Как класть сварочный шов: Как правильно класть красивый сварочный шов электросваркой?
alexxlab | 21.03.2023 | 0 | Разное
Обратноступенчатый способ сварки длинных швов • PROFNASTILI.RU
Этот метод используется при выполнении одно- и двухслойных швов длиной выше 800 мм, также при наложении слоев секционным и другими методами сварки мультислойных швов. Способ уменьшает остаточные сварочные напряжения и деформации.
Длинноватые швы делают обратноступенчатым методом от середины к краям (рис. 25, г). Этот способ уменьшает сварочные напряжения и деформации. При сварке металла большой толщины шов делают за несколько проходов слоями или валиками.
Практика показала, что при сварке слоями внутренние напряжения и, следовательно, деформации снижаются в большей степени, чем при сварке валиками.
Сварка двойным слоем (рис. 25, д) предназначается в основном для наложения первых слоев шва в жестких конструкциях или на сталях с повышенной склонностью к трещинообразованию. Такой способ позволяет выполнять корневые слои шва с увеличенным поперечным сечением и обеспечивает снижение скорости охлаждения накладываемых участков шва. При сварке двойным слоем на первый шов длиной 150—200 мм немедленно (после очистки от шлака) накладывается второй слой. В такой же последовательности сваривают шов и на всех других участках.
С целью сокращения времени между наложением отдельных слоев при многослойной сварке разделку рекомендуется заполнять каскадным методом или горкой (рис. 25, е). Сварку осуществляют таким образом, чтобы каждый последующий шов частично накладывался на еще не остывший металл предыдущего слоя. Сварка горкой — разновидность каскадного способа. При большой длине шва сварку ведут от середины к краям одновременно 2 сварщика.
Сварку каскадом или горкой рекомендуется использовать для стали большой толщины и стали, обладающей повышенной склонностью к развитию трещин. Этот способ сварки снижает объемные сварочные напряжения в соединениях и уменьшает скорость охлаждения металла шва.
Сварку секциями (рис. 25, ж) следует применять при выполнении протяженных многослойных швов на стали толщиной более 20 мм и особенно стали, склонной к образованию трещин. Этот способ сварки уменьшает остаточные сварочные напряжения и деформации, а также снижает скорость охлаждения металла шва. При сварке секциями многослойный шов выполняют отдельными участками длиной 500—800 мм. Каждую секцию можно сваривать обратноступенчатым способом, двойным слоем или каскадом. Сварку секциями рекомендуется выполнять без длительных перерывов до окончания сварки всего шва.
Сварочные работы: Практическое пособие для электрогазосварщика (24 стр.)
Рис. 66. Способы выполнения шва: а – сварка швов “на проход”; б – сварка швов средней длины; в – сварка швов обратноступенчатым способом; г, д – сварка длинных швов
Короткие швы по длине обычно сваривают “на проход” (рис. 66, а). Швы средней длины сваривают от середины к краям (рис. 66, б) либо обратноступенчатым способом (рис. 66, в). Длинные швы однопроходных стыковых соединений и первый проход многопроходных швов сваривают от середины к концам обратноступенчатым способом (рис. 66, г), а в соединениях с угловыми швами также от середины к концам обратноступенчатым способом (рис. 66, д).
Обратноступенчатая сварка является наиболее эффективным методом уменьшения остаточных напряжений и деформаций.
Предыдущий шов остывает до температуры 200-300 °С. При охлаждении одновременно с уменьшением ширины шва уменьшается и первоначально расширенный зазор, именно поэтому остаточные деформации становятся минимальными.
При сварке стыковых или угловых швов большого сечения шов выполняется несколькими слоями (рис. 67). При этом каждый слой средней и верхней части шва может выполняться как за один проход (рис. 67, а), так и за два и более проходов (рис. 67, б).
С точки зрения уменьшения остаточных деформаций сварка за один проход предпочтительнее. Если ширина шва достигает 14-16 мм, то чаще применяется многопроходный способ сварки швов.
Классификация швов в зависимости от длины
Средними – от 300 до 1000 мм. Дистанцию делят на несколько зон, каждую сваривают в направлении, противоположном предыдущей. Протяжённость соединений выбирают так, чтобы на них уходило от 2 до 3 целых электродов.
Длинные – больше 1000 мм. Делают обратноступенчатым способом от середины к краям. Соединения такой протяжённости применяют в судостроении и при изготовлении резервуаров большого объёма.
Сварка швов различной протяженности: а — от середины к краям шва; б — обратно-ступенчатым способом от одного конца шва к другому; в, г — обратно-ступенчатым способом от середины к краям шва; д — обратно-ступенчатым способом от середины к краям шва вразбивку
Сварка Обратно-ступенчатым способом электродом.Сварка тонкого меттала без деформаций
Обратный провод
Необходимо разбираться в такой тонкости, как обратный провод, и что допустимо применять в его качестве при сварке. Обратный провод при сварочных работах — это провод, обеспечивающий соединение с источниками тока. В качестве него используются:
- провода — жесткие и гибкие;
- шины в виде полосок минимального сечения 40х4 мм из стали или алюминия;
- сварочные плиты.
Обратный провод обязан иметь такую же изоляцию, как и прямой. Элементы, которые используются для него, должны быть надежно соединены между собой.
Обратноступенчатый способ сварки: суть и назначение
Производится несколькими сварщиками одновременно. Применяется для уменьшения деформаций при сварке большой протяжённости и для того, чтобы избежать коробления заготовок от перегрева.
Напряжения и деформации возникают от неравномерного охлаждения или в результате усадки сварочной ванны в процессе охлаждения. Усадка вызывает деформации в прилегающем к ванне металле.
При автоматическом техпроцессе – однослойных швов любой длины, а также при ручной сварке – коротких, до 300 мм, швы заваривают с начала до конца, способ называют – напроход. Обратноступенчатый метод, как правило, подразумевает разбивку на участки от 100 до 300 мм.
Преимущества метода
Важно понимать, для каких целей используется схема обратноступенчатой сварки. Обратноступенчатая сварка является эффективным методом сведения к минимуму деформаций и напряжений, возникающих при работе. Кроме того, такой способ помогает избегать коробления свариваемых деталей.
Напряжение внутри детали появляется вследствие неодинакового нагревания и понижения температуры различных ее частей, когда происходит их сжатие и расширение. Уменьшение размеров сварочной ванны как следствие ее усадки может привести к деформациям частей металлических изделий, граничащих со швом. Это происходит потому, что при остывании она сужается, что приводит к растягиванию ближайших слоев металла и появлению в них перекосов.
При грамотном выполнении работы напряжения внутри хотя и присутствуют, но сильных деформаций свариваемых изделий не вызывают. Данный способ уменьшает внутренние напряжения. При наложении соседних маленьких участков шва деформации в них имеют противоположные направления.
Способы выполнения сварочных швов различной длины
Размер каждого захвата определяют так, чтобы ушло целое число электродов. Делают это для того, чтобы сварочная ванна прогревалась равномерно. Если металл тонкий – швы короче, толстый – длиннее. Разновидности обратноступенчатой сварки:
Чтобы избежать деформации, используют электроды большего диаметра и большую величину тока. Вертикальный нахлёсточный и кольцевой тавровый шов делают с двух сторон обратноступенчатым способом.
Заготовки толщиной больше средней соединяют многослойными швами. При этом первый – непрерывный, последующие – обратноступенчатые, секциями. Концы участков в смежных слоях совпадать не должны, их сдвигают на 15-20 мм из-за того, что в конечных точках вероятны шлаковые включения и непровары.
Железная лаборатория
Сварочные напряжения и деформации иметь в стальных конструкциях нежелательно, так как слишком большие сварочные напряжения могут стать причиной появления трещин в швах, с переходом их на основной металл. Деформации искажают геометрическую форму элементов, что приводит либо к снижению их прочности, либо усложняет монтаж. Полностью устранить сварочные напряжения и деформации невозможно. Изучение характера и причин образования сварочных напряжений и деформаций позволило разработать мероприятия значительно снижающие их. При сборке и сварке необходимо выполнять следующие основные конструктивные и технологические мероприятия. 1. В проектах стальных конструкций не следует назначать завышенное сечение сварных швов. Раскрытие фасок в стыковых швах должно быть минимально допустимым по техническим условиям. Во время сварки нельзя допускать увеличения сечения швов по сравнению с проектом. 2. При сварке листовых конструкций нужно применять преимущественно стыковые швы, а не нахлесточные, так как в нахлесточных швах неравномерно распределяется силовой поток. 3. Швы необходимо располагать симметрично относительно центральной оси элемента, чтобы сварочные напряжения могли уравновешиваться. 4. Части конструкций, геометрическая форма которых должна быть сохранена без искажения, надо закреплять для сварки в жестких кондукторах и приспособлениях, в которых они должны находиться до полного остывания изделия. 5. В случаях несимметричного расположения швов относительно центральной оси изделия конструкциям или деталям нужно придавать предварительные выгибы, противоположные тем, которые образуются после сварки.
Сварку длинных швов производят обратноступенчатым способом. Шов делят на участки длиной 150—200 мм. При однослойном шве сварку ведут от середины к концам отдельными участками, как указано на рисунке, сварку многослойных швов выполняют каскадами.
а — обратноступенчатый способ, б — сварка каскадом
При сварке стыка в прокатных двутавровых балках и швеллерах надо сначала заваривать стенку, а затем полки. 8. При сварке труб, состоящих из нескольких обечаек, в первую очередь должны завариваться продольные стыки и только после этого заваривать кольцевые швы. 9. При сборке стержней Н-образного сечения необходимо сначала собрать отдельно стенки и полки деталей, из которых они состоят, заварить стыки, зачистить на полках швы в местах примыкания стенки и только после этого собирать из листов стержни элемента. 10. При заварке стыка в стержнях двутаврового составного сечения следует продольные швы, прикрепляющие полки к стенке стержня, не доводить до стыка на 500—700 мм. Сначала заваривают стык вертикальной стенки, затем сваривают стыки полок и в последнюю очередь заваривают участки швов, соединяющих стенку с полками.
При приварке уголков решетки к фасонкам или к поясным уголкам в решетчатой конструкции надо вести сварку в направлении к концу уголка, как указано стрелками на рисунке.
а — заварка стыка в листовом стержне Н-образного сечения, б — приварка уголков в узле фермы
Приварку ребер жесткости следует вести от середины к концам. 13. Заварку трещины в металле следует вести только после предварительной подготовки ее к заварке. Сначала надо трещину максимально раскрыть. Существует два способа раскрытия трещины: механический и тепловой. В обоих случаях в конце шва засверливается два отверстия, чтобы устранить концентрацию напряжений и не допустить дальнейшее распространение трещины.
READ Замена фурнитуры на балконной двери
При механическом способе раскрытия трещины с обеих ее сторон приваривают по два уголка, которые с наибольшим усилием стягивают болтами. При этом в зоне трещины возникают упругие растягивающие напряжения. Затем трещину заваривают и болты снимают, в результате чего раздвинутые кромки трещины беспрепятственно смещаются в первоначальное положение при одновременной усадке остывающего шва.
а — механический способ раскрытия трещины, б — тепловой способ раскрытия трещины
Тепловой способ заключается в раскрытии трещины путем нагрева до температуры 150—200° участка металла за концами трещины. Нагрев производится газовыми горелками. Металл в нагретых зонах стремится расшириться, в зоне трещины создаются сжимающие напряжения, вследствие чего кромки трещины расходятся. Нагревая металл, необходимо следить, чтобы кромки трещины не нагревались. Охлаждение кромок производится прикладыванием влажных асбестовых жгутов. После заварки трещины шов остывает одновременно с нагретыми участками металла. Кромки трещины сближаются, снижая напряжение в сокращающемся шве.
Виды швов в зависимости от длины (протяженности)
Короткие швы имеют длину до 300 мм. Средняя длина шва составляет от 300 до 1000 мм. Швы длиной более 1000 мм называют длинными или швами большой протяженности. Каждый вид имеет свои особенности, о которых нужно знать в процессе сварочных работ.
Короткие сварные швы варятся в одном направлении. Средние швы разделяются на несколько зон, каждая из которых сваривается в направлении, противоположном предыдущему. В этом случае нужно выбрать такую длину зоны, чтобы на ней можно было использовать от двух до четырех электродов. Для варки средних по протяженности швов может использоваться обратноступенчатый способ сварки. Использование длинных швов происходит в резервуаростроении, судостроении. В этом случае также используется обратноступенчатая сварка.
Обратноступенчатая сварка используется для минимизации сварочных деформаций и напряжений при сварочных работах со швами средней и большой длины, а также во избежание коробления деталей.
Большая Энциклопедия Нефти и Газа
Обратноступенчатый способ сварки применяют для однослойных и многослойных швов. [1]
При многослойном обратноступенчатом способе сварки начала и концы отдельных ступеней в каждом проходе следует смещать относительно предыдущих на 20. 40 мм. [3]
При сварке длинных швов листовых конструкций применяют обратноступенчатый способ сварки. [4]
Способ, показанный на рис. 60 д, предпочтителен, называется он так: обратноступенчатый способ сварки от середины к краям шва вразбивку. [5]
Выверка осей обечаек при сборке. [6] |
Для избежания возникновения значительных деформаций необходимо соблюдать следующие правила: применять электроды большого диаметра и большие величины тока; вести сварку одновременно двумя сварщиками; применять обратноступенчатый способ сварки. [7]
При автоматической сварке однослойных швов любой длины и при сварке коротких швов ( до 300 мм) вручную их заваривают от начала до конца. напроход. При обратноступенчатом способе сварки весь шов разбивают на отдельные участки длиной 100. 300 мм. [9]
Во время сварки и особенно наплавки необходимо избегать непрерывного подвода тепла в одном направлении. Для этой цели используется обратноступенчатый способ сварки, сварка и наплавка вразброс. При наплавке больших поверхностей их разбивают на ряд равносторонних треугольников или прямоугольников с длиной сторон 130. 150 мм. Каждую из таких маленьких площадок наплавляют паралелельными валиками, но при переходе от площадки к площадке направление наплавляемых валиков изменяют. Рекомендуется наплавка с перерывами. В этом случае исключается возможность непрерывного и интенсивного нарастания внутренних напряжений и деформаций. [10]
Сварку ведут от центра к краям. Лучшие результаты получаются при обратноступенчатом способе сварки. [11]
При монтаже решетчатых металлических конструкций монтажные швы сваривают ручной электродуговой сваркой, полуавтоматической порошковой проволокой и в защитной среде углекислого газа. При сварке рельсов подкрановых путей применяют ванную сварку. При этом сварку низкоуглеродистых сталей выполняют во всех пространственных положениях электродами Э42, Э42А, Э46 и Э50 с применением существующих приемов и технологии ручной электродуговой сварки. поперечного колебания электрода поперек угла раскрытия шва, обратноступенчатого способа сварки длинных швов, сварки горкой и каскадным методом, а также сварки углом назад и вперед. Сварку порошковой проволокой применяют только в нижнем положении. [12]
READ Тканевый натяжной потолок своими руками
Длину участка выбирают такой, чтобы провести сварку целым чис. Лом электродов. При сварке тонкого металла участки делают короче, при сварке более толстого. длиннее. Сварку каждого участка ( ступени) ведут в направлении, обратном общему направлению сварки. Обратноступенчатый способ сварки имеет несколько разновидностей. Швы средней длины сваривают обратноступенчатым способом от одного конца шва к другому. Сварка каждой ступени производится в направлении предыдущего сваренного участка таким образом, что конец каждой ступени сваривают с началом предыдущей. [13]
Можно также взять флюс, состоящий из смеси 50 % буры и 50 % борной кислоты или 80 % буры и 20 % окиси кремния. Флюс замешивается на воде до консистенции сметаны. На кромки изделия он наносится за 15. 20 мин до сварки. Наносить флюс необходимо с лицевой и с обратной сторон кромок. Для уменьшения коробления применяется обратноступенчатый способ сварки, причем начинают сварку на расстоянии 75. 100 мм от края изделия. Желательно также св-арку вести на медной или стальной подкладке, что усиливает отвод тепла от шва. Сварку следует вести быстро и в один проход, колебаний проволокой не производить. Сварочная ванна должна быть покрыта тонким слоем шлака, а конец проволоки. погружен в ванну. Сварка производится как левым, так и правым способами. [14]
После приемки узлов конденсатора-холодильника производят сортировку узлов и деталей ящика с учетом последовательности их сборки и монтажа. Сборку ящика начинают со сборки днища. Листы днища собирают встык с зазором 3. 4 мм на прихватках через 300. 400 мм. По окончании сборки днища листы днища сваривают с применением главным образом полуавтоматической или автоматической сварки. Швы сваривают без разделки кромок на остающейся стальной подкладке толщиной 2. 3 мм и шириной 300. 400 мм, которую прихватывают перед стыковкой листов. Сварку ведут от центра к краям. Лучшие результаты получаются при обратноступенчатом способе сварки. [15]
Pereosnastka.
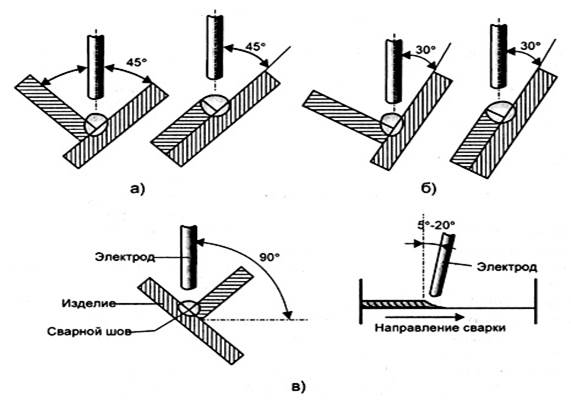
Сварные швы по протяженности делят на три группы. Протяженность сварных швов имеет большое значение для выбора порядка их выполнения.
Короткие швы сваривают способом «на проход», т. е. непрерывным движением дуги от одного конца шва к другому в одном направлении. При многослойной сварке каждый последующий слой накладывают в направлении, противоположном предыдущему.
Швы средней длины сваривают от середины шва к краям, либо обратноступенчатым способом. Такой порядок наложения швов уменьшает внутренние напряжения и деформации. Деформации, возникающие при наложении двух соседних коротких швов, имеют противоположное направление.
Обратноступенчатый способ сварки заключается в том, что весь шов разбивают на участки длиной 200—300 мм (ступени). Длину участка выбирают такой, чтобы провести сварку целым числом электродов. При сварке тонкого металла участки делают короче, при сварке более толстого — длиннее. Сварку каждого участка (ступени) ведут в направлении, обратном общему направлению сварки. Обратноступенчатый способ сварки имеет несколько разновидностей. Швы средней длины сваривают обратноступенчатым способом от одного конца шва к другому. Сварка каждой ступени производится в направлении предыдущего сваренного участка таким образом, что конец каждой ступени сваривают с началом предыдущей.
Швы большой протяженности сваривают обратноступенчатым способом от середины к краям. Если сварку выполняет один сварщик, то он накладывает швы в очередности, показанной на рис. 1 в.
Способ, показанный на рис. 60 д, предпочтителен, называется он так: обратноступенчатый способ сварки от середины к краям шва вразбивку. Если сварку выполняют два сварщика, то они накладывают швы в очередности, показанной на рис. 1 г.
При сварке обратноступенчатый способом многослойных швов концы участков (ступеней) в смежных слоях не должны совпадать, и их необходимо сдвигать на 15—20 мм, Это делают потому, что в точках начала и конца швов наиболее вероятно появление дефектов (непроваров, шлаковых включений). Каждый последующий слой следует выполнять в направлении, противоположном предыдущему.
Sources:
https://elsvarkin.ru/texnologiya/obratnostupenchataya-svarka/ https://samsvar.ru/stati/obratnostupenchatyj-sposob-svarki.html
Обратноступенчатая сварка
95. Обратноступенчатая сварка
Сварка, при которой сварной шов выполняется следующими один за другим участками в направлении, обратном общему приращению длины шва
5.1.11 обратноступенчатая сварка:
Сварка, при которой короткие участки шва выполняют в направлении, обратном общему приращению длины шва, итак, чтобы конец одного участка перекрывал начало предыдущего участка (см. рисунок 54).
1
– газовое пламя;
2
– заготовка;
3
– присадочный пруток;
Рисунок 54 – Обратноступенчатая сварка
Словарь-справочник терминов нормативно-технической документации . academic.ru . 2015 .
Смотреть что такое “Обратноступенчатая сварка” в других словарях:
обратноступенчатая сварка — Сварка, при которой сварной шов выполняется следующими один за другим участками в направлении, обратном общему приращению длины шва. [ГОСТ 2601 84] [Терминологический словарь по строительству на 12 языках (ВНИИИС Госстроя СССР)] Тематики сварка,… … Справочник технического переводчика
Сварка обратноступенчатая — – сварка, при которой сварной шов выполняется следующими один за другим участками в направлении, обратном общему приращению длины шва. [ГОСТ 2601 84] Рубрика термина: Сварка Рубрики энциклопедии: Абразивное оборудование, Абразивы,… … Энциклопедия терминов, определений и пояснений строительных материалов
Сварка — – получение неразъемных соединений посредством установления межатомных связей между соединяемыми частями при их нагревании и (или) пластическом деформировании. [ГОСТ 2601 84] Сварка – получение неразъемных соединений посредством… … Энциклопедия терминов, определений и пояснений строительных материалов
сварка блоками — Обратноступенчатая сварка, при которой многослойный шов выполняют отдельными участками с полным заполнением каждого из них [ГОСТ 2601 84] [Терминологический словарь по строительству на 12 языках (ВНИИИС Госстроя СССР)] Тематики сварка, резка,… … Справочник технического переводчика
СВАРКА БЛОКАМИ — обратноступенчатая сварка, при которой многослойный шов выполняют отдельными участками с полным заполнением каждого из них (Болгарский язык; Български) многослойно заваряване по отделни участъци (Чешский язык; Čeština) svařování po blocích… … Строительный словарь
Сварка — 1. Сварка Получение неразъемных соединений посредством установления межатомных связей между соединяемыми частями при их нагревании и (или) пластическом деформировании Источник: ГОСТ 2601 84: Сварка металлов. Термины и определения основных понятий … Словарь-справочник терминов нормативно-технической документации
Сварка блоками — 96. Сварка блоками Обратноступенчатая сварка, при которой многослойный шов выполняют отдельными участками с полным заполнением каждого из них Источник: ГОСТ 2601 84: Сварка металлов. Термины и определения основных понятий … Словарь-справочник терминов нормативно-технической документации
СВАРКА ОБРАТНОСТУПЕНЧАТАЯ — сварка, при которой сварной шов выполняется следующими один за другим участками в направлении, обратном общему приращению длины шва (Болгарский язык; Български) обратностьпаловидно заваряване (Чешский язык; Čeština) svařování vratným krokem… … Строительный словарь
ГОСТ Р ИСО 857-1-2009: Сварка и родственные процессы. Словарь. Часть 1. Процессы сварки металлов. Термины и определения — Терминология ГОСТ Р ИСО 857 1 2009: Сварка и родственные процессы. Словарь. Часть 1. Процессы сварки металлов. Термины и определения оригинал документа: 6.4 автоматическая сварка: Сварка, при которой все операции механизированы (см. таблицу 1).… … Словарь-справочник терминов нормативно-технической документации
ГОСТ 2601-84: Сварка металлов. Термины и определения основных понятий — Терминология ГОСТ 2601 84: Сварка металлов. Термины и определения основных понятий оригинал документа: 47. Cвapкa трением Сварка с применением давления, при которой нагрев осуществляется трением, вызванным относительным перемещением свариваемых… … Словарь-справочник терминов нормативно-технической документации
Главная>>Способы сварки>>Ручная дуговая сварка>>Сварка швов в нижнем положении Сварка швов в нижнем положении наиболее технологична, и проста для выполнения. ![]() Кроме того, сварка в нижнем положении способствует выходу газов и шлака на поверхность сварочной ванны. Из-за лёгкого выделения шлака и газов, качество сварного соединения получается наиболее высоким. Исходя из этого, для повышения качества сварки, рекомендуется ручную дуговую сварку выполнять в нижнем положении, если это возможно. Рекомендуемый порядок выполнения сварных швов — слева направо, или на себя. Такая техника ручной дуговой сварки позволяет рабочему-сварщику постоянно контролировать место соединения, длину электрической дуги, движение электрода и формирование сварного шва. Обычно, ширина валика составляет 3-4 диаметра электрода. |
Толщина заготовок, мм | 1-2 | 3-5 | 4-10 | 12-24 | 30-60 |
Диаметр стержня | 2-3 | 3-4 | 4-5 | 5-6 | 6-8 |
Значения являются примерными, поскольку они зависят от множества факторов. Например, при работе с потолочными швами не стоит применять элементы диаметром более 4 мм. Не пользуются такими стержнями и при многопроходной сварке. Это способствует неравномерному провару кромок.
Сварка стыковых швов в нижнем положении
Сварка стыковых швов без скоса кромок, при сварке в нижнем положении, производится наплавкой валика вдоль стыка с небольшим расширением в стороны. Сварной шов выполняют с небольшим усилением. Величина усиления, обычно, составляет 2мм. Изделие сваривают с двух сторон. После проварки соединения с одной стороны, изделие переворачивают, производят очистку от наплывов и шлака и сваривают с обратной стороны, используя аналогичную технику сварки.
Сварку стыковых швов при толщине свариваемого металла мене 8мм, допускается выполнять одним слоем за один проход. Если толщина превышает 8мм, сварка металла выполняется в несколько слоёв. При этом, необходимо первый слой выполняют высотой 3-5мм электродом, диаметром 3-4мм. Для выполнения последующих слоёв выбирают электроды диаметром 4-5мм.
До выполнения очередного слоя, разделку кромок очищают при помощи металлической щётки от шлака, металлических брызг и грата. После того, как вся разделка окажется заполненной, изделие переворачивают. Далее, в корне сварного шва делают небольшую канавку и затем её аккуратно заплавляют. Если нет возможности перевернуть изделие и выполнить подобную канавку и подварку с другой стороны, то к выполнению первого валика следует отнестись особенно внимательно.
Стыковые швы с X-образной разделкой, при сварке в нижнем положении, выполняют с обеих сторон аналогично сварке многослойных V-образных швов.
Преимущества и недостатки
В отличие от других способов сварки, тавровые соединения обладают следующими достоинствами:
- они формируют надежное соединение в труднодоступных местах;
- для них не нужно использовать укрепляющие накладки;
- применяются для сварки заготовок различной толщины;
- выдерживают большую нагрузку.
Недостатки:
- для соблюдения перпендикулярности детали нужно скреплять перед сваркой;
- односторонние швы ненадежны;
- при сварке тонкостенных деталей велика вероятность термодеформации;
- высок риск внутренних дефектов (непроваров, несплошностей, кратеров).
Сварка угловых швов в нижнем положении
Сварку угловых швов в нижнем положении рекомендуется производить «в лодочку». Если сварное соединение невозможно установить «в лодочку», то при выполнении сварки необходимо особенно внимательно проварить корень шва и проплавить свариваемые кромки. При этом сначала необходимо начать провар с поверхности нижней кромки, а затем, через разделку, переходить на вертикальную кромку, как показано на рисунке:
При выполнении многослойного шва, первый валик накладывают электродом, диаметром 3-4мм. При наплавке первого валика необходимо выполнить хороший провар с основным металлом для исключения появления дефектов в корне сварного шва. После наплавки валика перед тем, как наплавить следующий слой, необходимо произвести зачистку предыдущего валика. После зачистки накладывают последующие слои.
Более подробно техника выполнения угловых и стыковых швов отдельно рассмотрена на страницах «Сварка угловых швов. Техника выполнения углового сварного шва» и «Сварка стыковых швов. Техника выполнения сварных стыковых швов». Рекомендуем ознакомиться с ними для получения полной информации об особенностях выполнения таких швов.
источник
Наиболее оптимальная технология
Лучшим для сварки угловых соединений считается метод «в лодочку». Такая технология позволяет дуге доставать до корня. При этом нужно правильно закреплять заготовки. Угол между свариваемыми краями должен быть прямым.
Сварку начинают снизу, постепенно сдвигая сварочную ванну вверх. Перед тем как варить, нужно изучить схему движения стержня. При толщине деталей менее 1,4 см скашивать кромки необязательно. Края более толстых заготовок срезают.
Установить детали для сварки «в лодочку» правильно удается не всегда.
При использовании иной технологии обращают внимание на катет шва. При его длине до 8 мм делают однослойное соединение.
При большей величине шов должен быть многопроходным. На первом этапе проваривают корень, используя тонкий электрод. После этого выполняют следующие проходы.
Техника сварки в нижнем положении
Это пространственное положение позволяет получать сварные швы наи-более высокого качества, так как облегчает условия выделения неметалличес-ких включений, газов из расплавленного металла сварочной ванны. При этом также наиболее благоприятны условия формирования металла шва, так как рас-плавленный металл сварочной ванны от вытекания удерживается нерасплавив-шейся частью кромок.
Стыковые швы сваривают без скоса кромок или с V-, Х- и U-об-разным скосом. Положение электрода относительно поверхности изделия и готового шва показано на рис. 14.
Рисунок 14– Положение электрода при сварке в нижнем положении:
а — поперек оси шва; б — сбоку
Стыковые швы без скоса кромок в зависимости от толщины сваривают с одной или двух сторон. При этом концом электрода совершают поперечные колебания (см. рис. 12) с амплитудой, определяемой требуемой шириной шва. Следует тщательно следить за равномерным расплавлением обеих свариваемых кромок по всей их толщине и особенно стыка между ними в нижней части (корня шва).
Однопроходную сварку с V-образным скосом кромок обычно выполняют с поперечными колебаниями электрода на всю ширину разделки для ее заполнения так, чтобы дуга выходила со скоса кромок на необработанную поверхность металла. Однако в этом случае очень трудно обеспечить равномерный провар корня шва по всей его длине, особенно при изменении величины притупления кромок и зазора между ними.
При сварке шва с V-образным скосом кромок за несколько проходов обе-спечить хороший провар первого слоя в корне разделки гораздо легче. Для этого обычно применяют электроды диаметром 3—4 мм и сварку ведут без поперечных колебаний. Последующие слои выполняют в зависимости от толщины металла электродом большего диаметра с поперечными колебаниями. Для обеспечения хорошего провара между слоями предыдущие швы и кромки следуеттщательно очищать от шлакаи брызг металла.
Заполнять разделку кромокможно швами с шириной на всю разделку или отдельными валиками (рис. 15). В многопроходных швах последний валик (11на рис.15, в)
для улучшения внешнего вида иногда можно выполнять на всюширину разделки (декоративный слой).
а— однопроходных; б — многослойных; в— многопроходных;
Рисунок 15– Поперечные сечения стыковых швов
Сварку швов с Х- или U-образным скосом кромок выполняют в общемтак же, как и с V-образным скосом. Однако для уменьшения остаточных де-формаций и напряжений, если это возможно, сваркуведут, накладывая каждый валик или слой попеременно с каждой стороны. Швы с Х- или U-образным ско-сом кромок по сравнению с V-образным имеют преимущества, так как в первом случае в 1,6—1,7 раза уменьшается объем наплавленного металла (повышается производительность сварки). Кроме того, уменьшаются угловые деформации, а возможный непровар корня шва образуется в нейтральном по отношению к из-гибающему моменту сечении. Недостаток U-образного скоса кромок – повы-шенная трудоемкость его получения.
Сварку стыковых швов можно выполнять различными способами (рис. 16). При сварке на весу наиболее трудно обеспечить провар корня шва и фор-мирование хорошего обратного валика по всей длине стыка. В этом отношении более благоприятна сварка на съемной медной или остающейся стальной подк-ладке. В медной подкладке для формирования обратного валика делают форми-рующую канавку. Однако для предупреждения вытекания расплавленного ме-талла из сварочной ванны необходимо плотное поджатие подкладок к сварива-емым кромкам. Кроме того, остающиеся подкладки увеличивают расход ме-талла и не всегда технологичны. При использовании медных подкладок воз-никают трудности точной установки кромок вдоль формирующей канавки. Ес-ли с обратной стороны возможен подход к корню шва и допустимо усиление обратной стороны шва, целесообразна (рис. 16, г)
подварка корня швом не-большого сечения с последующей укладкой основного шва. В некоторых слу-чаях при образовании непроваров в корне шва после сварки основного шва дефект в корне разделывают газовой, воздушно-дуговой строжкой или меха-ническими методами (рис. 16,
д)
с последующим выполнением подварочного шва.
а— на весу; б — на медной съемной подкладке; в— на остающейся стальной подкладке; г— с предварительным подварочным швом;
д — удаление непровара в корне шва для последующей подварки;
1— медная подкладка; 2— остающаяся подкладка; О— основной шов; П — подварочный шов
Сварку угловых швов в нижнем положении можно выполнять двумя при-емами. Сварка вертикальным электродом в лодочку (рис. 17, а)
обеспечивает наиболее благоприятные условия для провара корня шва и формирования его усиления.
Рисунок 17– Положение электрода и изделия при сварке:
а — в лодочку; б — таврового соединения; в— внахлестку; г— углового соединения
По существу этот прием напоминает сварку стыковых швов с V-об-разным скосом кромок, так как шов формируется между свариваемыми поверхностями. Однако при этом способе требуется тщательная сборкасоединения под сварку с минимальным зазоромв стыке для предупреждения вытеканияв него расплавленногометалла.
При сварке наклонным электродом (рис. 17, б — г)
трудно обеспечитьпровар шва по нижнейплоскости (ввиду натекания на нее расплавленного металла) и предупредить подрез на вертикальной плоскости(ввиду стекания расплавленного металла). Поэтому таким способом обычно сваривают швы с катетом до 6—8 мм. Присварке угловых швов наклонным электродом трудно также обеспечитьглубокий провар в корне шва, поэтому в односторонних и ш двусторонних швах без скоса кромок может образоваться непровар (рис. 18,
а),
который при нагружении шва послужит началомразвития трещин. Для предуп-реждения этого в ответственных соединениях при толщине металла 4 мм и более необходим односторонний скос, а при толщине 12 мм и более — двусторонний скоскромок.
При сварке наклонным электродом многопроходных швов первым вы-по-лняют шов на горизонтальной плоскости (рис. 18, б).
1-6 –последовательность наложения швов
Рисунок 18- Сварка угловых швов
Формирование последующего валика происходит с частичным удержани-ем расплавленного металла сварочной ванны нижележащимваликом. При свар-ке угловых швов применяют поперечные колебания электрода. Особенно важен правильный выбор их траектории при сварке наклонным электродом с целью предупреждения возникновения указанных выше дефектов.
Техника сварки на горизонтальной и потолочной плоскостях.
Сварка швов в положениях, отличающихся от нижнего, требует повы-шенной квалификации сварщика в связи с возможным под действием сил тя-жести вытеканием расплавленного металла из сварочной ванны или падением капель электродного металла мимо сварочной ванны. Для предотвращения этого сварку следует вести по возможности наиболее короткой дугой, в большинстве случаев с поперечными колебаниями.
Расплавленный металл в сварочной ванне от вытекания удерживается в основном силой поверхностного натяжения. Поэтому необходимо уменьшать ее размер, для чего конец электрода периодически отводят в сторону от ванны, давая возможность ей частично закристаллизоваться. Ширину валиков также уменьшают до двух-трех диаметров электродов. Применяют пониженную на 10—20% силу тока и электроды уменьшенного диаметра (для вертикальных и горизонтальных швов не более 5 мм, для потолочных не более 4 мм).
Рисунок 19 – Положение электрода при сварке швов:
а— вертикальных; б— потолочных; в— горизонтальных
Сварку вертикальных швов можно выполнять на подъем (снизу вверх, рис. 19, а)
или на спуск. При сварке на подъем нижележащий закристаллизовав-шийся металл шва помогает удержать расплавленный металл сварочной ванны. При этом способе облегчается возможность провара корня шва и кромок, так как расплавленный металл стекает с них в сварочную ванну, улучшая условия теплопередачи от дуги к основному металлу. Однако внешний вид шва — гру-бочешуйчатый. При сварке на спуск получить качественный провар трудно: шлак и расплавленный металл подтекают под дугу и от дальнейшего стекания удерживаются только силами давления дуги и поверхностного натяжения. В некоторых случаях их оказывается недостаточно, и расплавленный металл вы-текает из сварочной ванны.
Сварка горизонтальных стыковых швов (рис. 19, в)
более затруднена, чем вертикальных, из-за стекания расплавленного металла из сварочной ванны на нижнюю кромку. В результате возможно образование подреза по верхней кромке. При сварке металла повышенной толщины обычно делают скос только одной верхней кромки, нижняя помогает удерживать расплавленный металл в сварочной ванне. Сварка горизонтальных угловых швов в нахлесточных соединениях не вызывает трудностей и по технике не отличается от сварки в нижнем положении.
Сварка швов в потолочном положении (рис. 19, б)
наиболее сложна и ее по возможности следует избегать. Сварку выполняют периодическими ко-роткими замыканиями конца электрода на сварочную ванну, во время которых металл сварочной ванны частично кристаллизуется, что уменьшает объем сва-рочной ванны. В то же время расплавленный электродный металл вносится в сварочную ванну. При удлинении дуги образуются подрезы. При сварке этих швов ухудшены условия выделения из расплавленного металла сварочной ванны шлаков и газов. Поэтому свойства металла шва несколько ниже, чем при сварке в других пространственных положениях.
Техника сварки пробочных и прорезных соединений практически не отличается от рассмотренной выше техники сварки стыковых или угловых швов.
В зависимости от протяженности шва, толщины имарки металла, жестко-сти конструкции и т. д. применяют различные приемы последовательности сварки швов и заполнения разделки (рис. 20).
а — напроход; б — от середины к концам; в — обратноступенчато;
г — блоками; д— каскадом; е —
горкой;
А— направление заполнения разделки. Стрелками указаны по-следовательность и направление сварки в каждом слое (1—5)
Сварку напроход обычно применяют при сварке коротких швов (до 500 мм). Швы длиной до 1000 мм лучше сваривать от середины к концам или об-ратноступенчатым методом. При последнем способе весь шов разбивают на участки по 150—200 мм, которые должны быть кратны длине участка, наплав-ляемого одним электродом. Сварку швов в ответственных конструкциях боль-шой толщины выполняют блоками, каскадом или горкой, что позволяет влиять на структуру металла шва и сварного соединения и его механические свойства.
Способы повышения производительности.Применение электродов диаметром более 8 мм обычно не позволяет повысить производительность процесса, так как увеличивающийся при этом вес электрода и держателя (в связи с повышением силы сварочного тока) приводит к быстрому утомлению сварщика. То же наблюдается при ручной дуговой сварке трехфазной дугой. Эти способы могут находить ограниченное применение при ванной сварке стержней арматуры железобетонных конструкций. Однако и здесь предпочтительнее применение одного электрода.
При ванной сварке расплавление основного металла осуществляется ду-гой и частично за счет теплоты, передаваемой изделию перегретым жидким металлом сварочной ванны (рис. 21). Поэтому сварку проводят при повышен-ной силе тока. Стык стержней собирают с зазором в формах: стальной оста-ющейся (из металлической полосы) или медной съемной многократного ис-пользования, или графитовой одноразового использования.
1 – стержни; 2— форма; 3 –
прихватки
Рисунок 21– Сборка под ванную сварку
горизонтальных стержней арматуры
Сварку начинают в нижней части формы, расплавляя дугой нижние кромки стыка. До окончания сварки металл в верхней части сварочной ванны стараются поддерживать в расплавленном состоянии на возможно большую глубину и обязательно на всю ширину разделки и формы. Шов наплавляют несколько выше поверхности стержней. Процесс проводят вручную, хотя и были попытки создания установок для механизированной сварки, в которых расплавление электрода происходило автоматически, а их смена выполнялась вручную. Однако установки оказались сложными в эксплуатации и малопроизводительными.
Повышение производительности процесса достигается также применением электродов, содержащих в покрытии железный порошок. С применением этих электродов сварка возможна только в нижнем положении, так как при сварке в других пространственных положениях увеличенный размер сварочной ванны приводит к вытеканию из нее расплавленного металла. Техника сварки швов в нижнем положении также усложняется по этой причине, но принципиально не отличается от сварки обычными электродами. В основном они применяются для сварки угловых швов в нижнем положении на металле разной толщины. Сварные швы имеют плавные переходы к основному металлу, разбрызгивание незначительное. Производительность при сварке некоторыми марками электродов сравнима с производительностью механизированной сварки (до 13 кг/ч).
При сварке с глубоким проваром (другие названия: опиранием электрода, погруженной дугой и т. д.) повышение производительности сварки достигается за счет более глубокого проплавления основного металла. Сварку выполняют специальными электродами, дающими при их расплавлении козырек повышен-ных размеров, на который и опирают электрод (рис. 70).
Рисунок 70- Образование провара специальными электродами
для сварки с глубоким проваром
Сварщик, удерживая электрод под углом 70—85° к поверхности изделия, перемещает его вдоль свариваемых кромок без поперечных колебаний. Исполь-зуется максимально допустимый ток. Выделяющиеся при расплавлении элект-рода газы, оттесняя расплавленный металл сварочной ванны из-под дуги, уве-личивают глубину проплавления, которая регулируется изменением угла наклона электрода и скоростью его перемещения. Сварку выполняют в нижнем положении стыковых и угловых швов.
При способах сварки лежачим и наклонным электродами также применяют специальные электроды, расплавление покрытия которых, образуя козырек определенных размеров, предупреждает короткое замыкание дуги. Повышение производительности труда достигается за счет того, что один сварщик одновременно обслуживает несколько дуг. Лежачим электродом (рис. 22, а)
сваривают стыковые и нахлесточные соединения и угловые швы на стали толщиной 0,5—6 мм.
1 – электрод;2 — медный брусок; 3 — медная съемная
подкладка; 4 — обойма; 5 — штатив
Дата добавления: 2016-11-24 ; | Нарушение авторских прав
источник
Газовая сварка в различных пространственных положениях
Перед газовой сваркой кромки свариваемого металла и прилегающие к ним участки должны быть очищены от ржавчины, окалины, краски и других загрязнений. Очищают свариваемые кромки металлической щеткой или пламенем сварочной горелки с последующей зачисткой металлической щеткой.
Перед сваркой детали соединяют друг с другом сваркой в отдельных местах короткими швами, с тем чтобы в процессе газовой сварки зазор между ними оставался бы постоянным. Эти соединения называют прихватками. Размеры прихваток и расстояние между ними выбирают в зависимости от толщины свариваемого металла и длины шва.
При газовой сварке тонкого металла и коротких швах длина прихваток не должна превышать 5 мм, а расстояние между ними — 50-100 мм. При газовой сварке толстолистовой стали и швов значительной длины длина прихваток может составлять 20-30 мм при расстоянии между ними 300-500 мм. Прихватки выполняют на тех же режимах, что и сварку. Во время сварки особое внимание необходимо обращать на тщательное приваривание участка прихватки во избежание непровара в этих местах.
Стыковые швы можно выполнять и без прихваток, в этом случае для сохранения постоянного зазора в процессе сварки листы укладывают так, чтобы они образовали между собой небольшой угол. По мере сварки листы стягиваются за счет поперечной усадки шва и таким образом величина зазора остается постоянной по всей длине шва.
От правильной и тщательной подготовки и сборки деталей под газовую сварку во многом зависит качество, внешний вид сварочного соединения, его надежность и прочность.
При газовой сварке длинных швов применяют ступенчатую и обратноступенчатую сварку. При данных способах сварки весь шов разбивается на участки, которые сваривают в определенном порядке. Схема наложения швов показана на рисунке 1. При наложении каждого последующего участка предыдущий участок перекрывают на 10-20 мм в зависимости от толщины свариваемого металла.
а — сварка от кромки, б — сварка от середины шва
Рисунок 1 — Порядок наложения швов при газовой сварке
В зависимости от положения в пространстве сварные швы подразделяют на:
Нижние швы выполнять наиболее легко, так как расплавленный присадочный металл под действием силы тяжести стекает в кратер и не вытекает из сварочной ванны. Кроме того, наблюдение за газовой сваркой нижнего шва наиболее удобно. Нижние швы выполняют как левым, так и правым способами в зависимости от толщины свариваемого металла.
Вертикальные швы при малых толщинах выполняют сверху вниз правым способом и снизу вверх левым способом. При газовой сварке металла толщиной от 2 до 20 мм вертикальные швы целесообразно выполнять способом двойного валика. В этом случае скоса кромок не делают и свариваемые детали устанавливают с зазором, равным половине толщины свариваемого металла. Процесс ведется снизу вверх.
а — сверху вниз, б, в — снизу вверх, г — схема сварки двойным валиком
Рисунок 2 — Выполнение вертикальных швов газовой сваркой
При толщинах более 6 мм сварку ведут два сварщика. При этом способе в нижней части стыка проплавляется сквозное отверстие. Пламя, располагаясь в этом отверстии и постепенно поднимаясь снизу вверх, оплавляет верхнюю часть отверстия. Шов формируется на всю толщину, а усиление получается с обеих сторон стыка. Затем перемещают пламя выше, оплавляя верхнюю кромку отверстия и накладывая следующий слой металла на нижнюю сторону отверстия и так до полного выполнения шва.
Горизонтальные швы, при газовой сварке которых металл стремится стечь на нижнюю кромку, выполняют правым способом, держа конец проволоки сверху, а мундштук горелки снизу ванны. Сварочная ванна располагается под некоторым углом к оси шва, что облегчает формирование шва и удерживание жидкого металла от стекания.
Наибольшие трудности возникают при газовой сварке потолочных швов. При сварке этих швов кромки нагревают до начала оплавления и в этот момент в сварочную ванну вводят присадочную проволоку, конец которой быстро оплавляется. Металл сварочной ванны удерживается от стекания вниз давлением газов пламени. Сварку лучше вести правым способом и выполнять в несколько слоев с минимальной толщиной каждого слоя.
источник
Как создавать пользовательские символы сварки в SOLIDWORKS
Перейти к содержимомуПри создании схем сварки и определении типов сварных швов, которые вы хотите разместить на деталях, существует список стандартных типов сварных швов, которые можно использовать. Если ваша компания создала собственные обозначения сварки или хочет использовать нестандартные обозначения, вы можете создать их самостоятельно для использования в SOLIDWORKS.
Чтобы создать пользовательский символ сварного шва, выберите параметр «Символ сварного шва» на вкладке «Аннотации», чтобы добавить на чертеж символ сварного шва. Вы можете настроить параметры, которые хотите использовать для спецификации сварного изделия.
Если нужный символ отсутствует в списке, его можно добавить вручную, отредактировав файл библиотеки символов. Чтобы найти расположение файла библиотеки символов, перейдите к Инструменты > Параметры > Параметры системы > Расположение файлов > Файл библиотеки символов .
Щелкнув правой кнопкой мыши по этому файлу, вы сможете выбрать Открыть с помощью и выбрать программу «Блокнот» или любой другой текстовый редактор, который может быть установлен на вашем компьютере. Я рекомендую искать раздел символов сварки, который вас интересует. Многие стандарты доступны для редактирования в этом разделе, поэтому обязательно добавьте новый символ к правильному стандарту.
Структура пользовательских символов сварки
На этом этапе вы увидите все перечисленные варианты символов, которые начинаются со звездочки (*). Структура кодирования следующая:
*[Сокращенный код],[Полное имя]
A,[Тип объекта] [Вводы измерений]
- Сокращенный код — это внутренний код, используемый программным обеспечением при связывании значений.
Это может быть любой пользовательский код длиной от 3 до 5 символов. Убедитесь, что этот код уникален для используемого вами стандарта.
- Полное имя будет полным именем пользовательского символа, который вы создаете.
- Тип объекта будет либо ДУГА, КРУГ, либо ЛИНИЯ, в зависимости от геометрии, которую вы хотите создать, поскольку это единственные типы геометрии, которые SOLIDWORKS может использовать в символах.
- Ввод размеров структурирован в координатах X и Y и используется для определения геометрии. Обратите внимание, что целые числа должны иметь десятичную дробь после запятой, и в этом синтаксисе нет нулей перед десятичной дробью для чисел <1.
Как показано на изображении выше, нормальный угловой шов имеет код, указанный ниже в качестве примера. Эти трехлинейные элементы создают треугольник, который является символом углового сварного шва.
*ЗАПОЛНЕНИЕ, скругление
A,LINE .1,0.,.9,0.
А, ЛИНИЯ . 1,0.,.1,.9
А, ЛИНИЯ .1,.9,.9,0.
Синтаксис для каждого типа предприятия перечислен ниже:
Страна
x Старт, Y START, x END, Y END
ARC
X CENGE, Y
CENTER, CENTER,
YCENTER.
Диаметр, градус начало, градус конецОкружность
X центр, Y центр, радиус
После завершения создания или изменения символов сварки можно сохранить этот файл и перезапустить его для SOLIDWORKS. новые символы вступят в силу. Затем вы можете распространить новый файл библиотеки символов среди всех сотрудников вашей компании, которым необходимо показать новые символы сварки. После выполнения обновлений вы можете открыть этот файл библиотеки и скопировать добавленные вами пользовательские элементы.
Дополнительные ресурсы SOLIDWORKS
Если вы хотите узнать больше, ознакомьтесь с дополнительными ресурсами ниже:
- SOLIDWORKS How-To: копирование детали с помощью виртуального компонента
- SOLIDWORKS How-To: Создание виртуальных Sharps в эскизах
- SOLIDWORKS How-To: Добавление взаимосвязей с общими конечными точками эскиза
- SOLIDWORKS How-To: Изменение цвета компонента в виде чертежа
Свяжитесь с нами
Вы увлечены своим делом. Мы заинтересованы в том, чтобы способствовать вашему успеху. Свяжитесь сегодня, и давайте начнем разговор.
Свяжитесь с одним из наших экспертов: 800-454-2233
Познакомьтесь с автором
Джош Хелман
Джош имеет более чем 10-летний опыт работы с SOLIDWORKS и любит помогать клиентам расти с помощью их программного обеспечения. Работая инженером технической поддержки, он специализируется на решении проблем с производительностью, сбоями и аппаратным обеспечением. Он имеет степень бакалавра в области машиностроения UW Platteville и является сертифицированным специалистом по SOLIDWORKS (CSWP).
Подпишитесь на нашу рассылку новостей
Получайте последние передовые практики и учебные пособия по 3D-инженерии ежемесячно на свой почтовый ящик.
Имя
Фамилия
Эл. адрес*
Вебинары и часы работы SOLIDWORKS
Предстоящие занятия
W189 N11161 Kleinmann Dr
Джермантаун, Висконсин 53022
1-800-454-2233
Ресурсы
Подписывайтесь на нас
Подпишитесь на нашу рассылку
© 2023 ГСК | Все права защищены.
Прокрутите вверхДобавление меток ручной сварки на чертежи
Перейти к основному содержанию
- Главная
- Tekla Structures
- Создание чертежей
- Редактирование чертежей
- Сварные швы на чертежах
- Добавление ручных меток сварных швов на чертежи
Текла Структуры
2019
Tekla Structures
На чертежи можно вручную добавлять метки сварных швов модели и метки сварных швов. Метки сварных швов модели относятся к сварным швам, созданным в модели. Метки сварки на чертеже не имеют связанного физического сварного шва в модели.
На открытый чертеж можно добавлять ручные метки сварки. Tekla Structures создает метки сварных швов вручную, используя свойства в диалоговом окне «Свойства метки сварного шва».
- Удерживая нажатой клавишу Shift, на вкладке «Аннотации» нажмите «Метка сварного шва», чтобы открыть диалоговое окно «Свойства метки сварного шва».
- Введите или измените содержимое и внешний вид метки сварного шва.
- Чтобы точно разместить метку сварки в выбранном вами положении и сохранить ее там, нажмите кнопку «Поместить…» и выберите «Фиксированный» в списке «Размещение».
- Нажмите «Применить» или «ОК», чтобы сохранить свойства.
- Выберите положение для метки сварки.
Вы можете свободно перетаскивать созданную метку сварного шва на чертеже в более подходящее место с помощью маркера базовой точки выноски.
Вы можете добавлять метки к меткам сварки модели на открытом чертеже. Tekla Structures создает метки сварных швов модели, используя свойства, определенные для модельного сварного шва в модели. Можно настроить параметры видимости и внешнего вида метки сварного шва на чертеже.
- Откройте чертеж, содержащий сварные швы, созданные в модели.
- Выполните одно из следующих действий:
- Выберите сварной шов модели на чертеже.
- Выберите на чертеже несколько сварных швов модели с помощью переключателя Выбрать сварные швы и выбора области или Диспетчера содержимого чертежа.
Если на чертеже не видны сварные швы, проверьте настройки видимости сварных швов в свойствах вида.
- Щелкните правой кнопкой мыши и выберите “Добавить метку сварки”.
- Чтобы изменить параметры видимости и внешнего вида метки сварного шва модели:
- Дважды щелкните метку сварного шва на чертеже и настройте свойства.
- Дважды щелкните метку сварного шва на чертеже и настройте свойства.