Дефекты литья чугуна: Дефекты отливок из чугуна и стали по ГОСТ 19200-80 и их исправление
alexxlab | 10.02.2023 | 0 | Разное
5 типов дефектов литья и способы их предотвращения в вашей продукции
Как следует из названия, дефекты литья относятся к нарушениям, возникающим в процессе литья металла. В этом разделе мы обсудим различные дефекты литья в песчаные формы и их причины. Только так вы сможете предотвратить дефекты литья металла и избежать брака продукции. Это руководство начинается с 5 типов дефектов литейного литья и их причин, которые помогут вам определить, исправить и избежать проблем с литьем.
Дефекты литья металла и причины
Общие дефекты металлических отливок делятся на пять категорий: отверстия, трещины, поверхностные дефекты, неподходящие формы, размеры и вес, а также неподходящие компоненты, конструкции и свойства. (Примечание: в основном появляются дефекты стального литья, которые легко вызывают трещины)
1. Дефекты перфорированного литья
Дефекты стального литья отверстий включают поры, усадочные отверстия, усадочную пористость, шлаковые отверстия, трахому и железные бобы.
устьице
Также известен как газовые глазки, пузыри, дефекты литья отверстий, вызванные газом. Характеристики литейных пор: обычно круглые или неправильные отверстия, внутренняя поверхность отверстий гладкая, цвет белый или со слоем старого темного цвета.
Причинами дефектов литья являются: сырость или коррозия материала печи; поверхность не чистая, пар в топке газ и другие газы; корпус печи и ковш после ремонта не просушены; газ в полости и неправильная система заливки; газ участвует в литье, плохая проницаемость формы или керна и т. д.
Усадочная полость
Это дефекты литья отверстий, вызванные усадкой. Характерными чертами усадочной полости являются неправильная форма, шероховатость отверстия и крупные кристаллические зерна.
Причиной дефектов литья является усадка металла при разжижении и затвердевании. Основные моменты заключаются в следующем: неразумная конструкция литейной конструкции; неправильная система литья; размер, количество и местонахождение охлаждённого железа не соответствуют действительности; химический состав расплавленного чугуна не соответствует требованиям, например избыточное содержание фосфора. Температура заливки слишком высока, скорость работы слишком высока и т. д.
усадка
Также называется рыхлостью, сотовыми отверстиями, а также дефектами литья с небольшими отверстиями и множеством отверстий, вызванными сопротивлением усадке. Усадочная пористость характеризуется:
- Крошечные и разрозненные поры.
- Крупные кристаллические зерна с явными отверстиями сетки между кристаллическими зернами.
- Просачивание воды во время гидравлического испытания.
Подонок глаз
Дефекты литья шлакового отверстия также вызваны включениями шлака, шлаковым мешком, грязным глазом, низкой температурой расплавленного чугуна и неправильным литьем шлака. Характеристики шлакового отверстия: форма отверстия неправильная и не гладкая; отверстие полностью или частично заполнено шлаком.
Причинами дефектов литья являются: недостаточная чистота расплавленного чугуна; плохое удаление шлака и плохое удержание шлака при заливке; плохое удержание шлака литниковой системой, шибер не заполняется и не прорезается при заливке.
Трахома
Трахома – дефекты отливки трахомы с песком между ними. Характеристики трахомы: отверстия неправильной формы, отверстия заполнены формовочным песком или стержневым песком.
Причины дефектов литья: Формовочная смесь повреждается и отслаивается при закрытии коробки. Рыхлый песок или песчаные глыбы в полости не очищаются. Формовочная смесь имеет плохую плотность, при заливке разбивается стержень; неправильная конструкция литниковой системы, плохое покрытие поверхности сердечника и т. д.
Железные бобы
Железные бобы – это отверстия, в которых находятся железные шарики. Также известен как железная бусина, глаз фасоли, трахома железной фасоли и т. Д. Характеристики железной фасоли: отверстия относительно правильные, а отверстия содержат крошечные металлические шарики. Такие литейные дефекты часто встречаются в чугунных отливках.
2. Дефекты литья в виде трещин
Дефекты растрескивания стального литья включают дефект горячего разрыва, теплое растрескивание и дефект холодного закрытия.
Горячая трещина(дефект горячей слезы)
Литейные дефекты термического растрескивания возникают при более высокой температуре и вблизи температуры затвердевания. Характеристиками термического растрескивания являются проникающие или непроникающие трещины на отливке; она искривлена, а поверхность трещины окислена.
Причинами дефектов литья металла являются избыточное содержание серы или избыток примесей в железе; плохая производительность формы для литья в песчаные формы; неправильный контроль температуры заливки; жесткий переход перехода толщины стенки отливки; ворота, холодное железо, усадочные ребра, вентиляционные отверстия Неправильный размер и расположение и т. д.
Теплая трещина
Термический крекинг также называют термическим растрескиванием. Эти дефекты металлического литья вызваны неправильной резкой, сваркой или термической обработкой. Характерными признаками теплого растрескивания являются: наличие на отливке проникающих или непроникающих трещин; металлическая поверхность трещины окисляется.
Холодная трещина (дефект холодного закрытия)
Холодные трещины – это дефекты литья в виде трещин, возникающие при отливках при более низких температурах. Характеристиками холодного растрескивания являются проникающие или непроникающие трещины на отливке; она линейна, поверхность трещины не окислена.
Причинами дефектов литья (дефектов литья с изображениями) являются:
- Неразумная структура отливки, неравномерная толщина.
- Плохая производительность отливки формы для литья в песчаные формы или глиняного керна.
- Неравномерное охлаждение различных частей отливки, склонность самого сплава к высоким напряжениям.
3. Дефекты поверхностного литья
Поверхностные дефекты стального литья включают прилипание песка, рубцевание, включения песка и холодную изоляцию.
Холодная изоляция
В основном мы представляем холодную перегородку, которая может вызвать трещины в литье. Холодный отсек еще называют противопожарным, приемным огневым и так далее.
Характеристики холодной перегородки: на поверхности заготовки имеются неровные и очевидные линейные линии спада (существуют два вида проникающих и непроникающих).
Его форма маленькая, длинная и узкая, и он имеет тенденцию к развитию под действием внешней силы. Судя по характеристикам холодового барьера, повредить организм матери легко. Трещины, дефекты литья, вызванные жестким барьером, проявятся не сразу. При эксплуатации под действием трения и удара образуются усталостные трещины.
Причина дефектов литья:
Несколько ковшей и несколько точек разливаются одновременно, так что два металлических потока соединяются. Но неполное сплавление и отсутствие включений между ними отсутствуют, поэтому двухслойная металлическая связь непрочна; температура заливки слишком низкая, скорость заливки слишком низкая, а время заливки слишком велико. Сплав имеет плохую текучесть, слишком низкое содержание углерода и кремния и высокое содержание серы. Или несколько ковшей разливаются последовательно, и время отключения переднего и заднего ковша слишком велико; секция литья тонкая и длинная, поток расплавленного чугуна неблагоприятный, поток литья прерывается, песчаная литейная форма заканчивается, одноразового расплавленного чугуна недостаточно, а дополнительная заливка несвоевременна.
4. Дефекты металлического литья неквалифицированных размеров, формы и массы.
К дефектам металлического литья неквалифицированных размеров, формы и массы отливок относятся: мясистость, недостаточная заливка, выпадение песка, вздутие коробки, эксцентриситет, деформация, неправильная коробка, повреждение, несоответствие формы, размера и веса и др.
5. Дефекты литейного литья с неудовлетворительным составом и характеристиками.
К дефектам стального литья неквалифицированного состава и характеристик относятся неквалифицированный химический состав; неквалифицированная металлография; неквалифицированная сегрегация, чрезмерная твердость и неквалифицированные физико-механические свойства.
Обработка дефектов стального литьяОбработка дефектов стального литья более критична, особенно при работе с трещинами. Если не обратить внимание на какое-либо звено в процессе, это вызовет новые трещины. Поэтому мы должны обращать внимание на детали обработки, строго выполнять процесс и обеспечивать качество.
1. Принцип устранения дефектов в литейных стальных отливках:
Ремонт дефектов литья должен производиться без ухудшения качества изделия. Ремонт должен производиться в соответствии с действующими стандартами и соответствующими техническими регламентами. Например, разрешены ли к ремонту имеющиеся дефекты литья и соответствующие технические требования к их совершенствованию.
2. Способ обработки трещин стального литья.
Сварочный ремонт является одним из основных технологических процессов стального литья. Почти все дефекты литья на стальных отливках можно устранить сваркой. Широко применяется дуговая сварка.
Основные моменты сварочного ремонта: Для обеспечения качества сварочного ремонта следует тщательно очистить от липкого песка, оксидной окалины, включений и т. д. дефекты литья; открыть паз; выполнять предварительный подогрев перед сваркой и термообработку после сварки в зависимости от свариваемости стали.
(1) Остановить трещины и устранить трещины
Трещины могут быть устранены дуговой строжкой, шлифованием угловым шлифовальным кругом и методом холодной ликвидации методом ветряной мельницы. Предполагается, что устранение трещин основных частей должно быть максимально исключено с помощью холода, чтобы максимально уменьшить нагрев. Поверхностные трещины нельзя использовать в качестве трещиноостанавливающих отверстий. Глубина и ширина трещины относительно велики, и отверстие для остановки трещины диаметром 5-8 мм должно быть предварительно изготовлено в пределах 10 мм от конца трещины перед обработкой, чтобы предотвратить расширение трещины.
(2) Готовый паз и зазор
При ликвидации трещин в отливках заводского ремонта, посадочных местах рулевых тяг, буксов и т. д. сварные швы необходимо проваривать насквозь. Как правило, используется 60-градусный V-образный паз с зазором 2 мм. Для основных деталей, Т-образных соединений или угловых соединений с серьезными трещинами рекомендуется открыть 30-градусный V-образный паз на вертикальной пластине, чтобы обеспечить качество сплавления.
(3) Подготовка перед сваркой
Для борьбы с трещинами мы рекомендуем использовать щелочные электроды для повышения трещиностойкости и ударной вязкости. Перед сваркой требуется подогрев электрода до 200-250℃, а рабочая температура должна быть не ниже 150℃. Температура окружающей среды не ниже 5 градусов.
Требуется отшлифовать шлифовальный круг в пределах 20 мм от поверхности канавки и поверхности сварки. На рифленой поверхности не допускается наличие канавок более 2 мм. Поверхность металла свободна от масляных пятен, оксидов и ржавчины.
Перед сваркой стальную литейную матрицу рекомендуется предварительно подогреть. Лучше всего использовать общий предварительный подогрев. Если общий предварительный нагрев невозможен, можно использовать частичный предварительный нагрев. Диапазон местного предварительного подогрева составляет не менее трехкратной ширины сечения толщины сварного шва с обеих сторон сварного шва.
Сварочный процесс
Сварка должна выполняться квалифицированным персоналом, прошедшим испытание на сварку плоских поверхностей. При сварке следует выбирать разумную спецификацию сварки. При запуске дуговой сварки следите за тем, чтобы дуга не повредила поверхность отливки. Запрещается поджигать крюк в несвариваемой зоне. Свариваемые детали следует избегать искусственного обдува и сквозняков. Стыковой шов не может быть заполнен за один раз слишком сильно, и должна быть принята многослойная сварка, которая не должна быть менее трех слоев. Первый слой сварки сваривается электродом меньшего диаметра для предотвращения термических трещин. После сварки каждого слоя следует полностью удалить шлак перед пайкой следующего слоя. При сварке прослойка шва должна поддерживаться не ниже температуры предварительного подогрева. Для сварки более длинных швов более 200 мм следует использовать сегментный метод. Начальное и конечное положения дуги каждого слоя должны быть сдвинуты не менее чем на 20 мм. Старайтесь избегать слепых зон и терминальной дуги, которая начинается или заканчивается.
3. Сварочный ремонт чугунных деталей
Если такие дефекты литья, как поры, песчинки, шлаковые включения, трещины, течи на чугунных отливках не превышают допустимых пределов сварочного ремонта, они могут быть устранены сваркой. Однако сварочные характеристики чугуна плохие. После сварки часто появляются поры, деформация, легко ломается, трудно обрабатывается и другие проблемы. Поэтому при сварке и ремонте чугуна следует быть очень осторожным.
(1) Метод ремонта сваркой: Способ сварки чугуна обычно классифицируют по температуре предварительного нагрева заготовки.
(2) Холодная сварка называется холодной сваркой, если она не подвергается предварительному нагреву перед сваркой или только предварительно нагревается до температуры ниже 250 ℃; предварительный подогрев до 250~450℃ перед сваркой называется полугорячей сваркой; предварительный нагрев до 500~700℃ перед сваркой называется горячей сваркой.
ЗаключениеЗдесь мы представили основы пористости, усадки, материалов форм, заливки металла, металлургии и дефектов формы отливки. Включены конкретные примеры дефектов, которые могут возникнуть в отливках. Теперь, когда вы лучше знакомы с типами отказов, которые могут возникнуть при литье, вы готовы начать покупку? Если это так, вы можете проверить нашу подробную информацию. Или, если вы хотите ознакомиться с дополнительными отраслевыми руководствами, вы можете посетить раздел «Руководства» на нашем веб-сайте, чтобы получить полезную информацию, которая поможет вам совершать более выгодные покупки.
Дефекты ВЧШГ: причины и способы их устранения
На обрабатываемых поверхностях отливок допускаются любые дефекты в пределах припуска на механическую обработку. Допустимые без исправления дефекты оговариваются в технических требованиях чертежа отливки по согласованию с заказчиком. Дефекты отливок выходящие за пределы допустимых, подлежат исправлению. Вид, количество, размеры, расположение дефектов и способ их исправления оговариваются в заказе или другой нормативно-технической документации, утвержденной в установленном порядке. Метод исправления дефектов не должен ухудшать обрабатываемости отливок.
Возможные отклонения технологического процесса получения ЧШГ причины образования, способы их предупреждения и меры по устранению приведены в табл. 1.
Таблица 1.
Вид отклонения | Причины образования | Способы предупреждения | Меры по устранению |
1. Несоответствие механических свойств | |||
1.1. Высокая твердость (НВ) | Отклонение химического состава ВЧШГ от заданного. Высокая скорость охлаждения отливок. Ранняя выгрузка отливок из контейнера. Нарушен режим вторичного модифицирования. | Повысить содержание: углерода, кремния. содержание: марганца. хрома, магния. Снизить скорость остывания отливки увеличив расстояние между отливкой и стенкой контейнера. Увеличить длительность остывания отливки в форме перед выбивкой. Проверить качество инокулятора при несоответствии заменить, при соответствии — увеличить расход. | Отливки подвергнуть высокотемпературному отжигу |
1.2. Низкая твердость (НВ) | Отклонение химического состава ВЧШГ от заданного.![]() Низкая скорость остывания отливок. Нарушен режим вторичного модифицирования | Снизить содержание: углерода, кремния. Повысит содержание: марганца, хрома, магния, меди, никеля. Сократить длительность остывания отливки в форме перед выбивкой. Снизить расход инокулятора. | Подвергнуть отливки нормализации. |
1.3. Низкое относительное удлинение | Отклонение химического состава чугуна от заданного. | Снизить содержание: хрома, марганца. | Провести — низкотемпературный отжиг. |
1.4. Низкий предел прочности. | Отклонение химического состава ВЧШГ от заданного. | Повысить содержание: марганца, никеля, меди, молибдена. Снизить содержание кремния. | Подвергнуть отливки нормализации. |
2. Несоответствие микроструктуры | |||
2.![]() | Отклонение химического состава от заданного. Повышенное содержание серы в “исходном чугуне”. Некачественный комплексный модификатор. Высокая температура чугуна подвергаемого модифицированию. Присутствие элементов-деглобуляторов в “исходном чугуне”. Недостаточное количество введенного комплексного модификатора. Длительная разливка. | Повысить содержание магния в ВЧШГ. Подвергнуть “исходный чугун” десульфурации. Исключить из употребления шихтовые материалы с высоким содержанием серы. Проверить содержание магния в комплексном модификаторе. Снизить температуру модифицирования. Увеличить массу пригрузочного материала. Исключить из употребления шихтовые материалы с высоким содержанием элементов-деглобуляторов. Контроль правильности навески комплексного модификатора. Сократить длительность разливки до 10-15 мин. | |
2.![]() | Отклонение химического состава ВЧШГ. Высокая скорость кристаллизации и остывания отливок. Нарушение режима модифицирования. | Повысить содержание: углерода, кремния. Снизить содержание: хрома, марганца, магния. Увеличить длительность пребывания отливки в форме, увеличить расстояние между отливкой и стенкой контейнера. Увеличить расход инокулятора. | Подвергнуть отливки высокотемпературному отжигу |
3. Отклонение химического состава ВЧШГ от заданного | |||
3.1. Отклонение химического состава ВЧШГ от заданного | Усилить контроль за доводкой “исходного чугуна” до заданного состава. Исключить длительные простои после окончания корректировки “исходного чугуна” и началом модифицирования. ![]() | ||
3.2. Пониженное содержание магния. | Нарушение режима модифицирования. Использование мелких фракций модификатора. Низкое качество модификатора. | Понизить температуру модифицирования. Увеличить расход сфероидизирующего модификатора. Увеличить массу пригрузочного материала Использовать пригрузочный материал большей толщины. Увеличить крупность фракций модификатора и отсеять пыль. Заменить сфероидизирующий модификатор. | |
3.3. Повышенное содержание магния. | Нарушение режима модифицирования | Уменьшить расход сфероидизирующего модификатора. | Отливки подвергнуть высокотемпературному отжигу. |
4. Отклонение химического состава “исходного чугуна” от заданного | |||
4.1. Повышенное содержание марганца.![]() | Неправильно рассчитан состав шихты. Нарушение режима выплавки “исходного чугуна”. | Произвести перерасчет шихты. Усилить контроль за взвешиванием и использованием шихтовых материалов. | Снизить содержание марганца в “исходном чугуне” (введя в печь чушковой чугун с низким содержанием марганца). |
4.2. Пониженное содержание марганца. | Неправильно рассчитан состав шихты. | Произвести перерасчет шихты. Усилить контроль за взвешиванием и использованием шихтовых материалов. | Ввести в чугун ферромарганец. |
4.3. Повышенное содержание углерода. | Неправильно рассчитан состав шихты. Нарушение режима выплавки “исходного чугуна”. | Произвести перерасчет шихты. Усилить контроль за взвешиванием и использованием шихтовых материалов. ![]() | Ввести в чугун лом стальной или ферросилиций. |
4.4. Пониженное содержание углерода. | Неправильно рассчитан состав шихты. Нарушение режима выплавки “исходного чугуна. | Произвести перерасчет шихты. Усилить контроль за взвешиванием и использованием шихтовых материалов. | Ввести в чугун электродный бой или графитовую стружку. |
4.5. Повышенное содержание кремния. | Неправильно рассчитан состав шихты. Нарушение режима выплавки “исходного чугуна. | Произвести перерасчет шихты. Усилить контроль за взвешиванием и использованием шихтовых материалов. | Ввести в чугун лом стальной, электродный бой или графит. |
4.6. Пониженное содержание кремния | Неправильно рассчитан состав шихты. Нарушение режима выплавки “исходного чугуна. ![]() | Произвести перерасчет шихты. Усилить контроль за взвешиванием и использованием шихтовых материалов. | Ввести в чугун ферросилиций |
5. “Черные пятна” | |||
5.1. “Черные пятна” | Нарушение режима модифицирования. Высокое содержание серы в “исходном чугуне”. Нарушение режима заливки. *Плохо спечен пенополистирол в моделях или литниково-питающей системе. *Повышенная плотность моделей. | Снизить остаточное содержание магния до 0,03-0,05%. Использовать шихтовые материалы с ограниченным содержанием серы. Очистить металл от шлака, заливку производить при температуре предусмотренной техпроцессом. Неправильно выбрана литниково-питающая система. Изменить конструкцию литниковой системы. Обеспечить полное спекание моделей. Понизить плотность моделей и литниковой системы. |
* Только при получении отливок по газифицируемым моделям.
Об авторе
Олег Виноградов / https://on-v.com.ua/
Технический директор ООО «Полимер-инжиниринг», Агентства Литье ++, г. Киев, Украина; т.: +38 (096) 574-17-11; e-mail: [email protected]
21 Дефекты литья и способы их предотвращения в ваших изделиях
Имеются ли у ваших изделий дефекты литья? Хорошая новость в том, что их можно полностью предотвратить. Читайте дальше о причинах и предотвращении дефектов верхнего литья.
Ваша чугунная металлическая сковорода покидает завод с проколами, что приводит к множеству жалоб от ваших клиентов. Что случилось? Как вы могли предотвратить это?
Литейное производство представляет собой сложный многоэтапный процесс. Технический уровень каждого процесса сильно различается. Навыки оператора, управление качеством и оборудование могут повлиять на конечное качество отливки.
Ключом к предотвращению дефектов ваших литых изделий является установление четких ожиданий и допусков в отношении проблем с качеством вместе с вашим поставщиком ( , связанный с : Как опытные импортеры ограничивают дефекты продукции в 3 этапа [электронная книга] ).
Но прежде чем вы сможете это сделать, вам необходимо иметь четкое представление о различных типах дефектов литья и их причинах. Только в этом случае вы сможете предотвратить дефекты литья и избежать отправки бракованных изделий своим клиентам.
Прочтите или щелкните ссылки ниже, чтобы перейти к разделу, посвященному каждому из этих типов дефектов литья.
- Отверстия
- Подземное дыхало
- Открытые отверстия
- Открытая усадка
- Закрытая усадка
- Стрижка и стирка
- Фьюжн
- Выход из строя
- Набухает
- Капли
- Крысиные хвосты, вены и пряжки
- Металлический проход
- Горячий разрыв/трещина
- Горячие/твердые места
- Холодный затвор/нахлест
- Ошибки
- Холодные уколы
- Шлаковые включения (парша)
- Сдвиг/несоответствие
- Заусенец, ребро и заусенцы
- Деформация
Газовая пористость Дефекты литья и их причины
Газовая пористость возникает, когда металл захватывает газ (чаще всего азот, кислород или водород) во время литья.
Когда отливка остывает и затвердевает, образуются пузырьки, потому что твердая форма металла не может удерживать столько газа, сколько жидкая форма. Эти пузырьки появляются на отливке в виде округлых, круглых полостей или отверстий.
Существует три типа дефектов литья, связанных с газовой пористостью:
1. Проколы
Проколы, также иногда называемые пористостью ) часть пресс-формы, в плохо вентилируемых карманах.
Они обычно появляются вместе в большом количестве либо на поверхности, либо непосредственно под поверхностью отливки. Они всегда видны невооруженным глазом и не требуют оборудования для идентификации.
2. Подповерхностное дыхало
Дыхание или просто дыхало представляет собой более крупную полость, чем точечное отверстие.
На внутренней стороне отливки появляется подповерхностное дыхало, которое обычно не видно до окончания механической обработки.
Подповерхностные дыры трудно обнаружить до механической обработки, для этого требуется гармонический, ультразвуковой, магнитный или рентгеновский анализ.
3. Открытые отверстия
Эти отверстия появляются на поверхности отливки, и их легче обнаружить, чем подповерхностные отверстия.
Причины и предотвращение газовой пористости
Существует несколько причин дефектов полости.
- Плохая вентиляция формы и стержней
- Недостаточная сушка формы и стержней
Как можно предотвратить пористость газа?
Шрамы представляют собой неглубокие удары, возникающие на плоской поверхности, а волдыри представляют собой рубцы, покрытые тонким слоем металла.
- Чрезмерная влажность формовочной смеси
- Недостаточная газопроницаемость формовочной смеси
Возможные решения включают:
- Внедрить передовые методы флюсования и плавки: плавить металл в вакууме, в среде малорастворимых газов или под флюсом, предотвращающим контакт с воздухом
- Повышение газопроницаемости песка: более крупный песок имеет более высокую газопроницаемость
- Повышение проницаемости формы и стержней.
Дайте воздуху и газу выйти из полости пресс-формы
- Высушите формы и стержни перед использованием и храните в сухом месте
- Увеличение скорости затвердевания за счет снижения температуры металла во время литья
Дефекты литья в виде усадки и их причины
Усадка происходит из-за того, что металлы менее плотны в жидком состоянии, чем в твердом.
Усадочная полость представляет собой углубление в отливке, возникающее в процессе затвердевания. Усадочная пористость появляется с угловатыми краями по сравнению с круглыми поверхностями газовой пористости. Полости также могут сочетаться с дендритными изломами или трещинами.
Большие усадочные полости могут нарушить целостность отливки и привести к ее разрыву под нагрузкой.
Усадка может привести к двум типам дефектов литья.
4. Открытые дефекты усадки
Они открыты для атмосферы. Воздух компенсируется по мере образования усадочной полости.
Трубы представляют собой открытые усадочные дефекты, образующиеся на поверхности и внедряющиеся в отливку. Выемки представляют собой неглубокие открытые дефекты усадки, которые образуются на поверхности отливки.
5. Закрытые усадочные дефекты
Также известные как усадочная пористость , закрытые усадочные дефекты образуются внутри отливки. Макроусадку можно увидеть невооруженным глазом, а микроусадку — нет.
Закрытые усадочные дефекты обычно появляются в верхней части горячих точек или изолированных луж горячей жидкости.
Предотвращение усадочных раковин за счет улучшения структуры отливки
Сплавы всегда дают усадку при переходе из расплавленного состояния в твердое. Это связано с тем, что плотность литейного сплава в расплавленном состоянии ниже, чем в твердом состоянии.
Вы должны ожидать некоторую усадку во время затвердевания. Перед литьем учитывайте припуск на усадку в дизайне модели.
Предотвратить появление усадочных дефектов литья можно за счет улучшения общей структуры литья:
- Спроектировать проточную (литниковую) систему со стояками, обеспечивающими непрерывный поток расплавленного металла
- Увеличьте локальное рассеивание тепла за счет установки внутренних охладителей, охлаждающих ребер или охлаждающих змеевиков
- Уменьшите температуру литья, чтобы ограничить общий дефицит объема
Дефекты отливки материала формы и их причины
Дефекты отливки материала формы связаны с материалом формы, которым чаще всего является песок. Как правило, вы и ваш поставщик можете устранить эти дефекты литья и их причины, модифицировав литейную форму.
6. Порезы и промывки
Порезы и промывки представляют собой области избыточного металла. Они появляются, когда расплавленный металл разрушает формовочную смесь.
Вырез выглядит как низкий выступ вдоль поверхности тормозной поверхности, уменьшающийся по высоте по мере того, как он проходит от одной стороны отливки к другой.
Причины и предотвращение порезов и промывок
Порезы и промывки могут быть вызваны потоком расплавленного металла с высокой скоростью, в результате чего слишком много металла проходит через затвор.
Проще всего предотвратить порезы и мытье:
- Правильно спроектировав литниковую систему
- Повышение прочности формы и стержня
- Добавление дополнительных вяжущих в облицовочный и основной песок
7. Плавление
Плавление происходит, когда песчинки сплавляются с расплавленным металлом. Он выглядит как тонкая корка с хрупким стекловидным внешним видом, прочно прилипшая к отливке.
Причины и предотвращение плавления
Два основных фактора могут вызвать плавление:
Повышение огнеупорности формовочного материала и/или снижение температуры заливки расплавленного металла поможет предотвратить плавление.
8. Выбег
Выбег – это вытекание жидкого металла из формы, что приводит к неполной или отсутствующей отливке.
Неисправная форма или опока являются причиной вытекания.
Предотвращение биения и неполной отливки
Чтобы предотвратить этот дефект литья, спроектируйте литейную форму с точностью. Осмотрите и замените любые дефектные формы перед литьем.
Высокие температуры могут привести к чрезмерному износу пресс-формы. Используйте качественное сырье для вашей формы, которое может противостоять высоким температурам.
9. Свеллы
Свеллы являются расширением отливки. Вздутия обычно принимают форму небольшой гладкой выпуклости на вертикальной поверхности отливок.
Причины и профилактика отеков
Вздутие обычно возникает из-за неправильной или мягкой трамбовки формы или формы с низкой прочностью.
Формы должны быть сконструированы таким образом, чтобы выдерживать давление жидкого металла. В противном случае стенка пресс-формы может прогнуться или отойти назад, вызывая вздутие.
Использование прочной, правильно утрамбованной формы предотвращает вздутие.
10. Капли
Капли образуются, когда кусочки песка падают в металлическую отливку, когда она еще жидкая. Капли появляются в виде выступов неправильной формы на верхней (верхней) поверхности отливки.
Причины и предотвращение падений
Четыре возможные причины падений и меры по их предотвращению включают:
- Низкая прочность песка: Используйте песок более высокой прочности, если это ваш виновник
- Мягкая трамбовка: Обеспечьте жесткую трамбовку
- Недостаточное флюсование расплавленного металла : Надлежащее флюсование расплавленного металла удаляет примеси
- Недостаточное усиление выступов песка в своде : Укрепите выступы песка с помощью гвоздей или кляпов, чтобы решить эту проблему
11.
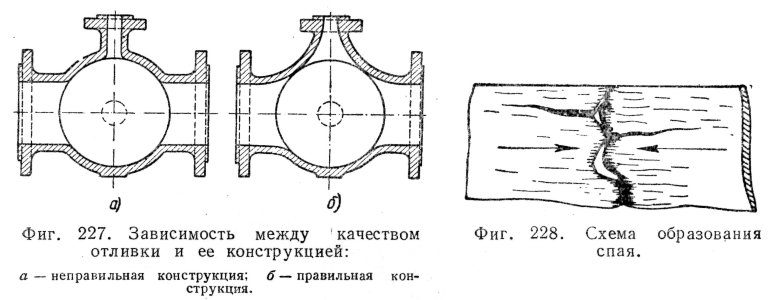
Крысиные хвосты или жилки появляются в виде неровной линии или трещины на отливке, когда поверхность формовочной смеси изгибается. Крысиные хвосты обычно образуются на поверхности дна формы, области, покрытой расплавленным материалом.
Пряжки являются более серьезной формой крысиных хвостов.
Причины и профилактика образования «крысиных хвостов» и «изгибов»
«Крысиные хвосты» и изгибов возникают, когда чрезмерный нагрев металла вызывает расширение песка. Это может быть вызвано:
- Плохое расширение песка : Добавлять в песок горючие добавки.
- Температура горячей заливки : Уменьшить температуру заливки металла.
- Плохая конструкция пресс-формы : Большие и плоские секции более склонны к образованию крысиных хвостов. Форма также не должна быть слишком твердой, так как она должна обеспечивать правильное расширение.
12. Проникание металла
Проникновение металла происходит, когда жидкий металл проникает в зазоры в формовочной смеси. Проникновение видно невооруженным глазом как шероховатая и неровная поверхность отливки.
Причины и предотвращение проникновения металла
Проникновение металла обусловлено:
- Использованием песка с низкой прочностью и высокой проницаемостью
- Использование крупных или крупных песчинок: чем крупнее песчинки, тем сильнее проникает металл
- Отсутствие смывки формы
- Мягкая утрамбовка песка
Предотвратите проникновение металла, зафиксировав эти участки. Используйте высокую прочность, мелкую зернистость, низкую проницаемость и жесткую трамбовку песка. Обеспечьте защитный барьер от проникновения металла, покрыв поверхность форм смывкой для форм.
Обычно проникновение металла можно удалить путем шлифовки шероховатой поверхности отливки.
Металлургические дефекты литья и их причины
Существует два типа металлургических дефектов, на которые следует обратить внимание.
13. Горячий разрыв/трещина
Трещины появляются в виде щелей неправильной формы с разветвленным рисунком.
Некоторые трещины очевидны и легко видны, в то время как другие требуют увеличения.
Трещины возникают по мере остывания отливки, ближе к концу затвердевания.
Причины и предотвращение горячих разрывов и трещин
Если затвердевающий металл не обладает достаточной прочностью, чтобы противостоять силам растяжения во время затвердевания, появятся горячие разрывы.
Горячие разрывы чаще всего возникают из-за плохой конструкции пресс-формы. Модификация пресс-формы для улучшения разборности может легко решить эти проблемы.
14. Горячие/твердые точки
Горячие точки — это точки, которые более твердые, чем окружающие области. Это потому, что они охлаждались быстрее, чем окружающий материал.
Твердые участки могут мешать обработке и увеличивать износ инструмента.
Причины и предотвращение появления горячих точек
Горячие точки являются прямым результатом неправильного охлаждения. Есть два возможных решения, если вашей проблемой являются горячие точки:
- Начните с исправления практики охлаждения
- Также рассмотрите возможность изменения химического состава металла
Дефекты заливки и причины их возникновения
Дефекты заливки металла возникают в процессе заливки металла в форму. Если у вас есть дефект заливки металла, он попадает в одну из следующих категорий:
15. Холодный затвор/нахлест
Холодный затвор — это тип поверхностного дефекта. Вы увидите линию или трещину с круглым краем на поверхности отливки.
Этот дефект виден невооруженным глазом и часто приводит к отбраковке гипса, так как создает слабое место.
Причины и предотвращение холодного закрытия
При попадании расплавленного металла в кристаллизатор через два литника потоки встречаются на стыке. Низкие температуры могут препятствовать сплавлению на стыке, заставляя потоки затвердевать перед сплавлением, создавая холодный затвор.
Холодное запирание обычно является результатом недостаточной текучести расплавленного металла или плохой конструкции литниковой системы.
Наилучший способ предотвратить холодное запирание – увеличить текучесть расплавленного металла. Это можно сделать несколькими способами:
- Оптимизация литниковой системы для минимизации узких перекрестных путей и обеспечения коротких путей потока
- Повышение температуры заливки для предотвращения преждевременного затвердевания
- Улучшение газопроницаемости пресс-формы (за счет более крупного размера зерна и т. д.)
16. Пропуски тесно связаны с холодными затворами
Пропуски возникают, когда жидкий металл слишком холодный, чтобы течь к краям полости формы перед замерзанием и затвердеванием.
Жидкий металл не полностью заполняет полость формы. Пропуск – это незаполненная часть или пространство в форме.
Причины и предотвращение несоответствия
Причины преждевременного затвердевания те же, что и при холодном закрытии. Если у вас ошибка, проверьте:
- Конструкция пресс-формы
- Конструкция литниковой системы и
- Текучесть расплавленного металла
17. Холодные уколы
Разбрызгивание во время наливания жидкости может привести к образованию твердых шариков.
Когда эти шарики замерзают, они застревают в отливке.
Холодная дробь обычно имеет форму шара, капли или жемчуга и свободно прикреплена к металлу.
Причины и предотвращение обморожения
Во избежание разбрызгивания и обморожения учитывайте
- Изменение процедур заливки для минимизации турбулентности
- Регулировка конструкции литниковой системы для уменьшения скорости ворот
18. Шлаковые включения (парши)
Металлические корки неправильной формы обнаруживаются на поверхности отливки. Струпья обычно имеют толщину всего несколько миллиметров, но их можно увидеть невооруженным глазом. Обычно они имеют острые края, неправильную форму и прочно скреплены с отливкой.
Струпья тесно связаны с крысиными хвостами и обычно появляются вместе. Удаление струпьев обычно обнажает под ними крысиный хвост.
Причины и предотвращение шлаковых включений
Шлаковые включения возникают, когда расплавленный металл, содержащий частицы шлака, заливается в полости формы и затвердевает.
Предотвращение включения шлака — это простое решение. Удалите частицы шлака из расплавленного металла перед его заливкой в полость формы.
Шлак можно удалить:
- Плавление металла с флюсом, в вакууме или в инертной атмосфере
- Добавление ингредиентов в смесь, чтобы шлак всплывал наверх, где его можно было легко увидеть и удалить перед заливкой. Либо использовать специальный ковш, заливающий металл снизу.
- Добавление керамического фильтра в литниковую систему
Дефекты формы отливки и их причины
Эти типы дефектов отливки связаны с общей формой окончательной отливки.
19. Смещение/несоответствие
Смещение формы происходит из-за несоосности верхней (корпус) и нижней (перетаскивания) частей формы. Смещение пресс-формы обычно отражается как горизонтальное смещение.
Смещение пуансона похоже на смещение формы, но смещается пуансон, а не форма. Сдвиг ядра обычно отражается как вертикальное смещение.
Причины и предотвращение смещения
Некоторые причины смещения могут включать:
- Ослабленные штифты коробки
- Штифты неточной схемы или
- Неосторожность при размещении накладки на тормозе, что привело к смещению
Если вы столкнулись со сдвигом, попробуйте проверить установку и выравнивание шаблона согласующей пластины. Убедитесь, что используете правильную формовочную коробку и закрывающие штифты.
20. Заусенцы, ребра и заусенцы
Заусенцы являются одним из наиболее часто встречающихся дефектов литья, а также частым дефектом литья под давлением.
Заусенцы, также известные как литейные плавники или заусенцы, представляют собой любой нежелательный и лишний материал, прилипший к отливке. Обычно это тонкий лист металла, который формируется на разделяющих поверхностях. Вспышка — это отходы, которые после переплавки превращаются в окалина.
Причины и предотвращение заусенцев, ребер и заусенцев
Заусенцы на поверхности отливки возникают из-за трещины или зазора на поверхности сердечника. Недостаточная нагрузка на форму или неправильный зажим опоки могут привести к образованию зазора.
Устраните эту проблему путем повторной сборки пресс-формы и стержней. На верхнюю часть формы должен быть достаточный вес, чтобы две части плотно прилегали друг к другу.
Вспышка может варьироваться от незначительной до очень серьезной. Если это не слишком серьезно, производители могут удалить заусенец, сломав его молотком или плоскогубцами и подпилив его до линии разъема. Однако это может быть дорогостоящим процессом.
21. Деформация
Деформация – это нежелательная деформация отливки, которая может возникнуть с течением времени и привести к изменению размеров конечного продукта. Это может произойти во время или после затвердевания.
Причины и предотвращение деформации
Деформация обычно является результатом разной скорости затвердевания разных секций, что вызывает напряжение в прилегающих стенах. Большие и плоские секции более подвержены короблению.
Нормализация термической обработки может снять остаточное напряжение в чугунном литье. Выпрямление между процессами закалки и старения может также потребоваться для алюминиевого литья.
Заключение
Знание дефектов литья и их причин необходимо для управления качеством литья.
Вы должны установить четкие допуски по дефектам и требования к качеству со своими поставщиками до начала производства, чтобы помочь им понять ваши стандарты качества.
Допуск на дефекты может варьироваться в зависимости от продукта и типа дефектов литья. Определение вашего допуска к этим дефектам литья может помочь вашему поставщику лучше понять ваши стандарты и предотвратить будущие недоразумения и проблемы с качеством.
В конечном итоге производитель должен строго контролировать качество каждого процесса литья. Опытные импортеры полагаются на проверки контроля качества, чтобы ограничить дефекты литья в своей продукции до того, как она покинет завод.
Есть ли у вас опыт устранения любого из этих дефектов литья? Поделитесь своими советами в разделе комментариев ниже!
Дефекты литья – песчаная форма, металлическое литье
Представляем различные металлы дефекты литья со многими фотографиями Dandong Foundry в Китай. Это общие дефекты литья в песчаные формы на поверхности и внутри чугунных и стальных литых деталей.
1. Отверстие и точечное отверстие
Это
является своего рода дефектом полостей, который также делится на
точечное и подповерхностное дыхало. Пинхол — это очень маленькое отверстие, некоторые из них видны на поверхности.
Подповерхностное дыхало можно увидеть только после механической обработки или шлифовки.
Большинство подповерхностных пузырей можно обнаружить после механической обработки или шлифовки. Если поверхность плоская, наш литейный завод в Даньдуне может проверить их с помощью ультразвукового дефектоскопа.
Точечный дефект
2. Дефект выгорания песка
Этот дефект включает химическое пригорание и проникновение металла. Обычно вы могли видеть дополнительные металлические материалы в угловых позициях. Это связано с плохим песком. Металл проник в песчаные формы.
Дефект выгорания песка
3. Включение песка и шлака
Эти дефекты также называются паршой или чернеющая парша. Это дефекты включения. Похоже есть шлак внутри металлических отливок.
Дефект включения песка
4. Дефект песчаной дыры
Песчаная дыра – типичный дефект усадочной полости. Вы могли видеть пустое отверстия после пескоструйной обработки или механической обработки. Песок высыпался из форм для песка, перекатывался в жидкий металл, а затем образовывал песчаные дыры.
Это проблема песчаной формы или слишком высокая скорость потока металла, поэтому ее могут решить литейные заводы.
Дефект песчаной ямы
5. Холодный притир Дефект
Его также называют холодным закрытием. Это трещина с круглым
края. Холодный притир возникает из-за низкой температуры плавления или плохого литникового затвора.
система. Это не просто поверхностный дефект. Обычно это положение может привести к утечке воздуха, кроме того, качество материала в этом положении будет очень низким, поэтому он может быть хрупким.
Дефект холодного притира
6. Заусенцы, ребра и заусенцы
Совместная заусенец также называется литейным плавником, который представляет собой тонкий выступ за пределы поверхности металлических отливок. Совместная вспышка должна быть удаляются в процессе очистки и шлифовки.
Острые ребра и заусенцы аналогичны проблемам с заусенцами. На самом деле, большой заусенец – это проблема литья, литейщик должен улучшить ее, изменив выкройки, но мелкие ребра и заусенцы не являются дефектами литья, литейщики просто должны их отшлифовать и удалить.
Пластина, плавник и заусенец
7. Дефект неправильного запуска
Это своего рода дефект неполного литья, который приводит к незавершенному литью. Край дефекта округлый и гладкий; плавный.
Дефект неправильного запуска
8. Пористость Дефект усадки
Дефекты усадки включают рассеянную усадку, микроусадку и пористость. При большой пористости на поверхности их было легко увидеть, а при малой рассеянной усадке их можно увидеть после механической обработки. На следующем фото показано уменьшение пористости. Плотность металла очень низкая, после механической обработки можно было увидеть много мелких отверстий.
Пористость Дефект усадки
9. Усадочные полости Дефект
Их также называют усадочными отверстиями, т.е. тип серьезного дефекта усадки, вы можете легко увидеть эти отверстия на шероховатой поверхности металлических отливок. Литейные заводы могли бы улучшить свои литниковые и вентиляционные системы, а затем решить эти проблемы с усадкой.
Усадочная полость Дефект
10. Усадочная депрессия
Этот дефект также является разновидностью усадочного дефекта, который имеет вид углубления на поверхности металлических отливок. Этот дефект не является серьезным, как усадочная полость, но все же вызывает плохое качество поверхности и может иметь некоторые внутренние дефекты, поэтому литейщики должны сделать все возможное, чтобы решить или улучшить его.
Усадочная депрессия Дефект
11. Дефект кожи слона
Тип поверхностного дефекта, вызывающий неравномерность или морщины формы поверхностей. Этот дефект вызван плохой температурой плавления металла или плохой песчаной формой.
Дефект кожи слона
12. Дефект вен
Его также называют крысиным хвостом, который похож на многие небольшие следы течения воды на поверхности металлических отливок. Иногда это происходит из-за низкой температуры расплавленного металла или из-за неразумной системы литников и вентиляции.
Дефект вен
13. Шероховатая поверхность
Шероховатая поверхность также является своего рода поверхностным дефектом.
Обычные шероховатые поверхности не могут быть оценены как дефекты, но слишком шероховаты. и неровная поверхность будет дефектом.
Дефект шероховатой поверхности
14. Несоответствие и дефект смещения
Этот дефект пресс-формы вызван смещением пресс-формы мигает. Это вызовет дислокацию на линии разъема. Вблизи линии разъема левая сторона может быть на несколько миллиметров ниже или выше другой стороны. Линия разъема не является дефектом, но если левая сторона имеет другую высоту, чем правая сторона, это будет один дефект литья. Если нет особых требований, допускается несоответствие менее 1 мм. Никакое несоответствие невозможно для процесса литья в песчаные формы.
Однако, если несоответствие повлияло на функцию отливок, то литейщики должны контролировать его, шлифовать или подвергать механической обработке в соответствии с требованиями.
Несоответствие дефекта пресс-формы
15. Механические повреждения
Это не дефект литья, а реальная проблема качества литья, с которой вы можете столкнуться. Это повреждение во время механической обработки или процессы доставки. Работники должны уделять больше внимания этой проблеме.
Механическое повреждение Дефект
16. Шлаковое включение Дефект
Этот дефект также называют экзогенным включением, захваченным шлак. Обычно шлак получают из расплавленного металла. В процессе плавки металла литейщики должны полностью удалять загрязнения и включения, иначе эти включения будут выливаться в отливки.
Дефект включения шлака
17. Дефект приподнятой формы
Из-за флотации жидкого металла
опоки формы приподняты, что привело к тому, что верхняя часть отливки стала
выше или толще нижней части.
Дефект выпуклой формы
18. Трещина Дефект
Трещина обычно возникает внутри металлических отливок. Этот дефект снизит физические свойства металлических отливок. На поверхности тоже есть трещинки.
Трещина Дефект
19. Аномальный узелковый дефект
Это также называется недостаточным узелковым дефектом. Из-за многих причинам сфероидизация графита для ковкого чугуна будет пострадавшие, следовательно, вызвали плохую скорость сфероидизации. Под металлоскопом можно увидеть очень мало графитовых шариков и много червеобразного графита.
Это материальная проблема. В этом случае его механические свойства не будут соответствовать требованиям стандарта, что может привести к поломке отливок в процессе эксплуатации.
Аномальный узелковый дефект
20. Дефект неравномерной твердости
Означает неравномерную твердость на одном и том же поверхности. Твердость неоднородна, некоторые позиции могут иметь сверхвысокую твердость. При обработке более твердых позиций обработка будет становиться сложнее. Сверло может сломаться.
Это материальная проблема. Место со сверхвысокой твердостью может остыть быстрее, чем локальные области.
Дефект неравномерной твердости
21. Дефект капли песка
Его также называют песчаной дробилкой. Некоторые блоки песка упали из формы для песка, поэтому они вызовут отверстия в песке аналогичной формы или
неполный. Это проблема песчаных форм. Песочные формы могут быть недостаточно плотными.
Дефект капли песка
22. Проблема деформации
Эта проблема приведет к слишком большому допуску плоскостности и прямолинейность. Это очень распространенный дефект для длинных отливок и плоских отливки с тонкой стенкой. Причины естественны деформация в процессе охлаждения в песчаных формах или на воздухе, иногда чрезмерная пескоструйная обработка также может вызвать эту проблему.
Проблема деформации
23. Проблема ремонта сварки
После ремонта сваркой, даже после механической обработки
или шлифовка, следы сварки все равно будут видны. Что касается
неважные литейные поверхности, если клиент разрешает ремонт сваркой,
то эти отметки должны быть приемлемыми. Но для высокого давления подшипника
позиции, или клиент явно запретил какой-либо сварочный ремонт,
то эти отметки будут считаться дефектами.
Знаки ремонта сварки
24. Метки холодного железа
Холодное железо может эффективно снизить
усадка для ключевых позиций, поэтому использование кокильного железа очень распространено
в чугунолитейных цехах. Тем не менее, края холодных утюгов могут быть
четко обнаруживается при визуальном осмотре. Некоторым клиентам не требуется
отшлифуйте их, если эти следы не влияют на внешний вид. Тем не менее
клиенты могут потребовать от производителя литья шлифовать их только
для улучшения внешнего вида поверхности. Пожалуйста, обратите внимание, что эти метки
не следует рассматривать как дефекты литья. Обратитесь к iron-foundry.com.
Метки холодного железа
25. Дефект охлаждения литья
Его также называют «белым железом». Поверхность отливок с этим дефектом будет быть очень белым, блестящим и гладким. Бракованные отливки будут хрупкими и хрустящими, поэтому при механической обработке некоторые края и кончики будет сломан. Этот дефект был вызван низкой температурой песчаные формы и преждевременно из песчаных форм, поэтому горячее железо быстро охлаждаться. Правильная отжиговая термообработка к ним может устранить этот дефект.
Дефекты охлаждения литья
26. Массивный свободный карбид
На фотографии металлографа можно увидеть много карбида без рыбьей кости. Это серьезный недостаток чугунный материал, обычно бывает с ковким чугуном. Из-за обратного дефекты охлаждения и плохая прививка, будет бесмассовая карбид, который сделает хрупкие, плохие сварочные свойства пластичными чугунные отливки. Высокотемпературная термообработка отжигом может улучшить его качество.
Массивный свободный карбид
27. Холодное короткое или короткое железо
Этот дефект также называют внутренней потливостью. Там
железные бобы в отливках. Это из-за необоснованного
конструкция ворот, из-за которой жидкое железо внезапно превратилось в бобы,
затем эти бобы были обернуты другими жидкими утюгами. Это
поверхностный дефект, но вызовет серьезные проблемы, если они расположены в ключе
позиции.
холодная короткая, короткая железная
28. Дефект зачистки
На поверхности очень тонкая железная пленка. отливки. Два слоя. Это из-за неразумной системы ворот, из-за чего существовали очень тонкие слои воздуха. Этот дефект является поверхностным дефект, поэтому обычно его можно стачивать. Однако следует отбрасывается, если он не просто на поверхности.
Дефект зачистки
29. Чугун Графит Флотация
Этот дефект является своего рода материальной проблемой. Это вызвано низкой температурой заливки и высоким содержанием углеродистого элемента.