Как производится сталь: Как производится сталь | Мир ковки
alexxlab | 13.02.1990 | 0 | Разное
Производство стали: способы, технология и сырье
Сталь – это прочный материал и основной конструкционный материал для машиностроения. Он представляет сплав железа с углеродом, содержание которого в структуре составляет 0,01–2,14%. В состав также входят в незначительных количествах кремний, марганец и сера. Этот материал обладает исключительными механическими свойствами: твердостью и ковкостью, благодаря им он считается основным конструкционным материалом в машиностроении. Трудно представить, что могло бы заменить материал. Но активное развитие производство стали и других металлов. Из стали изготавливаются самые разнообразные изделия – от канцелярских скрепок до станин многотонных прессов и обшивки корпусов морских судов.
Содержание
- Процесс производства
- Особенности процесса
- Особенности второго этапа
- Раскисление
- Мартеновский способ
- Конвертерный метод
- Особенности процесса
- Кислородно-конвертерный способ получения стали
- Электросталеплавильный способ
- Особенности электроиндукционных печей
- Виды получаемых сталей по химическому составу
Процесс производства
Производится сталь плавкой. Исходным сырьем служат чугун, лом самой стали или чугуна, окатыши, флюсы и ферросплавы.
Сам чугун по природе – недостаточно твердый и хрупкий материал, поэтому имеет ограниченное применение.
Однако, он незаменим в качестве сырья для получения стали. Суть плавки состоит, в случае применения передельного чугуна, в снижении процентного содержания углерода в нем до требуемого уровня.
Выводятся не предусмотренные в конечной рецептуре примеси. Традиционный состав шихты представляет 55% чугуна и 45% стального лома (скрапа). Существует также рудный процесс, когда к компонентам добавляется рудный материал или скрап-процесс для переработки отходов машиностроительного производства.
Чтобы в процессе плавки примеси и углерод легче выводился из состава компонентов, они переводятся в газы и шлак. В первую очередь при взаимодействии чугуна с кислородом железо окисляется, образуя закись железа FeO.
Одновременно окисляются C, Si, Mn и P, при этом происходит отдача кислорода оксидом железа химически активным примесям. К массе шихты добавляют флюс для лучшего растворения металла: известняк или известь, боксит. В качестве топлива используют каменноугольную пыль, жидкий мазут, природный или коксовый газ.
Особенности процесса
Процесс производства стали происходит последовательно в три этапа.
Первый этап – расплавление породы. На этапе его проведения формируется расплав в ванне и окисляется металл, отдавая одновременно кислород кремнию, фосфору и марганцу.
Одна и главных задач этого этапа – удаление фосфора. Для ее осуществления требуется сравнительно невысокая температура и присутствие в достаточном количестве FeO. При взаимодействии ингредиентов фосфорный ангидрид образует с оксидом железа нестойкое соединение (FeO)3 + P2O5.
Присутствие в шлаке более стойкого основания СаО вызывает замещение FeO. В результате оно связывает фосфорный ангидрит в другое соединение (CaO)4 х P2O5 + 4 Fe, чего и требовалось добиться.
Чистый Fe высвободился в расплаве, а фосфор образовал шлак, который удаляется с зеркала металла и утилизируется за ненадобностью. Поскольку фосфорный ангидрид преобразует состав шлака, процесс должен идти непрерывно.
Поэтому FeO должен непрерывно пополняться за счет загрузки новых партий железной руды и окалины, наводящих в расплаве железистый шлак.
Особенности второго этапа
Технология производства стали на втором этапе называется кипением стали. Основное назначение заключается в процентном снижении содержания углерода за счет окисления. FeO + C = CO + Fe.
Реакция окисления происходит более интенсивно при кипении и сопровождается поглощением тепла. Поэтому необходимо создавать постоянный приток тепла в ванну, а также для выравнивания температуры в расплаве.
При такой реакции окисления интенсивно выделяется газ оксида углерода CO, что вызывает бурное кипение в жидком агрегатном состоянии, по этой причине процесс называют кипением. Чтобы излишки углерода интенсивнее преобразовывались в окись, производство качественной стали предусматривает вдувание чистого кислорода и добавление в расплавленную структуру окалины. Поэтому таким важным является качество сырья для производства стали. Все исходные материалы проходят щепетильную проверку.
Немаловажным на этом этапе является вывод серы, благодаря чему повышается качество конечной стали. Используемая в компонентах сера, присутствует не в прямом виде, а в форме сульфида железа FeS.
При высоких температурах компонент также взаимодействует с оксидом СаО, образуя сульфид кальция CaS, который растворяется в шлаке, не соединяясь с железом. Это позволяет беспрепятственно выводить сульфид за пределы ванны.
Раскисление
Третий этап – раскисление металла. После добавления кислорода (на предыдущем этапе) требуется снизить его содержание в чистой стали. Использованием О2 удалось добиться окисления примесей, но его остаточное присутствие в конечном продукте снижает качественные характеристики металла. Требуется удалить или преобразовать окислы FeO, связав кислород с другими металлами.
Для этого существуют два метода раскисления:
- диффузионное;
- осаждающее.
При диффузионном методе в расплавленный состав вводят добавки: алюминий, ферромарганец и ферросилиций. Они восстанавливают оксид железа и переводит в шлак. В шлаке оксид распадается и высвобождает чистое железо, которое поступает в расплав. Второй высвободившийся элемент – кислород улетучивается в окружающую среду.
Осаждающий метод предусматривает введение добавок, имеющих большее сродство с кислородом, чем Fe. Происходит замещение этими веществами железа в окисле. Они, как менее плотные, всплывают и выводятся вместе со шлаком.
Процесс раскисления продолжается при затвердевании слитка, в кристаллической структуре которого оксид железа и углерод взаимодействуют. В результате чего вместе с пузырьками азота, водорода он выводится.
Чем больше при раскислении выводится включений различных металлов, тем выше ковкость получаемой стали. Для проверки раскаленный кусок металла подвергают ковке, на нем не должны образовываться трещины. Такая проверка пробы говорит о правильном проведении процесса раскисления.
В зависимости от степени раскисления специалисты могут получить:
- спокойную сталь полного раскисления;
- кипящую раскисленную не полностью сталь, когда процесс выведения пузырьков угарного газа СО продолжается в ковше и изложнице.
Для получения легированных сталей с добавками некоторых металлов в расплавленный металл добавляются ферросплавы или чистые металлы. Если они не окисляются (Ni, Co, Mo), то такие добавки могут вводиться на любом этапе плавки. Более чувствительные к окислению металлы Si, Mn, Cr, Ti добавляют в ковш или, что обычно и происходит, в форму для отливки металла.
Существуют основные способы получения стали в сталеплавлении.
Мартеновский способ
Этот способ применяется для производства сталей высокого качества, применяемых в особо ответственных деталях машинах и точных механизмах.
В свое время он заменил трудоемкие и малопроизводительные тигельную и пулдинговую плавки, применявшиеся ранее.
Емкость загрузки одной отражательной печи, используемой при этом методе, достигает 500 тонн. Особенностью мартеновского способа является возможность переплавки не только передельного чугуна, но и металлургических отходов, металлического лома.
Температура нагрева жидкой стали достигает 2 тыс. градусов. Этот результат достигается специальной конструкцией мартеновской печи:
- применением дополнительного тепла регенераторов, получаемого сжиганием коксовального или доменного газа в струе горячего воздуха;
- отражения от свода закачиваемого газа в результате сгорание топлива в нем происходит над ванной с металлом, что способствует быстрому нагреву содержимого;
- применением реверсирования нагревающего потока.
Мартеновская печь состоит из следующих элементов:
- рабочего пространства с огнеупорной футеровкой стенок и завалочными окнами;
- подины (основания) из магнезитового кирпича;
- свода печи;
- головки печи;
- шлаковика для выведения пыли;
- регенератора с перекидными клапанами.
Процесс плавки занимает от 4 до 12 часов. С целью ускорения процесса плавки объем закачиваемого кислорода превышает потребности, что повышает производительность плавки на 20–30%.
Конвертерный метод
В конверторах выплавляют сорта стали для производства автомобильного листа, инструментальной стали сварных конструкций и других стальных заготовок. По качеству они уступают мартеновскими применяются для изготовления менее ответственных изделий.
В них содержится больше примесей, чем при мартеновском изготовлении. Благодаря высокому объему загрузки одной печи до 900 тонн, способ считается самым производительным, поэтому получил широкое распространение.
Производство стали и другого вида металла этим методом основано на продувке жидкого чугуна воздухом или кислородом под давлением 0,3–0,35 МПа, при этом металл разогревается до 1600 градусов. Плавка скоротечна и длится до 20 минут. За это время происходит окисление углерода, кремния и марганца, содержащихся в сырье, которые извлекаются из ванны с расплавом шлака.
Конвертер представляет сосуд ретортообразной (грушевидной) формы, состоящий из стальных листов с футеровкой изнутри. Для заливки чугуна и выпуска готовой стали используется одно отверстие, в него также загружается чугун и скрап.
Особенности процесса
Вместе с ними загружаются шлакообразующие вещества: известь и бокситы. Корпус охвачен опорным кольцом, прикрепленным к поворотным цапфам. С их помощью сосуд наклоняется и через это отверстие – летку выливается готовая сталь. Нижняя продувка осуществляется через сквозные отверстия (фурмы), сделанные в днище печи.
Исторически повелось, что используемый везде способ называется томасовским, бессемеровским. В прошлом веке преобладающим стал мартеновский процесс. Нагрев регенератора осуществляется продувкой печных газов, после чего он нагревается холодный воздух, поступающий на расплав.
В современных конструкциях чаще применяют верхний способ, при котором продувка на огромной скорости осуществляется через опускаемые к поверхности металла сопла. В России преимущественно используется именно верхняя продувка печей.
Находясь под струей воздуха, чугун интенсивно окисляется в зоне контакта. Поскольку его концентрация значительно больше других примесей, преимущественно образуется оксид железа. Но он растворяется в шлаке. Поэтому металл обогащается выделяемым кислородом.
Окисляются C, Cr и Mn, снижая процентное содержание в структуре металла. Окисление сопровождается выделением тепла. Благодаря присутствию шлаков СаО и FeO до разогрева происходит выведение фосфора в самом начале продувки.
Шлак с ним сливается и наводится новый. Производство стали сопровождается экспресс-анализами и контролем текущих изменений приборами контроля, вмонтированных в печь. Содержание фосфора в чугуне не должно превышать 0,075%.
Кислородно-конвертерный способ получения стали
Производство стали сегодня осуществляется в основном этим способом. На долю кислородно-конверторного производства совсем недавно приходилось до 60% мирового производства стали.
Однако, этот процент снижается в связи с появлением электродуговых печей (ЭДП). Продувка печей осуществляется чистым кислородом (99,5%) под высоким давлением.
Продукт кислородно-конвертерной печи представляет сталь с заданными химическими свойствами. Она поступает в машину непрерывного литья заготовок (МНЛЗ), где материал застывает в форме блюма или плиты. Для получения определенных жестких параметров металл подвергается вторичной переработке.
Электросталеплавильный способ
Производство стали электрической плавкой обладает рядом неоспоримых преимуществ. Этот способ считается основным при выплавке высококачественных легированных сталей.
Достигаемая при этом высокая температура позволяет выплавлять стали, содержащие тугоплавкие металлы:
- молибден;
- вольфрам;
- ванадий.
Высокое качество достигается практическим отсутствием в сталях фосфора, серы и кислорода. Этот способ также применяется для производства широкой номенклатуры строительных сталей.
Выделение тепла не связано с потреблением окислителя, а происходит в результате преобразования электрической энергии в тепловую. Она выделяется при прохождении электрической дуги или наведения вихревых токов. В зависимости от принципа работы печи подразделяются на электродуговые и индукционные.
Электродуговая печь способна принять одновременно от 3,5 до 270 тонн сырья:
- жидкой стали из конвертеров;
- скрапа;
- железной руды.
Она имеет несколько электродов из графитосодержащего материала, к которым подводится электрическое напряжение. Время плавки составляет до 1,5 часа, при этом температура дуги достигает 6 тыс. градусов.
Особенности электроиндукционных печей
В электроиндукционных печах сталь выплавляют в небольших по объему (4,5–60 тонн) емкостях, именуемых огнеупорными тиглями. Вокруг тигля располагается индуктор, состоящий из большого количества витков провода.
При прохождении переменного тока внутри индуцируются вихревые токи большой силы, вызывающее плавление содержимого тигля. Электромагнитные силы одновременно перемешивают расплав стали. Продолжительность плавки в таких печах не превышает 45 мин.
Электросталеплавильный способ производит мало дыма, пыли и меньше излучает световой энергии. Однако, высокая стоимость электрооборудования при малой вместительности ограничивает применение этого способа.
Схема электросталеплавильной печи
Помимо рассмотренных вариантов, существуют не только основные способы производства стали. В современном сталеплавлении используется плавка в вакуумных индукционных печах и обогащение процентного содержания железа в окатышах плазменно-дуговым переплавом.
Виды получаемых сталей по химическому составу
Производимая этими методами сталь делится, в зависимости от химического состава, на две большие группы:
- углеродистую;
- легированную.
Процентное содержание элементов в углеродистой стали:
Наименование | Fe | С | Si | Mn | S | P |
Содержание в процентах | до 99,0 | 0,05–2,0 | 0,15–0,35 | 0,3–0,8 | до 0,06 | до 0,07 |
В углеродистых сталях прочность недостаточно сочетается с пластичностью. Недостаток устраняется введением добавок других металлов, такая сталь называется легированной.
Согласно ГОСТ 5200 выделяют три группы легированных сталей с допустимым содержанием примесей:
- низколегированная не более 2,5%;
- среднелегированная в диапазоне 2,5–10%;
- высоколегированная свыше 10%.
С каждым годом способы плавки усовершенствуются благодаря вводу в строй нового высокотехнологичного оборудования. Это позволяет получать в сталелитейной промышленности высококачественные стали с оптимальным содержанием добавок и металлов.
Видео по теме: Производство чугуна и стали
Основные способы производства стали
Основные способы производства стали
Сталь представляет собой сплав железа с углеродом, причем углерода содержится от сотых долей до двух целых четырнадцати сотых процента. В состав стали могут входить также в определенном процентном соотношении и другие элементы.
По своим механическим свойствам и химическому составу сталь значительно отличается от чугуна. Она обладает высокой вязкостью, пластичностью, легко поддается механической и термической обработкам.
Производство стали осуществляется из передельного чугуна, стального лома, металлизированных окатышей, в специальных печах. Процесс получения стали основан на окислении в чугуне избытка углерода и других примесей с помощью твердых окислителей или газообразного кислорода.
Рекламные предложения на основе ваших интересов:
Дополнительные материалы по теме:
В настоящее время применяют главным образом конверторный, мартеновский и электросталеплавильный процессы выплавки стали.
Процесс получения стали в бессемеровском конверторе заключается и заполнении конвертора жидким чугуном и продувке его воздухом через днище. Основное преимущество итого способа и дальнейших его аналогов состоит в высокой производительности и отсутствии потребности в дополнительном топливе.
Современный кислородно-конверторный способ имеет примерно ту же технологию, что и бессемеровский способ. Отличием является конструкция конвертора с глухим дном (рис. 20) и применение для продувки технически чистого кислорода.
Кислород подают в конвертор через вертикальную трубчатую водоохлаждаемую фурму, не доходящую до металлической ванны. Из-за этого кислород не вдувается в толщу металла, как в старых конверторах, а подается на поверхность металла. При этом развивается высокая температура, что дает возможность перерабатывать чугун практически любого химического состава, а также добавлять в чугун скрап (железный лом).
Началом плавки считается загрузка в конвертор железного лома. После этого заливают жидкий чугун, опускают фурму, подают в нее технический кислород и загружают шлакообразующие материалы. Весь процесс выжигания примесей и избыточного углерода, включая слив шлака, занимает 50—60 мин, а продувка кислородом продолжается 18—26 мин.
Выплавка стали в кислородном конверторе отличается достаточно высокой точностью получения заданного содержания углерода при низком содержании вредных добавок фосфора и серы.
Недостатком кислородно-конверторного способа получения стали является большое пылеобразование, что требует применения дорогих пылеочистительных установок.
Мартеновский способ выплавки стали предложен в 1865 г. французским инженером П. Мартеном, который использовал для этой цели пламенную печь с регенерацией тепла отходящих газов для подогрева, топлива -и воздуха.
По этому принципу строятся и работают современные сталеплавильные мартеновские печи. Они отапливаются обычно смесью природного газа и мазута, имеют два-четыре регенератора.
Рабочее пространство печи ограничено снизу подом, сверху сводом, а с боков — стенками. Внутренняя полость печи имеет головки, сообщающиеся каналами с регенераторами.
В передней стенке мартеновской печи расположены рабочие окна 9, ЧеРез которые загружают материал для плавки и ведут за нею контроль. Под печи наклонен в сторону задней стенки, где расположена летка для выпуска стали.
Рис. 1. Кислородный конвертор на 130 т: 1 — станина; 2 — опорный подшипник; з — корпус конвертора; 4 — механизм наклона; г — выпускное отверстие для стали; в — водоохлаждаемая форма, 7 — днище конвертора
Рис. 2. Схемы мартеновской печи (а) и регенератора (б)
В печь загружают жидкий или в виде чушек чугун и стальной лом в разных соотношениях в зависимости от разновидности мартеновского процесса.
Серьезным недостатком мартеновского процесса получения стали является его продолжительность (7—10 ч) и значительный расход топлива. С целью совершенствования и ускорения мартеновского процесса применяют кислород для обогащения воздушного дутья или непосредственного введения его в ванну с металлом через свод печи. На некоторых заводах комбинируют способы применения кислорода и даже разрабатывают для этого двухванные печи.
Получение стали в электрических печах основано на плавлении шпхты при использовании электрической энергии. Отсутствие окислительного пламени и доступа воздуха в электрических печах позволяют лучше управлять процессом плавки и получать сталь точно заданного состава.
В нашей стране этот способ применяют для выплавки высококачественных углеродистых и легированных сталей, сплавов на основе никеля и кобальта.
По принципу преобразования электрической энергии в тепловую электрические печи делятся на дуговые и индукционные. Для наклона и слива металла и шлака печь оборудована роликами с электроприводом.
В дуговых электрических печах плавят отходы сталеплавильного прокатного производства, а также привозной стальной лом. В зависимости от состава сырья и материала, а также футеровки печей процесс плавки может носить основной или кислый характер.
Выплавка стали в индукционных печах применяется реже, чем в дуговых. Такая печь состоит из индуктора в виде катушки, окружающей огнеупорный тигель, куда загружают металл для плавки. При включении электрического тока в катушке образуется магнитное силовое поле, пронизывающее металл. За счет поля в металле индуктируются вихревые токи, которые нагревают и плавят его.
В индукционных печах получают легированные стали с малым содержанием углерода и различные сложные сплавы.
Рис. 3. Схемы дуговой (а) и индукционной (б) электрических печей
Металл, залитый в ковш, выдерживают в течение 10 мин для выравнивания его состава и выделения газов и неметаллических включений. После этого ковш подают на разливку.
Изложницы представляют собой чугунные или стальные сосуды определенной формы, позволяющие получать слитки квадратного, прямоугольного, многоугольного или круглого сечения в зависимости от назначения получаемых слитков. Изложницы заполняют жидким металлом из ковша сверху через центральный литник по каналам или снизу (сифонная разливка). Разливкой сверху получают крупные слитки массой до 35—45 т для прокатки.
Сифонная разливка применяется для получения слитков массой до 14—16 т высокого качества.
При непрерывной разливке сталь из разливочного ковша через промежуточный ковш равномерной струей заливается в кристаллизатор, представляющий короб, охлаждаемый проточной водой. Здесь быстро формируются стенки слитка, откуда он вытягивается валками с определенной скоростью, равной скорости кристаллизации. Ниже валков слиток полностью отвердевает и от него кислородной горелкой отрезаются заготовки-необходимой длины, которые автоматически направляются на транспортные тележки.
Непрерывная разливка стали обеспечивает высокое качество слитков, уменьшает потери металла и повышает производительность труда.
Качество стали повышается при разливке за счет применения ее вакуумирования. Этот метод заключается в удалении из стали растворенных газов путем вакуумной обработки стали в ковшах перед ее разливкой в изложницы и разливочную машину. В результате сталь становится более пластичной и прочной.
Разливка стали в вакууме применяется для получения высококачественных и легированных марок сталей. Этот способ требует применения дополнительного сложного оборудования.
—
Сталью называется сплав железа с углеродом и другими примесями (марганец, сера, фосфор, кремний и др.) при содержании углерода до 2%. Сталь по своим свойствам значительно отличается от чугуна. Она лучше поддается механической и термической обработке, хорошо куется, прокатывается и т. д. Детали машин, изготовленные из стали, более прочны по сравнению с чугунными деталями.
Сталь получают из чугуна или из смеси чугуна со стальным ломом при переработке их в мартеновских печах, в конвертерах и в электропечах. Сущность этих способов получения стали заключается в удалении углерода и других примесей до пределов, определяемых маркой стали. Удаление примесей происходит в результате окисления их при высоких температурах расплавленного металла с последующим переводом окислов в шлак. Удаляются примеси также в виде газообразных продуктов сгорания.
Мартеновское производство стали
Наиболее широкое применение находит производство стали в мартеновских печах. Крупнейшие в мире мартеновские печи построены в СССР. Емкость каждой из них составляет 900 т.
Сырьем служит твердый или жидкий чугун и стальной или чугунный лом. В качестве флюсов применяют: известняк, плавиковый шпат, бокситы. Топливом служит мазут, генераторный газ, смесь доменного и коксового газов, а также природный газ. Устройство мартеновской печи показано на рис. 2. Шихтусостоящую из расплавленного чугуна, холодного чугуна и флюсов, подают в рабочее пространство печи через завалочные окна.
В настоящее время широко применяют обогащение кислородом воздуха, поступающего в мартеновскую печь. Это ускоряет процесс горения, кроме того, обогащение воздуха кислородом облегчает процесс окисления примесей.
Регенераторы представляют собой камеры с насадками2 из огнеупорного кирпича. Насадки нагреваются за счет тепла отходящих из рабочего пространства газов. После того как насадки левых регенераторов достаточно охладятся газом и воздухом, а насадки правых регенераторов нагреются отходящими продуктами сгорания, клапаны 1 и шиберы 2, приводимые в движения электрическими лебедками, изменят направление газа, воздуха и продуктов сгорания на обратное, В результате газ и воздух будут нагреваться, проходя через правые, регенераторы, а левые регенераторы нагреваются отходящими продуктами сгорания.
Таким образом, применение регенераторов позволяет в результате предварительного подогрева газа и воздуха получить достаточно высокую температуру в рабочем пространстве печи и частично использовать тепло отходящих газов.
Рис. 4. Устройство мартеновской печи:
1 — клапаны; 2 — шиберы; 3 — левые регенераторы; 4 — правые регенераторы; 5 — рабочее пространство печи; 6 — дымовая труба
Подача жидкого чугуна из доменного цеха в мартеновский производится в ковшах на четырехосных чугуновозных тележках. В мартеновском цехе расплавленный чугун сливают при помощи мостового крана в миксер, который представляет собой футерованный огнеупорным кирпичом цилиндр емкостью 1,3 • 10 кг (1300 г) жидкого чугуна. Миксер обеспечивает работу мартеновских печей независимо от времени выпуска чугуна в доменном цехе и, кроме того, позволяет выравнивать состав и температуру жидкого чугуна.
В мартеновских цехах при помощи заливочных кранов заливают жидкий чугун в печь; при помощи завалочных кранов или напольных завалочных машин производят завалку в печь твердых составляющих шихты; разливочными кранами поднимают и переносят разливочные ковши и производят разливку стали в изложницы; остывшие слитки вынимают из изложниц при помощи кранов для раздевания слитков, снабженных специальным механизмом для выталкивания слитков из изложниц. Таким образом, в мартеновских цехах краны непосредственно участвуют в технологическом потоке.
Кроме перечисленных кранов, мартеновский цех, его шихтовый двор и уборочный пролет обслуживают магнитогрейферные краны и краны общего назначения. Всего в современном мартеновском цехе насчитывается 25-—30 мостовых кранов.
Производство стали в конвертерах
В современном отечественном производстве начинают применять 100-г и проектируют 250 и 500-г конвертеры.
Раньше производство стали в конвертерах заключалось в продувке воздуха через расплавленный чугун. Во время продувки сначала окисляется железо, при этом выделяется большое количество тепла, за счет которого поддерживают необходимую температуру в течение всего процесса. Образующееся за-кисное железо растворяется в металле и раскисляет содержащиеся в чугуне примеси.
Сталь, полученная по описанному способу, содержит большое количество шлаковых включений и газы (азот, кислород), что ухудшает механические качества стали и ограничивает область применения конвертерного метода . производства стали, так как по этому методу можно было получать сталь только из руд определенного состава.
В настоящее время при конвертерном производстве широко практикуют продувку через чугун, смеси воздуха с кислородом или чистого кислорода. При этом процесс идет значительно быстрей, появляется возможность использовать руды любого состава и .получать сталь то качеству такую же, как и при мартеновском способе производства. Отличительной чертой конвертерного производства является его высокая производительность: на 1 г емкости конвертера приходится более 60 т выплавленной стали в сутки.
В конвертерах, предназначенных для продувки жидкого чугуна воздухом, последний подается через керамические фурмы, расположенные в днище конвертера. Применение для продувки кислорода вместо воздуха позволяет отказаться от неудобных в эксплуатации керамических фурм, заменив их более долговечными водоохлаждаемыми подвесными фурмами.
Продувку жидкого чугуна кислородом производят сверху, для чего подвесную фурму на время продувки опускают в горловину конвертера. Для слива шлака и стали конвертер поворачивают при помощи механизма с электрическим приводом.
Для слива шлака и стали конвертер поворачивается в цапфах. Механизм поворота конвертера состоит из двух электрических двигателей, червячного редуктора и цилиндрического редуктора. Слив происходит через специальное отверстие в верхней части конвертера.
Скорость поворота конвертера регулируется в широких пределах. Максимальная скорость поворота равна приблизительно одному обороту в минуту.
Учитывая высокую производительность конвертеров на кислородном дутье и высокое качество стаЛи, выплавляемой при этом процессе, правительство Советского Союза взяло курс на значительное развитие конвертерного производства стали.
Производство стали в электрических печах
В современном отечественном сталеплавильном производстве самыми крупными являются 80-т электрические печи. В настоящее время в СССР проектируют электрические печи емкостью 120 т.
Электрические печи для выплавки стали разделяют на дуговые и индукционные.
В дуговых электропечах тепло для расплавления сообщается шихте электрической дугой, возбужденной между угольными электродами
Рис. 5. Конвертер на кислородном дутье (общий вид)
В индукционных печах металл плавится электрическим током, наведенным в шихте индукционным путем. Классическим примером индукционной печи является печь, где ванна для металла выполнена в виде кольца вокруг магнитопровода трансформатора. В этом случае ванна является коротко-замкнутой вторичной обмоткой трансформатора.
Производство стали в электропечах является самым совершенным. Но вследствие относительно высокой стоимости электрической энергии в дуговых электрических печах выплавляют только качественные, высококачественные и легированные стали и их сплавы. Индукционные же печи применяют в сравнительно редких, специальных случаях для выплавки сталей с улучшенной структурой.
Современный уровень развития техники предъявляет высокие требования к качеству стали.
С целью получения наиболее высококачественных сталей применяют вакуумирование стали. Вакуумированием жидкой стали удается в значительной степени уменьшить содержание в ней вредных газов (особенно водорода), ухудшающих ее качество.
Одной из новинок, позволяющей увеличить коэффициент использования жидкой стали, является непрерывная разливка. При этом способе жидкая сталь поступает в кристаллизатор с одного конца и, затвердевая, выходит слитком на другом конце кристаллизатора. Процесс происходит непрерывно. При непрерывной разливке стали значительно сокращаются потери металла, неизбежные при обычном способе разливки вследствие образования усадочных раковин.
Независимо от способа получения стали ее химический состав контролируют специальные лаборатории на протяжении всего технологического процесса, в результате чего стали присваивают марку, обозначающую ее химический состав и механические свойства.
Читать далее: Основные марки сталей и чугунов, применяемых при производстве и ремонте автомобилей
Производство стали в электропечах | Металлургический портал MetalSpace.
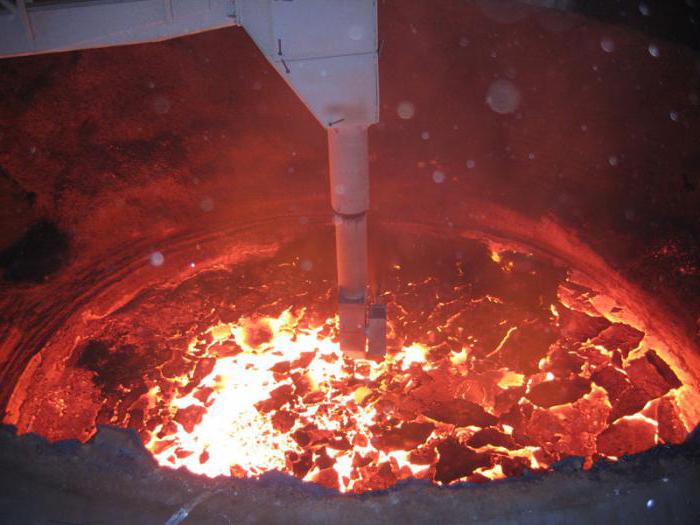
- возможность быстрого нагрева металла, что позволяет вводить в печь большое количество легирующих добавок;
- возможность создать окислительную, восстановительную, нейтральную или вакуумную атмосферу, что позволяет выплавлять сталь любого состава, раскислять металл с образованием минимального количества неметаллических включений;
- возможность плавно и точно регулировать температуру металла.
Поэтому электропечи используют для выплавки высоколегированных, конструкционных, специальных сталей и сплавов.
Плавильные печи
бывают:
- дуговыми;
- индукционными.
Основное количество электростали выплавляют в дуговых печах. Доля стали, выплавляемой в индукционных печах, в общем объеме выплавки невелика.
Дуговая плавильная печь
Дуговая электропечь состоит из рабочего пространства с электродами и токоподводами и механизмов, обеспечивающих наклон печи, удержание и перемещение электродов и загрузку шихты (рисунок 24). Плавку стали ведут в рабочем пространстве печи, ограниченным куполообразным сводом, снизу сферическим подом и с боков стенками. Огнеупорная кладка пода и стен заключена в металлический кожух. Она может быть основной (магнезитовой, магнезитохромитовой) или кислой (динасовой). В съемном своде расположены три цилиндрических электрода из графитизированной массы, которые с помощью специальных механизмов могут перемещаться вверх или вниз, автоматически регулируя длину дуги. Печь питается трехфазным переменным током.
Шихтовые материалы загружают на под печи сверху в открываемое рабочее пространство. После их расплавления в печи образуется слой металла и шлака. Плавление и нагрев шихты осуществляется за счет тепла электрических дуг, возникающих между электродами и жидким металлом или металлической шихтой.
Для управления ходом плавки в печи имеются рабочее окно и отверстие для выпуска по желобу готовой стали (летка). С помощью поворотного механизма печь может наклоняться в сторону сталевыпускного отверстия или рабочего окна. Вместимость дуговых печей может составлять 0,5 – 400 т. В металлургических цехах используют электропечи с основной футеровкой, а в литейных – с кислой.
В основной дуговой печи можно осуществить плавку двух видов:
- без окисления примесей методом переплава шихты из легированных отходов;
- с окислением примесей на углеродистой шихте.
Плавка без окисления примесей
Шихта для такой плавки должна иметь низкое содержание фосфора и меньше, чем в выплавляемой стали, марганца и кремния. Производят нагрев и расплавление шихты. По сути это переплав. Однако в процессе плавки часть примесей окисляются (алюминий, титан, кремний, марганец).
После расплавления шихты из металла удаляют серу, наводя основной шлак. При необходимости науглероживают и доводят металл до заданного химического состава. Затем проводят диффузионное раскисление, подавая на шлак мелкораздробленный ферросилиций, алюминий, молотый кокс. Плавкой без окисления примесей выплавляют стали из отходов машиностроительных заводов.
Плавка с окислением примесей
Плавку применяют для производства конструкционных сталей и ведут на углеродистой шихте. В печь загружают шихту, состоящую из стального лома (~90%), чушкового передельного чугуна (до 10%), электродного боя или кокса для науглероживания металла и известь (2-3%) . Затем опускают электроды, включают ток и начинают плавку. Шихта под действием тепла дуги плавится, металл накапливается на подине печи. Во время плавления шихты кислородом воздуха, оксидами шихты окисляются железо, кремний, фосфор, марганец и частично углерод. Оксид кальция и оксиды железа образуют основной железистый шлак, способствующий удалению фосфора из металла.
После прогрева металла и шлака до температуры 1500 – 1550 °С в печь загружают руду и известь и проводят период кипения. Когда содержание углерода будет меньше заданного на 0,1%, кипение прекращают и удаляют из печи шлак. Затем проводят удаление серы и раскисление металла, доведение химического состава до заданного. Раскисление проводят осаждением и диффузионным методом. После удаления железистого шлака в печь подают раскислители (силикокальций, силикомарганец) для осаждающего раскисления. Затем в печь загружают известь, плавиковый шпат, шамотный бой для получения высокоосновного шлака. После расплавления флюсов и образования высокоосновного шлака на его поверхность вводят раскислительную смесь для диффузионного раскисления (известь, ферросилиций, плавиковый шпат, молотый кокс). Углерод кокса и кремний ферросилиция восстанавливают оксид железа в шлаке и содержание его в шлаке снижается.
В этот период создаются условия для удаления из металла серы, что объясняется высоким содержанием СаО в шлаке (около 60%), низким содержанием FeO (менее 0,5 %) и высокой температурой металла. Для определения химического состава металла берут пробы и при необходимости в печь вводят ферросплавы для получения заданного химического состава металла. Затем выполняют конечное раскисление стали и выпускают из печи в ковш.
В дуговых печах выплавляют высококачественные углеродистые стали. Это конструкционные, инструментальные, жаропрочные и жаростойкие стали.
Индукционная плавильная печь
Печь состоит из водоохлаждаемого индуктора, внутри которого находится тигель с металлической шихтой (рисунок 25). Через индуктор от генератора высокой частоты проходит переменный ток повышенной частоты. Ток создает переменный магнитный поток, пронизывая куски металла в тигле, наводит в них мощные вихревые токи, нагревающие металл до расплавления и необходимых температур перегрева. Тигель может быть изготовлен из кислых и основных огнеупоров. Емкость тигля составляет до 25 т.
В соответствии с заданным химическим составом металла при загрузке тщательно подбирают состав шихты. Необходимое для этого количество ферросплавов загружают на дно тигля вместе с шихтой. После расплавления шихты на поверхность металла загружают шлаковую смесь для уменьшения тепловых потерь металла и уменьшения угара легирующих элементов, а также для защиты его от насыщения газами.
При плавке в кислой печи после расплавления и удаления шлака наводят новый шлак с высоким содержанием SiO2. Металл раскисляют ферросилицием, ферромарганцем и алюминием перед выпуском его из печи. В печах с кислой футеровкой выплавляют конструкционные стали, легированные другими элементами.
В печах с основной футеровкой выплавляют высококачественные легированные стали с высоким содержанием марганца, никеля, титана, алюминия.
Индукционные печи имеют ряд преимуществ перед дуговыми. Основными их них являются:
- отсутствие электрической дуги, что позволяет выплавлять сталь с низким содержанием углерода, газов и малым угаром элементов;
- наличие электродинамических сил, которые перемешивают металл в печи способствуют выравниванию химического состава, всплыванию неметаллических включений;
- небольшие размеры печей позволяют помещать их в камеры, где можно создать любую атмосферу или вакуум.
К недостаткам этих печей можно отнести:
- недостаточная температура шлака для протекания металлургических процессов между металлом и шлаком;
- малая стойкость футеровки, что приводит к частым ремонтам и остановкам.
Поэтому в индукционных печах выплавляют сталь из легированных отходов методом переплава или методом сплавления чистого шихтового железа и скрапа с добавкой ферросплавов.
ПОДЕЛИСЬ ИНТЕРЕСНОЙ ИНФОРМАЦИЕЙ
Процесс производства стали – Как производится сталь?
Процесс производства стали — как производится сталь?
10 апреля 2020 г.
Производство стали является критически важной отраслью, оказывающей значительное влияние на нашу мировую экономику. С середины 1800-х годов сталь стала одним из самых надежных материалов во всем мире, обслуживая бесчисленные производственные и строительные рынки. По данным Всемирной ассоциации производителей стали, мировое производство стали поддерживает или способствует росту цен на 2,9 долл.триллиона мировой экономической деятельности, что делает его важнейшим материалом, поддерживающим миллионы рабочих мест на международном уровне.
Сталь может показаться не товаром, связанным с передовыми технологиями, но процесс ее производства прошел долгий путь. В этом руководстве по процессу производства стали мы рассмотрим историю производства стали и сравним ее с тем, как сталь производится и используется в современных приложениях.
История производства стали
Сталь — это открытие железного века, периода, начавшегося около 1200 г. до н. э. Железная руда была впервые добыта в Центральной Азии и Европе, и в то время люди использовали железо для изготовления инструментов и оружия в практике, называемой черной металлургией. Изделия из железа развивались в это время, начиная с кузнецов, производящих изделия из кованого железа. Эти торговцы научились нагревать железную руду, и, используя процесс молота и наковальни, кузнецы удаляли примеси из металла и производили прочный и ковкий конечный продукт из железа.
Железо приняло несколько других форм, прежде чем в конечном итоге превратилось в то, что сегодня считается сталью. В Китае металлурги железного века нагревали железо в больших печах, плавя вещество в жидкость и смешивая его с древесным топливом. Затем расплавленную жидкость заливали в формы, которые затем оставляли затвердевать, в конечном итоге принимая форму кухонных инструментов и других предметов из форм. Этот процесс, известный как литье чугуна, позволил получить более прочный продукт, чем кованое железо, но он был хрупким, что затрудняло его форму и изгибание.
После чугуна кузнецы Центральной Европы начали покрывать изделия из кованого железа древесным углем, чтобы повысить прочность железа при сохранении его гибкости. После этого железо прошло последнюю итерацию, которая больше всего напоминает сегодняшнюю сталь. В Индии рабочие-металлурги разработали процесс выплавки железа, сочетающий в себе идеальное соотношение железа и углерода. Используя тигли или глиняные контейнеры, мастера по металлу смешивали куски железа и древесного угля в высокотемпературной печи. Во время приготовления железо плавилось и поглощало атомы углерода из древесного угля. После охлаждения тигли содержали то, что мы теперь знаем как сталь — сплав железа с углеродом.
После открытия железоуглеродистых сплавов различные цивилизации начали расширять свои методы производства стали, что позволило им создавать улучшенное оружие, инструменты и конструкции. Начиная с железного века, люди стремились усовершенствовать процесс производства стали не только для того, чтобы производить ее в больших количествах, но и для того, чтобы производить ее более эффективно. Постоянное совершенствование производства стали является причиной того, что сегодня сталь стала таким важным мировым товаром.
Как сегодня производится сталь?
Современный процесс производства стали начался в 1856 году в рамках процесса, известного как бессемеровский процесс. Считается, что это был первый процесс массового производства стали. По словам историков, два разных изобретателя, один в Великобритании и один в Питтсбурге, одновременно разработали процесс производства стали, который включал удаление примесей железа с помощью струи воздуха.
С этим открытием другие производители стали начали совершенствовать процесс, в конце концов найдя способ использовать технику струйной очистки воздуха, чтобы помочь сохранить содержание углерода при полном удалении примесей. Наконец, этот процесс превратился в экономически эффективный способ массового производства высококачественной стали, который мы используем до сих пор.
Сегодняшняя сталь обычно производится одним из двух способов:
- Доменная печь: Процесс доменной печи, также известный как основной кислородный процесс (BOP), объединяет сырую железную руду с небольшим количеством стального лома в печь. Затем в печь вдувают чистый кислород, повышая ее температуру. При этой температуре металлолом не только плавится в жидкость, но и примеси железа окисляются, полностью испаряясь. Кроме того, высокая температура снижает содержание углерода до идеального соотношения, что приводит к получению жидкой стали.
- Электродуговые печи: В методе электродуговой печи (ЭДП) сильноточные электрические дуги от электродов плавят большое количество стального лома в жидкость. Пока стальной лом плавится, техники добавляют другие ферросплавы до тех пор, пока жидкий металл не достигнет желаемого соотношения стали и других сплавов, таких как хром и никель, которые образуют нержавеющую сталь.
Затем для очистки стали в печь подается кислород и добавляются известь и плавиковый шпат. Эти вещества соединяются с примесями стали, превращаясь в шлак. Затем шлак всплывает на поверхность расплавленной стали, где его удаляют, оставляя чистую сталь.
Метод ЭДП является сегодня наиболее распространенным методом производства стали. Сегодняшние современные сталеплавильные печи ЭДП производят 150 тонн стали за плавку, что занимает примерно 90 минут.
Изготовление металла на заказ
Сталь— это универсальный, доступный и широко распространенный материал, что делает его идеальным материалом для использования в бесчисленных производственных мощностях. Производители оригинального оборудования и другие компании-производители полагаются на ценность стали при производстве своих оригинальных компонентов и продуктов.
Во всем мире предприятия используют сталь и сплавы металлов для производства своей продукции и воплощения своих проектов в жизнь. Изготовление и проектирование металлоконструкций на заказ — это важнейшая профессиональная услуга в мировой экономике, потому что именно она позволяет компаниям изобретать новые и полезные товары и рисковать инновационными проектами, которые помогают формировать и улучшать нашу повседневную жизнь.
Производство и проектирование металлоконструкций объединяет целый ряд экспертов, от дизайнеров, инженеров и консультантов до сварщиков, слесарей и монтажников. Каждый эксперт играет свою роль в обеспечении того, чтобы сталь и металлические материалы превращались в хорошо спроектированные, высококачественные компоненты и конечные продукты, которые будут играть важную роль на нашем глобальном рынке.
Выберите Summit Steel для контрактного производства металла на заказ
Производителям и OEM-предприятиям требуются надежные, профессиональные и знающие партнеры по контрактному производству металлоконструкций, которые помогут им эффективно производить сталь и готовую металлическую продукцию в соответствии с самыми высокими стандартами. Если вы ищете компанию по производству прецизионных металлов для удовлетворения ваших уникальных потребностей бизнеса, выберите Summit Steel.
Уже более 25 лет Summit Steel помогает предприятиям эффективно производить детали с помощью передовых производственных процессов. Наши услуги по контрактному производству металлов варьируются от первоначального проектирования и инженерной поддержки до лазерной резки, 3D-обработки и процессов сварки стали и металлов. Наши гибкие предложения услуг могут быть адаптированы для удовлетворения любого объема производства, необходимого вашему бизнесу. Summit Steel может поставлять высококачественные, точно изготовленные металлические и стальные изделия и детали для вашей отрасли, начиная от возможностей одного поставщика и заканчивая крупными заказами.
Для получения дополнительной информации о заключении контрактов с Summit Steel на изготовление металлоконструкций на заказ свяжитесь с нами сегодня. Позвоните нам по телефону (610) 921-1119 или запросите расценки онлайн.
Брайан Рид
Брайан Рид — вице-президент по продажам и развитию бизнеса в Summit Steel & Manufacturing Inc.
Как сталь может, наконец, избавиться от привычки использовать уголь
Угольная хватка в мировом электроэнергетическом секторе ослабевает по мере того, как все больше коммунальных предприятий и компаний инвестируют в возобновляемые источники энергии. Но одному крупному потребителю угля — сталелитейной промышленности — все труднее избавиться от этой привычки.
Сталелитейные компании ежегодно производят почти 2 миллиарда тонн высокопрочного материала для мостов, зданий, железных и автомобильных дорог. Печи, которые плавят железную руду для производства стали, потребляют огромное количество угля. В результате на долю отрасли приходится примерно 8 процентов ежегодных выбросов углекислого газа, а также токсичный бульон из загрязнителей воздуха.
Сталелитейщики во всем мире сталкиваются с растущим давлением со стороны государственных регулирующих органов и потребителей, требующих обезуглероживания производства. По словам экспертов, это необходимо для ограничения глобального потепления до 1,5 градусов по Цельсию и предотвращения большинства наихудших последствий изменения климата. В последние месяцы три ведущих мировых производителя — европейская ArcelorMittal, китайская Baowu Steel и японская Nippon Steel — взяли на себя обязательство добиться нулевых выбросов к 2050 году, повторяя цели, установленные в их странах.
Но для того, чтобы сократить выбросы углерода в атмосферу при производстве стали, отрасли придется изменить способ традиционного производства этого материала.
За пределами Бостона, в промышленном пригороде Воберна, одна компания работает над заменой угля электронами. Boston Metal, подразделение Массачусетского технологического института (MIT), использует электрические токи для нагрева железной руды до ярко-оранжево-белой жидкости, которая превращается в металл и охлаждается в виде серых стальных блоков. Процесс не создает выбросов парниковых газов, а при питании от возобновляемой электроэнергии может быть полностью без выбросов.
Grist полагается на поддержку таких щедрых читателей, как вы. Сделайте пожертвование сегодня, чтобы наши климатические новости оставались бесплатными. Все пожертвования совпали!
- Один раз
- Ежемесячно
- 10 долларов
- 15 долларов
- Другой
Тадеу Карнейро, генеральный директор компании, сказал, что Boston Metal «открывает новую эру металлургии». Девятилетний стартап привлек в январе 50 миллионов долларов от множества инвесторов, в том числе от возглавляемой Биллом Гейтсом Breakthrough Energy Ventures и венчурного подразделения BHP, одной из крупнейших в мире горнодобывающих компаний. Новое финансирование позволит построить демонстрационный завод в Вобурне, который сможет производить 25 000 тонн металла в год; до сих пор компания произвела всего несколько тонн стали.
Подход Boston Metal — одна из немногих передовых технологий, способных обезуглероживать производство стали. Компании тестируют системы по всей Европе, которые используют водород в печах вместо угля. В Бразилии некоторые сталелитейные заводы смешивают биоуголь, который производится из сельскохозяйственных отходов. Другие фирмы продолжают использовать уголь, но рассматривают возможность переоснащения объектов устройствами улавливания углерода, чтобы свести к минимуму выбросы.
Тестирование и масштабирование технологий, которые удаляют выбросы при производстве стали, — не единственная проблема обезуглероживания строительного материала. Более экологичные продукты также должны конкурировать в отрасли с относительно низкой нормой прибыли и избыточным предложением недорогой китайской стали.
Чтобы уравнять правила игры, государственные учреждения и частные предприятия должны будут установить политику, поощряющую покупку стали без выбросов или удорожание покупки обычных материалов, сказал Нейт Аден, старший научный сотрудник Института мировых ресурсов, изучающий трансформации промышленного сектора. (Калифорния, например, ограничивает общий объем выбросов углерода, связанных со сталью и другими материалами, используемыми в строительных проектах, поддерживаемых государством.)
«У нас не было достаточно исследований и разработок в этой области за последние пару десятилетий, — сказал Аден. “Это увлекательно.”
Около 70 процентов стали сегодня производится так, как она производилась всегда: в гигантских, чрезвычайно горячих печах. Очищенный уголь или «кокс» нагревают и расплавляют с оксидом железа и известняком, затем вводят кислород для уменьшения содержания углерода в смеси и удаления примесей.
Почти вся остальная сталь производится из металлолома, который переплавляется в электродуговой печи. Этот подход не использует кокс в качестве сырья. Но для нагрева металла до почти 3000 градусов по Фаренгейту требуется значительное количество электроэнергии, и большая часть этой энергии поступает от угольных электростанций.
В исследовательском центре Boston Metal процесс производства стали происходит внутри приземистого металлического цилиндра, называемого электролитической ячейкой. Электричество подается сверху и течет по похожей на дымоход трубе, сделанной из сплава на основе хрома. Затем электрический ток проходит через жидкий раствор, состоящий из оксида железа и других металлических минералов. Это нагревает расплав оксида и запускает химические реакции, которые приводят к образованию газообразного кислорода и жидкого железа. Кислород пузырится наверху, а укрепленное железо скапливается на дне камеры и в конечном итоге затвердевает в сталь.
Дональд Садоуэй, профессор химии материалов в Массачусетском технологическом институте, сказал, что идея «электролиза расплавленного оксида» пришла ему в голову несколько десятилетий назад, когда он исследовал альтернативные способы производства алюминия, другого металла, получаемого с помощью углеродоемкого процесса. В 2012 году он вместе с двумя партнерами стал соучредителем Boston Electrometallurgical (также известного как Boston Metal), и они начали тестировать метод в лабораторных ячейках размером со стакан для хайбола. В настоящее время компания управляет тремя пилотными линиями на заводе в Уобурне.
Садоуэй сказал, что с инвестициями в размере 50 миллионов долларов от Breakthrough, BHP и других компаний цель состоит в том, чтобы продемонстрировать технологию в достаточно большом масштабе, чтобы убедить инвесторов поддержать строительство промышленного объекта. По его оценкам, если этот будущий завод будет реализован, процесс Boston Metal будет потреблять примерно на 20 процентов меньше энергии, чем обычная доменная печь. И если объект может использовать дешевую, обильную возобновляемую электроэнергию, возможно, от гидроэлектростанции, его сталь будет стоить меньше, чем у конкурентов.
«Мы рассчитываем производить более качественный металл с меньшими затратами и без выбросов CO2», — сказал он.
Поскольку Boston Metal расширяет свои усилия в области электролиза, многие сталелитейные компании делают ставку на водород для сокращения выбросов.
Водород не выделяет парниковых газов при сжигании и может быть получен с использованием возобновляемой электроэнергии для разрушения молекул воды (хотя большая часть водорода сегодня производится из природного газа посредством процесса, называемого паровым риформингом метана). В сталеплавильном производстве водород запускает химическую реакцию, которая удаляет кислород из железной руды, устраняя необходимость в очищенном угле в доменной печи.
Компания ArcelorMittal со штаб-квартирой в Люксембурге строит в Германии демонстрационный завод, использующий этот метод, называемый водородным ПВЖ, что означает «железо прямого восстановления». Японская Mitsubishi Heavy Industries планирует опробовать технологию в этом году на сталелитейном заводе мощностью 250 000 тонн в год в Австрии. А в Швеции производитель стали SSAB и его партнеры построили пилотную установку для производства водородных запасов и испытали водородный метод прямого восстановления, используя для обеих операций только гидроэлектроэнергию.
Создание сталелитейной промышленности на основе водорода потребует значительных затрат не только на строительство новых заводов, но и на производство, транспортировку и хранение зеленого водорода. Чтобы эти проекты были экономически жизнеспособными в мире дешевой стали, цены на водород и возобновляемую электроэнергию должны значительно упасть, а цена на двуокись углерода должна вырасти, написал Аден в статье 2020 года в составе международной группы экспертов.
Есть еще одна долгосрочная задача для новых, чистых проектов. Спрос на сталь снижается или стагнирует на ключевых рынках, включая США и Японию. Производители уже производят больше стали, чем нужно миру. Тем временем строительные компании и производители автомобилей все чаще используют в своих проектах легкий алюминий, пластик и даже дерево. По словам Адена, это может затруднить обоснование будущих инвестиций или исследований.
Тем не менее, сталелитейная промышленность остается важной частью мировой экономики, а также значительным источником мировых выбросов.
«Ясно одно: в ближайшие несколько десятилетий нам понадобится сталь, — сказал Аден. «Поэтому я думаю, что все эти новые проекты стоят того».
Различные типы стали и способ их изготовления
Существует множество различных типов стали, каждый из которых уникален из-за способа его изготовления или типа ингредиентов, из которых он изготовлен. Каждый из этих различных типов стали имеет разную прочность и уровень гибкости, и лучший тип стали для проекта зависит от конкретных характеристик и требований, которые вы ожидаете от своего стального продукта, независимо от того, используется ли он в производстве крупных коммерческие фабрики или современный архитектурный шедевр.
Процесс производства стали сильно изменился за эти годы, а усовершенствования в производстве стали сделали доступность и доступность стали намного выше в прошлом веке.
Как делают сталь
Археологи нашли древние образцы стали, датируемые 1400 г. до н.э. Многие древние люди использовали сталь для изготовления оружия и инструментов, необходимых для охоты и приготовления пищи. Есть два основных типа металла: черные металлы и цветные металлы. Черные металлы относятся к использованию железа в качестве основного компонента, что означает, что черные металлы состоят в основном из железа. Самый примитивный метод изготовления стали заключался в плавлении и соединении кованого железа и чугуна. Однако количество железа, необходимого для производства этой стали в качестве побочного продукта, и стоимость обеспечения этими ингредиентами были настолько велики, что сталь было трудно достать и она была доступна только богатым. Дополнительные затраты также лежали в процессе плавки. Количество угля, необходимое для производства достаточно сильного тепла, чтобы расплавить железо, также сделало сталь своего рода предметом роскоши.
По мере того, как Америку охватила промышленная революция, а небоскребы и другие большие здания и памятники стали признаком промышленного и экономического превосходства, потребность в массовом, прочном и гибком строительном материале росла в геометрической прогрессии. Время и усилия были направлены на совершенствование процесса производства стали и превращение стали в краеугольный камень современной американской архитектуры. Было обнаружено, что кокс, золу и остатки серы из угля можно использовать для нагревания металла так же, как и уголь, и за гораздо меньшую, чем половину цены.
В 1858 году человек по имени Генри Бессемер обнаружил, что смесь железной руды и известняка или антрацита можно плавить с использованием кокса в качестве реакционного агента, и в результате получается прочная, но гибкая сталь, которая не зависит исключительно от железа. как его основной ингредиент. Это открытие дало толчок производству стали в многомиллиардной отрасли, какой мы ее знаем сегодня, и подтвердило, что сталь станет основой национальной строительной отрасли.
Различные типы стали
Сталь – это то, что известно как сплав, что означает, что он не встречается в природе, а создается человеком, состоящим из комбинации различных материалов и металлов. Тип стали, получаемой в конце процесса производства стали, зависит как от различных типов металлов, которые были расплавлены вместе для получения конечного продукта, так и от того, как эти металлы нагреваются, охлаждаются и обрабатываются во время производства. Различные типы стали различаются по цене и подходят для разных типов проектов, например, используется ли сталь для строительства домов или изготовления инструментов.
Нержавеющая сталь
Нержавеющая сталь является одним из самых дешевых металлов в производстве. Одной из причин, по которой нержавеющая сталь стала настолько популярной в строительных проектах, является тот факт, что она не ржавеет и не разрушается под воздействием влаги, по этой причине нержавеющая сталь также известна как коррозионностойкая сталь. В отличие от других распространенных форм стали, нержавеющая сталь изготавливается из хрома, а не из углерода, который образует защитный слой над внутренними слоями стали и придает нержавеющей стали неагрессивные свойства. Нержавеющая сталь также широко используется во многих известных произведениях архитектуры, поскольку она приобрела популярность в период ар-деко благодаря своему блестящему и яркому внешнему виду. Третья причина, по которой нержавеющая сталь является популярным строительным материалом, связана с тем, что она легко перерабатывается. Нержавеющая сталь на 100 процентов пригодна для вторичной переработки, а процесс переработки стали на самом деле очень безвреден для окружающей среды.
Кобальтовая сталь
Кобальтовая сталь по составу очень похожа на быстрорежущую сталь, за исключением более высокой концентрации кобальта. Кобальт является очень термостабильным элементом, что делает кобальтовую сталь идеальной для стальных деталей, которые будут подвергаться сильному нагреву или трению. Как и нержавеющая сталь, кобальтовая сталь также устойчива к коррозии и другим пятнам. Однако кобальт очень твердый и хрупкий, что делает его подверженным разрушению или растрескиванию под экстремальными весовыми нагрузками или силами давления. Кобальт имеет характерный ярко-синий цвет, а большинство кобальтовых сталей имеют голубоватый оттенок, если только они не подвергались химической обработке после производства.
Углеродистая сталь
Углеродистая сталь бывает двух видов: высокоуглеродистая сталь и высоколегированная сталь, каждая из которых чрезвычайно пластична и мягка, а также очень экономична. Углеродистая сталь и высоколегированная сталь являются самыми дешевыми вариантами на рынке. Углеродистая сталь названа удачно, потому что основным компонентом этого материала является углерод, который представляет собой проблему, поскольку открытая углеродистая сталь, которая не защищена должным образом от окисления, может легко ржаветь и подвергаться коррозии. Чем выше содержание чистого углерода, тем тверже становится сама сталь, но она также становится менее гибкой и легкой в обработке.
Карбид Сталь
Карбид — очень прочный элемент, прочность которого в три раза выше, если сравнивать оба элемента в их естественном состоянии.