Дробеметная очистка металла: Дробеметная обработка и особенности ее применения
alexxlab | 31.12.2022 | 0 | Разное
Дробеметная обработка и особенности ее применения
Дробеметные установки применяются для обработки отливок, поковок, штамповок, труб, длинных листов металла, проката, сварных конструкций и других крупногабаритных изделий из металла. В связи с этим они часто используются в литейной и трубопрокатной промышленности. Дробеметные установки активно используются для подготовки поверхностей к нанесению покрытий ( предпокрасочные операции ), удаления старых покрытий, а также коррозии и грязи.
Назначение дробеметной обработки в условиях единичного и массового производства:
- удаление ржавчины;
- удаление окалины;
- удаление формовочных масс;
- удаление лакокрасочных покрытий;
- подготовка поверхности под покраску;
- микроковка (наклеп) – поверхностное упрочнение;
- создание декоративного внешнего вида.
Как известно, практически все коррозийные и усталостные повреждения металла зарождаются на его поверхности. На ряду с очисткой металла дробеметная обработка позволяет придать обрабатываемому изделию дополнительную износостойкость и другие полезные свойства. Дробеметная и дробеструйная обработка – это процессы холодной обработки металла, суть которых заключается в бомбардировании поверхности металла небольшими шарообразными частичками. Каждый удар дроби вызывает деформацию поверхности металла (то есть оставляет на нем микроскопический след). Под обработанной поверхностью формируется слой с высокими сжимающими напряжениями, тем самым изделия, прошедшие дробеметную обработку надежно защищены от возникновения и зарождения трещин. Поскольку дробь, воздействуя на металл, образует на его поверхности равномерный слой с высоким напряжением, дробеметная (как и дробеструйная) обработка поверхности металла способствует значительному увеличению долговечности металлического изделия, уменьшают риск возникновения усталостных повреждений, коррозийного разрушения и коррозийно-механического растрескивания, а также риск некоторых других повреждений металла.
Кроме защиты металла, дробеструйная или дробеметная обработка также позволяют придать ему некоторые свойства – например, необходимую аэродинамичность, что активно используется в современном авиастроении.
Практические советы по применению дробеметных установок
- Во избежание больших колебаний в шероховатости применяйте дробь с высокой стойкостью.
- Дробеметная установка должна обслуживаться оператором, имеющим достаточный уровень знаний и соблюдать правила эксплуатации дробеметных и дробеструйных установок .
- Регулярно контролируйте рабочую смесь и параметры турбин.
- Добавляйте новую дробь своевременно и в нужном количестве.
- Производите ремонт узлов дробеметной установки и замену быстроизнашивающихся деталей своевременно.
Технология дробеструйной обработки – основана на передаче кинетической энергии турбины абразивному материалу. Абразивный материал разгоняется до скорости 80 – 100 м/сек и направленным потоком подается на обрабатываемую поверхность. Взаимодействие на высокой скорости абразивного материала с обрабатываемой деталью, вызывает поверхностное разрушение окалины, ржавчины и т.д. без деформации основного материала.
Дробеметная очистка металла – «ОХТА»
Металлические поверхности часто имеют следы ржавчины, масел, старых лакокрасочных покрытий. Качественная очистка профильного и листового металлопроката подразумевает полное удаление возможных загрязнений, ржавчины, окисления. Среди способов обработки – дробеметная (дробеструйная).
К преимуществам относят:
- высокую скорость проведения;
- упрочнение поверхности за счет созданного дробинками напряжения металла в верхних слоях;
- полное очищение поверхности от окислов (высокопрочной оксидной пленки, что важно перед проведением сварочных работ и нанесением антикоррозийных составов), от старых покрытий и масел.
Обрабатываемые детали поступают с помощью кран-балки в специальную камеру, где расположены дробеметы. Весь процесс обработки автоматизирован. Далее детали проходят окончательную очистку от остатков дроби, пыли. В качестве рабочей фракции применяют чугунную (стальную) дробь или другие абразивы.
Кроме очищения от загрязнений и окислов, дробеструйная обработка металла применяется для:
- удаления окалины, остающейся на металле в процессе заводской обработки;
- матирования или полировки металлических поверхностей;
- придания определенной степени шероховатости для дальнейшей обработки;
- лучшего сцепления антикоррозийных покрытий с поверхностью металла – после дробеструйной обработки обезжиривание металла не требуется;
- удаления оксидных пленок высокой прочности перед выполнением сварочных работ.
Благодаря высокой производительности и возможности любой степени очистки, дробеметные установки применяют на крупных предприятиях по изготовлению металлоконструкций и металлообработке.
Дробеметная установка для очистки металла
Дробеметная обработка представляет собой эффективный метод подготовки поверхности к дальнейшей эксплуатации. Для обеспечения сцепления последующего покрытия с обрабатываемой деталью дробеметную очистку осуществляют при температуре не меньше +10°С и относительной влажности воздуха от 65 до 75%.
ООО «ОХТА» использует дробеметную установку кранового типа УИД-376.
Характеристики:
Эффективный размер очистки (Ø мм) | 800 |
Эффективный размер очистки (высота мм) | 1500 |
Очистка со всех сторон | да |
Производительность (тонн/час) | 1 |
Мощность установки (кВт) | 22. |
Дробеметная установка производит очистку поверхности согласно ИСО 8501-1, степень очистки SA-2 – SA-2.5. Оборудование оснащено тельфером, что упрощает и ускоряет проведение работ, а также пылеуловителем. Для разных операций, проводимых с помощью дробеметной установки (шлифование, матирование, очистка или упрочнение металла) применяют дробь и абразивные частицы диаметром от 0,3 до 3,6 мм.
Стены камеры дробеметного оборудования обшиты высоколегированной сталью, специальный транспортер забирает со дна абразив, который направляется для вторичного использования (только целая дробь). Технология очистки с установкой
УИД-376 максимально проста и быстра. Деталь или лист металла помещается с помощью тельфера в камеру, далее происходит метание дроби (установка оснащена специальными лопатками).
Все процессы полностью автоматизированы и управляются компьютером, поэтому через заданное время, необходимое для завершения обработки, метание дроби прекращается, камера открывается. Благодаря продуманной конструкции установки на выходе качественный результат.
Очистка металла от ООО «ОХТА»
ООО «ОХТА» производит дробеметную и пескоструйную очистку металлических изделий в соответствии с установленным порядком и правилами.
В таблице ниже указана стоимость на услуги:
Дробеметная очистка металла | от 190 руб/м2 |
Пескоструйная обработка металла | от 350 руб/м2 |
Подробности узнавайте по телефону 8 (812) 645-51-15 или приходите в наш офис по адресу 195030, г. Санкт-Петербург, ул.Коммуны, д.67, лит. Ж, а/я 36. (территория завода “Пластполимер”).
Примеры:
Также мы предлагаем:
- Токарные работы на станках с ЧПУ
- Фрезерные работы (в том числе с ЧПУ)
- Шлифовальные работы
- Сверлильные работы
- Сварочные работы
- Слесарная обработка
- Гибка металла
Стальная дробь и песок для струйной очистки
Эффективное использование стальной дроби и песка для струйной очистки
E.
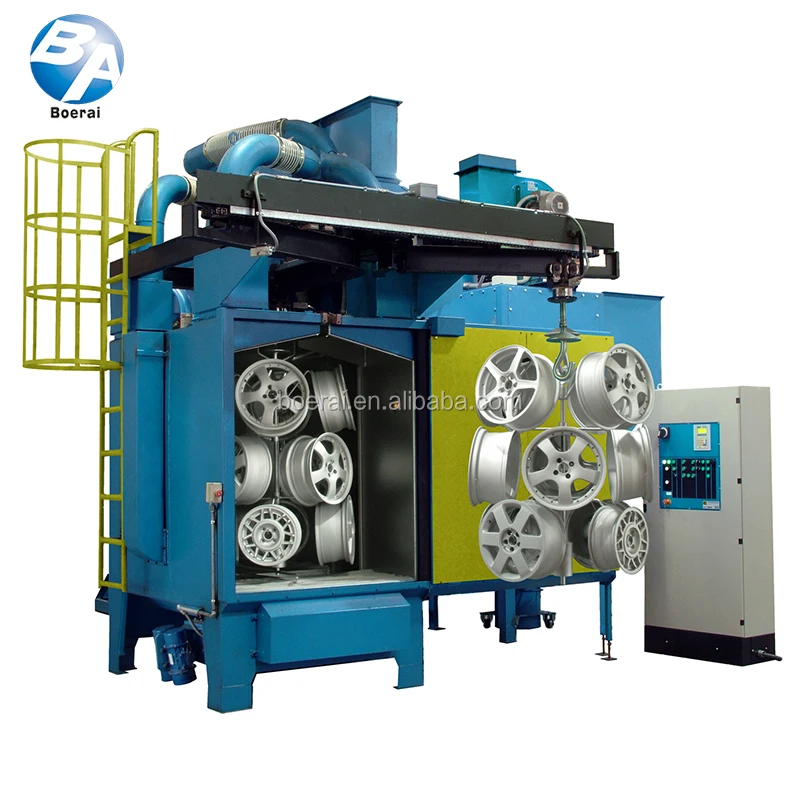
Важным условием эффективной и рентабельной операции струйной очистки является четкое базовое понимание характеристик абразивов для струйной очистки литой стали, их выбора и использования, а также знание оборудования для струйной очистки. , его техническое обслуживание и основные функции управления технологическим процессом.
Металлообрабатывающая промышленность является основным потребителем литой стальной дроби и крупки: сталелитейные заводы, литейные заводы черных и цветных металлов, кузнечные цеха и предприятия по производству металлов. Дробеструйная очистка стальными абразивами является жизненно важной и ответственной операцией на различных стадиях производства первичного металла. Основные функции, выполняемые пескоструйной очисткой, подразделяются на следующие категории:
- Удаление поверхностных загрязнений с получением абсолютно чистой поверхности, что помогает при проверке технологических дефектов.
- Подготовка поверхности: придайте поверхности профиль (травление, матирование или анкерный рисунок) перед дальнейшей обработкой, такой как покраска, покрытие, склеивание и т.
д.
Процесс пескоструйной очистки
Дробеструйную очистку стальной дробью лучше всего можно описать как ударную очистку, при которой поверхность заготовки подвергается последовательной бомбардировке высокоскоростной струйной струей, содержащей миллионы затвердевших частиц эффективного размера. литые стальные абразивные частицы. Влияние этого мощного потока взрывной волны на работу двоякое:
- Загрязнение разбито, измельчено и удалено, обнажая чистую девственную металлическую поверхность.
- Одновременно ударная сила отдельных стальных частиц придает чистой поверхности заготовки профиль отделки, внешний вид и текстура которого определяются выбором пользователем размера, твердости и формы стального абразива (дробь или зернистость).
Механика струйной очистки
При правильном использовании процесс струйной очистки не только будет эффективным для удовлетворения потребностей пользователей в качестве и целей, но также обеспечит оптимальную производительность и минимальные эксплуатационные расходы.
Опросы, проведенные группой Ervin Industries по пескоструйной очистке, показали, что семь из десяти пользователей этого процесса часто не соблюдают надлежащие методы работы. Результат: Некондиционное качество отделки, производительность на 33-50% ниже, чем должна быть, а эксплуатационные расходы на 50% и более выше, чем должны быть. Есть три ключевых рабочих параметра, на которые приходится 90% причин, по которым пользователям не удается добиться как эффективной очистки, так и приемлемых эксплуатационных расходов.
Цель этой статьи — познакомить пользователей с тремя переменными и описать простые и удобные меры контроля, необходимые для защиты от разрушительных проблем, которые они вызывают.
Учитывая, что сила удара отдельных стальных частиц выполняет двойную функцию удаления загрязняющих веществ и профилирования, необходимо понять, как сила удара сначала генерируется, а затем используется и контролируется, чтобы обеспечить эффективность и экономичность. -эффективные результаты. Конечно, можно видеть, что процесс должен представлять собой очень большую проблему для этих мощных мелких стальных абразивных частиц: размер
S-660 – 1/16 дюйма
размер S-70 – приблизительно 1/100 дюйма
Энергия удара стального абразива определяется его массой и скоростью в соответствии с уравнением кинетической энергии: KE = 1/2 МВ в квадрате.
Ключом к пониманию влияния выбора размера на фактор «массы» является то, что масса сферы изменяется пропорционально кубу ее диаметра.
Удвоение размера дроби увеличивает массу или силу удара дроби в восемь раз! И наоборот, удвоение размера дроби уменьшает количество гранул на фунт до одной восьмой.
Скорость определяется либо безвоздушным струйным оборудованием, в котором стальная дробь выбрасывается под действием центробежной силы от лопастного колеса (рис. 1), либо с помощью струйного оборудования, в котором абразив содержится и дозируется в поток сжатого воздуха посредством конвейера шланги и насадки для воздействия на заготовку. Скорость в центробежных струйных установках определяется диаметром колеса и числом оборотов в минуту. Стандарт 19Колеса диаметром -1/2 дюйма при 2250 об/мин развивают скорость абразива приблизительно 245 футов в секунду.
Рис. обнаружил, что скорость 245 футов в секунду эффективна для подавляющего большинства приложений струйной очистки. При использовании стандартных колес коэффициент скорости можно считать постоянным. Таким образом, сила удара, приложенная к заготовке, будет изменяться только в том случае, если масса Фактор (размер абразива) изменяется. Зависимость размера абразива от силы удара и покрытия показана на рис.0003
Сила удара: сколько?
Глядя на другую сторону медали, каковы характеристики загрязнителя, который необходимо удалить? Какая сила удара требуется?
До появления металлических абразивов пескоструйная очистка производилась с использованием песка в качестве среды, т. е. пескоструйной очисткой. Даже с легким песком удара было достаточно, чтобы удалить загрязняющее вещество и произвести травление. Размер по размеру, при той же скорости, стальной абразив имеет в 2-1/2 раза большую ударную силу, чем песок, а когда стальная дробь или крупка крупнее песка, его ударная сила будет во много-много раз больше, тем самым очищая быстрее и лучше.
Рассмотрим, например, оксидную накипь. Как правило, он твердый и ломкий. Если небольшой кусочек отколоть или отколоть, а затем слегка ударить молотком, он превратится в порошок. Для этого не требуется удар кувалдой (который также отлично справится с разрушением заготовки).
Проблема удаления большинства оксидных отложений заключается не в прочности и высокой стойкости к разрушению. В первую очередь это способ крепления к заготовке на границе между чистым металлом и первым слоем оксидной окалины. Абразив должен воздействовать на каждую долю каждого квадратного дюйма. Только забрасывая многие миллионы в минуту мини-молотков с шаровой головкой (дробь) или мини-зубил (песок) в заготовку, можно выполнить работу эффективно и экономично.
Эффективная рабочая смесь
Эффективная и экономичная рабочая смесь содержит должным образом сбалансированное распределение крупных, средних и мелких частиц. Крупные гранулы с максимальной силой удара должны быть достаточно большими, чтобы выполнять основную задачу по разрыхлению густых, плотно прилипших загрязнений и при этом обеспечивать приемлемый профиль отделки. Мелкие частицы обеспечивают покрытие, необходимое для быстрого удаления более легких загрязнений, а также для очистки и удаления ржавчины и т. д. в мельчайших ямках и щелях, недоступных для крупной дроби или песка.
Выбор новой дроби или зернистости исходного размера для использования автоматически определяет, насколько большими будут самые большие частицы в рабочей смеси. Что определяет, насколько маленькими должны быть самые маленькие частицы? Во-первых, все загрязняющие вещества (оксидная окалина, песок, отработанный абразив и т. д.) не должны попадать в рабочую смесь. (Всего 2% песка в рабочей смеси может привести к двойному износу компонентов дробеметной машины.) Система сепаратора и пылеуловителя, ее состояние и работа определяют, что удаляется, а что остается в системе!
Насколько мелкими могут быть абразивные частицы, которые при этом помогают в очистке? Возможно, на этот вопрос лучше всего ответить, указав, что дробь размером до S70 эффективна для удаления стойкой оксидной окалины с горячекатаной полосы из нержавеющей стали.
Разработка комплекса работ
При разумной помощи в виде надлежащих методов работы Мать-природа разработает хорошо сбалансированный комплекс работ. В то время как песок в качестве среды для струйной очистки не мог выдержать даже одного удара по заготовке, стальная дробь и песок выдерживают многие сотни ударов, прежде чем окончательно погибнут.
Первым эффектом ударного воздействия является упрочнение поверхности стальной частицы, что приводит к отслаиванию/отслаиванию, показанному на рис. 3. Этот эффект «луковой кожуры» может привести к уменьшению диаметра гранулы. стать на один-два размера меньше, чем в новом состоянии.
Рис. 3. Отслаивание/отслоение стальной дроби
Во время фазы отслаивания/отслаивания окатышам наносятся серьезные внутренние повреждения, о чем свидетельствуют пустоты и разрывы, которые в конечном итоге пробиваются на поверхность и вызывают разрушение. отказ. Раздробленные частицы удивительным образом при последующих повторяющихся ударах подвергаются холодной обработке или выковке в сферы меньшего диаметра, которые в конечном итоге снова распадаются на еще более мелкие частицы.
Именно эта комбинация событий создает рабочий микс. Эта смесь новых, почти новых, очищенных от луковой шелухи и сломанных частиц составляет необходимый баланс надлежащего воздействия и покрытия. Распределение размеров рабочей смеси для плитки будет подвергаться постоянным изменениям по мере того, как отработанная мелочь выводится из системы и вносятся новые абразивные добавки (достаточно часто, чтобы рабочая смесь не колебалась от слишком мелкой до слишком грубой).
Принимая во внимание огромные различия в воздействии в зависимости от размера дроби на рис. 2, становится очевидным, что управление распределением размеров в рабочей смеси струи дробеструйной обработки должно быть первоочередной задачей для группы уборщиков помещений пользователя.
Несбалансированные рабочие смеси
Рабочая смесь с преобладанием мелких частиц имеет недостаточную силу удара, чтобы быть эффективной (слишком мало крупных гранул для разрушения густого загрязнения). И наоборот, рабочая смесь с преобладанием крупных гранул имеет малое количество гранул, что приводит к широкому открытому рисунку, требующему гораздо больше времени для выполнения работы.
Несбалансированные рабочие смеси, требующие увеличения времени дробеструйной обработки или снижения скорости линии и/или повторной дробеструйной обработки, оказывают серьезное неблагоприятное воздействие на отделку продукта, производительность и эксплуатационные расходы.
Контрольный список устранения неполадок
Рабочая смесь слишком грубая: причины
- (a) Большие и редкие добавления нового материала.
- (b) Избыточное количество воздуха через сепаратор, вытягивающее средние и мелкие абразивные частицы.
- (c) Чрезмерный вынос с работой, требующий интенсивного пополнения.
Рабочая смесь слишком мелкая: Причины
- (a) Плохое распределение по пластине зева.
- (b) Недостаточно воздуха через сепаратор.
- (c) Чрезмерный промежуток времени между добавлениями.
- (d) Крупные спорадические добавления переработанного абразива из-за разлива пола или утечки из системы.
Контроль рабочей смеси
- Добавляйте новый абразив каждую рабочую смену. Всегда держите бункер подачи на уровне 3/4 или выше.
- Не допускайте скопления рассыпания или утечки абразива; возвращаться в систему ежедневно.
- Еженедельно проверяйте распределение размеров рабочей смеси. Рекомендуется: используйте прибор Ervin Spot-Check Gauge (рис. 4), который требует менее пяти минут для использования и обеспечивает мгновенную обратную связь, показывающую, находится ли рабочая смесь в надлежащем состоянии.
Рис. 4. Прибор для выборочной проверки Ervin
Взрывная струя… Попадание в цель?
Неправильное направление потока струйной очистки, при котором часть абразива не попадает в работу и вместо этого воздействует на изнашиваемые детали оборудования, приводит к следующим проблемам:
- Неполное удаление загрязняющих веществ
- Чрезмерный износ деталей
- Чрезмерное время простоя машины
- Избыточное использование абразива
- Более низкая производительность из-за увеличения времени дробеструйной обработки или повторной дробеструйной обработки
На вопрос: «Когда вы в последний раз проверяли схему взрыва и как часто это делается?» — большинство пользователей не знали, никогда не видели, как это делается. Другие посчитали это излишним, потому что «установка колесного циферблата там, где она всегда была». Обследования оперативной группы Эрвина выявили целых 7 из 10 взрывных волн с нецелевыми потоками — рис. 5. Даже 10-процентное отклонение направления струи от правильного направления может привести к 25-процентному снижению эффективности очистки.
Рис. 5. Плохо направленная струя струи
Необходимо признать, что неизбежный фактор износа компонентов струйной турбины в конечном итоге вызовет изменение местоположения и концентрации струи струи. Исключительная устойчивость к износу заложена в дробеструйном оборудовании, но когда износ превышает этот допуск, компоненты больше не могут работать должным образом, и схема дробеструйной обработки отклоняется от цели.
Рассмотрим колесо мощностью 40 л.с. Каждую минуту 1000 фунтов абразива проходят через крыльчатку, выходят из отверстия управляющей клетки и затем сбрасываются с лопастей. Крыльчатка: Когда износ передней кромки сегментов крыльчатки превышает 1/8 дюйма, абразив ударяется о заднюю часть лопасти, а не попадает на поверхность метателя. Горячая точка и общая картина струи становятся плохо рассеянными. Плохая цель! Контрольная рамка: Когда износ скошенной кромки превышает 1/2 дюйма (в некоторых случаях только 1/4 дюйма), площадь струйной очистки удлиняется, часто до такой степени, что часть абразива не попадает в работу. Лезвия: Когда лезвия становятся глубоко канавчатыми, происходит желобообразование абразива, а из-за того, что он не протекает по всей ширине лезвия, рисунок искажается.0102 Посторонние металлы: При заклинивании между рабочим колесом и клеткой управления посторонние металлы могут вызвать смещение клетки и схемы струйной очистки.
Проверка схемы дробеструйной очистки
Подумайте, где находится очищаемая поверхность заготовки по отношению к дробеструйному колесу. Цель состоит в том, чтобы поместить и закрепить мишень из листового металла в месте расположения заготовки, а затем, после струйной обработки в течение 10, 20 или 30 секунд, проверить, чтобы увидеть область и расположение картины струйной обработки. Горячая точка (горячая на ощупь, обычно размером около 3 x 10 дюймов) должна располагаться примерно на 8 дюймов впереди центральной линии колеса. Это область концентрации максимальной интенсивности.
В то время как проверка степени износа компонентов должна быть плановой (каждые восемь (8) часов работы), определение точной степени износа в сравнении с критическим допустимым износом в лучшем случае затруднено. Слишком часто суждения ошибочны. Еженедельная проверка схемы взрывов — это надежная процедура, которая прямо сейчас сообщает вам, соответствует ли схема взрыва цели.
Недостаточный поток абразива
Амперметр: Это чувствительное устройство регистрирует амперную нагрузку на двигатель, приводящий в движение дробемет. Это единственный практичный способ определить, сколько абразива выбрасывается кругом во время цикла струйной очистки. Максимальная эффективность дробеструйного оборудования достигается только при выбросе кругом расчетного максимального количества абразива (рис. 6).
Рис. 6. Амперметр при полной нагрузке Рис. 7. Низкое значение амперметра
Когда время цикла струйной обработки или линейная скорость основаны на номинальном максимальном расходе, но амперметр показывает ток меньше полной нагрузки (Рис. 7), происходит неполное удаление загрязнений. Когда для улучшения очистки увеличивается время цикла дробеструйной обработки, снижается скорость линии или требуется повторная дробеструйная обработка, производительность снижается, а затраты резко возрастают.
Низкий ток — Причины:
- Непонимание того, что амперметр является чувствительным устройством в неблагоприятных условиях эксплуатации, может привести к отказу и неточности. Что делать: регулярно калибруйте все амперметры. Обязательно держите их в хорошем рабочем состоянии.
- Неспособность установить и разместить целевые значения силы тока при полной нагрузке прямо над амперметром, чтобы операторы полностью знали, какими должны быть показания силы тока.
Что делать: Разместите показания силы тока при полной нагрузке над амперметром и убедитесь, что они всегда хорошо видны.
- Уровень бункера слишком низкий. Что делать: Абразивные добавки, добавляемые каждую рабочую смену; всегда поддерживайте бункер подачи не менее чем на 3/4.
- Чрезмерный износ крыльчатки, который может привести к затоплению желоба колеса, так как крыльчатка теряет способность справляться с потоком абразива. Что делать: Ежедневно проверяйте износ рабочего колеса. Когда передние кромки изношены более чем на 1/8 дюйма, замените рабочее колесо.
- Проскальзывание ремня: На приводе от двигателя к колесному валу – передача мощности упадет ниже нормы. На лентах элеватора – элеватор не может подать необходимое количество абразива. Что делать: Регулярно проверяйте ремни.
- Посторонний материал в системе, препятствующий прохождению абразива через экраны скальпа, башмаки элеватора, водостоки.
Что делать: Не допускайте попадания мусора в оборудование для пескоструйной очистки.
Выявление проблем
Ключ к эффективной и экономичной пескоструйной очистке заключается в способности распознавать проблемы по мере их возникновения. Это можно сделать с помощью описанных быстрых и простых системных проверок. Образование важно для понимания используемых инструментов и их функций, а также делает рабочие данные более значимыми для работника.
Твердое базовое понимание принципов пескоструйной очистки в сочетании с дисциплиной в следовании программе оценки эффективности (SPC) сделает отдел абразивоструйной очистки эффективной и рентабельной частью любой операции.
Очистка стальных поверхностей абразивоструйной очисткой
26 апреля 2019 г. – Группа КУЭ
Абразивоструйная очистка часто называется пескоструйной, дробеструйной или пескоструйной очисткой и является наиболее эффективным способом очистки стальных поверхностей при подготовке к последующему неразрушающему контролю или нанесению красок, покрытий или облицовки.
Абразивоструйная очистка является коммерчески выгодной альтернативой ручной очистке и позволяет сэкономить до 75% времени по сравнению с другими методами очистки. Сами абразивные материалы относительно недороги и в некоторых случаях могут быть переработаны и повторно использованы для дальнейшего снижения затрат.
В этой статье мы стремимся повысить осведомленность о стандартах подготовки стальных поверхностей, обычно используемых в Великобритании и Европе. В других местах часто упоминаются NACE и SSCP, и они будут рассмотрены и сравнены в следующей публикации.
BS EN ISO 8501-1:2007 — это визуальная оценка чистоты поверхности, которая определяет ряд степеней ржавчины и степеней подготовки стальных поверхностей. Различные сорта определяются письменными описаниями вместе с фотографиями и кратко изложены ниже.
Степени ржавчины
A) Поверхность стали в значительной степени покрыта налипшей прокатной окалиной, но ржавчины мало, если она вообще есть.
B) Стальная поверхность, которая начала ржаветь и с которой начала ржаветь прокатная окалина.
C) Стальная поверхность, с которой прокатная окалина стерлась или с которой ее можно соскоблить, но с небольшой точечной коррозией, видимой при обычном зрении.
D) Стальная поверхность, на которой проржавела прокатная окалина и на которой при обычном зрении видна общая точечная коррозия.
Подготовка поверхности пескоструйной очисткой Обозначается буквами «Sa»
- Sa1: Легкая пескоструйная очистка – При осмотре без увеличения поверхность должна быть свободна от видимых масел, жиров и грязи, а также от слабо приставшей прокатной окалины , ржавчина, лакокрасочные покрытия и посторонние вещества.
- Sa2: Тщательная пескоструйная очистка – При осмотре без увеличения на поверхности не должно быть видимых следов масла, жира и грязи, а также большей части прокатной окалины, ржавчины, лакокрасочных покрытий и инородных тел.
Любое остаточное загрязнение должно быть прочно прилипшим.
- Sa2½: Очень тщательная пескоструйная очистка – При осмотре без увеличения на поверхности не должно быть видимых следов масла, жира и грязи, а также прокатной окалины, ржавчины, лакокрасочных покрытий и посторонних частиц. Любые оставшиеся следы загрязнения должны проявляться только в виде незначительных пятен в виде пятен или полос.
- Sa3: – Дробеструйная очистка до визуально чистой стали – При осмотре без увеличения на поверхности не должно быть видимых следов масла, жира и грязи, а также прокатной окалины, ржавчины, лакокрасочных покрытий и инородных тел. Он должен иметь однородный металлический цвет.
Достижение правильной отделки
Мы предлагаем услуги по подготовке стальной поверхности на заказ в зависимости от исходного состояния вашей стальной поверхности и требуемой степени подготовки. Мы используем различные инструменты для достижения этих результатов самым быстрым и экономичным способом, в том числе специально построенные дробеструйные камеры и мобильные дробеструйные установки.