Горячее цинкование металла: 💥Услуга горячего цинкования металлоконструкций – цена оцинковывания и покрытия металла цинком
alexxlab | 08.01.1986 | 0 | Разное
Цинкование металлоконструкций – холодное и горячее цинкование металла в Москве
Завод Свайных Конструкций предлагает нанесение цинкового покрытия толщиной от 20 до 200 микрон различными способами. Стоимость услуг по оцинковке металла зависит от выбранного способа и объема заказа. Подробнее о стоимости услуг вы можете узнать, позвонив в наш офис.
Технологии нанесения цинка.
На сегодняшний день для защиты металлических изделий от коррозии применяются различные анодные покрытия. Одним из самых популярных методов защиты от коррозии является горячее цинкование стали. Данная технология представляет собой обработку поверхности заготовок слоем серебристо-белого металла или же его сплавом. Кроме этого, также производится цинковое насыщение поверхностных слоев металлической конструкции для защиты от коррозийных процессов.
Различные методы оцинковки давно применяются в самых разнообразных отраслях: строительстве, энергетике, газодобывающей, нефтедобывающей и нефтеперерабатывающей промышленности, сельском хозяйстве, автомобилестроении.
Хотя цинковая защита актуальна практически для любых металлических конструкций, чаще всего защищают:
- Металлоконструкции зданий.
- Оборудование, используемое на речных и морских судах.
- Опоры ЛЭП.
- Дорожные ограждения.
Популярность обработки различных изделий цинком очень легко объясняется. Во-первых, покрытие обладает высокой устойчивостью к различным внешним воздействиям, во-вторых, оно полностью безопасно, в-третьих, цены нанесения покрытия невелики. Стационарный потенциал покрытия на 0.2-0.3 мВ более отрицателен, чем железо, поэтому при воздействии агрессивных сред цинк растворяется медленнее за счет электрохимических реакций, соответственно, защищая ферритную подложку.
Цинковое покрытие – это лучшая защита металлоконструкции от коррозии в средах, значения кислотности которых близки к нейтральным. К примеру, в атмосфере, пресной и морской воде, почве. В сильнокислых или же сильнощелочных средах цинковое покрытие не будет обладать нужным уровнем стойкости.
Как наносятся цинковые покрытия.
Подобные покрытия наносятся путем электроосаждения, погружения в расплав, металлизации, напыления, химического осаждения, диффузии, испарения цинка в вакууме с последующей конденсацией паров на защищаемой поверхности.
Перед процедурой холодного цинкования или нанесения защитного покрытия по иной технологии любое металлическое изделие сначала предварительно обрабатывают для того, чтобы впоследствии избежать образования газовых пузырей. В изделиях проделываются специальные технологические отверстия. Методы нанесения слоя цинка могут быть весьма разнообразны: горячее и холодное цинкование металлоконструкций, гальваническая и термодиффузионная обработка. Метод, а также необходимая толщина оцинковки выбираются исходя из степени агрессивности факторов окружающей среды. Толщина обычно варьируется в пределах 0.8-2 мкм. О каждом методе цинкования мы подробно расскажем чуть ниже.
Горячее цинкование
Технология горячего цинкования наиболее используема, т. к. именно данная процедура обеспечивает высокую коррозийную устойчивость. Этот показатель в несколько раз превышает аналогичный у покрытий, к примеру, нанесенных гальваническим методом. Наши специалисты, которыми осуществляется горячая обработка металлоконструкций, смогут порекомендовать оптимальный метод сбережения ваших сооружений в зависимости от их специфики. Ведь там, где есть плюсы, не обойтись и без минусов. Отрицательные моменты, сопровождающие цинкование металла, выражаются в высокой стоимости покрытия, неравномерности покрытия, а также сложности оборудования для осуществления данной технологии. Также следует сказать о необходимости повторной проточки резьбы и возможном возникновении напряжения в заготовках.
Как происходит горячее цинкование.
Металлические изделия (трубы или другие изделия из стали) окунают в ванну с расплавленным цинком при температуре около 460 °C. С данным покрытием срок эксплуатации металлического изделия продлевается до 50 лет. Во время процесса цинкования между цинком и самой металлической конструкцией образуется очень устойчивое соединение, благодаря которому и достигается высокая устойчивость к коррозии даже с учетом появления на поверхности изделия какого-либо повреждения.
Этапы горячего цинкования:
1. Предварительная обработка металлических изделий: обезжиривание, очищение при помощи пескоструйного метода, травление кислотой, промывка под сильным напором чистой воды.
2. Флюсование. На поверхность изделия наносится тонкий слой пленки, благодаря которой металл не окислится, а взаимодействие с цинком будет лучше.
3. Просушка.
4. Цинкование металла. Изделие погружается в ванну с чистым расплавленным защитным покрытием.
5. Изделия медленно вынимаются, а избыток цинка удаляется при помощи дренажа, вибрирования или же центрифугирования.
6. Охлаждение изделий в воде или на атмосферном воздухе после извлечения из ванны.
7. Проверка.
Холодное цинкование
Если технологии горячего, гальванического и термодиффузионного цинкования достаточно сложны и энергоемки, то технология холодного цинкования металла, которое наша компания осуществляет по самой доступной в Москве цене, не нуждается в создании каких-то особых условий. Также не требуется применение различных реактивов. В качестве предварительной обработки перед началом холодного цинкования осуществляется традиционная очистка металла.
После предварительной обработки на металлическую поверхность наносятся специальные красители или грунтовки. Их основой служит цинковая пудра. Так же, как и при технологии горячего цинкования, цинк становится анодом в гальванической паре с железом, обеспечивая его катодную защиту. Данный вид покрытия наносится при помощи распылителя. После холодного цинкования металлическое изделие будет надежно защищено от коррозии. Следовательно, оно отличается долговечностью в эксплуатации и имеет красивый внешний вид. Говоря о последнем, следует сказать, что при использовании холодного цинкования металлические изделия не будут иметь металлического блеска. Зато на конструкции можно наносить практически любые виды лакокрасочных материалов.
Гальваническое цинкование
Осуществляется за счет электрохимического процесса в специальном барабане и может иметь разный цвет: голубой, белый, матовый белый или радужный.
Технология гальванического цинкования обладает рядом преимуществ. К примеру, высокая производительность, равномерные и блестящие покрытия. Но сразу же стоит сказать и про минусы, которыми обладает гальваническое цинкование, а именно низкие адгезионные характеристики, а соответственно, и коррозийные свойства. Еще одним минусом является возможность водородного охрупчивания металла при анодировании.
В наше время технология гальванического цинкования – самый популярный способ защиты метизов и различных крепежных изделий, т. к. производительность процесса достаточно высока, а себестоимость, наоборот, низкая. Кроме этого, для подобных изделий степень защиты от коррозии достаточна.
Как происходит гальваническое цинкование.
В ванне с электролитом находятся два металла: металлические изделия и чистый цинк. Далее к ним подводится электрический ток.
Данную технологию можно разделить на три способа: цианидный, щелочной и кислотный. Чаще всего предпочтение отдается цинкованию в слабокислых электролитах. Благодаря данной технологии обеспечивается высокая степень защиты, а также улучшенный внешний вид изделия. Также применение данной технологии способствует снижению склонности цинкуемых изделий из углеродистых и легированных сталей к водородной хрупкости. Это позволяет цинковать детали сложной конфигурации, в том числе, для изготовления которых использовалась сталь или чугун.
Этапы проведения цинкования.
1. Очистка изделий от окалины, остатков технологической смазки, ржавчины.
2. Нанесение на металл цинкового покрытия.
3. Осветление (декапирование – травление в слабом растворе азотной кислоты).
4. Пассивация с целью не только придания изделию коррозийной стойкости, но и улучшения декоративных характеристик.
Термодиффузионное цинкование
Термодиффузионное цинкование производится при температуре 290-400°C. Нужная температура устанавливается исходя из марки стали, а также типа обрабатываемого изделия и нормативов производителя. Горячее цинкование металлоконструкций по данному методу представляет собой постоянное вращение контейнера с загруженными изделиями, который останавливается только после завершения процесса. Далее он выгружается из печи, остужается и разгружается. После этого происходит пассивация.
Подвергшиеся горячему цинкованию детали проходят через специальную установку и подвергаются обработке специальными пассивационными растворами, благодаря которым достигается невосприимчивость покрытия к агрессии атмосферного воздуха. Параллельно с пассивацией производится галтовка керамическими или пластмассовыми чипсами, которая способствует улучшению внешнего вида покрытия и положительно влияет на его качество.
Пассивация осуществляется только один раз в том случае, если в дальнейшем предполагается какая-либо обработка деталей: окрашивание, склейка и т.д. В остальных случаях пассивация проводится второй раз.
Последним этапом, который включает в себя горячее цинкование металла по данной технологии, является высушивание деталей в установке проходного типа. Время, затрачиваемое на процедуру, составляет 90 или 180 минут. Это зависит от типа используемой цинковой смеси и мощности установки.
Основными плюсами данной технологии являются:
1. Обеспечение высокой коррозийной стойкости.
2. Покрытие точно воспроизводит обрабатываемое изделие, к примеру, любой тонкий рельеф, резьбу, маркировку трубы и т. д.
3. Оцинкованное покрытие обладает высоким уровнем твердости в отличие от других цинковых покрытий. Микротвердость покрытия не только составляет примерно 4500 МПа, но и обладает хорошим сопротивлением абразивному износу.
4. Наводораживание во время нанесения покрытия на сталь или трубы исключено.
5. Учитывая невысокую температуру насыщения, нанесение покрытия возможно на предварительно термообработанные детали.
6. Технология термодиффузионного цинкования может быть применена для нанесения покрытий на пористые изделия, на предварительно собранные узлы, а также на изделия, произведенные по порошковой технологии.
7. В отличие от холодного цинкования данный метод способствует получению минимального адгезионного износа при дальнейшей обработке лакокрасочными покрытиями, резиной, пластмассой и т. д.
8. Предварительная обработка труб и других изделий перед термодиффузионным цинкованием не требует каких-либо больших затрат, а кроме того, на изделиях допускается присутствие пятен от коррозии, остатков смазки или СОЖ.
9. В некоторых случаях толщина покрытия может варьироваться в пределах от 15 до 100 мкм и выше.
Если говорить о минусах данной технологии, то следует сказать о небольшой производительности, ограниченной объемами камер для цинкования, а также об отсутствии эстетических характеристик у изделия: сдержанность цветового исполнения, отсутствие блеска.
Данный процесс представляет собой нанесение цинка на металлическую трубу с целью повышения сопротивления коррозии. Таким образом продлевается срок ее службы. Оцинкованная труба используется для прокладки внутренних коммуникаций в различных помещениях, как жилых, так и промышленных. Компания «Завод Свайных Конструкций» также специализируется на цинковании различных конструкций из металла. Достаточно часто обработке подвергается труба для прокладки в агрессивных внешних условиях. Обратившись к нашим специалистам, вы гарантированно получите качественные услуги. На цинкование труб нами установлена оптимальная для заказчиков из Москвы и других регионов цена.
Читайте также: | |
Оцинкованные винтовые сваи – максимальная защита от коррозии | |
Очистка металла от коррозии | |
Свайно-винтовой фундамент для ангаров | |
Преимущества технологии винтовых свай |
Отличие холодное цинкования от горячего Cumixan
Методов защиты металла довольно много: гальванический способ, диффузионное, газодинамическое, холодное и горячее цинкование. Несмотря на разнообразие способов защиты металла, самыми распространенными являются методы холодного и горячего цинкования. И так, давайте рассмотрим, какой же из этих методов лучше?
Для начала, давайте разберем, что такое цинкование?
Цинкование – это покрытие металла слоем цинка для защиты от коррозии. Цинковое покрытие всегда обеспечивает активную (катодную) и пассивную (барьерную) защиты.
При контакте металла и цинка возникает электрохимическая реакция. Цинк утрачивает свои электроны и расходуется первым, не давай коррозии образовываться на металле, до тех пор пока не истощится. Уже начавшийся процесс ржавления останавливается. Этот способ назван катодной или активной защитой.
Кроме этого, цинковое покрытие дает еще пассивную (барьерную) защиту, образовывает на поверхности плотную пленку. Пленка не пропускает влагу и кислород к защищенному железу. Все виды цинкования (нанесения цинка) дают металлу активную и пассивную защиту.
Горячее цинкование — покрытие металла слоем цинка путём окунания изделия в ванну с расплавленным цинком при температуре около 460 °C. Далее, конструкцию подвешивают и ждут до полного высыхания. По мере высыхания, цинком заполняются все труднодоступные места, поры и микротрещенки изделия и покрытие получается ровным и не имеет пропусков.
Данный метод изобрели более 100 лет назад, поэтому его называют самым проверенным способом защиты металлов от коррозии. С возникновения метода в его технологическом процессе практически ничего не изменилось.
Холодное цинкование – нанесение на подготовленную поверхность металла состава с содержанием цинка 92-96%. Применяется холодное цинкование как обычные краски – наносится кистью, валиком, краскопультом и окунанием.
Метод холодного цинкования разработан относительно недавно, в восьмидесятых годах 20-го столетия. Изобрел его один из ученых УрО РАН (Уральского Отделения Российской Академии Наук). С тех пор его популярность растет с каждым годом из-за удобства и практичности.
Само покрытие может иметь небольшие механические повреждения, царапины, поры, но во время периода эксплуатации эти недостатки «забиваются» (тем самым уплотняя покрытие) продуктами растворения цинка. Метод холодного цинкования наиболее легок в исполнении, дешевый и доступный. Холодное цинкование можно осуществить на месте эксплуатации металлоконструкции без ее демонтажа. Каких либо ограничений по размерам и формам конструкции при этом не существует. Подготовку поверхности перед холодным цинкованием также производят на месте.
Само покрытие может иметь небольшие механические повреждения, царапины, поры, но во время периода эксплуатации эти недостатки «забиваются» (тем самым уплотняя покрытие) продуктами растворения цинка. Холодное цинкование можно осуществить на месте эксплуатации металлоконструкции без ее демонтажа. Каких либо ограничений по размерам и формам конструкции при этом не существует. Подготовку поверхности перед холодным цинкованием также производят на месте.
Процесс нанесения цинкнаполненного состава довольно легок в исполнении, т.к. можно применять окунание, покраску кистью (валиком) либо распыление. Оцинковку проводят при температурах от -10 до +40 °С.
Покрытие абсолютно пожаробезопасно и электропроводно.
Преимущества и недостатки методов
Холодное цинкование |
Горячее цинкование |
Преимущества |
|
– Быстрое высыхание (точное время зависит от толщины покрытия). – Совместимость с многими ЛКМ. – Подходит обычный растворитель. – Под покрытием не образуется коррозия. – Допускается сварка после нанесения. – Конструкции не нужно перевозить – нет расходов на транспортировку. – Адгезия – 1 балл. – Не ржавеет в местах повреждения. – Легко восстановить поврежденные участки. |
– Маленькие изделия окунаются легко и быстро. – 100% проникновение в труднодоступные места. – Цена рассчитывается исходя из веса конструкции. – Качество покрытия не зависит от того, кто наносит. – Образует сплошное покрытие, без стыков и границ. – Придает металлам внешнюю привлекательность. – Все за вас сделают специалисты– меньше вашего времени и усилий. |
Недостатки |
|
– Качество покрытия зависит от того, кто его наносит. – Соблюдение условий при нанесении и высыхании покрытия. – Требуется тщательная подготовка поверхности. – Сложно покрыть внутренние полости и труднодоступные места. |
– Ванны для окунания ограниченных размеров – не подходит для очень крупных конструкций. – Не работает с некоторыми марками металлов. – Деформация тонких конструкций при нагреве. – Сварка деталей после «горячего» цинкования разрушает защиту. – Поврежденное покрытие нельзя отремонтировать, только оцинковывать заново всю конструкцию. – При сборке конструкции после цинкования стыки и места сборки необходимо дополнительно защищать от коррозии. – Необходимо привезти конструкции в место цинкования и обратно – дополнительные расходы на транспортировку. – При транспортировке разрушаются участки, которые потом нуждаются в дополнительной защите. – После цинкования могут остаться некрасивые подтеки «жидкого» цинка. |
Вывод:
Определиться однозначно с выбором метода цинкования довольно непросто. Однако, несмотря на надежность и результат, проверенный столетиями, метод горячего цинкования связан с определенными расходами, это и расходы на транспортировку, покупка ванн нужных размеров и саму процедуру. Холодное цинкование выходит несколько дешевле, ничуть не теряя в качестве. К тому же, холодное цинкование проще наносится, более устойчиво к внешней среде и воздействиям, а при повреждениях, быстро ремонтируется.
Холодное цинкование даст Вам уверенность в качестве выпускаемой продукции, ведь после нанесения можно не вспоминать о коррозии на срок до 25 лет.
Читайте также на эту тему:
Холодное цинкование – что это? | Холодное и горячее цинкование – отличия | Цинкование – защита от коррозии | Ремонтопригодность цинковых покрытий |
Как оставить заявку или получить консультацию от наших специалистов?
Наша организация всегда готова предложить качественное покрытие по демократичным ценам. А технические специалисты просчитают и составят самую оптимальную систему покрытия, опираясь на необходимый срок эксплуатации, что в дальнейшем, сэкономит Вам время и деньги.
Не знаете, как составить заявку или остались вопросы?
Позвоните нам 8 (800) 777-28-99, или напишите [email protected] и мы с радостью ответим на все Ваши вопросы. Мы находимся в Екатеринбурге.
Горячее цинкование металлоконструкций | Металл Индустрия
В поиске недорогого и надежного способа защиты металла от коррозии заказчики выбирают горячее цинкование металлоконструкций. В Краснодаре услуги по обработке изделий от негативного воздействия внешней среды методом опускания в цинковую ванну предоставляет ООО «Металл Индустрия».
Цинкование – процесс многоэтапный. Чтобы добиться высокой степени адгезии цинка с поверхностью, на подготовительной стадии проводится многоуровневая обработка заготовки в соответствии с требованиями ГОСТ. Непосредственно этап цинкования продолжается до 15 минут с поддержанием оптимального температурного режима и скорости изъятия изделия из ванны. Высокое качество покрытия, соблюдение сроков выполнения заказа, низкие цены за тонну оцинкованных металлоконструкций выделяют наше предприятие на фоне других компаний.
Технология горячего цинкования подходит изделиям, эксплуатация которых предполагается в интенсивном режиме, в т.ч. в регионах с холодным климатом. Производственные мощности нашего завода рассчитаны на обработку многих тонн металлоконструкции ежедневно. Мы без задержек обслуживаем предприятия родного Краснодара и клиентов из других, в т.ч., отдаленных регионов России.
Технология горячего цинкования –
последняя ступень в эволюции систем антикоррозионной защиты. Экономические преимущества методики очевидны. Выбор в пользу этого способа обработки демонстрируют профессионализм руководителя – более успешного и перспективного по сравнению с теми, кто не считает цинкование передовой технологией.
Какие изделия подлежат цинкованию
Завод горячего цинкования металлоконструкций ООО «Металл Индустрия» принимает на обработку:
- Изделия и конструкции из стали (кремнийсодержащей, нержавеющей и др.), чугуна;
- Трубы;
- Швеллеры, арматуру, уголки, двутавровые балки, другие виды сортового проката;
- Стальные листы;
- Сетку;
- Нестандартные конструкции, габариты которых превышают размер емкости с цинком;
- Конструкции с подвижными деталями;
- Изделия с высоким весом, большими габаритами.
Работаем с опорными колоннами сооружений, фермами перекрытий. Проводим горячее цинкование дорожных ограждений, стальных профилей для опор ЛЭП и др. Уточнить информацию о продукции, с которой мы работаем, можете по телефону.
Почему производители металлоконструкций выбирают горячее цинкование
Использование эффективной методики защиты сократит расходы на изготовление металлоконструкции в целом. Учитывая долговечность созданного покрытия, отпадает необходимость в повторной обработке, а это уже другие сэкономленные суммы. Те, кто еще не сталкивался с цинкованием и до сих пор пользуется окрашиванием поверхностей, обновляют защиту с периодичностью раз в 1-2 года. Иначе изделия покроется ржавчиной и потребуется больше денег на его замену.
Кроме профилактики коррозии цинковая пленка создает металлу электрохимическую защиту за счет образования на поверхности ферроцинкового сплава. Ни ЛКМ, ни полимеры, ни металлизированная пыль не в состоянии поднять защитные свойства на такой же уровень.
На заводе установлена ультрасовременная автоматическая линия горячего цинкования. Заготовку защитного состава мы осуществляем из компонентов высокого качества. Сырье нам поставляют лидеры российского и мирового рынка.
Цинковое покрытие замедляет скорость коррозии черного металла примерно в 50 раз. Срок службы металлоконструкции достигает 80 лет.
Другие преимущества горячего цинкования:
- Пленка смягчает удары, делает конструкцию прочнее;
- За долгий период эксплуатации на поверхности скапливается меньше отложений, чем при отсутствии цинка;
- При соединении конструкции с фрикционными муфтами оцинковка сохраняется;
- Болтовые крепления удается просто размонтировать;
- Поддерживает антикоррозионные свойства в щелочной среде.
Цена на горячее цинкование металлоконструкций
Расчет стоимости цинкования проводим с учетом объема и сложности конструкции. Можете позвонить нам по номеру +7 (861) 279-17-00 или оставить заявку на обратный звонок, чтобы заказать калькуляцию по своим параметрам.
Ведущие позиции горячего цинкования в настоящем и будущем сложно оспаривать. Для получения веских аргументов превосходства технологии над окрашиванием достаточно сравнить стоимость обеих методик за последние 2-3 десятилетия. При этом учтите, что подготовку поверхности к нанесению ЛКМ проводят пескоструйным способом, а это достаточно дорогая процедура. С большой вероятностью можно утверждать, что такое соотношение цен сохранится в будущем. Россия не испытывает дефицита в цинке. Возможно, его себестоимость станет еще ниже материалов-конкурентов.
Горячее цинкование в Краснодаре – лучшие предложения
Заказав обработку металлоконструкций горячим цинкованием в нашей компании, кроме преимуществ самой методики вы получите больше привилегий от сотрудничества с одним из ведущих предприятий отрасли. Предлагаем:
- Оптимальные сроки и гарантии их соблюдения;
- Низкие тарифы;
- Качественную, экономически выгодную логистику;
- Доступность изготовления металлоконструкций с последующим цинкованием в одном месте.
В заявке просим указать габаритные размеры изделий, марку металла, толщину заготовки, желаемую дату готовности заказа.
Горячее цинкование металлоконструкций – статьи о металлоконструкциях от ООО «КАСКАД»
Одним из наиболее эффективных способов антикоррозионной защиты является анодное покрытие. Существует несколько методик его выполнения, различающихся типом применяемого оборудования, сложностью процесса, затрачиваемым временем и стоимостью. Наибольшее распространение получило горячее цинкование металлоконструкций. По популярности данная технология уступает только электролитическому способу, поскольку стоит несколько дороже. Зато покрытия, полученные посредством горячего цинкования, намного долговечнее.
Базовые преимущества горячего оцинкования
- Универсальность.
Технологию можно применять на металлических заготовках любой формы, сложности, типа и сферы использования.
- Самовосстановление. При небольших механических повреждениях дефект покрытия уменьшается и со временем исчезает.
- Надежность. Устойчивость цинкового покрытия, нанесенного горячим способом, в 6 раз выше по сравнению с защитными слоями, полученными другими методами.
- Маскировочный эффект. Слой цинка скрывает поры и другие дефекты основы, избавляя от дополнительных работ по их устранению.
- Высокая адгезия. Технология горячего цинкования металлоконструкций обеспечивает надежное сцепление защитного покрытия с поверхностью заготовки.
- Небольшие эксплуатационные расходы. Затраты на эксплуатацию снижаются благодаря отсутствию необходимости систематически окрашивать металлоконструкцию.
Принцип оцинкования горячим способом
На поверхность заготовки наносится слой цинка толщиной 40–65 микрон. Полученное покрытие исключает прямой контакт материала изделия с жидкостями, благодаря чему и обеспечивается эффективная антикоррозионная защита. Горячее цинкование металлоконструкций в Московской области и других регионах используется преимущественно для стали и железа. По экспертным оценкам, покрытие, полученное с помощью описываемой методики, сохраняет свои защитные свойства минимум 65–70 лет.
Согласно технологии горячего цинкования, предварительно подготовленная конструкция погружается в емкость с расплавленным цинком. Жидкий металл обволакивает изделие, попадая даже в труднодоступные места. Более подробная информация о данной технологии изложена в ГОСТ № 9.307 (1989 г.). Чтобы понять принцип такой обработки, рассмотрим ее базовые этапы.
Подготовка металлоконструкции к горячему цинкованию
Механическая обработка. Она призвана удалить окалину, грязь и прочие загрязнения с поверхности. Механическая обработка выполняется с помощью пескоструйных аппаратов.
Обезжиривание. Данный технологический этап необходим, чтобы увеличить силу сцепления цинка с поверхностью заготовки, ведь наличие посторонних веществ (например, масла) может привести к отслоению защитного покрытия. Обезжиривание проводится при температуре порядка 75 °С с применением специальных реагентов.
Промывка. Она позволяет удалить с поверхности деталей все посторонние вещества, например применяемые в процессе обезжиривания.
Травление. На металлических поверхностях всегда присутствует определенное количество окислов, включая ржавчину. Травление посредством соляной и других кислот позволяет удалить их. Обработка выполняется при температуре (23 ± 1) °С, концентрация раствора подбирается в зависимости от уровня загрязненности и составляет 140–200 г/л. После травления осуществляется промывка, позволяющая очистить конструкцию от остатков кислотного раствора и продуктов произошедших химических реакций.
Флюсование. Это финальный этап подготовки к горячему цинкованию металлоконструкций. Тонкий слой флюса блокирует окисление металла и повышает надежность сцепления цинка с основанием. Как правило, для флюсования используются составы на основе хлоридов цинка и аммония.
Термическая обработка металлоконструкций
После подготовки изделия с помощью растворов его тщательно просушивают. Наличие жидкости на поверхности приводит к парообразованию, что негативно сказывается на качестве защитного покрытия. Кроме того, предварительный разогрев изделия до 100 °С уменьшает энергетические расходы на дальнейшие этапы, предусмотренные технологией горячего цинкования металлоконструкций. Для максимального просушивания используют минимум 2 термические камеры.
Горячее цинкование
После завершения термообработки заготовку покрывают слоем цинка. Оптимальный температурный режим подбирают с учетом специфики конструкции и внешних условий. В среднем обработка осуществляется при температуре 420–455 °С. Базовые технологические особенности процесса:
- наличие мощной вытяжки, поскольку процесс оцинкования сопровождается активным паровыделением;
- четкое соблюдение скорости погружения заготовки, времени выдержки ее в резервуаре с расплавленным цинком.
Технология горячего цинкования металлоконструкций предусматривает выполнение следующих базовых операций:
- погружения;
- выдержки в резервуаре на протяжении 4–10 мин. Если появляется шлак, его удаляют механическими методами;
- выемки конструкции из ванны. Толщина покрытия во многом зависит от скорости извлечения изделия, поэтому она индивидуально рассчитывается для каждого образца.
После горячего цинкования металлоконструкция подвергается естественному или принудительному охлаждению в закрытом помещении. После этого она готова к эксплуатации.
Горячее цинкование
- Главная
- Производство
- Горячее цинкование металлоконструкций
Главным направлением деятельности завода металлоконструкций ООО “Гофра 2001” является осуществление горячего цинкования металлоконструкций любой сложности.
Данный метод защиты металла от коррозии является передовым, современным и самым эффективным. Горячее цинкование в целях антикоррозийной защиты металлоконструкций значительно повысит срок их службы. После того, как будет произведена оцинковка, поверхность изделия может быть окрашена. Процесс горячего оцинкования – это экономически выгодный подход для защиты металлоконструкций от коррозии, который позволит забыть о проблеме коррозии на десятки лет.
Почему горячее цинкование?
* Эффективность.
Покрытие, образующееся при горячем цинковании, служит прочным и, что самое главное, активным барьером на пути коррозии металлоконструкции
* Надежность
Во время горячего цинкования стальная заготовка полностью погружается в расплавленный цинк, в результате чего покрывается вся поверхность детали
* Экономичность
Несмотря на относительно высокую стоимость цинка, способ защиты от коррозии методом горячего цинкования является экономичным
* Экологичность
Цинк является абсолютно безопасным для окружающей среды элементом
Где используется горячее цинкование?
После того, как изделия пройдут процесс горячего цинкования, они могут быть использованы в следующих областях:
Дорожное строительство Опорные, перильные и шумопоглощающие ограждения, пролетные конструкции трубопроводов и мостов, направляющие и столбы, барьеры безопасности, водовыпускные и дренажные трубы, рабочие платфрмы, мачты освещения, опоры для дорожных занаков, арматурная сетка. |
Городская инфраструктура Мосты, мостки, флагштоки, элементы рекламных конструкций, стальные решетки и другие декоративные ограждения, лестницы, металлические скульптуры, контейнеры для мусора, парковые скамейки, элементы автобусных остановок, спортивных и игровых площадок. |
Связь
Антенны, радиомачты сотовой и радиосвязи, ретрансляторы для телефонной связи, СВЧ-опоры, каналы для кабелей и проводов. |
Строительство Каракасы систем зданий, стальная крупнощитовая опалубка, фасадные панели, рельсы, фермы, решетки, люки, заклдадные детали, кровля, ограждающие элементы лестниц, водосточная система, оконные отливы, защитные колпаки для вентиляции и другие строительные металлоконструкции. |
Энергетика Опоры ЛЭП, соединительные элементы и подвесная арматура для проводов, трансформаторные будки, опоры трубопроводов, вышки, элементы опорных и несущих конструкций газовых и электрических подстанций. |
Промышленность Детали для сельского хозяйства и животноводства, целлюлозной промышленности, элементы конструкций для переработки сточных вод и другого промышленного оборудования, стальные двери, окна, склады и ангары, различные контейнеры, шлюзы, опоры и перемычки для крнов, бункеры, емкости, навесы, элементы теплиц и другие конструкции. |
Технологический цикл горячего цинкования.
Технология горячего цинкования предусматривает погружение металлических изделий в расплав цинка. Наиболее используемым в промышленности методом цинкования является жидкофазный способ, преимущество которого заключается в высокой производительности с регулируемым качеством и количеством покрытия, а также в применении относительно простого оборудования.
В процессе контакта поверхности стали с жидким цинком, после смачивания за счет диффузионных процессов образуются твердые фазы железо-цинк. При выходе изделия из ванны с цинковым расплавом на поверхности интерметаллических соединений образовывается слой покрытия, который соответствует составу металла в ванне. В том случае, если в некоторых местах на поверхности стали не образовался железоцинковый сплав, то она не смачивается цинком. Участки поверхности, непокрытые цинком, называются «чернотами».
Взаимодействие цинка с металлическим изделием зависит от температуры расплава, длительности взаимного контакта, химического состава расплава цинка и стали, а также ее структуры. Для получения толстого, однородного и пластичного цинкового покрытия горячее цинкованиевыполняют при температуре от 430 до 450 C.
В целях повышения равномерности распределения покрытия и исключения появления наплывов цинка на поверхности стальных изделий применяют сглаживающие устройства. Они могут быть механическими – протиры из стеклоткани или асбеста, сыпучими с применением древесно — угольной засыпки зеркала ванны в месте выхода металлоизделия из ванны и пневматическими, при которых производится интенсивная обдувка струей воздуха.
Во избежание дефектов оцинкованного металла, ухудшающих его потребительские качества, внешний вид и значительно снижающих коррозионные свойства покрытия, перед оцинковкой металлическая поверхность должна быть тщательно очищена от технологической смазки, окалины, жировых или других загрязнений. Стальные изделия подвергаются обезжириванию, горячей и холодной промывке, травлению и флюсованию.
Горячее цинкование, как наиболее эффективная и экономичная технология защиты от коррозии, сегодня достаточно распространено во всем мире. Оцинковка металла применяется для повышения коррозионностойкости металлоконструкций для сооружения мостов, опор линий электропередач, вышек разного предназначения, металлокаркасов зданий, эксплуатируемых в условиях высокой влажности, в конструкциях нефтеперерабатывающих производств, в автомобильной промышленности и многих других сферах, требующих долговечности изделий из металла.
Горячее цинкование в СПб на заводе металлоконструкций Гофра-2001.
С учетом потребностей рынка, на предприятии была смонтирована линия горячего цинкования итальянской компании “Gruppo Maccabeo”. Цех оборудован ванной размерами 12,5 х 1,6 х 2,6 м, вмещающей 350 тонн цинка. В ней могут быть обработаны:
Опоры высоковольтных линий
Опоры контактной сети
Ригели жестких поперечен
Элементы мостов
Металлические гофрированные конструкции (МГК)
Автомобильные кузова и рамы
Строительные металлоконструкции и др.
Металлоконструкции проходят полный цикл подготовки, очистки, сушки поверхности. Мы даем гарантию на цинковое покрытие от 25 лет в сложных климатических и агрессивных условиях. При использовании оцинкованного материала в более типичных условиях (городская среда, сельская местность, легкая промышленность, внутри помещений) срок его службы до 50 лет и дольше, поэтому нам и доверяют горячее цинкование в Спб. Такой метод защиты метала от коррозии, не смотря на относительно высокую стоимость материала, является самым экономичным, т. к. на протяжении долгих лет эксплуатации оцинкованных металлоконструкций не нужно затрачивать средства на контроль за их состоянием и на поддержку антикоррозийного покрытия.
Технические требования, предъявляемые к стальным металлоизделиям
Особенности и требования к металлоконструкциям при горячем цинковании
Горячее цинкование металла в Липецке от завода «Спецтрансмонолит-Т»
Обработка горячим цинком (цинкование) – один из наиболее надежных и эффективных методов защиты металла от коррозии. Требования к процедуре закреплены в ТУ 25.61.11.111-010-00-194228-2016 и ГОСТ 9.307-89.
Если вам понадобилось горячее цинкование в Липецке, то обращайтесь к нам – на завод «Спецтрансмонолит-Т», а ниже мы расскажем подробнее о самом процессе и его преимуществах.
КАК ВЫПОЛНЯЕТСЯ ГОРЯЧЕЕ ЦИНКОВАНИЕ МЕТАЛЛА
Метод применим к крупногабаритным и мелким элементам, не имеющим полостей. Процесс включает следующие этапы:
-
очистка поверхностей от ржавчины, жира, масел, следов ЛКМ;
-
травление соляной кислотой;
-
флюсование для очистки от остатков оксидов;
-
сушка при температуре 100 °C до полного испарения воды;
-
цинкование металла погружением в расплав цинка;
-
финишная сушка в центрифуге.
ПРЕИМУЩЕСТВА МЕТОДА ГОРЯЧЕГО ЦИНКОВАНИЯ ИЗДЕЛИЙ
Непрерывное горячее цинкование возможно благодаря сравнительно низкой температуре плавления этого металла. Она составляет 419 °C, что намного ниже, чем у стали, железа и других черных металлов или их сплавов. Благодаря этому покрытию, показатели стойкости к коррозии возрастают в 5 раз. Свойства любого металла приближаются к характеристикам нержавейки.
Рассмотрим основные преимущества этого метода.
Универсальность. Цех горячего цинкования оснащен оборудованием, рассчитанным на конструкции размерами до 12,5×1,4×2,4 м и массой до 3000 кг. Возможна обработка крупногабаритных опор, кронштейнов, мелких деталей, труб, кузовов авто и многих других элементов без внутренних полостей. В отличие от холодного метода, цинкование горячим цинком позволяет охватить 100% поверхности, включая труднодоступные участки.
Долговечность. Горячее цинкование изделий обеспечивает антикоррозийную защиту на десятки лет. Точный срок службы покрытия зависит от особенностей климата и экологии. Например, если оцинкованная конструкция установлена в сельской местности, повторная обработка не потребуется в ближайшие 100 лет. Кроме того, слой этого металла способен к самовосстановлению без применения дополнительных средств при нагреве до 70 °C.
Прочность. Покрытие стойко к механическим воздействиям, появление сколов и трещин практически исключено. Заказать горячее цинкование – простой способ предотвратить повреждение заготовок при перевозке и монтаже.
Эстетика. Цинкование стали или любого другого металла позволяет сформировать гладкое однотонное покрытие серебристо-голубого оттенка. Защищенные им конструкции гармонично смотрятся в любом ландшафте. Кроме того, на металл легко ложится краска. Если вы заказали цинкование и купили защитную эмаль, антикоррозийные свойства покрытия сохранятся в 2 раза дольше.
Экономичность. Цинкование горячим способом формирует долговечное покрытие, способное к восстановлению. Оно требует обновления не чаще, чем раз в 20-70 лет, что существенно снижает расходы на обслуживание объекта.
Благодаря большой грузоподъемности оборудования и возможности обработки крупногабаритных конструкций, горячее цинкование металла завершается относительно быстро. Оно требует намного меньше времени, чем нанесение покрытия вручную.
В России горячее цинкование – один из самых востребованных методов защиты металлов от коррозии. «Спецтрансмонолит-Т» – ведущее предприятие этого направления. Услуги горячего цинкования здесь заказывали многие крупные компании, в том числе Opora Engineering, производитель мачт освещения для сочинской Олимпийской деревни.
Завод «Спецтрансмонолит-Т» находится в Туле, неподалеку от Москвы, горячее цинкование выполняется в современных цехах с несколькими производственными линиями. Даже если вы находитесь в Липецке, то вы можете заказать у нас услугу – мы готовы предложить компенсацию логистических издержек. Это обсуждается в индивидуальном порядке.
№ |
Цена на услуги горячего цинкования |
Цена за кг. |
1 |
Опора освещения |
от 22,5 р. |
2 |
Опора освещения граненная |
от 29 р. |
3 |
Пешеходные ограждения (толщина стенки 1,5-2мм) |
от 45 р. |
4 |
Стойка |
от 26 р. |
5 |
Металлоконструкции более 5 кг (толщина от 3 мм) |
от 26 р. |
6 |
Металлоконструкции менее 5 кг |
от 50 р. |
* не является публичной офертой
Указанные цены являются приблизительными и носят информационный характер.
Чтобы рассчитать, сколько стоит цинкование металла в Липецке, и уточнить условия сотрудничества, отправьте запрос на электронную почту [email protected], либо позвоните нам по телефону 8 (800) 707-90-12.
Hot Dipped Galvanized Steel Company
Защита от коррозии с помощью горячеоцинкованных стальных листов и рулонов от Alliance Steel.
Горячее цинкование — это процесс покрытия стали тонким слоем цинка, который служит барьером между сталью и окружающей средой. Отделка наносится путем пропускания стали через ванну с расплавленным цинком при высокой температуре.
Возможности обслуживания горячеоцинкованных стальных листов и рулонов Alliance Steel включают резку, резку, вырубку, обезжиривание и чистку щеткой, выравнивание носилок и металлургическую поддержку.
Применение для изделий из стали, оцинкованной погружением
Оцинкованная сталь хорошо подходит для применений, где требуются материалы, устойчивые к ржавчине по конкурентоспособной цене, защита от ультрафиолетового излучения и простая интеграция с другими материалами. Отрасли, в которых используются изделия из стали, оцинкованной горячим способом, включают:
- Автомобильная промышленность
- Трубы и трубки
- Отдых на свежем воздухе
- Сельское хозяйство
- Строительство
Горячеоцинкованный лист
Alliance Steel Возможности многократной заготовки:
Толщина материала: 0,015–0,135 дюйма
Макс. 15,00–74,00”
Ширина выхода: 5,00–74,00”
Длина: 6,00–144”
Ширина/длина Дол: +/-.010”
Ширина выхода: 4,00”–
Макс. вес рулона: 50 000 фунтов
Горячеоцинкованный рулон
Alliance Steel Возможности продольной резки:
Толщина материала: 0,010–0,500 дюйма
Мин. /макс. ширина щели: 0,375–84 дюйма
Мин./макс. внутренний диаметр: 20–30 дюймов
Макс. внешний диаметр: 84 дюйма
Ширина щели Допустимое отклонение: +/-.005″
Для получения дополнительной информации о листах и рулонах из горячеоцинкованной стали обращайтесь в Alliance Steel.
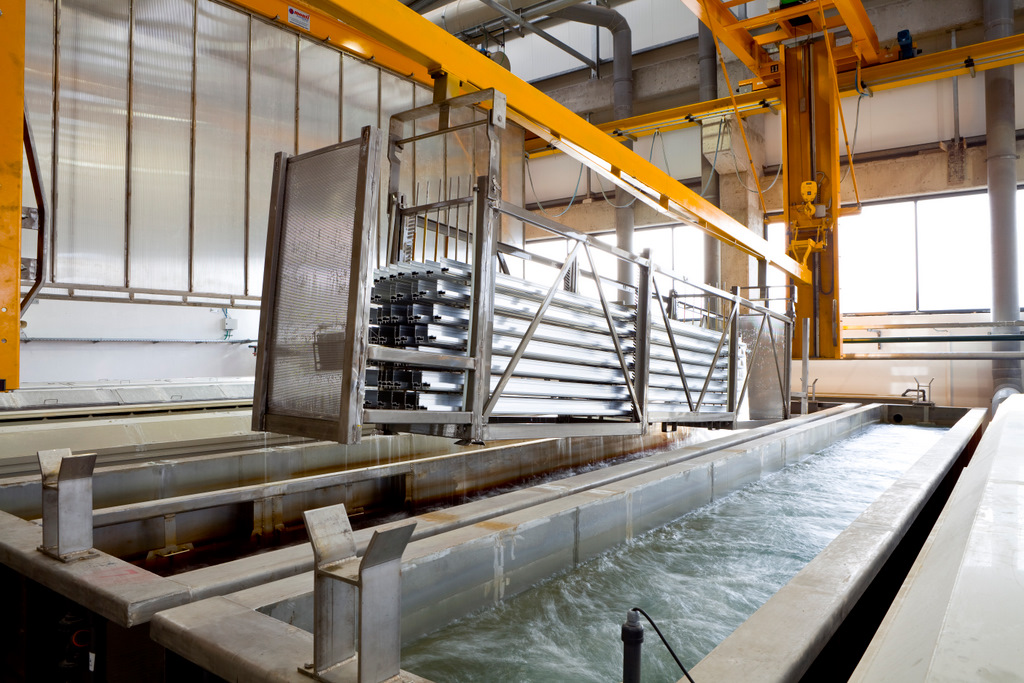
Классы HSLA | С | Мн | Р | С | Ал | Си | Медь | Ni | Кр | Пн | В | Кб | Ти | Н |
---|---|---|---|---|---|---|---|---|---|---|---|---|---|---|
45C1 | 0,22 | 1,35 | 0,04 | 0,04 | 0,2 | 0,2 | 0,15 | 0,06 | 0,005 | 0,005 | 0,005 | |||
45C2 | 0,15 | 1,35 | 0,04 | 0,04 | 0,2 | 0,2 | 0,15 | 0,06 | 0,005 | 0,005 | 0,005 | |||
50C1 | 0,23 | 1,35 | 0,04 | 0,04 | 0,2 | 0,2 | 0,15 | 0,06 | 0,005 | 0,005 | 0,005 | |||
50C2 и 55C2 | 0,15 | 1,35 | 0,04 | 0,04 | 0,2 | 0,2 | 0,15 | 0,06 | 0,005 | 0,005 | 0,005 | |||
55C1 | 0,25 | 1,35 | 0,04 | 0,04 | 0,2 | 0,2 | 0,15 | 0,06 | 0,005 | 0,005 | 0,005 | |||
60C1 и 65C1 | 0,26 | 1,5 | 0,04 | 0,04 | 0,2 | 0,2 | 0,15 | 0,06 | 0,005 | 0,005 | 0,005 | |||
60C2 и 65C2 | 0,15 | 1,5 | 0,04 | 0,04 | 0,2 | 0,2 | 0,15 | 0,06 | 0,005 | 0,005 | 0,005 | |||
70C1 | 0,26 | 1,65 | 0,04 | 0,04 | 0,2 | 0,2 | 0,15 | 0,16 | 0,005 | 0,005 | 0,005 | |||
70C2 | 0,15 | 1,65 | 0,04 | 0,04 | 0,2 | 0,2 | 0,15 | 0,16 | 0,005 | 0,005 | 0,005 |
Общие классы | С | Мн | Р | С | Ал | Си | Медь | Ni | Кр | Пн | В | Кб | Ти | Н |
---|---|---|---|---|---|---|---|---|---|---|---|---|---|---|
CSA | 0,1 | 0,6 | 0,03 | 0,035 | 0,2 | 0,2 | 0,15 | 0,06 | 0,008 | 0,008 | 0,025 | |||
ЦСБ | 0,02–0,15 | 0,6 | 0,03 | 0,035 | 0,2 | 0,2 | 0,15 | 0,06 | 0,008 | 0,008 | 0,025 | |||
CSC | 0,08 | 0,6 | 0,1 | 0,035 | 0,2 | 0,2 | 0,15 | 0,06 | 0,008 | 0,008 | 0,025 | |||
БН | 0,012 | 1,5 | 0,12 | 0,03 | 0,2 | 0,2 | 0,15 | 0,06 | 0,008 | 0,008 | 0,025 | |||
ФСА | 0,1 | 0,5 | 0,02 | 0,035 | 0,2 | 0,2 | 0,15 | 0,06 | 0,008 | 0,008 | 0,025 | |||
ФСБ | 0,02–0,15 | 0,5 | 0,02 | 0,03 | 0,2 | 0,2 | 0,15 | 0,06 | 0,008 | 0,008 | 0,025 | |||
ДДС | 0,06 | 0,5 | 0,02 | 0,025 | .![]() | 0,2 | 0,2 | 0,15 | 0,06 | 0,008 | 0,008 | 0,025 | ||
ЭДДС | 0,02 | 0,4 | 0,02 | 0,02 | .01* | 0,2 | 0,2 | 0,15 | 0,06 | 0,1 | 0,1 | 0,15 |
Как работает горячее цинкование — AZZ объясняет процесс цинкования
Горячее цинкование — это процесс, при котором сталь покрывается защитным слоем цинкового сплава для защиты от коррозии. Это не только относительно простой и экономичный процесс, но и получаемые в результате преимущества будут сохраняться десятилетиями.
Процесс Подготовка В первую очередь необходимо тщательно проверить саму сталь, чтобы убедиться, что выполнены требования по дренажу и вентиляции. Не годится иметь бракованный продукт с самого начала.
Перед началом процесса цинкования сталь необходимо как можно тщательнее очистить. Это не только для внешности. Цинковое покрытие просто не может сцепиться со стальной поверхностью, если присутствуют посторонние материалы. Очистка состоит из нескольких шагов:
- Сталь погружают в емкость с щелочью при температуре 180°F для удаления остатков краски. Затем его промывают в резервуаре с пресной водой при температуре окружающей среды для удаления едкого материала.
- Сталь протравливается погружением в емкость с нагретой серной кислотой при температуре 140–145 °F для удаления прокатной окалины. После этого его снова промывают в баке с пресной водой.
- Наконец, сталь промывают в ванне с флюсом, содержащей смесь хлорида цинка и хлорида аммония, при температуре 140–170 °F для обеспечения защиты от окисления перед цинкованием.
После выполнения этих шагов сталь готова к нанесению нового защитного покрытия.
Свежеочищенная сталь погружается в котел с расплавленным цинком при температуре 830–850°F. Затем цинк связывается со сталью в результате диффузионной реакции, создавая совершенно новый слой из металлургически связанного цинкового сплава. Прежде чем сталь с новым покрытием можно будет извлечь из резервуара, поверхность расплавленного цинка необходимо очистить, чтобы удалить все остатки, чтобы убедиться, что сталь выходит через чистый цинк.
ОхлаждениеСразу после извлечения из котла для цинкования сталь подвергается закалке в водном дихромате натрия при температуре окружающей среды, чтобы помочь ей остыть перед процессом окончательной очистки. Это также помогает оцинкованной стали сохранять свою блестящую поверхность в течение более длительного периода времени.
Окончательная очистка После оцинковки покрытая поверхность стали очищается от грязи, следов капель или излишков цинка, чтобы убедиться, что конечный продукт готов к испытаниям.
Затем сталь выносят наружу и размещают на опорах для испытаний на прокатку. Эти тесты подтверждают, что процесс прошел успешно и что цинковое покрытие имеет правильную толщину. Различные области применения стали могут потребовать различной толщины покрытия.
Другие ключевые аспекты горячего цинкования Защита от ржавчины посредством горячего цинкованияОсновная цель горячего цинкования погружением заключается в защите стали от ржавчины, естественного хищника стали. Одним из основных преимуществ покрытия из цинкового сплава, помимо высокой устойчивости к истиранию, является то, что цинк и ржавчина являются неотъемлемыми врагами. Ржавчина просто не может проесть цинк, следовательно, она не может проесть сталь под цинком. либо.
Долгая история горячего цинкования Цинкование металлов — это процесс, который мы используем уже более 150 лет. Первое известное использование было в 17 годах индийских доспехов, и этот процесс был промышленно внедрен для защиты железа на британских военно-морских кораблях. С тех пор он прижился практически во всех областях применения стали и железа в развитых странах.
Кристаллиты цинкового покрытия или зерна являются видимой особенностью оцинкованной стали. Эта особенность называется «блестками», и ее можно варьировать и регулировать по вкусу, изменяя количество частиц, добавляемых при гетерогенном зародышеобразовании, а также скорость охлаждения в процессе горячего цинкования. При желании блестки можно сделать однородными, а зернистость будет слишком мелкой, чтобы ее можно было увидеть невооруженным глазом.
Общие области применения горячего цинкования Горячее цинкование стали чаще всего используется в строительстве. Этот процесс обеспечивает защиту каркасов зданий, пешеходных дорожек, лестниц и многого другого в крупных городах по всему миру. Большинство из нас почти наверняка соприкасалось с горячеоцинкованной сталью, даже не подозревая об этом.
Оцинкованные трубы также широко используются в ирригации и других решениях для наружного хранения и транспортировки воды из-за их превосходной способности противостоять коррозионным силам элементов и устойчивости к ржавчине.
Экономическая эффективность горячего цинкованияГорячее цинкование популярно среди фермеров, инженеров, архитекторов и других специалистов благодаря своим защитным свойствам, но оно также обеспечивает другие экономические преимущества.
Благодаря своей долговечности и ударной вязкости горячеоцинкованная сталь требует меньше обслуживания, и ее ремонт или замена могут длиться десятилетиями. Устойчивость к истиранию также способствует получению более гладких поверхностей, которые легче очищать и окрашивать.
Обзор последних разработок в области систем покрытий для горячеоцинкованной стали
Введение
Коррозия стали неизбежна как в производстве, так и в повседневной жизни. Общие экономические потери, вызванные коррозией, оцениваются в более чем 3% ВВП в каждой стране ежегодно (Koch et al., 2002). Соответственно, жизненно необходимо проводить защиту стали покрытием. На сегодняшний день цинк и его сплавы обеспечивают наиболее эффективную защиту стали от коррозии (Маэда, 1996; Крылова, 2001). Гальванический слой в первую очередь служит барьерным покрытием для защиты от агрессивных сред, таких как Cl 9.0828 – ионов от проникновения в матрицу стали. Это накопление продуктов коррозии цинка еще больше усилит барьерное действие гальванического слоя. Кроме того, гальванический слой может выступать в качестве расходуемого анода, который преимущественно подвергается коррозии цинка по сравнению со сталью (Maaß et al., 2011; Schulz and Thiele, 2012). Однако вышеупомянутый HDGS имеет определенные недостатки, такие как относительно неадекватные характеристики защиты для работы во все более суровых природных условиях. В качестве альтернативы была предложена новая стратегия, включающая комбинацию слоя предварительной обработки и органического покрытия, называемая дуплексными покрытиями (Dallin et al.
, 2018; Svoboda et al., 2018). Поэтому поиск новых дуплексных покрытий стал актуальной задачей.
Как правило, слой предварительной обработки представляет собой хроматное или фосфатное покрытие, что неблагоприятно для окружающей среды. Следовательно, возрос интерес к разработке и совершенствованию «зеленой» технологии предварительной обработки (Van Schaftinghen et al., 2004). Новые слои предварительной обработки, такие как силановая пленка (Van Ooij et al., 2000), конверсионная пленка из редкоземельных элементов (Tianlan and Ruilin, 2009), проводящий полимер (Le et al., 2001) и самособирающаяся пленка (Yamamoto et al., 2009). al., 1993) и др., переживали бум в последние годы. Чтобы полностью реализовать потенциал этих новых технологий, необходимо точно выбрать подходящий слой предварительной обработки и оценить его особые физико-химические свойства и синергетические электрохимические параметры. Тем не менее, имеется мало литературы, оценивающей срок службы дуплексных покрытий. Основываясь на вышеупомянутых фактах, мы хотели бы обобщить обзор недавних исследований HDGS по следующим трем аспектам: (1) антикоррозионный контроль цинковых покрытий для соответствия требованиям HDGS, (2) новые и современные дуплексные покрытия. для HDGS, (3) оценка срока службы вышеупомянутых систем покрытия. Наконец, были предложены будущие разработки систем покрытий.
Антикоррозийный контроль цинковых покрытий в соответствии с требованиями HDGS
Цинк является амфотерным металлом. Имеется большое количество исследовательских статей о механизме коррозии цинка в нейтральном растворе (Cachet et al., 2001, 2002; Dafydd et al., 2005). Принято считать, что цинк в процессе коррозии трансформируется двумя-тремя промежуточными веществами. Каше и др. (2001) использовали EIS для изучения процесса коррозии цинка в аэрированном растворе сульфата и обнаружили, что индуктивное сопротивление на низкочастотном хвосте появляется в спектрах импеданса. Они полагали, что это связано с трансформацией трех адсорбированных частиц, образующихся в процессе коррозии цинка, а именно Zn+ ад, Zn2+ ад и ZnOH ад. Zn сначала теряет электрон и становится Zn+ ad. Затем Zn проходит следующие три пути превращения:
Путь2:Zn+Znad+→Znsol2++Znad++2e-
Путь3:Znad+→Znsol2++e→-Znsol2+
Path4:2Zn+2HO2→2Znsol2++2ZnOHad+h3ZnOHad→ZnOHsol2++e-
Keddam et al. (1992) обнаружили, что основными продуктами коррозии цинка в средах с высоким содержанием хлора являются основной хлорид цинка, основной карбонат цинка и оксид цинка. На воздухе и хлориде натрия в существующих нейтральных условиях коррозионная реакция цинка:
Zn→Zn+2-2e-
O+22HO2+4e→-4Oh3-
2Zn+O+22HO2→2Zn(OH)2
По мере развития коррозии в анодной области также будут протекать следующие коррозионные реакции.
5Zn+2Cl+-8HO2→Zn(OH)5Cl2+28H+
Zn+2+2Cl→-ZnCl2
4Zn(OH)+2ZnCl→2Zn(OH)5Cl82
В нейтральной или щелочной среде основной хлорид цинка будет осаждаться на поверхности подложек для защиты матрицы от коррозии, но в кислой среде он легко растворяется. Следовательно, основной хлорид цинка может быть легко смыт дождем при воздействии окружающей среды. Это является причиной точечной коррозии цинка (Cachet et al., 2002). Другая причина питтинга цинка в присутствии Cl – – градиент pH. Коул и др. (2010) исследовали продукты коррозии капель морской воды, взаимодействующих с цинком после кратковременного воздействия. Было обнаружено, что оксидный слой постепенно утолщается и начинает существенно препятствовать диффузии ионов, что приводит к локальному закислению в прианодной области. Это также могло вызвать питтинг в месте локального дефекта закисления, которое произошло по границам зерен.
Углекислый газ является еще одним ключевым фактором, влияющим на коррозию цинка. За исключением гидроксида цинка, карбонат цинка является наиболее распространенным продуктом коррозии цинка. Основными формами карбоната цинка являются ZnCO 3 и Zn 5 (CO 3 ) 2 (OH) 6 (Chen et al., 2006; Persson et al., 2007). Коррозионные реакции:
ZnO+CO→2ZnCO3
Zn(OH)+2CO→2ZnCO+3HO2
3Zn(OH)+22ZnCO→3Zn(CO)35(OH)26
Основной карбонат цинка будет прикреплен к поверхности подложек, чтобы предотвратить диффузию ионов и снизить скорость коррозии подложек. Было обнаружено, что скорость коррозии цинка будет увеличиваться с увеличением концентрации СО 2 (Фальк и др. , 1998). Кроме того, большое количество SO 2 , NO x, и других загрязняющих веществ в промышленных условиях также значительно повлияет на коррозию цинка. SO 2 является основным источником кислотных дождей и склонен вызывать равномерную коррозию цинка. В среде, где SO 2 сосуществует с NaCl, между ними возникнет синергетический эффект, который приведет к сильной коррозии цинка (Qu et al., 2002).
Кроме того, тщательно исследовался механизм коррозии цинка в сильнощелочной среде, особенно в железобетоне. В начальный период эксплуатации поры бетона в основном насыщены раствором гидроксида кальция. Когда значение pH составляет 12~14 (Yeomans, 2004), оцинкованный слой в основном находится в пассивированном состоянии. Среди факторов, приводящих к коррозии арматуры ГДС, CaCO 3 образуются в результате реакции нейтрализации CO 2 в воздухе с Ca(OH) 2 в поровой жидкости бетона и Cl – оказывают наиболее серьезное воздействие (Al-Mehthel et al. , 2009 ; Манна, 2009). Бетон HDGS находится в пассивированном состоянии в насыщенном растворе Ca(OH) 2 с pH 12~13. Плотность тока коррозии I корр близка к критическому значению пассивации. Когда рН превышал 13,5, плотность тока коррозии составляла I корр будет быстро увеличиваться из-за отсутствия защитной пленки. Когда pH меньше девяти, гальваническая пленка может непосредственно вызвать реакцию выделения водорода и, таким образом, повредить структуру покрытия.
Когда Cl – попадает в бетонную среду, он разрушает первичную пленку продуктов коррозии (состоит из цинката кальция), покрывающую оцинкованный слой, заставляя оцинкованный слой снова войти в состояние активации. При концентрации Cl – меньше критического значения (0,4~0,5 моль/л), пассивирующая пленка будет слегка изъедена Cl – в локальной области цинката кальция со слабой защитой, и может образоваться другой продукт коррозии – основной хлорид цинка. в местных микрорайонах. В плотной области, покрытой цинкатом кальция, питтинга Cl – не произойдет. Локальный непрерывный основной хлорид цинка, образованный точечной коррозией, вместе с плотным цинкатом кальция на большой площади все еще может обеспечить лучшую защиту оцинкованного слоя. При концентрации Cl – больше или равно критическому значению, степень коррозии оцинкованного слоя увеличится, а проникновение Cl – в пассивирующую пленку изменится с точечной коррозии на местную коррозию. При увеличении концентрации Cl – в области, где защита цинката кальция была относительно слабой, образовывалось большое количество рыхло отложившегося основного хлорида цинка. Основной хлорид цинка не был прочно связан с поверхностью оцинкованного слоя и легко отрывался. кл – будут непрерывно проникать в дно цинката кальция из сарая и постепенно разрушать плотную мембранную структуру цинката кальция, чтобы увеличить коррозию оцинкованного слоя и разрушить основной металл (Yeomans, 2004).
В настоящее время используется относительно зрелая технология горячего цинкования для HDGS, которая может конкурировать с холодным цинкованием и термическим напылением цинка, что имеет огромные преимущества перед последним. Например, преимущества горячего цинкования заключаются в более низких затратах на обработку, комплексной защите, меньших затратах труда и времени, а также большей долговечности и надежности (Шульц и Тиле, 2012 г.). Существуют различные факторы, влияющие на свойства цинковых покрытий, такие как тип стали, подготовка поверхности стали перед цинкованием, легирующие добавки цинковых ванн, температура и продолжительность процесса цинкования, а также методы последующего охлаждения цинкования (Chen et al. , 1992; Штрутценбергер и Фадерл, 1998 г.; Сере и др., 1999; Моримото и др., 2002; Сафаирад и др., 2008 г.; Цай и др., 2010). Следовательно, существуют также определенные проблемы, связанные с требованиями к процессу горячего цинкования, применяемому для HDGS. Эти задачи включают в себя: поиск подходящих легирующих элементов для повышения коррозионной стойкости покрытий, достижение экологически безопасного процесса цинкования и обеспечение превосходной адгезии с более однородным покрытием. Таким образом, открытие оптимального процесса горячего цинкования будет применяться для защиты стали от коррозии. Эта актуальная тема откроет новые пути для исследовательского сотрудничества между областями металлургии и материаловедения.
Кроме того, с целью лучшего контроля коррозии нового процесса горячего цинкования следует принять во внимание следующие аспекты, чтобы найти более подходящий процесс горячего цинкования для HDGS. Как показано на Рисунке 1, общая стратегия контроля коррозии для согласования процесса горячего цинкования с HDGS должна охватывать следующие вопросы: (1) оптимальный выбор подходящей матричной стали, (2) соответствующую модификацию состава сплава в цинке. ванна, (3) подходящая температура и время горячего цинкования, (4) принятие процесса пассивации. Во-первых, следует точно выбрать подходящую матричную сталь. Предполагаемое гальваническое покрытие после иммерсионного цинкования может быть реализовано при взаимодействии с соответствующим типом стали. Фактически, на микроструктуру и механические свойства приготовленных гальванизированных покрытий существенное влияние оказывает химический состав матричной стали (Бреваль и Рахлиц, 19).88; Лин, 1999; Вурлиас и др., 2004 г.; Винсент и др., 2006 г.; Маас и др., 2011; Шульц и Тиле, 2012 г.; Каниа и Либерски, 2014 г.; Покорный и др., 2016). Содержание углерода и кремния в матрице играло определяющую роль в свойствах покрытия, в то время как составляющая марганца, фосфора и серы относительно слабо на них влияла. Например, разные формы углеродного элемента по-разному влияют на реакцию между Fe и Zn. Когда углерод находится в форме сферического перлита и пластинчатого перлита, он ускоряет реакцию Fe-Zn. Однако на скорость реакции Fe-Zn это не повлияет, поскольку элемент C существует в виде отпущенного мартенсита или графита. Кроме того, чем выше содержание элемента С, тем быстрее протекает реакция Fe-Zn. Ускорение реакции Fe-Zn приведет к снижению механических свойств гальванического покрытия.
Поэтому в качестве матричной стали часто выбирают низкоуглеродистые стали. Более того, присутствие элемента Si может ускорить скорость растворения Fe в цинковой ванне. Сталь с низким содержанием Si могла получить более плотное стойкое покрытие после процесса цинкования. Более высокое содержание элемента Si в стали будет приводить к эффекту Санделина, заставляя ζ-фазу (хрупкую фазу) интенсивно расти и образовывать серое покрытие с плохой адгезией, что существенно повлияет на внешний вид, микроструктуру и свойства гальванического покрытия. То есть исследование подходящего химического состава стали будет первым шагом в управлении процессом горячего цинкования. Во-вторых, изменение состава сплава в цинковой ванне для заданной матричной стали играет существенную роль в оптимизации процесса цинкования (Fasoyinu and Weinberg, 19).90; Павлиду и др., 2005; Асгари и др., 2007 г.; Пистофидис и др., 2007; Кулкаси и др., 2009). В частности, температура плавления, вязкость и поверхностное натяжение цинковой ванны могут быть изменены некоторыми определенными легирующими элементами, так что толщина покрытия, блеск поверхности и механическая прочность HDGS могут быть настроены в лучшую сторону.
Следовательно, изменение состава сплава путем введения различных легирующих элементов, таких как Al, Mg или Ni, может повысить коррозионную стойкость гальванического покрытия. Кроме того, добавление редкоземельных элементов или Sb также может улучшить текучесть цинковой ванны и уменьшить степень адгезии цинка на поверхности HDGS. Sb имеет относительно плохую растворимость в цинковой ванне, которая будет осаждаться в виде Sb 3 Zn 4 . Таким образом, будут образовываться гальванические элементы Sb 3 Zn 4 /Zn. Адгезивное покрытие наносится с добавлением Sb через барьер и гальваническую защиту (Peng et al., 2020). В-третьих, подходящая температура и время для горячего цинкования являются еще одним ключевым фактором для оптимизации или регулирования свежеподготовленного цинкового покрытия для улучшения процесса горячего цинкования (Fasoyinu and Weinberg, 1990; Asgari et al., 2007; Culcasi et al.). др., 2009). Если температура цинковой ванны слишком высока или слишком низка, это отрицательно скажется на свойствах покрытия.
Что касается времени горячего цинкования, то необходимо сократить время погружения из соображений обеспечения определенной толщины покрытия, что могло бы уменьшить толщину ζ-фазы и повысить пластичность цинкового покрытия. В-четвертых, эффективный процесс пассивации также полезен для оптимизации гальванического покрытия. Технология хроматной пассивации, благодаря простоте процесса, низкой стоимости и хорошей адгезии пленки, является классическим процессом, обычно используемым для повышения коррозионной стойкости HDGS (Van Schaftinghen et al., 2004). К сожалению, хроматное покрытие очень канцерогенно и токсично. Поэтому из соображений безопасности и защиты окружающей среды в последние годы также были разработаны некоторые малотоксичные или нетоксичные методы лечения. Оптимальное гальваническое покрытие, полученное в результате такой хроматной пассивации, обогащает большое семейство процессов горячего цинкования и удовлетворяет различным требованиям, предъявляемым к HDGS.
Рисунок 1. Предлагаемые стратегии борьбы с коррозией для согласования процесса горячего цинкования с HDGS; ключевые факторы включают в себя выбор подходящей матричной стали, модификацию состава сплава в ванне с цинком, соответствующую температуру и время горячего цинкования, а также разработку процесса пассивации.
Появляющиеся и современные дуплексные покрытия для HDGS
Появляющиеся и современные системы защиты покрытий обычно изготавливаются из соответствующей матричной стали с дуплексными покрытиями, обычно состоящими из металлического цинкового покрытия с слой предварительной обработки, за которым следует органическое покрытие. К настоящему времени было обнаружено, модифицировано или усовершенствовано множество новых и перспективных дуплексных покрытий, которые подтвердили их применимость в отношении коррозионной стойкости HDGS. В свете форм слоев предварительной обработки эти дуплексные покрытия покрывают силановые пленки (Субраманиан и Ван Оой, 19).98; Ван Оой и Чайлд, 1998; Ван Оой и др. , 2000; van Ooij and Zhu, 2001), редкоземельные конверсионные пленки, проводящие полимеры и самособирающиеся пленки. Многие новые дуплексные покрытия были успешно изобретены путем проведения различных предварительных обработок матрицы HDGS. В таблице 1 перечислены четыре типа типичных систем дуплексного покрытия для HDGS. Поэтому мы суммируем эти вышеупомянутые новые и современные дуплексные покрытия в соответствии с категорией технологий их предварительной обработки.
Таблица 1. Типичные дуплексные покрытия, наносимые на HDGS.
Силановые пленки
Самой известной силановой пленкой, без сомнения, является бис-1,2-[триэтоксисилил]этан (BTSE) с функциональным силаном, таким как γ-уреидопропилтриэтоксисилан (γ-UPS) или γ-аминопропилтриэтоксисилан (γ-APS) (Ван Оой и др., 2000). Стабильные ковалентные связи между металлическим субстратом и силанами могут быть образованы за счет дегидратации водородных связей. Кроме того, функциональные силаны могут улучшить целостность формируемой пленки. Таким образом, компактная силановая пленка может обеспечить высокоэффективную барьерную защиту (Chang et al., 2019).). На рис. 2 показан состав системы покрытия после типичного процесса пленкообразования BTSE. Как показано на фиг. 2, сначала формируется тонкий конверсионный силикатный слой, состоящий из [Me-O] × [SiO 3 X] y . Впоследствии образуется слой конденсированного силана. После этого между конденсированным силаном и сшитой органикой образуется взаимопроникающее покрытие. Многочисленные микроячейки будут образовываться на границе раздела раствор/субстрат, когда HDGS погружают в раствор силана. Микроанодная и микрокатодная реакции, соответственно, представляли собой растворение цинка и восстановление кислорода, что могло привести к локальному повышению рН в микрокатодной области. При дальнейшем усилении микроэлектрохимической реакции гидроксиды цинка будут генерироваться и осаждаться на поверхности раздела раствор/подложка. Синхронно, водородные связи между группами Si-OH, происходящие из раствора и гидроксидов цинка, будут образовываться через гидролизованные силаны.
Более того, силаны могут взаимодействовать друг с другом посредством водородных связей. После процесса отверждения группы Zn-OH и Si-OH будут дополнительно конденсироваться с образованием связей Zn-O-Si. Кроме того, группы Si-OH также будут сшиваться с образованием ковалентных связей Si-O-Si (Li et al., 2020). Предпосылками для ее формирования являются совместимости смачиваемости границы раздела и поверхностной энергии. Не все функциональные группы могут улучшить совместимость, поэтому выбор подходящих и эффективных функциональных групп становится трудностью, которую необходимо срочно преодолеть. Чем сильнее совместимость, тем сильнее адгезия между силаном и органикой. Таким образом, окончательная система покрытия сильно предотвратит проникновение воды и коррозионно-активных ионов в металл в результате образования прочной гидрофобной поверхности раздела между конденсированным силаном и органикой. Однако комбинация BTSE и функциональных силанов не является универсальной для различных металлов (Van Schaftinghen et al.
, 2004; Zhu and van Ooij, 2004). Почти для каждого металла требуется очень специфический силановый компонент для удовлетворения потребностей в ингибировании коррозии. Следовательно, более универсальная силановая композиция, не чувствительная к металлу подложки, могла бы иметь большие перспективы применения.
Рис. 2. Схематическое изображение границы раздела полимер/металл после процесса формирования пленки.
Высокоприемлемая силановая смесь бис-1,2-[триметоксисилилпропил]амина (BTSPA) и бис-1,2-[триэтоксисилилпропил]тетрасульфида (BTSPS) представляет собой еще один модифицированный вид силанов, о котором впервые сообщили Zhu и van Ooij (2004). Его можно использовать для эффективной защиты различных видов металлов (таких как нержавеющая сталь, HDGS, электрооцинкованная сталь, алюминиевый сплав и медь), компенсируя недостатки комбинации BTSE и функциональных силанов. Кроме того, пропорция BTSPA и BTSPS может быть изменена произвольно, а силановая смесь может быть гидролизована или не гидролизована перед нанесением. Разнообразные органические покрытия, такие как эпоксидные смолы, полиуретан, полиэстер и т. д., могут быть прочно связаны со смешанными силановыми пленками, что еще больше повысит коррозионную стойкость системы покрытия. Кроме того, их группа также подготовила силановые пленки, легированные различными наночастицами, с целью улучшения адгезии и антикоррозионных свойств (Паланивел и др., 2003).
В средах с высоким содержанием щелочи силановые пленки для предварительной обработки HDGS также находят широкое применение, особенно в области производства цемента. На поверхности ГДГС в диапазоне рН 6–13 образуется устойчивая защитная пленка, что может снизить скорость коррозии цинка. За исключением указанного выше диапазона рН, образовавшиеся защитные пленки разрушались, а цинк подвергался коррозии (Roetheli et al., 1932). Фигейра и др. (2013; 2014; 2015; 2016) исследовали композиционные органо-неорганические покрытия на основе неорганических силанов, дополненных пятью различными органическими олигомерами в растворе или растворе, имитирующем поры бетона. Двумя типичными типами систем покрытия были аминоспиртовые силикаты (А(Х)) и уреасиликаты (U(Х)). Методы покрытия погружением также применялись для легкого осаждения этих функциональных пленок на HDGS. По результатам электрохимических измерений силановые пленки на основе U(X) и олигомеров показали более высокую коррозионную стойкость, чем на основе A(X) и олигомеров. Кроме того, молекулярная масса олигомеров оказала большое влияние на коррозионную стойкость HDGS с покрытием. В принципе, пленка будет более шероховатой с увеличением молекулярной массы олигомеров. Следовательно, чем больше молекулярная масса, тем меньше защитные свойства пленок. Они также исследовали влияние технологии погружения на барьерную защиту подготовленных покрытий. Метод погружения с одной, двумя или тремя стадиями, по-видимому, не дает значительного улучшения коррозионной стойкости. Следует отметить, что вышеупомянутые силановые пленки могут быть легко и просто получены путем погружения металлической подложки в свежеприготовленный раствор предшественников силана на определенное время, и этот метод можно назвать приготовлением покрытия погружением.
Недостатком этих свежеприготовленных пленок является их относительная неоднородность, что может оказывать побочное влияние на коррозионную стойкость покрытия.
С целью дальнейшего улучшения коррозионно-ингибирующих свойств вышеупомянутых силановых пленок в процесс получения этих органосилановых пленок внедряется технология электрохимического осаждения (Woo et al., 1993; Shacham et al., 1999; Sheffer et al., 2003; Ганди и ван Оой, 2004). Группа Ху провела многочисленные исследования по этому аспекту (Hu et al., 2006, 2007; Li et al., 2010; Jiang et al., 2015; Liu et al., 2017; Xu et al., 2018). Во-первых, силановые пленки были успешно электроосаждены в растворах BTSE при различных потенциалах осаждения на сплавах AA 2024-T3 (Hu et al., 2006). Пленки силана показали улучшение свойств коррозионной стойкости при осаждении при катодных потенциалах, и, наоборот, он будет оказывать отрицательное влияние на защиту от коррозии для подготовленных пленок при анодных потенциалах. Как показано на рисунке 3, антикоррозионные способности электроосажденных силановых покрытий сначала улучшаются, а затем снижаются по мере того, как приложенные катодные потенциалы постепенно отклоняются от потенциала холостого хода, а оптимальный катодный потенциал составляет -0,8 В/SCE.
Рис. 3. Сложная плоскость сплавов AA 2024-T3 без покрытия (7) и с покрытием BTSE. Пленки силана осаждаются при ОКФ В/СКЭ (4), –0,2 В/СКЭ (6), –0,4 В/СКЭ (5), –0,6 В/СКЭ (3), –0,8 В/СКЭ (2), и –1,0 В/SCE (1) (Hu et al., 2006).
Во-вторых, в условиях электроосаждения силановых покрытий предпринимаются попытки легирования в силановые пленки различными технологиями легирования (Li et al., 2010). Они обнаружили, что легированные наночастицы, такие как SiO 2 и TiO 2 могут заполнить дефект электроосажденных силановых пленок. Кроме того, композит редкоземельных ионов и электроосажденных силановых пленок придает полученной пленке свойство самовосстановления (Желюдкевич и др., 2005). Совместное электроосаждение активного металла и органического силана может обеспечить дополнительную катодную защиту для приготовленных силановых пленок. Все эти технологии легирования могут улучшить антикоррозионные характеристики силановых пленок (Ferreira et al. , 2004; Cabral et al., 2006; Montemor and Ferreira, 2007). Как показано выше, все силановые пленки являются органическими. Сила связывания органосилановой пленки с покрытием высокоизбирательна и не подходит для различных видов защитных органических покрытий. Кроме того, в органосилановой пленке отсутствует шероховатая и пористая структура поверхности, что может повлиять на адгезию к органическим краскам или покрытиям, а также на количество и качество загрузки ингибиторов коррозии. Таким образом, вновь возникающие электроосаждения неорганического SiO 9Возникает пленка 0894 2 (Hu et al., 2006). Толщина пленки электроосаждения SiO 2 может достигать 10 мкм, и эти пленки демонстрируют отличную адгезию и высокую микроскопическую шероховатость, что благоприятно для связывания с органическими покрытиями и нанесения ингибиторов коррозии (Liu et al., 2017). Система композитного покрытия, содержащая пленку E-SiO 2 , загруженную ингибиторами коррозии, была успешно синтезирована, как показано на рис.
4. Приготовленные образцы по-прежнему имеют чрезвычайно высокий модуль импеданса (более 10 11 Ом · см 2 , при 0,01 Гц), даже при погружении в раствор NaCl с концентрацией 3,5% масс. почти на 1 год, превосходит почти все высокоэффективные дуплексные покрытия, о которых сообщалось в литературе до сих пор. Это показывает, что эта новая система дуплексного покрытия, использующая пленку e-SiO 2 как в качестве слоя предварительной обработки, так и в качестве контейнера с ингибиторами коррозии, должна иметь большие перспективы применения в области защиты от коррозии HDGS.
Рис. 4. Принципиальная схема системы композиционного покрытия с покрытием из сплавов AA 2024-T3.
Вкратце, системы покрытий, содержащие силановую промежуточную прослойку, представленную BTSE, продемонстрировали огромный потенциал и использовались для защиты от коррозии алюминиевых сплавов. Однако относительно плохая совместимость и адгезионные свойства приготовленных силановых пленок ограничивают их дальнейшее применение, особенно в различных стальных материалах. Поэтому по-прежнему необходимы некоторые новые силановые средства предварительной обработки с улучшенными антикоррозионными свойствами, такие как появляющийся электроосажденный органосилан и неорганический SiO 9 .Пленка 0894 2 , описанная выше, при нанесении силановой пленки на HDGS.
Редкоземельные конверсионные пленки
Редкоземельные конверсионные пленки также играют важную роль в технологическом дизайне новых средств предварительной обработки для защиты HDGS от коррозии. В частности, конверсионные пленки редкоземельных элементов, образованные солями церия и их модификациями, вызывают большой интерес в связи с их потенциальными применениями (Rudd et al., 2000; Xingwen et al., 2001; Ferreira et al., 2004; Lu et al. и др., 2006 г.; Монтемор и др., 2008 г.; Тяньлан и Жуйлинь, 2009 г.; Дэн и др., 2010 г.; Яньхуа и др., 2013 г.; Маджд и др., 2019). В качестве основного компонента конверсионной пленки редкоземельных элементов редкоземельные ионы могут включать относительно сложные составы пленок, которые обычно содержат широкий спектр отрицательных ионов за счет различной предварительной обработки поверхности металлической подложки, PH в растворе, времени погружения, концентрации редкоземельных элементов. ионы земли в растворе и температура осаждения (Brachetti-Sibaja et al., 2011). Общепризнано, что редкоземельные элементы могут действовать как ингибиторы коррозии, ингибируя катодные реакции (Karaxi et al., 2019).). Среди этих редкоземельных конверсионных пленок широко распространены пленки, содержащие ионы церия или лантана, и их антикоррозионные свойства и применение в качестве слоев предварительной обработки широко исследовались (Aldykewicz et al., 1995; ?; Wang et al., 2004; Kumar et al. др., 2012). На рисунке 5 представлена схема кинетики формирования пленки на основе церия (Sun et al., 2019; Li et al., 2020). Процесс образования конверсионной пленки редкоземельных элементов обычно можно разделить на три стадии в соответствии с процессами электрохимических реакций с разным временем погружения. Первую стадию можно назвать стадией инициирования пленки редкоземельных элементов, при которой поверхность металла начинает растворяться и вокруг поверхности металла появляются коррозионные язвы, сопровождающиеся осаждением гидроксида церия.
Как правило, растворение металла происходит в прианодной области (реакция 1: Me → Me 2– + 2e – ). В то же время кислород начинает восстанавливаться в катодной области (реакция 2: 2H 2 O + O 2 + 4e – → 4OH – ). Осаждение Ce(OH)n ( n = 3, 4) и гидроксида металла начинают проявляться упорядоченно по мере увеличения рН в области микрокатода. Следует отметить, что для окисления Ce 3+ в Ce 4+ необходим pH более 8,7. Однако прямое окисление Ce 3+ на CeO 2 невозможно. Кроме того, присутствие H 2 O 2 может способствовать процессу окисления, ускоряя образование гидроксидов и оксидов Ce (Karaxi et al., 2019). Вторая стадия может быть известна как стадия формирования пленки редкоземельных элементов и стадия зарождения трещины, при которой растворение металла продолжается наряду с осаждением гидроксида церия. Как следствие, толщина этих конверсионных пленок продолжает увеличиваться.
Кроме того, частичный гидроксид этих осадков мог дегидратироваться в соответствующие оксиды на воздухе, и на пленке могло появиться небольшое количество трещин. Третью стадию можно назвать стадией развития трещины, когда пассивирующая пленка редкоземельных элементов становится толще, а трещины становятся глубже и шире, частичная область пленки может постепенно отваливаться и отделяться.
Рисунок 5. Схематическая диаграмма процесса роста конверсионного покрытия на основе лантана.
С тех пор, как Хинтон и Уилсон (1989) впервые представили предварительную обработку на основе солей редкоземельных элементов для защиты металлов от коррозии в 1989 году, за последние десятилетия были проведены многочисленные исследования конверсионных пленок редкоземельных металлов. Они обнаружили, что оксид или гидроксид церия могут быть очень эффективными в сдерживании скорости коррозии цинка посредством подавления катодной реакции. Арамаки (2001a, b, 2005) также исследовал механизм ингибирования коррозии солями церия, нанесенными на цинк. Образование каркасной сетки полуторного оксида церия на поверхности цинка может быть причиной ингибирования катодных реакций. Радд и др. (2000) исследовали различные предварительные обработки солями редкоземельных элементов для предотвращения коррозионного воздействия магния и его сплавов. Они обнаружили, что эти подложки при обработке солями лантана, церия или празеодима будут иметь улучшенную коррозионную стойкость по сравнению с необработанными образцами, что можно объяснить соосаждением покрытий из гидроксила/оксида редкоземельных элементов и смешанного гидроксила/оксида магния. товары. Брачетти-Сибаха и др. (2011) изучали влияние условий ванны при обработке церием и лантаном на эффективность защиты от коррозии сплава AA6061. Повышение антикоррозионных свойств алюминиевого сплава АА6061 предположительно связано с улучшенными барьерными характеристиками редкоземельного конверсионного слоя. Лу и др. (2006) исследовали оптимальную технологию обработки, регулируя и контролируя время погружения горячеоцинкованной стали (HDGS) в раствор соли церия.
С увеличением времени погружения антикоррозионные свойства редкоземельной конверсионной пленки сначала усиливаются в течение 1 ч за счет большей толщины покрытия при ней, а затем через 1 ч ослабевают из-за появления трещин и отслоения пленки. покрытие.
Как видно из вышеизложенного, конверсионные пленки на основе редкоземельных элементов обладают огромным потенциалом в использовании различных видов защиты металлов перед предварительной обработкой. В последнее время, чтобы справиться с ухудшающейся природной средой, было обнаружено много новых конверсионных пленок редкоземельных элементов. Например, двухэтапная обработка триметокси(вини)силансом и солью лантана используется для защиты от коррозии оцинкованной стали (Tianlan and Ruilin, 2009). Этот двухэтапный метод обеспечивает превосходную адгезию краски и более эффективные антикоррозионные свойства, чем Cr 9.0828 6+ только предварительная обработка. Для алюминиевого сплава используются дуплексные конверсионные пленки редкоземельных элементов (Xingwen et al. , 2000) для повышения коррозионной стойкости сплава LY12. Последствия поляризации показывают, что коррозионная стойкость дуплексных конверсионных пленок выше, чем у хроматных конверсионных покрытий. Кроме того, коррозионная стойкость конверсионной пленки, содержащей соединения церия, на алюминиевом сплаве (Zhang and Zuo, 2008) также может быть улучшена с помощью процесса последующей обработки. Улучшение может объясняться тем, что последующая обработка устранит микротрещины на поверхности пленки. Что касается стали, Yanhua et al. (2013) изучали комбинацию солей редкоземельных элементов и молибдата натрия для получения составных ингибиторов, содержащих редкоземельные элементы и молибден, для стали Х70. Синергетический эффект между молибдатом натрия и редкоземельным элементом был значительным в ингибировании коррозии стали X70, и наилучшее молярное соотношение иона редкоземельного элемента к иону молибдена составляло 1:1.
В целом конверсионные пленки редкоземельных элементов, классически представленные покрытием из оксида/гидроксида церия, показали большой потенциал и применяются для практической защиты металлических поверхностей. Тем не менее относительно слабая коррозионная стойкость конверсионных пленок редкоземельных элементов по сравнению с хроматными конверсионными пленками ограничивает их дальнейшее применение, в частности, в морских и промышленных условиях. Здесь по-прежнему необходимы новые и эффективные способы обработки редкоземельных конверсионных пленок с улучшенной коррозионной стойкостью, такие как широко распространенная двухэтапная обработка и дуплексные конверсионные пленки редкоземельных элементов, представленные выше.
Проводящие полимеры
Проводящие полимеры, представленные покрытиями из полипиррола (PPy) (Tallman et al., 1999, 2002; Le et al., 2001; Spinks et al., 2002; Shinde et al., 2006), имеют историю использование в борьбе с коррозией в сталелитейной промышленности. В настоящее время также были обнаружены и описаны многие неотерические многообещающие проводящие полимерные системы. Тем не менее, для разработки этих полимеров необходимо преодолеть трудности обработки проводящих полимеров, сочетающихся со всеми видами металлов. Большинство этих проводящих полимеров можно было осаждать только на некоторые конкретные металлы из-за недостаточной плавкости и растворимости. Ширмайзен и Бек (1989) гальваностатически исследовал осаждение полипропиленового покрытия на железо. Этот процесс электрополимеризации изучался в различных водных и неводных электролитах. Также было обнаружено, что пленки PPy с превосходными гладкими и адгезионными свойствами могут быть сформированы только из водных нитратных электролитов. Кроме того, Феррейра и соавт. (1996) решили проблему растворения полипропилена путем предварительной обработки металлической подложки в 10% водном растворе HNO 3 перед электроосаждением. После этого было внедрено множество новых предварительных обработок, таких как нитрат и щавелевая кислота, для частичной пассивации стали. Де Брюйне и др. (1998) применили метод электроосаждения для получения пленки полипропилена толщиной приблизительно 800 нм на полированной стали. Электролиты водные 0,1 М H 2 C 2 O 4 (оксалат) и 0,5 М Na 2 SO 4 .
Подтверждены преимущества оксалата, промежуточный слой оксалата железа которого формировался до процесса электроосаждения. Этот промежуточный слой может в основном отвечать за сильную адгезию между проводящим полимером и сталью. В свою очередь коррозионная стойкость образцов полипропилена с покрытием повысилась. Модель «зерно-границы-поры» используется для объяснения процесса защиты от коррозии. Когда PPy был нанесен на поверхность железа, электроны будут находиться на нижнем занятом уровне молекулярной орбиты. Положительно заряженная металлическая поверхность Fe 3 O 4 /Fe 2 O 3 интерфейс сформирован. Дефицит электронов в слое Fe 3 O 4 изменит химический потенциал, что сделает его более устойчивым к окислению Fe 2+ . Кроме того, заряженный слой будет тормозить процесс диффузии Fe 2+ и O 2–, способствуя замедлению коррозии.
Помимо применения проводящих полимеров для защиты стали от коррозии, проводящие полимеры чаще используются для защиты от коррозии алюминиевых сплавов. Как правило, большинство этих проводящих полимеров содержат либо полианилин, либо полипиррол. Прежде всего, были обнаружены различные полианилиновые образования для защиты от коррозии алюминиевых сплавов, на примере осажденного на сплав Al 2024-T3 (Tallman et al., 2000) эмеральдиновой соли (ES), осажденного на Al 2024-T3 и Сплавы Al 3003 на основе эмеральдина (EB) (Epstein et al., 1999), так и осажденных на сплав Al 7075 (Racicot et al., 1995, 1997) молекулярными комплексными формами (ES форма с полиэлектролитными противоионами). Все эти осажденные покрытия в указанных выше исследованиях были основаны на растворах, состоящих из электроактивных проводящих полимеров (ECP). Расико и др. (1995, 1997) впервые применили полианилин для предотвращения коррозии алюминиевого сплава. Они успешно применили метод синтеза, ориентированный на матрицу, для синтеза молекулярного комплекса, содержащего полианилин и полианионы, с получением двухцепочечных полианилинов. Введение полианионов может придать металлам с покрытием некоторые желательные свойства, такие как улучшенная растворимость в обычных растворителях и улучшенная адгезия к подложке или верхнему покрытию.
Полианионы обычно представляли собой виниловые сополимеры, состоящие из боковых групп карбоксильной кислоты и алкила для лучшего облегчения обработки и адгезии. Молекулярная запутанность и электростатика могут полностью связать молекулярный комплекс, и по этой причине полианилины могут сохранять свойства легирующей примеси и проводимости. Образцы, покрытые полианилином, демонстрируют превосходную коррозионную стойкость благодаря различным тестам, таким как потенциодинамическая поляризация (PP), спектроскопия электрохимического импеданса (EIS) и тест в солевом тумане, которые могут быть сравнимы или лучше, чем обработка Alodine-600 (хроматно-конверсионные покрытия). Эпштейн и др. (1999) исследовали антикоррозионную защиту чистого алюминия и алюминиевых сплавов 3003 и 2024-Т3 через форму ЭБ для осаждения полианилинового покрытия. Покрытие EB представляет собой окисленное, но непроводящее состояние полианилина и может значительно повысить антикоррозийные свойства алюминия с покрытием и его сплавов.
В последнее время некоторые исследователи пытались использовать полипиррол для защиты от коррозии алюминиевых сплавов и получили неожиданные результаты. Таллман и др. (2002) обнаружили, что питтинговое поведение сплавов на основе полипиррола может быть подавлено более эффективно, чем у сплавов на основе полианилина. Кроме того, группа Хе обсудила взаимодействие между поли(3-октилпирролом) (POP) и сплавом Al 2024-T3 с помощью метода сканирующего вибрирующего электрода (SVET). Текущий поток сплавов с покрытием POP показывает значительную задержку по сравнению со сплавами с эпоксидным покрытием. Кроме того, в области дефекта сплава с покрытием POP был обнаружен только ток восстановления, в то время как ток окисления и ток восстановления наблюдались в области дефекта сплава с эпоксидным покрытием. Кроме того, для более широкого применения СОЗ Gelling et al. (2001) изучали долговременное погружение системы композитного покрытия, состоящей из слоя предварительной обработки POP и верхнего полиуретанового покрытия, которое было нанесено на алюминиевый сплав 2024-T3.
Это композитное покрытие могло поддерживать высокие значения импеданса и не показало признаков отказа после 2,5-летнего эксперимента с погружением, который показал превосходные долговременные антикоррозионные характеристики свежеприготовленных образцов. Совсем недавно Naoi et al. (1995) использовали сульфонаты поверхностно-активных веществ для стимулирования роста полипиррольных пленок. Мазь в том, что антикоррозионная защита этой пленки не оценена.
Тем не менее, разработка новых проводящих полимеров (КП), обладающих лучшими антикоррозионными характеристиками в различных средах, остается сложной задачей. В настоящее время широко используемые методы для достижения этой цели можно разделить на три категории в соответствии с различными механизмами. Конкретные классификации следующие: (1) сополимеризационные ХП, (2) наноструктурированные ХП, (3) композиты ХП. Например, коррозионная стойкость мягкой стали может быть повышена за счет использования поли( N -метилпиррол) и/или его сополимер (Weidlich et al. , 2005). Кроме того, пиррол также был сополимеризован с терполимером (пиррол-со-о-анизидин-со-толуидин), улучшая водостойкость CP (Yalçınkaya et al., 2010). Яо и др. (2008) синтезировали полианилиновые нановолокна на углеродистой стали методом межфазной полимеризации и сравнили коррозионное поведение с обычной углеродистой сталью, покрытой полианилином, в растворах хлорида натрия. Коррозионный ток покрытия из полианилиновых нановолокон был ниже, чем у обычного полианилинового покрытия на углеродистую сталь, что было связано с образованием более плотного слоя покрытия, индуцированного нановолокнами. Ян и др. (2010) успешно использовали три метода полимеризации для синтеза полианилиновых нановолокон в водном растворе серной кислоты. Они обнаружили, что оптимальным синтетическим методом является прямая смешанная реакция. По сравнению с двумя другими методами полимеризации (традиционная полимеризация и межфазная полимеризация) пленки, прошедшие прямую смешанную реакцию, обладают более однородной морфологией и улучшенной коррозионной стойкостью.
И последнее, но не менее важное: композиционные материалы могут сочетать характеристики ХП и разнообразных функциональных материалов, что придаст покрытиям лучшую коррозионную стойкость. Различные виды металлов, частицы оксидов металлов, неметаллические частицы и наноматериалы могут быть инкапсулированы в полианилиновые покрытия. Введение наночастиц цинка между полианилиновыми покрытиями может улучшить проводимость и антикоррозионную защиту по сравнению с микроразмерными частицами цинка (Olad and Rasouli, 2010). Более того, наноSiO 2 – одна из наиболее перспективных наночастиц для антикоррозионных покрытий. Композиты NanoSiO 2 -полианилин, нанесенные на мягкую сталь, обладают улучшенными защитными характеристиками по сравнению с одним полианилином. Синергетический эффект гидрофобной способности nanoSiO 2 и окислительно-восстановительного каталитического свойства полианилина будет отвечать за улучшение антикоррозионных свойств (Weng et al., 2012). Вообще говоря, ХП следует уделять гораздо больше внимания в аспекте практического применения защиты от коррозии, так как они обладают отличной химической совместимостью, могут применяться в различных формах, а некоторые из них могут проявлять очень стабильную коррозионную стойкость.
Самособирающиеся пленки
Самособирающиеся пленки также привлекли большое внимание из-за их пригодности для применения в покрытиях и для защиты от коррозии, несмотря на то, что самособирающиеся пленки имеют некоторые недостатки, связанные с резким ухудшением коррозионной стойкости самособирающегося монослоя ( SAM), так как их термическая стабильность относительно низкая. Тем не менее, такие свойства, как простота изготовления, характеристики и манипулирования, гарантируют, что SAM остается популярным среди областей покрытия. Например, SAM алкантиолов, представленный C n H 2n + 1 SH ( n = 6~18) хорошо подходят для защиты меди от коррозии, поскольку они могут адсорбироваться на поверхности меди и действовать как плотное барьерное покрытие (Yamamoto и др., 1993). Ожидается, что реакции гидролиза и конденсации объяснят процесс защиты от коррозии. Сшитый алкантиоловый слой непосредственно хемосорбируется на поверхности металла и сополимеризуется с гидролизованными силанами, что может сделать поверхность более гидрофобной и повысить коррозионную стойкость. Для преодоления потенциальных недостатков, таких как относительно недостаточно высокие защитные способности ПАВ в растворах некоторых агрессивных сред, были обнаружены модификации ПАВ и некоторые новые типы ПАВ с повышенной коррозионной стойкостью с целью их потенциального применения в защите от коррозии. .
Группа Шахраби сообщила о серии SAM, полученных из оснований Шиффа и их модификаций, в качестве новых кандидатов для применения в защите от коррозии Cu (Эхтешамзаде и др., 2006). Два лиганда, основания Шиффа, N,N’ – орто--фенилен-бис (салицилиденимин) (S- или -ph-S) и N,N’ -этилен-бис (салицилиденимин) (S-E-S) были выбраны для хемосорбции на поверхности меди для достижения SAM. Поведение ингибирования коррозии исследовали с помощью EIS и поляризационной кривой Тафеля. Электрохимические результаты показали, что эффективность ингибирования коррозии ПАВ С- o -ph-S выше, чем у S-E-S. Термодинамические расчеты S- o -ph-S и S-E-S подтвердили, что S- o -ph-S будет демонстрировать более отрицательную свободную энергию адсорбции и большую константу адсорбции по сравнению с S-E-S, что может дополнительно подтвердить электрохимические результаты. Они также попытались модифицировать SAM оснований Шиффа двумя видами алкантиолов: 1-додекантиолом и пропантиолом. Два вида алкантиолов усиливали эффективность ингибирования коррозии приготовленных ПАВ на основе оснований Шиффа за счет более плотного формирования покрытий при значительно меньшем количестве дефектов на поверхности. К сожалению, упомянутые выше эффективные ингибиторы являются токсичными, что наносит вред как окружающей среде, так и организму человека. Поэтому экологически чистые ингибиторы в последние годы постепенно становятся актуальным вопросом. Типичным нетоксичным ингибитором является имидазол, в котором два атома азота присутствуют в гетероциклической группе (Zhang et al., 2009).). Помимо защиты меди, Hackerman et al. исследовали ингибирующие коррозию свойства гетероциклических диазолов для предотвращения коррозии железа в кислых средах (Babiæ-Samardžija et al., 2005). Они пришли к выводу, что два атома азота в разных положениях в гетероцикле имидазола могут оказывать более сильное влияние на ингибирование коррозии полученных покрытий.
Ингибирование коррозии производными имидазола было лучше, чем у производных пиразола. Различия между пиразолом и имидазолом заключаются в том, что два атома азота пиразола являются смежными в гетероцикле, в то время как между двумя атомами азота имидазола находится атом углерода. Заместитель у атома углерода будет иметь положительный эффект между SAM и железом, что приведет к улучшению ингибирования коррозии. Недавно (Чжан и др., 2009 г.) Группа Чена применила имидазол и его производные, которые присоединялись либо к алкановым цепям разной длины, либо к разным функциональным группам, чтобы исследовать последствия защиты железа с покрытием в кислом растворе. Названия и аббревиатуры представляют собой, соответственно, имидазол (IMZ), 1-бензил-1H-имидазол (BIMZ), (E)-3-(4-((1H-имидазол-1-ил)метил)фенил)акриловую кислоту (IMMP). ), 1-бутил-1H-имидазол (BTIM), 1-тозил-1H-имидазол (TSIM) и (E)-метил 3-(4-((1H-имидазол-1-ил)метил)фенил)акрилат ( МИММП). Поведение этих шести SAM в отношении ингибирования коррозии было изучено путем изменения времени погружения, температуры сборки и концентрации раствора для сборки.
Электрохимические испытания подтвердили, что ряд соединений имидазола является подходящим ингибитором коррозии для кислой коррозии железа и что MIMMP является лучшим ингибитором среди них. Но в этой статье не упоминался конкретный механизм, объясняющий, почему MIMMP обладает оптимальным ингибированием коррозии.
В качестве краткого заключения можно сказать, что самособирающиеся пленки, особенно имидазол и его производные, могут быть потенциальным вариантом для защиты стали от коррозии на практике, если удастся решить проблему термической стабильности или еще больше повысить ее. Относительно простые методы синтеза и различные модификации в сочетании с подходящими функциональными группами гарантируют, что эта серия самособирающихся пленок привлекает большое внимание в отношении их будущих применений.
Оценка срока службы вышеупомянутых систем покрытий
Горячеоцинкованная сталь на основе вышеупомянутых систем покрытий имеет большое значение для различных применений; следовательно, эти новые системы покрытий с оптимизированными или ожидаемыми свойствами постоянно исследуются исследователями материалов или химиков. В то же время оценка срока службы этих систем дуплексных покрытий является достаточно сложной, но необходимой и также привлекает внимание большого числа исследователей. Целью оценки срока службы этих систем покрытия для HDGS является количественная оценка коррозионной стойкости покрытий и определение того, не удается ли системе покрытия избежать больших потерь, таких как коррозионное разрушение. До настоящего времени не существовало единого определения срока службы систем дуплексного покрытия. Существует три основных мнения, позволяющих судить о сроке службы систем покрытий: (1) любая ржавчина, появившаяся на поверхности металла с покрытием, (2) перфорация металла с покрытием, (3) площадь ржавчины на металле с покрытием, достигающая заданного значения. значение (Чжэнь, 2005). Из-за недостатка длительного цикла полевых испытаний испытания на ускорение коррозии в помещении могут эффективно оценить срок службы покрытий за короткое время в определенных условиях. Таким образом, был достигнут консенсус в отношении того, что прогноз срока службы металлов с покрытием обычно получают путем суммирования корреляции результатов испытаний на ускорение коррозии в помещении и полевых испытаний среди научных исследователей.
Другими словами, жизненно важно понять механизм коррозии металла с покрытием в условиях испытаний на ускорение коррозии в помещении и предложить соответствующие методы оценки, основанные на механизме коррозии. Что касается металла с однократным покрытием (металлические покрытия или органические покрытия), был предложен и признан метод ускоренной оценки коррозии металла (например, различные стандарты), и некоторые из этих стандартов также содержат количественные критерии оценки. Для металлических покрытий в качестве примера можно взять гальваническое покрытие. Срок службы гальванического покрытия традиционно относят к времени достижения площади красной ржавчины 5% от всей площади гальванического слоя в условиях ускоренного испытания. Чжан и Сюй (2007) рассмотрели корреляцию между испытаниями на ускоренную коррозию и фактическими условиями коррозии, сосредоточив внимание на соотношении скоростей коррозии стали и цинка. «Предсказатель срока службы цинкового покрытия» также был придуман на основе многочисленных статистических данных о коррозии стали и цинка.
Fujita и Mizuno (2007) исследовали перфорационную коррозию цинка или стали, покрытой цинковым сплавом, и оценили срок службы различных стальных листов с покрытием на основе различных видов испытаний на ускоренную коррозию. Они разделили процедуру перфорационной коррозии на четыре периода. Стадия 1: вся поверхность стальной подложки покрыта цинковым покрытием и не подвергается коррозии ни что иное, как цинковое покрытие (τ 1 ). Стадия 2: цинковое покрытие частично теряется, и эта пленка продолжает жертвенно корродировать для защиты стали (τ 2 ). Стадия 3: полностью теряется цинковое покрытие и начинается коррозия стали. Между тем, продукты коррозии цинка могут замедлять общую скорость коррозии оцинкованной стали (τ 3 ). Стадия 4: цинковое покрытие полностью теряет защитное действие и сталь быстро корродирует (τ 4 ). Схематическая диаграмма процесса коррозии оцинкованной стали была показана на рисунке 6. Чтобы продемонстрировать связь между различными испытаниями на ускоренную коррозию и фактической коррозией, они взяли за основу (Zhang and Xu, 2007) и предложили концепцию, названную индексом перфорационной коррозии ( PCI) для оценки сквозной коррозии оцинкованной стали.
Конкретная формула была следующей:
Рисунок 6. Схематическая диаграмма процесса коррозии оцинкованной стали (Fujita and Mizuno, 2007).
PCI=V/SteelVZinc(1)
Where, V Z i n c and V S t e e l были определены соответственно следующим образом:
V=цинк/покрытие(τ+1τ+2τ)3(2)
V=Сталь/Стальτ4(3)
d покрытие и d сталь соответственно толщина цинкового покрытия и стали.
По этой формуле PCI ускоренных испытаний на коррозию совпадал бы с фактической коррозией в Детройте, доказывая осуществимость PCI. К сожалению, он не универсален для различных металлов и различных условий коррозии.
Что касается прогнозирования срока службы органических покрытий, Мейн объединил закон диффузии Фика с электрохимией стального листа с покрытием, чтобы предложить формулу прогнозирования срока службы органического покрытия, основанную на «теории контроля сопротивления поляризации покрытия» (Maitland, 19). 62). Формула была следующей:
L=l2/(6D)+ϕ(psσn)(4)
Где L и l были, соответственно, сроком службы покрытия и глубиной покрытия, D представляло диффузию коэффициент ионов покрытия, ϕ был постоянным, p s и σ n , соответственно относился к адгезии покрытия и приложенному давлению на поверхность стали. Chuang (1997) создал математическую модель на основе образования пузырьков в покрытии, где скорость роста пузырьков составляет V рассматривается как функция крутящего момента, свойств материала и температуры. Наконец, срок службы системы покрытия был получен:
Vmin=1,83(σf/W)5/4(DbδbΩ/kT)[Eh4/12(1-ν2)]1/4(5)
Where, σ f was the layered stress, W was the cross-sectional area of the coating, D b δ b was interfacial diffusivity, Ω, k и T были постоянными, ν и E были, соответственно, коэффициентом Пуассона и модулем упругости покрытий в условиях смачивания, h были общей толщиной покрытий. Хотя формула прогнозирования срока службы органического покрытия была установлена, ее точность была под вопросом. Из-за разнообразия покрытий и различий в коррозионной среде до сих пор не найдено общей формулы, которая могла бы точно предсказать срок службы покрытий.
Помимо вышеупомянутой формулы прогнозирования срока службы, технология EIS постепенно становится мощным инструментом для прогнозирования срока службы органических покрытий. EIS дает in situ неразрушающее измерение коррозионного поведения защитного покрытия, которое может отражать информацию о реакции коррозии, переносе массы и переносе заряда (Grundmeier et al., 2000; Vogelsang and Strunz, 2001). Этот метод усиливается токовой реакцией малого синусоидального возмущения электродного потенциала в вариациях с частотой возмущения. Методы эквивалентных схем обычно используются для анализа и интерпретации данных EIS. Эквивалентная схема обычно состоит из электрических элементов, имитирующих границу раздела электрод/раствор. Сопротивление ( R ) и конденсаторы ( C ) являются наиболее часто используемыми электрическими компонентами. В некоторых случаях вместо конденсаторов ( C ) были введены элементы с постоянной фазой (CPE) для достижения удовлетворительных результатов. Импеданс Варбурга подходит для процесса диффузии. Принятые модели эквивалентных схем должны учитывать следующие принципы: (1) Электрические компоненты, используемые в эквивалентных схемах, должны иметь четкое физическое значение. То есть они должны соответствовать физическим свойствам системы, которая может производить такие электрические отклики; (2) Эквивалентные схемы должны генерировать спектры, а параметры в схемах должны иметь соответствующие значения. Хотя спектры отличаются от экспериментальных спектров, допускаются допустимые ошибки; и (3) Предлагаемые эквивалентные схемы должны быть максимально простыми. Цао и Чжан (2002) предложили шесть моделей эквивалентных схем в соответствии с характеристиками спектров импеданса систем органических покрытий в разные периоды погружения.
Для широкого спектра систем органических покрытий характерны три основных физических процесса: (1) процесс диэлектрической релаксации. Этот процесс представлен емкостью покрытия C c , который обычно встречается в высокочастотной области спектров импеданса; (2) Процесс переноса заряда на границе металл/раствор. Этот процесс представлен сопротивлением переноса заряда R ct и емкостью двойного слоя C dl , что происходит после того, как коррозионный раствор достигает границы органического покрытия/металла; (3) Процесс диффузии. Этот процесс обычно происходит в порах покрытия и происходит в низкочастотной части спектров импеданса (Strunz, 2000).
Секин и др. (1992) обнаружили линейную зависимость между f θmax и R c , в которой R c представляет собой сопротивление покрытия, а f 95max относится к фазе с фазой 90 по максимуму. Соотношение может служить стандартом для оценки коррозионной стойкости органических покрытий, тогда как f θmax можно легко измерить. Mahdavian и Attar (2006) проанализировали и сравнили различия в антикоррозионных характеристиках покрытий из фосфата цинка и покрытий из хромата цинка в зависимости от фазового угла на частоте 10 кГц. Харуяма и Судо (1993) выдвинул новую концепцию: частота излома f b , частота, при которой сначала фазовый угол снижается до 45°, и обнаружил лучшую корреляцию между отслоившимися областями органического покрытия на металле и частотой излома. Мансфельд и Цай (1991) предложили два новых параметра: θ мин и f θмин , которые соответственно представляют минимальный фазовый угол и соответствующую частоту. Можно указать, что θ мин и пропорции f b /f θmin все до области зачистки между свежеприготовленными органическими покрытиями и металлом подложки. Все вышеупомянутые методы анализируют высокочастотные области спектра импеданса для прогнозирования характеристик органических покрытий, что позволяет избежать измерений в низкочастотных областях спектра импеданса и разработать быструю оценку срока службы органических покрытий.
Кроме того, Zuo et al. (2008) обнаружили, что фазовый угол и сопротивление покрытия в области средних частот из графиков Боде имеют аналогичные нисходящие тенденции. Изменение фазового угла при частоте 10 Гц в зависимости от времени выдержки в 3,5% растворе NaCl соответствовало изменению стойкости покрытия, что могло качественно отражать коррозионную стойкость органического покрытия. В случае, если фазовый угол при 10 Гц уменьшился до диапазона 20-40°, электролиты полностью проникли в органические покрытия, и электрохимические реакции под этими защищенными покрытиями начали протекать быстро. Таким образом, фазовый угол на частоте 10 Гц может применяться для быстрой оценки характеристик органического покрытия.
Совсем недавно Hu et al. изучили спектры электрохимического импеданса алюминиевого сплава LY12/эпоксидного покрытия на различных стадиях погружения в 3,5% раствор NaCl (Hu et al., 2003; Zhang et al., 2004). Они считали, что старение органических покрытий можно разделить на четыре этапа.
Стадия 1: В начальный момент времени погружения на спектре электрохимического импеданса появляется только одна постоянная времени, которая показывает эквивалентную схему сопротивления пор покрытия ( R p ) параллельно с обволакивающим конденсатором ( C c ), в котором R s – растворное сопротивление. На рис. 7 показаны эквивалентный режим А, графики Найквиста и графики Боде для композитного электрода, погруженного в 3,5% раствор NaCl на 12 мин.
Рис. 7. (A) Комплексная плоскость импеданса, модель цепи и диаграмма Боде (B) алюминиевого сплава LY12 с эпоксидным покрытием, погруженного в 3,5% раствор NaCl на 12 мин (Hu et al., 2003).
Стадия 2: Когда вода, O 2, и другие вещества с большими коэффициентами диффузии проходят через покрытие и достигают подложки, устанавливается электрохимическая граница раздела металл/электролит, и начинает появляться импеданс электрохимической реакции. Эквивалентная схема этого каскада показана в модели Б на рисунке 8. Высокочастотный участок спектра импеданса соответствует самому покрытию ( C c R p ), а низкочастотные области соответствуют импедансу электрохимической реакции ( C dl R ct ) на границе металл/раствор, где C dl относится к емкости двойного слоя и R ct – стойкость к электрохимическим реакциям.
Рис. 8. (A) Комплексная плоскость импеданса, модель цепи и (B) фазовая угловая диаграмма металла с покрытием, погруженного в чистую воду на 3 часа (Hu et al., 2003).
Стадия 3: Под действием барьера покрытия ингибируется переход продуктов коррозии на поверхность металла, в результате чего возникает диффузионное сопротивление Z диф . Эквивалентная схема этого каскада показана в модели С на рис. 9. Кроме того, на рис. 9 также показан комплексный план импеданса электрода, погруженного в чистую воду на 48 ч.
Рисунок 9. Комплексная плоскость импеданса и модель контура металла с покрытием, погруженного в чистую воду на 48 часов (Hu et al., 2003).
Стадия 4: Когда коррозионные ионы с малыми коэффициентами диффузии, такие как ионы Cl – , достигают границы раздела металл/покрытие через покрытие, химические реакции между Cl – и растворимыми продуктами коррозии на границе раздела образуют соляную пленку. . Импеданс Фарадея представляет собой сумму импеданса соляной пленки ( R sf C sf ) и импеданса электрохимического растворения ( R ).0934 из С из ) из сплава. Эквивалентная схема этой ступени показана в модели D на рисунке 10. Рисунок 10 иллюстрирует появление двойных дуг емкости на примере комплексного плана импеданса металла с покрытием, погруженного в 3,5% раствор NaCl на 388 часов. Считается, что высокочастотная емкостная дуга соответствует характеристическому сопротивлению реакции пленкообразования с участием ионов Cl – на поверхности алюминиевой подложки, а низкочастотная емкостная дуга соответствует импедансу анодной электрохимической реакции поверхности алюминиевой подложки. .
Рис. 10. (A–C) Комплексная плоскость импеданса и модель контура металла с покрытием, погруженного в 3,5% раствор NaCl на 388 ч (Hu et al., 2003).
Говоря о дуплексных покрытиях, до сих пор не существовало стандарта оценки ускоренной коррозии для композитных систем покрытий, таких как углеродистая сталь, покрытая сначала гальваническим покрытием, а затем органическим покрытием. Нецелесообразно оценивать коррозионную стойкость композиционных покрытий, просто применяя критерии оценки одиночных покрытий. Например, некоторые исследователи (Bacon et al., 1948) обнаружил, что когда модуль электрохимического сопротивления органических покрытий достигает 10 8 Ом см 2 или выше, органические покрытия обладают лучшей коррозионной стойкостью. В то время как модуль электрохимического импеданса органических покрытий был менее 10 8 Ом⋅см 2 , их антикоррозионные характеристики были относительно низкими. Даже когда модуль электрохимического импеданса снизился до 10 6 Ом⋅см 2 , покрытия можно было считать полностью разрушенными. Но для ВГДС его модуль импеданса обычно не превышает 10 6 Ом⋅см 2 . Нельзя сказать, что цинковое покрытие разрушилось только по модулю импеданса, и фактически цинковое покрытие может быть неповрежденным. Следовательно, этот стандарт оценки не применяется к металлическому покрытию. То есть стандарт оценки одиночного покрытия не подходит для составного покрытия.
Однако, подытоживая приведенные выше исследования по оценке срока службы металлических и органических покрытий, было обнаружено, что процесс разрушения двух различных типов покрытий, исследованных выше, в некоторой степени похож друг на друга, и оба их процесса разрушения можно рассматривать как прохождение четырех стадий. Основываясь на этом, мы предлагаем новый метод оценки ускоренного срока службы системы композитного покрытия. Существует синергизм между общим сроком службы композитных покрытий ( L c ) (Dallin et al. ) для композитного покрытия система: L c = k ( L f + L z ), k = 1,5~2,3. Таким образом, исследование срока службы композитного покрытия можно разделить на два аспекта: срок службы органического покрытия и срок службы гальванического покрытия. Для органических покрытий мы можем оценить процесс разрушения по четырем стадиям, предложенным группой Ху, и появление дуг двойной емкости знаменует окончательную жизнь органического покрытия. Что касается гальванических покрытий, нам необходимо не только оценить четыре стадии процесса коррозии, но также необходимо объединить потенциальное обращение стали и цинка, чтобы всесторонне оценить срок службы оцинкованного слоя. Из-за расходуемой анодной защиты гальванического слоя, даже когда коррозионные вещества, такие как Cl – проходят через слой цинкования и достигают подложки, углеродистая сталь может не сразу подвергнуться коррозии, в результате чего время, в течение которого коррозионно-активные ионы, такие как Cl – , достигают границы раздела металл/покрытие, не обязательно совпадает со временем на срок защиты гальванического покрытия. Новые и высокоэффективные коррозионно-стойкие системы покрытий для HDGS очень важны для их широкого применения в таких вещах, как детали высокоскоростных железнодорожных воздушных линий. Они важны, например, для управления процессом цинкования, нанесения лакокрасочных покрытий и электрохимической защиты; они гарантируют, что глобальное поле HDGS находится на лидирующих позициях, применяя различные системы покрытий для их превосходной коррозионной стойкости. На данный момент новые системы покрытий все еще нуждаются в получении коррозионно-стойких покрытий с лучшей адгезией к подложкам на основе типов HDGS, а также нуждаются в повышении эффективности коррозионной стойкости с целью продления срока службы устройств или выполнения требований. Будущие разработки систем покрытий для HDGS затронут ряд областей. Во-первых, на модификации существующих систем покрытий можно повлиять, например, посредством структурной модификации силановых пленок и оптимизации состава конверсионных редкоземельных пленок. Также это повлияет на открытие новых систем покрытий. Чтобы справиться с ухудшающейся окружающей средой, для будущих применений HDGS потребуются новые системы покрытий с улучшенной коррозионной стойкостью. В-третьих, на исследование методологии оценки этих вышеупомянутых систем покрытий будут влиять любые разработки в области систем покрытий для HDGS. Этот обзор в основном выполнен ZY под руководством HM и JH. Настоящее исследование выполнено при финансовой поддержке Национальной ключевой программы исследований и разработок Китая (2017YFB1200800). Авторы заявляют, что исследование проводилось при отсутствии каких-либо коммерческих или финансовых отношений, которые могли бы быть истолкованы как потенциальный конфликт интересов. Aldykewicz, A., Isaacs, H., и Davenport, A. (1995). Исследование церия как катодного ингибитора алюминиево-медных сплавов. Дж. Электрохим. соц. 142, 3342–3350. doi: 10.1002/chin.199604011 CrossRef Full Text | Google Scholar Аль-Мехтель М., Аль-Дулайджан С., Аль-Иди С. Х., Шамим М., Али М. и Маслехуддин М. (2009). Эффективность обычных и патентованных ингибиторов коррозии в железобетоне, загрязненном хлоридами. Конструкт. Строить. Матер. 23, 1768–1774 гг. doi: 10.1016/j.conbuildmat.2008.10.010 CrossRef Полный текст | Google Scholar Арамаки, К. (2001a). Ингибирующее действие катионных ингибиторов на коррозию цинка в аэрированном 0,5 М NaCl . Коррос. науч. 43, 1573–1588. doi: 10.1016/S0010-938X(00)00144-X Полный текст CrossRef | Google Scholar Арамаки, К. (2001b). Обработка поверхности цинка азотнокислым церием (III) для предотвращения коррозии цинка в аэрируемых 0,5 М NaCl . Полный текст CrossRef | Google Scholar Арамаки, К. (2005). Самовосстанавливающаяся защитная пленка, полученная на цинке обработкой в растворе Ce(NO3)3 и модифицированием Ce(NO3)3. Коррозия. науч. 47, 1285–1298. doi: 10.1016/j.corsci.2004.05.022 CrossRef Полный текст | Google Scholar Асгари Х., Торогинежад М. и Голозар М. (2007). Текстура, коррозионная стойкость и морфология горячеоцинкованных цинковых покрытий. заявл. Поверхностные науки. 253, 6769–6777. doi: 10.1016/j.apsusc.2007.01.093 CrossRef Полный текст | Google Scholar Babiæ-Samardžija, K., Lupu, C., Hackerman, N., Barron, A.R., и Luttge, A. (2005). Ингибирующие свойства и морфология поверхности группы гетероциклических диазолов как ингибиторов кислотной коррозии железа. Ленгмюр 21, 12187–12196. doi: 10.1021/la051766l PubMed Abstract | Полный текст перекрестной ссылки | Google Scholar Бэкон Р. CrossRef Полный текст | Google Scholar Бера С., Раут Т., Удаябхану Г. и Нараян Р. (2016). Экологически чистое эпоксидно-силановое гибридное покрытие на водной основе для улучшенной защиты от коррозии и адгезии к оцинкованной стали. Прог. Орг. Пальто. 101, 24–44. doi: 10.1016/j.porgcoat.2016.07.010 CrossRef Полный текст | Академия Google Бракетти-Сибаха, С., Домингес-Креспо, М. А., Торрес-Уэрта, А. М., Де ла Крус-Эрнандес, В., и Онофре-Бустаманте, Э. (2011). Роль условий ванны в обеспечении защиты от коррозии алюминиевого сплава с использованием конверсионных покрытий редкоземельных элементов. Дж. Электрохим. соц. 159, С40–С57. doi: 10.1149/2.035201jes CrossRef Full Text | Google Scholar Бреваль Э. и Рахлиц М. (1988). Горячеоцинкованная сталь: структура поверхности и адгезия красок. CrossRef Полный текст | Google Scholar Кабрал А., Трабелси В., Серра Р., Монтемор М., Желудкевич М. и Феррейра М. (2006). Коррозионная стойкость горячеоцинкованной стали и стали AA2024-T3, предварительно обработанной растворами бис-[триэтоксисилилпропил]тетрасульфида, легированного Ce(NO3) 3. Corros. науч. 48, 3740–3758. doi: 10.1016/j.corsci.2006.01.010 CrossRef Полный текст | Google Scholar Cachet, C., Ganne, F., Joiret, S., Maurin, G., Petitjean, J., Vivier, V., et al. (2002). ЭИС-исследование растворения цинка в аэрированной сульфатной среде. Часть II: цинковые покрытия. Электрохим. Acta 47, 3409–3422. doi: 10.1016/S0013-4686(02)00277-3 Полный текст CrossRef | Google Scholar Cachet, C., Ganne, F., Maurin, G., Petitjean, J., Vivier, V. и Wiart, R. (2001). ЭИС-исследование растворения цинка в аэрированной сульфатной среде. Часть I: сыпучий цинк. Электрохим. Полный текст CrossRef | Google Scholar Цао, К., и Чжан, Дж. (2002). Введение в спектроскопию электрохимического импеданса. 909:35 Нью-Йорк, штат Нью-Йорк: Издательство Science Publishing Company. Google Scholar Капелосси, В. Р., и Аоки, И. В. (2013). Влияние обработки ультразвуком на антикоррозионные свойства сульфосилановой пленки, легированной Се (IV), на оцинкованной стали. Прог. Орг. Пальто. 76, 812–820. doi: 10.1016/j.porgcoat.2013.01.012 CrossRef Полный текст | Google Scholar Чанг Дж.-К., Лин К.-С., Ченг В.-Дж., Ло И.-Х. и Ван В.-Р. (2019). Устойчивое к окислению силановое покрытие для горячеоцинкованной штампованной стали. Коррос. науч. 164:108307. doi: 10.1016/j.corsci.2019.108307 CrossRef Полный текст | Google Scholar Чен Ю., Чанг С. и Ши Х. (2006). Исследования начальных стадий атмосферной коррозии цинка в присутствии хлорида. CrossRef Полный текст | Google Scholar Чен З., Кеннон Н., См. Дж. Б. и Бартер М. (1992). Technigalva и другие разработки в области серийного горячего цинкования. ДжоМ 44, 22–26. doi: 10.1007/BF03222746 Полный текст CrossRef | Google Scholar Чуанг Т. (1997). «Модель неосмотического роста пузырей в системах покрытий», в Damage and Failure of Interfaces. 1-я Международная конференция. Труды. , (Амстердам: издательство AA Balkema), 22–24. Google Scholar Коул И., Мастер Т., Лау Д., Райт Н. и Азмат Н. С. (2010). Продукты, образующиеся при взаимодействии капель морской воды с цинковыми поверхностями II. Результаты коротких экспозиций. Дж. Электрохим. соц. 157, C213–C222. doi: 10.1149/1.33 Полный текст CrossRef | Google Scholar Кулкаси, Дж. Д., Элснер, К. И., и Ди Сарли, А. Р. (2009). Влияние размера кристаллов цинка на деформацию оцинкованной стали и электрохимическое поведение. , 2018) и срок службы органического покрытия ( L f ) и срок службы цинкового покрытия ( L 5z
Когда скорость коррозии оцинкованной стали быстро увеличивается, потенциал холостого хода оцинкованной стали должен измениться. В то время как цинк теряет анодную защиту стали и подложка из углеродистой стали начинает быстро подвергаться коррозии, скорость коррозии оцинкованной стали должна быстро увеличиваться, а потенциал холостого хода оцинкованной стали будет меняться на противоположный. Конкретная экспериментальная проверка все еще продолжается и готова к публикации.
Заключение и будущая работа
применения HDGS в более суровых природных условиях. Следовательно, было изобретено множество новых и эффективных систем покрытий, о которых сообщалось в виде краткого обзора в этом свете. Кроме того, последняя опубликованная литература проиллюстрировала действенную тактику открытия новых систем покрытий, таких как силановые пленки, конверсионные пленки редкоземельных элементов, проводящие полимеры и самособирающиеся пленки.
Из-за отсутствия унифицированных методов оценки срока службы для этих систем композитных покрытий желательно установить разумные критерии оценки срока службы. Создание методов оценки окажет огромное положительное влияние на производство и срок службы, поскольку позволит нам судить о том, потеряют ли системы покрытий защитные функции, чтобы избежать больших потерь. Следовательно, важно всесторонне понять экспериментально и теоретически присущие коррозионному процессу системы композитных покрытий HDGS в связи с оценкой срока службы этих систем покрытий и проектированием предпочтительных систем покрытий для HDGS.
Вклад авторов
Финансирование
Конфликт интересов
Ссылки
Коррос. науч. 43, 2201–2215. doi: 10.1016/S0010-938X(00)00189-X
К., Смит Дж. Дж. и Рагг Ф. М. (1948). Электролитическая стойкость в оценке защитных свойств покрытий на металлах. Индивидуальный инж. хим. 40, 161–167. doi: 10.1021/ie50457a041
Дж. Матер. науч. 23, 1835–1840 гг. doi: 10.1007/BF01115729
Acta 47, 509–518. doi: 10.1016/S0013-4686(01)00740-X
Коррос. науч. 48, 3547–3564. doi: 10.1016/j.corsci.2005.12.007
Матер. Рез. 12, 273–279. doi: 10.1590/S1516-1439200
Полный текст CrossRef | Google Scholar
Каттон Л.Д.К., Кристини С., Труэба М. и Трасатти С. (2016). Электрохимическое исследование смесей полианилина на оцинкованной стали. Прог. Орг. Пальто. 96, 65–79. doi: 10.1016/j.porgcoat.2016.02.011
CrossRef Полный текст | Google Scholar
Дафидд Х., Уорсли Д. и МакМюррей Х. (2005). Кинетика и механизм катодного восстановления кислорода на гальванизированных покрытиях из цинка и сплава цинка с алюминием. Коррос. науч. 47, 3006–3018. doi: 10.1016/j.corsci.2005.05.036
CrossRef Полный текст | Google Scholar
Даллин Г., Гудвин Ф. Э. и Поул С. (2018). «Дуплексные цинковые покрытия для защиты от коррозии стальных конструкций», в 97-е ежегодное собрание Совета по исследованиям в области транспорта , Вашингтон, округ Колумбия.
Google Scholar
Дэн З., Цзе С., Чжан Л., Юн Т. и Цзи Л. (2010). Коррозионное поведение конверсионного покрытия на основе редкоземельного церия на алюминиевом сплаве. J. Редкие земли 28, 371–374. doi: 10.1016/S1002-0721(10)60338-9
Полный текст CrossRef | Google Scholar
Де Брюйне А., Дельпланке Ж.-Л. и Винанд Р. (1998). Сравнение полипиррольных пленок, полученных на мягкой стали электрополимеризацией из водных растворов щавелевой кислоты и сульфата натрия. Поверхностное покрытие. Технол. 99, 118–124. doi: 10.1016/s0257-8972(97)00417-9
Полный текст CrossRef | Google Scholar
Дешпанде П., Вагге С., Джагтап С., Хиарнар Р., Келкар С. и М. М. (2012). Нанесение красок на основе полианилина на горячеоцинкованную низкоуглеродистую сталь для защиты от коррозии. Болгарский хим. коммун. 44, 318–323.
Google Scholar
Ди Сарли А. Р., Эльснер К. И. и Томачук К. (2014). Характеристика и коррозионная стойкость оцинкованной стали//Пассивация композитными/полиуретановыми лакокрасочными системами. Бр. Дж. Заявл. науч. Технол. 4, 853–878. doi: 10.9734/BJAST/2014/6813
Полный текст CrossRef | Google Scholar
Эхтешамзаде М. , Шахраби Т. и Хоссейни М. (2006). Ингибирование коррозии меди самоорганизующимися пленками новых оснований Шиффа и их модификация алкантиолами в водной среде. Заяв. Поверхностные науки. 252, 2949–2959. doi: 10.1016/j.apsusc.2005.05.003
Полный текст CrossRef | Google Scholar
Эль-Сайед А.-Р., Харм У., Мангольд К.-М. и Фюрбет В. (2012). Защита оцинкованной стали от коррозии в растворе NaCl путем покрытия фитиновой кислотой SAM, модифицированной некоторыми катионами и тиолами. Коррос. науч. 55, 339–350. doi: 10.1016/j.corsci.2011.10.036
CrossRef Полный текст | Google Scholar
Эль-Шазли, А., и Аль-Тураиф, Х. (2011). «Улучшение коррозионной стойкости для гальванического соединения стали с оцинкованной сталью с полипиррольным покрытием», в Key Engineering Materials (Швейцария: Trans Tech Publication), 25–33. doi: 10.4028/www.scientific.net/kem.478.25
Полный текст CrossRef | Google Scholar
Эпштейн А., Смоллфилд Дж. , Гуан Х. и Фалман М. (1999). Защита алюминия и алюминиевых сплавов от коррозии полианилинами: потенциодинамическое и фотоэлектронно-спектроскопическое исследование. Синтез. Металлы 102, 1374–1376. doi: 10.1016/s0379-6779(98)00383-x
Полный текст CrossRef | Google Scholar
Фальк Т., Свенссон Дж. Э. и Йоханссон Л. Г. (1998). Роль углекислого газа в атмосферной коррозии цинка лабораторное исследование. Дж. Электрохим. соц. 145, 39–44. doi: 10.1149/1.1838207
Полный текст CrossRef | Академия Google
Фасойину, Ф., и Вайнберг, Ф. (1990). Образование блесток в покрытиях из оцинкованной листовой стали. Металл. Транс. В 21, 549–558. doi: 10.1007/BF02667868
Полный текст CrossRef | Google Scholar
Феррейра К., Эйяч С., Аарон Дж. Дж. и Лаказ П. (1996). Электросинтез прочно сцепляющихся полипиррольных покрытий на чугуне и мягкой стали в водной среде. Электрохим. Акта 41, 1801–1809 гг. doi: 10.1016/0013-4686(95)00498-X
Полный текст CrossRef | Академия Google
Феррейра, М. , Дуарте, Р., Монтемор, М., и Симойнс, А. (2004). Силаны и соли редкоземельных элементов в качестве заменителей хромата для предварительной обработки оцинкованной стали. Электрохим. Acta 49, 2927–2935. doi: 10.1016/j.electacta.2004.01.051
CrossRef Полный текст | Google Scholar
Фигейра Р. Б., Силва С. Дж. и Перейра Э. В. (2015). Горячеоцинкованная сталь, покрытая уреасиликатным гибридом погружением в раствор, имитирующий поры бетона: оценка морфологии покрытия и эффективности защиты от коррозии. Прог. Орг. Пальто. 88, 245–255. doi: 10.1016/j.porgcoat.2015.07.008
CrossRef Полный текст | Google Scholar
Фигейра Р. Б., Силва С. Дж. и Перейра Э. В. (2016). Гибридные золь-гель покрытия для защиты от коррозии оцинкованной стали в растворе, моделирующем поры бетона. Дж. Пальто. Технол. Рез. 13, 355–373. doi: 10.1007/s11998-015-9751-7
CrossRef Full Text | Google Scholar
Фигейра, Р. Б., Силва, С. Дж., Перейра, Е. В., и Сальта, М. М. (2013). Гибридные уреасиликатные покрытия для защиты от коррозии оцинкованной стали в цементных средах. J. Electrochem Soc. 160, C467–C479. doi: 10.1149/2.033310jes
CrossRef Full Text | Google Scholar
Фигейра, Р. Б., Силва, С. Дж., Перейра, Е. В., и Салта, М. М. (2014). Спиртово-аминосиликатные гибридные покрытия для защиты от коррозии оцинкованной стали в растворе. Дж. Электрохим. соц. 161, C349–C362. doi: 10.1149/2.103406jes
CrossRef Full Text | Google Scholar
Франциско Дж. С., Капелосси В. Р. и Аоки И. В. (2014). Оценка предварительной антикоррозионной обработки сульфосиланом оцинкованной стали по сравнению с фосфатом под эпоксидным покрытием на водной основе. Электрохим. Acta 124, 128–136. doi: 10.1016/j.electacta.2013.09.144
CrossRef Полный текст | Google Scholar
Фудзита С. и Мизуно Д. (2007). Коррозия и методы испытаний на коррозию оцинкованных стальных листов на автомобилях. Коррос. науч. 49, 211–219. doi: 10.1016/j.corsci.2006.05.034
Полный текст CrossRef | Google Scholar
Ганди, Дж. С., и ван Оой, В. Дж. (2004). Улучшенная защита алюминиевых сплавов от коррозии электроосаждением силанов. Дж. Матер. англ. Производительность 13, 475–480. doi: 10.1361/105994016
Полный текст CrossRef | Google Scholar
Ган К., Линъянь Л., Цзиньтан Л., Чуньшань К. и Чжун З. (2010). Исследование конверсионного покрытия из солей лантана, модифицированного лимонной кислотой, на горячеоцинкованной стали. J. Редкие земли 28, 461–465. doi: 10.1016/S1002-0721(09)60134-4
Полный текст CrossRef | Google Scholar
Геллинг В. Дж., Вист М. М., Таллман Д. Э., Бирваген Г. П. и Уоллес Г. Г. (2001). Электропроводящие полимеры для защиты от коррозии: 4. Исследования поли(3-октилпиррола) и поли(3-октадецилпиррола) на алюминиевом сплаве 2024-Т3. Прог. Орг. Пальто. 43, 149–157. doi: 10.1016/S0300-9440(01)00186-2
Полный текст CrossRef | Google Scholar
Гонг Л. -Х., Тан Р.-Р., Чжу Ю.-К. и Чен Д.-Л. (2012). Влияние силанового аппрета на конверсионное пленкообразование оцинкованной стали, обработанной солью церия. Междунар. Дж. Мин. Металл. Матер. 19, 800–804. doi: 10.1007/s12613-012-0631-1
Полный текст CrossRef | Google Scholar
Грундмайер Г., Шмидт В. и Стратманн М. (2000). Защита от коррозии органическими покрытиями: электрохимический механизм и новые методы исследования. Электрохим. Acta 45, 2515–2533. doi: 10.1016/S0013-4686(00)00348-0
Полный текст CrossRef | Google Scholar
Харуяма С. и Судо С. (1993). Электрохимический импеданс для крупной структуры в почве. Электрохим. Акта 38, 1857–1865 гг. doi: 10.1016/0013-4686(93)80307-L
CrossRef Full Text | Google Scholar
Хинтон Б. и Уилсон Л. (1989). Ингибирование коррозии цинка хлоридом серы. Коррос. науч. 29, 967–985. doi: 10.1016/0010-938x(89)
CrossRef Full Text | Google Scholar
Ху, Дж. , Чжан, Дж., и Цао, К. (2003). Определение водопоглощения и диффузии иона Cl- в эпоксидной грунтовке на алюминиевых сплавах в растворе NaCl методом электрохимической импедансной спектроскопии. Прог. Орг. Пальто. 46, 273–279. doi: 10.1016/S0300-9440(03)00010-9
Полный текст CrossRef | Google Scholar
Hu, J.-M., Liu, L., Zhang, J.-Q., and Cao, C.-N. (2006). Влияние потенциала электроосаждения на коррозионные свойства пленок бис-1,2-[триэтоксисилил]этана на алюминиевом сплаве. Электрохим. Acta 51, 3944–3949. doi: 10.1016/j.electacta.2005.11.008
CrossRef Полный текст | Google Scholar
Hu, J.-M., Liu, L., Zhang, J.-Q., and Cao, C.-N. (2007). Электроосаждение силановых пленок на алюминиевых сплавах для защиты от коррозии. Прог. Орг. Пальто. 58, 265–271. doi: 10.1016/j.porgcoat.2006.11.008
CrossRef Полный текст | Google Scholar
Джафарзаде С., Адхикари А., Сандалл П.-Э. и Пан Дж. (2011). Исследование проводящего полимера PANI-MeSA, диспергированного в отверждаемом УФ-излучением полиэфирном акрилате, на оцинкованной стали в качестве антикоррозионного покрытия. Прог. Орг. Пальто. 70, 108–115. doi: 10.1016/j.porgcoat.2010.10.011
CrossRef Полный текст | Google Scholar
Цзя, М.-З., Чжан, З., Руан, и Ву, Ф.-М. (2013). Ингибирующее коррозию действие самособирающихся пленок производных имидазола для нержавеющей стали 316. Поверхностная технология. 42, 23–27.
Google Scholar
Цзян, М.-Ю., Ву, Л.-К., Ху, Дж.-М., и Чжан, Дж.-К. (2015). Эпоксидные покрытия с добавлением силана на алюминиевом сплаве (AA2024). Часть 1: улучшенные антикоррозионные характеристики. Коррос. науч. 92, 118–126. doi: 10.1016/j.corsci.2014.11.046
CrossRef Полный текст | Google Scholar
Каниа Х. и Либерски П. (2014). «Синергетическое влияние добавления Al, Ni и Pb в цинковую ванну на кинетику роста и структуру покрытий», в Solid State Phenomena , (Швейцария: Trans Tech Publication), 115–120. doi: 10.4028/www.scientific.net/ssp.212.115
CrossRef Full Text | Google Scholar
Каракси, Э. К., Картсонакис, И. А., и Харитидис, К. А. (2019 г.). Оценка самовосстанавливающихся покрытий на основе эпоксидной смолы, содержащих микрокапсулы, нанесенных на горячеоцинкованную сталь. Фронт. Матер. 6:222. doi: 10.3389/fmats.2019.00222
Полный текст CrossRef | Google Scholar
Картсонакис И., Баласкас А., Кумулос Э., Харитидис К. и Кордас Г. (2012). Включение керамических наноконтейнеров в эпоксидные покрытия для защиты от коррозии горячеоцинкованной стали. Коррос. науч. 57, 30–41. doi: 10.1016/j.corsci.2011.12.037
Полнотекстовая перекрестная ссылка | Google Scholar
Картсонакис И. А., Станчу С. Г., Матей А. А., Христу Р., Карантонис А. и Харитидис К. А. (2016). Сравнительное исследование ингибиторов коррозии на горячеоцинкованной стали. Коррос. науч. 112, 289–307. doi: 10.1016/j.corsci.2016.07.030
CrossRef Полный текст | Google Scholar
Кеддам М., Хьюго-ле-Гофф А., Такеноути Х., Тьерри Д. и Аревало М. (1992). Влияние тонкого слоя электролита на процесс коррозии цинка в хлоридсодержащих растворах. Коррос. науч. 33, 1243–1252. doi: 10.1016/0010-938X(92)-N
Полный текст CrossRef | Google Scholar
Кобаяши Ю. и Фудзивара Ю. (2006). Защита от коррозии цериевого конверсионного покрытия, модифицированного самоорганизующимся слоем моно-н-алкилового эфира фосфорной кислоты. Электрохим. Твердотельное письмо. 9, В15–В18. doi: 10.1149/1.2162328
Полный текст CrossRef | Google Scholar
Кох, Г. Х., Бронгерс, М. П., Томпсон, Н. Г., Вирмани, Ю. П., и Пайер, Дж. Х. (2002). Стоимость коррозии и профилактические стратегии в США. Вашингтон, округ Колумбия: Федеральное управление автомобильных дорог.
Google Scholar
Крылова И. (2001). Живопись электроосаждением на пороге 21 века. Прогр. Орг. Пальто. 42, 119–131. doi: 10.1016/S0300-9440(01)00146-1
Полный текст CrossRef | Google Scholar
Кумар Э., Селвараджан П. и Мутурадж Д. (2012). Получение и характеристика нанокомпозита полианилин/диоксид церия (CeO 2) посредством полимеризации in situ. Дж. Матер. науч. 47, 7148–7156. doi: 10.1007/s10853-012-6655-0
Полный текст CrossRef | Google Scholar
Le, HNT, Garcia, B., Deslouis, C., and Le Xuan, Q. (2001). Защита от коррозии и проводящие полимеры: полипиррольные пленки на железе. Электрохим. Acta 46, 4259–4272. doi: 10.1016/s0013-4686(01)00699-5
Полный текст CrossRef | Google Scholar
Li, M., Yang, Y.-Q., Liu, L., Hu, J.-M., and Zhang, J.-Q. (2010). Электроассистированное приготовление композиционных пленок додецилтриметоксисилан/TiO2 для защиты от коррозии AA2024-T3 (алюминиевый сплав). Электрохим. Acta 55, 3008–3014. doi: 10.1016/j.electacta.2009.12.081
CrossRef Полный текст | Google Scholar
Li, C., Liang, T., Ma, R., Du, A., Fan, Y., Zhao, X., et al. (2020). Супергидрофобная поверхность, содержащая соль церия и органосилан, для защиты от коррозии оцинкованной стали. J. Alloys Compd. 825:153921. doi: 10.1016/j.jallcom.2020.153921
Полный текст CrossRef | Google Scholar
Лин, К.-В. (1999). Влияние хроматных конверсионных покрытий с полиакриловой кислотой и без нее на способность к прессованию, свойства сдвига и долговечность ламинатов из оцинкованной стали с использованием поливинилбутираля в качестве основного материала. Дж. Матер. науч. 34, 3951–3956. doi: 10.1023/A:10046
931Полный текст CrossRef | Google Scholar
Лю Ю.-Х., Сюй Ж.-Б., Чжан Ж.-Т. и Ху Ж.-М. (2017). Промежуточный слой из пленки электроосажденного кремнезема для активной защиты от коррозии. Коррос. науч. 120, 61–74. doi: 10.1016/j.corsci.2017.01.017
CrossRef Полный текст | Google Scholar
Лонги М., Кунста С. Р., Белтрами Л. В. Р., Керстнер Э. К., Сильва Филью С. И., Сарменто В. Х. В. и др. (2015). Влияние количеств тетраэтоксисилана (ТЭОС) на антикоррозионные свойства гибридных покрытий силоксан-ПММА на подложках из оцинкованной стали. Матер. Рез. 18, 1140–1155. doi: 10.1590/1516-1439.321614
Полный текст CrossRef | Google Scholar
Лу, Дж.-Т., Ву, Х.-Дж., Ганг, К., Че, К.-С., и Сюй, К.-Ю. (2006). Рост и коррозионное поведение пленки редкоземельных элементов на горячеоцинкованной стали. Пер. Цветной металл Soc. Китай 16, 1397–1401. doi: 10.1016/S1003-6326(07)60027-2
Полный текст CrossRef | Google Scholar
Maaß, P., Peissker, P. and Ahner, C. (2011). Справочник по горячему цинкованию. Хобокен, Нью-Джерси: Интернет-библиотека Wiley
Google Scholar
Маэда, С. (1996). Химия поверхности оцинкованных стальных листов, имеющая отношение к адгезионным характеристикам. Прог. Орг. Пальто. 28, 227–238. doi: 10.1016/0300-9440(95)00610-9
CrossRef Full Text | Google Scholar
Махдавиан М. и Аттар М. (2006). Еще один подход к анализу лакокрасочных покрытий с помощью измерения ЭИС: фазовый угол на высоких частотах. Коррос. науч. 48, 4152–4157. doi: 10.1016/j.corsci.2006.03.012
Полнотекстовая перекрестная ссылка | Google Scholar
Мейтленд, К. (1962). Факторы, влияющие на электролитическую стойкость полимерных пленок. Выкл. Дайджест 34:972.
Google Scholar
Майд, М. Т., Шахраби, Т., и Рамезанзаде, Б. (2019). Модификация поверхности низкоуглеродистой стали эффективной антикоррозионной нанокомпозитной пленкой на основе неодим-полиакриловой кислоты-бензимидазол. J. Alloys Compd. 783, 952–968. doi: 10.1016/j.jallcom.2018.12.367
Полнотекстовая перекрестная ссылка | Google Scholar
Малекзаде М., Сивакуган Н., Казум О. и Матан Б. (2017). Влияние электродов из оцинкованной стали с полианилиновым покрытием на электрокинетическое осаждение буровых растворов драгирования. Кан. Геотех. Дж. 54, 1150–1157. doi: 10.1139/cgj-2016-0127
Полный текст CrossRef | Google Scholar
Манна, М. (2009). Влияние стальной подложки на обработку фосфатированием: возможность имитации поверхности арматурного стержня ТМТ. Коррос. науч. 51, 451–457. doi: 10.1016/j.corsci.2008.11.021
CrossRef Полный текст | Google Scholar
Мансфельд Ф. и Цай К. (1991). Определение износа покрытия с помощью ЭИС: I. Основные соотношения. Коррозия 47, 958–963. doi: 10.5006/1.3585209
Полный текст CrossRef | Google Scholar
Монтемор, М., и Феррейра, М. (2007). Наночастицы, активированные солью церия, в качестве наполнителей для силановых пленок: оценка эффективности ингибирования коррозии на подложках из оцинкованной стали. Электрохим. Acta 52, 6976–6987. doi: 10.1016/j.electacta.2007.05.022
CrossRef Полный текст | Google Scholar
Монтемор М., Росквист А., Фагерхольм Х. и Феррейра М. (2004). Раннее коррозионное поведение горячеоцинкованной стали, предварительно обработанной бис-1,2-(триэтоксисилил)этаном. Прог. Орг. Пальто. 51, 188–194. doi: 10.1016/j.porgcoat.2004.07.011
CrossRef Полный текст | Google Scholar
Монтемор М., Симойнс А. и Феррейра М. (2001). Состав и поведение пленок церия на оцинкованной стали. Прог. Орг. Пальто. 43, 274–281. doi: 10.1016/S0300-9440(01)00209-0
Полный текст CrossRef | Google Scholar
Монтемор, М., Симоес, А., и Феррейра, М. (2002). Состав и коррозионное поведение оцинкованной стали, обработанной солями редкоземельных элементов: влияние катиона. Прог. Орг. Пальто. 44, 111–120. doi: 10.1016/S0300-9440(01)00250-8
Полный текст CrossRef | Google Scholar
Монтемор М., Симоес А., Феррейра М. и Кармезим М. (2008). Состав и коррозионная стойкость конверсионных цериевых пленок на магниевом сплаве АЗ31 и их связь с солевым анионом. Приложение. Поверхностные науки. 254, 1806–1814 гг. doi: 10.1016/j.apsusc.2007.07.187
CrossRef Полный текст | Google Scholar
Монтемор М., Трабелси В., Желудевич М. и Феррейра М. (2006). Модификация растворов биссилана катионами редкоземельных элементов для улучшения защиты от коррозии оцинкованных стальных подложек. Прог,. Орг. Пальто. 57, 67–77. doi: 10.1016/j.porgcoat.2006.06.009
CrossRef Полный текст | Google Scholar
Моримото Ю., Хонда К., Нисимура К., Танака С., Такахаши А., Шиндо Х. и др. (2002). Горячеоцинкованный стальной лист «super dyma» из сплава Zn-Al-Mg-Si с превосходной коррозионной стойкостью. Синниттэцу Гихо 22–24.
Google Scholar
Мотте К., Поэльман М., Рубрук А., Федель М., Дефлориан Ф. и Оливье М.-Г. (2012). Улучшение коррозионной защиты оцинкованной стали путем введения в силановый слой модифицированных лантанидами наноглин. Прог. Орг. Пальто. 74, 326–333. doi: 10.1016/j.porgcoat.2011.12.001
CrossRef Полный текст | Google Scholar
Наои К., Оура Ю., Маеда М. и Накамура С. (1995). Электрохимия полипиррольной пленки (I), легированной поверхностно-активными веществами: формирование столбчатой структуры путем электрополимеризации. Дж. Электрохим. соц. 142:417. doi: 10.1149/1.2044042
Полный текст CrossRef | Google Scholar
Обот И. , Мадханкумар А., Уморен С. и Гасем З. (2015). Защита поверхности мягкой стали производными бензимидазола: экспериментальный и теоретический подход. J. Прилипатели. науч. Технол. 29, 21:30–21:52. doi: 10.1080/01694243.2015.1058544
CrossRef Полный текст | Google Scholar
Олад, А., и Расули, Х. (2010). Усиленное антикоррозионное покрытие на основе проводящего нанокомпозита полианилин/цинк. J. Appl. Полим. науч. 115, 2221–2227. doi: 10.1002/app.31320
Полный текст CrossRef | Google Scholar
Паланивел В., Чжу Д. и Оойдж В. Дж. В. (2003). Силановые пленки, наполненные наночастицами, как заменители хромата для алюминиевых сплавов. Прог. Орг. Пальто. 47, 384–392. doi: 10.1016/j.porgcoat.2003.08.015
CrossRef Полный текст | Google Scholar
Павлиду Э., Пистофидис Н., Вурлиас Г. и Стергиудис Г. (2005). Изменение направления роста цинковых покрытий, связанное с добавками элементов в ванну цинкования. Матер. лат. 59, 1619–1622. doi: 10.1016/j.matlet.2004.08.045
CrossRef Полный текст | Google Scholar
Пэн С., Се С.-К., Сяо Ф. и Лу Дж.-Т. (2020). Коррозионное поведение блесток на партии горячеоцинкованной Zn-0. 05 Покрытие Al-0,2Sb в 3,5 мас.% растворе NaCl. Коррос. науч. 163:108237. doi: 10.1016/j.corsci.2019.108237
CrossRef Полный текст | Google Scholar
Перссон Д., Михайлов А. и Тьерри Д. (2007). Полевые исследования коррозии при сушке закрытых цинковых поверхностей. Мат. Коррос. 58, 452–462. doi: 10.1002/maco.200604029
Полный текст CrossRef | Google Scholar
Пистофидис Н., Вурлиас Г., Конидарис С., Павлиду Э. и Стергиудис Г. (2007). Совместное влияние никеля и висмута на структуру горячеоцинкованных покрытий. Матер. Позволять. 61, 2007–2010 гг. doi: 10.1016/j.matlet.2006.08.002
Полный текст CrossRef | Google Scholar
Покорный П., Колиско Дж., Балик Л. и Новак П. (2016). Влияние химического состава стали на структуру горячеоцинкованного покрытия. Металлургия 55, 115–118.
Google Scholar
Qu, Q., Yan, C., Wan, Y., and Cao, C. (2002). Влияние NaCl и SO2 на начальную атмосферную коррозию цинка. Коррос. науч. 44, 2789–2803. doi: 10.1016/S0010-938X(02)00076-8
Полный текст CrossRef | Google Scholar
Racicot, R., Brown, R. and Yang, S.C. (1997). Защита алюминиевых сплавов от коррозии двухнитевым полианилином. Синтез. Встретились. 85, 1263–1264. дои: 10.1016/s0379-6779(97)80232-9
CrossRef Полный текст | Google Scholar
Расико Р., Кларк Р. Л., Лю Х. Б., Ян С., Алиас М. и Браун Р. (1995). Антикоррозионные исследования новых токопроводящих полимерных покрытий на алюминиевых сплавах. MRS Online Proc. Библиотечная арка. 413, 529–534. doi: 10.1557/proc-413-529
Полный текст CrossRef | Google Scholar
Ротели Б., Кокс Г. и Литреал В. (1932). Влияние рН на продукты коррозии и скорость коррозии цинка в насыщенных кислородом водных растворах. Мет. Сплавы 3, 73–76.
Google Scholar
Радд А.Л., Бреслин С.Б. и Мансфельд Ф. (2000). Защита от коррозии, обеспечиваемая конверсионными покрытиями из редкоземельных элементов, нанесенными на магний. Коррос. науч. 42, 275–288. doi: 10.1016/s0010-938x(99)00076-1
CrossRef Full Text | Google Scholar
Safaeirad, M., Toroghinejad, M., and Ashrafizadeh, F. (2008). Влияние микроструктуры и текстуры на формуемость и механические свойства горячеоцинкованных стальных листов. Дж. Матер. Процесс. Технол. 196, 205–212. doi: 10.1016/j.jmatprotec.2007.05.035
Полный текст CrossRef | Google Scholar
Ширмайзен М. и Бек Ф. (1989). Электропокрытие железа и других металлов полипирролом. J. Appl. Электрохим. 19, 401–409. doi: 10.1007/BF01015243
Полный текст CrossRef | Google Scholar
Шульц В. и Тиле М. (2012). Общее горячее цинкование. Париж: Евгений, 30–36.
Google Scholar
Секине И., Сакагучи К. и Юаса М. (1992). Оценка и прогноз деградации пленок покрытий по частоте при максимальном фазовом угле. Дж. Пальто. Технол. 64, 45–49.
Google Scholar
Сере П., Кулкаси Дж. Д., Элснер К. И. и Ди Сарли А. Р. (1999). Взаимосвязь между текстурой и коррозионной стойкостью горячеоцинкованных стальных листов. Поверхностное покрытие. Технол. 122, 143–149. doi: 10.1016/s0257-8972(99)00325-4
Полный текст CrossRef | Академия Google
Сере, П.Р., Дейя, К., Эгли, В.А., Эльснер, К.И., и Ди Сарли, А.Р. (2014). Защита оцинкованной стали силанами: сравнение с хромом (VI). Дж. Матер. англ. Производительность 23, 342–348. doi: 10.1007/s11665-013-0746-1
Полный текст CrossRef | Google Scholar
Шахам Р., Авнир Д. и Мандлер Д. (1999). Электроосаждение метилированных золь-гель пленок на проводящие поверхности. Доп. Матер. 11, 384–388. doi: 10.1002/(sici)1521-4095(199903)11:5<384::aid-adma384>3.0.co;2-m
CrossRef Full Text | Google Scholar
Шеффер М. , Гройсман А. и Мандлер Д. (2003). Электроосаждение золь-гель пленок на Al для защиты от коррозии. Коррос. науч. 45, 2893–2904. doi: 10.1016/S0010-938X(03)00106-9
Полный текст CrossRef | Google Scholar
Шинде В., Сайнкар С., Гангал С. и Патил П. (2006). Синтез антикоррозионных поли(2,5-диметиланилиновых) покрытий на низкоуглеродистой стали. Дж.Матер. науч. 41, 2851–2858. doi: 10.1007/s10853-006-2375-7
CrossRef Full Text | Google Scholar
Спинкс, Г. М., Доминис, А. Дж., Уоллес, Г. Г., и Таллман, Д. Е. (2002). Электроактивные проводящие полимеры для защиты от коррозии. J. Твердотельная электрохимия. 6, 85–100. doi: 10.1007/s100080100211
Полный текст CrossRef | Google Scholar
Струнц, В. (2000). Диэлектрическая релаксация в барьерных покрытиях: процесс квадратного корня из времени. Прог. Орг. Пальто. 39, 49–60. doi: 10.1016/S0300-9440(00)00099-0
Полный текст CrossRef | Google Scholar
Штрутценбергер Дж. и Фадерл Дж. (1998). Затвердевание и образование блесток при горячем цинковании цинковых покрытий. Металл. Матер. Транс. А 29, 631–646. doi: 10.1007/s11661-998-0144-8
CrossRef Full Text | Google Scholar
Su, H.-Y., Chen, P.-L., and Lin, C.-S. (2016). Золь-гель покрытия, легированные органосиланом и церием, для улучшения свойств горячеоцинкованной стали. Коррос. науч. 102, 63–71. doi: 10.1016/j.corsci.2015.09.019
CrossRef Полный текст | Google Scholar
Субраманиан В. и Ван Оой В. (1998). Влияние функциональной группы амина на скорость коррозии железа, покрытого пленками органофункциональных силанов. Коррозия 54, 204–215. doi: 10.5006/1.3284845
Полный текст CrossRef | Google Scholar
Сун, З. В., Конг, Г., Че, К. С., Ван, Ю. К., и Мяо, X. Р. (2019). Рост конверсионного покрытия на основе церия на сплаве Zn-5% Al. Поверхностный анализ интерфейса. 51, 465–474. doi: 10.1002/sia.6603
Полный текст CrossRef | Google Scholar
Свобода Дж. , Кудлачек Дж., Крайбих В. и Легутко С. (2018). «Альтернативные методы химической предварительной обработки поверхности горячего цинкования для адгезии органических покрытий», в Advances in Manufacturing , редакторы А. Хамрол, О. Цишак, С. Легутко и М. Юрчик, (Берлин: Springer) , 687–695. doi: 10.1007/978-3-319-68619-6_66
Полный текст CrossRef | Академия Google
Таллман, Д., Пае, Ю., и Бирваген, Г. (1999). Проводящие полимеры и коррозия: полианилин на стали. Коррозия 55, 779–786. doi: 10.5006/1.3284033
Полный текст CrossRef | Google Scholar
Tallman, D., Pae, Y.-Q., and Bierwagen, G.P. (2000). Проводящие полимеры и коррозия: часть 2 — Полианилин на алюминиевых сплавах. Коррозия 56, 401–410. doi: 10.5006/1.3280544
Полный текст CrossRef | Google Scholar
Таллман Д. Э., Спинкс Г., Доминис А. и Уоллес Г. Г. (2002). Электроактивные проводящие полимеры для защиты от коррозии. J. Твердотельная электрохимия. 6, 73–84. doi: 10.1007/s100080100211
Полный текст CrossRef | Google Scholar
Тяньлан П. и Жуйлинь М. (2009). Редкоземельные элементы и силан в качестве заменителей хромата для защиты от коррозии оцинкованной стали. J. Редкие земли 27, 159–163. doi: 10.1016/S1002-0721(08)60212-4
Полный текст CrossRef | Google Scholar
Цай, К.-Ю., Лю, Дж.-С., Чен, П.-Л., и Лин, К.-С. (2010). Двухэтапное фосфатно-молибдатное пассивирующее покрытие вальцеванием стального листа, оцинкованного горячим способом. Коррос. науч. 52, 3385–3393. doi: 10.1016/j.corsci.2010.06.020
CrossRef Полный текст | Google Scholar
Ван Оой, В., и Чайлд, Т. (1998). Защита металлов с помощью силановых аппретов. Хим.техн. 28:26.
Google Scholar
Van Ooij, W., Zhu, D., Prasad, G., Jayaseelan, S., Fu, Y. и Teredesai, N. (2000). Заменители хромата на основе силана для контроля коррозии, адгезии краски и склеивания резины. Поверхностный инж. 16, 386–396. doi: 10.1179/026708400101517369
CrossRef Full Text | Google Scholar
van Ooij, WJ, and Zhu, D. (2001). Электрохимическая импедансная спектроскопия бис-[триэтоксисилилпропил]тетрасульфида на подложках Al 2024-T3. Коррозия 57, 413–427. doi: 10.5006/1.32
Полный текст CrossRef | Google Scholar
Ван Шафтинген Т., Ле Пен К., Террин Х. и Хорценбергер Ф. (2004). Исследование барьерных свойств силанов на холоднокатаной стали. Электрохим. Acta 49, 2997–3004. doi: 10.1016/j.electacta.2004.01.059
CrossRef Полный текст | Google Scholar
Винсент Г., Бонассо Н., Лекомт Дж., Колине Б., Гей Б. и Эслинг К. (2006). Взаимосвязь между вязкостью разрушения и характеристиками границ зерен в горячеоцинкованных цинковых покрытиях. Дж. Матер. науч. 41, 5966–5975. doi: 10.1007/s10853-006-0274-6
Полный текст CrossRef | Google Scholar
Фогельсанг, Дж., и Струнц, В. (2001). Новая интерпретация электрохимических данных, полученных с органических барьерных покрытий. Электрохим. Acta 46, 3817–3826. doi: 10.1016/S0013-4686(01)00668-5
CrossRef Full Text | Google Scholar
Вурлиас Г., Пистофидис Н., Стергиудис Г. и Ципас Д. (2004). Влияние легирующих элементов на характер кристаллизации и свойства гальванических покрытий. Хрусталь Рез. Технол. 39, 23–29. doi: 10.1002/crat.200310144
Полный текст CrossRef | Google Scholar
Ван К., Цзян Ф. и Ван Ф. (2004). Характеристика и коррозионная стойкость цериевых химических конверсионных покрытий для нержавеющей стали 304. Коррос. науч. 46, 75–89. doi: 10.1016/S0010-938X(03)00135-5
Полный текст CrossRef | Google Scholar
Вейдлих К., Мангольд К.-М. и Юттнер К. (2005). Исследование EQCM ионного обмена полипиррола с различными противоионами в разных электролитах. Электрохим. Acta 50, 1547–1552 гг. doi: 10.1016/j.electacta.2004.10.032
CrossRef Полный текст | Google Scholar
Вэн, К.-Дж., Чанг, К.-Х., Линь, И.-Л., Е, Дж. -М., Вэй, Ю., Хсу, К.-Л., и др. др. (2012). Перспективные антикоррозионные материалы для покрытий на основе фторполианилин-кремнеземных композитов с синергетическим эффектом супергидрофобности и окислительно-восстановительной каталитической способности. Поверхностное покрытие. Технол. 207, 42–49. doi: 10.1016/j.surfcoat.2012.04.097
CrossRef Полный текст | Google Scholar
Ву Х., Ройкрофт П. и Джейкоб Р. (1993). Электроосаждение органофункциональных силанов и его влияние на структурное адгезионное соединение. J. Прилипатели. науч. Технол. 7, 681–697. doi: 10.1163/156856193X00367
Полный текст CrossRef | Google Scholar
Xingwen, Y., Chunan, C., Zhiming, Y., Derui, Z., and Zhongda, Y. (2000). Коррозионное поведение конверсионных покрытий из редкоземельных металлов (РЗМ) на алюминиевом сплаве LY12. Матер. науч. Eng.A 284, 56–63. doi: 10.1016/s0921-5093(00)00795-4
CrossRef Full Text | Google Scholar
Xingwen, Y., Chunan, C. , Zhiming, Y., Derui, Z. и Zhongda, Y. (2001). Исследование двухслойного конверсионного покрытия редкоземельными металлами на алюминиевом сплаве LY12. Коррос. науч. 43, 1283–1294. doi: 10.1016/s0010-938x(00)00141-4
CrossRef Full Text | Google Scholar
Сюй, Дж.-Б., Цао, Ю.-К., Фанг, Л. и Ху, Дж.-М. (2018). Одноэтапная подготовка наполненных ингибитором наноконтейнеров из диоксида кремния для самовосстанавливающихся покрытий. Коррос. науч. 140, 349–362. doi: 10.1016/j.corsci.2018.05.030
CrossRef Полный текст | Google Scholar
Xue, D., and Van Ooij, WJ (2013). Улучшение коррозионных характеристик сталей, оцинкованных горячим способом (HDG), путем электроосаждения бис-[триэтоксисилил]этановых (BTSE) покрытий, модифицированных эпоксидной смолой и сложным эфиром. Прог. Орг. Пальто. 76, 1095–1102. doi: 10.1016/j.porgcoat.2013.03.004
CrossRef Полный текст | Google Scholar
Ялчинкая С., Тюкен Т., Языджи Б. и Эрбиль М. (2010). Электрохимический синтез и коррозионное поведение поли(пиррол-со-о-анизидин-со-о-толуидина). Текущее заявл. физ. 10, 783–789. doi: 10.1016/j.cap.2009.09.015
CrossRef Full Text | Google Scholar
Ямамото Ю., Нишихара Х. и Арамаки К. (1993). Самособирающиеся слои алкантиолов на меди для защиты от коррозии. Дж. Электрохим. соц. 140, 436–443. doi: 10.1149/1.2221064
Полный текст CrossRef | Google Scholar
Ян X., Ли Б., Ван Х. и Хоу Б. (2010). Антикоррозионные свойства полианилиновых наноструктур на мягкой стали. Прог. Орг. Пальто. 69, 267–271. doi: 10.1016/j.porgcoat.2010.06.004
CrossRef Полный текст | Google Scholar
Яньхуа З., Чжуан Дж., Юншэн Ю. и Сянгуан З. (2013). Исследование антикоррозионных свойств редкоземельного ингибитора для стали Х70. J. Редкие земли 31, 734–740. doi: 10.1016/S1002-0721(12)60350-0
Полный текст CrossRef | Google Scholar
Яо, Б., Ван, Г., Йе, Дж., и Ли, X. (2008). Ингибирование коррозии углеродистой стали полианилиновыми нановолокнами. Матер. лат. 62, 1775–1778 гг. doi: 10.1016/j.matlet.2007.10.001
CrossRef Полный текст | Google Scholar
Йоманс, С. (2004). Арматура из оцинкованной стали в бетоне. Амстердам: Эльзевир.
Google Scholar
Чжан Х. и Цзо Ю. (2008). Повышение коррозионной стойкости конверсионных пленок церия на алюминиевом сплаве путем последующей обработки фосфатом. Заяв. Поверхностные науки. 254, 4930–4935. doi: 10.1016/j.apsusc.2007.12.066
Полнотекстовая перекрестная ссылка | Google Scholar
Чжан Дж., Ху Дж., Чжан Дж. и Цао К. (2004). Исследования моделей импеданса и характеристик водного транспорта металлов с полипропиленовым покрытием в растворе NaCl. Прог. Орг. Пальто. 49, 293–301. doi: 10.1016/S0300-9440(03)00115-2
Полный текст CrossRef | Google Scholar
Чжан С., Ян Б., Конг Г. и Лу Дж. (2018). Влияние предварительной обработки силикатом на лантановое конверсионное покрытие горячеоцинкованной стали. Междунар. Дж. Электрохим. науч. 13, 10247–10258. doi: 10.20964/2018.11.04
CrossRef Полный текст | Google Scholar
Чжан С. Х., Ян Б., Чжай В., Ван З. Г. и Ли С. (2019). «Влияние лимонной кислоты на конверсионное цериевое покрытие горячеоцинкованной стали», в Key Engineering Materials (Швейцария: Trans Tech Publication), 144–151. doi: 10.4028/www.scientific.net/kem.814.144
Полный текст CrossRef | Google Scholar
Чжан, X., и Сюй, Н. (2007). Прогнозирование жизни оцинкованной стали в Интернете. Коррос. прот. 28, 49–53. doi: 10.3969/j.issn.1005-748X.2007.01.015
Полный текст CrossRef | Google Scholar
Чжан З., Чен С., Ли Ю., Ли С. и Ван Л. (2009). Исследование ингибирования коррозии железа имидазолом и его производными самоорганизующимися пленками. Коррос. науч. 51, 291–300. doi: 10.1016/j.corsci.2008.10.040
CrossRef Полный текст | Google Scholar
Желудкевич М.Л., Серра Р., Монтемор М.Ф. и Феррейра М. Г. (2005). Резервуары оксидных наночастиц для хранения и длительного высвобождения ингибиторов коррозии. Электрохим. Коммуни. 7, 836–840. doi: 10.1016/j.elecom.2005.04.039
Полный текст CrossRef | Google Scholar
Чжэнь Ф. (2005). Простой разговор о теории прогноза срока службы покрытия. Пекин: Tsinghua Tongfang Knowledge Network Technology Co., Ltd.
Google Scholar
Zhou, C., Lu, X., Xin, Z., and Liu, J. (2013). Коррозионная стойкость нового полибензоксазинового покрытия с силан-функциональными группами на стали. Corros Sci. 70, 145–115. doi: 10.1016/j.corsci.2013.01.023
Полнотекстовая перекрестная ссылка | Google Scholar
Zhu, D., and van Ooij, WJ (2004). Повышенная коррозионная стойкость стали AA 2024-T3 и горячеоцинкованной стали с использованием смеси бис-[триэтоксисилилпропил]тетрасульфида и бис-[триметоксисилилпропил]амина. Электрохим. Acta 49, 1113–1125. doi: 10.1016/j.electacta.2003.10.023
CrossRef Полный текст | Google Scholar
Zuo, Y. , Pang, R., Li, W., Xiong, J. и Tang, Y. (2008). Оценка характеристик покрытия по вариациям фазовых углов в средне- и высокочастотной областях ЭИС. Коррос. науч. 50, 3322–3328. doi: 10.1016/j.corsci.2008.08.049
CrossRef Полный текст | Google Scholar
Улучшение внешнего вида горячеоцинкованной стали
Фото предоставлено НатинойАланой Фосса и Джоном Крживицки
Внешний вид партии горячеоцинкованной стали может быть загадкой. Различия в первоначальном внешнем виде покрытия от одного проекта к другому и естественное выветривание стали HDG часто вызывают путаницу и несоответствие ожиданий в сообществе дизайнеров. Профессионалы-проектировщики могут ожидать, что вся оцинкованная сталь будет постоянно сохранять блестящую, гладкую или блестящую поверхность, характерную для оцинкованного листового металла (например, воздуховоды ОВиК или гофрированные панели), и в конечном итоге будет иметь матово-серое покрытие после установки стали HDG на стройплощадке. . Это может привести к разочарованию в проектах, где ожидается определенная эстетика.
Для периодического производства горячего цинкования трудно точно контролировать металлургическую реакцию между железом и цинком, которая формирует покрытие HDG. Создание одинакового внешнего вида покрытия на различных стальных изделиях, которые они ежедневно обрабатывают, является невыполнимой задачей. Дизайн, спецификация, химический состав стали и методы изготовления — все это влияет на внешний вид покрытия HDG. Хотя внешний вид не влияет на долговечность или коррозионную стойкость стали HDG, он может повлиять на предполагаемое использование продукта. При правильном общении между профессиональным дизайнером, изготовителем и оцинковщиком большинство проблем с внешним видом можно смягчить. Однако, когда проекты требуют особой эстетики, к оцинкованной поверхности можно применить дополнительную обработку, чтобы изменить окончательный вид. Эти варианты последующей обработки, по сути, обеспечивают неограниченный окончательный внешний вид стали HDG.
Первоначальный внешний вид HDG
Поскольку цинковое покрытие подвергается воздействию естественных циклов влажного и высыхания в окружающей среде, оно начинает формировать пассивный слой продуктов коррозии на поверхности. Через период от шести месяцев до двух лет цинковая патина полностью разовьется. Образование цинковой патины создает матовый, однородный и выветренный серый вид, сглаживая различия, которые могли существовать изначально (рис. 1). Первоначальные неоднородности покрытия исчезают через короткое время, и внешний вид на протяжении большей части срока службы стали остается однородным. Это свойство оцинкованной стали важно для применений, которые могут быть не очень чувствительны к эстетике.
Конструкция и спецификация
Первоначальный внешний вид стали HDG трудно предсказать и контролировать по разным причинам, включая дизайн, технические характеристики, химический состав стали, напряжение, возникающее при обработке стали, и скорость охлаждения после цинкования ( Read the American Публикация Ассоциации гальванотехников (AGA) о внешнем виде горячеоцинкованного покрытия (2016)) . На самом деле известно, что сталь HDG может иметь различные первоначальные характеристики: яркую и блестящую, тусклую, покрытую блестками, пятнистую или даже матово-серую (рис. 2). Эти различия могут возникать между отдельными произведениями и даже внутри частей одного и того же произведения.
Рисунок 2: В этом проекте горячее цинкование привело к различным исходным видам различных стальных изделий, включая яркие и блестящие, матово-серые, блестящие и крапчатые.
Многие не осознают, что гальванизатор имеет ограниченный контроль над внешним видом поверхности и отделкой покрытия HDG. Вместо этого для оптимальной защиты от коррозии и эстетики требуются совместные усилия и открытая коммуникация между профессиональным дизайнером, изготовителем и гальванистом. Спецификаторы должны обращаться к ASTM A385, Стандартная практика обеспечения высококачественных цинковых покрытий (горячее цинкование) , для методов проектирования и изготовления, направленных на оптимизацию стальных деталей для улучшенного горячего цинкования. Основой спецификации является правильный выбор стали, так как она оказывает наибольшее влияние на первоначальный вид, гладкость, структуру и толщину оцинкованного покрытия. Спецификация также определяет проблемы проектирования, такие как перекрывающиеся поверхности, различная толщина материала в сборке, движущиеся части внутри сборки и сквозные отверстия, которые требуют особого внимания для нанесения покрытия. Крайне важны в этой спецификации детали вентиляционных и дренажных отверстий для обеспечения свободного потока чистящих растворов, а также воздуха и цинка, необходимых для гладкого и однородного покрытия. Эти детали, наряду с передовыми методами цинкования, позволят не только производить высококачественные гальванизированные покрытия, но также улучшать эстетику, снижать затраты и улучшать оборот.
Практический пример: Cliffwalk на подвесном мосту Капилано
Протягиваясь над туманным пространством вечнозеленой листвы, Cliffwalk на подвесном мосту Капилано в Ванкувере, Британская Колумбия, Канада, предлагает посетителям пройтись по открытому каньону внизу и полюбуйтесь живописным видом с уникальной точки зрения скалолаза. Расположение Cliffwalk затрудняет обслуживание или ремонт, поскольку арка висит на 90 м (295 футов) над рекой внизу. Кроме того, достопримечательность находится всего в нескольких милях от побережья Тихого океана, окружающего Ванкувер, из-за чего агрессивная влага постоянно контактирует с открытыми стальными элементами. Сталь HDG была смешана с другими материалами, такими как дерево, стекло, алюминий, сталь с дуплексным покрытием и атмосферостойкая сталь, чтобы создать ощущение легкости и воздушности. Естественная матово-серая эстетика стали HDG легко сочетается с обрывом скалы и лесной средой, не отвлекая внимания от прекрасного природного окружения. Эстетика и экологичность были ключевыми факторами в этом проекте, и горячее цинкование обеспечило и то, и другое.
Страницы: 1 2 3 4
09 Покрытия Разделы 05 Горячеоцинкованная сталь Спецификации металлов
Горячеоцинкованная сталь и предварительное цинкование: в чем разница?
Содержание
- I. Определение
- 1. Что такое горячее цинкование?
- 2. Что такое предварительное цинкование?
- II. Различия между горячим цинкованием погружением и предварительным цинкованием
- 1. Сравнение применений
- 2. Сравнение покрытий
- a. Толщина покрытия
- б. Постоянное покрытие
- c. Связка покрытия
- d. Формуемость покрытия
- e.
Внешний вид покрытия
- 3. 03. Сравнение стойкости к истиранию
- 4. Защитная защита
- Chinh Dai Steel – известный производитель оцинкованной стали
- Заключительные слова
Существует распространенное заблуждение, что любое цинковое покрытие можно назвать горячим цинкованием, но на самом деле это не так. это не так, поскольку предварительное цинкование также является популярным методом изготовления оцинкованной стали. Так в чем же между ними разница и какой из них обладает большим количеством преимуществ? Давайте узнаем ниже.
I. Определение
Прежде всего, нам нужно знать, как определить 02 наиболее популярных метода изготовления оцинкованной стали: горячее цинкование погружением и предварительное цинкование.
1. Что такое горячее цинкование?
Горячее цинкование — это процесс, при котором металл погружают в ванну с расплавленным цинком. Чтобы изготовить оцинкованную сталь с использованием этого метода, нам нужно выполнить 4 этапа: очистить поверхность, флюсование, горячее погружение и охлаждение.
Горячее цинкование погружением является одним из наиболее распространенных методов цинкования стали и других металлов
2. Что такое предварительное цинкование?
Предварительное цинкование также известно как заводское цинкование. Этот процесс очень близок к горячему цинкованию, но выполняется на самом первом этапе производства. Это всегда происходило на сталелитейном заводе на материалах, которые уже имеют определенную форму или до того, как они были разрезаны на размеры и обработаны.
Предварительное цинкование включает несколько этапов горячего цинкования погружением, таких как очистка поверхности, погружение в горячую ванну с жидким цинком в сочетании с процессом отдачи.
II. Различия между горячим цинкованием погружением и предварительным цинкованием
1.
Сравнение применений
Горячее цинкование погружением является экономичным выбором, если вы ищете решение, которое можно выполнить как для простых, так и для сложных форм. Он часто используется на объектах, которые были изготовлены заранее, но еще не оцинкованы, и горячее цинкование играет роль последнего шага.
При этом предварительное цинкование, как следует из его названия, выполняется на первом этапе производства. Следовательно, в основном это происходило на фабриках, а результаты процесса будут разрезаны по размеру и изготовлены позже.
2. Сравнение покрытий
Поскольку основным объектом процесса цинкования является нанесение защитного покрытия на сталь и металлы, мы не можем упустить возможность сравнить отделку покрытия методами 02 для изготовления оцинкованной стали.
а. Толщина покрытия
Оба метода обеспечивают равномерную толщину покрытия. Однако горячее цинкование дает более толстый защитный слой, чем предварительное цинкование. Минимальная средняя толщина горячеоцинкованной стали составляет 45-85 мкм, в то время как для предварительно оцинкованной продукции она составляет от 20 до 30 мкм». \
\
Предварительное цинкование дает более тонкое и однородное цинковое покрытие, чем горячее цинкование погружением
b. Непрерывное покрытие
Поскольку горячее цинкование погружением требует погружения всей стали/металлов в ванну с расплавленным цинком, оцинкованная сталь, полученная в результате этого процесса, имеет сплошное покрытие на поверхности. Предварительное цинкование выполняется на первом этапе перед порезкой листов на размеры и куски, поэтому кромки реза не покрыты лаком.
г. Связующее покрытие
Первыми этапами этих 02 процессов изготовления оцинкованной стали являются очистка поверхности механическим, химическим или обоими способами. Следовательно, связь между основным металлом (сталью) и защитным покрытием является металлургической и прочной.
д.
Способность к формованию покрытия
Способность к формованию покрытия для этих 02 процессов совершенно различна. Поскольку предварительное цинкование выполняется на заводах, любое покрытие, нанесенное на его результаты, может быть нанесено без повреждения слоя. Однако формообразующее покрытие, наносимое на горячеоцинкованную сталь, не рекомендуется, так как это может привести к повреждению защитного покрытия изделий.
Так как любое покрытие может быть нанесено на предварительно оцинкованные изделия без повреждения слоя, проще изготовить готовые изделия, такие как погрузочная рампа, панели для крупного рогатого скота, сено для крупного рогатого скота…
e. Внешний вид покрытия
Горячее цинкование окунанием образует обычно блестящую поверхность оцинкованной стали, хотя она также может быть различной. Что касается процесса предварительного цинкования, то он обеспечивает равномерную блестящую отделку покрытия.
3. Сравнение стойкости к истиранию
После процесса горячего цинкования на основном металле образуются слои сплава 03. Эти слои металлургически связаны со сталью и становятся неотъемлемой частью самой стали, образуя идеальное защитное покрытие.
В процессе предварительного цинкования получается оцинкованная сталь с более тонким покрытием, что делает ее немного подверженной коррозии.
4. Защитное покрытие
Процесс горячего цинкования защищает сталь тремя основными способами, но, пожалуй, наиболее заметным из них является защитное покрытие стали. Цинк в защитном покрытии играет роль анода для стали. После горячего цинкования защитная способность повышается, так как цинк становится неотъемлемой частью стали.
В то же время, поскольку предварительно оцинкованные изделия имеют тонкое покрытие и позже будут обрезаны по размеру и форме, жертвенная защита может быть такой же хорошей, как у стали, оцинкованной горячим способом.
Особенность | Горячие ограбления | Предварительно ограждание | |
---|---|---|---|
Толщина покрытия | Толстая покрытие с минимальными средним требованиями 45-85 мкм.![]() | ||
Покрытие постоянно | Непрерывное покрытие по всему объекту | Облаженная площадь с разрезом | |
Связанная с покрытием | Сильная металлургическая связь с базовой сталь | Сильная металлургальная связь с базовой сталью | 01101010111010119 | Формовка после горячего цинкования не рекомендуется, так как это может повредить покрытие | Тонкое покрытие может формироваться без каких-либо повреждений |
Внешний вид покрытия | Обычно светлая, но может быть различной устойчивость к истиранию | ||
Уменьшенная защита | Обеспечивает высочайший уровень остаточной защиты | Сниженная остаточная защита из-за тонкослойного покрытия и на некоторых непокрытых участках (кромки реза) |
Chinh Dai Steel – известный производитель оцинкованной стали
Имея более чем 20-летний опыт работы на международных рынках и в настоящее время имея 03 завода с производственной мощностью более 600 000 тонн в год, Chinh Dai Steel производит и поставляет оцинкованную сталь продукты, отвечающие всем этим требованиям.
Chinh Dai Industrial специализируется на производстве рулонной оцинкованной стали, труб и других изделий из оцинкованной стали.
Оцинкованные стальные изделия компании Chinh Dai Steel (такие как оцинкованный стальной прокат в рулонах, трубы, прогоны и другие готовые изделия) изготавливаются из высококачественных импортных материалов с цинковым покрытием от Z120 до Z275. Наши продукты также соответствуют международным стандартам, таким как ASTM (A500, A53 и A513) AS/NZ 1163, JIS G3444 и EN 10219. Вы можете легко проверить происхождение каждого продукта на его этикетках с помощью QR-кодов.
Заключительные слова
Существует несколько различий между процессами горячего цинкования и предварительным цинкованием. Знание этих различий позволит нам выбрать наиболее подходящий метод и продукты для ваших проектов. Прежде всего, всегда необходимо выбирать лучшие изделия из оцинкованной стали среди различных предложений на рынке.
Горячеоцинкованная сталь
Горячеоцинкованная сталь
Свойства горячеоцинкованной стали: прочное покрытие, полная защита, меньше обслуживания и долгий срок службы.
Горячеоцинкованная сталь сочетает в себе практичность и красоту. Он состоит из олова, хрома, цинка или краски, которые представляют собой дополнительную отделку, наносимую на поверхность из натуральной стали. Нанесение покрытия предназначено для защиты поверхности стали от окисления, а также для повышения требований к внешнему виду.
Механические свойства
Марка стали – JIS G3302 SGC340
- Предел текучести или испытательное напряжение
- 245 мин. МПа
- Прочность на растяжение
- 340 мин. МПа
- Удлинение
- 20 мин. %
Спецификация и размер продукта:
Рулонная сталь с горячим цинкованием
ЦНС 1244 2013 | JIS G 3302 2019 | АСТМ А653М 2017 | АС1397 2011 | ЕН 10346 2015 | |||
Технические характеристики | Горячекатаная основа: SGHC сингапурских долларов СГХ 340 400 440 490 540 | Холоднокатаная основа: SGCC SGCD 1~3 СГК 340 400 440 490 570 | Горячекатаная основа: SGHC сингапурских долларов СГХ 340 400 440 490 540 | Холоднокатаный База: SGCC SGCD 1~3 СГК 340 400 440 490 570 | ДС ДДС CS ТИП A, B, C ФС ТИП А, В СС МАРКА 33(230) 37(255) 40(275) 50(340)КЛАСС 1~3 80(550)КЛАСС 1~3 | Г1~Г3 G250 300 350 400 450 550 | ДС51-52-53Д С220ГД (250 280 320 350 550) |
Толщина основной стали (мм) | 1,2~4,60 | SGCD1~3: 0,27~2,0 мм SGCC/SGC: 0,19~2,0 мм | 1,2~4,60 | SGCC, SGC340: 0,18~3,0 мм; | ДС: 0,27~2,0 мм; ДДС: 0,25~2,0 мм; CS/FS: 0,19~4,50 мм; СС КЛАССА 33~80: 0,19~4,50 мм; CS ТИП A, B, C, класс 33, 37: 0,18~3,0 мм; FS ТИП A, B: 0,295~2,0 мм; Класс 40, 50: 0,229~3,0 мм; Класс 55 (380): 0,35~3,0 мм; Класс 60 (410): 0,47~1,6 мм; Класс 65 (450): 0,6~3,0 мм; Класс 80: 0,229~2,2 мм | G1: 0,19~4,50 мм; G2 и G3: 0,27~2,0 мм; G250~550GD: 0,19~4,6 мм; G300: 0,229~2,3 мм; G350: 0,229~3,0 мм; G450: 0,6~3,0 мм; G500: 1,1~2,5 мм; G550: 0,229~2,2 мм | DX51D: 0,19~4,50 мм; S220~550GD: 0,19~4,6 мм; S250GD: 0,18~2,02 мм; DX52D: 0,295~2,0 мм; DX53D, 54D: 0,25~2,0 мм; S280GD, S350GD: 0,229~3,0 мм; S320GD: 0,229~2,3 мм; S550GD: 0,229~2,2 мм |
Масса покрытия: Обычные блестки (толщина > 0,60 мм) Свернутый (ноль) Блестка | З08~З60 | З08~З60 | З90~З600 | З100~З600 | З100~З350 | ||
Отделка поверхности | Обычные блестки, минимальные (нулевые) блестки, очень гладкие | ||||||
Обработка поверхности | Хромирование, промасливание, смоляное покрытие (защита от отпечатков пальцев) или зеленая обработка (экологически чистая защита от отпечатков пальцев) | ||||||
Примечания | 1.![]() 2. Все продукты толщиной 2,0 мм и меньше могут проходить через кожу. 3. Спецификация для горячекатаного основного металла толщиной менее 1,6 мм в соответствии с JIS G3302 будет такой же, как и для толщины 1,6 мм. 4. Внутренний диаметр рулона может быть 508 мм или 610 мм. Максимальный внешний диаметр рулона составляет 2000 мм. 5. Пожалуйста, обращайтесь в наш отдел продаж и маркетинга для продуктов со специальными характеристиками. 6. Масса покрытия, превышающая указанные выше спецификации, может быть предоставлена Yieh Corp. по взаимному согласию между заказчиком и нами. 7. Масса покрытия Z08, Z09 и Z90 применяется только для холоднокатаных основных металлов. |
Доступный размер
Название продукта | Базовый тип | Толщина (мм) | Ширина (мм) |
Горячеоцинкованная стальная катушка | Холоднокатаная основа | 0,17~3,00 | 670~1650 |
Основание горячекатаное | 1,20~4,60 | 670~1300 |