Форма литьевая: Литьевая форма: классификация и особенности литья
alexxlab | 26.11.1993 | 0 | Разное
Литьевая форма: классификация и особенности литья
Литьевая форма применяется в термопластавтоматах для изготовления объемных деталей различных конфигураций из пластика, металла, резины.
В пресс-форме литьевой машины может одновременно производится одна или несколько деталей. Используется в массовом или серийном производстве.
Рис. 1. Литьевая форма.
Что такое пресс-форма
Литьевые формы состоят из неподвижных матриц и подвижных пуансонов, имеющих внутри полость для формирования заготовок.
Материал внутрь формы подается с помощью литниковых систем, которые бывают холодноканальные, горячеканальные и комбинированные.
В некоторых конструкциях форм возможна установка закладных деталей.
Классификация литья
Литье пластмассы в пресс-форму применяется для создания тонкостенных изделий различной конфигурации.
Технология литья позволяет создавать армированные и пустотелые детали, многоцветные и соединяющие в себе различные полимерные материалы.
Требуемый показатель давления — от 80 до 200 Мпа. При более низком давлении могут образовываться полости или недоливы.
Превышение показателей может привести к образованию облоя.
Литье в песчаные формы
Один из самых распространенных видов литья объемных заготовок.
Применяется в автомобильной отрасли, станкостроении и других отраслях промышленности. Эта технология используются при массовом производстве, изготовлении небольших серий или единичных товаров простой или сложной формы.
При таком литье получаются изделия низкого качества. Возможно наличие пустот и различных посторонних включений.
Обычно литье в песчано-глиняные формы применяют для изготовления станин для металлообрабатывающей отрасли, корпусных элементов машин и оборудования, различных колес, колец и прочих объемных и тяжелых заготовок.
Литье в вакуумно пленочные формы
Технология применяется для отливок любого количества изделий весом от одного килограмма до десяти тонн, размерами до нескольких метров.
Формы изготавливаются в следующем порядке:
Рис. 2. Литье в вакуумную форму.
Аналогично изготавливаются все детали и собираются в единую форму.
В течение всего технологического процесса составные элементы формы находятся под вакуумом.
В собранную форму заливается расплавленный металл. После охлаждения отливок вакуумное устройство отключается, вследствие чего песок удаляется из формы, отливка легко вынимается из формы.
Литье в кокиль
Кокиль — металлическая многооборотная форма из чугуна, алюминия или стали.
Литье в кокиль подходит для изготовления изделий из алюминия, цветных и черных металлов.
Технология литья в кокиль состоит из нескольких этапов:
Рис. 3. Литье в кокиль.
Отливки в кокиль отличаются высоким качеством и геометрической точностью размеров.
Литье по выплавляемым моделям
Способ получения отливок заключается в изготовлении модели из легкоплавких составов в пресс формах. Затвердевшая модель вынимается из формы и покрывается несколькими слоями суспензии и обсыпки, образующими после высыхания керамическую скорлупу. Модель внутри скорлупы выплавляется, создавая оболочку формы с тонкими керамическими стенками.
В полученную форму заливается расплавленная смесь, которая после остывания образует изделие, точно повторяющее конфигурацию модели.
Детали, по выплавляемым моделям отличается высоким качеством и чистотой поверхности, не требуют дополнительной обработки.
Литье по газифицируемым моделям
Способ получения литых изделий с использованием моделей из материалов, которые превращаются в газ при контакте с расплавленным металлом. Больше всего подходит для этого вспененный полистирол.
Модели изготавливаются на модельных автоматах или путем заливки литейного полистирола мелких фракций под давлением в пресс-формы, с последующим спеканием под действием высоких температур.
Элементы моделей склеиваются или спаиваются в блоки, покрываются огнестойким покрытием путем облива или окунания и формируются на вибростоле в специальные опоки.
Расплавленный металл подается прямо на модельные блоки, выжигая и газифицируя полистирол.
Готовые отливки охлаждаются в формах, затем извлекаются и очищаются от антипригарного покрытия.
Технология литья по газифицируемым моделям позволяет выпускать изделия с гладкими точными формами.
Газы, образуемые при выжигании полистирола. удаляются при помощи вытяжных устройств.
Центробежное литье
Применяется для изготовления полых цилиндрических емкостей.
В основе технологии лежит принцип формирования отливок в поле центробежных сил.
Расплавленный металл из ковша(3) подается через заливочную воронку (2) во вращающийся цилиндр, внутренняя сторона которого (1) является формообразующей поверхностью.
Полученный пустотелый цилиндр после остывания и затвердевания металла извлекается из формы.
Рис. 4. Центробежное литье.
Литье в оболочковые формы
Технология применяется для изготовления особо точных деталей с повышенными требованиями к качеству.
Оболочковые формы изготавливаются из смоляно-песчаной смеси, термореактивных смол, кварцевого или цирконового песка на автоматических линиях.
Литье включает ряд последовательных операций:
Оболочковые формы применяются для изготовлени изделий из чугуна, стали, цветных металлов и алюминия.
Технология изготовления литьевых форм
Пресс формы для литья пластмасс изготавливаются на основании разработанного проекта.
- Из стального литья вырезается заготовка по параметрам будущего изделия.
- Форма обрабатывается на фрезерных станках, и шлифуется на шлифовальных машинах.
- Изделия проходят термообработку в специальных печах, хромируются и полируются.
- Готовые изделия тестируются и испытываются в лабораториях.
- Составляются линейные карты и подписываются двусторонние акты выполненных работ.
- Пресс-формы упаковываются и передаются заказику.
По желанию заказчика, специалисты компании «Имстек» выполнят установку и наладку оборудования, обучат технический персонал заказчика.
Определение стоимости изготовления литьевых форм
Стоимость пресс-форм определяется с учетом следующих показателей:
Дешевле стоят машины с боковыми или прямыми литниками и холодноканальные системы.
Усадка
При изготовлении литьевых пресс-форм необходимо учитывать возможную технологическую усадку формообразующих деталей в процессе охлаждения.Усадка может зависеть от следующих факторов:
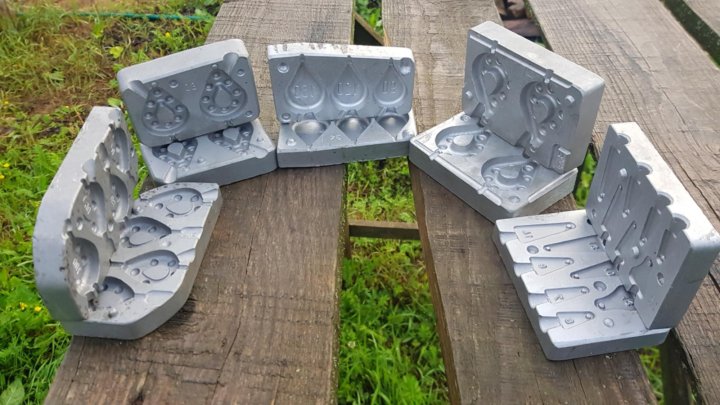
Снизить усадочные явления поможет добавление в сырье армирующих волокон.
Проектирование конструкции литьевой формы
Разработка проекта литьевых форм выполняется на основании технического задания заказчика.
Выполняются необходимые расчеты, создается 3D модель будующего изделия, выполняются рабочие чертежи.
От грамотного проекта и выбранной технологии изготовления зависит качество и долговечность пресс-форм.
Деформация форм
Деформации литьевых форм может произойти при нарушениях технологии литья:
Отступление от проектных параметров литья могут привести к деформациям и преждевременному износу форм.
Сдвиг пуансонов
Смещения и перекосы пуансонов относительно матрицы могут произойти из-за увеличенного зазора между деталями, повреждения кромок или неравномерных нагрузок на направляющие колонны.
Сдвиг происходит из-за неправильного крепления пуансона или большого усилия при выталкивании детали из пресс форм.
Извлечение отлитых изделий
Готовые изделия извлекаются из пресс-форм с помощью сжатого воздуха, выталкивающих стержней, вкладышей или плит.
При отсутствии устройств для автоматического извлечения отливок, готовые изделия удаляются вручную.
Обслуживание литьевых форм
Для надежной и долговечной работы пресс-форм требуется регулярный осмотр и техническое обслуживание.
При смене оснастки проводите очистку направляющих штифтов и гнезд от смолы, смазки и прочих загрязнений.
Чтобы избежать коррозии, важно защищать устройство от влажности и смазывать форму антикоррозийными средствами.
Проверяйте на легкость движения подвижные элементы пресс-форм. При необходимости, выполняйте своевременно настройку.
Способы устранения дефектов, возникающих в процессе литья под давлением
В процессе литья под давлением могут проявляться различные дефекты, которые можно устранить, зная причины их образования:
- Расслоения на поверхности изделий устраняются при повышении температуры расплава и понижении скорости впрыска.
- Облой может появится при использовании большого объема впрыска или недостаточном смыкании пресс-формы.
- Пустоты могут образовываться при недостаточном объеме впрыска или длительном и неравномерном охлаждении изделия.
- Коробление изделий бывает из за низкой текучести материала, недостаточной скорости впрыска или неравномерного охлаждения изделий в форме.
- Хрупкость и ломкость изделия возникает при малой толщине стенок изделий или низкой температуры форм при заливке.
Для профессионального обслуживания литьевых форм обратитесь в компанию «ИМСТЕК» выполняющую поставку, пусконаладку и техническое сопровождение литьевого оборудования.
Вахитов Ринат
Пресс-форма – что это такое? | Статья про пресс-формы
Пресс-форма — это сложный по конструкции технологический инструмент для производства изделий из пластмасс, которое задает конфигурацию изделия при литье под давлением.
Литьевая форма определяет параметры будущей отливки, от первичных: длина, ширина, высота, и до вторичных: шероховатость и фактура поверхности, плотность изделия (плотность напрямую связана с прочностью). Этот инструмент — главное звено в серийном и массовом производстве деталей из пластика и других материалов.
Этапы производства пресс-форм.
Изготовление проходит этапы – от проектирования до испытаний формы на работоспособность.
Дизайн изделия
Первый этап определяет необходимый объем работ. Перед проектированием формы конструктор должен понимать, как будет выглядеть отливка, для этого, предварительно, делают наброски готового изделия.
На основе этих эскизов проектируется 3D-модель отливки, количество изделий в литьевом механизме, производится расчет поперечного сечения литников, размеров формообразующих деталей (матрицы, пуансона, знаков), расчет усадки изделия.
На данном этапе появляется возможность выявить погрешности, устранив дефекты, неточности. Модель изделия проходит проверку по нескольким параметрам методом конечно-элементного анализа. Результаты анализов дают рекомендации, где лучше всего выбрать точку впрыска, определяет кривизну поверхности, равномерность толщины стенок, скругления, уклоны.
Проектирование пресс-формы
На втором этапе рождается 3D- модель непосредственно пресс-формы и конструкторская документация. Эта стадия определяет необходимый набор стандартных изделий, составных частей и компонентов литьевой оснастки. Все элементы составляющей должны быть точно подобраны друг к другу.
Этап изготовления пресс-формы
Значительная часть всех составляющих элементов литьевой оснастки проходит обработку на оборудовании с ЧПУ и электроэрозионных станках. Предполагается следующая технология обработки:
- Черновая механическая обработка, при которой снимается основное слой материала, назначаются припуски на рабочие поверхности от 0,5 до 1,5мм.
- Термическая обработка в вакуумной печи, которая предполагает закалку формообразующих деталей, создавая износостойкость рабочих поверхностей.
- Получистовая и чистовая обработка – значимая часть, на которой выполняются точная обработка рабочих поверхностей. Если в отливке преобладают тонкостенные ребра, поднутрения, острые, прямые углы, то пуансон с матрицей проходят обработку дополнительно на электроэрозионных станках.
- Финишная доводка и отделка рабочих поверхностей может включать в себя различные методы – от ручной полировки до электрохимической и лазерной обработки.
- При необходимости на формообразующие поверхности наносятся различные покрытия и выполняется поверхностное упрочнение.
Сборка и испытание.
Для подгонки и сборки пресс-форма переходит в руки слесаря-инструментальщика, так как для надежной работы механизма необходима тщательная пригонка всех его частей. Именно на этой стадии обнаруживаются недоработки, исправляются все ошибки.
Каждая пресс-форма индивидуальна, поэтому сборка – ответственный момент, который может затянуться, пока не будут выполнены все требования по геометрии формующих поверхностей и работы механизмов пресс-формы, согласно чертежу
Все этапы преследуют одну цель – получение литьевой оснастки заданного качества. Поэтому испытания проводятся в реальных условиях эксплуатации.
Если во время испытаний выявились недочеты, то группа инженеров мгновенно принимает решение о доработке, при необходимости – связывается с заказчиком.
Устройство пресс-формы.
Итак, подытожим, что литьевая оснастка – это конструкция для создания серийного количества однотипных изделий конкретной геометрии и стабильного качества. Из чего же она состоит?
Основными узлами являются:
Пакет плит (корпус пресс-формы)
В общем случае он состоит: верхние и нижние плиты крепления, брусья, обойма матрицы, обойма пуансона, плита толкателей, плита хвостовика. В зависимости от типа и сложности формы состав пакета может изменяться.
Формообразующие детали (ФОД)
Это детали, которые при закрытии пресс-формы образуют полость, в которую заливается пластмасса. К ФОД относятся, как правило, следующие детали:
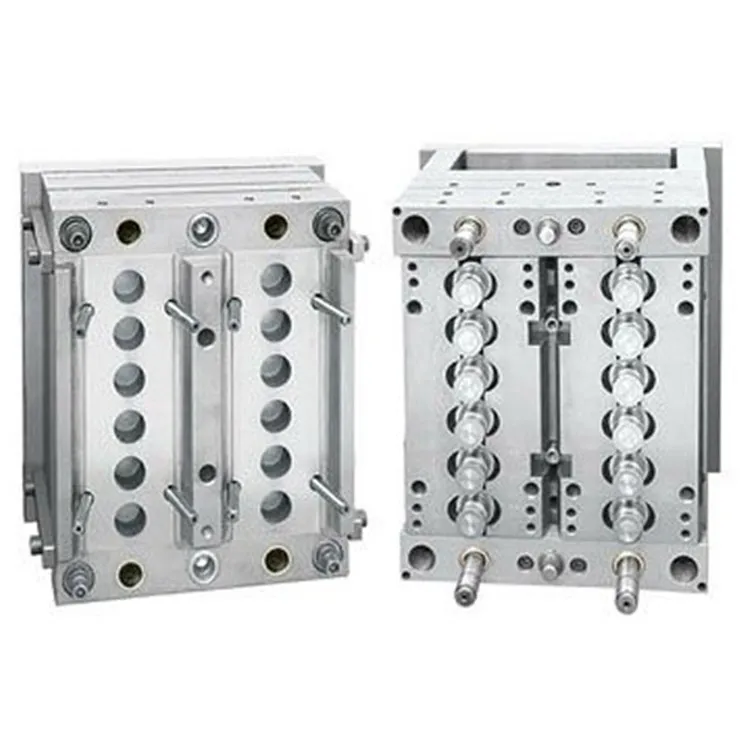
Следует упомянуть так называемые закладные знаки. Они применяются для опытных и малосерийных пресс-форм. Закладной знак представляет из себя элемент ФОД, который устанавливается в пресс-форму перед каждым циклом литья, извлекается из пресс-формы вместе с отливкой, извлекается из отливки и устанавливается обратно в пресс-форму.
Для выполнения внутренней резьбы применяются вращающиеся знаки, они могут иметь механический, гидравлический или электрический привод. Для выполнения резьбы в недорогих вариантах изготовления пресс-форм используются закладные резьбовые знаки, они выкручиваются из отливки оператором и устанавливаются в пресс-форму вручную. В таком случае изготавливается несколько комплектов закладных знаков. Этот вариант не подходит для воспроизводительной работы, т.к. ТПА работает только в режиме Полуавтомат.
Элементы ФОД могут быть как цельными деталями, так и сборными узлами. Конкретное исполнение ФОД зависит от геометрии отливки, технических требований к пресс-форме и технологических возможностей изготовителя.
Литниковая система.
Элемент пресс-формы, который обеспечивает попадание расплава из сопла термопластавтомата (ТПА) в формообразующую полость пресс-формы. Конструкций литниковых систем существует много, от простых холодноканальных с ручным откусыванием литника от детали до сложных горячеканальных систем с автоматическим управлением клапанами, которые сильно экономят материал и позволяют качественно замаскировать точку впрыска. Тип и конструкция литниковой системы оказывают существенное влияние на цену пресс-формы.
Система охлаждения.
Так как литьё под давлением предусматривает переход материала отливки из расплавленного состояния в твердое, предусмотрено охлаждение формообразующей полости. Львиная доля машинного времени цикла литья, как раз приходится именно на охлаждение детали. Отсюда следует, что система охлаждения является очень важным элементом пресс-формы. Система охлаждения представляет из себя совокупность каналов охлаждения в ФОД, которые объединяются в контуры, по которым циркулирует жидкий теплоноситель. От качества проектирования и работы системы охлаждения во многом зависит время цикла (читай цена отливки) и качество – эффективность охлаждения сильно влияет на коробление отливки при окончательном остывании, после извлечения из формы.
Также система охлаждения применяется для поддержания рабочей температуры ФОД при литье некоторых видов пластмасс. Например, при литье поликарбонатов, рекомендуемая температура ФОД – 55-75°C. Для этого система охлаждения подключается к термостату.
При проектировании пресс-форм работа системы охлаждения проходит проверку в процессе комплексного математического моделирования процесса литья под давлением.
Для подключения системы охлаждения используются стандартные БРС (быстро разъемные соединения) или любые другие, по желанию заказчика.
Литниковая система.
Элемент пресс-формы, который обеспечивает попадание расплава из сопла термопластавтомата (ТПА) в формообразующую полость пресс-формы. Конструкций литниковых систем существует много, от простых холодноканальных с ручным откусыванием литника от детали до сложных горячеканальных систем с автоматическим управлением клапанами, которые сильно экономят материал и позволяют качественно замаскировать точку впрыска. Тип и конструкция литниковой системы оказывают существенное влияние на цену пресс-формы.
Система выталкивания изделия.
Предназначена для извлечения отливки из пресс-формы, как правило, представляет из себя различное количество цилиндрических выталкивателей. Менее распространены системы с плитой съема, многоступенчатое выталкивание (когда выталкиватели движутся не синхронно), съем вывинчиванием (для резьбовых деталей), проворотом (для косозубых шестерен).
Менее распространены системы с плитой съема, многоступенчатое выталкивание (когда выталкиватели движутся не синхронно), съем вывинчиванием (для резьбовых деталей), проворотом (для косозубых шестерен).
Работа системы выталкивания обычно обеспечивается стандартным приводом ТПА, но возможны варианты с внешним приводом: гидравлика, пневматика, электропривод.
Особенностью проектирования системы выталкивания являются требования к циклу работы пресс-формы: деталь выпадает на транспортер или в накопитель, деталь снимается оператором или роботом.
Элементы управления.
Не совсем удачный термин включает в себя: направляющие колонки, направляющие втулки, лекальные колонки, запирающие клинья, центраторы, счетчики циклов и т.п. Как правило, покупаются как стандартные детали у производителя комплектующих для пресс-форм. Нашей компании доступны как отечественные, так и европейские производители, комплектующие из Азии и Северной Америки не используем – политика компании.
Классификация пресс-форм.
В данном разделе приведен классификатор сложности пресс-форм, который поможет вам сформировать первоначальное представление о пресс-форме, которую вы хотите получить.
Мы знаем, сто существует ГОСТ 27358-87, где есть классификатор сложности, но он, к сожалению, мало информативен для потребителя отливок.
По количеству смыканий:
Количество смыканий | Отличия | Плюсы | Минусы | Влияние на цену |
---|---|---|---|---|
До 10 000 | ФОД изготовлены из предзакаленного материала твердостью Корпус изготовлен из Ст.45 ГОСТ 1050 | Подходит для опытных партий нацеленных, на «прощупывание рынка» или для заранее известного количества необходимых отливок. | В случае увеличения потребности в отливках, как правило – заказ новой пресс-формы. Но возможны варианты, если при заказе была оговорена возможность замены ФОД на более стойкие. | Самый доступный вариант для отдельной пресс формы* |
До 150 000 | ФОД изготовлены из материала твердостью 36…42HRC (Nimax Uddeholm, Formadur 400, 1.2083, 40Х13 ГОСТ 5632) Корпус изготовлен из 1.1730, Ст.45 ГОСТ 1050 | Подходит для изготовления большинства товарных партий деталей, возможен капитальный ремонт с восстановлением ресурса.![]() | Не выявлено. | Самый распространенный заказ. |
Свыше 150 000 | ФОД изготовлены из материала, с термической обработкой твердостью >50HRC (1.2083, 40Х13 ГОСТ 5632), возможно, с покрытием и поверхностным упрочнением. Корпус изготовлен из 1.2085, 1.1730, 1.2311, 1.2714, 1.2738 | Подходит для массового деталей, возможен капитальный ремонт с восстановлением ресурса. | Высокая цена, увеличенное время изготовления, по сравнению с предыдущими вариантами, сложность последующих изменений (при необходимости заказчика внести изменения в дизайн отливки) | Самый дорогой вариант. |
* – возможно изготовление отдельно комплекта ФОД для применения в стандартизированном (в нашей компании) корпусе пресс формы (Блоке), это самый доступный вариант, но он имеет свои ограничения по возможным габаритам и геометрии отливки. Размещение заказа на литьё, соответственно, возможно только в нашей компании.
По литниковой системе:
Вид литниковой системы | Отличия | Плюсы | Минусы |
---|---|---|---|
Холодноканальная с впрыском в изделие.![]() | Литник представляет собой одно целое с отливкой. | Надежность | Литник остается на отливке, удаляется оператором или потребителем, т.е. необходима отдельная операция по удалению литника. Расход материала включает в себя, помимо объема отливки, объем литника. (Литник можно переработать впоследствии, но понадобится гранулятор или дробилка, и это возможно не на всех материалах.) |
Холодноканальная с самоотрывным литником. | Литник отделяется от отливки механизмом пресс-формы. | Возможность получения деталей без непосредственного участия оператора в их изготовлении – оператор занят только обслуживанием ТПА. Более стабильное качество деталей, т.к. отсутствует ручная операция, связанная с обработкой отливки. | Необходимость сортировки (ручной или автоматической) отливок и литников. Расход материала включает в себя, помимо объема отливки, объем литника. (Литник можно переработать впоследствии, но понадобится гранулятор или дробилка, и это возможно не на всех материалах) |
С обогреваемой литниковой втулкой.![]() | Хорошо комбинируется с предыдущими вариантами, с их плюсами и минусами. | Повышение качества литья – путь расплава в холодной части пресс-формы сокращается. Экономия материала, т.к. объем материала в литниковой втулке не уходит в отходы. | Усложняет эксплуатацию пресс-формы: появляется еще одна зона контроля температуры. |
Горячеканальная система с коллектором | Применяется для многоточечного впрыска в отливку (отливки) или для переноса точки впрыска в отдаленную по расстоянию/углу область детали. (Существуют детали, литье которых без такой системы невозможно. Например, крупногабаритные тонкостенные детали) | Полное исключение отходов при серийном производстве, гибкость наладки при изменении свойств материала (к сожалению, встречается в разных партиях одного и того же материала). Легкость полной автоматизации процесса литья. | Нуждается в высококвалифицированном персонале: наладчиках и технологах. |
Горячеканальная система с коллектором и запорными клапанами.![]() | Аналогично предыдущей. Применяется, когда надо замаскировать точки впрыска, или в особо сложных деталях, когда нужно управлять последовательность впрыска в различные зоны детали или гнезда пресс-формы. | Полное исключение отходов при серийном производстве, гибкость наладки при изменении свойств материала (к сожалению, встречается в разных партиях одного и того же материала). Легкость полной автоматизации процесса литья. Позволяет замаскировать точку впрыска даже на лицевой поверхности отливки. Позволяет более гибко управлять процессом литья сложных в производстве деталей. | Нуждается в высококвалифицированном персонале: наладчиках и технологах. Нуждается в качественном ТО, обученным персоналом. Нуждается в подводе сжатого воздуха или гидравлики к запорным клапанам. |
По гнездности (количеству мест в пресс-форме):
Гнездность | Отличия | Плюсы | Минусы |
---|---|---|---|
1 | Изготовление одной отливки за один цикл работы ТПА | Нет | Не всегда можно сделать одноместную пресс-форму: если объем минимальной дозы впрыска ТПА больше объема детали, это приведет к деструкции материала от длительного нагрева.![]() |
N – гнездная | За один цикл работы ТПА получается N отливок. (Напоминаем, что цена отливки, в общем случае, формируется из цены материала и цены одного цикла ТПА) | Снижение в N раз стоимости работы по изготовлению отливок. | На многогнездных формах часто применяется ГКС в разных видах, что оказывает соответствующие влияние на цену, но, как правило, возможны и различные холодноканальные варианты конструкции. |
N+M – гнездная (N и M от единицы) | За один цикл лить ТПА получаются детали двух и более видов. | Снижение в N раз стоимости работы по изготовлению отливок. Если отливки собираются в один узел, то этот вариант улучшит его собираемость. Т.К. режимы литья, и усадка материала (зависит от партии материала) одинаковы для всех деталей узла. | Не всегда возможно применение данного метода: детали должны иметь схожий объем, толщину стенок и ряд других параметров. Часто применяется ГКС в разных видах, что оказывает соответствующие влияние на цену, но, как правило, возможны и различные холодноканальные варианты конструкции.![]() |
По гнездности (количеству мест в пресс-форме):
Цикл работы | Отличия | Плюсы | Минусы | Влияние на цену |
---|---|---|---|---|
Ручное | Применяется для опытного производства и маленьких серий. Как правило, используется для пресс-форм с закладными знаками. | Нет | Низкая стабильность цикла, т.к. время цикла зависит от стабильности действий оператора. | Самое простое решение. |
Полуавтомат – человек | Применяется для литья с закладными деталями или необходимостью ручного извлечения детали, не допускающего её падения в накопитель. В этом случае система выталкивания, в конце цикла, обеспечивает положение отливки удобное для её съема оператором. | Удобство и простота эксплуатации. | Низкая стабильность цикла, т.к. время цикла зависит от стабильности действий оператора. | Не имеет. |
Полуавтомат -робот (роботизированный автомат) | Применяется для литья с закладными деталями или необходимостью аккуратного извлечения детали, не допускающего её падения в накопитель.![]() | Высокая стабильность работы комплекса с использованием робота манипулятора для ТПА, гарантированно высокое качество. | Обязательно наличие робота и обученного персонала по его наладке и обслуживанию. Необходим жесткий контроль выполнения всех регламентных работ по обслуживанию пресс-формы и соответствующий персонал. | Не значительно, если информация по использованию робота была своевременно внесена в ТЗ на пресс-форму. |
Автомат | Применяется для крупных партий деталей. Плюсы и минусы соответствуют выбранным гнездности и литниковой системе. | Самая высокая производительность и стабильность качества без особых требований к операторам. | Нуждается в качественном ТО, обученным персоналом. | Зависит от общей конфигурации: литниковая система, гнездность. |
Производительность и ресурс работы.

В чем же секрет ресурса литьевого инструмента? Чтобы спроектированный механизм работал с большим «выхлопом» необходимо пройти все этапы производства со строгим соблюдением правил. Но весомым фактором в этом играет материал, из которого сделаны формообразующие детали. ФОД изготавливают из высококачественной инструментальной стали. Наша компания, если нет особых требований заказчика, применяет коррозионностойкую (нержавеющую) сталь 40Х13 или её европейский аналог 1.2083 (1.2083ESR), с требуемой термообработкой. Данный вид материала исключителен тем, что после термической обработки его кристаллическая решетка формируется таким образом, что материал не подвергается коррозии и износу, тем самым увеличивая ресурс работы на сотни тысяч циклов. Применяя современные технологии, нынешние пресс-формы долговечны, изготовление придерживается строгому соблюдению тех. процесса и прохождению всех этапов «рождения» механизма для литья
Пресс-форма – цена изготовления
«Сколько будет стоить пресс-форма?» – частый вопрос при обращении к изготовителю. Обычно, вместо ответа клиент получает массу малопонятной информации, которая запутывает его.
Так от чего же всё-таки её зависит цена?
Основные параметры изделия, влияющие на цену это:
– Размер изделия – чем больше размер, тем больше и тяжелее форма и дороже ее обработка.
– Вид
– Ресурс
– Надежность конструкции
– Тип литниковой системы
– Тип системы толкателей
– Требования к поверхности отливки. Нанесение шагрени или полировки являются доп. операциями.
С учетом всех внешних параметров составляют итоговую цену, к которой относят 2 основных слагаемых.
1) Цена материалов
2) Стоимость работ.
Следующий вероятный вопрос «А, всё-таки, почему так дорого?» Приведу два сравнения: 1. Тепловые нагрузки аналогичны таковым на рабочих лопатках последних ступеней компрессора авиадвигателя. 2. Механический нагрузки и рабочие давления сопоставимы с нагрузками на узел затвора крупнокалиберной гаубицы типа «Мста».
Общие принципы расчета цены в РФ одинаковы, они не зависят от изготовителя. На пресс-форму, после ее испытания, составляется паспорт, предлагается гарантия на обслуживание и ремонт, связанный с восстановлением знаков, пуансонов, системы толкания.
Качество литьевой оснастки влияет на ее срок службы, а её цена влияет на качество. Не стоит смущаться большой цены за маленькую форму. Ресурс качественного, рабочего механизма измеряется сотнями тысяч литьевых циклов. Такие пресс-формы окупают себя при производстве изделий. Готовая продукция получается с меньшим количеством брака и согласно чертежу.
Автор статьи:
Дмитрий Владимирович Щербина
Технический директор ООО «МПИ»
Список используемой литературы для подготовки статьи:
- Как делать литьевые формы? (Георг Мендес, 2007 год)
- Конструирование литьевых форм в 130 примерах (Гастров, 2006)
- ГОСТ 27358-87 ПРЕСС-ФОРМЫ ДЛЯ ИЗГОТОВЛЕНИЯ ИЗДЕЛИЙ ИЗ ПЛАСТМАСС. ОБЩИЕ ТЕХНИЧЕСКИЕ УСЛОВИЯ
Больше информации и цены на услуги
в области переработки пластмасс можно получить здесь:
Узнать подробнее
Изготовление пресс-форм
Узнать подробнее
Ремонт пресс-форм
Узнать подробнее
Литье пластмасс
Узнать подробнее
Проектирование изделий
1.
2. Машина для литья под давлением
3. Форма
4. Молдинг
5. Использование переработанных материалов
6.
|
Руководство для начинающих по литью под давлением
Спинка
Материалы
Материалы по обслуживанию
Материалы для инъекции.
Мы создали подробное руководство по заменителям смолы для АБС, поликарбоната, полипропилена и других формованных термопластов.
Скачать
Ресурсы
Советы по дизайну Руководства и отчеты о тенденциях Истории успеха Вспомогательные средства дизайна Вебинары и выставки
Блог Видео Часто задаваемые вопросы Преподаватели и студенты Глоссарий
Отрасли Медицинский Аэрокосмическая промышленность Автомобильный Бытовая электроника Промышленное оборудование
О нас
Кто мы Почему Протолабс? Исследования и разработки Награда за крутую идею Партнерские отношения Устойчивое развитие и социальное воздействие
Карьера Инвесторы Места Нажимать Procurement
Contact Us
Proto Labs, Inc.
5540 Pioneer Creek Dr.
Maple Plain, MN 55359
United StatesP: 877.479.3680
F: 763.479.2679
E: [email protected]Лучшее в своем классе онлайн-предложение
После загрузки проекта детали вы получите онлайн-предложение, включающее производственный анализ, который поможет улучшить технологичность детали. В своем предложении вы также можете настроить количество и материал и увидеть изменения цен в режиме реального времени.
Узнать больше
Получить предложениеВойти
Изучите основы процесса литья под давлением, в том числе: как он работает, принципы проектирования, материалы и системы качества
Перейти к разделу
→ Как работает литье под давлением?
→ Принципы проектирования
→ Материалы
→ Отделка поверхности
→ Передовые технологии
→ Контроль качества
Что такое литье под давлением?
Литье под давлением предназначено для производства больших объемов деталей. По сравнению с другими производственными технологиями, такими как обработка на станках с ЧПУ и 3D-печать, она требует предварительных капитальных вложений в инструменты. Но цена поштучной детали будет существенно меньше по сравнению с другими способами изготовления пластиковых деталей. Такая структура затрат делает его доступным решением для производственных циклов.
Чаще всего используется для изготовления пластиковых деталей в больших масштабах из-за малого количества отходов материала и низкой себестоимости детали. Это идеальный производственный процесс для таких отраслей, как медицинские устройства, потребительские товары и автомобилестроение.
Как работает литье под давлением?
Изготовление оснастки: После окончательной разработки конструкции для литья под давлением первым этапом производственного процесса является фрезерование оснастки, которая обычно изготавливается из стали или алюминия. В большинстве случаев металлический блок материала помещают на фрезерный станок с ЧПУ, который затем вырезает негатив из окончательной пластиковой детали. Затем к инструменту можно применить дополнительные обработки, такие как полировка или лазерное травление, для достижения определенной чистоты поверхности.
Производство деталей: Фактическое производство пластиковых деталей начинается с загрузки гранул смолы в бочку. Температура ствола повышается до тех пор, пока гранулы смолы не достигнут расплавленного состояния, а затем сжимаются. Затем расплавленный пластик впрыскивается в металлический инструмент через систему желобов, которые затем подаются в полость пресс-формы через заслонки. Затем деталь остывает, затвердевает и выталкивается из инструмента с помощью выталкивающих штифтов.
Типы литья под давлением
Термин литье под давлением охватывает несколько процессов, при которых жидкая смола впрыскивается в инструмент для формирования пластиковых деталей. Вот четыре распространенных типа:
Литье термопластов под давлением: Литье термопластов под давлением является наиболее распространенным типом литья. Он впрыскивает термопластичную смолу в форму, где материал охлаждается для формирования конечной детали.
Литье из жидкого силиконового каучука: В жидком силиконовом каучуке используются термореактивные материалы, а пластмассовая деталь создается в результате химической реакции.
Многослойное формование: Многослойное формование — это процесс, используемый для изготовления пластиковых деталей из двух или более материалов. Вы часто найдете это на деталях, чтобы улучшить сцепление, добавив резину к рукоятке.
Литье с вкладышем: Литье с вкладышем — это процесс, который начинается с помещения в форму вставного компонента до того, как в него поступит смола. Затем материал впрыскивается и обтекает вставку, обычно металлическую, для формирования конечной детали. Это часто используется для деталей, которые требуют металлической резьбы.
Основные принципы проектирования для литья под давлением
Допуски
Благодаря нашему процессу литья под давлением мы можем поддерживать точность обработки около ±0,003 дюйма . Допуск на усадку зависит главным образом от конструкции детали и выбора смолы. Она варьируется от 0,002 дюйма/дюйм. для стабильных полимеров, таких как ABS и поликарбонат, по 0,025 дюйма/дюйм. для нестабильных смол, таких как TPE.
Толщина стенки
Толщина стенки важна, поскольку она может привести к таким дефектам, как впадина и коробление. Лучше всего поддерживать одинаковую толщину по всей детали, отлитой под давлением. Мы рекомендуем стены быть не менее чем от 40 до 60 процентов толщины смежной стенки , и все они должны соответствовать рекомендуемым диапазонам толщины для выбранного полимера.
Геометрия сердцевины
Вырежьте сердцевину деталей для устранения толстых стенок. Вы получаете ту же функциональность в хорошей формованной детали. Ненужная толщина может изменить размеры детали, снизить прочность и потребовать последующей обработки.
Вытяжка
Применение вытяжки к формованным деталям имеет решающее значение для обеспечения того, чтобы детали не деформировались в процессе охлаждения, и помогает легко извлечь деталь из формы. Применение От 1 до 2 градусов хорошо работает в большинстве сценариев . Если есть вертикальные грани, мы советуем включить 0,5 градуса осадки.
Наша онлайн-платформа котировок выделяет объекты, которые слишком толстые, выделяя их темно-синим цветом, как показано выше.
Наша платформа котировок идентифицирует функции подрезания, требующие боковых действий, с помощью сплошных стрелок и граней соответствующего цвета.
Боковые элементы
Часть пресс-формы, которая вдвигается на место при закрытии пресс-формы с помощью кулачковой направляющей. Как правило, побочные действия используются для устранения подрезки или иногда для обеспечения отсутствия уклона внешней стены. Когда форма открывается, боковое действие оттягивается от детали, позволяя вытолкнуть деталь. Также называется «камера».
Поднутрения
Часть детали, затеняющая другую часть детали, создавая сцепление между деталью и одной или обеими половинами пресс-формы. Примером может служить отверстие, перпендикулярное направлению открытия пресс-формы, просверленное в боковой части детали. Поднутрение предотвращает выталкивание детали или открытие пресс-формы, или и то, и другое.
Бобышки
Приподнятая шпилька, которая используется для зацепления крепежных элементов или поддержки элементов других деталей, проходящих через них. Может возникнуть тенденция к проектированию толстых бобышек, что увеличит вероятность образования раковин и пустот в детали. Рассмотрите возможность усиления бобышек ребрами жесткости или косынками для дополнительной прочности
Вентили
Вентили — это отверстие в инструменте для литья под давлением, которое позволяет смоле входить и заполнять полость. Существует три распространенных типа ворот для литья под давлением.
- Шиберы с выступами являются наиболее распространенным типом литников, поскольку они хорошо работают с добавками и являются наиболее экономичным вариантом.
- Шибер Hot Tip лучше всего подходит для деталей, внешний вид которых является приоритетом.
Эти литники также могут снизить износ оснастки и заусенцев.
- Штифтовые, опорные или туннельные ворота идеально подходят для косметических деталей, не требующих остатков. Иногда не вариант в зависимости от материала и геометрии.
Ребра
Ребро — это тонкий стенообразный элемент, параллельный направлению открытия пресс-формы. Он используется для придания прочности и поддержки таким элементам, как бобышки и стенки. Для предотвращения усадки ребра должны составлять не более 60% толщины стенки .
Выталкивающие штифты
Выталкивающие штифты устанавливаются на стороне B пресс-формы и помогают высвободить пластиковую деталь из инструмента после того, как деталь достаточно остынет. Проектирование с достаточным уклоном может помочь уменьшить потребность в выталкивающих штифтах на детали.
Логотипы и текст
Шрифты без засечек будет проще всего превратить в форму с текстом. Мы рекомендуем шрифт больше 20 pt. и не глубже, чем от 0,010 до 0,015 дюйма.
В 3D-рендеринге вашего производственного анализа вы также можете увидеть, где будут расположены выталкивающие штифты и затворы.
Смолы для литья под давлением
При выборе материала для вашей детали важными свойствами могут быть механическая, физическая, химическая стойкость, термостойкость, электрическая стойкость, воспламеняемость или устойчивость к ультрафиолетовому излучению. Производители смол, составители компаундов и независимые поисковые системы смол имеют данные в Интернете. Вот краткий обзор некоторых распространенных товарных и инженерных смол.
Обычные инженерные смолы
АБС: АБС — отличный выбор для подавляющего большинства деталей. Он недорогой, прочный, относительно прочный, имеет приличный внешний вид и прощает ошибки, даже если вы не соблюдаете все стандартные правила проектирования пластиковых деталей.
Ацеталь: Прочный материал с хорошей смазывающей способностью
LCP: Очень прочный материал с хорошей текучестью, особенно для тонких деталей. Производит слабые трикотажные линии.
Нейлон: Доступная стоимость, прочность и износостойкость. Может подвергаться усадке и деформации, особенно стеклонаполненный нейлон.
Поликарбонат (ПК): Может выдерживать более высокие температуры и более долговечен, чем типичный АБС, но менее щадящий, когда речь идет о формуемости.
ПММА (акрил): Доступный вариант для прозрачных деталей, хотя он может быть хрупким.
Термопластический материал поставляется в виде гранул, которые нагревают до расплавленного состояния для введения в инструмент.
Товарные смолы
Полипропилен (ПП): ПП — дешевый материал, который хорош, когда внешний вид и жесткость не являются приоритетом. Химически стойкий и подходит для живых конструкций петель.
Полиэтилен: Варианты высокой и низкой плотности. Прочный и химически стойкий.
Полистирол: Твердый термопласт, дешевый и прозрачный.
Ознакомьтесь с нашим руководством по материалам для литья под давлением, если вы хотите глубже изучить выбор пластика.
Красители и добавки к смолам для литья под давлением
Стандартные цвета от поставщика смолы, как правило, черные и натуральные. Натуральный может быть белого, бежевого, янтарного или другого цвета. Полунестандартные цвета создаются при добавлении гранул красителя к натуральным смолам. Чтобы узнать о доступных цветах, посетите нашу страницу материалов. Дополнительная плата за цвета в нашем ассортименте не взимается. Они могут не совпадать точно и могут создавать полосы или завихрения в отдельных частях.
Добавки к смоле
Короткие стекловолокна используются для усиления композита и уменьшения ползучести, особенно при более высоких температурах. Они делают смолу более прочной, жесткой и хрупкой. Они могут вызвать деформацию из-за разницы в усадке при охлаждении между смолой и волокнами.
Углеродное волокно используется для усиления и/или придания жесткости композиту, а также для рассеивания статического электричества. У него те же ограничения, что и у стекловолокна. Углеродное волокно может сделать пластик очень жестким.
Минералы , такие как тальк и глина, часто используются в качестве наполнителей для снижения стоимости или увеличения твердости готовых деталей. Поскольку при охлаждении они не дают такой усадки, как смолы, они могут уменьшить деформацию .
ПТФЭ (тефлон) и дисульфид молибдена используются для обеспечения самосмазывающихся деталей подшипников.
Длинные стеклянные волокна используются так же, как и короткие стеклянные волокна, для усиления и уменьшения ползучести, но делают смолу намного прочнее и жестче. Недостатком является то, что они могут быть особенно сложными для формования деталей с тонкими стенками и/или длинными потоками смолы.
Арамидные (кевларовые) волокна похожи на менее абразивные стеклянные волокна, только менее прочные.
Стеклянные шарики и чешуйки слюды используются для придания жесткости композиту и уменьшения коробления и усадки. При высокой нагрузке их введение может быть затруднено.
Волокна из нержавеющей стали используются для контроля EMI (электромагнитных помех) и RFI (радиочастотных помех), как правило, в корпусах электронных компонентов. Они обладают большей проводимостью, чем углеродное волокно.
УФ-ингибитор для наружного применения.
Статическая обработка позволяет смолам рассеивать статическое электричество.
Поверхностная обработка литых деталей
Поверхностная обработка является еще одним важным фактором при литье под давлением, поскольку детали, как правило, косметические и предназначены для конечного использования. Имейте в виду, что текстурированная поверхность потребует больше черновика, чем более полированная отделка. Это необходимо для обеспечения выхода детали из формы и для того, чтобы дробеструйная обработка могла быть правильно применена к инструменту.
Это наши варианты отделки поверхности для литья термопластика и силиконового каучука
Термопласт | Жидкая силиконовая резина |
|
|
В дополнение к нашим стандартным вариантам отделки поверхности мы также предлагаем стандартные отделки Mold Tech для более сложных текстур. Их можно использовать для улучшения захвата ручки детали или скрытия косметических дефектов, таких как линии разъема. Текстуры Mold Tech можно использовать для достижения следующих эффектов:
- отделка, полученная дробеструйной обработкой или полировкой поверхности формы
- зернистость под дерево или кожу
- галечные поверхности
- матовая, глянцевая или матовая отделка и многие другие
Постобработка и передовые методы литья
Ультразвуковая сварка: использует высокочастотную вибрацию для выработки тепла и введения вставки в деталь. В более сложных процессах литья его также можно использовать для сплавления деталей .
Маркировка детали: Существует два способа нанесения изображений, часто логотипов, на детали: тампопечать и лазерная гравировка.
Тампопечать позволяет добавлять цветную графику к формованным деталям в масштабе. Это можно использовать для добавления логотипов, графики и инструкций на детали. Мы предлагаем тампопечать на АБС, ПК и смолах АБС/ПК.
Лазерная гравировка использует лазер для выжигания 2D-изображения на детали или полости пресс-формы. Хотя цвет не подходит для лазерной гравировки, это более экономичный и быстрый способ маркировки пластиковых деталей по сравнению с тампопечатью.
Пикауты: Пикауты — это вставки, которые обрабатываются отдельно от оснастки и помещаются в форму перед впрыском материала. Они используются для получения подрезов на внутренних поверхностях. Пикауты выталкиваются вместе с пластиковой частью и помещаются обратно в пресс-форму. Использование пикаута преодолевает многие ограничения по форме и расположению, но обходится дороже, чем скользящие затворы или использование бокового действия.
Штифты со стальным сердечником: Стальной штифт достаточно прочен, чтобы выдерживать усилие выталкивания, а его поверхность достаточно гладкая, чтобы его можно было аккуратно высвободить из детали без сквозняка. На получившейся детали не должно быть никакого косметического эффекта; если есть, то он будет внутри дыры, где его не будет видно.
Системы контроля качества литья под давлением
Поскольку компании используют литье под давлением для производства тысяч, а иногда и миллионов деталей, контроль качества имеет решающее значение.
Scientific Molding: Scientific Molding описывает стандартный процесс, используемый для разработки, оптимизации и документирования идеального процесса настройки для каждого проекта литья под давлением, чтобы один и тот же процесс и параметры выполнялись для каждого отдельного запуска. Это обеспечивает согласованность деталей для каждой партии деталей.
Проверка первого изделия (FAI): FAI — это метод, используемый для проверки соответствия деталей спецификации. Мы придерживаемся критического подхода к качеству литья под давлением FAI. Используя GD&T, клиенты могут назвать наиболее важные размеры своей детали.
Процесс утверждения производственных деталей (PPAP): PPAP — это процесс проверки качества, обычно используемый в автомобильной промышленности. Этот метод используется для проверки того, что производственный процесс может надежно производить качественную деталь многократно. Проверка PPAP состоит из 18 компонентов, которые варьируются от утверждения клиентом до производства образцов деталей.
ISO 13485: ISO 13485 является стандартом для медицинской промышленности. Сюда входят проектная квалификация (DQ), эксплуатационная квалификация (OQ) и эксплуатационная квалификация (PQ).
Связанные ресурсы
Совет по проектированию
Рекомендации по углу уклона для литья под давлением
Заблаговременно и часто применяйте правильный уклон к деталям, изготовленным методом литья под давлением, чтобы сэкономить время и деньги производства
Прочтите Совет по проектированию
Руководство по выбору термопластичных материалов Литье под давлением
Из этого технического обзора термопластичных смол вы узнаете, как выбрать правильный материал для вашей конструкции литья под давлением.