Как определить твердость металла: Твердомеры для металлов. Методы Бринелля и Роквелла
alexxlab | 26.07.1988 | 0 | Разное
Определение твердости металлов — МегаЛекции
Твердостью называется свойство металла сопротивляться внедрению в него другого, более твердого тела. Испытания на твердость широко применяются в производственных условиях, так как имеют следующие преимущества:
– поверхностное испытание твердости не сопровождается разрушением заготовок или деталей;
– приборы для проверки твердости отличаются высокой
производительностью (до 300 испытаний в час) и простотой обслуживания;
– в условиях серийного и массового производства испытанию на твердость можно подвергать 100% ответственных деталей, тогда как при других видах испытаний может быть осуществлен только выборочный контроль для определения среднего качества металла изготовленных деталей;
– результаты испытаний на твердость позволяют с достаточной для практических целей точностью судить о других прочностных характеристиках испытываемого металла, а также определять его способность поддаваться обработке.
Применяемые в настоящее время методы определения твердости металлов делятся на статические и динамические.
Наиболее распространенными статическими методами испытания на твердость являются методы, основанные на плавном и постепенном вдавливании в испытываемый образец стального закаленного шарика, алмазного конуса или алмазной пирамиды – измерение с медленно нарастающей (статической) нагрузкой (твердость по Бринеллю, по Роквеллу и по Виккерсу).
Из числа динамических испытаний можно назвать метод упругой отдачи (метод Шора) и метод ударного вдавливания стального закаленного шарика.
Для определения микротвердости (твердости отдельных структурных составляющих) существуют специальные приборы, на которых вдавливание наконечника в испытуемую поверхность производится под небольшими нагрузками (5 – 500 Г).
Твердость по Бринеллю определяется на прессе Бринелля. Нагрузка с помощью гидроцилиндра с маслом и поршня передается на шарик определенного диаметра из закаленной стали, который вдавливается в испытуемый материал с силой P, превышающей предел упругости материала, в результате чего в испытуемой детали образуется углубление в виде шарового сегмента. Если F – площадь наружной поверхности сегмента, то твердость выражается числом HB = P/F кГ/мм2. Величина F может быть вычислена по глубине вдавливания h или по диаметру сегмента d (рис. 3.17)
Рис.3.17
Таким образом для определения твердости по Бринеллю необходимо измерить диаметр отпечатка шарика, который для этих целей используется размером D = 10 мм; D = 2,5 мм и вдавливается под давлением P = 3000 кг; P = 1000 кг и P = 250 кг и по таблице определить твердость в зависимости от диаметра этого отпечатка.
Необходимо отметить, однако, что более точным способом является измерение не диаметра отпечатка, а его глубины, так как лишь при измерении глубины отпечатка удается получить цифры твердости
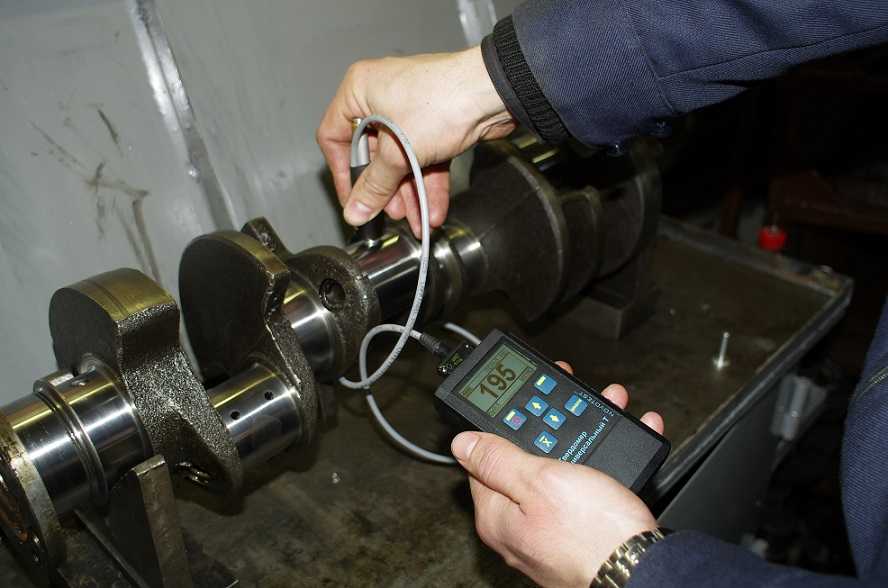
Диаметр шарика и давление должны соответствовать испытываемому образцу. Поверхность образца должна быть тем чище приготовлена, чем больше его твердость. Нужно удалить окалину и грат, а также обезуглероженный поверхностный слой.
Твердость по Бринеллю и сопротивление разрыву стоят в тесной связи. Так как для стали (при HB > 175 кг/мм2) временное сопротивление разрыву равно твердости по Бринеллю, умноженной на 0,345; для стали с HB < 175 кг/мм2 – sb = 0,362 HB; для никелевой и хромоникелевой стали sb = (0,35-0,34) HB; для дюралюминия sb = 0,35 HB.
В случае, если не требуется высокая точность измерения твердости и нет в наличии пресса Бринелля можно воспользоваться небольшим прибором Польди. Этот прибор, в отличие от пресса, работает динамической, а не статической нагрузкой. Для практических целей этот способ вполне пригоден, так как дает ошибку, не превышающую 7 %.
Твердость по Виккерсу измеряется на приборе, построенном фирмой Виккерс, при помощи алмазной пирамиды с углом при вершине 136°. Твердость определяется отношением нагрузки 50 кг к поверхности отпечатка. Размер отпечатка на приборе Виккерса измеряется специальным микроскопом, являющимся частью всего прибора. Измерение твердости по Виккерсу обладает преимуществом по сравнению с испытанием по Бринеллю, так как в пределах больших твердостей дает более точные результаты. Кроме того при измерении по Виккерсу удобством является большая четкость отпечатка алмазной пирамиды, чем стального шарика.
Твердость по Роквеллу определяется глубиной внедрения в испытуемый материал стального шарика или конического алмаза при определенном повышении давления. Глубина погружения измеряется индикатором, стрелка которого непосредственно отсчитывает твердость. Для мягких материалов обычно применяется стальной шарик Æ 1,59 мм (1/16¢¢) (отсчеты производятся по красной шкале В), для более твердых конический алмаз с конусностью в 120° (черная шкала С). В обоих случаях первоначальное давление составляет 10 кГ. Конечное давление для стального шарика доводится до 100 кг, для алмаза – 150 кГ. Увеличение давления производится автоматически и равномерно при помощи масляного тормоза в течение от 3 до 5 с. Глубина внедрения колеблется от 0,06 мм для алмазного конуса и закаленной стали и до 0,25 мм для стального шарика и мягких материалов.
Для проверки твердости на приборе Роквелла (рис.3.18) образец 3 устанавливается на стол 4. Затем с помощью винта, вращаемого маховиком 5, вводят образец в соприкосновение с алмазным или шариковым наконечником 2 до тех пор, пока малая стрелка индикатора не подойдёт к нулю, а большая не займёт приблизительно вертикальное положение. Это положение стрелок соответствует предварительной нагрузке 10 кГ. После этого шкалу 1 индикатора поворачивают до совпадения конца большой стрелки с нулевым делением (при измерении алмазом) или с тридцатым делением внутренней шкалы (при испытании шариком).
– наружную (обычно черного цвета) для отсчета величины твердости при проверке алмазным конусом по шкале С при нагрузке 150 кГ и по шкале А при нагрузке 60 кГ;
– внутреннюю (обычно красного цвета) для отсчета числа твердости при проверке шариком по шкале В.
а б
Рис.3.18. Прибор Роквелла (а) и шкала индикатора прибора (б)
Твердость по Шору определяется склероскопом. Последний состоит из стального ударника с алмазным наконечником весом 2,6 кг, падающего с определенной высоты (257 мм) на горизонтальную поверхность испытуемого образца.
Кроме указанных методов используются методы измерения твердости по Мосу (метод царапания для минералов и металлов) и по Герберту с помощью маятникового прибора. Ввиду очень высокой чувствительности последнего этот метод очень редко используется для заводской работы и применяется большей частью в научно-исследовательских лабораториях и институтах.
Таблица 3.13
Сравнительная таблица твердости металлов и сплавов (ориентировочно) по Бринеллю, Роквеллу, Виккерсу и Шору
Бринелль НВ | Роквелл НRС | Виккерс НV | Шор | Бринелль НВ | Роквелл НRС | Виккерс НV | Шор |
- | |||||||
- | |||||||
- | |||||||
- | |||||||
Продолжение табл.![]() | |||||||
- | |||||||
- | |||||||
- | |||||||
- | |||||||
- | |||||||
- | |||||||
- | |||||||
- | |||||||
- | |||||||
- | |||||||
- | |||||||
- | |||||||
- | |||||||
- | |||||||
- | |||||||
- |
Технологические пробы
Технологическими пробами называются испытания, выявляющие способность металла деформироваться (изменять форму) под воздействием внешних сил. К ним относятся проба на загиб, проба на осадку, проба проволоки на навивание, проба на обрабатываемость, проба листового металла на вытягивание и др.
Порядок проведения технологических проб и требования к образцам стандартизированы.
Проба на загиб производится в холодном или нагретом состоянии на прессах, в тисках или на специальных приборах и служит для определения способности металла поддаваться загибу в соответствии с заданными размерами и формой. Результаты испытания считаются удовлетворительными, если в образце после загиба отсутствуют трещины, расслоения или излом.
Пробе на осадку подвергаются цилиндрические образцы из черных металлов и алюминиевых сплавов, которые в виде прутков и проволоки применяются для изготовления болтов, заклепок и других крепежных деталей. Образцы испытывают в холодном или горячем состоянии под прессом или механическим или пневматическим молотом. Материал считается годным, если на боковой поверхности образцов, подвергнутых испытанию, нет трещин, закатов и надрывов. На боковой поверхности образцов из алюминиевых сплавов не должно быть также шероховатости и расслоений.
Испытание проволоки на навивание производится в холодном состоянии. Проволоку диаметром до 6 ммнавивают плотно прилегающими друг к другу витками на цилиндрическую оправку, диаметр которой задается техническими условиями.
После испытания проволока не должна иметь надрывов, трещин и излома как в материале образца, так и в его защитном слое (в оцинкованных, луженых и тому подобных деталях).
Кроме указанного метода испытания проволоки на навивание, стандартами установлены методы технологических испытаний на перегиб и на скручивание холоднотянутой и горячекатаной проволоки диаметром 0,8 – 10 мм.
Стандартизованы также испытания металлов на кручение, расплющивание, прокаливаемость, свариваемость, перегиб, развертывание фасонного материала, испытание тонколистового материала на двойной кровельный замок, испытание труб гидравлическим давлением, а также бортование, загиб, раздачу и сплющивание.
Оглавление
Воспользуйтесь поиском по сайту:
Обзор методов измерения твердости металлов и сплавов
Исторически с развитием технологий обработки металлов появлялись и совершенствовались способы контроля качества металлических изделий.
Известно множество способов определения твердости металлов и сплавов:
- Вдавливание индентора под действием статической нагрузки (нагрузка прикладывается плавно) – по методу Бринелля, Роквелла, Супер-Роквелла, Виккерса, М.С.Дрозда, Герца, Лудвика, монотрон Шора;
- Динамическое вдавливание индентора (нагрузка прикладывается ударом) – по методу Мартеля, Польди, вертикальный копер Николаева, пружинный прибор Шоппера и Баумана, маятниковый копер Вальцеля, маятник Герберта, маятниковый склерометр Кузнецова;
- Измерение микротвердости статическим вдавливанием – по методу Липса, Егорова, Хрущева, Скворцова, Алехина, Терновского, Шоршорова, Берковича, Кнупа, Петерса, Эмерсона, микротвердомер Цейсса-Ганеманна;
- Метод упругого отскока бойка – склероскоп Шора;
- Измерение твердости царапанием – по Моосу, напильник Барба, прибор Мартенса, Хенкинса, микрохарактеризатор Бирбаума, склерометр О’Нейля, Григорович, Беркович).
В целом, по характеру воздействия индентора на поверхность исследуемого объекта можно узнать конкретные свойства материала: вдавливание определяет способность к сопротивлению пластической деформации, отскок показывает упругие свойства, царапанье характеризует сопротивление разрушению.
Многие приемы сейчас используются редко или вовсе ушли в прошлое.
На данный момент основные и самые распространенные методы контроля твердости металлов условно делят на две группы: прямые и косвенные.
Прямые методы измерения твердости
основаны на способности материала сопротивляться внедрению другого, более твердого тела – индентора. Инденторы изготавливаются в форме конуса или пирамиды из алмаза, в форме шарика – из закаленной стали или карбида вольфрама.
Прямые методы реализуют в основном стационарные твердомеры по шкалам Бринелля (HB), Роквелла (HRA, HRB, HRC), Супер-Роквелла (HRN и HRT), Виккерса (HV).
Сущность испытаний заключается в том, что после внедрения индентора, при приложении заданной статической нагрузки, происходит пластическая деформация исследуемого материала. На поверхности образца остается отпечаток.
Вычисление значения твердости строится на зависимости приложенного усилия и определенных геометрических параметров отпечатка. Для каждого прямого метода предусмотрена своя зависимость (см. таблицу ниже). Например, при замерах по Роквеллу фиксируется глубина отпечатка: чем она меньше, тем выше твердость объекта.
Плюсы: стационарные твердомеры применяются для контроля любых металлов и сплавов; выдают результат с минимальной погрешностью; не требуют дополнительной калибровки.
Минусы: работают на одном месте, как правило в специально оборудованной лаборатории; необходимо заранее готовить образцы, либо изделие должно иметь конкретные габариты; необходима квалификация оператора; невысокая скорость выполнения исследований.
Косвенные методы измерения твердости
подразделяются на ультразвуковой и динамический – они не напрямую измеряют твердость, а только оценивают значение твердости металла в зависимости от других физических свойств.
Косвенные методы реализуют портативные твердомеры – ультразвуковые и динамические. Результат можно получить как в самых распространенных единицах твердости, таких как Роквелл С (HRC), Бринелль (НВ), Виккерс (HV), так и в реже используемых единицах Роквелла А и В (HRA, HRB), Шора D (HSD) и других.
Ультразвуковой метод (ультразвуковой контактный импеданс) основан на фиксации степени затухания резонансной частоты колебаний металлического стержня с алмазным наконечником (индентором) при внедрении его в поверхность металлического изделия.
При глубоком внедрении индентора в мягкий металл будет большая площадь контакта алмаза с материалом, значит будет выше степень затухания частоты колебаний.
Применим к изделиям практически любых габаритов по массе и размерам; оставляет незаметный отпечаток; подходит для измерения твердости поверхностно упрочненных слоев; удобен для образцов со сложной конфигурацией (шестерни, подшипники, метизы). Применение на изделиях с крупнозернистой структурой ограничено (чугуны, бронза).
Динамический метод (Либа) основан на определении отношения скорости бойка при отскоке от поверхности измеряемого образца к скорости бойка при соударении с поверхностью образца. В качестве бойка используется твердосплавный шарик (карбид вольфрама WC-Co).
Чем ниже твердость металла, тем больше энергии удара уходит на формирование отпечатка и тем меньше скорость отскока бойка.
Подходит для массивных изделий; образцов с высокошероховатой поверхностью; объектов со значительной толщиной упрочненного или закаленного слоя.
Плюсы: портативные твердомеры автономны, просты в управлении, работают в труднодоступных зонах, обладают высокой скоростью проведения замеров.
Минусы: погрешность результатов измерений выше, чем у стационарных приборов; иногда требуется дополнительная калибровка шкал.
Общие требования к испытаниям
- Вне зависимости от величины прилагаемого усилия или затрачиваемой энергии, значение твердости для однородного тела при постоянной температуре должно быть материальной константой.
- Поверхность объекта должна быть подготовлена в соответствии с методикой измерения.
- Образец должен быть надежно зафиксирован, чтобы исключить смещение относительно оси приложения нагрузки со стороны прибора.
- Твердость должна иметь совершенно определенный и ясный физический смысл, правильную размерность, характеризующую сопротивление материала пластической деформации.
Чем выше твердость образца, тем более высокая нагрузка нужна при его исследовании. Чем точнее метод, тем выше требования к подготовке поверхности контролируемого экземпляра. Вообще, чем тщательнее будет подготовлен образец для испытаний, тем меньше будет погрешность результата при использовании и стационарного, и портативного твердомера.
Классические прямые методы измерения твердости путем внедрения индентора под действием статической нагрузки
Метод | Принцип вычисления твердости | Шероховатость поверхности образца, Ra | Индентор | Нагрузка | Шкала | Применение |
Бринелля | По диаметру отпечатка — как приложенная нагрузка, деленная на площадь поверхности отпечатка (кгс/мм²) | 1,25 – 2,5 | Твердосплавный шарик диаметром 1; 2; 2,5; 5 и 10 мм | 1 кгс (9,8Н) – 3000 кгс (29420Н) | HB | Закаленные и незакаленные стали, мягкие металлы и сплавы (свинец, олово), титан, медь, алюминий, чугун, высокопрочные сплавы (на основе никеля, кобальта и др.![]() |
Роквелла | По глубине вдавливания — как относительная разница в глубине вдавливания индентора при приложении основной и предварительной (10 кгс) нагрузки | 0,38 – 2,5 | Алмазный конус с углом при вершине 120° | 60 кгс (588Н) | HRA | Коррозионностойкие и жаропрочные стали |
Твердосплавный шарик диаметром 1/16 дюйма (1,588 мм) | 100 кгс (980Н) | HRB | Сплавы меди, алюминиевые сплавы, бронза, ковкий чугун, низкоуглеродистые стали | |||
Алмазный конус с углом при вершине 120° | 150 кгс (1471Н) | HRC | Высокоуглеродистые стали после термической или химико-термической обработки | |||
Супер-Роквелла | 0,08 – 0,16 | Алмазный конус с углом при вершине 120° или твердосплавный шарик диаметром 1/16 дюйма (1,588 мм) | 15 кгс (147,1Н) 30 кгс (294,2Н) 45 кгс (441,3Н) | HRN, HRT | Алюминиевые сплавы, детали с упрочненными поверхностными слоями, тонкие малогабаритные образцы | |
Виккерса | Производится деление нагрузки на площадь боковой поверхности полученного отпечатка | 0,02 – 0,04 | Алмазный индентор в форме правильной четырехгранной пирамиды с углом 136° между противоположными гранями | 1 кгс (9,8Н) – 100 кгс (980Н) | HV | Высокопрочные стали, чугун, цветные металлы и сплавы; закаленные и незакаленные стали, литье; тонкие листовые материалы; поверхности с гальваническим (цинкование, хромирование), азотированным, луженым покрытием различной толщины |
Микро-Виккерса | 0,01 кгс (0,098Н) – 5 кгс (49Н) | Тонкие закаленные слои; анодированные, цементированные, азотированные детали; поверхности с тонким гальваническим покрытием; изделия из высокопрочных металлов и сплавов; тонколистовые стали |
Контроль твердости металлов и сплавов по Бринеллю, Роквеллу, Виккерсу в СПб, цена от 500р
Рассчитать стоимость
Измерение твердости металла — одно из наиболее распространенных испытаний при определении механических характеристик материала. Для определения твердости в металлическую поверхность вдавливают другое тело — индентор – которое может иметь вид шарика из карбида вольфрама, алмазного конуса, алмазной пирамиды.
ТМ — это свойство материала оказывать сопротивление при проникновении в него другого физического тела. Измерение ТМ дает возможность определить соответствие фактических механических свойств материала, заявленным в технической документации.
После вдавливания измеряется диаметр вмятины, образованной на поверхности. По размеру деформации на основе определенных формул определяется твердость. Существует несколько технологий измерения твердости. Современные измерительные приборы и программное обеспечение может автоматически конвертировать результаты из одной шкалы в другую.
Способы контроля твердости металлов совершенствовались по мере развития технологий. Основные из них, использующиеся на производствах:
- Впрессовывание наконечника динамическое. С помощью удара идет нагрузка. Этот способ определения называют: мятник Герберта, пружинное устройство Баумана и Шоппера, твердометр с маятником Кузнецова, способ Польди, Мартеля.
- Индентор вдавливают с помощью нагрузки статического характера. Это значит, что давление на металлы идет плавно. Этот способ носит имя: Супер-Роквелл, Hertzа, монотрон Шора, Бриннеля, Виккерса, Лудвика, М. С. Дрозда.
- Микротвердость измеряют при помощи статического вдавливания. Метод носит имя: Петерса, Хрущева, Алехина, Липса, Скворцова, Берковича, Терновского, Цейсса-Ганеманна.
- Замеряют твердость с помощью царапания. Способ носит названия: склерометр О’Нейля, Мооса, прибор мартенса, Берковича, Хенкинса, микрохарактеризатор Бирбаума.
- Способ отскока упругого бойка. Используют склероскоп Шора.
Из числа всех способов, преимущественно используются такие методы определения твердости:
- По Бринеллю — во время измерений твердости в исследуемый образец вдавливается стальной шарик. Учитывается диаметр индентора и оказываемая нагрузка. Измеряется отпечаток, который образовался на поверхности.
- По Роквеллу — индентором при измерениях твердости служит или шарик из закаленной стали, или алмазный конус.
Измеряется не площадь оставленного отпечатка, а глубина его проникновения внутрь исследуемой детали.
- По Виккерсу — определяют твердость путем вдавливания алмазной пирамиды с четырьмя гранями. Угол граней пирамиды составляет 136о. Замеряется диагональ образованного отпечатка.
С помощью воздействия индентора на материал, узнают определенные свойства металла (твердость и не только). Царапанье определяет устойчивость к разрушению. Отскок измеряет свойства упругости. Возможность противостоять пластической деформации измеряет вдавливание.
Способов определения твердости– более 15. Но не все они используются на практике. Большая их часть не применяется. Специалисты же собрали самые распространенные методы чтобы замерить твердость и условно разделили их на 2 категории: косвенную и прямую.
Цена на измерение твердости металлов и сплавов |
||
---|---|---|
Наименование услуги | Ед.![]() |
Цена |
Определение твердости металла ГОСТ 9013-59 | 1 образец | 500 руб |
Прямые
В основе данных способов замерить твердость лежит способность металла оказывать сопротивление внедрению индентора. Последний – это более твердое тело, чем испытуемое сырье. Инденторы производят в форме пирамиды либо конуса. Материал изготовления – алмаз. Иногда делают его в виде шара. Но для сырья используют карбид вольфрама либо закаленную сталь.
Методы прямого определения твердости используют преимущественно стационарные твердомеры. Используют следующие шкалы:
- Супер-Роквелл (HRT, HRN).
- Бриннеля (НВ).
- Виккерса (HV).
- Роквелла (HRB, HRA, HRS).
Суть исследования твердости состоит в том, что после использования индентора с заданной нагрузкой статического характера, происходит деформация материала. На его поверхности остается след.
Последующее вычисление на твердость проходит при сравнении оказанного усилия и конкретных видимых параметров отпечатка индентора на поверхности. Для каждого метода есть определенная зависимость. Например, в способе по Роквеллу замеряется глубина следа. Чем меньше этот показатель, тем выше твердость металла.
Достоинства прямых методов исследования твердости:
- Стационарные измерители твердости используют для оценки любого сплава и металла.
- Погрешность в результате мала.
- Калибровка дополнительная не нужна.
Недостатки:
- Нет мобильности. Работать с твердомерами можно только в определенном оборудованном месте.
- Для работы нужна предварительная подготовка. Для нее готовят образцы либо придает исследуемому объекту нужный размер.
- Скорость исследования низкая.
Для правильного контроля твердости нужен квалифицированный оператор. Только специалист сможет провести процедуру верно.
Стандартные прямые методы исследования твердости с помощью внедрения индентора под влиянием статической нагрузки | |||
Способ | Индентор | Шкала твердости | Где применим (для каких металлов) |
Бринелля | Шарик из твердого сплава. Его диаметр: 2, 10, 1, 5 или 2,5 мм. | НВ | Стали закаленные и незакаленные, свинец, медь, олово, чугун, титан, алюминий. Подшипниковые сплавы. Сплавы на основе кобальта, никеля, т. е. все высокопрочные, с твердостью. |
Роквелла | Шарик из твердого сплава диаметром 1,588 мм или 1/16 дюйма. | HRB | Низкоуглеродистые стали. Сплавы: медные, алюминиевые. Бронза и чугун ковкий. |
Конус алмазный с углом при вершине 120 градусов.![]() |
HRA | Стали: жаропрочные и устойчивые к коррозии. | |
HRC | Стали высокоуглеродистые после химико-термической или термической обработки. | ||
Супер-Роквелла | Два варианта. Шарик из твердого сплава диаметром 1,588 мм или 1/16 дюймов. Конус алмазный, 120 градусов при вершине. | HRN HRT |
Малоразмерные тонкие образцов металлов, сплавы из алюминия, предметы с поверхностными упрочненными слоями. |
Виккерса | Форма – пирамида с 4 гранями правильной формы. Материал изготовления – алмазный. Угол между противоположными гранями 136 градусов. | HV | Чугун, незакаленные и закаленные типы стали, а также высокопрочные металлы. Литье, материалы листовые тонкие. Пригодны поверхности с гальваническим покрытием (хромирование или цинкование). Металлы с луженым слоем разной толщины или азотированном покрытием. ![]() |
Микро-Виккерса | Металлы с закаленными тонкими слоями. Детали азотированные, анодированные, цементирование. Объекты с покрытием гальваническим. Материалы из высокопрочных сплавов и металлов. Тонкие листы стали. |
Косвенные и ультразвуковые
В эту группу входят динамический и ультразвуковой методы измерения твердости. Их отличие – оценка твердости металла происходит в сравнении с рядом физических свойств, а не напрямую.
Исследования в косвенных методах проводят с помощью портативных твердомеров:
- Динамических.
- Ультразвуковых.
Результаты анализа выдают в наиболее популярных единицах твердости:
- Бриннель (НВ).
- Роквелл С (HRC).
- Виккрес (HV).
Часть приборов выдает показания в следующих единицах:
- Шора D
- Роквелла В и А.
При желании можно найти твердомеры и с иными способами измерения.
Ультразвуковой способ замера на твердость включает использование контактного УЗ импеданса. В основе метода лежит фиксация уровня угасания резонансной частоты, отслеживающей колебания стержня из металла с наконечником из алмаза (индентор). Его внедряют в поверхность исследуемого объекта.
Когда индентор внедряют глубоко в металл мягкой текстуры, площадь контакта алмаза с объектом будет немалая. Значит, степень угасания частоты колебаний будет выше. Этот метод пригоден для работы с предметами любого размера, формы или веса. После исследования на твердость следов на поверхности не остается.
Пригоден для изучения упрочненных поверхностных слоев. Достоинство в том, что способ замера на твердость применим к анализу деталей сложной конструкции. К ним относят:
- Метизы.
- Подшипники.
- Шестерни.
Также используется способ для работы с чугуном или бронзой. Металл с крупнозернистой структурой не помеха для исследования.
Метод Либа, динамический
В структуре замеров твердости металлов лежит подсчет отношения скорости бойка в момент отскока от изучаемого объекта. Сопоставляют показатель со скоростью бойка в период соударения. Роль бойка выполняет шарик из твердого сплава. Обычно используют карбид вольфрам WC-Co.
Твердость металла действует на формирование отпечатка. Чем она ниже, тем больше уходит энергии на удар и меньше скорость отскока бойка.
Сильные стороны метода, чтобы измерить металлы:
- Измеряют предметы с шероховатой поверхностью.
- Можно изучать детали из закаленного слоя либо с существенной толщиной.
- Можно исследовать крупный металл.
К недостаткам относят высокую погрешность показателей твердости. Ее показатель больше, чем у приборов стационарного использования. Поэтому часто необходимо делать дополнительную калибровку шкал.
Соотношение показаний твердости
При сравнении показателей твердости (полученных любыми методами) между собой со свойствами механического характера материалов, стоит помнить, что таблицы или зависимости эмпирические.
Ведь при вдавливании разных инденторов с любой нагрузкой на металлы, твердость вычисляют при абсолютно разных напряженных состояний объектов. Даже если использовать один способ, значение будет зависеть от нагрузки. При малом воздействии показатели твердости выходят более высокими.
Общие условия для проведения исследования
Правила анализа на твердость:
- Исходя из методики исследования, поверхность предмета подготавливают.
- Материальной константой в исследовании выступает показатель твердости для однородного предмета при стабильной температуре.
- Исключают смещение предмета в период испытания. Материал плотно фиксируют.
Чтобы избежать сильной погрешности показателя твердости, исследуемые металлы тщательно подготавливают.
Компания «Прометей» оказывает услуги по измерению ТМ в готовых изделиях и предоставленных образцах. В нашей тестовой лаборатории есть современное оборудование для выполнения замеров по разным методам. Мы гарантируем достоверность и быстроту исследования.
Калькулятор расчета
Мы уже сотрудничаем с компаниями в Ленинградской, Тульской, Московской, Мурманской областях, а также следующих городов России:
Москва
Нижний Новгород
Чехов
Лахденпохья
Дзержинск
Санкт-Петербург
Новороссийск
Тольятти
Сортавала
Владивосток
Тверь
Советск
Севастополь
Самара
Ростов-на-Дону
Рязань
Питкяранта
Владикавказ
Как измерить твердость металлов
Измерение твердости металловИзображение предоставлено Shutterstock/Thaweesak Thipphamon
Существует несколько различных методов испытаний и шкал, которые используются для измерения относительной твердости таких материалов, как металлы. Ниже приводится краткое изложение наиболее распространенных из этих методологий.
Испытание на твердость по Бринеллю
Испытание по Бринеллю для определения твердости металлических материалов заключается в приложении известной нагрузки к поверхности испытуемого материала через закаленный стальной шарик известного диаметра. Измеряют диаметр полученного постоянного отпечатка в металле, а затем рассчитывают число твердости по Бринеллю (BHN) по следующей формуле, в которой D = диаметр шарика в миллиметрах, d = измеренный диаметр по краю отпечатка в миллиметрах, и P = приложенная нагрузка в килограммах.
Если бы стальной шарик не деформировался под действием приложенной нагрузки и если бы отпечаток действительно был сферическим, то предыдущая формула была бы общей, и можно было бы использовать любую комбинацию приложенной нагрузки и размера шарика. Отпечаток, однако, не совсем сферическая поверхность, потому что всегда должна быть некоторая деформация стального шарика и некоторое восстановление формы металла в отпечатке; следовательно, для стандартного теста Бринелля размер и характеристики мяча, а также величина приложенной нагрузки должны быть стандартизированы. В стандартной пробе Бринелля используется мяч диаметром 10 мм и нагрузка 3000, 1500 или 500 кг. Желательно, хотя и не обязательно, чтобы испытательная нагрузка была такой величины, чтобы диаметр отпечатка находился в диапазоне от 2,50 до 4,75 мм. Следующие испытательные нагрузки и приблизительные числа Бринелля для этого диапазона диаметров оттисков составляют: 3000 кг, от 160 до 600 BHN; 1500 кг, от 80 до 300 BHN; 500 кг, от 26 до 100 руб. При проведении теста Бринелля нагрузку следует прикладывать постоянно и без рывков в течение не менее 15 с для железа и стали и не менее 30 с при испытании других металлов. Минимальный период 2 минуты, например, рекомендуется для магния и магниевых сплавов. (Для более мягких металлов иногда используются нагрузки 250, 125 или 100 кг.)
В соответствии со стандартом E10-66 Американского общества по испытаниям и материалам стальной шарик можно использовать для материала с BHN не более 450, шар Hultgren — для материала не более 500 или карбидный шарик — для материала не более 630. Испытание на твердость по Бринеллю не рекомендуется для материалов с BHN выше 630.
Испытание на твердость по Роквеллу
Твердомер по Роквеллу представляет собой прибор, который измеряет твердость путем определения глубины проникновения пенетратора в образец при определенных фиксированных условиях испытания. Пенетратор может представлять собой стальной шарик или алмазный сфероконический пенетратор. Число твердости связано с глубиной вдавливания, и число выше, чем тверже материал. Сначала прикладывается небольшая нагрузка в 10 кг, вызывающая начальное проникновение; циферблат устанавливается на ноль на черно-цифровой шкале, и прикладывается основная нагрузка. Эта основная нагрузка обычно составляет 60 или 100 кг, когда в качестве пенетратора используется стальной шар, но при необходимости могут использоваться и другие нагрузки. Шаровой пенетратор обычно имеет диаметр 1 дюйм, но для мягких металлов можно использовать другие пенетраторы большего диаметра, например 18 дюймов. При использовании алмазного сфероконического пенетратора нагрузка обычно составляет 150 кг. Опыт определяет наилучшее сочетание нагрузки и пенетратора для использования. После того, как большая нагрузка приложена и снята, в соответствии со стандартной процедурой, показания снимаются, пока еще действует второстепенная нагрузка.
Шкалы твердости по Роквеллу
Различные шкалы Роквелла и их применение показаны в следующей таблице. Тип пенетратора и нагрузка, используемая с каждым из них, показаны в таблицах 5 и 6, в которых приведены сравнительные значения твердости для различных шкал твердости.
Там, где желателен неглубокий отпечаток или небольшая площадь для материалов, более мягких, чем закаленная сталь.
Склероскоп Шора
Склероскоп — это прибор, который измеряет твердость изделия с точки зрения эластичности. Молоток с алмазным наконечником падает с известной высоты на испытуемый металл. Когда этот молоток ударяет по металлу, он отскакивает, и чем тверже металл, тем сильнее отскок. Записывается предельная высота отскока, и среднее число показаний, снятых на одном изделии, даст хорошее представление о твердости работы. Гладкость поверхности работы влияет на показания прибора. На показания также влияют контур и масса изделия и глубина гильзы, а в науглероженном изделии мягкий сердечник малоглубинного науглероживания, пакетной закалки или цианидной закалки, поглощающий силу удара молотка. и уменьшая отскок. Молоток весит около 40 гран, высота отскока закаленной стали составляет около 100 по шкале, или около 614 дюймов (158,8 мм), а общее падение составляет около 10 дюймов или 255 миллиметров.
Испытание на твердость по Виккерсу
Критерий Виккерса в принципе аналогичен критерию Бринелля. Стандартный пенетратор Виккерса представляет собой алмазную пирамиду с квадратным основанием, имеющую угол при вершине 136 градусов. Числовое значение числа твердости равно приложенной нагрузке в килограммах, деленной на площадь пирамидального вдавления. Требуется гладкая, прочно поддерживаемая, плоская поверхность. Нагрузка, которую обычно прикладывают в течение 30 секунд, может составлять 5, 10, 20, 30, 50 или 120 килограммов. 50-килограммовая нагрузка – самая обычная. Число твердости основано на длине диагонали квадратного отпечатка. Тест Виккерса считается очень точным и может применяться как к тонким листам, так и к более крупным профилям при надлежащем регулировании нагрузки.
Числа твердости по Кнупу
Испытание на твердость по Кнупу применимо к чрезвычайно тонким металлам, поверхностям с покрытием, исключительно твердым и хрупким материалам, очень мелким науглероженным или азотированным поверхностям, а также в тех случаях, когда приложенная нагрузка должна быть ниже 3600 граммов. Индентор Кнупа представляет собой алмаз, отшлифованный до вытянутой пирамидальной формы, и он производит отпечаток, имеющий длинные и короткие диагонали с соотношением примерно 7 к 1. Продольный угол индентора составляет 172 градуса, 30 минут, а поперечный угол 130 градусов. . Прибор Tukon Tester, в котором используется индентор Кнупа, является полностью автоматическим с электронным управлением. Число твердости по Кнупу равно нагрузке в килограммах, деленной на проектируемую площадь вмятины в квадратных миллиметрах. Число отпечатков, соответствующее длинной диагонали и заданной нагрузке, можно определить по таблице, рассчитанной для теоретически идеального индентора. Нагрузку, которая может варьироваться от 25 до 3600 грамм, прикладывают в течение определенного времени и всегда перпендикулярно испытуемой поверхности. Необходимы притертые плоские поверхности без царапин.
Индикатор твердости Monotron
С помощью этого инструмента импрессорный наконечник с алмазным шариком диаметром 34 мм вдавливается в материал на глубину 95000 дюймов; давление, необходимое для создания этого постоянного отпечатка, указывает на твердость. Один из двух циферблатов показывает давление в килограммах и фунтах, а другой — глубину отпечатка в миллиметрах и дюймах. Показания в числах Бринелля можно получить с помощью шкалы, обозначенной как М-1.
Тест Крепости
С помощью этого устройства стандартное стальное сверло делает определенное число оборотов, прижимая его со стандартной силой к испытуемому образцу. Твердость автоматически записывается на диаграмме, на которой совершенно мягкий материал дает горизонтальную линию, а материал, такой же твердый, как само сверло, дает вертикальную линию, промежуточная твердость представлена соответствующим углом между 0 и 90 градусами.
Резюме
В этой статье обобщены общие методы и шкалы для определения твердости металлов, включая тесты на твердость по Бринеллю, Роквеллу и Виккерсу. Узнайте больше о свойствах материалов из Справочника по машинному оборудованию, 30-е издание, которое опубликовано и доступно в Industrial Press на Amazon.
Чтобы найти источники поставок приборов для измерения твердости, посетите платформу поиска поставщиков Thomas, где вы можете найти потенциальные источники поставок для более чем 70 000 различных категорий продуктов и услуг.
Другие изделия из металлов
- Ведущие производители и поставщики вольфрама и карбида вольфрама в США
- Циркониевый закаленный оксид алюминия
- Типы бронзы
- О проволочных формах — краткое руководство
- О проволочных изделиях — краткое руководство
- О нержавеющей стали – краткое руководство
- Титан: плотность, другие характеристики и применение
- Типы алюминиевых и никелевых сплавов
- Стандартные размеры листового металла
- Ведущие поставщики металлов
Еще из раздела Инструменты и элементы управления
Как определить твердость металлов?
РЕКЛАМА:
Следующие пункты выделяют три основных теста, проводимых для определения твердости металла. Тесты следующие: 1. Тест на твердость по Бринеллю 2. Тест на отскок (склероскоп Шора) 3. Тест на царапанье.
В этом испытании стандартный шарик из закаленной стали вдавливается в поверхность образца путем постепенного приложения нагрузки, которая удерживается на образце в течение определенного времени.
Полученный таким образом оттиск (рис. 2.50) измеряют с помощью микроскопа и определяют число твердости по Бринеллю (B.H.N.) по следующему уравнению:
где P = нагрузка (кг),
D = диаметр шара (мм) и
d = Диаметр отпечатка (мм).
Испытание проводят шариком из закаленной стали или карбида диаметром 10 мм. Нагрузку 3000 кг применяют для испытания ферросплавов и сплавов аналогичной твердости. При испытании латуни и мягких сплавов используют нагрузку 500 кг. Время загрузки указано между 10 и 30 секундами, в зависимости от исследуемого сплава.
РЕКЛАМА:
(i) Твердомер по Бринеллю:
Испытание на твердость проводят следующим образом:
Испытываемый образец помещается на верхнюю часть подъемного винта, и винт поднимается. Когда винт движется вверх, происходит электрическое соединение, и отражатель освещает поверхность образца. Затем на экране из матового стекла появляется четкое изображение стали, показывающее качество поверхности.
РЕКЛАМА:
Теперь, когда приборная панель настроена на правильную скорость нагрузки, рычаг нагрузки поднят почти на 30°, из этого положения он автоматически перемещается дальше до упора. За это время индентор перемещается в положение образца и производит вдавливание/отпечаток.
Рычаг возвращается в исходное положение примерно через 15 секунд. Одновременно объектив микроскопа занимает нормальное положение над образцом и таким образом на экране снимается отпечаток, увеличенный в 70 раз. Левый угол оттиска на экране совпадает с удобной градуировкой шкалы винтом с накатанной головкой, а правый угол – микрометрическим винтом и снимается отсчет.
Наконец, применяя уравнение:
Число твердости рассчитывается.
РЕКЛАМА:
Число твердости по Бринеллю в некоторой степени является показателем предела прочности металла на растяжение, которое можно определить, умножив число Бринелля на константу, которая зависит от характера металла или сплава. Эти константы также перечислены в таблицах.
Меры предосторожности:
(i) Испытание по Бринеллю следует проводить на гладких, плоских образцах, с которых были удалены грязь и окалина.
РЕКЛАМА:
(ii) Последовательные оттиски, сделанные слишком близко друг к другу, имеют тенденцию давать высокие показания (если нет перекрытия) из-за наклепа.
(iii) Испытание не должно проводиться на образцах настолько тонких, что отпечаток виден сквозь металл, а также не следует делать отпечатки слишком близко к краю образца.
Преимущества:
(i) Тест Бринелля, хотя и более сложный, чем тест на отскок, все же прост.
(ii) Не требует такой тщательной подготовки поверхности, как тест на отскок (или тест по Шору) и испытание по Роквеллу.
(iii) Его результаты хорошо коррелируют со свойствами при растяжении.
(iv) Хотя влияние модуля упругости входит в показатель твердости, это менее важный фактор, чем при испытании на отскок, где он вызывает некоторые трудности.
(v) Оттиск, сделанный машиной Бринелля, достаточно велик, чтобы дать довольно репрезентативную твердость, нечасто затронутую небольшими мягкими пятнами и небольшими твердыми пятнами.
Ограничения/недостатки:
(i) Ограничением теста Бринелля является размер отпечатка. Стандартный тест Бринелля производит настолько сильное впечатление, что при некоторых обстоятельствах его считают разрушающим тестом.
(ii) Большая часть испытательного оборудования имеет большой вес, хотя доступны портативные приборы.
(iii) Размер образца, который может быть испытан, ограничен отверстием между наковальней и пенетратором.
(iv) Тест довольно медленный из-за времени, необходимого для измерения диаметра и определения твердости.
(v) Тест Бринелля не совсем надежен, при работе с твердыми материалами указанная твердость часто меньше, чем твердость испытуемого материала. Очень твердые материалы могут деформировать шар, и показания станут ненадежными при температуре более 500 единиц по Бринеллю. В результате вместо измерителя Бринелля часто используются твердомеры, в которых используется алмаз конической или пирамидальной формы.
(ii) Испытание на твердость по Виккеру:
Здесь используется полированный алмазный инструмент с квадратным основанием и углом между гранями 136°. Этот инструмент при постепенной нагрузке оставляет отпечаток на образце. Нагрузка, деленная на площадь вдавливания в мм 2 , дает то, что известно как число твердости пирамиды (D.P.N.).
Это дается выражением-
Где, P = нагрузка в кг,
θ = угол между противоположными гранями и
d = средняя длина двух диагоналей в мм.
Нагрузка на плунжер с алмазом создается кулачком, который вращается барабаном, на который намотана проволока с грузом. Таким образом, нагрузка и время, в течение которого она применяется, контролируются механически.
Преимущества:
1. Преимущество Виккерса перед Бринеллем состоит главным образом в большей точности измерения диагонали квадрата по сравнению с диаметром круглого отпечатка Бринелля.
2. Тестер Виккера можно также использовать для испытания более твердых материалов, поскольку в нем используется алмаз.
Ограничения/недостатки:
1. Твердомеры Виккера намного сложнее и дороже, чем приборы Роквелла или Бринелля.
2. Их можно рассматривать как полумикротвердомеры из-за небольшого размера оттиска.
Примечание:
Твердомеры, в которых производится оттиск в форме ромба, даже более чувствительны, чем приборы Виккера, благодаря большей точности, с которой можно измерить длинную диагональ алмаза. Это настоящие микротвердомеры, основное применение которых заключается в измерении твердости составляющих частиц сплавов, тонких поверхностных упрочненных слоев, фольги и т. д.
Твердомер Бергсмана, который производит отпечаток типа Виккера, несколько дешевле, чем оборудование многих других производителей, потому что он адаптируется к стандартным металлографам и не требует собственного специального микроскопа.
(iii) Испытание на твердость по Роквеллу:
Испытание на твердость по Роквеллу, вероятно, является наиболее широко используемым методом определения твердости. Тестер Роквелла использует гораздо меньшие пенетраторы и нагрузки, чем тестер Бринелля. Доступны твердые шарики четырех размеров от 1/16 дюйма до 1/2 дюйма в диаметре, а также алмаз в форме конуса.
Для испытания металлических материалов чаще всего используются шар диаметром 1/16 дюйма и алмазный пенетратор. Патрон пенетратора механически соединен с циферблатным индикатором, реагирующим на вертикальное движение пенетратора. Поскольку пенетраторы маленькие, образец должен быть отшлифован гладко и чисто.
Образец помещают на наковальню машины, а пенетратор усаживают с помощью небольшой нагрузки 10 кг. Циферблатный индикатор обнуляется, а затем прикладывается большая нагрузка в 60, 100 или 150 кг, вдавливающая пенетратор в образец. После снятия большой нагрузки образец с отпечатком немного восстанавливается, а окончательная глубина проникновения регистрируется непосредственно на циферблатном индикаторе в виде числа твердости.
Различные комбинации пенетратора и основной нагрузки используются и обозначаются серией букв. Двумя наиболее распространенными весами являются весы HRB и весы HRC, соответствующие шару 1/16 дюйма с нагрузкой 100 кг и алмазному пенетратору с основной нагрузкой 150 кг. Как правило, алмазным пенетратором проверяются очень твердые материалы.
Мягкая сталь может иметь значение HRB 90; закаленная легированная сталь может иметь твердость HRC 55. Они обозначаются как HRB 90 и HRC 55.
Меры предосторожности:
(i) Последовательные оттиски не должны накладываться друг на друга или делаться слишком близко друг к другу при определении твердости.
(ii) Измерение не должно производиться слишком близко к краю или на образце настолько тонком, что отпечаток остается с другой стороны.
(iii) Тщательность, необходимая при подготовке поверхности для теста Роквелла, больше, чем для теста Бринелля, из-за меньшего отпечатка Роквелла.
(iv) Поверхность образца должна быть плоской и свободной от пружинящего действия.
(v) Поскольку отпечаток небольшой, желательно провести несколько измерений, чтобы получить репрезентативное значение твердости.
Преимущества:
(i) более гибкий, чем метод Бринелля; большое количество комбинаций инденторов и нагрузок делает более полезным испытание более широкого диапазона материалов.
(ii) Тестер Rockwell также оснащен рядом приспособлений для испытания металлических деталей различных размеров и форм.
(iii) Измерения твердости по Роквеллу можно производить почти так же быстро, как с помощью склероскопа Шора, поскольку они считываются непосредственно со шкалы прибора.
(iv) Из-за небольшого размера оттиска Роквелла тест считается неразрушающим для большинства применений.
Недостатки/Ограничения:
Тест Роквелла ограничен необходимостью большей осторожности при подготовке образцов, но это компенсируется его большей чувствительностью по сравнению с тестером Бринелля.
Это испытание было проведено А. Ф. Шором в 1910 году. В этом испытании стальной цилиндрический молот падает с высоты 25 см. через стеклянную трубку на исследуемую поверхность. Высота отскока используется как мера твердости поверхности. Испытываемая поверхность должна быть гладкой, очищенной от масла, а трубка должна быть строго вертикальной. Число твердости по Шору для стали составляет от 1/6 до 1/7 числа твердости по Бринеллю (B.H.N.).
Меры предосторожности:
(i) Инструмент должен быть расположен так, чтобы молоток падал и отскакивал вертикально.
(ii) Измерение не должно производиться на слишком тонких материалах.
(iii) Небольшие детали должны быть надежно закреплены на наковальне, чтобы избежать поглощения энергии при движении образца.
Преимущества:
(i) Небольшой размер отступа (еле виден), скорость и портативность.
(ii) Прибор легко брать с собой на работу.
(iii) Кроме того, поскольку не требуется, чтобы образцы подвергались давлению между пенетратором и наковальней, его можно использовать для изделий неограниченного размера.
Недостатки/Ограничения:
(i) Этот тест не обязательно дает более высокие показания для более твердых материалов.
(ii) Показания по Шору не так хорошо коррелируют с пределом прочности на растяжение, как твердость по Бринеллю, Роквеллу и Виккеру.
3. Испытание на царапанье:А Мартенс в 1890 году определил твердость царапания или нагрузку в граммах, при которой алмаз под углом 90° оставляет царапину шириной 0,01 мм. Согласно тесту Мора твердость железа и стали варьируется от 4 до 9 в зависимости от термической обработки и содержания сплава.
Главная ›› Металлургия ›› Металлы ›› Твердость ›› Определение ›› Как ›› Определение твердости металлов
Анализ твердости | Struers.

Struers – Обеспечение уверенности / Знания / Испытание на твердость
Согласие на использование файлов cookie
Файлы cookie используются в статистических целях и для улучшения сайта. Файлы cookie будут использоваться после того, как вы нажмете «ОК» или если вы продолжите использовать www.struers.com.
- Принять
- Подробнее
Определение твердости является ключевым элементом многих процедур контроля качества и научно-исследовательских работ.
Что такое испытание на твердость? Как выбрать наилучший метод определения твердости? Какое приложение лучше всего подходит для измерения твердости? А как можно делать выводы испытаний на твердость? Следующие страницы отвечают на эти и другие вопросы.
Чтобы ознакомиться с нашим ассортиментом машин и принадлежностей для определения твердости, посетите нашу страницу с оборудованием для определения твердости.
См. наши указания по применению для определения твердости
См. наш плакат о переходе на твердость
- О
- Как
- Исправление проблем
- Контакт
Применение испытаний на твердость позволяет вам оценить свойства материала, такие как прочность, пластичность и износостойкость, и, таким образом, помочь вам определить, подходит ли материал или обработка материала для требуемой цели.
Испытание на твердость определяется как «испытание для определения стойкости материала к остаточной деформации при проникновении в другой более твердый материал». Однако твердость не является фундаментальным свойством материала. Поэтому, делая выводы по тесту на твердость, всегда следует оценивать количественное значение в отношении:
- Приведенная нагрузка на индентор
- Определенный профиль времени загрузки и определенная продолжительность загрузки
- Особая геометрия индентора
Как работают тесты на твердость?
Испытание на твердость обычно выполняется путем вдавливания нагруженного предмета (индентора) определенного размера в поверхность тестируемого материала. Твердость определяется путем измерения глубины проникновения индентора или измерения размера отпечатка, оставленного индентором.
- Испытания на твердость, которые измеряют глубину проникновения индентора, включают: испытание по Роквеллу, инструментальное испытание на вдавливание и твердость на вдавливание шариком
- Испытания на твердость, которые измеряют размер отпечатка, оставленного индентором, включают: Виккерса, Кнупа и Бринелля
ВЫБОР НАИЛУЧШЕГО МЕТОДА ИЗМЕРЕНИЯ ТВЕРДОСТИ
Как выбрать метод испытания
Выбранный вами тест на твердость должен определяться микроструктурой, т.е. однородность – тестируемого материала, а также тип материала, размер детали и ее состояние.
Во всех испытаниях на твердость материал под отпечатком должен отражать всю микроструктуру (если только вы не пытаетесь определить различные компоненты микроструктуры). Поэтому, если микроструктура очень грубая и неоднородная, вам нужен больший оттиск, чем для однородного материала.
Существует четыре основных теста на твердость, каждый из которых имеет свои преимущества и требования. Для этих тестов существуют разные стандарты, в которых подробно объясняются процедуры и применение теста на твердость.
При выборе метода определения твердости важно учитывать следующее:
- Тип материала, подлежащего испытанию на твердость
- Требуется ли соответствие стандарту
- Примерная твердость материала
- Однородность/неоднородность материала
- Размер детали
- Требуется ли монтаж
- Количество образцов для испытаний
- Требуемая точность результата
Четыре наиболее распространенных теста на твердость при вдавливании
Испытание на твердость по Роквеллу
По Роквеллу — это быстрый метод определения твердости, разработанный для производственного контроля, с прямым считыванием, в основном используемый для металлических материалов. Твердость по Роквеллу (HR) рассчитывается путем измерения глубины отпечатка после того, как индентор был вдавлен в материал образца при заданной нагрузке.
- Обычно используется для образцов более крупной геометрии
- «Быстрый тест», используемый в основном для металлических материалов
- Может использоваться для расширенных испытаний, таких как испытание Джомини (концевая закалка) (HRC)
Узнайте больше о тесте на твердость по Роквеллу
Испытание на твердость по Виккерсу
Испытание на твердость по Виккерсу для всех твердых материалов, включая металлические материалы. Твердость по Виккерсу (HV) рассчитывается путем измерения длины диагонали отпечатка в материале образца, оставленного индентором с алмазной пирамидой при заданной нагрузке. Диагонали отпечатка измеряются оптически, чтобы определить твердость, используя таблицу или формулу.
- Используется для определения твердости всех твердых материалов, включая металлические материалы
- Подходит для широкого спектра применений
- Включает подгруппу испытаний сварных швов на твердость
Узнайте больше о тесте на твердость по Виккерсу
Испытание на твердость по Кнупу
Испытание по Кнупу (HK) является альтернативой испытанию по Виккерсу в области измерения микротвердости. Он в основном используется для преодоления трещин в хрупких материалах, а также для облегчения проверки твердости тонких слоев. Индентор представляет собой асимметричный пирамидальный алмаз, а отпечаток измеряется оптическим измерением длинной диагонали.
- Используется для твердых и хрупких материалов, таких как керамика
- Подходит для небольших вытянутых поверхностей, таких как покрытия
Подробнее о тесте твердости по Кнупу
Испытание на твердость по Бринеллю
Испытание на твердость по Бринеллю используется для испытания на твердость больших образцов материалов с крупнозернистой или неоднородной структурой. Вдавливание при испытании на твердость по Бринеллю (HBW) оставляет относительно большой отпечаток с использованием шарика из карбида вольфрама. Размер отступа читается оптически.
- Используется для материалов с крупнозернистой или неоднородной структурой
- Используется для больших образцов
- Подходит для поковок и литья с большими структурными элементами
Узнайте больше о тесте на твердость по Бринеллю
КАК ОБЕСПЕЧИТЬ ТОЧНОСТЬ И ПОВТОРЯЕМОСТЬ ПРИ ИСПЫТАНИЯХ НА ТВЕРДОСТЬ
Правильное применение определения твердости требует тщательной подготовки и выполнения. Однако, как только у вас есть основы, большинство тестов на твердость обеспечивают хорошую точность и воспроизводимость.
Факторы, влияющие на определение твердости
На результаты испытаний на твердость влияет ряд факторов. Как правило, чем меньшую нагрузку вы используете при испытании на твердость, тем больше факторов необходимо контролировать, чтобы обеспечить точное заключение испытания на твердость.
Вот несколько наиболее важных факторов, которые следует учитывать, чтобы обеспечить точное заключение по результатам испытания на твердость.
- Необходимо контролировать внешние факторы, такие как свет, грязь, вибрации, температура и влажность
- Тестер и столик должны быть закреплены на твердом горизонтальном столе, а образец должен быть зажат или удерживаться в держателе или наковальне
- Индентор должен быть перпендикулярен тестируемой поверхности
- Параметры освещения должны быть постоянными во время теста при использовании Виккерса, Кнупа или Бринелля
- Тестер следует повторно калибровать/поверять каждый раз, когда вы меняете индентор или линзу объектива
Требования к подготовке поверхности для определения твердости
Перед испытанием на твердость металлических материалов или других материалов необходимо подготовить поверхность. Требуемое состояние поверхности зависит от типа испытания и используемой нагрузки. Как правило, качество подготовки поверхности оказывает прямое влияние на результат теста на твердость, поэтому вам следует рассмотреть компромисс между качеством поверхности и разбросом результатов теста, прежде чем принимать решение о менее качественной подготовке поверхности.
Определение макротвердости
Обычно достаточно отшлифованной поверхности, иногда подготовка не требуется.
Измерение микротвердости
Из-за меньших нагрузок, используемых при измерении твердости, для определения микротвердости требуется полированная или электрополированная поверхность. Важно, чтобы границы/углы оптически оцениваемого оттиска были хорошо видны. Это может быть выполнено механическим, химическим или электрохимическим способом. Важно, чтобы нагрев или холодная обработка не изменили свойства поверхности образца.
Деформации
Резка и шлифовка могут привести к деформации. Их необходимо удалить путем полировки до 6,0, 3,0 или 1,0 мкм, в зависимости от испытательной нагрузки на твердость.
При небольших нагрузках (менее 300 гс1) поверхность должна быть полностью бездеформационной, а образцы требуют оксидной или электролитической полировки для получения полностью неповрежденной поверхности. Также следует учитывать, что мягкие и/или пластичные материалы (т.е. для HV менее 120-150) более чувствительны к введению артефактов препарирования.
В таблице ниже приведены требования к подготовке поверхности для различных испытаний на твердость.
ОПРЕДЕЛЕНИЕ НАГРУЗОК ДЛЯ ИСПЫТАНИЙ НА ТВЕРДОСТЬ
Официально нагрузки для испытания на твердость выражаются в ньютонах (Н). Однако исторически нагрузки выражались в килограммах-силах (кгс), граммах-силах (гс) или весах (p). Соотношение между кгс, кп и Н составляет: 1,0 кгс = 1000 гс = 1,0 кп = 9,81 Н.
- Термин «испытание на микротвердость» обычно используется, когда нагрузки на вдавливание меньше или равны 1 кгс
- Термин «испытание на макротвердость» используется, когда нагрузки превышают 1 кгс
Если стандарты позволяют, используйте максимально возможную нагрузку/силу для наибольшего отступа, чтобы обеспечить наиболее точные результаты.
Нагрузки, используемые каждым из четырех методов определения твердости металлических материалов*, соответствуют различным стандартам ISO и ASTM.
РАСПРЕДЕЛЕНИЕ ВПЕЧАТКИ
Во время испытания на твердость вмятина деформирует окружающий материал и изменит его свойства. Во избежание неправильного толкования воспринимаемой твердости стандарты предписывают определенное расстояние между несколькими углублениями.
Примеры расположения отпечатков при определении твердости по Виккерсу для металлических материалов
- Для стали, меди и медных сплавов: расстояние между отпечатками должно быть не менее трех ширин по диагонали
- Для свинца, цинка, алюминия и олова: расстояние между зубцами должно быть не менее шести диагоналей
ПОИСК И УСТРАНЕНИЕ НЕИСПРАВНОСТЕЙ ПРИ ИСПЫТАНИЯХ НА ТВЕРДОСТЬ
Проблема
При подготовке к испытанию на твердость могут возникнуть трудности с получением плоскопараллельных поверхностей. Кроме того, индентор должен располагаться перпендикулярно тестируемой поверхности. Для теста на твердость по Виккерсу измеренные диагонали не должны отклоняться друг от друга более чем на 5,0%. Для теста на твердость по Кнупу две половины длинных диагоналей не должны отличаться друг от друга более чем на 10,0%.
Показать больше
Решение:
Если отклонение не связано с анизотропией материала, лучшим решением будет использование приспособления для удержания образца таким образом, чтобы индентор проникал в поверхность перпендикулярно. Если приспособление отсутствует, убедитесь, что механическая подготовка образца дает плоскопараллельные торцевые поверхности.
Если поверхность образца слишком шероховатая, может быть трудно оценить углы отпечатка, особенно при использовании автоматического оборудования. Царапины от препарирования могут привести к неправильному считыванию размера отпечатка при использовании автоматического определения твердости.
Показать больше
Решение
Используйте полированную поверхность. Требования к подготовке поверхности зависят от приложенной нагрузки и твердости материала: чем мягче материал, тем лучше требуется полировка. См. требования к подготовке в разделе «Как проводить испытание на твердость» и найдите подходящий метод подготовки для материала в e-metalog.
Если образец не очищен должным образом после механической подготовки и вы выполняете оптическое считывание теста на твердость, автоматическое считывание может привести к неправильной интерпретации углов отпечатка.
Показать больше
Раствор
Всегда проверяйте, чтобы образцы были должным образом очищены перед выполнением теста на твердость, в противном случае загрязнения от полировальной ткани (например, грязь или волокна) могут затруднить измерение.
Для сильно протравленного образца может быть трудно оценить углы отпечатка, что может привести к менее точным выводам теста на твердость.
Показать больше
Раствор
По возможности следует избегать травления, так как оно приводит к снижению отражающей способности поверхности. Если необходимо травление, предпочтительнее легкое травление, чтобы можно было выделить углы отпечатка. Иногда может потребоваться травление, например, при оценке сварного шва.
Твердость выше ожидаемой.
Показать больше
Решение
Проверьте правила относительно правильного расстояния между зубцами для предполагаемого испытания на твердость. Если углубления твердости расположены слишком близко друг к другу, может появиться деформационное упрочнение.
ПОЛНЫЙ АССОРТИМЕНТ МАШИН ДЛЯ ИЗМЕРЕНИЯ ТВЕРДОСТИ
Определение твердости является ключевым в большинстве процедур контроля качества. Вот почему мы предлагаем полный спектр оборудования и принадлежностей для измерения твердости для любых нужд, от небольших лабораторных приложений до тяжелых испытаний на твердость в производстве.
Ознакомьтесь с нашим ассортиментом оборудования для измерения твердости, чтобы убедиться, что ваше оборудование соответствует поставленной задаче.
Посмотрите наше оборудование для измерения твердости
УЗНАТЬ БОЛЬШЕ О ТЕСТИРОВАНИИ ТВЕРДОСТИ
Если вы хотите узнать больше о методах измерения твердости металлических и других материалов, включая полное определение определения твердости, различные области применения испытаний на твердость и способы подготовки к испытаниям на твердость, загрузите нашу Ресурсы.
См. наши указания по применению для определения твердости
См. наш плакат о переходе на твердость
Хелле Михаэльсен
Global Business Solution & Application Manager
Struers Aps.
Баллеруп, Дания
Контакт
Биргитте Нильсен
Металлограф,
Специалист по применению
Struers Aps.
Баллеруп, Дания
Контакт
Мария Линдегрен
Кандидат наук. в обработке металлов давлением,
Специалист по применению
Struers Aps.
Баллеруп, Дания
Контакт
Олафур Олафссон
PhD, инженер-механик,
Специалист по применению
Struers Aps.
Баллеруп, Дания
Контакт
Фарук Музафер
Специалист по применению
Struers ApS
Ballerup, Дания
Контакт
Мэтью Кодуэлл
Заведующий лабораторией
Struers Ltd.
Ротерхэм, Великобритания
Контакт
Хольгер Шнарр
Степень доктора технических наук и степень инженера в области материаловедения,
Специалист по применению
Struers GmbH
Виллих, Германия
Контакт
Ульрих Сетцер
Инженер-материаловед, степень технического ассистента по металлографии и материаловедению,
Специалист по применению
Struers GmbH
Виллих, Германия
Контакт
Римский герундий
Степень технического ассистента по металлографии и материаловедению,
Специалист по применению
Struers GmbH
Willich, Германия
Контакт
Кэролайн Муссу
Руководитель лаборатории
Struers SAS
Шампиньи-сюр-Марн, Франция
Контакт
Кристиан Вегерски
Специалист по применению
Struers GmbH
Willich, Германия
Контакт
Марко Карузо
Металлограф,
Специалист по применению
Struers S. A.S.
Арезе, Италия
Контакт
Генри Удомон
Менеджер приложений
Struers Inc.
Кливленд, Огайо, США
Контакт
Келси Торболи
Инженер по применению
Struers Inc.
Кливленд, Огайо, США
Контакт
Брайан Джонс
Инженер по применению
Struers Inc.
Кливленд, Огайо, США
Контакт
Эллис Перри
Инженер по применению
Struers Inc.
Кливленд, Огайо, США
Контакт
Сюпин Цзян
к.т.н., магистр наук. в области материаловедения и инженерии,
Менеджер по применению и лаборатории
Struers Ltd.
Шанхай, Китай
Контакт
Райан Яо
Специалист по применению
Struers Ltd
Шанхай, Китай
Контакт
Киничи Исикава
г-жа К. в области промышленных наук,
Специалист по применению
Struers K.