Изготовление стали: Производство стали – технология, оборудование, этапы
alexxlab | 09.06.2023 | 0 | Разное
Производство стали – технология, оборудование, этапы
- Особенности процесса
- Необходимое оборудование
Производство стали сегодня осуществляется в основном из отработанных стальных изделий и передельного чугуна. Сталь представляет собой сплав железа и углерода, последнего в котором содержится от 0,1 до 2,14%. Превышение содержания углерода в сплаве приведет к тому, что он станет слишком хрупким. Суть процесса производства стали, в составе которой содержится гораздо меньшее количество углерода и примесей, по сравнению с чугуном, состоит в том, чтобы в процессе плавки перевести эти примеси в шлак и газы, подвергнуть их принудительному окислению.
Процесс производства стали
Особенности процесса
Производство стали, осуществляемое в сталеплавильных печах, предполагает взаимодействие железа с кислородом, в процессе которого металл окисляется. Окислению также подвергаются углерод, фосфор, кремний и марганец, содержащиеся в передельном чугуне. Окисление данных примесей происходит за счет того, что оксид железа, образующийся в расплавленной ванне металла, отдает кислород более активным примесям, тем самым окисляя их.
Производство стали предполагает прохождение трех стадий, каждая из которых имеет свое значение. Рассмотрим их подробнее.
Расплавление породы
На данном этапе расплавляется шихта и формируется ванна из расплавленного металла, в которой железо, окисляясь, окисляет примеси, содержащиеся в чугуне (фосфор, кремний, марганец). В процессе этого этапа производства из сплава необходимо удалить фосфор, что достигается за счет содержания в шлаке расплавленного оксида кальция. При соблюдении таких условий производства фосфорный ангидрид (Р2О5) создает с оксидом железа (FeO) неустойчивое соединение, которое при взаимодействии с более сильным основанием — оксидом кальция (CaO) — распадается, и фосфорный ангидрид превращается в шлак.
Чтобы производство стали сопровождалось удалением из ванны расплавленного металла фосфора, необходима не слишком высокая температура и содержание в шлаке оксида железа.
Кипение ванны расплавленного металла
Дальнейший процесс производства стали сопровождается кипением ванны расплавленного металла. Такой процесс активизируется с повышением температуры. Он сопровождается интенсивным окислением углерода, происходящим при поглощении тепла.
Процесс производства стали в электропечах
Производство стали невозможно без окисления излишков углерода, такой процесс запускают при помощи добавления в ванну расплавленного металла окалины или вдувания в нее чистого кислорода. Углерод, взаимодействуя с оксидом железа, выделяет пузырьки оксида углерода, что создает эффект кипения ванны, в процессе которого в ней снижается количество углерода, а температура стабилизируется.
На данной стадии производства из сплава также удаляется сера, присутствующая в нем в форме сульфида железа (FeS). При повышении температуры шлака сульфид железа растворяется в нем и вступает в реакцию с оксидом кальция (CaO). В результате такого взаимодействия образовывается соединение CaS, которое растворяется в шлаке, но раствориться в железе не может.
Раскисление металла
Добавление в расплавленный металл кислорода способствует не только удалению из него вредных примесей, но и увеличению содержания данного элемента в стали, что приводит к ухудшению ее качественных характеристик.
Чтобы уменьшить количество кислорода в сплаве, выплавка стали предполагает осуществление процесса раскисления, который может выполняться диффузионным и осаждающим методом.
Диффузионное раскисление предполагает введение в шлак расплавленного металла ферросилиция, ферромарганца и алюминия. Такие добавки, восстанавливая оксид железа, снижают его количество в шлаке. В результате растворенный в сплаве оксид железа переходит в шлак, распадается в нем, высвобождая железо, которое возвращается в расплав, а высвобожденные оксиды остаются в шлаке.
Производство стали с осаждающим раскислением осуществляется путем введения в расплав ферросилиция, ферромарганца и алюминия. Благодаря наличию в своем составе веществ, обладающих большим сродством к кислороду, чем железо, такие элементы образуют соединения с кислородом, который, отличаясь невысокой плотностью, выводится в шлак.
Производство стали в мартеновских печах
Регулируя уровень раскисления, можно получать кипящую сталь, которая не полностью раскислена в процессе плавки. Окончательное раскисление такой стали происходит при затвердевании слитка в изложнице, где в кристаллизующемся металле продолжается взаимодействие углерода и оксида железа. Оксид углерода, который образуется в результате такого взаимодействия, выводится из стали в виде пузырьков, также содержащих азот и водород. Полученная таким образом кипящая сталь, содержит незначительное количество металлических включений, что придает ей высокую пластичность.
Производство сталей может быть направлено на получение материалов следующего типа:
- спокойных, которые получаются, если в ковше и печи процесс раскисления полностью завершен;
- полуспокойных, которые по степени раскисления находятся между спокойными и кипящими сталями; именно такие стали раскисляются и в ковше, и в изложнице, где в них продолжается взаимодействие углерода и оксида железа.
Если производство стали предполагает введение в расплав чистых металлов или ферросплавов, то в результате получаются легированные сплавы железа с углеродом. Если в стали данной категории необходимо добавить элементы, которые имеют меньшее сродство к кислороду, чем железо (кобальт, никель, медь, молибден), то их вводят в процессе плавки, не опасаясь за то, что они окислятся.
Необходимое оборудование
Технология производства стали предполагает использование на сталелитейных заводах следующего оборудования.
Участок кислородных конверторов:
- системы обеспечения аргоном;
- сосуды конверторов и их несущие кольца;
- оборудование для фильтрации пыли;
- система для удаления конверторного газа.
Участок электропечей:
- печи индукционного типа;
- дуговые печи;
- емкости, с помощью которых выполняется загрузка;
- участок складирования металлического лома;
- преобразователи, предназначенные для обеспечения индукционного нагревания.
Участок вторичной металлургии, на котором осуществляется:
- очищение стали от серы;
- гомогенизация стали;
- электрошлаковый переплав;
- создание вакуумной среды.
Кипящая сталь
Участок для реализации ковшовой технологии:
- LF-оборудование;
- SL-оборудование.
Ковшовое хозяйство, обеспечивающее производство стали, также включает в себя:
- крышки ковшей;
- ковши литейного и разливочного типа;
- шиберные затворы.
Производство стали также предполагает наличие оборудования для непрерывной разливки стали. К такому оборудованию относится:
- поворотная станина для манипуляций с разливочными ковшами;
- оборудование для осуществления непрерывной разливки;
- вагонетки, на которых транспортируются промежуточные ковши;
- лотки и сосуды, предназначенные для аварийных ситуаций;
- промежуточные ковши и площадки для складирования;
- пробочный механизм;
- мобильные мешалки для чугуна;
- оборудование для обеспечения охлаждения;
- участки, на которых выполняется непрерывная разливка;
- внутренние транспортные средства рельсового типа.
Производство стали и изготовление из нее изделий представляет собой сложный процесс, сочетающий в себе химические и технологические принципы, целый перечень специализированных операций, которые используются для получения качественного металла и различных изделий из него.
Производство стали | Металлургический портал MetalSpace.ru
Производство стали
- Образование и карьера
- Интерактивный учебник
Online учебник
На основе современных представлений рассмотрены основные металлургические производства
АНАЛИТИКА
Научные статьи и методические материалы о природных и вторичных ресурсах металлов, а также металлургических технологиях
Производство и наука
- Эколого-экономическая эффективность реновации технических изделий июль 22, 2019
- Сжиженный природный газ март 19, 2018
- Ветроэнергетика в России, развитие технологии в ветроэнергетике янв 23, 2018
Методические материалы
- Модернизация барабанных летучих ножниц – Дипломный проект дек 03, 2020
- Схема рециклинга автомобильных катализаторов, содержащих металлы платиновой группы авг 15, 2018
- Историко-реконструкторское движение в России фев 04, 2017
Интерактивный учебник
- Как правильно согнуть металлический квадрат апр 01, 2020
- Сталь с полимерным покрытием янв 04, 2019
- Топливо из ТБО дек 17, 2018
Потенциал Забайкальского .
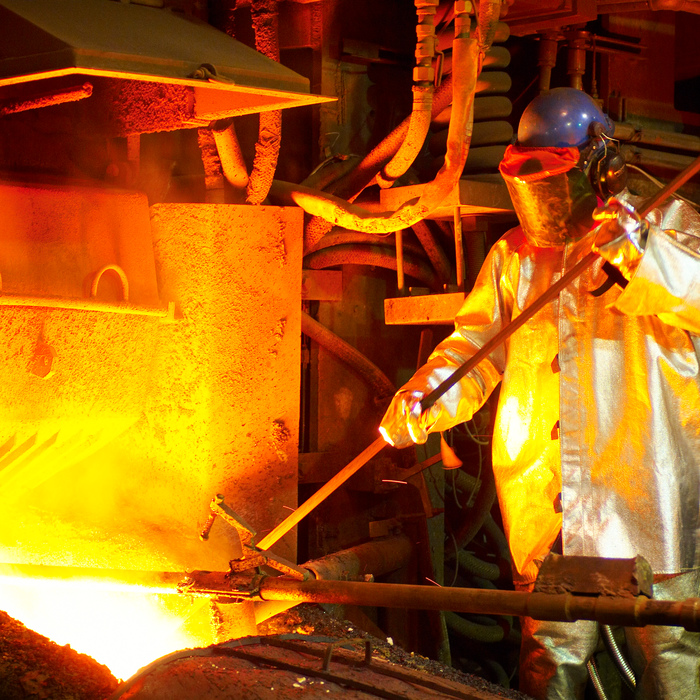
Обработка металлов …
Пластическая деформация …
Металлургические технологии …
Основоположники отечественной …
Основоположники отечественной …
Русская средневековая .
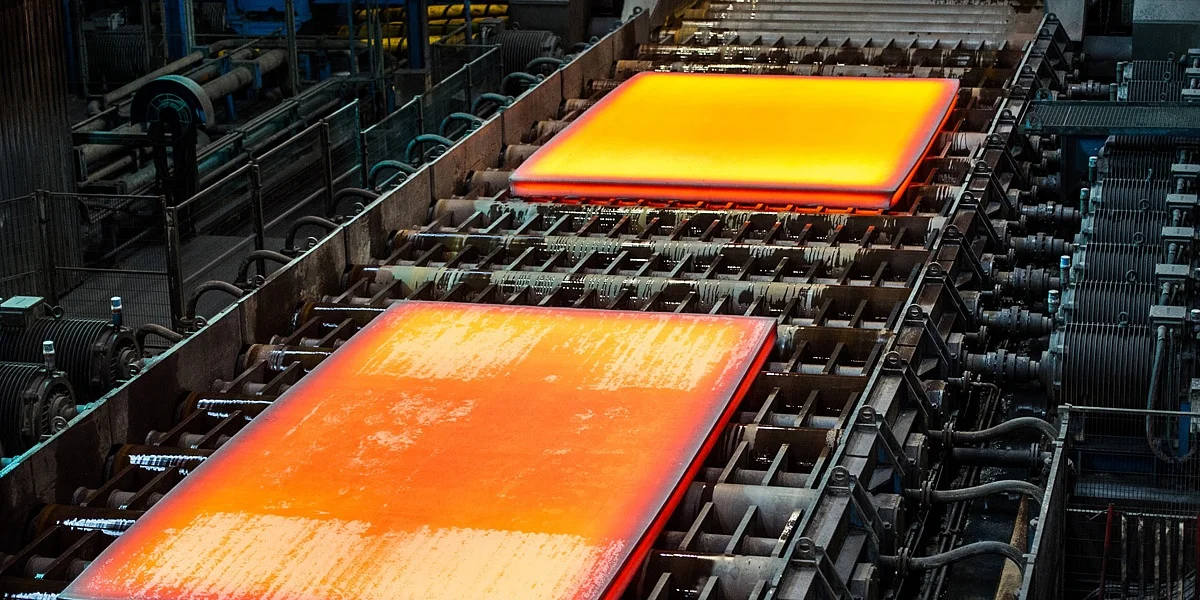
Русская средневековая …
ИНТЕРАКТИВ
Интерактивная картина мира металлов на ключевых этапах истории цивилизации
Энциклопедия «Металлургия и время»
- «Дредноуты» и «крупповские пушки» март 10, 2014
- Преимущества получения ферромарганца в электропечах март 09, 2014
- Проблемы производства доменных ферросплавов март 08, 2014
Металлургические объекты
- Музей истории МИСиС.
Металлургия – кузница победы апр 20, 2020
- Доменная печь Лиенсхютте (Lienshytte blast-furnace) авг 28, 2014
- Железоделательный завод Энгельсберг (Engelsbergs bruk) авг 27, 2014
Обучающие игры
- Маша и компания – Таланты дек 07, 2014
- Маша и компания – Игры на природе дек 06, 2014
- Легенды огня и металла Часть 3.
Мушкет июнь 19, 2014
Copyright © 2011 – 2022 MetalSpace
Обещание углеродно-нейтральной стали
На производство стали приходится около семи процентов выбросов парниковых газов человечеством. У этого поразительного факта есть две причины. Во-первых, сталь производится с использованием металлургических методов, знакомых нашим предкам железного века; во-вторых, он является частью практически всего, включая здания, мосты, холодильники, самолеты, поезда и автомобили. По некоторым оценкам, мировой спрос на сталь почти удвоится к 2050 году. Поэтому «зеленая» сталь крайне необходима, если мы хотим противостоять изменению климата.
Чтобы понять сталь, нужно мыслить на уровне школьной химии — хватит даже той химии, которую вы выучили в первый день. По сути, сталь — это железо с добавлением небольшого количества углерода для повышения прочности: крошечные атомы углерода располагаются между более крупными атомами железа, делая сталь более плотной и пластичной. В некотором смысле железо найти не так уж и сложно — оно составляет пять процентов земной коры по весу, — но металлы в горных породах смешаны с другими элементами. Вы должны получить их в чистом виде, прежде чем сможете построить этот меч или Эйфелеву башню. В этом отношении железо представляет особую проблему: атомы железа прочно связаны с атомами кислорода, как дополнительные части головоломки. Два железа и три кислорода образуют оксид железа, или Fe 9.0005 2 O 3 — цельная картина, которую трудно разобрать. Оксид железа образуется легко — настолько легко, что в присутствии воды голое железо будет прилипать к кислороду воздуха, вызывая ржавчину.
Таким образом, на протяжении большей части истории человечества проблема извлечения железа была неразрешимой. Пять тысяч лет назад древние египтяне делали бусы из железа, но металл они получали из метеоритов, в которых он уже был отделен от кислорода каким-то неизвестным внеземным процессом. Пройдет еще тысяча лет, прежде чем станет возможным производство пригодного для использования железа посредством процесса, называемого восстановлением. Где-то около 2000 г. до н. э. было обнаружено, возможно, случайно, что тяжелая железная порода или руда становилась ковкой, когда ее нагревали на углях. Сегодня мы можем объяснить, почему это происходит: при достаточно высоких температурах атомы железа ослабляют свою хватку на атомах кислорода. Кислород связывается с углеродом в древесном угле, образуя CO 2 , который улетает в воздух. Остается очищенное или «восстановленное» железо. Процесс сокращения позволил начаться железному веку.
Трудно точно сказать, когда впервые была изготовлена сталь. Время от времени он возникал, когда углерод диффундировал из древесного угля в железо, укрепляя его. Но производство стали было трудно контролировать до тех пор, пока несколько сотен лет назад не была изобретена доменная печь. С помощью мехов сталелитейщики увеличили температуру угольных топок почти до трех тысяч градусов — достаточно, чтобы расплавить железо в больших количествах. Сегодня доменные печи по-прежнему являются основным методом восстановления стали. Нынешние модели имеют высоту около ста футов и могут производить десять тысяч тонн железа в день. Вместо древесного угля они используют кокс, переработанную форму угля. Кокс и руда идут в верхнюю часть печи, а снизу выходит расплавленное железо, пропитанное углеродом; это железо можно легко переработать в сталь. Сталелитейная промышленность производит около двух миллиардов тонн его каждый год на рынке в 2,5 триллиона долларов, при этом выбрасывая более трех миллиардов тонн CO 2 ежегодно, в основном из доменных печей.
К счастью, с тех пор мы узнали, что существует несколько способов очистки железа. Вместо того чтобы использовать углерод для удаления кислорода из руды, создавая CO 2 , мы можем использовать водород, создавая H 2 O, то есть воду. Многие компании работают над этим подходом; этим летом шведское предприятие использовало его для производства стали на экспериментальном заводе. Если бы этот метод широко применялся, он мог бы сократить выбросы сталелитейной промышленности на девяносто процентов, а наши глобальные выбросы — почти на шесть процентов. Это большой шаг к спасению мира.
В рамках шведского проекта под названием HYBRIT — Прорывная технология производства водородного чугуна — был построен экспериментальный завод в Лулео, в северной части Швеции. « HYBRIT » написано гладким шрифтом без засечек по бокам объекта; высокая сборка серых коробок напоминает ангар космического корабля или музей современного искусства — чистое будущее, а не суровое прошлое. Проект является результатом сотрудничества между Vattenfall, шведской государственной электроэнергетической компанией; L.K.A.B., государственная компания по добыче железной руды; и S.S.A.B., частная сталелитейная корпорация. Когда завод открылся в августе прошлого года, премьер-министр Швеции выступил с речью, назвав это «исторической возможностью». я спросил HYBRIT на видеотур, а его представители отказались, сославшись на необходимость защиты фирменной технологии. Но, хотя то, что происходит внутри, является чем-то вроде секрета, то, что вышло этим летом, было очевидно: «зеленое» железо, которое впервые было превращено в сталь и доставлено заказчику.
Как правило, сталь получается в результате нескольких стадий производства. Чаще всего железную руду измельчают и окатывают. Тем временем уголь перерабатывается в кокс. Руда, кокс и известняк отправляются в доменную печь, создавая раскаленное жидкое железо вместе с побочным продуктом, называемым шлаком, и огромным количеством CO 9 .0005 2 . Очищенное железо затем нагревают второй раз, без кокса, в так называемой «основной кислородной» печи. На этом этапе поверхность расплавленного чугуна обдувают кислородом, чтобы стимулировать образование CO и CO 2 . Это снижает содержание углерода в железе примерно с четырех процентов до менее одного процента. В этот момент он становится стальным. «Это немного похоже на большой кулинарный рецепт», — сказал мне Валентин Фогль, аспирант, который пишет диссертацию по обезуглероживанию сталелитейной промышленности в Лундском университете в Швеции. «Есть люди, работающие на сталелитейных заводах, чья жизнь связана с наблюдением за доменной печью, и они понимают доменную печь на интуитивном уровне». Готовый продукт отливается в пластины и прессуется в листы, затем прокатывается и отгружается.
HYBRIT использует другую, более экологичную стратегию, которой придерживаются и некоторые другие предприятия. В его системе железорудные окатыши попадают в верхнюю часть так называемой шахтной печи, размер которой примерно равен размеру доменной печи. Вместо кокса внизу идет газообразный водород. Внутри происходит процесс, известный как «прямое восстановление». Температура в печи достигает полутора сотен градусов, чего недостаточно, чтобы расплавить железо; в результате получаемое «прямовосстановленное железо» остается твердым. Он почти не содержит углерода, поэтому его отправляют в электродуговую печь — сосуд, в котором разряды электричества проходят между внутренними электродами. Там он плавится вместе с небольшим количеством угля, производя сталь (и небольшое количество CO 2 ). Метод старой школы выделяет уйму углерода на каждом этапе; новый процесс излучает как можно меньше. Пилотная установка HYBRIT в настоящее время производит около тонны стали в час. Следующим шагом является строительство промышленного демонстрационного завода в Елливаре, также на севере, который к 2026 году будет производить 1,3 миллиона тонн стали в год. годы. Мартин Пей, главный технический директор сталелитейной компании S.S.A.B., сказал мне, что для масштабирования процесса не существует серьезных научных препятствий. Вместо этого в основном речь шла об оптимизации условий эксплуатации: например, инженерам нужно было экспериментировать с оборудованием, которое нагревает водород перед его закачкой. Настоящим препятствием, по словам Пей, является подача водорода.
Чистый водород получают в основном из природного газа, обычно из метана, но для получения водорода из метана требуется энергия, а также образуется угарный газ, который производит CO 2 при сжигании. Существует зеленый источник водорода: вода. Воду можно разделить на водород и кислород, пропуская через нее ток, в процессе, называемом электролизом. Но электролиз, в свою очередь, экологически чистый только в том случае, если задействованные электроны также поступают из возобновляемых источников энергии.
Пилотная установка HYBRIT небольшая, и у них нет проблем с получением зеленого водорода. Но, по словам его инженеров, для создания посредством электролиза достаточного количества зеленого водорода для производства тонны стали требуется около двадцати шестисот киловатт-часов электроэнергии — этого достаточно для питания среднего американского дома в течение трех месяцев. HYBRIT также планирует использовать экологически чистое электричество для подготовки руды, электродуговой печи и стальных валков, что в сумме составит тридцать пятьсот киловатт-часов на тонну стали. Умножьте это на почти два миллиарда тонн стали, которые мы сейчас производим в год, и вы получите почти семь тысяч тераватт-часов электроэнергии. Чтобы удовлетворить этот спрос, не производя CO 2 , нам потребуется почти удвоить годовой мировой объем производства ядерной и возобновляемой электроэнергии. Это означало бы строительство примерно сотни копий крупнейшего существующего ядерного объекта человечества, атомной электростанции Касивадзаки-Карива, в Японии. Так что проблема с питанием. Нам также пришлось бы заменить наши существующие металлургические и сталелитейные заводы и построить массивные электролизные заводы. Даже в этом случае, поскольку добыча полезных ископаемых и транспорт, вероятно, по-прежнему будут выделять CO 2 , производство не будет полностью экологичным.
Тем не менее капитальный ремонт должен где-то начинаться — в данном случае в Швеции. Страна планирует стать первой страной, достигшей нулевых чистых выбросов к 2045 году. Она надеется, что другие страны последуют этому примеру; Китай, который поставляет большую часть стали в мире, также стремится сократить свои выбросы. Пей сказал мне, что, по его мнению, сырая сталь будет стоить на двадцать-тридцать процентов дороже, чем традиционная сталь, по крайней мере, поначалу. Но по мере того, как процессы электролиза и экологически чистые источники энергии становятся более эффективными, стоимость может снизиться. Между тем, субсидии, налоги, тарифы и другие меры государственного вмешательства могут сделать сырую сталь конкурентоспособной. Если подешевеет, то возьмет верх.
Сырое железо HYBRIT после превращения в сталь было прокатано компанией S.S.A.B. Первая партия зеленой стали этой компании была отправлена Volvo, и в этом месяце S.S.A.B. также объявила о партнерстве с Mercedes-Benz. Гёкче Мете, возглавляющий группу перехода отрасли в Стокгольмском институте окружающей среды, сказал мне, что автомобили, изготовленные из экологически чистой стали, будут стоить примерно на триста евро дороже. (Стиральные машины, еще один потенциальный продукт, будут стоить примерно на двадцать евро больше. ) Она считает, что многие покупатели с радостью заплатят наценку. «Зеленая сталь очень популярна в Швеции, — сказал Мете. «Можно услышать, как молодые люди, даже хипстеры, говорят об этом в кафе со своими покебоулами. Зеленая сталь становится действительно горячей темой в повседневной жизни». Она приписывает энтузиазм сочетанию освещения в СМИ, широкой страсти к климату и индустриальной экономике Швеции: по оценкам, каждый десятый швед работает в сфере передового производства.
Сванте Аксельссон, национальный координатор правительственной инициативы «Свободная от ископаемых в Швеции», призван помочь правительству и промышленности договориться о том, как преобразовать экономику. «С нами все партии, все профсоюзы, а также люди на улицах, потому что они работают в этих компаниях», — сказал он мне. «В каком-то смысле мы перешли от проблемы климата к вопросу о том, как мы можем создавать рабочие места в будущем?» Аксельссон сказал, что «новая роль государства» заключалась в «снижении рисков, если мы хотим действовать в условиях открытой экономики». Среди прочего, это включает в себя попытки сделать так, чтобы государственные закупки, банковские инвестиции, выдача разрешений, обучение работников и регулирование работали гармонично, вокруг общих целей. «Я изменил свой язык с «танго до двух» на «кадриль», — сказал он. «Потому что нам нужно так много участников, чтобы делать правильные шаги в правильном направлении».
Нержавеющая сталь может быть не крутой в Америке, но аналогичная и потенциально более значимая программа существует в США. Хотя прямое восстановление железа чистым водородом является новым, прямое восстановление с помощью природного газа — нет. Midrex, сталелитейная компания, базирующаяся в Северной Каролине, впервые применила последний метод и построила свой первый экспериментальный завод в 1967 году. Сегодня компания имеет десятки заводов, работающих по этому принципу, по всему миру, производя больше железа прямого восстановления, чем ее конкуренты вместе взятые. . Midrex превращает природный газ в монооксид углерода и водород, которые вместе восстанавливают железо в шахтной печи; по сравнению с доменной печью, использующей кокс, это дает от трети до половины меньше углекислого газа.
Midrex, как и HYBRIT , стремится полностью перейти на водород. В Гамбурге, Германия, к 2025 году планируется построить демонстрационный промышленный завод для ArcelorMittal, второго по величине производителя стали в мире; завод сможет использовать либо водород и монооксид углерода, либо чистый водород, и правительство Германии покроет половину его стоимости в сто десять миллионов евро. Переключение между двумя методами сопряжено с некоторыми инженерными проблемами. «Не так уж очевидно, что вы просто меняете шланг и впрыскиваете водород», — сказал Лутц Бандуш, исполнительный директор ArcelorMittal, управляющий заводом в Гамбурге и шестью другими в Европе. Когда вы используете природный газ для восстановления железа, на поверхности железных окатышей образуется полезная оболочка из углерода; это защищает гранулы от ржавчины и возгорания. Без такого слоя компании придется изменить способ плавки, хранения и обращения с железом. Фабрис Патиссон, инженер Школы горного дела Нанси во Франции, изучал железо прямого восстановления на основе водорода в лаборатории и построил компьютерное моделирование полномасштабных печей Midrex; он не видит препятствий, а только вопросы — об оптимальной форме печи или лучшем месте для добавления водорода, — на которые нужно найти ответ.
Паттисон подозревает, что сталелитейщиков будет труднее спроектировать. «Главная трудность, по крайней мере, в Европе, заключается в том, что они уже столетие полагаются на доменную печь, и им совсем не нравится идея отказаться от нее», — сказал он мне. Сопротивление, по его словам, «конечно, экономическое, потому что оно означает создание новых вещей. А также психологические, для практиков сталелитейного производства. Доменные печи достаточно оптимизированы». Бандуш, менеджер ArcelorMittal, согласился. «Мы потратили уже двести лет на оптимизацию доменной печи, — сказал он. «Но у нас нет еще двухсот лет, чтобы преобразовать сталелитейную промышленность. Все это нам предстоит сделать за десять-двадцать лет. И многие коллеги, которых я знаю, очень напуганы». Тем не менее, Midrex надеется отработать все это на своем демонстрационном заводе, а затем преобразовать остальное. Существует соревновательный дух, оживляющий усилия. Ссылаясь на Сделка HYBRIT с Mercedes-Benz, Бандуш сказал: «Создается впечатление, что они производят тысячи автомобилей из этой стали. На самом деле, если вы посмотрите на объем, это почти ничего». Он утверждает, что масштаб и опыт Midrex и ArcelorMittal дают им огромное конкурентное преимущество, когда речь идет о сырой стали.
Производство стали – SteelConstruction.info
Человечество веками производило железо и сталь. Сталь подпитывала промышленную революцию и остается основой современной промышленно развитой экономики. Трудно представить мир без стали — будь то строительство, транспортные средства, двигатели или машины, сталь всегда присутствует во всем, что мы делаем и все, что мы делаем.
Универсальность стали с точки зрения ее состава и свойств, ее отношения прочности к весу и ее способности многократно перерабатываться в новые продукты отличает сталь от других материалов и играет важную роль в ее постоянном успехе. В этой статье кратко объясняется, как производятся железо и сталь. В отдельных статьях обсуждается, как материал превращается в стальные строительные изделия, и основные свойства стали, которые используются при проектировании.
Содержание
- 1 История производства стали
- 2 Современное производство чугуна
- 3 Преобразование в сталь
- 3.1 Производство стали в кислородном кислороде
- 3.2 Электродуговая печь
- 3.3 Вторичное производство стали
- 4 Побочные продукты производства чугуна и стали
- 5 Литье стальное
- 5.1 Непрерывное литье
- 6 ресурсов
- 7 Дальнейшее чтение
- 8 См. также
[наверх]История сталеплавильного производства
Еще 6000 лет назад ранние цивилизации использовали железную руду, найденную в метеоритах, для изготовления примитивных инструментов. Первые железные печи появились около 1400 г. до н.э. Это были очень простые округлые очаги, в которых железная руда и древесный уголь нагревались до очень высоких температур. При повторном нагреве металлурги могли ковать металл, удаляя примеси и повышая твердость. Было осознано, что, нагревая высококачественное железо и добавляя несколько других металлических элементов, можно получить еще более прочный материал.
Небольшое количество необработанной стали впервые было произведено в Восточной Африке и Индии еще в 300 г. до н.э. Европейцы и китайцы разработали процессы производства стали на несколько сотен лет позже. Промышленная революция оказала большое влияние на спрос на сталь для машин, железных дорог и других амбициозных промышленных проектов, и в 1855 году Генри Бессемер получил патент на свой процесс придания чугуну ковкости путем введения воздуха в жидкий металл для удаления углерода. .
История бессемеровского сталеплавильного производства — классический пример военного импульса для технологического развития. Во время Крымской войны Бессемер изобрел артиллерийский снаряд нового типа. Генералы сообщили, что чугунные пушки того времени были недостаточно сильны, чтобы противостоять силам более мощного снаряда, поэтому Бессемер разработал свой усовершенствованный процесс плавки железа, который производил большое количество стали высшего качества. Современная сталь по-прежнему производится по технологии, основанной на бессемеровском процессе.
[top]Современное производство чугуна
Железо производится в доменной печи. Во-первых, железная руда смешивается с коксом и нагревается с образованием богатого железом клинкера, называемого «агломератом». Агломерация является важной частью общего процесса, поскольку она снижает количество отходов и обеспечивает эффективное сырье для производства чугуна.
Кокс производится из тщательно отобранных сортов угля. Различные сорта угля складируются отдельно и смешиваются перед отправкой в коксовые печи. Уголь нагревается или «обугливается» в печах до тех пор, пока не станет коксом. Затем его вынимают из печи, охлаждают и сортируют перед использованием в доменной печи. Угольный газ, образующийся при карбонизации, собирается и используется в качестве топлива в производственном процессе, а побочные продукты, такие как смола, бензол и сера, извлекаются для дальнейшей очистки.
Аглофабрика
Коксовые печи
Кокс, руда и агломерат подаются или «загружаются» в верхнюю часть доменной печи вместе с известняком. Поток горячего воздуха, от которого печь получила свое название, подается через сопла, называемые «фурмами», в основании печи. Дутьевой воздух может быть обогащен кислородом, а иногда также впрыскивается уголь или нефть для обеспечения дополнительного тепла и снижения потребности в коксе. Дутье нагревает печь до белого каления, а железо в руде и агломерате выплавляется, образуя ванну расплавленного металла на дне или поде печи. Известняк соединяется с примесями и расплавленной породой из железной руды и агломерата, образуя жидкий «шлак», который, будучи легче металла, плавает поверх него.
- Доменная печь
Система загрузки в верхней части печи также действует как клапанный механизм для предотвращения утечки газа, который отводится по трубам большого диаметра на газоочистку. Важной особенностью производства чугуна является то, что процесс является непрерывным. Когда в горне доменной печи накапливается достаточное количество расплавленного чугуна, его сливают в ковши для выплавки стали. По мере того, как шлак накапливается на поверхности расплавленного металла, его также через равные промежутки времени выпускают через отдельную «выемку» или летку. Тем временем сырье продолжает загружаться в верхнюю часть печи, а нагретый воздух подается снизу. Этот процесс продолжается на протяжении всей «жизни» печи, которая может составлять 10 и более лет, прежде чем футеровка из жаропрочного кирпича начнет разрушаться. Затем печь перефутеровывают.
Рафинирование железной руды для доменной печи
Изготовление железа
[наверх]Переработка в сталь
Основным сырьем для производства стали является чугун из доменной печи, стальной лом или их смесь. Пропорции используемого материала варьируются в зависимости от процесса и типа требуемой стали. Сталь можно описать в общих чертах как железо, из которого удалена большая часть углерода, что делает его более прочным и пластичным. Существует множество форм (марок) стали, каждая из которых имеет свой специфический химический состав и свойства для удовлетворения потребностей множества различных применений. Сегодня в Великобритании используются два основных процесса производства стали.
[вверх]Сварка стали с кислородом
Горячий металл из доменной печи и стальной лом являются основными материалами, используемыми в производстве стали с кислородом. Современные печи или «конвертеры» вмещают до 350 тонн шихты и превращают ее в сталь примерно за 15 минут. Водоохлаждаемая кислородная фурма опускается в конвертер, и на металл под очень высоким давлением подается кислород высокой чистоты. Кислород соединяется с углеродом и другими нежелательными элементами, удаляя их из расплавленной шихты. Эти реакции окисления производят тепло, а температура металла регулируется количеством добавляемого лома.
Основные этапы процесса BOS
Углерод выходит из конвертера в виде газа, монооксида углерода, который после очистки может быть собран для повторного использования в качестве топлива. Во время «продувки» известь добавляется в качестве флюса, чтобы помочь удалить другие окисленные примеси в виде плавающего слоя шлака. Количество лома, чугуна, извести и других флюсов рассчитывается для обеспечения правильной температуры и состава стали. На многих заводах процессу рафинирования способствует подача газов, в том числе аргона, азота и углекислого газа, через основание печи. После рафинирования стали и отбора проб для проверки температуры и состава конвертер наклоняют и сталь сливают в ковш. Обычно содержание углерода в стали в конце рафинирования составляет около 0,04%. Во время выпуска могут быть сделаны добавки в сплав, чтобы скорректировать окончательный состав стали.
Когда вся сталь выпущена, конвертер переворачивается вверх дном, а остаточный шлак высыпается в ожидающий шлаковый ковш для удаления в пруд-охладитель шлака, откуда он подвергается дальнейшей обработке для извлечения любого материала, который может быть возвращен в процесс.
Процесс BOS
[вверх]Дуговая электропечь
Электродуговая печь (ЭДП)
В электродуговой печи (ЭДП) используется только холодный металлолом. Первоначально этот процесс использовался исключительно для производства высококачественной стали, например, для станков и пружинной стали, поскольку он давал более точный контроль над составом. Однако сегодня он также используется для производства более широко используемых сталей, в том числе легированных и нержавеющих, а также некоторых специальных углеродистых и низколегированных сталей. Современные электродуговые печи могут производить до 150 тонн стали за одну плавку.
Электродуговая печь состоит из круглой ванны с подвижной крышей, через которую можно поднимать или опускать три графитовых электрода. В начале процесса электроды извлекаются, и крыша раскачивается. Затем стальной лом загружают в печь из большой стальной корзины, спускаемой с мостового крана. Когда загрузка завершена, свод откидывается в исходное положение, а электроды опускаются в печь. Через шихту пропускают мощный электрический ток, создается дуга, а выделяющееся тепло расплавляет лом. В качестве флюсов добавляют известь и плавиковый шпат, а в расплав вдувают кислород. В результате примеси в металле объединяются, образуя жидкий шлак.
Электродуговая печь (ЭДП)
Образцы стали берутся и анализируются для проверки их состава, и, когда правильный состав и температура достигнуты, печь быстро выпускается в ковш. Окончательные корректировки в соответствии с точной спецификацией заказчика могут быть выполнены путем добавления сплавов во время выпуска или, впоследствии, на вторичном сталеплавильном агрегате.
(Поскольку сталь ЭДП изготавливается из 100% лома, возникает искушение указать это вместо стали BOS в благонамеренных усилиях по снижению воздействия на окружающую среду. Металлургическая промышленность не одобряет это, и причины объясняются в Ресурсах. раздел).
Основные этапы процесса ЭДП
[вверх]Вторичное производство стали
После выпуска расплавленного металла в ковш из печи BOS или ЭДП его часто подвергают одной или нескольким дополнительным обработкам в зависимости от марки стали. требуется сталь. Эти дополнительные этапы рафинирования в совокупности известны как вторичное производство стали и могут включать перемешивание в ковше с аргоном, вдувание порошка или проволоки, вакуумную дегазацию и дуговой нагрев ковша. Некоторые высококачественные стали сочетают в себе все эти виды обработки. Эти процессы улучшают гомогенизацию температуры и состава, обеспечивают тщательную подгонку до точного состава, удаляют вредные и нежелательные газы, такие как водород, и снижают содержание таких элементов, как сера, до очень низкого уровня.
Вторичное производство стали
[top]Побочные продукты производства железа и стали
Как и во всех крупномасштабных производственных процессах, при производстве железа и стали образуются побочные продукты. В среднем производство 1 тонны стали приводит к образованию от 200 кг (ЭДП) до 400 кг (ДП/КК) побочных продуктов.
Основными побочными продуктами производства чугуна и стали являются шлаки (90%), пыль и шламы. Средняя мировая степень извлечения шлака колеблется от более чем 80% для сталеплавильного шлака до почти 100% для чугунолитейного шлака.
Существует три основных типа продаваемых доменных или доменных шлаков, классифицируемых по способу охлаждения: воздушное охлаждение, гранулирование и гранулирование (или вспучивание).
Шлак воздушного охлаждения твердый и плотный и особенно подходит для использования в качестве строительного заполнителя. Он также используется в товарном бетоне, бетонных изделиях, асфальтобетоне, дорожных основаниях и покрытиях, наполнителях, клинкерном сырье, железнодорожном балласте, кровельных работах, минеральной вате (для использования в качестве изоляции) и кондиционере почвы.
Гранулированный шлак образует частицы стекла размером с песок и в основном используется для изготовления вяжущих материалов. Бетоны, содержащие гранулированный шлак, как правило, набирают прочность медленнее, чем бетоны, содержащие только портландцемент – наиболее распространенный тип цемента, – но могут иметь лучшую долговременную прочность, выделять меньше тепла во время гидратации, иметь меньшую проницаемость и, как правило, демонстрируют лучшую устойчивость к химическому воздействию. атака.
Гранулированный или расширенный шлак имеет пузырчатую текстуру (как вулканическая порода) и чаще всего используется в качестве легкого заполнителя. В случае мелкого помола он также обладает цементирующими свойствами.
Сталеплавильный шлак (конвертерный и электродуговый) охлаждается аналогично доменному шлаку с воздушным охлаждением и используется для большинства тех же целей. Поскольку производственный процесс на этом этапе варьируется в зависимости от типа производимой стали, получаемые шлаки также имеют различные химические свойства, что делает их более сложными в использовании, чем шлаки для производства чугуна. Некоторая часть восстановленного шлака используется внутри сталеплавильных печей или агломерационных заводов, в то время как примерно 50% извлеченного шлака используется снаружи в строительстве, в первую очередь при строительстве дорог.
Газы от производства железа и стали после очистки почти полностью повторно используются внутри предприятия. Коксовый газ содержит около 55% водорода и в будущем может стать важным источником водорода. Он полностью повторно используется на сталеплавильном заводе и может обеспечивать до 40% мощности завода.
Пыль и шлам собираются в очистном оборудовании (фильтрах), присоединенном к процессам производства чугуна и стали.
Шлам образуется из пыли или мелочи в различных сталеплавильных и прокатных процессах и имеет высокое содержание влаги.
Пыль и шлам, удаляемые из газов, состоят в основном из железа и в основном могут снова использоваться в сталеплавильном производстве. Оксиды железа, которые не могут быть переработаны внутри компании, могут быть проданы другим отраслям промышленности для различных применений, от портландцемента до сердечников электродвигателей.
[top]Стальное литье
Прежде чем расплавленную сталь можно будет прокатать или сформировать в готовые изделия, она должна затвердеть и превратиться в стандартные литейные полуфабрикаты, которые доступны в основных формах, называемых заготовками, блюмами или плитами. До разработки процесса непрерывного литья эти формы всегда производились путем «разливки» (разливки) расплавленной стали в изложницы. Слитки помещают в ямы для выдержки (печи для повторного нагрева слитков), чтобы довести их до однородной температуры, прежде чем они поступают на первичные станы, которые затем начинают прокатывать их в требуемые формы. Однако большинство современных сталей в настоящее время разливают непрерывно.
Для литья прядей разного поперечного сечения используются разные принципы проектирования. Заготовочные машины затвердевают квадраты или круги размером от 80 до 175 мм, блюмовые разливочные машины затвердевают секции 300 на 400 мм, а балочные заготовочные машины производят большие, похожие на собачьи кости секции, которые непосредственно подаются в прокатный стан двутавровой или двутавровой балки. Огромные слябовые МНЛЗ затвердевают на производстве секции толщиной до 250 мм и шириной 2600 мм.
[вверх]Непрерывное литье
Процесс непрерывного литья заготовок
В процессе непрерывной разливки расплавленный металл заливают непосредственно в разливочную машину для производства заготовок, блюмов или слябов. Непрерывная разливка устраняет необходимость в первичных и промежуточных прокатных станах, ямах для выдержки, а также в хранении и использовании большого количества изложниц. Это также увеличивает выход полезного продукта из данного веса стали и перерабатывает сталь в форму полуфабриката, более близкую к форме готового продукта.
При этом ковш со сталью доставляется на установку непрерывной разливки стали мостовым краном и после предварительной обработки, которая может включать перемешивание путем подачи инертного газа (аргона), открытая горловина ковша закрывается теплоизоляционная крышка для снижения потерь тепла. Вся установка поднимается краном на вращающуюся башню. Это делает возможной последовательную разливку – разливку нескольких ковшей из стали одной марки без остановки машины. Это также является важным фактором снижения затрат. Перед разливкой снаружи на стакан ковша устанавливается газонепроницаемая огнеупорная труба. Это устройство предотвращает поглощение жидкой сталью избыточного кислорода и азота из атмосферы. Затем открывается сопло ковша, позволяя стали вытекать из ковша в промежуточный ковш, резервуар, питающий водоохлаждаемую медную форму литейной машины, через другую газонепроницаемую трубу с контролируемой скоростью.