Характеристики стали 20х: Легированная сталь характеристики, свойства
alexxlab | 17.06.2023 | 0 | Разное
404 – Страница не найдена
Ваш регион
- Абакан
- Анадырь
- Архангельск
- Астрахань
- metall.life/marochnik/stal-20x”>
Барнаул
- Белгород
- Биробиджан
- Благовещенск metall.life/marochnik/stal-20x”> Брянск
- Владивосток
- Владикавказ
- Владимир metall.life/marochnik/stal-20x”> Волгоград
- Вологда
- Воронеж
- Горно-Алтайск metall.life/marochnik/stal-20x”> Грозный
- Екатеринбург
- Иваново
- Ижевск metall.life/marochnik/stal-20x”> Иркутск
- Йошкар-Ола
- Казань
- Калининград
- Кемерово
- Киров
- Кострома metall.life/marochnik/stal-20x”> Краснодар
- Красноярск
- Курган
- Ленинградская область
- Липецк
- Магадан metall.life/marochnik/stal-20x”> Магас
- Махачкала
- Москва metall.life/marochnik/stal-20x”> Московская область
- Мурманск
- Нальчик
- Нарьян-Мар metall.life/marochnik/stal-20x”> Нижний Новгород
- Новгород
- Новосибирск
- Омск metall.life/marochnik/stal-20x”> Орёл
- Оренбург
- Пенза
- Пермь metall.life/marochnik/stal-20x”> Петрозаводск
- Петропавловск-Камчатский
- Псков
- Ростов-на-Дону metall.life/marochnik/stal-20x”> Рязань
- Салехард
- Самара
- Санкт-Петербург metall.life/marochnik/stal-20x”> Саранск
- Саратов
- Симферополь
- Смоленск metall.life/marochnik/stal-20x”> Ставрополь
- Сыктывкар
- Тамбов
- Тверь metall.life/marochnik/stal-20x”> Томск
- Тула
- Тюмень
- Улан-Уде metall.life/marochnik/stal-20x”> Ульяновск
- Уфа
- Хабаровск
- Ханты-Мансийск
- metall.life/marochnik/stal-20x”>
Чебоксары
- Челябинск
- Черкесск
- Чита
- metall.life/marochnik/stal-20x”>
Элиста
- Южно-Сахалинск
- Якутск
- Ярославль
Оформить заявку
Сталь 20Х – расшифровка марки стали, ГОСТ, характеристика материала
- Нелегированные стали
- Легированные стали
- Нержавеющие стали
- 65Г
- ШХ15
- Р18
- Р6М5
- 9ХС
- ХВГ
- 09Г2С
- Х12МФ
- 12Х1МФ
- 12ХН3А
- 20Х
- 30ХМА
- 30ХГСА
- 40Х
- 40ХН
- 45Х
Марка стали – 20Х
Стандарт – ГОСТ 4543
Заменитель – 15Х, 20ХН, 12ХН2, 18ХГТ
Сталь 20Х содержит в среднем 0,2% углерода, Х – указывает содержание хрома в стали примерно 1%.
Из легированной конструкционной стали 20Х изготовляют детали (преимущественно некрупные) подвергаемые цементации и закалке: втулки, пальцы, зубчатые колеса, толкатели, валики, обоймы, гильзы, диски, плунжеры, рычаги, стяжные кольца, штоки впускных клапанов, шпиндели, оправки, червяки, направляющие планки и другие детали, к которым предъявляются требования высокой поверхностной твердости при невысокой прочности сердцевины, детали, работающие в условиях износа при трении.
Массовая доля основных химических элементов, % | |||
---|---|---|---|
C – углерода | Si – кремния | Mn – марганца | Cr – хрома |
0,17-0,23 | 0,17-0,37 | 0,50-0,80 | 0,70-1,00 |
Температура критических точек, °С | |||
---|---|---|---|
Ac1 | Ac3 | Ar1 | Ar3 |
750 | 825 | 665 | 755 |
Технологические свойства | |
---|---|
Ковка | Температура ковки, °С: начала 1260, конца 750.![]() |
Свариваемость | Сваривается без ограничений, кроме деталей после химико-термической обработки. Способы сварки: ручная дуговая сварка. Контактная сварка – без ограничений. |
Обрабатываемость резанием | В горячекатаном состоянии состоянии при HB 131 и σв = 460 МПа: Kv твердый сплав = 1,7 Kv быстрорежущая сталь = 1,3 |
Флокеночувствительность | Малочувствительна |
Склонность к отпускной хрупкости | Не склонна |
Физические свойства | Температура испытаний, °С | |||||||||
---|---|---|---|---|---|---|---|---|---|---|
20 | 100 | 200 | 300 | 400 | 500 | 600 | 700 | 800 | 900 | |
Модуль нормальной упругости E, ГПа | 216 | 213 | 198 | 193 | 181 | 171 | 165 | 143 | 133 | – |
Модуль упругости при сдвиге кручением G, ГПа | 84 | 83 | 76 | 74 | 71 | 67 | 62 | 55 | 50 | – |
Плотность ρn, кг/м3 | 7830 | 7810 | 7780 | – | 7710 | – | 7640 | – | – | – |
Коэффициент теплопроводности λ, Вт/(м*К) | 42 | 42 | 41 | 40 | 38 | 36 | 33 | 32 | 31 | – |
Удельное электросопротивление ρ, нОм*м | – | – | – | – | – | – | – | – | – | – |
20-100 | 20-200 | 20-300 | 20-400 | 20-500 | 20-600 | 20-700 | 20-800 | 20-900 | 20-1000 | |
Коэффициент линейного расширения α*106, K-1 | 10,5 | 11,6 | 12,4 | 13,1 | 13,6 | 14,0 | – | – | – | – |
Удельная теплоемкость c, Дж/(кг*К) | 496 | 508 | 525 | 537 | 567 | 588 | 626 | 706 | – | – |
Структура металлических зерен и микроскопический анализ
Struers – Обеспечение уверенности / Знание / Материалы / Металлические зернистые структуры
Металлические материалы часто интерпретируются с точки зрения их внутренней структуры, известной как микроструктура. Эти рекомендации по применению, подготовленные в сотрудничестве с экспертами в области оптики и оптоэлектроники Zeiss, объясняют все, что вам нужно знать о структурных свойствах металла, подготовке материалов для микроструктурного анализа и интерпретации результатов.
Загрузите полную информацию о приложении
- Основные показатели
- Металлографическая подготовка
- Микроскопический анализ
- Характеристика анализа
- Оборудование
Внутренняя структура металла состоит из отдельных кристаллических областей, известных как «зерна». Структура, размер и ориентация этих зерен зависят от состава материала (сплава) и способа изготовления материала (например, ковка, литье или аддитивное производство). Зерна образуются из расплавленного материала при его затвердевании, взаимодействуют друг с другом и с другими ингредиентами, такими как фазы и загрязнения. Как правило, структура зерна адаптирована к техническому применению.
Размер и ориентация зерен и другие структурные характеристики напрямую связаны с механическими и технологическими свойствами этих материалов. Структурные характеристики также зависят от последующих внешних воздействий. Эти воздействия включают:
- Химические воздействия (например, коррозию)
- Химические и/или физические воздействия (например, процессы термообработки)
- Механические воздействия (например, после процессов формовки, таких как ковка, прокатка, гибка и т. д.)
Микроструктура
Рис. 1: Чистая медь, протравленная в DIC
Микроструктуру можно оценить только под микроскопом (стереомикроскопом, световым микроскопом с использованием отраженного света, цифровым микроскопом или сканирующим и просвечивающим электронным микроскопом). Обычно размер наблюдаемых характеристик колеблется от долей миллиметров до микрометров и даже нанометров. Наблюдения за микроструктурой используются для широкого круга исследований, например, для определения размеров зерен, проверки на наличие дефектов, подготовки мишеней в микроэлектронике, всех видов сварных швов и анализа отказов.
Макроструктура
Рис. 2: Макрошлиф чистой меди, часть литого блока, травление
Макроструктуру можно увидеть невооруженным глазом, через увеличительное стекло или стереомикроскоп. Эти наблюдения менее распространены, чем микроструктурные исследования. Области применения, в которых наблюдается макроструктура, обычно представляют собой сварные швы, отливки некоторых цветных металлов или деформацию и сегрегацию на литых или кованых деталях. Грубая оценка покрытий или геометрии также может быть предметом макроструктурных исследований.
Почему микроскопический анализ?
После завершения металлографической подготовки структурные свойства металла можно проанализировать под микроскопом. После этого можно сделать выводы о характеристиках материала. Например, микроскопический анализ можно использовать для оценки характеристик на этапах проектирования и обработки металла, а также случаев, когда произошло повреждение.
Структурные элементы, которые можно оценить с помощью светового или электронного микроскопа, включают:
- Зерна/кристаллиты и границы их зерен
- Интерметаллические фазы и выделения
- Неметаллические включения и фазы
Оценка основана на следующих критериях:
- Тип и форма
- Размер и номер
- Распределение и ориентация
На основе всей этой информации затем можно создать всестороннее описание микроструктуры и сделать выводы относительно ее потенциальных характеристик.
Понятие о сплавах
Материалы, используемые сегодня в практических целях, представляют собой смесь различных химических элементов, часто также называемую «сплавами». Сталь и чугун, например, по существу представляют собой сплавы на основе железа (Fe) с легирующими добавками углерода (C), которые отвечают за твердость железосодержащего материала. Микроструктурный анализ позволяет сделать выводы о свойствах сплава, в том числе о его прочности, твердости и пластичности
Рис. 3: Перлитный чугун с пластинчатым графитом, протравленный ниталом. Углерод в основном присутствует в виде графита в пластинчатой форме, что приводит к снижению прочности. Сама перлитная матрица обладает достаточно высокой степенью твердости.
Изображение получено с помощью ZEISS Axio Imager, объектив 50x, яркое освещение
Рис. 4: Ферритный чугун со сфероидальным графитом, протравленный ниталом. Углерод в основном присутствует в виде графита в сферической форме. Сферическая форма обеспечивает повышенную прочность по сравнению с пластинчатым чугуном, но твердость материала ниже из-за отсутствия цементита в чисто ферритной матрице.
Изображение сделано с помощью ZEISS Smartzoom 5, прибл. 500-кратное увеличение
Рис. 5: Ферритная сталь с прибл. 0,1 % С, протравлен ниталом. Углерод в основном присутствует в форме цементита и в виде небольшого количества перлита между ферритными зернами. Матрица, которая поэтому является почти чисто ферритной, имеет низкую степень твердости, но очень хорошую пластичность.
Снимок сделан с помощью ZEISS Smartzoom 5 прибл. 500-кратное увеличение, коаксиальное освещение с малой долей кольцевого света
Рис. 6: Ферритно-перлитная сталь с прибл. 0,2 % C, протравлен ниталом. Углерод в основном присутствует в виде пластинчатого цементита в более твердой части перлита, прилегающей к ферритным зернам. Это приводит к тому, что цементит выглядит полосатым. Перлитные зерна отражают меньше света, чем ферритные зерна, и поэтому кажутся более темными. Матрица этого типа имеет более высокую твердость, но более низкую пластичность.
Изображение получено с помощью ZEISS Axiolab, объектив 50x, яркое освещение
Металлографическая подготовка металла к микроструктурному анализу
Чтобы обеспечить правильное представление структурных свойств металла, образец должен быть правильно подготовлен.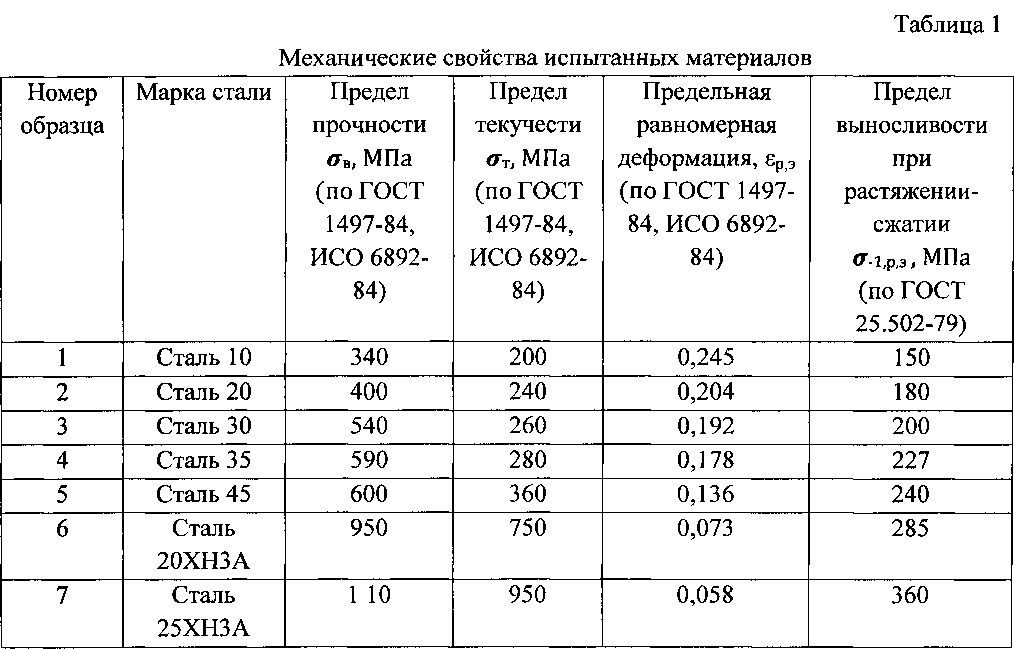
Шаг 1: Резка заготовок для микроструктурного анализа
Процесс мокрой абразивной резки используется для отбора репрезентативной пробы из заготовки. Процесс резки следует выбирать таким образом, чтобы образец не подвергался никаким повреждениям, способным изменить его структуру, и должен быть адаптирован к материалу и применению.
Рис. 7: Станок для мокрой абразивной резки с зажатым зубчатым колесом, используемый для взятия образца с участка зуба зубчатого колеса. Как правило, секция подвергается индукционной или поверхностной закалке. Образец будет использоваться для изучения структуры и твердости среза.
Узнать больше
- Получите больше знаний, опыта и знаний в нашем разделе резки.
- Ознакомьтесь с нашим ассортиментом режущего оборудования.
- Приобрести расходные материалы и аксессуары для металлографической резки.
Этап 2: Установка образцов для микроструктурного анализа
Процесс монтажа используется для фиксации отрезанных деталей, чтобы с ними было легче обращаться, и для стандартизации их размеров. Можно использовать различные методы горячего и холодного монтажа и смолы, хотя типичными являются эпоксидная или акриловая смола.
- Холодный монтаж: прибл. 100°С, при атмосферном давлении или в вакууме
- Горячий монтаж: при макс. 350 бар и 180 °C
Рис. 8: Множество встроенных образцов различной формы. Покрытие образца синтетической смолой обеспечивает хороший результат подготовки и повышает эффективность остальной части процесса.
Узнать больше
- Получите больше знаний, опыта и знаний в нашем разделе монтажа.
- Ознакомьтесь с нашим ассортиментом монтажных машин и оборудования.
- Приобрести расходные материалы и аксессуары для металлографического горячего и холодного монтажа.
Этап 3: Шлифовка и полировка образцов для микроструктурного анализа
Процесс шлифовки и полировки является наиболее важным этапом подготовки образца для исследования под микроскопом. Во время этого процесса макроскопическая шероховатость поверхности реза уменьшается до отражающей поверхности.
Если цель состоит только в том, чтобы сделать видимой макроструктуру – обычно для исследования с использованием стереомикроскопа или увеличительного стекла – достаточно нескольких стадий грубой шлифовки и контрастирования кислыми или щелочными растворами. (Эти образцы часто готовятся в размонтированном виде для экономии времени.)
Чтобы микроскопические элементы конструкции были видны под микроскопом в отраженном свете, требуется зеркальное покрытие. Процесс шлифовки и полировки зеркала выглядит следующим образом:
- На поверхности выполняется начальная грубая шлифовка.
- Поверхность аккуратно полируется абразивами от мелких до очень мелких до тех пор, пока не будут удалены почти все поврежденные участки, обычно с использованием алмаза, оксида алюминия или коллоидного диоксида кремния на подходящих тряпках и дисках для полировки.
- Поверхность проверяется с помощью дифференциального интерференционного контраста (ДИК) — опции контраста в микроскопах отраженного света — для обеспечения достаточно высокого качества поверхности для продолжения травления. Если деформация все еще видна в DIC, требуются дополнительные этапы полировки.
- Поверхность протравлена для усиления контрастов, невидимых или видимых только в ограниченной степени в условиях яркого поля. Обычно используют только слабые кислоты.
- Низкоконцентрированные травители, содержащие 1-3% азотной кислоты в этаноле (нитал), очень часто используются для низколегированных и среднелегированных углеродистых сталей или чугуна.
- Коррозионностойкая сталь требует специальных процессов травления, таких как цветное травление.
Рис. 9: Сварочный шов, зачищенный на двух уровнях фольги SiC, с последующим макротравлением 5 % водным раствором азотной кислоты.
Изображение получено с помощью стереомикроскопа ZEISS Stemi 508 при 15-кратном увеличении
Рис. 10: Ферритная сталь с включениями карбида и оксида титана после механической обработки алмазом размером 1 мкм. На дифференциально-интерференционно-контрастном изображении еще можно наблюдать тонкие следы деформации. Образец не подвергался травлению.
Изображение получено с помощью ZEISS Axio Imager, DIC, объектив 100x .
Рис. 11: Коррозионностойкая аустенитная сталь после окончательной полировки с помощью OP-S и последующего цветного травления по Лихтенеггеру и Блеху. Становятся видны зерна аустенита с двойниками и ложными линиями в направлении деформации.
Изображение получено с помощью ZEISS Axio Imager, яркое освещение, объектив 20x .
Рис. 12: Коррозионностойкая аустенитно-ферритная сталь (дуплекс) после электролитического травления в 20 % растворе гидроксида натрия. Зерна аустенита (светло-коричневые) внедрены в голубовато-коричневую ферритную матрицу.
Снимок сделан с помощью ZEISS Axiolab, DIC, объектив 20x
Подробнее
- Получите больше знаний, опыта и информации о нашем участке шлифовки и полировки.
- Ознакомьтесь с нашим ассортиментом шлифовальных и полировальных станков и оборудования.
- Приобрести расходные материалы и аксессуары для металлографической шлифовки и полировки.
Анализ структуры металлических зерен
После завершения металлографической подготовки структуры металлических зерен можно визуально проанализировать под световым микроскопом. Обычно это происходит при увеличении от 25x до 1000x, что соответствует ограничениям традиционной световой микроскопии. Решетчатые дефекты, структуры и элементы на субмикроскопическом уровне (менее 1 мкм) и вплоть до атомарного уровня оцениваются с помощью электронных микроскопов.
Таблица 1: Примеры применения методов контрастирования для исследования металлических конструкций
Методы контрастирования
Существует ряд методов контрастирования, которые можно использовать для оценки структурных свойств металла. Ваш выбор метода контрастирования зависит от ряда факторов, в том числе от того, с каким материалом вы работаете и какие характеристики вам необходимо проанализировать. Какие методы контрастирования существуют и когда их следует использовать?
Светлое поле
Брайтфилд — это стандартный метод для всех типов анализа материалов. Трещины и поры, неметаллические фазы и продукты окисления сначала наблюдают в непротравленном состоянии, поскольку они обычно демонстрируют иное отражающее поведение, чем основной металл. С другой стороны, расположение трещин и пор по отношению к другим структурным характеристикам обычно можно оценить только в том случае, если было проведено соответствующее химическое травление.
Рис. 13: Лазерный сварной шов на высоколегированных сталях с трещинами и порами после электролитического травления. Они также видны в непротравленном состоянии, но межкристаллитный ход трещин можно оценить только после завершения травления.
Изображение получено с помощью ZEISS Axio Imager, яркое освещение, объектив 5x .
Темное поле
Метод темного поля в основном используется в микроскопии неметаллических материалов. Однако он дает несколько преимуществ при характеристике металлов, а также при оценке окрашенных структур, таких как слои лака или пластиковых покрытий на металлических подложках. Его также можно использовать для оценки продуктов коррозии. Микроскопию в темном поле можно использовать для выявления очень мелких царапин на полированных образцах. способ проверки качества помола.
Рис. 14: Место коррозии на латунной трубе, непротравленное. Отражающие участки кажутся темными (металлическая подложка) при освещении в темном поле, тогда как продукты коррозии можно наблюдать в собственном цвете.
Изображение получено с помощью ZEISS Axio Imager, освещение темного поля, объектив 20x
ДИК (дифференциально-интерференционный контраст)
ДИК — полезный инструмент для анализа очень тонких деформаций, которые все еще могут присутствовать на поверхности после полировки. Его также можно использовать для различения твердых и мягких структурных элементов, так как твердые фазы в процессе окончательной полировки удаляются в меньшей степени, чем более мягкие, и поэтому «выступают» с поверхности. Эта минимальная разница обычно не видна в светлопольном микроскопе, но ее можно увидеть в ДИК. В результате ДИК можно использовать для качественного различия между твердостью различных фаз.
С помощью DIC также можно сделать структуры зерен, такие как границы зерен, видимыми в непротравленном состоянии. Это позволяет оценить структуру перед травлением, избавляя от необходимости использовать химические вещества на труднопротравливаемых материалах, таких как коррозионно-стойкие металлы. Однако в этом случае требуется идеальная окончательная полировка.
Рис. 15: Медный сплав после окончательной полировки. Из-за своей отражательной способности различные фазы имеют разные цвета под микроскопом со светлым полем.
Изображение получено с помощью ZEISS Axiolab, яркое освещение, объектив 100x .
Рис. 16: Медный сплав после окончательной полировки. Из-за своего поведения при абляции фазы различной твердости имеют разную высоту, которая видна только в ДИК-микроскопии. Это позволяет качественно различать их твердость. В то же время зернистую структуру можно сделать видимой уже в непротравленном состоянии.
Изображение получено с помощью ZEISS Axiolab, DIC, объектив 100x
Контраст поляризации
Поляризационный контраст в основном используется при анализе материалов с гексагональной структурой решетки, таких как титан, цинк и магний. Алюминий и его сплавы также можно анализировать в поляризованном свете, если они были подвергнуты электролитическому травлению тетрафторборной кислотой (травление Баркера).
Рис. 17: Технически чистый титан (сорт 1) после механической полировки, вид под поляризационно-контрастным микроскопом, без травления. Поляризованный свет усиливается или устраняется на гранях кристалла благодаря гексагональной структуре решетки, которая проявляется как контраст между светлым и темным. Изображение появляется в цвете благодаря так называемой пластине λ/4.
Изображение получено с помощью ZEISS Axio Imager, поляризационный контраст, объектив 20x
Рис. 18. Сварочный шов алюминия после электролитического травления тетрафторборной кислотой (травление по Баркеру), вид под поляризационно-контрастным микроскопом. Травление создает слой оксида различной толщины в зависимости от ориентации кристаллов; поляризованный свет может мешать этому оксидному слою, что приводит к эффектам устранения и усиления.
Изображение получено с помощью ZEISS Axio Imager, поляризационный контраст, объектив 5x
Флуоресценция
Флуоресценция может использоваться в микроскопии металлов и материалов, поскольку некоторые материалы возбуждаются при определенной длине волны и поэтому излучают видимый свет при другой длине волны.
Флуоресцентные порошки (например, EpoDye) смешиваются с монтажной смолой (обычно прозрачной эпоксидной смолой) в процессе монтажа и проникают в существующие и открытые поры и трещины. Эта процедура поддерживается вакуумной пропиткой. После отверждения и подготовки свет микроскопа в синем спектре возбуждает флуоресцентный краситель, который затем излучает свет в желто-зеленом спектре. Заполненные поры или трещины подсвечиваются желто-зеленым цветом.
Рис. 19: Поры и трещины между покрытием из карбида вольфрама и сталью, на которую оно нанесено. На соответствующем контрасте микроскопа он подсвечивается желто-зеленым цветом, потому что трещина была пропитана монтажным агентом с флуоресцентным порошком. Трещина была до монтажа. Это могло произойти во время изготовления или в процессе резки.
Изображение получено с помощью ZEISS Axio Imager, флуоресцентный контраст, объектив 5x .
Рис. 20: Трещины в композитном материале из углеродного волокна.
Изображение получено с помощью ZEISS Axio Imager, флуоресцентный контраст, объектив 20x
Световой микроскоп для анализа структуры зерна
Микроструктурный анализ — чрезвычайно полезный инструмент в металлографии, так как он позволяет получить большой объем информации о структурных свойствах металла и его характеристиках. Это можно использовать для оценки этапов проектирования и обработки металла, а также для контроля качества и анализа отказов. Однако при рассмотрении структурных свойств металла необходимо использовать специальную оптику, поскольку возбуждение и освещение объекта направляются через одну и ту же оптическую систему. Камеры также должны быть способны обрабатывать высокие значения контрастности.
- Микроскопы отраженного света используются для визуализации структур в диапазоне от нескольких миллиметров до примерно 1 мкм (объективы 10x/20x/50x/100x типичны для микроскопа материалов). Микроскоп может быть как прямым, так и перевернутым. Однако перевернутое положение предпочтительнее для больших образцов или при просмотре зажатых образцов в держателях образцов.
- Стереомикроскопы высокого разрешения реже используются для структурной интерпретации. Изображение, созданное микроскопом, должно быть воспроизведено точно и подходить для интеграции в существующие системы документирования.
Точное выравнивание поля (EPI)
Поскольку освещение и контрастирование отражающих образцов осуществляется визуализирующей оптикой – объективом микроскопа, к конструкции и световоду предъявляются особые требования. Кроме того, объектив должен иметь точные характеристики выравнивания поля для измерения объекта. Эти типы объективов специально оптимизированы для образцов в отраженном свете и могут быть распознаны по аббревиатуре EPI (например, ZEISS 50x EC EPIPLAN # 422070-9).961-000).
Цифровые камеры
Требования к цифровой камере для металлических образцов должны быть оптимизированы для целей измерения и документирования. Микросхема высокодинамичной видеокамеры идеально отображает металлические поверхности и их высокий уровень контрастности. Специальные пакеты промышленного программного обеспечения (такие как «ZEN core» и его материальные модули) доступны для помощи при использовании камеры этого типа (например, ZEISS Axiocam 305) в практических условиях.
Микроскопы для начинающих
Микроскопы, такие как ZEISS Primotech, включают наиболее распространенные методы контрастирования, а также могут использоваться с упрощенным программным обеспечением MATSCOPE и решениями для планшетов (MATSCOPE для iPad).
Цифровые микроскопы
Благодаря быстрому развитию оптики цифровые микроскопы становятся все более интересным инструментом для структурного анализа. Эти устройства просты в использовании и сочетают в себе преимущества стереомикроскопии и микроскопии в отраженном свете. Они также охватывают относительно широкий спектр увеличения и области применения, а также предоставляют большие возможности для цифровой постобработки изображений для широкого круга измерительных задач. Однако цифровые микроскопы не обладают таким высоким разрешением, как микроскопы отраженного света, что является недостатком при работе с очень мелкими структурными элементами.
СКАЧАТЬ ПРИЛОЖЕНИЕ
Получить представление о других материалах
Если вы хотите узнать больше о материалографии других металлов и материалов, посетите нашу страницу материалов.
Получить полную информацию о приложении
Хотите прочитать полную информацию о структуре металлических зерен и микроскопическом анализе? Загрузите его здесь.
Это указание по применению было подготовлено нашим специалистом по применению Хольгером Шнарром в сотрудничестве с оптикой и оптоэлектроникой. специалисты Цейсс. Для получения конкретной информации о структуре металлических зерен и микроскопическом анализе свяжитесь с нашими специалистами по применению.
Свойства проволоки из углеродистой стали
23 декабря 2022 г. 23 декабря 2022 г. | 4:28
Для инженеров и рабочих-металлистов понимание свойств проволоки из углеродистой стали необходимо для производства высококачественной продукции. Как один из наиболее часто используемых металлов, проволока из углеродистой стали сочетает в себе прочность, пластичность и доступность. В этом сообщении блога мы обсудим различные характеристики, которые делают проволоку из углеродистой стали таким универсальным материалом.
Химический состав
Проволока из углеродистой стали состоит в основном из железа с низким содержанием других элементов, таких как углерод и марганец. Количество углерода, присутствующего в металле, может варьироваться от 0,5% до 2%, а содержание марганца колеблется от 0,4% до 1,4%. Это изменение в составе придает углеродистой стали уникальные свойства, которые подходят для использования в различных областях.
Механические свойства
Механические свойства углеродистой стали определяются ее химическим составом и процессом термической обработки. Предел прочности при растяжении и предел текучести зависят от количества углерода, присутствующего в сплаве; более высокие уровни приводят к более высоким прочностным характеристикам с большей устойчивостью к концентрациям стресса. Кроме того, коэффициент теплового расширения углеродистой стали относительно низок по сравнению с другими материалами, что делает ее идеальной для использования в условиях частых перепадов температуры или экстремальных температур.
Пластичность
Одним из наиболее важных механических свойств проволоки из углеродистой стали является ее пластичность. Пластичность – это мера способности материала деформироваться при растяжении. Проволока из углеродистой стали очень пластична, а это означает, что ее можно вытягивать в тонкие проволоки, не ломая. Это свойство необходимо для многих применений, например, при производстве электрических кабелей и проволочной сетки.
Прочность на растяжение
Еще одним важным механическим свойством проволоки из углеродистой стали является ее прочность на растяжение. Прочность на растяжение — это мера способности материала выдерживать растяжение или растяжение без разрушения. Проволока из углеродистой стали обладает очень высокой прочностью на растяжение, что делает ее идеальной для применений, где присутствуют высокие уровни натяжения, например, в растяжках или подвесных мостах.
Эластичность
Проволока из углеродистой стали также имеет высокую степень эластичности. Эластичность – это мера способности материала возвращаться к своей первоначальной форме после деформации. Проволока из углеродистой стали способна возвращаться к своей первоначальной форме после растяжения или вытягивания, что делает ее идеальной для применений, в которых присутствует повторяющаяся нагрузка, например, в пружинах или амортизаторах.
Высокотемпературная стойкость
Проволока из углеродистой стали также имеет превосходную жаропрочность. Это означает, что он может сохранять свою структурную целостность при повышенных температурах, что делает его идеальным для использования в высокотемпературных средах, например, в печах или котлах.
Коррозионная стойкость
Проволока из углеродистой стали также обладает хорошей коррозионной стойкостью. Это означает, что она не будет легко ржаветь под воздействием влаги или других агрессивных веществ.
Физические свойства
Углеродистая сталь также имеет несколько физических свойств, которые делают ее привлекательным выбором при работе с металлами. Температура плавления большинства сортов колеблется в пределах 1500-1600 градусов по Цельсию, что позволяет легко придавать ему различные формы с помощью процессов литья или ковки. Кроме того, благодаря своей пластичности он может пластически деформироваться без необходимости какой-либо термической обработки после формования, что способствует снижению производственных затрат. Наконец, поскольку он легко подвергается коррозии при воздействии воды или влаги, он должен быть защищен покрытиями или обработанными сплавами при использовании на открытом воздухе или во влажной среде для обеспечения долговременной работы и надежности.
Плотность
Плотность проволоки из углеродистой стали обычно составляет от 7,8 до 8,1 грамма на кубический сантиметр. Это дает ему относительно высокую плотность по сравнению с другими металлами, что делает его идеальным для применений, где важным фактором является вес.
Прочность
Проволока из углеродистой стали также очень прочная, с пределом прочности на разрыв до 2200 мегапаскалей. Это делает его идеальным для применений, где требуются прочность и долговечность, например, при строительстве мостов или зданий.
Коррозионная стойкость
Проволока из углеродистой стали обладает отличной коррозионной стойкостью благодаря наличию в ее составе хрома. Это делает его идеальным для наружного применения или для использования в средах, где коррозия может быть проблемой.
Теплопроводность
Проволока из углеродистой стали имеет теплопроводность приблизительно 50 Вт на метр на кельвин. Это означает, что он является отличным проводником тепла, что делает его идеальным для приложений, где требуется быстрая передача тепла.
Электропроводность
Проволока из углеродистой стали также является отличным проводником электричества, ее проводимость примерно на 60% больше, чем у меди. Это делает его идеальным для электрических применений, где важна проводимость.
Магнетизм
Проволока из углеродистой стали также слабомагнитна из-за наличия в ее составе железа.