Что дает молибден в стали: Молибден. Свойства, применение, марки. Соединения, сплавы молибдена
alexxlab | 24.06.2023 | 0 | Разное
Учимся расшифровывать ножевые стали | Лучшие статьи, обзоры и новости
История производство ножевой стали исчисляется веками, так как хороший клинок во все времена служил не только для охоты или обороны, но был и своеобразным вложением капитала, стоимость которого росла год от года. Широко востребованная современная ножевая сталь для успешного производства требует серьёзных знаний характеристик металлических сплавов и целого ряда передовых технологий.
Cталь — это в первую очередь сплав железа с углеродом. Если последнего вещества слишком много, то образуется чугун. Если наоборот мало, то получается жесть. А сталью называется сплав с одинаковым количеством обеих компонентов. Различные типы стали определяются в первую очередь не пропорциям углерода и железа, а легированием добавками и примесями, которые наделяют заготовку различными свойствами. Вот про эти добавки и примеси пойдёт речь.
Основные элементы
Среди наиболее часто используемых химических элементов, которые встречаются в стальных сплавах, стоит отметить следующие:
- Углерод (С) — У
- Хром (Cr) — Х
- Никель (Ni) — Н
- Ванадий (V) — Ф
- Молибден (Mo) — М
Эти символы можно встретить в большинстве маркировок сталей, которые встречаются на современном ножевом рынке. Особенно это касается сталей российского или китайского производства, например: Х12МФ, 8Cr13MoV, У8, 65Х13 и т.д. Давайте разберем подробнее влияние тех или иных элементов на сталь.
Углерод — главный элемент, определяющий свойства стали. Именно благодаря углероду сталь способна принимать закалку. От количества углерода зависит твёрдость и прочность стали для ножей, хотя он же повышает склонность стали к коррозии. Относительно стали для ножей, нас интересуют стали с количеством углерода не меньше 0.6%. Именно с этой отметки сталь может принимать закалку на нормальную твёрдость. Правда производители часто используют стали и с количеством углерода 0.4%-0.6%, как правило, на кухонных и просто недорогих ножах.
Хром — следующий по распространённости в сталях элемент. Хром помогает сплаву сопротивляться коррозии и делает её нержавеющей. Официально сталь считается «нержавеющей» если хрома в ней не меньше 14%. Но помимо своего главного свойства Хром имеет негативное влияние на прочность стали.
Никель — так же повышает коррозионную стойкость стали и способен несколько повысить прочность. В комбинации с хромом и молибденом никель еще больше повышает способность сталей к термическому упрочнению, способствует повышению вязкости и усталостной прочности сталей. Много никеля присутствует, например, в стали Н1.
Ванадий — замечательный элемент, способный улучшать свойства многих сплавов. Улучшает прочность и значительно повышает износостойкость стали. Его добавляют в быстрорежущие и инструментальные стали. Для нас это означает, что сталь для ножа будет дольше держать заточку при резе картона, войлока, канатов и других подобных материалов. Но нож будет тяжелее точиться. Самые известные стали обогащенные ванадием — это порошковые сплавы марки Crucible американского производства, такие как: CPM S30V, CPM S90V и подобные им.
Молибден — используется как легирующая добавка, повышающая жаропрочность и коррозионную стойкость стали. Молибден усиливает действие хрома в сплаве, улучшает прокаливаемость, делает состав более равномерным. По сути, улучшает почти все свойства сплава. Молибден обязательный элемент в быстрорежущих сталях. Стали с добавкой молибдена используются для изготовления деталей работающих в агрессивных средах и при высокой температуре. То есть в химической промышленности, в деталях реактивных двигателей. Нож из самолётной турбины уже стал своеобразной притчей. Те стали, из применяемых в производстве ножей, в составе которых имеется этот элемент, зарекомендовали себя с наилучшей стороны. Стоит отметить такие стали, как американскую CPM 154CM и японскую ATS-34, в которых содержание молибдена не меньше 4%. По задумке, 154CM изначально и предназначалась для тех самых турбин.
Дополнительные примеси
Следующие элементы тоже зачастую используются во многих современных сплавах, но обычно в куда меньших количествах. Тем не менее они способны оказывать непосредственное влияние на характеристики сплава:
- Вольфрам (W) — В
- Кобальт (Co) — К
- Азот (N) — А
- Марганец (Mn) — Г
- Кремний (Si) — C
Вольфрам — металл с самой высокой температурой плавления из всех металлов. Используется во множестве всевозможных приборов и отраслей, от лампочек до ядерных реакторов. Вольфрам, неотъемлемый элемент в составе быстрорежущих сталей. Помимо устойчивости к температурам, сталь для ножа получает свойства, положительно влияющие на твёрдость и износостойкость.
Кобальт — ещё один металл с множеством применений, от корма для коров до космических кораблей. В некоторых количествах кобальт добавляется в быстрорежущие стали и твёрдые сплавы. Кобальт можно встретить в таких популярных ножевых сталях, как N690 (и других сплавах концерна Böhler-Uddeholm) а также японской стали VG-10 в количестве около 1.5%.
Азот — применяют в сталях как заменитель углерода и никеля. Азот повышает стойкость к коррозии и износостойкость стали для ножа. И позволяет стали с очень низким содержанием углерода принимать закалку. Например японская сталь Н1, в которой всего лишь 0.15% углерода, но 0.1% Азота позволяют закалять её на 58HRC и делают её практически абсолютно нержавеющей.
Марганец — как полезный и нужный элемент применяется на стадии выплавки стали, способен повышать твёрдость стали. Обычно этот элемент можно встретить в сплавах, из которых изготавливают наиболее прочные вещи — рельсы, танки, сейфы и т.д.
Кремний — ещё один необходимый в производстве сталей элемент. Он удаляет из металла кислород. Ну и заодно несколько повышает прочность и коррозионную стойкость.
Прочие элементы
Дополнительные примеси, которые изредка можно встретить в ножевых сталях, но которые тоже стоит упомянуть:
- Сера (S)
- Фосфор (P) — П
- Ниобий (Nb) — Б
- Цирконий (Zr) — Ц
- Лантан (La)
- Цезий — (Cs)
- Неодим (Nd)
- Медь (Cu) — Д
- Титан (Ti) — Т
- Алюминий (Аl) — Ю
Сера — это совсем не полезный элемент, она снижает механические свойства стали и уменьшает стойкость стали к коррозии. Поэтому серы в сталях обычно очень мало (не превышает 0,02-0,03%), лишь то, что не удалось удалить из стали в процессе её производства.
Фосфор — вредная примесь, в стали ему не место, а особенно в стали для ножа, ибо он повышает хрупкость и снижает механические свойства стали. Фосфор стараются удалить из стали.
Ниобий — повышает коррозионную стойкость и износостойкость стали. Ниобий в сталях (или стали с ниобием) жуткая экзотика, но его можно найти, например, в сплаве CPM S110V.
Цирконий — оказывает особое влияние на величину и рост зерна в стали , измельчает зерно и позволяет получать сталь с заранее заданной зернистостью.
Лантан — уменьшают пористость, способствуют уменьшению содержания серы в стали, улучшают качество поверхности, измельчают зерно.
Цезий — способствуют уменьшению содержания серы в стали , улучшают качество поверхности, измельчают зерно.
Неодим — уменьшают пористость, способствуют уменьшению содержания серы в стали.
Медь — увеличивает антикоррозионные свойства, она вводится главным образом в строительную сталь.
Титан — может добавляться в сплавы для повышения прочности, стойкости к коррозии и температурам. В ножевых сталях титан, как добавка в принципе не актуален, так как количества его там ничтожные.
Алюминий — повышает жаростойкость и стойкость к окалине.
Далеко не у каждой современной стали в названии имеются обозначения, указывающие на её состав, поэтому внимательно ознакомьтесь с их описанием или хотя бы с аналогами.
Попробуйте наши предложения:
Для того, чтобы оставить комментарий, зарегистрируйтесь или войдите
Влияние химического состава сталей на их структурно-фазовое состояние и коррозионную стойкость » Ремонт Строительство Интерьер
При изготовлении оборудования для переработки нефти и газа весьма широко используются стали, для которые основными легирующими компонентами являются хром и никель. Композиция на основе железа, содержащая 18% хрома и 10% никеля, является базовой. Около 70% выплавляемых в России и за рубежом коррозионно-стойких сталей приходится на группу Х18Н10. Дополнительное легирование этой композиции позволяет придать стали дополнительные свойства.
Хром и никель оказывают на фазовое состояние стали противоположное влияние. Хром, являясь ферритообразующим элементом, стабилизирует у-фазу. Никель, аустенитообразующий эле мент, соответственно стабилизирует у-фазу. Остальные легирующие элементы, вводимые в металл для придания ему повышен ной коррозионной стойкости и хороших механических и технологических свойств, также по-разному могут влиять на фазовое состояние стали. Молибден, титан, ниобий, кремний являются ферритообразующими, тогда как углерод, марганец, азот стабилизируют аустенит. Для определения фазового состоянии хромоникелевых сталей часто пользуются диаграммой Шеффлера (рис. 5.16), в которой учитывается суммарное содержание феррито- и аустенитообразующих элементов.
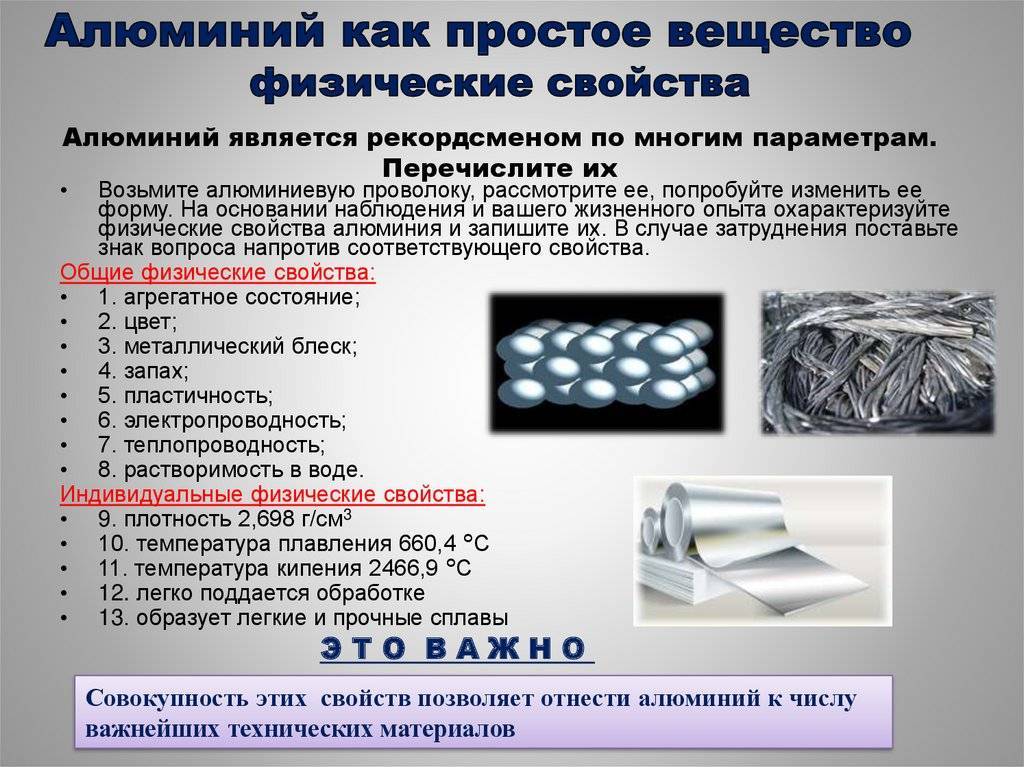
При нагреве до температуры 400—600°С происходит выделение карбидов хрома, преимущественно по границам зерен. Это, как было показано ранее, приводит к связыванию хрома в карбиды и обеднению хромом границ зерен. Следствием таких процессов является развитие у стали склонности к MKK. При нагреве стали до температуры 900—950°С (стабилизирующий отжиг) диффузия хрома к границе зерна восстанавливает необходимое для надежной пассивации количество хрома на границах зерен и ликвидирует возникшую склонность к MKK. Легирование стали элементами, образующими более стабильные карбиды, чем хром (титаном, ниобием, танталом), а также уменьшение содержания углерода, снижает вероятность возникновения склонности хромо-никелевых сталей к MKK при нагреве в опасном интервале температур. В случаях, когда содержание углерода в стали типа 18-10 не достигает 0,03%, стали свойственна высокая устойчивость против MKK даже без введения в нее дополнительного количества активных карбидообразующих элементов.
Молибден вводится в стали типа 18-10 в количестве 2—3%. Он является ферритообразующим элементом. Поэтому для сохранения аустенитного состояния введение молибдена требует повышение содержания никеля в стали. Молибден входит в состав пассивирующих слоев и способствует повышению их защитных свойств. Поэтому стали, легированные молибденом, проявляют более высокую коррозионную стойкость, чем стали без молибдена. По этой же причине легированные молибденом стали имеют больший инкубационный период при развитии питтинговой коррозии. В то же время легирование молибденом расширяет температурный интервал образования у-фазы, существенно ускоряя этот процесс. Это увеличивает опасность охрупчивания сталей, легированных молибденом, при эксплуатации их в интервале температур 650—950°С. Существует мнение, что легирование молибденом сопровождается изменением дислокационной структуры стали с ячеистой, с неупорядоченным расположением дислокаций, на компланарную, с расположением дислокаций по плоскостям. Стали с компланарной дислокационной структурой проявляют, как правило, пониженное сопротивление развитию трещины. Поэтому влияние молибдена на сопротивление питтинговой коррозии и хлоридному коррозионному растрескиванию неоднозначно: с одной стороны, существенно увеличивается инкубационный период разрушения, а с другой — снижается сопротивление его развитию.
Легирование кремнием, ферритообразующим элементом, несколько снижает вязкость стали и соответственно сопротивление коррозионному растрескиванию. Для сохранения исходной аус-тенитной структуры введение кремния требует повышенного содержания аустенитообразующих элементов (углерода, никеля). Положительная роль кремния связана с повышение защитных свойств поверхностных слоев, возникающих как при электрохимической коррозии, так и, особенно, при коррозии, протекающей по неэлектрохимическому механизму при высоких температурах.
Введение в сталь большего количества хрома (до 25%) и необходимого для сохранения аустенитного фазового состояния никеля (13—18%) обеспечивают еще более легкое пассивирование стали, а также еще большую устойчивость к высокотемпературным видам коррозии при сохранении таких механических свойств, как высокая вязкость и пластичность. Введение в сплав с высоким содержанием хрома и никеля молибдена и меди существенно повышает его стойкость в неорганических кислотах, особенно в серной.
Легирование стали марганцем и азотом способствует стабилизации аустенита и в ряде случаев позволяет сэкономить дефицитный в России дорогостоящий никель без ущерба для коррозионной стойкости сталей. Для изготовления оборудования перерабатывающих заводов допускается использование сталей, содержащих до 8% марганца. Чисто хромомарганцевые стали существенно уступают хромоникелевым по стойкости к питтинговой коррозии и МКК. Они более склонны к развитию 475°-й хрупкости. При сварке этих сталей в зоне термического влияния сварного соединения образуется о-фаза, в результате чего вязкость сварного шва падает. Введение в хромомарганцевую сталь никеля (до 4%) улучшает коррозионные и механические свойства этих сталей. Азот — сильный аустенитообразователь. Он позволяет существенно снизить содержание никеля в стали. Однако введение его в сталь способствует выделению второй фазы — нитридов. Это снижает гомогенность стали и делает ее менее устойчивой к коррозии.
Другой путь экономии никеля связан с использованием хромоникелевых двухфазных, феррито-аустенитных, сталей. Для изготовления нефтегазовой аппаратуры рекомендованы стали, содержащие (в %) 20—25 хрома, 5—8 никеля и до 3 молибдена. При таком составе соотношение ферритной и аустенитной фаз могут сильно различаться. Как правило, используют стали с содержанием ферритной фазы от 40 до 70%. В большинстве сред, характерных для переработки нефти и газа, стали этого класса не уступают по стойкости электрохимической коррозии сталям аустенитного класса. Считается, что по стойкости против питтинговой коррозии и хлоридного коррозионного растрескивания они даже несколько превосходят аустенитные стали, причем стойкость эта повышается по мере увеличения содержания в них ферритной фазы. Стойкость против MKK достигается путем легирования сталей титаном и ниобием и ограничения содержания углерода. По стойкости к MKK и межкристаллитному коррозионному растрескиванию феррито-аустенитные стали также не только не уступают, но превосходят аустенитные. Это связывают с тем, что, во-первых, для двухфазных сталей характерна мелкозернистая структура, а следовательно, большая протяженность границ зерен, обуславливающая меньшую концентрацию карбидных выделений. Во-вторых, при образовании карбидов типа Ме23С6 на границе аустенита с ферритом из-за высокого содержания хрома в ферритной фазе и повышенной скорости диффузии легирующих элементов в объемно-центрированной решетке аустенита облегчается выравнивание химического состава в приграничных областях, и концентрация хрома не опускается ниже допустимого уровня. По прочности аустенито-ферритные стали существенно превосходят стали аустенитного класса, что позволяет понизить металлоемкость изготавливаемых из них конструкций. Это, наряду с пониженным содержанием в них никеля, дает возможность рассматривать их как заменителей аустенитных сталей, применение которых позволяет экономить никель.
Помимо указанных коррозионно-стойких материалов на нефте- и газоперерабатывающих заводах применяют аппараты и элементы металлоконструкций, изготовленные из биметалла. В биметалле основным слоем служит углеродистая, или низколегированная, сталь, а плакирующим — нержавеющая (хромистая или хромоникелевая). Биметалл обладает рядом преимуществ по сравнению с коррозионно-стойким монометаллом. Благодаря тому, что металл основы имеет обычно более высокую прочность, чем плакирующий слой, биметаллическая металлоконструкция существенно менее металлоемка. Применение биметалла позволяет уменьшить расход дорогостоящих высоколегированных сталей. Биметалл с плакирующим слоем из стали типа 18-10 лучше противостоит питтинговой коррозии и хлоридному коррозионному растрескиванию, чем сталь типа 18-10: зародившийся питтинг не может преодолеть линию сплавления. В то же время применение биметалла требует определенной осторожности. He рекомендуется использовать биметалл для работы в средах, содержащих сероводород: продиффундировавший сквозь плакирующий слой водород способен скапливаться под плакирующим слоем и отрывать его от основного металла. Кроме того, в случае, когда плакировка — сталь типа 18-10, при сварке биметалла в зоне сплавления может образоваться мартенсит, по которому легко распространяется коррозионная трещина в наводороженном металле.
Помимо сталей (сплавов на основе железа) для изготовления элементов металлоконструкций в ряде случаев используются сплавы на основе меди (латуни) и никеля (монель-металл). Латуни хорошо противостоят питтинговой коррозии в нейтральных и слабокислых средах. Их используют для изготовления трубных пучков холодильников, предназначенных главным образом для охлаждения головного погона атмосферных колонн установок АВТ. Применение защелачивания и ингибирования головных погонов позволяет обходиться для этих целей углеродистыми сталями. Монель-металл (сплав никеля с молибденом) практически не подвергается питтинговой коррозии и хлоридному коррозионному растрескиванию даже в кислых средах, и рекомендовался для плакикрования верхней части атмосферных колонн на установках первичной переработки нефти, работавших без блока (установки) ЭЛОУ. Повсеместное введение подобных блоков и установок избавило от необходимости применения этого дорогостоящего материала. Применение латуней и монель-металла в наше время весьма ограничено и не считается перспективным. Поэтому в настоящем пособии особенности влияния их химического состава и структуры на коррозионное поведение не рассматривается.
Металлургия молибдена в нержавеющей стали
Использование молибдена
- Использование нового молибдена
- Нержавеющая сталь с содержанием молибдена
- Нержавеющая сталь, свойства и изготовление
- Аустенитная нержавеющая сталь
- Дуплексная нержавеющая сталь
- Металлургия молибдена в нержавеющей стали
- Обучение из нержавеющей стали
- Архитектура, строительство
- Нержавеющая сталь в водопроводе
- Нержавеющая сталь, свойства и изготовление
- Легированная сталь и чугун с содержанием молибдена
- Суперсплавы с молибденом
- Молибден металлический и сплавы
- Химия и применение молибдена
Молибден повышает коррозионную стойкость и жаропрочность
Молибден в первую очередь повышает коррозионную стойкость нержавеющих сталей (см. Марки и свойства). Молибденсодержащие марки нержавеющей стали, как правило, более устойчивы к коррозии, чем марки, не содержащие молибден. Они используются в приложениях, которые являются более агрессивными, например, на химических заводах или в морских условиях. Существует множество марок нержавеющих сталей с различным содержанием молибдена (а также хрома, никеля, азота и т. д.). Наилучший сорт для данного применения выбирается на основе коррозионной активности рабочей среды.
Молибден в виде крупного атома повышает прочность нержавеющих сталей при повышенных температурах за счет закалки на твердый раствор. Этот эффект используется в теплообменниках и другом оборудовании с повышенной температурой, например, в автомобильных выхлопных системах.
Молибден является ферритообразователем
Чтобы обсудить влияние молибдена на металлургию нержавеющих сталей, полезно рассмотреть металлургию нержавеющих сталей в целом. По своей микроструктуре нержавеющие стали делятся на следующие семейства:
- аустенитный
- ферритный
- мартенситный
- дуплекс
- дисперсионно-твердеющий
Разделение на основе микроструктуры целесообразно, поскольку элементы одного семейства, как правило, имеют сходные физические и механические свойства. Однако свойства одного семейства могут сильно отличаться от свойств другого семейства. Например, аустенитные нержавеющие стали немагнитны, а ферритные и дуплексные нержавеющие стали — магнитны.
Разница между семействами фундаментальна на атомарном уровне. Расположение атомов в кристалле феррита отличается от такового в кристалле аустенита:
В ферритной нержавеющей стали атомы железа и хрома расположены по углам куба и в центре этого куба. В аустенитных нержавеющих сталях атомы железа, хрома и никеля расположены по углам куба и в центре каждой из граней куба.
Эта, казалось бы, небольшая разница сильно влияет на свойства этих сталей.
Рис. 1. Ферритная нержавеющая сталь слева имеет объемно-центрированную кубическую (ОЦК) кристаллическую структуру. При добавлении никеля в эту нержавеющую сталь структура изменяется с ОЦК на гранецентрированную кубическую (ГЦК), которая называется аустенитной.
Свойства | Аустенитный | Ферритный |
---|---|---|
Прочность | Очень высокая | Умеренный |
Пластичность | Очень высокая | Умеренный |
Свариваемость | Хорошо | Ограниченный |
Термическое расширение | Высокий | Умеренный |
Стойкость к коррозионному растрескиванию под напряжением | Низкий | Очень высокая |
Магнитные свойства | Немагнитный | Ферромагнитный |
Благодаря хорошим механическим свойствам и простоте изготовления аустенитные нержавеющие стали используются гораздо шире, чем ферритные. Около 75 % всей нержавеющей стали, используемой в мире, является аустенитной, а около 25 % — ферритной. Остальные семейства, мартенситные, дуплексные и дисперсионно-твердеющие нержавеющие стали, составляют менее 1% от общего объема рынка.
Кроме никеля существуют и другие элементы, которые делают структуру аустенитной. Эти элементы называются аустенитообразователями. Легирующие элементы, которые делают структуру ферритной, называются ферритообразователями.
Ферритовые накладки | Аустенитные накладки |
---|---|
Железо | Никель |
Хром | Азот |
Молибден | Углерод |
Кремний | Марганец |
Медь |
Молибден является ферритовым формирователем. Это означает, что при добавлении молибдена для улучшения коррозионной стойкости аустенитной нержавеющей стали необходимо добавить формирователь аустенита, такой как никель или азот, чтобы сохранить структуру аустенитной.
Дуплексные нержавеющие стали имеют в своей микроструктуре смесь аустенитных и ферритных зерен; следовательно, они имеют «дуплексную» структуру. Этот эффект достигается за счет добавления меньшего количества никеля, чем необходимо для изготовления полностью аустенитной нержавеющей стали.
Молибден в основном используется для повышения коррозионной стойкости аустенитных и дуплексных нержавеющих сталей. В аустенитные нержавеющие стали добавляют от двух до семи процентов, в дуплексные нержавеющие стали – от трех до пяти процентов. Добавление одного или двух процентов молибдена к ферритным нержавеющим сталям также значительно повышает коррозионную стойкость и прочность этих нержавеющих сталей при повышенных температурах.
Рис. 2: Добавление 8% никеля к ферритной хромистой нержавеющей стали позволяет получить аустенитную хромоникелевую нержавеющую сталь, например нержавеющую сталь типа 304. Если к хромистой стали добавляется меньше никеля, около четырех или пяти процентов, создается дуплексная структура, смесь аустенита и феррита, как в дуплексной нержавеющей стали 2205.
Использование молибдена в сталелитейной промышленности
Использование молибдена в сталелитейной промышленности
0 Комментарий admin
Просмотры сообщений: 3,394
Молибден является тугоплавким редким металлом как вольфрам . Молибден и молибденовые сплавы имеют широкий спектр применения и хорошие перспективы в важных отраслях, таких как металлургия, сельское хозяйство, электротехника, химическая промышленность, защита окружающей среды и аэрокосмическая промышленность. В этой статье мы рассмотрим применения олибдена m в сталелитейной промышленности .
Использование молибдена в сталелитейной промышленности
Молибден играет незаменимую роль в регулировании твердости и ударной вязкости стали. В процессе выплавки стали молибден может повысить прочность и твердость чугуна за счет снижения температуры перлитного превращения. Это также может улучшить прочность и сопротивление ползучести при высоких температурах.
Молибденсодержащий чугун с высоким содержанием хрома обладает большей ударной вязкостью, чем безмолибденовый чугун с высоким содержанием хрома, и идеально подходит для применения в жестких абразивных условиях, например, в горнодобывающей промышленности, фрезеровании, дроблении и других процессах. Эти чугуны имеют приемлемые свойства, что устраняет необходимость в дорогостоящей термической обработке, что делает их недорогой альтернативой другим фрикционным материалам.
Железо, содержащее молибден и кремний, вызывает все больший интерес. Его хорошая прочность при температуре 600 °C делает его эффективной и недорогой альтернативой чугуну и стали с более высоким содержанием сплава в высокотемпературных применениях, таких как корпуса турбонагнетателей, выпускные коллекторы двигателей и компоненты нагревательных печей. Ковкий чугун, закаленный аустенитом, имеет уникальную микроструктуру. Его прочность превышает 1000 МПа и обладает хорошей ударной вязкостью. Их специфика делает их идеальными для специальных применений, таких как большие шестерни и коленчатые валы, необходимые для производства электроэнергии, судовые двигатели и крупное горнодобывающее оборудование.
Основным ограничением для увеличения содержания легирующих элементов в высоколегированных слитках, таких как быстрорежущая сталь , является склонность к расслоению при медленном охлаждении. Технология порошковой металлургии распыляет расплавленную сталь на капли, которые чрезвычайно быстро остывают, предотвращая возникновение внутренней ликвации. Сталь, полученная при коагуляции этих частиц, имеет достаточно однородную микроструктуру. По сравнению со сталью той же традиционной марки она имеет бесчисленное количество преимуществ. Многие быстрорежущие стали порошковой металлургии, нержавеющие стали и сплавы на основе никеля были поставлены на рынок в больших количествах, и эта технология указывает на то, что в будущем может быть произведено новое поколение продукции из высоколегированной стали.