Электрохимическая обработка металлов: Электрохимическая обработка металлов: виды и назначение
alexxlab | 05.05.2019 | 0 | Разное
Электрохимическая обработка металлов: виды и назначение
Методом электрохимической обработки можно проводить практически любые операции по изготовлению деталей, доводке изделий либо заточке инструмента при отсутствии всякого негативного вмешательства в структуру металла.
Под электрохимической обработкой металлов понимают такие различные процессы, которые связаны со специфическим воздействием на металлические детали путем растворения поверхности электролитическим способом. Метод широко применяется в промышленности, в таких отраслях машиностроения, как создание космической техники, авиационных аппаратов, автомобильная индустрия, производство техники для медицинских нужд, установок энергетического назначения, различных микросистем.
Путем электрохимической обработки можно работать с металлами любого типа, марки, проводить операции со сплавами высоколегированными на основе никеля, крепкими титановыми сплавами и материалами, которые прошли закалку. Поскольку метод не предполагает контактного силового взаимодействия между инструментом и заготовкой, деталь не подвергают нагреву, это исключает возникновение таких негативных моментов, как выработка инструмента, растрескивание тела заготовки, покрытие пленочными оксидами, необходимость проведения доводочных работ по устранению заусенцев.
Изделия из металла, подвергнутые обработке электрохимическим способом, не имеют напряжений внутри структуры, изменений в кристаллической решетке, заусенцев на поверхности.
Назначение электрохимической обработки металла
Электрохимическая обработка деталей – иногда единственно возможный метод придания формы изделию из металла. Связано это с тем, что другие виды обработок: термическая или механическая – в некоторых случаях могут привести к изменению структуры поверхностного слоя. Изменятся свойства металла: увеличится хрупкость, потеряются эластичность и упругость, снизится сопротивляемость коррозии. Все это сделает невозможным дальнейшее использование детали в узле механизма, особенно если это ответственная конструкция.
Другой причиной, по которой целесообразно применение электрохимической обработки, это работа с твердыми сплавами. Обыкновенные резцы не всегда способны дать высокую точность обработки. Может понадобиться много операций доводки, а это финансово не всегда оправдано, ведь в итоге электрохимическая обработка дает самые точные прецизионные результаты всего лишь за один цикл операции обработки. Здесь также важен момент отсутствия влияния электрохимического инструмента на кристаллическую решетку металлической заготовки.
Чтобы понять, как можно использовать метод, нужно иметь представление о процессе обработки. Взаимодействие между инструментом и деталью проходит в растворе электролита и, по сути, представляет собой электролиз.


Процесс обработки металла
Процесс выглядит следующим образом:
- Заготовку и инструмент помещают в емкость, чтобы они не соприкасались между собой.
- К детали подсоединяют «+» клемму источника постоянного тока, к инструменту – «-» клемму.
- В емкость заливают электролит на основе нейтральной соли и подают напряжение.
- Между заготовкой и инструментом начинает течь электрический ток, и происходят окислительно-восстановительные реакции, где металл заготовки окисляется, а инструмент восстанавливается.
- В результате деталь приобретает определенную форму, а в электролите оседает шлам в виде продуктов окисления.
Разновидности обработки
Электролитический способ настолько универсален, что электрохимическими методами обработок можно добиться выполнения практически любых результатов, как при механической обработке. Можно затачивать инструмент, выполнять полировку, получать отверстия в металлической заготовке, получать деталь любой формы. Все это можно представить, как если бы над деталью трудилось одновременно несколько токарных и фрезерных станков.
Методом электрохимической обработки можно создавать формы произвольной конфигурации из любого без исключения металла.
Режущие операции
За счет того что ток можно уплотнить до очень высоких показателей, с поверхности металла в области протекания электролиза съем частиц будет более интенсивным. На этом принципе основана электрохимическая резка. Чтобы электрохимический процесс был стабильным, добиваются постоянной скорости окисления с одновременной подачей в рабочую область электрода катода. В итоге прорезь канавок в заготовке будет проходить непрерывно.
Дополнительно для эффективного удаления окислов из рабочей зоны при помощи насоса в емкости постоянно прокачивают раствор электролита. Катодом в таком автоматизированном процессе обычно служит металлическая проволока, которая с заданной скоростью перематывается между двумя барабанами с одного на другой. Электрохимический процесс позволяет получить очень узкий рез, сопоставимый с десятыми долями миллиметра.
Получение отверстий методом прошивания
Способ, когда металл прошивают, очень схож с тем, как игла входит в материю, только в нашем случае иголкой выступает катод, на торец которого подается плотный ток, как в случае резки металла. Между торцом и металлической деталью в области взаимодействия начинает протекать электролиз, и металл постепенно окисляется. Катод в виде стержня также медленно подают в рабочую зону по мере растворения поверхности изделия.
Материал электрода в этом случае подбирают очень тщательно. Недопустимо, чтобы в процессе движения происходила вибрация электрода, что приведет к неточности образования отверстия. Все части электрода, которые не участвуют в операции, надежно изолируют, дабы избежать электролиза в других частях заготовки и не испортить последнюю. Точность диаметра, с какой можно получить отверстие путем электрохимического прошивания, не выходит за пределы 0.15 мм.
Метод копирования
Применяется этот электрохимический метод тогда, когда в заготовке необходимо получить точную копию матрицы, в роли которой выступает анод. В этом случае плотность тока подается по всей поверхности образца, который располагают над заготовкой и постепенно, контролируя зазор, опускают в растворяемый металл до тех пор, пока он полностью не «впечатается» в тело заготовки.
Метод имеет свои сложности из-за необходимости тщательно контролировать толщину зазора, причем по трем осям координат. Точность обработки при этом может доходить до практически идеальных показателей при отклонениях до 3 микрон. Еще одна сложность – достичь высокого сходства параметров у деталей, полученных от одной прецизионной матрицы. Здесь разбег может составлять до 10 микрон.
Получение точных размеров путем электролиза
Для получения высокоточных параметров размера детали в электрохимической обработке применяют способ принудительной прокачки электролита под давлением с одновременным его обновлением. Это позволяет создавать стабильно высокую плотность тока в зазоре и уменьшать зазор до максимально возможного значения.
Операции по заточке инструмента
Метод электрохимической заточки основан на принципе создания неравномерной плотности тока, направленной вдоль кромки режущего инструмента. В результате выборка металла идет под углом, и резец заостряется. Можно изменить угол заточки путем изменения угла наклона анодного инструмента.
Объем и скорость снятия металла напрямую зависят от силы тока и времени обработки изделия.
Если вы сталкивались с процессом электрохимической обработки металлов, имеете практический опыт проведения таких операций или базовые знания в этой области, поддержите тему в комментариях. Всегда интересно и полезно знать мнение специалистов!
Электрохимическая обработка металлов: методы и станки
Автор admin На чтение 4 мин. Просмотров 761 Опубликовано
Электрохимическая обработка металлов основана на использовании эффекта растворения «тел» электродов, участвующих в процессе электролиза.
Причем разрушительной силы этого физико-химического процесса вполне достаточно для обработки не только обычных металлов, но и чрезвычайно твердых токопроводящих сплавов.
Под электролизом понимают физико-химический процесс, в результате которого происходит перенос вещества (на атомарном уровне) с поверхности токопроводящего электрода в электролит и в обратном направлении.
Используя в качестве электродов (или одного из электродов) обрабатываемые заготовки, погруженные в электролит, можно спровоцировать процесс изменения их формы и размеров. Причем скорость процесса и направление движения частиц контролируется с помощью изменения напряжения и полярности на электродах.
То есть, попеременно превращая обрабатываемую деталь то в катод, то в анод, можно «прибавлять» или «убавлять» габариты изделия. А если поверхность детали покрыть диэлектриком, который препятствует ионному обмену, то наращивание или убывание металла произойдет только в «нужных» местах.
Электрохимические методы обработки металлов
По способу воздействия на деталь электрохимические процессы подразделяются на:
- Анодную обработку, когда заготовку подключают к положительному полюсу.
- Катодную обработку, когда заготовку подключают к отрицательному электроду.
- Попеременную обработку, когда заготовка может включаться в цепь, и в роли анода, и в виде катода.
К типовым разновидностям анодной обработки относятся такие процессы, как:
- Электрохимическое травление.
- Полировка.
- Обработка по размеру.
Формообразование детали осуществляется за счет локализованного растворения металла на аноде или окисления верхних слоев заготовки с последующим удалением мягких оксидов.
Самые распространенные «анодные» технологии:
- Электрохимическое травление (эхт).
- Полирование (эхп).
Причем ЭХТ
Технология ЭХП (электрохимической полировки) предполагает травление шероховатостей на поверхности заготовки. Причем деталь можно «разгладить» до состояния «зеркала» (глянцевания). Еще одна сфера применения ЭХП – дезактивация побывавших в зоне радиоактивного заражения изделий. Технология ЭХП позволят в относительно короткие сроки «снять» с поверхности детали слой толщиной до 80-100 микрометров.
Кроме растворения с помощью анодных технологий можно реализовать еще и процесс формообразования, когда на анод «растворяется» до габаритов шаблона-катода. Кроме того, с помощью анодных технологий на поверхности детали можно вырастить очень тонкую оксидную пленку, защищающую изделие от всевозможных «неприятностей».
Катодная обработка распространена меньше, чем ее анодный аналог. Эта технология реализуется в виде гальванических процессов, предполагающих напыление металла. Такие технологии объединены под единым названием – гальваностегия (она же – гальванопластика). Смысл этого действа заключается в формировании на поверхности электрода, в качестве которого может выступать даже покрытая графитом модель, слоя напыляемого металла.
Попеременная обработка, предполагающая переключение полярности электродов, дает возможность воспользоваться всеми преимуществами и анодной и катодной технологии.
Станки электрохимической обработки
С помощью станков и обрабатывающих комплексов, ориентированных на использование электрохимических технологий металлообработки можно реализовать достаточно сложные операции.
Однако такие станки используются только в узкоспециализированных технологических процессах. То есть, можно утверждать, что электрохимическое оборудование рассчитано на исполнение одного-двух пунктов из технологической карты.
И чаще всего с помощью такого оборудования выполняется уплотнение или наклеп поверхности, термоуплотнение труднодоступных участков, повышение квалитета качества плоскости детали, высокоточная шлифовка и резка. Причем последняя операция – резка заготовки – осуществляется без механического воздействия на тело изделия, поэтому качество и точность электрохимического среза, просто вне конкуренции.
Кроме того, очень популярны и копирно-прошивочные станки, используемые в инструментальном производстве. Такие агрегаты применяются в процессе изготовления сверхпрочных режущих инструментов, матриц, пуансонов и прочих деталей.
электрохимическая обработка металлов — Химическая энциклопедия
ЭЛЕКТРОХИМИЧЕСКАЯ ОБРАБОТКА МЕТАЛЛОВ
группа методов, предназначенных для придания обрабатываемой металлич. детали определенной формы, заданных размеров или свойств поверхностного слоя. Осуществляется в электролизерах (электролитич. ваннах, электрохим. ячейках спец. станков, установок), где обрабатываемая деталь является либо анодом (анодная обработка), либо катодом (катодная обработка), либо тем и другим попеременно. Осн. вид катодной Э. о. м. — гальваностегия (см. гальванотехника). Анодными методами Э. о. м. являются разл. виды электрохим. травления, полирование, формообразование, размерная обработка, оксидирование и др. Во всех анодных процессах происходит либо растворение металла (локализованное в определенных местах или равномерное по всей поверхности), либо превращение поверхностного слоя металла в оксидный или др. слой (см. анодное растворение).
Электрохим. травление (ЭХТ). Термин объединяет неск. технологий, основанных на анодном растворении металла. ЭХТ применяют для очистки поверхности всевозможных деталей, проволоки, лент, труб от разнообразных загрязнений (оксидных, жировых и др.) в качестве предварит. обработки перед нанесением покрытий, прокаткой и др. ЭХТ для очистки от загрязнений производят в растворах кислот, обычно содержащих разл. добавки (напр., ингибитор коррозии), в щелочных растворах или расплавах при постоянном или переменном токе. ЭХТ подвергают практически любые металлы и сплавы. ЭХТ используют для осуществления т. наз. электрохим. фрезерования с целью получения заданного “рисунка” на поверхности детали локальным анодным растворением металла. Места, которые не должны подвергаться растворению, покрывают слоем фоторезисторного материала или спец. трафаретом. Т. обр. можно производить обработку деталей типа печатных плат, перфорирование, а также травление в декоративных целях. Анодным травлением удаляют заусенцы и скругляют острые кромки.
Важная область использования ЭХТ — развитие поверхности (увеличение уд. площади поверхности). Наиб. широкое пром. применение имеет травление алюминиевой фольги в хлоридных растворах для электролитич. конденсаторов; этот процесс позволяет повысить уд. поверхность в сотни раз и увеличить уд. емкость конденсаторов, уменьшить их размеры. Развитие поверхности методом ЭХТ применяют для улучшения адгезии металла к стеклу или керамике в электронной технике, копировального слоя к печатным формам в полиграфии, усиления сцепления покрытия с металлом при эмалировании металлических изделий и др. Анодным травлением снимают дефектные гальванич. покрытия с деталей с тем, чтобы возвратить их в производство, а также при регенерации металлич. пластин офсетных биметаллич. печатных форм.
ЭХТ применяют в практич. металловедении; широко известно анодное травление металлографич. шлифов для выявления микроструктуры сплавов. При этом травление проводят в таких условиях, когда достаточно резко проявляется различие скоростей растворения разных по хим. и фазовому составу компонентов сплава. В результате избирательного ЭХТ м. б. выявлены границы фаз, сегрегация фосфора в стали, дендритная структура титановых сплавов, сетка трещин в хромовом гальванопокрытии, оценена склонность нержавеющей стали к межкристаллитной коррозии.
Электрохим. полирование (ЭХП) заключается в преимущественном анодном растворении выступов на шероховатой поверхности и приводит к достижению низкой шероховатости (электрохим. сглаживание) или зеркального блеска поверхности (глянцевание). Глянцевание улучшает декоративные свойства изделия, придает поверхности высокую отражат. способность. ЭХП и сглаживание поверхности применяют для повышения эксплуатац. надежности, долговечности и др. эксплуатац. свойств деталей. положит. влияние ЭХП на изделие объясняется неск. причинами: 1) удаление дефектного (деформированного, имеющего трещины, повышенное содержание вредных элементов) поверхностного слоя, образовавшегося при мех., термич., электрич. обработке изделия; 2) уменьшение шероховатости поверхности и сглаживание профиля поверхности; 3) образование тонкой поверхностной оксидной пленки, предохраняющей металл от коррозионного воздействия среды.
Анодное растворение в режимах ЭХП тонкого поверхностного слоя металла, загрязненного радиоактивными веществами, — один из осн. методов радиохим. дезактивации оборудования. При ЭХП обычно удаляется слой металла от 2,5 до 80 мкм. Конечная шероховатость поверхности определяется исходной шероховатостью, продолжительностью ЭХП, условиями проведения процесса (температура, плотность тока), составом электролита (растворы щелочей, солей, но чаще всего смеси кислот). Получению высокого качества ЭХП мешают большие размеры кристаллитных зерен, неравномерная структура, наличие неметаллич. включений (напр., карбидов), глубокие следы прокатки, ока-линные загрязнения, слишком высокая начальная шероховатость поверхности.
Анодное формообразование (ЭХФ) используют для изготовления деталей с заданными формой, размерами и качеством поверхности. При ЭХФ деталь получают в условиях, когда форма катода-инструмента копируется на аноде-заготовке. Процесс проводится в потоке электролита (обычно растворы солей, напр. NaNO3) при плотностях тока в десятки А/см2, межэлектродном расстоянии порядка 0,1 мм. По мере растворения анода-заготовки катод с помощью спец. механизма продвигается в направлении растворения. В отличие от традиционной мех. обработки, ЭХФ характеризуется отсутствием мех. контакта между инструментом и деталью, низкими температурой и давлением в рабочей зоне, отсутствием износа инструмента и заусенцев на обработанной детали. ЭХФ пригодно для обработки легкодеформируемых деталей, хрупких и твердых материалов, обработки в труднодоступных местах.
Электрохим. растворением с помощью вращающегося дискового электрода или др. катода-инструмента производят разрезание заготовок из разл. металлов и сплавов, тонкостенных труб, металлич. монокристаллов, полупроводниковых материалов.
Разновидность Э. о. м. — электролитный нагрев с целью термич. или хим.-термич. обработки деталей (нагрев с последующей закалкой в электролите, науглероживание, азотирование поверхностного слоя). Этот вид обработки проводится в таком режиме, когда растворение металла крайне мало, а сильный нагрев происходит при прохождении тока через парогазовый приэлектродный слой, который возникает из-за вскипания электролита около электрода при высоких значениях плотности тока и напряжения.
Электрохим. оксидирование имеет две осн. разновидности: получение барьерных тонких (толщиной до мкм) и пористых толстых (до неск. сотен мкм) анодных оксидных пленок. Барьерные пленки получают в растворах электролитов типа H3BO3, не растворяющих оксиды, обычно в два этапа. На первом этапе — в гальваностатич. условиях; при этом напряжение увеличивается во времени, а толщина оксидной пленки пропорциональна прошедшему количеству электричества. После достижения заданного напряжения режим изменяют на вольтостатический: ток снижается во времени, диэлектрич. свойства оксидной пленки повышаются. Одна из наиб. важных областей применения барьерных оксидных пленок — получение диэлектрич. слоя электролитич. конденсаторов.
Пористые анодные оксидные пленки выращивают в агрессивных по отношению к оксиду электролитах, напр. в 15%-ной H2SO4, при постоянном напряжении. Такие пленки состоят из двух слоев: тонкого барьерного и значительно более толстого пористого. Они широко применяются в качестве декоративно-защитных покрытий. Для улучшения защитных свойств после оксидирования пористые пленки подвергают операции “наполнения” (“уплотнения”), чаще всего обработкой в горячей воде. Для повышения декоративных свойств пористые пленки на алюминии окрашивают в разные цвета, подвергая обработке растворами красителей или дополнит. электрохим. обработке переменным током в электролитах, содержащих соли Cu, Ni, Sn (см. крашение оксидированного алюминия).
Новое направление Э. о. м. — микродуговое оксидирование, т. е. формирование анодной оксидной пленки в условиях протекания электрич. микроразрядов на аноде, что расширяет возможность получения оксидных покрытий с различными полезными свойствами.
Э. о. м. применяют для маркирования изделий. Нужные знаки на металлич. поверхности получают локальным изменением цвета в результате очень неглубокого травления (или оксидирования) либо в результате рельефного травления. Получили развитие комбинир. методы обработки, в которых электрохим. воздействие на металл совмещено с к.-л. другим (напр., мех., эрозионным, лазерным).
Лит.: Ямпольский A.M., Травление металлов, М., 1980; Анодные оксидные покрытия на металлах и анодная защита, 2 изд., К., 1985; Штанько В.М., Животовский Э.А., Электрохимическая обработка металлопродукции, М., 1986; Грилихес С. Я., Электрохимическое и химическое полирование, Л., 1987; Дураджи В.Н., Парсаданян А. С., Нагрев металлов в электролитной плазме, Киш., 1988; Давыдов А.Д., Козак Е., Высокоскоростное электрохимическое формообразование, М., 1990.
А. Д. Давыдов
Источник: Химическая энциклопедия на Gufo.me
Значения в других словарях
- ЭЛЕКТРОХИМИЧЕСКАЯ ОБРАБОТКА металлов — ЭЛЕКТРОХИМИЧЕСКАЯ ОБРАБОТКА металлов — осуществляется электрическим током в электролите. См. также Электролиз. Большой энциклопедический словарь

Электрохимическая размерная обработка металлов. Назначение, особенности и преимущества технологии
С активным развитием электрохимических технологий набирают популярность все более сложные процессы обработки металлов, помимо традиционных гальванизации и механической обработки деталей. Одновременно получают новые импульсы к развитию давно известные и хорошо себя зарекомендовавшие технологии. Одной из таких традиционных, но незаслуженно забытых технологий в нашей стране, в отличие от стран Запада, является электрохимическая размерная обработка металлов (ЭХРО). Этот процесс начинает привлекать к себе внимание благодаря появлению более функциональных и надежных источников питания и совершенствования систем управления станками для ЭХРО.
Область применения ЭХРО достаточно обширна и включает многие отрасли промышленности за счет широкого спектра решаемых задач. В частности, метод используется для таких работ, как:
- Серийное высокоточное производство металлических изделий — с помощью ЭХРО проводится объемное копирование, когда форма катода (инструмента) проецируется на форму анода (изделия). Это наиболее распространенный способ применения ЭХРО, поскольку позволяет массово изготовлять с высокой повторяемостью и точностью металлические детали (компоненты механизмов, медицинские инструменты и т.д.), а также производить литейные и пресс-формы.
- Прошивание (аналог сверления) металлических изделий с помощью струи электролита.
- Шлифовка и улучшение поверхности изделий (электрополирование) — ЭХРО позволяет выполнить высококачественную обработку поверхности, даже если изначально она покрыта неровностями и заусенцами.
- Резка заготовок — ЭХРО способна резать металлические изделия, создавая значительно более «аккуратные» срезы, чем стандартная распиловка.
Суть ЭХРО состоит в электрохимическом растворении металла анода (изделия) с помощью катода (инструмента) с целью придания ей нужной формы. Во время процесса катод подводится к аноду на малое расстояние, буквально несколько микрон. Важно, что обработка происходит в объеме, что позволяет проводить не только обработку изделия готовой формы, но и создавать требуемую форму из заготовки. При ЭХРО электролит равномерно циркулирует между анодом и катодом со скоростью, обеспечивающей полный вынос продуктов растворения анода.
В качестве примера серийного производства изделий с помощью ЭХРО можно привести декоративные металлические изделия: кулоны, брелки, гравюры, а также изделия из жаропрочных и твердых сплавов: лопатки турбин и компрессоров и т. д.
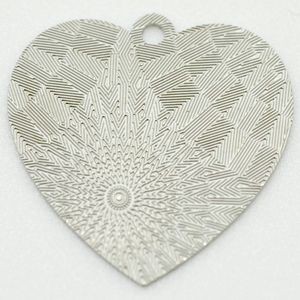
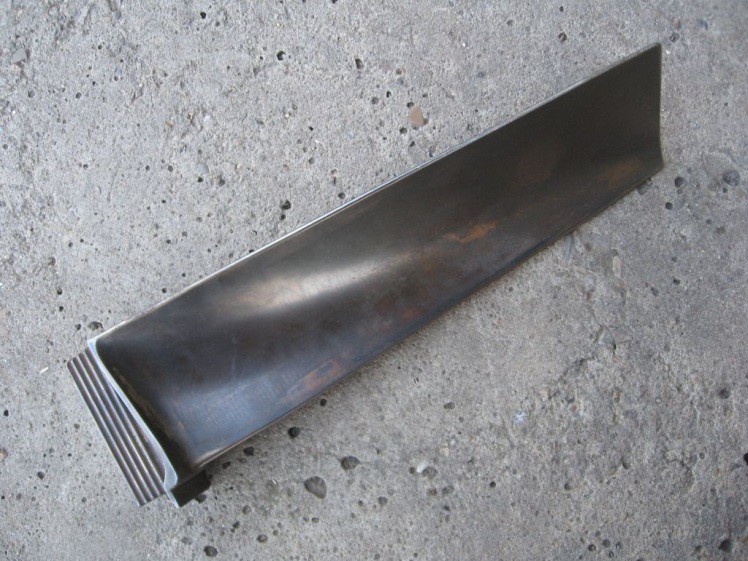
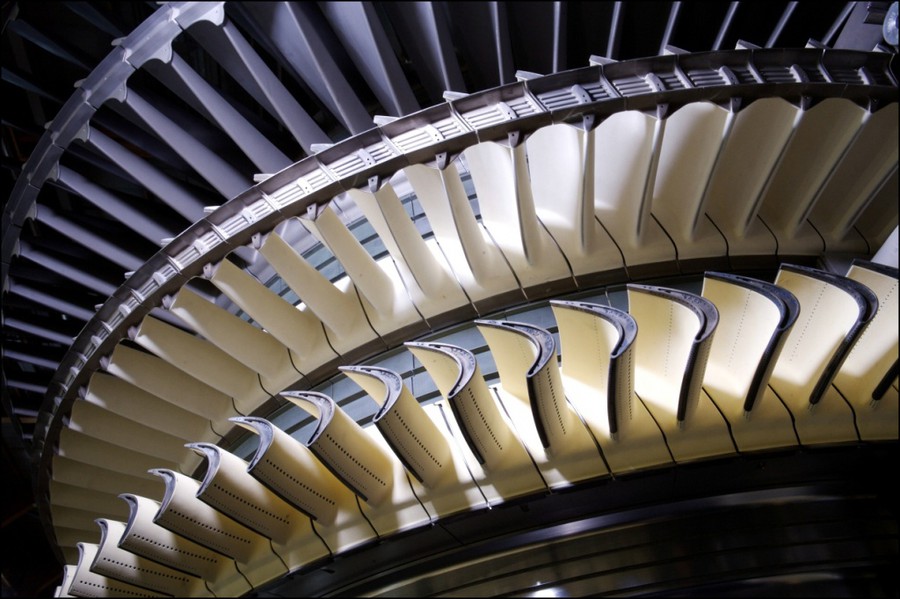
По сравнению с другими методами обработки металлов, ЭХРО имеет целый ряд преимуществ:
- Инструмент обработки (катод) не изнашивается в процессе.
- Эффективность не зависит от механических свойств обрабатываемых металлов.
- Структура поверхностного слоя не меняется, при этом устраняются неровности и заусенцы, а дополнительная обработка изделия после завершения процесса часто уже не требуется.
- Отсутствие температурного воздействия на обрабатываемую поверхность и отсутствие контакта инструмента с заготовкой. В итоге структура изделия не страдает от перепада температур.
- Обработке могут подвергаться даже мелкие детали из высокопрочных сплавов, механическая работа с которыми затруднительна. Это особенно актуально при наличии требований к точным размерам изделий. При этом катод (инструмент) может быть изготовлен из любых металлов, в том числе имеющих невысокие механико-физические свойства.
- ЭХРО является одним из самых эффективных по производительности процессов в электрохимической обработке.
- В качестве электролита используются водные растворы нейтральных солей малой концентрации, что делает работу более безопасной и экологичной.
Значительным отличием ЭХРО от обычной электрохимической обработки можно назвать работу в условиях чрезвычайно высоких (до нескольких тысяч А/см2) плотностей тока при крайне малых (от сотен до единиц микрон) зазорах между анодом и катодом. Это накладывает требования на механическую конструкцию, поэтому ЭХРО проводится не в обычных гальванических ваннах, а исключительно с помощью специальных установок.
Одним из важнейших факторов для работы установок ЭХРО является обеспечение источником питания импульсного режима работы с высокими требованиями к временным параметрам импульсов тока. Есть прямая связь между длительностью и частотой импульсов тока и точностью изготовления деталей. Не менее важным фактором является наличие импульсного режима стабилизации тока.
В обычных источниках питания, применяемых в установках ЭХРО, практически всегда реализован импульсный режим стабилизации напряжения, или вообще режим без стабилизации. При этом случайное попадание в маленький зазор между анодом и катодам частицы металла или простое соприкосновение катода с анодом в какой-либо точке поверхности вызывает короткое замыкание (КЗ).
В режиме стабилизации напряжения при КЗ происходит мгновенный рост тока в цепи и выброс значительного количества энергии, что приводит к «выгоранию» металла с поверхностей матрицы и заготовки — появление так называемых «прижогов».
Это приводит к необходимости править матрицу или вообще изготавливать ее заново, что недешево! В режиме стабилизации тока таких последствий удается избежать — ток ограничивается источником питания, а напряжение при этом падает практически до нуля, в результате отсутствует выброс большого количества энергии.
Модели источников технологического тока (выпрямителей), обладающих импульсным режимом стабилизации тока и специально разработанные для этих задач, выпускает российская компания «Навиком» на базе силовых модулей «Пульсар Смарт 225/30». Выпрямители на основе данных силовых модулей с успехом применяются в промышленности и зарекомендовали себя как надежные и удобные в эксплуатации выпрямители.
«Навиком» уже более пятнадцати лет поставляет на рынок силовое оборудование для промышленного и частного использования, и за это время накопила огромный опыт разработки надежных устройств, отвечающих высочайшим требованиям к параметрам выходного тока и напряжения.
Электрохимическая обработка металлов. Часть 4.
Наши эксперименты по обработке металлов электричеством и химией продолжаются. И на смену установке ЭХ-3 пришла установка ЭХ-4И:Индекс “И” означает, что у данной установки есть дополнительная функция электроискровой обработки, которую мы также сегодня протестируем. В качестве штатива использован наш любимый конструктор ЧПУ станков “Кулибин”, а в качестве ванночки – прозрачная коробка из-под mp3-плеера.
Ванночка не так огромна как раньше, и укреплена на столе станка толстым двусторонним скотчем, а деталь в ней – термоклеем.
Еще одной особенностью данной установки является отсутствие насоса для прокачки электролита, с которым было так много проблем в прошлый раз, фильтров, и цифровой регулировки тока и расстояния между инструментом и заготовкой. Вместо этого, установлена система вибрации рабочего электрода – толстой швейной иглы. Электромагнит, соединенный последовательно с рабочими электродами поднимает иглу вверх и разрывает цепь когда игла приближается слишком близко к обрабатываемому изделию.
Напряжение блока питания около 36 В, сопротивление электромагнита – около 36 Ом. Таким образом, максимальный ток в цепи ограничен одним ампером. А поскольку игла будет постоянно прыгать, то возможно этот ток будет или достигаться в очень короткие промежутки времени, или никогда не достигаться. С другой стороны, электромагнит – это индуктивность, и при разрыве цепи напряжение может повышаться до высоких значений, чтобы сохранить ток (отсюда и искры при электроискровой обработке).
Электромагнит, направляющая и все прочее, что входит в этот узел, соединено термоклеем, а неэстетичные потеки термоклея закрыты черной самоклеющейся пленкой.
Соединение подвижного сердечника электромагнита с зажимом:
Чтобы подвижная часть (игла, сердечник и направляющая) не выпадала, прикрепим термоклеем к электромагниту ограничитель перемещения инструмента, представляющий собой гнутую стальную пластинку:
Протестируем работу системы на воздухе – идет треск, искра – все в порядке. Видимых повреждений ни на заготовке, ни на игле нет:
На этот раз мы повысим и точность приготовления 8% раствора нитрата натрия:
Запускаем процесс! Но что это?! В отличие от воздушной среды, в электролите мы не имеем никаких прыганий и искр! Одни обынчые пузыри на довольно большой площади детали.Оказалось, что электролит обладает очень хорошей проводимостью, и электромагнит срабатывает до того, как игла касается заготовки, и даже до того как она приблизится к ней на достаточно близкое расстояние. В итоге игла “зависает” довольно далеко от поверхности заготовки и травление идет по большой площади, что, увы, не совместимо с идеей точности обработки.
Искрение и прыжки начинаются когда игла находится не на границе “электролит-деталь”, а на границе “воздух-электролит”. Тогда на этой границе возникает сгусток электрического пламени характерного для соединений натрия желтого цвета:
Что ж,попробуем работу в электроискровом режиме. Для этого сольем часть электролита (возможность слива была к сожалению не предусмотрена, поэтому фактически пришлось его вычерпать), так чтобы обнажилась поверхность детали, и зальем поверх раствора масло. В книгах по электроискровой обработке используют керосин, но его под рукой не было, поэтому было использовано подсолнечное масло. Залили же его поверх раствора не из высоких научных соображений, а из экономии масла и неудобства вычерпывания раствора до дна.
В масле дело пошло веселее – появился красивый сине-зеленый огненный шарик и треск, свидетельствующий о работе установки.
Из шарика образовывались и поднимались пузыри паров масла, тонкими концентрическими кругами расходились мелкие темные частицы то ли металла, то-ли обугленного масла, а возможно и того и другого:
На фотографии сбоку из-за преломления света в масле шарик на фотографии кажется смещенным относительно иглы, хотя на самом деле он окутывал ее острие:
Из рабочей зоны пошел легкий дымок и по комнате стал распространяться аромат жареной стали (похожий на запах из работающего щеточного электродвигателя, но более тонкий).
Промоем и высушим заготовку. ЭХО (проводимая на большом расстоянии между электродами) дала широкую (гиперболическую?) пупырчатую долину. Кстати, что это за пупырышки? Чем дальше от центра, чем они меньше и многочисленнее. И есть радиус, за которым их нет. И есть радиус, за которым нет следов ЭХО. Понимание этих вещей может быть важно для развития технологии ЭХО. Возможно, имеет смысл устроить автоматизированный эксперимент с перебором ряда напряжений и прочих параметров, и составлением графика этих факторов.
Может быть, эти пупырышки – отпечатки пузырей кислорода, возникающих на менее необезжиренных участках поверхности? Не знаю. Но очен интереса проблема границы, за которой нет следов ЭХО (видна на фото слева внизу). Наверное, из-за все-же ненулевого сопротивления раствора, там напряжение падает до такого, на котором уже невозможен электролиз. Тогда для уменьшения радиуса вовлеченной в электролиз поверхности надо точно установить напряжение чуть-чуть выше минимального – тогда электролиз будет идти в минимальном радуисе вокруг электрода, что значительно повысит точность обработки.
Под микроскопом на образованном ЭИО темном пятнышке видно множество черных, видимо, вороненых (воронение ведь как раз заключается в протирке маслом раскаленной стали) микроямок.
Судя по темной области внизу скопления ямок, там они суммировались и образовали небольшой котлован. Кучность “стрельбы” оставляет желать лучшего – микроямки отстоят друг от друга намного больше собственного радиуса. Ну а что мы хотели с такой направляющей. Надо сделать более профессиональную, безлюфтовую, чтобы ямки попадали одна в другую.
Видео работы установки (если не появилось, загляните сюда через минут 15):
Выводы:
- Электромагнитная система контроля межэлектродного расстояния быстрее и точнее шаговой. Она заслуживает дальнейшего развития и применения.
- Безнасосная система надежна и хороша. Сможем ли мы обходиться только ей?
- Маленькая съемная ванна – это удобно. Крепление заготовки термоклеем – тоже (термоклей надежно фиксирует заготовку, но при некотором усилии легко отрывается рукой). Отделение ванны с двустороннего скотча проблемно, надо предусмотреть винтовое или иное удобосъемное крепление.
- Предусмотреть слив рабочей жидкости из ванны самотеком.
- Надо повышать рабочий ток, если мы хотим добиться видимых результатов. 1А это мало, то есть надо разделить контуры электромагнита (лимитирующего ток) и электролита.
- Индуктивность, соединенная последовательно с электролитом это, видимо, хорошо: стабилизация тока при ЭХО и усиление (генерация?) искры при ЭИО. Надо вместо отделенного электромагнита установить в цепь электролита дроссель с по возможности большой индуктивностью и низким омическим сопротивлением.
- С уходом от цифрового контроля тока в рабочей зоне и электромагните мы явно поторопились. Надо его вернуть.
- Надо посерьезнее подойти к выбору рабочей среды для ЭИО. Хотя бы раздобыть керосин.
- Нужна жесткая безлюфтовая система линейных перемещений.
- Нужная точная регулировка напряжения в режиме ЭХО.
ЭЛЕКТРОХИМИЧЕСКАЯ ОБРАБОТКА МЕТАЛЛОВ – это… Что такое ЭЛЕКТРОХИМИЧЕСКАЯ ОБРАБОТКА МЕТАЛЛОВ?
, группа методов, предназначенных для придания обрабатываемой металлич. детали определенной формы, заданных размеров или св-в поверхностного слоя. Осуществляется в электролизерах (электролитич. ваннах, электрохим. ячейках спец. станков, установок), где обрабатываемая деталь является либо анодом (анодная обработка), либо катодом (катодная обработка), либо тем и другим попеременно. Осн. вид катодной Э. о. м.- гальваностегия (см. Гальванотехника). Анодными методами Э. о. м. являются разл. виды электрохим. травления, полирование, формообразование, размерная обработка, оксидирование и др. Во всех анодных процессах происходит либо растворение металла (локализованное в определенных местах или равномерное по всей пов-сти), либо превращение поверхностного слоя металла в оксидный или др. слой (см. Анодное растворение).
Электрохим. травление (ЭХТ). Термин объединяет неск. технологий, основанных на анодном растворении металла. ЭХТ применяют для очистки пов-сти всевозможных деталей, проволоки, лент, труб от разнообразных загрязнений (оксидных, жировых и др.) в качестве предварит. обработки перед нанесением покрытий, прокаткой и др. ЭХТ для очистки от загрязнений производят в р-рах к-т, обычно содержащих разл. добавки (напр., ингибитор коррозии), в щелочных р-рах или расплавах при постоянном или переменном токе. ЭХТ подвергают практически любые металлы и сплавы. ЭХТ используют для осуществления т. наз. электрохим. фрезерования с целью получения заданного “рисунка” на пов-сти детали локальным анодным растворением металла. Места, к-рые не должны подвергаться растворению, покрывают слоем фоторезисторного материала или спец.
трафаретом. Т. обр. можно производить обработку деталей типа печатных плат, перфорирование, а также травление в декоративных целях. Анодным травлением удаляют заусенцы и скругляют острые кромки.
Важная область использования ЭХТ – развитие пов-сти (увеличение уд. площади пов-сти). Наиб. широкое пром. применение имеет травление алюминиевой фольги в хлоридных р-рах для электролитич. конденсаторов; этот процесс позволяет повысить уд. пов-сть в сотни раз и увеличить уд. емкость конденсаторов, уменьшить их размеры. Развитие пов-сти методом ЭХТ применяют для улучшения адгезии металла к стеклу или керамике в электронной технике, копировального слоя к печатным формам в полиграфии, усиления сцепления покрытия с металлом при эмалировании металлич. изделий и др. Анодным травлением снимают дефектные гальванич. покрытия с деталей с тем, чтобы возвратить их в произ-во, а также при регенерации металлич. пластин офсетных биметаллич. печатных форм.
ЭХТ применяют в практич. металловедении; широко известно анодное травление металлографич. шлифов для выявления микроструктуры сплавов. При этом травление проводят в таких условиях, когда достаточно резко проявляется различие скоростей растворения разных по хим. и фазовому составу компонентов сплава. В результате избирательного ЭХТ м. б. выявлены границы фаз, сегрегация фосфора в стали, дендритная структура титановых сплавов, сетка трещин в хромовом гальванопокрытии, оценена склонность нержавеющей стали к межкристаллитной коррозии.
Электрохим. полирование (ЭХП) заключается в преимущественном анодном растворении выступов на шероховатой пов-сти и приводит к достижению низкой шероховатости (электрохим. сглаживание) или зеркального блеска пов-сти (глянцевание). Глянцевание улучшает декоративные св-ва изделия, придает пов-сти высокую отражат. способность. ЭХП и сглаживание пов-сти применяют для повышения эксплуатац. надежности, долговечности и др. эксплуатац. св-в деталей. положит. влияние ЭХП на изделие объясняется неск. причинами: 1) удаление дефектного (деформированного, имеющего трещины, повышенное содержание вредных элементов) поверхностного слоя, образовавшегося при мех., термич., электрич. обработке изделия; 2) уменьшение шероховатости пов-сти и сглаживание профиля пов-сти; 3) образование тонкой поверхностной оксидной пленки, предохраняющей металл от коррозионного воздействия среды.
Анодное растворение в режимах ЭХП тонкого поверхностного слоя металла, загрязненного радиоактивными в-вами,-один из осн. методов радиохим. дезактивации оборудования. При ЭХП обычно удаляется слой металла от 2,5 до 80 мкм. Конечная шероховатость пов-сти определяется исходной шероховатостью, продолжительностью ЭХП, условиями проведения процесса (т-ра, плотность тока), составом электролита (р-ры щелочей, солей, но чаще всего смеси к-т). Получению высокого качества ЭХП мешают большие размеры кристаллитных зерен, неравномерная структура, наличие неметаллич. включений (напр., карбидов), глубокие следы прокатки, ока-линные загрязнения, слишком высокая начальная шероховатость пов-сти.
Анодное формообразование (ЭХФ) используют для изготовления деталей с заданными формой, размерами и качеством пов-сти. При ЭХФ деталь получают в условиях, когда форма катода-инструмента копируется на аноде-заготовке. Процесс проводится в потоке электролита (обычно р-ры солей, напр. NaNO3) при плотностях тока в десятки А/см 2, межэлектродном расстоянии порядка 0,1 мм. По мере растворения анода-заготовки катод с помощью спец. механизма продвигается в направлении растворения. В отличие от традиционной мех. обработки, ЭХФ характеризуется отсутствием мех. контакта между инструментом и деталью, низкими т-рой и давлением в рабочей зоне, отсутствием износа инструмента и заусенцев на обработанной детали. ЭХФ пригодно для обработки легкодеформируемых деталей, хрупких и твердых материалов, обработки в труднодоступных местах.
Электрохим. растворением с помощью вращающегося дискового электрода или др. катода-инструмента производят разрезание заготовок из разл. металлов и сплавов, тонкостенных труб, металлич. монокристаллов, полупроводниковых материалов.
Разновидность Э. о. м.- электролитный нагрев с целью термич. или хим.-термич. обработки деталей (нагрев с последующей закалкой в электролите, науглероживание, азотирование поверхностного слоя). Этот вид обработки проводится в таком режиме, когда растворение металла крайне мало, а сильный нагрев происходит при прохождении тока через парогазовый приэлектродный слой, к-рый возникает из-за вскипания электролита около электрода при высоких значениях плотности тока и напряжения.
Электрохим. оксидирование имеет две осн. разновидности: получение барьерных тонких (толщиной до мкм) и пористых толстых (до неск. сотен мкм) анодных оксидных пленок. Барьерные пленки получают в р-рах электролитов типа Н 3 ВО 3, не растворяющих оксиды, обычно в два этапа. На первом этапе – в гальваностатич. условиях; при этом напряжение увеличивается во времени, а толщина оксидной пленки пропорциональна прошедшему кол-ву электричества. После достижения заданного напряжения режим изменяют на вольтостатический: ток снижается во времени, диэлектрич. св-ва оксидной пленки повышаются. Одна из наиб. важных областей применения барьерных оксидных пленок – получение диэлектрич. слоя электролитич. конденсаторов.
Пористые анодные оксидные пленки выращивают в агрессивных по отношению к оксиду электролитах, напр. в 15%-ной H2SO4, при постоянном напряжении. Такие пленки состоят из двух слоев: тонкого барьерного и значительно более толстого пористого. Они широко применяются в качестве декоративно-защитных покрытий. Для улучшения защитных св-в после оксидирования пористые пленки подвергают операции “наполнения” (“уплотнения”), чаще всего обработкой в горячей воде. Для повышения декоративных св-в пористые пленки на алюминии окрашивают в разные цвета, подвергая обработке р-рами красителей или дополнит. элек-трохим. обработке переменным током в электролитах, содержащих соли Сu, Ni, Sn (см. Крашение оксидированного алюминия).
Новое направление Э. о. м.- микродуговое оксидирование, т. е. формирование анодной оксидной пленки в условиях протекания электрич. микроразрядов на аноде, что расширяет возможность получения оксидных покрытий с различными полезными св-вами.
Э. о. м. применяют для маркирования изделий. Нужные знаки на металлич. пов-сти получают локальным изменением цвета в результате очень неглубокого травления (или оксидирования) либо в результате рельефного травления. Получили развитие комбинир. методы обработки, в к-рых электрохим. воздействие на металл совмещено с к.-л. другим (напр., мех., эрозионным, лазерным).
Лит.: Ямпольский A.M., Травление металлов, М., 1980; Анодные оксидные покрытия на металлах и анодная зашита, 2 изд., К., 1985; Штанько В. М., Животовский Э. А., Электрохимическая обработка металлопродукции, М., 1986; Грилихес С. Я., Электрохимическое и химическое полирование, Л., 1987; Дураджи В. Н., Парсаданян А. С., Нагрев металлов в электролитной плазме, Киш., 1988; Давыдов А. Д., Козак Е., Высокоскоростное электрохимическое формообразование, М., 1990.
А. Д. Давыдов.
Химическая энциклопедия. — М.: Советская энциклопедия. Под ред. И. Л. Кнунянца. 1988.
Электрофизические и электрохимические методы обработки заготовок
Содержание страницы
Появление новых материалов, повышение требований к точности обработки, специфические требования к качеству поверхностного слоя вызвали потребность производства в применении новых методов обработки, основанных на иных, чем резание, физических процессах. К часто используемым относятся: электрофизические и электрохимические (ЭФЭХ) методы обработки; светолучевая и плазменно-лучевая обработки и обработка поверхности поверхностным пластическим деформированием.
Электрофизические и электрохимические методы используются для формообразования поверхностей заготовок из труднообрабатываемых материалов (весьма вязких, твердых и очень твердых, керамических, металлокерамических) и позволяют обрабатывать сложные фасонные внешние и внутренние поверхности, отверстия малых диаметров и т. д.
При ЭФЭХ-методах обработки механические нагрузки на обрабатываемую поверхность настолько малы, что практически не влияют на точность обработки. При ЭФЭХ-обработке не появляется наклеп обработанной поверхности, устраняются прижоги после шлифования, повышаются эксплуатационные характеристики поверхностного слоя (износостойкость, коррозионная стойкость, прочность), и лишь в ряде случаев образуется незначительный дефектный слой. Простота кинематических цепей станков для этих методов позволяет обеспечивать автоматизацию обработки и точное регулирование процессов формообразования.
1. Электрофизическая и электроэрозионная обработка
Электрофизические методы основаны на разрушении (эрозии) поверхности заготовки, происходящем в результате теплового воздействия импульсов электрического разряда, которые возникают между электродами (инструментом и заготовкой), поэтому называются электроэрозионными. Электрический разряд между электродами происходит в газовой среде или при заполнении межэлектродного промежутка диэлектрической жидкостью (керосин, минеральное масло). Эрозия электродов в жидкой среде происходит значительно интенсивнее.
При замыкании электрической цепи межэлектродное пространство ионизируется. При достижении пороговой разности потенциалов образуется канал проводимости, по которому проходит искровой или дуговой разряд. За время 10–8–10–5 с плотность тока возрастает до 8–10 кА/мм2. В результате температура на поверхности заготовки возрастает до 10 000–12 000 °С, что влечет плавление, испарение и выброс частиц материала с поверхности заготовки. Следующий импульс тока пробивает межэлектродный промежуток там, где расстояние между электродами окажется минимальным. Эрозия металла происходит до тех пор, пока расстояние между электродами не окажется больше критического (0,01–0,05 мм). При сближении электродов процесс эрозии повторяется. Кроме теплового, имеют место электростатическое, электродинамическое воздействие и кавитационные явления.
Электроэрозионную обработку подразделяют на электроискровую и электроимпульсную.
1.1 Электроискровая обработка
Электроискровая обработка основана на использовании импульсного искрового разряда между анодом (заготовкой) и катодом (инструментом). Принципиальная схема процесса показана на рис. 1. В ванне с диэлектрической жидкостью 4 размещены подставка-изолятор 7 и заготовка 6. Между заготовкой и инструментом 3 пропускается импульсный ток амплитудой 100–200 В. Импульс продолжительностью 20–200 мкс генерируется RС-генератором 1. В зависимости от энергии импульса различают обработку на особо мягких, мягких, средних и жестких режимах. Мягкие режимы позволяют вести обработку с размерной точностью до 2 мкм и шероховатостью обработанной поверхности до Rz 0,32 мкм.
Обработка на средних и жестких режимах позволяет получать фасонные открытые полости (полость штампа), цилиндрические отверстия с радиусной осью, прошивать сквозные отверстия любой поперечной формы диаметром 1–50 мм и разрезать заготовку.
Обработка на особо мягких режимах позволяет шлифовать внутреннюю поверхность особо точных отверстий малого диаметра (фильер) и проводить окончательную отделку заготовки.
Электроискровая обработка применяется для изготовления штампов, пресс-форм, фильер, режущего инструмента, деталей топливной аппаратуры двигателей, сеток и сит. Кроме того, электроискровая обработка применяется для повышения износостойкости, жаростойкости и коррозионной стойкости поверхности деталей машин, стойкости режущего инструмента, для создания шероховатости под последующее гальваническое покрытие, легирования поверхностных слоев, увеличения размеров изношенных деталей.
Рис. 1. Электроискровая обработка: 1 – RС-генератор; 2 – подача электролита; 3 – инструмент; 4 – диэлектрическая жидкость; 5 – слив электролита; 6 – заготовка; 7 – изолятор; Ds – движение подачи
Сущность электроискрового упрочнения заключена в образовании мелкодисперсной закалочной структуры и в легировании поверхностных слоев материала анода при искровом разряде в воздушной среде.
Электроискровому упрочнению подвергают кулачки, фиксаторы, направляющие, прижимы, толкатели, стержни выпускных клапанов, клинья, пазы, шлицы, отверстия.
Электроискровое упрочнение требует предварительной подготовки заготовок: удаление загрязнений, заусенцев и пятен коррозии; обеспечение шероховатости обрабатываемой поверхности не более Rz 80 мкм.
Электроискровое упрочнение проводят на мягких, средних и жестких режимах. Мягкие режимы обеспечивают получение тонкого плотного мелкодисперсного слоя. Жесткие режимы позволяют получать более толстые слои, но не обеспечивают однородность упрочненного слоя.
1.2 . Электроимпульсная обработка
Электроимпульсная обработка основана на повышенной эрозии анода при подаче импульсов малой и средней продолжительности. При импульсах большой продолжительности (дуговой разряд) значительно быстрее разрушается катод.
Униполярные импульсы создаются электромашинным 7 (рис. 2) или электронным генератором.
Продолжительность импульса составляет 500–10 000 мкс. Заготовку 5 размещают на изоляторе 6 в ванне с диэлектрической жидкостью 3. При данной обработке инструмент 2 изнашивается медленнее, чем при электроискровой. Значительная мощность импульса обеспечивает высокую производительность, но малую точность обработки, поэтому метод целесообразно применять для черновой обработки обширных полостей, фасонных наружных поверхностей и отверстий.
Высокочастотная электроискровая обработка основана на использовании высокочастотных (100–150 кГц) импульсов при малых значениях энергии разряда. Производительность метода в 50–150 раз выше по сравнению с электроискровой обработкой при одновременном повышении точностных параметров обработанной поверхности. Схема установки показана на рис. 3.
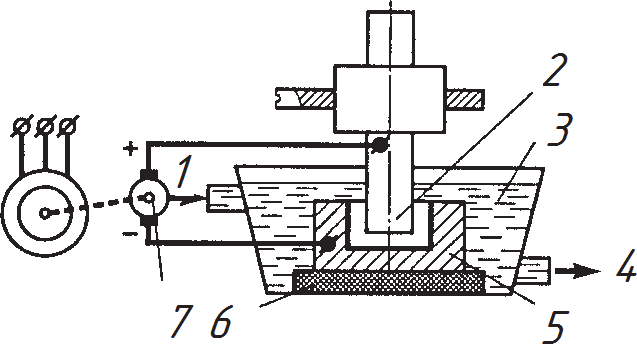
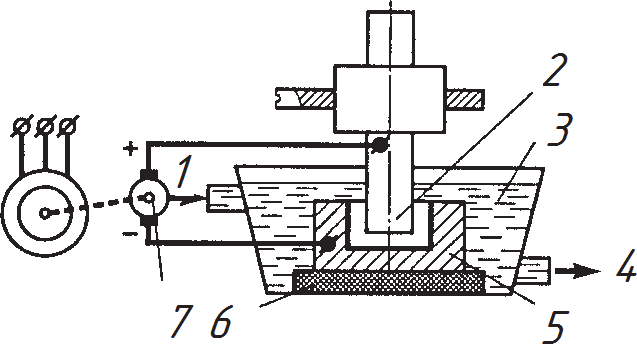
Рис. 2. Электроимпульсная обработка: 1 – подача электролита; 2 – инструмент; 3 – диэлектрическая жидкость; 4 – слив электролита; 5 – заготовка; 6 – изолятор; 7 – электромашинный генератор
Рис. 3. Высокочастотная электроимпульсная обработка: 1 – подача электролита; 2 – диэлектрическая жидкость; 3 – трансформатор; 4 – прерыватель тока; 5 – выпрямитель; 6 – слив электролита; 7 – заготовка; 8 – инструмент; Ds – движение подачи
Заготовка 7 и инструмент 8 установлены в ванне с диэлектрической жидкостью 2. Постоянное напряжение от выпрямителя 5 разрывается прерывателем тока 4 и подается на первичную обмотку импульсного трансформатора 3. Включение заготовки и инструмента во вторичную цепь трансформатора позволяет избежать возникновения дугового разряда.
2. Электрохимические методы обработки
2.1 Электрохимическая обработка, основанная на анодном растворении
Электрохимический метод обработки основан на анодном растворении выступов и впадин микронеровностей при электролизе. При прохождении постоянного электрического тока через электролит 2 (рис. 4, а)
на поверхности анода – заготовки 3 происходят химические реакции, и поверхностные слои металла превращаются в химические соединения. Продукты электролиза переходят в раствор или удаляются механическим способом.
Рис. 4. Электрохимическая обработка, основанная на анодном растворении: а – полирование; б – размерная обработка; 1 – ванна; 2 – электролит; 3 – заготовка; 4 – подача электролита; 5 – катод; 6 – слив электролита; 7 – продукты растворения; 8 – микронеровности; 9 – отверстие
При электрохимическом полировании заготовку помещают в ванну 1 с электролитом, которым в зависимости от обрабатываемого материала служат растворы кислот или щелочей. Заготовку подключают к аноду. Катод 5 представляет собой пластину из свинца, меди или стали.
При замыкании электрической цепи начинается растворение материала анода – выступов микронеровностей 8 (наибольшая плотность тока – на их вершинах). Продукты растворения 7 (окислы или соли, имеющие пониженную проводимость) заполняют впадины и препятствуют растворению металла. Избирательная скорость растворения по выступам и впадинам сглаживает микронеровности. Обработанная поверхность получает металлический блеск.
Электрохимическое полирование уменьшает глубину микротрещин, не деформирует заготовку, исключает термические изменения структуры и позволяет обрабатывать нежесткие заготовки одновременно по всей поверхности. Чаще всего этот способ применяется для финишной обработки режущих инструментов.
Особенностью электрохимической размерной обработки является электролиз в струе электролита, прокачиваемого под давлением через межэлектродный промежуток, образуемый заготовкой 3 (рис. 4, б) и катодом 5. Струя электролита удаляет и продукты электролиза из рабочей зоны. Способ позволяет одновременно обрабатывать всю поверхность за готовки, находящуюся под воздействием катода (необрабатываемые участки поверхности изолируются). Электрохимической размерной обработке подвергаются нежесткие заготовки, сложно-фасонные заготовки, фасонные полости или фасонные глухие (сквозные) отверстия в труднообрабатываемых материалах. При обработке полостей или отверстий электролит подается по сквозному или глухому центральному каналу катода через отверстия 9.
2.2 Электроабразивная обработка
Особенность электроабразивной обработки состоит в том, что катодом является абразивный инструмент 2 (рис. 5, а), выполненный на электропроводящей связке (например, бакелитовая с графитным наполнителем). Между анодом – заготовкой 1 и инструментом имеется межэлектродный зазор за счет абразивных зерен 3, выступающих из связки. В этот зазор подается электролит 4. До 90 % припуска 5 удаляется за счет анодного растворения, 10–20 % припуска удаляется механической обработкой. При использовании алмазного абразивного инструмента (электроалмазная обработка) анодным растворением удаляется до 75 % припуска. Способ применяется для отделочной обработки нежестких заготовок и заготовок из труднообрабатываемых материалов.
а б
Рис. 5. Электроабразивная обработка: а – шлифование; б – хонингование; 1 – заготовка; 2 – инструмент; 3 – абразивные зерна; 4 – электролит; 5 – припуск; 6 – хонинговальная головка; 7 – ванна; 8 – токосъемное кольцо; 9 – стол; 10 – изолятор; Dr – главное движение; Ds – движение подачи
При электрохонинговании (рис. 5, б) заготовку 1, установленную на токосъемное кольцо 8 и изолятор 10, помещают в ванну 7 с электролитом 4. Ванну устанавливают на стол 9 хонинговального станка. Кинематика процесса аналогична кинематике обычного хонингования. Однако хонинговальная головка 6 оснащена не абразивными брусками, а брусками из липы, ольхи или пластмассы. Предварительное хонингование ведут в растворе электролита NaNO3 (натриевая селитра) с добавлением абразивного
порошка зернистостью не более М28. Окончательное хонингование ведут в том же электролите, но с добавлением оксида хрома. Способ обеспечивает более низкую шероховатость поверхности – Ra 0,04–0,16 мкм (зеркальный блеск) и повышение производительности обработки в 4–5 раз.
2.3 Анодно-механическая обработка
Анодно-механическая обработка основана на комбинированном (механическом, электроэрозионном и электрохимическом) воздействии на материал заготовки. Анод – заготовку 1 (рис. 6, а) и катод – режущий инструмент 3 включают в общую электрическую цепь постоянного тока. В зазор между ними подают электролит 2 (обычно жидкое стекло – водный раствор силиката натрия). Вследствие анодного растворения на заготовке образуется защитная пленка, которая разрушается режущим инструментом. При снятии пленки между выступающими частями электродов происходят электрические разряды, что приводит к электрической эрозии.
Применение комбинации трех процессов позволяет за счет регулирования энергии отдельных составляющих проводить обработку в широких пределах. При черновой обработке операцию выполняют при большой плотности тока.
Рис. 6. Анодно-механическая обработка: а – разрезание; б – точение; в – обработка плоскости; 1 – заготовка; 2 – электролит; 3 – инструмент; Dr – главное движение; Ds – движение подачи
Основное значение имеет тепловое электроэрозионное воздействие, приводящее к интенсивному снятию материала заготовки в результате плавления и взрывообразного испарения металла в среде электролита. Анодное растворение необходимо только для образования защитной пленки, обеспечивающей концентрацию дуговых разрядов на вершинах микронеровностей. Механическое воздействие обеспечивает вынос продуктов разрушения из зоны обработки. Чистовую обработку осуществляют при малой плотности тока. Основное значение имеет механизм анодного растворения и механического разрушения пленки. Эти процессы происходят на вершинах микронеровностей, что позволяет существенно уменьшить шероховатость поверхности и повысить точность обработки.
Анодно-механической обработке подвергаются все токопроводящие материалы, высокопрочные и труднообрабатываемые сплавы, твердые сплавы, вязкие материалы. Анодно-механической обработкой разрезают заготовки (рис. 6, а), прорезают пазы и щели, точат (рис. 6, б), обрабатывают плоские поверхности (рис. 6, в), полируют поверхности, затачивают режущий инструмент.
3. Упрочнение поверхности без снятия стружки – чистовая обработка пластическим деформированием
Обработка поверхностей заготовок без снятия стружки основана на пластическом деформировании поверхностных слоев, в результате чего обеспечивается низкая шероховатость и необходимые физико-механические свойства поверхностей заготовок. Уменьшение шероховатости сопровождается смятием выступов микронеровностей.
Поверхностное пластическое деформирование (ППД) сопровождается упрочнением обработанной поверхности – наклепом, в результате повышаются все характеристики сопротивления металла деформации, уменьшается его пластичность и увеличивается твердость. В процессе ППД кристаллы сплющиваются в направлении деформации, образуется упорядоченная структура «волокнистого характера» (текстура). Упрочнение металла в незакаленных сталях происходит за счет изменений и уменьшения несовершенств структуры металла (рыхлости, уменьшение дислокаций, дробление зерен). При упрочнении закаленных сталей, кроме того, идет частичное превращение остаточного аустенита в мартенсит. Интенсивность наклепа тем выше, чем мягче сталь. Наибольшее повышение твердости наблюдается в аустенитных сталях, наименьшее – у сталей с избыточным ферритом. Поверхность, обработанная ППД, становится более долговечной и износостойкой. Обкатыванием и раскатыванием упрочняют наружные и внутренние цилиндрические, фасонные и плоские поверхности. Сущность процесса заключается в силовом воздействии на поверхность заготовки инструмента высокой твердости; в качестве такого инструмента применяют твердосплавные или закаленные ролики (рис. 7) и шарики или кристалл алмаза. Давление осуществляется только в зоне контакта инструмента с заготовкой. За счет вращения заготовки и движения подачи пятно контакта перемещается, и вся обрабатываемая поверхность оказывается пластически деформированной. Для уменьшения трения и задиров в зону обработки подают машинное масло.
Наиболее совершенным является обкатывание (раскатывание) несколькими роликами (рис. 7, б), особенно при их установке на упругих элементах, наименее производительным – обкатывание шариком. Метод реализуется на универсальных токарных станках: в резцедержатель (в пиноль задней бабки) достаточно установить оправку с обкатным инструментом.
Калибрование отверстий – перемещение с натягом в отверстии жесткого инструмента, который сглаживает микронеровности, упрочняет поверхность, повышает размерную точность. Простейшим инструментом является шарик (рис. 8, а), проталкиваемый штоком пресса. При использовании оправки с закаленным роликом (дорн), инструмент проталкивается сквозь отверстие (рис. 8, б) или вытаскивается (аналогично действию прошивки). Инструмент не обладает большой стойкостью, однако метод широко применяется вследствие простоты инструмента, оснастки и наладки.
Рис. 7. Схемы ППД: а, в – обкатывание; б – раскатывание; Dr – главное движение; Ds – движение подачи
Рис. 8. Схемы обработки отверстий: а – калибрование отверстия; б – дорнование; F – выталкивающая сила
Для повышения износостойкости заготовок на поверхностях трения выдавливают неглубокие канавки, в которых размещается смазка. Канавки выполняют вибронакатыванием (рис. 9, а). Инструмент (шарик или алмазный карандаш) устанавливают в резцедержателе и придают ему движение подачи и дополнительное движение от вибратора. Изменяя амплитуду и частоту колебаний вибратора, на обработанной поверхности получают требуемый рисунок.
Рис. 9. Разновидности ППД: а – схема вибронакатывания; б – схема накатывания рифлений; Dr – главное движение; Ds – движение подачи
Методами ППД можно нанести различные рифления на поверхность заготовки. На рис. 9, б показана схема и результат обработки. Обкатку с рифлеными роликами устанавливают в резцедержателе, а заготовку – в рабочем приспособлении токарного станка. Ролики внедряются в обрабатываемую поверхность и перемещаются вдоль заготовки. Крестовое рифление получают двумя роликами с разнонаправленными рифлениями.
Упрочнение поверхностей заготовки методами ППД возможно с применением свободного инструмента (дробеструйная обработка), ударного или виброинструмента. Способы основаны на концентрированном (ударном) воздействии инструмента на обрабатываемую поверхность. Удар производится по очень маленьким площадкам, в результате чего создается большое местное давление. Зоны, воспринявшие удар, располагаются близко друг к другу, поэтому вся обработанная поверхность оказывается наклепанной. При дробеструйной обработке заготовку подвергают ударному воздействию потока дроби, изготавливаемой из отбеленного чугуна, стали, алюминия, стекла. Заготовки помещают в закрытую емкость. Дробь под воздействием потока воздуха (или за счет центробежных сил во вращающейся емкости) с большой скоростью ударяет о заготовки. Исходная шероховатость при этом не изменяется, происходит только наклепывание поверхности. Данным способом упрочняют пружины, рессоры, штоки и т. п.
Просмотров: 2 026
Обзор процесса– ECM Technologies
Прецизионная электрохимическая обработка (pECM / PECM) – это передовая технология обработки металлов, которая предлагает решение для продуктов, которые сложно или невозможно произвести с помощью обычных технологий. PECM можно использовать для обработки практически всех металлов и сплавов. Посмотрите это видео, чтобы узнать больше о технологии pECM и ее преимуществах по сравнению с традиционными методами обработки металлов. |
/// Точная электрохимическая обработка (PECM)
Точная электрохимическая обработка, сокращенно PECM или pECM, представляет собой передовую технологию металлообработки, с помощью которой можно обрабатывать изделия, которые сложно или невозможно спроектировать с помощью традиционной обработки. Это чрезвычайно точный метод, позволяющий обрабатывать любую электропроводящую деталь благодаря тому факту, что технология основана на электролизе (т.е.е. химическое изменение, особенно разложение, производимое в электролите электрическим током). Среди его широких возможностей применения материалов даже улучшенные и жесткие для обработки металлических сплавов независимо от их твердости, прочности или термических свойств.
Во время процесса металлическая заготовка растворяется на (Обработка), локально, через , электричество (Электро), и , химия (Химия) , пока не будет достигнута требуемая сложная трехмерная форма конца.
Катод (электрод) не касается анода (заготовки).Продукт не разрезан, а растворен
/// Подробно о процессе
В процессе pECM металл растворяется в заготовке постоянным током с контролируемой скоростью в электролитической ячейке. Заготовка служит анодом и отделена зазором (который может составлять всего 10 мкм) от инструмента, который служит катодом. Следовательно, заготовка и рабочий инструмент ни в коем случае не соприкасаются. Электролит, обычно раствор соли в воде, прокачивается под давлением через межэлектродный зазор, таким образом вымывая растворенный металл с детали.По мере того, как электродный инструмент движется к заготовке, чтобы поддерживать постоянный зазор, заготовке обрабатывается форма, дополняющая инструмент.
PECM напоминает гальваническое покрытие в обратном направлении: вместо добавления материала PECM удаляет его. Этот метод также можно описать как противоположность электрохимическому или гальваническому покрытию или процессу осаждения. Благодаря бесконтактному принципу обработки заготовка не подвергается механической или термической нагрузке.
Скорость съема материала (MRR) является важной характеристикой при оценке эффективности нетрадиционных процессов обработки. В pECM удаление материала происходит за счет атомарного растворения рабочего материала. Кроме того, в отличие от предыдущих поколений машин pECM, текущая техника pECM имеет преимущества от пульсирующего источника питания и вибрирующей оси. Эта концепция позволяет обрабатывать даже продукты с минимальным зазором всего в несколько микрометров, а также формировать сложные формы как внутри, так и снаружи.
PECM состоит из четырех узлов: механической, технологической воды, управления и мощности, представленных следующими модулями:
- Система подачи инструмента
- Система фильтрации и подачи электролита
- Система управления
- Блок питания
График А.Цикл процесса PECM: путь оси механической вибрации
Это схематическое изображение синусоподобной вибрации и электрических импульсов, которые растворяют материал. Механическая вибрация с длиной хода 400 мкм обеспечивает как цикл ополаскивания, так и технологический цикл с регулируемой частотой импульсов от 0,5 мс до 5 мс. Кроме того, также можно проводить исследования и / или производство, используя более старый метод постоянного тока (с постоянным током). Это может быть особенно полезно для приложений, где скорость обработки имеет приоритет над уровнем точности.
График B. Технологический цикл PECM: взаимодействие катода и анода
Выше схематически показан электрод с осью вибрации (регулируемая частота 20-50 Гц) и заготовка с копией формы электрода. Технологическая жидкость (электролит) используется как проводящая среда и среда для переноса продуктов реакции, последние состоят из ионов металлов, гидроксидов металлов, оксидов металлов, газа и тепла.
/// Преимущества PECM
PECM имеет множество преимуществ перед традиционными методами обработки, которые можно разделить на следующие четыре группы:
- ТОЧНОСТЬ ОБРАБОТКИ
- ПРЕВОСХОДНАЯ СТАБИЛЬНОСТЬ ПРОЦЕССА
- МОЖЕТ СОЗДАТЬ МИКРОСТРУКТУРЫ
- ХРУПКИЕ И ТОНКИЕ СЕЧЕНИЯ МОЖНО БЕЗОПАСНО ОБРАБОТАТЬ
- СВОБОДА ДИЗАЙНА
- ПОЛНОФОРМА (ВКЛ.3-D ПРОДУКТЫ) ЗА ОДИН ШАГ
- ПОЛУЧЕНИЕ СЛОЖНЫХ ФОРМ И КОНТУРОВ
- ПОДХОДИТ ДЛЯ ОБРАБОТКИ ТРУДНО ДОСТУПНЫХ МЕСТ
- ЦЕЛОСТНОСТЬ ПОВЕРХНОСТИ
- ОТЛИЧНАЯ ОТДЕЛКА ПОВЕРХНОСТИ БЕЗ СОЗДАНИЯ ЗАПОРОСОВ
- СИЛЬНО ИЗНОС ЛЮБОГО ИНСТРУМЕНТА
- ОТСУТСТВИЕ МЕХАНИЧЕСКОЙ ИЛИ ТЕПЛОВОЙ НАГРУЗКИ НА ОБОРУДОВАНИЕ
- ИННОВАЦИИ В ПРОЦЕССЕ
- МАТЕРИАЛ РАСТВОРЕН, НЕ РЕЗАНО
- ОБРАБОТКА НОВЫХ ЭКЗОТИЧЕСКИХ МЕТАЛЛИЧЕСКИХ СПЛАВОВ
- ЧРЕЗВЫЧАЙНО ПОДХОДИТ ДЛЯ ОБЪЕМНОГО ПРОИЗВОДСТВА
Что такое электрохимический процесс? (с иллюстрациями)
Электрохимический процесс – это химическая реакция, которая вызывает или вызывается движением электрического тока. Эти процессы представляют собой тип окислительно-восстановительной реакции, в которой один атом или молекула отдает электрон другому атому или молекуле. В электрохимических реакциях атомы или молекулы в этой реакции находятся относительно далеко друг от друга по сравнению с другими реакциями, заставляя переносимые электроны перемещаться на большее расстояние и тем самым производить электрический ток.Многие природные явления основаны на электрохимических процессах, таких как коррозия металлов, способность некоторых морских существ генерировать электрические поля и работа нервной системы людей и других животных. Они также играют важную роль в современных технологиях, в первую очередь в хранении электроэнергии в аккумуляторах, а электрохимический процесс, называемый электролизом, важен в современной промышленности.

Деятельность нервных систем, от простых реакций и инстинктивного поведения, обнаруживаемых даже у примитивных животных, до сложных способностей к обучению и рассуждению людей, зависит от электрохимических процессов. Нейроны используют электрохимические процессы для передачи информации через нервную систему, позволяя нервной системе общаться между собой и с остальным телом.Чтобы послать сигнал, химические процессы в нейроне генерируют электрический импульс, который проходит через удлиненную структуру, называемую аксоном, до тех пор, пока не достигнет синапса, точки контакта между нейроном и соседними клетками. В синапсе электричество вызывает высвобождение химических веществ, называемых нейротрансмиттерами, которые проходят через синапс в сигнальную клетку. Затем нейротрансмиттеры химически связываются со структурами, называемыми рецепторами, на клетке-мишени, инициируя дальнейшие биохимические процессы в ней.

Способность рыб, таких как электрические угри, звездочеты и торпедные скаты, создавать электрические поля является результатом электрохимического процесса.Электрические рыбы обладают специализированными клетками, называемыми электроцитами. Транспортные белки связываются с положительными ионами калия и натрия в клетке и уносят их, создавая в клетке электрический заряд. Когда это электричество необходимо, часть нервной системы, называемая мозговым управляющим ядром, посылает электрический импульс другим нервным клеткам, который вызывает высвобождение нейромедиатора ацетилхолина. Нейротрансмиттер связывается с ацетилхолиновыми рецепторами электроцитов, что вызывает высвобождение заряда электроцитов.

В электрических батареях используются электрохимические процессы для хранения и высвобождения электричества.Химические реакции внутри электрических элементов, составляющих батарею, создают разницу в заряде между двумя половинами каждой ячейки, производя электрический ток. Перезаряжаемые батареи вырабатывают электричество с помощью обратимых химических реакций, поэтому их можно вернуть к своей исходной химической конфигурации, если электричество подается из внешнего источника. Реакции в неперезаряжаемых батареях не обладают этим качеством, хотя обычно они производят больше электроэнергии, чем аккумуляторная батарея может обеспечить за один заряд.
В аккумуляторах используется множество различных химических реакций. Никель-кадмиевые батареи, которые обычно используются в осветительных приборах и бытовых приборах, основаны на отдельных реакциях кадмия и никеля с щелочью, обычно с раствором гидроксида калия (КОН), и водой. Никель-металлогидридные батареи аналогичны, но заменяют кадмий интерметаллическим соединением, состоящим из марганца, алюминия или кобальта, смешанного с редкоземельными металлами, такими как празеодим, лантан и церий.Литиевые батареи могут использовать различные реакции с участием литиевых соединений, наиболее распространенный тип – диоксид марганца (MnO 2 ) и раствор перхлората лития (LiClO 4 ), диметоксиэтан (C 4 H 10 O). 2 ) и пропиленкарбонат (C 4 H 6 O 3 ).
Электролиз – это электрохимический процесс, в котором электрический ток используется для запуска химических реакций в веществе, содержащем свободные ионы, называемом электролитом.Электролит либо расплавляется, либо растворяется в растворителе, и в него погружаются два электрода, называемые анодом и катодом. Когда между электродами прикладывается электрический потенциал, между ними начинает течь электричество, и каждый электрод начинает притягивать ионы с зарядом, противоположным его собственному. Ионы приобретают или теряют электроны на электродах, вызывая окисление молекул около анода и восстановление молекул около катода. Электролиз используется во многих областях промышленных процессов, в том числе в металлургии, производстве химических веществ, таких как хлорат калия и (KClO 3 ) трифторуксусной кислоты (C 2 HF 3 O 2 ), а также при экстракции реактивные элементы, которые не встречаются в природе в элементарной форме, такие как натрий и магний.

Какие металлы можно использовать в качестве электродов в этой электрохимической ячейке?
Металлический магний и металлический марганец
Предложите два электролита для этой электрохимической ячейки.
Сульфат магния и сульфат марганца или нитрат магния и нитрат марганца
В каком направлении будет течь ток?
Твердое тело \ (\ text {Mg} \) окисляется с образованием ионов \ (\ text {Mg} ^ {2 +} \) на аноде.Ионы {2 +} \) восстанавливаются до формы \ (\ text {Mn} (\ text {s}) \) на катоде. Это делает катод положительным.
Электронный поток идет от отрицательного к положительному, то есть от анода к катоду. Обычный ток в обратном направлении (от катода к аноду).
Следовательно, обычный ток идет от марганцевой пластины к магниевой пластине.
Нарисуйте простой эскиз всей ячейки.
,5. Электрохимические ячейки – Chemistry LibreTexts
Прежде чем разрабатывать аналитические методы, основанные на электрохимии, стоит изучить аспекты, касающиеся электрохимических ячеек. Концепции, необходимые для понимания природы электрохимической ячейки, информативны для понимания некоторых аналитических методов, которые мы разработаем. С более практической точки зрения, батареи являются примерами электрохимических элементов.