Д16 закалка – Термообработка Д16 – Термообработка – Металлический форум
alexxlab | 24.07.2020 | 0 | Разное
Термообработка Д16 | Всё о цветных металлах и сплавах (бронза, медь, латунь и др)
Март 19, 2019 · 2:00 пп
Топик с форума Чипмейкер
- Скажите, пожалуйста, технологию ТО Д16 в Д16Т. Мех. св-ва реально повысятся и на ск-ко? Особенно интересует твёрдость, т.к. в справочниках твёрдость Д16Т не попадалась.
- Просмотрел всю имеющуюся литературу — где говориться, что ТО сильно повышает мехи Д16, где не значительно!? Особенно поражает ГОСТ 21488-97 в котором сигма для не термообработанной 245 МПА, что соответствует отожённым в других источниках. Единственное у всех одно — это временное после ТО+старение: 420 МПа.Твёрдость после ТО, так понял, что где-то 110 НВ. Нужны мехи (особенно твёрдость) для поставки без ТО. Хорошо бы получить инфу от людей, которые у себя приёмочные испытания проводили.
- Закалка 485-495 градусов на воду подогретую до70,старение 185-195 градусов на воздух. HB 130-150
- Наконец получил данные с Каменск-Уральского МЗ. У Д16 (нетермообработанного) прутка и трубы: временное 245, текучести 120, удлинение 12, твёрдость 75…85. Твёрдость после закалки — 125…130.
- Кстати о воде и закалке д16. Есть различные мнения. Кто-то говорит, что должна быть почти 80, кто-то 70, кто-то до 40. Вроде все сходятся, что не ниже 30. Но злые языки говорят, что прочность д16 набирает именно при температурах более низких. http://gmehanik.ru/materialy/mat_kost_al_o…moobrabotki.php Повышенную температуру используют для снижения коробления, внутренних напряжений. При этом прочность снижается. Но с другой стороны, д16 после закалки можно обрабатывать давлением.
- А на практике приходится калить летом — +20С , зимой — около 0 (металловеды наверное проклянут меня). Извините, Саян, никогда не видел чуда с подогревом пресной воды, селяви
- Товарищ термообрабатывал Д16. Калил в воду из под крана. Остальных подробностей от него трудно узнать, но температуры вроде какие надо были. Упрочниться-то оно упрочнилось, но на части заготовок появились какие-то ПУЗЫРИ. Ну, натурально, пузыри :wacko:, газовые. Как волдыри на поверхности. Толщина металла стенки пузырей 0.5 — 1 мм. Скажите, от чего такое может быть.
- Перегрел конечно же. Видимо температура нагрева высоковата была. Каменичный пишет, что такое бывает из-за неравномерной температуры в печи. Сам калил Д16 на 500 градусов в муфеле. Охлаждал в воду 70 градусов. Качество отличное, твердость правда не мерил, но по фрезеровке сразу видно.
- Привожу результаты т/о в нашей термичке по Д16:
Закалка 500+-5 гр., вода — НВ 125
Искусственное старение 185-195 гр., воздух НВ 134
Добавлю, по справочным данным, для Д16 желательно делать естественное старение, при искусственном снижаются антикоррозионные свойства сплава.
Понравилось это:
Нравится Загрузка…
Похожее
Filed under Полезное, Самоделкин, алюминий, с форумов
Tagged as Д16Т, алюминий, дюраль, закалка, отжиг, полезности, термообработка, умелые руки
tsvetmet.wordpress.com
Способ термической обработки заготовок из алюминиевого сплава д16
Изобретение относится к области термической обработки и может быть применено при закалке заготовок из сплава Д16 для последующего изготовления из них высокоточных деталей. Сплав нагревают до температуры закалки. Затем проводят охлаждение с температуры закалки до 430°С со скоростью 130-150°С в час и выдержку в течение 3 минут. Последующее охлаждение осуществляют в воде с температурой 80-100°С, а затем в воде с температурой 20°С, после чего проводят старение. Данный способ позволяет уменьшить деформацию при закалке и старении. 1 табл.
Предлагаемое изобретение относится к области термической обработки и может быть применено при закалке заготовок из сплава Д16 для последующего изготовления из них высокоточных деталей.
Известен способ термической обработки сплава Д16, который заключается в закалке с температуры 490°С, выдержке при этой температуре, охлаждении в воде с температурой 10-40°С и последующем старении при температуре 190°С – 12 часов [1]. Способ принят в качестве аналога.
Охлаждение заготовок при этом способе производят непосредственно с температуры закалки в воде. В этом случае из-за большой разности температур возникают значительные напряжения, приводящие к деформации заготовок. Эти деформации приходится устранять за счет обработки (съема) оставленного припуска фрезерованием, что в дальнейшем приводит к изменению формы и размеров деталей, а это недопустимо, т.к. требует увеличения значительного припуска под дальнейшую обработку.
Известен способ закалки алюминиевых сплавов, который заключается в нагреве до температуры закалки, выдержке при этой температуре и охлаждении в воде с температурой 80-100°С [2].
Способ взят в качестве прототипа. При этом способе температура при закалке снижается до 390-410°С по сравнению со способом-аналогом. Однако это недостаточно эффективно уменьшает деформацию, т.к. напряжения возникают при охлаждении во время закалки при температуре выше 480°С, когда предел текучести (σ0,2) алюминиевого сплава очень мал (˜10 кгс/мм2), что и приводит к значительным деформациям заготовок. Эти деформации не устраняются при последующем старении, а после механической обработки на заданные размеры детали самопроизвольно изменяют форму и размеры. Эти изменения размеров невозможно исправить. Поэтому и этот способ термической обработки неэффективен для изготовления высокоточных деталей сложной конфигурации (рам, кронштейнов, корпусов и т.п.).
Технический результат, достигаемый от применения предлагаемого способа, заключается в уменьшении деформации при закалке и старении.
Технический результат достигается тем, что в предлагаемом способе термической обработки заготовок сплава Д16, включающем закалку в воде с температурой 80-100°С в воде цеховой температуры и старение, охлаждение с температуры закалки производят со скоростью 130-150°С в час до температуры 430°С, выдержка до 3-х минут.
Отличительный признак предлагаемого способа – охлаждение с температуры закалки со скоростью 130-150°С в час до 430°С, выдержка до 3-х минут при этой температуре, что и обеспечивает технический результат.
Пример практического применения.
Подвергали закалке образцы из сплава Д16 по различным режимам. Результаты исследования указаны в таблице.
Таблица. Результаты исследования сплава Д16 после различных режимов термической обработки. | |||||||||
№ | Сорт | Режим закалки | Изменение размеров ± мм после | Свойства | Примечание | ||||
после закалки | Старение 190°C – 12 ч. | ||||||||
Закалки | Старения 190°С 12 час | σв кгс/мм2 | δ % | σв кгс/мм2 | δ % | ||||
1 | 2 | 3 | 4 | 5 | 6 | 7 | 8 | 9 | 10 |
Плита ≠35 мм | Нагрев до 490°С, выд. 1,5 часа, охлаждение: | Способ-аналог | |||||||
1 | а) в воде с температурой 20°С | +0,58 | -0,06 | 36 | 17 | 42 | 15 | ||
б) в воде с температурой 90°С | +0,25 | -0,04 | 37 | 19 | 41 | 17 | Способ-прототип | ||
Плита ≠20 мм | а) -«- | +0,68 | -0,05 | 37 | 19 | 42 | 18 | Способ-аналог | |
б) -«- | +0,18 | -0,06 | 38 | 16 | 43 | 15 | Способ-прототип | ||
Плита ≠35 мм | Нагрев до 490°С, выд. 1,5 часа, охлажд. с печью со скоростью | +0,08 | -0,02 | 40 | 17 | 42 | 15 | Предлагаемый режим | |
2 | Плита ≠20 мм | 130°С в час до 430°С, выд. 3 мин, охлажд. в воде с температурой 90°С, выд. 3 мин, охлажд. в воде с температурой 20°С | +0,05 | -0,02 | 41 | 16 | 43 | 14 | |
Плита ≠35 мм | Нагрев до 490°С. выд. 1,5 часа, охлажд. с печью со скоростью | +0,09 | -0,02 | 40,5 | 16 | 42 | 15 | Предлагаемый режим | |
3 | Плита ≠20 мм | 150°С в час до 430°С, выд. 3 мин, охлажд. в воде с температурой 90°С, выд. 3 мин, охлажд. в воде с температурой 20°С | +0,06 | -0,03 | 41,5 | 18 | 43 | 14 | |
Плита ≠35 мм | Нагрев до 490°С, выд. 1,5 часа, охлажд. с печью со скоростью | +0,07 | -0,01 | 37 | 18 | 38 | 17 | Способ, выходящий за пределы предлагаемого | |
4 | Плита ≠20 мм | 120°С в час до 430°С, выд. 3 мин, охлаждение в воде с температурой 90°С, выд. 3 мин, охлаждение в воде с темпер. 20°С. | +0,05 | -0,01 | 38 | 19 | 39 | 18 | |
Плита ≠35 мм | Нагрев до 490°С, выд. 1,5 часа, охлажд. с печью со | +0,01 | 0,01 | 33 | 20 | 34 | 19 | -«- | |
5 | Плита ≠20 мм | скоростью 150°С в час до 400°С, выд. 3 минуты, охлаждение в воде с температурой 90°С, выд. 3 минуты, охлаждение в воде с температурой 20°С | +0,01 | 0 | 34 | 21 | 35 | 20 | |
Примечания к таблице. 1. Выдержку при термической обработке отсчитывали после достижения образцами заданной температуры. 2. При термической обработке использовали образцы тип III ГОСТ1497-84. Торцы образцов доводили до шероховатости для повышения точности измерения длины образцов. 3. На каждый режим термической обработки использовали по три образца, вырезанные из каждой плиты Д16 согласно ГОСТ 17232-99. 4. Результаты измерения размеров (длины) образцов являются среднеарифметическим результатом измерения 3-х образцов. Измерения длины (60 мм) образцов выполняли с точностью ±0,001 мм. 6. Температура закалки обеспечивалась с точностью ±5°С. Из результатов таблицы следует, что предлагаемый режим обеспечивает уменьшение деформации образцов более чем в 6 раз после закалки и более чем в 2 раза после старения при практически равных механических свойствах (σв; δ). |
Использование предлагаемого способа позволяет:
1. Существенно уменьшить деформацию как после закалки, так и после старения (190°С – 12 часов).
2. Изготавливать детали (рамы, корпуса, кронштейны) сложной конфигурации с точными размерами из плит, профилей, прутков сплава Д16.
Источники информации
1. Производственная инструкция ПИ 1.2А510-98 с.15-20. Термическая обработка полуфабрикатов и деталей из алюминия и алюминиевых деформированных сплавов, ВИАМ.
2. Патент РФ №2125618. Способ термической обработки отливок из алюминиевых сплавов.
Способ термической обработки заготовок из алюминиевого сплава Д16, включающий нагрев сплава до температуры закалки, охлаждение с температуры закалки до 430°С со скоростью 130-150°С в час и выдержку в течение 3 мин, охлаждение в воде с температурой 80-100°С, а затем в воде с температурой 20°С и старение.
findpatent.ru
способ термической обработки заготовок из алюминиевого сплава д16 – патент РФ 2324000
Изобретение относится к области термической обработки и может быть применено при закалке заготовок из сплава Д16 для последующего изготовления из них высокоточных деталей. Сплав нагревают до температуры закалки. Затем проводят охлаждение с температуры закалки до 430°С со скоростью 130-150°С в час и выдержку в течение 3 минут. Последующее охлаждение осуществляют в воде с температурой 80-100°С, а затем в воде с температурой 20°С, после чего проводят старение. Данный способ позволяет уменьшить деформацию при закалке и старении. 1 табл.
Предлагаемое изобретение относится к области термической обработки и может быть применено при закалке заготовок из сплава Д16 для последующего изготовления из них высокоточных деталей.
Известен способ термической обработки сплава Д16, который заключается в закалке с температуры 490°С, выдержке при этой температуре, охлаждении в воде с температурой 10-40°С и последующем старении при температуре 190°С – 12 часов [1]. Способ принят в качестве аналога.
Охлаждение заготовок при этом способе производят непосредственно с температуры закалки в воде. В этом случае из-за большой разности температур возникают значительные напряжения, приводящие к деформации заготовок. Эти деформации приходится устранять за счет обработки (съема) оставленного припуска фрезерованием, что в дальнейшем приводит к изменению формы и размеров деталей, а это недопустимо, т.к. требует увеличения значительного припуска под дальнейшую обработку.
Известен способ закалки алюминиевых сплавов, который заключается в нагреве до температуры закалки, выдержке при этой температуре и охлаждении в воде с температурой 80-100°С [2].
Способ взят в качестве прототипа. При этом способе температура при закалке снижается до 390-410°С по сравнению со способом-аналогом. Однако это недостаточно эффективно уменьшает деформацию, т.к. напряжения возникают при охлаждении во время закалки при температуре выше 480°С, когда предел текучести (0,2) алюминиевого сплава очень мал (10 кгс/мм2), что и приводит к значительным деформациям заготовок. Эти деформации не устраняются при последующем старении, а после механической обработки на заданные размеры детали самопроизвольно изменяют форму и размеры. Эти изменения размеров невозможно исправить. Поэтому и этот способ термической обработки неэффективен для изготовления высокоточных деталей сложной конфигурации (рам, кронштейнов, корпусов и т.п.).
Технический результат, достигаемый от применения предлагаемого способа, заключается в уменьшении деформации при закалке и старении.
Технический результат достигается тем, что в предлагаемом способе термической обработки заготовок сплава Д16, включающем закалку в воде с температурой 80-100°С в воде цеховой температуры и старение, охлаждение с температуры закалки производят со скоростью 130-150°С в час до температуры 430°С, выдержка до 3-х минут.
Отличительный признак предлагаемого способа – охлаждение с температуры закалки со скоростью 130-150°С в час до 430°С, выдержка до 3-х минут при этой температуре, что и обеспечивает технический результат.
Пример практического применения.
Подвергали закалке образцы из сплава Д16 по различным режимам. Результаты исследования указаны в таблице.
Таблица. Результаты исследования сплава Д16 после различных режимов термической обработки. | |||||||||
№ | Сорт | Режим закалки | Изменение размеров ± мм после | Свойства | Примечание | ||||
после закалки | Старение 190°C – 12 ч. | ||||||||
Закалки | Старения 190°С 12 час | в кгс/мм2 | % | в кгс/мм2 | % | ||||
1 | 2 | 3 | 4 | 5 | 6 | 7 | 8 | 9 | 10 |
Плита 35 мм | Нагрев до 490°С, выд. 1,5 часа, охлаждение: | Способ-аналог | |||||||
1 | а) в воде с температурой 20°С | +0,58 | -0,06 | 36 | 17 | 42 | 15 | ||
б) в воде с температурой 90°С | +0,25 | -0,04 | 37 | 19 | 41 | 17 | Способ-прототип | ||
Плита 20 мм | а) -«- | +0,68 | -0,05 | 37 | 19 | 42 | 18 | Способ-аналог | |
б) -«- | +0,18 | -0,06 | 38 | 16 | 43 | 15 | Способ-прототип | ||
Плита 35 мм | Нагрев до 490°С, выд. 1,5 часа, охлажд. с печью со скоростью | +0,08 | -0,02 | 40 | 17 | 42 | 15 | Предлагаемый режим | |
2 | Плита 20 мм | 130°С в час до 430°С, выд. 3 мин, охлажд. в воде с температурой 90°С, выд. 3 мин, охлажд. в воде с температурой 20°С | +0,05 | -0,02 | 41 | 16 | 43 | 14 | |
Плита 35 мм | Нагрев до 490°С. выд. 1,5 часа, охлажд. с печью со скоростью | +0,09 | -0,02 | 40,5 | 16 | 42 | 15 | Предлагаемый режим | |
3 | Плита 20 мм | 150°С в час до 430°С, выд. 3 мин, охлажд. в воде с температурой 90°С, выд. 3 мин, охлажд. в воде с температурой 20°С | +0,06 | -0,03 | 41,5 | 18 | 43 | 14 | |
Плита 35 мм | Нагрев до 490°С, выд. 1,5 часа, охлажд. с печью со скоростью | +0,07 | -0,01 | 37 | 18 | 38 | 17 | Способ, выходящий за пределы предлагаемого | |
4 | Плита 20 мм | 120°С в час до 430°С, выд. 3 мин, охлаждение в воде с температурой 90°С, выд. 3 мин, охлаждение в воде с темпер. 20°С. | +0,05 | -0,01 | 38 | 19 | 39 | 18 | |
Плита 35 мм | Нагрев до 490°С, выд. 1,5 часа, охлажд. с печью со | +0,01 | 0,01 | 33 | 20 | 34 | 19 | -«- | |
5 | Плита 20 мм | скоростью 150°С в час до 400°С, выд. 3 минуты, охлаждение в воде с температурой 90°С, выд. 3 минуты, охлаждение в воде с температурой 20°С | +0,01 | 0 | 34 | 21 | 35 | 20 | |
Примечания к таблице. 1. Выдержку при термической обработке отсчитывали после достижения образцами заданной температуры. 2. При термической обработке использовали образцы тип III ГОСТ1497-84. Торцы образцов доводили до шероховатости для повышения точности измерения длины образцов. 3. На каждый режим термической обработки использовали по три образца, вырезанные из каждой плиты Д16 согласно ГОСТ 17232-99. 4. Результаты измерения размеров (длины) образцов являются среднеарифметическим результатом измерения 3-х образцов. Измерения длины (60 мм) образцов выполняли с точностью ±0,001 мм. 5. Охлаждение деталей и образцов со скоростью 130-150°С в час производили вместе с печью. 6. Температура закалки обеспечивалась с точностью ±5°С. Из результатов таблицы следует, что предлагаемый режим обеспечивает уменьшение деформации образцов более чем в 6 раз после закалки и более чем в 2 раза после старения при практически равных механических свойствах (в; ). |
Использование предлагаемого способа позволяет:
1. Существенно уменьшить деформацию как после закалки, так и после старения (190°С – 12 часов).
2. Изготавливать детали (рамы, корпуса, кронштейны) сложной конфигурации с точными размерами из плит, профилей, прутков сплава Д16.
Источники информации
1. Производственная инструкция ПИ 1.2А510-98 с.15-20. Термическая обработка полуфабрикатов и деталей из алюминия и алюминиевых деформированных сплавов, ВИАМ.
2. Патент РФ №2125618. Способ термической обработки отливок из алюминиевых сплавов.
ФОРМУЛА ИЗОБРЕТЕНИЯ
Способ термической обработки заготовок из алюминиевого сплава Д16, включающий нагрев сплава до температуры закалки, охлаждение с температуры закалки до 430°С со скоростью 130-150°С в час и выдержку в течение 3 мин, охлаждение в воде с температурой 80-100°С, а затем в воде с температурой 20°С и старение.
www.freepatent.ru
Всё о цветных металлах и сплавах (бронза, медь, латунь и др)
ООО ВПО ПромМеталл http://bronza555.ru/
[email protected] +7-903-798-09-70 (звоните!)
Складскую справку можно скачать здесь
Деформируемые алюминиевые сплавы разделяют на неупрочняемые термической обработкой и упрочняемые. Кнеупрочняемым алюминиевым сплавам относят сплавы марки АМц2, АМг2, АМгЗ, имеющие невысокую прочность и высокую пластичность; их применяют для изделий, получаемых глубокой вытяжкой, упрочняют холодной обработкой давлением (нагартовкой).
Наиболее распространены сплавы, упрочняемые термической обработкой. К ним относят дюралюминий марок Д1, Д16, Д3П, в состав которых входят алюминий, медь, магний и марганец. Основными видами термического упрочнения дюралюминия являются закалка и старение. Закалку проводят при 505—515° С с последующим охлаждением в холодной воде. Старение применяют как естественное, так и искусственное. При естественном старении сплав выдерживают в течение 4—5 сут, при искусственном — 0,8—2,0 ч; температура старения — не ниже 100—150°С; прочность после обработки уВ = 490 МПа, 6=14%. Сплавы Д1 и Д16 применяют для изготовления деталей и элементов строительных конструкций, а также изделий для летательных аппаратов.
Авиаль (АВ, АВТ, АВТ1)—это деформируемый сплав, обладающий более высокой пластичностью, свариваемостью и коррозионной стойкостью, чем дюралюминиевые; подвергают закалке в воде при 515—525° С и старению: сплавы АВ и АВТ — естественному, сплав АВТ1 — искусственному при 160° С с выдержкой 12—18 ч. Применяют авиаль для производства листов, труб, лопастей винтов вертолетов и т. п.
Высокопрочные (ув=550-700 МПа) алюминиевые сплавы В95 и В96 имеют меньшую пластичность, чем дюралюминий. Термическая обработка этих сплавов заключается в закалке при 465—475° С с охлаждением в холодной или горячей воде и искусственном старении при 135—145° С в течение 14—16 ч. Применяют сплавы в самолетостроении для нагруженных конструкций, работающих длительное время при 100—200° С.
Ковочные алюминиевые сплавы марок АК1, АК6, АК8 подвергают закалке при 500—575° С с охлаждением в проточной воде и искусственному старению при 150—165° С с выдержкой 6—15 ч; прочность сплава уВ = 380-460 МПа, относительное удлинение д = 7-10%.
Литейные алюминиевые сплавы называют силуминами. Наиболее распространены термически упрочняемые сплавы марок АЛ4, АЛ6 и АЛ20 Отливки из сплавов АЛ4 и АЛ6 закаливают при 535—545° С с охлаждением в горячей (60—80° С) воде и подвергают искусственному старению при 175° С в течение 2—3 ч; после термической обработки ув=260 МПа, д = 4-6%, твердость НВ 75—80. Для снятия внутренних напряжений отливки из этих сплавов отжигают при 300° С в течение 5—Ю ч с охлаждением на воздухе. Жаропрочные сплавы марок АЛ 11 и АЛ20, идущие для изготовления поршней, головок цилиндров, топок котлов, работающих при 200—300° С, подвергают закалке (нагрев до 535—545° С, выдержка при этой температуре в течение 3—6 ч и охлаждение в проточной воде), а также стабилизирующему отпуску при 175—180° С в течение 5—10 ч; после термической обработки ув=300-350 МПа, д=3-5%.
tsvetmet.wordpress.com
Температура нагрева под закалку
Основное требование при выборе температуры нагрева под закалку алюминиевых деформируемых сплавов — получение максимально возможной концентрации легирующих элементов в твердом растворе для обеспечения высокого эффекта упрочнения при последующем старении.
Увеличение степени пересыщения твердого раствора при закалке достигается повышением температуры нагрева при необходимой для наиболее полного растворения избыточных фаз выдержке и резким охлаждением.
Нагрев под закалку не всегда переводит сплав в однофазное состояние, так как во многих алюминиевых сплавах содержание легирующих элементов превышает предел растворимости. В зависимости от диаграммы состояния, фазового состава и особенностей структуры, обусловленных предыдущей обработкой, алюминиевые сплавы могут иметь различный интервал закалочных температур. Верхняя граница температурного интервала нагрева под закалку устанавливается во избежание пережога с учетом присутствия или образования в сплаве наиболее легкоплавких эвтектик, возможного перепада температуры и точности контроля (регулирования) теплового режима в объеме рабочего пространства термических агрегатов. Нижний предел интервала закалочных температур определяется требуемым комплексом свойств.
Для большинства промышленных алюминиевых сплавов нагрев под закалку можно осуществлять в достаточно широком температурном интервале, однако рекомендуемый интервал, обеспечивающий оптимальное сочетание свойств, несколько уже и, как правило, не превышает 10°С . Наибольший интервал температур, при которых можно производить нагрев под закалку, характерен для сплавов системы Al—Zn—Mg (350—500°С) и Al—Zn—Mg—Сu (460—500 °С).
Система | Марка сплава | T, °C |
Al-Zn-Mg | В92Ц | 450—470 |
1911, 1915, 1925 | 450—460 | |
Al—Zn—Mg—Си | B91, B95, В96Ц, В96Ц-1 |
465—475 |
В96ЦЗ | 460—470 | |
B93 | 450—465 | |
Al—Сu—Mg | Д1 | 495-510 |
Д19, ВД17 | 495—505 | |
ВАД1, M40 | 498—508 | |
Д16 | 490—498 | |
Al—Си—Li | 1230 | 515—525 |
Al—Си—Mn | Д20, 1201 | 530—540 |
Д21 | 520—530 | |
Al—Си— Mg—Fe—Ni | AK4-1 | 525—535 |
Al—Си—Mg—Si | AK8 | 495—505 |
AK6 | 505—525 | |
Al—Mg—Si | АД31, АДЗЗ, АД35 | 525—535 |
АВ | 510—530 | |
Al—Mg—Li | 1420 | 450—465 |
Свойства сплава В95 в состаренном состоянии мало зависят от изменения температуры нагрева под закалку в интервале 460 — 480°С. Для холоднокатаных листов этот интервал, может быть расширен. Однако максимальная температура ограничена из-за интенсивной диффузии легирующих элементов в плакирующий слой. Широким интервалом закалочных температур (450—500 °С) характеризуется также сплав 1420. Для сплавов системы Al—Си—Mg (дюралюмины) требуется наиболее точное выполнение температурного режима нагрева под закалку — в пределах 6 — 8°С, так как максимально допустимая температура всего лишь на несколько градусов ниже температуры солидуса. Это особенно важно для сплава Д16, у которого начальные стадии пережога иногда обнаруживаются даже при рекомендованных ранее температурах нагрева (498 — 500 °С) в случае содержания меди и магния на верхнем пределе по ГОСТу. В связи с этим максимальную температуру нагрева под закалку сплава Д16 рекомендуется ограничить 498 °С. В случае содержания основных легирующих элементов ближе к нижнему пределу по ГОСТу возможно допустить закалку с температуры не выше 503°С.
В большинстве случаев рекомендуется проводить закалку с максимально возможной температуры в указанных интервалах. Однако при этом следует учитывать, что для многих сплавов эта температура лишь на 5 —10 °С ниже температуры солидуса, которая может значительно колебаться в зависимости от химического состава сплава даже в пределах одной марки и от технологии предшествующих обработок.
Максимальную температуру нагрева под закалку регламентируют и в тех случаях, когда требуется сохранить нерекристаллизованную структуру, уменьшить рост зерна и диффузию в плакирующий слой, предотвратить сильное окисление поверхности, уменьшить склонность к трещинообразованию при охлаждении массивных полуфабрикатов с крупнокристаллическим ободком, а также уменьшить коробление.
В процессе закалки необходима высокая точность выполнения температурного режима и равномерность нагрева садки металла. Для обеспечения оптимального сочетания свойств перепад температуры в термических агрегатах не должен превышать ±5°С, а часто даже ±3°С.
Упрочнение в результате закалки определяется не только режимом этого процесса, но и системой легирования, на базе которой разработан сплав. Из промышленных сплавов наибольшим приростом прочности в результате закалки по сравнению с прочностью в отожженном состоянии характеризуются сплавы системы Al—Zn—Mg—Сu. Эффект закалки этих сплавов достигает 200—230МПа. Большинство сплавов, разработанных на базе систем Al—Сu—Mg, Al—Сu—Li, Al—Сu—Mn, Al—Mg—Si, Al—Mg—Si—Сu и Al—Mg—Li, имеют эффект закалки 100 — 180МПа. Некоторые сплавы, относящиеся к системе Al—Zn—Mg, даже несколько теряют прочность из-за большей гомогенности в закаленном состоянии по сравнению с отожженным.
www.metmk.com.ua
Д16 – bulatstal.ru
На современном рынке конструкционных материалов сегодня можно встретить довольно большой выбор различных марок металлов. Для большинства покупателей их названия не известны. А ведь по маркировке можно легко узнать характеристики металла и его основные свойства.
Одним из таких сплавов является марка Д16. Мало кто знает, что это самый обычный и всем известный дюраль. Он очень широко используется в самых различных отраслях.
Особенности сплава Д16 и его состав.
Химический состав в % материала Д16ГОСТ 4784 — 97
Fe | Si | Mn | Cr | Ti | Al | Cu | Mg | Zn | Примесей | — |
до 0.5 | до 0.5 | 0.3 — 0.9 | до 0.1 | до 0.15 | 90.9 — 94.7 | 3.8 — 4.9 | 1.2 — 1.8 | до 0.25 | прочие, каждая 0.05; всего 0.15 | Ti+Zr < 0.2 |
Механические свойства при Т=20oС материала Д16 .
Сортамент | Размер | Напр. | sв | sT | d5 | y | KCU | Термообр. |
— | мм | — | МПа | МПа | % | % | кДж / м2 | — |
Трубы, ГОСТ 18482-79 | 390-420 | 255-275 | 10-12 | |||||
Пруток, ГОСТ 21488-97 | 245 | 120 | 12 | |||||
Пруток, ГОСТ 21488-97 | Ø 8 — 300 | 390-410 | 275-295 | 8-10 | Закалка и старение | |||
Пруток, высокой прочности, ГОСТ 51834-2001 | 450-470 | 325-345 | 8-10 | Закалка и старение | ||||
Пруток, повышенной пластичности, ГОСТ 51834-2001 | 410 | 265 | 12 | Закалка и старение | ||||
Лента отожжен., ГОСТ 13726-97 | 235 | 10 | ||||||
Профили, ГОСТ 8617-81 | 10 — 150 | 412 | 284 | 10 | Закалка и искуственное старение | |||
Профили отожжен., ГОСТ 8617-81 | 245 | 12 | ||||||
Плита, ГОСТ 17232-99 | 345-420 | 245-275 | 3-7 | Закалка и старение |
Твердость Д16 после закалки и старения , | HB 10 -1 = 105 МПа |
Твердость Д16 , Сплав отожженный | HB 10 -1 = 42 МПа |
Физические свойства материала Д16 .
T | E 10— 5 | a 10 6 | l | r | C | R 10 9 |
Град | МПа | 1/Град | Вт/(м·град) | кг/м3 | Дж/(кг·град) | Ом·м |
20 | 0.72 | 2770 | ||||
100 | 22.9 | 130 | 0.922 |
В качестве легирующих элементов в сплаве Д16 применяют медь (Cu 4,4%), магний (Mg 1,5%), марганец (Mn 0,5%) и очень незначительное количество кремния (Si до 0,5%), железа (Fe до 0,5%), хрома (Cr до 0,1%), титана (Ti до 0,15%) и цинка (Zn до 0,25%).
Чистый сплав Д16 применяется очень редко, так как он обладает недостаточной прочностью и твердостью. По этой причине дюраль закаляют и подвергают старению. Эти процессы заключаются в нагреве деталей до 500 градусов Цельсия и дальнейшем охлаждении в воде. Старение в свою очередь может применяться искусственное и естественное. При этом название сплава изменяется на Д16Т.
Д16Т является самым востребованным алюминиевым сплавом. Он легкий, прочный и имеет отличные показатели сопротивления усталостным нагрузкам.
Основные характеристики и области применения
Благодаря очень низким показателям теплопроводности сплав Д16 прекрасно себя показывает при высоких температурах (от 120 до 250 градусов Цельсия). В этих пределах ему нет равных. Но изделия из данного сплава категорически запрещается использовать в условиях, когда температура выше 500 градусов Цельсия.
Применяют сплав Д16 в виде плит, листов, уголков и прутков разных размеров. Но лучше всего он себя демонстрирует в трубах, изготовленных для химической, нефтяной, газовой и пищевой промышленности. Также Д16 является материалом для изготовления заклепок.
bulatstal.ru
Прокаливаемость при закалке алюминиевых сплавов
Без прокаливаемости нет термоупрочнения
Какой максимальный диаметр прутка из слава алюминия можно упрочнить термообработкой? До какай толщины промышленность производит термообработанные плиты из Д1, Д16, 2024, И95 и др.? При закалке поверхность деталей и полуфабрикатов остывает быстрее середины. Последущее старение упрочняет изделие неравномерно по толщине, поэтому важно определить прокаливаемость алюминиевого сплава, зависимость прокаливаемости от марки алюминия и формы заготовки. Прокаливаемость является важной характеристикой алюминиевых сплавов, позволяющей оценивать возможность сквозной закалки различных по сечению и габаритам полуфабрикатов и деталей. Прокаливаемость — способность сплава после закалки сохранять степень пересыщения твердого раствора, которая обеспечвает при последующем старении требуемые свойства. Прокаливаемость зависит от критической скорости охлаждения (υкр) и от всех факторов, влияющих на устойчивость пересыщенного твердого раствора. Определенное влияние на уровень прокаливаемости оказывают габариты и конфигурация деталей, схема их расположения в садке, состояние поверхности деталей, перемещение садка в охлаждающей среде или ее циркуляция.
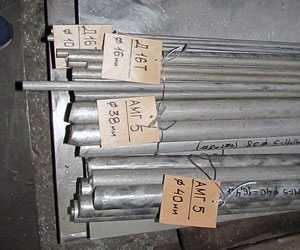
Оценка глубины закалки
Наиболее широко для количественной оценки глубины прокаливаемости алюминиевых сплавов используют методы пробной и торцовой закалки . Метод пробной закалки заключается в определении свойств по сечению изделия (темплета) и в сопоставлении полученных значений этих свойств в соответствующих точках сечения. В основу метода торцовой закалки положено моделирование условий охлаждения массивных полуфабрикатов различной конфигурации с помощью торцового образца переменного сечения, закаливаемого в специальной установке.
Глубина прокаливаемое устанавливается с учетом глубины зоны, равнопрочной (снижение не более 5%) с поверхностью охлаждаемого изделия (темплета) или торцового образца. Поскольку прокаливаемость зависит не только от толщины, но и от формы изделия, то представляется целесообразным при сравнительной оценке различных алюминиевых сплавов использовать значения критического диаметра (dкp), т. е. максимальный диаметр прутка, прокаливаемого насквозь.
Максимальные диаметры прутков под закалку в воду
На основании результатов исследований и производственного опыта могут быть рекомендованы следующие предельно допустимые диаметры прутков (dкp) с удовлетворительными механическими свойствами по всему сечению после закалки в воде комнатной температуры:
Марка | В96ЦЗ | В95, ВАД23 | Д1, Д16, ВД17, Д19, 1191, М40, Д20, 1201, АВ, АК6, АК8, 1960 | АК4-1 | В93 (закалка в воде 75—85°С) |
dкp, мм | 100 | 120 | 150 | 250 | 200 |
Приведенные значения dкp могут несколько изменяться в зависимости от концентрации легирующих элементов в пределах требования ГОСТа для каждой марки сплава.
www.metmk.com.ua