Характеристики стали 09г2с: Сталь 09Г2С – Сталь конструкционная низколегированная.
alexxlab | 30.03.2023 | 0 | Разное
Характеристика и применение, показатели прочности и износостойкости
1 Сталь 45
2 Особенности марки стали 09г2с и ее характеристики
3 Характеристики металла, используемого при производстве стали
Сталь — сплав железа, содержащий в своем составе качестве постоянной примеси углерод (до 2,14%), а также иные легирующие элементы (кремний, марганец, хром,никель и пр.) и мешающие примеси (сера, фосфор, водород, азот и пр.).
Сталь различных марок широко используется в качестве основного конструкционного материала в машиностроении, строительстве и прочих отраслях промышленности. Марки стали различаются между собой химическим составом, структурой, эксплуатационными характеристиками, способом выплавки и др. Ниже представлена краткая характеристика таких марок стали как — сталь 45, сталь 09г2с.
Сталь 45
Высокопрочную и износостойкую сталь, имеющую номер 45, изготавливают согласно требованиям ГОСТа.
- 1. Валов разных видов
- 2. Бандажей
- 3. Шпинделей
- 4. Цилиндров разных видов
- 5. Изготавливаются кулачки любых форм
Марка 45 соответствует всем требованиям ГОСТа и содержит в своем составе такие элементы, как:
- Фосфор
- Медь
- Никель
- Марганец
- И ряд других элементов.
Она обладает довольно большими показателями своих механических характеристик. Благодаря этим характеристикам практически все температурные колебания она способна противостоять, не теряя своих качеств. Сталь номер 45 при испытании подвергается температурным колебаниям от 200 до 600 градусов.
Особенности марки стали 09г2с и ее характеристики
Такое обозначение, а точнее аббревиатура 09г2с принадлежит недорогой и марке стали с невысоким содержанием углерода и присадок.
09г2с – характеристики: повышенная механическая прочность, значительная стойкость к различным температурным воздействиям, податливость при закалке и отпуске. Такая сталь обладает хорошей особенностью сохранять отличные свойства при сваривании. Во время этой процедуры отпадает необходимость дополнительного температурного воздействия на нее. Варится она без проблем, обеспечивая при этом небольшой уровень концентрации углерода, что позволяет металлу после отпуска быть менее вязким и устойчивым при сгибании.
Характеристики металла, используемого при производстве стали
В первую очередь, используемый металл, должен быть очень стойким к высоким температурам. Для получения высококачественного материала необходимо следовать всем нормам и стандартам, в том числе и при подборе сырья. Это позволяет в дальнейшем задействовать сталь в машиностроительном производстве.
Используемый материал состоит из никеля и железа, устойчивые к высокой температуре, а также хрома, способствующего увеличению сопротивления процессу окисления. Однако, при этом, следует опасаться избыточного количества Хрома, т.к. теряются свойства устойчивости к повышенным температурам. Содержащийся в его составе углерод составляет лишь два десятых процента, поскольку его содержание в повышенном количестве крайне вредно. Регламентированные для металла 20х23н18 характеристики, позволяют его широко использовать.
Категории Это интересноИспользование рентгеновского анализа профиля пиков для определения структурного состояния упругонапряженной стали 09Г2С
[1] А.Б. Арабей, Разработка технических требований на металл труб газопроводов, Известия высших учебных заведений, Черная металлургия. 7 (2010) 3 – 10.
[2]
Ю. Л. Воробьев, В.А. Акимов, Ю.И. Соколов, Системные аварии и катастрофы в техносфере России, МЧС России. М.: ФГБУ ВНИИ ГОЧС (ФК), 2012. 308 с.
[3] В.М. Кушнаренко, Ю.А. Чирков, К.Н. Матерко, А.В. Лукашов, Д.Н. Щепинов, Методы прогнозирования остаточного ресурса опасных производственных объектов, Машиностроение и машиностроение, Разведка, Инновационные инвестиции. 7 (2016) 177 – 123.
[4] Н.П. Алешин, Оценка остаточного ресурса сварных конструкций, Сварка и диагностика. 2 (2007) 4 – 10.
[5]
Е. Ю. Приймак, А.П. Фот, А.В. Степанчукова, Анализ случайных повреждений разведочных бурильных труб в процессе эксплуатации, Вопросы материаловедения. 1(89) (2017) 187 – 194.
[6] В.В. Клюев, Б.В. Артемьев, В.И. Матвеев, Состояние и развитие методов технической диагностики, Заводская лаборатория, Диагностика материалов. 81, 4 (2015) 73-78.
[7] Н.П. Алешин, Возможности методов неразрушающего контроля для оценки напряженно-деформированного состояния нагруженных металлоконструкций, Сварка и диагностика. 6 (2011) 44 – 47.
[8]
Расчеты и испытания на прочность, Метод рентгеноструктурного анализа трещин.
[9] Э.О. Киле, В.В. Корчевский, А.В. Сюй, Влияние инструментальных погрешностей рентгеновского дифрактометра на ширину дифракционной линии, Фундаментальные проблемы современного материаловедения. 2011. 8, 4 (2011) 7-10.
[10]
В.В. Корчевский, Е.А. Жуков, Е.О. Киле, А.В. Сюй, Исключение систематических погрешностей измерения ширины дифракционных линий численными методами, Вестник Тогу, Информатика, вычислительная техника и управление.
[11] Д.М. Левин, М.В. Булавин, С.А. Куликов, Исследование остаточных напряжений и текстур в стенках стальных труб методом нейтронной стресс-дифрактометрии, I. Пространственное распределение остаточных напряжений и микродеформаций, Вестник Тульского государственного университета, Естественные науки. 2, 1 (2013) 194–206.
[12]
П.А. Ершов, С.М. Кузнецов, И.И. Снигирева, В.А. Юнкин, А.Ю. Гойхман, А.А. Снигирев, Рентгеновская дифрактометрия высокого разрешения с использованием одномерных и двумерных преломляющих линз, Поверхностные, рентгеновские, синхротронные и нейтронные исследования. 6 (2015) 55–59.
DOI: 10.1134/s1027451015030234
[13] О.Г. Оспенникова, Е.И. Косарина, О.А. Крупнина Радиационный неразрушающий контроль – необходимый инструмент при создании и совершенствовании технологий новых авиационных материалов, 213-224.
[14] СРЕДНИЙ. Котелкин, И.Г. Роберов, Д.Б. Матвеев, И.С. Леднев, Определение остаточного ресурса и методы повышения уровня безопасности при эксплуатации конструкционных материалов в авиации, Современные материалы, техника и технологии. 1(4) (2016) 104 – 113.
[15]
Э. М. Гринберг, А.А. Алексеев, С.Г. Шеверев, Изменение тонкой структуры при низкотемпературном распаде мартенсита закаленной среднеуглеродистой стали, Проблемы материаловедения. 2(86) (2016) 20 – 25.
[16] А.Н. Тюменцев, И.А. Дитенберг, М.А. Корчагин, Исследование влияния интенсивного механического напряжения на параметры микроструктуры механокомпозитов состава 3Ti + Al, Физика металлов и металлургия. 111, 2 (2011) 195–202.
DOI: 10.1134/s0031918x11010236
[17]
Д.Н.Коротаев, Е.В. Иванова, Субструктурное поверхностное упрочнение деталей трибосистем электроискровым легированием, Перспективные материалы. 2 (2011) 98 – 102.
[18] А.Г. Акуличев, В.В. Трофимов, Измерение твердости закаленной стали рентгеноструктурным методом, Контроль и диагностика. 8 (2011) 45 – 49, https//lib. руконт. ком/эфд/486048.
Компьютерное моделирование и новые технологии
2019
2019, Том 23, № 1
2018
2018, Том 22, № 1
2017
2017, том 21, №4
2017, том 21, №3
2017, том 21, №2
2017, том 21, №1
2016
2016, том 20, №4
2016, том 20, №3
2016, том 20, №2
2016, том 20, №1
2015
2015, том 19, №6
2015, том 19, №5
2015, том 19, №4
2015, том 19, №3
2015, том 19, №2
2015, том 19, №1
2014
2014, том 18, №12
2014, том 18, №11
2014, том 18, №10
2014, том 18, №9
2014, том 18, №8
2014, том 18, №7
2014, том 18, №6
2014, том 18, №5
2014, том 18, №4
2014, том 18, №3
2014, том 18, №2
2014, том 18, №1
2013
2013, том 17, №5
2013, том 17, №4
2013, том 17, №3
2013, том 17, №2
2013, том 17, №1
2012
2012, том 16, №4
2012, том 16, №3
2012, том 16, №2
2012, том 16, №1
2011
2011, том 15, №4
2011, том 15, №3
2011, том 15, №2
2011, том 15, №1
2010
2010, том 14, №4
2010, том 14, №3
2010, том 14, №2
2010, том 14, №1
2009
2009, том 13, №4
2009, том 13, №3
2009 г.
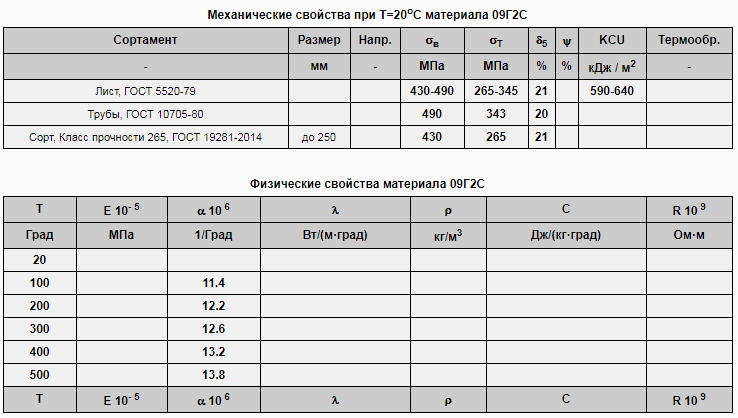