Как изготавливают подшипники: Узнайте как делают подшипники, про технологию производства
alexxlab | 05.05.2023 | 0 | Разное
Узнайте как делают подшипники, про технологию производства
Подшипник представляет собой функциональный узел, который выполняет функцию поддержки и направления вращающегося вала и оси. Устройство предназначено для снижения трения между движущейся частью механизма, а также его неподвижными элементами.
Подшипники позволяют сбавить потери энергии, устранить нагрев и снизить износ деталей.
Ведущие производители
Среди известных мировых брендов специалисты особо выделяют следующих производителей:
- шведская промышленная группа SKF поставляет изделия в 130 стран мира;
- немецкий производитель FAG;
- словацкий концерн Kinex
- французская компания SNR — считается крупнейшим поставщиком для Европы;
- японские компании NSK, NTN и Koyo;
- американский концерн TIMKEN
Для изготовления качественных изделий обязательно четкое соблюдение технологических норм на всех этапах производства. Этому требованию обычно соответствуют только известные мировые бренды.
Особенности и этапы производства
Производство подшипников требует использования особых марок стали. Для колец и тел качения подбирается сталь, сделанная из железа, в то время как для сепаратора потребуются сплавы из тяжелых и легких металлов, таких как чугун, бронза, алюминий и латунь.
Сейчас разработано большое количество специализированных подшипников, каждый из которых имеет свои технологические цепочки производства. Независимо от этого все изделия в процессе изготовления проходят токарную обработку, обработку с помощью давления, термообработку, шлифовку, а также сборку.
Далее, на примере шарикового радиального подшипника, рассмотрены основные этапы производства.
Производство колец
Данные элементы изготавливаются по следующей схеме:
- Из металлических труб и прутков подготавливаются заготовки по рассчитанному диаметру.
- Вальцеванием и давлением происходит первоначальная обработка.
- Проводятся токарные работы, направленные на нарезку отдельных колец и общую обработку поверхности.
- Нагрев колец до 850ºС, затем быстрое охлаждение до 40ºС.
- Отпуск деталей при температуре 170ºС.
- Шлифовка торцевых, внутренних и внешних поверхностей, дорожек качения.
- Финишная шлифовка дорожек качения до требуемых значений шероховатости.
Изготовление тел качения
Технологическая цепочка производства данных деталей имеет следующий вид:
- С помощью специальной стальной проволоки определенного диаметра нарезаются исходные заготовки.
- Детали сдавливаются специальным прессом для придания им шарообразной формы.
- Производится окончательная обработка давлением, с помощью которой достигается припуск в 100 мкм.
- Термическая обработка, по той же методике, что и для колец.
- Шлифовка и полировка изделия.
Производство сепаратора
Для изготовления сепаратора потребуются другая технологическая цепочка:
- Подготовка заготовки – стального листа.
- Пробивка в листе отверстий, соответствующих телам качения.
- Черновая и чистовая штамповка заготовки, направленная на придание ей необходимой формы.
- Сверловка отверстий для заклепок.
- Финишная обработка отверстий.
Сборка
Для сборки подшипника необходимо вставить внутреннее кольцо в наружное и уложить между ними тела качения. Далее в двух местах с помощью заклепок устанавливается сепаратор. Перед сдачей готовых изделий в продажу требуется обязательная проверка работоспособности, маркировка и смазка прдукта.
Подшипники как это делают| Статьи на Podsnab
По своей конструкции импортные подшипники представляют собой функциональный узел, что крайне необходим для поддержки и направления оси и вала, что постоянно вращается. Подшипниковый узел применяют для того, чтобы уменьшить процесс трения между движущимися деталями рабочего механизма. То же самое касается и неподвижных частей конструкции.
За счет шарикоподшипников удается уменьшить возможные потери рабочей энергии, устранить нагрев и свести к минимуму износ всех рабочих запчастей. Это положительно сказывается на процессе эксплуатации всего оборудования.
Производством подшипниковых узлов занимаются такие популярные компании-производители:
• SKF – шведская промышленная группа, которая осуществляет поставки своей продукции в 130 стран мира;
• TIMKEN – популярный американский концерн, что занимается сборкой шариковых изделий;
• NSK, NTN и Koyo – три главных производителя из Японии;
• Kinex – известный словацкий концерн;
• SNR – ведущий французский производитель, что считается одним из самых крупных европейских поставщиков.
Чтобы разобраться с тем, как делают шариковые подшипники вместе с необходимым набором шариков, важно детально ознакомиться с каждым этапом производства. Компании применяют необычные техники и качественные материалы, строго соблюдая технологический процесс и нормы.
Особенности производства
Изготовление подшипников качения подразумевает использование определенных марок стали. Этого требует установленный ГОСТ на подшипники. К примеру, для производства набора колец и тел качения рекомендуется подбирать сталь, что выполнена из железа. Для сепараторов, наоборот, используют более тяжелые виды материалов или сплавы – из тяжелых и легких металлов (это может быть чугун, латунь, алюминий или бронза).
На сегодняшний день в продаже предложена различная маркировка подшипников, каждый из которых отличается определенными технологическими процессами. Несмотря на конкретные модели и специфику их разработки, чтобы в дальнейшем узлы могли качественно работать, они подвергаются токарной обработке. Затем, производители используют обработку под большим давлением, термическую обработку, шлифовку и только после этого – начинают собирать готовую продукцию.
Процесс производства колец
Разбираясь с тем, как собрать подшипник, важно начать свое знакомство с процесса производства колец. Такая процедура отличается поэтапным выполнением всей работы, что позволяет производителю не упустить важные моменты:
1. Необходимо подготовить заготовки, что производят из труб и прутков, выполненных из металла с антикоррозийными свойствами. Для этого важно учитывать заранее выбранный диаметр.
3. Далее, мастера выполняют токарные процессы, что позволяет нарезать кольца и произвести стандартную процедуру обработки их поверхности.
4. Затем, происходит нагрев деталей до температуры +850 градусов, а после – мгновенное охлаждение до +40 градусов.
5. Отпуск конструкций осуществляется при соблюдении температурного режима +170 градусов.
На заключительных этапах происходит шлифовка всех торцевых поверхностей, шлифовка внутри и снаружи, а также обработка дорожек качения. Посмотреть весь процесс можно на видео в интернете. Там также будет представлена окончательная шлифовка дорожек качения до необходимых показателей шероховатости.
Изготовление тел качения и сепараторов
Тела качения изготавливают с применением стальной проволоки соответствующего диметра, которую нарезают для будущих заготовок.
Чтобы понять, как делают подшипники качения для различных машин, для начала следует ознакомиться с процедурой создания сепараторов:
• Далеко не все модели сепараторов имеют малый вес – все зависит от определенных подшипниковых узлов, для которых они изготавливаются. Чаще всего разработчики применяют в качестве заготовки стальные листы.
• Далее, в листе делают специальные отверстия – их размер должен соответствовать размеру уже готовых тел качения.
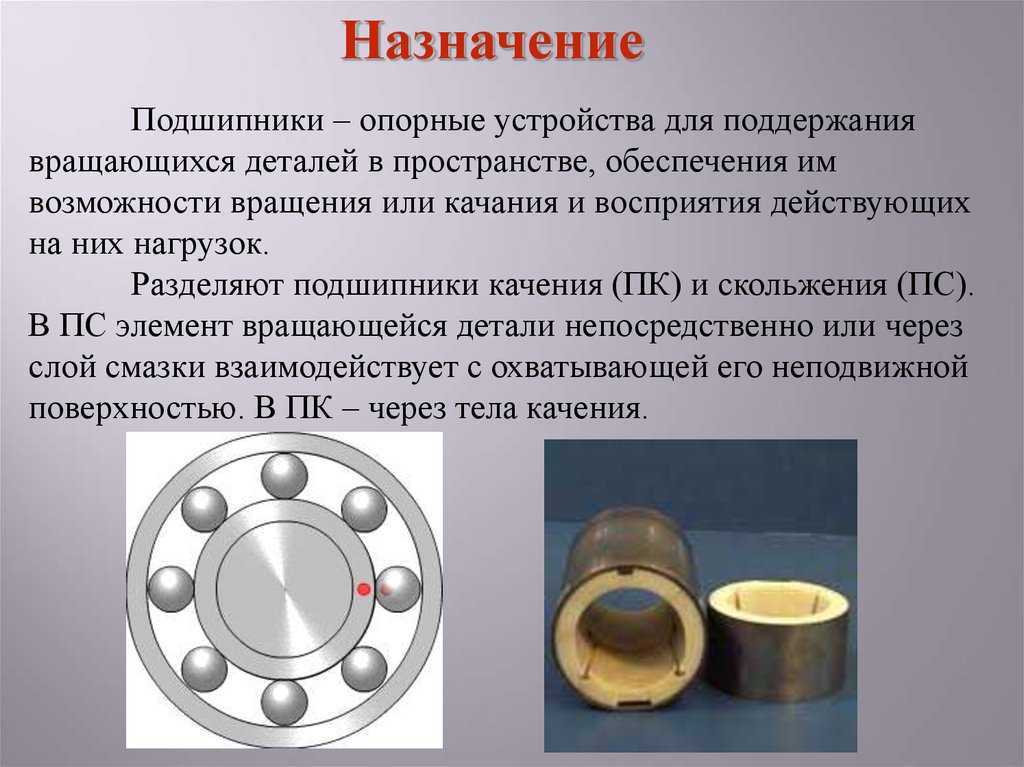
Для заклепок нужно будет проделать специальные отверстия. Проводится заключительная обработка выполненных отверстий. После этого можно приступать к следующему финишному этапу – сборка будущей конструкции.
Процесс сборки
Сборка начинается с того, что мастера вставляют внутреннее кольцо в наружное, а между ними фиксируют готовые тела качения. После этого в нескольких участках, используя заклепки, нужно установить сепаратор. Перед продажей все модели проходят тщательную проверку на работоспособность, выполняется маркировка и смазка продукта.
Подходящую модель подбирают с учетом некоторых параметров. Выбрать подшипник по размерам онлайн можно на сайте, воспользовавшись специальной схемой поиска.
Поделитесь в соц. сетях
Как изготавливаются подшипники
С тех пор, как человеку стало необходимо перемещать предметы, он использовал круглые ролики, чтобы облегчить работу. Вероятно, первыми роликами были палки или бревна, что было большим улучшением по сравнению с перетаскиванием вещей по земле, но все же довольно тяжелой работой. Египтяне использовали бревна для скатывания огромных каменных блоков для пирамид. В конце концов, кому-то пришла в голову идея прикрепить каток к тому, что перемещается, и был построен первый «автомобиль» с «колесами». Однако у них все еще были подшипники, сделанные из материалов, трущихся друг о друга, а не катящихся друг о друга. Только в конце восемнадцатого века была разработана базовая конструкция подшипников. В 1794 февраля валлийский мастер по производству железа Филип Вон запатентовал конструкцию шарикоподшипников для поддержки оси вагона. Развитие продолжалось в девятнадцатом и начале двадцатого веков, чему способствовало развитие велосипеда и автомобиля
Существуют тысячи размеров, форм и видов подшипников качения; шариковые подшипники, роликовые подшипники, игольчатые подшипники и конические роликовые подшипники являются основными видами. Размеры варьируются от достаточно маленьких, чтобы приводить в действие миниатюрные двигатели, до огромных подшипников, используемых для поддержки вращающихся частей на гидроэлектростанциях; эти большие подшипники могут иметь диаметр десять футов (3,04 метра), и для их установки требуется кран. Наиболее распространенные размеры можно легко держать в одной руке, и они используются в таких вещах, как электродвигатели.
В этой статье будут описаны только шарикоподшипники. В этих подшипниках вращающаяся часть представляет собой шарик, который катится между внутренним и наружным кольцами, называемыми дорожками качения. Мячи удерживаются клеткой, которая удерживает их на равномерном расстоянии вокруг гонок. В дополнение к этим деталям существует множество дополнительных деталей для специальных подшипников, таких как уплотнения, удерживающие масло или смазку и не допускающие попадания грязи, или винты, удерживающие подшипник на месте. Мы не будем беспокоиться об этих причудливых дополнениях.
Сырье
Почти все детали всех шарикоподшипников изготовлены из стали. Поскольку подшипник должен выдерживать большие нагрузки, он должен быть изготовлен из очень прочной стали. Стандартная отраслевая классификация стали для этих подшипников — 52100, что означает, что она содержит один процент хрома и один процент углерода (называемые сплавами при добавлении к основной стали). Эту сталь можно сделать очень твердой и прочной путем термической обработки. Там, где ржавчина может быть проблемой, подшипники изготавливаются из стали 440C нержавеющая сталь.
Сепаратор для шариков традиционно изготавливается из тонкой стали, но в настоящее время в некоторых подшипниках используются формованные пластмассовые сепараторы, поскольку их изготовление обходится дешевле и вызывает меньшее трение.
Производство
Процесс
Стандартный шарикоподшипник состоит из четырех основных частей: наружного кольца, шариков качения, внутреннего кольца и сепаратора.
Гонки- 1 Обе гонки сделаны практически одинаково. Поскольку оба кольца стальные, процесс начинается со стальных труб соответствующего размера. Автоматы, подобные токарным станкам, используют режущие инструменты для вырезания основной формы дорожки, оставляя все размеры немного большими. Причина того, что они оставлены слишком большими, заключается в том, что перед отделкой обоймы должны быть подвергнуты термической обработке, и сталь обычно деформируется во время этого процесса.
После термической обработки они могут быть возвращены к их окончательному размеру.
- 2 Необработанные обоймы помещаются в печь для термообработки при температуре около 1550 градусов по Фаренгейту (843 градуса по Цельсию) на срок до нескольких часов (в зависимости от размера деталей), затем погружаются в масляную ванну, чтобы охладить их и придать им форму. очень сложно. Это закаливание также делает их хрупкими, поэтому следующим шагом будет их отпуск. Для этого их нагревают во второй печи примерно до 300 градусов по Фаренгейту (148,8 градусов по Цельсию), а затем дают остыть на воздухе. Весь этот процесс термообработки делает детали одновременно твердыми и прочными.
- 3 После термической обработки беговые дорожки готовы к чистовой обработке. Однако дорожки теперь слишком сложно резать режущими инструментами, поэтому остальную работу необходимо выполнять шлифовальными кругами . Это очень похоже на то, что вы найдете в любом магазине для заточки сверл и инструментов, за исключением того, что для завершения гонок требуется несколько разных видов и форм.
Почти каждое место на гонке обработано шлифовкой, в результате чего получается очень гладкая и аккуратная поверхность. Поверхности, где подшипник входит в машину, должны быть очень круглыми, а стороны — плоскими. Поверхность, по которой катятся шарики, сначала шлифуется, а затем притирается. Это означает, что очень мелкая абразивная суспензия используется для полировки качения в течение нескольких часов до получения почти зеркального блеска. На этом гонки закончены и готовы к сборке с мячами.
- 4 Мячи сделать немного сложнее, хотя их форма очень проста. Удивительно, но шарики начинаются как толстая проволока. Эта проволока подается из рулона в машину, которая отрезает короткий кусок, а затем разбивает оба конца по направлению к середине. Этот процесс называется холодной высадкой. Его название происходит от того факта, что проволоку не нагревают перед тем, как разбить, и что первоначально этот процесс использовался для надевания шляпок на гвозди (что до сих пор делается).
Во всяком случае, теперь шары выглядят как планета Сатурн с кольцом посередине, которое называется «вспышка».
- 5 Первый процесс обработки удаляет этот заусенец. Шариковые подшипники помещаются между поверхностями двух чугунных дисков, где они перемещаются по канавкам. Внутренняя часть канавок шероховатая, что отрывает заусенец от шариков. Одно колесо вращается, а другое остается неподвижным. Стационарное колесо имеет сквозные отверстия, чтобы шарики можно было вставлять и вынимать из канавок. Специальный конвейер подает шарики в одно отверстие, шарики гремят по желобку, а затем выходят из другого отверстия. Затем они подаются обратно на конвейер для многократных проходов через канавки колес, пока они не будут обрезаны до достаточно круглых размеров, почти до нужного размера, и облоя полностью не исчезнет. Опять же, шарики оставляют большего размера, чтобы их можно было измельчить до окончательного размера после термической обработки.
Осталось на доводку стали немного; всего около 8/1000 дюйма (0,02 сантиметра), что примерно равно толщине двух листов бумаги.
- 6 Процесс термической обработки шариков аналогичен тому, который используется для обойм, поскольку используется та же сталь, и лучше всего, чтобы все детали изнашивались примерно с одинаковой скоростью. Как и беговые, шарики после термической обработки и отпуска становятся твердыми и жесткими. После термической обработки шарики снова помещают в машину, которая работает так же, как и устройство для удаления грата, за исключением того, что вместо режущих кругов используются шлифовальные круги. Эти колеса перемалывают шарики так, чтобы они были круглыми и имели размер в пределах нескольких десятитысячных дюйма от их конечного размера.
- 7 После этого шарики перемещаются в притирочный станок с чугунными колесами, в котором используется та же абразивная притирочная паста, что и на беговых дорожках. Здесь они будут притираться в течение 8-10 часов, в зависимости от того, для какой точности подшипника они изготавливаются.
И снова в результате получается чрезвычайно гладкая сталь.
- 8 Стальные клетки штампуются из довольно тонкого листового металла, как формочки для печенья, а затем сгибаются до окончательной формы в штампе. Матрица состоит из двух кусков стали, соединенных вместе, с отверстием в форме готовой детали, вырезанным внутри. Когда клетка помещается между ними и матрица закрывается, клетка изгибается по форме внутреннего отверстия. Затем штамп открывается, и готовая деталь вынимается, готовая к сборке.
- 9 Пластиковые сепараторы обычно изготавливаются методом литья под давлением. В этом процессе полая металлическая форма заполняется путем впрыскивания в нее расплавленного пластика и позволяет ему затвердевать. Форма открывается, и готовая клетка вынимается, готовая к сборке.
- 10 Теперь, когда все детали готовы, нужно собрать подшипник. Во-первых, внутренняя обойма помещается внутрь внешней обоймы, только в одну сторону, насколько это возможно.
Это делает пространство между ними на противоположной стороне достаточно большим, чтобы вставлять между ними мячи. Вставляется необходимое количество шариков, затем обоймы перемещаются так, чтобы они обе располагались по центру, а шарики равномерно распределялись по подшипнику. На этом этапе устанавливается клетка, удерживающая шары друг от друга. Пластиковые сепараторы обычно просто защелкиваются, в то время как стальные сепараторы обычно вставляются и склеиваются вместе. Теперь, когда подшипник собран, он покрыт средством от ржавчины и упакован для транспортировки.
Контроль качества
Изготовление подшипников — дело очень точное. Испытания проводятся на образцах стали, поступающей на завод, чтобы убедиться, что в ней содержится нужное количество легированных металлов. Испытания на твердость и ударную вязкость также проводятся на нескольких этапах процесса термообработки. По пути также проводится множество проверок, чтобы убедиться, что размеры и формы правильные. Поверхность мячей и места, где они катятся по беговым дорожкам, должны быть исключительно гладкими. Шарики не могут быть некруглыми более чем на 25 миллионных дюйма, даже для недорогого подшипника. Для высокоскоростных или прецизионных подшипников допускается только пять миллионных долей дюйма.
Будущее
Шариковые подшипники будут использоваться еще много лет, потому что они очень просты и стали очень недорогими в производстве. Некоторые компании экспериментировали с изготовлением мячей в космосе на космическом челноке. В космосе капли расплавленной стали можно выплюнуть в воздух, а невесомость позволяет им парить в воздухе. Капли автоматически превращаются в идеальные сферы, пока они остывают и затвердевают. Однако космические путешествия по-прежнему дороги, поэтому на земле можно сделать много полировки по цене одного «космического шара».
Однако на горизонте появляются и другие виды подшипников. Подшипники, в которых два объекта никогда не соприкасаются друг с другом, эффективны в эксплуатации, но их сложно изготовить. В одном из них используются магниты, которые отталкиваются друг от друга и могут использоваться для удержания предметов друг от друга. Так строятся поезда «маглев» (для магнитной левитации). Другой тип нагнетает воздух в пространство между двумя плотно прилегающими поверхностями, заставляя их парить друг от друга на подушке сжатого воздуха. Однако оба этих подшипника намного дороже в изготовлении и эксплуатации, чем скромный, надежный шарикоподшипник.
Как изготавливаются шарикоподшипники
Главная » Блог » Как изготавливаются шариковые подшипники Круглые предметы, такие как шарикоподшипники, всегда использовались для облегчения работы. Существует множество типов подшипников качения, которые также бывают самых разных размеров. Чаще всего шарикоподшипники можно держать на ладони.
Изучая, как изготавливаются шарикоподшипники, мы должны сначала обратить внимание на используемые материалы. Большинство шарикоподшипников изготовлены из стали. Этот материал используется из-за его устойчивости к нагрузкам. Для достижения необходимых отраслевых стандартов сталь, используемая для шарикоподшипников, может быть закалена или сделана более жесткой с помощью термической обработки. В то время как в некоторых новых подшипниках теперь используются литые пластиковые сепараторы из соображений экономии, многие сепараторы традиционно изготавливаются из тонкой стали.
Процесс производства шарикоподшипников можно разбить на четыре компонента: наружное кольцо, внутреннее кольцо, шарики качения и формирование сепаратора.
1-2. Обоймы
Внутренние и внешние обоймы изготавливаются с использованием одинакового процесса. Начиная со стальных труб, инструменты для механической резки разрезают трубы немного больше, чем форма дорожки. Разрез сделан больше, чтобы обеспечить усадку во время термообработки, когда температура в печи установлена примерно на 1550 градусов по Фаренгейту. После того, как грубая гонка провела несколько часов в печи, ее погружают в масляную ванну для охлаждения и затвердевания. После завершения процесса термообработки беговые дорожки обрабатываются с помощью шлифовальных кругов для получения окончательной гладкой поверхности.
3. Шарики
Более сложный процесс, чем формирование гонок, шары изготавливаются из толстой проволоки. Проволока, подаваемая из рулона сырья, затем проходит процесс холодной высадки. В результате этого процесса на центральной линии мяча образуется выпуклость, которую необходимо удалить. Затем шарики перемещаются в канавки, расположенные между одним вращающимся и одним неподвижным чугунным диском. Затем созданное трение удаляет вспышку/выпуклость. На протяжении всего этого процесса шарики немного увеличиваются в размерах из-за термической обработки. Подобно термообработке гонок, шарики закаляются и делаются жесткими. После термической обработки шарики снова помещают в аналогичный процесс между двумя дисками, принимая теперь, что круги являются шлифовальными, а не режущими кругами, принимая шарики в пределах нескольких десятитысячных дюйма от окончательного размера.