Что такое скорость резания: Элементы режима резания | Учебные материалы
alexxlab | 11.07.2020 | 0 | Разное
Элементы режима резания. Основные понятия
Режимом резания называется совокупность элементов, определяющих условия протекания процесса резания.
К элементам режима резания относятся – глубина резания, подача, период стойкости режущего инструмента, скорость резания, частота вращения шпинделя, сила и мощность резания.
При проектировании технологических процессов механической обработки или режущих инструментов возникает необходимость в определении и назначении элементов режима резания. Отечественная практика механической обработки накопила огромный нормативно – справочный материал, с помощью которого можно назначить любой режим резания для любого вида механической обработки. Однако, табличный метод назначения режимов резания является весьма громоздким, так как требует анализа большого количества справочной информации. Более того, все режимные параметры взаимосвязаны и при изменении хотя бы одного из них автоматически изменяются и другие, что еще более усложняет процесс назначения режимов резания.
Аналитический (расчетный) метод определения режима резания менее трудоёмок и более предпочтителен при учебном проектировании технологических процессов механической обработки резанием. Он сводится к определению, по эмпирическим формулам, скорости, сил и мощности резания по выбранным значениям глубины резания и подачи.
Для проведения расчетов необходимо иметь паспортные данные выбранного станка, а именно – значения подач и частот вращения шпинделя, мощности электродвигателя главного движения. При отсутствии паспортных данных расчет выполняется приблизительно, в проделах тех подач и частот вращения шпинделя, которые указаны в справочной литературе.
Выбор режущего инструмента
Его следует начинать с анализа шероховатости поверхностей детали, которая задана на чертеже. В зависимости от параметра шероховатости выбирается метод обработки данной поверхности, которому соответствует свой специфический режущий инструмент. В табл. 1 приведена зависимость шероховатости поверхности от различных методов обработки.
Немаловажное значение для расчета режимов резания имеет выбор материала инструмента. При его выборе следует руководствоваться рекомендациями табл. 2. Для тонких (отделочных) методов обработки материалов с высокими скоростями резания (свыше 500 м/мин) рекомендуется применение сверхтвердых инструментальных материалов.
Наиболее распространенными среди них являются материалы, полученные на основе кубического нитрида бора.
Выбор и назначение глубины резания
Рис. 1.Схема к определению глубины резания при точении
Глубиной резания называется расстояние между обрабатываемой и обработанной поверхностями, измеренное по нормали к последней.
При черновых методах обработки назначают по возможности максимальную глубину резания
В данной работе рекомендуются следующие глубины резания t, мм:
черновая обработка t >2;
получистовая и чистовая обработка t = 2,0 – 0,5;
отделочная обработка (3,2 мкм і Ra > 0,8 мкм) t = 0,5 – 0,1.
При сверлении глубина резания t=0,5·D, при рассверливании, зенкеровании и развертывании t=0,5·(D-d) мм, где
D – диаметр осевого инструмента,
d – диаметр предварительно полученного отверстия, мм.
Рис. 2.Схемы для определения глубины резания при сверлении ( а) и рассверливании (б) отверстий.
При отрезании, точении канавок и фасонном точении глубина резания приравнивается длине лезвия резца (см. рис. 3).
Рис. 3. Схема к определению глубины резания при отрезании
Выбор величины подачи
Подачей называется путь, пройденный какой-либо точкой режущей кромки инструмента, относительно заготовки, за один оборот заготовки (режущего инструмента), либо за один двойной ход режущего инструмента.
Различают подачу на один зуб Sz, подачу на один оборот S и подачу минутную Sм, мм/мин, которые находятся в следующей зависимости:
(1)
где: – частота вращения режущего инструмента, мин-1;
– число зубьев режущего инструмента.
При черновой обработке выбирают максимально возможную подачу, исходя из жесткости и прочности системы, мощности привода станка, периода стойкости режущего инструмента и других ограничивающих факторов. При чистовой обработке – в зависимости от требуемого параметра шероховатости обработанной поверхности.
При черновом точении выполняется вариантный расчёт режимов резания для нескольких значений подач в диапазоне, ограниченном чистовой (табл. 3) и максимальной подачей, допустимой прочностью режущей пластины (табл. 4).
При обработке отверстий осевым режущим инструментом выбирают рекомендуемую подачу, допустимую по прочности инструмента (табл.5).
Исходной величиной подачи при фрезеровании является подача Sz – на зуб. Рекомендуемые подачи для чистового фрезерования приведены в табл. 6.
В учебных целях рекомендуется значения подач выбирать из наиболее распространённого диапазона: 0,05- 0,5 мм/об.
Меньшие значения назначать для чистовой обработки, большие – для черновой.
Выбор значения периода стойкости
Периодом стойкости (стойкостью) режущего инструмента называется время его непрерывной работы между двумя смежными переточками.Выбор значения периода стойкости режущего инструмента рекомендуется сделать из следующего ряда:
15;30;45;60;90;120 мин.
Меньшие значения периода стойкости следует назначать для мелких инструментов.
Расчёт режимов резания при сверлении, рассверливании, зенкеровании и развёртывании
Расчёт режимов резания при резьбонарезании
Расчёт режима резания при шлифовании
Расчёт режимов резания при строгании и долблении
Расчёт режимов резания при фрезеровании
Режимы резания*
Теоретические основы по выбору режимов резания на фрезерных станках
Ширина фрезерования – ширина обрабатываемой поверхности задается, как правило, в чертеже и определяется размером детали или заготовки. В случае обработки нескольких заготовок закреплённых рядом, ширина фрезерования кратно увеличивается.
Глубина фрезерования (или глубина резанья) – толщина слоя снимаемого фрезой материала за один проход. Если снимать много то фреза делает два и более проходов. При этом последний проход производят с небольшой глубиной резанья для получения более чистой поверхности обработки. Такой проход называют чистовым фрезерованием в отличие от предварительного или чернового фрезерования, которое производят с большей глубиной резанья. Однако при небольшом припуске на обработку, фрезерование производится за один проход.
Скорость резания – это путь (обычно обозначаемый в метрах), который проходят режущие кромки зубьев фрезы в одну минуту. Скорость резания рассчитывается по следующей формуле: длину окружности фрезы умножаем на количество зубьев фрезы и на количество оборотов в минуту и все делим всё на 1000 (переводим миллиметры в метры).
Скорость резания обычно определяют по справочным таблицам режимов резания. Так как скорость резания при фрезеровании зависит от стойкости конкретной фрезы, то рекомендуемая в таблицах скорость резания соответствует тому, на какой максимальной скорости может происходить резание без поломки фрезы.
Подача – это величина (обычно обозначаемая в миллиметрах) перемещения шпинделя станка в продольном – Y, поперечном – X или вертикальном – Z направлении.
Подача в одну минуту – величина перемещения шпинделя в миллиметрах за время, равное одной минуте. Вычисляется по формуле: подача в одну минуту равна подачи на один зуб фрезы умноженной на число зубьев фрезы и умноженной на количество оборотов фрезы в минуту.
Как известно, основами резания являются скорость вращения шпинделя и скорость подачи. Выбор диаметра фрезы для работы определяется по двум параметрам – ширине и глубине фрезерования. Ширина фрезерования, или ширина обрабатываемой поверхности, задается, как правило, в чертеже и определяется размером детали или заготовки. В случае обработки нескольких заготовок, закрепленных рядом, ширина фрезерования кратно увеличивается.
Глубина фрезерования – толщина слоя снимаемого фрезой материала за один проход. Если снимать много, то фреза делает два и более проходов. При этом последний проход производят с небольшой глубиной резанья для получения более чистой поверхности обработки. Такой проход называют чистовым фрезерованием в отличие от предварительного или чернового фрезерования, которое производят с большей глубиной резанья. Однако при небольшом припуске на обработку фрезерование производится за один проход.
Скорость резанья – это путь (обычно обозначаемый в метрах в минуту), который проходят режущие кромки зубьев фрезы в одну минуту.
Скорость резанья обычно определяют по справочным таблицам режимов резанья. Так как скорость резанья при фрезеровании зависит от стойкости конкретной фрезы, то рекомендуемая в таблицах скорость резанья соответствует тому, на какой максимальной скорости может происходить резанье без поломки фрезы.
Подача в одну минуту – величина перемещения шпинделя в миллиметрах за время, равное одной минуте. Вычисляется она по следующей формуле: подача в одну минуту равна подаче на один зуб фрезы, умноженной на число зубьев фрезы и умноженной на количество оборотов фрезы в минуту.
Общие рекомендации по режимам резания:
Для мягкой древесины (сосна)
Тип инструмента Рабочая подача мм/мин Скорость вращения Глубина за проход
Торцевая 6мм 2000-3000 20 000-24 000 7,5-8
Торцевая 3мм 1000-1500 20 000-24 000 4,5
Гравер 30°х0,2 800-600 20 000-24 000 3
Для твердой древесины (бук, дуб, фанера)
Торцевая 6мм 1500-2500 20 000-24 000 7,5-8
Торцевая 3мм 500-1000 20 000-24 000 4,5
Гравер 30°х0,2 300-600 20 000-24 000 3
Для двухслойного пластика
Торцевая 3 мм 2000 12 000 0,3
Гравер 30°х0,2 2000 20 000 0,3
Для акрила и полистирола
Торцевая 6 мм 1000-1300 10 000-12 000 3
Торцевая 3 мм 800-1000 12 000-16 000 1,5
Гравер 30°х0,2 300-500 18 000-20 000 0,3-0,6
Для ПВХ
Торцевая 6 мм 1500-2000 12 000 8-10
Торцевая 3 мм 1500-2000 12 000-15 000 4-6
Для алюминиевых сплавов
Торцевая 6 мм 800-1000 14 000 – 18000 0,6
Торцевая 3 мм 500-800 13 000-15 000 0,3
Главная
Форум
Модели для обработки на станках с чпу
Режимы резания при фрезеровании: таблица, элементы, выбор режимов
Поверхностная обработка заготовок методом фрезерования может проводиться исключительно после разработки технологической карты, в которой указываются основные режимы обработки. Подобной работой, как правило, занимается специалист, прошедший специальную подготовку. Режимы резания при фрезеровании могут зависеть от самых различных показателей, к примеру, типа материала и используемого инструмента. Основные показатели на фрезерном станке могут устанавливаться вручную, также проводится указание показателей на блоке числового программного управления. Особое внимание заслуживает резьбофрезерование, так как получаемые изделия характеризуются довольно большим количеством различных параметров. Рассмотрим особенности выбора режимов резания при фрезеровании подробно.
Скорость резания
Наиболее важным режимом при фрезеровании можно назвать скорость резания. Он определяет то, за какой период времени будет снят определенный слой материала с поверхности. На большинстве станков устанавливается постоянная скорость резания. При выборе подходящего показателя учитывается тип материала заготовки:
- При работе с нержавейкой скорость резания 45-95 м/мин. За счет добавления в состав различных химических элементов твердость и другие показатели меняются, снижается степень обрабатываемости.
- Бронза считается более мягким составом, поэтому подобный режим при фрезеровании может выбираться в диапазоне от 90-150 м/мин. Она применяется при изготовлении самых различных изделий.
- Довольно большое распространение получила латунь. Она применяется при изготовлении запорных элементов и различных клапанов. Мягкость сплава позволяет повысить скорость резания до 130-320 м/мин. Латуни склонны к повышению пластичности при сильном нагреве.
- Алюминиевые сплавы сегодня весьма распространены. При этом встречается несколько вариантов исполнения, которые обладают различными эксплуатационными характеристиками. Именно поэтому режим фрезерования варьирует в пределе от 200 до 420 м/мин. Стоит учитывать, что алюминий относится к сплавам с низкой температурой плавления. Именно поэтому при высокой скорости обработки есть вероятность существенного повышения показателя пластичности.
Встречается довольно большое количество таблиц, которые применяются для определения основных режимов работы. Формула для определения оборотов скорости резания выглядит следующим образом: n=1000 V/D, где учитывается рекомендуемая скорость резания и диаметр применяемой фрезы. Подобная формула позволяет определить количество оборотов для всех видов обрабатываемых материалов.
Рассматриваемый режим фрезерования измеряется в метрах в минуту режущие части. Стоит учитывать, что специалисты не рекомендуют гонять шпиндель на максимальных оборотах, так как существенно повышается износ и есть вероятность повреждения инструмента. Поэтому полученный результат уменьшается примерно на 10-15%. С учетом этого параметра проводится выбор наиболее подходящего инструмента.
Скорость вращения инструмента определяет следующее:
- Качество получаемой поверхности. Для финишной технологической операции выбирается наибольший параметр. За счет осевого вращения с большим количеством оборотов стружка получается слишком мелкой. Для черновой технологической операции, наоборот, выбираются низкие значения, фреза вращается с меньшей скоростью, и размер стружки увеличивается. За счет быстрого вращения достигается низкий показатель шероховатости поверхности. Современные установки и оснастка позволяют получить поверхность зеркального типа.
- Производительность труда. При наладке производства уделяется внимание и тому, какова производительность применяемого оборудования. Примером можно назвать цех машиностроительного завода, где налаживается массовое производство. Существенное снижение показателя режимов обработки становится причиной уменьшения производительности. Наиболее оптимальный показатель существенно повышает эффективность труда.
- Степень износа устанавливаемого инструмента. Не стоит забывать о том, что при трении режущей кромки об обрабатываемую поверхность происходит ее сильный износ. При сильном изнашивании происходит изменение показателей точности изделия, снижается эффективность труда. Как правило, износ связан с сильным нагревом поверхности. Именно поэтому на производственной линии с высокой производительностью применяется оборудование, способное подавать СОЖ в зону снятия материала.
При этом данный параметр выбирается с учетом других показателей, к примеру, глубины подачи. Поэтому технологическая карта составляется с одновременным выбором всех параметров.
Глубина резания
Другим наиболее важным параметром является глубина фрезерования. Она характеризуется следующими особенностями:
- Глубина врезания выбирается в зависимости от материала заготовки.
- При выборе уделяется внимание тому, проводится черновая или чистовая обработка. При черновой выбирается большая глубина врезания, так как устанавливается меньшая скорость. При чистовой снимается небольшой слой металла за счет установки большой скорости вращения инструмента.
- Ограничивается показатель также конструктивными особенностями инструмента. Это связано с тем, что режущая часть может иметь различные размеры.
Глубина резания во многом определяет производительность оборудования. Кроме этого, подобный показатель в некоторых случаях выбирается в зависимости от того, какую нужно получить поверхность.
Мощность силы резания при фрезеровании зависит от типа применяемой фрезы и вида оборудования. Кроме этого, черновое фрезерование плоской поверхности проводится в несколько проходов в случае, когда нужно снять большой слой материала.
Особым технологическим процессом можно назвать работу по получению пазов. Это связано с тем, что их глубина может быть довольно большой, а образование подобных технологических выемок проводится исключительно после чистовой обработки поверхности. Фрезерование т-образных пазов проводится при применении специального инструмента.
Подача
Понятие подачи напоминает глубину врезания. Подача при фрезеровании, как и при проведении любой другой операции по механической обработке металлических заготовок, считается наиболее важным параметром. Долговечность применяемого инструмента во многом зависит от подачи. К особенностям этой характеристики можно отнести нижеприведенные моменты:
- Какой толщины материал снимается за один проход.
- Производительность применяемого оборудования.
- Возможность проведения черновой или чистовой обработки.
Довольно распространенным понятием можно назвать подачу на зуб. Этот показатель указывается производителем инструмента, зависит от глубины резания и конструктивных особенностей изделия.
Как ранее было отмечено, многие показатели режимом резания связаны между собой. Примером можно назвать скорость резания и подачу:
- При увеличении значения подачи скорость резания снижается. Это связано с тем, что при снятии большого количества металла за один проход существенно повышается осевая нагрузка. Если выбрать высокую скорость и подачу, то инструмент будет быстро изнашиваться или попросту поломается.
- За счет снижения показателя подачи повышается и допустимая скорость обработки. При быстром вращении фрезы возможно существенно повысить качество поверхности. На момент чистового фрезерования выбирается минимальное значение подачи и максимальная скорость, при применении определенного оборудования можно получить практически зеркальную поверхность.
Довольно распространенным значением подачи можно назвать 0,1-0,25. Его вполне достаточно для обработки самых распространенных материалов в различных отраслях промышленности.
Ширина фрезерования
Еще одним параметром, который учитывается при механической обработки заготовок считается ширина фрезерования. Она может варьировать в достаточно большом диапазоне. Ширина выбирается при фрезеровке на станке Have или другом оборудовании. Среди особенностей отметим следующие моменты:
- Ширина фрезерования зависит от диаметра фрезы. Подобные параметры, которые зависят от геометрических особенностей режущей части, не могут регулироваться, учитываются при непосредственном выборе инструмента.
- Ширина фрезерования также оказывает влияние на выбор других параметров. Это связано с тем, что при увеличении значения также увеличивается количество материала, который снимается за один проход.
В некоторых случаях ширина фрезерования позволяет получить требуемую поверхность за один проход. Примером можно назвать случай получения неглубоких канавок. Если проводится резание плоской поверхности большой ширины, то число проходов может несколько отличаться, рассчитывается в зависимости от ширины фрезерования.
Как выбрать режим на практике?
Как ранее было отмечено, в большинстве случаев технологические карты разработаны специалистом и мастеру остается лишь выбрать подходящий инструмент и задать указанные параметры. Кроме этого, мастер должен учитывать то, в каком состоянии находится оборудование, так как предельные значения могут привести к возникновению поломок. При отсутствии технологической карты приходится проводить выбор режимов фрезерования самостоятельно. Расчет режимов резания при фрезеровании проводится с учетом следующих моментов:
- Типа применяемого оборудования. Примером можно назвать случай резания при фрезеровании на станках ЧПУ, когда могут выбираться более высокие параметры обработки по причине высоких технологических возможностей устройства. На старых станках, которые были введены в эксплуатацию несколько десятков лет назад, выбираются более низкие параметры. На момент определения подходящих параметров уделяется внимание и техническому состоянию оборудования.
- Следующий критерий выбора заключается в типе применяемого инструмента. При изготовлении фрезы могут применяться различные материалы. К примеру, вариант исполнения из быстрорежущей качественной стали подходит для обработки металла с высокой скоростью резания, фреза с тугоплавкими напайками предпочтительно выбирается в случае, когда нужно проводить фрезерование твердого сплава с высоким показателем подачи при фрезеровании. Имеет значение и угол заточки режущей кромки, а также диаметральные размер. К примеру, с увеличением диаметра режущего инструмента снижается подача и скорость резания.
- Тип обрабатываемого материала можно назвать одним из наиболее важных критериев, по которым проводится выбор режима резания. Все сплавы характеризуются определенной твердостью и степенью обрабатываемости. К примеру, при работе с мягкими цветными сплавами могут выбираться более высокие показатели скорости и подачи, в случае с каленной сталью или титаном все параметры снижаются. Немаловажным моментом назовем то, что фреза подбирается не только с учетом режимов резания, но и типа материала, из которого изготовлена заготовка.
- Режим резания выбирается в зависимости от поставленной задачи. Примером можно назвать черновое и чистовое резание. Для черного свойственна большая подача и небольшой показатель скорости обработки, для чистовой все наоборот. Для получения канавок и других технологических отверстий и вовсе показатели подбираются индивидуально.
Как показывает практика, глубина резания в большинстве случаев делится на несколько проходов при черновой обработке, при чистовой он только один. Для различных изделий может применяться таблица режимов, которая существенно упрощает поставленную задачу. Встречаются и специальные калькуляторы, проводящие вычисление требуемых значений в автоматическом режиме по введенным данным.
Выбор режима в зависимости от типа фрезы
Для получения одного и того же изделия могут применяться самые различные виды фрез. Выбор основных режимов фрезерования проводится в зависимости от конструктивных и других особенностей изделия. Режимы резания при фрезеровании дисковыми фрезами или другими вариантами исполнения выбираются в зависимости от нижеприведенных моментов:
- Жесткости применяемой системы. Примером можно назвать особенности станка и различной оснастки. Новое оборудование характеризуется повышенной жесткостью, за счет чего появляется возможность применения более высоких параметров обработки. На старых станках жесткость применяемой системы снижается.
- Уделяется внимание и процессу охлаждения. Довольно большое количество оборудования предусматривает подачу СОЖ в зону обработки. За счет подобного вещества существенно снижается температура режущей кромки. СОЖ должна подаваться в зону снятия материала постоянно. При этом также удаляется и образующаяся стружка, что существенно повышает качество резания.
- Стратегия обработки также имеет значение. Примером можно назвать то, что получение одной и той же поверхности может проводится при чередовании различных технологических операций.
- Высота слоя, который может сниматься за один проход инструмента. Ограничение может зависеть от размера инструмента и многих других геометрических особенностей.
- Размер обрабатываемых заготовок. Для больших заготовок требуется инструмент с износостойкими свойствами, который при определенных режимах резания сможет не нагреваться.
Учет всех этих параметров позволяет подобрать наиболее подходящие параметры фрезерования. При этом учитывается распределение припуска при фрезеровании сферическими фрезами, а также особенности обработки концевой фрезой.
Классификация рассматриваемого инструмента проводится по достаточно большому количеству признаков. Основным можно назвать тип применяемого материала при изготовлении режущей кромки. К примеру, фреза ВК8 предназначена для работы с заготовками из твердых сплавов и закаленной стали. Рекомендуется применять подобный вариант исполнения при невысокой скорости резания и достаточной подаче. В тоже время скоростные фрезы могут применяться для обработки с высоким показателем резания.
Как правило, выбор проводится с учетом распространенных таблиц. Основными свойствами можно назвать:
- Скорость резания.
- Тип обрабатываемого материала.
- Тип фрезы.
- Частота оборотов.
- Подача.
- Тип проведенной работы.
- Рекомендуемая подача на зуб в зависимости от диаметра фрезы.
Использование нормативной документации позволяет подобрать наиболее подходящие режимы. Как ранее было отмечено, разрабатывать технологический процесс должен исключительно специалист. Допущенные ошибки могут привести к поломке инструмента, снижению качества поверхности заготовки и допущению погрешностей в инструментах, в некоторых случаях, поломке оборудования. Именно поэтому нужно уделять много внимания выбору наиболее подходящего режима резания.
Выбор режима в зависимости от материала
Все материалы характеризуются определенными эксплуатационными характеристиками, которые также должны учитываться. Примером можно назвать фрезерование бронзы, которое проводится при скорости резания от 90 до 150 м/мин. В зависимости от этого значения выбирается величина подачи. Сталь ПШ15 и изделия из нержавейки обрабатываются при применении других показателей.
При рассмотрении типа обрабатываемого материала уделяется внимание также нижеприведенным моментам:
- Твердости. Наиболее важной характеристикой материалов можно назвать именно твердость. Она может варьировать в большом диапазоне. Слишком большая твердость делает деталь прочной и износостойкой, но при этом усложняется процесс обработки.
- Степени обрабатываемости. Все материалы характеризуются определенной степенью обрабатываемостью, зависящая также от пластичности и других показателей.
- Применение технологии улучшения свойств.
Довольно распространенным примером можно назвать проведение закалки. Подобная технология предусматривает нагрев материала с последующим охлаждением, после чего показатель твердости существенно повышается. Также часто проводится ковка, отпуск и другие процедуры изменения химического состава поверхностного слоя.
В заключение отметим, что сегодня можно встретить просто огромное количество различных технологических карт, которые достаточно скачать и использовать для получения требуемых деталей. При их рассмотрении уделяется внимание типу материала заготовки, виду инструмента, рекомендуемому оборудованию. Самостоятельно разработать режимы резания достаточно сложно, при этом нужно делать предварительную проверку выбранных параметров. В противном случае может пострадать как инструмент, так и применяемое оборудование.
Режимы резания при токарной обработке: расчет, таблица
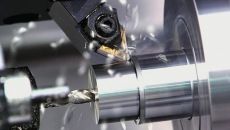
Точение – один из многофункциональных методов обработки деталей разного типа. Он используется для чистовой и черновой работы с изделиями в процессе выполнения их ремонта или изготовления. Внимательный подход к подбору режимов резанья обеспечивает существенное повышение продуктивности данного процесса.
Что это такое
Под режимом резания чаще всего подразумевают характеристики, которые находят расчетным путем. Это глубина, скорость и подача. Данные величины являются очень важными. Без них качественно выточить любую деталь просто невозможно.
При расчете режимов работы учитывают и другие характеристики производимых рабочих манипуляций:
- допустимые припуски;
- вес заготовок;
- частота вращения шпинделя станка.
При необходимости учитываются много других характеристик тех элементов, которые влияют на процесс обработки деталей.
Характеристика режимов работы
Расчет операции резания выполняется с использованием специальных справочных и нормативных документов, которых на данный момент существует немало. Необходимо тщательно изучить представленные таблицы и выбрать в них подходящие значения. Правильно выполненный расчет гарантирует высокую эффективность применяемого режима обработки детали и обеспечивает достижение лучшего результата.
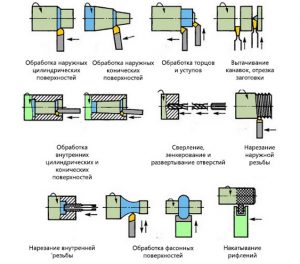
Основные виды токарных работ по металлу
Но такой метод расчета является не всегда удачным, особенно в условиях производства, когда нецелесообразно тратить много времени на изучение таблиц с огромным числом значений. Установлено, что все величины режимов резания взаимосвязаны между собой. Если изменить одно значение, закономерно, что все остальные характеристики обработки станут иными.
Поэтому очень часто специалисты предпочитают применять расчетную или аналитическую методику определения режимов резания. Используются специальные эмпирические формулы, при помощи которых определяются все необходимые нормы. Чтобы расчеты по данной методике были абсолютно точными, необходимо знать следующие параметры токарного станка:
- частота вращения шпинделя;
- величины подач;
- мощность.
На современных производствах для выполнения подобных расчетов используют специальное программное обеспечение. Специалисту достаточно ввести известные данные, после чего компьютер выдаст вычисляемые величины. Применение программ для расчетов существенно облегчает работу специалистов и делает производство более эффективным.
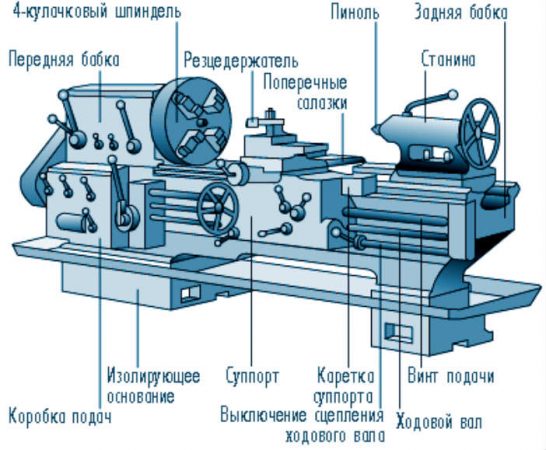
Устройство токарного станка
Схема расчетов
Перед выполнением расчетов операции резания необходимо определить, какой тип режущего инструмента будет использоваться в данном случае. При токарной или абразивной обработке хрупких материалов выбирают оснащение с минимальными показателями. Следует не забывать, что во время работы деталь обычно довольно сильно нагревается. Если скорость обработки будет очень высокая, она может деформироваться, что приведет к ее непригодности.
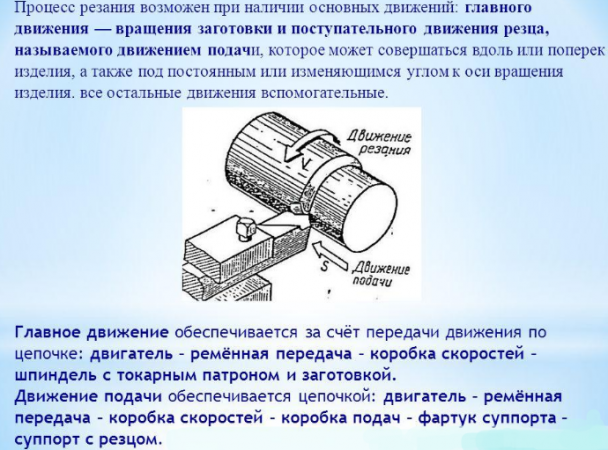
Процесс резания металла
Обязательно учитывается, какая обработка будет осуществляться – чистовая или черновая. В первом случае подбирают рабочие параметры, которые обеспечат максимальную точность. Специалисты обращают внимание и на толщину срезаемого слоя. В зависимости от данной характеристики выбирается количество проходок для выполнения обрезки на специальном оборудовании.
Глубина
Глубина является одним из важнейших параметров для обеспечения качества изготовленных заготовок. Она определяет толщину срезаемого слоя за одну проходку. При выполнении подрезки торца за глубину принимают диаметр детали.
Учитывается количество проходов, что определяется припусками на обработку:
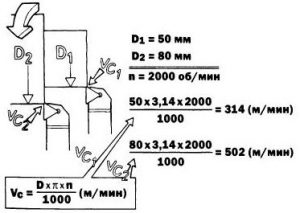
Изменение обрабатываемого диаметра
- 60% на черновую;
- 20–30% на получистовую;
- 10–20% на чистовую.
Для определения глубины обрезки цилиндрических заготовок используется следующая формула:
k=(D-d)/2, где к – глубина обрезки, D – первоначальный диаметр, d – получаемый диаметр.
При определении режимов резания при работе с плоскими деталями вместо диаметров используют длину. Принято считать, что при черновой обработке глубина должна составлять больше 2 мм, получистовой – 1–2 мм, чистовой – меньше 1 мм. Данный параметр зависит от требований к качеству деталей. Чем меньше класс точности, тем больше проходов необходимо выполнить для достижения необходимых свойств изделий.
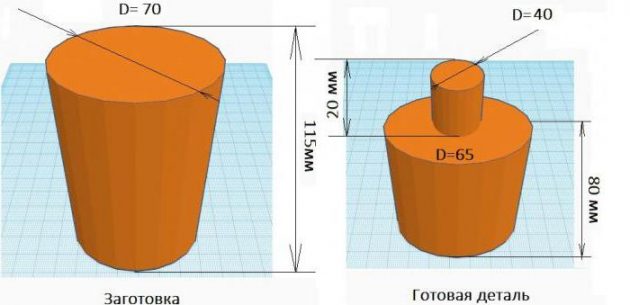
Схема черновой обработки металла
Подача
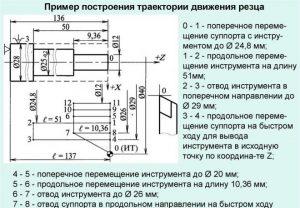
Пример построения траектории движения резца
Под подачей подразумевают величину перемещения резца за один оборот заготовки. При выполнении черновой обработки данный параметр может иметь максимально возможные значения. На завершительном этапе работ значение подачи определяется с учетом квалитета шероховатости. Данная характеристика зависит от глубины обрезки и габаритов заготовки. Чем меньше размеры, тем она ниже. При большой толщине срезаемого слоя выбираются минимальные параметры подачи.
Чтобы облегчить работу специалистам, разработаны специальные таблицы. Там указаны значения подачи при разных условиях режима резанья. Для выполнения точных расчетов иногда необходимо знать размер державки резца.
Если резанье выполняется с существенными ударными нагрузками, значения с таблицы необходимо умножать на коэффициент 0,85. При работе с жаропрочной конструкционной сталью подача не должна быть больше 1 мм/об.
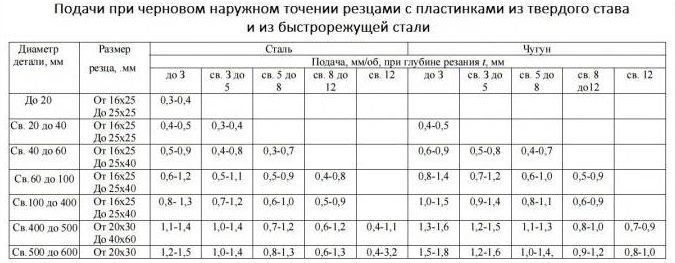
Подачи при черновом наружном точении
Скорость
Скорость резания – это один из важнейших показателей, который определяется на этапе расчетов перед выполнением основных работ. Ее значения зависят от проводимых операций. Обычно отрезание торцов происходит при максимально возможной скорости. Сверление или точение имеют совсем иные требования к данному рабочему параметру. Поэтому для качественного выполнения поставленных задач необходимо знать следующее:
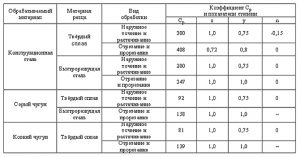
Таблица для расчета режимов резания
- тип выполняемой слесарной операции;
- вид применяемого токарного инструмента;
- материал, из которого изготовлена заготовка.
При традиционной токарной обработке скорость определяется путем умножения диаметра заготовки на количество ее оборотов за минуту и на π. Полученное значение необходимо разделить на 1000. Также скорость резанья можно определить, используя стандартные таблицы для режимов резанья.
Проверка выбранных рабочих характеристик
Когда глубина, подача и скорость определены, их необходимо проверить. Полученные рабочие параметры не должны быть больше нормативных значений, которые указаны в паспорте эксплуатируемого токарного станка.
Обязательно необходимо определить мощность оборудования. Для этого силу обрезки умножают на ее скорость и делят на 1000. Полученное значение сравнивают с тем, что указано в паспорте станка. Если рассчитанные по формулам параметры больше, необходимо корректировать глубину, подачу и скорость, чтобы избежать повреждения оборудования и инструментов.
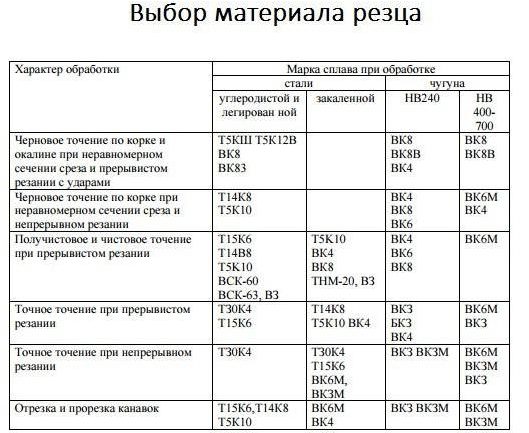
Выбор материала резца при токарной обработке
Какой режущий инструмент использовать
Изготовление деталей на подобных станках осуществляется при помощи специальных токарных резцов. Они должны обеспечивать следующее:
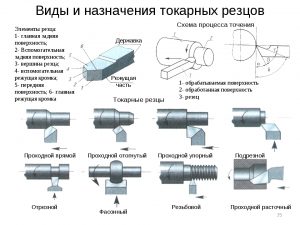
Виды и назначения токарных резцов
- качественную обработку деталей с получением нужной формы и размеров;
- достижение высокого качества обрабатываемой поверхности;
- высокую производительность при минимальных энергетических затратах;
- технологичность в изготовлении;
- ремонтоспособность;
- минимальный расход дорогих материалов для их изготовления.
Токарные резцы классифицируют по разным параметрам. По виду производимых работ они могут быть отрезными, проходными, фасонными, подрезными и т. д. Резцы изготовляются из различных материалов – алмазов, вольфрама, титан-вольфрама и других. В зависимости от конструктивного исполнения данные инструменты бывают цельными, сборными и комбинированными.
Выбор конкретного типа инструмента осуществляется с учетом режимов проводимых рабочих операций, твердости заготовки, геометрических параметров режущей части и других характеристик.
Видео по теме: Токарная обработка металла
Растачивание
Скорость резания, vc
Расточной инструмент вращается с определённым числом оборотов (n) в минуту, растачивая определённый диаметр (DC). Этот процесс обеспечивает определённую скорость резания vc, измеряемую в м/мин на режущей кромке. Скорость резания непосредственно влияет на стойкость инструмента.
Подача, fn

Осевое перемещение инструмента называется подачей и измеряется в мм на оборот. Величина подачи вычисляется путём перемножения значения подачи на зуб (fz) и эффективного числа зубьев (т.е. числа зубьев, обрабатывающих поверхность). Подача на оборот является ключевой величиной, определяющей качество обработанной поверхности и обеспечивающей стружкообразование в пределах, допускаемых геометрией режущей пластины.
Минутная подача, vf
Минутная подача – это скорость осевого перемещения, значительно влияющая на производительность.
Скорость съёма металла, Q
Скорость съёма металла – это количество металла, которое может быть снято за определённый период времени; она значительно влияет на производительность черновой обработки.
Глубина резания, ap
Глубина резания – это разность радиусов предварительного отверстия и отверстия после растачивания.
Главный угол в плане, kr (º)
Положение режущей кромки относительно обрабатываемой поверхности определяется углом в плане, т.е. углом между главной режущей кромкой и направлением подачи.
Потребляемая мощность, Pc

Потребляемая мощность – это мощность, которую станок должен передавать режущей кромке для осуществления процесса резания. При выборе режимов резания должны приниматься во внимание механические и электрические характеристики станка.
Крутящий момент, Mc
Это внутреннее усилие, возникающее в процессе резания под действием внешних нагрузок на инструмент.
Скорость главного движения резания – это… Что такое Скорость главного движения резания?
- Скорость главного движения резания
6. Скорость главного движения резания
F. Vitesse de coupe
Словарь-справочник терминов нормативно-технической документации. academic.ru. 2015.
- Скорость гармонической волны
- скорость горения
Смотреть что такое “Скорость главного движения резания” в других словарях:
скорость главного движения резания — (v) Скорость рассматриваемой точки режущей кромки или заготовки в главном движении резания. 1 направление скорости результирующего движения резания; 2 направление скорости главного движения резания; 3 рабочая плоскость Ps; 4 … Справочник технического переводчика
скорость результирующего движения резания — (ve) Скорость рассматриваемой точки режущей кромки в результирующем движении резания. 1 направление скорости результирующего движения резания; 2 направление скорости главного движения резания; 3 рабочая плос … Справочник технического переводчика
скорость — 05.01.18 скорость (обработки) [rate]: Число радиочастотных меток, обрабатываемых за единицу времени, включая модулированный и постоянный сигнал. Примечание Предполагается возможность обработки как движущегося, так и неподвижного множества… … Словарь-справочник терминов нормативно-технической документации
скорость движения подачи — (vs) скорость подачи Скорость рассматриваемой точки режущей кромки в движении подачи. 1 направление скорости результирующего движения резания; 2 направление скорости главного движения резания; 3 рабочая плоскость Ps; 4 рассматрив … Справочник технического переводчика
рабочая скорость шлифовального (полировального, отрезного) круга — рабочая скорость Скорость главного движения резания, измеренная в точке, максимально удаленной от центра шлифовального (полировального, отрезного) круга, при которой производят абразивную обработку. [ГОСТ 21445 84] Тематики обработка абразивная,… … Справочник технического переводчика
ГОСТ 25762-83: Обработка резанием. Термины, определения и обозначения общих понятий — Терминология ГОСТ 25762 83: Обработка резанием. Термины, определения и обозначения общих понятий оригинал документа: 51. Вспомогательная задняя поверхность F. Face de dépouille complémentaire Определения термина из разных документов:… … Словарь-справочник терминов нормативно-технической документации
движение подачи — (Ds) Ндп. подача Прямолинейное покупательное или вращательное движение режущего инструмента или заготовки, скорость которого меньше скорости главного движения резания, предназначенное для того, чтобы распространить отделение слоя материала на всю … Справочник технического переводчика
касательное движение — (Dк) Прямолинейное поступательное или вращательное движение режущего инструмента, скорость которого меньше скорости главного движения резания и направлена по касательной к режущей кромке, предназначенное для того, чтобы сменять контактирующие с… … Справочник технического переводчика
Обработка металлов резанием — технологические процессы обработки металлов путём снятия стружки, осуществляемые режущими инструментами на металлорежущих станках (См. Металлорежущий станок) с целью придания деталям заданных форм, размеров и качества поверхностных слоев … Большая советская энциклопедия
Металлорежущий станок — машина для обработки резанием металлических и др. материалов, полуфабрикатов или заготовок с целью получения из них изделий путём снятия стружки металлорежущим инструментом (См. Металлорежущий инструмент). М. с. являются основным … Большая советская энциклопедия
Сила резания, составляющие силы резания, силы резания при точении, расчет силы резания, сила резания при фрезеровании
Сила резания R – результирующая сил сопротивления перемещению, действующих на инструмент.
Силу резания R принято раскладывать на составляющие силы – тангенциальную Pz , радиальную Py и осевую Px.
При точении, растачивании, отрезании, прорезании пазов и фасонном точении тангенциальную составляющую, H, рассчитывают по формуле
(8)
где:
Сp; xp; yp; np – эмпирические коэффициент и показатели степени, приведённые в табл.15;
t – глубина резания (при отрезании, прорезании и фасонном точении – длина лезвия резца), мм;
Kp = KMp·Kjp·Kgp·Klp·Krp – поправочный коэффициент, учитывающий фактические условия резания. Численные значения этих коэффициентов приведены в табл. 13 и 16.
Для определения сил Py и Px существуют аналогичные эмпирические формулы. Однако для упрощения и ускорения расчётов величины радиальной Py и тангенциальной Px сил резания рекомендуется [3] принимать по следующим соотношениям
Px=(0,1…0,25) · Pz, (9)
Py=(0,25…0,5) · Pz
Мощность резания, кВт, рассчитывают по формуле
(10)
С учётом потерь, мощность привода, кВт, определится
(11)
где h – к.п.д. станка, (принимается равным 0,85).
Проверка режима резания по мощности резания
Расчитаный режим резания необходимо проверить на достаточность мощности привода станка. Найденное значение Nпр сравнивается с паспортным значением Nпрпасп станка, проверяется условие
(12)
В случае несоблюдения этого условия следует уменьшить силу резания соответствующим изменением периода стойкости инструмента, подачи или глубины резания.
Проверка резца на изгиб
После проведения проверки по мощности резания производится проверка прочности державки резца на изгиб от действия тангенциальной составляющей силы резания (см. рис. 4).
Рис. 4. Схема к определению длины вылета резца.
При этом должно соблюдаться условие:
(13)
где:
B – ширина поперечного сечения державки резца, мм ;
Н – высота поперечного сечения державки резца, мм ;
lр – вылет резца из резцедержателя, мм:
- при наружном продольном точении lр» (1,2 – 1,25)Н,
- при подрезании торцев lр»(D/2)+5, мм;
- при растачивании отверстий lр » L+5 мм;
L – длина обработки, мм (см. формулу 39).
[sи]= 200 МПа – предельно допустимые напряжения на изгиб для державки из конструкционной стали.
При несоблюдении данного условия следует уменьшить вылет резца, увеличить размеры поперечного сечения державки, или уменьшить Pz соответствующим изменением режима резания.
Проверка на точность обработки
Радиальная составляющая силы резания Py может вызвать продольный изгиб заготовки. Поэтому необходима проверка жёсткости обрабатываемой детали, которая проводится исходя из условий точности обработки.
Максимальная нагрузка, Н, допускаемая жёсткостью заготовок, определяется по формуле:
(14)
где:
f – стрела прогиба детали, мм.
- Можно рекомендовать:
- при черновом точении f = 0,1 – 0,2 мм,
- при получистовом – f=0,1 мм,
- при точных работах 20 – 25 % от величины поля допуска на размер обрабатываемой поверхности;
k – коэффициент продольной упругости, зависящий от способа установки детали:
- k = 3 – деталь закреплена в патроне;
- k = 70 – деталь закреплена в центрах;
- k = 130 – деталь закреплена в патроне с поджатием задним центром;
E – модуль продольной упругости, МПа, табл. 17;
– момент инерции поперечного сечения детали (круга), мм;
D – диаметр круга, мм;
ld – длина детали (заготовки).
Если условие не выполняется, необходимо изменить схему закрепления детали; уменьшить глубину резания, величину подачи, геометрические параметры режущего инструмента.
Что такое высокоскоростная резка?
Термин «высокоскоростная резка» (также известный как высокоскоростная обработка) значительно расширился в обрабатывающей промышленности за последние 5–10 лет. Несмотря на его новообретенный статус «модного слова», определение этого процесса остается несколько неуловимым или, в лучшем случае, определяется как простое фрезерование при достаточно высоких оборотах. Реальность высокоскоростной резки немного более тонкая, но, тем не менее, требует внимания из-за значительной эффективности, которую она обеспечивает.В этом посте мы рассмотрим зарождение и развитие высокоскоростной резки как процесса. Исследования и разработка методологии высокоскоростной резки получили наибольшее развитие в конце 70-х – начале 80-х годов в рамках Программы перспективных производственных исследований, финансируемой DARPA. Целью этой программы было определение средств более быстрого снятия материала за счет использования значительно более высоких оборотов в минуту и скорости подачи, чем обычно. Эта программа проверила скорость резания (Vc) в диапазоне от нуля до нуля.От 05 дюймов / мин до 960 000 дюймов / мин и выше. Подобные исследования проводились в Европе в середине 1980-х годов в Техническом университете Дармштадта. Результатом этих исследований стало осознание того, что «золотая середина» высокоскоростного процесса резания зависит от фрезерованного материала, а также от геометрии режущего инструмента. В общем, эти зоны наилучшего восприятия определяются следующим образом:Параметры высокоскоростной резки различных измельчаемых материалов (см. Выше).
По достижении порогового значения диапазона HSM преимущества этого метода резки начинают проявляться.Преимущества высокоскоростной резки реализуются в четырех основных областях:
1.) Повышенная точность обработки
По мере увеличения скорости резания сила резания уменьшается из-за явления, называемого тиксотропией – или свойства материала «размягчаться при работе» из-за деформации сдвига, передаваемой ему режущей кромкой инструмента, а затем возвращаться обратно к исходные свойства твердости после завершения процесса резки. Это свойство особенно характерно для алюминиевых сплавов, что делает алюминий идеальным кандидатом для высокоскоростной резки.
2.) Улучшение качества поверхности
Общие знания о механической обработке говорят нам, что теплота трения в процессах фрезерования генерируется одинаково с каждой стороны режущей кромки инструмента (составляет почти 80% всей индуцированной теплоты трения), а еще 20% генерируется за счет деформации или изгиба образовавшейся чип. В процессе высокоскоростной резки стружка отводится с такой высокой скоростью, что большая часть (примерно 60%) тепла, вызванного трением, не имеет достаточного времени для передачи в окружающую заготовку или сам инструмент.В результате обработка обработанной поверхности демонстрирует превосходное качество с заметным снижением температурной деградации заготовки.
3.) Уменьшение образования заусенцев
Основываясь на исследованиях, посвященных передовым методам высокоскоростной обработки, наблюдается заметное уменьшение образования заусенцев после достижения достаточно высокой скорости резания. Это уменьшение образования заусенцев является функцией как самой скорости резания, так и правильного геометрического дизайна режущей кромки. Короче говоря, режущий инструмент, который был правильно спроектирован для обработки обрабатываемого материала, который вращается с достаточной скоростью, воздействует на рез, который достаточно быстрый, чтобы разрезать материал полностью и чисто, тем самым уменьшая или исключая образование бора.
4.) Улучшенная эвакуация стружки
Подобно уменьшению образования заусенцев, улучшение эвакуации стружки, которым пользуются те, кто использует методы высокоскоростной резки, в первую очередь является результатом геометрии режущего инструмента в сочетании с высоким энергетическим состоянием, создаваемым применением RPM. Благодаря скорости резания, превышающей 500 м / мин, и режущему инструменту, оптимизированному для удаления большого объема стружки за короткий период времени, результирующая стружка может быть выброшена из зоны обработки с высокой скоростью, что значительно снижает вероятность повторной обработки стружки или повреждения детали из-за обилия остаточной стружки.Поскольку скорости шпинделя в диапазоне от 8000 до 12000 об / мин становятся очень распространенными на рынке станков, возможность использовать преимущества высокоскоростной резки стали, чугуна и сплавов на основе никеля уже доступна производителям, которые готовы к адаптации. их стратегии к тем, которые соответствуют лучшим практикам HSC. Высокоскоростная резка цветных металлов, таких как латунь, алюминий и инженерные пластмассы, требует значительно более высоких оборотов в минуту, и поэтому желающие воспользоваться преимуществами высокоскоростной резки этих материалов должны сосредоточиться на фрезерном оборудовании, способном работать на высокая скорость вращения шпинделя от 25 000 до 50 000 об / мин и более.Учитывая потребность в обрабатываемых деталях, которые демонстрируют постоянно растущий уровень точности и качества, высокоскоростная резка предлагает средства работы «умнее, а не тяжелее» – за счет использования фрезерной системы с ЧПУ, где синергия между материалом, режущим инструментом и скоростью резания обеспечивает уровень производительности, невиданный в традиционных методах обработки.
.Полное руководство (обновлено на 2020 год)
Как машинисты рассчитывают подачу и скорость?
Подачи и скорости важны, потому что они являются ключом к увеличению срока службы инструмента, более высокой скорости обработки (за счет более высокой скорости съема материала) и лучшего качества поверхности. Но они включают в себя множество разных концепций, из-за которых их сложно усвоить.
Мы опросили наших читателей, чтобы спросить опытных специалистов по ЧПУ, какие самые сложные концепции и методы ЧПУ нужно изучить, и вот что они сказали:
Подачи и скорости – это сложнее всего выучить в ЧПУ…
Ответ, с большим отрывом, заключался в том, что подача и скорость – это самые сложные вещи для изучения в ЧПУ.Это руководство призвано облегчить вам процесс обучения!
Для начала стоит спросить: “Как машинисты определяют подачу и скорость?” Мы опросили наших читателей и вот что они сказали:
Есть несколько подходов:
– Вы можете создать или позаимствовать электронную таблицу. Это наименее популярный вариант по причинам, о которых я расскажу. По сути, это большая работа с множеством ограничений.
– Примерно столько же используют Справочник по машинам.Он довольно устаревший, особенно для приложений с ЧПУ.
– Поразительно мало используют свое программное обеспечение CAM, хотя в большинстве CAM оно предусмотрено. Причина проста, и мы обнаружили ее в наших опросах по CAM Software. Большинство программ CAM действительно плохо справляются с подачей и скоростью. Вам довольно легко добиться большего успеха.
– Вы можете полагаться на звук или ощущение. Для этого требуется довольно много опыта, и, хотя у этого есть свои преданные, в принципе это не работает. Если бы это было так, вы могли бы купить компакт-диски «Тренировка слуха» для машинистов, и компания Boeing потребовала бы, чтобы вы прошли тест на аудиосигнал с передачей и скоростью на слух, прежде чем вас наняли бы.Ничего из этого не происходит, потому что вы можете слышать только очень плохую подачу и скорость. Вы не можете слышать что-то плохое, и вы точно не можете отличить нормальную и действительно отличную подачу и скорость.
– Вы можете положиться на стандартные разрезы, которые работали в прошлом, или на практические правила. Этот метод довольно популярен, но он явно ограничивает. В конце концов, все ли карманы вы прорезаете одинаковой глубины? В каждой работе есть различия, и если вы ограничены лишь несколькими стандартными сокращениями, вы упускаете возможности.Кстати, одна из причин, по которой CAM делает такую паршивую работу, заключается в том, что он использует подход стандартных сокращений в базе данных. Каждая работа индивидуальна.
– Вы можете полагаться на данные из таблицы подачи и скорости в Каталоге инструментов. Эти данные важны, но они используются сами по себе и имеют ограничения. Например, диаграмма подачи и скорости представляет собой двухмерную таблицу. Он может охватывать только 2 переменные. Наш калькулятор подачи и скорости G-Wizard охватывает 60 переменных! Когда вы в последний раз просматривали 30 графиков, чтобы определить подачу и скорость? Вы в принципе не можете этого сделать, поэтому:
– Безусловно, наиболее популярным вариантом является использование калькулятора каналов и скорости, такого как G-Wizard.Если вы готовы принять калькулятор каналов и скорости и хотите двигаться дальше и изучать другие вещи, нажмите здесь. Если вы хотите узнать больше о других возможностях, продолжайте читать.
Почему я не могу просто спросить других опытных специалистов по ЧПУ об их подаче и скорости?
Вы все время видите это в Интернете на форумах. Кто-то хочет узнать лучшие каналы и скорости для нового материала или с каким-то новым инструментом. Вы даже можете потратить деньги, чтобы присоединиться к службе, где эксперты предоставят вам свои проверенные рецепты с видео, чтобы вы знали, что это работает.
Боже мой! Все эти вещи настолько ограничены, отнимают много времени и потенциально дороги.
Первая проблема заключается в том, что вы не представляете, какого качества вы получаете из этих внешних источников. Каковы были их критерии тестирования? Насколько тщательно они протестировали?
Даже когда у вас есть видео, вы на самом деле не знаете, если они не проверяют на разрушение инструмента в видео гораздо больше, чем на той конкретной машине, когда инструмент был настроен этим конкретным человеком, с этим конкретным материалом, инструмента хватило на то, чтобы снять видео.Вы не представляете, сколько было прогиба (я называю прогиб инструмента «бесшумным убийцей инструмента») или какой формы была форма фрезы после обработки.
А те ребята, которых вы спросите в Интернете? Вы действительно понятия не имеете, что там происходит.
Чтобы стать успешным специалистом по ЧПУ, вы должны контролировать подачу и скорость. Вы должны иметь возможность в любое время получить хорошие подачи и скорости для вашего станка, инструментов, материалов и передового опыта.
Могу ли я выполнить эти вычисления по «базовой формуле», возможно, в электронной таблице?
Совершенно верно! Вся информация доступна.Но, и это важно, происходит гораздо больше, чем могут учесть простые формулы, используемые для расчета скорости подачи с ЧПУ и частоты вращения шпинделя. В духе полного раскрытия информации вы можете найти простые формулы во многих местах, но я дам ссылку на Википедию.
Эти формулы принимают в качестве входных данных скорость резания и диаметр инструмента для расчета скорости вращения шпинделя, а также количество канавок, скорость вращения шпинделя и нагрузку на стружку для расчета скорости подачи с ЧПУ. Фактически, я даже построил калькулятор, используя только простые формулы, и сделал его бесплатным онлайн.Проверьте это:
[Простой калькулятор скорости подачи формулы и подачи]
Кажется, просто, так в чем же проблема?
Ну, в резке задействовано много непонятной физики.
Например, существует так называемое «радиальное утонение стружки». Я объясню это ниже, но эти формулы в Википедии не учитывают истончение стружки, поэтому каждый раз, когда вы режете менее половины диаметра фрезы в качестве шага или ширины реза, они ошибаются.
Чем тоньше разрез, тем больше они ошибаются, и в конечном итоге они будут очень неправильными.Под неправильным я подразумеваю, что, если вы используете эти подачи и скорости, они преждевременно изнашивают ваш резак. Итак, вам нужно изучить формулы для утонения стружки, чтобы вы тоже могли их добавить.
Вам также понадобится большая таблица материалов с указанием стружкодробления и поверхностной скорости. В идеале ваша таблица должна быть достаточно большой, чтобы быть базой данных материалов, которая учитывает не только широкие классы материалов, но и отдельные сплавы, а также состояние сплава и соответствующим образом корректирует цифры.
Вы захотите уменьшить ваши цифры, если вы играете в слоты. Фактически, вы хотите отрегулировать, исходя из того, насколько широк и глубина разреза. Существуют таблицы производителей, которые помогут вам в этом, и это всего лишь еще один шаг, который нужно добавить в ваш процесс.
Говоря о шагах, все это складывается, и, в конце концов, у вас есть очень много шагов, чтобы вводить числа в калькулятор, одновременно бешено листая вперед и назад, чтобы посмотреть на различные диаграммы. Для этого подхода вы можете использовать электронную таблицу Excel.Фактически, именно так мой G-Wizard загружает и ускоряет программное обеспечение, но я предупреждаю вас, вы перерастете Excel, если будете продолжать добавлять навороты, как я.
Как вы знаете, калькулятор G-Wizard учитывает почти 60 различных переменных. Но становится еще хуже. Подсчет любой индивидуальной формулы – это неплохо. Даже вычисление 60 – это не конец света. Но справиться со всеми их взаимодействиями, особенно с обратным вычислением, в электронной таблице невозможно. Они созданы для решения формул только в одном направлении, и их способность возвращаться назад сильно ограничена.
Привет, я написал одну из самых популярных электронных таблиц в то время под названием «Quattro Pro». Я кое-что знаю о таблицах. Продолжайте читать, и я расскажу вам, почему электронные таблицы не работают и почему я вместо этого написал калькулятор G-Wizard.
А как насчет калькуляторов подачи и скорости?
LOL, я думал, вы никогда не спросите (и держу пари, вы полагали, что я приеду сюда рано или поздно, потому что я продаю программное обеспечение, которое рассчитывает подачи и скорости).
Дело в том, что вы можете выяснить все, что вам нужно знать, чтобы делать то, что делает программа, и вы можете сделать это самостоятельно.Все данные доступны, если вы хотите найти время на их изучение.
Чтобы написать G-Wizard, я, вероятно, просмотрел несколько сотен научных работ, написанных докторами наук, и бесчисленные тысячи страниц в других местах в Интернете. У меня есть постоянные поисковые запросы Google, которые каждое утро предупреждают меня, если кто-то публикует новую статью о скоростях и каналах, которые могут быть интересны. Я потратил годы на создание всего этого в программном обеспечении G-Wizard, поэтому, если вы начнете сегодня, вам потребуются годы, чтобы получить что-то столь же сложное, и к тому времени G-Wizard будет еще лучше улучшен.
Есть две важные причины, по которым вы захотите изучить калькулятор подачи и скорости, такой как G-Wizard:
1. Они работают и дают лучшие результаты, чем более простые методы. Программа может учитывать гораздо больше переменных, чем вы можете ввести в свой настольный калькулятор. Он может представить все это в пользовательском интерфейсе, который намного эффективнее электронной таблицы. И он может выполнять математические вычисления, которые просто невозможно выполнить в электронной таблице. Все это сэкономит вам время и деньги, будь вы любитель или профессионал.А если вы новичок, это также избавит вас от многих разочарований.
2. Потому что у вас нет времени на все исследования и навыков для создания программного обеспечения, которое объединяет все это воедино. Или даже если вы это сделаете, G-Wizard дешев, так зачем беспокоиться? Использование специального калькулятора Feeds and Speeds выполняется быстро и легко.
Вот отличное видео от G-Wizard Video University, которое показывает, как легко решить самую сложную проблему, существующую в CNC Feeds and Speeds с G-Wizard:
Я не буду вдаваться в подробности, кроме как сказать, что не могу понять, почему каждый машинист не захочет использовать какой-либо калькулятор (независимо от того, выберете ли вы G-Wizard или нет).В конце концов, кому не нужны наилучшие скорости съема материала, качество поверхности или стойкость инструмента?
Основываясь на результатах нашего опроса, я полагаю, что большинство машинистов понимают, что им нужен калькулятор подачи и скорости. Вы можете получить в свои руки лучший калькулятор подачи и скорости, доступный прямо сейчас: Ознакомьтесь с некоторыми из тысяч производителей мирового класса, которые сегодня используют G-Wizard:
Какова роль рекомендаций производителя?
В этот момент появится несколько машинистов и спросят о рекомендациях производителя.В конце концов, разве производитель не знает лучше всего, как использовать его инструменты?
Короткий ответ: «Да, но это намного сложнее».
Во-первых, помните, когда мы говорили о двухмерных диаграммах подачи и скорости с ЧПУ? А помните, как G-Wizard считает 60 переменных? Если вы просто просматриваете графики подачи и скорости в каталогах инструментов, вы упускаете множество переменных.
Но есть более серьезная проблема: о чем вам не говорят производители?
Некоторые машинисты считают, что их производитель заявляет агрессивные маркетинговые соображения.Они предлагают невероятно высокие скорости подачи и резания, которые инструмент на самом деле не может поддерживать или которые не сработают, когда машинист попробует их. В некоторых случаях это верно, но большинство производителей не могут себе этого позволить. В конце концов, если резаки не работают, вы собираетесь их заказывать?
То, что они могут себе позволить, – это оттенять вещи в сторону агрессивных. В конце концов, кто должен сказать, являются ли цифры немного агрессивными и инструмент изнашивается немного быстрее, чем должен?
Для этого есть средства.G-Wizard, например, учитывает множество рекомендаций производителя в отношении соответствия яблок и яблок (то есть одинаковых покрытий и геометрии). Затем он выполняет очень сложную обработку чисел, чтобы попытаться отделить факт от вымысла. Другими словами, он пытается определить, является ли производитель чрезмерно агрессивным (отличный MRR, более низкий срок службы инструмента) или чрезмерно консервативным (большая стойкость инструмента, более низкий MRR), чтобы получить некоторые «сбалансированные» показатели. Для этого он анализирует как минимум 3 производителя на предмет редко используемых инструментов и 12-15 производителей на предмет часто используемых инструментов (например,грамм. концевые фрезы или спиральные сверла). Затем он предоставляет ползунок, с помощью которого вы можете настроить, хотите ли вы быть консервативными или агрессивными:
Педаль газа G-Wizard или слайдер «черепаха-заяц»…
Мы называем эту особенность «педалью газа», и она изображается в виде черепахи и зайца, во многом как старые ручные мельницы Бриджпорта для регулирования скорости. Я расскажу больше о том, как использовать педаль газа и как думать о том, насколько агрессивным вы хотите быть, в статье «Инструментальный цех по сравнению с производственными потоками и скоростями», которая является следующей после этой статьи.
Возможность делать свой собственный выбор относительно консервативности или агрессивности полезна, но вот реальный способ думать о калькуляторах и другом программном обеспечении для машинистов: Все дело в том, сколько переменных вы можете освоить. .
Базовая диаграмма подачи и скорости, подобная тому, что есть в вашем каталоге инструментов, представляет собой двумерный объект. Следовательно, он охватывает только 2 переменные. Они используют несколько диаграмм, добавляют столбцы и практические правила, чтобы охватить еще несколько переменных – может быть, от 4 до 6.
Сложное программное обеспечение подачи и скорости позволяет управлять гораздо большим количеством переменных, чем вы могли бы управлять вручную. Чем больше переменных вы сможете освоить, тем точнее будут ваши подачи и скорости. Каждый раз, когда вы учитесь управлять некоторыми дополнительными переменными, вы можете добиваться лучших результатов. G-Wizard помогает освоить как можно больше. Чтобы дать представление о том, насколько это безумно, G-Wizard учитывает почти 60 различных переменных при вычислении скорости и подачи.
Сравните это с полдюжиной формул, рассмотренных в Википедии, и вы начнете понимать сложность современных калькуляторов подачи и скорости.Помимо 60 переменных, он обращается к 14 отдельным базам данных. Общий размер всех этих данных делает G-Wizard калькулятором больше, чем G-Wizard редактором G-кода, когда я пишу это, хотя редактор G-кода – гораздо более сложная часть программного обеспечения.
Калькулятор больше из-за огромного объема баз данных. И он может рассматривать все эти данные вместе со всеми этими переменными и производить вычисления в мгновение ока, которые дают результаты.Вернемся еще раз к данным производителя. Мы говорим, что вы должны игнорировать это? Я вижу два случая:
- Вы новичок или тот, кого не волнует энная производительность фрез. В этом случае вам следует игнорировать данные производителя. Настройки G-Wizard по умолчанию консервативны и поступят правильно. В любом случае большинство пользователей получают более короткое время цикла и более длительный срок службы инструмента благодаря настройкам по умолчанию.
- Вам нужен каждый прирост производительности, который вы можете получить.Вы должны использовать данные производителя. Но можно подумать, что данные калибруют G-Wizard, чтобы он мог творить чудеса на еще более высоком уровне.
Если вы относитесь к последнему лагерю и используете определенную линейку инструментов, как и большинство магазинов, вам нужно, чтобы ваш калькулятор мог импортировать и использовать данные производителя. В идеале он будет импортировать и использовать его вместе со всеми другими встроенными правилами и формулами.
Последний пункт важен: вам нужно применить все математические вычисления, даже если у вас есть данные производителя.Зачем? Потому что данные производителя должны быть упрощены в интересах презентации.
Помните, что в двумерной таблице учитываются всего 2 переменные, например, материал и диаметр инструмента, чтобы найти скорость резания и нагрузку на стружку. Если вам повезет, они дадут вам пару дополнительных столов и, возможно, несколько практических правил:
– «Эти числа подходят для глубины резания 1/2 диаметра».
– «Уменьшите SFM на 50% для полного прорезания пазов или при резке более чем на 2 диаметра в глубину.”
Вы наверняка видели такие правила. И снова калькулятор может рассматривать гораздо более сложные модели. Он может плавно интерполировать от 0 до 2-х кратной глубины диаметра, постоянно регулируясь. При расчете радиального утонения стружки он может учитывать любую ширину пропила, а не только те, которые указаны в таблицах производителя.
Это ценно и позволяет повысить производительность независимо от того, для чего вы пытаетесь оптимизировать. Данные производителя дополняют 60 переменных и 14 баз данных внутри G-Wizard, но не заменяют их.Кроме того, производители любят давать большие диапазоны для поверхностной скорости и загрузки стружки, а затем очень мало рассказывают о том, как выбрать лучшую точку в пределах диапазона.
Вот в чем хорош G-Wizard – дает точный ответ вместо диапазона.
Итак, введите данные производителя в свой калькулятор, чтобы он мог повысить ценность этих данных. G-Wizard позволяет вам импортировать данные в виде файлов электронной таблицы (CSV), чтобы упростить задачу. Он также включает в себя большой каталог загружаемых данных производителя, поэтому вам, возможно, вообще не придется вводить какие-либо данные.Наконец, если в вашем калькуляторе есть поддержка таблицы инструментов (набор инструментов) и возможность импорта данных производителя, они станут идеальными инструментами для сравнения производительности различных инструментов.
Ресурсы
Если вы все еще не уверены, что вам нужен калькулятор подачи и скорости, попробуйте следующие ресурсы: ИНФОГРАФИЯ: Зачем нужен калькулятор подачи и скорости 11 распространенных ошибок простых формул скорости резания
.Высокоскоростная обработка (HSM) [Подробное руководство + скорости и подачи]
Примечание : Высокоскоростная обработка – это урок 11 нашего бесплатного мастер-класса по электронной почте и скорости. Щелкните здесь, чтобы узнать больше о мастер-классе.
Datron M8 Cube использует высокоскоростной шпиндель и методы высокоскоростной обработки для достижения максимальной производительности…
Что такое высокоскоростная обработка (HSM)?
Это видео из моей серии CNC Chef для журнала Cutting Tool Engineering Magazine дает краткое введение в Что такое высокоскоростная обработка (HSM):
Чтобы быстро перейти к высокоскоростной обработке (HSM), попробуйте мое видео CNC Chef…
Существует множество определений высокоскоростной обработки (HSM).MMSOnline использует слоган «Достижение высоких показателей съема металла с помощью быстрых проходов фрезерования» для зоны HSM на своем сайте. Еще одно очень высокотехнологичное определение HSM – «Обработка на резонансной частоте станка», которое относится к методам HSM для выбора скоростей шпинделя, которые минимизируют вибрацию. Вы могли подумать, что «высокоскоростная» часть HSM будет делать упор на более высокие скорости шпинделя (Sandvik утверждает, что HSM начинается с 18000 об / мин), но такая интерпретация не универсальна, так как различные цеха обнаружили, что методы HSM могут хорошо работать даже на более медленных фрезерных шпинделях.Другие утверждают, что HSM – это высокая скорость съема материала и получение достаточно хорошей поверхности, которую можно назвать готовой за один проход.
Одной из вещей, которая заставила людей задуматься о HSM, было открытие, что после определенного момента увеличение скорости шпинделя фактически снижает нагрев при резке :
Эта удивительная таблица взята из книги доктора Герберта Шульца «История высокоскоростной обработки».
Пунктирными линиями показаны температуры при различных скоростях поверхности, измеренные в м / мин.Вот США, мы больше привыкли к SFM. Хотите понять, что такое поверхностная скорость, SFM, и как перейти от SFM к RPM на шпинделе? Если вы не знакомы, это простой вопрос, и ссылка на него объяснит.
Обратите внимание, что все материалы неуклонно поднимаются вверх, а затем в конечном итоге снова начинают опускаться вниз по мере увеличения поверхностной скорости. Каким-то образом высокоскоростная обработка вызывает снижение температуры сверх определенной скорости вращения шпинделя!
Этот график в метрах в минуту, поэтому умножьте значения примерно на 3, чтобы получить SFM.Для алюминия, например, у нас довольно хороший провал к тому времени, когда мы достигаем 1000 SFM. Фактически, его температура более эквивалентна менее чем 300 SFM по другую сторону алюминиевой кривой – для алюминия это ничего. Черт возьми, если у нас будет достаточно быстрый фрезерный шпиндель, будет даже место для более быстрой работы из быстрорежущей стали и более низких температур (вы заметите, что критические температуры для различных материалов фрез также отмечены отметкой – оставайтесь ниже линии для фрезы!).
Сталь и чугун сужаются более мягко, чем алюминий, но эффект сохраняется.Да, Вирджиния, конечно, есть какое-то странное поведение, когда вы начинаете с этого HSM!
То же исследование показало, что силы резания также снижаются, и это, по крайней мере, одна из причин, почему падают температуры и почему при HSM-обработке в правильных диапазонах частоты вращения вы можете достичь высокого MRR при меньших силах резания.
Боковая панель: Температура активации покрытия, шоковое охлаждение и отключение охлаждающей жидкости Говоря о температуре, иногда важно немного тепла.Некоторые покрытия, такие как TiAlN, требуют минимальной температуры «активации». При этой температуре их химический состав изменяется, покрытие «активируется», и только тогда оно выполняет свою работу по защите резца. Сочетание желания активировать покрытие и желания избежать шокового охлаждения хрупкого карбида (что приводит к его растрескиванию и расколу) – вот почему мы можем видеть рекомендацию производителя инструмента выключать охлаждающую жидкость даже при очень высокой скорости шпинделя, общие для высокоскоростной обработки. |
Методы высокоскоростной обработки
Каким бы ни было ваше любимое определение HSM, мне нравится смотреть на HSM как на совокупность методов, которые «выросли» вместе в различных операциях аэрокосмической обработки, таких как Boeing. Первоначально в нем использовались очень высокоскоростные шпиндели, но с тех пор оказалось, что многие из этих методов применимы даже для низкоскоростных фрезерных шпинделей.
Эти методы настолько полезны, что многие программы CAM включают в себя траектории HSM, которые упрощают использование HSM для любой работы.
Перечислим некоторые из этих методов:
– HSM предпочитает комбинировать черновые и чистовые проходы. На самом деле это возможно только с более высокоскоростными шпинделями, потому что более низкие скорости просто не дают качества поверхности. Возможность пропустить финишный проход также зависит от пакета CAM. Некоторые алгоритмы HSM более плавные, чем другие. Если вы пытаетесь обойтись более медленным шпинделем, вам придется разделить на более традиционные черновой и чистовой проходы. Для чистового прохода используйте инструмент с максимально возможным количеством канавок.Чистовая обработка предполагает, что все внутренние углы были зачищены, поэтому будет достаточно свободного места для стружки. Чем больше у вас канавок, тем быстрее вы сможете выполнять работу при заданной загрузке стружки. Следовательно, производительность повышается. Единственная причина использовать меньше канавок – улучшить зазор от стружки.
– HSM предпочитает меньший инструмент, который движется быстрее, чем очень большой медленно движущийся инструмент, предназначенный для «забивания». Инструмент меньшего размера позволяет сэкономить на смене инструмента и упрощает достижение идеала, заключающегося в устранении необходимости в отдельных черновых и чистовых проходах.
– Чтобы максимально увеличить срок службы инструмента, воспользуйтесь преимуществом относительно низкой ширины реза от 10-15% диаметра инструмента до 5%, в зависимости от того, где находится оптимальное значение для максимальной скорости вращения фрезерного шпинделя и SFM, с которым ваш инструмент может справиться в материал. Эти низкие радиальные глубины позволяют инструменту лучше очищать стружку и время для охлаждения на воздухе, что обеспечивает гораздо более высокую производительность, особенно при работе с более твердыми материалами. См. Статью об отводе тепла от разреза, чтобы получить представление о том, как это работает. При небольшой ширине реза увеличьте глубину пропила.Это позволяет задействовать больше канавок фрезы вместо того, чтобы просто изнашивать нижнюю часть концевой фрезы.
– Более высокое MRR (и более короткое время цикла) обычно требует немного большей ширины реза. Думайте о сроке службы инструмента больше с точки зрения того, сколько кубических дюймов материала можно удалить с помощью инструмента, а не с точки зрения того, сколько минут он может проработать, и вы быстро увидите, что такая большая ширина реза имеет больший экономический смысл. Некоторое тестирование проводится для того, чтобы найти свой баланс.
– Когда скорость шпинделя является ограничивающим фактором, рассмотрите возможность использования концевой фрезы с высокой подачей.Концевые фрезы с высокой подачей максимизируют осевое утонение стружки и позволяют значительно увеличить скорость подачи. Еще одна популярная стратегия черновой обработки, когда скорость шпинделя не так велика, как хотелось бы, а жесткость станка не велика, – это врезная черновая обработка.
– Используйте стратегии траектории CAM, позволяющие избежать «Тирания угла» (подробнее о фрезах см. Ниже). К таким стратегиям относятся стратегии постоянного угла зацепления инструмента, такие как Volumill или адаптивная очистка, трохоидальное фрезерование и нарезка или снятие углов.
– Поскольку настоящие шпиндели HSM предлагают гораздо более широкий диапазон оборотов в минуту, чем обычные шпиндели, HSM часто делает упор на выборе скоростей шпинделя, которые обеспечивают максимальную стабильность зон фрезерования, где вибрация гораздо менее вероятна.Те же принципы защиты от вибрации могут быть применены к более низким скоростям шпинделя, просто у вас будет меньше оборотов в минуту, чтобы найти стабильную зону, которая максимизирует производительность. См. Нашу статью о вибрации, чтобы узнать больше о стабильных зонах фрезерования и роли частоты вращения шпинделя в вибрации.
Итак, у вас есть небольшой арсенал стратегий на выбор для повышения вашей производительности с использованием идей, изученных в мире HSM. Давайте подробнее остановимся на некоторых из них.
Радиальное утонение стружки при высокоскоростной обработке
Одна из первых проблем, с которыми вы столкнетесь при попытке применить HSM с его малой шириной резания (или шаговым шагом), – это радиальное утонение стружки.Мы написали несколько статей на эту тему, но для быстрого обзора рассмотрим следующую диаграмму:
Вид вниз по оси фрезы показывает, как работает радиальное утонение стружки…
Обратите внимание на то, как малая ширина пропила создает намного более тонкую стружку, чем полная глубокая резка. Каждый раз, когда ваша ширина реза меньше половины диаметра фрезы, вам нужно начать учитывать уменьшение толщины стружки. Невыполнение этого требования означает, что вы не работаете с нагрузкой на чип, рекомендованной производителем.В лучшем случае вы оставляете деньги на столе, не сокращая их так быстро, как только можете. В худшем случае эти слишком тонкие стружки приводят к истиранию и полировке, в результате чего инструмент нагревается и быстрее изнашивается.
Между прочим, такая геометрия утонения стружки возникает снова и снова. Вы можете представить себе диаграмму выше, как если бы она смотрела вниз по оси концевой фрезы. Или вы можете рассматривать его как острие фрезы с шариковой головкой (да, мы получаем утонение стружки по-другому!). Вы также можете думать об этом как о форме пластины, которая помогает объяснить, почему фрезы с круглыми пластинами могут быть такими эффективными.
Тороидальный резак Tormach использует круглые или пуговичные вставки для лучших результатов…
Стандартные расчеты машиниста для подачи и скорости не учитывают утонение стружки и все эти другие геометрические эффекты. Достаточно просто подумать о том, как они складываются, чтобы у вас закружилась голова: происходит ли утонение стружки при небольшой ширине реза в двух разных измерениях?! ??
Вам понадобится более мощный калькулятор машиниста, такой как G-Wizard, чтобы определить правильную подачу и скорость, где утонение стружки является фактором.
Высокоскоростная обработка, избегающая тирании углов
Освоив радиальное утонение стружки как усовершенствованную подачу и скорость, вам предстоит решить еще одну задачу, прежде чем вы сможете должным образом освоить методы HSM. Это включает в себя борьбу с Тираниями Угла. Каждый раз, когда ваш резак перемещается от резки по прямой линии к изменению направления в углу, силы резания и зацепление резца возрастают. Это довольно легко увидеть из диаграммы:
Ввод угла увеличивает вдвое зацепление фрезы…
Стрелка показывает направление реза справа налево в угол.На диаграмме показано около 50% радиального зацепления. Как видите, перемещение в угол удваивает угол зацепления инструмента примерно с 90 до 180 градусов. Когда это происходит, силы резца удваиваются, способность очищать стружку уменьшается вдвое, а время, в течение которого канавка находится в воздухе, где она может выделять тепло, также уменьшается вдвое. Это действительно очень сложно для фрезы, и удар от нее возникает очень внезапно, так как фрезу не нужно далеко двигаться, чтобы полностью врезаться в угол.
Практический результат всего этого заключается в том, что рекомендуемые производителем подачи и скорости для инструмента основаны на необходимости сохранения некоторого запаса прочности для углов – довольно большого запаса прочности, исходя из того, что мы видим.В G-Wizard есть калькулятор угла зацепления инструмента, который позволяет вам поиграть с расчетом углов зацепления инструмента на основе описания угла, инструмента и желаемого реза. Вот снимок экрана оценщика:
Калькулятор угла захвата инструмента G-Wizard
В этом случае мы показываем концевую фрезу 1/2 дюйма, которая делает рез с радиальным зацеплением 10% в кармане с углами 90 градусов. Мы видим, что как только фреза попадает в угол, угол зацепления инструмента, который представляет собой количество градусов окружности фрезы, участвующей в резании, достигает пика в 126 градусов.Для сравнения, прорезь – это угол зацепления 180 градусов, и это примерно так плохо, как вы можете (ну, врезание составляет 360 градусов!).
Долгое время мир ЧПУ имел дело только с Тираниями Углов. Была проделана некоторая работа по изменению скорости подачи, чтобы замедлить фрезу, когда она заходила в угол, но сделать это очень сложно. Включение в поворот происходит так быстро, что замедление должно продолжаться задолго до поворота. Это мешает повысить производительность за счет более быстрой работы фрезы по прямой.Что, если бы мы могли придумать стратегию траектории инструмента, которая гарантировала бы, что резец никогда не должен входить в угол таким образом?
Эта стратегия траектории поддерживает постоянный угол зацепления резца, что является сутью траекторий высокоскоростной обработки. Добро пожаловать в новый мир высокопроизводительной высокоскоростной обработки!
Насколько помогает избегание этих углов?
Возвращаясь к нашему примеру из приведенного выше снимка экрана, углы 90 градусов означают TEA (углы захвата инструмента) до 126 градусов.Несмотря на то, что у нас такой неглубокий срез (10% диаметра), это очень важно. Но если мы режем по прямой линии без углов, этот TEA опускается до 36 градусов. Вау, представьте, насколько быстрее мы сможем управлять фрезой, если будем знать, что угол зацепления никогда не превысит 36 градусов? Если бы дело было только в соотношении TEA (это не так!), Мы могли бы двигаться по траектории в 3,5 раза быстрее.
Итак, как мы можем этого добиться?
Траектории трохоидального фрезерования и снятия или резки углов
Некоторые из самых ранних попыток включают траектории так называемого трохоидального фрезерования и углового отслаивания (или нарезки).Начнем с пилинга. Представьте себе такой угол:
Дуги траектории для зачистки угла…
Предположим, что когда фреза движется в угол, она отклоняется по серии дуг, а не врезается глубоко в угол. Каждая дуга «отслаивает» другой слой, а глубина резания дуг регулируется, чтобы соответствовать уменьшенным силам резания, чтобы мы могли пройти через отслаивание на полной скорости. Вы видите, как Corner Peeling может помочь вам пройти этот угол быстрее, чем просто вспахивание резаком?
Трохоидальное фрезерование аналогично концепции.Возьмем, к примеру, слот, который очень требователен к сокращению и заставляет нас замедляться. Предположим, у нас есть фреза, диаметр которой составляет 1/2 ширины паза. Теперь у нас есть место для работы. Давайте относиться к этому так же, как к отшелушиванию углов, и выполним серию петлевых движений, которые срезают небольшие кусочки паза, а не просто копают прямо с помощью большого резака. Это трохоидальное фрезерование, разновидность высокоскоростной обработки.
Вот пример того, как это выглядит для нашего слота:
Трохоидальное фрезерование паза…
Есть несколько вариантов, например, используем ли мы полные круглые петли или делаем сторону втягивания короче, делая маленькие буквы D.Выбор последнего зависит от способностей вашей машины к ускорению. D требует более быстрой и жесткой машины, в то время как петли могут быть немного более щадящими для более медленных машин.
Дело в том, что эти виды резов могут приводить инструмент в движение настолько быстро, что они могут побить большой резак при съеме материала, особенно если у вас нет большой тяжелой машины с большой мощностью, чтобы поддержать большую измельчитель.
Каков следующий уровень доработки этой идеи?
Траектории с постоянным углом захвата инструмента для HSM
Трохоидальное фрезерование и пилинг углов – особые случаи.Трохоиды созданы для работы с узкими щелевидными карманами, и, конечно же, Corner Peeling предназначена для углов. Первоначально мир CAM хотел решить HSM, взяв те траектории, с которых они начали, и используя такие методы для устранения их слабых мест. Но вскоре люди начали думать о траекториях, которые никогда не создают углов, потому что они полагались на совершенно новые стратегии. Это траектории с постоянным углом захвата инструмента, которые выпускаются под многими торговыми марками, такими как Volumill, Dynamic Milling или Adaptive Clearing.Все они создают сложные циклические траектории, где резец отклоняется от чрезмерного зацепления в самый последний момент.
Вот сравнение типичных HSM и традиционных траекторий для одного и того же кармана, выполненного в GibbsCAM:
Сравнение того же кармана, выполненного с помощью HSM и традиционных траекторий инструмента в GibbsCAM, как показано в GWE CNC Simulator…
Как видите, на обычной траектории наверняка есть много острых углов. Неудивительно, что HSM может быть намного быстрее!
Подачи и скорости высокоскоростной обработки
Вопрос в том, насколько быстрее может быть HSM? Фактически, какие типы подачи и скорости мне следует использовать с HSM?
Долгое время для подачи и скорости не было особой помощи.Поставщики CAM публиковали различные отчеты о том, как быстро заказчики резали, но связать такие анекдоты с вашей собственной обработкой проблематично. По крайней мере, вы не знаете, являются ли эти цифры базовыми или настроенными вручную числами, разработанными для изготовления конкретной детали с большим количеством проб и ошибок. Если это последнее, они, скорее всего, выйдут из строя, если вы подключите их к другой детали на другом станке с немного другим алгоритмом траектории HSM и так далее.
HSM – это не то, что вы можете легко понять с помощью нескольких таблиц.К счастью, для этого есть математические методы. В конце концов, HSM – это просто физика, и там, где есть физика, следует некоторая степень предсказуемости. Хитрость заключается в том, чтобы проанализировать угол зацепления инструмента, используемый для конкретного реза (который можно вычислить с помощью калькулятора HSM на основе ширины реза), и использовать эту информацию вместе со знанием того, как рассчитать обычные скорости и подачи для «обратного хода». консерватизм применяется к обычным подачам и скоростям из-за углов. Следует учитывать два основных эффекта: зазор стружки и нагрев инструмента.Низкие значения TEA дают инструменту большую часть круга вращения, в которой он охлаждается на воздухе или под воздействием охлаждающей жидкости.
G-Wizard имеет встроенный калькулятор HSM:
HSM, вырезанный из алюминия 6061…
Показанный пример резания представляет собой концевую фрезу 1/2 дюйма из алюминия 6061, радиальное зацепление 10%, о чем мы говорили, и полная глубина резания 1 дюйм. Благодаря траектории инструмента HSM, которая гарантирует, что углы не будут обрезаны, мы можем работать со скоростью 6747 об / мин при скорости подачи 125,8 дюймов / мин.Это сокращение на 1,2 л.с. Без HSM (снимите флажок HSM в строке «Cut») скорость резки снижается до 4272 об / мин при 34,89 дюймов / мин для резки с мощностью всего 0,3 л.с.
Скорость съема материала HSM примерно в 5 раз выше, чем у HSM. Вам не нужно много думать, чтобы понять, почему эти траектории HSM стали почти незаменимыми для многих магазинов.
Вы также можете использовать G-Wizard для подачи и ускорения этих трохоидальных фрезерных прорезей, и мы написали сообщение в блоге, чтобы рассказать вам, как именно.
Компромисс между стойкостью инструмента и производительностью при высокоскоростной обработке
Недавно я получил записку от клиента G-Wizard, который интересовался некоторыми проблемами износа инструмента, которые он видел. У него было две траектории: одна – HSM (высокоскоростная обработка), а другая – обычная. Он резал горячекатаную сталь твердосплавной концевой фрезой длиной 1/2 дюйма и делал множество небольших карманов глубиной чуть более 1/2 дюйма. Окалина на горячекатаном листе может быть жесткой на резцах, поэтому он решил сначала удалить ее.Его вопрос касался стойкости инструмента после прохода, выполненного другой фрезой.
Резка HSM была сделана путем предварительного просверливания входа и последующей скорости вращения 2800 об / мин, нагрузки стружки 0,005 дюйма и снижения на 0,185 дюйма за шаг. Степень была 65%. Обычная резка производилась с входом с линейным наклоном контура и постоянным шагом 0,045, при гораздо более высокой нагрузке на стружку 0,014 дюйма и более высоких оборотах 4500 об / мин. Срок службы инструмента был намного лучше по сравнению с обычным, поэтому его вопрос был в основном: «Почему чудо-траектория HSM не оказалась лучше?»
Это очень интересный случай, потому что он действительно дает понять, в чем заключаются преимущества траекторий HSM по сравнению с обычными траекториями.Вот мой ответ ему:
Все дело в ступенчатом или радиальном зацеплении.
В высокоскоростной версии вы работаете с шагом 65%. В версии без HSM вы используете шаг перехода 0,045 / 0,500 = 9%.
Итак, нужно учитывать две вещи.
Во-первых, единственное различие между HSM и не-HSM траекторией состоит в том, что HSM играет уловки, чтобы избежать радикального увеличения зацепления фрезы в углах. Для квадратных углов и 50% уклона вы переходите от 90 градусов к 180 градусов в углу, поэтому резак работает в два раза сильнее в углу.Таким образом, путь HSM не должен работать в поворотах так же интенсивно, как ваш путь нарастания, но у него нет других особых преимуществ в результате использования пути HSM.
Это подводит меня ко второму пункту.
С помощью G-Wizard мы можем преобразовывать шаги шага в углы захвата инструмента. Итак, 65% уклон, если мы все это введем, окажется 107 градусов. Это немного лучше, чем корпус на 180 градусов, но не намного.
Калькулятор угла захвата инструмента G-Wizard
Если бы шаг на 9% был выполнен с траекторией HSM, это было бы 34 градуса, что действительно начинает готовить с огнем.
Причина, по которой этот угол зацепления так важен, связана с двумя факторами: зазором стружки и способностью инструмента остывать. Когда мы начинаем думать об этих углах, довольно легко понять, почему они важны. Если канавки инструмента закрыты только на 34 градуса из 360 полного вращения, они довольно широко открыты. Стружку легко убрать, а канавки имеют много времени на воздухе и охлаждающей жидкости для охлаждения во время вращения. При 107 градусах времени намного меньше.Мы переходим от только обрезки около 9% оборота к 30%. Резак работает как минимум в 3 раза больше.
Итак, давайте соберем все это вместе. Если бы мы работали только по прямой линии, каждая траектория была бы траекторией HSM – не о каких углах беспокоиться. Кроме того, из двух использованных вами резов ступенчатая резка 0,045 дюйма выполняется резаком в 3 раза легче. При прочих равных условиях он может работать в 3 раза быстрее по скорости подачи или может иметь в 3 раза большую стойкость инструмента при той же скорости и т. Д. Это излишние упрощения, но вы поняли идею.
В этом случае переход на траекторию HSM был настолько близок к не-HSM в квадратно-угловом кармане (например, зацепление 107 градусов против 180 градусов), что вы не получили большого преимущества от пути HSM для инструмента жизнь.
FWIW, хороший начальный шаг для HSM для увеличения стойкости инструмента – 15%.
Но здесь есть более крупный вопрос:
При измерении стойкости инструмента по времени упускается из виду производительность. Стойкость инструмента следует измерять в кубических дюймах удаленного материала.
Верно? Мы используем инструмент для удаления материала.Если он удаляет намного больше материала в течение срока службы инструмента, чем какой-либо другой сценарий, но инструмент не прослужит столько минут, тем лучше. Это означает, что инструмент снимает больше материала и делает это намного быстрее . Что может быть лучше?
Я уже упоминал об этом ранее, но для производства вы хотите оптимизировать скорость съема материала на траектории HSM. Функция CADCAM Wizard в G-Wizard отлично справляется с этой задачей.
G-Wizard оптимизирует эти компромиссы для вас!
Вот то, что не умеет ни один другой калькулятор каналов и скорости:
G-Wizard автоматически рассмотрит сотни сценариев, чтобы найти оптимальную комбинацию глубины реза и ширины реза, которая максимизирует ваши кубические дюймы удаляемого материала при сохранении срока службы инструмента.
Вау! Представьте, что это может сделать для продуктивности вашего магазина.
Вот видео-демонстрация CADCAM Wizards от G-Wizard, функции, которая делает этот ловкий трюк:
.
Рекомендации по использованию инструмента для высокоскоростной резки
Скорость съема металла сегодня выше, чем когда-либо. То, что считалось высокоскоростной обработкой всего несколько лет назад, сегодня считается обычным делом. Многие факторы подталкивают цеха к более высокой скорости резки металла. К ним относятся лучшие и более производительные станки и процессоры с ЧПУ, которые позволяют станку выполнять точную резку на все более высоких скоростях и подачах.
Коммерческие соображения также подталкивают магазины к более высокой производительности.Потребность в увеличении нагрузки на станки заставляет предприятия постоянно совершенствовать процессы металлообработки.
В то время как большая часть дискуссий о высокоскоростной обработке имеет тенденцию сосредотачиваться на роли станка, фреза является его партнером в высокоскоростной обработке. И этому посвящена данная статья. Мы собираемся посмотреть, что нужно знать магазину о выборе режущих инструментов для их высокоскоростных приложений.
Чтобы получить представление об инструментах для высокоскоростной обработки, мы связались с Kennametal (Роли, Северная Каролина), чтобы обсудить высокоскоростной режущий инструмент.
Что считается высокоскоростной резкой?
Общее определение высокоскоростной обработки неуловимо. Высокая скорость относительна. То, что очень быстро для одного сегмента отрасли, кажется ледяным для другого.
Скорость обработки очень зависит от области применения. Вызов высокой скорости процесса обработки приводит к сравнению его текущей и предыдущей производительности. Например, высокая скорость может означать переход с инструмента из быстрорежущей стали на твердосплавный, что позволяет увеличить подачу и скорость станка.Поскольку твердосплавные фрезы во многих сферах применения могут удалять металл быстрее, чем HSS, цех, использующий твердосплавные инструменты, обрабатывает их быстрее по сравнению с HSS. Но это относительно, потому что другой цех, использующий металлокерамические или керамические фрезы, может резать быстрее, чем карбид.
Итак, мы не собираемся давать окончательное значение высокой скорости. Достаточно сказать, что высокоскоростная обработка означает более быструю резку металла, что является обычным для вашей работы.
Некоторые основы: SFM и IPT
Невозможно определить, как высокоскоростная обработка, но существуют измерения, используемые для скорости обработки.Это позволяет сравнивать разные скорости обработки и помогает цеху определить свое место в континууме скорости обработки.
Чтобы количественно оценить, насколько быстро станок на самом деле режет металл, необходимо преобразовать число оборотов шпинделя в более полезное. По словам Дэна Спановича, специалиста по применению Kennametal, эта цифра выражается в поверхностных футах в минуту (sfm).
Аналогичным образом, скорость подачи для станка обычно измеряется в дюймах в минуту (ipm). Но для режущих инструментов он выражается в дюймах на зуб (ipt).Используя оптимальные значения sfm и ipt для материала заготовки, можно определить и запрограммировать частоту вращения станка и ipm.
Эти два измерения зависят друг от друга и определяют скорость, с которой можно поддерживать деталь. Например, титан можно эффективно резать со скоростью около 250 футов в минуту. Это при загрузке микросхемы 0,005 ipt. Тем не менее, некоторые цеха сообщают, что обрабатывают титан со скоростью около 500 футов в минуту, но для этого требуется меньшая нагрузка на стружку.
В зависимости от материала фрезы можно регулировать нагрузку на стружку и скорость резания, чтобы обеспечить наилучшее сочетание для применения в цехе.Если целью является удаление тяжелых металлов, увеличение нагрузки на стружку и sfm максимизирует эффективность резки. Для лучшей отделки, уменьшение нагрузки стружки при сохранении sfm на высоком уровне даст хорошее качество поверхности.
Нет конкретных формул для определения лучших комбинаций и результатов. Чтобы найти оптимальную подачу и скорость для конкретного применения, нужно немного поэкспериментировать.
Различия в материалах
Материал режущего инструмента имеет определенные атрибуты, которые позволяют использовать его в металлообрабатывающей промышленности.Поскольку области применения сильно различаются, существует множество комбинаций режущих материалов, из которых можно выбирать.
Но, как правило, для определения применимости резака используются только два критерия эффективности. Это вязкость или сопротивление разрушению (пластичность) и термическая твердость (устойчивость к нагреванию). Можно создать множество комбинаций покрытий, подложек и основных материалов, чтобы обеспечить определенные пропорции ударной вязкости и термической твердости, подходящие для различных областей применения.
Материалы для режущего инструмента можно разделить на пять основных категорий.Материалы расположены от лучших характеристик ударной вязкости до наилучшей термической твердости:
- HSS,
- Карбид вольфрама (без покрытия и с покрытием),
- Кермет,
- керамика и
- Алмаз и CBN.
Начиная с HSS и переходя к покрытиям из алмаза и CBN, можно постепенно увеличивать шкалу от лучших характеристик ударной вязкости до наилучшей термической твердости. Быстрорежущие стали терпят удары, но не выдерживают большого количества тепла.Керамика и фрезы с алмазным покрытием выдерживают тепло, но легко ломаются.
По словам г-на Спановича, фрезы из карбида вольфрама обычно имеют рабочий диапазон от 100 до 1200 квадратных футов в минуту (HSS достигает примерно 100 футов в минуту). Керамика, в том числе нитрид кремния, увеличивает диапазон до 4000 квадратных футов в минуту. Инструменты с поликристаллическим алмазом и покрытием CBN увеличивают стандартную погрешность до 4000 единиц. Эти скорости приведены при загрузке чипа от 0,003 до 0,030 ipt.
Эти скорости представляют собой оптимальный потенциал резания при правильном сочетании материала заготовки и материала резца.Однако есть и другие факторы, которые необходимо учитывать, прежде чем цех сможет приблизиться к таким скоростям резания.
Инструмент для высокоскоростной обработки
Невозможно переоценить важность жесткого крепления при высокоскоростной обработке. В то время как цель любого крепления или зажимной установки – надежно удерживать заготовку и обеспечивать повторяемое расположение последующих деталей, требования к высокой скорости усиливают любые недостатки в установке заготовки.
При высокоскоростной обработке зажимное приспособление должно поддерживать заготовку на твердом основании и иметь достаточную массу, чтобы гасить вибрации, вызываемые резцом.Приспособления для высоких скоростей не обязательно должны быть слишком сложными, но должны соответствовать хорошей производственной практике.
Например, хороших тисков достаточно, если они надежно поддерживают заготовку. Рекомендуется использовать положительные упоры для предотвращения закручивания или перемещения заготовки в ответ на движение фрезы.
Сила с тобой
Правильный выбор режущего инструмента, особенно режущего инструмента со сменными пластинами, рассчитанного на вращение с повышенной скоростью, очень важен. Чтобы не придавать этому большого значения, но мы говорим о потенциально серьезных или даже смертельных авариях, если магазин попытается превысить номинальные скорости инструмента.
Причина – простая центробежная сила. По той же причине, по которой производители шин устанавливают рейтинги скорости для радиальных колес, производители инструмента устанавливают для резцов “не превышать” число оборотов в минуту. Сила, создаваемая вращением тела, экспоненциально зависит от скорости вращения. Эта сила пытается оторвать вставки от их мест. Любая часть фрезы, вылетающая на скорости 10 000, 15 000 или 20 000 об / мин, представляет опасность для жизни и здоровья.
Инструменты со сменными пластинами для высоких оборотов отличаются от инструментов для обычных скоростей вращения.Пластины по-разному крепятся к корпусу фрезы для высокоскоростных сменных инструментов. По словам г-на Спановича, простой зажим с установочным винтом не подходит для большого вращения. Пластины крепятся к корпусу фрезы штифтом, который вставляется в фиксатор, отформованный во вставке. Он закреплен на корпусе фрезы в направлении, перпендикулярном центробежным силам, возникающим при вращении.
Сухая резка
При повышенных скоростях резания и подаче СОЖ может потребоваться меньше, чем при обычных скоростях.Тепло – это побочный продукт механической обработки. Вообще-то это враг металлистов. Однако все чаще для облегчения процесса резки используется тепло.
При идеальном резании материал заготовки, подачи станка, скорости шпинделя и фрезы – все это вносит свой вклад оптимальным образом. Когда фреза образует стружку, тепло, выделяемое этим действием, передается стружке. Когда стружка ломается и покидает зону резания, тепло уносится вместе с ней.
Большим преимуществом высокоскоростной обработки является то, что при повышенных скоростях и подаче стружка режется и удаляется так быстро, что имеет тенденцию передавать мало тепла или не передавать его совсем.При обычных скоростях обработки у тепла есть время, чтобы перейти от стружки к неразрезанному металлу и создать условия деформационного упрочнения. Это увеличивает силу, необходимую для создания чипа, который создает больше тепла, и он идет дальше. Охлаждающая жидкость смягчает цикл, снижая температуру в зоне резания и смывая стружку.
Но при очень высоких оборотах вращение инструмента выбрасывает охлаждающую жидкость из зоны резания, поэтому без очень высокого давления или протяжки через инструмент она никогда не достигает зоны резания.«В некоторых случаях, – говорит г-н Спанович, – застрявшая стружка может оставаться в резе, что позволяет повторно разрезать ее инструментом. Мы обнаружили, что воздушный поток очень эффективен для удаления стружки при высоких скоростях».
Термический удар – еще один фактор, который следует учитывать пользователям высокоскоростных инструментов, особенно керамических и более твердых режущих кромок. Неравномерное распределение охлаждающей жидкости в резе может создать для этих фрез нестабильную зону нагрева. Разработанный для работы при повышенных температурах, режущий материал может подвергаться последовательным циклам нагрева и охлаждения в зоне резания, что может привести к преждевременному выходу из строя в результате теплового удара.
Прямой угол
Скорость резца является основным фактором нагрева режущей кромки инструмента. Поддержание высокой загрузки стружки или подачи – вот способ отвода тепла. Правильный IPT в сочетании с правильным передним углом резца для обрабатываемого материала дает стружку достаточной плотности для отвода тепла от зоны резания, что позволяет избежать наклепа.
Загрузка стружки – это скорость подачи для каждой режущей кромки инструмента. Для инструментов со сменными пластинами это нагрузка на каждую пластину.У фрез с твердым корпусом нагрузка стружки рассчитывается на каждый зуб. По словам г-на Спановича, хороший рабочий диапазон загрузки микросхемы обычно составляет от минимум 0,003 IPT до максимум 0,012 IPT.
Угол атаки режущей кромки, ее передний угол, влияет на нагрузку стружки на фрезу. Углы наклона варьируются от положительного и нейтрального до отрицательного. Положительный передний угол обеспечивает более острый край заготовки. Это также более слабое преимущество. Инструменты с положительным передним углом притягивают заготовку к себе во время резки.Они также имеют тенденцию выталкивать стружку вверх и от зоны резания.
Инструменты с отрицательным передним краем имеют гораздо более прочную переднюю кромку и имеют тенденцию давить на заготовку в направлении подачи резца. Эта геометрия менее свободна для резки, чем положительные грабли, и поэтому для резки требуется больше лошадиных сил.
Геометрия высокоскоростного инструмента в целом отражает геометрию традиционной обработки. «Все, что вы знаете о геометрии инструмента для традиционной обработки, переносится на высокоскоростные приложения», – говорит г-н.Спанович. «Если есть тенденция к высокой скорости, то это к инструменту с положительным углом опережения. Этот эффект угла опережения позволяет увеличить ipt за счет подъема стружки при сохранении той же толщины стружки. Эта большая скорость подачи приводит к более высокой скорости обработки.
«Целью является формирование достаточно толстой стружки», – говорит г-н Спанович. «Идея состоит в том, чтобы использовать стружку в качестве теплоотвода. При высоких скоростях выделяется больше тепла, поэтому направление тепла на стружку становится критически важным при высокоскоростной обработке.«
Часы Wobble
Успешная высокоскоростная обработка зависит от статической и динамической жесткости многих компонентов, которые объединяют инструмент и заготовку. Решающим фактором здесь является очень жесткое соединение между инструментом, державкой и шпинделем станка.
Баланс инструмента становится большой проблемой при высоких скоростях шпинделя. «Мы рекомендуем инструменты с гладким хвостовиком для концевых фрез и сверл, которые удерживаются гидравлическим или цанговым патроном с роликовым фиксатором для высоких скоростей», – говорит г-н.Спанович. «Баланс становится проблемой при 5000 об / мин и выше. На этих скоростях хвостовик с надрезом и установочным винтом может сдвинуть инструмент достаточно далеко от центра, чтобы вызвать вибрацию – следовательно, дребезжание». Для скоростей 20 000 об / мин и выше рекомендуется индивидуальный баланс инструмента и комбинации резцедержателя.
Коническое соединение с V-образным фланцем является потенциальным источником высокоскоростной вибрации. До недавнего времени конус с V-образным фланцем и измерительные приборы, используемые производителями режущего инструмента, соответствовали стандартам ANSI / ASME B5.10.«До появления высокоскоростных приложений стандарт ANSI / ASME работал хорошо, – говорит Дэвид Льюис, штатный инженер Kennametal и вице-председатель комитета по стандартизации ANSI / ASME B5.
Посадка конуса между корпусом инструмента и шпинделем станка может иметь допуск (согласно ANSI / ASME B5.10) и по-прежнему вызывать проблемы с биением и эксцентриситетом для высокоскоростной фрезы. Г-н Льюис и другие, представляющие американских производителей инструмента, рекомендуют применять европейский стандарт ISO 1947 AT3 вместо ANSI / ASME B5.10. Стандарт ISO требует вдвое большей точности, чем ANSI / ASME, и обеспечивает лучшее соединение между конусом шпинделя и инструментом с V-образным фланцем. Чтобы убедиться, что инструмент, который вы приобретаете для высокоскоростного применения, соответствует новым стандартам, укажите ISO 1947 AT3 или эквивалентный от вашего производителя инструмента для державок и цанговых патронов. Для шпинделей станков укажите ISO 1947 AT2 (меньшее число AT означает лучшее соответствие). Г-н Льюис рекомендует приобрести калибр для проверки конуса шпинделя и инструмента в мастерской.
Несколько слов о HSK
Много было написано о HSK или аналогичных инструментах в качестве возможной замены V-образного фланцевого соединения при обработке. «Хотя концепция дизайна имеет некоторые преимущества, – говорит г-н Льюис, – ее широкое применение частично сдерживается отсутствием производственных стандартов».
Основное различие между HSK и другими державками с полым хвостовиком и коротким конусом заключается в том, как инструмент входит в шпиндель станка. HSK использует одновременную посадку между коротким конусом и торцом шпинделя.Связь очень жесткая.
«Проблема с HSK, – говорит г-н Льюис, – это не руководящий орган, который установил стандарт для производства инструментальных средств. Существует немецкий стандарт DIN, который рассматривается ISO, но до сих пор не утвержден. также некоторые проблемы для HSK из Японии, других европейских стран и США. Вопрос о том, как будет выглядеть HSK, еще не решен.
«В то же время цехам, которые хотят проводить высокоскоростную обработку на своих обрабатывающих центрах, может быть лучше выбрать инструмент с V-образным фланцем AT3 или лучше, чем ждать стандартной конфигурации инструмента HSK», – говорит г-н.Льюис. Возможно, пройдет некоторое время, прежде чем появится HSK или аналогичный стандарт для инструментов, шпинделей и манометров.
Почему более высокая скорость?
Внедрение высокоскоростной обработки в цехе имеет много преимуществ, некоторые из которых очевидны, а другие менее очевидны. Очевидно, что более быстрое изготовление деталей помогает удовлетворить потребности клиентов в более быстрой доставке, несмотря на более короткие сроки выполнения заказа. Есть также преимущества, связанные с увеличением стойкости инструмента. Это может показаться парадоксальным, но обработка на высокой скорости с использованием подходящего инструмента, соответствующего области применения, может снизить износ инструмента из-за уменьшения сил резания на высокой скорости.
Высокоскоростная обработка может помочь цеху производить более точные детали с лучшей обработкой поверхности. Часто из-за того, что станок и установка детали должны быть очень жесткими для высокоскоростной обработки, в результате получаются более стабильные детали.
Менее очевидное преимущество высокоскоростной обработки для цехов, движущихся в этом направлении, связано с ее реализацией. Обучение тому, что необходимо для успешной высокоскоростной обработки, может одновременно поднять другие аспекты предприятия до эквивалентного уровня производительности.
.