Изделия электроугольные: Электроугольные изделия | Электроматериаловедение | Архивы
alexxlab | 04.12.2020 | 0 | Разное
Электроугольные изделия | Электроматериаловедение | Архивы
Страница 58 из 59
РАЗДЕЛ ПЯТЫЙ ЭЛЕКТРОУГОЛЬНЫЕ ИЗДЕЛИЯ, ПРИПОИ И КЛЕИ
ГЛАВА XVI.
ЭЛЕКТРОУГОЛЬНЫЕ ИЗДЕЛИЯ
§ 91. Электроугольные материалы и изделия
К электроугольным изделиям относятся щетки для электрических машин, электроды для электрических печей, контактные детали, высокоомные угольные сопротивления и некоторые другие изделия.
Электроугольные изделия изготовляют из смеси углеродистых материалов. К углеродистым материалам относятся; природный графит, нефтяной и пековый кокс, сажа, антрацит и древесный уголь. Кроме углеродистых материалов, в исходный состав некоторых электроугольных изделий входят металлические порошки: медный, свинцовый, оловянный и др. Металлические порошки применяют для изготовления металлографитных электрощеток и контактных деталей, предназначенных для работы при больших плотностях тока.
Кроме перечисленных порошкообразных материалов, в производстве электроугольных изделий применяют также связующие и пластифицирующие вещества — каменноугольные смолы и пеки.
Все углеродистые материалы (за исключением графита и сажи) подвергают прокаливанию при температуре 1200—1300° С. Цель предварительного прокаливания — удалить из углеродистых материалов влагу, летучие вещества и тем самым уменьшить объемную усадку электроугольных изделий. Затем прокаленные углеродистые материалы измельчают в дробилках до порошкообразного состояния.

Взятые в определенном соотношении исходные порошкообразные материалы (углеродистые и металлические) тщательно смешивают друг с другом в смесителях. Затем в смесь вводят связующие вещества (смолы, пеки), которые смешивают с порошкообразными материалами при температуре 110—230° С, пропуская их через специальные смесители.
Полученную после смешивания исходную электроугольную массу сушат, а затем выгружают из смесителя и после остывания до комнатной температуры размалывают и просеивают через сито. В результате этого получают прессовочный порошок (пресс-порошок). Электроугольные порошкообразные массы без связующего (сухие смеси) просеивают и сразу получают пресс-порошок. Из пресс-порошка изготовляют прессованием в стальных разъемных пресс-формах различные электроугольные изделия или заготовки (блоки), из которых механической обработкой (распиливанием и шлифованием) получают электрощетки и другие изделия.
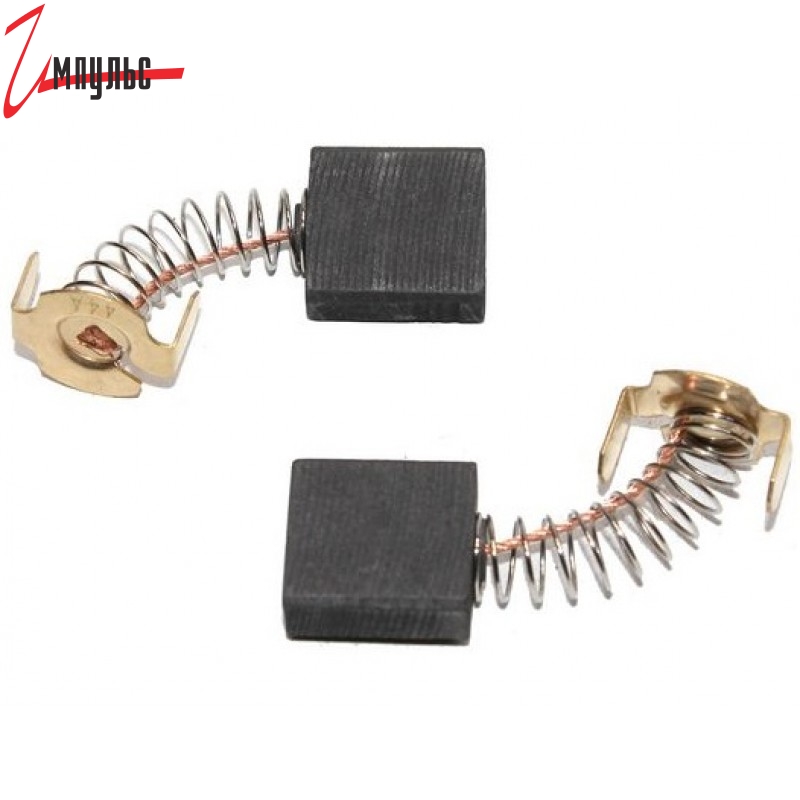
Прессование электроугольных изделий производится при комнатной температуре или при 180—210° С (в зависимости от взятого связующего). В случае связующего, размягчающегося или полимеризующегося при повышенных температурах, прессование электроугольных изделий производится также при повышенных температурах. Прессуют электроугольные изделия при удельных давлениях от 1000 до 3000 кГ/см2.
Изготовление изделий, с большой линейной протяженностью (электроосветительные угли, блоки и др.) производят методом выдавливания нагретой пластичной исходной массы через стальной мундштук винтового пресса.
Полученные электроугольные изделия или их заготовки (блоки) подвергают высокотемпературной обработке — обжигу в специальных печах. Обжиг производится в интервале температур от комнатной до 1000—1300°С — в зависимости от состава исходной массы и получаемых электроугольных изделий.
В процессе обжига происходит спекание — соединение частиц исходных материалов и цементация их коксом, образующимся из связующих органических веществ.

В результате обжига электроугольные изделия приобретают механическую прочность и способность к механической обработке. При этом уменьшается величина их удельного электрического сопротивления. Электроугольные изделия, содержащие сажу, кокс и другие неграфитовые компоненты, после обжига подвергают дополнительной термической обработке (при 2400—2800° С), называемой графитизацией. При этом неграфитовые компоненты в изделиях превращаются в графит, а большинство примесей испаряется. В результате графитизации электрощетки (группы ЭГ) и другие изделия приобретают некоторую мягкость, уменьшается коэффициент трения и резко снижается удельное электрическое сопротивление изделий.

Пропитка электроугольных изделий производится при температурах 80—200° С и выше, когда пропитывающее вещество находится в жидком состоянии. Пропитка имеет целью устранить пористость и уменьшить гигроскопичность электроугольных изделий, а иногда ввести в них смазочные вещества (воскообразные). Пропитка электроугольных изделий металлами резко увеличивает их механическую прочность и повышает их проводимость.
Пропитанные и некоторые непропитанные электроугольные изделия (электрощетки и др.) подвергают механической обработке для придания им окончательной формы и чистоты поверхности. Заготовки (блоки) электрощеток и других изделий разрезают на мелкие части с помощью фрез или тонких карборундовых кругов на специальных станках. Затем в изделиях сверлят отверстия под гибкие соединительные провода.
Некоторые типы электрощеток и осветительных углей после механической обработки подвергают омеднению.
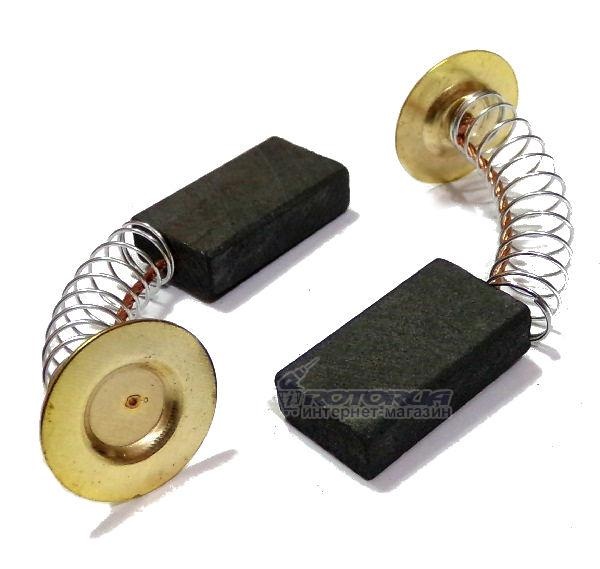
Рис. 178. Основные конструкции щеток с арматурой и токоподводящими проводами:
1 — тело щетки, 2 — токоподводящие провода, 3 — крепящие детали
У готовых электрощеток Проверяют размеры, твердость, механическую прочность, удельное электрическое сопротивление, падение напряжения между щеткой и коллектором, коэффициент трения, переходное сопротивление между токоподводящим проводом и электрощеткой и другие характеристики.
На рис.

§ 92. Основные свойства электроугольных изделий
Из электроугольных изделий наибольшее применение имеют электрощетки, которые чаще всего называют просто щетками.
Применяемые в настоящее время угольные электрощетки делятся на четыре основные группы: графитные, угольно-графитные, металло-графитные и электрографитированные.
Графитные щетки (марки Г-3 и Г-20) изготовляют из натурального графита без применения и с применением связующих. Графитные щетки, получаемые без связующего, после прессования не подвергают спеканию (обжигу). При применении связующих веществ (смолы) отпрессованные графитные щетки спекаются при температуре 1000—1100° С. В высокоомные графитные щетки вводится резольная смола, и после прессования они спекаются при температуре 200—400° С.
Графитные щетки обладают мягкостью и при работе вызывают незначительный шум. Они могут применяться при окружных скоростях коллектора или колец от 12 до 25 м/сек, а натурально-графитные до 70 м/сек.
Высокоомные графитные щетки применяются в машинах высокого напряжения. Остальные сорта графитных щеток находят применение главным образом в быстроходных машинах постоянного и переменного тока (турбогенераторы и асинхронные электродвигатели). Графитные щетки обладают очень хорошими антифрикционными свойствами.
Допустимая плотность тока для всех графитных щеток (за исключением высокоомных) 7—12 а/см2, для высокоомных 5-7 а/см2. Удельное нажатие 200—250 г/см2.
Угольно-графитные щетки (марки Т2 и др.) изготовляют из графита с введением других углеродистых материалов (сажа, кокс) и связующих веществ (смолы, пеки). После прессования исходной смеси щетки (или их блоки) подвергаются спеканию при температуре 1000—1200° С. Полученные щетки омедняются в электролитической ванне.
Угольно-графитные щетки имеют повышенную твердость и механическую прочность.

Угольно-графитные щетки средней твердости находят применение в генераторах и электродвигателях небольшой и средней мощности. Щетки с повышенной твердостью применяют в электрических машинах с толчкообразной нагрузкой.
Металло-графитные щетки (марки М-1, М-3, М-6, М20, МГ6, МГС-5 и др.) изготовляют из порошков графита и меди. В некоторые из них вводят еще порошки свинца (МГС5), олова и серебра. В щетках с большой допустимой плотностью тока содержание меди доходит до 80—90%. Этим достигается уменьшение величины удельного электрического сопротивления щеток и малое падение напряжения.

Отпрессованные щетки и блоки щеток спекаются в печах при температуре 700—1000° С.
Эта группа щеток отличается малым удельным сопротивлением 1—-6 ом-мм2/м, а у некоторых даже 0,03—0,25 ом-мм2/м. У щеток этой группы с пониженным содержанием меди (меньше 50%) удельное электрическое сопротивление достигает значений 5-12 ом-мм2/м (М-3). Допустимая плотность тока для щеток этой группы лежит в пределах от 12 до 25 а/см2. Удельное нажатие 180—230 г/см2.
Металло-графитные щетки применяют при окружных скоростях от 20 до 35 м/сек в автомобильных и авиационных генераторах и электродвигателях, а также в синхронных машинах и в тяговых машинах с пониженным напряжением, но при больших значениях силы тока.
Электрографитированные щетки (марки ЭГ-2а, ЭГ4, ЭГ8, ЭГ74 и др.) изготовляют из порошков графита и других углеродистых материалов (кокс, сажа) с введением связующих. После прессования и обжига (спекания) изделия поступают в электрические печи для графитизации.
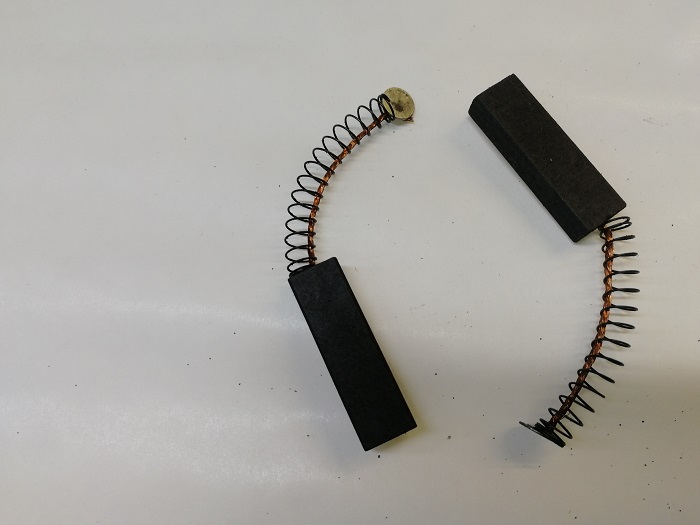
Электрографитированные щетки хорошо переносят толчкообразное изменение нагрузки и могут работать при больших скоростях — 40—60 м/сек.
Удельное электрическое сопротивление щеток этой группы равно 9—70 ом-мм2/м. Они применяются в электрических машинах средней и большой мощности, в машинах с изменяющейся нагрузкой и тяжелыми условиями коммутации тока (ЭГ14), в тяговых электродвигателях и в быстроходных электрических машинах со стальными кольцами (ЭГ74). Группа электрографитированных щеток имеет самую большую область применения в электротехнике.
Из других электроугольных изделий следует отметить электроды для дуговых печей и электролизных ванн, сварочные электроды, аноды для ртутных выпрямителей, электроугольные контакты и контактные детали для подвижных токосъемных устройств, электровозов, троллейбусов и т.

Электроугольные электроды очень стойки к электрической дуге. Они не горят, не плавятся и очень медленно окисляются при температуре дуги около 3800° С.
Технология производства перечисленных изделий в основном не отличается от технологии изготовления щеток. Удельное электрическое сопротивление электродов находится в пределах 9—14 ом-мм2/м и 42—55 ом-мм’2/м (угольно-графитные).
Электроугольные контакты изготовляют из медно-графитных и серебряно-графитных электроугольных масс. Эти изделия отличаются малым удельным сопротивлением 0,02—0,05 ом-мм2/м и тем, что они не свариваются друг с другом и с металлическими контактами в процессе работы.
Контактные электроугольные детали изготовляют прессованием или выдавливанием через мундштук. Для повышения сопротивления истиранию готовые (спеченные) контактные изделия пропитывают свинцово-оловянистыми сплавами и другими металлами.
Кроме рассмотренных, существует целый ряд других видов электроугольных изделий (электроосветительные угли, микрофонные порошки, подшипники скольжения и др.

Электроугольные изделия – Энциклопедия по машиностроению XXL
Электроугольные изделия (табл. 3) изготовляют из чистых углеродистых материалов, графита или в композиции (смеси) с различными металлическими порошками или другими компонентами. [c.378]Электроугольные изделия и их технические показатели [c.379]
Электроугольные изделия. Прожекторные и другие осветительные угли, угли для электросварки и электроэрозионной обработки металлов, трубы Для электрофильтров и печей. [c.407]
ЭЛЕКТРОУГОЛЬНЫЕ ИЗДЕЛИЯ. ПОЛУПРОВОДНИКОВЫЕ МАТЕРИАЛЫ. ЛЮМИНОФОРЫ [c.448]
Предприятия по производству электроизоляционных изделий (миканитов и слюдинитов, слоистых электроизоляционных и электроустановочных материалов, лакотканей электроизоляционных и др.), свинцовых и щелочных аккумуляторов, гальванических элементов и батарей, электроугольных изделий, электротехнического фарфора, керамики и изоляторов из стекла
[c. 321]
Среди твердых неметаллических проводниковых материалов наибольшее значение имеют материалы на основе углерода электротехнические угольные изделия, сокращенно электроугольные изделия . Из угля изготовляют щетки электрических машин, электроды для прожекторов, для дуговых электрических печей и электролитических ванн, аноды гальванических элементов. Угольные порошки используют в микрофонах для создания сопротивления, изменяющегося от звукового давления. Из угля делают высокоомные резисторы, разрядники для телефонных сетей угольные изделия применяют в электровакуумной технике. [c.43]
Различные изделия из угля с добавкой связующих веществ и т. п. применяют в электротехнике в виде щеток электрических машин, сопротивлений и реостатов, для электродов дуговых печей и ламп, гальванических ванн и элементов, изделий для слаботочной электротехники. Мы рассмотрим лишь одну группу электроугольных изделий — щетки для электрических машин.
[c. 217]
К электроугольным изделиям, применяемым в электротехнике и технике связи, относятся электрические щетки для коллекторов электромашин, Электроугли, применяемые в лампах и электропечах, электроды — в гальванических элементах, угольные мембраны, микрофонные порошки, аноды для радиоламп. [c.283]
Электроугольные изделия. В качестве сырья для производства электроугольных изделий можно использовать сажу, природный графит или антрацит. Для получения стержневых электродов измельченная масса со связующим веществом, в качестве которого используется каменноугольная смола, а иногда и жидкое стекло, продавливается через мундштук. [c.297]
ГЛАВА V. ЭЛЕКТРОУГОЛЬНЫЕ ИЗДЕЛИЯ [c.194]
Рассмотрим одну из групп электроугольных изделий. (рис. 54) для электрических машин (табл. 78 и 79), [c.194]
Электроугольные изделия (щетки для электрических машин) [c.336]
Электроугольными изделиями являются щетки для электрических машин, электроды для дуговых печей, контактные детали и другие изделия. Электроугольные изделия изготовляют методом прессования из исходных Порошко-
[c.336]
Рз1 смотрим одну из групп электроугольных изделий — щетки (рис. 97) для электрических машин. [c.263]
Электроустановочные прессматериа-лы — Характеристики 58—61 Электроугольные изделия 376, 378—381 Электрощетки 378, 380, 381 Эмалевые покрытия защитные — Назначение и способы нанесения 476 [c.543]
Лаки бакелитовые выпускаются (ГОСТ 901—78) марок ЛБС-1, ЛБС-2, ЛБС-3 ЛБС-14 — для склеивания, пропитки и покрытия материалов, ЛБС-4, ЛБС-5, СБС-1, лак 180 — в качестве связующего соответственно пластмасс, электроугольных изделий, древеснослопстых пластиков, оболочковых форм и стержней, ЛБС-8 — для клеев, ЛБС-9 и ЛБС-10 — для фильтрующих материалов, ЛБС-16 — для стеклотекстолитовых изделий, ЛБС-20 — для прессовочных материалов, ЛБС-29 — для текстолита. [c.259]
Графит для электроугольных изделий (ГОСТ 10274—79) в зависимости от месторождения выпускают следующих марок ЭУЗ (завальевскп электроуголь-нып) сортов М (малозольный), I и II УУТ (тайгинскпй) I, II и III сортов ЭУИ (погпнскпй).

Обработка твердосплавных деталей штампов, высадочных матриц заточка твердосплавного инструмента, резка твердых материалов обработка драгоценных и полудрагоценных камней, шлифование, сверление, резка и вырезка оптического стекла обработка ферритов, керамики, стекол, электроугольных изделий. Выполнение работ, связанных сболы ими съемами материала при сравнительно низких требованиях к шероховатости поверхности (не выше 8-го класса) [c.636]
ВНИИПТИэлектроугольных изделий Всесоюзный научно-исследовательский и проектно-технологический ин-т электроугольных изделий ВНИИФТРИ Всесоюзный научно-исследовательский ин-т физико-технических и радиотехнических измерений [c.427]
В качестве сырья для производства электроугольных изделий используют сажу, графит или антрацит. Для получения стержневых электродов измельченную массу со связкой, в качестве которой используют каменноугольную смолу, а иногда и жидкое стекло, продавливают через мундштук. Изделия более сложной формы изготовляют в соответствующих пресс-формах. Угольные заготовки проходят процесс обжига. От режима обжига зависит форма, в которой углерод находится в изделии. При высоких температурах обжига (до 2200° С) углерод искусственно переводится в форму графита, вследствие чего такой процесс называют графитированием.
[c.43]
Электротехническая сталь 90 Электротехнические материаль) 6 Электроугольные изделия 217 Эмалированная проволоха 219 Эмаль КВД 94 [c.272]
Основными электроугольными изделиями, применяемыми в автотракторном электрооборудовании, являются щетки для генераторов, стартеров и электродвигателей. Различают угольно-графитные, графитные, металлографитные щетки. Они выпускаются размерами от (толщинаХширйнаХвысота) 1,6Х2Х8 до 40x50x100 мм. [c.206]
Электроугольные изделия —щетки для электрических машин, электроды для дуговых печей, контактные детали и другие изготовляют методом прессования из исходных порошкообразных масс с последующей высокотемпературной обработкой — обжигом изделий. Исходные порошкообразные массы составляют из смеси углеродистых материалов (графит, сажа, кокс, антрацит и др.), связующих и пластифицирующих веществ (каменноугольные и синтетические емейлы, пеки и др.). В некоторые электроугольные массы вводят порошки металлов меди, серебра и др.
[c.194]
1. Описать технологию получения, виды и область применения электроугольных материалов – Документ
1. Описать технологию получения, виды и область применения электроугольных материалов.
Из числа твердых неметаллических
проводниковых материалов наибольшее
значение имеют материалы на основе
углерода (электротехнические
угольные изделия, сокращенно электроугольные
изделия). К
электроугольным изделиям,
применяемым в электротехнике и
технике связи, относятся: электрические
щётки для коллекторов электромашин,
электроугли, применяемые в лампах и
электропечах, электроды – в гальванических
элементах, угольные мембраны, угольные
порошки используют в микрофонах для
создания сопротивления, изменяющегося
от звукового давления. Из угля делают
высокоомные резисторы, разрядники
для телефонных сетей; угольные изделия
применяют в электровакуумной технике.
В качестве сырья для производства электроугольных изделий можно использовать сажу, графит или антрацит. Для получения стержневых электродов измельченная масса со связующим, в качестве которого используется каменноугольная смола, а иногда и жидкое стекло, продавливается сквозь мундштук. Изделия более сложной формы изготовляют в соответствующих пресс-формах. Угольные заготовки проходят процесс обжига. Режим обжига определяет форму, в которой углерод будет находиться в изделии. При высоких температурах достигается искусственный перевод углерода в форму графита, вследствие чего такой процесс носит название графитирования.
Производство электрощёток
включает в себя обжиг
обычных щеток для электрических машин
ведут при температуре около 800 °С;
графитированные щетки нагревают при
обжиге до 2200 °С. Щетки служат для
образования скользящего контакта между
неподвижной и вращающейся частями
электрической машины, т. е. для подвода
(или отвода) тока к коллектору или
контактным кольцам и, кроме того,
осуществляют коммутацию переменной
э.д.с., индуктированной в обмотке
якоря.
Щетки применяют на коллекторах электромашин постоянного и переменного тока, в тяговых электродвигателях с добавочными полюсами, в крановых двигателях, двигателях для подъемников, прокатных станов, компрессоров в шахтных и рудничных моторах, на одноякорных преобразователях, а также на многих других генераторах и двигателях постоянного и переменного тока асинхронных и синхронных.
Угольные электроды термического назначения служат:
1)в качестве нагревательных элементов электрических печей, где они выполняют роль резисторов;
2)в качестве проводника электроэнергии к нагревательному элементу, состоящему из угольной крупки в печах сопротивлений.
Электроды применяют в производстве
ферросплавов, электростали, карбида
кальция, абразивных материалов для
шлифования, электролизе алюминия,
электросварке.
Угольные электроды, работа которых будет протекать при высоких температурах, обжигаются также при очень высокой температуре, вплоть до 3000 °С. Угольные электроды, как и другие угольные изделия, имеют отрицательный температурный коэффициент удельного сопротивления.
Для освещения в качестве электродов вольтовой дуги употребляют специальные сорта углей. Различают угли для постоянного и переменного токов. Положительный электрод для постоянного тока обычно применяют с фитилем, диаметр его больше диаметра отрицательного угля в 1,5-2 раза потому, что накаливается он сильнее. В случае одинаковых диаметров он сгорел бы скорее.
Осветительные угли подразделяются на: прожекторные, кинопроекционные, для постоянного тока, переменного тока, киносъемочные и различных марок. Угли изготовляются в виде стержней диаметром от 5 до 30 мм, длиной от 120 до 450 мм.
Угли для гальванических элементов
применяют в качестве положительного
полюса гальванических элементов в
виде пластин в цилиндре различных
размеров.
2. Нарисовать диаграмму состояния сплавов железа с углеродом, пояснить практическое значение и провести сравнение свойств сплавов с содержанием углерода 0,4% и 2,5%
Диаграмма состояния железо-цементит имеет большое практическое значение. Ее применяют для определения тепловых режимов термической обработки и горячей обработки давлением (ковка, горячая штамповка, прокатка) железоуглеродистых сплавов. Ее используют также в литейном производстве для определения температуры плавления, чтo необходимо для назначения режима заливки жидкого железоуглеродистого сплава в литейные формы.
Основными компонентами, от
которых зависит структура и свойства
железоуглеродистых сплавов, являются
железо и углерод. Чистое железо – металл
серебристо-белого цвета; температура
плавления 1539°С. Железо имеет две
полиморфные модификации: α и γ. Модификация
α существует при температурах ниже
911°С и выше 1392°С; γ-железо – при 911-1392°С.
В
зависимости от температуры и концентрации
углерода железоуглеродистые сплавы
имеют следующие структурные составляющие.
1. Феррит (Ф) – твердый раствор
внедрения углерода в α-железе. Растворимость
углерода в α-железе при комнатной
температуре до 0,005%; наибольшая
растворимость – 0,02% при 727°С. Феррит имеет
незначительную твердость (НВ 80-100) и
прочность (σв=250 МПа), но высокую
пластичность (δ=50%; φ=80%).
2. Аустенит
(А) – твердый раствор внедрения углерода
в γ-железе. В железоуглеродистых сплавах
он может существовать только при высоких
температурах. Предельная растворимость
углерода в γ-железе 2,14% при температуре
1147°С и 0,8% – при 727°С. Эта температура
является нижней границей устойчивого
существования аустенита в железоуглеродистых
сплавах. Аустенит имеет твердость НВ
160-200 и весьма пластичен (δ=40-50%).
3. Цементит (Ц) – химическое соединение
железа с углеродом (карбид железа Fe3C).
В цементите содержится 6,67% углерода.
Температура плавления цементита около
1600°С. Он очень тверд (НВ~800), хрупок и
практически не обладает пластичностью.
Цементит неустойчив и в определенных
условиях распадается, выделяя свободный
углерод в виде графита по реакции
Fe3C→3Fe+C.
4. Графит – это свободный
углерод, мягок (НВ 3) и обладает низкой
прочностью. В чугунах и графитизированной
стали содержится в виде включений
различных форм (пластинчатой, шаровидной
и др.). С изменением формы графитовых
включений меняются механические и
технологические свойства сплава.
5. Перлит (П) – механическая смесь
(эвтектоид, т. е. подобный эвтектике, но
образующийся из твердой фазы) феррита
и цементита, содержащая 0,8% углерода.
Перлит может быть пластинчатым и
зернистым (глобулярным), что зависит от
формы цементита (пластинки или зерна)
и определяет механические свойства
перлита. При комнатной температуре
зернистый перлит имеет предел прочности
σв=800 МПа; относительное удлинение δ=15%;
твердость НВ 160. Перлит образуется
следующим образом. Пластинка (глобуль)
цементита начинает расти или от границы
зерна аустенита, или центром кристаллизации
является неметаллическое включение. При этом соседние области обедняются
углеродом и в них образуется феррит.
Этот процесс приводит к образованию
зерна перлита, состоящего из параллельных
пластинок или глобулей цементита и
феррита. Чем грубее и крупнее выделения
цементита, тем хуже механические
свойствперлита.
6. Ледебурит
(Л) – механическая смесь (эвтектика)
аустенита и цементита, содержащая 4,3%
углерода. Ледебурит образуется при
затвердевании жидкого расплава при
1147°С. Ледебурит имеет твердость НВ
600-700 и большую хрупкость. Поскольку при
температуре 727°С аустенит превращается
в перлит, то это превращение охватывает
и аустенит, входящий в состав ледебурита.
Вследствие этого при температуре ниже
727°С ледебурит представляет собой уже
не смесь аустенита с цементом, а смесь
перлита с цементитом.
Сплав с содержанием углерода 0,4% называется доэвтектоидной сталью. Структура доэвтектоидной стали при комнатной температуре после медленного охлаждения состоит из Феррита и Перлита (эвтектоидной смеси Феррита и Цементита). Данный сплав имеет высокую пластичность и относительно низкую прочность (после отжига).
Сплав с содержанием углерода 2,5% называется доэвтектическим чугуном. Структура данного сплава при комнатной температуре после медленного охлаждения состоит из Перлита, Цементита вторичного и превращенного Ледебурита. Данный сплав имеет высокую прочность и относительно низкую пластичность.
3. Сущность диффузионной металлизации сталей. Методы диффузионной металлизации и цели.
Диффузионной металлизацией называется процесс насыщения поверхности стальных деталей алюминием, хромом, кремнием, бором и другими элементами для повышения коррозионной стойкости, жаростойкости, твердости и износостойкости. При насыщении алюминием процесс называется алитированием, при насыщении хромом – хромированием, при насыщении кремнием – силицированием, при насыщении бором – борированием. Диффузионная металлизация проводится в твердых, жидких и газообразных средах при температурах 950-1150°С и требует длительного времени (до 25 ч). Высокая температура необходима для увеличения скорости диффузии насыщающих металлов.
Различают следующие методы металлизации:
При диффузионной металлизации в твердой среде металлизатором является сплав железа с алюминием, хромом, кремнием, бором и т. п. (ферросплавы) с добавлением хлористого аммония. Хлористый аммоний при нагреве диссоциирует с выделением хлористого водорода, который, взаимодействуя с насыщающим металлом, образует летучее соединение хлора с металлом. Хлориды металлов при контакте с железом диссоциируют с образованием атомарного насыщающего металла, который диффундирует вглубь, образуя с железом твердые растворы замещения.
Процесс химико- термической обработки | Состав смеси, % |
Алитирование | 49-49,5 Al; 49-49,5 Аl203; 1-2 NH4Cl 99,5 FeAl; 0,5 NH5C1 |
Хромирование | 50 FeCr; 43 AI2О3; 7 NH4CI 60 FeCr; 38,8 каолин; 1,2 NH4CI |
Силицирование | 40 Si; 59 AI203; 1 NH4CI 75 FeSi; 20 шамот; 5 NH4C1 |
Жидкая диффузионная металлизация производится погружением детали в расплавленный металл (например, в алюминий) или соляные ванны с добавлением в них ферросплавов.
Газовая диффузионная металлизация проводится в газовых средах, содержащих хлориды различных металлов. Хлориды металла при нагреве взаимодействуют с железом, образуя атомарные насыщающие металлы. При диффузионной металлизации алюминием детали приобретают высокую окалиностойкость; при металлизации хромом – коррозионную устойчивость, кислотоупорность и поверхностную твердость; при металлизации кремнием – кислотоупорность; при металлизации бором – высокую твердость, износоустойчивость и кислотоупорность.
Алитированию, хромированию и силицированию подвергают сплавы на железной, никелевой и других основах. Эти диффузионные покрытия способны защищать детали от окисления при высоких температурах, так как на их поверхности в окислительной среде образуются плотные пленки из AI2O3, Сr2О3 и SiO2, препятствующие диффузии кислорода. Хромирование среднеуглеродистых сталей (0,3 – 0,4 % С) приводит к повышению их поверхностной твердости и износостойкости, так как на поверхности образуется тонкий слой (0,025 – 0,030 мм) карбида (Сr,Fe)7C3 или (Cr,Fe)23C6 с твердостью 1200 – 1300 HV. Несмотря на низкую твердость (200 – 300 HV), силицированный слой хорошо сопротивляется износу.
Поверхность диффузионно-металлизированной детали обладает высокой жаростойкостью, поэтому жаростойкие изделия изготавливают из простых углеродистых сталей с последующим алитирова-нием, хромированием силицированием. Исключительно высокой твёрдостью (до HV 2000) обладают и высоким сопротивлением абразивному износу обладают борированные слои, вследствие образования на поверхности высокотвёрдых боридов железа – FeB и Fe2B.
Диффузионными покрытиями можно значительно повысить коррозионную стойкость углеродистых сталей в разбавленных водных растворах неорганических кислот. Наибольшей стойкостью к действию 10 %-й HNO3 обладают хромотитанированные и хромоалитированные стали, несколько уступают им хромированные и хромотитаноалитированные стали. Бори- рованные стали хорошо сопротивляются действию 10 %-й H2SO4 и 30 %-й НС1. Борированные и особенно хромосилицированные стали обладают высокой коррозионной стойкостью в 40 %-й Н3РО4. Хромированные стали устойчивы к коррозии в 3 %-м водном растворе NaCl (морской воде), лучшие результаты получены после цирконоалитирования и титаноалитирования сталей. Хромированные высокоуглеродистые стали обладают хорошей коррозионной стойкостью к действию даже 50 %-й уксусной кислоты СН3СООН.
4. Расшифровать марки материалов и описать их область применения: 40Г; Р9М3; Бр.О-6; СЧ35; 5ХЗВЗМФС.
40Г– Сталь конструкционная легированная (марганоцовистая).
В марке стали цифра перед буквами указівает на содержание углерода в сотых долях процента (сталь содержит ≈0,40% углерода). Буква «Г» указывает на легирование стали марганцем. Цифра после буквы указывает на содержание легирующего элемента в %. Отсутствие цифры после буквы указывает на содержание легирующего элемента ≈1% (сталь содержит ≈1% марганца).
Применение: Оси, коленчатые валы, шестерни, штоки, бандажи, детали арматуры, шатуны, звездочки, распределительные валики, головки плунжеров и другие детали, к которым предъявляются требования повышенной прочности.
Р9М3 – быстрорежущая инструментальная сталь.
Буква «Р» в марке стали указывает принадлежность к быстрорежущим сталям. Цифра после буквы «Р» указывает на содержание воль в процентах (сталь содержит 9% вольфрама). Буква «М» указывает на легирование молибденом. Цифра после буквы указывает на содержание легирующего элемента в процентах (сталь содержит 3% молибдена).
Применение: резцы, сверла, фрезы, резьбовые фрезы, долбяки, развертки, зенкеры, метчики, протяжки для обработки конструкционных сталей с прочностью до 1000 МПа, от которых требуется сохранение режущих свойств при нагревании во время работы до 600 °С.
БрО-6 – бронза оловянная, обрабатываемая давлением.
В маркировке буквы «Бр» обозначают—бронза, затем следуют буквы, указывающие названия входящих элементов, а затем цифры. процентного содержания этих элементов. Буква «О» указывает на легирование оловом. Содержание олова 6%.
Применение: детали приборов, пружины.
СЧ35 – чугун серый.
В маркировке буквы «СЧ» обозначают серый чугун. Цифры после букв указывают на прочность в МПа *10-1. Чугун имеет прочность 350 МПа.
Применение: для изготовления различных отливок особо ответственного назначения – блоков и головок цилиндров, гильз, маховиков в транспортном машиностроении; тяжелонагруженных деталей работающих при сжатии (башмаков, колонн) в строительстве; тяжелонагруженных станин прессов, гидроцилиндров в станкостроении; наиболее ответственных деталей с самыми высокими требованиями в дизелестроении; тяжелонагруженных деталей со значительными колебаниями сечений в химическом машиностроении; наиболее ответственных деталей, работающих на износ в сельскохозяйственном машиностроении; отливок деталей трубопроводной арматуры и приводных устройств к ней; частей литых соединительных для трубопроводов.
Электроугольные изделия – Справочник химика 21
I — пеки —связующие, применяемые при изготовлении само— обжигающихся или обожженных анодов, графитированных электродов, электроугольных изделий и конструкционных материалов на основе графита [c.61]В производстве электродных и электроугольных изделий применяют донецкие антрациты, которые по своим свойствам удовлетворяют требованиям прочности. [c.11]
Электроугольные изделия, полученные из кокса камерной смолы, по всем показателям не уступают электродам из нефтяного кокса. Пек камерной смолы не пригоден в качестве связующего при получении изделий, подлежащих графитизации. [c.250]
ФГУП Научно-исследовательский институт электроугольных изделий, [c.104]
Посвящается пятидесятилетию Научно-исследовательского института электроугольных изделий [c.9]
Применение сажи в производстве углеграфитовых материалов относится в основном к изготовлению щеток для электрических машин, углей для гальванических батарей, угольных столбов для регуляторов напряжения и других видов электроугольных изделий. [c.178]
Больше всего сажу потребляют в качестве наполнителя (усилителя) резины, для красок и изготовления электроугольных изделий. Ходовые сорта сажи нормируют стандартами (табл. 11). [c.70]
Для электроугольных изделий характерно использование в качестве основного сырья сажи и металлических порошков. В производстве электродных изделий и конструкционных графитов эти виды сырья не используются. [c.109]
Т. у. применяют как наполнитель резин (св. 80% выпускаемой сажи) и пластмасс, пигмент для типографских красок, копировальной бумаги, лент для пишущих машин и др. в произ-вах нек-рых сплавов, спец. сортов бумаги, электроугольных изделий (напр., электродов), гальванических элементов. [c.562]
Для придания антрациту свойств, необходимых при использовании его в качестве сырья в производстве электроугольных изделий (увеличения электропроводности, прочности, плотности), его подвергают термообработке, нагревая в специальных печах в определенном режиме до температуры 1000—1400° С. Полученный таким образом продукт, называемый термоантрацитом, затем измельчают, смешивают в определенном соотношении со связующим (каменноугольный пек, смолы и пр.) и формуют изделие. Сырую ( зеленую ) заготовку подвергают обжигу, в ходе которого происходит коксование связующего и цементация зерен в монолитную структуру. [c.161]
Промышленное производство мелких электроугольных изделий в России началось в 1875—1876 г. (г. Кинешма), [c.11]
Кроме того, изучалась возможность применения пека камерной смолы в качестве связующего материала при производстве электроугольных изделий. [c.358]
В дальнейшем кокс камерной смолы назван образцом 1, а сланцевый кокс камерных печей — образцом № 2 (табл. 1). Кокс № 1 изучался па возможность изготовления электроугольных изделий. Кокс Л 2 опробовался на возможность выплавки карбида кальция. [c.359]
Анализ пека камерной смолы приведен в табл. 3. Пек камерной смолы опробовался в качестве связуюш,его при изготовлении электроугольных изделий. [c.359]
Прокаленный кокс Л 1 пригоден для производства электроугольных изделий. [c.364]
Машинисты мельниц (мельники) и мешальщики сухой массы для свинцовых аккумуляторов, элементных и электроугольных изделий. [c.244]
Уголь марки ТЛ, выжженный из древесины твердо л истовых пород, применяют для производства активированного угля, сероуглерода, карбюризатора и электроугольных изделий. [c.77]
В промышленности для изготовления электроугольных изделий вместо каменноугольного пека в относительно малых количествах применяются препарированная каменноугольная смола, смолопеки, а также синтетические связующие в смеси с каменноугольным пеком или отдельно. [c.100]
Допускается содержание влаги до 20%, но с перерасчетом веса на уголь нормальной влажности (6%). Заводам, получающим древесину сплавом, разрешается поставлять уголь с содержанием золы не более 4%. Уголь, поставляемый в качестве топлива для газогенераторных автомобилей и тракторов, не должен содержать головней и посторонних примесей. Уголь марки ТЛ, поставляемый для производства сероуглерода, должен быть крупный. Уголь марки ТЛ, поставляемый для производства активированного угля, должен быть выжжен из древесины не смешанных твердолиственных пород (отдельно березовый, буковый и т. п.) и иметь размеры кусков, установленные для крупного угля. Вес 1 л такого угля— не более 220 г. Уголь, поставляемый для электроугольных изделий, должен иметь размер кусков в любом линейном направлении не менее 50 мм допускается не более 10% во весу кусков размером менее 50 мм и не более 1,5% мелочи (размером менее 12 мм). [c.78]
Получение электроугольных изделий [c.8]
Федеральное государственное унитарное предприятие Научно-исследовательский и проектно-технологический институт электроугольных изделий , г. Электроугли Московской обл. E-mail niiei dio.ru. [c.89]
И наконец, в 1948-1949 гг. был освоен новый вид продукции, полученный на основе принципиально отличной от электродной технологии. Это графит, разработанный для изготовления анодов ртутных вьшрямителей и электровакуумных приборов — АРВ и ЭВП. Впоследствии этот графит однородной мелкозернистой структуры при использовании для других целей получил наименование МГ-1. Его технология близка к изготовлению электроугольных изделий и основана на первоначальном смешивании мелких (тонких) фракций нефтяного кокса, вернее его пыли, с каменноугольным пеком и формовании кулича. После его охлаждения такой кулич подвергается дроблению и размолу до пекококсового порошка. Последний формуется в глухой матрице, а затем проходит стадии обычного обжига и графитации. Может быть подвергнут и пропитке в целях уплотнения. Прочностные характеристики такого графита в 2-3 раза выше, чем у электродного, а однородность его структуры позволяет вести весьма точную его мехобработку. Однако его размеры были на значительный период ограничены диаметром 320 мм и примерно этой же длиной. Впоследствии такой графит нашел широкое применение в виде различного рода фасонных изделий для высокотемпературных процессов тиглей, экранов, нагревателей и т.д. [c.39]
Основное количество сажи (более 95% общего объема производства) используется в резиновой промышленности. Она производится печным методом из жидких углеводородов, преимущественно нефтяного происхождения. В указанном процессе в пламя, которое создается обычно природным газом и воздухом, впрыскиваются нефтяные и каменноугольные масла. В частности, для получения марки П803(П805Э), применяемой для производства электроугольных изделий, используется зеленое масло (керосино-газойлевая фракция нефти 170-360 С). Прежнее ее название, сохранившееся в классификации США, — ламповая сажа. [c.181]
Использование антрацитов и термографитов в электроугольных изделиях / Фиалков А. С,, Занина Н. К., Гилязов У. Ш. и др. — В сб. Электротехническая промышленность. Электротехнические материалы, 1981, № 6 (131), с. 3-5. [c.673]
Высокоплавкие пеки используются в производстве электроугольных изделии, углеродных конструкционных материалов, металлургического кокса, брикетированных углей и коксов, лаков, мастик, кровельных материалов, пеконаполненных полимеров, препарированных смол. Умеренно высокотемпературные пеки с Тразм=Ю5..,140 С используются в цветной металлургии кик связующие в производстве предварительно обожжённых и самообжигаюши.чся (с боковым теплоподводом) анодов. Пеки с Тразм=120,,,140°С и коксуемостью 51.,,54% используются в чёрной металлургии для изготовления углеродных литейных форм, а пеки с Трю. [c.120]
В имеющихся справочниках материалы обычно группируются по различным признакам — по области применения, распространенности, классу соединений и т. п. Составители данного справочника, считаясь с принятой в СССР организацией углеграфитовой промышленности, систематизировали сведения об углеграфитовых материалах преимущественно по промышленному признаку. Так, сведения о графитнрованных анодах, используемых только в электролитических процессах (электролиз поваренной соли), помещены в гл. 4 Электродные изделия , а сведения об анодах и сетках, применяемых в электровакуумных приборах, — в гл. 5 Электроугольные изделия . [c.5]
Создание двухслойных покрытий, в которых первый слой — метал-лополимер, а второй — электролитическая медь, позволило значительно повысить коррозионную стойкость металлических покрытий на электроугольных изделиях и существенно упростить технологический процесс их получения. [c.119]
Демидова А.К., Сенина O.E., Дол атоз Л.Б , Фролов В.И. – Применение различных нефтяных пеков о технологш производства электроугольных изделий. – Химия твердого топлива, 1975, 15, с. ID – 117. . [c.150]
В производстве электроугольных изделий для повышения однородности меднографитовых смесей и интенсификации процесса нх перемешивания предложено использовать электромагнитный аппарат с вихревым слоем и встроенными устройствами (11]. [c.34]
В результате исследований для производства электроугольных изделий разработаны конструкции непрерывнодействующих установок для смешивания порошков меди, графита, олова и свинца (13]. В состав установки входят бункеры для исходных компонентов, дозаторы объемного и весового типов, вихревой смеситель, маслостанция и блок управления установкой. В зависимости от свойств перерабатываемых сыпучих материалов предлагаются различные конструкции дозаторов и питателей — от серийно выпускаемых до оригинальных, разработанных авторами. [c.34]
Применение. Алмазы применяют для сверления, резки, огранки и шлифовки особо твердых материалов при бурении горных пород для изготовления деталей приборов и инструментов, фильтров и абразивных материалов в ювелирном деле. Графит употребляют в производстве огнеупоров, электротехнических изделий и материалов в химическом машиностроении в качестве конструкционного материала как компонент смазочных и антифрикционных составов для производства карандашей и красок для предупреждения образования накипи на стенках котлов. Из искусственного кускового графита и пирографита изготовляют сопла ракетных двигателей, камеры сгорания, носовые конусы и некоторые детали ракет блоки иэ особо чистого искусственного графита используют в ядерной технике как замедлители нейтронов. Уголь является топливом, применяется в черной и цветной металлургии (в производстве алюминия, при рафинировании меди и др.), а также в производстве сероуглерода, активного угля, электроугольных изделий, для получения жидких каменноугольных продуктов и, путем подземной газификации, газообразпого топлива. Технический является ингредиентом резин и пластмасс, основным черным пигментом для печатных и малярных красок используется при изготовлении линолеума, клеенки, кирзы, галантерейных материалов, лент для пишущих машинок, копировальной бумаги и др. входит в некоторые полировочные составы как теплоизоляционный материал в дорожном строительстведобавка [c.293]
У. д. широко применяют в народном хозяйстве основные областн применения черная (доменное иро-из-во) и особенно цветная (получение кремния, в ироиз-ве алюминия, рафинирование меди и др.) металлургия, произ-во Sj, активного угля, карбюризатора, электроугольных изделий и др. Выход У. д. 30—40 % от веса сухой древесины. См. такн е Сухая перегонка древесины. [c.164]
методические указания к практической работе
Открытая электронная библиотека научно-образовательных ресурсов Оренбуржья
Проект выполнен при поддержке Правительства Оренбургской области, Оренбургского регионального отделения Партии «Единая Россия» и Министерства образования Оренбургской области
Пожалуйста, используйте этот идентификатор, чтобы цитировать или ссылаться на этот ресурс: http://elib.osu.ru/handle/123456789/8951
Название: | Изучение неметаллических проводников и электроугольных изделий : методические указания к практической работе |
Авторы: | Бушуй, Л. А. |
Ключевые слова: | проводники по виду материалов проводниковые материалы неметаллические проводники проводники неметаллические материалы для электроугольных изделий электроугольные изделия электротехнические угольные изделия природный графит пиролитический углерод сажа бороуглеродистые пленки антрацит методические указания |
Дата публикации: | 2009 |
Издатель: | ГОУ ОГУ |
Аннотация: | Методические указания предназначены для проведения практической работы «Изучение неметаллических проводников и электроугольных изделий» по дисциплине «Материаловедение, электрорадиоматериалы и радиокомпоненты» для студентов второго курса специальности «Техническое обслуживание и ремонт радиоэлектронной техники». Методические указания составлены с учетом Государственного образовательного стандарта среднего профессионального образования по направлению подготовки дипломированных специалистов утвержденного 18.03.2002 Министерством образования Российской Федерации. |
URI: | http://elib.osu.ru/handle/123456789/8951 |
Располагается в коллекциях: | Учебники, учебные пособия |
Все ресурсы в архиве электронных ресурсов защищены авторским правом, все права сохранены.
Вход в личный кабинетКонтекстная рекламаУЗИП серии ETHERNET Для защиты оборудования, использующего интерфейс Ethernet. От гроз, электростатических разрядов и др.
Щитовое оборудование CHINT Официальный представитель производителя CHINT.
Силовые автоматические выключатели CHINT Такое нельзя пропустить! Смотрите запись от 1 февраля 2021 г. Неожиданные новинки, сенсационное партнерство.
Корпус RS52 – решение для Вас! Цените своё время и беспокоитесь о безопасности при установке электрооборудования? Вам нужен RS52 ТМ «Узола»!
Face Temp Многофункциональный терминал для распознавания лица и измерения температуры. Доставка. | Вы здесь | Поиск по сайтуКонтекстная рекламаЛестничные лотки LESTA IEK® Металлические кабельные лотки высотой: 55, 80, 100, 150 мм. Высокая нагрузка и стойкость к коррозии. Надежная прокладка кабельной трассы.
Автоматические выключатели CHINT Широкий ассортимент электрооборудования и низковольтной аппаратуры удобно приобрести в интернет магазине официального представителя.
Автоматические выкл. ВА88 MASTER IEK Рабочее напряжение до 690 В. Служат для защиты электрических сетей от КЗ, перегрузки, снижений напряжения. Компактные размеры.
H07RN-F медный кабель от производителя Кабели по международному стандарту. Напрямую с завода, доставка по всей России, комплексные заказы.
Надёжное электрощитовое оборудование! Широкий ассортимент, доступные цены и высокое качество. Добро пожаловать на страницы каталога ГК «Узола»!
Свежий номерРассылкаПодпишитесь на нашу бесплатную рассылку! */ ]]]]>]]> |
Электроугольное изделие – Технический словарь Том VII
Электроугольные изделия ( табл. 3) изготовляют из чистых углеродистых материалов, графита или в композиции ( смеси) с различными металлическими порошками или другими компонентами.Электроугольные изделия, полученные из кокса камерной смолы, по всем показателям не уступают электродам из нефтяного кокса. Пек камерной смолы не пригоден в качестве связующего при полутении изделий, подлежащих графитизации.
Электроугольные изделия ( табл. 3) изготовляют из чистых углеродистых материалов, графита или в композиции ( смеси) с различными металлическими порошками или другими компонентами.
Магнитные характеристики магнитотвердых ферритов. Электроугольные изделия – щетки для электрических машин, электроды для дуговых печей, контактные детали и другие изготовляют методом прессования из исходных порошкообразных масс с последующей высокотемпературной обработкой – обжигом изделий.
Электроугольные изделия ( осветительные, элементные, сварочные и др. угли) имеют небольшие размеры по сечению и длине. В связи с этим конструкция их значительно проще, чем у электродных прессов, потому что многие вспомогательные операции не требуют специальных гидравлических приводов.
Электроугольные изделия хранят в упакованном виде на стеллажах с гнездами но маркам, размерам и сортам при относительной влажности возуха до 80 %, при температуре от 5 до 30 С. Угольные щетки, снятые с хранящихся электромашин, укладывают отдельно.
Щетка на контактном кольце электрической машины. Электроугольными изделиями являются щетки для электрических машин, электроды для дуговых печей, контактные детали и другие изделия.
Основными электроугольными изделиями, применяемыми в автотракторном электрооборудовании, являются щетки для генераторов, стартеров и электродвигателей. Они выпускаются размерами от ( толщинаХширйнаХвысота) 1 6X2X8 до 40x50x100 мм.
Для электроугольных изделий характерно использование в качестве основного сырья сажи и металлических порошков. В производстве электродных изделий и конструкционных графитов эти, виды сырья не используются.
Пропитка электроугольных изделий производится в автоклавах, которые являются сосудами, работающими под давлением.
К электроугольным изделиям, применяемым в электротехнике и технике связи, относятся: электрические щетки для коллекторов электромашин, Электроугли, применяемые в лампах и электропечах, электроды – в гальванических элементах, угольные мембраны, микрофонные порошки, аноды для радиоламп.
Угольные электроды. Сырьем для электроугольных изделий служат сажа, графит или антрацит. В качестве связующего материала применяется каменноугольная смола, При высоких температурах обжига электроугольных изделий протекает процесс перехода углерода в форму графита, называемый графитированием.
При пропитке электроугольных изделий расплавленными металлами: свинцом, кадмием и др. – пропитчики должны работать в валенках, прорезиненном переднике, шерстяных рукавицах и надетом головном уборе.
Механическая обработка электроугольных изделий должна производиться в отдельном изолированном от других помещении, оборудованном приточно-вы-тяжной вентиляцией с местными отсосами, обеспечивающими удаление пыли непосредственно у мест ее образования. Приток воздуха в помещение механической обработки должен составлять не более 80 – 90 % объема механической вытяжки.
При обработке электроугольных изделий рабочие должны пользоваться защитными очками или экранами.
В производстве электродных и электроугольных изделий применяют донецкие антрациты, которые по своим свойствам удовлетворяют требованиям прочности.
В производстве электродных и электроугольных изделий применяются донецкие антрациты, которые по своим свойствам удовлетворяют требованиям промышленности.
Материалы, полуфабрикаты, электроугольные изделия и прочие грузы должны храниться на территории предприятия на специально подготовленных для этого площадках или складах правильными рядами, штабелями или пачками, не загромождая проходов и проездов. Разгрузка и укладка материалов должны производиться согласно инструкции, разработанной администрацией.
Щетка на контактном кольце электрической машины. Рассмотрим одну из групп электроугольных изделий – щетки ( рис. 97) для электрических машин.
Оборудование для производства заварок электроугольных изделий: смесители, пьяные бочки и барабаны, вальцы и др. – должно размещаться в отдельном изолированном от других помещении.
Цехи и отделения прессования электроугольных изделий, как правило, должны размещаться в отдельных помещениях. Допускается установка горизонтальных гидравлических прессов в помещении смесильного отделения и эксцентриковых прессов в арматурном отделении.
В качестве сырья для производства электроугольных изделий можно использовать сажу, графит или антрацит. Для получения стержневых электродов измельченная масса со связующим, в качестве которого используется каменноугольная смола, а иногда и жидкое стекло, продавливается сквозь мундштук. Изделия более сложной формы изготовляют в соответствующих пресс-формах. Угольные заготовки проходят процесс обжига. Режим обжига определяет форму, в которой углерод будет находиться в изделии. При высоких температурах достигается искусственный перевод углерода в форму графита, вследствие чего такой процесс носит название графитирования.
В качестве сырья для производства электроугольных изделий используют сажу, графит или антрацит. Для получения стержневых электродов измельченную массу со связкой, в качестве которой используют каменноугольную смолу, а иногда и жидкое стекло, продавливают через мундштук. Изделия более сложной формы изготовляют в соответствующих пресс-формах. Угольные заготовки проходят процесс обжига. От режима обжига зависит форма, в которой углерод находится в изделии. При высоких температурах обжига ( до 2200 С) углерод искусственно переводится в форму графита, вследствие чего такой процесс называют графитированием.
Мы рассмотрим лишь одну группу электроугольных изделий – щетки для электрических машин.
В качестве сырья для производства электроугольных изделий можно использовать сажу, графит или антрацит. Для получения стержневых электродов измельченная масса со связующим, в качестве которого используется каменноугольная смола, а иногда и жидкое стекло, продавливается сквозь мундштук. Изделия более сложной формы изготовляют в соответствующих пресс-формах. Угольные заготовки проходят процесс обжига. Режим обжига определяет форму, в которой углерод будет находиться в изделии. При высоких температурах достигается искусственный перевод углерода в форму графита, вследствие чего такой процесс носит название ерафитирования.
Высокоплавкие пеки используются в производстве электроугольных изделий, углеродных конструкционных материалов, металлургического кокса, брикетированных углей и коксов, лаков, мастик, кровельных материалов, пеконаполненных полимеров, препарированных смол. С используются в цветной металлургии как связующие в производстве предварительно обожженных и самообжигающихся ( с боковым теплоподводом) анодов.
В качестве сырья для производства электроугольных изделий используют сажу, графит или антрацит. В частности, для электродов дуговых электропечей используется углеграфитовый материал марок ГЭ и ЭГ-0.
Прессы всех типов для испытания электроугольных изделий на сжатие и разрыв должны быть оборудованы защитными ограждениями, предохраняющими работающих от осколков при разрушении образцов.
Оборудование для гальванического луженая арматуры электроугольных изделий должно размещаться в отдельном изолированном помещении высотой 5 м, причем травильное отделение должно быть изолировано от помещения, где производится лужение.
Изложенные соображения по выбору марки электроугольных изделий дают основные, принципиальные указания относительно методов решения подобной задачи. В отдельных случаях могут возникнуть обстоятельства, изменяющие описанную схему. Возможны отклонения от схемы, связанные с теми или иными особенностями отдельных конкретных электрических машин. Однако в своей принципиальной основе предлагаемая схема является экспериментально обоснованной. Применяя ее совместно с данными таблиц приложений, задачу выбора марки электрощетки можно решить достаточно, надежно.
Некоторые типы щеткодержателей. Во всех прочих случаях, когда электроугольное изделие работает в неподвижном щеткодержателе и перемещается относительно него, рассматриваемый контакт создается либо только за счет непосредственного соприкосновения с неподвижной обоймой, либо путем подключения к нему дополнительной параллельной электрической цепи.
Это время соответствует началу промышленного производства электроугольных изделий на Западе. Карре [ В-2 ] были предложены основные операции производства углеграфитовых материалов: прокаливание, измельчение, смешение, прессование ( в пресс-форме и выдавливанием) и обжиг.
Прокаленный кокс № 1 пригоден для производства электроугольных изделий.
Более сложные технологические схемы применяются при производстве электроугольных изделий, например при производстве щеток, которые преимущественно готовят по двустадийной технологии.
Рабочие места для папки и горячего лужения электроугольных изделий могут быть размещены а арматурном отделении. Они должны быть оборудованы местными вытяжными вентиляционными отсосами, гарантирующими отвод образующихся в процессе пайки и лужения газов. Скорость воздуха непосредственно на месте пайки должна быть не менее 0 6 м / сек. В помещении устраивается также приточная вентиляция, разномерно подающая воздух в верхнюю зону.
Такая пропитка осуществляется с целью улучшения антифрикционных свойств электроугольных изделий при трении по коллектору, троллее или по какой-либо другой поверхности. Это особенно важно для достижения нормальной работы электрощеток и снижения износа в условиях вакуума, низкой температуры и др. Пропитка ведется в автоклавах по вакуум-компрессионному методу. После пропитки производится очистка и сушка изделий. Качество пропитки определяется по привесу изделий до и после пропитки. Если ее проводить солями, кристаллизующимися с достаточным количеством воды, то при нагревании такие соли легко переходят в жидкое состояние, не требуя дополнительного растворителя. Так, например, ведут себя квасцы.
ЛБС-5 – предназначается в качестве связующего для изготовления электроугольных изделий.
Расположение зданий на территории предприятия должно соответствовать технологическому процессу производства электроугольных изделий.
Машины, электротехнические устройства, электровакуумные изделия, химические источники тока, электроугольные изделия, 1 оптические, акустические и тепловые приборы.
Прессы для прессования изделий черных марок должны размещаться изолированно от прессов для прессования цветных электроугольных изделий.
Для придания антрациту свойств, необходимых при использовании его в качестве сырья в производстве электроугольных изделий ( увеличения электропроводности, прочности, плотности), его подвергают термообработке, нагревая в специальных печах в определенном режиме до температуры 1000 – 1400 С. Полученный таким образом продукт, называемый термоантрацитом, затем измельчают, смешивают в определенном соотношении со связующим ( каменноугольный пек, смолы и пр. Сырую ( зеленую) заготовку подвергают обжигу, в ходе которого происходит коксование связующего и цементация зерен в монолитную структуру.
Среди твердых неметаллических проводниковых материалов наибольшее значение имеют материалы на основе углерода электротехнические угольные изделия, сокращенно электроугольные изделия. Из угля изготовляют щетки электрических машин, электроды для прожекторов, для дуговых электрических печей и электролитических ванн, аноды гальванических элементов. Угольные порошки используют в микрофонах для создания сопротивления, изменяющегося от звукового давления. Из угля делают высокоомные резисторы, разрядники для телефонных сетей; угольные изделия применяют в электровакуумной технике.
Больше всего сажу потребляют в качестве наполнителя ( усилителя) резины, для красок и изготовления электроугольных изделий.
Этот же принцип был положен в основу классификаций, о которой говорилось выше и которая существовала долгое время – электродные и электроугольные изделия.
Уголь марки ТЛ, выжженный из древесины твердолистовых пород, применяют для производства активированного угля, сероуглерода, карбюризатора и электроугольных изделий.
Сажа, так же как и графит, применяется в качестве проводящего компонента в композиционных резистивных материалах и для изготовления электроугольных изделий.
Для того чтобы обеспечить надежный электрический контакт между телом электрощетки и проводом, заделываемым способами развальцовки и пайки, поверхность электроугольного изделия покрывают слоем омеднения толщиной 10 – 50 мк. Исключение из этого правила делают для изделий с развальцовкой, изготавливаемых из полуфабриката, содержащего в своем составе более 60 % металла. При заделке способом конопатки омеднение не производится.
К классу 3 относятся решающие электрические блоки, электрические машины, электротехнические устройства, электровакуумные изделия, химические источники тока, электроугольные изделия, оптические, акустические и тепловые приборы.
Уголь марки ТЛ, выжженный из древесины твердо л истовых пород, применяют для производства активированного угля, сероуглерода, карбюризатора и электроугольных изделий.
Amazon.com: выбор электрический угольный стартер, печь, угольная горелка, продукты для барбекю: сад и на открытом воздухе
- Убедитесь, что это подходит введя номер вашей модели.
- Материал: сталь Размеры продукта: 5,5 “X 7” x 7 “Диаметр лотка: 4,5 дюйма
- Продолжительность розжига примерно: 3-5 минут Напряжение: 110 В 60 Гц
- Мощность: 650 Вт В комплект входит: 1 электрический угольный стартер
- Поставляется с подарочной картой Crazysoft на 10 долларов.
Производство электроэнергии и побочные продукты | ND Studies Energy Curriculum
- Химическая энергия, запасенная в угле, выделяется при его сжигании и превращается в тепловую (тепловую) энергию, которая используется для производства пара.
- Пар вращает турбину, и эта механическая энергия используется для вращения генератора для производства электричества.
Этапы производства электроэнергии из бурого угля
- Бурый уголь доставлен на электростанцию.
- В зависимости от электростанции, бурый уголь измельчается до размера угля размером примерно ¼ дюйма или измельчается в мелкий порошок, поэтому он будет гореть быстрее.
- Измельченный или пылевидный уголь затем выдувается в камеру сгорания котла или топку.
- Трубы внутри котла несут воду, которая превращается в пар из-за высокой температуры сгорания.
- Пар достигает температуры до 1000⁰ F.
- Пар под высоким давлением нагнетается в турбину.
- Пар достигает давления до 3500 фунтов на квадратный дюйм (psi).
- Пар высокого давления заставляет лопатки турбины вращаться, вращая приводной вал.
- Приводной вал соединен с генератором, в котором магниты вращаются внутри катушек из проволоки для выработки электричества.
- Отработанный пар из турбины втягивается в конденсатор, который переводит пар обратно в жидкое состояние.
- Затем паровая вода возвращается в котел для повторения цикла.
- Сжигание угля приводит к образованию зольного остатка, летучей золы и различных газов.
- Зола улавливается и превращается в полезные побочные продукты; газы «очищаются», а затем выпускаются через выхлопные трубы.
- Зольный остаток – это крупный зольный материал, который удаляется со дна печи.
- Используется в заполнителях для дорожных оснований, тротуаров и в качестве продукта для шлифования обледенелых зимних дорог.
- Летучая зола состоит из частиц, которые удаляются из выхлопных газов.
- Перерабатывается и используется в строительстве и других коммерческих целях.
- Зола-унос получила свое название потому, что могла вылететь с электростанции, если бы не была захвачена.
- Зола-унос, добавляемая в бетон, дает бетон, с которым легче работать, он прочнее, служит дольше и имеет более высокое качество, чем бетон, изготовленный на портландцементе.
- К другим продуктам, обогащенным летучей золой, относятся ковры, краска, изоляция, потолочная и напольная плитка, пиломатериалы, кирпич и черепица.
- Летучая зола также используется для укрепления почвы и в качестве стабилизатора почвы для предотвращения эрозии почвы.
- Зольный остаток – это крупный зольный материал, который удаляется со дна печи.
- Труба на электростанции действует как дымоход и позволяет выхлопным газам покидать электростанцию.
- Видимый шлейф, выходящий из дымовой трубы на угольной электростанции, особенно зимой, почти полностью состоит из водяного пара.
- Энергетические компании Северной Дакоты потратили около 2 миллиардов долларов (2 000 000 000 долларов) на новые технологии для контроля выбросов на электростанциях.
- Зола улавливается и превращается в полезные побочные продукты; газы «очищаются», а затем выпускаются через выхлопные трубы.
Станция «Долина Антилоп» возле Беула: Северная Дакота – один из семи штатов, отвечающих всем стандартам качества воздуха, установленным федеральным правительством (США) (по состоянию на 2014 год). «Угольная страна» Северной Дакоты неизменно получает оценку «А» по качеству воздуха от Американской ассоциации легких.Фото любезно предоставлено Бассейновым электроэнергетическим кооперативом
- Технология контроля выбросов используется для удаления загрязняющих веществ из выхлопных газов перед их выбросом в воздух.
- Два типа устройств для улавливания твердых частиц: рукавный фильтр и осадитель .
- Рукавный фильтр – это гигантский фильтр, удаляющий частицы из выхлопных газов растений.
- Электрофильтр использует притяжение положительных и отрицательных электрических частиц для улавливания частиц в дымовых газах.
- Зола, улавливаемая рукавным фильтром или электростатическим фильтром, перерабатывается и используется в строительстве и других коммерческих целях.
- Скрубберы используются для удаления SO x или выбросов на основе серы.
- Это делается с помощью химического процесса.
- Дымовой газ смешивается с распыляемой водой и химическим веществом (обычно известью), позволяя газам соединяться с распыляемой жидкостью, которую необходимо удалить.
- Оксиды азота (NO x ) восстанавливаются за счет усовершенствований котла и / или химических добавок.
- NO x встречается в природе при таких событиях, как удары молнии и лесные пожары. NO x возникает в котле, автомобиле или печи из-за высокой температуры и присутствия азота и кислорода.
- По данным Агентства по охране окружающей среды США (EPA), 50 процентов выбросов NO x происходит от автомобилей и других мобильных источников, 20 процентов – от электростанций и 30 процентов – от множества других источников, таких как промышленные печи и производство. материалов.
Электростанции - в Северной Дакоте с 2006 года инвестировали около 1 миллиарда долларов в новые технологии для сокращения выбросов и повышения эффективности.
- Северная Дакота – один из семи штатов, отвечающих всем стандартам качества чистого воздуха EPA по состоянию на 2014 год.
- Два типа устройств для улавливания твердых частиц: рукавный фильтр и осадитель .
Сила Америки: угольный флот в меняющейся электросети | Mitchell, Williams, Selig, Gates & Woodyard, P.L.L.C.
Скачать PDF
America’s Power недавно выпустила трехминутный видеоролик, в котором подчеркивается важность национального угольного флота и его роль в поддержании надежности, устойчивости и топливной безопасности.Видео можно посмотреть здесь.
ВидеоThe America’s Power подчеркивает важность технологического подхода к решению проблемы выбросов углерода в электроэнергетическом секторе, а также подчеркивает необходимость исследований и разработок, а также политики, стимулирующей внедрение передовых технологий, таких как улавливание, использование углерода и т. Д. и хранение (CCUS).
В объявлении, сопровождающем выпуск своего видео, America’s Power делает следующие наблюдения:
- Национальная электросеть переживает переходный период, который вызывает все большую зависимость от непостоянных источников энергии, таких как ветер и солнце, и переход от управляемых (всегда доступных при необходимости) источников электроэнергии, таких как уголь.
- Существует множество экономических и технических проблем, связанных с переходом на энергосистему, которые директивным органам необходимо решить, чтобы обеспечить нам надежное и доступное электроснабжение во время и после перехода.
- Недавние чрезвычайные ситуации с электричеством в Техасе в прошлом месяце и Калифорнии в августе прошлого года служат предупреждением о рисках потери разнообразия видов топлива – и слишком большой зависимости от одного или двух источников электроэнергии – и снижения топливной безопасности за счет закрытия электростанций, которые являются надежными, потому что у них всегда есть топливо, независимо от погодных условий и других сбоев.
С комментариями Дона Гастона, генерального директора Энергетического кампуса штата Прери, и Стивена Винберга, бывшего помощника министра энергетики, видеоролик America’s Power освещает некоторые из этих проблем, а также подчеркивает важность исследований и разработок, а также разработки политики для стимулировать внедрение передовых технологий, таких как улавливание, использование и хранение углерода (CCUS), для решения задачи дальнейшего сокращения выбросов углерода в электроэнергетическом секторе, сохраняя при этом разнообразие видов топлива и топливную безопасность.
America’s Power – единственная национальная торговая организация, единственная миссия которой состоит в том, чтобы выступать на федеральном уровне и на уровне штатов в интересах угольной энергетики и угольного флота. В его состав входят представители основных отраслей – производителей электроэнергии, угледобывающих компаний, железных дорог, операторов барж и производителей оборудования – которые занимаются выработкой электроэнергии из угля.
7 ЭЛЕКТРОЭНЕРГЕТИКА | Уголь: энергия будущего
Gilbert / Commonwealth, Inc.1994. Оптимизация очистки газового потока в трех системах IGCC. Подготовлено для Министерства энергетики США по контракту DE-AC01-88FE61660. Ридинг, Пенсильвания: Gilbert / Commonwealth, Inc.
Кит, Р.Дж., П.А. Ирландия и П. Рэдклифф. 1991. Экономические оценки 28 процессов ДДГ. Стр. 273-2-90 в Proceedings of the 1991 SO 2 Control Symposium, декабрь 1991 г., Пало-Альто, Калифорния, TR-101054. Пало-Альто, Калифорния: Исследовательский институт электроэнергетики.
Коккинис, А., J.E. Cichanowicz, D. Eskinazi, J. Stallings и G. Offen. 1992. NO x регуляторы для общего котла: основные моменты семинара EPRI в июле 1992 года. Журнал Ассоциации по обращению с воздухом и отходами 42 (11): 1498-1505.
LaHaye, P.G., and M.R. Bary. 1994. Цикл сжигания на внешнем топливе (EFCC): проект Министерства энергетики США по очистке угля V – эффективные средства омоложения для старых угольных станций. Доклад представлен на выставке ASME Turbo Expo ’94, Гаага, Нидерланды, 13-16 июня.
Лохрасби, Дж., Г. Эшби и Ф. Уолтер. 1991. Экономика МГД модернизации и новых заводов. P. x1.2.1 в материалах 29-го симпозиума по инженерным аспектам магнитогидродинамики, Новый Орлеан, Луизиана, 18-20 июня. Таллахома, Теннесси: Симпозиумы по инженерным аспектам MHD, Inc.
Маканси, Дж. 1993a. Контроль выбросов SO 2 . Мощность 137 (6): 23-56.
Маканси, Дж. 1993b. Снижение выбросов NO x от современных электростанций. Мощность 137 (5): 11-28.
Мод, К.1993. Advanced Power Generation – Сравнительное исследование вариантов конструкции для угля. Лондон: Исследование угля Международного энергетического агентства.
Миллер, С.А., Г.Дж. Фогель, С. Gehl, J.E. Hanway, R.F. Генри, К. Паркер, Э. Смык, В. Свифт и В.Ф. Подольский. 1982. Техническая оценка: технология сжигания в псевдоожиженном слое. Аргоннская национальная лаборатория, ANL / FE-81-65. Вашингтон, округ Колумбия: Типография правительства США.
MIT. 1993. Оценка потребностей в исследованиях по улавливанию и удалению диоксида углерода с электростанций, работающих на ископаемом топливе.Отчет Министерства энергетики США, грант № DE-FG02-92ER30194. Кембридж, Массачусетс: Энергетическая лаборатория Массачусетского технологического института.
NRC. 1992. Политические последствия потепления парниковых газов. Комитет по науке, технике и государственной политике Национального исследовательского совета. Вашингтон, округ Колумбия: National Academy Press.
Ормерод, W.G., I.C. Вебстера, Х. Аудуса и У. Ример. 1993. Прогресс в оценке технологий улавливания, использования и удаления двуокиси углерода.Документ, представленный на Одиннадцатой Международной конференции по электростанциям, Association des Ingenieurs de l’Institut Montefiore, сентябрь, Льеж, Бельгия.
Ороско, штат Нью-Джерси, 1993. Керамический воздухонагреватель высокого давления для газовых турбин с косвенным обогревом. Документ, представленный на Совещании по совместному рассмотрению подрядчиков, конференции FE / EE по усовершенствованным турбинным системам, конференции FE по топливным элементам и угольным тепловым двигателям. Министерство энергетики США, Центр энергетических технологий Моргантауна. Моргантаун, Западная Вирджиния, август.3-5.
Pigeaud, E. 1994. Полировка множественных загрязнений холодным газом. Документ представлен на совещании подрядчиков Министерства энергетики США по рассмотрению топливных элементов ’94, Моргантаун, Западная Вирджиния, август. Документ P11.
Престон, Г. 1992. Усовершенствованные турбины внутреннего сгорания: взгляд в прошлое. Доклад, представленный на конференции Energy Daily по усовершенствованным турбинам внутреннего сгорания, Вашингтон, округ Колумбия, 25 июня.
Рубин Е.С., М.Б. Беркенпас, Х. Фрей и Б. О’Нил. 1993. Моделирование неопределенности в выбросах опасных загрязнителей воздуха.Документ, представленный на Второй Международной конференции по управлению опасными загрязнителями воздуха, Институт исследований в области электроэнергетики, Пало-Альто, Калифорния. Июль.
Рут, Л. 1994. Котлы с низким уровнем выбросов. Документ представлен Комитету по стратегической оценке угольной программы Министерства энергетики Национальной академии наук, Вашингтон, округ Колумбия, 13 января.
Шарер Б. и Н. Хауг. 1993. Применение технологии SCR в Германии. Документ, представленный на Одиннадцатой Международной конференции по электростанциям, Association des Ingenieurs de l’Institut Montefiore, сентябрь., Льеж, Бельгия.
Coal Power for Kids – Выбор электрики
Уголь – это ископаемое топливо, например нефть и природный газ. Ископаемое топливо – это природный энергетический ресурс. Земля формирует их более ста миллионов лет из останков растений или животных.
Уголь состоит из энергии растений, выросших на болотах. Слои камней и грязи покрывали эти растения более миллиона лет. Камни и грязь создавали сильное давление и тепло. В результате все эти останки превратились в уголь.
Чтобы добраться до угля, нужно закопать землю глубоко. Добыча угля известна как добыча угля. Шахтеры – это люди, которые копают и собирают уголь. Есть два основных способа добычи угля. В их числе
Открытые горные работы
Шахтеры могут использовать экскаваторы и бульдозеры для добычи угля, если он находится на глубине менее 200 футов под землей. Они удаляют почву, а затем слои породы, чтобы обнажить или обнажить уголь. Иногда шахтерам приходится использовать динамит для снятия вершин гор.Это облегчает доступ к углю. После того, как уголь собран, территория засыпается почвой, а растения и деревья снова высаживаются. Этот метод дешевле и безопаснее подземной добычи.
Подземная добыча
Часть угля находится намного глубже под землей. Есть шахты глубиной более 1000 футов! Шахтерам приходится спускаться на лифте в шахты, а затем ловить небольшие поезда, чтобы пройти через туннели, чтобы добраться до угля.
Виды угля
Есть четыре различных типа угля.Они разные из-за того, сколько тепловой энергии они могут производить. Типы включают,
Антрацит ? Этот вид угля используется для производства металлов. Он выделяет больше всего тепла из всех углей.
Битумный ? Этот тип составляет большую часть угля, добываемого в Америке. Ему от 100 до 300 миллионов лет! Он используется для производства электроэнергии и является ключевым ингредиентом в производстве железа и стали.
Суббитуминозный ? Этот уголь создает меньше тепловой энергии, чем битуминозный, и ему около 100 миллионов лет.
Бурый уголь ? Этот вид угля производит наименьшее количество энергии. Это более молодое ископаемое топливо, чем другие. Кроме того, он шелушится и влажен, что также не помогает ему пригорать.
Уголь в США
В угле замечательно то, что его можно использовать по-разному.
Электроэнергия
Большая часть угля используется для производства электроэнергии. Это электричество помогает осветить ваш дом и запитать вашу технику! Электростанции сжигают уголь для создания пара.Затем этот пар приводит в движение специальные турбины для выработки энергии.
Тепло
Есть много предприятий, которые используют уголь для управления своими производственными процессами и заводами. Например, бумажные компании сжигают уголь для получения тепла. Другие отрасли, такие как сталелитейная промышленность, используют уголь в своей продукции.
Газ и жидкость
Другие компании перерабатывают уголь в газ или жидкость и используют его для производства других продуктов. Результат называется синтетическим топливом или синтетическим топливом. Эти виды топлива особенные. Когда они горят, они не создают столько загрязнения.
В Америке есть много мест, где можно найти уголь. Тем не менее, 5 штатов несут ответственность за значительную часть добычи полезных ископаемых в стране. Эти государства включают,
1. Вайоминг
2. Западная Вирджиния
3. Кентукки
4. Иллинойс
5. Пенсильвания
Уголь? Факты о Fast & Fun
Сегодня уголь используется по-разному по разным причинам. Дело в том, что он существует всегда! Знаете ли вы, что уголь помог выработать электричество в 19 веке? Продолжайте читать, чтобы узнать больше интересных фактов об этом древнем топливе.
- Уголь веками использовался в международной торговле. Даже Римская империя обменивала другие товары на уголь!
- Это самый дешевый источник энергетического топлива в мире. Это даже дешевле, чем нефть и природный газ.
- Более 90 000 человек в США имеют работу, связанную с углем. Эти рабочие места включают горнодобывающую промышленность, инженерию, геологию и многое другое.
- Он носит титул «Самого богатого ископаемого топлива в мире!». В земле больше угля, чем нефти и природного газа.
- Все четыре типа угля можно найти и добыть в Канаде.
Уголь и окружающая среда
В районах открытой добычи угля районы навсегда меняются. Поскольку часто используется динамит, разрушаются горы, ручьи и деревья. Чтобы предотвратить попадание в водные источники значительного ущерба или загрязнения, правительство Соединенных Штатов приняло строгие законы. Необходимо контролировать процессы добычи. Когда работа закончена, область должна быть восстановлена как можно ближе к исходному состоянию.
Сжигание угля приводит к загрязнению, наносящему вред как людям, так и окружающей среде. Со временем компании изобрели разные способы решения этой проблемы. Закон о чистом воздухе и другие государственные законы помогают осуществить эти улучшения.
Уголь? Плюсы и минусы
Есть много плюсов и минусов у использования угля для производства электроэнергии и тепла. Взгляните на оба списка ниже, чтобы увидеть эти плюсы и минусы.
ПРОФИ
- Уголь дешевле многих других ископаемых видов топлива.
- В мире много угля, и большая часть его легко добывается!
- Может преобразовываться в более чистую форму в жидкости или газе.
Минусы
- Уголь – невозобновляемый источник энергии. Это означает, что со временем он закончится.
- Поверхностные горные работы разрушают окружающую среду.
- При сжигании угля в воздух выделяются вредные вещества.
Производство электроэнергии на основе электролиза угольной суспензии с последующим использованием производимого водорода в топливных элементах
- B.А. Трошенькин
- В.Б. Трошенькин
Доклад конференции
- 1 Цитаты
- 1,9 км Загрузки
Реферат
Текущая практика горных работ позволяет извлекать чуть более половины промышленных запасов угля, тогда как другая половина остается под землей по технологическим и техническим причинам.Только от 10 до 15% добываемого на поверхности угля используется в производстве электроэнергии. Оставшаяся часть теряется с отходами добычи угля, обогащением угля и в золоотвалах в виде несгоревшего углерода. Но основная часть энергии, извлекаемой из угля, безвозвратно рассеивается в окружающую среду с продуктами сгорания и конденсации, поскольку КПД ТЭС не превышает 33-35%.
Известным решением этой проблемы является создание и использование энергетических установок с угольными топливными элементами (ТЭ) [1–3].Как правило, сначала газифицируется уголь, а затем генераторный газ подается в топливные элементы. Однако оксид углерода, который образуется при частичном окислении угля и углеводородов, представляет собой чрезвычайно нестабильное соединение, которое при определенных условиях рекомбинирует с образованием твердого углерода, то есть топливной сажи, которая закупоривает поры ТЭ и повреждает электрохимическое оборудование.
От образования сажи можно избавиться, увеличив давление газификации до 15–20 МПа, а температуру до 200–250 ° C. При этом смещение реакции взаимодействия углерода с водой на образование устойчивых к разложению водорода и диоксида углерода осуществляется электролизом угольной пульпы.Электрический ток снижает энергию активации углерода, что позволяет проводить процесс газификации при относительно низких температурах. Углекислый газ легко абсорбируется из смеси с растворами щелочей. После отделения углекислого газа чистый водород подается в топливный элемент.
Ключевые слова
Электролизные водородные топливные элементы для электролиза угольной суспензииЭто предварительный просмотр содержания подписки,
войдите в систему, чтобы проверить доступ.
Предварительный просмотр
Невозможно отобразить предварительный просмотр.Скачать превью PDF.
Список литературы
[1]
Васильев О. Склад топлива // Электропанорама. – Киев, 2000. – 3. – С. 18–20.
Google Scholar[2]
Патент США. 4226683. Класс США: 204/101; 204/129. МПК: C25B 001/02, C25B 001/00. Способ и устройство для получения водорода в абсорбирующей жидкости электрохимическим методом угля и воды / Вазин, Веспер А. (США). —№ 065210; Подана 07.10.80; Publ. 09.09.79. -14 с.
Google Scholar[3]
U.С. Пат. 4670113. Класс США: 204/80; 204/129; 204/101; 0423 / 415A. МПК: C25B 001/00. Электрохимическая активация химических реакций / Льюис, Арлин К. (США). —№ 788148; Подана 02.06.87; Publ. 16.10.85. – 12 шт.
Google Scholar
Информация об авторских правах
Авторы и аффилированные лица
- B.A. Трошенькин
- В.Б. Трошенькин
- 1.Институт проблем машиностроения Национальной академии наук Украины, Харьков, Украина,
ПРОИСХОЖДЕНИЕ Зольный остаток угля и котельный шлак – это крупные, гранулированные негорючие побочные продукты, которые собираются со дна печей, сжигающих уголь для генерации пара, выработки электроэнергии или того и другого.Большая часть этих побочных продуктов угля производится на угольных электростанциях, хотя значительное количество шлака и / или котельного шлака также производится из многих небольших промышленных или институциональных угольных котлов и на автономных предприятиях по производству энергии, работающих на угле. . Тип получаемого побочного продукта (например, зольный остаток или котельный шлак) зависит от типа печи, используемой для сжигания угля.Пепельная зола Самым распространенным типом угольных печей в электроэнергетике является сухой котел с донным измельчением угля.Когда пылевидный уголь сжигается в сухом нижнем котле, около 80 процентов несгоревшего материала или золы уносится с дымовыми газами, улавливается и восстанавливается в виде летучей золы. Остальные 20 процентов золы – это сухой зольный остаток, темно-серый, гранулированный, пористый материал с преимущественно размером песка минус 12,7 мм (½ дюйма), который собирается в заполненном водой бункере на дне печи. (1) Когда в бункер падает достаточное количество зольного остатка, он удаляется с помощью водяных струй под высоким давлением и транспортируется по водоотводным каналам в пруд-отстойник или в отстойник для обезвоживания, дробления и складирования для утилизация или использование. (2) В 1996 году в коммунальном хозяйстве было произведено 14,5 миллионов метрических тонн (16,1 миллиона тонн) шлаков. (3) Котельный шлак Есть два типа котлов с мокрым днищем: шлаковый котел и циклонный котел. В котле с отводом используется угольная пыль, а в циклонном котле – измельченный уголь. В каждом типе зольный остаток хранится в расплавленном состоянии и выпускается в виде жидкости. Оба типа котлов имеют прочное основание с отверстием, которое можно открыть, чтобы расплавленная зола, скопившаяся у основания, могла стекать в зольный бункер, расположенный ниже.Зольный бункер в печах с мокрым подом содержит воду для закалки. Когда расплавленный шлак вступает в контакт с охлаждающей водой, он мгновенно разрушается, кристаллизуется и образует гранулы. Образующийся котельный шлак, часто называемый «черной красавицей», представляет собой крупный, твердый, черный, угловатый, стекловидный материал. При сжигании пылевидного угля в печи с отводом шлака до 50 процентов золы остается в печи в виде котельного шлака. В циклонной печи, в которой сжигается измельченный уголь, от 70 до 80 процентов золы остается в виде котельного шлака, и только 20-30 процентов покидают печь в виде летучей золы. (1) Котельный шлак с мокрым подом – это термин, который описывает расплавленное состояние золы, когда она забирается из нижней части шлакоудаления или циклонной печи. Через определенные промежутки времени струи воды под высоким давлением вымывают котельный шлак из бункера в шлюз, который затем направляет его в сборный бассейн для обезвоживания, возможного дробления или просеивания, а также утилизации или повторного использования. (4) В 1995 году коммунальные услуги в Соединенных Штатах произвели 2,3 миллиона метрических тонн (2.6 млн т) котельного шлака. (1) Общая диаграмма, изображающая производственные и технологические операции, связанные с обращением с зольным остатком и котельным шлаком, представлена на Рисунке 4-1. Рисунок 4-1. Производство и переработка золы или котельного шлака. Дополнительную информацию об использовании зольного остатка и / или котельного шлака можно получить по телефону: Американская ассоциация угольной золы (ACAA) 2760 Эйзенхауэр-авеню, офис 304 Александрия, Вирджиния 22314 Научно-исследовательский институт электроэнергетики 3412 Hillview Road Пало-Альто, Калифорния 94304 ОПЦИИ ТЕКУЩЕГО УПРАВЛЕНИЯ Переработка Согласно последним статистическим данным об использовании побочных продуктов сжигания угля, 30.Было утилизировано 3 процента всего шлака и 93,3 процента всего котельного шлака, произведенного в 1996 году. Основные области применения зольного остатка – это контроль снега и льда в качестве заполнителя в кирпичных блоках из легкого бетона и сырья для производства портландцемента. Зола также использовалась в качестве заполнителя дорожного основания и основания, конструкционного заполнителя (5) , а также в качестве мелкого заполнителя при асфальтовом покрытии и текучей засыпке. Основные области применения котельного шлака – это абразивоструйная очистка, гранулы кровельной черепицы, а также борьба со снегом и льдом.Котельный шлак также использовался в качестве заполнителя при укладке асфальта, в качестве конструкционного наполнителя, (5) , а также в дорожных основаниях и основаниях. (2) Агентство по охране окружающей среды США в настоящее время проводит исследование отходов электростанций перед их утилизацией коммунальным предприятием. Возможно, что исследование EPA по смешанным отходам электростанций может оказать регулирующее влияние на полезное использование или повторное использование любых смешанных материалов. Ожидается, что это расследование будет завершено в 1998 году. Утилизация Зольный остаток и котельный шлак вывозятся на свалки или в отстойники-хранилища. При сливе в отстойники зольный остаток или котельный шлак обычно смешивают с летучей золой. Эта смешанная летучая зола и зольный остаток или котельный шлак называются зольной пылью. Примерно 30 процентов всей угольной золы перерабатывается во влажном состоянии и утилизируется в виде скопившейся золы. (3) Зола в скоплении потенциально пригодна для использования, но ее характеристики различаются из-за способа утилизации.Из-за различий в удельном весе летучей золы и зольного остатка или котельного шлака более грубый зольный остаток или частицы котельного шлака оседают первыми, а более мелкая летучая зола дольше остается во взвешенном состоянии. Зольную золу можно утилизировать и складировать, в течение этого времени ее можно обезвоживать. При благоприятных условиях сушки зола может быть обезвожена до уровня влажности, близкого к оптимальному. Чем выше процент зольного остатка или котельного шлака в накопленной золе, тем легче ее обезвоживать и тем выше ее потенциал для повторного использования.Восстановленный зола использовалась в стабилизированных смесях основания или основания и при строительстве насыпи, а также может использоваться в качестве мелкозернистого заполнителя или наполнителя в текучей засыпке. ИСТОЧНИКИ РЫНКА Хотя электроэнергетические компании производят золу на своих угольных электростанциях, большинство коммунальных предприятий не обрабатывают, не утилизируют и не продают золу, которую они производят. По большей части управление зольным остатком или котельным шлаком передается по контракту фирмам по сбыту золы или местным подрядчикам по транспортировке.В Соединенных Штатах, во всех штатах, кроме Гавайев, работает около 50 коммерческих фирм по сбыту золы. В дополнение к коммерческим организациям по сбыту золы, некоторые энергокомпании, работающие на угле, имеют собственные официальные программы сбыта золы. Большинство угольных электроэнергетических компаний в настоящее время нанимают специалиста по маркетингу золы, который отвечает за мониторинг образования, качества, использования или удаления золы, а также за взаимодействие с продавцами золы или брокерами, которые работают по контракту с коммунальными компаниями. ЭКСПЛУАТАЦИЯ НА ДОРОГАХ И ТРЕБОВАНИЯ К ОБРАБОТКЕ Асфальтобетонный заполнитель (зола и котельный шлак) И зольный остаток, и котельный шлак использовались в качестве заменителя мелкозернистого заполнителя в изнашиваемых поверхностях и базовых слоях горячего асфальта, а также в изнашиваемых поверхностях и базовых слоях из холодного эмульгированного асфальта. Из-за «попкорна», клинкероподобной низкой прочности некоторых частиц зольного остатка, зольный остаток чаще используется в базовых слоях, чем в изнашиваемых поверхностях.Котельный шлак использовался для изготовления изнашиваемых поверхностей, базовых слоев, а также для обработки поверхности асфальта или нанесения герметизирующего покрытия. Известно, что зольный остаток не используется для обработки поверхности асфальта или нанесения герметизирующего покрытия. Просеивание негабаритных частиц и смешивание с другими заполнителями обычно требуется для использования зольного остатка и котельного шлака в дорожных покрытиях. Пирит, который может присутствовать в зольном остатке, также следует удалить (с помощью электромагнитов) перед использованием. Пирит (сульфид железа) волюметрически нестабилен, расширяется и оставляет красноватое пятно при воздействии воды в течение длительного периода времени. Гранулированная основа (зола и котельный шлак) И зольный остаток, и котельный шлак иногда использовались в качестве несвязанного заполнителя или гранулированного основного материала для строительства дорожных покрытий. Зола и котельный шлак при этом считаются мелкими заполнителями. Чтобы соответствовать требуемым спецификациям, зольный остаток или шлак может потребоваться смешать с другими природными заполнителями перед их использованием в качестве основного или вспомогательного материала. Просеивание или измельчение также могут быть необходимы перед использованием, особенно для шлакового остатка, где в золе присутствуют частицы большого размера, обычно более 19 мм (3/4 дюйма). Стабилизированный основной заполнитель (зола и котельный шлак) Зольный шлак и котельный шлак использовались в качестве стабилизированной основы. Стабилизированная основа или смеси подосновы содержат смесь заполнителя и вяжущих материалов, которые связывают заполнители, обеспечивая смеси большую несущую способность. Типы цементирующих материалов, которые обычно используются, включают портландцемент, цементную пыль или пуццоланы с активаторами, такими как известь, цементная пыль и известковая пыль.При строительстве стабилизированного основания с использованием зольного остатка или котельного шлака требуется как контроль влажности, так и надлежащий размер. Также следует удалить вредные материалы, такие как пирит. Материал насыпи или засыпки (в основном, ясень) Зола и зола были использованы в качестве конструкционных наполнителей при строительстве насыпей автомагистралей и / или засыпке устоев, подпорных стен или траншей. Эти материалы также могут использоваться в качестве основы для труб вместо песка или мелкого гравия.Чтобы быть подходящими для этих применений, зольный остаток или зола должны иметь оптимальное содержание влаги или достаточно близко к нему, не содержать пирита и / или частиц, подобных «попкорну», и быть некоррозийными. Восстановленная зола должна быть складирована и должным образом обезвожена перед использованием. Зольный шлак может потребовать просеивания или измельчения для удаления или уменьшения негабаритных материалов (размером более 19 мм (3/4 дюйма). Текучий заполнитель (в основном зола) Зольный остаток использовался в качестве заполнителя в текучих смесях для заполнения.Зола в скоплении также может быть переработана и использована в качестве жидкого наполнителя. Поскольку большинство текучих смесей-заполнителей обладают сравнительно низкой прочностью на сжатие (чтобы при необходимости можно было проводить выемку грунта в более позднее время), предварительной обработки зольного остатка или накопленной золы не требуется. Ни зольный остаток, ни зольный остаток не должны иметь какое-либо конкретное содержание влаги для использования в текучих смесях наполнителя, потому что количество воды в смеси можно регулировать для обеспечения желаемой текучести. СВОЙСТВА МАТЕРИАЛА Физические свойства Зола на дне имеет угловатые частицы с очень пористой текстурой поверхности. Размер частиц донной золы варьируется от мелкого гравия до мелкого песка с очень низким процентным содержанием частиц размером с илово-глинистую. Зола обычно представляет собой хорошо сортированный материал, хотя в пробах золы, взятых с одной и той же электростанции в разное время, могут наблюдаться различия в гранулометрическом составе.Зольный остаток преимущественно имеет размер песка, обычно от 50 до 90 процентов проходит через сито 4,75 мм (№ 4), от 10 до 60 процентов проходит через сито 0,42 мм (№ 40), от 0 до 10 процентов проходит через сито 0,075 мм (№ 40). 200), а верхний размер обычно находится в диапазоне от 19 мм (3/4 дюйма) до 38,1 мм (1-1 / 2 дюйма). В Таблице 4-1 сравниваются типичные градации зольного остатка и котельного шлака. Таблица 4-1. Гранулометрический состав зольного остатка и котельного шлака. (4)
Котловые шлаки преимущественно одинарные и имеют размер от 5,0 до 0,5 мм (сито № 4 – № 40). Обычно котловые шлаки имеют гладкую текстуру поверхности, но если газы задерживаются в шлаке, когда он выпускается из печи, закаленный шлак становится несколько везикулярным или пористым.Котельный шлак от сжигания лигнита или полубитуминозного угля имеет тенденцию быть более пористым, чем шлак восточных битуминозных углей. (6) Котловой шлак представляет собой по существу крупнозернистый или средний песок, от 90 до 100 процентов проходит через сито 4,75 мм (№ 4), от 40 до 60 процентов проходит через сито 2,0 мм (№ 10), проходит 10 процентов или меньше. через сито 0,42 мм (№ 40) и 5 процентов или менее, проходящих через сито 0,075 мм (№ 200). (4) Удельный вес сухого зольного остатка зависит от химического состава, при этом более высокое содержание углерода приводит к более низкому удельному весу.Зольный остаток с низким удельным весом имеет пористую или везикулярную текстуру, характерную для частиц попкорна, которые легко разрушаются при загрузке или уплотнении. (7) В Таблице 4-2 перечислены некоторые типичные физические свойства шлаков и шлаков. Таблица 4-2. Типичные физические свойства зольного остатка и котельного шлака.
Химические свойства Зольный шлак и котельный шлак состоят в основном из кремнезема, глинозема и железа с меньшим процентным содержанием кальция, магния, сульфатов и других соединений. Состав зольного остатка или частиц котельного шлака определяется в первую очередь источником угля, а не типом топки. В Таблице 4-3 представлен химический анализ выбранных проб шлака и шлака из различных типов угля и из разных регионов. Таблица 4-3. Химический состав отобранных проб золы и котельного шлака
Зольный шлак или котельный шлак, полученный из лигнита или полубитуминозных углей, имеет более высокий процент кальция, чем зольный шлак или котельный шлак из антрацита или битуминозных углей. Хотя сульфат не показан в Таблице 4-2, он обычно очень низкий (менее 1,0 процента), если только пириты не были удалены из зольного остатка или котельного шлака. Из-за содержания соли и, в некоторых случаях, низкого pH шлака и котельного шлака эти материалы могут проявлять коррозионные свойства.При использовании зольного остатка или котельного шлака в насыпи, засыпке, подоснове или даже, возможно, в грунте, возможность коррозии металлических конструкций, которые могут контактировать с материалом, вызывает озабоченность и должна быть исследована перед использованием. Тесты индикатора коррозионной активности, обычно используемые для оценки зольного остатка или котельного шлака, включают pH, удельное электрическое сопротивление, содержание растворимых хлоридов и содержание растворимых сульфатов. Материалы считаются некоррозионными, если pH превышает 5.5, удельное электрическое сопротивление превышает 1500 Ом-сантиметров, содержание растворимого хлорида составляет менее 200 частей на миллион (ppm) или содержание растворимого сульфата составляет менее 1000 частей на миллион (ppm). (8) Механические свойства В Таблице 4-4 перечислены некоторые типичные значения характеристик уплотнения шлака и котельного шлака (максимальная плотность в сухом состоянии и оптимальная влажность), характеристик долговечности (стойкость к истиранию и натрию по Лос-Анджелесу), прочности на сдвиг и характеристик несущей способности (угол трения и) и проницаемость. Максимальные значения плотности сухого остатка золы и котельного шлака обычно на 10-25% ниже, чем у природных гранулированных материалов. Оптимальные значения влажности зольного остатка и котельного шлака выше, чем у природных гранулированных материалов, при этом оптимальное содержание влаги в зольном остатке значительно выше, чем в котельном шлаке. Котельный шлак обычно демонстрирует меньшие потери на истирание и прочность, чем шлак, из-за его стекловидной текстуры поверхности и меньшей пористости. (9) На некоторых электростанциях угольный колчедан утилизируют вместе с зольным остатком или котельным шлаком. В таких случаях некоторое количество пирита или растворимого сульфата содержится в зольном остатке или котельном шлаке, (9) , что может отражаться в более высоких значениях потери прочности сульфатом натрия. Заявленные значения угла трения находятся в том же диапазоне, что и для песка и других обычных источников мелкого заполнителя. (7) Таблица 4-4. Типичные механические свойства зольного остатка и котельного шлака.
Калифорния Значения коэффициента несущей способности сопоставимы со значениями для высококачественного гравия.Можно ожидать, что и сухой зольный остаток, и котельный шлак будут иметь коэффициенты проницаемости, которые находятся в примерно одном диапазоне. (7) Проницаемость связана с процентом мелких частиц (минус 0,075 мм или сито № 200) материала. ССЫЛКИ
|