Электроплазменная полировка: Электролитно-плазменная полировка поверхности (ЭПП) – Научный центр «Износостойкость»
alexxlab | 18.04.1989 | 0 | Разное
Плазменная полировка | Оборудование | Основы технологии
Перевести страницу
Поиск по каталогу
Каталог продукции / Технология электролитно-плазменной обработки различный металлов / Полезная информация о технологии плазменной обработки
1
Оформить заказ
Электролитно-плазменная обработка металлических изделий
С оборудованием плазменной полировки можно ознакомиться здесь
Технология электроимпульсного полирования металлов основана на использовании самопроизвольных импульсных разрядов, проходящих вдоль всей поверхности обрабатываемого изделия, погруженного в электролит, под действием постоянного напряжения положительной полярности величиной около 30 вольт. Отрицательный полюс этого напряжения прикладывается к корпусу ванны. Ванна изготавливается из нержавеющей стали и выполняет двойную задачу – является емкостью для электролита и, проводя электрический ток, распределяет его по всему объему электролита. Площадь боковой поверхности ванн превышает площадь обрабатываемой детали в несколько раз. Вдоль стенок ванны (а также со дна в небольшом количестве) при обработке выделяется водород (в мизерной концентрации), который необходимо удалять соответствующей вентиляцией.
Электролитом является водный раствор соли. Тип соли, концентрация раствора, вид добавок выбираются в зависимости от типа обрабатываемого металла.
При опускании металла в электролит, под действием сходящихся на детали со всех сторон ванны линий тока, электролит у поверхности детали вскипает, образуя парогазовую оболочку, которая начинает отделять поверхность детали от электролита, прекращая ток. В этот момент все рабочее напряжение оказывается приложенным к тонкому слою парогазовой оболочки, вызывая движение газообразных ионов. Одновременно происходит конденсация пара на электролите, прилегающем к поверхности детали, и толщина парогазовой оболочки уменьшается.
В определенный момент электролит в виде мостика касается выступа детали, происходит бросок тока, электролитный мостик вскипает и в результате чего производится воздействие на поверхность детали и восстановление изолирующих свойств парогазовой оболочки.
Указанные явления происходят на всей поверхности погруженной в электролит детали, устраняя выступы и полируя поверхность металла. При этом чистота поверхности улучшается на три-четыре класса, мелкие выступы удаляются, а крупные сглаживаются, деталь приобретает устойчивый (долговременный) металлический блеск, острые кромки притупляются, а заусенцы с толщиной при основании менее 0,3 мм удаляются.
При обработке с поверхности детали полностью удаляются жировые загрязнения, некоторые виды лакокрасочных покрытий, электрохимические и вакуумно-плазменные покрытия.
Удаляется также внедренный абразив и другие посторонние включения металла, что вместе с полированием поверхности и обнажением чистой структуры металла производит хорошую подготовку под последующее нанесение на поверхность изделий различных видов покрытий.
Указанные особенности делают технологию электроимпульсного полирования пригодной для использования в условиях массового и серийного производств. Она обладает возможностью полной автоматизации технологического процесса, простотой и доступностью устройств его реализации. Несложность и универсальность процесса, высокое качество полировки, возможность одновременной полировки в данной ванне большого количества деталей и, соответственно, высокая производительность процесса отличает и выделяет этот способ полирования от других, как прогрессивный и высокоэффективный процесс.
По производительности и экономическому эффекту она выше механического способа в З÷4 раза и в 5÷6 раз выше электрохимического.
Перед началом полировки изделий (особенно если они покрыты консистентной смазкой и т.д.) желательно обезжирить их поверхности. Это обусловлено тем, что жировые загрязнения оседают на стенках ванны в виде черного налета. Обезжиривание может проводиться любым способом, важно только, чтобы вместе с деталями в ванну полирования не заносились посторонние вещества.
Для обезжиривания могут быть рекомендован следующий состав раствора:
натр едкий, ГОСТ 22-63-79 | 20-40 г/л, |
сода кальцинированная, ГОСТ 5100-73-40 | 40-50 г/л |
натрий фосфорнокислый (трех замешенный), ГОСТ 201-76 | 20-40 г/л |
вода, ГОСТ 2874-82 | остальное |
Электролит в рабочей ванне в процессе полирования должен иметь температуру порядка 80°С. Это наиболее оптимальная температура, обеспечивающая качественное прохождение процесса полировки. Разогрев электролита производится встроенными в рабочую ванну ТЭНами. Возможно разогреть электролит самим процессом полирования, используя для этого детали небольших размеров в виде тонких штырей, располагая их вертикально.
В процессе обработки, вследствие образования парогазовой оболочки и постоянной конденсации ее на окружающем деталь электролите, выделяется большое количество тепла, которое разогревает электролит и может довести до его кипения.
При повышении температуры уменьшается потребляемый ток, соответственно уменьшается съем металла и удлиняется время обработки. При достижении температуры кипения электролита процесс полирования практически прекращается. Поэтому в процессе работы электролит необходимо охлаждать. Это производится за счет наличия в ванне рубашки охлаждения.
При работе установки по периметру ванны выделяется водород, а на детали -кислород и водяной пар, поэтому работа на установке допускается только при действии соответствующей вентиляции.
Потребляемый ток при обработке зависит от площади погруженных в электролит деталей и от температуры раствора. При увеличении площади деталей ток увеличивается, при увеличении температуры раствора ток уменьшается.
В связи с этим может возникнуть такая ситуация, когда при горячем электролите определенное количество обрабатываемых деталей потребляет допустимый ток обработки. Если тоже количество деталей опустить в холодный электролит, то ток превысит допустимый уровень для установки в несколько раз, что создаст аварийный режим и приведет к срабатыванию защиты по току.
Аналогично запрещается подавать напряжение на опущенную подвеску с деталями в электролит, это приведет к значительной перегрузке по току, так как номинальный ток призван лишь поддерживать существование парогазовой оболочки, которая создается вокруг детали при медленном опускании. При подаче напряжения на опущенную деталь, на создание всей парогазовой оболочки требуется значительное количество энергии. Поэтому необходимо подавать напряжение на поднятую подвеску с деталями, а потом медленно опускать ее в электролит.
Для протекания устойчивого анодного процесса необходимо, чтобы площадь катода была не менее чем в 5 раз более площади обрабатываемых изделий. Электрический контакт между токопроводом и изделием должен быть жестким и обеспечивать безнагревное протекание тока через обрабатываемую деталь.
Полировка “устойчиво” проводится для изделий различных конфигураций – плоских, криволинейных, сложно-профильных. Наличие глубоких отверстий (где глубина превышает диаметр отверстий) в изделии не обеспечивает качественного получения полировки по всей глубине тонких отверстий.
Существенным фактором, влияющим на качество полировки, является наружный размер изделия. Во-первых – габариты изделия должны быть такими, чтобы при полном погружении в электролит изделие не коснулось стенок и дна рабочей ванны. Во-вторых – площадь его поверхности должна быть в несколько десятков раз меньше поверхности ванны. Максимальная площадь полирования определяется размером рабочей ванны и электрической мощностью трансформатора.
Изделия мелких размеров погружаются в электролит полностью. Изделия больших размеров могут обрабатываться с погружением до половины с последующим переворотом и обработкой. Небольшой коричневый след, который остается на месте границы погружения, устраняется кратковременной обработкой (погружением).
При полировании плоских поверхностей из нержавеющей стали съем металла составляет около 2 мк/мин на сторону, а с острой грани прямого угла – около 4 мк/мин, т.е. в два раза больше. Этим объясняется быстрое притупление острых кромок.
При обработке поверхности деталей снятый металл остается в растворе в виде мелких частиц (гидроокиси железа если обрабатывается сталь), постепенно оседая на дно ванны, образуя шлам, который является ценным сырьем для лакокрасочных и других видов промышленности.
Дополнительное применение электроимпульсная обработка в электролите может найти, если необходимо удалить с поверхности детали жировые загрязнения, некоторые виды лакокрасочных покрытий, электрохимические и вакуумно-плазменные покрытия; а также для удаления с поверхности абразивных вкраплений.
Электроимпульсный метод может применяться не только для финишной поверхностной обработки и декоративного полирования широкого круга изделий, но и весьма перспективен при подготовке поверхностей различных металлов под последующее нанесение покрытий.
Важным фактором для качества полировки является правильно выдержанный состав и концентрация электролита.
Изучение возможностей электролитно-плазменной полировки конструкционных и нержавеющих сталей
Find:
Highlight allMatch case
Current View
Current View
Automatic ZoomActual SizeFit PageFull Width50%75%100%125%150%200%300%400%
Enter the password to open this PDF file:
File name:
–
File size:
–
Title:
–
Author:
–
Subject:
–
Keywords:
–
Creation Date:
–
Modification Date:
–
Creator:
–
PDF Producer:
–
PDF Version:
–
Page Count:
–
МИНОБРНАУКИ РОССИИ
Федеральное государственное бюджетное образовательное учреждение
высшего образования
«Костромской государственный университет»
(КГУ)
Институт физико-математических и естественных наук
Кафедра химии
Направление (направленность) 04. 03.01 Химия (Химия)
ИЗУЧЕНИЕ ВОЗМОЖНОСТЕЙ ЭЛЕКТРОЛИТНО-ПЛАЗМЕННОЙ
ПОЛИРОВКИ КОНСТРУКЦИОННЫХ И НЕРЖАВЕЮЩИХ СТАЛЕЙ
Выпускная квалификационная работа
Бакалаврская работа
Исполнитель: Алтухова Ольга Леонидовна, 17-Хбо-3
Руководитель: Наумов Александр Рудольфович, к.х.н., доц.
Кострома
2021
ОГЛАВЛЕНИЕ
ВВЕДЕНИЕ………………………………………………………………….……….3
Глава 1. Обзор литературы……………….………………………………………6
1.1. ЭПП как метод обработки поверхности………………………………….…6
1.1.1. Установка для ЭПП……………………………………….………………….6
1.1.2. Режимы……………………………………………………………..………..7
1.2.
Условия
электролитно-плазменной
полировки
конструкционных
и
нержавеющих сталей, влияющие на качество поверхности………………….10
1.2.1. Состав электролита……………………………………………………..….11
1.2.2. Напряжение…………………………………………………………………12
1.2.3. Температура электролита………………………………………………….15
1.2.4. Концентрация электролита…………………………………………………18
Глава 2. Материалы и методы исследования………………………………..21
2.1. Методика эксперимента……………………………………………………. …21
2.2. Контроль и управление процессом………………………………………….22
Глава 3. Экспериментальные результаты и их обсуждение……………….25
3.1. Выбор режимов ЭПП нержавеющей стали…………………………………25
3.2. Выбор режимов ЭПП конструкционной стали………………………….…29
ЗАКЛЮЧЕНИЕ………………………….………..………………………………35
СПИСОК ИСПОЛЬЗУЕМЫХ ИСТОЧНИКОВ..…………………………….36
2
ВВЕДЕНИЕ
В настоящее время для очистки, травления, электрополирования и
дезактивации
широко
используются
различные
химически
активные
растворы и композиции, часто включающие агрессивные коррозионноопасные, летучие, ядовитые, горючие компоненты, в том числе на основе
смесей сильных кислот [1].
Электролитно-плазменная
высокопроизводительная
и
полировка
экологически
(ЭПП)
чистая
–
технология,
это
которая
позволяет обрабатывать в водных растворах солей изделия из нержавеющих
и углеродистых сталей, медных и алюминиевых сплавов, латуни, цинка,
титана, кремния. Данный метод во многом лишен недостатков, присущих
традиционной электрохимической полировке в высококонцентрированных
растворах кислот, и позволяет экономить материальные и финансовые
ресурсы. Наряду с высокой производительностью электролитно-плазменная
технология имеет лучшие технические характеристики и высокое качество
обработанной поверхности: скорость обработки изделия, класс чистоты
поверхности, отсутствие внедрения частичек абразива, обезжиривание
поверхности.
Технологический
процесс
может
быть
полностью
автоматизирован; для размещения оборудования не требуются большие
производственные площади. В отличие от электрохимической полировки в
кислотных растворах, в электролитно-плазменной технологии используются
экологически безопасные водные растворы солей низкой концентрации (3–
6%), которые в несколько раз дешевле токсичных кислотных компонентов [2].
Если говорить в целом о перспективах электролитно-плазменной
технологии, то она может быть применена практически во всех отраслях
промышленности.
В
первую
очередь
следует
назвать
следующие
направления: авиастроение, железнодорожный транспорт, судостроение,
ракетостроение и космические аппараты, ядерная энергетика, энергетическое
машиностроение, ювелирная, химическая промышленность и др.
[3].
3
Полировка металлических изделий применяется не только для
придания им декоративного блеска. После полировки улучшаются их
эксплуатационные характеристики, такие как долговечность, надежность,
гигиеничность и т. д. [2].
Шероховатость поверхности связана также и с рядом других важных
функциональных показателей изделий, таких как плотность и герметичность
соединений, отражательная способность поверхности, контактная жесткость
поверхности, прочность сцепления при притирании и склеивании, качество
гальванических и лакокрасочных покрытий.
Прочность деталей также зависит от шероховатости поверхности.
Разрушение детали, особенно при переменных нагрузках, в большой степени
объясняется
концентрацией
напряжений,
являющихся
следствием
имеющихся неровностей. Чем «чище» поверхность, тем меньше возможность
возникновения поверхностных трещин от усталости металла. Чистовая
отделка деталей (доводка, полирование и т.п.) значительно повышает их
усталостную прочность.
Уменьшение шероховатости поверхности существенно улучшает
антикоррозионную стойкость деталей. Это особенно важно в том случае,
когда для поверхностей не могут быть использованы защитные покрытия
(поверхности цилиндров двигателей и др.) [4].
Практика [2] показала, что электролитно-плазменная обработка
способствует повышению работоспособности турбинных лопаток для
газовых и паровых электростанций, рабочих колес насосов и компрессоров.
При этом у полированных деталей не только повышается сопротивляемость
усталостным
знакопеременным
нагрузкам,
но
и
снижается
гидродинамическое сопротивление (увеличивается обтекаемость) в газовой и
жидкой средах, в результате чего рассеивается меньше энергии и возрастает
производительность аппарата.
Электролитно-плазменный метод позволяет производить обработку
изделий по следующим основным направлениям:
4
полирование сложнопрофильных поверхностей ответственных деталей;
зачистка заусенцев и скругление острых углов;
декоративное полирование металлоизделий;
удаление загрязнений и подготовка под нанесение покрытий [5].
Целью данной работы является исследование влияния условий
электролитно-плазменной
полировки
на
шероховатость
поверхности
конструкционных и нержавеющих сталей. Задачи данной работы:
Ознакомиться с набором режимов, считающихся оптимальными для ЭПП
конструкционных и нержавеющих сталей
Сформулировать технологию оценки эффективности процесса ЭПП через
контроль убыли массы металла, обосновать её достоинства
Утвердить подходящую для исследования форму образцов
Изучить закономерности изменения массы для разных режимов
Протестировать
технологию
оценки
эффективности
полирования,
основанную на измерении количества электричества, прошедшего через
систему. Отобрать в ходе эксперимента оптимальные режимы полировки
конструкционных и нержавеющих сталей
Сравнить
полученные
полученными
без
результаты
использования
с
литературными
данной
технологии
данными,
оценки
эффективности полирования.
Предметом исследования является влияние температуры, состава и
концентрации электролита на эффективность электролитно-плазменного
полирования конструкционных и нержавеющих сталей.
Объектом исследования являются условия электролитно-плазменного
полирования сталей.
5
ГЛАВА 1. ОБЗОР ЛИТЕРАТУРЫ
1.1.
ЭПП как метод обработки поверхности
1.1.1. Установка для ЭПП
Рис. 1. Схема экспериментальной установки для электролитноплазменного полирования в условиях естественной конвекции. 1- подставка,
2- токоподвод (-), 3- нагревательный элемент, 4 – ячейка с электролитом, 5держатель образца, 6 – направляющая планка, 7 – токоподвод (+), 8 –
станина, 9 – подъемный механизм [5]
Обрабатываемое изделие является анодом, и к нему подводится
положительный потенциал от источника питания, а катодом является рабочая
ванна, и к ней подводится отрицательный потенциал (рис. 1.). Ванна
изготавливается из нержавеющей стали и выполняет двойную задачу –
является емкостью для электролита и, проводя электрический ток,
распределяет его по всему объему электролита. Площадь боковой
поверхности ванн превышает площадь обрабатываемой детали в несколько
десятков раз. Электролитом является водный раствор соли. Тип соли,
концентрация раствора, вид добавок выбираются в зависимости от типа
обрабатываемого металла. При работе установки по периметру ванны выделяется водород, а на
детали – кислород и водяной пар, поэтому работа на установке допускается
только при действии соответствующей вентиляции.
6
При обработке поверхности деталей снятый металл остается в растворе
в виде мелких частиц (гидроокиси железа, если обрабатывается сталь),
постепенно оседая на дно ванны, образуя шлам, который является ценным
сырьем для лакокрасочных и других видов промышленности [6].
В зависимости от приложенного напряжения при прохождении
электрического тока через водный раствор электролита наблюдаются
различные режимы электрических процессов вблизи анода. Полировка
осуществляется при определённом анодном процессе [3].
1.1.2. Режимы
В
основе
данной
обработки
лежит
принцип
использования
электрических разрядов, которые происходят вдоль всей поверхности
изделия, погруженного в электролит [2]. Совместное воздействие на
поверхность детали химически активной среды и электрических разрядов
создает эффект полирования изделий. После превышения некоторых
критических величин плотностей тока и напряжения вокруг металлического
анода образуется парогазовая оболочка, оттесняющая электролит от
поверхности металла. При этом возникает многофазная система металл–
плазма–газ–электролит, а явления, происходящие в приэлектродной области,
не укладываются в рамки классической электрохимии.
При напряжении более 200 В вокруг анода образуется устойчивая
парогазовая оболочка (ПГО), оттесняющая электролит от поверхности
металла и характеризующаяся малыми колебаниями тока при U = const. В
этой области напряжений (200–350 В) происходит процесс электролитноплазменной обработки. Плотность тока уменьшается до 0,5–1,0 А/см2.
Сплошная парогазовая оболочка вокруг анода имеет толщину порядка 50
мкм и постоянно изменяет свою форму (рис. 2.). Стадии формирования
парогазовой оболочки показаны на рис. 3.
7
Рис. 2. Модель парогазовой оболочки [1]
Электрический ток в прианодной области протекает от металлического
анода к электролитному катоду через сложную систему металл–плазма–газ–
электролит. Напряженность электрического поля в оболочке достигает 6*106
В/м. При температуре около 100 °С такая напряженность вызывает
ионизацию паров, эмиссию ионов и электронов, необходимую для
поддержания стационарного тлеющего электрического разряда в оболочке.
Вблизи микровыступов напряженность электрического поля возрастает, и на
этих участках возникают импульсные искровые разряды [5].
Указанные явления происходят на всей поверхности погруженной в
электролит детали, устраняя выступы и полируя поверхность металла. При
этом чистота поверхности улучшается на три-четыре класса, мелкие выступы
удаляются, а крупные сглаживаются, деталь приобретает устойчивый
(долговременный) металлический блеск, острые кромки притупляются, а
заусенцы с толщиной при основании менее 0,3 мм удаляются. При
полировании плоских поверхностей из нержавеющей стали съем металла
составляет около 2 мкм/мин на сторону, а с острой грани прямого угла –
около 4 мкм/мин, т.е. в два раза больше. Этим объясняется притупление
острых кромок [6].
8
На практике выбор состава и концентраций компонентов электролитов
и режимов обработки по напряжению, температуре и времени осуществляют
экспериментальным путем. Получение заданной шероховатости поверхности
образца или натурного изделия и высокой светоотражательной способности
еще не означает решения технической проблемы, а является лишь
доказательством
возможности
осуществления
полировки.
Решение
технической проблемы полировки означает оптимизацию технологического
процесса по ряду параметров. Так возможна оптимизация по: классу
шероховатости поверхности, блеску, затратам электроэнергии на единицу
площади,
стоимости
обработки,
производительности,
коррозии
оборудования, ресурсу работоспособности электролита, возможности его
регенерации и утилизации, экологическим параметрам.
Таким образом, предполагается, что процесс полировки может быть
осуществлен во многих составах электролита, режимах, с использованием
устройств
различающихся
конструктивно,
обладающих
различными
технологическими и эксплуатационными свойствами. Задача состоит в том,
чтобы из многих вариантов выбрать наиболее приемлемый, учитывающий
все параметры оптимизации.
Электролитно-плазменная
полировка
дает
высокое
качество
поверхности металлов и сплавов при обработке в хорошо прогретом
электролите. Однако диапазон температур для одного и того же электролита,
при котором получают лучший результат, для различных материалов не
одинаков. Так, оптимальная температура обработки сплавов цинка 65-70 °С,
для нержавеющих сталей 75-85° С, для сплавов меди 80-90 °С, а для
алюминия 90-95 °С.
При оптимизации процесса полировки важную роль играет состав
материала.
Установлено
[3],
что
процесс
полировки
аустенитной
нержавеющей стали характеризуется низким съемом металла и эффективно
проходит при низких плотностях тока (0,15-0,2 А/см2) и при напряжениях
(300-340 В), в течение 3-5 минут. В то же время медные сплавы эффективно
9
полируются при более низких рабочих напряжениях (260-280 В) и при более
высоких плотностях тока (0,6-0,8 А/см2), но за короткое время (0,5-1) минута,
и при этом происходит интенсивный съем металла. Рис. 3. Стадии образования парогазовой оболочки (ПГО): а) подача
напряжения отсутствует; б)-д) рост и формирование ПГО; е) ПГО в
стационарном режиме [3]
Перед началом полировки изделий (особенно если они покрыты
консистентной смазкой и т.д.) желательно обезжирить их поверхности. Это
обусловлено тем, что жировые загрязнения оседают на стенках ванны в виде
черного налета. Обезжиривание может проводиться любым способом, важно
только, чтобы вместе с деталями в ванну полирования не заносились
посторонние вещества.
1.2.
Условия ЭПП конструкционных и нержавеющих сталей,
влияющие на качество поверхности
Качественными факторами, определяющими характеристики ЭПП,
являются составы электролитов, обрабатываемые металлы и сплавы, а также
гидродинамические
условия
в
электролизере.
Рабочее
напряжение,
продолжительность полирования, температура электролита, концентрации
его компонентов и другие относятся к количественным факторам. Их
10
влияние на шероховатость поверхности и показатели удаления материала
после ЭПП рассмотрено на примерах известных опубликованных данных. 1.2.1. Состав электролита
Нержавеющие стали разных марок имеют различный состав, поэтому
для полировки каждой из них подходят избирательно лишь некоторые
электролиты, приведенные в табл. 1
Таблица 1
Компоненты электролитов для полирования нержавеющих сталей
Компоненты
Сульфат аммония
Сульфат натрия
Фосфат аммония
Цитрат аммония
Карбонат натрия
Гидрокарбонат
натрия
Соляная кислота
Лимонная кислота
Серная кислота
Маннит
Этилендиаминтетраа
цетат динатрия
(Трилон Б)
Полируемые
нержавеющие стали
20Х13, 40Х13, 08Х18Н10Т,
12Х18Н10Т,
03Х16Н15М3,
1.4404, SUS304, 1.4301, Х18Н9Т
20Х13, 08Х18Н9Т, AISI 201,
12Х18Н10Т
20Х13
20Х13
08Х18Н10Т
12Х18Н10Т
12Х18Н10Т
20Х13
20Х13, 12Х18Н10Т, 1.4404
40Х13, Х18Н9Т
20Х13, 03Х16Н15М3
Ссылки
[7-12]
[9, 13]
[14]
[15]
[16]
[17, 18]
[19]
[12, 20]
[18, 21]
[22]
[18, 23]
Аналогично для полировки конструкционных сталей различных марок
может применяться лишь узкий круг определенных электролитов, указанных
в табл. 2
11
Таблица 2
Компоненты электролитов для полирования конструкционных сталей
Компоненты
Хлорид аммония
Сульфат аммония
Фторид аммония
Этилендиаминтетраа
цетат динатрия
(Трилон Б)
Полируемые
Ссылки
конструкционные стали
Углеродистые: 08кп, Ст3, 10, [2, 24-26]
20, 35, 65Г, У8А
Легированные:
30ХГСА, [27, 28]
38Х2Н2МА
Легированная: 38Х2Н2МА
[27]
Углеродистая: 65Г
Легированная: 38Х2Н2МА
[2]
[27]
Как видно, для ЭПП разных типов стали перечень допустимых
составов
электролитов
различен,
что,
несомненно,
сказывается
на
применимости тех или иных добавок. Так, лимонная кислота способна
растворять гидроксиды и оксиды двух- и трехвалентного железа, а также
оксиды хрома и никеля, переводя металлы в прочные водорастворимые
комплексы [29]. Поэтому удельный съем металла из коррозионностойких
сталей при добавке лимонной кислоты возрастает, чего не наблюдается на
конструкционных углеродистых сталях из-за активирующего действия
хлорид-ионов в процессах растворения железа и его оксидов.
1.2.2. Напряжение
Важной характеристикой результатов полирования является блеск
обработанной поверхности. ЭПП хромоникелевых сталей показало, что
глянцевая поверхность с шероховатостью Ra 0,02 мкм получается при
скорости удаления материала не более 5 мкм/мин [30]. Ее увеличение
повысит производительность, но эффект блеска будет потерян.
12
Показано, что повышение напряжения при полировании стали 20Х13 в
5%-ном растворе сульфата аммония приводит к некоторому увеличению
поверхностной шероховатости при прочих равных условиях и снижению
скорости удаления материала [31]. Эта же тенденция еще более выражена
при ЭПП нержавеющей стали SUS304 в 3%-ном растворе сульфата аммония
(рис. 4) [32]. Уменьшение напряжения также способствует увеличению съема
материала, что указывает на интенсификацию анодного растворения (рис. 5).
Рис. 4. Зависимость шероховатости поверхности стали SUS304 после
ЭПП в 3%-ном растворе сульфата аммония при его температуре 70 С при
различных напряжениях [32]
Рис. 5. Уменьшение толщины образца из стали SUS304 (40504 мм)
при ЭПП в 3%-ном растворе сульфата аммония [32].
Аналогичные данные получены для полирования стали 304, где
скорость уменьшения толщины удаляемого слоя убывает от 3,2 мкм/мин до
1,5 мкм/мин при росте напряжения от 200 до 350 В [33]. По мнению авторов,
13
более тонкая ПГО увеличивает вероятность контакта детали с электролитом,
который при соприкосновении с анодом выделяет много тепла и быстро
удаляет материал в этом месте.
Несколько
отличается
влияние
напряжения
на
шероховатость
конструкционной стали 30ХГСА, полируемой в растворах хлорида аммония
с концентрациями от 0,1 до 0,5 моль/л, то есть от 0,5 до 2,5 массовых
процентов (рис. 6) [28]. В этом случае зависимость Ra от напряжения имеет
минимум при 311 В, при более высоких напряжениях шероховатость
увеличивается.
Также показано [25], что удельный съем металла при ЭПП стали 20 в
растворе хлорида аммония от напряжения практически не зависит.
Рис. 6. Зависимость величины шероховатости стали 30ХГСА от значения
рабочего напряжения и концентрации раствора хлорида аммония (время
обработки — 6 мин) [28]
14
1.2.3. Температура электролита
Температура электролита определяет устойчивость ПГО, влияя на
электропроводность раствора, поверхностное натяжение, угол смачивания и
вязкость [34]. Кроме того, повышение температуры электролита влияет на
критические напряжения, определяющие переход от одного режима
прохождения тока к другому. Максимум тока в режиме электролиза,
наблюдаемый при переходе к режиму прерываний тока, смещается в сторону
меньших напряжений при повышении температуры электролита (рис. 7) [35].
Очевидно, что для локального вскипания нагретого электролита требуется
меньшее выделение мощности. После повышения напряжения до 180 В
происходит снижение тока до постоянного минимального значения.
Сплошная и устойчивая ПГО, оттесняющая электролит от анода, образуется
только при температурах электролита не ниже 50 С, что подтверждается
резким ростом температуры образца-анода на рис. 8.
Рис. 7. Вольт-амперная характеристика прохождения тока через
раствор сульфата аммония (5%) при его различных температурах [35]
15
Рис. 8. Вольт-температурная характеристика прохождения тока через
раствор сульфата аммония (5%) при его различных температурах [35]
Ниже 70 С качество полирования заметно ухудшается, возможен
переход в режим нагрева. Выше 90 С качество обработки также может
снизиться, а некоторые компоненты электролита быстро разлагаются,
образуя летучие продукты. Но от 70 до 90 градусов температура электролита
на шероховатость поверхности влияет мало [31].
Скорость съема стали 20 при ЭПП при повышении температуры
электролита от 50 до 90 С убывает почти в 5 раз по закону близкому к
линейному (рис. 9) [25]. Это объясняется уменьшением парообразования при
понижении
температуры
электролита
и
возрастанием
концентрации
агрессивной газовой фазы.
Близкие результаты получены при полировании стали 12Х18Н10Т в
4%-ном растворе сульфата аммония (рис. 10) [36].
16
Рис. 9. Зависимость удельного съема стали 20 при ЭПП от температуры 2,5%-ного раствора хлорида аммония. Напряжение 320 В [25] Рис. 10. Зависимость удельного съема стали 12Х18Н10Т при ЭПП от температуры 4%-ного раствора сульфата аммония. Напряжение 320 В [36] 17
1.2.4. Концентрация электролита
Состав электролита и концентрации его компонентов оказывают
влияние на очень многие стороны ЭПП. К ним относятся состав и
электропроводность ПГО, распределение тепловых потоков в системе
электролит – оболочка – электрод, химические и электрохимические реакции
в электролите, ПГО и на поверхности анода, которые и являются основой
ЭПП. Разнообразия явлений приводит к различным закономерностям,
которые описывают частные случаи полирования. Влияние концентрации раствора хлорида аммония на шероховатость
полируемой
стали
30ХГСА
показано
на
рис.
11.
[37].
Интервал
концентраций, обеспечивающих снижение шероховатости поверхности
относительно невелик.
При ЭПП нержавеющей стали SUS304 установлено, что шероховатость
поверхности снижается при повышении концентрации электролита до 6%,
достигая Ra 0,194 мкм, что ниже исходной шероховатости 0,5 мкм [38].
Снижению шероховатости стали 12Х18Н10Т при струйной подаче
электролита способствуют увеличение концентрации сульфата аммония до
0,3 моль/л и продолжительности ЭПП до 6 мин при напряжении 300 В [13].
Рис. 11. Влияние концентрации раствора хлорида аммония на
шероховатость стали 30ХГСА после ЭПП. Время полирования (мин): 1 – 5; 2
– 7; 3 – 3 [37].
18
Влияние концентраций сульфата аммония и хлорида аммония
объясняется их влиянием на процесс растворения железа. При повышении
концентраций сульфата аммония от 2,0 до 6,0 % и хлорида аммония от 1,0 до
4,0 % сульфат-ионы и хлорид-ионы активируют растворение из-за
образования нестабильных адсорбционных комплексов Fe h3Oадс SO42–адс
(рис. 12) [39]. Замедление растворения при дальнейшем повышении
концентрации указанных солей приводит к вытеснению их ионами
адсорбированных молекул
воды
с поверхности
анода
и
активным
образованием комплексов, блокирующих активные центры.
Рис. 12. Влияние концентраций сульфата аммония на удельный съем
стали 20Х13 (а) и концентрации хлорида аммония на съем стали 20 (б).
Напряжение 310 В, температура электролитов 70 С [39].
19
Изучив литературу, я пришла к выводу, что для ЭПП нержавеющих
сталей
используются
сульфат,
фосфат,
цитрат
аммония,
карбонат,
гидрокарбонат натрия, лимонная и соляная кислоты, маннит и другие
вещества. Повышение концентраций сульфата аммония от 2% до 6%
считается
нецелесообразным.
Для
ЭПП
конструкционных
сталей
используются хлорид, сульфат, фторид аммония, трилон Б, причем
наименьшая шероховатость в растворе хлорида аммония достигается при
массовой концентрации 1%. Оптимальной считается температура 70–90 °С,
причем в этом диапазоне влияние температуры на качество полирования
минимально. 20
ГЛАВА 2. МАТЕРИАЛЫ И МЕТОДЫ ИССЛЕДОВАНИЯ
2.1. Методика эксперимента
Образцы-аноды из среднеуглеродистой стали 45 и нержавеющей стали
марки Х18Н10Т диаметром 10 мм и высотой 15 мм со скругленными краями
(чтобы исключить влияние краевого эффекта, когда скорость притупления
грани прямого угла в два раза выше скорости полирования плоских
поверхностей)
обрабатывались
в
цилиндрической
ячейке
в
условиях
естественной конвекции. Выбор нержавеющей стали в качестве материала для
исследований объясняется его широким использованием и удобством в
проведении экспериментов в связи с малой склонностью к ржавению.
Применение в данной работе среднеуглеродистой стали обусловлено изучением
возможности
электролитно-плазменной
полировки
деталей
после
электролитно-плазменного насыщения этой стали легкими элементами.
В качестве электролитов использовались водные 1–7%-ные растворы
сульфата аммония х.ч. (производитель: Германия), температура которых
варьировалась от 40 до 100 ℃. Объем каждого электролита составлял 2 л, что
позволяло считать их выработку незначительной в процессе измерений, не
превышающих 20 мин. Свежий электролит перед началом работы подвергался
небольшой выработке пропусканием около 200 Кл/л и выдерживался несколько
суток, чтобы полировка всех образцов проходила в приблизительно равных
условиях.
Перед обработкой образцы зачищались затертой наждачной бумагой
зернистостью 220 с целью снятия наружного слоя после токарной обработки и
приведения поверхности к минимальной шероховатости около Ra=0.10 мкм,
после чего доводились наждачной бумагой зернистостью 100 до достижения
поверхностной шероховатости по параметру Ra=0.7±0.05 мкм и очищались
ацетоном в ультразвуковой ванне.
После подачи напряжения образцы погружались в электролит на глубину
3мм от верхнего торца. Погруженная в электролит часть токоподвода
изолировалась керамической втулкой, чтобы предотвратить характерное для
ЭПП разбрызгивание электролита и растворение токоподвода. Показания тока
и напряжения регистрировались с помощью самодельного двухканального
аналогово-цифрового
преобразователя.
Шероховатость
поверхности
измерялась профилометром TR-200. Изменение массы образцов определялось
на электронных аналитических весах Citizon CY224C с точностью ±0.0001 г.
Для соблюдения одинаковой убыли массы с образцов в ходе
эксперимента с помощью самодельного кулонометра измерялось количество
электричества, прошедшего через систему, из предположения, что при равном
количестве пропущенных кулонов травится одинаковое количество металла по
закону Фарадея.
Эффективность полировки рассчитывалась как процент уменьшения
шероховатости после обработки по сравнению с начальной, отнесенный к
убыли массы при обработке в миллиграммах.
2.2.
Контроль и управление процессом
Для имеющегося технологического процесса основными вызовами
являются стабильность температуры электролита и избежание анодного
нагрева. Система управления процессом ЭПП подробно представлена в виде
алгоритма на рисунке 13. Используемая в технологическом процессе система
управления обеспечивает регулирование параметров технологических режимов.
Для реализации этих функций счетчиком ампер-часов определяется количество
электричества,
прошедшего
через
раствор
Qп,
путем
интегрирования
фактического тока Iф по времени.
Датчиком температуры электролита
осуществляется мониторинг температуры электролита Тэ, напряжение системы
Uс
регистрируется
встроенным
в
аналогово-цифровой
вольтметром.
22
преобразователь
Рис. 13. Блок-схема алгоритма управления процессом ЭПП Перед началом работы оператор задает (блок 2) требуемые значения технологических параметров, такие как температура электролита T и начальное напряжение U. В случае, если фактическая температура электролита Тэ ниже требуемой T (блок 5) – его подогревают нажатием на рабочей камере кнопки «Вкл.», а если Тэ выше T (блок 8) – охлаждают с помощью вентилятора. После достижения необходимой температуры (блок 7) начинают поднимать напряжение системы Uс до заданного значения U. При запуске процесса – 23
погружении детали в электролит происходит сильное падение напряжения из-за
образования у поверхности образца парогазовой оболочки (ПГО), вследствие
чего требуется дополнительная корректировка напряжения до достижения
равенства Uс = U (блок 13). При напряжении 200–350 В определится
возможность образования ПГО. В случае, если напряжение будет слишком
высоким, а температура при том слишком низкой для образования толстого
слоя ПГО, обладающего высоким сопротивлением, то сила тока возрастет выше
5 А (это значение является предельным для нормального функционирования
кулонометра) и эксперимент будет неудачно завершен (блок 16). При высоких
токах вместо анодного растворения процесс уходит в анодный нагрев. В случае
образования ПГО, обладающей достаточным сопротивлением, идет процесс
полировки (блок 17). Завершение процесса происходит по прохождении через
систему заданного количества электричества Q=Qп (блок 18) отключением
напряжения (блок 20).
24
ГЛАВА 3. ЭКСПЕРИМЕНТАЛЬНЫЕ РЕЗУЛЬТАТЫ И ИХ
ОБСУЖДЕНИЕ
3.1. Выбор режимов ЭПП нержавеющей стали
Эффективность полировки рассчитывалась как процент уменьшения
шероховатости после обработки по сравнению с начальной, отнесенный к
убыли массы при обработке в миллиграммах. В литературных источниках [40,
41] также в качестве показателя эффективности полирования предлагается
использовать
отношение
снижения
шероховатости
к
удельной
массе
удаленного материала. Вообще контролировать убыль массы непременно
необходимо, так как скорость съема металла выше вначале, когда травятся
выступы профиля, а в различных режимах скорость травления разная, и
сравнивать эти режимы между собой при простом соблюдении одинакового
времени акта полировки нельзя. Однако ни в одной из работ других
исследователей не был обнаружен подход, при котором обязательным условием
справедливой оценки эффективности полирования является одинаковая убыль
массы с образцов. Для правильной интерпретации эффективности на
миллиграмм необходима одинаковая убыль массы, чтобы относительная
эффективность делилась на одинаковое значение. Для соблюдения одинаковой
убыли массы с образцов в ходе эксперимента с помощью самодельного
кулонометра измерялось количество электричества, прошедшего через систему,
из предположения, что при равном количестве пропущенных кулон травится
одинаковое количество металла по закону Фарадея.
Вначале исследовалось влияние состава электролита на сталь Х18Н10Т,
пробовались 3%-ный раствор сульфата и 3%-ный раствор хлорида аммония.
Абсолютным лидером для этой марки стали, как и показано в литературном
источнике [9], стал сульфат аммония, поскольку в хлориде при одинаковом
изменении шероховатости убыль массы в 2 раза больше, чем в сульфате, при
прочих равных условиях. Это наглядно представлено в табл. 3:
25
Таблица 3
Данные попарной полировки в 3масс% хлорида аммония и 3масс%
сульфата аммония при прочих равных условиях
Номер образца
Электролит
Q, Кл
Время, с
Т, °С
Δm, мг
1 Хлорид
100
87
80
4
2 Хлорид
200
198
80
8,02
3 Сульфат
100
74
80
1,37
4 Сульфат
200
177
80
2,96
Далее изучались закономерности изменения массы образца из стали
марки Х18Н10Т в зависимости от температуры электролита при полировке в
3%- и 5%-ных растворах сульфата аммония. Выяснилось, что допущение, в
соответствии с которым у сплавов при разных режимах полировки одинаковый
электрохимический эквивалент, неверно. На рис. 14 видно, что с увеличением
температуры убыль массы возрастает по закону близкому к линейному для
обеих концентраций, причем в 5% растворе убыль массы выше чем в 3%. Несмотря на тот факт, что во всех случаях через систему было пропущено
одинаковое
количество
электричества,
убыль
массы
для
различных
концентраций и температур различна.
Рис. 14. Зависимость убыли массы стали Х18Н10Т от температуры
электролита в 3% и 5% растворах сульфата аммония
26
Но используя электрохимический эквивалент, можно высчитать, какое
количество электричества необходимо пропустить через систему в каждом из
режимов, чтобы добиться одинаковой убыли массы и иметь возможность
справедливо сравнивать эти режимы. Добавив к эксперименту еще 7%-ный
раствор сульфата аммония, мы вычислили электрохимический эквивалент для
всех режимов (на рис. 15 представлен график зависимости эквивалента от
температуры для каждой из концентраций), и далее в каждом режиме
пропустили через систему такое необходимое количество электричества, что
убыль массы для каждого образца стала одинаковой.
Рис. 15. Зависимость электрохимического эквивалента стали Х18Н10Т от
температуры электролита в 3%-, 5%- и 7%-ных растворах сульфата аммония. Напряжение 300 В
Таким образом, появилась возможность сравнивать эффективность
полировки при различных значениях температуры и концентрации. Стоит
заметить, что графики относительной эффективности (отношение уменьшения
шероховатости к начальной шероховатости, выраженное в процентах) (рис. 16)
и эффективности на миллиграмм (относительная эффективность на каждый
27
миллиграмм снятого металла) (рис. 17) идентичны. Это связано с тем, что масса при вычислении эффективности на миллиграмм везде одинакова. Рис. 16. Зависимость относительной эффективности полировки стали Х18Н10Т от температуры электролита в 3%-, 5%- и 7%-ных растворах сульфата аммония. Напряжение 300 В Рис. 17. Зависимость эффективности на миллиграмм полировки стали Х18Н10Т от температуры электролита в 3%-, 5%- и 7%-ных растворах сульфата аммония. Напряжение 300 В 28
Исходя из представленных опытных данных, оптимальной температурой
для полировки в 3%-ном растворе сульфата аммония является 60 °С, для
полировки в 5%-ном растворе она несколько повышается, и с увеличением
концентрации раствора до 7% она возрастает до 80 °С. Причем самый высокий
показатель эффективности у 3%-ного раствора, а самый низкий – у 5%-ного.
Приблизительно этот же диапазон температур рекомендует источник [31],
однако авторы считают, что температура от 70 до 90 °С на эффективность
влияния не оказывает, а ниже 70 °С и выше 90 °С она снижается.
Полученные
данные
по
оптимальной
концентрации
электролита
расходятся с полученными в работе [13], авторы которой считают, что наиболее
высокий показатель эффективности у 5%-ного раствора сульфата аммония.
3.2. Выбор режимов ЭПП конструкционной стали
В качестве модельной конструкционной стали для исследования влияния
условий на эффективность полировки была выбрана среднеуглеродистая сталь
45. Для выбора рабочего напряжения был проведен эксперимент, результаты
которого представлены на рис. 18.
сильные колебания
При напряжении 250 В наблюдались
парогазовой оболочки, что приводило к коротким
замыканиям, когда электролит касался поверхности образца, и прекращению
процесса полировки. При напряжении свыше 350 В наблюдалось очень малое
изменение шероховатости по сравнению с начальной.
Видно, что влияние
напряжения обработки
в диапазоне 275-350 В на шероховатость не
наблюдается, а вот убыль массы образца минимальна при 300В.
29
а б Рис. 18. Влияние напряжения обработки на получаемую шероховатость (а) и убыль массы образца (б) в 3%-ном растворе сульфата аммония, при 80°С Влияние концентрации сульфата аммония представлено на рис. 19. Минимальное подтравливание образца достигается в 3%-ном растворе, а минимальная шероховатость – в 5%-ном. а б Рис. 19. Влияние концентрации сульфата аммония на убыль массы образца (а) и получаемую шероховатость (б). Напряжение 300В, температура 80 °С, начальная шероховатость 1,5мкм 30
Изменение температуры электролита должно влиять на толщину паровой
оболочки, так как при увеличении температуры уменьшается количество
энергии, необходимой для испарения воды и формирования паровой оболочки,
что должно увеличивать ее толщину при одинаковой вводимой мощности в
систему. На рис. 20 видно, что минимальная шероховатость достигается при
температуре 70-80 °С, при том что убыль массы образца уменьшается при
увеличении температуры обработки. Рис. 20. Влияние температуры электролита на получаемую шероховатость и
убыль массы образца при напряжении 300 В в 3%-ном растворе сульфата
аммония . Начальная шероховатость 1,5мкм
В дополнение к вышеизложенному, стоить заметить, что названные
наиболее эффективные температуры могут быть несколько искажены и в
действительности, вероятно, имеют чуть более высокие значения. Это вызвано
недостаточно
интенсивным
перемешиванием
в
условиях
естественной
конвекции, при этом электролит у поверхности образца разогрет сильнее, чем в
общем объеме, где происходит измерение. Взглянув на графики зависимости
силы тока от времени полировки (рис. 21, рис. 22, рис. 23), можно косвенно
предположить, до каких температур нагревается электролит у поверхности
31
образца на самом деле. При низких температурах в первый момент времени ток
очень высокий из-за медленного образования ПГО и ее малой толщины. С
течением времени происходит сильное падение тока, так как электролит у
поверхности разогревается сильнее, и ПГО становится толще. А при
температуре 100 °С ток во времени не изменяется, так как выше температуры
кипения электролит нагреться не может.
Рис. 21. Зависимость силы тока от времени полировки в 3%-ном растворе
сульфата аммония, где 1–40 °С, 2–60 °С, 3–80 °С, 4–100 °С
Рис. 22. Зависимость силы тока от времени полировки в 5%-ном растворе
сульфата аммония, где 1–40 °С, 2–60 °С, 3–80 °С, 4–100 °С
32
Рис. 23. Зависимость силы тока от времени полировки в 7%-ном растворе
сульфата аммония, где 1–40 °С, 2–60 °С, 3–80 °С, 4–100 °С
На падении тока также может сказываться уменьшение площади
поверхности обрабатываемой детали в ходе полировки при сохранении
плотности тока.
Перед началом работы через электролит пропускалось небольшое
количество электричества около 200 Кл/л, в этом состоянии раствор
выдерживался при комнатной температуре от нескольких часов до нескольких
суток, чтобы сократить влияние выработки, так как обнаруживается большая
разница в значениях водородного показателя между свежим и слегка
проработанным
электролитом. Зависимость
pH
среды
от
количества
пропущенного электричества представлена на рис. 24. Чем больше кулонов
пропущено через систему, тем кислее становится среда. Это явление можно
объяснить тем, что на аноде, помимо его растворения (1.1, 1.2), идет процесс
окисления гидроксид-анионов до кислорода и воды (2). Происходящая в этот
момент на катоде реакция восстановления катионов водорода до молекулы (3)
идет медленнее, не со 100%-ным выходом по току, из-за чего ионы OHˉ
забираются из электролита быстрее, чем H+.
33
(1.1) (1.2) (2) (3) Также подкисление среды в ходе полировки может объясняться химической реакцией (4.1, 4.2), в результате которой ионы растворившегося железа забирают из раствора гидроксид-анионы, переводя их в осадок. (4.1) (4.2) Рис. 24. Зависимость pH среды от Q для 3%- и 5%-ного растворов сульфата аммония 34
ЗАКЛЮЧЕНИЕ
1. Подходящей для исследования формой образцов является цилиндр
диаметром 10 мм и длиной 15 мм со скругленными краями (чтобы
исключить влияние краевого эффекта, когда скорость притупления
грани прямого угла в два раза выше скорости полирования плоских
поверхностей). 2. Эффективность полировки целесообразно рассчитывать как процент
уменьшения шероховатости после обработки по сравнению с
начальной, отнесенный к убыли массы при обработке в миллиграммах.
Используя электрохимический эквивалент, можно высчитать, какое
количество электричества необходимо пропустить через систему в
каждом из режимов, чтобы добиться одинаковой убыли массы и иметь
возможность справедливо сравнивать эти режимы.
3. С увеличением температуры убыль массы возрастает по закону
близкому к линейному, причем в 5%-ном растворе убыль массы выше,
чем в 3%-ном.
4. Для ЭПП нержавеющей стали марки Х18Н10Т рекомендуется
раствор сульфата аммония 3%-ный, причем у 7%-ного раствора
показатель эффективности чуть ниже, а у 5%-ного – самый низкий
температура электролита 60 °С для полировки в 3%-ном растворе,
несколько выше – для полировки в 5%-ном растворе, и 80 °С – для
полировки в 7%-ном растворе.
5. Для ЭПП конструкционной стали 45 рекомендуется
рабочее напряжение 300 В
3–5%-ный раствор сульфата аммония
температура электролита 70-80 °С.
35
СПИСОК ИСПОЛЬЗУЕМЫХ ИСТОЧНИКОВ
1. Куликов И.С. Электролитно-плазменная полировка как возможный
элемент ядерных технологий / И.С. Куликов, А.Я. Каменев, Л.А.
Климова, А.В. Левчук, А.В. Глембоцкий, П.И. Ширвель // Известия
национальной академии наук Беларуси. – Минск, 2011. – №4. – с. 54-56.
2. Куликов И.С. Электролитно-плазменная обработка материалов :
монография / И.С. Куликов. – Минск : Белорусская наука, 2010. – 232 с.
– ISBN: 978-985-08-1215-5.
3. Куликов И.С. Основные особенности и перспективы применения
технологии
электролитно-плазменной
обработки
материалов
//
Современные проблемы железнодорожного транспорта: сборник
трудов по результатам международной интернет-конференции. – 2
том., ред. К.А. Сергеев, 2019. – с. 8-14.
4. Шероховатость поверхности : методические указания к лабораторной
работе № 5 по курсу «Взаимозаменяемость и технические измерения» /
А.И. Аристов [и др.]. – М.: МАДИ, 2015. – 32 с.
5. Установка
электролитно-плазменного
полирования
струйным
поливом: сайт. – URL: http://tm.spbstu.ru/Установка_электролитноплазменного_полирования_струйным_поливом.html (дата обращения:
15.05.2020).
6. Мехтехнолоджи: офиц. сайт. – URL: http://mehtehn.ru/products/17522597
(дата обращения: 01.06.2020).
7. Belkin P.N. Plasma Electrolytic Saturation of Steels with Nitrogen and
Carbon / P.N. Belkin, A.L. Yerokhin, S.A. Kusmanov // Surf. Coat.
Technol. – 2016. – 307 Part C. – p. 1194–1218.
8. Pat. 2118412 RU (С25F3/24), Method of electrochemical polishing of
products from chromium-nickel steels. A.V. Stavyshenko, S.V. Scythian,
P.E. Nauk. 27.08.1998.
36
9. Kurguzov S.A. Electrolytic-plasma surface cleaning of steel metal / S.A.
Kurguzov, Yu.D. Zaletov, V.I. Kosmatov, O.S. Guseva, I.N. Shevtsova //
Electrotech. system. complex. – 2016. – p. 48–51.
10.Sinkevich Yu.V. Investigation of the mechanism of electric current passing
through a vapor-gas shell during the anode process / Yu.V. Sinkevich, I.N.
Yankovsky // Progr. Technol. Sist. Mach. – 2011. – p. 287–292.
11.Parfenov E.V. Plasma electrolytic treatment: modeling, diagnostics,
control : monograph / E.V. Parfenov. – Mashinostroenie, 2014. – 380 p.
12.Chirkunova
N.V.
Совершенствование
технологии
электролитно-
плазменного полирования аустенитной нержавеющей стали / N.V.
Chirkunova, A.P. Volenko, R.R. Mulyukov , M.V. Shlom // Lett. Mater. –
2013. – c. 309-311.
13.Pat. 7291 Belarus (С1). Electrolyte for plasma-electrolyte polishing of
products from aluminum and its alloys. I.S. Kulikov, A.Ya. Kamenev, V.L.
Ermakov, S.V. Vashchenko, L.A. Klimova. 30.09.2005.
14.Volenko A.P. Электролитно-плазменная обработка металлических
изделий / A.P. Volenko, O.V. Boychenko, N.V. Chirkunova // Vektor
nayki. – Tolyatti Stat. Univ., 2012. – p. 144–147.
15. Zakharov S.V. Электролитно-плазменное полирование сложнопрофильных
изделий из алюминиевого сплава Д16 / S.V. Zakharov, M.T. Korotkich //
Vestnik Concern Almaz-Antey. – 2017. – p. 83–87.
16.Plotnikov N.V. To the question of the model of electrolyte-plasma polishing
of the surface / N.
V. Plotnikov, A.M. Smyslov, D.R. Tamindarov // Vestnik
Ufa State Aviation Tech. Univ. – 2013. – p. 90–95.
17.Yerokhin A. Charge transfer mechanisms underlying Contact Glow
Discharge Electrolysis / A. Yerokhin, V.R. Mukaeva, E.V. Parfenov, N.
Laugel, A. Matthews // Electrochimica Acta. – 2019. – p. 441–456.
18.Duradji V.N. Aluminum treatment in the electrolytic plasma during the
anodic process / V.N. Duradji, D.E. Kaputkin, A.Y. Duradji // J. Eng. Sci.
Technol. Rev. – 2017. – p. 81–84.
37
19.Pat. 2283903 RU (C25F3/16, A47K10/06). Method of manufacturing a
heated towel rail. N.I. Nikitin, (RU), A.E. Parshuto, (BY), V.A.
Khlebtsevich (BY). 20.09.2006.
20.Pat. 2550393 RU (C25F5/00, C25F3/20). Method of plasma electrolytic
treatment of metal surface. V.N. Duradji, D.E. Kaputkin. 10.05.2015.
21.Veselovsky A.P. Features of electrolyte-plasma processing of metals in
non-toxic
electrolytes
/
A.P.
Veselovsky,
S.V.
Kubarsep,
L.A.
Ushomirskaya // Metalloobrab. – 2002. – p. 29–31.
22. Смыслова М.К. Влияние электролитно-плазменной обработки на
физико-химическое состояние поверхности и механические свойства
лопаток паровых турбин из стали 20Х13 / М.К. Смыслова, Д.Р.
Таминдаров, А.Б. Самаркин // Авиакосмические технологии. – 2011. –
с. 25–28.
23.Pat. 2155828 RU (7С 25F3/00). Method of electrochemical surface
treatment of metal products. Yu.V. Sinkevich. 10.09.2000
24.Иванова Н.П. Исследование морфологии и химического состава
электроимпульсно
полированной
поверхности
углеродистых
и
коррозионностойких сталей / Н.П. Иванова, Ю.В. Синькевич, В.К.
Шелег, И.Н. Янковский // Наука. Технологии. – 2012. – с. 3–10.
25.Sinkevich
Yu.V.
Исследование
выхода
металла
по
току
при
электроимпульсном полировании конструкционных углеродистых
сталей / Yu.V. Sinkevich, V.K. Sheleg, I.N. Yankovsky // Vestnik
Baranivichi State. Univ. Ser. Fiz-Math nauki. – 2013. – p. 125–130.
26.Синькевич Ю.В. Вероятностно-статистическая оценка шероховатости
поверхности
электроимпульсно
полированных
деталей
/
Ю.
В.
Синькевич, А.А. Гриневич, И.Н. Янковский // Вестник БНТУ. – 2011. –
№5. – с. 9–18.
27.Ablyaz T.R. Improving the quality of the surfaces of products obtained by
electric discharge machining by applying the technology of electrolyteplasma polishing / T.R. Ablyaz, K.R. Muratov, E.Yu. Kochergin, T.V.
38
Shakirzyanov // Vestnik Perm National Research Polytechnic University.
Engineering, Materials Science. –2018. – p. 86–93.
28.Loktev D.E. Study of the parameters of electrolyte-plasma polishing of low
alloy steel by the method of planning a full factorial experiment / D.E. Loktev,
L.A. Ushomirskaya, V.I. Novikov // Metalloobrab. – 2009. – p. 15–18.
29.Ivanova N.P. The mechanism of anodic dissolution of corrosion-resistant
and structural carbon steels in the conditions of electric pulse polishing /
N.P. Ivanova, Yu.V. Sinkevich, V.K. Sheleg, I.N. Jankowski // Nauka.
Tech. – 2013. – p. 24–30.
30.Wang J. Influence of Voltage on Electrolysis and Plasma Polishing / J.
Wang, X. Zong, J. Liu, S. Feng // Icmeim, 2017. – p. 10–15.
31.Novikov V.I. Возможности электролитно-плазменного полирования
при
обработке
деталей
с
различным
начальным
уровнем
шероховатости поверхности / V.I. Novikov, A.I. Popov, M.I. Tyukhtyaev,
M.N. Zeydan // Metalloobrab. – 2011. – p. 13–15.
32.Патент 2 495 967 РФ (С25F3/16). Method of plasma electrolytic polishing
of parts made of titanium alloys. A.M. Smyslov, D.R. Tamindarov, A.D.
Mingazhev, M.K. Smyslova, A.B. Samarkina. 20.10.2013.
33.Pat. 2133943 RU (G 01 B 7/34) Method of measuring of surface roughness.
N.A. Amirkhanova, R.R. Nevyantseva, N.F. Izmailova, T.M. Timergazina,
E.V. Parfenov. 27.07.1999.
34.Podhorsky Š. Plasma polishing of stainless steels – the electrolyte
concentration vs. gloss level, Research papers faculty of materials science
and technology in Trnava / Š. Podhorsky, V. Bajĉiĉak // Slovak Univ.
Technol. Bratislava. – 2018. – p. 171–176.
35.Pat. 2119975 RU (C 25 F 5/00). Method for determining the moment of
completion of the process of plasma electrolytic removal of coating.
N.A.
Amirkhanova, R.R. Nevyantseva, T.M. Timergazina, E.V. Parfenov.
10.10.1998.
39
36.Mukaeva V.R. Investigation of the acoustic spectrum of the process of
electrolyte-plasma polishing for the diagnosis of surface roughness / V.R.
Mukaeva, M.V. Gorbatkov, R.G. Farrakhov, E.V. Parfenov, A.L. Yerokhin
// Vestnik Ufa State Aviation Tech. Univ. – 2017. – p. 32–39.
37.Pat. 2116391 RU (С25F3/16). Method of polishing products. ON.
Amirkhanova, V.A.
Belonogov, R.G.
Kasimov,
V.N.
Goryainov.
27.07.1998.
38.Pat. 2227181 RU (C 25 F 5/00). Method for determining the moment of
completion of the process of plasma electrolytic removal of coating. R.R.
Nevyantseva, S.A. Gorbatkov, E.V. Parfenov, A.A. Bybin. 20.04.2004
39.Pat. 2355829 RU. A.M. Smyslov, M.K. Smyslova, A.D. Mingazhev, K.S.
Selivanov, V.Yu. Gordeev, S.P. Pavlinich. Method of plasma electrolytic
polishing of metal products. 20.05.2009
40.Rajput A.S. Analysis of voltage and current during the Plasma electrolytic
Polishing of stainless steel / A. S. Rajput, H. Zeidler, A. Schubert // Proc.
17th Int. Conf. Eur. Soc. Precis. Eng. Nanotechnology. – EUSPEN, 2017. –
p. 2–3.
41.Алексеев Ю.Г. Электролитно-плазменное полирование титановых и
ниобиевых сплавов / Ю.Г. Алексеев, А.Ю. Королев, В.С. Нисс, А.Е.
Паршуто, А.С. Будницкий // Наука и техника. – 2018. – с. 211–219.
40
Электролитно-плазменная обработка (ЭПО) – Prometal.by
Project Description
отполироватьповерхность
изделияочистить
сварные
швыпритупить
острые
кромкипридать
зеркальный блеск
изделиюобезжирить
поверхность и провести
подготовку для нанесения покрытийобеспечить
безупречный
внешний вид продукцииудалить
заусенцы, побежалости,
окалины и загрязненияЕСЛИ ВАМ НЕОБХОДИМО притупить острые
кромкиочистить сварные
швыпридать зеркальный
блеск изделиюотполировать поверхность
изделияудалить заусенцы,
побежалости, окалины
и загрязненияобезжирить поверхность и
провести подготовку для
нанесения покрытийобеспечить безупречный
внешний вид продукции
ЭЛЕКТРОЛИТНО-ПЛАЗМЕННАЯ ОБРАБОТКА
(ЭЛЕКТРОХИМПОЛИРОВКА В РАСТВОРЕ СОЛЕЙ)
Cовременный и безопасный метод полировки металлов
до сенсационной шероховатости Ra 0,1 – 0,01 мкм
ЭЛЕКТРОЛИТНО-ПЛАЗМЕННАЯ ОБРАБОТКА
(ЭЛЕКТРОХИМПОЛИРОВКА В РАСТВОРЕ СОЛЕЙ)
Cовременный и безопасный метод полировки металлов до сенсационной шероховатости Ra 0,1 – 0,01 мкм
Хотите узнать больше?
Ответим на все вопросы!
+(37529) 762 68 17
Хотите узнать больше?
Ответим на все вопросы!
Индивидуальноподберем способ
полирования
Вашего изделия, что обеспечит
оптимальное соотношение
«цена-качество»Полируем
без брака
изделия самых сложных форм,
малого сечения и жесткости
(максимальная площадь
одновременно обрабатываемой
поверхности: 20 дм2)Работаем с широчайшим
спектром металлов и сплавов:
полировка нержавеющей стали,
низкоуглеродистой стали, железа,
никеля, хрома, сплавов алюминия,
меди и даже титана, циркония и тантала!Беремся даже за самые
сложные и
«безнадежные» заказы
благодаря многолетнему
научному опыту и собственным
разработкамПОЧЕМУ ИМЕННО МЫ?Индивидуально подберем способ
полирования Вашего изделия,
что обеспечит оптимальное
соотношение «цена-качество»Полируем без брака изделия
самых сложных форм, малого
сечения и жесткости (max.
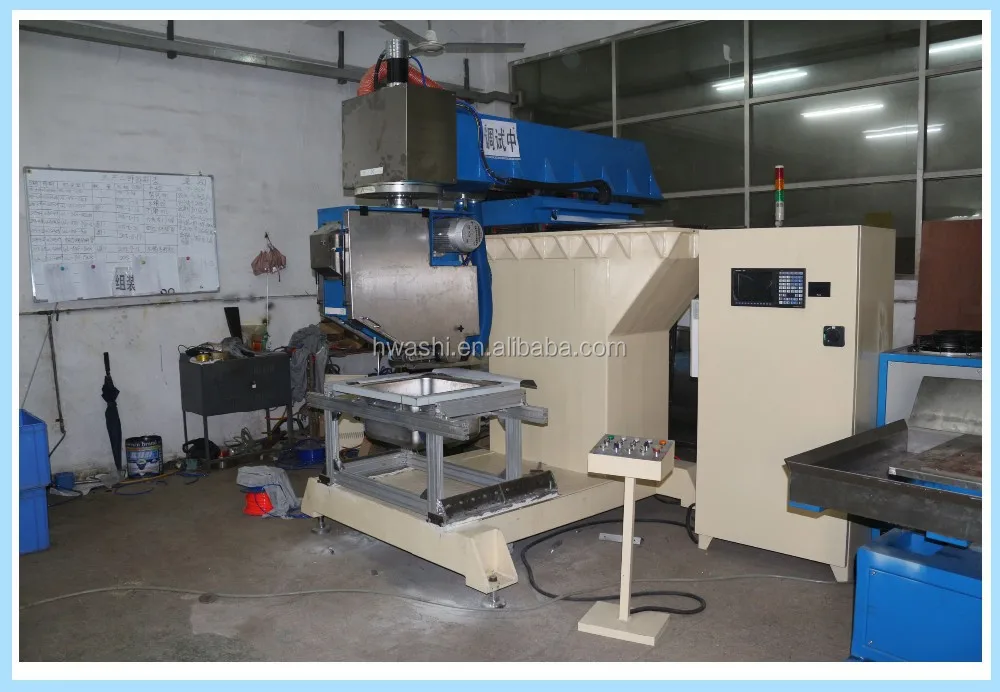
одновременно обрабатываемой
поверхности: 20 дм2)Беремся даже за самые сложные и
«безнадежные» заказы благодаря
многолетнему научному опыту и
собственным разработкамРаботаем с широчайшим спектром
металлов и сплавов: полировка железа,
нержавеющей стали, низкоуглеродистой
стали, никеля, хрома, сплавов алюминия,
меди и даже титана, циркония и тантала!
ЭПО – прекрасная альтернатива неэкологичной и высокозатратной электрохимической обработке!
+(37529) 762 68 17
ЭПО – прекрасная альтернатива неэкологичной и высокозатратной электрохимической обработке!
Как это работает?
Ещё больше сочных видео на нашем канале!
Хочу посмотреть
Снижение текущих затратна полирование на 30-40%
Срок окупаемости
готового оборудования для ЭПО
составляет 1,5 — 2 годаИспользуемый электролит
на 95% состоит из воды
Легко утилизируется
традиционными методами.
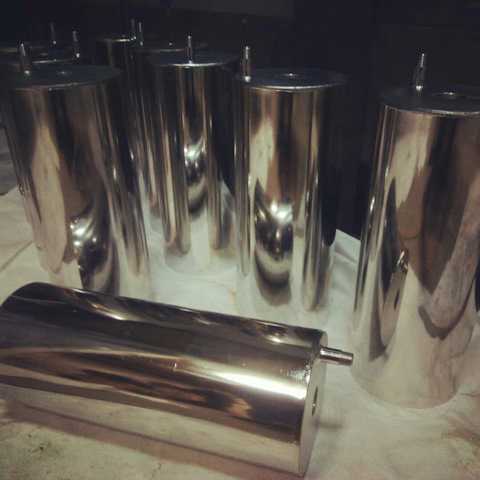
Рабочая ванна не подвергается
коррозии и эксплуатируется
в течение всего срока работы
оборудования ЭПО – более 15 лет!Уменьшение использования
растворов токсичных
кислот на 100%
Отсутствует запах при полировании.
Достаточно установки стандартных
систем вентиляции для отвода
образующегося водяного пара.
Минимальное обучение сотрудниковПолирование широкой
номенклатуры изделий:
сложной формы, малого сечения
и жёсткости, длинномерных
наружных и внутренних
поверхностей до Ra=0,1 — 0,01 мкмПРЕИМУЩЕСТВАСнижение текущих затрат на
полирование на 30-40%. Срок
окупаемости готового оборудования
для ЭПО составляет 1,5 — 2 годаПолирование широкой номенклатуры
изделий: сложной формы, малого
сечения и жёсткости, длинномерных
наружных и внутренних
поверхностей до Ra=0,1 — 0,01 мкмИспользуемый электролит на 95%
состоит из воды.

традиционными методами. Рабочая
ванна не подвергается коррозии и
эксплуатируется в течение всего срока
работы оборудования ЭПО – более 15 лет!Уменьшение использования растворов
токсичных кислот на 100%. Отсутствует
запах при полировании. Достаточно
установки стандартных систем вентиляции
для отвода образующегося водяного пара.
Минимальное обучение сотрудников
А Вы знаете, что мы ЭПОлируем даже титан марки 5!
+(37529) 762 68 17
А Вы знаете, что мы ЭПОлируем даже титан марки 5!
сантехническогооборудования:
кранов, декоративных
накладок, змеевиков,
полотенцесушителей
деталей осветительных
приборов:
отражатели,
корпусамебельной
фурнитуры:
ручек, декоративных
накладок, мебельных опордеталей торгового
оборудования:
крючков, вешалок,
держателейизделий пищевой промышленности
из нержавеющих сталей:
ложей, вилок, ножей,
тарелок, лопаток, блюдецизделий медицинской техники:
зубных и костных имплантатов,
черепных пластин,
фиксаторов позвоночника,
листов, фольги и проволоки,
используемых для скрепления тканей
и др.

отличных от деталей вращения,
деталей с полостями, поднутрениями,
выступающими конструктивными
элементамиИдеальное технологическое решение для предприятий, реализующих процессы финишной обработкисантехнического
оборудования:
кранов, декоративных накладок,
змеевиков, полотенцесушителей
мебельной фурнитуры:
ручек, декоративных
накладок, мебельных опордеталей осветительных
приборов: отражатели, корпусадеталей торгового оборудования:
крючков, вешалок, держателейизделий пищевой промышленности
из нержавеющих сталей:
ложей, вилок, ножей,
тарелок, лопаток, блюдецизделий медицинской техники:
зубных и костных имплантатов, черепных
пластин, фиксаторов позвоночника, листов,
фольги и проволоки, используемых для
скрепления тканей и др.
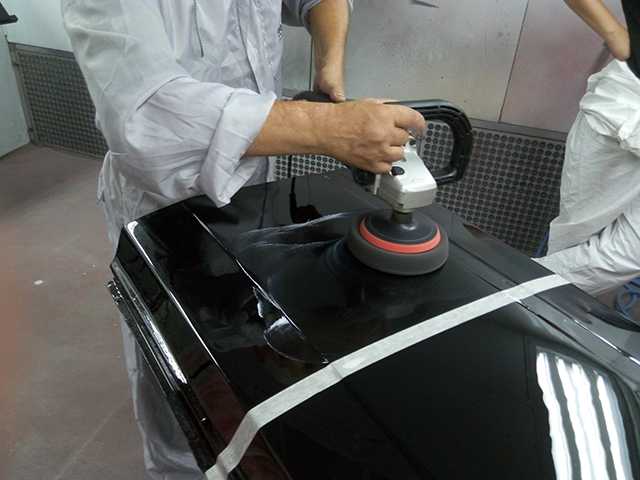
отличных от деталей вращения, деталей с
полостями, поднутрениями, выступающими
конструктивными элементами
ИЗГОТОВИМ ОБОРУДОВАНИЕ ДЛЯ ЭПО ПОД ЗАКАЗ!
Мощность: от 3 до 1000 кВт
Максимальный рабочий ток: 830 А
Максимальная площадь одновременно обрабатываемой поверхности: 280 дм2
Узнать больше
ИЗГОТОВИМ ОБОРУДОВАНИЕ ДЛЯ ЭПО ПОД ЗАКАЗ!
Мощность: от 3 до 1000 кВт
Максимальный рабочий ток: 830 А
Максимальная площадь одновременно обрабатываемой поверхности: 280 дм2
Узнать больше
Внедрение оборудования для ЭПО не требует капитальных затрат, специальных производственных помещений и систем утилизации!
+(37529) 762 68 17
Внедрение оборудования для ЭПО не требует капитальных затрат, специальных производственных помещений и систем утилизации!
автотракторное
и машиностроение,
приборостроение
кораблестроение
авиационная
промышленность
производство изделий
медицинского
назначения
технологическое
оборудование для
пищевой промышленности
химическая
промышленностьОБЛАСТИ ПРИМЕНЕНИЯ
автотракторное
и машиностроение,
приборостроение
кораблестроение
авиационная
промышленность
производство изделий
медицинского
назначения
технологическое
оборудование для
пищевой промышленности
химическая
промышленность
Полируем с сенсационной чистотой обработки Ra 0,01 мкм!
+(37529) 762 68 17
Полируем с сенсационной чистотой обработки Ra 0,01 мкм!
РАССЧИТАЕМ СТОИМОСТЬ ЗАКАЗА
ПО ВАШИМ СОБСТВЕННЫМ ЭСКИЗАМ
Присылайте
технические условия,чертежи, эскиз или фото детали/изделия
на нашу электронную почту
s-galgo65@park.
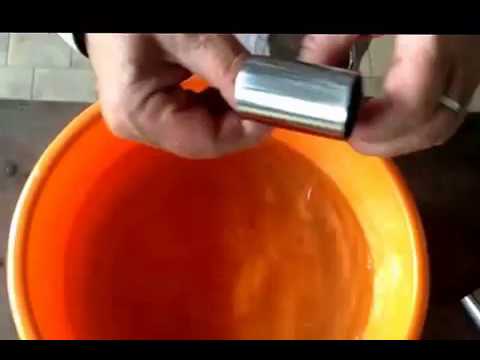
Или звоните по телефону
+(37529) 762 68 17
Заполнить заявку
Project Type
О нас
Республиканское инновационное унитарное предприятие “Научно-технологический парк БНТУ “Политехник”
25 лет разрабатываем и внедряем передовые технологии обработки металлов и нанесения покрытий
Контакты
Как нас найти?
TopПроцесс электролитно-плазменной полировки
Процесс электролитно-плазменной полировки стал применяться в промышленности сравнительно недавно и до сих пор относительно неизвестен. Нижеследующее должно объяснить процесс плазменной полировки и его преимущества. Более подробное описание смотрите по ссылкам в конце каждого раздела.
Процедура
Анодно-поляризованные металлические заготовки помещаются в электролитическую ванну для процесса плазменной полировки. Электролит состоит из раствора примерно 98% воды и 2-3% соли. При этом образуется газ, который смачивает полируемую заготовку, что приводит к возникновению плазмы, вызванной процессом. Эта плазма покрывает заготовку и приводит к уменьшению шероховатости, а также удаляет органические и неорганические загрязнения с минимальной потерей массы. В зависимости от спецификации материала типичный съем материала составляет от 2 до 8 мкм в минуту. Геометрическая форма детали практически сохраняется.
В настоящее время электролиты используются для лечения:
Группы | Материалы |
---|---|
Черные металлы: | все нержавеющие стали (полировка зависит от степени легирования и содержания углерода) |
Цветные металлы: | Латунь и ее сплавы Сплавы хром-кобальт Сплавы хром-кобальт-молибден Вольфрам Молибден |
Легкие металлы: | Титан и сплавы титана некоторые сплавы магния |
Более подробное описание процесса электролитно-плазменной полировки и сравнение с обычными процессами электрополировки.
Инновационный процесс плазменной полировки представляет собой решение в таких областях, как полировка поверхности, удаление заусенцев и очистка благодаря своим многочисленным преимуществам, таким как:
- выравнивание микронеровностей (< 0,01 мкм)
- минимальный съем материала
- возможна обработка любых контуров
- достижение беспрецедентной степени блеска
- предварительная обработка или очистка заготовок не требуются
- экологически чистые электролиты на 98% состоят из Н3О
- без использования вредных для окружающей среды веществ или высококонцентрированных кислот
- после обработки поверхности становятся более устойчивыми к коррозии, чем в исходном состоянии
- самое низкое термическое и механическое напряжение на поверхности ( t < 100°C )
- не ожидается цитотоксических эффектов на полированных плазмой поверхностях
Для получения более подробной информации о преимуществах процесса электролитно-плазменной полировки, пожалуйста, [Ссылка на сайт]
До лечения
Результат после плазменной полировки
Изображение:
BECKMANN-INSTITUT für Technologieentwicklung e. V.
Изображение:
BECKMANN-INSTITUT für Technologieentwicklung e.V.
Описание процесса плазменной полировки и существенные отличия от электрополировки
Глянцевые поверхности по эстетическим и функциональным причинам приобретают все большее значение. Для создания блестящих поверхностей необходимо удалить ряд остатков, которые образуются в процессе производства этих деталей. Они образуются, например, из-за остатков процесса литья, следов механической обработки или слоев, образующихся в результате термической обработки или процессов сварки.
По этим причинам необходимы операции полировки, обеспечивающие получение поверхностей без бороздок и других структурных дефектов геометрии поверхности. В настоящее время эффекты полировки в основном достигаются с помощью механических или химических процедур, а в последнее время также с помощью лазерных процессов. Каждый из этих процессов применяется только к ограниченному набору материалов и имеет ограничения в отношении затрат, времени обработки и воздействия на окружающую среду.
Новый метод плазменной полировки позволяет преодолеть недостатки традиционных методов полировки.
Плазменная полировка представляет собой новый подход к полировке и основан на физико-химическом воздействии, которое происходит на поверхности электродов электролитической системы в сочетании с высоким напряжением. Плазменная полировка — это электролитический процесс, при котором анодно поляризованные металлические компоненты за счет формирования плазменной мембраны, вызванной термическими и электрохимическими процессами, достигают беспрецедентного блеска, которого нельзя достичь с помощью обычных процессов полировки.
Локальное газообразование электролита на меньшем электроде (часть, служащая анодом) приводит к газовому потоку, который покрывает всю поверхность заготовки и способствует образованию плазменной мембраны. Помимо выравнивания микронеровностей с минимальной потерей массы, он также удаляет заусенцы, а также органические и неорганические загрязнения поверхности. Кроме того, вы можете наблюдать достойное ингибирование коррозии в зависимости от материала на полированных плазмой поверхностях. Плазменная полировка металла характеризуется улучшенной защитой от коррозии по сравнению с исходным состоянием.
Этот процесс дополняет или решает проблемы существующих методов обработки поверхности с достигаемыми значениями шероховатости менее 0,01 мкм. Типичное удаление материала при плазменной полировке составляет 4-8 мкм/мин в зависимости от спецификации материала и, следовательно, меньше, чем при электрополировке. Металлические детали в ванне плазменной полировки не нагреваются выше 100 °C, в том числе поверхностно.
Процесс хорошо подходит для полировки и снятия заусенцев с фрезерных, токарных и инвестиционных отливок. Этот процесс обеспечивает стабильность размеров и минимальное снятие фасок для соблюдения требуемых допусков. Поверхности закаленных деталей полируются. Термически приведенная в движение плазма вызывает горение поверхностных органических слоев за счет окислительного характера процесса. Но и неорганические вещества на поверхности могут окисляться и удаляться, если температура испарения или температура разложения продуктов реакции меньше 2000К.
Этот процесс является дополнением или решением проблемы существующих процессов обработки поверхности с достижимыми значениями шероховатости менее 0,01 мкм.
Подходящие электролиты были разработаны для следующих материалов:
Группы | Материалы |
---|---|
Черные металлы: | все нержавеющие стали, степень полировки зависит от количества легирующих элементов и содержания углерода |
Цветные металлы: | Сплавы хром-кобальт Сплавы хром-кобальт-молибден Вольфрам Молибден |
Легкие металлы: | Титан и сплавы титана некоторые сплавы магния |
Некоторые металлические композиты и технологические детали, изготовленные MIM.
О процессе плазменной полировки
Процесс плазменной полировки похож на электрополировку по своей конструкции. Деталь, которая должна быть отполирована, электрически контактирует для использования в качестве анода и погружается в электролитическую ванну в обоих случаях.
Процесс электрополировки имеет три основных отличия. Во-первых, это напряжение в электрической ванне, которое должно быть выше 200 вольт для воспламенения плазмы под водой. Результирующая поверхностная плотность тока сравнима с электрополировкой. Однако типичный съем материала при плазменной полировке со скоростью 1 мкм/мин в 10–30 раз меньше, чем при электрополировке.
Вторым важным отличием является состав электролита, который требует лишь небольшой доли растворенных в воде солей для процесса плазменной полировки.
И, наконец, третье отличие заключается в том, что до сих пор нам удавалось находить нетоксичные комбинации солей для создания стабильной плазмы, производящей особый полирующий эффект. Поскольку при плазменной полировке используются только экологически чистые химические вещества, это позволяет избежать проблем с опасными условиями труда по сравнению с традиционными методами полировки. Кроме того, плазменная полировка является экологически чистой за счет использования нетоксичных химических веществ в низкой концентрации. Любая разработка дополнительных электролитов для конкретных материалов будет осуществляться с учетом концепции воздействия на окружающую среду, возможного загрязнения материала и утилизации.
Особенности:
Металлические детали никогда не нагреваются выше 100 °C, даже поверхностно, в процессе плазменной полировки.
Плазменная полировка металла характеризуется улучшенной защитой от коррозии по сравнению с исходным состоянием.
Используемый химикат:
- Сульфат аммония с водорастворимой серой < 10 %
- дополнительно: Фосфорная кислота ок. 10% (только для удаления пятен)
- деионизированная вода
Ток полировки зависит от плотности тока на рабочей поверхности: 0,22 А/см²
Ток полировки напрямую зависит от поверхности полируемой детали.
Обзор обрабатываемых нержавеющих сталей
Ассортимент нержавеющих сталей, которые могут быть обработаны, включает в себя все спецификации материалов, удаление материала и степень блеска поверхности, которая зависит от соответствующих компонентов сплава.
Описание процесса электрополировки Основы электрополировки
Электрополировка определяется как электрохимическая обработка, которая приводит к выравниванию, блеску и пассивации металлической поверхности, которая изначально была матовой и шероховатой. Электрополировка связана с электроабразивными методами производства согласно DIN 8580. Это электрохимическое удаление поверхности в результате переноса электрического заряда между металлической заготовкой и жидкой средой – электролитом.
В принципе электрополировка представляет собой обратный гальванический процесс, при котором заготовка подключается к положительному полюсу источника постоянного напряжения (анод). Части поверхности материалов растворяются под действием постоянного тока электролита. Поверхность заглаживается, выравнивается и пассивируется.
Существенными преимуществами или особенностями электрополировки заготовок из нержавеющей стали являются достижения оптических и технических свойств поверхности. Существенной характеристикой электрополировки является истирание неровностей, что сначала приводит к уменьшению микрошероховатости, а при длительном времени обработки может уменьшить микрошероховатость. Предпочтительное истирание острых материалов приводит к тому, что края заготовки удаляются быстрее, чем остальная поверхность, а последствия механической обработки приводят к удалению мелких заусенцев. Это известно как снятие заусенцев с помощью электрополировки. Также на коррозионную стойкость нержавеющей стали благоприятно влияет электрополировка. Поскольку коррозия зависит от поверхности материала и, следовательно, от размера поверхности, особенно на микроуровне, она имеет особое значение. Кроме того, электрополировка нержавеющей стали связана с эффектом пассивации, потому что анодная цепь очень сильно подает кислород к заготовке. Таким образом, оксид хрома может образовываться на поверхности сплошным и толстым слоем, что неизбежно для коррозионной стойкости. Электрополированные поверхности из нержавеющей стали обладают большими преимуществами с гигиенической точки зрения, поскольку они также удаляют микробы и патогены во время очистки и пассивации, а также значительно снижают развитие микроорганизмов. Это особенно важно для использования в общественных местах, таких как больницы и в пищевой промышленности.
Заготовки должны удовлетворять следующим требованиям для электрополировки:
- выгодная геометрия заготовки – возможность увеличения объема для массовых деталей
- стены не должны быть слишком тонкими – контакты для блока питания
- Поверхность с высокой электропроводностью
- механически обработанная поверхность
Необходимо предусмотреть дополнительные отверстия или вентиляционные отверстия, чтобы полости можно было полностью заполнить электролитом и обеспечить последующее удаление газов, образующихся во время электрополировки, и избежать газовых карманов. Узкие зазоры, швы и валики трудно очистить от проникновения кислот, поэтому их следует избегать. В отношении допусков на прилипание следует также учитывать, что типичный съем материала во время электрополировки обычно составляет от 10 до 30 мкм, что может потребоваться ограничить соответствующими средствами.
Для качественной электрополировки необходима тщательная предварительная очистка обрабатываемых деталей. Особенно вредны смазки и оксидные слои для электрополировки. Легкие оксидные пленки, такие как налет на светящейся нержавеющей стали, легко удаляются. Перед электрополировкой необходимо всегда удалять остатки накипи.
Электрополировка нержавеющей стали в основном осуществляется в электролитах из высококонцентрированных смесей фосфорной и серной кислот с добавками для улучшения блеска, гладкого выравнивания и эффективности. Электролиты не взаимодействуют с нержавеющей сталью в безэлектролитном состоянии. Большинство электролитов для электрополировки были разработаны в США и Франции, и некоторые из них запатентованы. Содержание воды используется для оптимизации проводимости и полирующего эффекта. Электрополировочные установки обычно представляют собой ванны с соответствующей арматурой для нагрева, охлаждения и электричества.
Питание подается бесступенчатым выпрямителем. Ванна обычно имеет длину около 10 м в зависимости от применения. Детали необходимо промыть проточной водой и очистить от электролитов после электрополировки. Это можно сделать в несколько этапов, чтобы полностью удалить все остатки кислоты.
Технология
Полированные поверхности для функционального и эстетического применения приобретают все большее значение во многих областях. Для получения блестящих поверхностей необходимо удалить ряд остатков, образовавшихся в процессе изготовления этих деталей. Остатки могут образовываться, например, в процессе литья, в результате механической обработки следов или слоев, образующихся в результате процессов термообработки или сварки.
По этой причине требуются операции полировки, которые обеспечивают поверхности без бороздок и других структурных дефектов геометрии поверхности. В настоящее время эффекты полировки могут быть достигнуты с помощью механических, химических или электрохимических процессов, а в последнее время – с помощью лазерных методов. Каждый из этих методов может использоваться только для ограниченного набора материалов и имеет ограничения в отношении стоимости, времени обработки и воздействия на окружающую среду. Компания plasotec GmbH разработала новую инновационную технологию электролитно-плазменной полировки, отвечающую высоким требованиям в области обработки поверхностей.
Преимущества
Инновационный метод плазменной полировки предлагает ряд преимуществ, которые позволяют использовать его в различных областях применения. Уникальные особенности плазменной полировки делают эту технологию особенно подходящей для решения проблем полировки, очистки и удаления заусенцев с металлических поверхностей.
- выравнивание микронеровностей (< 0,01 мкм)
- типичный съем материала 2–8 мкм/мин (в 10–30 раз меньше, чем при электрополировании)
- возможна обработка любых контуров
- достижение беспрецедентной степени блеска (особенно для нержавеющих сталей)
- предварительная обработка или специальная очистка заготовок не требуются
- экологически чистые электролиты состоят из 98% водного раствора, без использования вредных для окружающей среды веществ или высококонцентрированных кислот
- после обработки поверхности более устойчивы к коррозии, чем в исходном состоянии (в зависимости от спецификации материала)
- самое низкое термическое и механическое напряжение на поверхности ( t < 100°C )
На поверхности, отполированные плазмой, нельзя ожидать цитотоксических эффектов.
Электрополировка (EP)
Электролитическая полировка обеспечивает высокий уровень гигиены и стабильность состава продукта
Электрополировка (EP) Промышленные шарики для душа с обработанной поверхностью
Электролитическая полировка (электрополировка, электрополировка, EP) использует электролитическую реакцию для расплавления металлических поверхностей, таких как нержавеющая сталь, титан и алюминий. Этот процесс используется для плавления сверхтонких неровностей и превращения объектов в сглаженные и зеркальные металлические поверхности. На поверхности электрополированного металла образуется однородная, богатая хромом пассивирующая пленка с отличной коррозионной стойкостью.
Удалите грязь с металлической поверхности и сделайте ее трудно пачкаемой
Даже если нержавеющая сталь полируется, на поверхности все еще остаются мелкие заусенцы, царапины, частицы и т. д. В случае труб и резервуаров, используемых на пищевых и химических предприятиях, это может привести к проблемам с качеством и безопасностью, таким как рост микробов из-за застойных веществ, влияние на состав продукта и коррозию металлических поверхностей.
(1) Удаляет такие загрязнения, как абразивы, металлический порошок, масла и жиры (2) Образует гладкую поверхность, которую трудно загрязнить и которую легко чистить.
Покройте металлическую поверхность однородной пленкой и создайте основание, на котором пленка может быть легко восстановлена, даже если она повреждена.
Нержавеющая сталь представляет собой сплав с превосходной коррозионной стойкостью к ржавчине, вызывающей различные проблемы. Эта характеристика достигается благодаря пассивирующей пленке (слою оксида хрома), покрывающей поверхность металла. (3) необходимо сформировать идеальную пленку, чтобы не было зазоров для ржавчины, и (4) сделать ее основой, которую можно легко ремонтировать автоматически, чтобы она могла выдерживать длительное использование.
Для электролитической полировки нержавеющая сталь, которая легко обрабатывается и не ржавеет на поверхности, дополнительно упрочняется с (1) по (4). Благодаря этим шагам внутренняя часть труб и резервуаров из нержавеющей стали всегда остается чистой.
Содержание (со ссылками)
1.Пассивация нержавеющей стали
2.Преимущества и особенности электролитического полирования
3.Электрополировочное оборудование
4. Принципы электролитической полировки
5. Состояние поверхности после электролитической полировки
6. Более совершенная электролитическая полировка
7. Электролитическая полировка для материалов, отличных от нержавеющей стали
3
e 8.Ncessity3 учитывать требования к этапам обработки до и после электролитической полировки
1. Пассивирующая пленка из нержавеющей стали
Нержавеющая сталь — это сплав железа, который очень полезен, так как не ржавеет. В дополнение к нержавеющей стали (железу) титан и алюминий обладают свойством легко подвергаться химической коррозии, но они также обладают свойством отталкивать ржавчину благодаря образующейся на поверхности оксидной пленке (пассивирующей пленке).
Даже если пассивирующая пленка нержавеющей стали повреждена, хром (Cr) в нержавеющей стали соединяется с наружным воздухом и влагой, в результате чего пленка немедленно автоматически восстанавливается, поэтому нержавеющая сталь используется в различных условиях.
Электролитическая полировка (Electro полировка, EP), как следует из названия, также сглаживает поверхность металла путем электролитического растворения, и более важным моментом является создание пассивирующей пленки в идеальном состоянии для защиты и ремонта.
Рис.1: Пассивирующая пленка из оксида хрома из нержавеющей стали
* Пассивирующая пленка из нержавеющей стали представляет собой оксид хрома (левая часть рисунка), но в реальных условиях (атмосфера и т. д.) существует в состоянии гидратированного оксигидроксида в сочетании с водой и кислородом (правая часть рисунка).
Даже если объект представляет собой материал из нержавеющей стали для санитарных целей, состояние поверхности металла из-за полировки и обработки не такое идеальное, как на молекулярной модели, показанной на рис. 1, из-за царапин, пятен и изменений. Общеизвестно, что «нержавеющая сталь не ржавеет легко». Однако, чтобы в полной мере использовать свои возможности, состояние поверхности нержавеющей стали должно быть физически и молекулярно подготовлено, чтобы она могла быстро и правильно реагировать на коррозию. Электролитическая полировка (Electro Polishing, EP) — электролитический процесс, обеспечивающий физическое сглаживание и химическую гомогенизацию для приведения поверхности нержавеющей стали в наилучшее состояние.
2. Преимущества и особенности электролитической полировки (ЭП)
(1) Особенности электролитической полировки (ЭП)
Обработанная поверхность гладкая и зеркальная
Формируется плотная пассивирующая пленка
Покрыт слоем с высоким содержанием хрома (слой с высоким содержанием хрома) с отличной коррозионной стойкостью
(2) Преимущества электролитической полировки (EP)
Удаление грязи
Снимается обработанный слой альтерации и снижается влияние на коррозионную стойкость.Трудно загрязняется
Мелкий порошок и грязь с меньшей вероятностью прилипают и остаются. Влияние их на продукт вряд ли проявится.
Очистка становится проще, а нагрузка по очистке снижается.Защита от ржавчины
Улучшается эффект предотвращения ржавчины, а влияние коррозии на продукт и аварии с утечкой становятся менее вероятными.
Повышенная устойчивость к химическим веществам и пищевым материалам, что упрощает поддержание качества.
(3) Зачем нужна электролитическая полировка (EP)? Скрытые проблемы в нагартованном слое
Проблемы нагартованного слоя
Нагартованный слой — это поверхностный слой металла, металлический материал которого изменился механически и термически из-за обработки, такой как механическая полировка, и представляет собой место, где энергия высока, то есть химически нестабильна и легко изменяется. В реальности он находится в сложном состоянии из-за разводов и царапин от полировки, грязи от абразивов и органических веществ. Обработанные трубы из нержавеющей стали и тому подобное обертываются таким неустойчивым слоем.
[Фото 2-3-1] Потенциальная хрупкость обработанного слоя и металлической поверхности
※ На рис. 2 показано изображение металлической поверхности. Это преувеличенный воображаемый вид, а не диаграмма реальной фотографии в разрезе.
Коррозионная стойкость нержавеющей стали может быть улучшена за счет формирования пассивирующей пленки на поверхности металла. Однако, когда состояние поверхности микроскопически шероховатое, трудно получить чистую и однородную пассивирующую пленку, даже если оксидная пленка образуется путем пассивации.
Даже если он визуально близок к зеркальной поверхности, существует вероятность того, что причина проблем, таких как будущая коррозия и вымывание примесей, может быть внутренней, и нельзя отрицать, что это может привести к проблемам с качеством в тяжелых производственных условиях. .
Электролитическая полировка (электрополировка, EP) – это работа по улучшению состояния и выравниванию грунта.
Обработка для удаления полировки улучшает этот нестабильный рабочий слой и максимизирует свойства, присущие нержавеющей стали. Это как переработка сайта.
[Удаление металлолома и т.п.]
Удаляет налипшие и накопившиеся загрязнения
[Разрушение хрупких пород и засыпка заболоченных участков]
Плавление структурно неустойчивых по составу металла деталей
[Выравнивание плоскостей строительным оборудованием]
Выравнивание неровностей на металлическая поверхность
[Укладка щебня и заливка бетона]
На подготовленной металлической поверхности образуется однородная неподвижная пленка.
Это создает стабильную землю, которая не позволяет осадкам течь даже в дождевой воде, не трескается на солнце, не вызывает впадин или поднятий, легко очищается и легко проходит.
Кроме того, при выравнивании обследованная площадь земли почти равна общей площади фактической поверхности, включая холмы и впадины, и сводится к минимуму. Точно так же на металлических поверхностях минимизация площади контакта с окружающей средой и жидкостями также сводит к минимуму возможность потенциальных проблем.
Слой Beilby:
Полировка металла создает на его поверхности жидкий слой толщиной приблизительно 1-10 нм. Он заполняет неровности на поверхности металла и создает кажущуюся гладкой поверхность. Слой выглядит как полированная поверхность металла, но проявляет неметаллические свойства и химически нестабилен.
Пластическая деформация:
Деформация, при которой деформация из-за внешней силы сохраняется, даже если приложенная внешняя сила устранена. Деформация, возвращающаяся к исходной, называется упругой деформацией, но при ее превышении предела возникает пластическая деформация, и форма не может быть восстановлена.
Пассивирование:
Нержавеющая сталь образует оксидную пленку даже в атмосфере, но ее легко разрушить, поскольку она тонкая и неоднородная. Следовательно, это обработка, при которой поверхность принудительно окисляется путем погружения ее в жидкость, такую как азотная кислота, для повышения коррозионной стойкости. Это также имеет эффект удаления загрязняющих веществ.
3. Оборудование для электролитической полировки
Материал помещают в раствор для электролитической полировки, а металлический материал используется в качестве анода для проведения постоянного тока.
Фактическая электролитическая полировка не так проста, как в модели ниже, а форма и расположение электродов регулируются в соответствии с формой материала и детали, подлежащей электрополировке. Мы получаем много запросов на электрополировку сложных форм, таких как сборные трубы и изготовленные на заказ емкости и внутреннюю поверхность, и мы используем различные ноу-хау для контроля электролиза.
【Рис. 3-1】Конфигурация оборудования для электролитической полировки
*Электролитическая полировка представляет собой микроскопический процесс химической реакции, который не устраняет большие неровности.
*Необходимо предварительно обработать материал из нержавеющей стали полировкой и т.д.
【Изображение 3-2】Оборудование для электролитической полировки VINA ASTEC, дочерней компании во Вьетнаме
4.

материал (нержавеющая сталь) в качестве примера.
(1) Электролитическая полировка сантехнических материалов
При увеличении изображения поверхности сантехнического материала можно увидеть множество следов полировки и царапин размером менее 1/100 мм. Существует также загрязнение мелкими частицами. Я объясню процесс сглаживания этих неровностей электролитической полировкой.
【Рисунок 4-1】Схема сечения металлического материала, подлежащего полировке
【Рисунок 4-2】Состояние поверхности металлического материала
*Единица символа SI:
Длина 1 мкм равна 1×10−6 метрам 1 мкм=0,001 мм=1000 нм
(2) Погружение в жидкость для электролитической полировки
Подсоедините электрополируемый санитарный материал к аноду (+) источника постоянного тока и погрузите его в раствор для электролитической полировки. Поместите катоды так, чтобы вся электрополированная поверхность (или каждая полируемая поверхность) металлического материала была примерно одинаковой.
【Рисунок 4-3】Погрузите материал в раствор для электролитической полировки
(3)Формирование вязкого начального оксидного слоя
При подаче напряжения металлический материал на стороне анода вступает в реакцию с раствором электролита с образованием вязкого начального оксидного слоя. Расстояние (граница раздела) между этим слоем и жидкостью электролитического полирующего раствора практически плоское. Если катод расположен правильно, интерфейс и электрод будут обращены друг к другу на почти равных расстояниях.
【Рисунок 4-4】Формирование вязкого начального участвующего слоя
По сравнению с электролитическим раствором с хорошим возбуждением, исходный оксидный слой имеет электрическое сопротивление примерно на порядок, что затрудняет прохождение электричества. Поэтому потенциал почти эквипотенциален от катода к границе раздела, а оттуда к металлу, толщина исходного оксидного слоя становится электрическим сопротивлением и происходит большое изменение протекания тока.
(4) Приоритетное элюирование с выпуклой части металла
Поскольку металлическая выпуклая часть, выступающая в сторону границы раздела, имеет низкое электрическое сопротивление, протекает большой ток и происходит растворение. Поскольку металлическая выемка находится на расстоянии от поверхности раздела, и ток не проходит легко, плавление затруднено.
Поэтому выпуклые части металла избирательно и преимущественно оплавляются, а поверхность металла постепенно становится плоской.
【Рисунок 4-5】Селективное элюирование металлов
【Рисунок 4-6】Причина избирательного элюирования выпуклых частей поверхности металла
(5) Прекращение действия электролитической полировки и образование пассивирующей пленки расстояние между границей раздела и металлом становится равным. Тогда электрическому току становится трудно равномерно протекать в любом месте металла, и эффект электролитической полировки постепенно уменьшается.
【Рисунок 4-7】Состояние металла после электролитической полировки
Чрезвычайно однородная и прочная пассивирующая пленка (оксид хрома) образуется на сплющенной металлической поверхности, покрывающей металлическую деталь. Даже при наличии неоформленной части пленки ток течет преимущественно по ней, что способствует пленкообразованию и в результате в целом формируется однородная пассивирующая пленка.
*Толщина пассивирующей пленки при обычной электролитической полировке составляет приблизительно от 1 до 3 нм (нанометров).
5. Состояние вблизи поверхности после электролитической полировки
(1) Однородная пассивирующая пленка
При полировке сантехнического материала из нержавеющей стали первоначально образовавшаяся пассивирующая пленка соскабливается, поэтому ее обычно пропитывают азотной кислотой или Например, для принудительного формирования пассивирующей пленки (метод погружения в азотную кислоту / пассивирующая обработка). Однако этим методом сложно сформировать однородную пассивирующую пленку на «микрошероховатой» металлической поверхности.
Как упоминалось выше, электролитическая полировка (ЭП) удаляет загрязнения и образует однородную пассивирующую пленку без несформированных частей на хорошо отглаженной металлической поверхности.
【Рисунок 5-1】Состояние поверхности металлического материала – после электролитической полировки
(2) Повышение способности к самовосстановлению! Поверхность с высоким содержанием хрома
Как показано на рис. 6 ниже, металлический поверхностный слой после электролитической полировки имеет концентрацию хрома (Cr) 60 % (30 % железа), что обычно составляет около 18 % в нержавеющей стали SUS316 при поверхностный слой от 1 до 3 нм. Вы можете видеть, что он находится в состоянии более высокой коррозионной стойкости, богатой хромом.
【Рисунок 5-2】Состояние поверхности нержавеющей стали после электролитической полировки концентрированного хрома
【Рисунок 5-3】Начальное изменение скорости коррозии из-за различных обработок поверхности (кипение・сверхчистая вода・в 18 МОм・SUS316)
*Толщина пассивирующей пленки при обычной электролитической полировке составляет приблизительно 1 ~ 3 нм (нанометры)
6. Более совершенная электролитическая полировка – GOLD EP / GOLD EP WHITE
У нас есть технологии и ноу-хау для выполнения GOLD EP ( или GEP) и GOLD EP WHITE (или GEPW), которые образуют более прочную пассивирующую пленку в дополнение к обычной электролитической полировке (EP) для клиентов, которым требуется более высокое качество поверхности.
Раствор для предварительной электролитической полировки | Раствор для электролитической полировки | Обработка GEP | Обработка GEPW |
---|---|---|---|
Неоднородная степень окисления и зернистые частицы легко удаляются после воздействия на поверхность. | Устранить равномерную степень окисления с помощью электрополировки. Поверхность становится ровной и гладкой металлической поверхностью. | Сжечь объект в окислительной атмосфере. Пассивирующий слой пленки оксида хрома растет и увеличивается в толщине. Кроме того, верхний слой покрывает пассивирующий слой из пленки оксида железа. | Удалить пленку оксида железа с поверхности химическим раствором. Поверхностный слой представляет собой пассивный слой из пленки оксида хрома толщиной в три раза больше, чем обычный ЭП.. |
На поверхность металла сильно влияет физическая обработка, такая как ухудшение кристаллической структуры и прилипание грязи. | Образуется обогащенный хромом слой с отличной коррозионной стойкостью. Его толщина составляет от 1 до 3 нанометров. | Эта поверхность металла подавляет вымывание ионов металлов из спиртовой жидкости или озоновой воды, имеющей большое количество остаточного кислорода. | Эта поверхность металла подавляет элюирование ионов металлов в сверхчистой воде или растворе органического амина с сильным коррозионным действием. |
【Рис. 6-1】 Сравнение общей электролитической полировки (EP) с GOLD EP и GOLD EP WHITE
* GEP означает GOLD EP, а GEPW означает GOLD EP WHITE.
Характеристики GOLD EP/GOLD EP WHITE
Эффективен против вымывания ионов металлов и загрязнения TOC (общий органический углерод)
GOLD EP: устойчив к элюированию спиртом и озоном в воде с большим количеством остаточного кислорода
GOLD EP WHITE: устойчив к элюированию сверхчистой водой и органическими аминамиВ результате получается очень гладкая поверхность, устойчивая к таким частицам, как пыль, загрязнения и т.
д.)
Отличная термостойкость и устойчивость к давлению, широкий спектр применения
Отличная обрабатываемость, например, при гибке, соединении наконечников и сварке.
Механическая прочность эквивалентна нержавеющей стали
Повышенная коррозионная стойкость за счет образования толстой пассивирующей пленки (в случае GOLD EP толщина пленки примерно в 10 раз больше, чем у обычного EP)
Подробнее о «GOLD EP/GOLD EP WHITE»
【Рисунок 6-2】 Сравнение EP и GOLD EP/GOLD EP WHITE
* GEP означает GOLD EP, а GEPW означает GOLD EP WHITE.
Мы опубликуем фотографию обычного муфтового соединения, которое было нами подвергнуто электрополировке.
(1) Электролитическая полировка сантехники / GOLD EP
Левая сторона – колено 90 градусов после общего EP (TEE 2.0S сзади), а правая сторона – GOLD EP с образованием пленки оксида железа на поверхности нержавеющей стали путем дальнейшей термообработки. Визуально большой разницы нет, кроме цвета, но GOLD EP имеет прочную пассивирующую пленку, которая примерно в 10 раз толще обычного EP.
【Рисунок 6-3】Сравнение внешнего вида фитингов с общей электролитической полировкой (ЭП) и ЗОЛОТОЙ ЭП
(2)Образцы сантехнических труб после ЗОЛОТОЙ ЭП/ЗОЛОТО ЭП БЕЛАЯ
Золотая труба – это ЗОЛОТАЯ ЭП, а белая ЗОЛОТОЙ ЭП БЕЛЫЙ. GOLD EP WHITE является результатом удаления пленки оксида железа GOLD EP, образовавшейся в результате термической обработки, путем химической обработки. Под удаленной пленкой оксида железа образуется пассивирующая пленка из толстой пленки оксида хрома (примерно в 3 раза больше, чем у обычного EP), поэтому элюирование в сверхчистую воду и органические аминовые реагенты минимально.
【Изображение 6-4】 Образцы труб после GOLD EP, GOLD EP WHITE
(3) Ротор после GOLD EP
Не только трубопроводы, по которым проходят продукты, но и оборудование, подвергающееся воздействию капель, таких как приправы и коррозионно-активные жидкости, требуют мер по защите от коррозии для важных частей, чтобы обеспечить долгосрочную работу.
【Изображение 6-5】Сравнение внешнего вида фитингов с общей электролитической полировкой (EP) и GOLD EP
Подробнее о “GOLD EP/ GOLD EP WHITE”
7. Электролитическая полировка материалов, отличных от нержавеющей стали
VINA ASTEC CO., LTD., – наша местная дочерняя компания во Вьетнаме, начала проводить электролитическую полировку активных металлов, таких как титан (Ti) и алюминий (Al) в дополнение к к нержавеющей стали (Fe).
(1) EP для алюминиевого материала
Ниже представлен образец электролитической полировки (круглый брусок) алюминия. Слева — фото до ВП, справа — фото после ВП. Отделка поперечного сечения и боковой поверхности круглого прутка отличается, но при прокатке металла в круглый прут кристаллическая структура имеет направленность, поэтому поперечное сечение имеет сатинированную поверхность. Сатинирование также проявляется в ЕР круглых прутков из нержавеющей стали.
【Изображение 7-1】Сравнение внешнего вида до и после электролитической полировки алюминиевого круглого прутка
(2) EP для титанового материала
Это образец электролитической полировки титановой детали.
【Изображение 7-2】Сравнение внешнего вида титановой детали до и после электролитической полировки
(3) Окраска титанового материала поверхность оксидной пленки отражала свет. Контролируя толщину образующейся оксидной пленки (прозрачной), можно добиться желаемого цвета.
【Изображение 7-3】Окрашивание путем образования оксидной пленки на титановых винтах
【Рисунок 7-4】интерференция отраженного света (фазовый сдвиг) поверхности металла различаются расстоянием, которое проходит через пассивацию даже при одном и том же источнике света (красная часть на рис. 7-4 слева), и, следовательно, фазовому сдвигу. В результате возникает явление, называемое «интерференцией света», при котором свет определенной длины волны (цвета) ослабляется или усиливается.
В отличие от покраски и окрашивания, окрашивание титана осуществляется с помощью этой интерференции света, поэтому, даже если вы соскребете металл, краска того цвета, который вы видите, не выйдет. Если сделать толщину пассивирующей пленки одинаковой по всему объекту, весь металл будет выглядеть одинакового цвета, а при контроле толщины пассивирующей пленки видимый цвет будет различаться.
Активный металл
Металлы с низкой энергией ионизации (слабая способность удерживать электроны на собственных атомах) легко ионизируются и называются «активными металлами». Железо, алюминий, титан и др. — активные металлы, легко растворяющиеся при взаимодействии с водой или кислотой. Кроме того, титан и алюминий являются металлами с гораздо более высокой активностью, чем железо, и можно сказать, что они «склонны к коррозии». Однако, поскольку элюированные ионы сразу же образуют твердую оксидную пленку (пассивирующую пленку), он практически используется как очень стабильный металл. Обратите внимание, что эти высокоактивные металлы также активно выделяют газ в процессе электролитической полировки.
8. Необходимость учитывать требования к этапам обработки до и после электролитической полировки
В 1985 году (Showa 60) был выпущен блокбастер Super Mario Bros., и, когда Nippon Telegraph and Telephone Public Corporation была приватизирована и стала NTT, мы промышленная электролитическая полировка. Кроме того, с 2015 года наша дочерняя компания во Вьетнаме VINA ASTEC CO., LTD. осуществляет электролитическую полировку японского качества во Вьетнаме.
Форма и размер изделий, подлежащих полировке
Мы также обладаем богатыми ноу-хау в области обработки длинномерных труб, фитингов и нестандартных изделий различной формы, таких как операции по выполнению равномерной и качественной электролитической полировки, электродов и приспособлений.
【Рис. 8】 Актуальная электролитическая полировка (ЭП) (опубликовано на YouTube))
Качество обработки поверхности, включая предварительную и последующую обработку
На наших заводах мы можем выполнять все, от механической обработки до обработки поверхности и монтажных работ, и мы всегда знаем, что наша продукция будет работать на производственных объектах и складах наших клиентов.