Дуга сварка: Электрическая дуга | Сварка и сварщик
alexxlab | 23.12.2021 | 0 | Разное
Что такое дуговая сварка – определение
Справочник сварочных определений и терминов – Shindaiwa
Shindaiwa в Украине, поставки сварочного оборудования из Японии
Определение понятия. Классификация. История
Дуговая сварка – процесс сплавления материалов, при котором нагрев осуществляется электрической дугой. Температура электрической дуги (до 7000 °С) превосходит температуры плавления всех существующих металлов.
По степени механизации различают следующие виды дуговой сварки:
- ручную (ММА -Manual Metal Arc), при которой операции, необходимые для образования шва, выполняются человеком вручную без применения механизмов.
- механизированную (полуавтоматическую) (MIG/MAG -Metal Inert/Active Gas). Последняя выполняется плавящимся электродом с автоматизированной подачей электродной проволоки в сварочную зону, а остальные операции этого процесса остаются ручными.
- автоматическую дуговую, при которой механизируются операции по возбуждению дуги, поддержанию определённой длины дуги, перемещению дуги по линии наложения шва; при этом режим сварки (ток, напряжение, скорость перемещения дуги и др.
Применительно к сварочным аппаратам и агрегатам, виды дуговой сварки соотносят с режимами сварки. (Смотрите режимы для сварочных агрегатов DGW310, DGW400, DGW500).
По типу сварочной дуги различают:
- прямого действия (зависимую дугу) – дуга горит между электродом и основным металлом, который также является частью сварочной цепи;
- косвенного действия (независимую дугу) – дуга горит между двумя электродами.
По свойствам сварочного электрода различают способы сварки: плавящимся электродом и неплавящимся электродом (угольным, графитовым и вольфрамовым).
В настоящее время дуговая сварка покрытыми электродами, плавящимся и неплавящимся электродами в защитных газах, а так же дуговая сварка под флюсом широко применяются в различных отраслях промышленности.
Историческая справка о процессе дуговой сварки.
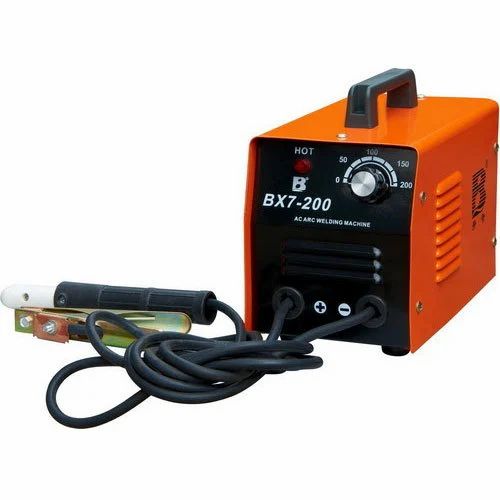
Явление вольтовой электрической дуги в 1802 г. открыл В. В. Петров – русский физик-экспериментатор, электротехник-самоучка, основоположник отечественной электротехники.
Изобрёл электрическое сваривание с применением угольных электродов русский инженер Н. Н. Бенардос в 1882 году, которое запатентовал в Германии, Франции, России, Италии, Англии, США и других странах, назвав свой метод «электрогефестом».
В 1888 г. другой русский инженер Славянов Н. Г. предложил производить дуговую сварку плавящимся металлическим электродом. Он создал первый сварочный генератор, предложил флюсы, позволяющие получить высококачественные сварные швы.
Шведский инженер Оскар Кельберг в 1907 году создал первый покрытый электрод. При сварке покрытыми электродами использовался постоянный ток, получаемый от сварочных генераторов. Сварку покрытыми электродами на переменном токе стали применять начиная с 20-х годов XX-го столетия.
В 30 – 40-х годах прошлого столетия был разработан способ полуавтоматической и автоматической сварки под флюсом, позволяющий повысить производительность процесса сварки в несколько раз.
Дата публикации: 18 06 2018 ✎
Дата последнего изменения: 29 05 2020
Похожие статьи о сварке
Дуговая сварка со струйным переносом металла с импульсным управлением
Скачать PDF |
Технология, сферы применения и преимущества нового принципа дуговой сварки
В связи с ростом стоимости сырья производители стали и присадочного металла стремятся уменьшить долю дорогостоящих сплавов в своей продукции или заменить их на более экономичные аналоги. Однако, изменение состава металлов требует новых программ сварки и сварочных технологий для различных условий дуговой сварки. Компания Fronius, ведущий разработчик сварочных технологий и техники, предоставляет подробные сведения о порядке программирования сварочных параметров, а также о технологических решениях, областях применения и преимуществах новой системы PCS (дуга со струйным переносом металла с импульсным управлением).
В базе данных компании Fronius, в настоящее время, хранится около 1300 готовых программ с различными параметрами сварки. Применение этих программ способно решить практически любые промышленные задачи. Тем не менее, иногда требуется задать совершенно новую сварочную программу. Такая ситуация может возникнуть, например, при использовании новых присадочных металлов, защитных газов или диаметров сварочной проволоки, характеристики которых пока отсутствуют в базе данных. Новые сварочные программы могут также потребоваться для оптимизации сварочных процессов за счет повышения скорости сварки, изменения глубины проплавления или внешнего вида шва. В первой части настоящего документа рассмотрены переменные сварочного процесса и принципы работы; вторая часть содержит описание технологии, областей применения и преимуществ новых параметров PCS. Новый набор параметров обеспечивает существенное повышение стабильности сварки, получение намного более высоких результатов сварки и значительно меньшей доработки деталей при соединении листов из низколегированной стали.
Настройка параметров сварки
«Цифровая революция» навсегда изменила сварочные технологии. Одним из пионеров данного процесса является компания Fronius австрийский производитель сварочных систем. Выпускаемые данной компанией системы оснащаются цифровыми процессорами и средствами графического отображения синергических параметров дуги. Это открывает совершенно новые возможности по контролю и управлению сварочным процессом. В результате точность и воспроизводимость результатов сварки заметно повышаются. Основным принципом данного подхода является определение, задание и воспроизведение параметров сварки в электронной форме. На практике очень удобно иметь под рукой актуальные значения параметров, которые могут быть автоматически отрегулированы в любое время для получения требуемого качества сварного соединения. Цифровые сварочные технологии обладают именно этим свойством, позволяя сварщикам точно настраивать системы для работы с различными материалами, присадочными металлами, защитными газами и технологическими условиями. Вместо внесения глубоких изменений в аппаратную часть источника всё, что необходимо пользователю, это наличие нового набора сварочных параметров, т.е. все изменения осуществляются программным способом. Понимание принципов работы увеличивает прозрачность процесса и выявляет важные взаимосвязи, особенно в отношении импульсно-дуговой сварки.
Форма волны электрического тока при выполнении импульсно-дуговой сварки отражает различные фазы и значения силы тока (рисунок 1). Вначале присутствует базовый ток с наложенным импульсным током. В то время, как ток замыкания на землю остается постоянным (горизонтальная ось), импульсный ток демонстрирует обычный рост и падение токовой кривой. Более конкретно, это относится к двум ограниченным по времени величинам тока для импульсного периода и периода отделения капли. Для импульсного периода характерно относительно плавное линейное нарастание тока до момента выравнивания. По прошествии импульсного периода начинается период тока отделения капли. Ток вначале резко падает, затем понижается линейно, затем наклон кривой уменьшается, и ток достигает базового уровня тока отделения капли. За данным этапом следует окончательное падение на заметно меньшую величину до базового тока. Значение отдельных фаз разъяснено ниже.
Рис. 1: Индивидуальное программирование характеристик является мощным средством оптимизации сварочных технологий. Однако, для этого необходимы глубокие знания ключевых особенностей дуговых процессов.
Ток заземления предназначен для поддержания дуги в период между отдельными фазами импульсного тока. Величина в данном случае зависит от правильного задания величины силы тока. При задании слишком высокого тока замыкания на землю раcплавление проволочного электрода окажется выше необходимого, а размер капель будет слишком большим. Это отрицательно повлияет на процесс отделения капель. Однако, при задании слишком низкого тока замыкания на землю также низкой окажется ионизация дуги, вследствие чего возможно прерывание дуги в фазе тока замыкания на землю.
В специальной литературе часто встречаются заявления относительно того, что импульсный ток предназначен для полного отделения капли от сварочной проволоки. Между тем задача импульсного тока заключается только в формировании такой капли, что для её полного отделения от сварочной проволоки будет достаточно лишь слабого тока отделения. Важным моментом здесь является выбор периода импульсного тока, точно подходящего к уровню импульсного тока; это необходимо для поддержания требуемой энергии импульса.
Уровень импульсного тока зависит в первую очередь от материала и диаметра проволочного электрода, а также от используемого защитного газа. При задании слишком короткого периода импульсного тока и слишком высокого импульсного тока можно не добиться требуемого эффекта отделения капли. Если необходимо обеспечить перенос металла без возникновения короткого замыкания, то для обеспечения надлежащего формирования капли импульсный ток должен превышать критический уровень.
Определяющими факторами для формирования капли являются уровень и продолжительность действия импульсного тока, а также действующие на каплю ускоряющие силы. Уровень импульсного тока также влияет на давление дуги, которое воздействует на сварочную ванну через плазменный шнур. Настройка указанных параметров сварки позволяет, например, увеличить глубину проплавления, что, в свою очередь, приведет к незначительному снижению скорости сварки. Однако, влияние силы тока на процесс оказывается намного более сложным. По причине высоких уровней энергии импульса слишком высокий импульсный ток может привести к разрушению капли и образованию нежелательных брызг. И наоборот, при задании слишком низкого импульсного тока энергии для формирования капли может оказаться недостаточно. В результате капля на конце проволочного электрода не будет сформирована должным образом, из-за чего процесс отделения капли будет более длительным и потребует нескольких импульсов для отделения. Такой процесс переноса капли может вызвать сильное брызгообразование и зачастую приводит к осаждению капли вне оси электрической дуги, рядом со сварным швом. Это значительно увеличивает объемы необходимой доработки сварных изделий.
Длина импульсной фазы, выраженная в миллисекундах, в основном зависит от свойств защитного газа, присадочного металла и диаметра проволоки. Чем ниже импульсный ток и больше диаметр проволоки присадочного металла, тем больший период импульсного тока следует задавать в целях обеспечения переноса материала без короткого замыкания. При разработке набора параметров необходимо принимать во внимание и множество других дополнительных факторов. Например, падение тока (выраженное в А/мс) в конце периода импульсного тока не должно быть слишком резким, если процесс отделения капли допускает такой подход. В результате будут снижены уровни помех. Интенсивность падения тока зависит от таких параметров, как свойства присадочного металла и состав защитного газа.
Рис. 2: Тавровые швы, полученные с применением PCS, выделяются своей глубиной и узкой шириной; две стальные пластины толщиной 8 мм, ширина катета шва (размер а) 5 мм, присадочный металл G3Si1, газовая смесь: 8% CO2 и 92% аргона.
Создание программ является мощным средством оптимизации сварочных технологий. Для этого, однако, требуются глубокие знания технологии дуговой сварки. Компания Fronius в рамках технической поддержки готова предоставить заинтересованным пользователям полезный инструмент универсальный блок управления RCU 5000i с модулем памяти. С помощью данного блока пользователи будут иметь возможность создания и сохранения программ для сварочных систем Fronius, предназначенных для выполнения импульсной и обычной сварки с применением любых стандартных присадочных материалов для сварки MIG/MAG (сварки плавящимся электродом в среде защитных газов).
Это обеспечит значительные преимущества в отношении воспроизводимости результатов сварки. Результаты, достигнутые сварщиком в определенных условиях с использованием определенных наборов параметров и настроек, могут быть получены снова в любое время. Сварщик анализирует имеющееся рабочее задание и назначает соответствующие параметры сварочного процесса. Таблица данных может быть сохранена в памяти сварочной системы, пульта дистанционного управления или внешнего устройства. Сварочные системы TransPuls Synergic 4000/5000 производства компании Fronius способны хранить в памяти до 100 сварочных программ или заданий; память устройства дистанционного управления RCU 5000i позволяет сохранять до 1000 программ. В целях создания базы данных практически неограниченного объема аппараты также могут подключаться к внешнему компьютеру через соответствующий интерфейс. Установленные таким образом рабочие параметры могут считываться из памяти с необходимой периодичностью.
PCS — новые возможности по повышению эффективности сварки стальных заготовок
PCS (дуга со струйным переносом металла с импульсным управлением) — это новый набор сварочных параметров, специально разработанный компанией Fronius. Эти параметры сочетают в себе настройки стандартной сварки и импульно-дуговой сварки со струйным переносом металла. Целью разработки данного набора являлось удовлетворение требований к высокопроизводительной сварке с невероятно широким полем настроек в верхнем диапазоне мощности. Это означает, что в случае необходимости сварка может начинаться «плавно» в импульсном режиме при сниженной мощности (например, до 50%). Затем, по прошествии заданного периода времени, уровень мощности повышается (вручную, либо автоматически) до рабочего уровня, определяемого набором параметров. Данная фаза процесса выделяется прямым переходом к «жесткому» режиму дуговой сварки со струйным переносом металла. Для тонких листов рабочая точка определяется набором параметров в диапазоне импульсной дуги; для толстых листов переход к струйному переносу осуществляется либо сразу, либо по прошествии периода работы со сниженной мощностью. Для сварных швов с заполнением кратера в конце шва процесс выполняется в обратном порядке. Все настройки процесса могут быть сохранены пользователем в виде рабочей программы для сварки толстолистовых материалов. Наиболее важными преимуществами нового набора параметров являются: повышенная глубина проплавления, скорость сварки и производительность наплавки, возможность выполнения сварки без короткого замыкания при скоростях подачи проволоки от 1,5 до 22 м/мин., возможность регулирования настроек в импульсном диапазоне и перенос металла с малым количеством брызг. Все эти преимущества позволяют компании Fronius удовлетворять запросы пользователей, предъявляющих высокие требования в отношении качества, производительности, надежности и воспроизводимости результатов.
Рис. 3: Сравнение традиционной технологии «короткая дуга/промежуточная дуга/дуга со струйным переносом» с инновационной технологией «импульсная дуга/импульсно-модулированная дуга/дуга со струйным переносом».
Подробное описание принципов PCS — увеличение производительности и КПД
Набор параметров PCS имеет фундаментальные отличия от традиционных наборов характеристик. В последних количество отделяемых капель определяется частотой изменений напряжения и тока импульсной дуги; в отличие от этого дуга со струйным переносом металла (например, с частотой свыше 300 Гц) характеризуется неопределённым, но, однако, очень высоким количеством капель. Эти капли отделяются (распыляются) со сварочной проволоки независимо от частоты. Стандартные технологии, уже предлагаемые на рынке, предусматривают поддержание напряжения дуги со струйным переносом металла на постоянном уровне. Компания Fronius, однако, выбрала иной путь — PCS предусматривает поддержание тока на постоянном уровне! В результате такого существенного технологического отличия набор параметров PCS не допускает формирования промежуточной дуги. Ключевым преимуществом данного подхода является практическое исключение брызгообразования и необходимости в доработке сварных изделий.
Новый набор параметров позволяет создать очень короткую, но по-прежнему мощную дугу со струйным переносом, что обеспечивает повышенную глубину проплавления при меньшей ширине сварочной ванны. Сварка в верхнем диапазоне мощности выполняется с существенно повышенной скоростью, швы обладают более высокой надежностью и качеством по сравнению со стандартными швами. Помимо значительного повышения производительности, основная выгода для пользователя заключается в повышении конкурентоспособности изделий. Компания Fronius разработала новый набор параметров PCS для объединения свойств импульсной и стандартной дуговой сварки со струйным переносом металла без необходимости формирования промежуточной дуги. Данный набор параметров совмещает частоту обычной импульсной дуги с частотой дуги со струйным переносом металла. Основными факторами, учитываемыми в PCS, являются основной металл, присадочный металл, диаметр проволоки и состав защитного газа. Например, при сварке ферритных сталей, набор PCS устанавливает следующий состав защитного газа: 8% CO2 + 92% Ar и сварочную проволоку G3Si1 (или ER70 по международному обозначению) диаметром 1,0 или 1,2 мм. По диаметру сварочной проволоки с учетом толщины заготовки определяется скорость подачи проволоки. Другими словами скорость подачи проволоки соответствует мощности, которая, в свою очередь, соответствует толщине заготовки и скорости сварки.
Рис. 4: Сечения обоих швов с очевидностью отражают различия. Первым показан шов, полученный импульсной сваркой; вторым — тавровый шов, выполненный с применением PCS (дуга со струйным переносом металла с импульсным управлением).
Гибкость в изменяющихся производственных условиях
Каков порядок действий в том случае, если значения параметров должны отличаться от установленных в наборе PCS? Это может произойти при определенных условиях, например, если количество CO2 намного меньше номинального. Отклонения содержания CO2 от расчетных 8% могут вызвать изменения длины дуги. В зависимости от этого выбирается подходящий набор PCS.
В принципе, для получения нужной длины дуги набор PCS может быть скорректирован изменением напряжения. Для корректировки длины дуги предусмотрен широкий диапазон регулирования в большую или меньшую сторону относительно «идеального» сварочного напряжения 30 В. Однако, изменение напряжения приведет к изменению электрической мощности и, соответственно, тепловложения. Это же условие применимо также к ЗТВ (зона термического влияния) в случае стабильной производительности наплавки.
Например, повышенное содержание CO2 приведет к увеличению диаметра и расфокусировке дуги. Вследствие этого, из-за уменьшения плотности тока и, соответственно, давления дуги расширится зона плавления и уменьшится глубина проплавления. Снижение давления дуги приводит к повышению напряжения, но тепловая мощность (меньшая) подается в расширенную околошовную зону. Данные факторы могут быть скомпенсированы изменением напряжения (как указано выше) или снижением скорости сварки. Иные отклонения параметров, например, диаметра проволоки, от установленных в наборе PCS, оказывают сравнимое с рассмотренным выше влияние и требуют аналогичных корректирующих действий. Однако, например, изменение диаметра проволоки на 1,0 мм вместо 1,2 мм, требует изменения таблиц параметров, в связи с чем создание дополнительного набора параметров будет гораздо более разумным решением.
Заключение: применение набора параметров PCS на практике
Новый набор параметров отличается высокой степенью универсальности в отношении толщины материалов, а также возможностью добиться высокой производительности наплавки. Если необходимо, импульсный процесс может быть начат в «мягком» режиме до переключения на «жесткий» струйный перенос металла без промежуточной стадии. Кроме того, тот же набор параметров может быть применен для сварки следующего шва в обычном режиме импульсно-дуговой сварки. Также данный набор обеспечивает дополнительные преимущества точной фокусировки дуги с соответствующим увеличением глубины проплавления. Благодаря этому повышаются скорости подачи проволоки, что увеличивает производительность наплавки и приводит к значительному росту скорости сварки с сохранением широкого катета шва (размера а). Сварка с применением набора параметров PCS осуществляется со скоростью подачи проволоки от 1,5 до 22 м/мин. с исключительно низким образованием брызг. В импульсном диапазоне может быть проведена настройка дуги.
Таким образом, благодаря новому набору параметров PCS компания Fronius создала стандартную технологию, обеспечивающую надежную, экономичную и высококачественную сварку с воспроизводимыми результатами и минимально необходимой доработкой сварных изделий. Широкий диапазон регулирования значительно расширяет область применения в отношении толщины материала по сравнению с аналогичными стандартными наборами параметров.
Рис. 5: Тавровый шов между стальной трубой и фланцем, a = 5 мм, скорость подачи проволоки: 12 м/мин., скорость сварки: 90 см/мин., присадочный металл ER 70 с диаметром проволоки 1,4 мм.
Общие процессы дуговой сварки | EDT Судебная инженерия и консалтинг
Сварка — это производственный процесс, при котором две или более деталей сплавляются друг с другом с помощью тепла, давления или того и другого, образуя соединение по мере охлаждения деталей. Хотя можно сваривать материалы, отличные от металла (например, пластмассы), этот процесс чаще всего связан с соединением металлических деталей. Дуговая сварка — это форма сварки, при которой электрическая дуга используется для выработки тепла, необходимого для нагревания свариваемых материалов до их температуры плавления и соединения — в большинстве случаев с добавлением присадочного материала, имеющего свойства, сравнимые со свойствами соединяемых материалов (стальные присадочные материалы). используются для соединения стальных изделий, алюминиевый наполнитель для алюминия и т. д.). Для целей этого обсуждения мы собираемся сосредоточиться на дуговой сварке металлов и процессах, наиболее часто используемых для создания предметов, с которыми мы сталкиваемся ежедневно.
Американское общество сварщиков (AWS) имеет стандартные сокращения и определения для многих сварочных процессов. Однако у этих процессов есть более распространенные полевые или промышленные названия, которые мы также будем использовать в этом обсуждении. Ниже приведены процессы сварки, которые мы рассмотрим:
Обозначение Американского общества сварщиков (AWS) Общепринятое или промышленное название (я)
GMAW (дуговая сварка металлическим газом) = сварка MIG (металл в инертном газе)
GTAW (дуговая сварка вольфрамовым электродом) = Сварка TIG (вольфрам в среде инертного газа)
SMAW (дуговая сварка защищенным металлом) = дуговая сварка или сварка электродом
Процесс сварки MIG:
Сварка MIG (сокращение от Metal Inert Gas) является одним из наиболее распространенных сварочных процессов, используемых сегодня, MIG используется в различных областях. Проще говоря, сварка МИГ характеризуется подачей проволочного электрода под напряжением в «лужу» расплавленного металла, образующую сварной шов. Чистота этой лужи/стыка расплавленного металла поддерживается путем окружения ее инертным (нереактивным) «защитным» газом, чаще всего двуокисью углерода, аргоном или их смесью. Присутствие этого защитного газа предотвращает реакцию расплавленного металла и наполнителя с кислородом, влагой и другими реактивными переносимыми по воздуху загрязнителями (и загрязнение ими). Процесс MIG можно адаптировать для использования с тонкими или толстыми металлами, изменяя напряжение дуги и скорость, с которой проволока подается в сварочную ванну. Нетрудно найти примеры изделий, сваренных методом MIG, в нашей повседневной жизни. MIG часто используется в автомобилестроении для соединения компонентов рамы автомобиля, выхлопных труб, каркасов сидений, преобразователей крутящего момента и других различных компонентов. Сварку MIG также можно найти на оборудовании игровых площадок, поручнях, велосипедах и других устройствах, где секции стальных труб соединяются вместе.
Сварка MIG на стали:
Сварка MIG также подходит для использования на изделиях, изготовленных из алюминия, таких как алюминиевые лодки, прицепы и других различных устройствах. В то время как для сварки MIG стали часто используются большие катушки проволоки весом 10-30 фунтов, алюминиевой проволоке не хватает жесткости стальной проволоки. Таким образом, алюминиевую проволоку нельзя протолкнуть от источника сварочного тока (там, где обычно находится катушка) к рабочей зоне без изгиба или защемления до того, как она достигнет сварочной горелки. Из-за этого сварщики алюминия часто используют шпульный пистолет, сварочную горелку/наконечник, в котором небольшие (обычно 1 фунт) катушки с проволокой находятся в насадке, а не в источнике сварочного тока (также известном как сварочный аппарат), требуя, чтобы проволока проталкивать только на несколько дюймов, а не на несколько футов, как обычно, от катушки до сварочной ванны. Для крупносерийного производства, где использование алюминиевых катушек меньшего размера нецелесообразно, используется система «тяни-толкай», в которой используется сварочная горелка с моторизованным механизмом подачи, который протягивает проволоку через провод сварочной горелки и подает проволоку из сварщик (аппарат/источник энергии, а не человек) к сварочной ванне.
В целом, сварка MIG предпочтительна из-за высокой производительности и простоты использования. Что касается ограничений сварки MIG, то тот факт, что она использует защитный газ, делает ее уязвимой для загрязнения сварного шва в ветреной среде, когда защитный газ может быть унесен от сварочной ванны, что приведет к образованию пористых, загрязненных сварных швов. которые могут не соответствовать требованиям их предполагаемого применения. Учитывая это ограничение процесса, процесс сварки MIG хорошо подходит для использования в заводских/производственных сварочных условиях, где климатические условия более или менее контролируются.
Процесс дуговой сварки
Самым старым и наиболее распространенным процессом дуговой сварки является «стержневая» сварка, также называемая SMAW (сокращение от «дуговая сварка с защитным металлом»). В этом процессе используется металлический сварочный электрод с флюсовым покрытием, также известный как сварочная «палка» или стержень. Флюсовое покрытие сварочного стержня служит защитным газом, используемым в процессе сварки MIG, защищая сварной шов от загрязнения. Флюсовые покрытия также могут влиять на скорость охлаждения сварочной ванны, тем самым влияя на окончательную прочность сварного шва. Состав флюсового покрытия также может влиять на пригодность сварочного электрода для использования в различных положениях (потолочном, вертикальном и т. д.). Несмотря на то, что он служит аналогичной цели защиты/экранирования сварного шва, флюс не рассеивается, как защитный газ для процесса MIG. Вместо этого флюс часто оставляет корку или «шлак» на сварном шве, который необходимо сколоть, чтобы открыть сварной шов.
Внешний вид сварного шва, отслоение шлака
Сварной шов, отколотый шлак
В дополнение к образованию шлака на сварных швах, этот процесс также имеет тенденцию к образованию большего количества дыма/дыма и брызг (разбрызгивания материала), чем процесс MIG, что делает его несколько менее желательным для использования внутри помещений – при этом стабильность процесса SMAW делает его отличным выбором для сварки на открытом воздухе, например, для сварки конструкционной стали, а также для ремонта в полевых условиях сельскохозяйственного, строительного, горнодобывающего и погрузочно-разгрузочного оборудования. . Сварочные электроды (или «стержни», как их обычно называют) для процесса SMAW доступны в различных составах, что делает их подходящими для конкретных задач. Для этого процесса после того, как электрическая дуга установится или «зажжется» (считается, что процесс напоминает зажигание спички), сварочный электрод вручную подается в сварочную ванну сварщиком (человеком, а не машиной/источником питания). . Это отличается от сварки MIG, где скорость подачи проволоки/электрода предварительно устанавливается до начала сварки в соответствии с потребностями формируемого соединения. Подобно сварке MIG, где диаметр проволоки/электрода может варьироваться в соответствии с потребностями конкретного соединения, при сварке электродом для этой цели используются электроды разного диаметра. Что касается настройки процесса TIG/SMAW для различной толщины металла, электрический ток изменяется (увеличивается для более толстых металлов/более крупных электродов), а не изменяется напряжение, как при сварке MIG.
В этом случае источники питания для сварки MIG нельзя легко заменить источниками питания, используемыми для сварки электродами. Как правило, процесс сварки SMAW/Stick сварки предпочтительнее при сварке в ветреную погоду или на открытом воздухе, а также в других местах, где нецелесообразно перемещать сварочный аппарат MIG к месту, где завершается сварка. Помимо работы в ветреную погоду, сварку электродом можно выполнять и под водой. Еще одна желательная черта дуговой сварки — простота оборудования. По сравнению со сварочным аппаратом MIG, для которого требуются механизмы для управления подачей проволоки и защитного газа, а также источник питания для создания дуги, сварочному аппарату для дуговой сварки требуется только источник питания. В этом случае первоначальная стоимость оборудования, как правило, ниже. В то время как сварка MIG обычно происходит в пределах нескольких футов от сварочного аппарата/источника питания, нередко сварка электродом выполняется на расстоянии 50-100 футов от источника питания.
Это особенно полезно при работе со стальными конструкциями, когда сварщик (человек) должен перемещаться между различными и часто возвышенными местами, где было бы нецелесообразно перемещать оборудование для сварки MIG из одного места в другое. Хотя это может быть не самый предпочтительный метод для некоторых применений, сварка электродами существует очень давно и, вероятно, останется наиболее распространенным типом сварки, учитывая низкую стоимость и универсальность процесса.
Сварка ВИГ
Еще одним процессом дуговой сварки, часто используемым для соединения металлических компонентов, является процесс ВИГ (вольфрам в инертном газе). В то время как в этом процессе используются источники питания, аналогичные тем, которые используются для сварки электродом, в TIG также используется защитный газ, как и при сварке MIG. Чистый аргон является наиболее распространенным защитным газом для процесса TIG, а гелий обычно используется в тех случаях, когда требуется дополнительное проплавление сварного шва. В то время как сварочное оборудование MIG контролирует подачу защитного газа и присадочного металла в сварочную ванну, сварка TIG полагается на то, что оператор контролирует подачу присадочного металла (прутка, часто диаметром от 1/16 до 1/8 дюйма) в сварочную ванну. сварочной ванны, управляя горелкой другой рукой и во многих случаях используя одну ногу для запуска/остановки дуги и регулировки сварочного тока. Процесс TIG аналогичен газовой сварке, когда кислородно-ацетиленовая горелка нагревает область сварки, образуя ванну (расплавленную область) одной рукой, а другой подает присадочный стержень. Тем не менее, TIG использует электрическую дугу, проходящую между вольфрамовым электродом и заготовкой, для выработки тепла, необходимого для образования сварочной ванны, а не пламени или дуги с меньшими ограничениями, и, как таковая, способна обеспечить очень точный и локальный нагрев сварного шва. материалы. В этом случае TIG создает меньшую ЗТВ (зону термического влияния) по сравнению с другими процессами сварки, тем самым сводя к минимуму неблагоприятное воздействие на свариваемые материалы.
Еще одна область, в которой процесс TIG отличается от сварки MIG и дуговой сварки, касается управления током дуги. Хотя для завершения сварки TIG можно использовать фиксированный ток, сварщик TIG (аппарат) часто использует ножную педаль, которая позволяет сварщику (человеку) увеличивать и уменьшать ток в соответствии с потребностями сварки. сварной шов. Используя защитный газ и стабильную и точную дугу, процесс TIG обеспечивает чистое сварное соединение без брызг и шлака. При выполнении квалифицированным сварщиком процесс TIG позволяет получить очень эстетичное сварное соединение по сравнению с другими процессами.
Сварное соединение ВИГ – сталь
Сварное соединение ВИГ – алюминий
Таким образом, процесс ВИГ сложен в освоении, он требует использования хорошо очищенных и плотно подогнанных материалов, а также намного медленнее, чем другие популярные процессы сварки . Таким образом, использование сварки TIG для соединения изделий также обходится дороже, чем альтернативные процессы — в этом случае сварка TIG зарезервирована для критических применений, когда другие процессы не подходят, или для тех, где конечный пользователь готов доплатить за более высокое качество. визуально привлекательный конечный продукт.
Хотя мы обсудили здесь несколько распространенных процессов дуговой сварки, мир сварки огромен и состоит из множества инновационных и увлекательных процессов соединения материалов. Процессы, которые мы здесь обсуждали, используются многими и доступны для всех, от любителей до высококвалифицированных мастеров. Независимо от того, какой процесс дуговой сварки выбран для данного применения, все вышеизложенное подвержено влиянию большого количества переменных. Таким образом, недостатки сварки и отказы могут принимать различные формы: некоторые из них легко заметить, в то время как другие менее заметны и требуют использования более продвинутых методов. Это то, что мы с нетерпением ждем, чтобы обсудить более подробно в следующем посте.
Об авторе
Chris S. Spies, P.E. работает инженером-консультантом в нашем офисе в Канзас-Сити, штат Миссури. Г-н Спайс предоставляет консультационные услуги в области анализа систем транспортных средств, анализа отказов механических систем и компонентов, а также анализа отказов промышленного/коммерческого оборудования. Вы можете связаться с Крисом по вопросам, связанным с судебной экспертизой, по адресу [email protected] или (913) 859-9580
. Узнайте о том, как EDT Forensic Engineering & Consulting подходит к причине повреждения и судебно-медицинской экспертизе, назначив файл сегодня.
Теги:
- Судебная экспертиза
- инженер-механик
- Автомобилестроение
Вернуться к блогу
Что такое дуговая сварка? Как работает дуговая сварка?
В этой статье вы узнаете, что такое дуговая сварка и как работает дуговая сварка. Здесь вы также узнаете о различных видах дуговой сварки, сварочном оборудовании, преимуществах и недостатках, а также о применении.
Что такое дуговая сварка?
Процесс соединения металла с металлом с помощью электрической дуги называется дуговой сваркой. В этом процессе сварки дуга используется для создания сильного тепла, и это тепло используется для соединения металлов. Дуга вводится между двумя металлическими деталями, и благодаря выделяемому теплу металлы плавятся, а при остывании образуется прочный сварной шов.
- Источником энергии, используемым при дуговой сварке, является электричество (электрический ток). Используемый электрический ток может быть как постоянным (DC), так и переменным (AC).
- Зона сварки защищена защитным газом, парами или шлаком. Защитный газ защищает зону сварки от атмосферных загрязнений.
- Может быть ручным, полуавтоматическим или полностью автоматизированным.
- Для сварки используются плавящиеся или неплавящиеся электроды.
- Этот вид сварки изобретен в конце 19 века.век. Во время Второй мировой войны он становится коммерчески важным в судостроении. В настоящее время он используется в производстве стальных конструкций и транспортных средств.
Типы дуговой сварки
1. Дуговая сварка металлическим электродом в среде защитного газа (SMAW)
2. Дуговая сварка металлическим газом (GMAW) или (MIG)
3. Дуговая сварка порошковой проволокой (FCAW)
4. Дуговая сварка под флюсом ( SAW)
5. Дуговая сварка вольфрамовым электродом в среде защитного газа (GTAW) или (TIG)
6. Плазменно-дуговая сварка (PAW)
7. Сварка атомным водородом (AHW)
8. Дуговая сварка углеродом (CAW)
9. Электрошлаковая сварка (ЭШС)
10. Электрогазовая сварка (ЭГС)
11. Дуговая сварка стержня
Принципиальная схема
Принципиальная схема дуговой сварки приведена ниже:
Основное оборудование
Различное 90 используемое оборудование: 1. Машина переменного или постоянного тока
2. Электрод
3. Держатель электрода
4. Кабели, кабельные разъемы
5. Отбойный молоток
6. Заземляющие зажимы
7. Проволочная щетка
8. Сварочная маска
9. Защитные очки
10. Перчатки для рук
11. Фартуки, нарукавники и т. д.
Читайте также:
- Что такое подводная сварка и как она работает?
- Сварка сопротивлением – принцип работы и применение
- Сварка трением с перемешиванием – принцип работы, преимущества, недостатки и применение
Работа дуговой сварки
- Сначала включите источник электроэнергии (переменного или постоянного тока).
- Когда электрод подносится к основному металлу (на расстоянии 2-4 мм), где должна выполняться сварка, между основным металлом и электродом возникает искра или дуга.
- Из-за дуги выделяется сильное тепло. Выделяемое тепло расплавляет основной металл, сердечник электрода (или в некоторых случаях присадочный материал) и флюсовое покрытие. Флюсовое покрытие на электроде обеспечивает защитную среду (защитный газ) сварного шва от атмосферных загрязнений. Расплавленный металл или шлак оседают между двумя соединяемыми металлическими частями и затвердевают. После затвердевания он образует прочную связь между двумя металлическими частями.
- Защитный газ используется для защиты расплава или сварного шва от атмосферного загрязнения.
- После завершения процесса сварки изделие (металлические детали) охлаждают, погружая его в соответствующую охлаждающую жидкость. Его также можно оставить для воздушного охлаждения.
Для лучшего понимания посмотрите видео ниже:
Преимущества
- Обладает высокой эффективностью и скоростью сварки.
- Улучшает условия сварки.
- Обеспечивает стабильное качество сварного шва.
- Образует прочную связь между соединяемыми металлами.
- Имеет простое сварочное оборудование.
- Источник питания не такой уж и дорогой.
- Это быстрый и надежный процесс.
- Оборудование может использоваться для нескольких функций.
- Легко переносится.
- Сварщики могут использовать стандартный бытовой ток.
Недостатки
- Требуется высококвалифицированный оператор.
Применение
Это универсальный процесс сварки. Это наиболее широко используемый процесс сварки в мире из-за его простоты и хорошей эффективности сварки. Почти во всех отраслях промышленности дуговая сварка используется для получения прочных соединений. Сегодня это остается важным процессом в производстве стальных конструкций и транспортных средств. Наиболее широко он используется в автомобилестроении, строительстве, строительстве зданий, судостроении, аэрокосмической промышленности, при ремонтных работах.