Искусственное старение алюминия – Термообработка алюминиевых сплавов: виды и режимы
alexxlab | 23.04.2020 | 0 | Разное
Термообработка алюминиевых сплавов: виды и режимы
Термическая обработка алюминиевых сплавов предназначена для корректировки характеристик материала с помощью воздействия высоких температур. Различными способами обработки можно добиться широкого разнообразия структуры и свойств.
Сплавы, которые содержат примеси в размере 15-18%, имеют вид твердого раствора. В качестве дополнительных компонентов применяются медь, магний, цинк, кремний и другие вещества, различное сочетание которых и их процентное соотношение прямо пропорционально влияют на свойства материала.
В обычном состоянии алюминиевые сплавы не отличаются высокой прочностью, при этом довольно пластичны. Наиболее неустойчивые сплавы включают в состав большое количество легирующих компонентов, которые влияют на равновесную структуру.
Для упрочнения алюминиевых сплавов применяется методы термообработки. Путем равномерного нагрева, который регламентируется техническими условиями, получают соответствующую структуру, необходимую для начальной стадии распада твердого раствора.
С помощью термообработки можно получить множество типов структуры материала, которые соответствуют требованиям производства. Термическая обработка позволяет создать структуру, не имеющую аналогов.
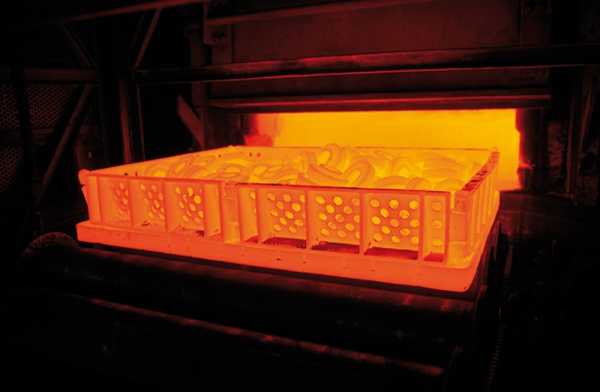
На сегодняшний день разработано множество методов термообработки алюминиевых изделий, среди которых наибольшую популярность обрели три: отжиг, закалка, старение.
Особенности термообработки алюминиевых сплавов
Алюминий и его сплавы требуют особого подхода к термообработке для достижения определенной прочности и структуры материала. Очень часто применяют несколько методов термообработки. Обычно, после закалки следует старение. Но некоторые типы материалов могут подвергаться старению без закалки.
Такая возможность появляется после отливки, когда компоненты, при повышенной скорости охлаждения, могут придать металлу необходимую структуру и прочность. Это происходит во время литья при температуре около 180 градусов. При такой температуре повышается уровень прочности и твердости, а также снижается степень тягучести.
Каждый из методов термообработки имеет некоторые особенности, которые стоит учитывать при обработке алюминиевых изделий.
Отжиг необходим для придания однородной структуры алюминиевому сплаву. С помощью этого метода состав становиться более однородным, активизируется процесс диффузии и выравнивается размер базовых частиц. Также можно добиться снижения напряжения кристаллической решетки. Температура обработки подбирается индивидуально, исходя из особенностей сплава, необходимых конечных характеристик и структуры материала.
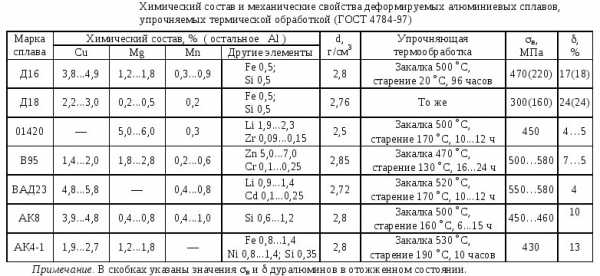
Состав и свойства алюминиевых сплавов, упрочняемых термической обработкой
Важным этапом отжига является охлаждение, которые можно проводить несколькими способами. Обычно проводят охлаждения в печи или на открытом воздухе. Также применяется поэтапное комбинированное охлаждение, сначала в печи, а потом на воздухе.
От скорости снижения температуры напрямую зависят характеристики готового материала. Быстрое охлаждение способствует образованию перенасыщенности твердого раствора, а медленное – значительного уровня распада твердого раствора.
Закалка требуется для упрочнения материала путем перенасыщения твердого раствора. Этот метод основан на нагреве изделий температурам и быстром охлаждении. Это способствует полноценному растворению составных элементов в алюминии. Используется для обработки деформируемых алюминиевых сплавов.
Для использования этого способа нужно правильно рассчитать температуру обработки. Чем выше степень, тем меньше времени требуется на закалку. При этом стоит подобрать температуру так, чтобы она превышала значение, необходимое для растворимости компонентов, но была меньше границы расплава металла.
Методом старения достигается увеличение прочности алюминиевого сплава. Причем необязательно подвергать изделия искусственному старению, так как возможен процесс естественного старения.
В зависимости от типа старения изменяется скорость структурных изменений. Поэтому искусственное старение более предпочтительно, так как оно позволяет повысить производительность работ. Подбор температуры и времени обработки зависит от свойств материала и характеристик легирующих компонентов.
Правильное сочетание уровня нагрева и времени выдержки позволяет повысить прочность и пластичность. Такой процесс называется стабилизацией.
Методы отжига алюминиевых листов
Отжиг алюминиевых сплавов не является обязательным к применению. Но в некоторых случаях без этого способа термообработки невозможно достичь желаемых характеристик материала.
Причиной применения отжига может стать особое состояние сплава, которое может выражаться в понижении пластичности материала.
Применение отжига рекомендуется при наблюдении трех типов состояний:
- Свойственное литым изделиям неравновесное состояние связано с разницей температурных режимов. Скорость охлаждения литых изделий значительно превышает рекомендуемую, при которой достигается эффект равновесной кристаллизации.
- Пластическая деформация. Такое состояние может быть вызвано технологическими требованиями к характеристикам и форме готового изделия.
- Неоднородная структура материала, вызванная иными методами термообработки, в том числе закалкой и старением. В таком случае происходит выделение одного из легирующих компонентов в интерметаллидную фазу, сопровождающуюся перенасыщением компонентов.
Вышеуказанные проблемы могут устранятся методом отжига. Нормализация структуры и состояния алюминиевого сплава сопровождается повышением пластичности. В зависимости от типа неравновесного состояния подбираются различные методы отжига.
На сегодняшний день выделяют три режима отжига:
- Гомогенизация. Предназначен для обработки литых слитков. В процессе термической обработки слитков при высоких температурах достигается равномерная структура. Это позволяет упростить процесс проката с уменьшением количества производственных расходов. В некоторых случаях может применяться для повышения качества деформированных изделий. Температура отжига соблюдается в пределах 500 градусов с последующей выдержкой. Охлаждение можно проводить несколькими способами.
- Рекристаллизация. Применяется для восстановления деформированных деталей. При этом требуется предварительная обработка прессом. Температура отжига варьируется в диапазоне от 350 до 500 градусов. Время выдержки не превышает 2-х часов. Скорость и способ охлаждения не имеет особых рамок.
- Гетерогенизация. Дополнительная отжиг после других методов термообработки. Этот метод необходим для разупрочнения алюминиевых сплавов. Данный метод обработки позволяет понизить степень прочность с одновременным повышением уровня пластичности. Отжиг производится примерно при 400 градусах Цельсия. Выдержка обычно составляет 1-2 часа. Этот тип отжига значительно улучшает эксплуатационные характеристики металла и повышают степень сопротивления коррозии.
Закалка алюминиевых отливов
Закалка подходит не для всех типов алюминиевых сплавов. Для успешного структурного изменения, сплав должен содержать такие компоненты как медь, магний, цинк, кремний или литий. Именно эти вещества способны полноценно растворится в составе алюминия, создав структуру, имеющую отличные от алюминия свойства.
Данный тип термообработки проводиться при интенсивном нагреве, позволяющем составным элементам раствориться в сплаве, с дальнейшим интенсивным охлаждением до обычного состояния.
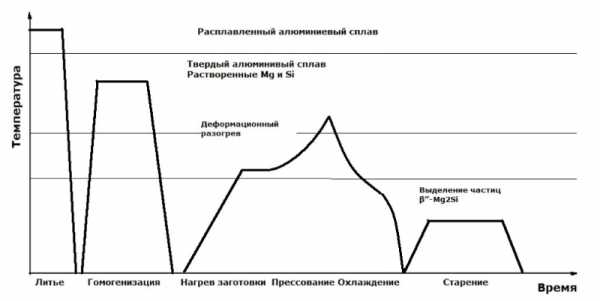
Термические превращения в сплавах 6060, 6063, АД31
При выборе температурного режима следует ориентироваться на количество меди. Также, нужно учитывать свойства литых изделий.
В промышленных условиях температура нагрева под закалку колеблется в диапазоне от 450 до 560 градусов. Выдержка изделий при такой температуре обеспечивает расплавление компонентов в составе. Время выдержи зависит от типа изделия, для деформированных обычно не превышает более часа, а для литых – от нескольких часов до двух суток.
Скорость охлаждения при закалке необходимо подбирать так, чтобы состав алюминиевого сплава не подвергался распаду. На промышленном производстве охлаждение проводят с помощью воды. Однако такой способ не всегда оптимально подходит, так как при охлаждении толстых изделий происходит неравномерное снижение температуры в центре и по краям изделия. Поэтому для крупногабаритных и сложных изделий применяются другие методы охлаждения, которые подбираются индивидуально.
Старение алюминиевых сплавов
Старение проводится для улучшения прочностных характеристик изделия. Этот вид термической обработки заключается в выдержке в условиях обычного температурного режима.
Повышение прочности достигается путем распада твердого раствора, что необходимо после закалки, так как закалка приводит к пресыщенности металла.
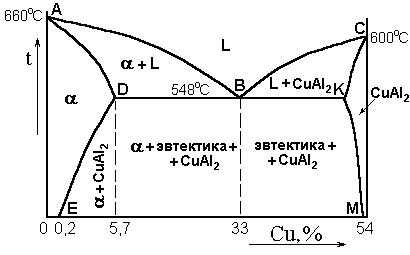
Термообработка дюралюминия
Существует два способа старения алюминиевых сплавов: естественное и искусственное.
Естественное старение происходит без предварительного нагрева при обычных температурах. Это может происходить в условиях обычного склада или промышленного помещения, где температура воздуха не превышает 30 градусов.
Естественное старение возможно из-за особого свойства алюминия, которое называется «свежезакаленное состояние». Свойства изделий значительно отличаются сразу после закалки и после некоторого времени пребывания на складе.
Искусственное старение проводится путем нагрева изделий до температуры 200 градусов. Это активирует процесс диффузии, что способствует улучшенному растворению составных элементов. Выдержка составляет от нескольких часов до нескольких суток.
Следует отметить, что искусственно состаренные сплавы можно вернуть к изначальному состоянию. Для этого нужно нагреть изделие до 250 градусов с выдержкой до одной минуты. Выдержка должна проводится в селитряной ванне в строго определенное время, с точностью до нескольких секунд.
Причем подобный возврат можно выполнять несколько раз, без потери прочности материала, но с небольшим изменением свойств. Возврат состаренного металла обычно проводят с целью восстановления пластичности, необходимой для изменения формы изделия.
Любой из типов термообработки широко используется в промышленности. Благодаря чему у производителей есть возможность получения материалов, полностью соответствующих требованиям производства. Причем такая обработка сплавов позволяет значительно улучшить свойства алюминия и получить материал, не имеющий аналогов.
Главное условие при термообработке – соблюдение требований и рекомендаций к температурному режиму обработки и времени выдержки. Малейшие отклонения могут привести к необратимым изменениям свойств материала.
Если вы нашли ошибку, пожалуйста, выделите фрагмент текста и нажмите Ctrl+Enter.
stankiexpert.ru
Закалка и старение алюминия
Закалка алюминиевых профилей на прессе
Скорость охлаждения алюминиевых профилей — закалка — сразу после выхода из пресса должна быть достаточно быстрой, чтобы задержать магний и кремний в твердом растворе. Это обеспечивает достижение максимальных механических свойств материала профиля за счет их выделения при последующем упрочнении старением.
Необходимая скорость охлаждения твердого раствора легирующих элементов — магния и кремния в алюминии — для обеспечения эффекта закалки зависят от размеров поперечного сечения алюминиевого профиля и способов его охлаждения:
- спокойным воздухом,
- вентиляторами,
- водяным туманом,
- водяным спрейерным охлаждением или
- в потоке воды.
На рисунке и в таблице показаны минимально допустимые скорости охлаждения алюминиевых профилей для различных сплавов серии 6ххх. Для алюминиевых профилей из сплава 6060 (алюминиевого сплава АД31) обычно бывает достаточно охлаждения на спокойном воздухе или вентиляторами, тогда как для профилей из сплава 6061 необходимо спрейерное охлаждение водой или охлаждение в потоке воды.
Старение алюминиевых сплавов
Старение сплавов серии 6ххх производят для повышения механических свойств алюминиевых профилей. Степень этого повышения свойств зависит от типа сплава и условий старения. Эти условия различаются для:
- естественного старения, которое происходит «само собой» при комнатной температуре, и
- искусственного старения, которое проводят при повышенных температурах, около 160-200 ºС.
Прочность сплавов серии 6ххх прямо связана с их способностью сопротивляться движению дислокаций в ходе деформирования. При приложении к материалу напряжений в нем образуются и двигаются дислокации. С увеличением напряжений количество и плотность дислокаций, двигающихся в материале, возрастает до тех пор, пока, наконец, материал не разрушается.
Движение дислокаций тормозится из-за присутствия частиц Mg 2Si и поэтому прочность состаренного алюминиевого сплава возрастает. Размеры и плотность этих частиц контролируются параметрами старения. Небольшое количество мелких частиц β»-Mg2Si мало могут сделать, чтобы остановить дислокации, которые двигаются через материал, но когда их много они препятствуют движению дислокаций и это повышает прочность материала.
Если же частицы вырастают слишком большими (β’-Mg2Si и β-Mg2Si), их становится слишком мало из-за ограниченного содержания Mg и Si в алюминии. В этом случае дислокации легко обходят эти частицы и прочность материала снижается.
Это демонстрирует схематический график типичного искусственного старения на рисунке ниже.
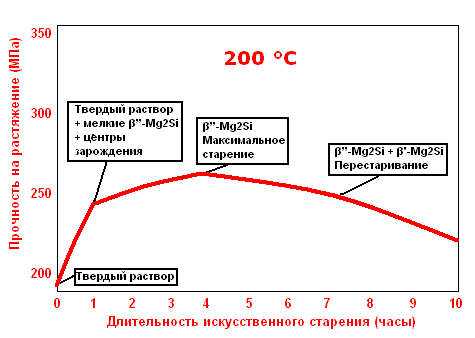
Пик прочностных свойств достигается при большом количестве мелких частиц β»-Mg2
Т-состояния алюминиевых сплавов
Различным вариантам параметров старения соответствуют различные обозначения состояния алюминиевых сплавов:
- Т1 – охлажденый после прессования до комнатной температуры и естественно состаренный;
- Т4 – после прессования закаленный с отдельного нагрева и естественно состаренный;
- Т5 – охлажденный после прессования до комнатной температуры и искусственно состаренный до максимума прочностных свойств;
- Т6 — после прессования закаленный с отдельного нагрева и искусственно состаренный до максимума прочностных свойств.
Для обозначения других обработок старением, которые специально разработаны для получения механических свойств, которые отличаются от максимальных прочностных свойств. Например, состояния Т52 и Т591 применяются для алюминиевых профилей, которые подвергаются гибке, а состояние Т7 – для профилей, которые применяются при повышенных температурах.
Растяжение и вылеживание профилей
Обычная практика изготовления прессованных алюминиевых профилей включает их растяжение от 0,5 % до 3 % и затем вылеживание с задержкой на сутки искусственного старения для профилей из малолегированных сплавов 6ххх (не более 0,9 % Mg2Si), например, алюминиевые сплавы АД31, 6060 и 6063. Это способствует достижению оптимальных механических свойств профилей после старения.
Однако такая задержка для более высокопрочных алюминиевых сплавов (содержание Mg2Si более 0,9 %), например, 6061, может привести к пониженным механическим свойствам материала алюминиевых профилей. Эти сплавы содержат медь в количестве не менее 0,1 %, которая противодействует влиянию задержки искусственного старения на конечные механические свойства термически упрочненных алюминиевых профилей.
Старение закаленных сплавов алюминия
После закалки алюминиевого сплава следует старение, когда сплав выдерживают при комнатной температуре несколько суток (естественное старение) или в течение 10 — 24 ч при повышенной температуре (искусственное старение).
В процессе старения происходит распад пересыщенного твердого раствора, что сопровождается упрочнением сплава. Распад пересыщенного твердого раствора, в решетке которого атомы меди располагаются статистически равномерно, происходит в несколько стадий в зависимости от температуры и продолжительности старения. При естественном (при 20°С) или низкотемпературном искусственном старении (ниже 100 — 150°С) не наблюдается распада твердого раствора с выделением избыточной фазы; при этих температурах атомы меди перемещаются только внутри кристаллической решетки α-твердого раствора на весьма малые расстояния и собираются по плоскостям {100} в пластинчатые образования или диски — зоны Гинье – Престона (ГП-1). Зоны ГП-1 в сплавах Al-Cu протяженностью 1—10 нм и толщиной 0,5—1 нм более или менее равномерно распределены в пределах каждого кристалла. Концентрация меди в зонах ГП-1 меньше, чем в CuAl 2 (54%).
Если сплав после естественного старения кратковременно (несколько секунд или минут) нагреть до 230 — 270 °С и затем быстро охладить, то упрочнение полностью снимается и свойства сплава будут соответствовать свежезакаленному состоянию. Это явление получило название возврата после старения. Разупрочнение при возврате связано с тем, что зоны ГП-1 при этих температурах оказываются нестабильными и поэтому растворяются в твердом растворе, а атомы меди вновь более или менее равномерно распределяются в пределах объема каждого кристалла твердого раствора, как и после закалки. При последующем вылеживании сплава при комнатной температуре вновь происходит образование зон ГП-1 и упрочнение сплава. Однако после возврата и последующего старения ухудшаются коррозионные свойства сплава, что затрудняет использование возврата для практических целей. Длительная выдержка при 100°С или несколько часов при 150°С приводит к образованию зон Гинье— Престона большей величины (толщина 1 — 4 нм и диаметр 20 — 30 нм) с упорядоченной структурой, отличной от α-твердого раствора. Концентрация меди в них соответствует содержанию ее в CuAl
Однако это не означает, что одно образование «на месте» переходит в другое. Возможно, что возникновение последующего образования или фазы происходит после растворения исходного.
Эта общая схема распада пересыщенного твердого раствора в сплавах Аl—Cu справедлива и для других сплавов. Различие сводится лишь к тому, что в разных сплавах неодинаков состав и строение зон, а также образующихся фаз.
Для стареющих алюминиевых сплавов разных составов существуют и свои температурно-временные области зонного (образование ГП-1 и ГП-2) и фазового (θ’ и θ-фаз) старения.
Величина упрочнения при закалке и старении зависит от природы фазы упрочнителя, размеров их частиц, количества их и распределения. Наибольшее упрочнение сплавов достигается благодаря MgZn2, Mg2Si и S-фазы (Al2CuMg), имеющих сложную структуру и состав, отличный от α-твердого раствора.
После зонного старения сплавы чаще имеют повышенный предел текучести и относительно невысокое отношение σ0,2/σв (≤0,6—0,7), повышенную пластичность, хорошую коррозионную стойкость и низкую чувствительность к хрупкому разрушению. Это объясняется тем, что дислокации при деформации пересекают зоны, не создающие значительного сопротивления начальным деформациям. Отсутствие границы раздела между зонами ГП-1 или ГП-2 с матричной фазой определяет хорошее сопротивление коррозии.
После фазового старения отношение σ0,2/σв повышается до 0,9— 0,95, а пластичность, вязкость, сопротивление хрупкому разрушению и коррозии под напряжением снижаются. В этом случае при деформации дислокации огибают частицы метастабильных фаз, образуя многочисленные дислокационные петли и отдельные скопления. Как следствие этого, сопротивление начальным деформациям повышается, а пластичность уменьшается. В процессе коагуляции образовавшихся фаз (коагуляционное старение) прочностные свойства на начальной стадии сначала возрастают, достигая максимального значения, а затем снижаются. Пластичность, вязкость и сопротивление коррозии возрастают.
Пресс-эффект
Температура рекристаллизации некоторых сплавов алюминия с марганцем, хромом, никелем, цирконием, титаном и другими переходными металлами, подвергнутых по определенным режимам горячей, а в некоторых случаях и холодной обработке давлением, превышает обычно назначаемую температуру нагрева под деформацию или закалку. Поэтому после закалки и старения таких сплавов в них сохраняется нерекристаллизованная (полигонизованная) структура с высокой плотностью дислокаций, что значительно повышает прочность по сравнению с рекристаллизованной структурой. Это явление получило название
В результате структурного упрочнения значения σ0,2 и σв повышаются до 30 — 40%. Наиболее сильно структурное упрочнение проявляется в прессованных полуфабрикатах (прутки, профили, трубы), поэтому это явление применительно к ним называют пресс-эффектом.
www.metmk.com.ua
Печи старения для алюминиевых профилей
Известно, что приблизительно 60-70 % прессованных алюминиевых профилей во всем мире производятся из сплавов серии 6ххх, в основном, из сплавов 6060, 6063, 6061 и 6005А. Эти алюминиевые сплавы являются термически упрочняемыми. Это означает, что они обладают способностью удерживать силицид магния в твердом растворе алюминия в результате быстрого охлаждения на прессе, а затем выделять его в контролируемых условиях повышенной температуры печи старения. Этот механизм имеет называние «упрочнение старением», а сама технологическая операция – искусственное старение. В ходе искусственного старения алюминиевые профили из сплавов серии 6ххх получают заданные прочностные характеристики – предел прочности, предел пластичности и относительное удлинение.
Естественное старение
Процесс выделения силицида магния из твердого раствора алюминия является весьма сложным. Он включает выделение и рост кластеров, которые препятствуют движению дислокаций, что и обеспечивает упрочнение материала. Сплавы серии 6ххх, которые после закалки оставляют вылеживаться при комнатной температуре, постепенно набирают прочность в течение времени от 100 до 500 часов. Этот процесс называется естественным старением. Для сплава 6060 с минимальным содержанием магния и кремния этот процесс может продолжаться несколько месяцев. Поэтому процесс естественного старения является в известной степени непрактичным из-за задержки поставки продукции. Вместе с тем, профили в состоянии Т4 обладают повышенной пластичностью. Поэтому это состояние применяется, например, для профилей, которые будут подвергаться гибке.
Искусственное старение
Процесс старения алюминиевых сплавов происходит значительно быстрее при повышенных температурах. При этом обычно достигается более высокий уровень прочности, чем при естественном старении.
Искусственное старения профилей из сплавов серии 6ххх включает нагрев до температуры около 180 ºС и выдержку при ней в течение нескольких часов, обычно, 4-5.
Такая обработка алюминиевых профилей обеспечивает ускоренную диффузию растворенных в алюминии атомов кремния и магния в направлении участков, в которых начинается выделение интерметаллических частиц Mg2Si. В то же время окружающая их кристаллическая решетка подвергается упругой деформации, так как эти выделения не вполне вписываются в нее. Все это создает препятствия для движения дислокаций, которые пытаются пройти через эти участки. В результате происходит увеличение предела текучести и предела прочности сплава.
Если алюминиевый сплав будет выдерживаться при повышенной температуре слишком долго, то происходит рост этих частиц, а некоторые из них исчезнут, а предел текучести сплава будет снижаться. В таком случае говорят, что алюминиевый сплав имеет перестаренное состояние (рисунок 1).
Рисунок 1 – Влияние длительности искусственного старения
на микроструктуру и прочность алюминиевого сплава [1]
На рисунке 2 представлена зависимость прочности профилей из сплава 6063 при искусственном старении при различной температуре от 170 до 245 ºС. Уровень прочности зависит как от температуры, так и от длительности выдержки при ней. Типичным процессом для старения профилей из сплава 6063 является выдержка в печи старения при температуре 185 ºС в течение 4-5 часов.
Рисунок 2 – Влияние температуры и времени нагрева
на уровень прочности профилей из сплава 6063 [1]
Как видно из рисунков 1 и 2 процесс искусственного старения требует обработки профилей при точной температуре в течение заданного времени для каждого конкретного алюминиевого сплава. Если температура профилей в печи старения будет значительно отличаться – по длине, ширине и высоте печи, то и прочностные свойства профилей в садке будут различными. Обычно допустимое отклонение температуры профилей по садке в печи составляет ± 3 ºС.
Состав печей старения
Печи старения могут иметь различные конструкции в соответствии с требованиями конкретного производства.
Большинство печей имеют следующие основные конструкционные элементы:
- Рабочая камера
- Система циркуляции воздуха
- Один или два вентилятора циркуляции воздуха.
- Камера сгорания газа и нагрева воздуха.
- Газовая горелка и ее система управления.
Прямой или косвенный нагрев
Большинство печей старения имеют прямой нагрев. Это означает, что продукты сгорания газа смешиваются с циркулирующим воздухом.
При непрямом — косвенном — нагреве газ горит в специальной радиантной трубе и выходит в дымовую трубу наружу. Циркулирующий воздух проходит вдоль наружной поверхности радиантной трубы и нагревается за счет излучения и конвекции. Непрямой нагрев исключает контакт поверхности профилей с продуктами сгорания, но требует повышенного расхода газа.
Продольный или поперечный поток воздуха
В большинстве конструкций печей старения горячий воздух продувается вдоль длины садки профилей (рисунок 3). Вместе с тем, существуют варианты конструкции печей с поперечным продувом воздуха (рисунок 4).
Рисунок 3 – Печь старения с продольным потоком воздуха [2]
Рисунок 4 – Печь старения с поперечным потоком воздуха [2]
Теоретически печи с поперечным продувом воздуха могут обеспечивать лучшую однородность температуры по садке профилей, но имеют более низкую тепловую эффективность [2].
Однородность температуры по садке профилей очень сильно зависит от вида садки и плотности укладки профилей. Передача тепла от горячего воздуха к профилями происходит в основном за счет конвекции. Поэтому важен максимальный контакт между поверхностью профилей и циркулирующим горячим воздухом.
Длина печи: эффективность и однородность
Тепловая эффективность печи старения возрастает с увеличением ее длины. Однако, к сожалению, с увеличением длины печи ухудшается однородность температуры садки. Поэтому оптимальная длина печи является компромиссом между этими двумя факторами. Обычно печи вмещают по длине от 1 или 2 корзины, бывают печи длиной в четыре корзины. Длина каждой корзины около 7 метров. Для длинных печей предусматривают несколько зон нагрева и циркуляции воздуха.
Современная печь старения
Примером современной печи старения может служить печь старения двойной длины компании Tecalex [3] (рисунок 5).
Рисунок 5 – Печь старения компании Tecalex [3]
Циркулируемый воздух нагревается по принципу прямого нагрева. Это обеспечивает печи максимальную термическую эффективность. Газовая горелка установлена в камере сгорания, которая отделена от рабочей камеры. Хорошо продуманная конструкция и высокое качество теплоизоляционных материалов обеспечивают этой печи очень низкой потребление энергии. Принцип работы печи основан на циркуляции горячего воздуха в продольном направлении.
Корзины с профилями перемещаются с помощью приводных роликов в полу цеха и печи. Температура в рабочей камере печи контролируется шестью термопарами, которые установлены в различных зонах.
На печи установлены две центробежные турбины, которые обеспечивают хорошую отдачу тепла от потока горячего воздуха по всему сечению садки профилей. Это дает хорошую однородность температуры по садке и, следовательно, одинаковую прочность (твердость) для всех профилей садки.
Двери печи снабжены серией дефлекторов, которые помогают равномерно распределять горячий воздух по сечению садки и эффективно возвращать его для нагрева.
Правильная загрузка печи старения
Если горячий воздух в печи старения находит какие-то пути в обход садки профилей, то теплоотдача от воздуха снижается, цикл нагрева становится длиннее, расход газа возрастает, а однородность температуры по садке ухудшается. Поэтому главной целью загрузки печи старения является обеспечить максимально прохождение воздушного потока через садку профилей. Пример нормальной плотной садки в печи старения показан на рисунке 6.
Рисунок 6 – Нормальная плотная загрузка профилей в печь старения [3]
При неполной загрузке печи – неполном количестве корзин или неполных корзинах – в сечении печи образуются свободные проходы для горячего воздуха. В этом случае горячий воздух почти не попадает между профилями и эффективность их нагрева значительно снижается (рисунок 7). Для эффективной обработки неполных садок обычно предусматривают систему специальных дефлекторов, которые направляют воздух по неполной садке.
Рисунок 7 – Циркуляция горячего воздуха при неполной загрузке печи старения [1]
Кроме того, при загрузке печи старения самые массивные профили садки нужно располагать так, чтобы им «доставался» самый горячий воздух. Массивные профили могут потребовать более длительного разогрева, поэтому такой способ загрузки способствует выравниванию температуры профилей в рабочей камере печи.
Источники:
- R.W. Hains Precipation Aging – Aluminum Extrusion technology Seminar, Chicago, 1977
- Al Kennedy Age Ovens //The Extrusion Press Maintenance Manual, 2004
- http://www.tecalex.com/en/furnaces.html
aluminium-guide.ru
Старение алюминиевых сплавов | Всё о красках
Алюминиевые сплавы набирают твердость, когда устанавливается контролируемое выпадение осадка элементов сплава (вследствие распада перенасыщения раствора, необходимого для эффективного затвердевания), и то, чтобы сформировавшийся осадок был связный (сцепленный) или частично связанный с решеткой микроструктуры основного металла.
Кинетика выпадения осадка перенасыщенного твердого раствора – это функция, т.е. химический состав. Например, для сплава 2024 старение достигается естественным путем, в то время как для сплава 7075 кинетика выпадения осадка в твердом растворе происходит только при +100 – 200°С.Сплавы, подвергающиеся естественному старению, могут быть состарены искусственно.
Но наилучшее сопротивление межгранулярной коррозии достигается искусственным путем. При естественном старении преимущество отдается характеристикам стойкости и большему сопротивлению распространению усталостных трещин.
При различных параметрах старения можно достичь одних и тех же результатов. Например, сплав 6060, достигаются одинаковые условия для 5 часов при 185 °С и для 11 часов при 170°С.
В недостаточно состаренных деталях может наблюдаться уменьшение уровня механических свойств при последующей обработке.
Перестаривание может произойти из-за пластической деформацией, выполненной после закалки до старения (посредством вальцовки, формовки, прокатки, вальцовки и др.)
Данные операции ускоряют кинетику выпадения осадка, пропорциональную степени деформации, в случаях однородной обработки (такой как растяжка, сжатие, накатывание, вальцовка).
Вообще комбинации таковые, чтобы привести сплав до максимальной твердости Т6.Т7 – большее старение, скорее перестаривание, с частичным уменьшением механических характеристик. При подобной обработке возможно увеличение стабильности по размерам изделия, которое позволяет применять изделие для работы при высоких температурах. Также можно развить большую сопротивляемость поверхностной коррозии или эксфолиативной коррозии (отшелушивание).
Изделия, которые будут работать при высоких температурах, например, части мотора могут достигать хорошей стабильности размеров только при искусственном старении, при обработке T5 очень редко в этих случаях используется материал, состаренный при естественном старении. (T1).
Сплавы с небольшим количеством легирующих веществ, такие как 6060 должны стариться до достижения максимальной твердости T6.
Для изделий, требующих большую точность (размеров) используются различные циклы обработки. В течение 1-2 часов при 175-200С после предварительной обработки (шлифование), после машинной обработки и при посреднических фазах.
На первой стадии изотермических циклов старения. Например, 6 часов при температуре 100°С, до 3часов при температуре 120°С. На второй стадии температура и время должно контролироваться, т.к. может вызвать изменения в физических свойствах детали. Температура в печи должна быть однородной.
Нежелательные эффекты перестаривания деталей могут быть вызваны продолжительным процессом, вызванным низкой скоростью разогрева, вызванной перегрузкой печи.
Время между закалкой (охлаждением) и старением не влияет на старение профиля. Но, необходимо помнить, что в некоторых сплавах серии 6060 механические свойства будут несколько более высокими, если старение выполнено немедленно после закалки. В то время как другие сплавы требуют выдержки при температуре окружающей среды перед старением для лучших механических свойств.
Максимальный интервал, предусмотренный между растворением веществ и закалкой (задержка закалки).
Номинальная толщина (мм) | Максимальное время (секунды) |
До 0,4 | 5 |
От 0,4 – до 0,8 | 7 |
От 0,8 – до 2,3 | 10 |
Свыше 2,3 | 15 |
ааа
Средство для закалки | Температура(°C) | Относительная скорость средства закалки и – изделия (м/с) | Коэффициент термического соответствия (В/см2 K) |
Вода | 27 | 0,00 | 3,55 |
0,25 | 4,78 | ||
Вода | 38 | 0,50 0,00
| 5,14 3,28
|
0,25 | 4,01 | ||
0,50 | 4,91 | ||
Вода | 49 | 0,50 0,00
| 5,14 3,65
|
0,25 | 4,29 | ||
0,50 | 5,61 | ||
0,50 | 5,14 | ||
Вода | 60 | 0,00 | 2,85 |
0,25 | 3,62 | ||
0,50 | 4,41 | ||
0,50 | 5,14 | ||
Вода | 71 | 0,00 | 0,70 |
0,25 | 1,89 | ||
0,50 | 2,62 | ||
0,50 | 5,14 | ||
Вода | 82 | 0,00 | 0,36 |
0,25 | 0,69 | ||
0,50 | 0,89 | ||
0,50 | 5,14 | ||
Вода | 93 | 0,00 | 0,20 |
0,25 | 0,27 | ||
0,50 | 0,30 | ||
0,50 | 5,14 | ||
Вода | 100 | 0,00 | 0,13 |
0,25 | 0,13 | ||
0,50 | 0,13 | ||
UCONA | 30 | 0,00 | 0,63 |
0,25 | 0,70 | ||
0,50 | 0,77 | ||
PVP90 | 30 | 0,00 | 1,49 |
0,25 | 1,34 | ||
0,50 | 1,41 |
vseokraskah.net
Термическая обработка алюминиевых отливок
Термическая алюминиевых литых деталей дает возможность улучшения их механических свойств или даже коррозионной стойкости.
Виды термической обработки отливок
В зависимости от метода литья и применяемого сплава к алюминиевой отливке могут применяться следующие виды термической обработки:
- отжиг для снятия остаточных напряжений;
- стабилизирующий отпуск;
- гомогенизация;
- полный отжиг;
- упрочнение старением.
Наиболее важным видом термической обработки для алюминиевых отливок является старение, обычно — искусственное старение.
Принципы упрочнения алюминиевых сплавов старением
Необходимым условием для того, чтобы в алюминиевом сплаве происходило упрочнение старением, является уменьшение растворимости в твердом растворе алюминия одного или нескольких компонентов сплава с понижением температуры.
Как правило, процесс искусственного старения включает три стадии:
- При нагреве на твердый раствор (нагреве под закалку) происходит растворение в твердом растворе алюминия достаточного количества компонентов сплава, которые обеспечивают упрочнение старением.
- При достаточно быстром охлаждении при закалке эти компоненты остаются в твердом растворе. В этом состоянии отливки остаются относительно мягкими.
- При старении – для литых изделий, в основном, искусственном – происходит выделение этих растворенных компонентов в форме мельчайших субмикроскопических фаз, которые дают повышение твердости и прочности алюминиевого сплава. Эти мельчайшие фазы, которые по-научному называют «когерентными или полукогерентными фазами», представляют собой препятствия для движения дислокаций в металле и поэтому упрочняют до этого мягкий металл.
Термически упрочняемые литейные алюминиевые сплавы
Термической обработке старением поддаются следующие типы алюминиевых литейных сплавов:
- алюминий-медь;
- алюминий-медь-магний;
- алюминий-кремний- магний;
- алюминий-магний-кремний;
- алюминий-цинк-магний.
Нагрев на твердый раствор (нагрев под закалку)
Для того, чтобы ввести упрочняющие компоненты сплава в твердый раствор так быстро, как это только возможно, температура нагрева на твердый раствор должна быть максимально высокой, не ближе чем 15 °С к температуре ликвидус, чтобы избежать локального подплавления. По этой причине часто литейные алюминиевые сплавы, содержащие медь, подвергают нагреву на твердый раствор в два этапа: сначала до 480 °С, потом до 520 °С.
Длительность нагрева под закалку зависит от толщины стенки отливки и метода литья. По сравнению с литьем в песчаные формы, литье в кокиль требует более короткий нагрев под закалку для растворения упрочняющих компонентов сплава благодаря более измельченной микроструктуре. В принципе, нагрева около одного часа обычно достаточно. Более длительный нагрев под закалку – до 12 часов – применяют, например, для сплавов алюминий-кремний-магний для сфероидизации или округления эвтектического кремния, чтобы повысить пластические свойства сплава (относительное удлинение).
В ходе нагрева под закалку прочность отливок остается еще очень низкой. Поэтому необходимо принимать меры по предотвращению их прогиба и коробления. Для этого большие и сложные отливки закрепляют в специальных приспособлениях.
Закалка алюминиевых отливок
Горячую отливку необходимо охладить в воде как можно быстрее – за 5-20 секунд в зависимости от толщины ее стенок, чтобы подавить любое нежелательное и преждевременное выделение растворенных компонентов сплава.
После закалки отливки имеют высокую пластичность. Резкое охлаждение отливки при закалке может приводить к образованию больших внутренних напряжений и короблению изделия. Эту проблему решают выбором закалочной среды и способа ее подачи: погружение в воду или подача воды через спрейеры — вода холодная, вода горячая или масло.
В любом случае, любые действия по правке изделия должны производиться после закалки, но до старения.
Операция старения
Операция старения приводит к значительному увеличению твердости и прочности литейной структуры за счет выделения мельчайших упрочняющих фаз. Только после этой операции изделие получает свои заданные свойства, свою окончательную форму и размеры.
Обычные сплавы подвергают искусственному старению. Искусственное старение – это старение при повышенных температурах, в отличие от естественного старения, которое проводят при температуре окружающей среды («комнатной» температуре).
Температура старения и ее длительность могут быть различными в зависимости от требуемых свойств алюминиевого сплава в отливке. Например, механические свойства можно «отрегулировать» так, чтобы получить высокую твердость и прочность, но за счет более низкой пластичности (относительного удлинения) материала отливки. И наоборот, можно достичь более высокой пластичности (относительного удлинения), но в ущерб твердости и прочности. При выборе температуры старения и длительности его выдержки применяют диаграммы старения конкретного сплава, которые разработаны для многих сплавов (рисунки 1-4).
Рисунок 1 – Зависимость предела текучести литейного алюминиевого сплава
Al Si10Mg от температуры его искусственного старения
Рисунок 2 — Зависимость относительного удлинения литейного алюминиевого сплава Al Si10Mg от температуры его искусственного старения
Рисунок 3 — Зависимость предела прочности литейного алюминиевого сплава
Al Si10Mg от температуры его искусственного старения
Рисунок 4 — Зависимость твердости литейного алюминиевого сплава Al Si10Mg
от температуры его искусственного старения
В сплавах алюминий-кремний-магний имеется дополнительная возможность влиять на уровень предела прочности и относительного удлинения материала отливки путем изменения содержания магния в комбинации с варьированием параметров термической обработки (рисунок 5).
Рисунок 5 – Влияние содержания магния в сплаве Al Si7 на предел прочности в литом и состаренном состояниях
Типичные параметры искусственного старения для различных типов литейных алюминиевых сплавов представлены на рисунке 6.
Рисунок 6 – Параметры искусственного старения литейных алюминиевых сплавов
Источник: Aleris International, 2014
aluminium-guide.ru
Остаточные напряжения и коробление алюминиевых деталей
Коробление – это то, что нередко случается при механической обработке деталей из термически упрочняемых алюминиевых сплавов. Причина коробления этих деталей – остаточные напряжения, которые образовались при их закалке в процессе термического упрочнения.
Кстати, знаменитые алюминиевые цельные корпусы аппаратов iPhone 5 и iPhone 6 компании Apple изготавливаются именно так. Цельную алюминиевую прессованную заготовку подвергают многочисленным фрезерным операциям на хитроумном станке с компьютерным управлением.
(См. подробнее: Алюминиевые сплавы в смартфонах и ноутбуках).
Закалка алюминиевых сплавов
Операция закалки алюминиевых сплавов состоит из двух этапов. Первый этап – это нагрев до температуры закалки: от 450 ºС для сплавов серии 7ххх до 520 ºС для сплавов серии 6ххх. После некоторой выдержки при температуре закалки следует быстрое охлаждение – для различных сплавов разное.
Необходимая для полной закалки скорость охлаждения значительно различается для различных алюминиевых сплавов, например:
- погружение в холодную или теплую воды для высокопрочного сплава 7075 (отечественный аналог – В95),
- охлаждение струями воды для сплава 6061 (АД33),
- охлаждение вентиляторами или сжатым воздухом для сплава 6060 (АД31).
Цель закалки – удержать в твердом растворе алюминия растворенные легирующие элементы – для разных сплавов разные. Вслед за закалкой следует стадия старения – естественного или искусственного (при повышенной температуре). В ходе старения за счет выделения из твердого раствора упрочняющих компонентов, содержащих легирующие элементы, происходит повышение прочности алюминиевого сплава.
Коробление – бич механической обработки алюминия
Это неприятное явление – коробление – особенно «неприятно» тем, что делает трудным или невозможным выдерживать жесткие размерные допуски алюминиевых изделий, которые получают механической обработкой, например, фрезерованием. Особенно это касается больших и/или сложных по форме изделий. Поэтому высокий уровень отбраковки фрезерованных алюминиевых деталей из термически упрочняемых сплавов из-за отклонений от заданных размеров по причине коробления является обычным делом.
На рисунке ниже показано коробление, которое возникло в листе из сплава 7075 в состоянии Т6 (закалка и искусственное старение) толщиной 25 мм и длиной 250 мм после разрезания на электро-эррозионном станке по центральной плоскости на две половинки. Максимальная величина образовавшейся щели достигла 4,3 мм.
Рисунок 1 – Коробление листа из сплава 7075-Т6
после разрезания вдоль центральной плоскости
Остаточные напряжения в алюминии – какие они?
Уровень остаточных напряжений в закаленном алюминиевом изделии, например в том же толстом листе, возрастает с увеличением его толщины, пока, наконец, не достигает предела текучести алюминиевого сплава в закаленном состоянии.
Знаменитый – аэрокосмический — сплав 7075 имеет значительно более высокий предел текучести в закаленном состоянии по сравнению с другими сплавами, в том числе, с таким популярным в промышленности, как сплав 6061. Поэтому сплав 7075 является наиболее склонным к образованию остаточных напряжений и, следовательно, короблению при механической обработке. Остаточные напряжения в закаленных листах из сплава 7075 толщиной более 33 мм могут достигать 230 МПа. В закаленных листах из сплава 6061 толщиной свыше 15 мм остаточные напряжения могут достигать «всего лишь» 90 МПа.
Почему возникают остаточные напряжения?
Остаточные напряжения возникают из-за неоднородного охлаждения изделия при закалке и связанного с этим неоднородного сокращения его размеров. Когда относительно толстые изделия погружают в закалочную водяную ванну, то поверхностные слои изделия охлаждаются первыми и поэтому сокращаются в размерах намного быстрее, чем его сердцевина. В то же время в начале охлаждения горячая сердцевина оказывает мало сопротивления сокращению размеров поверхностных слоев – мягкая сердцевина пластически деформируется под воздействием сжатия наружных слоев. Позднее в ходе закалки, однако, сердцевина тоже охлаждается и тоже «хочет» сократить свои размеры. Однако этому сокращению препятствуют уже холодные и относительно прочные наружные слои изделия.
Таким образом, внутри изделия образуются растягивающие остаточные напряжения потому что, материал здесь хочет сократить свои размеры, но не может этого сделать из-за сопротивления наружных слоев. Эти растягивающие напряжения во внутренних слоях изделия уравновешиваются сжимающими напряжениями вблизи его поверхности.
Остаточные напряжения в алюминиевых листах
На рисунке 2 показано распределение уравновешенных остаточных напряжений по толщине закаленного листа. Максимум сжимающих (отрицательных) напряжений достигается на обеих наружных поверхностях листа, а максимальные растягивающие остаточные напряжения возникают внутри листа — по центральной плоскости. Такое распределение остаточных напряжений характерно для простого случая полубесконечного листа (плиты). Для деталей менее правильной формы распределение остаточных напряжений будет намного более сложным.
Рисунок 2 — Пример уравновешенных остаточных напряжений
в алюминиевом толстом листе
Величины пиковых сжимающих и растягивающих остаточных напряжений в закаленном алюминиевом листе зависит от интенсивности закалки, толщины листа и уровня предела текучести сплава в закаленном состоянии. Обычно остаточные напряжения являются весьма не высокими в относительно тонких листах, но увеличиваются с ростом толщины и достигают предела текучести в закаленном состоянии алюминиевого сплава, из которого они сделаны, в очень толстых листах. Это происходит потому, что с увеличением толщины возрастает различие между температурой на поверхности листа и температурой в его сердцевине. Это приводит к более высоким остаточным напряжениям.
Если в ходе последующей механической обработки закаленного и состаренного листа материал удаляется асимметрично по отношению к распределению остаточных напряжений, то возникает коробление листа в виде его самопроизвольного прогиба.
Как избежать коробления?
Для снижения уровня остаточных напряжений в алюминиевых изделиях и предотвращения коробления деталей при их механической обработке могут в различной степени применяться четыре подхода.
- Закалка не в обычной, в подогретой воде. Снижает уровень остаточных напряжений, которые образуются при закалке. Однако эта технология может препятствовать достижению полной закалки алюминиевого сплава и снижению уровня прочности после последующего искусственного старения.
- Механическое снижение остаточных напряжений, например, путем растяжения, в закаленном состоянии, перед старением. Снижает уровень остаточных напряжений без ущерба для прочностных свойств. Однако трудно реализовать для изделий сложной формы.
- Термическое снижение остаточных напряжений (в ходе обычного искусственного старения или менее обычного перестаривания). При искусственном старении (Т6) происходит относительно незначительное снижение остаточных напряжений. При старении в режиме перестаривания (например, Т73) достигается более значительное снижение остаточных напряжений, но за счет нежелательного снижения прочностных свойств.
- Холодная пластическая деформация (после старения). Эта операция не снижает величину остаточных напряжений, но может изменить их распределение. Однако холодная обработка может привести к дополнительному короблению при последующей механической обработке.
Источник: http://prod.sandia.gov
aluminium-guide.ru