Дефект сварного шва: Дефекты сварных швов и соединений
alexxlab | 27.04.2023 | 0 | Разное
Дефекты сварных швов и соединений
Главная ГЛАВНАЯ Технология сварки УЧЕБНАЯ ПРОГРАММА ПО СВАРКЕ Дефекты сварных швов и соединений
ОСНОВНЫЕ ВИДЫ ДЕФЕКТОВ ПРИ СВАРКЕ
КРИТЕРИИ ОЦЕНКИ ТЕХНОЛОГИЧЕСКИХ ДЕФЕКТОВ В СВАРНЫХ КОНСТРУКЦИЯХ
Существующие нормы допустимых дефектов составлены главным образом из технологических возможностей производства, а в ряде случаев и волевым порядком, с ссылкой на опыт эксплуатации.
По вопросу влияния дефектов сварки (непроваров, пор, включений и т. д.) выполнено большое количество работ, однако до настоящего” времени не удалось выработать единый подход к оценке влияния технологических дефектов на служебные характеристики сварных конструкций, что сдерживает разработку и внедрение научно обоснованных норм по допустимым отклонениям. Анализ результатов экспериментальных и теоретических исследований по влиянию технологических отклонений (дефектов сварки) на служебные характеристики сварных соединений, позволяет утверждать, что при составлении нормативов по допустимым отклонениям необходимо рассматривать дефекты, как концентраторы и учитывать:
1. Чувствительность сварных соединений к концентрации напряжений в зоне дефекта.
2. Концентрацию напряжений, вызванную формой шва и дефектом.
3. Характер действующих нагрузок.
Критериями чувствительности сварных соединений к дефектам являются: при переменных (вибрационных) нагрузках- предел выносливости, а при статических нагрузках – предел прочности. Чувствительность к дефектам-концентраторам зависит от свойста основного металла, металла шва и технологии сварки.
Сварные соединения низкоуглеродистой стали (автоматическая и ручная сварка), стали Х18Н10Т (сварка в аргоне) не чувствительны к концентрации напряжений при статических нагрузках. Сварные соединения низколегированных сталей, сплавов АМг-6, Д16Т- чувствительны к концентрации напряжений при статических нагрузках.
В сварных соединениях, чувствительных к концентрации напряжений, при определении допустимости оставления в конструкции выявленных дефектов необходимо предварительно оценить влияние формы шва на механические характеристики сварных соединений, которая может значительно превысить влияние дефекта.

Метод разбраковки, названный «методом концентрации напряжений», основывается на предположении, что статический и динамический характер разрушения сварных соединений с технологическими концентраторами, имеющими конечный радиус, в том числе и от формы шва, должен быть приблизительно идентичный для одного и того же материала, если упругие коэффициенты их одинаковые. Для материалов и’ соединений, чувствительных к концентрации напряжений, разрушение всегда начинается в точках с максимальной концентрацией напряжений.
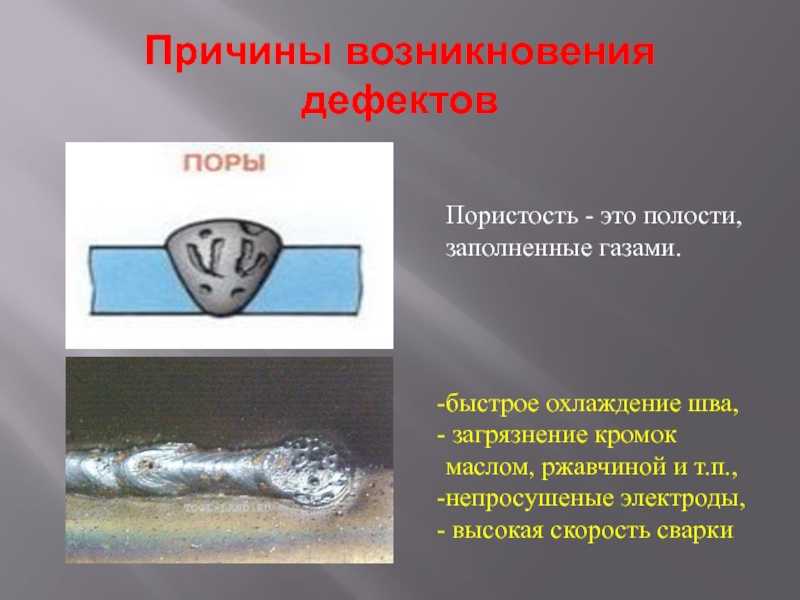
Для оценки концентрации напряжений от внутренних дефектов (пор, включений и т.д.) в общем случае требуется решение объемной задачи, то есть определение объемного коэффициента концентрации. Установлено, что объемный коэффициент концентрации и влияние на прочность сварного соединения объемных дефектов заметно меньше, чем у протяженных дефектов.
Метод сопоставления коэффициента концентрации напряжений применим к дефектам, имеющим конечный радиус (поры, включения) и не распространяется на такие дефекты, как непровар_и окисные пленки.
Необходимость учета характера действующих нагрузок и формы шва при назначении норм допустимости дефектов в сварных конструкциях подтверждается полученными экспериментальными данными по влиянию смещения кромок, шлаковых включений, пористости и других дефектов на прочность и выносливость сварных соединений.
Неразрушающий контроль сварных соединений
- Главная
- Поддержка
- Статьи
- Неразрушающий контроль сварных соединений
03. 10.2016
Неразрушающий контроль сварных соединений – очень важная процедура в таких отраслях, как строительство и эксплуатация трубо- и газопроводов. Качество сварных швов, при помощи которых трубы соединяют в трубопроводы, может оказать существенное влияние на продолжительность и безопасность эксплуатации всей магистрали.
Наиболее распространенными дефектами сварного соединения являются:
- Наплыв. Возникают при попадании расплава на пришовную зону, когда расплавленный металл натекает на основной, но не образует с ним гомогенного соединения. Могут быть в виде отдельных капель, а могут иметь продолговатую структуру. Сопровождаются неравномерным, некачественным проваром металла шва, а также приводят к появлению трещин. Устраняются срезанием с проверкой наличия непровара в этом месте.
- Подрез. Канавки в металле на границе сварного шва, в месте перехода “основной металл-сварной шов”. Подрезы уменьшают сечение шва, что в дальнейшем приводит к появлению избыточных напряжений и способно привести к появлению внешних и внутренних трещин.
Чаще всего этот дефект образуется в горизонтальных швах. Устраняют его наплавкой тонкого шва по линии подреза.
- Прожог. Сквозное проплавление и вытекание металла из сварочной ванны через сквозное отверстие в шве. Причинами появления таких дефектов служат – низкая скорость сварки, увеличенный зазор между торцами труб при их сваривании и превышение силы сварочного тока. Исправляют дефект зачисткой и последующей заваркой.
- Непровар. Непровары – это локальные несплавления наплавленного металла с основным, или слоев шва между собой. К этому дефекту относят и незаполнение сечения шва. Непровары существенно снижают прочность шва и могут явиться причиной разрушения конструкции. Дефект возникает из-за заниженного сварочного тока, неправильной подготовки кромок, излишне высокой скорости сварки, наличия на кромках свариваемых деталей посторонних веществ (окалины, ржавчины, шлака) и загрязнений. При исправлении нужно вырезать зонунепровара и заварить её.
- Кратер.
Это дефекты в виде углубления, возникающего в результате обрыва сварочной дуги. Кратеры снижают прочность шва из-за уменьшения его сечения. В них могут находиться усадочные рыхлости, способствующие образованию трещин. Кратеры надлежит вырезать до основного металла и заварить.
- Инородные включения. Включения могут состоять из различных веществ – шлака, вольфрама, окислов металлов и пр. Шлаковые включения образуются тогда, когда шлак не успевает всплыть на поверхность металла и остается внутри него. Это происходит при неправильном режиме сварки (завышенной скорости, например), плохой зачистке свариваемого металла или предыдущего слоя при многослойной сварке.Вольфрамовые включения возникают при сварке вольфрамовым электродом, окисные – из-за плохой растворимости окислов и чрезмерно быстрого охлаждения.Все виды включений уменьшают сечение шва и образуют очаг концентрации напряжения, снижая тем самым прочность соединения. Дефект устраняют вырезкой и завариванием.
- Пористость.
Полости, заполненные газами, возникающие из-за интенсивного газообразования внутри металла, при котором газовые пузырьки остаются в металле после его затвердевания. Размеры пор могут быть микроскопическими или достигать нескольких миллиметров. Нередко возникает целое скопление пор в сочетании со свищами и раковинами.
- Перегрев и пережог металла. Пережог и перегрев возникают из-за чрезмерно большого сварочного тока или малой скорости сварки. При перегреве размеры зерен металла в шве и околошовной зоне увеличиваются, в результате чего снижаются прочностные характеристики сварного соединения, главным образом – ударная вязкость. Перегрев устраняется термической обработкой изделия. Пережог представляет собой более опасный дефект, чем перегрев. Пережженный металл становится хрупким из-за наличия окисленных зерен, обладающих малым взаимным сцеплением. Причины пережога те же самые, что и перегрева, а кроме этого еще и недостаточная защита расплавленного металла от азота и кислорода воздуха.
- Свищ. Воронкообразное углубление в сварочном шве, развивающееся из раковины или большой поры. Причиной развития свища чаще всего является некачественная подготовка поверхности и присадочной проволоки под сварку. Дефект обнаруживается визуально и подлежит переварке.
- Поверхностное окисление. Окалина или пленка оксидов на поверхности сварного соединения. Поверхностное окисление зависит от плохой защиты сварочной ванны, качества подготовки свариваемых кромок, неправильной регулировки подачи защитного газа, его составом, большим вылетом электрода.
- Трещины. Трещины можно отнести к наиболее опасным видам дефектов. Они могут появиться в любой точке сварочной зоны (включая пришовную область металла) и иметь любое направление (продольное и поперечное). По своим размерам они подразделяются на микротрещины и трещины. Такой дефект вызывается как неправильными условиями кристаллизации расплава, так и превышением концентрации углерода, серы и фосфора в сварочной ванне.
Трещины заметно влияют на все основные параметры сварных соединений трубопроводов.
Методы неразрушающего контроля сварных соединений
Учитывая такое разнообразие дефектов, возникающих при сварке, способы контроля тоже могут существенно различаться.
Все сварные дефекты глобально можно разделить на внешние и внутренние, и если для контроля внешних дефектов чаще всего достаточно использования ВИК (визуально-измерительного контроля), то внутренние дефекты можно контролировать радиографическим или ультразвуковыми методами.
-
Визуально-оптический контроль – это один из методов неразрушающего контроля оптического вида. Он основан на получении первичной информации об объекте при визуальном наблюдении или с помощью оптических приборов. Это органолептический контроль, т.е. воспринимаемый органами чувств (органами зрения) ГОСТ 23479-79 “Контроль неразрушающий. Методы оптического вида” устанавливает требования к методам контроля оптического вида.
Визуальный метод контроля позволяет обнаруживать несплошности, отклонения размера и формы от заданных более 0,1 мм при использовании приборов с увеличением до 10х. Визуальный контроль, как правило, производится невооруженным глазом или с использованием увеличительных луп 2х до 7х. В сомнительных случаях и при техдиагностировании допускается увеличение до 20х.
- Радиационный вид неразрушающего контроля в соответствии с ГОСТ 18353-79 делится на методы: радиографический, радиоскопический, радиометрический. Радиографический метод контроля основан на преобразовании радиационного изображения контролируемого объекта в радиографический снимок. Требования к радиографическому контролю регламентированы ГОСТ 7512-82 “Контроль неразрушающий. Сварные соединения. Радиографический метод”.
Перейти к выбору приборов для радиографического контроля - Данный метод относится к акустическому виду неразрушающего контроля (ГОСТ 55724-2013 “Контроль неразрушающий. Соединения сварные.
Методы ультразвуковые”), применяется при толщине металла шва не менее 4 мм. Он основан на использовании ультразвуковых волн, представляющих собой упругие колебания материальной среды с частотой выше 0,5-0,25 МГц (выше той, которую способны воспринимать слуховые органы человека). В этом методе контроля используется способность ультразвуковых волн отражаться от границы раздела двух сред, обладающих разными акустическими свойствами. Когда при прохождении через сварной шов ультразвуковые волны встречают на своем пути дефекты (трещины, поры, шлаковые включения, расслоения и т. д.), они отражаются от границы раздела металл–дефект и могут быть зафиксированы при помощи специального ультразвукового дефектоскопа.
Перейти к выбору приборов для ультразвуковой дефектоскопии - Капиллярный контроль. Капиллярный контроль сварных соединений применяется для выявления наружных (поверхностных и сквозных) дефектов в сварных швах и прилегаюших зонах термического влияния.
Такой способ проверки позволяет выявлять такие дефекты, как горячие и холодные трешины в сварных швах, непровары, поры, раковины и некоторые другие.
Перейти к выбору приборов для капиллярного контроля
К списку статей
7 наиболее распространенных дефектов сварки, их причины и способы устранения
Дефекты распространены при любом производстве, в том числе при сварке. В процессе могут быть отклонения формы и размеров металлоконструкции. Это может быть вызвано использованием неправильного процесса сварки или неправильной техникой сварки. Итак, ниже мы узнаем о 7 самых распространенных дефектах сварки, их типах, причинах и способах устранения.
Трещина сварки
Наиболее серьезным типом дефекта сварки является трещина сварки, и она не допускается почти всеми стандартами в отрасли. Он может появиться на поверхности, в металле сварного шва или в зоне воздействия сильного тепла.
Существуют различные типы трещин в зависимости от температуры, при которой они возникают:
- Горячие трещины. Это может происходить в процессе сварки или в процессе кристаллизации сварного соединения.
Температура в этот момент может подняться более чем на 10000С.
- Холодные трещины. Эти трещины появляются после завершения сварки и снижения температуры металла. Они могут образоваться через несколько часов или даже дней после сварки. В основном это происходит при сварке стали. Причиной этого дефекта обычно являются деформации в структуре стали.
- Трещины кратера. Это происходит в конце процесса сварки до того, как оператор закончит проход сварного соединения. Обычно они образуются ближе к концу сварного шва. Когда сварочная ванна остывает и затвердевает, она должна иметь достаточный объем, чтобы преодолеть усадку металла шва. В противном случае образуется кратерная трещина.
Причины появления трещин:
- Использование водорода при сварке черных металлов.
- Остаточное напряжение, вызванное усадкой при затвердевании.
- Загрязнение основного металла.
- Высокая скорость сварки, но малый ток.
- Нет предварительного нагрева перед началом сварки.
- Плохая конструкция соединения.
- Высокое содержание серы и углерода в металле.
Способы устранения:
- Предварительно нагрейте металл по мере необходимости.
- Обеспечить надлежащее охлаждение зоны сварки.
- Используйте правильную конструкцию соединения.
- Удаление загрязнений.
- Используйте соответствующий металл.
- Убедитесь, что сварка имеет достаточную площадь сечения.
- Используйте правильную скорость сварки и силу тока.
- Чтобы предотвратить появление трещин в кратере, убедитесь, что кратер правильно заполнен.
Пористость
Пористость возникает в результате загрязнения металла шва. Захваченные газы создают заполненный пузырьками сварной шов, который становится слабым и со временем может разрушиться.
Причины пористости:
- Недостаточный раскислитель электрода.
- Использование более длинной дуги.
- Наличие влаги.
- Неправильный газовый щит.
- Неправильная обработка поверхности.
- Использование слишком большого расхода газа.
- Загрязненная поверхность.
- Наличие ржавчины, краски, смазки или масла.
Способы устранения:
- Очистите материалы перед началом сварки.
- Используйте сухие электроды и материалы.
- Используйте правильное дуговое расстояние.
- Проверьте расходомер газа и убедитесь, что он оптимизирован в соответствии с требованиями с правильными настройками давления и расхода.
- Уменьшите скорость перемещения дуги, что позволит выйти газам.
- Используйте правильные электроды.
- Используйте правильную технику сварки.
Подрез
Этот дефект сварки представляет собой образование канавки на кромке сварного шва, уменьшающую толщину поперечного сечения основного металла. Результатом является ослабление сварного шва и заготовки.
Причины:
- Слишком большой сварочный ток.
- Слишком высокая скорость сварки.
- Использование неправильного угла, который будет направлять больше тепла на свободные края.
- Электрод слишком большой.
- Неправильное использование газовой защиты.
- Неправильный присадочный металл.
- Неправильная техника сварки.
Способы устранения:
- Используйте правильный угол наклона электрода.
- Уменьшить длину дуги.
- Уменьшите скорость перемещения электрода, но она не должна быть слишком медленной.
- Выберите защитный газ с правильным составом для типа материала, который вы будете сваривать.
- Использование правильного угла наклона электрода, при котором больше тепла направляется на более толстые компоненты.
- Использование правильного тока, уменьшая его при приближении к более тонким участкам и свободным краям.
- Выберите правильную технику сварки, которая не требует чрезмерного переплетения.
- Использовать многопроходную технику
Неполное сплавление
Этот тип дефекта сварки возникает, когда отсутствует надлежащее сплавление между основным металлом и металлом сварного шва. Он также может появиться между соседними валиками сварного шва. При этом в стыке образуется зазор, не заполненный расплавленным металлом.
Причины:
- Низкое тепловложение.
- Поверхностное загрязнение.
- Неправильный угол наклона электрода.
- Диаметр электрода не соответствует толщине свариваемого материала.
- Слишком высокая скорость движения.
- Сварочная ванна слишком большая и опережает дугу.
Способы устранения:
- Используйте достаточно большой сварочный ток с соответствующим напряжением дуги.
- Перед началом сварки очистите металл.
- Не допускайте заливки сварочной дуги лужей расплава.
- Используйте правильный диаметр и угол электрода.
- Уменьшить скорость осаждения.
Неполное проплавление
Неполное проплавление происходит, когда канавка металла заполнена не полностью, что означает, что металл шва не полностью проходит через толщину соединения.
Причины:
- Слишком большое расстояние между свариваемыми металлами.
- Вы перемещаете буртик слишком быстро, что не позволяет достаточному количеству металла попасть в соединение.
- Вы используете слишком низкую силу тока, из-за чего сила тока недостаточна для плавления металла.
- Большой диаметр электрода.
- Несоосность.
- Неправильное соединение.
Способы устранения:
- Используйте правильную геометрию соединения.
- Используйте электрод подходящего размера.
- Уменьшить скорость перемещения дуги.
- Выберите правильный сварочный ток.
- Проверьте правильность выравнивания.
Шлак Включение
Шлаковые включения являются одним из дефектов сварки, которые обычно хорошо видны в сварном шве. Шлак представляет собой стеклообразный материал, который возникает как побочный продукт сварки электродом, дуговой сварки с флюсовой проволокой и дуговой сварки под флюсом. Это может произойти, когда флюс, который является твердым защитным материалом, используемым при сварке, плавится в сварном шве или на поверхности зоны сварки.
Причины:
- Неправильная очистка.
- Слишком высокая скорость сварки.
- Отсутствие очистки сварочного прохода перед началом нового.
- Неправильный угол сварки.
- Сварочная ванна остывает слишком быстро.
- Слишком низкий сварочный ток.
Средства правовой защиты:
- Увеличить плотность тока.
- Уменьшить быстрое охлаждение.
- Отрегулируйте угол наклона электрода.
- Удалите шлак с предыдущего валика.
- Отрегулируйте скорость сварки.
Брызги
Брызги образуются, когда мелкие частицы из сварного шва прилипают к окружающей поверхности. Это особенно распространено при дуговой сварке металлическим газом. Как бы вы ни старались, полностью избавиться от него не получится. Тем не менее, есть несколько способов свести его к минимуму.
Причины:
- Слишком высокая рабочая сила тока.
- Слишком низкое значение напряжения.
- Рабочий угол электрода слишком крутой.
- Поверхность загрязнена.
- Дуга слишком длинная.
- Неправильная полярность.
- Нестабильная подача проволоки.
Средства устранения:
- Очистите поверхности перед сваркой.
- Уменьшить длину дуги.
- Отрегулируйте сварочный ток.
- Увеличьте угол наклона электрода.
- Соблюдайте правильную полярность.
- Убедитесь, что у вас нет проблем с кормлением.
Итак, мы перечислили 7 наиболее распространенных дефектов сварки, их причины и способы устранения. При их обнаружении важно удалить их, чтобы предотвратить потерю свойств и прочности материала. Здесь вы также можете ознакомиться с нашим руководством по устранению дефектов сварки MIG.
Доля:
10 распространенных дефектов сварки, о которых следует знать.

Инженеры всегда признавали наличие несовершенств и работу с допусками. Допуск — это термин, определяющий степень приемлемости до несовершенства . Таким образом, любой допуск должен быть определен только для определенного применения, процесса и используемого материала.
Несовершенствами считаются любые различия в проекте сооружения. Они неизбежны в технике, но не все из них следует рассматривать как недопустимо .
В данной статье рассматриваются такие отклонения в отношении сварных швов.
Узнайте, какое отношение сентин имеет к сварным швам
Каковы основные категории дефектов сварки?
Дефекты, возникающие при сварке, можно разделить на три категории:
- Размерные Дефекты
- В сварном шве
- В зазоре
- 1
- 13 Неоднородности
- Несовершенства свойств материала
В этой статье рассматриваются дефекты, рассматриваемые как неоднородности, и содержится 10 распространенных дефектов.
Содержание
Что такое несплошности сварного шва?
Прерывистость – это нарушение типичной физической структуры материала, резко изменяющее свои свойства . Таким образом, простое изменение свойств не характеризует разрыв. Однако только несплошности, которые превышают предел допуска , следует рассматривать как дефекты сварки .
Таким образом, сварной шов с определенной трещиной может считаться одобренным или не одобренным для различных применений.
Что такое распространенные дефекты сварки?
Среди несплошностей, связанных с процессом сварки, можно выделить 10 видов:
- Непровар или неполный провар
- Непровар или непровар
- Подрез
- Брызги
- Шлаковые включения
- Трещины
- Пористость
- Перехлест
- Коробление
- Прожог
Узнайте, какое отношение сентин имеет к сварным швам
1.

неполное проплавление происходит, когда корень валика сварного шва не достигает корня стыка для сварки противоположной поверхности детали. Чтобы исправить эту неоднородность, вы можете увеличить силу тока, уменьшить скорость сварки или изменить геометрию соединения.
© Нуньес Р. 20202. Тип: несплавление
Неполное сплавление происходит с локальным несплавлением либо на стыковой кромке , либо на поверхности ранее наплавленной пряди . Чтобы исправить эту неоднородность, вы можете увеличить ток, уменьшить скорость сварки, изменить геометрию соединения или использовать некоторые хитрости, чтобы избежать магнитного дутья.
© Сантос А.Г.М. – 20193. Тип: Подрез
Встречается с углублением, как выемка , на ножке шнура . Чтобы исправить эту неоднородность, можно уменьшить силу тока или скорость сварки.
© Нуньес Р. 20204. Тип: Брызги
Брызги образуются при выбросе расплавленных частиц из валика сварного шва. Чтобы исправить этот разрыв, можно уменьшить ток и контролировать нестабильность переноса металла.
Ознакомьтесь со статьей о причинах и последствиях брызг при сварке.
© Сантос А.Г.М. – 20195. Тип: Шлаковое включение
Возникает при удерживании твердых материалов , металлических или нет, в металле сварного шва. Причины – недостаточная очистка поверхности сварного шва между проходами. Это также может произойти при однопроходных сварных швах, когда шлак попадает в корень и носки шва.
6. Тип: Трещины
Среди несплошностей металлургического происхождения можно отметить трещины, которые могут появиться в зоне воздействия сварного шва (зона плавления или зона термического влияния) из-за нескольких факторов, таких как сокращение затвердевающего металла и рост зерен, и могут быть классифицированы как холодные трещины, трещины затвердевания и трещины повторного нагрева.
7. Тип: Пористость
Происходит с образованием пузырьков газа, удерживаемых в зоне расплава. Это может происходить внутри, а также на поверхности. Для исправления этой неоднородности можно скорректировать расход защитного газа и использовать газы лучшего качества (с большей чистотой по своему составу).
8. Тип: Нахлест
Нахлест возникает, когда поверхность сварного шва выходит далеко за носок сварного шва . В основном это вызвано использованием слишком больших электродов или плохой техникой сварки.
9. Тип: Коробление
Коробление — это нежелательное изменение формы и положения металлических деталей. Это происходит при неправильном использовании тепла и вызвано сужением/расширением свариваемых деталей.
10. Тип: Прожог
Если металл шва проникает в основные детали , говорят о прожоге. Это обычная несплошность при сварке тонких деталей. Это происходит, когда корневое отверстие слишком велико или используется слишком большое напряжение.
Как найти дефекты сварки?
Неразрушающий контроль (НК)!
С целью утверждения сварного шва проводится несколько приемов, чтобы выяснить и доказать отсутствие дефектов, подвергающих сварную конструкцию риску. В отличие от разрушающих испытаний (ДТ), неразрушающие испытания (НК) направлены на возможность наблюдения несплошностей без нарушения сварной детали и проводятся на стадиях изготовления, строительства, сборки и технического обслуживания.
Узнайте, какое отношение сентин имеет к сварным швам
Неразрушающий контроль способствует контролю качества товаров и услуг, снижения себестоимости , сохранения жизни и окружающей среды , являясь конкурентным фактором для компаний, которые их используют. Помимо того, что он является фундаментальной частью для проведения исследований, основной целью которых является повышение показателей надежности промышленного оборудования.
При правильном применении неразрушающий контроль обеспечивает большую отдачу за счет экономии времени, снижения частоты отказов оборудования, повышения достоверности диагностики и повышения общего качества промышленного оборудования надежности .
Некоторые НК, поскольку они включают сложный анализ сигналов и изображений, становятся чрезвычайно сложными процессами, трудными для понимания неопытными операторами .
Пример: Ультразвуковой контроль — фазированная решетка
При обычном УЗ-контроле один преобразователь посылает в материал ультразвуковых волны . Датчики с фазированной решеткой содержат несколько преобразователей . Вводя задержку между импульсами, посылаемыми каждым преобразователем, можно влиять на угол луча, точку фокусировки и точку фокусировки фронта генерируемой волны.
Ультразвуковой контроль трубопровода
Ультразвуковой контроль с фазированной решеткой— это расширенное приложение. Его можно использовать для контроля сварных швов , обнаружения трещин и дефектов, измерения толщины и коррозии инспекции. Этот метод также можно использовать для анализа сварных швов в режиме реального времени.
Из-за подробной визуализации размера, формы, глубины и ориентации дефекта вместо рентгенографического контроля часто можно использовать фазированную решетку. Поскольку при этом не используется ионизирующее излучение, нет необходимости создавать зону безопасности, что обычно означает остановку производства.