Испытания по бринеллю: Твердомеры для металлов. Методы Бринелля и Роквелла
alexxlab | 23.03.2023 | 0 | Разное
Определение твердости по Бринеллю (НВ) ᐉ Заказать испытания металла | Лучшая Цена
Независимая аналитическая экспресс-лаборатория анализа металлов SendLab, является ведущим представителем на Украинском рынке в сфере лабораторно-технических и химических экспертиз металлов.
Мы предлагаем проведения измерения твердости по Бринеллю, которые проводиться на современном европейском оборудовании, высококвалифицированными специалистами в кратчайшие сроки.
Метод определения твердости по БринеллюЭто один из видов металловедческих экспертиз, который также проводиться нашей лабораторией.
Метод определения твердости по Бринеллю принадлежит к методу вдавливания. Для его проведения требуется образец из стали либо бетонный фрагмент и индентор, в большинстве случаев это стальной шар который вдавливается в образец.
Принцип определения твердости заключается в том, что после процедуры вдавливания, диаметр получившегося отпечатка подвергают измерению и классификации полученных данных. Процедура измерение твердости по Бринеллю, регламентируется согласно ГОСТ 9012 59.
Согласно Бринелю, твердость записывается как, «HBW» ,и рассчитывается такими испытаниями:
- Метода восстановленного отпечатка;
- Метода невосстановленного отпечатка.
О результатах испытаний твердости по методу Бринелля составляется соответствующее лабораторное заключение (протокол) с указанием условий и результатов проведенного теста. Протокол испытания дает оценку соответствия и качества предоставленного материала. Результаты проведенных исследований по определения твердости по Бринеллю, можно получить любым удобным способом:
- по телефону;
- электронная почта;
- вайбер.
Выдаче результатов осуществляется в течении 1-3 рабочих дней, с момента предоставления образца и полной предоплаты. Наше преимущество в том, что оплата осуществляется любым удобным для клиента способом:
- Безналичной формой оплаты;
- Наличной формой оплаты;
- Переводом на банковскую карту.
Независимая аналитические экспресс-лаборатории анализа металлов SendLab расположена в городе Днепр (Днепропетровск). Определение твердости металла по Бринеллю доступно как для юридических, так и для физических лиц, по всей территории Украины, в том числе:
- Харьков,
- Кривой Рог,
- Львов,
- Одесса,
- Запорожье,
- Киев.
Вы можете прислать нам образец для определения твердости металла методом Бринелля любой удобной службой доставки. Выдаче результатов осуществляется в течении 1-3 рабочих дней, с момента предоставления образца и полной предоплаты. Оплата осуществляется любым удобным для клиента способом:
- Безналичной формой оплаты;
- Наличной формой оплаты;
- Переводом на банковскую карту.
Стоимость наших услуг на рынке определяет адекватность и конкурентоспособность, в чем постоянно убеждаются наши клиенты. Результаты проведенных исследований можно получить любым удобным способом: электронная почта, вайбер. Так же, по запросу, мы можем оформить официальный протокол проведенных исследований.
Лаборатории анализа металлов SendLab https://www.sendlab.com.ua/ всегда готовы прийти на помощь своим клиентам, и в рядовых случаях и если стоит задача, требующая нестандартного и комплексного подхода для ее решения.
Если у вас остались вопросы, напишите нам.
Мы свяжемся с вами в течение одного рабочего дня.
Метод Бринелля – Словарь терминов | ПластЭксперт
Метод Бринелля
Твердость материалов и методы ее измерения
Твердостью называют способность тела к пластическим деформациям под действием еще более твердого инструмента, называемого индентором.
Существует несколько популярных способов испытаний материалов и прежде всего металлов на твёрдость. При помощи них можно получить как некое численный эквивалент прочности изделия, так и данные по его сопротивлению знакопеременным нагрузкам.
К основным методикам определения относятся:
-
1. Метод Бринелля (приборы и сам процесс подробно будут описаны ниже). При его использовании твёрдость определяется при помощи отпечатка от твердого, чаще всего металлического шарика, вдавливаемого в ровную площадку детали. По диаметрам следов и судят о твердостях.
Рис.1 Внешний вид современного твердомера.
-
2. Способ Роквелла. По нему значение твёрдости равно относительной глубине вдавливания подобного, используемому по Бринеллю, шарика или алмазного конуса в площадку на поверхности изучаемой детали и обозначается чаще всего символами HR. Т.к. величина относительная, то максимальная величина твёрдости по Роквеллу составляет HR=100. «Роквелл» имеет широкое распространение при оценке качества рабочих узлов оборудования для переработки пластмасс и эластомеров, а также технологической оснастки.
-
3. Способ Виккерса. Подобен способу определения по Бринеллю, но при его применении используют четырёхгранную алмазную пирамиду и, соответственно, след, оставляемый ею. Численное значение твёрдости (обозначается как HV) в этом случае равно отношению нагрузки, приложенной к пирамиде, к площади следа от нее.
-
4. Твёрдость по Шору (метод вдавливания, обозначается Шор А, Шор D). Является важнейшим для определения твердости пластмасс, эластомеров и композитов. По нему величина твёрдости материала равно глубине проникновения в него специально подготовленной стальной иглы, которую приводит в напряжение калиброванная пружина. Прибором, работающим по методике Шора является дюрометр. Регулируемая международным стандартом ASTM D2240, процесс включает применение 12 шкал, однако на практике подавляющее количество более мягких материалов (например резин и эластомеров испытывают по шкале A), а более жестких (пластмасс и композитов) по шкале D.
-
5. Дюрометры и шкалы Аскер является еще одним способом, относящемуся к разработкам Шора, похожим по способу измерения на предыдущий. Он применяется для получения значения для мягких веществ, используется главным образом в Японии и имеет несущественные отличия от «Шора», например особенностями оборудования, шкал и инденторов.
-
6. Твёрдость по Шору (метод отскока). Применяется для получения значений твёрдости для очень твёрдых деталей, например металлических. Величина показателя (имеет обозначение HSx) находится по высоте отскока специального бойка, который падает со стандартной высоты.
-
Кроме описанных основных способов существует еще набор более редких техник, например метод Кузнецова-Герберта-Ребиндера, методика Польди или двойного отпечатка шарика, определений по шкале Мооса, способ Бухгольца и т.п. В данной статье мы не будем рассматривать их подробнее и просим обращаться к специализированной литературе.
Методика измерения твердости по Бринеллю
В соответствии с рассматриваемой технологией значение твёрдости материала определяется как отношение усилия, применимого на шарик, к площади следа от него после удара о изучаемый образец. Важно, что указанная площадь рассчитывается как площадь сферической поверхности отпечатка, а не как площадь круга.
В соответствии с ГОСТ 9012-59 значение показателя пишется в числах без указания единиц измерения, хотя фактически единицей является кг-с/кв.мм. Твёрдость по Бринеллю обозначается как HB и применяется в основном для достаточно мягких металлических сплавов, цветных металлов, чугуна и незакалённой «сырой» стали.
Для измерения твердости по методу Бринелля, как правило, используют шарик или из стали или из карбида вольфрама. Карбидный индентор предназначен для исследования особо твердых материалов, например инструментальных сталей и сплавов. Стальной индентор подходит к металлам с твердостью до стали общего назначения, а также нержавеющей стали, дерева, цветных металлов, стекла и т. д.
В приборах по определению твердости по Бринеллю, использующихся в настоящее время, существует возможность плавно вводить шарик в деталь, что дает очень низкую погрешность измерения, не превышающую 1 процента. Это позволяет получать ее с высокой степени не только точности, но и повторяемостью.
Шарики-инденторы, которые примеряются в составе устройств, имеют диаметр 1, 2,5, 5 и 10 миллиметров. Усилие внедрения шарика и его размер выбирается исходя из типа изучаемого материала.
Испытания по методу Бринелля имеют следующие ограничения и особенности, которые нужно учитывать при его выборе и применении:
-
Неприменимы образцы, имеющие значение по Бринеллю более HB450/650 кгс/кв.мм.
-
Поверхность исследуемой детали должна быть плоская и чистая со всех сторон. Любая деформация может привести к искажению результата.
-
Диаметр каждого следа должен быть в интервале от 0,2 до 0,6 диаметра индентора.
-
Критический размер для образца материала, взятого для оценки твердости по Бринеллю – толщина не менее 10 глубин отпечатка индентора.
-
Расстояние от центра отпечатка до центра ближайшего следа должно быть 4 диаметра отпечатка или более.
-
Время выдержки под нагрузкой – 10-15 секунд для стали и 10-180 с для цветных металлов и сплавов исходя из их твёрдости.
Важно отметить, что не допускается измерять одинаковые детали и сравнивать результаты, полученные на твердомерах разного типа. Также нельзя получить точную твердость по методу Бринелля в месте, находящемся вблизи кромки образца.
При использовании данных после измерения твердости по методу Бринелля нужно обозначать условия получения данных.
В случае, если твёрдость образца выше HB450, то метод Бринелля не подходит, ввиду возможной деформации поверхности шарика при таких свойствах исследуемого вещества.
В ходе испытаний размер следа от индентора измеряют, используя специальную лупу с шагом шкалы 0,05 мм, которая названа также именем Бринелля, по двум перпендикулярным осям. Также возможно использование микроскопа для получения более точных данных. За значение диаметра принимают среднее арифметическое из этих измерений.
Важность для переработки пластмасс
Твердость по Бринеллю, несмотря на то что более распространенным является способ по Роквеллу, имеет широкий спектр применений в области получения изделий из пластмасс и эластомеров. Главным образом численные величины твердостей используется для оценки качества изготовления полимерного оборудования и технологической оснастки.
В области полимерного машиностроения нельзя пренебрегать твердостью исполнения узлов и агрегатов. Несмотря на кажущуюся мягкость и податливость расплавленного полимера, он может достаточно легко повредить и вывести из строя оборудование, не обладающее достаточным качеством металла, из которого оно изготовлено.
Рис.2. Проверка качества деталей оснастки
В частности, при приемке форм для литья пластмасс под давлением у недорогих изготовителей из Китая, крайне распространенной практикой является оценка твердостей формообразующих деталей. Этот процесс проводится при помощи ручного твердомера непосредственно на поверхности оснастки, чуть в стороне от формующей области. Наиболее требовательные заказчики возят свои собственные устройства на приемку пресс-форм.
Что касается непосредственно полимеров и эластомеров, то, как было указано ранее, наиболее распространенной методикой в мире (за исключением Японии и некоторых других стран) являются твердомеры, работающие по Шору и шкалам А и Д. Способ Бринелля может подойти только для особенно сильно наполненных полимеров, но он слишком неточен для стандартных крупнотоннажных пластмасс.
Введение, процедура, формула, стандарты (PDF) – Что такое трубопровод
Твердость материала – это его способность сопротивляться локализованной остаточной деформации, проникновению, царапанью или вдавливанию. Таким образом, это важный параметр в технике. Измерение твердости позволяет количественно определить твердость материала и является ключевым элементом многих процедур контроля качества и научно-исследовательских работ. Существует несколько методов определения твердости. Однако тесты на твердость по Бринеллю, Роквеллу, Виккерсу, Кнупу, Моосу, склероскопу и файлам являются наиболее широко используемыми тестами на твердость. В этой статье мы узнаем о тесте на твердость по Бринеллю, его процедуре, соответствующей формуле и стандартах.
Что такое испытание на твердость по Бринеллю?
Метод измерения твердости по Бринеллю является наиболее часто используемым методом измерения твердости в промышленности. При измерении твердости по Бринеллю твердость металла определяется путем измерения размера постоянного отпечатка, создаваемого индентором. Более твердые материалы будут давать неглубокие вмятины, а более мягкие – более глубокие. Этот метод испытаний был впервые предложен шведским инженером Йоханом Августом Бринеллем в 1900 году, и, судя по его имени, этот тест известен как тест на твердость по Бринеллю.
Процедура измерения твердости по Бринеллю
Испытание на твердость по Бринеллю проводится в установке для определения твердости по Бринеллю. В этом методе испытания заданную силу (F) прикладывают к шарику из карбида вольфрама фиксированного диаметра (D) и удерживают в течение заданного периода времени, а затем удаляют. Сферический индентор создает отпечаток (постоянную деформацию) на испытуемом металлическом образце. Этот отступ измеряется по двум или более диаметрам, а затем усредняется, чтобы получить диаметр отпечатка (d). Используя этот размер отпечатка (d), число твердости по Бринеллю (BHN) находится с помощью таблицы или рассчитывается по формуле определения твердости по Бринеллю. Оборудование, используемое для определения твердости по Бринеллю:
- Прибор для определения твердости по Бринеллю
- Сфера индентора и
- Микроскоп Бринелля для измерения полученного оттиска.
Прибор для определения твердости по Бринеллю:
Прибор для определения твердости по Бринеллю (рис. 1) состоит из системы загрузки, включающей в себя рычаги, грузы, гидравлический демпфер и плунжер, заключенный в корпусе прибора. Исследуемый материал удерживается на регулируемой наковальне. С помощью рычага сферический шариковый индентор опускается на материал с заранее определенной силой, которую можно увидеть на экране.
Для более мягких металлов применяется меньшее усилие, чем для более твердых металлов. Величина силы варьируется от 1 кгс до 3000 кгс. Общие испытательные усилия варьируются от 500 кгс, часто используемых для цветных металлов, до 3000 кгс для сталей и чугунов.
Для определения твердости по Бринеллю используются инденторы четырех размеров. Они бывают размером 1 мм, 2,5 мм, 5 мм и 10 мм.
Для получения одного и того же BHN с шарами разного диаметра должны быть выполнены геометрически одинаковые углубления. Можно, если Ф/Д 2 поддерживается постоянным.
Формула определения твердости по Бринеллю
После измерения среднего диаметра отпечатка можно рассчитать число твердости по Бринеллю (BHN или HBW) с использованием следующей формулы определения твердости по Бринеллю:
Реклама
Обратите внимание, что термин HBW означает твердость по Бринеллю и вольфрамовому карбиду.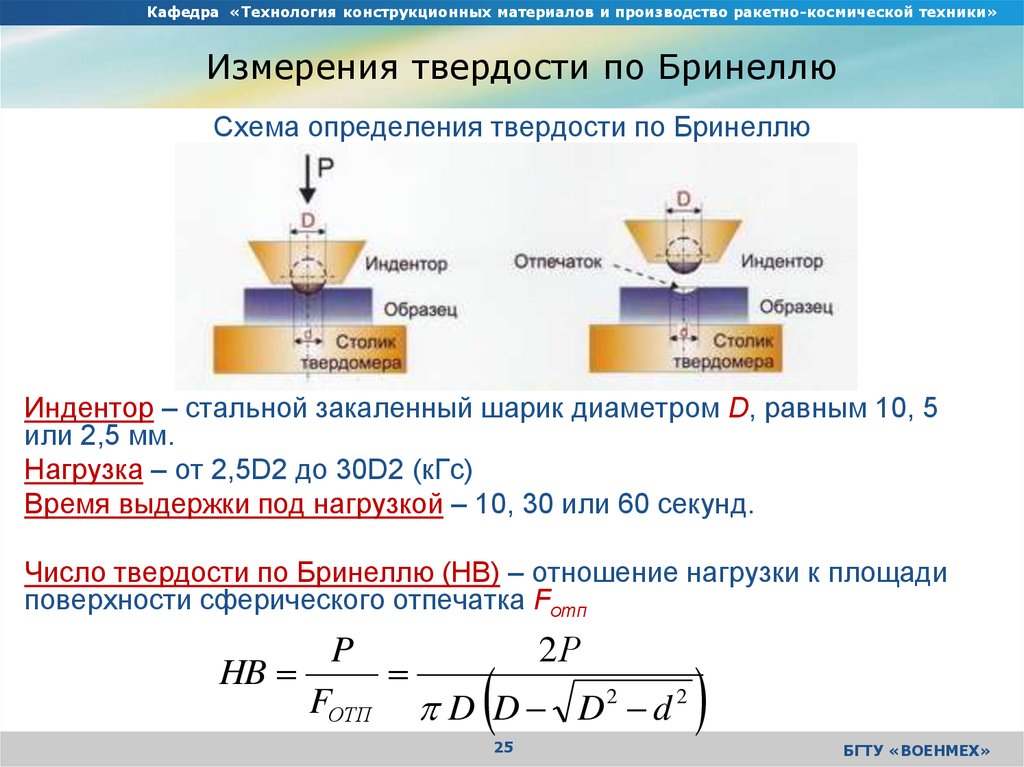
Карбид вольфрама (= карбид вольфрама) подчеркивает использование шариков из карбида вольфрама, в отличие от ранее использовавшихся (более мягких) стальных шариков (HBS). Рис. 3: Испытание на твердость по Бринеллю
Минимальная толщина испытательного образца должна быть не менее чем в 10 раз больше глубины вдавливания в соответствии со стандартом ASTM и не менее чем в 8 раз превышать глубину вдавливания в соответствии со стандартом ISO.
Указание числа твердости по Бринеллю
При указании числа твердости по Бринеллю (BHN или HB) необходимо указать условия испытаний, использованные для получения числа. Стандартный формат для указания «HBW 10/3000». «HBW» относится к шарику из карбида вольфрама, используемому в качестве индентора, в отличие от «HBS», что означает шарик из закаленной стали. «10» — это диаметр мяча в миллиметрах. «3000» — это сила в килограммах силы.
Иногда твердость по Бринеллю также указывается как «XXX HB YYD2», где
- XXX — прилагаемое усилие (в кгс)
- YY указывает тип материала (5 для алюминиевых сплавов, 10 для медных сплавов, 30 для стали).
Таким образом, твердость по Бринеллю типичной стали можно записать: 250 HB 30D2. На следующем изображении из Википедии представлены некоторые типичные значения твердости по Бринеллю для обычных материалов.
Рис. 4: Типичные значения твердости по БринеллюТребования к определению твердости по Бринеллю
- Перед испытанием образец необходимо тщательно очистить. Предпочтительно, чтобы испытательная поверхность была обработана, отшлифована и отполирована, чтобы получить более точное измерение вдавливания.
- Необходимо выбрать подходящий индентор (стальной шарик или карбидный шарик) в соответствии с требованиями.
- Необходимо заранее определить применимую силу.
- Нагрузка на образец должна поддерживаться в течение определенного периода времени.
- Отступы должны располагаться таким образом, чтобы оставался достаточный зазор от края образца и между отдельными отпечатками.
Стандарты для теста на твердость Бринелла
Широко используемые стандарты для теста на твердость Бринелла в промышленности:
- ASTM E10
- ISO 6506
- JIS Z 2243
.
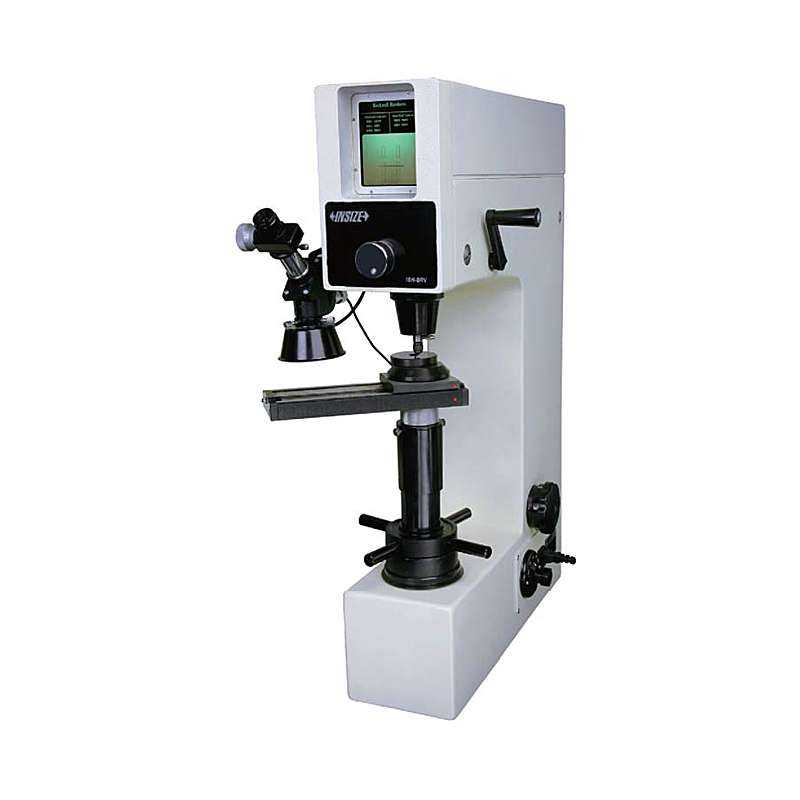
- Можно измерить твердость необработанных образцов, что сложно другими методами.
- Возможно применение высокой испытательной нагрузки (до 3000 кг).
- Широкий диапазон измерений благодаря наличию различных размеров инденторов и нагрузок
- Твердомер по Бринеллю может определять твердость всех типов металлов.
- Обеспечивает надежные результаты.
Однако метод Бринелля имеет и некоторые недостатки:
- Возможны ошибки измерения из-за использования оптических приборов.
- Дефекты поверхности могут повлиять на результаты испытаний, если поверхность не будет тщательно подготовлена.
- Требование плоской поверхности делает этот тест излишним для цилиндрических поверхностей.
Brinell vs Rockwell hardness Test
The main difference between Brinell and Rockwell Hardness Test is provided in the table below:
Brinell Hardness Test | Rockwell Hardness Test |
In Brinell Hardness Испытание индентором представляет собой сферический шарик из карбида вольфрама | Для испытания на твердость по Роквеллу индентор представляет собой небольшой стальной шарик (HRB) или алмазный конус (HRC) |
С помощью этой установки невозможно измерить твердость выше 650 HB.![]() | При измерении твердости по Роквеллу такого ограничения нет. |
Испытание на твердость по Бринеллю измеряет диаметр вмятины для расчета значения твердости. | Глубина вдавливания измеряется для расчета твердости по Роквеллу. |
Метод измерения твердости по Бринеллю является сравнительно медленным методом. | Определение твердости по Роквеллу — более быстрый процесс. |
Для определения твердости по Бринеллю требуется подготовка поверхности. | Для проведения испытаний на твердость по Роквеллу подготовка поверхности не требуется. |
Comparatively costly | Cheaper option |
Brinell, Rockwell, and Vickers Hardness Conversion Table
The approximate conversion of Brinell, Rockwell B & C, and Vickers hardness приведен ниже только для образца. Также добавлен еще один столбец, указывающий приблизительную эквивалентную прочность на растяжение.
Brinell Hardness (HB)-3000Kg-10 mm Ball | Rockwell Hardness (HRC)-150Kg Brale | Rockwell (HRB)- 100Kg 1/16″ Ball | Vickers Hardness (HV)- Diamond Pyramid 120 кг | Прибл. Tensile strength (N/mm²) | |||||||||||
800 | 72 | ||||||||||||||
780 | 71 | ||||||||||||||
760 | 70 | ||||||||||||||
752 | 69 | ||||||||||||||
745 | 68 | ||||||||||||||
746 | 67 | ||||||||||||||
735 | 66 | ||||||||||||||
711 | 65 | ||||||||||||||
695 | 64 | ||||||||||||||
681 | 63 | ||||||||||||||
658 | 62 | ||||||||||||||
642 | .![]() | ||||||||||||||
613 | 59 | ||||||||||||||
601 | 58 | 746 | |||||||||||||
592 | 57 | 727 | |||||||||||||
572 | 56 | .0132 | |||||||||||||
534 | 54 | 120 | 589 | ||||||||||||
513 | 53 | 119 | 567 | ||||||||||||
504 | 52 | 118 | 549 | ||||||||||||
486 | 51 | 118 | 531 | ||||||||||||
469 | 50 | 117 | 750 | 117 | 750 | 117 | 750 | 117 | 750 | .0127 | 49 | 117 | 497 | ||
456 | 48 | 116 | 490 | 1569 | |||||||||||
445 | 47 | 115 | 474 | 1520 | |||||||||||
430 | 46 | 115 | 458 | 1471 | |||||||||||
419 | 45 | 114 | 448 | 1447 | |||||||||||
415 | 44 | 114 | 438 | 1422 | |||||||||||
402 | 43 | 114 | 424 | 1390 | |||||||||||
388 | 42 | 113 | 406 | 1363 | |||||||||||
375 | 41 | 112 | 393 | 1314 | |||||||||||
373 | 40 | 111 | 388 | 1265 | |||||||||||
360 | 39 | 111 | 376 | 1236 | |||||||||||
348 | 38 | 110 | 361 | 1187 | |||||||||||
341 | 37 | 109 | 351 | 1157 | |||||||||||
331 | 36 | 109 | 342 | 1118 | |||||||||||
322 | 35 | 108 | 332 | 1089 | |||||||||||
314 | 34 | 108 | 320 | 1049 | |||||||||||
308 | 33 | 107 | 311 | 1035 | |||||||||||
300 | 32 | 107 | 303 | 1020 | |||||||||||
290 | 31 | 106 | 292 | 990 | |||||||||||
277 | 30 | 105 | 285 | 971 | |||||||||||
271 | 29 | 104 | 277 | 941 | |||||||||||
264 | 28 | 103 | 271 | 892 | |||||||||||
262 | 27 | 103 | 262 | 880 | |||||||||||
255 | 26 | 102 | 258 | 870 | |||||||||||
250 | 25 | 101 | 255 | 853 | |||||||||||
245 | 24 | 100 | 252 | 838 | |||||||||||
240 | 23 | 100 | 247 | 824 | |||||||||||
233 | 22 | 99 | 241 | 794 | |||||||||||
229 | 21 | 98 | 235 | 775 | |||||||||||
223 | 20 | 97 | 227 | 755 | |||||||||||
216 | 19 | 96 | 222 | 716 | |||||||||||
212 | 18 | 95 | 218 | 706 | |||||||||||
208 | 17 | 95 | 210 | 696 | |||||||||||
203 | 16 | 94 | 201 | 680 | |||||||||||
199 | 15 | 93 | 199 | 667 | |||||||||||
191 | 14 | 92 | 197 | 657 | |||||||||||
190 | 13 | 92 | 186 | 648 | |||||||||||
186 | 12 | 91 | 184 | 637 | |||||||||||
183 | 11 | 90 | 183 | 617 | |||||||||||
180 | 10 | 89 | 180 | 608 | |||||||||||
175 | 9 | 88 | 178 | 685 | |||||||||||
170 | 7 | 87 | 175 | 559 | |||||||||||
167 | 6 | 86 | 172 | 555 | |||||||||||
166 | 5 | 86 | 168 | 549 | |||||||||||
163 | 4 | 85 | 162 | 539 | |||||||||||
160 | 3 | 84 | 160 | 535 | |||||||||||
156 | 2 | 83 | 158 | 530 | |||||||||||
154 | 1 | 82 | 152 | 515 | |||||||||||
149 | 81 | 149 | 500 | ||||||||||||
147 | 80 | 147 | 490 | ||||||||||||
143 | 79 | 146 | 482 | ||||||||||||
141 | 78 | 144 | 481 | ||||||||||||
139 | 77 | 142 | 480 | ||||||||||||
137 | 76 | 140 | 475 | ||||||||||||
135 | 75 | 137 | 467 | ||||||||||||
131 | 74 | 134 | 461 | ||||||||||||
127 | 72 | 129 | 451 | ||||||||||||
121 | 70 | 127 | 431 | ||||||||||||
116 | 68 | 124 | 422 | ||||||||||||
114 | 67 | 121 | 412 | ||||||||||||
111 | 66 | 118 | 402 | ||||||||||||
107 | 64 | 115 | 382 | ||||||||||||
105 | 62 | 112 | 378 | ||||||||||||
103 | 61 | 108 | 373 | ||||||||||||
95 | 56 | 104 | |||||||||||||
90 | 52 | 95 | |||||||||||||
81 | 41 | 85 | |||||||||||||
76 | 37 | 80 | 9Таблица 2: Таблица преобразования твердости по Бринеллю, Роквеллу и Виккерсу для получения точных результатов. |
Рисунок 1: Для получения успешных результатов измерения твердости сверьтесь с таблицей минимальной твердости для толщины стенки образца. |
Минимальная толщина стенки. При испытании труб и труб особое внимание следует уделить толщине стенки и опоре контрольной точки. Метод испытания по Роквеллу определен в стандарте ASTM E18. Стандарт определяет минимальную толщину стенок, необходимую для получения хорошего результата (см. 9).0024 Рисунок 1 ).
Эти минимумы хорошо работают для плоских образцов, которые поддерживаются непосредственно под контрольной точкой. Однако образец трубки или трубки может вообще не работать, если он неправильно закреплен. Если труба или труба имеет большое отношение диаметра к толщине, вы не сможете провести надлежащий тест Роквелла, даже если толщина стенки соответствует требованиям таблицы из-за постоянного отклонения вокруг контрольной точки.
Прогиб. Одним из способов определить, является ли отклонение постоянным, является наблюдение за областью вокруг вмятины. Вы не должны иметь возможности наблюдать какую-либо остаточную деформацию в результате испытания, кроме фактической точки отпечатка. Любая визуальная деформация в другом месте указывает на серьезную проблему.
Поскольку одна точка Роквелла составляет всего 0,002 мм (0,00008 дюйма), возможно, произошло отклонение, которое вы не видите. Если вы сомневаетесь, попробуйте провести тот же тест на нарезанном образце с подходящей наковальней. Если вы получите тот же результат, вы можете быть уверены, что тест действителен. В противном случае вам придется либо перейти на весы с меньшим испытательным усилием, либо использовать внутреннюю оправку для поддержки детали под контрольной точкой.
Внутренние опоры. Внутренние опоры называются наковальнями «гусиная шея». Они бывают разных размеров, чтобы соответствовать диаметру детали. Необязательно иметь точную посадку, но чем ближе, тем лучше. Проблема со стандартными гусиными шеями заключается в том, что они могут проверять только конец детали, обычно в пределах дюйма. Чтобы проводить испытания дальше от конца трубы, можно спроектировать и изготовить специальные наковальни, но всегда будет практический предел, особенно для труб малого диаметра.
Также можно проводить испытания по внутреннему диаметру детали с помощью удлинителей индентора на гибкой шее. Они также ограничены тестированием ближе к концу детали. Доступны специальные внутренние тестеры, но они дороги, сложны в использовании и имеют ограниченное применение для испытаний труб и трубок.
Рис. 2: При испытании цилиндрических деталей иногда необходимы поправки, которые зависят от диаметра и твердости образца. ![]() |
Определение поправочных коэффициентов. В стандарте ASTM E18 также есть таблицы для определения поправочных коэффициентов при испытании цилиндрических форм (см. , рис. 2, ). Поправки варьируются в зависимости от диаметра и твердости образца и могут достигать шести баллов по шкале HRC и 12,5 баллов по шкале HRB.
Шкалы HRC и HRB являются наиболее популярными используемыми шкалами Роквелла. HRC использует алмазный индентор с испытательным усилием 150 кг и используется в основном для закаленных сталей. Шкала HRB обычно используется для мягких материалов, таких как сплавы алюминия и латуни. Он использует 1/16-дюймовый. шариковый индентор с испытательным усилием 100 кг.
Испытание по Бринеллю
Испытание по Бринеллю обычно используется для больших толстостенных труб. Поскольку тест Бринелля не является методом измерения глубины, он более щадящий. Однако чрезмерные прогибы, видимые невооруженным глазом, все же могут давать ошибочные результаты, если напряжения внутри материала повышены.
Если вы сомневаетесь, протестируйте разрезанный кусок, закрепленный должным образом, чтобы убедиться, что результаты совпадают. Если нет, вам придется уменьшить испытательное усилие или перейти на другой тест, например, Rockwell.
Трубы и шланги часто имеют круглую форму. Во время испытания на твердость кривизна испытательной поверхности может повлиять на результаты, поскольку опора вокруг индентора отличается от плоского образца.
Во время испытания по Бринеллю кривизна обычно не вызывает большого беспокойства, поскольку дополнительная толщина стенки обычно гарантирует достаточно большой диаметр для получения хорошего результата. Однако вы должны с подозрением относиться к любому некруглому отступу, указывающему на отсутствие поддержки отступа.
Учет возможных проблем приводит к правильным значениям твердости
Испытание на твердость труб требует некоторых особых соображений, помимо тех, которые обычно связаны с конкретным используемым методом испытаний.