Группы свариваемости сталей: Классификация сталей по свариваемости
alexxlab | 13.06.2023 | 0 | Разное
Классификация сталей по свариваемости
По свариваемости стали подразделяют на четыре группы: первая группа – хорошо сваривающиеся; вторая группа – удовлетворительно сваривающиеся; третья группа – ограниченно сваривающиеся; четвертая группа – плохо сваривающиеся.
Основные признаки, характеризующие свариваемость сталей,- склонность к образованию трещин и механические свойства сварного соединения.
К первой группе относятся стали, сварка которых может быть выполнена по обычной технологии, т.е. без подогрева до сварки и в процессе сварки и без последующей термообработки. Однако применение термообработки для снятия внутренних напряжений не исключается.
Ко второй группе относят в основном стали, при сварке которых в нормальных производственных условиях трещин не образуется. В эту же группу входят стали, которые для предупреждения образования трещин нуждаются в предварительном нагреве, а также в предварительной и последующей термообработке.
К третьей группе относят стали, склонные в обычных условиях сварки к образованию трещин. При сварке их предварительно подвергают термообработке и подогревают. Кроме того, большинство сталей, входящих в эту группу, подвергают обработке после сварки.
К четвертой группе относят стали, наиболее трудно поддающиеся сварке и склонные к образованию трещин. Эти стали свариваются ограниченно, поэтому сварку их выполняют с обязательной предварительной термообработкой, с подогревом в процессе сварки и последующей термообработкой.
Хорошо сваривающиеся углеродистые, низко- и среднелегированные стали. Условия сварки нормальные. Литые детали с большим объемом наплавленного металла рекомендуется варить с промежуточной термообработкой (отжиг или высокий отпуск по режиму термообработки для данной стали). Для конструкций, работающих под статической нагрузкой, термообработку после сварки не производят.
Для ответственных конструкций, работающих под динамическими нагрузками или при высокой температуре, термообработка производится в соответствии с техническими условиями.
При сварке электродами Э42, Э42А, Э50, Э50А, Э55 (ГОСТ 9467 – 75) сварное соединение обрабатывают нормальным режущим инструментом.
Свариваемость сталей по маркам приведена в табл. 1.
Удовлетворительно сваривающиеся углеродистые, низко- и средне- легированные стали. Термообработка стали до сварки различна в зависимости от марки стали и конструкции деталей. Для отливок из стали 30Л и 35Л обязателен отжиг. Детали машин из проката или из поковок, не имеющие жестких контуров, могут подвергаться сварке в термически обработанном состоянии (закалка и отпуск).
Сварка на морозе не допускается. Сварку деталей с большим объемом наплавленного металла, а также сварку усилительных вкладышей рекомендуется производить с промежуточной термообработкой (отжиг или высокий отпуск). При заварке мелких раковин на деталях и элементах из углеродистой стали, содержащей углерода 0,35%, и при невозможности последующего отпуска завариваемую деталь подвергают местному подогреву.
Таблица 1. Свариваемость сталей
Свариваемость | ГОСТ | Марка |
Углеродистые, низко- или среднелегированные стали | ||
Хорошая | 380 -75 | Ст1кп, Ст1пс, Ст1сп, Ст2кп, Ст2пс, СтЗкп, СтЗпс, СтЗсп, Ст4кп, Ст4пс, Ст4сп, Ст1кп, БСт1сп, БСт2кп, БСт2пс, БСт2сп, БСтЗкп, БСтЗпс, БСтЗсп, БСт4кп, Ст4пс, БСт4сп |
1050-60 | О,8; 10, 15, 20, 25, 15Г, 20Г | |
5520-69 | 15К, 20К | |
4543-71 | 15Х, 20Х, 20ХГСЛ, 12ХН2, 12Х2Н4А, 15НМ | |
5058-65 | 10ХСНД (СХЛ-4) | |
977-65 | 15Л, 20Л | |
Удовлетворительная
| 380-71 | БСт5сп, БСт5сп, БСт5Гсп |
1050-60 | 30, 35 | |
4543-71 | 12Х2Н4А, 20ХН3А | |
977-65 | З0Л, 35Л | |
5058-65 | 15ХСНД (СХЛ-1, НЛ-2) | |
Ограниченная | 380-71 | Ст6пс, Ст6сп, БСт6пс, БСт6сп |
1050-60 | 40, 45, 50 | |
4543-71 | 35ХМ, З0ХГС, 35СГ, ЗЗХС, 20Х2Н4А | |
5950-63 | 5ХНМ | |
977-65 | 40Л, 45Л, 50Л | |
Плохая | 1050-60 | 40Г, 45Г, 50Г, 60Г, 65Г, 70Г |
4543-71 | 50ХН | |
14959-69 | 50ХГ, 50ХГА, 55С2, 55С2А, 65, 75, 85, 60С2, 60С2А | |
5950-63 | 9Х | |
977-65 | 55Л | |
1435-54 | У7, У6, У8Г, У9, У10, У11; У12, У13, У7А, У8А, У8ГА, У9А, У10А, У11А, У12А, У13А | |
Легированные стали | ||
Хорошая
| 5632-61 | 0Х20Н14С2 (ЭИ732), Х23Н18 (ЭИ417), ОХ18Н10 (ОХ18Н9, ЭЯ0), Х18Н9Т (1Х18Н9Т, ЭЯ1Т) |
Удовлетворительная |
| 9Х14А, 12Х14А |
5632-61 | 2Х18Н9 (ЭЯ2), Х18Н9 (1Х18Н9, ЭЯ1) | |
Плохая | 5952-63 | Р18, Р9 |
5950-63 | Х12, Х12М, Х, 9Х, 7ХЗ, 8ХЗ, 9ХС, 4ХС. |
Термообработка после сварки различна для разных марок стали.
Для отливок из стали 30Л и 35Л при заварке сквозных трещин и сварке усилительных вкладышей обязателен отжиг или высокий отпуск. При заварке мелких дефектов на углеродистой стали, содержащей углерода более 0,35%, для улучшения механических свойств и обрабатываемости термическую обработку ведут по режиму для данной стали. Для других сталей, сваренных в термически обработанном состоянии, обязателен отпуск с нагревом до температуры на 50 – 100°С ниже температуры отпуска стали. Для стали 27ГС, 20ХГС и других сталей, склонных к отпускной хрупкости, температура отпуска после сварки должна быть вне области температуры отпускной хрупкости.
Сварные соединения, выполненные электродами Э42, Э42А, Э50, Э50А, Э55, можно обрабатывать нормальным режущим инструментом при условии, если содержание углерода в углеродистой стали не превышает 0,35% и объем наплавленного металла не меньше 20х20х10 мм.
Металл, наплавленный электродами ЦЛ-2, ЦЛ-4 (ГОСТ 10052 – 62), обрабатывают твердосплавным инструментом.
Ограниченно сваривающиеся углеродистые низко- и среднелегированные стали. Для отливок из стали ЛХН2 и 50Л до сварки обязателен отжиг независимо от конфигурации отливки. Мелкие дефекты допускается заваривать в термически обработанном состоянии отливки. Для деталей машин из проката или из поковок, не имеющих особо жестких контуров и жестких узлов, допускается заварка в термически обработанном состоянии (закалка и отпуск).
Тепловой режим сварки следующий. Без предварительного подогрева, можно сваривать в случаях, когда сварные соединения не имеют жестких контуров, толщина металла не более 15 мм, температура окружающего воздуха не ниже 5°С, а сварные соединения имеют вспомогательный характер. Во всех других случаях обязателен предварительный подогрев до температуры 200°С.
Термообработка после сварки имеет следующие особенности.
При заварке крупных дефектов на деталях из стали ЛХН2 требуется термообработка по режиму для данной стали. После заварки мелких дефектов в термически обработанной отливке обязателен повторный отпуск по режиму для данной стали. Для всякой другой стали рассматриваемой группы, сваренной в термически обработанном состоянии, обязателен отпуск для снятия напряжений с нагревом до температуры на 50 – 100°С ниже температуры отпуска стали. Для стали 30ХГСА и других сталей, склонных к отпускной хрупкости, температура отпуска после сварки должна быть вне области отпускной хрупкости.
При сварке электродами Э42, Э42А, Э50, Э50А, Э55 сварные соединения обрабатываются без затруднении, если деталь подвергнута отпуску при температуре не ниже 550 — 650°С.
Плохо сваривающиеся углеродистые низко- и среднелегированные стали. Сталь перед сваркой должна быть отожжена. Независимо от толщины свариваемых элементов и типа сварного соединения сталь необходимо предварительно подогревать до температуры не ниже 200°С.
Термообработку после сварки производят по специальной инструкции в зависимости от марки стали и ее назначения.
Механическая обработка сварного соединения возможна только после отжига или высокого отпуска.
Хорошо сваривающиеся легированные стали. Термообработку до сварки не производят. При значительном наклепе металл необходимо закалить до температуры 1050 – 1100°С. Тепловой режим сварки нормальный. Термообработку после сварки не производят.
Механическая обработка сварных соединений ввиду высокой вязкости большинства сталей рассматриваемой группы затруднена.
Удовлетворительно сваривающиеся легированные стали. Рекомендуется до сварки применять отпуск при температуре 650 – 710°С с охлаждением на воздухе. Тепловой режим сварки нормальный.
На морозе сварка не допускается. Предварительный подогрев до 150 – 200°С необходим лишь при сварке элементов с толщиной стенок более 10 мм.
После сварки для снятия напряжений и снижения твердости околошовной зоны, особенно при сварке электродами из стали 0Х14А, рекомендуется заваренные детали подвергать отпуску при температуре 650 – 710°С с охлаждением деталей на воздухе.
При сварке электродами ЦЛ-2 и ЦЛ-4 термообработку производят по специальному режиму. Механическая обработка возможна только после термообработки по специальному режиму.
Ограниченно сваривающиеся легированные стали. Термообработка до сварки для различных сталей различна. Для сталей 18Х14А и СХНА обязателен отпуск при температуре 650 – 710°С с охлаждением на воздухе. Для других сталей рекомендуется закалка в воде от температуры 1050 – 1100°С.
При сварке для сталей 18Х14А, СХНА, Х25Н13Л обязателен предварительный подогрев до температуры 200 – 300°С. Стали 9Х19НА, Х18Н9 и 2Х18Н9 сваривают в нормальных условиях с минимальным разогревом и минимальной скоростью охлаждения металла шва и зоны термического влияния.
После сварки для снятия напряжений и понижения твердости металла сварного соединения детали из стали 18Х14А должны подвергаться отпуску при температуре 650 – 710°С. Для стали 9Х19НА, Х18Н9, 2Х18Н9 обязательна закалка в воде от температуры 1050- 1100°С.
Механическая обработка сварного соединения из стали 18Х14А возможна только после отпуска. Для всех других сталей обрабатываемость сварного соединения – на уровне основного металла.
Плохо сваривающиеся легированные стали. До сварки рекомендуется отпуск по определенным режимам для различных сталей.
Допускается сварка инструментальной стали в термически обработанном состоянии, если шов наплавляется не на режущую часть инструмента.
Для стали Г13Л обязательна закалка. При сварке обязателен предварительный подогрев до 200 – 300°С, за исключением сталей РФ18 и Р9, подогрев которых должен быть не ниже 600°С. Сварка стали Г1ЗЛ в состоянии закалки должна производиться без подогрева.
Термообработку после сварки выполняют по специальным инструкциям в зависимости от марки стали и назначения. Для стали Г1ЗЛ термообработка не требуется.
Свариваемость сталей
Содержание страницы
- Понятие о свариваемости
- Свариваемость сталей
- Влияние элементов, содержащихся в сталях, на их свариваемость
- Классификация сталей по свариваемости
Понятие о свариваемости
Свариваемостью называется свойство металла (или другого материала) образовывать при установленной технологии сварки соединение, отвечающее требованиям, обусловленным конструкцией и эксплуатацией изделия (ГОСТ 2601).
Свариваемость различных металлов и их сплавов существенно отличается.
Степень свариваемости оценивают изменением свойств сварного соединения по отношению к основному металлу. Степень свариваемости сплава тем выше, чем больше способов сварки и режимов при каждом способе можно применить. Примером хорошей свариваемости является малоуглеродистая сталь.
Под технологической свариваемостью понимают отношение металла к конкретному способу сварки и режиму.
Физическая свариваемость определяется процессами, протекающими в зоне сплавления свариваемых металлов, по завершении которых образуется неразъемное сварное соединение. Все однородные металлы обладают физической свариваемостью. Свойства разнородных металлов зачастую препятствуют протеканию необходимых физико-механических процессов в зоне сплавления. В этом случае металлы не обладают физической свариваемостью.
Свариваемость сталей
Влияние элементов, содержащихся в сталях, на их свариваемостьУглерод. Малоуглеродистые стали хорошо свариваются всеми видами сварки. С увеличением содержания углерода в стали повышается твердость и снижается пластичность. Металл в сварном соединении закаливается, и образуются трещины. В результате интенсивного окисления углерода при сварке образуется значительное количество газовых пор.
Марганец. В количестве 0,3…0,8 % марганец не ухудшает свариваемость стали. Является хорошим раскислителем и способствует уменьшению содержания кислорода в стали. При содержании марганца 1,5…2,5 % свариваемость ухудшается и возможно появление трещин из-за увеличения твердости стали и образования закалочных структур.
Кремний. Содержание кремния в углеродистых сталях незначительно (0,03…0,35 %). Кремний вводят как раскислитель, и при содержании до 1 % он не влияет на свариваемость. С увеличением содержания кремния более 1 % свариваемость ухудшается, так как образуются тугоплавкие окислы, которые приводят к появлению шлаковых включений. Металл сварного шва имеет повышенные прочность, твердость и хрупкость.
Хром. В углеродистых сталях содержание хрома не превышает 0,25 % и в таком количестве его влияние на свариваемость не значительно. Конструкционные стали типа 15Х, 20Х, 30Х, 40Х содержат от 0,7 до 1,1 % хрома. При таком содержании хрома твердость увеличивается, а свариваемость ухудшается, особенно с увеличением содержания углерода. Стали, содержащие значительное количество хрома (Х5, 1X13, Х17) имеют самую плохую свариваемость. При сварке образуются тугоплавкие окислы, снижается химическая стойкость стали и образуются закалочные структуры.
Никель. Никель повышает прочность и пластичность металла сварного соединения и не ухудшает свариваемость.
Молибден. В теплоустойчивых сталях содержание молибдена составляет 0,2…0,8 %, а в специальных сталях, предназначенных для работы при высоких температурах, увеличивается до 2…3 %. Молибден значительно повышает прочность и ударную вязкость стали, но вызывает склонность к образованию трещин, как в самом шве, так и в переходной зоне.
Ванадий. Ванадий повышает прочность сталей. Содержание его в инструментальных и штамповых сталях достигает 1,5 %. Ванадий ухудшает свариваемость, так как способен сильно окисляться и при сварке необходимо вводить в зону плавления активные раскислители.
Вольфрам. Содержание вольфрама в специальных (инструментальных и штамповых) сталях составляет до 2 %. Стали с содержанием вольфрама имеют значительную твердость и прочность при высоких температурах. Вольфрам ухудшает свариваемость, сильно окисляется и поэтому сварка требует особых приемов.
Титан и ниобий. Титан и ниобий улучшают свариваемость стали. При сварке высоколегированных хромистых и хромоникелевых сталей углерод взаимодействует с хромом и образуются карбиды хрома. Это приводит к уменьшению содержания хрома по границам зерен, образованию межкристаллитной коррозии и разрушению сварных швов. При введении в стали титана или ниобия в количестве 0,5…1 % происходит их взаимодействие с углеродом, что препятствует образованию карбидов хрома.
Медь. В сталях, используемых для ответственных конструкций, содержание меди составляет 0,3…0,8 %. Медь улучшает свариваемость, повышает прочность, пластические свойства, ударную вязкость и коррозионную стойкость сталей.
Сера. Повышенное содержание серы приводит при сварке к образованию горячих трещин. Наибольшее допускаемое содержание серы до 0,06 %.
Фосфор. Повышенное содержание фосфора ухудшает свариваемость, так как вызывает при сварке появление холодных трещин. Допускается содержание фосфора в углеродистых сталях не более 0,08 %.
Кислород. Кислород ухудшает свариваемость стали, снижая ее механические свойства – прочность, пластичность, ударную вязкость.
Азот. Азот из окружающего воздуха при охлаждении сварочной ванны образует нитриды железа, которые повышают прочность и твердость стали и значительно снижают пластичность.
Водород. Водород попадает в сварочную ванну из влаги и коррозии на поверхности металла, скапливается в отдельных местах сварного шва, образует газовые пузырьки, вызывает появление пористости и мелких трещин.
Свариваемость сталей оценивается такими признаками как склонность к образованию трещин и механические свойства сварного соединения.
Количественной характеристикой свариваемости стали является эквивалентное содержание углерода Сэк, которое определяют по формуле
Сэк = С + (Мn/6) + [(Cr + Mo +V)/5 + (Ni + Cu)/15] ,
где С – содержание углерода, %;
Мn, Cr, Mo, V, Ni, Cu – содержание легирующих элементов (марганец, хром, молибден, ванадий, никель, медь), %.
Наибольшее влияние на свариваемость стали оказывает количество содержащегося в ней углерода и легирующих компонентов.
Стали по свариваемости делят на четыре группы: хорошо сваривающиеся стали, удовлетворительно сваривающиеся, ограниченно сваривающиеся и плохо сваривающиеся стали.
К первой группе относятся стали, сварку которых выполняют по обычной технологии без подогрева. Возможно применение термообработки для снятия внутренних напряжений.
Ко второй группе относятся стали, у которых при сварке в нормальных условиях, как правило, трещин не образуется. Для сварки сталей этой группы имеются ограничения по толщине свариваемого изделия и температуре окружающей среды.
К третьей группе относятся стали, склонные в обычных условиях сварки к образованию трещин. При сварке их предварительно подвергают термообработке и подогревают. Кроме того, большинство сталей, входящих в эту группу, подвергают термообработке после сварки.
К четвертой группе относятся стали, наиболее трудно поддающиеся сварке и склонные к образованию трещин. Эти стали свариваются ограниченно, поэтому сварку их выполняют с обязательной предварительной термообработкой, с подогревом в процессе сварки и последующей термообработкой.
В табл. 1 приведена свариваемость и условия сварки сталей различных видов и марок.
Таблица 1. Свариваемость сталей и условия сварки
Группа свариваемости | Эквивалентное содержание углерода, Сэк | Углеродистые стали | Легированные стали | Высоколегированные стали | Условия сварки |
I Хорошая | До 0,25 | ВСт1, ВСт2, ВСт3, ВСт4, Стали 08, 10, 15, 20, 25 | 15Г, 20Г, 15Х, 20Х, 15ХМ, 20ХГСА, 10ХСНД, 10ХГСНД, 15ХСНД | 08Х20Н14С2, 20Х23Н18, 08Х18Н10, 12Х18Н9Т, 15Х5 | Без ограничений, в широком диапазоне режимов сварки независимо от толщины металла, жесткости конструкции, температуры окружающей среды |
II Удовлетворительная | Свыше 0,25 и до 0,35 | ВСт5, Стали 30, 35 | 12ХН2, 12ХН3А, 20ХН, 20ХН3А, 30Х, 30ХМ, 25ХГСА | 30Х13, 25Х13Н2, 9Х14А, 12Х14А | Сварка при температуре окружающей среды не ниже + 5 оС и толщине металла до 20 мм при отсутствии ветра |
III Ограниченная | Свыше 0,35 и до 0,45 | ВСт6 Стали 40, 45 | 35Г, 40Г, 45Г, 40Г2, 35Х, 40Х, 45Х, 40ХМФА, 40ХН, 30ХГС, 30ХГСА, 35ХМ, 20Х2Н4МА | 17Х18Н9Т, 12Х18Н9, 36Х18Н25С2, 40Х9С2 | Сварка с предварительным или сопутствующим подогревом до 250 оС в жестком диапазоне режимов сварки |
IV Плохая | Свыше 0,45 | Стали 50, 55, 60, 65, 70, 75, 80, 85 | 50Г, 50Г2, 50Х, 50ХН, 45ХН3МФА, 6ХС, 7Х3 | 40Х10С2М, 40Х13, 95Х18, 40Х14Н14В2М, 40Х10С2М, Р18, Р9 | Сварка с предварительным и сопутствующим подогревом, термообработкой после сварки |
Система группировки основного металла – TWI
Введение
Когда процедуры сварки или сварочные работы (сварщики) аттестуются, образцы для испытаний подготавливаются с использованием определенной комбинации основного материала и расходных материалов. Чтобы сократить количество процедур сварки, которые должны быть аттестованы для производственных применений, нормы и стандарты предусматривают, что конкретный основной материал и присадочные материалы должны охватывать ряд других материалов, которые, как считается, обладают аналогичной свариваемостью (т. е. подвержены воздействию сварки аналогичным образом). ) или требовать аналогичных навыков для работы (квалификация сварщика). Кодексы и стандарты могут прямо указывать конкретную систему группировки материалов или ссылаться на другие кодексы и стандарты.
Нажмите здесь, чтобы посмотреть наши последние технические подкасты на YouTube .
Две наиболее часто используемые системы группировки предоставлены ISO (ссылочный стандарт ISO/TR 15608, заменивший CR 12187) и ASME/AWS (ASME Section IX, QW/QB-422, идентичный AWS B2.1). . Первый классифицирует материалы на «группы» и «подгруппы», определяемые числовым значением, в то время как второй присваивает «P-номера» (P-No, где «P» для исходного материала), как показано в Таблице 1 ниже.
Основное различие между ними заключается в том, что система ISO позволяет относить любой материал в рамках справочного стандарта к определенной группе, тогда как система ASME присваивает P-No только материалам, перечисленным в коде или имеющим тот же номер UNS, что и у перечисленных материалов (подробнее см. ниже). Конкретный случай AWS d1.1 описан в конце этой статьи о вакансиях.
Таблица 1: Сравнение групп материалов в соответствии с ISO/TR 15608 и ASME IX
Группа материалов | ИСО/ТР 15608 | ASME IX, QW-422 (сварка) | ASME IX, QB-422 (пайка) |
Стали | 1.г – 11.г | P-№. 1 – P-номер. 15Ф | P-№. 101 – P-№. 103 |
Алюминий и алюминиевые сплавы | 2x.y | P-№. 21 – P-№. 26 | P-№. 104 и P-№. 105 |
Медь и медные сплавы | 3x.![]() | P-№. 31 – P-№. 35 | P-№. 107 и P-No. 108 |
Никель и никелевые сплавы | 4x.y | P-№. 41 – П-№. 49 | P-№. 110 – П-№. 112 |
Титан и титановые сплавы | 5х.у | P-№. 51 – P-№. 53 | P-№. 115 |
Цирконий и циркониевые сплавы | 6х.у | P-Номер. 61 и P-No. 62 | P-№. 117 |
Чугун | 7х.у | Неприменимо | Неприменимо |
Квалификационные испытания сварщика и оператора сварки (EN 287, ISO 9606 и ISO 14732)
Для квалификации сварщика ISO 9606 (который заменил EN 287) предоставляет диапазоны квалификации как для основного материала, так и для присадочного материала. Более новые версии частей ISO 9606, такие как текущий ISO 9606-1 (сварка сталей плавлением), отошли от этой философии, чтобы принять систему, аналогичную ASME IX (описанную ниже), которая рассматривает состав присадочного материала как единственный «важная» переменная, когда сварщик имеет квалификацию для группы присадочных материалов, если основной материал находится в любой группе от 1 до 11 (см. Таблицу 1).
Для операторов сварки: EN ISO 14732 относится к операторам сварочного оборудования. Поскольку навыки сварщика не проверяются, диапазон квалификации вытекает из соответствующей квалификации процедуры сварки (например, в следующем разделе).
Квалификация процедуры сварки (ISO 15610, 15611, 15612, 15613 и 15614)
Стандарты ISO обычно допускают квалификацию ряда исходных материалов на основе материала, использованного для квалификационного испытания образца. Обычно это относится к материалам в той же группе и любой более низкой подгруппе. Полный перечень всех квалификационных диапазонов приводится в стандартах (обычно в виде таблицы или матрицы). Если материал попадает в две (под) группы, он всегда считается принадлежащим к группе с меньшим номером. Широкий спектр разнородных соединений может соответствовать требованиям, но их необходимо тщательно изучить, чтобы убедиться, что стандарт допускает это.
Испытываемые материалы-наполнители обычно квалифицируют другие материалы, которые имеют такую же форму, номинальный состав, механические свойства и содержание водорода. В некоторых частях стандарта есть определенные тонкости. В некоторых случаях, например, когда требуются характеристики ударной вязкости или для гипербарической сварки, квалифицируются только расходные материалы одного и того же производителя. Это также относится к EN ISO 15610, где свойства расходных материалов должны быть гарантированы в зависимости от процедуры квалификации.
Группировка материалов (ISO/TR 15608)
Этот стандарт разделяет возможные материалы, которые можно сваривать, на набор групп, чтобы можно было аттестовать несколько различных марок с помощью одного контрольного сварного шва. Стандарт распространяется на стали, алюминиевые сплавы, медные сплавы, никелевые сплавы, титановые сплавы, циркониевые сплавы и чугуны. Большинство групп относительно легко понять, с диапазонами составов, предусмотренными для соответствующих сплавов. Группировки основаны на преднамеренном легировании компонентов без учета примесей.
Группировка стали учитывает дополнительные факторы, а именно: предел текучести сплава и его термомеханическую обработку. Это может привести к неопределенности в определении точной группы или подгруппы сплава и может потребовать рассмотрения дополнительной информации помимо состава или свойств при растяжении. Например, стали S460 могут соответствовать нескольким различным стандартам. S460M, как указано в EN 10025-4, который относится к термомеханическим прокатным сталям, относится к группе 2.1, тогда как S460N, как указано в EN 10025-3, который относится к нормализованным сталям, находится в группе 1.3.
Из-за широкого спектра доступных сплавов и различных стандартов, относящихся к ним, отнесение сплава к определенной группе в рамках ISO/TR 15608 может оказаться затруднительным. Однако существуют три стандарта, которые могут быть полезны для определения группировки интересующего материала. PD CEN ISO/TR 20172, 20173 и 20174 перечисляет множество различных марок материалов и групп, к которым они относятся. Эти стандарты могут быть очень полезны при определении соответствующей группы и, следовательно, диапазона квалификации.
Нормы ASME для котлов и сосудов под давлением (Раздел IX)
Спецификации материалов, которые должны использоваться в рамках ASME BPVC, приведены в Разделе II норм. Это результат сотрудничества между ASME и ASTM, которые совместно работали над подготовкой спецификаций материалов, соответствующих требованиям безопасности в области оборудования, работающего под давлением, изготовленного из черных и цветных металлов. В результате код ASME принял спецификации материалов ASTM без изменений, за исключением идентификатора «SA» (например, ASTM A516 становится SA-516).
Группировка ASME производится с использованием буквенно-цифрового обозначения P-No для основного металла и F-номеров (F-No) для присадочного материала. Эта группировка основана на сопоставимых характеристиках материала, таких как свариваемость, механические свойства и состав.
Основные металлы перечислены в таблице QW/QB-422, которая позволяет определить P-No для определенного материала в зависимости от его спецификации в соответствии с ASTM или номером UNS. В QW/QB-422 перечислены только материалы, разрешенные для использования в конструкции компонентов, работающих под давлением, в соответствии с ASME BPVC, поэтому им можно присвоить P-No. Если металл не указан в таблице QW/QB-422, он считается «неназначенным» и не может быть сгруппирован под P-No. Если материал, не включенный в список, имеет тот же номер UNS, что и материал, указанный в списке, материал, не включенный в список, относится к тому же P-No, что и материал, указанный в списке. Этот список определяет для спецификации сварки/пайки «минимальное заданное растяжение» в качестве приемлемого значения для испытания на растяжение для аттестации процедуры сварки/пайки.
Для некоторых материалов таблица QW/QB-422 относится к назначению материалов в соответствии с критериями группировки ISO/TR 15608:2005. Этот список перекрестных ссылок предоставляется только для информации, поскольку раздел IX ASME не ссылается на эту группу как на основу для установления квалификационного диапазона квалифицированных основных металлов.
В таблице QW 424.1 приведены правила определения квалификации диапазона в зависимости от того, какой основной металл(ы) используется для квалификационного купона процедуры в соответствии с ASME BPVC, раздел IX QW-424.1. Кодекс также указывает, что группы как основного металла, так и присадочного материала не означают, что любой основной металл и расходуемый материал могут быть заменены без рассмотрения между основным и присадочным металлом.
Таблица 2 дополняет Таблицу 1 и предоставляет дополнительную информацию о типах материалов, включенных в каждый P-No.
Таблица 2: Система P-No, используемая ASME для стали
P-No | Материал |
1 | Углеродистая сталь, Максимум C, 0,030%, Si, 0,60%; Mn, 1,70%; с, 0,045%; Р, 0,045 % Другие отдельные элементы, не более 0,30 % Сумма всех других элементов, не более 0,80 % |
2 | Кованое железо |
3 | Номинальное содержание легированной стали 1/2% Mo и/или Cr |
4 | Номинальный l-1/4 % Cr, l/2 % Mo, легированная сталь |
5А | Номинальная легированная сталь 2-1/4 и 3% Cr, 1% Mo |
5Б | Номинальное содержание легированной стали от 5 до 10 % Cr, 1 Mo |
5С | Все металлы 5A и 5B термообработанные |
6 | Мартенситная нержавеющая сталь |
7 | Ферритная нержавеющая сталь |
8 | Аустенитная нержавеющая сталь |
9А | 2 % никелевая легированная сталь |
9Б | Сталь, легированная 3,5% никеля |
9С | 4,5% никелевая легированная сталь 8% и 9% Ni |
10А | Различные низколегированные стали* |
10Б | |
10С | |
11 | Низколегированная сталь, закаленная и отпущенная |
15 | Ферритные стали с повышенным сопротивлением ползучести |
*Включает углеродистые стали и низколегированные стали, свариваемость которых отличается от обычных углеродистых сталей, или которые обладают уникальными свойствами, не подпадающими под существующие артикулы
Система AWS перечислены в таблице 3.
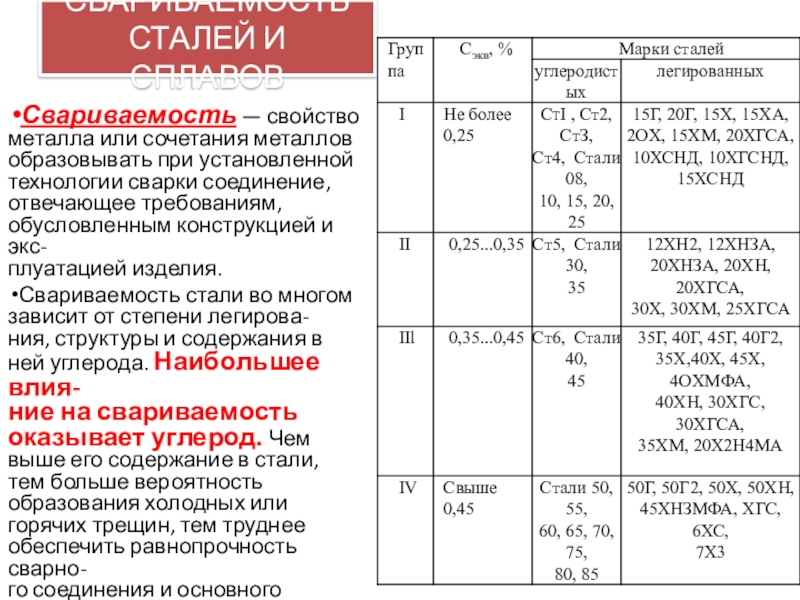
В случае процедур сварки, прошедших предварительную квалификацию, можно использовать только материалы, перечисленные в четырех группах таблицы 3.1 AWS D1.1. В Таблице 4.8 указано, что повторная квалификация будет необходима, если выбранный материал не попадает в квалификационный диапазон. Использование неперечисленных неблагородных металлов ограничено одобрением.
Для получения дополнительной информации свяжитесь с нами.
Ссылки
- ISO/TR 15608L: Сварка. Руководство по системе группирования металлических материалов, 2013 г.
- BS EN 287: Квалификационные испытания сварщиков. Сварка плавлением. Часть 1: Стали * Остается актуальной, 2011 г.
- BS EN ISO 9606 : Квалификационные испытания сварщиков. Сварка плавлением. Часть 1: Стали. ПОПРАВКА: 31 января 2014 г.; КОРРЕКЦИЯ: 29 февраля 2016 г.
- BS EN 14732 : Сварочный персонал. Квалификационные испытания операторов и наладчиков сварки для механизированной и автоматической сварки металлических материалов; 2013
- BS EN 288 : Спецификация и утверждение процедур сварки металлических материалов, часть 1: Общие правила сварки плавлением — AMD 9734: ноябрь 1997 г.
- BS EN ISO 15610 : Спецификация и квалификация процедур сварки металлических материалов. Квалификация на основе испытанных сварочных материалов; 2013
- BS EN ISO 15611 ; Спецификация и квалификация процедур сварки металлических материалов – Квалификация на основе предыдущего опыта сварки; 2003
- BS EN ISO 15612 : Спецификация и квалификация процедур сварки металлических материалов.
Квалификация путем принятия стандартной процедуры сварки; 2004
- BS EN ISO 15613 : Спецификация и квалификация процедур сварки металлических материалов. Квалификация на основе предпроизводственных сварочных испытаний; 2004
- BS EN ISO 15614 : Спецификация и квалификация процедур сварки металлических материалов. Проверка процедуры сварки. Часть 1. Дуговая и газовая сварка сталей и дуговая сварка никеля и никелевых сплавов. AMD: 30 апреля 2008 г.; AMD: 30 апреля 2012 г.
- PD CEN ISO/TR 20172: Сварка. Системы группировки материалов. Европейские материалы; 2009 г.
- PD CEN ISO/TR 20173: Сварка. Системы группировки материалов. Американские материалы; 2009
- PD CEN ISO/TR 20174: Сварка. Системы группирования материалов. Японские материалы. ПОПРАВКА: 31 июля 2011 г.
- ASME BPVC IX: Квалификационный стандарт для процедур сварки, пайки и пайки, сварщиков, пайки и операторов сварки, пайки и пайки – квалификация сварки, пайки и пайки, 2009 г.
- AWS D1.1/D1.1M: Правила сварки конструкций — сталь — 23-е издание; 2-я печать; 2016
Таблицы номеров сварных швов по ASME – базовый номер P и номер заполнения F
Снова суетитесь, чтобы найти таблицы номеров сварных швов ASME и завершить свой проект?
Как часто вы хотели, чтобы кто-нибудь сделал что-нибудь, чтобы облегчить вашу жизнь? У нас есть! Перейдите непосредственно к таблице, используя приведенные ниже ссылки, или, что еще лучше, загрузите все эти полезные таблицы номеров сварных швов ASME непосредственно на свой компьютер.
Воспользуйтесь ссылками ниже, чтобы перейти непосредственно к разделу:
Номер P (основной металл – сводка и таблица QW-423)
Номер S, (основной металл – без таблицы)
Номер группы (группы основного металла – таблица QW-420)
Номер F, (присадочный металл – таблица QW 423)
Номер A (присадочный металл – таблица QW-442)
Таблицы номеров сварных швов ASME предназначены для поддержки методологии системы нумерации, которая помогает значительно упростить создание процедур сварки и управление процедурами сварки, а также многое другое. доступный.
Эти цифры 1 были назначены как для основных металлов, так и для присадочных металлов, сгруппированные материалы для сокращения количества процедур сварки и квалификационных испытаний сварщиков, необходимых для квалификации широкого спектра материалов (основных металлов и присадочных металлов). Схема группировки основных металлов состоит из номеров P и номеров групп. Он также включал номера S, пока они не были удалены из кода ASME в 2009 году. Схема группировки присадочного металла состоит из номеров F и номеров A.
Примечание 1 : эти таблицы номеров и содержащаяся информация были точными на момент первой публикации в блоге в сентябре 2015 года, чтобы обеспечить соответствие текущим нормам, мы рекомендуем обратиться к последнему изданию свода правил или последней версии процедуры сварки. программное обеспечение для управления и поддержки кода ProWrite.
Неблагородные металлы: номер P
Этот номер используется для группировки схожих неблагородных металлов, что позволяет квалифицировать весь выбор по сравнению с квалификацией только одного. Эти основные металлы сгруппированы по материалам и им присвоены номера P в зависимости от того, из какого они материала. Например, номер P 1 присваивается основным металлам из углеродистого марганца или низкоуглеродистой стали.
В таблице ниже представлена приблизительная сводка назначений:
P-номер | Основной металл |
1 | Углеродистая марганцевая сталь (четыре групповых номера) |
2 | Не используется |
3 | 1/2 молибдена или 1/2 хрома, 1/2 Молибден (три номера группы) |
4 | 1 1/4 хром, 1/2 молибден (два номера группы) |
5А | 2 1/4 хром, 1 молибден |
5B | 5 хром, 1/2 молибден или 9 хром, 1 Молибден (два номера группы) |
5С | Хром, молибден, ванадий (пять групповых номеров) |
6 | Мартенситные нержавеющие стали (марки 410, 415, 429) (шесть групповых номеров) |
7 | Ферритные нержавеющие стали (марки 409, 430) |
8 | Аустенитные нержавеющие стали:
|
9А, Б, С | 2–4 никелевых стали |
10А, Б, С, Ф | Различные низколегированные стали |
10Ч | Дуплексная и супердуплексная нержавеющая сталь (Класс 31803, 32750) |
10I | Нержавеющая сталь с высоким содержанием хрома |
10 Дж | Нержавеющая сталь с высоким содержанием хрома и молибдена |
10 000 | с высоким содержанием хрома, молибдена, Никелевая нержавеющая сталь |
11А | Различные высокопрочные низколегированные стали (шесть групповых номеров) |
11Б | Различные высокопрочные низколегированные стали (десять групповых номеров) |
15E | 9 Хром, 1 Молибден |
от 16 до 20 | Не используется |
21 | Высокое содержание алюминия (серии 1000 и 3000) |
22 | Алюминий (серия 5000 – 5052, 5454) |
23 | Алюминий (серия 6000 – 6061, 6063) |
24 | Не используется |
25 | Алюминий (серия 5000 – 5083, 5086, 5456) |
от 26 до 30 | Не используется |
31 | с высоким содержанием меди |
32 | Латунь |
33 | медно-кремниевый |
34 | Медно-никелевый сплав |
35 | Медь Алюминий |
от 36 до 40 | Не используется |
41 | с высоким содержанием никеля |
42 | Никель, Медь – (монель 500) |
43 | Никель, хром, железо – (инконель) (C22, C276, X) |
44 | Никель, Молибден – (Хастеллой В2) |
45 | Никель, Хром, Si |
46 | Никель, хром, силикон |
47 | Никель, хром, вольфрам |
от 47 до 50 | Не используется |
51, 52, 53 | Титановые сплавы |
61, 62 | Циркониевые сплавы |
Из-за этих назначений стоимость непрерывной процедуры и проверки квалификации не существует. В большинстве случаев квалификация сварщика по конкретному материалу также влечет за собой квалификацию этого сварщика по целому ряду сопутствующих материалов.
«Например, сварщик, имеющий квалификацию P1 для материала P1, также имеет право сваривать от P-1 до P-15F, P-34 и любых P-40».
ЭКОНОМЬТЕ ВРЕМЯ И ПОЛУЧИТЕ КОНТРОЛЬПосмотрите это короткое видео и узнайте, как ПО ProWrite для управления сварочными документами может сократить время, затрачиваемое на работу с таблицами.
Дополнительные сведения приведены в следующих таблицах.
Таблица номеров раздела IX стандарта ASME из QW-423 «Квалификации сварщиков» представлена следующим образом:
Основные металлы для квалификации сварщика | Квалифицированные основные металлы |
P – № 1 до P – № 15F, P – № 34 или P – № 41 до P – № 49 | P – № 1 до P – № 15F, P – № 34 и P – № 41 до P – № 49 |
P – № 21 до P – № 26 | P – № 21 до P – № 26 |
P – № 51 до P – № 53 или P – № 61 или P – № 62 | P – № 51 по P – № 53 и P – № 61 и Р – № 62 |
В некоторых случаях квалификация производственного талона для спецификации процедуры также квалифицирует эту процедуру для более широкого диапазона материалов.
Таблица номеров ASME Раздела IX из QW-424 Квалификация процедуры показана следующим образом:
Основной металл(ы), используемые для производства Квалификационный талон | Квалифицированные базовые металлы |
Один металл из числа P на любой металл из тот же P – номер | Любые металлы, которым присвоен P-номер |
Один металл из P – № 15E на любой металл из P-№. 15Е | Любой металл P – № 15E или 5B к любому металлу, которому присвоено значение P-№. 15Е или 5В |
Один металл из числа P на любой металл из любой другой номер P | Любой металл, которому присвоен первый номер P любому металлу присвоен второй Р – номер |
Один металл из P – № 15E на любой металл из любого другой P – номер | Любой металл P – № 15E или 5B к любому металлу, которому присвоен номер второй P – номер |
Один металл от П – №3 до любого металла из П – № 3 | Любой металл P – № 3 к любому металлу, назначенному П – № 3 или 1 |
Один металл от P – №4 до любого металла из П – № 4 | Любой металл P – № 4 к любому металлу, назначенному P – № 4, 3 или 1 |
Один металл от П – № 5А до любого металла из П – № 5А | Любой металл P – № 5A для любого металла, которому присвоено значение P – № 5A, 4, 3 или 1 |
Один металл от П – № 5А до любого металла из П – № 4, П – № 3 или П – № 1 | Любой металл P – № 5A к любому металлу, присвоенному P – № 4, 3 или 1 |
Один металл от P – №4 до любого металла от П – № 3 или П – № 1 | Любой металл P – № 4 к любому металлу, назначенному П – № 3 или 1 |
Любой неназначенный металл тому же неназначенному металл | Неприсвоенный металл самому себе |
Любой неназначенный металл любому металлу с номером P | Неприсвоенный металл любому металлу, назначенному тот же номер P, что и у квалифицированного металла |
Любой неназначенный металл любому металлу из P – № 15E | Неприсвоенный металл любому металлу, назначенному P – № 15E или 5B |
Любой неназначенный металл любому другому неназначенному металл | Первый неназначенный металл второму неназначенный металл |
Номер S
Номер S был удален из раздела IX ASME в 2009 году. Назначение номера S было идентично номеру P. Однако эти номера были присвоены тем материалам, которые включены для трубопроводов в код ASME B31 для трубопроводов под давлением. Эти материалы также подпадали под номер P, но не наоборот.
Связанный: Хотите легкий доступ к этим таблицам ASME? Загрузите их здесь!
Номер группы
Этот номер используется только для испытаний на ударную вязкость черных металлов, подгруппируя материалы по номеру P по сходству металлургических свойств (см. таблицу номеров P выше). Однако в соответствии с разделом IX ASME «эти назначения основаны в основном на сравнимых характеристиках основного металла, таких как состав, свариваемость, способность к пайке и механические свойства, где это может быть сделано логически. Эти назначения не означают, что основные металлы могут быть без разбора заменены основным металлом, который использовался в квалификационных испытаниях, без учета совместимости с точки зрения металлургических свойств, термической обработки после сварки, конструкции, механических свойств и требований к эксплуатации». Эти группы можно найти в таблице QW/QB-422.
Следующая таблица является копией таблицы номеров QW-420 раздела IX ASME, в которой показаны группы присвоения для различных систем сплавов:
Основной металл | Сварка | Пайка |
Сталь и стальные сплавы | P – № 1 до P – № 15F | P – № 101 до P – № 103 |
Алюминий и алюминиевые сплавы | P – № 21 до P – № 26 | П – № 104 и П – № 105 |
Медь и сплавы на основе меди | P – № 31–P – № 35 | П – № 107 и П – № 108 |
Никель и сплавы на основе никеля | P – № 41 до P – № 49 | P – № 110 до P – № 112 |
Титан и сплавы на основе титана | P – № 51 до P – № 53 | П – № 115 |
Цирконий и сплавы на основе циркония | П – № 61 и П – № 62 | П – № 117 |
Присадочные металлы: F-номер
Этот номер используется для группировки присадочных металлов, используемых в процедурах сварки, и квалификации сварщиков. Определение номеров F приведено в QW-431 ASME IX:
«Группировка электродов и сварочных прутков в таблице QW-432 основана в основном на их характеристиках удобства использования, которые в основном определяют способность сварщиков выполнять удовлетворительные сварные швы. с заданным присадочным металлом. Эта группировка сделана для уменьшения количества процедур сварки и аттестаций производительности там, где это логически возможно. Группировка не означает, что основные металлы или присадочные металлы в пределах группы могут быть без разбора заменены металлом, который использовался в квалификационных испытаниях, без учета совместимости основного и присадочного металлов с точки зрения металлургических свойств, термической обработки после сварки. требования к конструкции и обслуживанию, а также механические свойства».
F-номера присадочных металлов можно найти в таблице номеров раздела IX ASME QW-432, выдержка показана следующим образом:
F – Номера | Электроды/сварочные стержни |
F – № 1 до F – № 6 | Сталь и стальные сплавы |
F – № 21 до F – № 25 | Алюминий и сплавы на его основе |
F – № 31–F – № 37 | Медь и медные сплавы |
F – № 41 до F – № 46 | Никель и никелевые сплавы |
F – № 51 до F – № 56 | Титан и титановые сплавы |
F – № 61 | Цирконий и сплавы на основе циркония |
F – № 71 до F – № 72 | Твердая металлическая накладка на сварной шов |
Таблица номеров раздела IX ASME QW-433 Альтернативные номера F для квалификации сварочных работ
Квалифицированный С →
| Ф – №1 | F – № 1 | F – № 2 | F – № 2 | F – № 3 | F – № 3 | Ф – №4 | F – № 4 | F – № 5 | F – № 5 |
Квалифицированный Для ↓ | С Подложка | Без Подложка | С Подложка | Без Подложка | С Подложка | Без Подложка | С Подложка | Без Подложка | С Подложка | Без Подложка |
Ф – №1 С Подложка | х | х | х | х | х | х | х | х | х | х |
Ф – №1 Без Подложка | х | |||||||||
F – № 2 С Подложка | х | х | х | х | х | х | ||||
F – № 2 Без Подложка | х | |||||||||
Ф – №3 С Подложка | х | х | х | х | ||||||
Ф – №3 Без Подложка | х | |||||||||
Ж – №4 С Подложка | х | х | ||||||||
Ж – №4 Без Подложка | х | |||||||||
Ф – № 5 С Подложка | х | х | ||||||||
Ф – № 5 Без Подложка | х |
Квалифицировано с | Квалифицировано Для |
Любой F – № 6 | Все F – № 6 [Примечание (1)] |
Любая от F – № 21 до F – № 25 | Все от F – № 21 до F – № 25 |
Любой Ф – № 31, Ф – № 32, Ф – № 33, F – № 35, F – № 36 или F – № 37 | Только тот же номер F, что и во время .![]() квалификационный тест |
F – № 34 или любой F – № 41 до Ф – № 46 | F – № 34 и все F – № 41 до Ф – № 46 |
Любой от F – № 51 до F – № 55 | Все F – № 51 до F – № 55 |
Любой F – № 61 | Все F – № 61 |
Любая от F – № 71 до F – № 72 | Только тот же номер F, что и во время .квалификационный тест |
ПРИМЕЧАНИЕ: (1) Наплавленный металл сварного шва, полученный с использованием оголенного стержня, на который не распространяется спецификация SFA, но который соответствует анализу, указанному в QW-442, считается классифицированным как F-№ 6. |
Число А
Число А представляет собой расчетное значение, основанное на сочетании химического состава присадочного металла (которое можно найти в ASME Section II Part C), и Таблица номеров A ASME Раздела IX QW-442:
Стол QW – 442 А Номера Классификация анализа черных металлов для аттестации процедуры |
Анализ, % [Примечание (1)] и [Примечание (2)] |
А-№.![]() | Тип сварного шва | С | Кр | Пн | Ni | Мн | Си |
1 | Мягкая сталь | 0,20 | 0,20 | 0,30 | 0,50 | 1,60 | 1,00 |
2 | Углерод – Молибден | 0,15 | 0,50 | 0,40-0,65 | 0,50 | 1,60 | 1,00 |
3 | Хром (от 0,4% до 2%) – молибден | 0,15 | 0,40–2,00 | 0,40-0,65 | 0,50 | 1,60 | 1,00 |
4 | Хром (от 2% до 4%) – Молибден | 0,15 | 2.00-4.00 | 0,40-1,50 | 0,50 | 1,60 | 2,00 |
5 | Хром (от 4% до 10,5%) – молибден | 0,15 | 4.![]() | 0,40-1,50 | 0,80 | 1,20 | 2,00 |
6 | Хром – мартенситный | 0,15 | 11.00-15.00 | 0,70 | 0,80 | 2,00 | 1,00 |
7 | Хром – Феррит | 0,15 | 11.00-30.00 | 1,00 | 0,80 | 1,00 | 3,00 |
8 | Хром-никель | 0,15 | 14.50-30.00 | 4,00 | 7.50-15.00 | 2,50 | 1,00 |
9 | Хром-никель | 0,30 | 19.00-30.00 | 6,00 | 15.00-37.00 | 2,50 | 1,00 |
10 | Никель до 4% | 0,15 | 0,5 | 0,55 | 0,80-4,00 | 1,70 | 1,00 |
11 | Марганец – Молибден | 0,17 | 0,5 | 0,25-0,75 | 0,85 | 1,25-2,25 | 1,00 |
12 | Никель-хром-молибден | 0,15 | 1,50 | 0,25-0,80 | 1,25-2,80 | 0,75-2,25 | 1,00 |
ПРИМЕЧАНИЯ: (1) Отдельные значения, показанные выше, являются максимальными. (2) Для определения A-чисел используются только перечисленные элементы. |
A-число является важной переменной для спецификаций процедуры сварки для нескольких сварочных процессов. Он идентифицирует родственные присадочные металлы на основе их химического состава и позволяет аттестовать процедуры для всего множества родственных материалов.
Система счисления
Цель системы счисления – помочь. Это сокращает дополнительное время и затраты за счет аттестации сварщиков и процедур для множества материалов путем простой аттестации одного из них.
Если вы хотите узнать больше о том, как ProWrite использует эту систему нумерации сварных швов для помощи в управлении процедурами сварки и управлении квалификацией сварщиков, посмотрите наш записанный веб-семинар 5 стратегий программного обеспечения для повышения эффективности процесса сварки. Он охватывает конкретные области, которые обеспечивают рентабельное повышение эффективности процесса сварки, и подробно описывает, как мы обеспечиваем единообразное применение общепринятых методов безопасной сварки при изготовлении котлов и сосудов под давлением.