Как определить твердость металла – . , , , . .
alexxlab | 24.01.2020 | 0 | Разное
Как определить твердость стали 🚩 Естественные науки
Автор КакПросто!
Одним из важнейших показателей любого металла является твердость, которая характеризует его способность сопротивляться проникновению в него другого тела, обладающего большей твердостью. Сталь не является исключением.
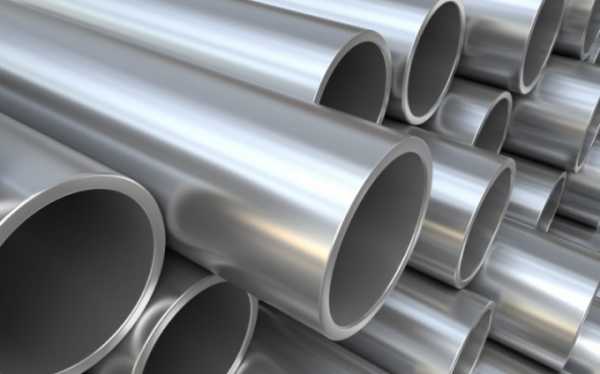
Статьи по теме:
Инструкция
Прочность стали тесно связана с такими ее характеристиками, как износостойкость, прочность и пр. Существует немало способов определения твердости металлов. Один из них – метод Бринелля, когда в поверхность металла (стали) с помощью специального пресса (пресса Бринелля) вдавливается стальной шарик. По окончании воздействия шарика на металлическую поверхность с помощью специальной лупы производится замер диаметра лунки. На основании данных таблиц, прилагаемых к прессу, определяется твердость стали НЕ. Следующий метод – метод Роквелла – предполагает вдавливание в стальную поверхность алмазного конуса с углом 1200 у вершины. Вдавливание осуществляется вначале с предварительной нагрузкой 10 кг, а затем полной – от 60 до 150 кг. Для этого также используется специальный пресс.При использовании данного метода необходимо соблюдать некоторые требования. Так, на исследуемой поверхности не должно быть окалины, трещин и выбоин. Воздействие на поверхность строго перпендикулярно. Для определения значения прочности также используются специальные таблицы. Существует четкая зависимость – чем тверже сталь, тем меньше глубина проникновения в нее при вдавливании и, следовательно, тем выше значение твердости.
С методом Роквелла схож метод Виккерса, в котором для вдавливания используется четырехгранная алмазная пирамида с углом у вершины 1360. Здесь по окончании нагрузки измеряется диагональ отпечатка. Для сталей время воздействия – 10-15 сек. При этом усилие должно прилагаться строго перпендикулярно поверхности с плавным нарастанием. Поверхность опытного образца может иметь шероховатость не более 0.16 мкм, а расстояние между центром отпечатка и краем образца или соседнего отпечатка – не менее 2.5 длины диагонали отпечатка.
Твердость стали определяется также методом ударного отпечатка посредством твердосплавного конического индентора или стального шара. К косвенным методам относится методика измерения твердости по Шору. В ней используется боек определенной массы с алмазным наконечником, вертикально падающий с определенной высоты на испытуемую поверхность. Высота отскока бойка является характеристикой твердости, которая измеряется в условных единицах.
Видео по теме
Совет полезен?
Статьи по теме:
Не получили ответ на свой вопрос?
Спросите нашего эксперта:
www.kakprosto.ru
Определение твердости металлов — МегаЛекции
Твердостью называется свойство металла сопротивляться внедрению в него другого, более твердого тела. Испытания на твердость широко применяются в производственных условиях, так как имеют следующие преимущества:
– поверхностное испытание твердости не сопровождается разрушением заготовок или деталей;
– приборы для проверки твердости отличаются высокой
производительностью (до 300 испытаний в час) и простотой обслуживания;
– в условиях серийного и массового производства испытанию на твердость можно подвергать 100% ответственных деталей, тогда как при других видах испытаний может быть осуществлен только выборочный контроль для определения среднего качества металла изготовленных деталей;
– результаты испытаний на твердость позволяют с достаточной для практических целей точностью судить о других прочностных характеристиках испытываемого металла, а также определять его способность поддаваться обработке.
Применяемые в настоящее время методы определения твердости металлов делятся на статические и динамические.
Наиболее распространенными статическими методами испытания на твердость являются методы, основанные на плавном и постепенном вдавливании в испытываемый образец стального закаленного шарика, алмазного конуса или алмазной пирамиды – измерение с медленно нарастающей (статической) нагрузкой (твердость по Бринеллю, по Роквеллу и по Виккерсу).
Из числа динамических испытаний можно назвать метод упругой отдачи (метод Шора) и метод ударного вдавливания стального закаленного шарика.
Для определения микротвердости (твердости отдельных структурных составляющих) существуют специальные приборы, на которых вдавливание наконечника в испытуемую поверхность производится под небольшими нагрузками (5 – 500 Г).
Твердость по Бринеллю определяется на прессе Бринелля. Нагрузка с помощью гидроцилиндра с маслом и поршня передается на шарик определенного диаметра из закаленной стали, который вдавливается в испытуемый материал с силой P, превышающей предел упругости материала, в результате чего в испытуемой детали образуется углубление в виде шарового сегмента. Если F – площадь наружной поверхности сегмента, то твердость выражается числом HB = P/F кГ/мм2. Величина F может быть вычислена по глубине вдавливания h или по диаметру сегмента d (рис. 3.17)
Рис.3.17
Таким образом для определения твердости по Бринеллю необходимо измерить диаметр отпечатка шарика, который для этих целей используется размером D = 10 мм; D = 2,5 мм и вдавливается под давлением P = 3000 кг; P = 1000 кг и P = 250 кг и по таблице определить твердость в зависимости от диаметра этого отпечатка.
Необходимо отметить, однако, что более точным способом является измерение не диаметра отпечатка, а его глубины, так как лишь при измерении глубины отпечатка удается получить цифры твердости
Диаметр шарика и давление должны соответствовать испытываемому образцу. Поверхность образца должна быть тем чище приготовлена, чем больше его твердость. Нужно удалить окалину и грат, а также обезуглероженный поверхностный слой.
Твердость по Бринеллю и сопротивление разрыву стоят в тесной связи. Так как для стали (при HB > 175 кг/мм2) временное сопротивление разрыву равно твердости по Бринеллю, умноженной на 0,345; для стали с HB < 175 кг/мм2 – sb = 0,362 HB; для никелевой и хромоникелевой стали sb = (0,35-0,34) HB; для дюралюминия sb = 0,35 HB.
В случае, если не требуется высокая точность измерения твердости и нет в наличии пресса Бринелля можно воспользоваться небольшим прибором Польди. Этот прибор, в отличие от пресса, работает динамической, а не статической нагрузкой. Для практических целей этот способ вполне пригоден, так как дает ошибку, не превышающую 7 %.
Твердость по Виккерсу измеряется на приборе, построенном фирмой Виккерс, при помощи алмазной пирамиды с углом при вершине 136°. Твердость определяется отношением нагрузки 50 кг к поверхности отпечатка. Размер отпечатка на приборе Виккерса измеряется специальным микроскопом, являющимся частью всего прибора. Измерение твердости по Виккерсу обладает преимуществом по сравнению с испытанием по Бринеллю, так как в пределах больших твердостей дает более точные результаты. Кроме того при измерении по Виккерсу удобством является большая четкость отпечатка алмазной пирамиды, чем стального шарика.
Твердость по Роквеллу определяется глубиной внедрения в испытуемый материал стального шарика или конического алмаза при определенном повышении давления. Глубина погружения измеряется индикатором, стрелка которого непосредственно отсчитывает твердость. Для мягких материалов обычно применяется стальной шарик Æ 1,59 мм (1/16¢¢) (отсчеты производятся по красной шкале В), для более твердых конический алмаз с конусностью в 120° (черная шкала С). В обоих случаях первоначальное давление составляет 10 кГ. Конечное давление для стального шарика доводится до 100 кг, для алмаза – 150 кГ. Увеличение давления производится автоматически и равномерно при помощи масляного тормоза в течение от 3 до 5 с. Глубина внедрения колеблется от 0,06 мм для алмазного конуса и закаленной стали и до 0,25 мм для стального шарика и мягких материалов.
Для проверки твердости на приборе Роквелла (рис.3.18) образец 3 устанавливается на стол 4. Затем с помощью винта, вращаемого маховиком 5, вводят образец в соприкосновение с алмазным или шариковым наконечником 2 до тех пор, пока малая стрелка индикатора не подойдёт к нулю, а большая не займёт приблизительно вертикальное положение. Это положение стрелок соответствует предварительной нагрузке 10 кГ. После этого шкалу 1 индикатора поворачивают до совпадения конца большой стрелки с нулевым делением (при измерении алмазом) или с тридцатым делением внутренней шкалы (при испытании шариком). Затем, поворачивая рукоятку 6, добавляют основную нагрузку. Под действием общей нагрузки (150, 100 или 60 кГ) алмаз или шарик вдавливается в испытываемую поверхность. При этом большая стрелка индикатора начинает вращаться. Когда стрелка остановится, основную нагрузку снимают, поворачивая рукоятку 6 в исходное положение, и непосредственно по шкале 1 индикатора отсчитывают твердость. После этого, ослабив винт, снимают образец со стола прибора. Индикатор имеет две концентрические шкалы с делениями от 0 до 100:
– наружную (обычно черного цвета) для отсчета величины твердости при проверке алмазным конусом по шкале С при нагрузке 150 кГ и по шкале А при нагрузке 60 кГ;
– внутреннюю (обычно красного цвета) для отсчета числа твердости при проверке шариком по шкале В.
а б
Рис.3.18. Прибор Роквелла (а) и шкала индикатора прибора (б)
Твердость по Шору определяется склероскопом. Последний состоит из стального ударника с алмазным наконечником весом 2,6 кг, падающего с определенной высоты (257 мм) на горизонтальную поверхность испытуемого образца. Чем тверже образец, тем меньше будет его деформация, вызванная кинетической энергией ударника, и тем выше будет его отскок. Направляющей для ударника служит стеклянная трубка, по делениям которой отсчитывается высота отскока ударника. Для мягких материалов применяется ударник с широкой нижней поверхностью без алмаза. Измерение твердости склероскопом может быть произведено чрезвычайно быстро (до 1000 промеров в час), что является большим преимуществом этого способа.
Кроме указанных методов используются методы измерения твердости по Мосу (метод царапания для минералов и металлов) и по Герберту с помощью маятникового прибора. Ввиду очень высокой чувствительности последнего этот метод очень редко используется для заводской работы и применяется большей частью в научно-исследовательских лабораториях и институтах.
Таблица 3.13
Сравнительная таблица твердости металлов и сплавов (ориентировочно) по Бринеллю, Роквеллу, Виккерсу и Шору
Бринелль НВ | Роквелл НRС | Виккерс НV | Шор | Бринелль НВ | Роквелл НRС | Виккерс
| Шор |
- | |||||||
- | |||||||
- | |||||||
- | |||||||
Продолжение табл. 3.13 | |||||||
- | |||||||
- | |||||||
- | |||||||
- | |||||||
- | |||||||
- | |||||||
- | |||||||
- | |||||||
- | |||||||
- | |||||||
- | |||||||
- | |||||||
- | |||||||
- | |||||||
- | |||||||
- |
Технологические пробы
Технологическими пробами называются испытания, выявляющие способность металла деформироваться (изменять форму) под воздействием внешних сил. К ним относятся проба на загиб, проба на осадку, проба проволоки на навивание, проба на обрабатываемость, проба листового металла на вытягивание и др.
Порядок проведения технологических проб и требования к образцам стандартизированы.
Проба на загиб производится в холодном или нагретом состоянии на прессах, в тисках или на специальных приборах и служит для определения способности металла поддаваться загибу в соответствии с заданными размерами и формой. Результаты испытания считаются удовлетворительными, если в образце после загиба отсутствуют трещины, расслоения или излом.
Пробе на осадку подвергаются цилиндрические образцы из черных металлов и алюминиевых сплавов, которые в виде прутков и проволоки применяются для изготовления болтов, заклепок и других крепежных деталей. Образцы испытывают в холодном или горячем состоянии под прессом или механическим или пневматическим молотом. Материал считается годным, если на боковой поверхности образцов, подвергнутых испытанию, нет трещин, закатов и надрывов. На боковой поверхности образцов из алюминиевых сплавов не должно быть также шероховатости и расслоений.
Испытание проволоки на навивание производится в холодном состоянии. Проволоку диаметром до 6 ммнавивают плотно прилегающими друг к другу витками на цилиндрическую оправку, диаметр которой задается техническими условиями.
После испытания проволока не должна иметь надрывов, трещин и излома как в материале образца, так и в его защитном слое (в оцинкованных, луженых и тому подобных деталях).
Кроме указанного метода испытания проволоки на навивание, стандартами установлены методы технологических испытаний на перегиб и на скручивание холоднотянутой и горячекатаной проволоки диаметром 0,8 – 10 мм.
Стандартизованы также испытания металлов на кручение, расплющивание, прокаливаемость, свариваемость, перегиб, развертывание фасонного материала, испытание тонколистового материала на двойной кровельный замок, испытание труб гидравлическим давлением, а также бортование, загиб, раздачу и сплющивание.
Оглавление
Рекомендуемые страницы:
Воспользуйтесь поиском по сайту:
megalektsii.ru
как измерить твердость стали народными способами
Balllu 17-09-2008 15:29Собственно САБЖ
Конечно понимаю что надфиль не берет, значит больше 60
стекло царапает значит, больше 62(с), но ведь есть и меньше 60, причем рабочий клинок получится и ведь для некоторых марок сталей данная твердость предпочтительней. А допустим начинающие энтузиасты просто недокаливают сталь(ну не получается). В этой связи кто нибудь может посоветовать простые способы измерения твердости в домашних условиях, но в более широком диапазоне хотя бы 56-62
“надфиль берет легко” – “надфиль еще берет” – “надфиль не берет” – “стекло царапает с трудом” – “стекло царапает уверенно” – “стекло царапает с хрустом и обильной крошкой”
Еще есть пособ аналогичный определению твердости по Моосу: взаимное царапание с эталонными клинками. Особенно пригоден для определения нижней границы пригодности: если китайский кухонник не царапает испытуемый клинок, то ништяк – 55HRC наберется.
GAU-8A 17-09-2008 16:36В граничащих областях, начиная с 58 и примерно до 62 довольно несложно определить с помощью качественного нового надфиля (не алмазного), но тоже нужен определенный опыт. А вот что ниже 57-55 довольно сложно, даже затрудняюсь что сказать. Может сравнивать с виксом и опинелями из нержи? Там все таки стабильно 53-54ед.
WeS 17-09-2008 16:59Сорри за ОФФ, а на Виксах какая сталька, кто знает?
Balllu 17-09-2008 17:15Просьба не флудить, офф не приветствуется, думаю сама тема интересна не только мне.
Если у кого еще мысли есть по поводу темы не стесняемся выкладываем.
Если кто знает твердость каких нибудь широко распространенных вещей у которых она стабильно, то тоже можно поделиться инфой.
Nasgul 17-09-2008 17:42мне вот с надфилями не совсем ясно.. я раньше серейтор на быстрорезе р6м5 надфилем делал, точнее надфилями и долго, но делал, так что мех полотно меньше 60?
GAU-8A 17-09-2008 18:13НЕ алмазный качественный надфиль имеет твердость 63-64ед. Рабочая твердость р6м5 такая же. Если вы обрабатывали ее, и долго, она должна иметь тв. не более 57ед. иначе надфиль попросту бы сел через полминуты.
DECEMBER 17-09-2008 18:18quote:
так что мех полотно меньше 60?
Не обязательно. Пока насечка новая, грызёт разницу в пару-тройку Роквеллов. На новом надфильке когда-то (для проверки ) насечку сошлифовали и подсунули под твёрдомер – показал 64HRC. Попадались и с 60HRC. Зависит от изготовителя и тех. процесса. Может просто цементацию сделали, а может и азотирование ( до 67…70 догнать можно).
GAU-8A 17-09-2008 18:19
quote:
Сорри за ОФФ, а на Виксах какая сталька, кто знает?
углер. 0,52%…хрома 15%…марг. 0,45%…кремн. 0,6%…молиб. 0,5%.
Категорично утверждать не буду, но вот такая инфа.
chief 17-09-2008 18:48
quote:
Originally posted by WeS:
Сорри за ОФФ, а на Виксах какая сталька, кто знает?
Твёрдость?
Кухонники 53-55, так написано.
они таки садились! и очень быстро, но грызли мал мал, по тому и засмущался, как это называть-берёт надфиль или не берёт.(долго в том смысле, что очень медленно)
спасибо за разъяснения
С Бокеревской 440С закаленной на 58ед. практически работать уже невозможно – надфиль быстро садится.
Balllu 17-09-2008 20:49Итак небольшой подитог: на надфиль полагаться не совсем корректно т.к. разброс твердости может составлять от 60 до 70. Обычный не алмазный надфиль всё же имеет твердость 63-64 и должен в этом случае царапать стекло.
Можно попробывать виксом или опинелем, у которых стабильно 53-54ед.
Всё так или у кого еще мнения… высказываемся
Balllu 17-09-2008 20:51quote:
Originally posted by GAU-8A:
В граничащих областях, начиная с 58 и примерно до 62 довольно несложно определить с помощью качественного нового надфиля
почему нового и как определить?kU 17-09-2008 20:59
надфиль грызет сталь по-разному в зависимости от износа.
GAU-8A 17-09-2008 21:31quote:
почему нового и как определить?
Как определить? лишь на основании предыдущего опыта… тут много от чего зависит, от нажима например. Ну, если грубо – берет уверенно 55-56…. берет и как бы не берет 59-60…еле цепляет примерно 61…начинает посвистывать – более 62х.
Пробовать нужно на ребре, на грани металла. А новым потому, что реультат будет более точным. На словах трудно передать…
boroda-fish 17-09-2008 23:30
Уважаемые!ИМХО имеется:
Многие из вас замечали-один лист стекла после алмаза-стеклореза режется(ломается по царапине) ровно, легко, другой же норовит трещину в бок направить-куда угодно только не по царапке(так называемое перекаленное стекло)?На работе, на тарированном твердомере проверяли-перекаленное стекло царапается железкой шлифованной на конус около60 градусов начиная с 62-64 единиц, уверенно, царапина глубокая, мелькие чешуёвинки стеклянные отлетают от линии реза;не “калёное”-уверенно царапается с 57-58 единиц с обламыванием даже по волнистой линии весьма уверенным(видимо такое подбирают продавцы китаёзных “чудо-стеклорезов”-ролики с пары таких показали 57-58 HRS возле рк.)Всё это ИМХО проверенное на приборчиках.
——————
С уважением boroda-fish
Есть несколько варварский способ – “ударный” (не факт что это работает, но мне кажется должно), просто делаю удар уголком-ребром интересуемой стали об уголок-ребро стали известной твердости (углы дожны быть одинаковые , допустим 90градусов). Затем делаю осморт, на какой стали осталась зарубка – эта сталь мягче. Если иметь допустим три образца известной твердости, тогда можно получить не плохой результат. Данный метод плох для готовых ножей, ибо становиться по-истене варварским. Для себя знаю, что хорошо закаленная и отпущенная 40Х13 это никак не больше 54единиц; тоже самое для 95Х18 – 57, ну с натягом 58 единиц; есть полотно от ножа для электофуганка (стальУ8) – точно 59 единиц. Надо бы подобрать что-то в районе 61ед. (надо попробовать кусок ШХ на работу отнести ).
Если я не прав, буду рад за наставление на путь истенный (надфиль и стекло тож пользую).
quote:
Для себя знаю, что хорошо закаленная и отпущенная 40Х13 это никак не больше 54единиц; тоже самое для 95Х18 – 57, ну с натягом 58 единиц; есть полотно от ножа для электофуганка (стальУ8) – точно 59 единиц.
Все это правильно ,если калить по тем технологиям, что расписаны в справочниках. Однако хороший опытный термист выжмет из этих сталей гораздо больше, не увеличивая при этом хрупкости. И вообще ,надо иметь в виду ,что заводские технологии написаны так ,что любой ПТУшник получит нужный результат ,имея хоть минимальные навыки .DECEMBER 18-09-2008 09:50
quote:
С Бокеревской 440С закаленной на 58ед. практически работать уже невозможно – надфиль быстро садится.
OFF:На подобные стали немного другие углы на инструменте нужны . Да и работать надфилем по калёной – это не жалеть инструмент . Камушки, брусочки, шкурочка… Вообще с нержавейкой мороки больше… (Для меня по крайней мере )
GAU-8A 18-09-2008 10:40
Udod, прошу понять меня правильно, то что напишу далее – не для спора, а только лишь истины ради, ну, если угодно, или приближения к ней.
Выжать конечно можно, но это уже нарушение т.о., а оно как известно берется не с бухты барахты, а с учетом хим-состава стали и ничего кроме как ухудшения на выходе конечного продукта за собой повлечь не может.
Ни сколько не сомневаюсь, что например сталь на Виксе (54ед.) можно закалить и на 58ед., а сталь Х12мф и на 64ед. и.т.д…. последствия этого не трудно представить.
Блин! что кроме стекла и надфиля ни чего нет?
Ну скажем как определить закалилась заготовка или нет, а то может там вообще 40 ед.
Или вот возьмем к примеру корпуса замков навесных, у многих они чугунно литые, может по ним заготовкой стучать и смотреть на зазубрины. Если нет готовых способов их надо самим придумать и проверить, так что велкам, выкладывайте идеи
Бутылка – лучший друг термиста.
Alan_B 18-09-2008 19:07quote:
Бутылка – лучший друг термиста.
+100
Но бутылко – оно разное бывает, например, Кронидура при 59-60 бутылку из под Старопрамена царапает уверенно и с хрустом а по Старому мельнику елозит едва цепляя… Наши бытылки – самые твердые в мире :-))
В общем и целом, имея некоторое количество предметов с известными свойствами можно достаточно точно определить твердость своего ножа.
quote:
Originally posted by Alan_B:
В общем и целом, имея некоторое количество предметов с известными свойствами можно достаточно точно определить твердость своего ножа
Вот и идея в том чтоб эти предметы выявить желательно массового производства и легко доступные в народе, а еще лучше те которые почти у каждого человека дома естьchief 18-09-2008 20:31
quote:
Originally posted by Balllu:
Вот и идея в том чтоб эти предметы выявить желательно массового производства и легко доступные в народе, а еще лучше те которые почти у каждого человека дома есть
У меня для этого есть несколько ножей со следами старика Роквелла
Более умного ничего не смог придумать…
http://www.tverdomer.ru/about/museum/ Обратите внiмание на набор надфилей с разноцветными ручками. Видел в продаже, помоему на кнайфворкс, не уверен.
Udod 18-09-2008 23:34quote:
Выжать конечно можно, но это уже нарушение т.о., а оно как известно берется не с бухты барахты, а с учетом хим-состава стали и ничего кроме как ухудшения на выходе конечного продукта за собой повлечь не может
Тоже чисто Имхо. Есть отрасли ,где результат может быть вычислен теоретически с помощью математических вычислений. А есть такие, где все определяется опытным путем . При этом ,в нашем случае, 20 экспертов-кузнецов умеют закалить сталь до 56 ед. А у одного-двух получается 62 Почему получается объяснить никто не может ,но получается и все без потери других качеств. Так как вы думаете, что будет записано в технологии?GAU-8A 19-09-2008 09:20
Автором темы флуд не приветствуется и если он сочтет нужным, то мое сообщение… можно на помойку.
А теперь по кузнецам-экспертам (!). Вокруг да около можно ходить до второго пришествия… В контексте вашего первоначального утверждения…. будьте добры указать более конкретно, сколько и из чего можно выжать, без потери в тех или иных характеристиках? Желательно с указанием марки стали и твердости.
quote:
будьте добры указать более конкретно, сколько и из чего можно выжать, без потери в тех или иных характеристиках?
Так ,не знаю ,однако. Знаю только, что у разных мастеров из одной и той же стали выходят клинки разного качества. А из таких сталей как 65Г ,например, если калить их по заводским нормам ,вообще нож делать не стоит ,а из 40х13 у нас один специалист на заводе такое делал ,что сейчас порой из 90х18 такое не получается.GAU-8A 19-09-2008 15:45
Все, спасибо, понял, что вы имели в виду.
Udod 19-09-2008 23:55Хорошие способы. Но
1. Если удается определить твердость клинка по Бринелю ,имхо, клинок можно выкидывать (ну или перекаливать.)
2. Второй способ еще лучше. Убить на точиле клинок к чертям ,чтобы узнать какой он был твердости до того ,как перестать быть клинком?…
Да у нас уже все заводы по растащили
ну почти все
guns.allzip.org
Контроль структуры и свойств металла
Механические свойства характеризуют способность материала сопротивляться деформации и разрушению под действием приложенных нагрузок.
По характеру изменения во времени действующей нагрузки механические испытания могут быть статическими (на растяжение, сжатие, изгиб, кручение), динамическими (на ударный изгиб) и циклическими (на усталость).
По воздействию температуры на процесс их делят на испытания при комнатной температуре, низкотемпературные и высокотемпературные (на длительную прочность, ползучесть).
Статические испытания проводятся при воздействии на образец с определенной скоростью постоянно действующей нагрузки. Скорость деформации составляет от 10–4 до 10–1 с–1. Статические испытания на растяжение относятся к наиболее распространенным. Свойства, определяемые при этих испытаниях, приведены в многочисленных стандартах по техническим условиям на материалы. К статическим относятся испытания на растяжение, сжатие, изгиб, кручение.
Динамические испытания характеризуются приложением к образцу ударной нагрузки и значительной скоростью деформации. Длительность испытания не превышает сотен долей секунды. Скорость деформации составляет около 102 с–1. Динамические испытания чаще всего проводят по схеме ударного изгиба образцов с надрезом.
Циклические испытания характеризуются многократными изменениями нагрузки по величине и по направлению. Примером испытаний являются испытания на усталость, они длительны и по их результату определяют число циклов до разрушения при разных значениях напряжения. В конечном итоге находят предельные напряжения, который образец выдерживает без разрушения в течение определенного числа циклов нагружения.
Испытания на твердость.
Простейшим механическим свойством является твердость. Методы определения твердости в зависимости от скорости приложения нагрузки делятся на статические и динамические, а по способу ее приложения – на методы вдавливания и царапания. Методы определения твердости по Бринеллю, Роквеллу, Виккерсу относятся к статическим методам испытания.
Твердость – это способность материала сопротивляться вдавливанию в него более твердого тела (индентора) под действием внешних сил.
При испытании на твердость в поверхность материалов вдавливают пирамиду, конус или шарик (индентор), в связи с чем различают методы испытаний, соответственно, по Виккерсу, Роквеллу и Бринеллю. Кроме того, существуют менее распространенные методы испытания твердости: метод упругого отскока (по Шору), метод сравнительной твердости (Польди) и некоторые другие.
При испытании материалов на твердость не изготавливают стандартных специальных образцов, однако к размерам и поверхности образцов и изделий предъявляются определенные требования.
Твердость по Виккерсу (ГОСТ 2999-75) устанавливают путем вдавливания в металл индентора – алмазной пирамиды с углом при вершине 136° под действием постоянной нагрузки Р: 1; 2; 2,5; 3; 5; 10; 20; 30; 50 или 100 кгс и выдержки под нагрузкой в течение 10-15 с. Для определения твердости черных металлов и сплавов используют нагрузки от 5 до 100 кгс, медных сплавов – от 2,5 до 50 кгс, алюминиевых сплавов – от 1 до 100 кгс. После снятия нагрузки с помощью микроскопа прибора находят длину диагонали отпечатка, а твердость HVрассчитывают по формуле
HV = 1,854*P/d2
где Р – нагрузка, кгс; d- диагональ отпечатка, мм.
Имеется таблица зависимости твердости от величины нагрузки и длины диагонали. Поэтому на практике вычислений не производят, а пользуются готовой расчетной таблицей. Твердость по Виккерсу HVизмеряется в кгс/мм2, Н/мм2 или МПа. Значение твердости по Виккерсу может изменяться от HV2060 до HV5 при нагрузке 1 кгс.
По методу Бриннелля вдавливают в образец или изделие стальной закаленный шарик диаметром 10, 5 или 2,5 мм под действием нагрузок 3000, 1000, 750, 500, 250, 62,5 кгс и др. (ГОСТ 9012-59, рис. 1.). Полученный круглый отпечаток на образце измеряют под лупой и по таблицам находят величину твердости по Бринеллю, значение которой не превышает 450 НВ. Твердость по Бринеллю почти совпадает со значениями твердости по Виккерсу.
Твердость НВ – это также величина напряжений сопротивления вдавливанию:
HB=P/Fot=P/πDt=2P/πD(D-√(D2-d2))
где P- нагрузка, кгс;
Fot– площадь отпечатка, мм2;
t- глубина сегмента отпечатка;
D- диаметр шарика, мм;
d- диаметр отпечатка, мм.
Твердость по Бринеллю НВ (по умолчанию) имеет размерность кгс/мм2, например, твердость алюминиевого сплава равна 70 НВ. При нагрузке, определяемой в ньютонах, твердость по Бринеллю измеряется в МПа. Например, твердость отожженной стали равна 207 НВ при нагрузке 3000 кгс, диаметре шарика 10 мм, диаметре отпечатка 4,2 мм или, учитывая коэффициент перевода: 1 Н = 9,8 кгс,
НВ = 2 028 МПа.
Рис. 1. Схема определения твердости по Бринеллю
По методу Роквелла (ГОСТ 9013-59) вдавливают алмазный конус с углом при вершине 120° (шкалы А и С) или стальной шарик диаметром 1,5875 мм (шкала В).
При этом определяют твердость, соответственно, HRA, HRC и HRB. В настоящее время измерение твердости по методу Роквелла является наиболее распространенным методом, потому что при использовании твердомеров Роквелла не требуется измерять отпечаток, число твердости считывается со шкалы прибора сразу после снятия основной нагрузки.
Метод заключается во вдавливании в испытуемый образец индентора под действием двух последовательно прикладываемых нагрузок – предварительной Р0 и основной Р1 которая добавляется к предварительной, так что общая нагрузка Р = Р0 + Р1 После выдержки в течение нескольких секунд основную нагрузку снимают и измеряют остаточную глубину проникновения индентора, который при этом продолжает находиться под действием предварительной нагрузки. Перемещение основной стрелки индикатора на одно деление шкалы соответствует перемещению индентора на 0,002 мм, которое принимается за единицу твердости.
На рис. 2 представлена схема измерения твердости по методу Роквелла алмазным или твердосплавным конусом. При испытаниях измеряют глубину восстановленного отпечатка. Шкалы А и С между собой совпадают, поскольку испытания проводят одним и тем же индентором – алмазным конусом, но при разных нагрузках: 60 и 150 кгс соответственно. Твердость в этом случае определяется как
HRC= t/0,002=100-(H-h)/0,002
По шкале В (нагрузка 100 кгс, шарик)
HRB = 130-(H-h)/0,002
Рис. 2. Схема определения твердости по Роквеллу (индентор – конус)
На практике значения твердости по Роквеллу не рассчитываются по формулам, а считываются с соответствующей (черной или красной) шкалы прибора. Шкалы HRC и HRA используются для высокой твердости, HRB -для низкой. Число твердости по Роквеллу измеряют в условных единицах, оно является мерой глубины вдавливания индентора под определенной нагрузкой.
Испытание на растяжение материалов проводят в соответствии с ГОСТ 1497-84 «Методы испытаний на растяжение». Стандарт устанавливает методы статических испытаний на растяжение черных и цветных металлов для определения при температуре 20 °С пределов пропорциональности, упругости, текучести, временного сопротивления разрыву, относительного удлинения и относительного сужения, модуля упругости.
Для испытаний применяют плоские и цилиндрические образцы, вырезанные из детали или специально изготовленные. Размеры образцов регламентированы указанным стандартом, они подчиняются геометрическому подобию и могут быть короткими и длинными. Для цилиндрического образца берется соотношение начальной рабочей длины l0 и исходного диаметра d0 : l0= 5d0– короткий образец, l0= 10d0 – длинный образец. Для плоского образцаберется соотношение рабочей длины l0 и площади поперечного сечения F0:
l0= 5,65√F0 – короткий образец, l0= 11,3√F0 – длинный образец. Цилиндрические образцы изготавливаются диаметром 3 мм и более. Образцы состоят из рабочей части длиной l0 и головок, форма и размер которых соответствуют захватам машины (рис. 3).
Рис. 3. Цилиндрические и плоские образцы до (а) и после (б) испытания на растяжение
Растяжение образца проводят на специальных машинах, позволяющих фиксировать величину прилагаемой нагрузки и изменение длины образца при растяжении. Эти же машины дают возможность записывать изменение длины образца при увеличении нагрузки (рис. 4), т.е. первичную диаграмму испытания на растяжение в координатах: нагрузка Р, Н, кН; и абсолютное удлинение образца А, мм.
Рис. 4. Первичная диаграмма растяжения
Измеряя величину нагрузки в характерных точках диаграммы испытаний на растяжение (рис.4), определяют следующие параметры механических свойств материалов:
σ пц– предел пропорциональности, точка р;
σ 0,05 – предел упругости, точка е;
σ т – предел текучести физический, точка s;
σ 0,2– предел текучести условный;
σ в – временное сопротивление разрыву, или предел прочности, точка b.
Значения 0,05 и 0,2 в записи предела упругости и текучести соответствуют величине остаточной деформации ∆l в процентах от l0 при растяжении образца. Напряжения при испытании на растяжение вычисляют путем деления нагрузки Р, соответствующей характерной точке на диаграмме, на площадь первоначального поперечного сечения F0 рабочей части испытуемого образца:
σпц=Pпц / F0 ; σ0,05=P 0,05 / F0 ; σт=Pт / F0 , или σв=P max / F0 ;
Площадь поперечного сечение F0определяется по следующим формулам:
для цилиндрического образца
F0 = πd02/ 4
для плоского образца
F0 = a0*b0
где а0 – первоначальная толщина; b0 – первоначальная ширина образца.
В точке k устанавливают напряжение сопротивления разрушению материала.
Предел пропорциональности и предел упругости определяют с помощью тензометра (прибор для определения величины деформации). Предел текучести физический и условный рассчитывают, находя нагрузку по диаграмме растяжения. Если на диаграмме нет площадки текучести, то для вычисления условного предела текучести необходимо провести графические построения на диаграмме (рис. 1.5). Вначале находят величину остаточной деформации, равную 0,2 % от l0, далее отмечают отрезок на оси деформации, равный 0,2 % от l0, и проводят линию, параллельную пропорциональному участку диаграммы растяжения, до пересечения с кривой растяжения.
Рис. 5. Определение предела текучести
Нагрузка P0,2 соответствует точке их пересечения. Физический и условный предел текучести характеризуют способность материала к началу пластической деформации, т.е. сопротивление малой пластической деформации.
Предел прочности можно подсчитать, используя показания силоизмерителя, по максимальной нагрузке Рmax при разрыве либо найти Рmax (Рв) по первичной диаграмме растяжения. Характер деформации при растяжении вязких и хрупких материалов существенно различается.
Хрупкие материалы после достижения максимальной нагрузки быстро разрушаются без значительной пластической деформации, поэтому σв для
хрупких материалов является характеристикой сопротивления разрушению, а для пластичных – характеристикой сопротивления деформации.
Напряжение разрушения определяют как истинное. При этом нагрузку разрушения делят на конечную площадь поперечного сечения образца после разрушения FK:
Sк=Pк/Fк
Все рассчитанные таким образом величины являются характеристиками прочности материала.
Пластичность, т.е. способность деформироваться без разрушения, характеризуется изменениями размеров образца. При испытании на разрыв определяют следующие характеристики пластичности:
относительное удлинение
δ=(lk-l0)/ l0*100%
относительное сужение
Ψ=(F0к-F)/ F0*100%
где lк, Fк — соответственно, длина рабочей части и площадь поперечного сечения образца после разрыва.
Рассчитанные характеристики механических свойств после испытания на растяжение заносятся в протокол.
Испытания на ударный изгиб.
Ударная вязкость характеризует удельную работу, затрачиваемую на разрушение при ударе образца с надрезом. Ударная вязкость испытывается на маятниковом копре с постоянным запасом работы маятника по ГОСТ 9454-78 «Металлы. Метод испытания на ударный изгиб при пониженной, комнатной и повышенной температурах». Стандарт распространяется на черные и цветные металлы и сплавы и устанавливает метод испытания при температурах от -100 до +1000 °С. Метод основан на разрушении ударом маятникового копра образца с концентратором напряжений. В результате испытания определяют полную работу, затраченную при ударе К, или ударную вязкость КС.
Используют образцы прямоугольной формы с концентратором типа U, V, Т (усталостная трещина). Наиболее распространенными образцами являются образцы размерами 55x10x10 мм с U-концентратом 2×2 мм (рис. 6).
Рис. 6. Стандартный образец с U-образным надрезом для испытаний на ударный изгиб
На разрушение ударом образца затрачивается только часть энергии маятника, в связи с чем маятник после разрушения образца продолжает двигаться, отклоняясь на определенный угол. Чем больше величина работы, затрачиваемой на разрушение образца, тем на меньший угол он отклоняется от вертикали после разрушения. По величине этого угла и определяют работу удара К или работу, затраченную на разрушение образца. Работу разрушения К относят к площади поперечного сечения образца Soв месте излома и тем самым находят КС – ударную вязкость:
KC = K/S0,
где Kизмеряется в Дж (кгс*м), S0— в м2 (см2).
В зависимости от вида концентратора ударная вязкость обозначается
KCU, KCV, КСТ и имеет размерность МДж/м2 (МДж/см2) или кгс*м/см2.
markmet.ru
Металлы Твердость — Определение — Метод
При определении предела прочности по измерениям твердости коэффициент пропорциональности зависит от степени равномерной деформации, т.е. от упрочнения материала, и для конструкционных сталей равен 0,33. Чем больше равномерная деформация, тем этот коэффициент больше. На сходстве кривых твердости и растяжения основаны методы определения прочностных свойств металла. [c.205]В зависимости от качества и состояния металла (закаленный, отожженный и т. п.) применяются различные способы определения твердости. Рассмотрим наиболее распространенные методы таких испытаний. [c.6]
Термоэлектрический метод основан на принципе термоэлектрического пирометра и применяется для установления степени обезуглероживания изделий в процессе его нагревов. Этот дефект, как правило, трудно устанавливается прибегают либо к микроскопическому исследованию, либо определяют его косвенно по понижению твердости. Магнитный и термоэлектрический методы определения обезуглероживания изделий позволяют относительно легко и быстро выполнять такие испытания, а следовательно, они могут быть применены для массового контроля и сортировки металла. [c.312]
Местное воздействие нагрузки на небольшую часть поверхности образца и малый объем испытуемого металла являются несомненным преимуществом этих методов испытания на твердость, при которых изделие не разрушается и поступает в эксплуатацию. При необходимости можно осуществлять 100-про центный контроль деталей. Приборы для определения твердости обычно портативны, просты в обслуживании и высокопроизводительны. Эти преимущества привели к широкому применению испытаний на твердость, которые являются самыми распространенными контрольными испытаниями. Особенно большой интерес при проведении тонких исследований представляет метод замера микротвердости. [c.364]
Твердость — свойство металлов сопротивляться проникновению в них других, более твердых тел. Твердость определяет многие эксплуатационные свойства металла сопротивляемость истиранию, режущие свойства инструмента для обработки металлов, эрозионную стойкость и т. д. По твердости иногда можно косвенным путем определить предел прочности и текучести металла, не вырезая образцов. Большинство методов определения твердости основано на принципе вдавливания в испытуемый металл более твердого шарика, конуса или пирамиды. [c.73]
Числа твердости металлов и сплавов при различных методах определения (ГОСТ 8.064—79) [c.117]
Определение твердости вдавливанием стального шарика (метод Бринеля). Этот метод испытания заключается в том, что в испытуемый металл вдавливается с определенной силой стальной закаленный шарик и затем измеряется площадь получившегося сферического отпечатка. [c.32]
Метод Бринеля применим для определения твердости незакаленной стали и цветных металлов. Твердость закаленных сталей определять вдавливанием стального шарика нельзя, так как при этом сам шарик может деформироваться. [c.14]
Методы определения твердости металлов. Твердостью называют свойство металла сопротивляться внедрению [c.48]
Универсальный прибор УПТ-1. Общий вид этого прибора, изображенный на фиг. 121, позволяет производить определение твердости металлов по трем независимым стандартным методам 1) “вдавливанием стального шарика диаметром 2,5 мм при нагрузках 187,5 62,5 и 15,6 кГ, по ОСТ 10241-40 2) вдавливанием алмазной пирамиды при нагрузках 50, 30, 10 и 5 кГ, по ГОСТ 2995-45 и 3) вдавливанием алмазного конуса и стального шарика диаметром 1,588 мм с предварительной нагрузкой 10 кГ по ОСТ 10242-40. [c.167]
Твердость гальванопокрытий испытывают методами царапания и затухающих колебаний маятника. Первый метод заключается в нанесении царапин на покрытие при помощи алмазной или сапфировой иглы под определенной нагрузкой с последующим измерением ширины нанесенных царапин. Второй метод заключается в измерении продолжительности затуханий маятника, опирающегося острием на поверхность покрытия. Полученные результаты сопоставляют с контрольными определениями металла, твердость которого известна. [c.613]
Методы определения твердости металлов. Твердостью называют свойство металла сопротивляться внедрению в него другого, более твердого тела. Испытания на твердость получили широкое применение в производственных условиях, представляя собой наиболее простой и быстрый метод испытания механических свойств. Так как при измерении твердости испытываются поверхностные слои металла, то для получения правильного результата поверхность металла не должна иметь таких дефектов, как окалина, забоины, крупные царапины и др. не должно также быть наклепа поверхности. Существуют различные способы измерения твердости металлов. Рассмотрим некоторые из них, наиболее широко применяемые в промышленности. [c.42]
Для определения твердости измеряют диаметр лунки с1 и находят по ней твердость в специальных таблицах. Метод Бринеля не рекомендуется применять для металлов твердостью более НВ 450, так как шарик может деформироваться, что исказит результаты испытания. [c.55]
Ниже приводятся описания экспериментальных методов изучения пластических деформаций по изменению микроструктуры металлов, а также определения степени деформации и интенсив ности напряженного состояния испытанием твердости. [c.431]
Твердость можно измерять на деталях небольшой толщины, а также в очень тонких слоях, не превышающих (для некоторых способов измерения твердости) десятых долей миллиметра, или в микрообъемах металла в последнем случае измерения проводят способом микротвердости. Поэтому многие способы измерения твердости пригодны для оценки различных по структуре 1 свойствам слоев металла, например поверхностного слоя цементованной, азотированной или закаленной стали, имеющей разную твердость по сечению детали. Методом определения микротвердости можно также измерять твердость отдельных составляющих в сплавах. [c.169]
Определение твердости металлов по Бринелю основано на методе вдавливания в металл стального шарика. Для испытания на твердость поверхность детали, подвергающейся испытанию, предварительно гладко зачищают напильником или наждачным кругом. После этого в нее вдавливается прессом (рис. 3) стальной закаленный шарик под действием заданной нагрузки. Через 10—30 секунд нагрузка снимается. [c.8]
В инструментальной практике применяются различные методы определения твердости. Характеристики твердости, определяемые при различных методах испытаний, получаются различными как по величине, так и по физическому смыслу. Поэтому показатель твердости металла (число твердости) должен во всех случаях сопровождаться указанием метода, которым он определен. [c.193]
Существующие методы определения твердости металлов можно разделить на две группы обычное определение твердости и определение микротвердости (например, твердости отдельных структурных составляющих). Величины характеристик твердости и микротвердости могут существенно отличаться вследствие неравномерного напряженного и деформированного состояния и неоднородности состава и структуры по объему образца или изделия. [c.16]
Испытание на твердость. Понятие твердости (см.) как физич. величины до сих пор не установлено. Твердость в техническом языке обозначает конгломерат свойств, более или менее связанных между собой. Сюда относятся сопротивление истиранию, сопротивление резанию, способность резать другие металлы, сопротивление пластической деформации, модуль упругости, предел текучести, прочность и др. Поэтому определение твердости заменяется условными технологич. методами, к-рых применяется несколько. [c.287]
При отсутствии сертификата марку металла устанавливают лабораторными анализами и испытанием отобранных образцов. Марку незакаленной стали можно примерно определить по ее твердости. Между твердостью стали и пределом ее прочности существует соотношение Ов = 0,36 НВ. В условиях монтажной площадки определение твердости стали производится относительным методом с использованием специального прибора (рис. 1). Установив прибор на испытываемый обр,зец, ударом молотка по бойку получают отпечатки шарика на эталонном и испытываемом образцах. По соотношению диаметров полученных отпечатков сравнивается твердость испытываемого материала по отношению к эталонному образцу. При незначительной разнице диаметров отпечатков считается, что твердость испытываемого образца равна твердости эталона. Если разность более 10%, то испытание повторяют с другим эталоном. [c.6]
При определении механических свойств металлов по твердости наиболее целесообразно использовать наконечник в форме шара по методу Бринелля, так как в этом случае по мере вдавливания увеличивается 3/ гол вдавливания, который характеризуется отношением d/D, а следовательно и степень деформации в лунке. [c.318]
Целью настоящей работы является ознакомление с приборами и методами измерения твердости металлов и сравнение результатов, полученных при определении твердости различными методами. [c.115]
Для определения и изучения механических свойств материалов в малых объемах перспективными и порой единственно возможными являются методы исследования твердости, микротвердости, испытания малых образцов на растяжение. Условно эти испытания могут быть отнесены к микромеханическим методам исследования свойств материалов [121, 128, 166, 205]. Развитие методов изучения прочности тугоплавких металлов при температурах, в 2—3 раза превышающих освоенный в испытательной технике уровень (до 1300 К), явилось весьма сложной задачей, решение которой потребовало преодоления больших конструкторских и методических трудностей. Было осуществлено создание комплекса новых специальных высокотемпературных установок повышенной точности, исключающих влияние на испытываемые образцы вредных побочных явлений испарения и окисления материалов, трения в направляющих и в уплотнениях микромашин, нагрева силоизмерительных устройств, вибрации частей установок и здания, а также многих других факторов. [c.4]
Определение понятия твердость . Суш,ествует большая группа методов оценки мате иала, основанных на том или ином контактном воздействии на поверхность материала. Сопротивляемость материала внедрению в него характеризуется некоторым числом, которое имеет в разных случаях разную природу. Все эти методы объединяются обш,им названием методы определения твердости. При этом, следуя Н. А. Шапошникову, будем считать, что под твердостью подразумеваются разнообразные характеристики сопротивляемости металла местной, сосредоточенной в небольшом объеме, деформации на его поверхности . [c.311]
Начальник Златоустовского металлургического завода, занимавшегося изготовлением холодного оружия для армии, П. П. Аносов (1797—1851 гг.) пришел к мысли, что наиболее совершенной сталью является булат, поскольку он сочетает в себе высокую твердость, высокую упругость, хорошую вязкость и исключительные режущие свойства. Аносов разработал микроскопический метод исследования металлов и внедрил его в лабораторную практику. Он установил, что между структурой стали и ее свойствами суп е-ствует определенная зависимость, что для цементации стали не обязательно соприкосновение последней с углеродом. Аносов изучил влияние различных элементов на свойства стали и процесс отжига стали и доказал, что он благотворно влияет на ее свойства. [c.185]
Требования к приборам для определения твердости металлов вдавливанием алмазной пирамиды (по методу Виккерса) и правила их поверки изложены в ГОСТ 7038—63, ГОСТ 2999—59, ГОСТ 9377—63 и в инструкции 235—56 По поверке приборов для измерения твердости металлов по методам Бринелля, Роквелла и Виккерса . [c.144]
Необходимо отметить, что числа твердости, полученные при испытании металлов по Бринелю и Роквеллу, не соответствуют друг другу.. Например, если твердость одного металла указана по Бринелю Нб = = 581, а другого — по Роквеллу R = 58, то по ним еще нельзя заключить, какой металл тверже. Для сравнения твердости металлов определенной различными методами, пользуются таблицами сравнения чисел твердости. Ниже приведена таблица сравнения чисел твердости, полученных при испытании металлов по методу Бринеля it Роквелла (табл. 2). [c.15]
Твердость — это способность металла сопротивляться внедрению в него другого более твердого тела. Твердость определяют специальными приборами, которые по способам приложения в них нагрузки делятся на статические и динамические. Наиболее распространенными видами статического определения твердости металлов и их сплавов являются методы Бринелля и Роквелла, а динамического— методы Шора, Польди и др. [c.75]
Определение твердости по Роквеллу (ГОСТ 9013—59). В этом методе твердость в отличие от метода Бринеля определяется не но диаметру, а по глубине отпечатка. Наконечником служит алмазный конус с углом при вершине 120 или стальной закаленный шарик диаметром 1,588 мм. Алмазный конус применяется для испытания твердых металлов, а шарик — для мягких металлов. [c.55]
Метод царапания является лишь сравнительным, и для сопоставления оолученных результатов испытания необходимо контрольное определение такого металла, твердость которого известна. [c.346]
Достаточво воспроизводямые результаты при испытании этим методом удаепа получать при покрытиях толщиной не меньще 20 мк. Данные испытаний рекомендуется сопоставлять с результатами контрольных определений металла, твердость которого известна. [c.347]
В комплект сварочной лаборатории обычно входят следующее оборудование, приборы и материалы разрывная машина для испытания образцов на разрыв и загиб, пресс для определения твердости металла, копер для определения ударной вязкости металла, слесарный специальный верстак с тисками, аппаратура для физических методов контроля, дозиметрические приборы, материалы для физических методов контроля, микроскоп, весы, сварочные автоматы п по.пуавтоматы, источники питапия сварочной дуги и т. д. [c.527]
Наряду с обычным (кратковременным) испытанием твердости практикуется определение твердости металла в периоде стабилизировавшейся пластической деформации ( длительная твердость ). Этот метод, разработанный В. П. Шишокиным (1937 г.) и А. А. Бочваром (1947 г.), используют преимущественно при исследовании цветных металлов и сплавов. [c.124]
Важной характеристикой для выбора режущих инструментов (напильников, резцов, метчиков, сверл и др.) является твердость, определяющая прочность и износоустойчивость металлов и сплавов. Имеется несколько методов определения твердости метод Бринелля (ГОСТ 9012—59 )—вдавливание закаленного стального шарика в поверхность испытываемого металла метод Роквелла (ГОСТ 9013—59) — вдавливание алмазного конуса или стального шарика в поверхность испытываемого металла метод Виккерса (ГОСТ 2999—75) — вдавливание алмазной пирамиды в поверхность испытываемого металла. [c.16]
Для количестаенного определения твердости металлов и сплавов применяют как методы механического нагружения образца, так и косвенные методы котроля (схема 2.3.1). [c.163]
Определение твердости по Бринеллю. Метод основан на том, что в плоскую поверхность металла под постоянной нагрузкой Р (Н) вдавливается 1вердьп 1 стальной шарик (рис. 43, а). После снятия нагрузки в испытуемом металле образуется отиечагок (лунка). [c.66]
Однако метод Бринеля имеет ряд недостатков. По этому методу нельзя испытывать образцы, если их твердость близка к твердости шарика, так как последний сам получает значительные деформации, что искажает результаты испытания. При использовании обычных стальных шариков это является причиной ограничения пробы по Бринелю пределами наибольшей твердости Нв 400 -н 500 кПмм . Вследствие большой глубины отпечатка нельзя определить твердость специально обработанного поверхностного слоя, так как шарик проникает через этот слой в более мягкую внутреннюю часть. Измерение диаметра отпечатка занимает сравнительно много времени и бывает неточным вследствие вспучивания выдавливаемого шариком металла около краев отпечатка. Поэтому появилась необходимость в других способах определения твердости. [c.51]
Твердость оценивается сопротивлением, которое одно тело оказывает проникновению в него другого, более твердого тела. Эта характеристика отражает в себе целый комплекс механических свойств. Испытания на твердость материалов с покрытиями могут проводиться для контроля качества нанесенного слоя, выявления изменений в поверхностных участках основного металла, для оценки структурной неоднородности по сечению покрытия, с целью исследования закономерностей изнашивания покрытий, определения прочности соединения покрытия с основным металлом и т. д. Данные о твердости широко используются благодаря ряду достоинств этого метода возможность 100%-ного контроля деталей после нанесения покрытий испытания не являются разрушающими, замеры можно производить непосредственно на детали серийные приборы не сложны по устройству, производительны и удобны в эксплуатации. [c.25]
Службой металлов и сварки Донбассэнерго проведены работы по устранению взаимозависимости механических характеристик металла со значениями твердости, определенными при вдавливании индентора. Существуют статические и динамические методы измерения твердости. [c.205]
Правомерность такого описания механизма ударноабразивного изнашивания подтверждается линейной зависимостью износостойкости стали от сопротивления срезу (отрыву) в хрупкой и вязкой областях разрушения. При снижении энергии удара сдвиговые процессы в зоне контакта, обусловливающие образование частиц износа, постепенно затухают. При определенном внешнем силовом воздействии на поверхность контакта внедрение твердой частицы аналогично действию индентора при соответствующих методах определения твердости. В этом случае абразивное действие твердой частицы ограничено поверхностью образуемой ею лунки, а сдвиговые процессы металла перемычек сведены к минимуму. [c.33]
Определяя твердость металла не в образце, а в изделии, удается установить косвенным путем предел прочности, не изготавливая образца и не доводя материал до разрушения в изделии. Соответствующим методам (неразрушаюш им) определения механических характеристик в последнее время уделяют большое внимание. [c.311]
mash-xxl.info