Формы из гипса для литья: Гипсовые формы для литья
alexxlab | 10.02.2023 | 0 | Разное
Гипсовая смесь для изготовления форм точного литья
Изобретение относится к литейному производству. Гипсовая смесь содержит, мас.%: гипс 30-35, воду 25-30, огнеупорный наполнитель – остальное. В качестве огнеупорного наполнителя используют золу уноса ТЭЦ, содержащую 60-75% SiO2, 12-15% С, 8-10% Al2O3, 3-5% CaO, 2-3% Fe2O3 и 1% MgO. Фазовый состав – 70% частиц размером 0,315 мм, 20% – 0,18 мм и 10% менее 0,18 мм. Повышается термостойкость и огнеупорность гипсовых литейных форм. 1 з.п. ф-лы, 1 табл.
Изобретение относится к области литейного производства, а именно к гипсовым формовочным смесям.
Известны составы гипсовых формовочных смесей, содержащие в качестве огнеупорного наполнителя кварцевый песок (О.Е.Кестнер, В.К.Бараданьянц и др., «Точное литье цветных сплавов в гипсовые и керамические формы», М.: – Машиностроение, 1968).
Недостатком известных изобретений является высокая стоимость огнеупорного наполнителя, низкая термостойкость и огнеупорность литейных форм.
Заявляемое изобретение позволяет снизить стоимость формовочной смеси, повысить термическую стойкость и огнеупорность форм. Сущность заявляемого изобретения заключается в том, что гипсовая смесь для изготовления форм точного литья, содержащая гипс, воду и огнеупорный наполнитель, в качестве огнеупорного наполнителя содержит золу уноса ТЭЦ. При этом в качестве огнеупорного наполнителя использована зола уноса ТЭЦ, содержащая: 60-75% SiO2, 12-15% С, 8-10% Al2O3, 3-5% CaO, 2-3% Fe2O3 и 1% MgO, а фазовый состав смеси следующий: 70% частиц размером 0,315 мм, 20% – 0,18 и 10% менее 0,18 мм.
Технический результат, получаемый при реализации изобретения, заключается в повышении термостойкости и огнеупорности гипсовых литейных форм.
Использование золы в качестве огнеупорного наполнителя позволяет повысить огнеупорность и трещиностойкость форм благодаря содержащемуся в золе обожженному кварцу с малым коэффициентом термического расширения, а также снизить стоимость литейных форм.
Предлагаемую гипсовую смесь используют при следующем количественном соотношении ингредиентов, мас.%:
гипс | 30-35 |
вода | 25-30 |
огнеупорный наполнитель | остальное. |
Исследование термической стойкости образцов литейных форм проводили согласно ГОСТ 7875.0-94 и ГОСТ 7875.2-94, определяя количество циклов теплосмен. В таблице приведены экспериментальные данные, характеризующие свойства форм, полученных из разных составов формовочных смесей.
Таблица | |||||
Наименование компонента | Исходный состав | Предложенный состав | |||
1 | 2 | 3 | 4 | ||
Вода, мас.% | 30 | 25 | 27 | 29 | 30 |
Гипс, мас.% | 70 | 30 | 32 | 33 | 35 |
Огнеупорный наполнитель, мас.% | – | остальное | остальное | остальное | остальное |
Свойства литейных форм, полученных из смесей с разным составом компонентов.![]() | |||||
Термостойкость 950-20°С, цикл | 0 | 2 | 1 | 1 | 1 |
Как видно из представленных данных, изготовленные из предложенных составов смесей образцы, содержащие золу уноса ТЭЦ, выдерживают 1-2 теплосмены, что позволяет изготавливать качественные отливки. Образцы литейных форм, изготовленные из исходной смеси, без золы, разрушились при первой теплосмене. Гипсовую формовочную смесь готовят следующим образом.
Сухие компоненты смеси в заданной пропорции (например, 30% гипса и 40% наполнителя от массы смеси) тщательно перемешивают и порциями засыпают в воду (например, взятую в количестве 30% от массы) при постоянном перемешивании. В качестве огнеупорного наполнителя использована зола уноса ТЭЦ, содержащая: 60-75% SiO2, 12-15% С, 8-10% Al2O3, 3-5% CaO, 2-3% Fe2O3 и 1% MgO, а фазовый состав смеси следующий: 70% частиц размером 0,315 мм, 20% – 0,18 и 10% менее 0,18 мм.
1. Гипсовая смесь для изготовления форм точного литья, содержащая гипс, воду и огнеупорный наполнитель, отличающаяся тем, что в качестве огнеупорного наполнителя она содержит золу уноса ТЭЦ при следующем соотношении ингредиентов, мас.%:
гипс | 30-35 |
вода | 25-30 |
огнеупорный наполнитель | остальное |
2. Смесь по п.1, отличающаяся тем, что в качестве огнеупорного наполнителя использована зола уноса ТЭЦ, содержащая 60-75% SiO2, 12-15% С, 8-10% Al2O3, 3-5% СаО, 2-3% Fe2O3 и 1% MgO, а фазовый состав смеси следующий: 70% частиц размером 0,315 мм, 20% – 0,18 мм и 10% менее 0,18 мм.
Похожие патенты:
Суспензия для изготовления форм точного литья методом электрофореза // 2481917
Изобретение относится к области литейного производства. .
Приводное устройство для приведения в движение закрывающей плиты в машине для вертикального литья в формы и машина, содержащая вышеуказанное устройство // 2481173
Изобретение относится к литейному производству.
Суспензия для изготовления форм точного литья методом электрофореза // 2481172
Изобретение относится к области литейного производства, а именно к форетическим суспензиям, используемым для изготовления керамических форм по удаляемым моделям методом электрофореза.
Клеевая композиция на основе фенольной смолы // 2480308
Изобретение относится к клеевой композиции на основе фенольной смолы и ее использованию для форм и стержней форм. .
Способ изготовления форм по выплавляемым моделям (варианты) // 2478453
Изобретение относится к области литейного производства. .
Смесь для изготовления литейных форм // 2478018
Изобретение относится к литейному производству, а именно к составам песчано-глинистых смесей, применяемых для изготовления разовых сырых форм. .
Облицовочная плита для облицовки формовочных камер формовочных машин // 2477192
Изобретение относится к литейному производству. .
Облицовочная плита для облицовки формовочных камер формовочных машин // 2477192
Изобретение относится к литейному производству. .
Способ изготовления литейных форм и устройство для его осуществления // 2472600
Изобретение относится к литейному производству. .
Смесь для изготовления литейных форм и стержней // 2472598
Изобретение относится к литейному производству, а именно к составам смесей с жидкостекольным связующим, отверждаемых тепловой сушкой. .
Способ изготовления комбинированных литейных форм из жидкостекольных самотвердеющих смесей // 2486987
Изобретение относится к литейному производству
Суспензия для изготовления форм точного литья методом электрофореза // 2488458
Изобретение относится к области литейного производства
Способ получения активированного бентонита // 2489388
Изобретение относится к способу получения активированного бентонита
Смесь для изготовления литейных форм и стержней // 2495731
Изобретение относится к литейному производству. Смесь содержит шламовый отход производства поливинилхлорида в количестве 97-99 мас. %, содержащий, мас.%: Н2О 50,2; CaSO4·2h3O 12,2; Са(ОН)2 7,2; NaCl 28,2; NaSO4 2,0; NaOH 0,2 и древесные опилки. Связующим в смеси являются кристаллогидраты солей NaCl. Смесь имеет высокие прочностные свойства и легко удаляется из отливок путем растворения связующего в воде. 1 з.п. ф-лы, 2 табл., 1 пр.
Способ изготовления средства замены бурового долота или сопла // 2498877
Изобретение относится к порошковой металлургии, в частности к получению керамической вставки для формирования в процессе литья в корпусе бурового инструмента полости для установки сменной детали. Керамические частицы измельчают до диаметра меньше чем 150 мкм, а частицы смолы – до диаметра меньше чем 100 мкм. Из измельченных керамических частиц и частиц смолы готовят порошковую смесь, вводят ее в литейную форму, имеющую полость, образующую требуемую сменную деталь, например буровое долото или сопло. Затем осуществляют уплотнение смеси и отверждение смолы. Вставка может содержать армирующие волокна или графитовый сердечник и керамическую оболочку.
Способ приготовления бескремнеземного связующего для литья по выплавляемым моделям химически активных сплавов // 2499650
Изобретение относится к области литейного производства. Водный раствор алюмоборфосфатного концентрата подвергают электродиализу при силе тока 0,2…1,5 А, затем смешивают с водным раствором поливинилового спирта в объемном соотношении (2…4):1. Обеспечивается повышение физико-механических свойств керамических форм на бескремнеземном связующем. 2 табл., 2 пр.
Стержневая смесь со связующим на основе сульфата магния // 2500499
Изобретение относится к литейному производству. Смесь содержит, мас.%: кварцевый песок 85,5-87,5; MgSO4·7h3O 4,0-4,5; маршаллит 3,0-3,5 и воду 5,5-6,5. Обеспечивается увеличение прочности смеси. 2 табл.
Суспензия огнеупорная для оболочковых форм по выплавляемым моделям // 2503520
Изобретение относится к литейному производству. Суспензия включает этилсиликат, спиртовой раствор нитрата алюминия девятиводного, микропорошки электрокорунда, алюминиевый порошок и оксид иттрия при следующем соотношении компонентов, мас.%: этилсиликат 5,0-8,0; спирт этиловый 14,0-17,0; нитрат алюминия девятиводный 1,3-2,0; кислота соляная или азотная 0,06-0,1; поливинилбутираль 0,03-0,09; алюминиевый порошок 3,0-6,0; оксид иттрия 4,0-8,0; микропорошки электрокорунда – остальное. Обеспечивается уменьшение степени взаимодействия керамической формы с металлом отливок. 2 табл.
Дисперсия, суспензия и способ получения формы для точного литья с использованием суспензии // 2504452
Суспензия для получения литейной формы содержит от 50 до 80 мас. % термостойких частиц, средний размер которых составляет от 0,5 до 150 мкм, от 5 до 35 мас.% частиц оксида алюминия, средний диаметр которых составляет менее 300 нм, и от 5 до 35 мас.% воды, pH указанной суспензии составляет от 5 до 12. Суспензию получают путем смешивания водной дисперсии, содержащей частицы оксида алюминия, с термостойкими частицами, средний размер которых составляет от 0,5 до 150 мкм, и, если это необходимо, с добавками. Средний диаметр частиц оксида алюминия в дисперсии составляет менее чем 300 нм в твердом виде, содержание частиц оксида алюминия составляет более чем 15 мас.%, а pH составляет от 5 до 12. С использованием суспензии получают литейную форму для точного литья. Обеспечивается повышение устойчивости суспензии, сокращение времени сушки формы, повышение прочности формы и упрощение ее изготовления. 5 н. и 10 з.п. ф-лы, 4 табл., 5 пр.
Устройство формовочной камеры для конвейерной формовочной установки // 2510813
Изобретение относится к литейному производству. Формовочная камера содержит основание 3, верхнюю часть 4, две боковые стенки 5, прижимную плиту 6 и поворотную плиту 10. Верхняя часть 4 снабжена одним или более отверстиями 22 для заполнения песка, сообщающимися с системой 14 подачи песка. Прижимная плита 6 снабжена сменной прижимной модельной плитой, имеющей прижимную модель 8, и присоединена к механизму 9 перемещения. Поворотная плита 10 снабжена сменной поворотной модельной плитой, имеющей поворотную модель 12, и установлена с возможностью поступательного и поворотного перемещения, для обеспечения выталкивания образуемых форм прижимной плитой 6. Для обеспечения регулирования гибкости размера образуемых форм, особенно высот образуемых форм, без изменения геометрии системы подачи песка формовочная камера снабжена средством 13 синхронного вертикального перемещения верхней части 4 и системы 14 подачи песка, или основания 3, или и того и другого относительно остальной формовочной камеры. 2 н. и 25 з.п. ф-лы, 12 ил.
Литье в гипсовые формы.
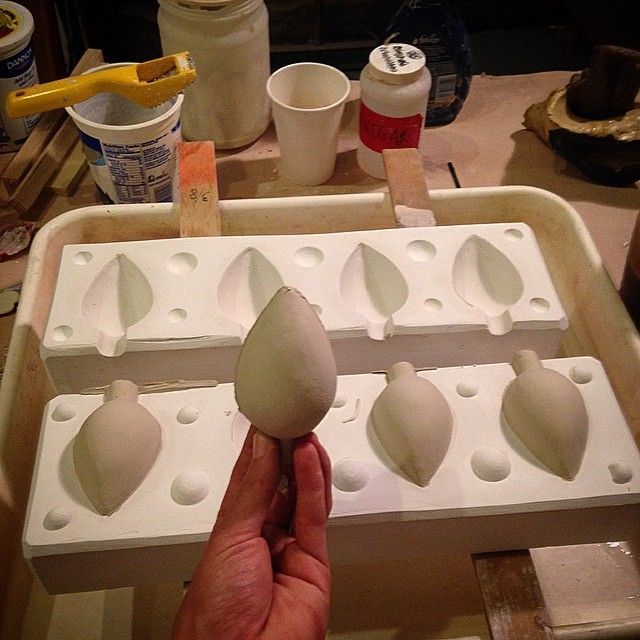
Гипс полугидрат CaSO4в смеси с полуангидридом веществаγCaSO4используется для отливок из цветных
сплавов, а так же для изготовления
моделей и модельных плит, для небольших
отливок изготавливают смесь из 20% гипса,
80% асбеста + воды. Механизм образования
прочности – гидратация (чем больше
асбеста, тем меньше берут воды). Для
тонкостенных отливок с тонким рельефом
и чистой поверхностью рекомендуют
вместо асбеста мелкозернистый порошок
кварца, такая смесь более прочная, чем
цементная и имеет низкую газопроницаемость,
поэтому ее проплавляют в автоклавах
при давлении 2 МПА в течение 8 часов,
после чего сушат 10-20 часов. Для повышения
гипсовых смесей в них можно вводить ПАВ
– это позволит, при вспенивании гипсового
шликера, повышение количества газовых
пузырьков, что при исследуемом
затвердевании смеси способствует
газопроницаемости.
Такая гипсовая форма
обладает микропористостью и высокой
газопроницаемостью, что позволяет
получать в ней отливки из сплавов,
выделяющих
при затвердевании повышенное
количество газов.
Химические процессы при твердении гипсовых смесей
Твердение системы гипс — вода
После перемешивания гипсовой смеси (ее основой являются безводный сульфат кальция, полуводный гипс и полуангидрид) с водой образуется твердый гидратированный сульфат кальция в соответствии с уравнением
2 (CaSO4) • Н2О + ЗН2О = 2 (CaSO4 • 2Н2О). (14)
Время твердения гипса зависит от марки гипса, количества воды, от температуры воды, от дисперсности гипса. При малом содержании воды смесь плохо заливается, быстро твердеет, выделяет повышенное количество тепла, с одновременным увеличением количества объема. Время твердения гипса с повышением температуры воды увеличивается, поэтому следует использовать холодную воду.
Технологические свойства гипсовых смесей
При
достаточном
количестве воды гипсовая
смесь кашеобразна, достаточно текуча,
медленно твердеет и не имеет склонности
к увеличению объема. После твердения
смеси и нагрева формы перед заливкой
возникает усадка, которая может вызвать
растрескивание гипсовых форм. Чем больше
воды содержит полуводный гипс,
тем больше его усадка при нагревании.
Для снижения усадки в гипсовую смесь вводят повышенное количество пылевидного кварца, минимальное количество гипса и добавки, вызывающие расширение гипса.
Прочность высушенных гипсовых смесей увеличивается при снижении содержания воды и пылевидного кварца. Смеси гипса с кварцевым заполнителем относительно малоупруги, поэтому формы, изготовленные из них, деформируются незначительно. Кварцевые смеси требуют меньшего количества воды, чем асбестовые, так как меньше ее поглощают. Линейная усадка таких смесей также меньше, чем асбестовых смесей.
Достоинства гипсовых смесей:
– Удовлетворительная прочность
– легкая выбиваемость
Недостатки:
– недостаточная термостойкость
– ограниченная область применения
– наличие усадки смеси и возможное
растрескивание форм. Для снижения
растрескивания вводят пылевидный кварц
и снижают количество гипса.
Литье в этилсиликатные формы.
Керамические формы применяются при изготовлении точных отливок по выплавляемым моделям или по Шоу-процессу. Формовочная смесь имеет кашеобразную консистенцию и состоит из твердого керамического компонента и жидкого связующего.
Для керамических форм используются следующие огнеупорные наполнители:
пылевидный кварц(маршалит) ПК1, ПК2, ПК3. Для керамических форм ПК2, ПК3.
электрокорунд. Используется для тугоплавких Ме и сплавов на основе Mg.
цирконовая мука
двуокись титана. Применяется для высоколегированных сталей и других сплавов с основным характером оксидов.
Чаще всего для керамических
форм применяется кремнезем SiO2 в виде пылевидного кварца (маршалита). Как уже отмечалось выше, кварц вследствие
изменения его кристаллических
модификаций отличается
резким изменением объема при нагревании
и плавится при температуре 1550°
С.
Кроме кварца при изготовлении керамических форм используют:
Глинозем А12О3 — искусственный корунд — применяется в виде порошка и крошки, температура плавления 2045° Q при нагреве не происходит существенных объемных изменений.
Силиманит А12О3 • SiO2 — природный силикат алюминия — пригоден для точного литья из цветных сплавов; плавится при температуре 1545° С.
Муллит ЗА12О3 • 2SiO2 — силикат алюминия, получаемый искусственно из каолина; плавится при температуре 1810°С.
Циркон ZrSiO4 — силикат циркония; температура плавления до 2430° С.
Молохит представляет
собой обожженный каолин, который, кроме
SiO2 и
А12О3,
содержит оксиды титана, железа
и щелочных металлов.
В качестве жидкого связующего применяют:
Алкозоли, или гидрозоли SiO2, которые являются коллоидными растворами некоторых органических соединений кремния. Среди них наиболее важный тетра-этилортосиликат, химическая формула которого SiO4(C2H5)4. Связь отдельных зерен наполнителя обеспечивается за счет пленок геля, образующегося под действием воды и кислого гидролизованного катализатора.
Гетеросилоксаны представляют
собой алюмосиликатные
эфиры, которые под действием влаги,
содержащейся в воздухе,
гидролитически расщепляются на коллоидные
растворы соединений алюминия
и кремния. Образующийся гель после
обжига связывает зерна керамики в
форме прочных алюмосиликатов. -Хлор-этоксититанат применяется
в растворе
бензола в качестве связующего форм
для сплавов из титана и других металлов
с высокой реакционной способностью. Аминоалкилсиликат и основной нитрат
алюминия применяются
в виде спиртовых
растворов, гидролиз и гелеобразование
которых вызываются аммиаком.
Кашеобразная формовочная смесь в несколько слоев наносится на модель, присыпается керамической крошкой и сушится. После извлечения или выплавления модели образуется керамическая форма. Сушка производится медленно при повышении температуры нагрева на 120° С в течение нескольких часов. После удаления остатков углеродистых соединений и упрочнения силикатного геля формы последовательно обжигают при температурах 400, 600, 800, 1000° С в течение 6—8 ч. Заливку форм металлом производят сразу после обжига, пока они не впитали влагу из воздуха. Как уже указывалось, в кварцевых материалах при охлаждении происходит обратная перекристаллизация, которая может вызвать растрескивание форм.
Пресс-формы для гипса – Etsy.de
Etsy больше не поддерживает старые версии вашего веб-браузера, чтобы обеспечить безопасность пользовательских данных. Пожалуйста, обновите до последней версии.
Воспользуйтесь всеми преимуществами нашего сайта, включив JavaScript.
Найдите что-нибудь памятное, присоединяйтесь к сообществу, делающему добро.
(более 1000 релевантных результатов)
Как сделать гипсовую форму для шликерного литья
Шликерное литье, вероятно, самый популярный способ изготовления керамических стеновых деталей, особенно если детали состоят из повторяющихся форм. Если вы задавались вопросом, как сделать гипсовую форму для шликерного литья, то сегодняшний пост для вас.
В этой выдержке из Ceramics Monthly архив Джеки Хед проведет вас через процесс изготовления гипсовой формы от изготовления прототипа до заливки гипсовой формы. Так что посмотрите и вычеркните «научиться делать гипсовую форму для шликерного литья» из своего списка дел! – Дженнифер Поэллот Харнетти, редактор
PS. Чтобы узнать больше о процессе отделки и установки Джеки, а также увидеть больше изображений ее работ, см.выпуск Керамика Ежемесячно !
Изготовление гипсовой формы для шликерного литья. Часть 1. Прототипы
Контуры плиток увеличены на 10 %, чтобы компенсировать усадку, возникающую при обжиге фарфоровой массы до конуса 6. Я распечатываю контур форм-прототипов, вырежьте их и обведите на ламинированных досках. Отдельные прототипы
Передняя и задняя половины каждой из фигур вылеплены из твердой глины с использованием глиняного тела без шамота для получения гладкой поверхности. Влажная глина грубо набивается на доски приблизительной формы и желаемой толщины прототипов плитки.
После сушки в течение нескольких часов глина начинает застывать, затем я вырезаю прототипы, придавая им более четкую форму (1). Как только прототипы достигают начальных стадий твердости кожи, я уточняю формы, используя инструменты с зазубренными петлями и различные ребра.
для достижения их окончательной формы, гарантируя отсутствие подрезов на прототипе (2).
При подготовке к созданию форм передней половины каждой формы прототипы дорабатываются в последний раз. Для этого используется мягкая кисть, смоченная в воде, для устранения любых дефектов, а гибкое ребро используется для создания гладкой поверхности. поверхности и укрепить любые острые углы.
Изготовление гипсовой формы для шликерного литья. Часть 2. Создание форм оставляя зазор в 1,5–2 дюйма между обшивкой и краем глиняной формы. Обшивка создает барьер, удерживающий гипс после его заливки на прототип (3).

После того, как гипс схватится, следующим шагом будет изготовление задней половинки. Создание обратной стороны плитки визуально приподнимает форму над стеной и делает ее более объемной и интерактивной для зрителя. Чтобы начать этот процесс, создайте регистрационные ключи
в первой половине формы. Используйте проволочный инструмент, чтобы аккуратно отделить заднюю часть формы прототипа от ламинированной доски. Поместите его поверх гипсовой формы так, чтобы он совпадал с твердой глиняной формой, которая все еще находится в форме. Этот шаг
требует терпения и внимания к деталям. Важно убедиться, что передняя и задняя часть плитки идеально совпадают. Для этого используйте металлическое ребро и постепенно состригайте стороны задней половины плитки,
до тех пор, пока не станет виден край глины с передней части плитки.