Измерение шероховатости поверхности – . |
alexxlab | 06.08.2019 | 0 | Разное
3.3.8. Измерение шероховатости поверхности оптическими способами
Микронеровности или шероховатости – совокупность неровностей с относительно малыми шагами, образующими рельеф поверхности изделий. От шероховатости поверхностного слоя (размеров, формы и взаимного расположения неровностей) зависят эксплуатационные качества и долговечность деталей и узлов. Поэтому важно контролировать качество обработки поверхностей деталей, назначаемых конструктором. Шероховатость поверхности рассматривается в пределах некоторого участка, длина которого (базовая длина l) выбирается в зависимости от характера поверхности. Чем грубее поверхность, тем больше должно быть значение l: предусмотрено шесть стандартных назначений базовой длины от 0,08 до 25 мм. По ГОСТ 2789 шероховатость поверхности для микропрофиля (рис. 18) оценивается двумя основными критериями: Rа – среднее арифметическое отклонение профиля
или
.
Rz – высота неровностей (среднее расстояние между находящимися в пределах базовой длины пятью высшими точками выступов и пятью низшими точками впадин, измеренное по линии, параллельной средней):
.
|
Рис. 18. Профиль шероховатой поверхности |
По ГОСТ 2789 установлено 14 классов чистоты поверхности. Для классов 1…5 и 13…14 оценку рекомендуется производить по критерию Rz, а для классов 6…12 – по критерию Rа. Максимальные числовые значения параметров шероховатости Rа лежат в пределах от 0,01 (14-й класс) до 80 мкм (1-й класс) и Rz от 0,05 до 320 мкм. В производственных условиях обычно приходится определять класс чистоты обработанной поверхности и измерять шероховатость. При этом используются методы измерения шероховатости и визуального сравнения. Визуальное сравнение дает надежные результаты только для поверхностей до 7-го класса чистоты. Для повышения надежности контроля шероховатости этим методом до 10-го класса применяются микроскопы для сравнения контролируемой поверхности с поверхностью образцовой шероховатости.
Шероховатость измеряют контактным методом с помощью щуповых приборов (профилометров и профилографов) и бесконтактными оптическими приборами (двойными микроскопами, микроинтерферометрами и др.).
При контактных методах измерения шероховатости поверхности по контролируемой поверхности перемещается алмазная или стальная игла (с радиусом закругления 1…12 мкм). При этом она получает микроперемещения в направлении своей оси, соответствующие изменению профиля поверхностных неровностей. Эти микроперемещения усиливаются и регистрируются отсчетными устройствами. Чаще применяются контактные приборы, построенные на пружинно-рычажных, оптико-механических и электромеханических принципах. Так, например, профилометры, разработанные на базе пружинно-измерительных головок (микаторов), имеют малые вес и габариты. Измерительная головка, снабженная ощупывающей иглой, перемещается по контролируемой поверхности от руки с помощью микрометрического винта. Стрелка прибора по шкале показывает высоту неровностей. По этим показаниям можно построить профилограмму и затем по формулам найти значение Rz или Rа.
Профилографы позволяют автоматически получить увеличенную запись микропрофиля поверхности в виде профилограммы. Для этой цели прибор имеет специальное самопишущее устройство.
Бесконтактные (оптические) методы измерения шероховатости поверхности делятся на метод светового сечения и интерференционные методы.
При методе светового сечения контролируемая поверхность освещается узкой полосой света (световой плоскостью). Контур профиля поверхности в виде линии пересечения световой плоскости с контролируемой поверхностью, искривленной микронеровностями (рис. 19,а), рассматривается при значительном увеличении. Приборы, построенные на этом принципе, называются двойными микроскопами (микроскопы МИС – системы акад. В.П. Линника, микроскопы ПСС), так как они состоят из осветительного О и визуального В микроскопов (рис. 19,б). Изображение щелевой диафрагмы 1 (рис. 19,в), расположенной в фокальной плоскости линзы 2, проектируется объективом осветительного микроскопа на исследуемую поверхность
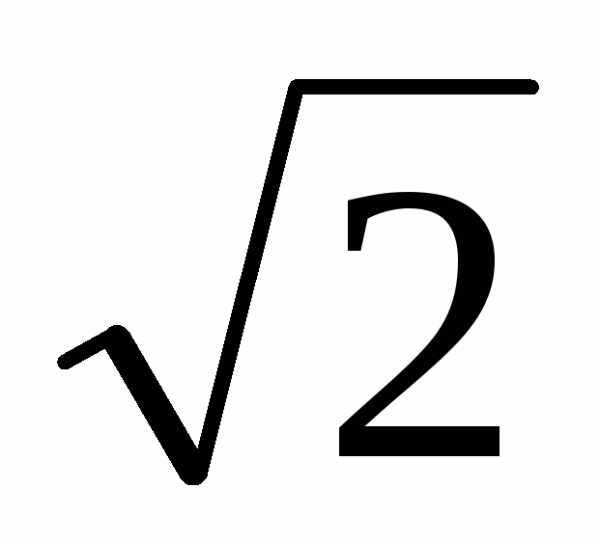
В поле зрения окуляра микроскопа (рис. 19,г) наблюдается картина распределения шероховатостей на некотором участке базовой длины (из-за небольшого поля зрения). Высота неровностей определяется умножением разности отсчетов по шкале окулярного микрометра при совмещении горизонтальной нити перекрестья с выступами и впадинами неровностей на цену деления окулярного микроскопа. Картину шероховатостей на отдельных участках исследуемой поверхности можно фотографировать (с помощью фотонасадок).
Для измерения шероховатости 3-9-го классов к микроскопу придаются несколько пар сменных микрообъективов. Погрешность показаний приборов зависит от общего увеличения и составляет от 7,5 до 24 %. С помощью двойных микроскопов можно измерять толщину тонких прозрачных пленок.
Рис. 19. Двойной микроскоп:
а – схема световых сечений; б – общий вид; в – оптическая схема; г – поле зрения микроскопа
При интерференционном методе измеряют шероховатость поверхности 10-14-го классов. Для этого используется интерференционный микроскоп В.П. Линника. На контролируемой поверхности изделия оптическая система микроскопа образует интерференционные полосы. Из-за неровностей поверхности интерференционные полосы искривляются соответственно профилю неровностей на рассматриваемом через окуляр участке (рис. 20,а). С помощью окулярного микрометра определяются значения искривления интерференционных полос – а и интервал между одноименными полосами – b на некотором участке интерферограммы (рис. 20,б).
Высоту неровности Н можно определить так:
,
мкм,
где – длина световой волны источника света, применяемого в приборе.
Параметр Rz определяется после измерения ординат пяти высших и пяти низших точек от линии, параллельной средней линии профиля.
а) | в) |
б) | |
Рис. 20. Микроинтерферометр: а и б – искривления интерференционных полос; в – оптическая схема |
Интерференционные микроскопы (микроинтерферометры) В.П. Линника имеют различные конструктивные разновидности. Их принципиальные оптические схемы идентичны (рис. 20,в). От источника света 1 лучи через конденсор 2, диафрагму 3 и линзу 4 попадают на полупрозрачную пластину 5 и разделяются на два когерентных луча, один из которых, отражаясь от посеребренного слоя, направляется через объектив 6 на контролируемую поверхность 7, находящуюся в фокальной плоскости объектива 6. Отразившись от контролируемой поверхности, луч проходит обратный путь и попадает в объектив 8. Второй луч света проходит через посеребренный слой пластины 5, на пластину 9 (она служит для уравнивания длины хода в стекле двух интерферирующих лучей), объектив 10 и собирается на зеркале 11, расположенном в его фокусе. Отразившись от зеркала 11, второй луч также попадает объектив 8. Оба луча собираются в фокусе объектива 8 на зеркале 12, где и возникает интерференционная картина, которая вместе с изображением контролируемой поверхности 7 рассматривается в окуляр 13. Фотоокуляр 14, зеркало 15 и экран 16 (матовое стекло, фотопленка и т.д.) служат для фотографирования интерференционной картины; при этом зеркало 12 из хода лучей выводят. Ширину и направление интерференционных полос можно изменять, смещая объектив 10 перпендикулярно его оптической оси.
studfiles.net
Шероховатость поверхности. Виды, методы и параметры. |
Поверхности деталей, которые обработаны самым тщательным образом, не может быть идеально ровной: от номинальной – заданной чертежом – она будет отличаться. Есть два вида возможных отклонений: макро- и микрогеометрические, и при том, что первые характеризуют волнистость детали и степень её несоответствия форме, то вторые определяют не что иное, как шероховатость поверхности.
Понятию «шероховатость» можно дать следующее определение: она представляет собой совокупность микронеровностей на поверхности детали или изделия. Ещё одно немаловажное уточнение – шаг неровности относительно базовой длины очень и очень мал.
Виды и параметры шероховатости:
Выделяют несколько видов шероховатости.
- Исходная шероховатость – следствие технологической обработки изделия абразивными материалами.
- Эксплуатационная шероховатость – шероховатость, которую приобрела поверхность вследствие изнашивания и трения.
- Равновесная шероховатость – эксплуатационная шероховатость, которая воспроизводится при стационарных условиях трения.
Согласно ГОСТ 2789-73 номенклатура параметров шероховатости выглядит следующим образом.
- Ra – среднее арифметическое значение отклонения профиля;
- Rz – высота неровностей профиля, снятая в 10 точках;
- S – средний шаг местных выступов профиля;
- Sm – среднее арифметическое значение шага неровности;
- Rmax – максимальная высота профиля;
- tp – относительная длина профиля (опорная), р – уровень сечения профиля.
Предпочтительным при задании шероховатости является параметр Ra.
Шероховатость во многом определяет эксплуатационные характеристики деталей и узлов, поэтому её точное измерение является одной из важных задач метрологии. Оценка может проводиться поэлементно (сравнение отдельных параметров) либо комплексно – путём сравнения исследуемой поверхности с эталоном.
В современных технологических исследованиях предпочтительным является первый способ.
Щуповой метод:
Щуповой метод измерения шероховатости поверхности относится к контактным методам и реализуется с помощью профилометра. Прибор представляет собой датчик, оснащённый тонкой остро заточенной алмазной иглой с ощупывающей головкой.
Игла перемещается по нормали к исследуемой поверхности. Естественно, в местах микронеровностей (впадин и выступов) возникают механические колебания относительно головки. Эти колебания передаются на датчик, который преобразует механическую энергию в электрическую. Сигнал, генерируемый преобразователем, усиливается и измеряется: его параметры точно характеризуют неровности поверхности детали или изделия.
В зависимости от типа преобразователя полезных сигналов профилометры подразделяются на индуктивные, электронные, индукционные и пьезоэлектрические, причём наибольшее распространение получили устройства первого вида. Кроме этого, существует ещё одна разновидность приборов – профилографы, позволяющие не только измерить, но и записать параметры профиля в заранее подобранном горизонтальном и вертикальном масштабах.
Исследование неровности проводится в несколько этапов: профиль «ощупывается» определённое количество раз, и лишь на основе серии измерений вычисляется окончательное – усредненное – значение параметра: количественная характеристика неровности относительно длины участка.
Оптические методы:
Группа оптических – бесконтактных – способов измерения шероховатости поверхности достаточно обширна. Самыми распространёнными входящими в неё методами являются следующие:
- светового и теневого свечения;
- микроинтерференционный;
- растровый.
Растровый метод
Суть данного метода достаточно проста: на исследуемую поверхность накладывается изготовленная из стекла пластинка, на которую нанесена растровая сетка (система равноудалённых параллельных линий) с достаточно малым шагом.
При наклонном падении световых лучей в местах микронеровностей штрихи отраженной сетки накладываются на штрихи реальной – возникают муаровые полосы, свидетельствующие о наличии впадин и выступов на изучаемой поверхности. Точное измерение параметров неровности осуществляется по изложенной в ГОСТ методике с помощью растрового микроскопа.
Стоит отметить, что данный метод используется при исследовании лишь тех поверхностей, следы обработки на которых имеют преимущественное направление.
Методы светового и теневого свечения
Метод светового свечения при измерении параметров неровности применяется наиболее часто и заключается в следующем. Исходящий от источника света световой поток преобразуется в тонкий пучок, проходя через узкую щель. Далее он с помощью объектива под определённым углом направляется на исследуемую поверхность. Отраженный луч снова проходит через объектив и формирует изображение щели в окуляре. Абсолютно ровная поверхность соответствует идеально прямой светящейся линии, шероховатая поверхность – искривлённой.
Теневой метод является «продолжением» светового: на небольшом расстоянии от изучаемой поверхности устанавливается линейка, ребро которой скошено. Пучок света проходит тот же путь, однако, словно ножом срезается ребром. На контролируемой поверхности появляется тень, верхняя часть которой точно повторяет изучаемый профиль. Рассматривая это изображение в микроскоп, делают выводы о характере и параметрах шероховатости.
Микроинтерференционный метод
Для реализации микроинтерференционного метода используют измерительный прибор, в состав которого входит интерферометр и измерительный микроскоп. С помощью первого устройства формируется интерференционная картина исследуемой поверхности с искривлениями полос в местах неровностей. Увеличивающий в разы полученную картину микроскоп позволяет измерить параметры шероховатости.
Метод слепков
Описанный ниже метод используют для оценки шероховатостей труднодоступных поверхностей и поверхностей, имеющих сложную конфигурацию.
Метод слепков заключается в снятии негативных копий (материалом для их изготовления, как правило, служит парафин, гипс или воск) поверхности при их дальнейшем исследовании оптическими или щуповым методами. Иными словами, метод слепков не является самостоятельным методом и используется лишь в сочетании с вышеописанными способами измерения шероховатости поверхности.
ndt-welding.com
3 Измерение шероховатости поверхности
3.1 Методы измерения
Два критерия оценки шероховатости Ra и Rz разделяют по-верхности на три обособленные группы, которые различают как по методам механической обработки, так и по методам контроля.
Первая группа – грубо обработанные поверхности
Rz = 323-10. Шероховатость этих поверхностей оценивается сравнением с образцами, на которых указано значение Rz и каким методом они обработаны. Существующие приборы не приспособлены для измерения шероховатости таких грубых поверхностей (у профилометров ломаются иглы, у микроско-пов не хватает поля зрения).
Вторая группа Ra = 2,5-0,02 – поверхности, получающиеся чистовой обработкой, шлифованием, притиркой, протягива-нием, разверткой. Шероховатость этих поверхностей измеряют профилометрами. Перемещения ощупывающей иглы с помо-щью оптико-механических или электрических устройств фиксируют по шкале, отградуированной в величинах Ra.
Третья группа Rz = 0,1 – 0,025 – поверхности, шерохова- тость, которых измеряют микроинтерференционным микро-скопом.
3.2 Устройство и принцип работы профилометра
Действие прибора основано на принципе ощупывания по-верхности исследуемой детали алмазной иглой щупа и преоб-разовании возникающих при этом механических колебаний щупа в изменение электрического сигнала.
Прибор состоит из датчика, привода, стойки и электронного блока.
В корпусе датчика 1 (рис.3.1) расположен щуп с алмазной иглой. На конце корпуса расположена твердосплавная опора с торроидальной поверхностью. Крепление датчика к корпусу осуществляется при помощи хвостовика. Алмазная игла защи-щена кожухом 2.
Перемещение датчика 1 осуществляется c помощью привода, который устанавливается на кронштейн стойки 3. Датчик вставляется в гнездо подвески 4 и закрепляется винтом 5. Вер-тикальное перемещение подвески 4 осуществляется при помощи винта 6 по направляющей 7. Закрепление подвески 4 на направ-ляющей 7 осуществляется винтом 8. Датчик 1 приводится в движение электродвигателем постоянного тока, установленного внутри привода.
Рис. 3.1. – Измерительный блок профилометра
Стойка предназначена для установки привода и базирования исследуемых деталей. Она состоит из плиты 9, колонны 10, каретки 11, кронштейна 3. Привод крепится к кронштейну 2 винтами 12. Перемещение кронштейна 3 по вертикали осуществляется гайкой 13, винтом 14. Каретка 11 закрепляется на колонне 10.
Рис. 3.2.- Электронный блок профилометра
Электронный блок выполнен в едином каркасе. На лицевой панели (рис.3.2) расположены органы управления 1 (с соответ-ствующими надписями), цифровое табло 2 для отсчета измерен-ного значения Ra , индикатор рабочей зоны 3, кнопка включения СЕТЬ 4 и кнопка ПУСК 5.
3.3. Порядок работы на профилометре
Включите профилометр в сеть.
Снимите с датчика защитный кожух.
Установите на плиту образец шероховатости при помощи гайки 13.
Опустите датчик до положения, при котором стрелка индикатора рабочей зоны займет среднее положение.
Установите на органах управления следующие парамет-ры: длина трассы – 1,5 мм; отсечка шага – 0,25 мм; предел измерения – 1 мкм.
Нажмите кнопку ПУСК.
Значение Ra образца шероховатости не должно отлича-ться более чем на 4% от указанного на образце.
Установите на столике исследуемый образец.
Установите требуемую отсечку шага в зависимости от ожидаемого значения Ra в соответствии с ГОСТ 2789-73, табл.5 приложения Б
Установите требуемую длину трассы по табл.3.1,
Таблица 3.1 – Длина трассы
l, мм
L, мм
0,25
08
2,5
1,5; 3
3; 6
6
3.3.11. Измерьте значение Rа. Порядок работы тот же, что и при определения Ra образца шероховатости. В процессе измерения проследите за индикатором рабочей зоны. Стрелка индикатора не должна зашкаливать. В против-ном случае требуется уточнить установку образца. Если полученное значение Ra может уложиться в меньший предел измерения, следует переключить предел измере-ния и повторить измерение для получения более точного результата. Если на табло загорелся сигнал перегрузки “Р”, то следует переключить предел измерений на больший и повторить измерения.
studfiles.net
Измерение и контроль шероховатости поверхности.
Аттестация шероховатости поверхности проводят по двум видам контроля:
Качественный контроль параметров шероховатости поверхности осуществляют путем сравнения с образцами или образцовыми деталями визуально или на ощупь.
ГОСТ 9378-75 устанавливает образцы шероховатостей, полученные механической обработкой, снятием позитивных отпечатков гальванопластикой или нанесением покрытий на пластмассовые отпечатки.
Наборы или отдельные образцы имеют прямолинейные, дугообразные или перекрещивающиеся дугообразные расположения неровностей поверхности.
На каждом образце указаны значения параметра Rа и вид обработки образца. Для повышения точности используют щупы и микроскопы сравнения.
Количественный контроль параметров шероховатости осуществляют бесконтактным и контактным средствами измерения.
Для количественной оценки шероховатости поверхности бесконтактным методом используется два способа – увеличение их с помощью оптической системы или использованием отражательных способностей обработанной поверхности.
Приборами, основанными на оценке поверхностных неровностей при увеличении их с помощью оптической системы, являются ”приборы светового сечения”, основанные на отражательной способности (ППС), теневой проекции (ТПС) и интерференции света (МИИ), изготовленные в соответствии с ГОСТ 9847-81.
Принцип действия приборов светового сечения заключается в получении увеличенного изображения профиля измеряемой поверхности с помощью лучей, направленных наклонно к этой поверхности, и измерении высоты неровностей в получаемом изображении. Наиболее распространенным является двойной микроскоп типа МИС-11 и ПСС-2.
Принцип действия микроинтерферометра такой же, как и обычно, но отличается тем, что в качестве одной из поверхностей, которая создает интерференционную картину, используется измеряемая поверхность с малыми неровностями, т.к. на грубых поверхностях интерференцию получить невозможно. В принципе микроинтерферометр представляет сочетание интерферометра и микроскопа (прибор ММИ-4).
Для количественной оценки шероховатости поверхности контактными средствами измерения выделяют профилографы-профилометры и профилометры.
Профилограф-профилометр состоит из двух приборов в зависимости от характера выдаваемой измерительной информации – профилографа и профилометра. Объединяются они вместе для расширения возможностей измерения поверхностных неровностей и в связи с тем, что многие функциональные узлы у них совпадают.
Эти приборы предназначены в основном для работы в лаборатории. Отечественная промышленность изготавливает несколько моделей приборов (201; 202; 252 и др.), связанных на индуктивном методе преобразования колебаний иглы в колебание напряжений.
Профилограф – прибор для измерения величин неровностей поверхности в нормальном к ней сечении в виде профилограммы, обработкой которой определяются параметры, характеризующие шероховатость и волнистость поверхности. В результате измерения на шкале прибора в виде значения одного из параметров, используемых для оценки этих неровностей, по критерию Ra, т.к. оценка шероховатости по параметру Rz связана с трудностями обработки сигнала.
studfiles.net
Волнистость и шероховатость. Измерение и контроль волнистости и шероховатости
Измерения и контроль параметров волнистости и шероховатости поверхностей относятся к линейно-угловым измерениям, однако измеряемые величины здесь очень малы. На производстве измерению подлежат высоты неровностей от 0,025 мкм и шагов начиная с 2 мкм. В последнее время в некоторых отраслях промышленности достигнуто определение сублимированностей с высотой 0,05 А (1 ангстрем = 10-10 м) и с шагом 2 А. Точность измерения, естественно, должна быть в несколько раз выше требуемой точности выполнения геометрических параметров деталей.
Большое значение шероховатости и волнистости поверхности деталей для эксплуатации узлов и механизмов обусловило возникновение большого разнообразия методов и средств оценки параметров микронеровностей. На рис. 2.60 представлена классификация современных приборов для измерения этих параметров.
Рис. 2.60. Классификация методов и средств измерений, приборов для определения параметров шероховатости
Рис. 2.61. Метод сравнения с образцами
Наиболее простым методом контроля шероховатости поверхностей деталей в цеховых условиях является метод сравнения с образцами визуально или на ощупь (рис. 2.61). Образцы в соответствии с межгосударственным стандартом ГОСТ 9378 — 93 (ИСО 2623-1—85, ИСО 2632-2 — 85) изготавливаются из тех же материалов, что и контролируемые детали, и обрабатываются теми же методами. Кроме того, форма образцов и основное направление неровностей поверхности должны соответствовать определенным указаниям. Так, для некоторых способов обработки эти указания представлены в табл. 2.15
Таблица 2.15. Способы обработки, воспроизводимые образцами, форма образца и основное направление неровностей поверхности образца | ||||||
Способ обработки | Форма образца | Расположение неровностей | ||||
Описание | Условное изображение | Вид поверхности и условное изображение на чертеже | ||||
Точение | Цилиндрическая выпуклая | Прямолинейное | ||||
Расточка | Цилиндрическая вогнутая | |||||
Фрезерование цилиндрическое | Плоская | |||||
Строгание | Плоская | |||||
Шлифование периферией круга | Плоская, цилиндрическая выпуклая, цилиндрическая вогнутая | |||||
Точение торцовое | Плоская | Дугообразное | ||||
Фрезерование торцовое | Плоская | |||||
Фрезерование торцовое | Плоская | Перекрещивающееся дугообразное | ||||
Шлифование торцовое | Плоская | |||||
Шлифование чашеобразным кругом | Плоская | |||||
Электроэрозионная обработка | Плоская | Не имеющее определенного направления штриха | ||||
Дробеструйная, пескоструйная обработка | Плоская | |||||
Полирование | Плоская, цилиндрическая выпуклая | Путанный штрих |
|
В стандарте установлены ряды номинальных значений параметров шероховатости Ra поверхности образца в зависимости от воспроизводимого способа обработки и базовой длины для их оценки. Так, для шлифования значения Ra варьируются от 0,050 до 3,2 мкм при базовой длине от 0,25 до 2,5 мм, а для точения и расточки — соответственно от 0,4 до 12,5 мкм при базовой длине 0,8…2,5 мм, для полирования — 0,006…0,2 мкм и 0,08…0,8 мм. Ширина образцов сравнения составляет не менее 20 мм, а длина 20…50 мм. Образцами могут быть и готовые детали.
Однако глазомерная оценка и оценка на ощупь субъективны и могут вызвать недоразумения. Особенно эти виды оценок затруднительны для точно обработаных деталей.
Для количественного определения параметров неровностей применимы бесконтактные и контактные методы измерений.
Наибольшее распространение из бесконтактных методов получили методы светового сечения, теневой проекции, метод с применением растров, микроинтерференционные, рефлектометрические методы (см. подразд. 2.2.4), методы электронной микроскопии, сканирующей туннельной микроскопии и др.
Рассмотрим один из них — метод светового сечения, реализуемый, например, двойным микроскопом МИС-11, ПСС-2, прибором теневого сечения ПК-1 и др.
Принципиальная схема этого метода приведена на рис. 2.62.
Рис. 2.62. Метод светового сечения:
а — принципиальная схема; б — увеличенное изображение щели
Освещенная узкая щель проецируется микроскопом на ступенчатую поверхность Р,Р2. При падении света в направлении, указанном стрелками, изображение светящейся щели на ступенчатой поверхности займет положение S2 на нижней части поверхности Р2 и положение S1 на нижней части поверхности P1. В поле зрения микроскопа наблюдения, расположенного под углом 90° к оси проецирующего микроскопа, изображение щели будет иметь вид, показанный на рис. 2.62, б, т. е. в данном случае видна не высота ступени Н, измеряемая по нормали к поверхностям Р, и Р2, а ее проекция h, которая и определяется с помощью винтового окулярного микрометра.
Оптическая схема двойного микроскопа МИС-11 представлена на рис. 2.63.
Рис. 2.63. Оптическая схема микроскопа МИС-11:
1 — окулярный микрометр; 3 — объектив; 3 — исследуемая поверхность; 4 и 5 — система линз; 6 — диафрагма; 7 — конденсор; 8 — осветительное устройство
Пучок света от осветительного устройства 8 через конденсор 7 и узкую щель диафрагмы 6 проходит в систему линз 5 и 4, проецирующую изображение щели на исследуемую поверхность 3. Полученное отраженное от этой поверхности изображение проецируется объективом 2 микроскопа наблюдения (визуального) на сетку окулярного микрометра 1, которым и выполняется измерение высоты неровностей.
Считается, что средства измерений, реализующие метод светового сечения, позволяют измерять неровности поверхности высотой от 0,5 до 40 мкм с допустимыми погрешностями показаний по норме порядка 24 и 7,5 % соответственно.
Основным вариантом профильного метода измерения параметров микронеровностей поверхности является контактный (щуповой) метод. Сущность этого метода заключается в том, что остро заточенная игла, имеющая контакт с исследуемой поверхностью, приводится в поступательное перемещение по определенной трассе относительно поверхности (рис. 2.64, а). Ось иглы 2 располагают по нормали к измеряемой поверхности 3. Опускаясь во впадины, поднимаясь на ее выступы во время движения ощупывающей головки 1, игла начинает колебаться относительно головки, повторяя по величине и форме огибаемый профиль поверхности.
Рис. 2.64. Контактный (щуповый) метод измерения шероховатости поверхности:
а — принципиальная схема; б — схема профилометра; 1 — ощупывающая головка; 2 — игла; 3 — измеряемая поверхность; 4 — катушки; 5 — генератор звуковой частоты; 6 — якорь
Механические колебания иглы преобразуются, как правило, в подобные им электрические колебания при помощи электромеханического преобразователя того или иного типа. Снятый с преобразователя сигнал после преобразования поступает либо на шкалу прибора (при профилометрировании), либо на записывающий прибор с соответствующим горизонтальным и вертикальным масштабами (при профилографировании). Соответственно щуповые электромеханические приборы, предназначенные для измерения параметров шероховатости поверхности, называются профилометрами, а такие же приборы для записи микронеровностей — профилографами. Комбинированные приборы, которые позволяют количественно определять и графически изображать микронеровности, называются профилометрами- профилографами.
В зависимости от назначения установлены следующие типы профилометров-профилографов: I — для лабораторных работ (стационарные) , II — цеховые (стационарно-переносные для контроля окончательно обработанных поверхностей), III — цеховые (портативные, предназначенные для межоперационного контроля).
Преимущественное распространение получили профилометры и профилографы, у которых в качестве преобразователя установлен индуктивный преобразователь. Это приборы моделей 201, 202, 240, 252 заводов «Калибр», «Телисарф-4» (Великобритания), «Профикордер» (США) и др.
В соответствии с этой схемой (рис. 2.64, б) движение алмазной иглы 2 по микронеровностям в вертикальной плоскости вызывает соответствующее перемещение якоря 6 в индуктивной ощупывающей головке 1, а вместе с тем изменение воздушных зазоров между якорем 6 и двумя расположенными по обеим сторонам оси его качения катушками 4. К одной из катушек якорь 6 приближается, что увеличивает ее индуктивность, а от другой он в то же время удаляется, что уменьшает ее индуктивность. Катушки и две половины первичной обмотки дифференциального входного трансформатора образуют мост, питание которого осуществляется от генератора звуковой частоты 5 (-5 кГц). Одновременное, но противоположное изменение индуктивности катушек соответственно изменяет напряжение в измерительной диагонали моста, которое связано с величиной перемещения Л ощупывающей иглы при ее механических колебаниях.
Рис. 2.65. Профилометр-профилограф мод. 170311 завода «Калибр»:
1 — записывающий прибор; 2 — предметный столик; 3 — датчик; 4 — мотопривод; 5 — стойка; 6 — электронный блок; 7 — блок-приставка
На рис. 2.65 изображен профилометр-профилограф модели 170311 завода «Калибр» блочной конструкции лабораторного типа. Он предназначен для измерения параметров шероховатости и волнистости плоских и цилиндрических поверхностей изделий, поверхностей шариков и роликов диаметром 1…25 мм, поверхностей отверстий малых диаметров (до 3 мм). Прибор имеет аналоговый выход на ЭВМ. Измерение шероховатости производится путем ощупывания поверхности алмазной иглой с радиусом при вершине 10 мкм и фиксацией цифровых показаний на табло по параметрам Ra, Rz, Rmax, Rp, Sm, tp или воспроизведения профиля на электротермической бумаге в прямоугольных координатах. Вертикальное увеличение микропрофиля варьируется по 11 ступеням от 100 до 200 000 крат, а горизонтальное — от 0,5 до 2 000 крат. Скорость трассирования датчика выбирается в зависимости от величины шероховатости в пределах 0,6…60 мм/мин. Статическое измерительное усилие алмазной иглы на измеряемую поверхность не превышает 0,003 Н. Погрешность показаний прибора по записывающему блоку составляет ±4,5 %, а по показывающему блоку составляет ±10%.
Профилометр-профилограф состоит из следующих основных блоков: датчик 3, мотопривод 4, электронный блок 6, записывающий прибор 1, стойка 5, предметный столик 2, блок-приставка 7.
Волнистость поверхности с шагами, большими 2,5 мм, а также неровности поверхности в отверстиях диаметром от 4 мм при глубине до 10 мм записывают и измеряют с помощью приспособления для проверки волнистости (рис. 2.66). Оно применяется в комплекте с обычным датчиком.
Рис. 2.66. Приспособление для проверки волнистости:
1 — коромысло; 2 — пятка; 3 — микровинт; 4 — корпус; 5 — плоская пружина; 6 — хомут; 7 — подвес; 8 — щуп; 9 — переходник; 10 и 12 — винты; 11— опора
Корпус 4 приспособления устанавливается на направляющую мотопривода.
К подвесу 7 на плоской пружине 5 крепится коромысло 1, имеющее доведенную опорную плоскость, на которой перемещается сферический винт 12 опоры 11. Пятка 2 коромысла 1 опирается на микровинт 3, предназначенный для регулировки положения опорной плоскости, выставляемой параллельно исследуемой поверхности.
Подвес 7 с помощью хомута 6 устанавливается на корпусе датчика. На переднем конце подвеса закреплен переходник 9 с доведенной верхней плоскостью, размещаемой непосредственно под иглой датчика. В отверстие переходника вставляется щуп 8 с закрепленным концом, который фиксируется в наконечнике винтом 10.
Контакт сферической поверхности винта 12 с опорной плоскостью опоры 11 обеспечивается двумя спиральными пружинами, надеваемыми на штифты подвеса и корпуса.
С помощью такого устройства определяют параметры волнистости — высоту волнистости Wz, наибольшую высоту волнистости Wmax и средний шаг волнистости.
www.eti.su
8. Измерение шероховатости поверхностей
8.1. Основные понятия и определения
Шероховатостью поверхности называют совокупность неровностей поверхности с относительно малыми шагами, выделенную с помощью базовой длины.
Базовой длиной ℓ называется длина базовой линии, используемая для выделения неровностей, характеризующих шероховатость поверхности.
По ГОСТ 2989-73 шероховатость поверхности количественно оценивается средним арифметическим отклонением профиля Ra, высотой неровностей профиля по десяти точкам Rz, наибольшей высотой неровностей профиля Rmax, средним шагом неровностей профиля Sm, средним шагом местных выступов профиля S, относительной опорной длиной профиля tp и другими параметрами.
Базовую длину ℓ, в пределах которой производят определение параметров шероховатости, устанавливают по табл. в зависимости от предполагаемой шероховатости поверхности детали.
Для измерения высоты неровностей служит двойной микроскоп МИС-11.
68. Значения параметров шероховатости Ra и Rz и базовой длины по ( ГОСТ 2989-73)
Rа, мкм | Rz , мкм | Рекомендуемая базовая длина, мм | |
Предпочтительные значения | значения | ||
1 | 2 | 3 | 4 |
50 | 80; 63; 40 | 360; 250; 200; 160 | 8 |
25 | 40; 32; 20 | 160; 125; 100; 80 | 8 |
12,5 | 20; 16; 10 | 80; 63; 50; 40 | 8 |
6,3 | 10; 8; 5 | 40; 32; 25; 20 | 2,5 |
3,2 | 5; 4; 2,5 | 20; 16; 12,5; 10 | 2,5 |
1,6 | 2,5; 1,2; 1,25 | 10; 8; 6,3 | 0,8 |
0,8 | 1,25; 1; 0,63 | 6,3; 5; 4; 3,2 | 0,8 |
0,4 | 0,63; 0,5; 0,32 | 3,2; 2,5; 2; 1,6 | 0,8 |
0,2 | 0,32; 0,25; 0,16 | 1,6; 1,25; 1; 0,8 | 0,25 |
0,1 | 0,16; 0,125; 0,08 | 0,8; 0,63; 0,5; 0,4 | 0,25 |
0,05 | 0,08; 0,063; 0,04 | 0,4; 0,32; 0,25; 0,2 | 0,25 |
0,025 | 0,04; 0,032; 0,02 | 0,2; 0,16; 0,125; 0,1 | 0,25 |
− | 0,01; 0,008 | 0,5; 0,04; 0,032 | 0,08 |
8.2. Лабораторная работа № измерение шероховатости поверхностей с помощью двойного микроскопа
Цель работы: изучение методики и техники измерения шероховатости с помощью двойного микроскопа МИС-11.
Задание: с помощью двойного микроскопа МИС-11 определить величину высоты неровностей профиля по десяти точкам Rz поверхности детали, дать заключение о годности детали.
Перечень приборов и принадлежностей, необходимых для выполнения работы: двойной микроскоп МИС-11, набор объективов, объект-микрометр, накладная призма, образцы шероховатости, объект измерения и его чертеж (выдает преподаватель), визуальные образцы шероховатости.
8.2.1. Описание двойного микроскопа мис-11
Двойной микроскоп предназначен для визуальной оценки, измерения и фотографирования высоты неровностей наружных поверхностей деталей. Принцип действия прибора основан на методе светового сечения.
Сущность метода светового сечения заключается в следующем (рис. 1.1). Освещенная узкая щель S проецируется микроскопом А1 на поверхности Р1 и Р2, образующие ступеньку высотой h. Изображение щели на поверхности Р1 займет положение S ‘1, а поверхности Р2 − положение S ‘2. В поле зрения микроскопа А2, ось которого расположена под углом 90° к оси проецирующего микроскопа, изображение щели будет иметь вид световой ступеньки. Размер ступеньки b, соответствующий смещению изображения S“2 относительно S“1 служит мерой высоты ступеньки h (высоты неровностей). По принципу светового сечения работают приборы МИС-11, ПСС-1 и др. Оптическая схема двойного микроскопа МИС-11 приведена на рис. 1.2
Рис. 1.1. Принципиальная схема метода светового сечения
Рис. 1.2. Оптическая схема двойного микроскопа
Техническая характеристика двойного микроскопа МИС-11 -Диапазон измерений Rz, Rmax, мкм – 40 …0,8 | ||
S, мм | 2,5 … 0,002 | |
− Диапазон перемещения предметного столика в двух взаимно перпенди- кулярных направлениях, мм | 10 | |
− Цена деления барабана микровинта перемещения предметного столика, мм | 0,01 | |
− Цена деления объект-микрометра, мм | 0.01 |
ТАБЛИЦА ВЫБОР ОБЪЕКТИВОВ В ЗАВИСИМОСТИ ОТ ШЕРОХОВАТОСТИ ПОВЕРХНОСТИ
Высота неровностей профиля по десяти точкам Rz мкм | Поле зрения окуляра К мм | Фокусное расстояние, мм | Коэффициент Е |
80….6.3 | 1.8 | 25.02 | 0.17 |
20…3.2 | 1.0 | 13.02 | 0.094 |
6.3…1.6 | 0.6 | 8.16 | 0.056 |
3.2…0.8 | 0.3 | 4.25 | О.028 |
Прибор имеет набор из четырех пар объективов с различным фокусным расстоянием. Выбирают объективы по таблице, в зависимости от шероховатости проверяемой поверхности, определенной на глаз или по набору эталонов шероховатости.
Салазки корпуса микроскопов 10 перемещают по направляющим крон-штейна при помощи реечной передачи вращением винта 12 (рис. 95). В корпусе помещены два микроскопа − осветительный 20 и визуальный 5.
В микроскопе 20 имеется прямолинейная щель, освещаемая источником света. Изображение щели на изделии рассматривают с помощью микроскопа 5, снабженного окулярным микрометром 8, с увеличением 15Х.
Общий вид двойного микроскопа МИС 11
Для того, чтобы иметь возможность установить изображение щели в се-редине поля зрения окуляра, осветительный тубус снабжен винтом 19. Микро-фокусировка осуществляется поворотом винта 11. Кольцо 18 служит для регулирования ширины щели.
Контролируемое изделие устанавливают на столе 2, снабженном микрометрическими головками, с помощью которых можно перемещать стол в двух взаимно перпендикулярных направлениях.
Поворот стола осуществляют при отстопоренном винте 1.
Для установки цилиндрических деталей служит накладная призма.
studfiles.net
3 Измерение шероховатости поверхности
3.1 Методы измерения
Два критерия оценки шероховатости Ra и Rz разделяют по-верхности на три обособленные группы, которые различают как по методам механической обработки, так и по методам контроля.
Первая группа – грубо обработанные поверхности
Rz = 323-10. Шероховатость этих поверхностей оценивается сравнением с образцами, на которых указано значение Rz и каким методом они обработаны. Существующие приборы не приспособлены для измерения шероховатости таких грубых поверхностей (у профилометров ломаются иглы, у микроско-пов не хватает поля зрения).
Вторая группа Ra = 2,5-0,02 – поверхности, получающиеся чистовой обработкой, шлифованием, притиркой, протягива-нием, разверткой. Шероховатость этих поверхностей измеряют профилометрами. Перемещения ощупывающей иглы с помо-щью оптико-механических или электрических устройств фиксируют по шкале, отградуированной в величинах Ra.
Третья группа Rz = 0,1 – 0,025 – поверхности, шерохова- тость, которых измеряют микроинтерференционным микро-скопом.
3.2 Устройство и принцип работы профилометра
Действие прибора основано на принципе ощупывания по-верхности исследуемой детали алмазной иглой щупа и преоб-разовании возникающих при этом механических колебаний щупа в изменение электрического сигнала.
Прибор состоит из датчика, привода, стойки и электронного блока.
В корпусе датчика 1 (рис.3.1) расположен щуп с алмазной иглой. На конце корпуса расположена твердосплавная опора с торроидальной поверхностью. Крепление датчика к корпусу осуществляется при помощи хвостовика. Алмазная игла защи-щена кожухом 2.
Перемещение датчика 1 осуществляется c помощью привода, который устанавливается на кронштейн стойки 3. Датчик вставляется в гнездо подвески 4 и закрепляется винтом 5. Вер-тикальное перемещение подвески 4 осуществляется при помощи винта 6 по направляющей 7. Закрепление подвески 4 на направ-ляющей 7 осуществляется винтом 8. Датчик 1 приводится в движение электродвигателем постоянного тока, установленного внутри привода.
Рис. 3.1. – Измерительный блок профилометра
Стойка предназначена для установки привода и базирования исследуемых деталей. Она состоит из плиты 9, колонны 10, каретки 11, кронштейна 3. Привод крепится к кронштейну 2 винтами 12. Перемещение кронштейна 3 по вертикали осуществляется гайкой 13, винтом 14. Каретка 11 закрепляется на колонне 10.
Рис. 3.2.- Электронный блок профилометра
Электронный блок выполнен в едином каркасе. На лицевой панели (рис.3.2) расположены органы управления 1 (с соответ-ствующими надписями), цифровое табло 2 для отсчета измерен-ного значения Ra , индикатор рабочей зоны 3, кнопка включения СЕТЬ 4 и кнопка ПУСК 5.
3.3. Порядок работы на профилометре
Включите профилометр в сеть.
Снимите с датчика защитный кожух.
Установите на плиту образец шероховатости при помощи гайки 13.
Опустите датчик до положения, при котором стрелка индикатора рабочей зоны займет среднее положение.
Установите на органах управления следующие парамет-ры: длина трассы – 1,5 мм; отсечка шага – 0,25 мм; предел измерения – 1 мкм.
Нажмите кнопку ПУСК.
Значение Ra образца шероховатости не должно отлича-ться более чем на 4% от указанного на образце.
Установите на столике исследуемый образец.
Установите требуемую отсечку шага в зависимости от ожидаемого значения Ra в соответствии с ГОСТ 2789-73, табл.5 приложения Б
Установите требуемую длину трассы по табл.3.1,
Таблица 3.1 – Длина трассы
l, мм
L, мм
0,25
08
2,5
1,5; 3
3; 6
6
3.3.11. Измерьте значение Rа. Порядок работы тот же, что и при определения Ra образца шероховатости. В процессе измерения проследите за индикатором рабочей зоны. Стрелка индикатора не должна зашкаливать. В против-ном случае требуется уточнить установку образца. Если полученное значение Ra может уложиться в меньший предел измерения, следует переключить предел измере-ния и повторить измерение для получения более точного результата. Если на табло загорелся сигнал перегрузки “Р”, то следует переключить предел измерений на больший и повторить измерения.
studfiles.net