей.
youtube.com/embed/T-eo1i0dyBc?feature=oembed” frameborder=”0″ allow=”autoplay; encrypted-media” allowfullscreen=””>При холодной ковке металла не происходит изменений во внутренней структуре металла, а это приводит к сохранению прочностных характеристик металла. При холодной ковке металла существует возможность искусственного старения металла и это позволяет производство деталей под старину.
В общем, можно сказать, то, что использование технологии холодной ковки позволяет выпускать относительно недорогую продукцию с высоким качеством.
Оборудование для горячей ковки
Если сравнивать холодный и горячий метод ковки, то сразу, можно сказать, то, что первый способ требует от работника значительно большего мастерства, наличия некоторых художественных навыков и, конечно, умения работать с набором необходимых инструментов.
Оборудование для горячей ковки
Ковка материала происходит после его предварительного нагрева в кузнечной печи. Ее называют горном. Горн оснащен оборудованием для принудительной подачи воздуха. Нагрев производят до заданной температуры и после этого переносят на наковальню. Это металлическая плита, на которой производят ударную обработку разогретой заготовки. Ее выполняют с помощью молотков и кувалд разного веса. Один работник, легким молотком наносит удар по нужному месту, а второй, вооруженный тяжелым молотком или кувалдой, наносит в обозначенное место сильный удар. После того как заготовка остыла, ее снова загружают в печь для нагрева. Все перемещения детали в процессе ее обработки выполняют с помощью клещей с длинными рукоятками.
Ручная горячая ковка
Кроме, вышеназванных основных инструментов при горячей ковке применяют множество специального инструмента, который позволяет резать горячий метал, формовать сложные поверхности при горячей ковке металла.
Кузнечный горн
Для нагрева заготовок применяют печи, которые называют кузнечным горном. В его конструкцию входит несколько узлов. В частности:
- ствол, выполненный из материала стойкого к воздействию огня;
- очаг, со встроенной колосниковой решёткой;
- системы подачи и отбора воздуха;
- рабочего окна через которые подают длинные заготовки;
- дымоход, через который происходит удаление продуктов горения.
Кузнечный горн газовый
Кроме того, в состав горна входит и закалочная ванна.В основе работы классического кузнечного горна лежит уникальная восстановительная способность углерода. Именно эта его способность с успехом противостоит окислению заготовки, то есть его горению. Тут важна и теплотворная способность углерода. Дело в том, что подавая воздух необходимо регулировать его количество. Его должно быть столько, что бы хватило сжечь углерод, а тепло, выделяемое при этом, поднимет температуру в горне еще выше.
Кроме того, подачу воздуха в горн необходимо настроить так, чтобы подаваемого кислорода не хватало для окисления металла. Но если разогретую заготовку продержать в таком состоянии свыше необходимого времени, то произойдет ее перенасыщение углеродом. Существует такой термин — пересушивание, то есть металл становится очень хрупким. Кстати, в качестве пересушенного металла можно привести чугун.
Муфельная печь
Оборудование, которое используют для разогрева деталей, выполненных из разных материалов до заданной температуры, называют муфельной печью.
Муфельная печь
Отличительной чертой этого оборудования является наличие муфеля. Так, называют деталь, которая защищает деталь от контакта с топливом и продуктами сгорания и в то же время служит камерой, в которой деталь нагревают.На практике применяют два вида таких печей, с постоянным и сменным муфелем. В первой печи загруженные детали проходят все операции — от нагрева до состояния готовности, во втором, только до охлаждения. То есть, по мере достижения необходимой температуры и определенной выдержки заготовки один муфель убирают и на его место устанавливают другой.
Надо отметить, что и кузнечный горн, и муфельные печи могут использовать разные виды топлива — газ, уголь, дрова, светлые и темные нефтепродукты и пр.
Наковальня
Один из ключевых инструментов применяемый и для холодной, и для горячей ковки металлов — наковальня. Именно на ее поверхности, кузнецы выполняют деформирование заготовки и приведение ее к готовому виду. Наковальню отличает большой вес и поэтому ее жестко фиксируют к деревянной колоде.
Наковальня — ключевых инструментов
Конструктивной наковальня состоит из:
- рога;
- наличника с отверстиями;
- основания с лапами для установки наковальни.
Для изготовления этого инструмента применяют сталь 45Л. Надо отметить, то что, наковальни — это продукция, выпускаемая в соответствии с рядом ГОСТ. Например, ГОСТ 11396-75 нормирует безрогие изделия с весом от 92 до 200 кг, а ГОСТ 11398-75, определяет требования к изделиям с двумя рогами и весом от 100 до 270 кг.
Твердость материала, из которого производят наковальни, составляет 340 — 477 по HB.
Станки для холодной ковки
Для выполнения работ по холодной ковке будут востребованы разные инструменты и технологическая оснастка. Большая часть необходимых инструментов можно приобрести в любом инструментальном магазине, но некоторые приспособления, вполне возможно, придется заказывать. Можно приобрести уже готовый набор для производства и приспособления для холодной ковки.
Станки для холодной ковки
В количество потребных инструментов входит сварочный аппарат. На рынке существует множество предложений по поставке сварочного оборудования, но для нужд кузни имеет смысл приобретать аппарат, который может работать как с постоянным, так и с переменным током. Такой аппарат позволяет работать с тонкими листами не опасаясь их испортить.Углошлифовальная машинка необходима для механической обработки заготовок. То есть, с ее помощью можно что-то подрезать, что-то отшлифовать. Такая машина должна обладать определенным запасом мощности и высокими оборотами. Не помешает и зачистная машинка, ее услуги будут востребованы в случае необходимости выравнивания сварного шва в труднодоступных местах, например, на стыке двух плоскостей. Из электроинструмента будет востребованы — дрель, перфоратор.
Кроме, перечисленного инструмента будет необходим и набор технологических приспособлений. Например, для получения отдельных деталей используют шаблон, его применяют для получения металлических дуг или колец. Без такого приспособления, как объемник невозможно получить узоры.Кузнечное оборудование для холодной ковки можно приобрести в составе готовых комплектов, а можно изготовить своими силами.
Станок улитка
С помощью оборудования под названием «Улитка» мастер может изготавливать различные завитки. Для большего удобства в работе применяют улитки с воротом.
Монолитная неразборная улитка
Станок торсионный
Торсионное оборудование для ковки предназначено для скручивания прутка вдоль оси.
Торсионы — ручная ковка
Для изготовления такого станка своими руками потребуются следующие материалы и инструменты:
- стальной лист;
- двутавр;
- слесарные тисы;
- крепеж;
- углошлифовальная машина;
- сварочный аппарат;
- приводная станция, которая состоит из редуктора и электрического двигателя.
Станок гнутик
Этот тип оборудования применяют для гиба пруткового материал или труб под определенный радиус и угол. Работа на таком оборудовании не требует приложения значительных усилий, а после обработки на нем, металл не изменяет свою структуру.
Гнутик для холодной ковки
Гнутики работают следующим образом. Для получения готового изделия заготовку устанавливают между гибочным валом и упором. Гибкий вал оказывает давление на заготовку, а упор, не дает ей деформироваться полностью.
Станок волна
Оборудование этого типа позволяет изготавливать изделия волнообразного типа из круга, квадрата и других типов проката. С его помощью получают такие детали, как волны и зигзаги.
Волны для выполнения волнообразного изгиба заготовки
Универсальный станок для холодной и горячей ковки НК-1Оборудование марки НК—1 это установка, в состав которой несколько блоков и позволяющий выполнять множество операций и изготавливать различные кованые детали, например, завитки, кольца и пр. Оборудование этой марки позволяет наносить рисунок на металлические полосы, трубы и другие виды профиля. При этом применяют метод холодной деформации.
Станки для холодной ковки своими руками
На самом деле качественные самодельные станки для выполнения холодной ковки встречаются нечасто. По-настоящему качественное оборудование возможно получить только в заводских условиях с использованием металлорежущего оборудования, термических установок и пр.
Если вы нашли ошибку, пожалуйста, выделите фрагмент текста и нажмите Ctrl+Enter.
stankiexpert.ru
Ручные станки для холодной ковки
Ручные станки для холодной ковки можно купить готовые, а можно собрать кузницу своими руками, приобретая или изготавливая всё собственноручно. Покупное оборудование, высокопроизводительное и дорогое. Для небольшой мастерской более подходит второй вариант.
Основные направления холодной ковки – ограды, ворота, оконные решетки, некоторые предпочитают художественную ковку и чувствуют себя дизайнерами по металлу.
Так как печь не нужна при холодной ковке, то из инструментов понадобятся только наковальня и молот. Из материалов – горячекатаная сталь: квадратный и круглый профиль различного сечения, листы.
Для художественной ковки могут понадобиться ещё и некоторые цветные металлы.Перед началом изготовления изделия нужно иметь представление о его конечном виде, кроме того желательно иметь чертёж или трафарет в натуральную величину.
Оборудование для холодной ковки позволяет гнуть, резать, клепать, делать отверстия. Условно технологические процессы производимые на них, делятся на два вида: гибка и скручивание.
Самыми распространенными устройствами являются: Гнутик, Твистер, Улитка, Глобус, Волна и Фонарик.
Гибочный ручной станок «Гнутик»
Это основной инструмент. Применяется для гибки прута, трубки под радиус или с заданным углом. Не требует больших усилий, не изменяет структуру металла. Принцип действия: Изделие устанавливается между центральным (гибочным) и упорным валами. Гибочный вал давит на металлопрофиль, а упорный не даёт загибаться всей заготовке.
Принцип действия устройства показан на видео.
Станок для скручивания «Твистер»
Позволяет закрутить профиль прямоугольного сечения вдоль продольной оси.
Видео: работа оборудования в действии.
Станок «Улитка»
Сворачивает стальные пруты в спирали, завитки, кольца и т.д. Радиус гибки ограничен только платформой. Представляет собой шаблон, для производства серийных изделий – литой, для индивидуальных работ – со съемными деталями.
Схема сборки приспособления своими руками
Общий вид
Как делать завитки на «Улитке»:
youtube.com/embed/T0T1FSxlKW4″ frameborder=”0″ allowfullscreen=”allowfullscreen”>Станок гибочный «Глобус»
«Глобус» это устройство, похожее на транспортир. Применяется для холодной ковки объемных изделий из полосы, прута квадратного сечения и трубок.Получается дуга с большим радиусом гиба, параллельно концы заготовок плавно сгибаются.
Работа на «Глобусе»:
Станок гибочный «Волна»
При помощи «Волны» создаются волнообразные изделия из проката различного профиля – квадрат, круг, шестигранник, трубки.Работа на приспособлении «Волна»:
Станок гибочный «Фонарик»
Позволяет изготавливать изделия сложной, объемной формы – «Корзинка», «Фонарик». Узкоспециальный станок, но для кого-то незаменимый. Плетение допустимо для сечения круглого профиля – 30мм, квадратного – 16мм.
Также для полноценной работы кузнечной мастерской может понадобиться обрезное устройство по металлу и пробойник отверстий.
Изготовление оборудования своими руками
А вот как он работает:
Вышеописанные приспособления для холодной ковки металла не слишком сложны в изготовлении, просты в эксплуатации, не прихотливы.
Если нет причин покупать высокопроизводительное оборудование для нужд, например, завода, а предполагается установка его в небольшую кузницу, есть все предпосылки сделать необходимое оборудование своими руками или заказать у мастеров – самодельщиков. Такое вложение средств окупится гораздо быстрее.
Можно начать с малого – с «Гнутика», постепенно расширяя свой станочный парк.
metmastanki.ru
Станок для холодной ковки
все для холодной ковки
“Прочный и универсальный, с
более чем 27 оснастками и
кондукторами, работающий с
материалом до 12мм
включительно за 44 тыс.

Оставьте заявку на станок
и мы свяжемся с вами!
Преимущества:
- Универсальный
- Компактный
- Удобный в работе
- Прочный
- С функцией трубогиба!
Фото полного комплекта:
В полный комплект входит:
- Станок с поворотной ручкой
- Универсальная станина
- Кондукторы для “радиусов”
- Оснастка для “торсиона”
- Кондукторы для “завитков”
- Кондукторы для “бубликов”
- Оснастка “вилка кузнечная”
- Оснастка для сгибания углов
- Кондуктор для “кольца”
а так же
весь необходимый крепеж,
ключи и инструкция.
Хотите узнать больше о станке ? закажите бесплатный обратный звонок!
Несколько слов разработчика:
“Здравствуйте.
Меня зовут Дмитрий. Я проектировщик станка.
Холодная ковка заинтересовала 5 лет назад, когда я только начинал
свой бизнес по производству художественных изделий. Гнул прутки на самодельных кондукторах, сделанных “на коленке”. Но хотелось большего
и я решил создать универсальный станок для холодной ковки.
Было потрачено много времени на его проектировку и реализацию.
Хотелось, чтобы станок был как надо: многофункциональным, прочным,
и с возможностью установки самодельных кондукторов если необходимо.
Цель была достигнута.
В нем есть все, что нужно: кондуктора для завитков, для кругов и овалов,
торсировка и сгибание углов… Я остался доволен проделанной работой.
Добавлю, точно такой же станок работает в моей мастерской,
и я гарантирую, что он будет приносить Вам не только деньги
от реализации изделий,но и удовольствие от работы на нем.
Присоединяйтесь!”
С уважением,
Дмитрий.
Основные базовые операции:
Гибка
завитков
“спираль
Архимеда”
Гибка
барашков
НОВИНКА!
В комплекте 4 кондуктора для гибки больших
и малых радиусов, в том числе из профильной
трубы до 20х40 – функция трубогиба!
Гибка
объемных
узоров
Так же Вы можете сделать свой кондуктор
нестандартной формы и закрепить его
на станке – крепления универсальные!
Работа с квадратом 10,12
Работа с
кругляком 10,12
Вы уже пробыли на сайте больше 15 секунд,
пожалуйста, уделите еще 45 секунд вашего времени-
это интересно!
Что вы получаете после покупки базовой комплектации станка ?
1. 28 кондукторов, позволяющие выполнять 100% поставленных
вами задач.
2. Стальной 10 мм! рабочий стол – круг, на котором
устанавливаются кондуктора. Выдержит любые нагрузки!
3. Многофункциональную станину, позволяющую устанавливать
дополнительное оборудование из комплекта “Профессионал”.
4. 2 усиленных подшипника вместо одного в узле вращения ручки.
5. Поворотную ручку из “усиленного швеллера” толщиной 6 мм.
Не боится никаких нагрузок!
6. Возможность установки 8ми кондукторов для профильной
трубы.(Отдельно продаются только владельцам станка!).
7. Возможность установки любого ,сделанного вами,
дополнительного кондуктора приглянувшейся формы.
8. Действительно проверенный в работе станок и кондуктора!
На таком же станке работаем сами.
Как купить станок ?
Вы оставляете
заявку
Оплачиваете
доставку по
тарифу
Транспортной
Компании
Мы отправляем
Вам станок
Оплачиваете
оставшуюся
часть суммы
РЕАЛЬНЫЕ ОТЗЫВЫ ЛЮДЕЙ, УЖЕ КУПИВШИХ СТАНОК:
youtube.com/embed/f29ruv4i9qk?autoplay=0&loop=0&showinfo=0&theme=light&color=red&controls=1&modestbranding=0&start=0&fs=1&iv_load_policy=3&wmode=transparent&rel=0″ frameborder=”0″ allowfullscreen=””>Евгений, Якутск.
Сергей, Санкт – Петербург.
Николай Б. Москва
“Хотелось что-то делать своими руками. В гараже был сварочный аппарат, болгарка,
и еще кой какой инструмент. Заинтересовала холодная ковка, и пересмотрев много вариантов решил заказать станок для холодной ковки в “Станковке”.
Через 4 дня станок был уже у меня в гараже.
Пока осваиваю, делаю пробные элементы, ведь скоро сезон начнется – будут заказы, уже и
некоторые соседи просили украсить одному калитку, другому ворота. Станок отличный – крепкий и много чего может делать.”
Немного о нас в цифрах:
Более 1000 городов России куда возможна доставка, 96% довольных клиентов, более 17 городов где уже работает наш станок, более 25 проданных комплектов, более 40 объектов оформленных изделиями с помощью нашего станка.
“Позвольте себе и Вы работать на качественном оборудовании!”
Где мы находимся ?
Наши контакты:
все для холодной ковки
stankovka.ru
Холодная ковка своими руками – типы, особенности, чертежи, станки
Владельцы частных домов и дач с удовольствием оборудуют свое жилище коваными изделиями. Такие предметы превосходно смотрятся в интерьере любого стиля. Они подходят для создания элементов декора в каменных, а также деревянных домах. Металлические предметы горячей обработки имеют главный недостаток – высокую цену. Отличной альтернативой является ковка холодная, готовые элементы которой имеют невысокую стоимость и доступную технологию изготовления. При таком процессе нагрев металла отсутствует, а получение необходимой конфигурации производится гибкой с последующим прессованием и выполнением сварки составляющих частей.
Типы ковки холодным методом
Выполнение операций по обработке металла требует соблюдения мер безопасности. Холодная ковка своими руками, видео основных процессов которой находится в свободном доступе, не требует специальных познаний. Достаточно иметь первоначальное обучение по работе со слесарными приспособлениями. Изготовление декоративных металлоизделий при холодной ковке своими руками выполняется при помощи трех основных типов технологических процессов:
- вытяжка;
- кручение;
- гнутье.
Вытяжка
На этом этапе металлическая заготовка удлиняется с одновременным уменьшением своего сечения. Для данного процесса применяются прессовочные или же раскаточные станки. Проходящая через вальцы заготовка постепенно изменяет свою форму. На валиках могут иметься насечки рельефного типа для придания детали особой текстуры. Таким способом обработки получают декоративные лапки, пики.
Кручение
При этой обработке проводится скручивание стального прута или же полосы. Этим способом можно закручивать несколько заготовок одновременно. При этом один конец металлоизделия крепится в зажиме тисков, а второй проворачивается вдоль оси. При приложении осевого усилия на несколько скрученных прутов получится фигурное утолщение («корзинка» или же красивый «фонарик»).
Гнутье
Это воздействие проводят, используя специальные станки, по заранее заготовленным шаблонам. Металлоизделие подвергается изгибу в разных плоскостях, что предоставляет возможность изготавливать разнообразные декоративные элементы. Предлагаемые производителями станки имеют высокую стоимость, однако их можно соорудить самостоятельно.
Особенности производства металлической ковки холодным методом
Созданные в домашних условиях элементы холодного типа ковки не настолько вычурные, как полученные горячим методом, однако имеют превосходный декоративный вид. Имея под рукой набор специальных приспособлений, инструментов, оборудования, материалов можно создавать великолепные вещи, при этом соблюдая порядок технологического процесса.
Сначала подготавливается эскиз изделия. На первом этапе для работы берутся элементарные вещи. После получения необходимых навыков и овладения приемами работы, можно приступать к изготовлению более сложной продукции. На эскизе изображается общий рисунок, размеры, необходимые составные части. Учтите, что имеющееся в распоряжении оборудование предназначено для определенных операций.
После предварительного эскизного этапа проводится расчет материалов для изготовления металлоизделия. В зависимости от его сложности будет зависеть список материальных компонентов. Для простой подставки можно обойтись металлической трубой и стальными полосами, а для изготовления ворот потребуется более широкий ассортимент материалов.
Перед началом производства повторно проверяются расчеты, от которых будет зависеть конечный вид готового металлоизделия. Этот этап весьма важен, так как исправлять и выполнять подгонку продукции всегда сложнее, чем изготовить новые детали. После этого начинается основной этап создания элементов будущей конструкции. Имея в наличии составные компоненты, проводится их сборка посредством сварки и клепки. На финальном этапе выполняется шлифовка, а также покраска готового металлоизделия.
Используя этот метод, можно получить декоративные компоненты для калиток, ворот, разнообразных заборов, цветочные подставки, обрамления для зеркал и солидных картин. Помимо этого, изготавливаются фигурные ножки для столов, скамеек, стульев, детали козырьков, навесов, перил, оконные решетки, а также прочие декоративные и защитные металлоизделия. Полученные узоры металлоизделий холодной ковки своими руками становятся уникальными авторскими находками.
Приспособления и станки
Домашняя холодная ковка применяет оборудование, сооруженное своими руками, видео с которым покажет основные этапы работы. Специальные станки оснащаются ручным приводом или же электрическим. Спецоборудование для формирования завитков и плоскостных спиралей называется твистерами или закручивателями. Приспособления торсионного типа применяются для винтового кручения металлического прута, деталей из спиралей объемного вида (филаментов): луковиц, фонариков, а также корзинок.
На инерционно-штамповочном оборудовании расплескивают в особые фасонные наконечники концы прутьев, выдавливают рельефную и волновую поверхность, а также штампуют соединительные декоративные хомуты. Станки гибочного типа подразделяются на протяжные, нажимного воздействия и комбинированные. При помощи протяжного оборудования получают завитки, кольца и разнообразные спирали, имеющие широкие ядра. Нажимные приспособления позволяют создавать зигзаги, волны, а комбинированные станки выполняют все вышеперечисленные операции.
Конструкция станков
Выполняемая холодная ковка своими руками, станки, чертежи, видео для которой представлены, позволяет создавать великолепные художественные металлоизделия. Используя основные типы станков, создаются красивые узоры из металлопродукции профильного типа. Упрощенное название гибочного ручного оборудования – гнутики.
Эти приспособления применяются для получения зигзагов и волновых деталей. Для изменения угла зигзага, а также высоты волны и шага заменяется клин или прижимной ролик в центральной части. В качестве материала для этого спецоборудования служит специальная сталь, способная выдерживать повышенные нагрузки.
Твистеры-улитки имеют широкие возможности и простейшую конструкцию. Они подразделяются на улитки с лемехом поворотного типа и воротом, а также рычажные с обводным роликом. На них можно выполнять холодную ковку из профильной трубы и прочих металлических заготовок.
Станки торсионного типа увеличивают производительность, а также качество производимых деталей. Они имеют прочную станину, на которую передается основная нагрузка. Для удержания квадратного прута служат патроны-оправки, имеющие квадратного сечения гнезда. Их крепление в скользящей задней бабке и шпинделе выполняется винтовыми зажимами. Скручивание участков металлических заготовок производится при помощи подвижного ограничителя со специальной вставкой.
Изготовление наконечников на прутьях выполняется на специальном штамповочном приспособлении. Этот специальный станок использует принцип маховика. Вращая грузовую штангу, отводится назад винтовой боек. После этого в специальное гнездо вставляется штамп, и устанавливается заготовка. Раскрученная штанга приводит ударный боек в движение и происходит удар по хвостовику штампа, воздействующего на конец прута.
Для самостоятельного изготовления такого спецоборудования необходимы валки из специальной стали, шестерни, втулки для подшипников и валы.
Изготовление станка собственноручно
Перед тем как сделать холодный ковки станок, определяются с его конструкцией, а также возможностями. Сооруженные своими руками специальные приспособления позволят проводить ковку металлических предметов в практически в домашних условиях. В качестве рабочего места вполне подойдет гараж, хозяйственный блок или сарай. Определившись с ассортиментом будущей продукции, приступают к созданию приспособлений по ее выпуску. Полноценная процедура производства требует наличия всех типов станков по ковке холодным способом. Для ускорения процесса изготовления оборудования следует просмотреть соответствующие видео, где представлены уроки по сборке станков, а также изготовлению металлоизделий. Сделать собственноручно подобный станок можно используя чертежи, схемы, которые можно брать в качестве основы и изучая видеоуроки. Это позволит избежать многочисленных нюансов при создании собственной мехмастерской.
Холодная ковка, оборудование для которой своими руками изготавливается бесплатно при помощи чертежей, позволит изготавливать авторские узоры разнообразных металлоконструкций. К наиболее распространенным станкам относятся улитки, которые предоставляют возможность изготавливать многочисленные кованые холодным способом завитушки из профильной трубы, а также прочего проката. На чертеже представлен классический вариант станка-улитки, который можно соорудить в любом гараже, а ниже приведено описание конструкции.
Для стола используется листовая сталь от 10 мм. В качестве ножки применяется круглая толстостенная труба или же другой подходящий профиль. Конструкция должна иметь прочное основание, так как воспринимает высокие боковые нагрузки при работе. Рычаг изготавливается из трубы квадратного профиля со стенкой порядка 3 мм. Оптимальным считается размер 25×40 мм. Рычаг крепится к ножке посредством подшипникового узла или же другим способом. Подшипник значительно облегчит работу для получения фигурного профиля. Такая конструкция может дополняться собственными идеями по использованию дополнительных станковых приспособлений.
К изготовлению своими руками станков и приспособлений следует подойти весьма ответственно и скрупулезно. От правильности чертежей, а также выполненных расчетов зависит качество станков, а также создаваемых металлоизделий. Получив навыки и сноровку, оборудование можно разнообразить для совершенствования выпускаемой продукции.
oxmetall.ru
Самодельный станок для холодной ковки: процесс изготовления
Создание кованых изделий производится при помощи горячей и холодной обработки. Последний метод не требует особых навыков, но для его осуществления нужны специальные приспособления. Существуют различные чертежи станков холодной ковки, многие из которых подходят для самостоятельного создания инструмента.
Особенности изготовления
Формируются кованные металлические элементы в результате деформации, при этом в процессе работ должны приниматься во внимание эксплуатационные характеристики материала.
Структура кристаллической решетки металла состоит из зерен, имеющих неправильную форму. Инструмент, используемый для ковки, воздействует на нее и приводит к изменению вида детали. Особое значение имеет подбор чертежей станков, так как заготовка должна сохранить свои прежние свойства.
Самодельный станок для холодной ковки: правила изготовления
Существуют определенные правила, соответствие которым обеспечивает получение необходимого результата:
- Создание подходящей конфигурации возможно при помощи нескольких инструментов.
- Перед началом изготовления производится расчет параметров формируемых изделий.
- Прутки, используемые для заготовок, могут иметь различный диаметр, который подбирается с учетом степени сложности техники и последующей эксплуатации.
- Обработке подлежит только низкоуглеродистая сталь, так как другие виды не имеют необходимой пластичности.
“Гнутик”
Ручные станки для холодной ковки можно изготовить самостоятельно, достаточно разобраться в тонкостях использования инструмента и подобрать подходящий чертеж. “Гнутик” необходим для создания углов различной конфигурации. Его основными конструктивными элементами являются движущий упор и два вала, размещенные на стальной пластине.
Самодельные гибочные станки холодной ковки подобного вида должны создаваться в соответствии с некоторыми особенностями. К примеру, изначально должен быть определен угол деформации. Также возможно добавление дополнительного гибочного элемента, в случае его использования монтируется третий вращающий вал.
Инструмент изготавливается из специальной стали, так как на него в процессе приходятся большие нагрузки. Стоит отметить возможность сбора различных деталей, в том числе и волнообразных.
“Твистер” и “Улитка”
Сегодня художественная ковка не обходится без деталей в форме шнека. Их создание обеспечивают ручные станки для холодной ковки под названием “Твистер”. Они имеют характерную особенность, заключающуюся в прокручивании прута вдоль оси. Инструмент состоит из подвижной и фиксирующей части. Поворотной рукоятью производится деформация заготовки, которая фиксируется между основными деталями конструкции. Стоит отметить, что спираль формируется со стороны крепления изделия, а прилагаемые усилия можно уменьшить при грамотном расчете рычага, оказывающего давление. Данное приспособление позволяет изготавливать детали для металлических оград и оконных решеток.
“Улитка” представляет собой простейший самодельный станок для холодной ковки, который обеспечивает формирование спиралей с требуемым количеством витков. Он отличается наибольшей популярностью и может адаптироваться для изготовления желаемого изделия. Инструмент оснащается ручным или электрическим приводом, вид которого подбирается в соответствии с интенсивностью эксплуатации.
Самодельный станок для холодной ковки: подготовка материалов
Для начала необходимо вычертить спираль с идентичным шагом всех витков. При этом нужно отталкиваться от используемых заготовок, так как ширина хода, как правило, находится в пределах 15 мм, в то время как инструмент предназначается для прутков с сечением в 10 мм. Свободное пространство необходимо для маневра, так как при полном сжатии заготовки изгиб станет невозможным.
Далее необходимо вырезать пластину размером 20х20 см из стального листа. Несмотря на небольшие габариты, она обеспечит оптимальное проведение рабочего процесса. В соответствии с длиной предполагаемой “улитки” выполняется отрез из стали. Полосу необходимо согнуть с помощью плоскогубцев, поместить на пластину и очертить ярким маркером со всех сторон.
Далее отрезается часть прута с длиной, равной ширине полосы из стали. Главное, чтобы она не превышала данный параметр, так как это может привести к травмам в процессе гибки. Прут необходим для закрепления материала на первом этапе создания изделия, чтобы предотвратить свободный ход в одной точке.
От профилированной трубы отрезается часть с длиной в 10 см. Она объединит лист и основание, на котором будет производиться фиксация. Из-за высокой степени нагрузки должны применяться только толстостенные материалы. После того как все основные элементы будут подготовлены, можно собирать самодельный станок для холодной ковки, чертеж которого представлен ниже.
Сборка конструкции
Стальная “улитка” разделяется на витки, первый из которых будет удерживать заготовку, а на других будут идти сами витки прута. Центральная часть приваривается к основанию, при этом на полученном шве должны отсутствовать даже малейшие недочеты. Куски прута привариваются к основной части полосы, расстояние между ними должно составлять 3 см. Необходимо проявить осторожность при формировании швов, после чего сбить их при помощи молотка.
Затем устанавливаются в необходимых местах отрезки полосы и обводятся маркером. Полученные круги нужны для формирования отверстий. Они должны полностью соответствовать диаметру ножек для обеспечения легкой установки и снятия.
Завершающим этапом становится приварка профильной трубы в нижней части, а также фиксирующего элемента рядом с “улиткой”. Фото самодельных станков холодной ковки, изготовленных подобным образом, представлено выше.
fb.ru
Как сделать станок для холодной ковки своими руками
Большая востребованность кованых металлических изделий поднимает спрос на изготовленный своими руками станок для холодной ковки. Красивые металлические двери, ворота, забор и иные элемента декора способствуют развитию бизнеса для домашних мастеров. Для него потребуется купить или сделать самостоятельно некоторые узлы.
Проектирование станка в домашних условиях
В процессе проектирования оборудования рекомендуется предусмотреть многовариантный тип аппарата, позволяющий выпускать изделия различной сложности. Помогает в этом применение множества сменных насадок.
При разработке учитываются факторы:
- базой служит металлическое полотно, габариты его зависят от количества применяемых узоров;
- поверх полотна размещаем шаблоны так, чтобы не мешать работе с другими заготовками;
- крепятся шаблоны как простые (с одним поворотом), так и модели, позволяющие делать узоры как улитка лемешного типа;
- используем для мобильных частей высокопрочный материал;
- смена насадок осуществляется благодаря прорези прямоугольной формы, куда ставятся шаблоны для ковки.
Насадки крепятся болтовыми соединениями.
Сборка агрегата
Пошаговая сборка состоит из пунктов:
- собирается опорная стойка из отрезков трубы равного размера, у которой патрубок приваривается к верхнему и нижнему краю;
- нарезаем круги и 4 равносторонних треугольника, последние свариваем в пирамиду, основание которой фиксируем сваркой в центре окружности;
- 4 горизонтальные планки болтами крепим к кругу;
- из нескольких металлических прутов сооружаем рукоятку;
- к концу рычага монтируем подшипники, а также к отрезку внизу конструкции;
- верхний отрез монтируем горизонтально, чтобы он позволил гнуть металл;
- в нижней части отрезка, где свободный конец, делает отверстие по сечению трубы.
Финишной операцией служит соединение рукоятки с “пирамидой” с помощью гайки большого диаметра. Улитку фиксируем для шаблона сваркой.
stankiwse.ru
Как делают болты? Вот производственный процесс
Болты являются одним из основных компонентов проектирования и строительства, однако их производство стало передовым высокотехнологичным процессом, состоящим из нескольких этапов. Узнайте, как необработанная сталь превращается в высокоточные и точные металлические инструменты.
Болты могут быть самых разных размеров и форм, но основной производственный процесс, как правило, остается одним и тем же. Он начинается с холодной ковки стальной проволоки в нужную форму, за которой следует термообработка для повышения прочности и обработка поверхности для повышения долговечности перед упаковкой для отправки. Однако для более сложных конструкций болтов производственный процесс может быть расширен за счет ряда дополнительных этапов.
Являясь одним из ведущих поставщиков крепежных изделий для автомобильной промышленности, шведский производитель Bulten обладает высокой квалификацией на каждом этапе производства болтов. «Мы не производим детали по каталогам — все, что мы производим, разрабатывается по индивидуальному заказу в соответствии со спецификациями заказчика», — говорит Хенрик Оскарсон, технический директор завода Bulten в Гальстахаммаре, Швеция.
«В зависимости от того, где будет использоваться крепеж, существует несколько различных вариантов изготовления именно того болта, который нужен».
Производственный процесс
Холодная ковка
Холодная ковка начинается с больших стальных прутков, которые разматываются и нарезаются по длине. Марка стали стандартизирована в отрасли в соответствии с требованиями ISO 898-1. Затем с помощью специальной оснастки проволоке придают нужную форму методом холодной ковки. Это в основном то, где сталь формуется при комнатной температуре, продавливая ее через серию штампов под высоким давлением. Сама оснастка может быть довольно сложной и содержать до 200 различных деталей с допусками в сотые доли миллиметра. После усовершенствования холодная ковка позволяет производить болты быстро, в больших объемах и с высокой однородностью.
Для более сложных конструкций болтов, которым нельзя придать форму только с помощью холодной ковки, может потребоваться дополнительная токарная обработка или сверление. Токарная обработка включает в себя вращение болта на высокой скорости, в то время как сталь отрезается для достижения желаемой формы и дизайна. Для просверливания отверстий в болте можно использовать сверление. При необходимости к некоторым болтам на этом этапе процесса могут быть прикреплены шайбы.
Термическая обработка
Термическая обработка — это стандартный процесс для всех болтов, который включает воздействие на болт экстремальных температур для упрочнения стали. Нарезание резьбы обычно применяется перед термической обработкой путем прокатки или резки, когда сталь мягче. Прокатка работает так же, как холодная ковка, и включает в себя пропускание болта через штамп, чтобы придать стали форму и сформировать резьбу. Резка включает в себя формирование резьбы путем резки и удаления стали.
Поскольку термическая обработка изменяет свойства стали и делает ее более твердой, проще и дешевле нарезать резьбу заранее. Однако нарезание резьбы после термической обработки будет означать более высокие усталостные характеристики.
«Термообработка может привести к образованию тепловых пятен и незначительным повреждениям болта», — объясняет Хенрик Оскарсон. «По этой причине некоторые клиенты требуют нарезания резьбы после термической обработки, особенно для таких применений, как болты двигателя и головки блока цилиндров. Это более дорогой процесс, так как вам нужно формовать закаленную сталь, но резьба будет лучше сохранять свою форму».
Размер и поверхность
Для длинных болтов, длина которых более чем в десять раз превышает диаметр болта, термическая обработка может привести к возвращению стали к круглой форме исходной стальной проволоки. Поэтому часто необходимо применять процесс выпрямления.
Выбор обработки поверхности определяется назначением болта и требованиями заказчика. Часто основным требованием для крепежа является коррозионная стойкость, поэтому обычным решением является оцинкованное покрытие, нанесенное путем электролитической обработки. Это процесс, при котором болт погружается в жидкость, содержащую цинк, и подается электрический ток, так что цинк образует покрытие на болте. Однако электролитическая обработка сопряжена с повышенным риском водородного охрупчивания. Другой вариант — цинковые чешуйки, которые обеспечивают еще более высокую коррозионную стойкость, хотя и по более высокой цене.
Если коррозионная стойкость не является проблемой, например, внутри двигателя или в системе, которая регулярно подвергается воздействию масла, использование фосфатов является более экономичным вариантом. После обработки поверхности стандартные болты обычно готовы к упаковке. Однако для более сложных конструкций может потребоваться дополнительная сборка, например кронштейны. Другие болты также потребуют исправления в той или иной форме, будь то фиксирующая заплата или жидкая заплата. Фиксирующая накладка состоит из толстого нейлонового слоя поверх нитей, который помогает улучшить сцепление. Жидкий пластырь поможет улучшить момент закручивания резьбы.
После выполнения этих шагов болт готов. Теперь все, что осталось, — это некоторая форма контроля качества, чтобы гарантировать однородность и согласованность, прежде чем болты можно будет упаковать и отправить.
Краткое описание производственного процесса:
- Проволока – Размотана, выпрямлена и нарезана по длине.
- Холодная ковка – Придание стали нужной формы при комнатной температуре.
- Головка болта – Постепенное формование путем продавливания стали в различные пресс-формы под высоким давлением.
- Нарезание резьбы – Резьба формируется накатыванием или нарезанием.
- Термическая обработка – Болт подвергается воздействию высоких температур для закалки стали.
- Обработка поверхности – Зависит от области применения. Цинкование часто используется для повышения коррозионной стойкости.
- Упаковка/хранение – После контроля качества для обеспечения однородности и согласованности болты упаковываются.
Понравилась эта статья и хотите еще?
Получайте информацию о проектировании и болтовых соединениях прямо на свой почтовый ящик. Подпишитесь на нашу информационную рассылку прямо сейчас!
Поделитесь этой статьей
Подпишитесь на наш бесплатный журнал
Будьте в курсе последних новостей, идей и знаний в индустрии болтовых соединений, подписавшись на журнал Bolted!
АЛ АК Аризона дополненная реальность Калифорния СО КТ DE Флорида Г.А. ЗДРАВСТВУЙ Я БЫ Иллинойс В Я КС Кентукки Лос-Анджелес МНЕ доктор медицины Массачусетс Ми МН РС МО МТ северо-восток НВ Северная Каролина Нью-Джерси Нью-Мексико Нью-Йорк Северная Каролина нет данных ОЙ ХОРОШО ИЛИ ЖЕ Пенсильвания Род-Айленд СК SD Теннесси Техас UT ВТ Вирджиния Вашингтон Западная Вирджиния Висконсин ВГ
Алжир Аргентина Аруба Австралия Австрия Бангладеш Бахрейн Беларусь Бельгия Белиз Бутан Боливия Босния и Герцеговина Бразилия Бруней Болгария Камбоджа Канада Чили Китай Колумбия Коста-Рика Хорватия Кипр Чешская Республика Дания Доминиканская Респблика Эквадор Египет Эль Сальвадор Эстония Фиджи Финляндия Франция Германия Греция Гуам Гватемала Гайана Гондурас Гонконг Венгрия Индия Индонезия Иран Ирландия Израиль Италия Япония Казахстан Кувейт Лаос Латвия Литва Люксембург Македония Малайзия Мексика Монголия Черногория Марокко Мозамбик Мьянма Намибия Нидерланды Непал Новая Каледония Новая Зеландия Никарагуа Нигерия Норвегия Оман Пакистан Панама Папуа – Новая Гвинея Парагвай Перу Филиппины Польша Португалия Пуэрто-Рико Катар Румыния Россия Сайпан Саудовская Аравия Сербия Сингапур Словакия Словения Южная Африка Южная Корея Испания Шри-Ланка Суринам Швеция Швейцария Тайвань Танзания Таиланд Тимор – Лесте Тринидад Тунис Турция Украина Объединенные Арабские Эмираты Соединенное Королевство Уругвай Соединенные Штаты Венесуэла Вьетнам Замбия Другой
Да – цифровой Да – Печать Да, оба
Чтобы узнать больше о том, как мы обрабатываем ваши контактные данные, ознакомьтесь с нашей Политикой конфиденциальности .
Спасибо за подписку на журнал Bolted!
Руководство по ковке Глоссарий терминов
СТАРИТЕЛЬНОЕ УПРОЧНЕНИЕ : Процесс повышения твердости и прочности сплава путем осаждения частиц фазы из пересыщенного твердого раствора сплава. Цикл закалки обычно состоит из нагревания или отжига при температуре, достаточно высокой для сохранения твердого раствора; быстрое охлаждение или закалка для сохранения пересыщенного твердого раствора и последующее нагревание при температуре ниже температуры отжига раствора для осуществления осаждения.
СПЛАВ : Вещество, имеющее металлические свойства, состоящее из двух или более элементов, по крайней мере один из которых является металлом.
ОТЖИГ : Процесс, включающий нагрев и охлаждение, предназначенный для: (1) размягчения холоднодеформированной структуры путем рекристаллизации или роста зерен, или того и другого; (2) размягчение дисперсионно-упрочненного сплава за счет почти полного выделения второй фазы в относительно крупнозернистой форме; (3) размягчение некоторых закаливаемых сплавов путем растворения второй фазы и достаточно быстрого охлаждения для получения пересыщенного раствора; (4) снятие остаточного напряжения.
ЭКСТРУДИРОВАННЫЙ : Состояние металлического проката, полученного в результате горячего прессования – мягкое, не очищенное, не вытянутое и не прокатанное по размеру. См. «ЭКСТРУЗИЯ»
BAKED ON : Состояние поковки, при котором смазка обугливается на поверхности поковки.
БИХРОМАТНОЕ ПОКРЫТИЕ : См. «ПОКРЫТИЕ»
ЗАГОТОВКА : Заготовка, вырезанная из прутка для нагрева и ковки.
ВЕС ЗАГОТОВКИ : Масса готовой, распиленной и очищенной от заусенцев заготовки или заготовки, вырезанной из кованого материала.
БЛОКИРОВКА : Штамп преформы или слепок, используемый, когда деталь не может быть изготовлена за одну операцию.
BOSS : Выступ, выходящий из основной части поковки.
НИЖНЯЯ МАТРИЦА : Стационарная полуматрица.
РАЗБОРКА : Операция предварительной ковки.
ЯРКАЯ ОТДЕЛКА : См. «ОТДЕЛКА»
ПРОШИВКА : Метод удаления металла путем его строгания рядом зубьев, движущихся по прямой линии, так что каждый зуб по мере своего продвижения удаляет определенное количество металла.
ПОЛИРОВАНИЕ : Отделка металлических поверхностей составом, наносимым на гибкое колесо, вращающееся с высокой скоростью. Окрашивание и стрижка — это два типа полировки.
ЗАРЕЦ : Тонкий гребень или шероховатость, оставленная в результате операции резания, такой как продольная резка, резка, вырубка или пиление.
УГЛЕРОД : Применительно к поковкам углеродистый остаток, образующийся в результате сжигания смазки на поверхности заготовки, вырезанной из деформируемого материала или штампованной детали.
CAST : Заливка расплавленного свинца или серы в полость штампа для обозначения формы поковки.
ПОЛОСТЬ : Оттиск в верхнем или нижнем штампе.
ФАСКА : Скошенная поверхность, обычно под углом от 150 до 450, для слома острого угла или кромки.
ДРОССЕЛЬ : Уменьшение площади для замедления потока металла.
ИЗМЕЛЬЧИТЕЛЬ ИЛИ ИЗМЕЛЬЧИТЕЛЬНЫЙ ПРЕСС : Машина, используемая для резки, а не для распиловки заготовок, вырезанных из кованого материала.
ЗАЖИМНАЯ ПРОУШИНА : проушина или бобышка, добавленная к поковке, чтобы можно было выполнять обработку и формовку по центру с помощью одной установки или зажима. Этот выступ обрабатывается или вырезается на готовом изделии.
CLIP : Для удаления вспышки.
ОБРЕЗАНИЕ И ОБРЕЗАНИЕ : Двойная операция, при которой одна режущая поверхность в обрезном штампе удаляет заусенец, а затем поковка проталкивается дальше за другую кромку, которая обрезает и формирует весь контур или внешнюю поверхность поковки.
ОБРЕЗНАЯ КРАЙ : Там, где вспышка обрезается или обрезается.
МОНЕТА : См. «ХОЛОДНАЯ ШТАМПОВКА»
ХОЛОДНОЕ ЗАКРЫТИЕ : На поковке часть поверхности, которая отделена оксидом от основной массы металла.
ХОЛОДНАЯ ШТАМПОВКА : Для повторного штамповки в холодном состоянии, чтобы обеспечить меньший допуск, заострить углы или очертания, уменьшить толщину сечения, сгладить определенную поверхность, повысить твердость или добавить надписи.
ПОКОВКА С ПОРОШКОМ : Обычная штамповка, изготовленная по специальной технологии, в которой используется горизонтальное действие штампа в сочетании с вертикальным действием ковочного пресса. Это приводит к образованию полостей, невозможных при стандартных процедурах ковки.
ЗЕНКОВКА : скашивание устья отверстия или полости таким образом, чтобы при сверлении не оставалось заусенцев, или для увеличения части отверстия, сужающейся под определенным углом и до определенного диаметра.
УДАР : Заусенцы удалены.
ПЛОТНОСТЬ : Вес на единицу объема.
МАТРИЦЫ : металлические блоки с полостями такой формы, чтобы придать желаемую форму металлической заготовке, когда матрицы соединяются вместе.
МАТРИЧНЫЙ БЛОК : Стальной блок, в котором вырезается или утапливается оттиск.
ДЕРЖАТЕЛИ МАТРИЦ : Стальные блоки, используемые для удержания пуансона или матрицы.
КОМПЛЕКТ МАТРИЦ : Держатели для автономного набора штампов, в которых выравнивание пуансона и штампа поддерживается без помощи пресса.
DIE SHIFT : Отпечаток верхнего штампа не совмещен с оттиском нижнего штампа, а также величина смещения.
ПРОЕКТ : конус на вертикальной поверхности для облегчения удаления поковки из штампа или пуансона.
ВЫТЯЖЕННАЯ ФОРМА : Заготовка, доведенная до окончательных размеров путем холодного волочения через штамп, независимо от состояния или предшествующих операций.
СВЕРЛИЛЬНЫЙ ЦЕНТР : Углубление, выкованное для облегчения запуска сверла.
ЭКСЦЕНТРИК : полость или любая часть поковки с центром, не совпадающим с центром основной детали.
УДЛИНЕНИЕ : Постоянное удлинение образца, который был растянут до разрыва при испытании на растяжение. Процентное удлинение является показателем пластичности. См. «ТЕСТ, НАТЯЖЕНИЕ»
.ПРОЦЕНТ КОНЦА : Поправка на потерю концов стержня.
ТРАВЛЕНИЕ :
(1) Применительно к изделиям проката и поковкам – воздействие коррозионных сред, приводящее к образованию ямок, мясистости или контуров структурных деталей металла
(2) В металлографии – процесс выявления структурных деталей с помощью преимущественное воздействие реагентов на металлическую поверхность.
ЭКСТРУДИРОВАННЫЙ БРУТ : Запас доведен до финала
ЭКСТРУДИРОВАННЫЙ СТЕРЖЕНЬ : Размеры по экструзии.
ЭКСТРУДИРОВАННАЯ ФОРМА : См. также «ЭКСТРУДИРОВАННАЯ»
ЭКСТРУЗИЯ : Процесс формования металла в выбранную непрерывную форму путем продавливания его через матрицу соответствующей формы. См. «ЭКСТРУДИРОВАННЫЙ»
ПЕРО ИЛИ РЕБРО : Тонкий выступ, образующийся на поковке, когда металл под давлением входит в волосяные трещины, вызванные нагревом и износом штампов или образованные обрезкой.
СОПРЯЖЕНИЕ : Изогнутый внутренний угол для увеличения прочности объекта в углу и улучшения внешнего вида. Также важно, поскольку это увеличивает срок службы кузнечного штампа.
ОТДЕЛКА : Состояние поверхности продукта, полученного обычным или специальным способом прокатки. Можно получить несколько типов отделки, в том числе:
(1) Бихроматная отделка погружением — полуматовая отделка, приближающаяся к истинному цвету металла, полученная путем погружения в водный раствор бихромата натрия и серной кислоты для удаления окалины и оксида.
(2) Bright Dipped Finish – блестящая отделка, имеющая истинный цвет металла, полученная путем погружения в водный раствор серной и азотной кислот.
ВЕС ОТДЕЛКИ : Вес обрезанной или обработанной поковки.
ПРИСПОСОБЛЕНИЕ : Устройство, используемое для удержания заготовки во время механической обработки.
ФЛАНЕЦ : Выступающий край для крепления или придания жесткости.
FLASH : Избыток металла, который вытекает между верхним и нижним штампами и требуется для получения желаемой формы поковки.
FLASH EXTENSION : Количество металла, выходящего за пределы детали на линии заусенца.
FLASH LINE : Линия, на которой происходит вспышка.
ПРАВКА : Предварительная операция, выполняемая на заготовке, вырезанной из кованого материала, для размещения металла для окончательной поковки, или выполняемая на готовой поковке для устранения последствий коробления.
ПЛАВАЮЩАЯ МАШИНА : Тип конструкции, в которой матрица поддерживается пружинами. Обычно используется для формирования глубоких полостей.
ПОТОЧНЫЕ ЛИНИИ : структура зернистой структуры металла, выявляемая на полированном и протравленном участке горячей или холодной штамповки, которая показывает, каким образом металл был деформирован для заполнения и повторения контура штампа.
СКЛАДКА : См. «LAP»
КОВКА : Производство полуфабрикатов из кованых металлических заготовок горячим или холодным способом в закрытых штампах внезапным резким ударом. См. «КОВКА В МОЛТОМ» и «КОВКА В ГОРЯЧЕМ ПРЕССЕ»
.ДИАПАЗОН КОВКИ : Температурный диапазон, в котором следует нагревать заготовку, вырезанную из кованого материала, для достижения оптимальных условий ковки.
ЗЕРНА : Средний диаметр зерен, обычно определяемый микроскопически, на протравленной плоской поверхности металла, как описано в стандартном методе ASTM E112.
ШЛИФОВКА : Процесс черновой отделки деталей с помощью вращающегося абразивного круга.
ЖЕЛОБ : Небольшое углубление, окружающее полость в головке, для сброса давления и контроля мгновенного потока.
МОЛОТНАЯ КОВКА : Процесс ковки, при котором деталь деформируется повторяющимися ударами.
ТВЕРДОСТЬ : Сопротивление металла пластической деформации при вдавливании. Распространенными методами измерения являются Роквелл, Бринелль, склероскоп и Виккерс.
HEAT CHECK : Мелкие трещины в ковочных штампах, вызванные чрезмерным нагревом или продолжительным использованием без полировки. Схема этих «тепловых проверок» воспроизводится на кованой детали.
ТЕРМООБРАБОТКА : Сочетание операций нагрева и охлаждения, применяемых к металлу или сплаву в твердом состоянии для получения желаемых свойств. См. также «СТАРЕНИЕ», «ОТЖИГ» и «ЗАКАЛКА»
.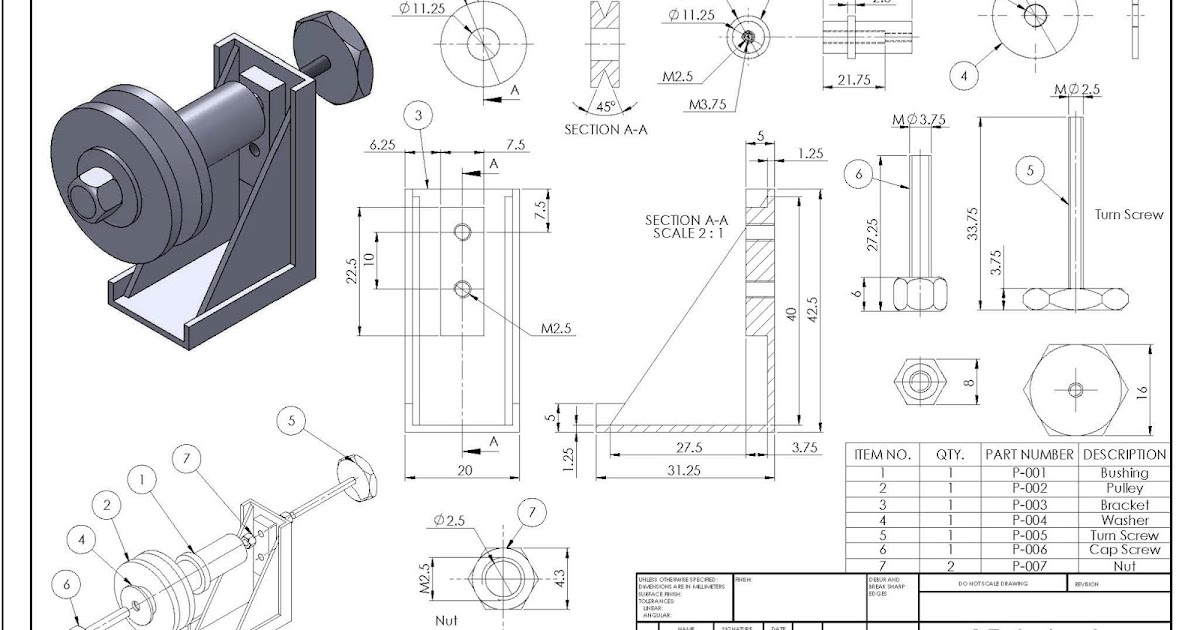
ГОРЯЧАЯ КОВКА : Способ штамповки деталей путем прессования нагретой заготовки, вырезанной из кованого материала, в закрытом штампе.
УДАР : Удар двух штампов вместе.
УДАРНАЯ ЭКСТРУЗИЯ : Формирование трубчатой крышки путем быстрого приложения силы через пуансон к металлической заготовке, при этом металл обтекает пуансон вверх, образуя трубчатую секцию.
ВПЕЧАТЛЕНИЕ : полость в штампе, которая формирует форму поковки.
ВКЛЮЧЕНИЯ : Частицы посторонних материалов (обычно стружка, грязь, углерод, оксиды), которые механически удерживаются на металле или внутри него.
ВСТАВКА : Сборная секция, которая экономит использование дорогой стали, за исключением тех мест, где это действительно необходимо.
КЛЮЧ . Штифт, как правило, с квадратным коническим поперечным сечением, используемый для фиксации штампов в штамповых блоках и т. д.
ПУНКТ ДЛЯ КЛЮЧА : Выемка, в которую вставляется ключ для соединения двух элементов вместе.
LAP : Поверхностный дефект в виде шва, вызванный складыванием горячего металла, ребер или острых углов и последующей прокаткой или ковкой, но не привариванием их к поверхности.
БЛОКИРОВКА : Состояние, при котором линия вспышки не находится в одной плоскости.
СМАЗКА : Протирка или опрыскивание штампов смазкой для обеспечения начального потока и облегчения извлечения поковки.
MASTER : Стандартная форма или шаблон, используемый для дублирования полостей штампа.
НЕСООТВЕТСТВИЕ : Смещение поковки на линии заусенцев, вызванное расположением штампа или полости. (Несоответствие не должно превышать допустимых допусков.)
МОДЕЛЬ : латунь, дерево, гипс и т. д., форма, которая служит образцом для вырезания штампа.
ОТКРЫТЫЕ МАТРИЦЫ : Металл не ограничен.
ЛИНИЯ РАЗЪЕМА : Линия, на которой штампы соединяются и заглушка удаляется.
ТРАВЛЕНИЕ : Жидкий процесс удаления поверхностного оксида и окалины с металла, подвергнутого горячей обработке.
НАБОР СТОЛОВ : Автономный набор штампов; тот, который не зависит от пресса для правильного выравнивания.
СТОЛБЫ : Направляющие стойки, используемые в наборе стоек.
ПОЛИРОВКА : Отделка металлических поверхностей составом, пропитанным на поверхности колеса с покрытием из твердой ткани, которое вращается с высокой скоростью. См. также «ПОЛИРОВКА»
ПРЕФОРМА : См. «РАЗБОРКА»
ПРЕССОВАНИЕ : См. «ГОРЯЧАЯ ПРЕССОВАЯ КОВКА»
НАГРУЗКА ДАВЛЕНИЕМ : Давление, необходимое для изготовления поковки, обычно выражается в тоннах.
ПУАНСОН : Обычно верхний элемент набора инструментов, который формирует дизайн верхней стороны поковки.
ЗАКАЛЧИВАНИЕ : Процесс быстрого охлаждения от повышенной температуры путем контакта с низкотемпературными жидкостями, газами или твердыми веществами.
ОТЖИГ : См. «ОТЖИГ»
RELIEVE : Процесс уменьшения размеров, чтобы одна часть подходила к другой.
ГРУБЫЙ ВЕС : Вес брутто.
НАКИПИ : Сильное поверхностное окисление металлов, вызванное нагреванием на воздухе или в другой окислительной атмосфере.
ПОКРЫТИЕ НАКИПИ : Процесс удаления накипи перед «Ярким погружением».
БРИТЬЕ : Процесс проталкивания поковки через обжимной штамп для более точного формирования или размера некоторого размера.
УСАДКА : Усадка, возникающая при охлаждении поковки.
РАКОВИНА : Для вырезания оттиска в штампе.
ЗАГОТОВКА : Заготовка, вырезанная из кованого материала, из которого изготавливается поковка, см. «ЗАГОТОВКА».
РАЗЪЕМНАЯ МАШИНА : Тип конструкции штампа, в которой две части разделены вертикально, чтобы сделать возможной ковку форм с полостями или деталями с поднутрениями.
НАПРЯЖЕНИЕ : Сила, приложенная к единице площади, обычно выражается в фунтах на квадратный дюйм (psi).
(1) Приложенное напряжение – напряжения, возникающие и существующие в теле во время приложения внешней нагрузки.
(2) Остаточное напряжение – напряжения, остающиеся в теле в результате пластической деформации.
ПРОЧНОСТЬ НА РАСТЯЖЕНИЕ : Значение, полученное путем деления максимальной нагрузки, наблюдаемой во время деформации на растяжение, на площадь поперечного сечения образца до деформации. Также называется «Абсолютная сила».
ИСПЫТАНИЕ :
(1) Удар – Испытание, проводимое для определения стойкости металлов к разрушению при внезапной ударной нагрузке. (См. ASTM E23.)
(2) Растяжение – испытание для определения одного или нескольких из следующих параметров: предел прочности при растяжении, предел текучести, относительное удлинение и уменьшение площади. (См. ASTM E8.)
ДОПУСК : Величина, на которую любая характеристика, такая как размерные, химические, физические или механические свойства, может отличаться от указанной.
ТРИМ : см. «CLIP»
ОБРЕЗАНИЕ И ОБРЕВАНИЕ : См. «ОБРЕЗАНИЕ И ОБРЕВАНИЕ»
ТУМБЛИРОВАНИЕ : Перекатывание во вращающемся контейнере для удаления острых краев и улучшения отделки.
ВЫМЫВАНИЕ : Износ штампов, вызванный течением металла.
WEB : Тонкий срез металла, остающийся на дне полости или углубления в поковке. Полотно можно удалить прокалыванием или механической обработкой.
ПРЕДЕЛ ТЕЧЕНИЯ : Как обычно применяется к меди и сплавам на основе меди, предел текучести представляет собой напряжение, которое вызывает удлинение на 0,5 процента под нагрузкой. Он известен как «предел текучести» (расширение 0,5%). См. «ИСПЫТАНИЕ, РАСТЯЖЕНИЕ» и ASTM E8.
Исследование упрощает выбор покрытий для холодной высадки
Когда крепежные детали или любые детали высадки высаживаются, выдавливаются или иным образом подвергаются холодной штамповке из нержавеющей стали или жаропрочных сплавов, результаты процесса в конечном счете зависят от надлежащего использования смазки для снижения трения .
Двумя компонентами смазки, конечно же, являются покрытия и смазочные материалы. Покрытия, основная тема этого обсуждения, представляют собой вещества, наносимые на проволоку гальванопокрытием, погружением или волочением на заводе. Смазочные материалы обычно представляют собой материалы, наносимые изготовителем во время холодной штамповки.
Будь то низкоуровневая осадка легко деформируемой в холодном состоянии нержавеющей стали или тяжелая экструзия (уменьшение площади более чем на 20 %) жаропрочного сплава, надлежащая практика смазывания необходима для предотвращения производственных трудностей, таких как истирание, штамповка заедание или поломка инструмента.
До недавнего времени выбор наилучшего покрытия для холодной штамповки был не таким простым, как хотелось бы многим, потому что не было доступных объективных тестов, которые помогли бы производителям оценить эффективность покрытия при различных операциях штамповки, выполняемых сегодня. В отсутствие удовлетворительного опыта выбор был сделан на основе оценок, а не надежных данных.
Этот недостаток был устранен после завершения интенсивного двухлетнего исследования, проведенного Институтом обработки металлов давлением при Университете Лихай, Вифлеем, Пенсильвания, при финансовой поддержке Carpenter Technology Corporation, Ben Franklin Technology Partners из Северо-Восточной Пенсильвании и Университета Лихай. Основными участниками были д-р Войцех З. Мисиолек из Лихай и Марио Э. Эплер.*
Тест Лехай
В течение этого двухлетнего периода инженерная школа разработала специальный тест для оценки относительных характеристик «Исходного сырья для проволоки с покрытием для изделий холодной высадки». Испытание имитирует реальный процесс производства крепежных изделий для пола. Это основано на существенной роли покрытий в производстве — для снижения усилий при вытяжке, обеспечения потока материала в сложные формы, уменьшения износа матрицы и минимизации повышения температуры. Испытание также было разработано для выявления изменений реакции материала на все условия процесса в зависимости от типа покрытия, его толщины, а также предела текучести исследуемого сырья.
В рамках программы тестирования было нанесено покрытие на три широко используемых материала подложки. (Рис. 1) Была выбрана нержавеющая сталь Carpenter Technology 430, потому что ее легче всего формировать из трех. Нержавеющая сталь Carpenter Technology Custom Flo 302HQ была выбрана из-за ее способности к формованию в среднем диапазоне, а сплав Carpenter Technology A-286 – из-за того, что его труднее всего поддается холодной штамповке, и этот сплав чаще всего используется при холодной штамповке при высоких температурах.
На проволоку из вышеперечисленных сплавов наносили различные покрытия и комбинации покрытий, используемые в промышленности, а затем оценивали и ранжировали в тестах Лехай в соответствии с их относительной эффективностью. Включены медь, мыло, Carpenter Technology Ecolube® II (дисульфид молибдена – MoS 2 ), оксалат и покрытие Carpenter’s Carpenter Technology KnightCote™. В дополнение к одинарным покрытиям были испытаны дуплексные покрытия для самых жестких условий холодной штамповки.
Для сравнения были протестированы на эффективность покрытия различной толщины от 50 микродюймов до 200 микродюймов. Некоторые неизолированные проволоки также были протестированы для измерения усилия, необходимого для экструдирования различных непокрытых подложек, по сравнению с энергией, необходимой для отдельных покрытий и комбинаций покрытий, измеренных в ходе испытаний.
Двухэтапный тест
Компания Lehigh разработала двухэтапный тест для изучения эффективности различных покрытий и комбинаций покрытий на трех типах проволоки-основы в исследовании. Испытание волочения проволоки и испытание экструзии с захваченной проволокой использовались для получения данных о характеристиках покрытия с точки зрения коэффициента трения (испытание волочением), а также максимальной нагрузки экструзии и вероятности разрушения покрытия (испытание экструзией).
Стандартные лабораторные испытательные машины использовались для сбора данных о силе деформации, которые затем интерпретировались через несколько механических взаимосвязей с характеристиками покрытия и обрабатываемостью материала. Недавно разработанный тест Лехай, расширение существующих возможностей тестирования в Carpenter, может служить универсальным тестом, проводимым производителем проволоки или производителем крепежных изделий.
Для испытания на вытягивание был рассчитан коэффициент трения для комбинации покрытие/основа. Для испытания на выдавливание/выдавливание характеристики покрытия оценивали по максимальному усилию выдавливания, энергии, необходимой для выдавливания части заданной геометрии, форме кривой, связанной с данными нагрузки/хода для выдавливания, и величине стандартного отклонения для максимальная загрузка.
Кривая экструзии, полученная в ходе теста экструзии, показала данные, весьма полезные для оценки характеристик покрытия. Наблюдаемые закономерности можно отнести к (а) типичной экструзии, (б) экструзии, при которой деталь застревает в матрице из-за уплотнения зоны деформации покрытием/смазкой, и (в) неравномерного трения во время деформации.
Исследователи обнаружили, что покрытия с самым высоким коэффициентом трения в тесте на вытягивание также демонстрировали уплотнение матрицы в тесте на экструзию. Это испытание подтвердило ожидания, максимальное усилие выдавливания было обратно пропорционально способности к напору.
Команда пришла к двум выводам, основанным на этих выводах: 1) сравнение максимального усилия экструзии между различными покрытиями может быть сделано, если в процессе эксплуатации возникают проблемы, связанные с трением, такие как чрезмерный износ штампа или дефекты отделки поверхности, и 2) Если заданная геометрия штока приводит к поломке пуансонов или набивки матрицы, следует заменить покрытие, которое демонстрирует более низкий потенциал отказа и более благоприятную кривую экструзии.
Испытание волочением проволоки
Использование испытания волочением позволяет в первом приближении рассмотреть фрикционные характеристики покрытий. Тот же тест также дает представление о адгезии покрытия, хотя его одного недостаточно, чтобы легко оценить способность покрытия сохраняться на протяжении нескольких этапов формования. Как правило, коэффициент трения, рассчитанный на основе теста на волочение, представляет собой стандартную меру эффективности, которая часто используется.
Трение в процессе волочения проволоки влияет на общую величину достижимой деформации, силы деформации, чистоту поверхности и распределение деформации, следовательно, на механические свойства деформированной проволоки. В то время как трение возникает в подводящей части матрицы (рис. 2), его влияние гораздо сильнее проявляется в опорной части матрицы. Форма раструба и угол подхода предназначены для обеспечения потока смазки в пресс-форму и увеличения гидростатического давления смазки. Очищается поверхность проволоки в опорной части матрицы, а также удаляются повреждения, которые могли быть вызваны износом матрицы.
Рис. 2 Матрица для волочения проволоки
Формуемость, функция материала и технологическая функция – все это исследуется в тесте волочения проволоки Lehigh. Способность к формованию представляет собой величину деформации, которую материал может выдержать без ухудшения поверхности, такого как растрескивание, разрыв или внутренние микропустоты. Функция материала включает свойства материала, такие как напряжение течения, прочность, зависимость скорости деформации от пластичности, а также зависимость напряжения и микроструктуры от температуры. Для волочения проволоки основными переменными процесса являются степень деформации (уменьшение поперечного сечения), конструкция матрицы, смазка и скорость волочения.
Одним из наиболее распространенных параметров, изменение которых влияет на характеристики деформации, является покрытие или смазка, используемые в процессе. Ниже приведены минимальные критерии, которые следует применять при выборе наиболее подходящей смазки: (а) она не должна чрезмерно вступать в реакцию с рабочим материалом или материалом штампа; (b) он должен в достаточной степени смачивать поверхность и достаточно прилипать, чтобы должным образом смазывать заготовку; (c) это должно привести к значительному снижению трения скольжения, сил деформации и температуры деформации.
Оценка покрытий/смазок в испытании на волочение проволоки основывалась на значении μ матрицы с различной длиной опоры, но для измерения усилия использовались аналогичные уменьшения и углы матрицы. Используя баланс механических сил, можно рассчитать значение μ для каждой матрицы и каждой комбинации покрытия/смазки.
Напряжение волочения определяли путем деления усилия волочения на площадь поперечного сечения проволоки после волочения. Измерения силы вытягивания считались точными до пяти значащих цифр (десятая часть фунта для тензодатчика на 5000 фунтов и сотая часть фунта для тензодатчика на 500 фунтов). Коэффициент трения μ был приведен к четырем значащим цифрам, чтобы можно было сравнить покрытия, демонстрирующие аналогичные значения коэффициента трения. Затем коэффициент трения для каждой комбинации покрытие/подложка можно было сравнить для любой заданной геометрии штампа.
Испытание на волочение проволоки дало полезное измерение силы, необходимой для деформации испытательной заготовки. Не оценивалось какое-либо влияние покрытия на износ матрицы или температуру в течение длительных периодов волочения на высоких скоростях. Различия в покрытиях учитывались различиями в напряжении течения материала с покрытием и геометрией матрицы.
Процедура волочения проволоки
Отрезки проволоки товарного качества из нержавеющей стали Carpenter Technology 430 (S43000), из нержавеющей стали Carpenter Technology Custom Flo 302HQ (S30430) и из сплава A-286 (K66286) Carpenter Technology были протянуты через различные матрицы с одинаковым обжатием и Угол штампа на гидравлическом чертежном столе Waterbury-Farrel. Пять образцов каждого покрытия были протянуты через штампы для каждой из испытанных марок. Длина каждого испытанного отрезка провода составляла около 3 футов (0,9144 м) в длину.
Все испытанные одинарные и дуплексные покрытия обозначены на рис. 3, включая образец оголенной проволоки из каждого сплава. В испытаниях использовались четыре различных длины кулачковых подшипников. Применяемая скорость протяжки составляла примерно 6,5 футов/мин (1,98 м/мин). Начальный диаметр проволоки составлял 0,1343 дюйма (3,411 мм) или 0,131 дюйма (3,327 мм). Волочение вызвало уменьшение примерно на 10,5%. Для смазывания проволоки использовалась коммерческая смазка для волочения Hammidraw 1846-B в волочильной коробке перед матрицей.
Сила вытягивания измерялась с использованием 5000- или 500-фунтового стержня. (22 241 или 2 244,1 Н) весоизмерительная ячейка Entran. Используемый тензодатчик зависел от длины подшипника и напряжения течения материала подложки. Выходной сигнал тензодатчика усиливался и считывался картой сбора данных National Instruments, реализованной с помощью программного обеспечения LabView компании. Сила вытягивания в фунтах определялась по зарегистрированным напряжениям с использованием компьютерной электронной таблицы и арифметических вычислений.
Испытание на экструзию
Второе испытание для определения характеристик покрытия основано на использовании реальных производственных штампов холодной высадки. На рис. 4 показано поперечное сечение экструзионной головки с захватом вперед, используемой для испытаний. Недеформированную тестовую заготовку помещают в емкость матрицы и продавливают при выдавливании через зону деформации и опорную часть матрицы, где возникает максимальная сила трения.
В испытаниях использовались экструзионные головки с защемлением вперед вместо экструзионных головок с открытым вперед, поскольку первые обеспечивают гораздо большее снижение (до 75%). Хотя открытые вперед матрицы более распространены, материал, экструдированный в открытых вперед головках, имеет тенденцию к опрокидыванию над нижней частью матрицы, где выполняется обжатие, если силы трения и деформации в зоне деформации слишком велики. Эта тенденция обычно ограничивает снижение до 30% или менее.
Процедура экструзии проволоки
Образцы проволоки товарного качества Carpenter Technology Custom Flow из нержавеющей стали 302HQ, Carpenter Technology 430 из нержавеющей стали и проволоки Carpenter Technology A-286 были подвергнуты холодной экструзии на установке для испытаний на растяжение Instron с использованием радиальной матрицы и набора плоских пуансонов (рис. 5). Вся проволока была предварительно вытянута во время испытания на волочение с использованием смазки или смазки для волочения. Были взяты секции от 0,1343 до 0,1270 дюйма в диаметре. (от 3,411 до 3,226 мм), затем экструдировали до конечного диаметра 0,101 дюйма (2,57 мм).
Для испытаний экструзионные заготовки были разрезаны на три разных длины – 0,716, 0,587 и 0,446 дюйма (18,2, 14,9 и 11,3 мм). Они были обозначены как длинные, средние и короткие экструзии. Однако самые короткие экструзии нельзя было использовать для испытаний, поскольку они были недостаточно длинными, чтобы отражать стационарные условия экструзии. Каждую экструзию проводили со скоростью траверсы 20 дюймов/мин. (0,5-8 м/мин.).
Во время экструзии данные о нагрузке/ходе регистрировались со скоростью 20 000 точек/сек. Полученные данные были преобразованы с помощью компьютера в максимальную нагрузку экструзии, форму экструзии и площадь под кривой. Остатки покрытий удаляли из отверстия матрицы, чтобы предотвратить образование отложений. Для каждой комбинации покрытие/подложка экструдировали пять образцов для каждой геометрии экструзии. Аналогичные испытания на экструзию проводились на производственном коллекторе на производственном предприятии.
Испытание на выдавливание произвело численные измерения максимальной нагрузки выдавливания и площади под кривой выдавливания. Форма кривой экструзии, величина стандартного отклонения для максимальной нагрузки и площадь под кривой используются для оценки характеристик покрытия.
Испытание на экструзию, по сравнению с испытанием на волочение, дает гораздо больше актуальных и полезных данных о характеристиках каждого покрытия при деформации при холодной высадке. Он очень точно имитирует процесс холодной высадки и, таким образом, весьма полезен при оценке материалов.
Рейтинг покрытий
Результаты для средней и длинной экструзии на рис. 6, 7 и 8 можно использовать для определения относительных характеристик покрытий. Рейтинги отражают возрастающее максимальное усилие выдавливания (фунты), необходимое для холодной проволоки из трех испытуемых сплавов в непокрытом состоянии и с различными покрытиями или их комбинациями.
В целом, дуплексные покрытия показали себя лучше, чем любое отдельное покрытие в тяжелых условиях эксплуатации, как и покрытие Carpenter Technology KnightCote поверх меди. В некоторых случаях одно только покрытие Carpenter Technology KnightCote работало так же, как дуплексное покрытие или медное покрытие, с экологическим преимуществом, устраняя проблемы с загрязнением и утилизацией.
Оксалатные покрытия не обладают такими же характеристиками, как покрытия Ecolube (дисульфид молибдена), медные покрытия толщиной 100 микродюймов и покрытия KnightCote. За исключением нержавеющей стали 430, покрытия Carpenter Technology Ecolube оказались менее эффективными, чем покрытия Carpenter Technology KnightCote.
Толщина некоторых покрытий может оказывать заметное влияние на эффективность покрытия. Например, испытание на выдавливание показало, что для холодной формовки проволоки с медным покрытием толщиной 100 микродюймов требуется меньшее максимальное усилие выдавливания, чем для проволоки того же диаметра с покрытием 50 и 200 микродюймов. В этом случае толщина медного покрытия толщиной 100 микродюймов близка к идеальной толщине покрытия для данного конкретного применения. Толщина 50 микродюймов недостаточна для обеспечения оптимальной смазки, а толщина 200 микродюймов слишком велика. Дополнительная медь в самом толстом покрытии фактически увеличивает усилие, необходимое для головки той же геометрии.
Выводы
Критическое значение при испытаниях имеют как условия трения при деформации, так и реакция покрытия на параметры процесса. Ни одно отдельное испытание не может воспроизвести сложную взаимосвязь между условиями трения при деформации и реакцией различных покрытий на параметры процесса. Тем не менее, взаимосвязь между ними была установлена, и максимальное усилие экструзии может быть измерено с помощью тщательно контролируемых и повторяющихся испытаний, чтобы обеспечить полезную оценку покрытий на тестируемых подложках.
При оценке необходимо учитывать как волочение проволоки, так и этап экструзии. Если покрытие не может пройти стадию волочения, гарантируя хорошую отделку поверхности и прямую проволоку, оно не будет эффективным для увеличения вытягиваемости.
Если износ штампа является проблемой, следует сравнить максимальные требуемые усилия экструзии для различных покрытий. Если поломка пуансона является проблемой, необходимо проверить кривую экструзии, чтобы убедиться, что используется покрытие, не имеющее признаков уплотнения матрицы.
Характеристики покрытия/смазки должны быть оценены для конкретной покрываемой поверхности. Каждый протестированный смазочный материал или комбинация смазочных материалов ведут себя по-разному с каждым тестируемым материалом подложки.
Будущая работа
Карпентер планирует усовершенствовать процедуру испытаний Lehigh и уже использует ее для получения данных испытаний разрабатываемых сплавов.
Исследователи Lehigh считают, что использование электронной микроскопии может помочь в изучении чистоты поверхности образцов, используемых в тестах волочения проволоки. Они считают, что внешний вид проволоки после волочения вместе с данными о силе волочения можно использовать более конкретно для определения условий трения для каждого покрытия.
___________
*Ссылка 1. Эплер, М.Е., Мисиолек, В.З., Разработка оценочных испытаний сырья для производства проволоки с покрытием для продукции холодной высадки, Грант Бена Франклина № 2298, Заключительный отчет, 11 февраля 2003 г.
Ссылка 2 Эплер, М.Е., Мисиолек, В.З., Экспериментальный метод оценки покрытия проволоки, Шестая конференция Easaform по формованию, Салерно, Италия, 28-30 апреля 2003 г.