Чугун формула: 2Fe + 3CO2 – это формула чугуна? если нет, то напишите правильно — Спрашивалка
alexxlab | 19.07.2023 | 0 | Разное
Жидкотекучесть чугуна
Жидкотекучесть чугуна
Высокая жидкотекучесть чугуна, как показали современные исследования, определяют не только его способность заполнять форму и воспроизводить самые тонкие ее очертания, но также, способствует хорошему питанию отливок и беспрепятственному удалению газов из металла, что уменьшает опасность получения пороков (усадочных и газовых раковин, пористости, горячих трещин и т. д.).
Экспериментально жидкотекучесть определяется измерением пути, проходимого металлом в форме (рис. 77). Аналитическое определение жидкотекучести очень сложно, так как оно зависит от многих факторов: физических свойств металла, условий теплопередачи, конструкции отливки, технологии форм и т. д. Поэтому формулы, предложенные для определения жидкотекучести, имеют приближенный и качественный характер. Например, формула Ю. А. Нехендзи в несколько измененном виде представляется следующим образом:
(73)
Где v – средняя скорость движения металла в форме, t м/сек; τ – время течения; R – приведенная толщина отливки или пробы на жидкотекучесть.
Рис. 77. Пробы на жидкотекучесть.
а – спираль; б – проба; в – брусок; г – гребешок; д – пластины.
d – уд. вес металла, г/см3; k – коэффициент теплоотдачи, кал/см/сек °С; с – теплоемкость металла, кал/2 °С; tж – t0 – перегрев над температурой нулевой текучести; m – относительное количество твердой фазы, при котором наступает нулевая текучесть; I – скрытая теплота кристаллизации, кал/г; tм – tф – переменная разность температур между металлом и формой;
k и k1 – коэффициенты пропорциональности.
Согласно этой формуле, жидкотекучесть чугуна (X) тем выше, чем больше скорость движения металла в форме (v)1, чем больше его теплосодержание по отношению к температуре нулевой текучести (dc(t – t0) + dmL), чем больше приведенная толщина отливки (R) и тем меньше интенсивность отвода тепла через форму (α (t м – tф). При этом главную роль играет период движения металла в форме до достижения температуры ликвидуса. Жидкотекучесть же в периоде кристаллизации имеет относительно небольшое значение, в особенности при высоких температурах заливки и нормальном давлении.
Как видно из формулы (73), жидкотекучесть определяется в основном условиями теплообмена между металлами и формой. Изменение физических свойств жидкого чугуна, его вязкости и поверхностного натяжения, оказывает значительно меньшее влияние на жидкотекучесть, чем условия теплопередачи. Динамическая вязкость чугуна, как и большинства других металлов, сравнительно мало отличается от вязкости воды, но значительно отличается от вязкости шлаков:
Это приводит к соответствующему увеличению числа (критерия) Peйнольдса:
Re = v/у = 4 R v/у (74)
где v – средняя скорость движения металла в канале; у – коэффициент кинематической вязкости; D – диаметр круглого канала или, в общем виде, учетверенный гидравлический радиус (4R)1.
С увеличением числа Рейнольдса связано уменьшение потерь при движении металла. Таким образом, уменьшение коэффициентов вязкости увеличивает, при прочих равных условиях, число Рейнольдса и повышает жидкотекучесть чугуна. Однако это в полной мере справедливо, главным образом, для ламинарного потока, который практически никогда но осуществляется при движении чугуна в форме.
Действительно, ламинарный поток, как известно возможен при Re < Reкp .Принимая для чугуна, как и для других жидкостей Reкр равным 2360, определим критическую скорость движения чугуна в форме:
(75)
Рис. 78. Вязкость серого (сплошные линии) и белого (пунктирные линии) чугунов.Легко подсчитать, что даже в самых тонкостенных отливках при R = 0,125 см (толщина стенки 2.5 мм) критическая скорость движения составляет только 13,5 – 27,0 см/сек, что значительно меньше обычной фактической скорости.
Рис. 78. Вязкость серого ( сплошные линии) и белого (пунктирные линии) чугунов.
При турбулентном же движении зависимость потерь от числа Рейнольдса выражается в сравнительно небольшой степени. Поэтому изменение вязкости чугуна оказывает па жидкотекучесть ограниченное влияние.
Величина коэффициентов вязкости зависит от многих факторов и прежде всего, конечно, от температуры и состава жидкого чугуна. Как покапывают литературные данные (рис. 78), вязкости чугуна уменьшается с повышением температуры и содержания углерода, причем у серого чугуна она больше, чем у белого. Это объясняется большим количеством субмикроскопических включений графита в сером чугуне и подтверждается тем, что при выдержке жидкого чугуна. При постоянной температуре скорость его уменьшается (графит переходит в раствор). По этой причине модифицирование чугуна путем присадки ферросилиции увеличивает вязкость.
Рис. 79. Влияние углерода, кремнии, марганца, серы и фосфора на относительную вязкость жидкого чугуна.
а – при постоянном перегреве; б – при постоянной температуре.
Выдержка жидкого чугуна после модифицирования, наоборот, способствует удалению или растворению включений и уменьшает вязкость. Влияние элементов на вязкость чугуна изучено в очень малой степени. Имеющиеся литературные данные показывают, что кремний, марганец и фосфор уменьшают вязкость чугуна, если вести испытание при одинаковом перегреве над ликвидусом (рис. 79, а). Тем более, конечно, и еще резче уменьшается вязкость е повышением концентрации этих элементов, если делать сравнение при постоянной температуре рис. 79, так как при этом понижается температура ликвидуса и, следовательно, повышается относительный перегрев над ликвидусом. Сера наоборот, повышает вязкость чугуна. Что касается поверхностного натяжения жидкого чугуна, то оно сравнительно велико и согласно И. Л. Кукину н Ю. Л, Клячко, Зауэрвальду и др. повышается с температурой (по крайней мере в исследованном интервале:
При уменьшении содержания углерода до 2.2% поверхностное натяжение чугуна увеличилось до 1500 при 1420°. Таким образом, уменьшение содержания углерода, связанное с повышением температуры плавления чугуна, увеличивает его поверхностное натяжение.
h = 2τ/rd = 2×1/r × 6.9 = 0.3/r (76)
где r – радиус канала; d – уд. вес жидкого чугуна, принятый равным 6,9 г/см3, τ – поверхностное натяжение, принятое равным 1000 дин/см ~ 1 г/см. Для обычных толщин отливок добавочный напор не играет, следовательно, значительной роля, и только при заполнении острых граней или углов высокое поверхностное натяжение может представить большое препятствие. Существенное влияние в этом отношении может оказать сманивание мета ялом стенок формы и стержней, что определяется силами взаимодействия между чугуном и формовочной смесью.
Таким образом, влияние поверхностного натяжения на жидкотекучесть чугуна весьма ограничено. Гораздо большее значение имеют оксидные пленки или включения в чугуне, представляющие уже серьезные препятствия для течения металла.
а) Влияние температуры заливки. С повышением температуры заливки увеличиваются теплосодержание, а следовательно, и жидкотекучесть чугуна. Влияние этого фактора настолько велико, что температура заливки является главной переменной, изменением которой достигается необходимая жидкотекучесть чугуна для заполнения разных форм.
В среднем можно принять, что при повышении температуры заливка на 10°, длина спирали сечением 50 мм увеличивается на 4 см. Такая зависимость между жидкотекучестью и температурой подтверждается большинством исследований. При этом в некоторых случаях, как то впервые показал Ю. А. Нехеидзи, обнаруживается закономерная тенденция к уменьшению влияния температуры по мере увеличения перегрева (рис. 80, кривая 2).
С уменьшением температуры заливки жидкотекучесть падает. Это особенно заметно при понижении температуры ниже ликвидуса вследствие выделения твердой фазы в интервале кристаллизации. По той же причине падает жидкотекучесть чугуна при температурах, близких к ликвидусу, в результате образования зародышей на основе колебания плотности и температур в жидком чугуне.
Рис. 80. Влияние температуры заливки на жудкотекучесгь чугуна.
1 – Гиршович; 2 – Нехеидзи и Хахалин; 3 – Циглер; 4 – Эндрю.
б) Влияние состава чугуна. Исследования А. А. Бочвара и др. ясно доказали связь между жидкотекучестью сплава и его положением на диаграмме состояния. Максимальная жидкотекучесть чугуна при постоянном перегреве над ликвидусом (истинная жидкотекучесть по терминологии Ю, А. Нехендзи) соответствует эвтектическому составу. Такая зависимость объясняется характером первичной кристаллизации. Чугун с большим интервалом затвердевания склонен к более развитой дендритной кристаллизации. Образующиеся на стенках
канала и внутри движущейся струи чугуна первичного аустенита уменьшают жидкотекучесть металла.
Кроме того, они способствуют более интенсивному теплоотводу. Поэтому достаточно уже 10 – 20% твердой фазы, чтобы течение чугуна стало невозможным, в то время как в эвтектическом чугуне значение коэффициента т в формуле (73) достигает 30%. В связи с этим малоуглеродистый чугун, располагающийся близко к границе между сталью и чугуном (около 2,0% С), характеризуется минимальной истинной жидкотекучестью. Наоборот, эвтектический чугун отличается наибольшей истинной жидкотекучестью. Тем более, следовательно, велика так называемая практическая жидкотекучесть эвтектического чугуна (жидкотекучесть при постоянной температуре), так как с приближением к эвтектическому составу температура ликвидуса понижается и относительный перегрев над ликвидусом увеличивается.
Рис. 81. Влияние углерода, кремния, фосфора и марганца на практическую жидкотекучесть чугуна.
Как видно из рис. 81, не все эвтектические чугуны характеризуются одинаковые жидкотекучестью. Например, с увеличением содержания кремния в эвтектических чугунах жидкотекучести падает, а с увеличением содержания фосфора переходит через минимум, соответствующий составу 4% и 1% р. Поэтому для получения наибольшей жидкотекучести кажется целесообразным пользоваться эвтектическим чугуном с максимальным содержанием углерода, в особенности при высоких температурах заливки. Рис. 81. Влияние углерода, кремния, фосфора и марганца на практическую жидкотекучесть чугуна
При низких температурах заливки высокое содержание фосфора в эвтектическом чугуне может оказаться более благоприятным, чем соответствующее количество углерода, так как фосфор понижает эвтектическую температуру. Кроме того, фосфор понижает вязкость чугуна и повышает смачиваемость металлом Стенок формы, вследствие чего получаются более острые грани на отливках. Поэтому для тонкого и художественного литья пользуются чугуном с повышенным содержанием фосфора (до 1.0%).
Следует отметить, что с увеличением содержания кремния в чугуне наблюдаются два максимума (0,3 и 0.75%) и два минимума (0,5 и 0,95%) на кривых практической жидкотекучести (рис. 81), Эти аномалии не получила еще должного объяснения и нуждаются в подтверждении. При очень высоком содержании кремния (6-18%) жидкотекучесть чугуна снижается вследствие образования большого количества включений и спели в чугуне. Все же при эвтектическом составе и этот чугун обладает еще достаточно хорошей жидкотекучестью, обеспечивающей заполнение сравнительно тонкостенных отливок.
Влияние марганца аналогично влиянию кремния и фосфора, но значительно меньше по интенсивности. При наличии же высокого содержания серы марганец, образуя, резко понижает жидкотекучесть чугуна, что приводит к большому браку по недоливам и спаям.
В отношении влияния серы на жидкотекучесть маломарганцовистого чугуна существует мало систематических исследований. Практические наблюдения и некоторые литературные данные убедительно говорят о повышении вязкости и понижении жидкотекучести чугуна с увеличением содержания серы свыше 0,18%.
Сведения о влиянии легирующих элементов на жидкотекучесть чугуна чрезвычайно скудны и ограничиваются, главным образом, качественной оценкой. Исследования П. Г. Петрова установили, что никель не оказывает заметного влияния на жидкотекучесть. В противоположность никелю, медь действует на жидкотекучесть чугуна явно положительно. Хром же понижает жидкотекучесть, в особенности при содержании свыше 1%.
Это влияние хрома объясняется повышением температура ликвидуса в хромовом чугуне и образованием оксидных пленок. Также неблагоприятно действует молибден, ванадий, алюминий и др. Однако при малых концентрациях влияние этих элементов на жидкотекучесть чугуна мало заметно.
в) Влияние жидкого состояния чугуна. Жидкое состояние чугуна также оказывает некоторое влияние на его жидкотекучесть. Так, например, некоторые исследования показывают, что с увеличением температуры перегрева чугуна жидкотекучесть его повышается даже в том случае, когда температура заливки остается без изменения. Объяснение этого явления следует искать в растворении всякого рода микроскопических и субмикроскопических твердых фаз (в том числе графита) при увеличении перегрева чугуна, что приводит к повышению жидкотекучести. Таким образом, температура перегрева чугуна действует в том же направлении, что и температура заливки.
Рис.82. Влияние температуры перегрева и заливки чугуна на жидкотекучесть.
1 – температура перегрева 1650 ,температура заливки 1540; 2 – температура перегрева 1540 , температура заливки 1540; 3 – температура перегрева 1540, температура заливки 1430; 4 – температура перегрева 1430, температура заливки 1430.
По той же причине модифицирование, повышая вязкость жидкого чугуна, несколько понижает его жидкотекучесть. Например, в некоторых исследованиях было обнаружено, что при присадке длина спирали при измерении жидкотекучести уменьшилась с 62 до 46 см. С другой стороны, присадка соды или сложных модификаторов увеличивает жидкотекучесть, если при этом не происходит понижения температуры. Это объясняется очищением металла от включении благодаря образованию легкоплавких соединений.
Так как “наследственные” свойства чугуна определяются устойчивым содержанием газов и неметаллических включения я формой графита в исходных материалах, то естественно, что и жидкотекучесть чугуна определяется в известной мере происхождением сырых материалов. Так, например, в исследованиях П, П. Берга и Н. В. Димитриева было найдено.
Эти данные, однако, нельзя рассматривать как постоянные. При изменении условий плавки изменяется и жидкотекучесть чугуна. Всякое увеличение количества газов и включений, а также укрупнение выделений графита в шихтовых материалах, уменьшают жидкотекучесть. Точно так же и многократный переплав чугуна в вагранке, как показали П. П. Берг и Н. В. Димитриев, может привести к уменьшению его жидкотекучести вследствие насыщения металла газами и включениями:
По той же причине увеличение содержания стали в шихте уменьшает жидкотекучесть чугуна даже в том случае, когда состав металла (судя по обычному химическому анализу) остается без изменения. Наоборот, плавка на древесноугольном, а также на специально перегретом в жидком состоянии чугуне повышает жидкотекучесть.
Согласно исследованиям Ю. А. Шульте на заводе “Коммунар” присадка руды в электропечь для создания окислительного характера шлаков с целью ошлакования включений кремнезема в металле повышает жидкотекучесть и необходима для хорошего заполнения тонкостенных отливок.
г) Влияние технологии формы. Жидкотекучесть чугуна определяется в значительной мере конструкцией отливки, сопротивлением формы и тепло-физическими константами ее материала. Очевидно, что факторы, повышающие сопротивление движению металла в форме и ускоряющие охлаждение, уменьшают время его течения и понижают жидкотекучесть.
Исследования автора показали, что с повышением влажности формовочной смеси до 6% и содержания угля до 7% жидкотекучесть чугуна сначала увеличивается, а затем падает (рис. 83) и заливки чугуна на жидкотекучесть.
Рис. 83. Влияние влажности и содержания угля в формовочной смеси на жидкотекучесть малокремнистого чугуна.
Благоприятное влияние небольших добавок влаги и угля объясняется созданием паровой пли газовой рубашки между металлом и стенками формы. По этой же причине, как показали В.И.Фундатор и М. М. Левин, жидкотекучесть повышается при покрашенной графитом форме, при добавке мазута (до 2%) в формовочную смесь и при применении припылов. При большой же влажности формовочной смеси или высоком содержании в ней газ отвори их веществ жидкотекучесть чугуна резко понижается вследствие обильного парообразования, что не только ускоряет охлаждение чугуна, но и повышает сопротивление его движению в форме.
Состав формовочных смесей влияет также на поверхностное натяжение чугуна и способность его давать острые грани на отливках. В этом отношении оказываются полезными органические добавки всякого рода, вследствие чего формовка в стержнях дает хорошее заполнение тонких сечений и ясные очертания на отливках.
С другой стороны, применение металлических форм, как это видно из некоторых литературных данных (рис. 84), значительно уменьшает жидкотекучесть чугуна вследствие повышенной теплоотдачи. Подогрев же формы действует, как показали опыты Н. Н. Рубцова и др., в обратном направлении. Некоторое влияние на жидкотекучесть имеет также гидростатический напор. Опыты показали, что повышение высоты стояка на 100 мм увеличивает длину спирали сечением 50 мм2 с 200 до 250 см. Согласно же исследованиям автора, увеличение гидростатического напора до 180 мм повышает жидкотекучесть чугуна; дальнейшее увеличение напора действует уже в обратном направлении вследствие охлаждения металла при движении по длинному стояку. Однако такое образование максимума характерно только для тонких сечений, в том числе для проб на жидкотекучесть, когда количество металла, заполняющее собственно форму, мало по сравнению с металлом литниковой системы. В других условиях стояк успевает хорошо прогреться и не действует столь отрицательно на жидкотекучесть. Поэтому во многих случаях пользуются повышением напора для лучшего заполнения формы и для уменьшения брака по недоливу и спаям на тонкостенных чугунных отливках.
Жидкотекучесть может быть значительно повышена также путем применения высоких давлений, как это имеет место при литье под давлением. В этом случае хорошее заполнение формы и получение ясных очертаний обеспечивается и при пониженной температуре заливки, в том числе даже в интервале кристаллизации.
Наконец, следует отметить, что немалое влияние на жидкотекучесть чугуна имеет сечение питателей. Опыты автора показали, что между жидкотекучестью и сечением питателя существует следующая зависимость:
γ = k√Fn (77)
Рис. 84. Сравнительная жидкотекучесть чугуна с разным содержанием кремния и марганца при заливке в песочные и металлические формы.
Таким образом, жидкотекучесть чугуна является функцией многих переменных, характеризующих металл, форму и условия заливки. Ввиду сложности этой зависимости, она не поддается пока точному математическому расчету. Поэтому для каждой отливки в данных условиях приходится подбирать состав чугуна, температуру заливки и конструкцию литниковой системы для обеспечения заполнения формы. На основе опыта и практических соображений можно, например, рекомендовать:
Плотность чугуна, значение и примеры
Онлайн калькуляторыНа нашем сайте собрано более 100 бесплатных онлайн калькуляторов по математике, геометрии и физике.
СправочникОсновные формулы, таблицы и теоремы для учащихся. Все что нужно, чтобы сделать домашнее задание!
Заказать решениеНе можете решить контрольную?!
Мы поможем! Более 20 000 авторов выполнят вашу работу от 100 руб!
Плотность чугуна и другие его физические свойства
Углерод в составе чугуна может присутствовать в различных формах: в виде соединения состава Fe3C, называемого цементитом или в виде графита (пластинчатого, хлопьевидного или сферического), причем от формы графита в значительной мере зависят свойства чугуна. Он в очень малой степени способен к пластической деформации (в обычных условиях не поддается ковке), но обладает хорошими литейными свойствами. Чугун дешевле стали.
Выделяют белый, серый, высокопрочный и ковкий чугун. Плотность чугуна показана ниже:
Чугун |
|||
белый |
серый (СЧ 10 ГОСТ 1412-85) |
высокопрочный (ВЧ 35 ГОСТ 7293-85 |
ковкий (КЧ 70-2 ГОСТ 1215-79) |
7400 – 7750 |
6800 |
7200 |
7000 |
Белый чугун содержит весь углерод в виде цементите. Он обладает высокой твердостью, хрупок и поэтому имеет ограниченное применение. В основном он выплавляется для передела на сталь.
В сером чугуне углерод содержится главным образом в виде пластинок графита. Серый чугун (рис. 1) характеризуется высокими литейными свойствами (низкая температура кристаллизации, текучесть в жидком состоянии, малая усадка) и служит основным материалом для литья. Он широко применяется в машиностроении для отливки станин станков и механизмов, поршней, цилиндров. Кроме углерода, серый чугун содержит другие элементы. Важнейшие из них – это кремний и марганец. В большинстве марок серого чугуна содержание углерода лежит в пределах 2,4-3,8%, кремния 1-4% и марганца до 1,4%.
Рис. 1. Серый чугун. Внешний вид.
Высокопрочный чугун получают присадкой к жидкому чугуну некоторых элементов, в частности магния, под влиянием которого графит при кристаллизации принимает сферическую форму. Сферический графит улучшает механические свойства чугуна. Из высокопрочного чугуна изготовляют коленчатые валы, крышки цилиндров, детали прокатных станов, прокатные валки, насосы, вентили.
Ковкий чугун получают длительным нагреванием отливок из белого чугуна. Его применяют для изготовления деталей, работающих при ударных и вибрационных нагрузках. Пластичность и прочность ковкого чугуна обусловлены тем, что углерод находится в нем в форме хлопьевидного графита.
Примеры решения задач
Понравился сайт? Расскажи друзьям! | |||
Типы чугуна (стр. 1), Серый и ковкий чугун
Марки чугуна
Для большинства современных автомобильных и потребительских применений чугун делится на 4 отдельные категории:
- Серый чугун (эта страница)
- Высокопрочный чугун (эта страница)
- Высокопрочный чугун с аустенитным отпуском (страница 2)
- Чугун с уплотненным графитом Страница 2)
В Северной Америке есть 2 промышленных общества, которые берут на себя ответственность за организацию и управление программами по регулированию и совершенствованию технологических процессов:
- Американское общество литейщиков (AFS)
- Общество ковкого чугуна (DIS)
Сравнение графита – микрофотографические исследования
Серый чугун – Пример микрофотографии Ковкий чугун – Пример микрофотографии Высокопрочный чугун с аустенитным отпуском – микрофотографияЧугун с уплотненным графитом – микрофотография Чугун представляет собой сплав железо-углерод-кремний, содержащий более 2% углерода, который заливают в форму, содержащую негатив желаемой окончательной формы. Механические свойства и поведение материала зависят от морфологии графита, который образуется в железной матрице в результате терморегулирования процесса и добавления элементов для получения желаемой формы графита. Все чугуны затвердевают в результате сложной эвтектической реакции, в которой участвуют Fe, C и Si. Есть также влияние Cu, Mn, S и P.
Серый чугун
Серый чугун — самая простая, самая распространенная и самая дешевая форма чугуна в мире. Микроструктура железа характеризуется качествами «чешуйчатого графита» в виде: а) типа, б) размера и в) матрицы.
Серый чугун обладает превосходными свойствами литья и механической обработки, что делает его очень ценным для деталей, которые могут быть тяжелыми. Кроме того, серый чугун обладает превосходными демпфирующими и тепловыми свойствами, что делает его идеальным для автомобильных тормозных систем. Хотя он прочный, он также хрупкий.
Типы чешуйчатого графита
Серый чугун на сегодняшний день является наиболее распространенным из чугунов. Наряду со сталью это наиболее широко используемый инженерный сплав. В 1 веке автомобильной промышленности это был предпочтительный материал для блоков цилиндров, головок и многих других компонентов трансмиссии. Название происходит от внешнего вида поверхности излома, которая имеет серый цвет. В сером чугуне графит затвердевает в виде взаимосвязанных чешуек, как показано выше в 3D-микроскопии с помощью сканирующего электронного микроскопа. Сгруппированные формы графита сравнивают с картофельными чипсами, склеенными вместе в центральном месте. Центральная точка — исходное графитовое ядро. Каждый кластер чешуек определяет эвтектическую ячейку в сером чугуне. Эвтектические ячейки несколько аналогичны зернам в других металлах. Прочность железа повышается за счет более мелких размеров ячеек.
Форма графита в сером чугуне является важным фактором, определяющим свойства сплава. Форма и размер графита могут заметно различаться в зависимости от скорости охлаждения и содержания сплава. Наиболее распространенная форма, как описано в предыдущем абзаце, называется Type A . Пять типов графита в сером чугуне классифицируются как b ASTM.
Тип A Чешуйчатая структура
Графит типа A имеет равномерное распределение и случайную ориентацию. Как правило, он обеспечивает наилучшие свойства и обычно используется для компонентов трансмиссии.
Серый чугун – Тип АСтруктура хлопьев типа B
Графит типа B выглядит как розетки со случайной ориентацией. Это чаще всего происходит в почти эвтектических сплавах, которые неправильно модифицированы и содержат очень мало зародышей графита. Графит типа B часто встречается на поверхности отливки, где в остальном он относится к типу A.
Серый чугун – тип BТип C Чешуйчатая структура
Графит типа C встречается в заэвтектических чугунах (CE больше 4,3), в которых графит образуется в качестве первичной фазы. Этот первичный графит называется графитом Киша. Его присутствие снижает свойства при растяжении, что может быть желательным для некоторых специальных применений.
Серый чугун – Тип CСтруктура хлопьев типа D
Графит типа D возникает в результате междендритной сегрегации в быстро охлажденных чугунах. Он состоит из мелких беспорядочно ориентированных чешуек между аустенитными дендритами. Тип D может привести к более высоким свойствам при растяжении, но может быть трудным для термической обработки из-за сегрегации.
Структура чешуек типа E
Графит типа E похож на тип D, но с ориентированными чешуйками между ветвями аустенитных дендритов. Чаще всего это происходит в чугунах с очень низким углеродным эквивалентом.
Серый чугун – Тип EРазмер чешуйчатого графита
В дополнение к типу графита ASTM установила спецификации для размера графита. Это определяется путем сравнения количества хлопьев на микрофотографии со 100-кратным увеличением со стандартной диаграммой.
Механические свойства серого чугуна
Как правило, серый чугун имеет низкую прочность и очень низкую пластичность. Чешуйки графита действуют как крошечные внутренние трещины, которые создают усиление напряжения. Это позволяет трещинам очень легко распространяться по материалу, что снижает прочность, пластичность и ударную вязкость (вязкость разрушения). Серый чугун определяется номером класса, который соответствует номинальной прочности сплава на растяжение. Например, серый чугун класса 30, который был типичен для блока цилиндров, имеет номинальную прочность на растяжение 30 000 фунтов на квадратный дюйм (207 МПа). Поскольку серый чугун имеет очень низкую пластичность, предел текучести и процентное удлинение, эти свойства редко измеряются или указываются. Поскольку YTS и UTS настолько близки (удлинение менее 1%), серый чугун классифицируется как «хрупкий материал». Другой способ определения серого чугуна – по твердости материала. Общество автомобильных инженеров (SAE) опубликовало стандарт материала для чугуна SAE J431, учитывающий как свойства прочности на растяжение, так и свойства твердости. Кроме того, каждый автомобильный OEM-производитель имеет собственный набор стандартов, регулирующих свойства серого чугуна, и специальные методы испытаний, необходимые для измерения качества материала.
Прочность и твердость
Прочность и твердость серого чугуна зависит как минимум от четырех основных факторов:
- Углеродный эквивалент
- Содержание сплава
- Модификация
- Скорость затвердевания 9001 5
- Предотвратить образование карбидов (цементита)
- Способствовать образованию графита
- Уменьшить сегрегацию
- Уменьшить усадку 90 008
- Улучшение обрабатываемости
- Повышение однородная структура
- Увеличение пластичности
- Извлечение Mg при конверсии = 20–25%
- Десульфурация основного сплава перед конверсией важна
- Реакция бурная и не рекомендуется для обеспечения безопасности
- Очень дымно во время конверсии
- Извлечение Mg при конверсии = 40-45%
- Десульфурация основного сплава важна перед конверсией
- Реакция бурная, но снижается, поскольку ковш глубже и имеет карман для обработки
- Все еще дымится во время конверсии и нуждается в вентиляционном колпаке
- Извлечение магния при конверсии = 60-65%
- Десульфурация основного сплава менее критична
- Дым уменьшается на 90% от конверсии в открытом ковше
- Извлечение магния = 70% (используется магниевая стружка)
- Десульфурация основного сплава, как правило, не требуется
- Закрытый конверсионный сосуд содержит реакционную смесь
- Безопасен для больших объемов ковша
- Извлечение магния при конверсии = 70% (используется магниевая стружка)
- Десульфурация основного сплава менее критична 900 08
- Песчаная форма содержит реакция
- Обычно в сочетании с автоматическим разливочным ковшом для регулирования потока
Прочность на растяжение быстро уменьшается с увеличением Углеродный эквивалент.
Углеродный эквивалент (CE)
Для чугуна формула углеродного эквивалента (CE) используется для понимания того, как легирующие элементы будут влиять на поведение отливки. Он используется в качестве предиктора прочности чугуна, поскольку дает приблизительный баланс аустенита и графита в конечной структуре.
CE = %C + 0,33 (%Si) + 0,33 (%P) – 0,027 (%Mn) + 0,4 (%S)
CE < 4,3%, доэвтектическое поведение при затвердевании
CE = 4,3, эвтектическое поведение при затвердевании
CE > 4,3%, заэвтектическое поведение во время затвердевания
Содержание сплава
Наиболее эффективными элементами для серого чугуна являются углерод и кремний. Когда цель состоит в том, чтобы разлить чугун по эвтектике, чтобы предотвратить образование карбидов железа, можно использовать добавки кремния в ковше для модификации расплавленного сплава, чтобы всегда достигался эвтектический эквивалент. Используя расчет CE и подтверждая соответствующее количество добавок ферросиликата, клиновидный блок используется для подтверждения того, что серый чугун находится на желаемом уровне CE.
Углерод и кремний
По сравнению с обычными марками стали содержание углерода в сером чугуне примерно в десять раз выше. Поскольку стальной лом составляет большую часть шихты расплава для чугунолитейного производства, углерод обычно приходится добавлять в какой-то момент процесса либо в основную шихту, либо после того, как железо находится в расплавленном состоянии. Поскольку в стальном шихтовом ломе очень мало углерода, металлургу необходимо учитывать все металлические шихтовые материалы (сталь, железный лом, чугун) в основной печи. Добавки, повышающие содержание углерода, в значительной степени зависят от метода плавки (плавка в вагранке с коксом приводит к повышению уровня углерода), количества используемого кремния и наличия дешевого графита. Однако по мере перехода чугунолитейной промышленности от вагранки к индукционной плавке с аналогичными высокими добавками стального лома в шихту требуются альтернативные добавки в ковше, в потоке или в литейной форме для получения чешуек типа А в сером чугуне.
Методы модифицирования
С переходом на индукционную плавку литейные заводы тщательно загружают в свои индукционные ковши тщательно взвешенные количества стального лома, лома железа и более дорогого чугуна. Сегодня большее количество низкоуглеродистой стали может быть получено за счет добавления модификаторов ферросилиция (FeSi). Процесс модифицирования включает добавление от 0,05 до 1% специального сплава FeSi, содержащего контролируемые количества одного или нескольких тщательно отобранных элементов для дальнейшего улучшения морфологии графита. Объяснение того, как эти тщательно отобранные элементарные добавки, включая Al, Ca, Ba, Sr, Ce, La, Mn, Bi, S, O и Zr, можно найти в Таблице 1.0 Структурные эффекты элементарных добавок к чугуну, показанной ниже. . В дополнение к повышению уровня кремния модификатор создает центры зародышеобразования, которые способствуют осаждению и росту графита, а также затвердеванию железа на основе стабильной системы Fe-C.
Когда необходимо приобрести углерод для добавления, дополнительный материал обычно имеет форму графита. Добавки графита часто поступают из угольных электродов, ранее использовавшихся в сталеплавильных печах.
Цель модифицирования
Целью модифицирования является стимулирование гетерогенного зародышеобразования графита путем введения элементов, образующих подходящие субстраты, которые будут действовать как зародыши и инициировать желаемое образование графита. Способствуя стабильному затвердеванию эвтектики, модифицирование позволяет C выходить из раствора в благоприятной форме графита, а не в виде карбида железа.
При тщательном контроле использование модифицирующей добавки поможет:
Эффект модифицирования представлен на рисунке ниже (Эффект модифицирования), где кривые охлаждения для немодифицированного железа обозначены черной пунктирной линией, а для модифицированного железа указаны в виде синей сплошной линии.
Модифицирование может происходить при выпуске, в ковше, в потоке во время литья или даже внутри формы. Модифицирующие сплавы доступны в гранулированной форме, упакованы в проволоку или отлиты/прессованы в различные формы. Размер регулируется в зависимости от точки добавления, времени и температуры, доступных для растворения в расплавленном железе. Как правило, количество добавок может быть уменьшено, если модифицирование происходит как можно ближе к заливке чугуна в форму, поэтому модифицирование «в потоке» гранулами FeSi является наиболее распространенным методом добавления.
Эффект модифицирования
На кривых охлаждения для железа без модифицирования (черная пунктирная линия) и модифицированного железа (синяя сплошная линия) влияние проявляется как снижение степени переохлаждения до образования графита (красная стрелка). ). Модификация также продлевает образование и рост графита, тем самым увеличивая время затвердевания (зеленая стрелка).
Влияние прививки на кривую охлаждения Формы испытания на охлаждение – результаты показывают стабильность состава железа и обработки для предотвращения образования карбидов.
При промышленном производстве чугуна модифицируют как серый, так и ковкий чугун, но серый чугун обычно требует меньших модифицирующих добавок, в зависимости от состава железного сплава, метода плавки и состава шихты. Внесение ферросилиция преобразует структуру из переохлажденного графита (графит типа E в сером чугуне) в полностью чешуйчатый или сфероидальный графит, как показано ниже.
Влияние модифицирования на структуру графита в сером и ковком чугунеПрочие элементы
Поскольку прочность чугуна зависит от содержания феррита по сравнению с содержанием перлита, для повышения прочности добавляются легирующие элементы, подавляющие образование феррита и увеличивающие количество перлита. Для изучения аффектов был изучен ряд элементов и даны общие описания. Для этой цели используются легирующие элементы, такие как хром (Cr), молибден (Mo) и вольфрам (W). Эти элементы способствуют образованию карбидов и повышают твердость железа. Дополнительную информацию см. в Таблице 1.0 Структурные эффекты добавок элементов к чугуну, приведенной ниже.
Ковкий чугун
Ковкий чугун (также называемый графитом с шаровидным графитом и шаровидным графитом) прочнее серого чугуна, более прочен и намного дешевле для литья сложных деталей, чем формование стали. Микроструктура железа характеризуется качеством «Узловатость» (округлость), размером узелков и плотностью узлов (узелков на мм²).
Ковкий чугун считается прочным материалом для деталей шасси (например, сталь), если его морфология является ферритной. В то время как прочность может быть увеличена путем использования добавок к сплаву для продвижения перлита вокруг конкреций, результирующий % удлинения снижается.
Резюме
Ковкий чугун прочнее и пластичнее (жестче), чем серый чугун. Он образуется путем обработки железа с относительно высоким углеродным эквивалентом шаровидным агентом, таким как магний (наиболее распространенный) или церий, для образования графитовых сфер, которые растут во время затвердевания. Наиболее распространены автомобильные детали, требующие высокой прочности и ударной вязкости при воздействии нагрузок, связанных с термоциклированием или ударами. Типы деталей включают: коленчатые валы, распределительные валы, выпускные коллекторы, поворотные кулаки, рычаги подвески, держатели дифференциала, пружинные хомуты и тому подобное. В сантехнике и трубопроводной промышленности использование ковкого чугуна стало большим достижением в производстве труб, соединений и клапанов, которые были менее дорогими, чем альтернатива из ковкого чугуна. При всех этих применениях расширяется применение ковкого чугуна, часто вытесняя конструкции из серого чугуна, так что можно добиться снижения веса за счет улучшенных механических свойств.
На ежегодной конференции AFS 1948 года участникам конференции была представлена новая морфология железа: ковкий чугун. Создателем этого нового материала обычно считается Кит Миллс, однако в первоначальном патенте 1949 года, переданном Международной никелевой компании (INCO), указаны трое человек: Кит Дуайт Миллис, Альберт Пол Ганнебин и Норман Боден Пиллинг. В своем патенте (US2485760A) изобретателям приписывают изобретение «литого ферросплава для производства ковкого чугуна путем обработки магнием».
Являясь патентообладателем ковкого чугуна с обработкой магнием, INCO продвигала преимущества свойств материала и знакомила дизайнеров и инженеров с ковким чугуном путем распространения технической литературы и проведения семинаров. По мере того, как знания о свойствах и экономичности ковкого чугуна распространялись, его использование резко возросло на протяжении пятидесятых и начала шестидесятых годов. После прекращения INCO продвижения ковкого чугуна в 1966 году, рост рынка ковкого чугуна продолжал опережать рост других отливок из черных металлов, но когда инженеры и дизайнеры, которые извлекли выгоду из первых усилий INCO по продвижению, ушли на пенсию, их заменило новое поколение, которое не было ознакомились с технологией процесса из своей академической подготовки. По этой причине было создано Общество ковкого чугуна (DIS) для обучения и ликвидации разрыва в знаниях с новыми поколениями металлургов, инженеров-конструкторов и инженеров-технологов.
Десульфуризация
Обработка ковкого чугуна имеет чрезвычайно важное значение для определения его свойств. Начальным этапом производства ковкого чугуна является удаление избыточной серы из расплавленного чугуна. В серый чугун иногда добавляют серу, поскольку она способствует образованию графитовых чешуек. По этой причине он должен быть практически исключен из расплавов ковкого чугуна. Есть некоторые литейные заводы, которые перерабатывают как серый, так и ковкий чугун из одного и того же шихтового материала, поэтому любой лом серого чугуна, перерабатываемый внутри компании, будет содержать серу, которую необходимо удалить. Удаление серы включает добавление CaO или какого-либо другого агента. Следует отметить, что литейные заводы, которые специализируются только на обработке ковкого чугуна, могут иметь возможность избежать обширных процедур десульфурации, но они всегда должны следить за этим при измерении химического состава.
Нодуляризация с использованием конверсии магния
Уникальной стадией обработки ковкого чугуна является формообразование графита. На этом этапе к расплавленному сплаву добавляют магний для создания остаточного уровня Mg примерно 0,03-0,06%, что является количеством, необходимым для образования сфероидов из графита. К сожалению, Mg испаряется при температуре значительно ниже температуры плавления чугуна с шаровидным графитом, поэтому для достижения такой конверсии были разработаны инновационные методы конверсии:
Конверсия в открытом ковше
Переделка ковша для сэндвичей
Конверсия промковша
Конвертерный метод Джорджа Фишера
Конверсия в литейной форме
Конверсия магния
Конверсия в разливочном ковше является наиболее распространенным методом конверсии и считается безопасным:
Извлечение Mg 60-65%, низкое выделение дыма, снижение потерь углерода.
Существуют и другие методы конверсии с разной степенью безопасности и эффективности извлечения магния: конверсия в открытом ковше (извлечение 20–25% Mg), конверсия в сэндвич-ковше (извлечение 40–45 Mg), конвертер Джорджа Фишера (извлечение 70% Mg), Конверсия в форме (извлечение 75% Mg)
Разливочный ковш – поперечное сечениеОбесцвечивание магния
Еще одна проблема, связанная с образованием комков, заключается в обесцвечивании Mg с течением времени, что представляет собой тенденцию Mg к постепенному испарению (или окислению) из раствора, когда поверхность ковша находится в контакте с воздухом. Когда Mg исчезает из состава сплава, уменьшается шаровидность, и механические свойства неожиданно меняются. Для предотвращения выгорания в открытом ковше сплав необходимо разливать в течение фиксированного промежутка времени (как правило, 10-12 минут). Однако при использовании закрытой автоматической разливочной станции этот срок может быть увеличен до часа, если используется инертный защитный газ для предотвращения контакта расплава с воздухом, тем самым предотвращая окисление магния.
Инокуляция
Последним этапом перед заливкой является модификация, которая также выполняется теми же методами, что и серый чугун. Как описано в разделе, посвященном серому чугуну, сплавы ферросилиция обычно добавляют в расплав непосредственно перед заливкой, чтобы обеспечить места для зародышеобразования графита. Более совершенные и более поздние методы инокуляции обеспечат более мелкое распределение конкреций и высокую плотность конкреций (количество конкреций на мм²). Количество узелков 200 и более часто указывается для более тонких срезов, но таких более высоких значений трудно достичь в толстых или тяжелых срезах.
Сравнительная таблица плотности конкреций из ковкого чугуна (100x)Ферритные и перлитно-графитовые конструкции
Из-за высоких скоростей удлинения, достижимых для литого ферритного сорта ковкого чугуна, автомобильные конструкторы, ответственные за критически важные для безопасности конструкции шасси, предпочитают использовать ковкий чугун. Для дизайнеров автомобилей ковкий чугун считается ценным материалом, потому что он дешевле, чем альтернативы, такие как кованая сталь, кованый алюминий или даже алюминиевые отливки, обработанные раствором. Благодаря высоким свойствам относительного удлинения и ударной вязкости, присущим конструкционным деталям из ковкого чугуна в литом состоянии, конструкторы автомобильных шасси имеют низкозатратный производственный процесс, который позволяет их конструкциям пройти строгие требования к краш-тестам. Однако, когда эти же конструкторы рассматривают возможность снижения общего веса автомобиля, они начинают указывать более прочные марки ковкого чугуна. Однако в то же время конструкторы также требуют высокой пластичности, измеряемой % удлинения при обычных производственных испытаниях на растяжение. Таким образом, теперь у нас есть марки железа, которые зависят от некоторого количества перлита в морфологии железа для увеличения YTS, но при этом сохраняют удлинение > 8%. Поэтому тщательный анализ морфологии железа необходимо сочетать с проверкой механических свойств, чтобы можно было строго контролировать химический состав сплава, чтобы получить ожидаемые результаты после извлечения образцов из литых деталей.
Отливки из ковкого чугуна, используемые для изготовления автомобильных шасси.
Металлографический анализ
Возможность оценки микроструктуры ковкого чугуна в литейном производстве особенно важна при использовании составов сплавов, в которые в сплав добавляют олово (Sn) или медь (Cu) с целью поднятия перлитных образований вокруг графитовых конкреций. Интерпретация этих типов микрофотографий и их корреляция с механическими свойствами очень важны для установления значимых пределов химического состава сплава, когда железо плавится и заливается на производственную линию.
Микроструктура пластин толщиной 2,5 мм: нелегированная – слева, легированная 0,5 % меди – справа. Нитал травленый. Изображение предоставлено для приведенных выше изображений микроструктуры:
Стефанеску, Дору М. и др., «Металлургия и механические свойства при растяжении тонкостенных чугунов со сфероидальным графитом», Международный журнал исследований литых металлов, 2003 г., том. 16 № 1-3.
https://www.researchgate.net/publication/260037434_The_Metallurgy_and_Tensile_Mechanical_Properties_of_Thin_Wall_Spheroidal_Graphite_Irons
Перлитный ковкий чугун
Когда свойства удлинения не так важны, как YTS и UTS, обычно используются контролируемые добавки Cu и Sn для стимулирования образования перлита вокруг графитовых конкреций. Было обнаружено, что количество образовавшегося перлита пропорционально улучшенной прочности на растяжение с экспоненциальным уменьшением % удлинения.
Изображение предоставлено:
Общество ковкого чугуна рис. 3.16
https://www.ductile.org/didata/Section3/Figures/pfig3_16.htm
Промышленные спецификации
На приведенной ниже диаграмме Общество автомобильных инженеров (SAE) публикует красивую диаграмму, в которой добавки к сплаву используются для изменения структуры от 100% феррита до повышения уровня перлита в морфологии железа. SAE классифицирует материалы по UTS (минимальное ожидание) и ожидаемому % удлинения. Как показано на рисунке 3.16 DIS, % удлинения уменьшается экспоненциально, в то время как механические свойства увеличиваются логарифмически.
Изображение предоставлено для диаграммы выше:
Общество ковкого чугуна – РАЗДЕЛ XII. СПЕЦИФИКАЦИИ
https://www.ductile.org/didata/Section12/12intro.htm
Испытание свойств на растяжение
Литейный цех по производству ковкого чугуна должен иметь возможность надлежащим образом испытывать образцы на растяжение более тщательно, чем литейный цех из серого чугуна. Оценка ковкого чугуна в соответствии с любой основной технической спецификацией потребует измерения YTS, UTS, % удлинения, образцов для удара по Шарпи и твердости по Бринеллю. Таким образом, в дополнение к проведению спектрографического и металлографического анализа литейный цех должен иметь точный прибор для испытаний на растяжение.
Определение YTS (предела текучести при растяжении)
В связи с требованием высокой прочности при растяжении и минимальной потери пластичности, измеряемой в % относительного удлинения, особое внимание следует уделить испытаниям на растяжение как части производственного процесса. Теперь у нас есть марки железа, которые зависят от некоторого количества перлита в морфологии железа для увеличения YTS, но при этом сохраняют удлинение > 8%. Поэтому тщательный анализ морфологии железа необходимо сочетать с проверкой механических свойств, чтобы можно было строго контролировать химический состав сплава, чтобы получить ожидаемые результаты после извлечения образцов из литых деталей. Имея это в виду, определение YTS на основе метода смещения 0,2% должно основываться на использовании принятой интерпретации на основе программного обеспечения. Кроме того, все испытательные лаборатории, связанные с измерением свойств при растяжении для данной категории продуктов, должны сравнивать результаты с «циклическими» формами испытаний. Все задействованные лаборатории должны демонстрировать разумную взаимосвязь между объектами и операторами.
Дополнительная информация:
Таблица 1.
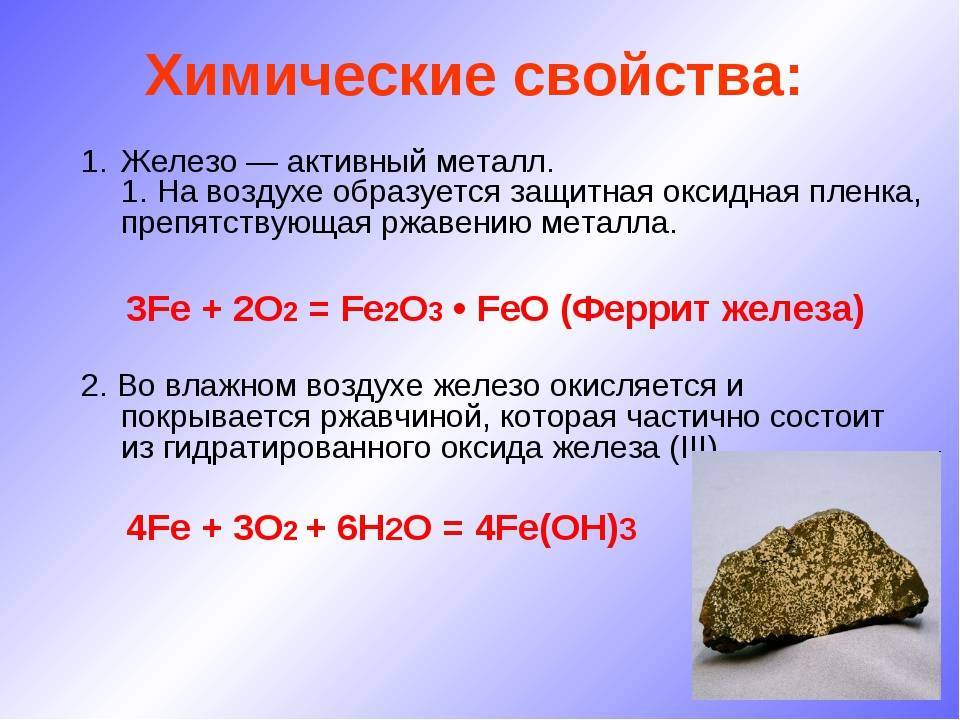
Алюминий
.
Сурьма
.
.
Висмут
.
.
Бор ≤ 0,15%
.
Бор > 0,15%
.
Хром
.
.
.
Медь
.
Марганец
.
Молибден
.
Никель
.
Кремний
.
Теллериум
.
.
.
Олово
.
.
Титан < 0,25%
.
Ванадий
Сильный графитизатор
.
Маленький эффект в использованном количестве
.
Карбидный промотор, но не карбидный формирователь
.
Сильный графитизатор
.
Твердосплавный стабилизатор
.
Прочный твердосплавный формирователь. Образует сложные карбиды, которые очень стабильны
.
Мягкий графитизатор
.
Мягкий твердосплавный формирователь
.
Мягкий твердосплавный формирователь
.
Графитизатор
.
Сильный графитизатор
.
Очень сильный карбидный активатор, но не стабилизатор
.
Небольшой эффект от использованного количества
.
Графитизатор.
.
Сильный карбидообразователь
Способствует формированию феррита и графита
.
Сильный стабилизатор перлита
.
.
Стабилизатор очень мягкого перлита
.
.
Способствует образованию графита
.
Прочный перлитный фиксатор
.
Сильный перлитообразователь
.
.
.
Способствует образованию перлита
.
Перлитный формирователь
.
Сильный перлитообразователь
.
Мягкий формирователь перлита
.
Способствует образованию феррита и графита
.
Очень мягкий стабилизатор перлита
.
.
.
Прочный перлитный фиксатор
.
.
Способствует образованию графита
.
Сильный формирователь перлита
| ЦЕВ | Сталь | Чугун | Сварка
Опубликовано Автор: admin
Метод эквивалентного содержания углерода используется для расчета характеристик черных металлов, таких как сталь и чугун, которые содержат не только углерод в качестве сплав. Этот метод преобразует процентное содержание других легирующих элементов в сопоставимое процентное содержание углерода, используя более понятную взаимосвязь между углеродом и железом. Этот подход обычно используется при сварке, термической обработке и литье чугуна.
ЧТО ДЕЛАЕТ УГЛЕРОДНЫЙ ЭКВИВАЛЕНТ ВАЖНЫМ?
Когда два куска металла будут соединяться вместе с помощью сварки, например, при соединении двух труб, крайне важно понимать углеродный эквивалент или значение CE. Факторы окружающей среды могут вызвать перемещение или расширение и сжатие труб. Вероятность того, что место сварки является слабым местом, увеличивается, если одна труба прочнее другой. Две трубы, соединенные сваркой, в идеале должны функционировать как единое целое. Сварной шов будет либо сдвигаться, либо ломаться, если два куска металла имеют слишком разные характеристики, чтобы функционировать как единое целое.
Сталь
Во время сварки эквивалентное содержание углерода (C.E.) используется для определения того, как различные легирующие элементы влияют на твердость свариваемой стали. Поскольку водородное холодное растрескивание является наиболее частым дефектом сварки стали, оно напрямую связано с ним, поэтому он является наиболее популярным методом оценки свариваемости. Более высокое содержание углерода и других легирующих элементов, включая марганец, хром, кремний, молибден, ванадий, медь и никель, имеют тенденцию к увеличению твердости при снижении свариваемости. Однако, поскольку каждый из этих элементов по-разному влияет на твердость и свариваемость стали, необходимо сравнить твердость двух сплавов, созданных из различных легирующих элементов, чтобы определить разницу в твердости между ними.
Согласно AWS существует риск образования трещин в околошовной зоне (ЗТВ) на кромках газовой резки и сварных швах при эквивалентном содержании углерода более 0,40%. Хотя CE редко используется в стандартах проектирования конструкций, они устанавливают максимальное процентное содержание для некоторых легирующих элементов. Этот обычай существовал еще до того, как появилась идея CE. Это создало проблемы, потому что в настоящее время используются некоторые высокопрочные стали, которые имеют хрупкие разрушения и CE выше 0,50%.
Для определения значения углеродного эквивалента следует использовать следующую формулу IIW (Международного института сварки):
Значение углеродного эквивалента по формуле IIW (Международного института сварки)Максимальный CEV на основе ковшового анализа:
ковшовый анализ b FN = кипячение стали не допускается; FF = полностью успокоенная сталь
c Для сортового проката применяется максимальное значение CEV 0,54.
d Применяется только для длинных изделий.
Чугун
Чтобы выяснить, как легирующие материалы повлияют на термообработку и поведение при литье чугуна, применяется идея эквивалентного содержания углерода (CE).