Как сделать форму для литья: Как сделать форму для литья
alexxlab | 29.03.1991 | 0 | Разное
Изготовление форм для литья из пластика. Особенности литьевого процеса
Переработка пластика — прибыльный бизнес, не требующий большого вложения начального капитала. Кроме того, решается проблема утилизации полимерных отходов, скапливающихся на свалках и мусорных полигонах.
Компания «Имстек» предлагает изготовление форм для литья изделий из пластика. Комплектующие и оснастка поставляется из Китая и Тайваня.
Процесс литья пластмассовых изделий осуществляется в термопластавтоматах с ЧПУ и включает в себя следующие этапы:
Развитие бизнеса по переработке пластмасс следует начинать с выбора производственного помещения и подбора персонала.
Помещение для бизнеса лучше взять в аренду. Это способствует быстрому запуску производственной линии.
Требования к помещениям для размещения производства для литья пластмасс:
Минимальная площадь производственного цеха — 50 м2, складского помещения — от 80 м2.
Необходимую площадь рассчитываем в зависимости от размеров и количества производимых изделий и исходя из собственных возможностей.
2. Подбор персонала
Успех предприятия и качество продукции напрямую зависит от профессионализма заведующего производством или технолога, осуществляющего руководство и контроль за соблюдением технологии литья.
В штате предприятия должен быть следующий персонал:
Для обслуживания малого производственного предприятия требуется штат специалистов и подсобных рабочих в количестве 6-8 человек. На работу нужно принимать проверенных и надежных специалистов, имеющий опыт работы и соответствующую квалификацию.
Основные виды сырья для литья пластмасс
Подбор полимерных составов для изготовления пластмассовых деталей — важнейший этап подготовки производства.
Для производства подойдут термопластичные и термореактивные полимеры, пенопласты:
Материалы имеют различную структуру, температуру плавления и пластичность. При смене сырья перенастраивается оборудование.
Полимерные отходы проходят сортировку и дробление, промываются и высушиваются.
Рис. 1. Полимерное сырье.
Основные технологии литья
Для литья пластмасс используются следующие способы:
- Экструзионный — выполняется с использованием литьевых машин методом выдавливания или выталкивания через формообразующую матрицу. Используется при изготовлении шлангов, кабельной продукции, погонажных изделий.
- Инжекционный, при котором расплавленный полимер, под действием высокого давления, впрыскивается в форму. Применяется для изготовления тонкостенных деталей сложных конфигураций, пластиковых корпусов электроинструмента и оборудования, детских игрушек.
- Выдувной — для создания полых изделий: пластмассовой тары, бутылок, банок, емкостей для лекарств, красок.
- Термоформовочный — пластиковая продукция изготавливается методом прессования. Используется для изготовления одноразовой посуды, контейнеров, упаковки.
- Интрузионный метод литья используется для литья толстостенных деталей. Сырье нагнетается при помощи вращающегося червячного шнека.
Кроме того существуют сложные технологии: соинжекционные, сэндвич, литье в поворотные или в многокомпонентные формы.
Такими способами изготавливаются многослойные, двухкомпонентные, разноцветные детали, изделия с четким разграничением цветов или наружным покрытиям.
Рис. 2. Виды литых изделий из пластмасс.
Технологии литья под давлением
Технология литья под давлением позволяет выпускать тонкостенные изделия различных конфигураций из термопластичных полимеров.
Процесс создания пластмассовых изделий в литьевых станках включает в себя:
Выбор необходимого оборудования
Выбор оборудования зависит от типа изготавливаемых товаров.
1. Термопластавтомат
Представляет собой литьевую машину с электрическим или гидромеханическим приводом для создания пластмассовых изделий под давлением.
Состоит из следующих конструктивных узлов:
Прессовые механизмы могут располагаться горизонтально, вертикально, быть угловыми с горизонтальным или вертикальным прессом.
Рис.3. Термопластавтомат от компании «Имстек».
Для различных изделий задаются индивидуальные параметры по объему впрыска, скорости, температуре плавления.
Могут быть с раздельной или совмещенной пластификацией и иметь несколько узлов смыкания. Бывают одно или двухчервячными, поршневыми и червячно-поршневыми.
2. Пресс-формы
Представляют собой модули из неподвижной матрицы и подвижных пуансонов. Внутри имеют полость для впрыскивания расплавленных полимеров. Предназначены для создания серийных деталей.
Пресс-формы изготавливаются по техническому заданию заказчика, в точности повторяют очертания будущих отливок.
Готовые формы крепятся к элементам смыкания литьевых машин, в полость впрыскивается жидкая полимерная масса.
Рис. 4. Пресс-формы для литья пластиковых изделий от компании «Имстек».
3. Вакуумный загрузчик сырья
Агрегаты для бесперебойной автоматической подачи полимерных гранул в термопластавтоматы или экструдеры. Состоят из приемных бункеров, насосов вакуумных, автоматического дозирующего модуля, очистителей выходящего из установки воздуха. Бывают моноблочные и раздельные.
Компактные моноблочные загрузчики могут размещаться непосредственно на литьевой машине.
Мощные раздельные загрузчики могут транспортировать сырье на значительные расстояния и большую высоту.
Компания «Имстек» поставляет загрузчики с индукционными двигателями, подключаемые к трехфазной сети 380 вольт и устройства, работающие от сети 220 вольт.
Подача сырья осуществляется методом вакуумного всасывания материала в приемный бункер, откуда воздух откачивается вакуумным насосом. Под давлением собственного веса оно поступает в модуль загрузки термопластавтомата, литьевой машины или экструдера.
Управление процессом загрузки осуществляется через автоматический блок управления. Выходящий из агрегата воздух очищается, проходя через воздушные фильтры.
Рис.5. Вакуумный загрузчик.
4. Холодильный агрегат
Предназначен для охлаждения готовых изделий при многосерийном производстве в термопластавтоматах.
Сокращает производственный цикл изготовления пластмассовых отливок из расплавленного сырья.
Автоматическая система управления обеспечивает точные температурные параметры.
Рис.6. Холодильный агрегат.
Домашнее литье пластика
Литье пластиковых изделий в домашних условиях применяется для изготовления ограниченных партий мелких изделий: сувениров, игрушек, посуды, всевозможных крышек или колпачков.
Для заливки полимерных материалов применяются силиконовые формы.
1. Оборудование для мелкосерийного литья
Малые партии товаров изготавливаются на настольных станках, легко размещающихся на малых площадях.
Для изготовления деталей на мини-станках необходимы пресс-формы и пластиковое сырье.
2. Самостоятельное изготовление пресс-форм из силикона
Пресс формы для пластиковых деталей можно изготовить из силикона в домашних условиях. Для этого потребуется прототип заданного изделия или мастер-модель, которая печатается на 3D принтере, или создается на станке ЧПУ. Готовая модель покрывается лаком и шлифуется до идеальной гладкости.
Мастер-модель устанавливается в опалубку, для создания половины формы. Объем заливается силиконом с отвердителем и помещается в камеру дегазации для удаления пузырьков. Сушатся силиконовые заливки в течение 6-8 часов, после чего модель вынимается из силикона.
Таким же образом создается вторая половина формы.
Рис. 7. Силиконовая форма разрезная.
Две половинки пресс-формы соединяются с помощью скотча, скоб или резинок, в них заливается жидкий двухкомпонентный полимер.
Для ускорения процесса сушки емкость с силиконом лучше подогреть, поместив в духовой шкаф с температурой 35-40°С.
При изготовлении сувенирной и брендовой продукции используются односторонние формы. Для их создания модель помещается в емкость из пластика, металла или оргстекла и заливается силиконом.
Рис. 8. Силиконовая форма односторонняя.
Пресс-формы из силикона четко копируют модель, заполняя все выемки и впадины.
Основные виды силикона для изготовления пресс-форм
По техническим параметром подходят составы:
- Sorta Clear, с показателями твердости 18, 37, 40. Полупрозрачный материал, используемый для создания сложных разрезных форм.
- Mold Star, твердостью 15,16,30. Двухкомпонентный пластичный состав, подходящий для изготовления тончайших деталей, отлично застывающий при температуре 18-22°С.
- Rebound 25, 40. Двухкомпонентный состав. Наносится послойно на подготовленную модель с помощью кисти.
Все материалы могут использоваться с ускорителями застывания и пластификаторами.
Основные характеристики двухкомпонентных пластиков
В жидком виде двухкомпонентные пластики используются при изготовлении небольших серий пластмассовых изделий.
Составы могут различаться по цвету, фактуре, плотности и твердости готовых изделий.
Процесс полимеризации начинается после смешивания компонентов. Полную прочность изделие набирает через 10-15 минут.
Технология литья в силиконовые формы
Для литья деталей используется жидкий пластик, не требующий дополнительного разогрева.
Силиконовые формы очищаются от возможных загрязнений, две половинки соединяются и скрепляются между собой скотчем, резинками, скобами и прочими подручными материалами.
Компоненты разводятся в емкости, при необходимости добавляются красители.
Через литники в форму подается двухкомпонентный раствор тонкой струйкой.
После застывания готовые изделия извлекаются.
Метод подходит для создания небольших партий деталей.
Технология литья с использованием ручного станка
Ручные станки используются в домашних условиях, лабораториях, СТО или нанебольших предприятиях. Они не требуют много места и могут размещаться на обычном столе.
Литье выполняется в следующем порядке:
Как изготавливать пресс-формы для литья под давлением, отливки и термоформования с помощью 3D-печати
Изготовление форм для литья используется в различных отраслях такими специалистами, как проектировщики, производственники и преподаватели при создании коротких производственных циклов, прототипов сложных пресс-форм, испытания изделий из пластмасс для дальнейшего использования на практике и, главным образом, в тех случаях, когда необходимо сделать несколько экземпляров детали без особых затрат и усилий. Это позволяет быстро изготавливать небольшие партии от 150 до 600 деталей или проверить конструкцию пресс-формы, прежде чем приступать к изготовлению дорогостоящей оснастки.
Изготовление формы с помощью настольной 3D-печати позволяет инженерам и проектировщикам расширить сферу использования материалов и возможности своего 3D-принтера за границы быстрого прототипирования в область промышленного производства. Изготовленные 3D-печатью модели для процессов формования, как правило, получаются быстрее и дешевле, чем модели, изготавливаемые фрезерованием на станках ЧПУ, и проще, чем изготовленные с помощью силиконовых форм.
Формы для небольших партий, напечатанные на 3D-принтере, как правило, не такие дорогие и более просты в изготовлении по сравнению с формами, изготавливаемыми на станках с ЧПУ или с помощью силиконовых форм.
В этой статье мы рассмотрим три технологии изготовления пресс-форм, которые легко дополняются 3D-печатью: литье под давлением, отливка и термоформование. Для более углубленного ознакомления с этими технологиями, а также для с рекомендациями по изготовлению форм и 3D-печати см. наш последний вебинар.
Смотреть вебинар сейчас
Литье под давлением было изобретено в 1872 году Джоном Уэсли Хайатом и вначале действовало по тому же принципу, что и шприц для подкожных инъекций. Современная установка для литья под давлением была окончательно создана в 1956 году в результате изобретения плавающего шнека.
В современном технологическом процессе литья под давлением плавающий шнек подает гранулы пластичного полимера из загрузочного бункера в обогреваемый цилиндр экструдера. По мере приближения к нагревателю гранулы плавятся и выталкиваются в полость формы, находящейся под давлением. После формования и остывания детали внутри формы она выталкивается, и форма используется повторно.
Небольшая пластиковая деталь, изготовленная с помощью формы для литья под давлением, полученной методом 3D-печати непосредственно из высокотемпературного полимера Formlabs High Temp Resin.
Полимеры, используемые для процессов литья под давлением, сравнительно дешевы и могут использоваться для достижения самых разнообразных свойств, поэтому литье под давлением широко применяется для создания упаковок и товаров массового потребления (любопытный факт: элементы LEGO, для которых важны как прочность, так и точность, изготавливаются литьем под давлением).
Благодаря доступным по цене настольным 3D-принтерам, термостойким материалам для 3D-печати и установкам для литья под давлением можно самим создавать формы для производства функциональных прототипов и небольших деталей из пластмасс. В случае малосерийного производства (примерно 10-100 деталей) созданные 3D-печатью формы для литья под давлением, в сравнении с дорогими металлическим формами, позволяют сэкономить время и деньги. Они также дают более гибкий подход к производству, позволяя инженерам и проектировщикам путем незначительных затрат времени и денег создавать прототипы литьевых форм и тестировать их конфигурации или легко изменять формы, продолжая работу над своими проектами.
Формы могут непосредственно печататься на 3D-принтере с использованием различных материалов, таких как стандартные или High Temp Resin Formlabs. Испытания для нашего технического доклада по литью под давлением проводились с использованием литьевой установки Galomb Model-B100 Injection Molder, стоимость которой составляет около 3500 долларов США.
Технический доклад
Загрузите наш технический доклад, чтобы получить пошаговое описание методов, использовавшихся для тестирования работоспособности напечатанных на 3D-принтере форм для литья под давлением, а также узнать о примерах передового опыта и рекомендациях при проектировании форм для 3D-печати.
Скачать технический доклад
Литье — популярная технология во многих отраслях, в частности, ювелирной промышленности, стоматологии и машиностроении. Оно может использоваться для изготовления как мелких, так и крупных деталей из самых различных металлов. Изобретенное свыше 5000 лет назад, литье позволяет работать с самыми разнообразными материалами и представляет собой один из самых простых способов изготовления деталей из металла.
При литье пустая форма создается по мастер-форме, которая может быть изготовлена вручную или напечатана на 3D-принтере (как это показано в видео-учебнике BJB Enterprises в разделе как изготовить силиконовую форму с помощью 3D-принтера Formlabs SLA). Мастер-форма погружается в материал литейной формы, например, песок, глину, бетон, эпоксидную смолу, гипс или силикон. Материал литейной формы затвердевает, пластик или металл заливается внутрь формы, и мастер-форма либо удаляется, либо сгорает, в результате чего образуется готовая деталь.
Можно напечатать точную мастер-форму для литья, используя. например, полимер Formlabs Castable Resin, который сгорает, образуя литейную форму многократного использования.
Технический доклад
Из этого технического доклада вы узнаете, как отливать ювелирные узоры по 3D-моделям, и как прямое литье по выплавляемым или по восковым моделям работает, как метод изготовления форм.
Скачать технический доклад
Отливки из вулканизированной резины могут использоваться для изготовления восковых моделей в количествах, необходимых для литья по выплавляемым моделям металлических деталей, таких как ювелирные изделия, мелкие детали промышленного назначения и игрушки.
3D-принтеры могут изготавливать мастер-модели, которые используются для формования отливок с вулканизацией при комнатной температуре (RTV) и даже отливок из жаростойкой вулканизированной резины.
Печатаемые непосредственно на 3D-принтере образцы ювелирных изделий могут использоваться для изготовления отливок из резины, вулканизируемой при комнатной температуре (RTV), или из природного каучука, вулканизируемого под действием высокой температуры.
При проектировании и производстве изготовление металлических отливок является наиболее экономичным и производительным технологическим процессом изготовления деталей с мелкими элементами и сложной геометрией. Производственники и проектировщики используют литье для изготовления критически важных деталей авиационной, автомобильной отрасли и здравоохранения.
Стереолитографические 3D-принтеры (SLA) идеально подходят для процессов литья при изготовлении металлических частей с меньшими затратами, большей гибкостью проектирования и за меньшее время, чем традиционные методы, без затрат, присущих 3D-принтерам прямой печати металлом.
Технический доклад
Из этого технического доклада вы узнаете, как можно использовать скорость и гибкость 3D-печати без затрат, характерных для принтеров прямого спекания металла, используя рабочие процессы литья металла, а также подробные пошаговые руководства по литью в песчаные формы; узнаете об инвестициях в процессы литья с использованием 3D-принтеров и полимеров Formlabs.
Скачать технический доклад
Два этих процесса: термоформования и вакуумного формирования похожи на литье под давлением тем, что используют нагрев и давление для создания готовых изделий из пластмассы. Эти методы были созданы в 40-е годы для производства безукоризненных фонарей кабин летательных аппаратов и рельефных армейских карт.
Сегодня их обычно используют для производства упаковки для автомобильных запчастей, где точность размеров может быть не столь критичной, а неравномерность толщины приемлема.
Упаковка для этой бритвы была сделана вакуумным формованием.
При термоформовании нагретый лист пластика сжимается между двух половинок формы для получения детали. При вакуумном формовании используется только одна половина формы, а для прижатия пластика к форме используется вакуум. Установки, используемые в этих технологических процессах, очень дешевы, их даже можно сделать своими руками.
На этой схеме А обозначает давление на обратной стороне формы, В – давление со стороны пластика, накладываемого на форму, и С обозначает тепло самого пластика.
Печать формы для термоформования на 3D-принтере SLA — быстрый и эффективный метод создания высококачественных вакуум-формованных деталей для мелкосерийного производства. Напечатанные формы для термоформания можно использовать для изготовления прототипов упаковки, прозрачных ортодонтических ретейнеров и безопасных для пищевых продуктов форм для шоколадных кондитерских изделий.
При моделировании деталей для изготовления пресс-форм, необходимо учитывать такие факторы, как давление, отвод газов, различия в охлаждении и нагреве.
Посмотрите наш вебинар , чтобы изучить различные технологии изготовления пресс-форм и узнать, как изготавливать формы для литья под давлением, формы для термоформования и литьевые формы.
Вебинар Formlabs: Изготовление пресс-форм с помощью 3D-печати (доступен только на английском языке)
Как сделать пресс-форму: руководство по изготовлению пресс-форм для профессионалов
07.06.2022
Появление форм в бронзовом веке позволило усовершенствовать грубые производственные процессы, применявшиеся нашими предками. С тех пор технологии изготовления пресс-форм находятся на подъеме, поскольку производители, использующие передовые технологии производства, такие как литье под давлением, термоформование или литье, продолжают полагаться на пресс-формы для создания большинства пластиковых, силиконовых, резиновых, композитных и металлических деталей.
Профессиональные производители, а также любители, заинтересованные в использовании преимуществ этих процессов, должны понимать, как происходит процесс изготовления пресс-форм, как они используются и как оптимизировать их использование для удовлетворения заданных требований к производительности.
Что такое пресс-формы и для чего они используются?
Различные производственные процессы включают в себя придание формы податливым сырьевым материалам с помощью разработанного, фиксированного инструмента, конструкции или каркаса, известного как пресс-форма. С точки зрения структуры, формы представляют собой полые контейнеры (негативная форма) или шаблоны форм (позитивная форма), разработанные в соответствии с окончательным дизайном, который планирует создать производитель.
Пресс-формы имеют решающее значение для этих производственных процессов, и их основная задача – воспроизведение единообразных копий заданного дизайна. При изготовлении пресс-форм используются такие материалы, как металлы, пластмассы, керамика, дерево, пенопласт и другие. После проектирования и разработки с использованием инструментов для изготовления пресс-форм, форму устанавливают в формовочное оборудование и заливают в нее или формируют вокруг нее сырье, например, термопласты. После застывания форма отпечатывает свой рисунок на материале, формируя готовое изделие.
Пресс-форма для термоформования пластиковой упаковки и конечная деталь.
Итак, что можно изготовить с помощью пресс-форм? Практически все – от прототипов до сложных деталей конечного использования. Методы формовки используются в производстве для создания автомобильных деталей, потребительских товаров, упаковки, ювелирных изделий, медицинских приборов и многого другого – на самом деле, трудно найти функциональные продукты, в которых не было бы ни одного компонента, изготовленного с помощью методов формовки.
Производственные процессы, в которых используются пресс-формы
Изготовление пресс-форм имеет решающее значение для различных производственных процессов; пресс-форма служит в качестве чертежа, на основе которого происходит тиражирование многих изделий массового производства. Производственные процессы, в которых используются пресс-формы, включают:
- Литье предполагает заполнение формы расплавленным металлом или другим жидким материалом. Расплавленный материал остывает и затвердевает в форме, образуя желаемое изделие. Литье обычно используется для производства металлических изделий, а также силиконовых и пластиковых деталей.
- Компрессионное формование — это производственный процесс, в котором отмеренное количество формовочного материала, обычно предварительно нагретого, сжимается в требуемую форму с помощью двух нагретых форм. Компрессионное формование обычно считается альтернативой литью под давлением для относительно простых конструкций для низких и средних серий производства деталей.
- Выдувное формование — это технология, похожая на выдувание стекла. Выдувная машина нагнетает воздух в нагретую трубкоподобную деталь, обычно из пластика или стекла, которая зажимается в пресс-форме. Когда воздух вдувается в форму, давление выталкивает пластик наружу, придавая ему форму формы. Выдувное формование обычно используется для производства полых изделий, таких как бутылки.
- Ламинирование композитов включает в себя сборку композитных материалов на пресс-форме и применение таких методов, как мокрая укладка, ламинирование препрега или литье с переносом смолы для формирования готовых композитных деталей из высокоэффективных материалов, включая углеродное волокно, стекловолокно и кевлар.
Типы пресс-форм
Существует множество типов пресс-форм, которые могут использоваться в качестве оснастки для производственных процессов, описанных выше. Например, в алюминиевом литье существует около семи типов форм, включая формы для литья в песчаные формы, керамические формы и оболочковые формы. Таким образом, для упрощения классификации различных типов пресс-форм применяется следующая классификация:
- Однокомпонентные формы относятся к простейшим типам форм с однородной поверхностью всех частей объекта, подлежащего формовке. Конструкции пресс-форм или объекты с одной плоской поверхностью также могут быть воспроизведены с помощью однокомпонентных или цельных пресс-форм. Хотя однокомпонентные пресс-формы могут быть изготовлены на основе моделей CAD, эти пресс-формы обычно разрабатываются на основе физической мастер-модели.
- Двухкомпонентные пресс-формы обеспечивают возможность изготовления пресс-форм для более сложных конструкций. Двухкомпонентная пресс-форма определяется как пресс-форма с двумя отдельными частями, соединенными вместе на линии разъема для производства конечного продукта. Каждая изготовленная деталь отражает различные особенности обеих частей дизайна модели или мастер-модели. Изготовление двухкомпонентной пресс-формы также обычно включает в себя разработку обеих частей пресс-формы на основе мастер-модели или модели CAD.
- Многокомпонентные пресс-формы идеально подходят для проектирования пресс-форм с более сложной геометрией, требующей иного подхода по сравнению с процессом разработки одно- или двухкомпонентных пресс-форм. Многокомпонентные формы учитывают различные аспекты или особенности модели. Таким образом, готовая пресс-форма будет состоять из нескольких частей, воссоздающих различные особенности модели.
- Многогнездные пресс-формы имеют несколько полостей, имеющих форму одной и той же детали, что позволяет изготавливать несколько деталей за производственный цикл, повышая тем самым производительность.
Цельная силиконовая форма, которую можно использовать для конструкций с плоской стороной и без глубоких подрезов. (рис.1)
Для более сложных конструкций, таких как этот колпачок с резьбой и подрезами, часто требуются формы из нескольких частей, со вставками или сердечниками бокового действия. (рис.2)
Другой важнейшей характеристикой, помогающей классифицировать различные типы пресс-форм, является коэффициент многократного использования разработанной пресс-формы. Коэффициент многократного использования относится к тому, сколько раз производитель намеревается использовать пресс-форму. В соответствии с этой классификацией различают следующие типы пресс-форм:
- Формы одноразового использования или жертвенные формы: В этих формах воспроизводится один объект, и после использования форма разрушается в процессе распалубки. Формы для одноразового использования обычно изготавливаются из песка, глины, силикона, воска или пластмассы.
- Многоразовые или постоянные пресс-формы: как следует из названия, эти формы можно использовать повторно в течение нескольких циклов, от небольших до крупных серий. При небольших объемах (иногда называемых мягкими формами) многоразовые формы могут быть изготовлены из силикона, пены, дерева, пластмассы или более мягких металлов, таких как алюминий.
При больших объемах, требующих более прочных форм, не изнашивающихся (часто называемых твердыми формами), формы чаще всего изготавливаются из твердых металлов, таких как сталь.
Одноразовые формы разрушаются в процессе распалубки (рис. 1)
Многоразовые формы можно использовать повторно в течение нескольких циклов (рис. 2)
Как выбрать технологию изготовления формы?
Какая технология изготовления пресс-форм лучше всего подходит для конкретной задачи? Это зависит от нескольких важных факторов, включая желаемый материал конечной детали, предполагаемый производственный процесс, геометрию модели и объем производства.
Ниже поэтапно рассматривается упрощенный, пошаговый подход к выбору наилучшей технологии для вашего производственного проекта:
- Определите критерии разработки вашего проекта
Генеральный план производства может помочь создать четкие детали того, что ожидается от проекта, сроки его разработки и доступный бюджет. Планируете ли вы создавать детали на заказ или серийно производить тысячи одинаковых изделий, определит, какие варианты выбрать на следующих этапах. Критерии разработки могут меняться в зависимости от проекта, но обычно они включают в себя дизайн детали, размер, материал, качество, требуемые допуски, сроки, требуемый объем производства, ограничения по стоимости и т.д.
При разработке продукции исходным документом, который отвечает на многие из этих вопросов, часто является документ о требованиях к продукции (PRD), а спецификация материалов (BOM) – это полный перечень деталей, элементов, узлов и других материалов, необходимых для создания продукции.
- Выбор производственного процесса
Выбор правильного производственного процесса для определенной детали в значительной степени зависит от критериев разработки. В некоторых случаях для создания любой конструкции может использоваться несколько производственных процессов. Как правило, выбирают тот процесс, который может произвести данную деталь с требуемым качеством, при наименьших затратах и при соблюдении остальных критериев разработки. Выбор материала и объем производства, вероятно, являются наиболее важными факторами, определяющими ваше решение.
- Выбор технологии изготовления пресс-формы
Как только вы остановились на правильном производственном процессе, тип пресс-формы для него также в значительной степени определяется критериями разработки. Хотя точные факторы зависят от производственного процесса, вот некоторые из наиболее важных соображений при выборе технологии изготовления пресс-формы:
- Конструкция детали: Постарайтесь максимально упростить конструкцию и согласовать ее с правилами проектирования данного производственного процесса, чтобы иметь возможность выбрать метод, позволяющий достичь наименьших затрат. Для простых конструкций могут потребоваться только формы, которые можно создать с помощью ручных методов, в то время как для сложных конструкций часто требуются формы из нескольких частей и цифровые производственные инструменты, такие как 3D-принтеры или обработка на станках с ЧПУ.
- Объем производства: для крупносерийного производства требуются прочные пресс-формы, которые могут точно копировать модели и не изнашиваться после нескольких использований. Однако изготовление таких инструментов сопряжено с высокими затратами и временем изготовления. Для разовых деталей и партий меньшего объема, возможно, эффективнее выбрать более дешевые формы, которые могут быть созданы быстрее, например, жертвенные формы или мягкие формы, которые можно выбросить, когда они начнут проявлять признаки непоправимого износа.
- Качество: более жесткие допуски требуют более точных форм и инструментов для создания, например, цифровых производственных инструментов, и должны быть более прочными, чтобы обеспечить стабильное качество деталей в течение нескольких циклов.
- Сроки: Изготовление сложных металлических форм часто занимает месяцы через поставщика услуг. Если вы работаете в более сжатые сроки, постарайтесь найти альтернативы, которые могут сократить время изготовления, например, 3D-печатная оснастка.
- Материал: Материалы с более высокой температурой плавления или более абразивные требуют более прочных пресс-форм, способных создавать необходимый объем деталей без разрушения.
Как изготовить пресс-форму для различных производственных процессов
В этом разделе представлен краткий обзор технологий изготовления пресс-форм для различных производственных процессов. Перейдите по нашим ссылкам, чтобы получить подробные руководства и пошаговый рабочий процесс для каждого процесса.
Существует два основных метода изготовления пресс-форм – прямой и непрямой. Косвенный метод изготовления пресс-форм предполагает разработку пресс-форм на основе физической мастер-модели, или шаблона. Прямой процесс предполагает разработку пресс-формы непосредственно на основе (цифрового) дизайна, чаще всего с использованием цифровых производственных процессов.
Силиконовые формы для литья
Литье в силиконовые формы – один из самых популярных процессов, в котором используются формы. Разработчики продуктов, инженеры, создатели DIY и даже повара – все они используют силиконовые формы для создания единичных или небольших партий деталей из пластика и других материалов. Силикон является отличным выбором для изготовления форм, поскольку с его помощью можно легко создавать индивидуальные конструкции, а сами формы достаточно прочны, поэтому их можно использовать многократно, не опасаясь поломки.
В зависимости от вашей конструкции вам может понадобиться пресс-форма из одной или двух частей. Процессы изготовления этих форм похожи, но для создания двухкомпонентной формы потребуется немного больше времени. Используйте пошаговую инструкцию в видео или наше практическое руководство по изготовлению силиконовых форм, чтобы создать свои собственные формы.
Пресс-формы для литья под давлением
Пресс-формы для литья под давлением традиционно изготавливаются из металла путем обработки на станках с ЧПУ или электроэрозионной обработки (EDM). Это дорогостоящие промышленные методы, требующие специализированного оборудования, высококлассного программного обеспечения и квалифицированной рабочей силы. В результате производство металлической пресс-формы обычно занимает от четырех до восьми недель и стоит от $2 000 до $100 000+ в зависимости от формы и сложности детали.
Однако существуют альтернативы обработке пресс-форм из металла. Использование собственной 3D-печати для изготовления литьевых форм для прототипирования и малосерийного производства значительно сокращает затраты и время по сравнению с металлическими формами, при этом обеспечивая производство высококачественных и повторяемых деталей.
Формы для термоформования
Формы, необходимые для процесса термоформования, могут быть разработаны с использованием различных производственных процессов, включая ручную лепку из дерева, обработку на станках с ЧПУ пластика, конструкционной пены, стекловолокна, инженерных композитов или металлов, 3D-печать полимеров, литье гипса или металла.
Многие предприятия обращаются к стереолитографии (SLA) 3D-печати для создания форм для процессов термоформования, поскольку она обеспечивает быстрое время выполнения заказа при низкой цене, особенно для коротких тиражей, нестандартных деталей и прототипов. 3D-печать также предлагает непревзойденную свободу проектирования для создания сложных и замысловатых форм.
Компрессионное формование
В зависимости от материала или заряда, который вы будете подвергать компрессионному формованию, у вас есть несколько вариантов создания форм, включая литье под давлением, обработку с ЧПУ или 3D-печать. Главное, чтобы ваши формы были способны выдержать процесс компрессионного формования, поэтому если вы используете нагрев, вам необходимо создать формы, способные выдерживать резкие изменения температуры. Формы также должны быть способны выдерживать давление, оказываемое при сжатии.
3D-печать – это быстрый и дешевый метод создания форм для компрессионного формования.
Формы для литья металлов
Хотя все методы литья металлов имеют одну и ту же основу, существуют различные методы, лучше подходящие для разных областей применения. Некоторые из наиболее распространенных методов включают литье под давлением, литье по выплавляемым моделям и литье в песчаные формы.
Форма для литья в песчаные формы.
Как шаблоны для косвенного изготовления форм, так и формы для непосредственного литья металлических деталей могут быть изготовлены несколькими методами. Подробнее о каждом из этих процессов читайте в нашем руководстве по литью металлов.
Начните работу с 3D-печатными формами
Сочетание традиционных производственных технологий, таких как литье под давлением, термоформование или литье силикона, с 3D-печатью форм позволяет быстрее выводить продукцию на рынок с более экономичным по времени и затратам производственным процессом. Настольная 3D-печать предлагает предприятиям универсальный, экономически эффективный подход к разработке мастер-моделей и пресс-форм для прямого и непрямого процессов изготовления форм, полностью в домашних условиях.
Предыдущая статья 3D-печать металлом – Ultimaker Metal Expansion Kit Следующая статья Обзор 3D-принтеров Creality: Ender 3, Ender 3 Pro и Ender 3 v2Учебное пособие по изготовлению форм: силиконовая форма для глиняной скульптуры
Джон Кэннон из The Whimsical
Гарденс привез свою глиняную скульптуру в наш центр, чтобы сделать слепок фигуры, а затем
воспроизвести его в пластике на машине ротационного литья. Подробная скульптура изображена ниже с разных
углы.
В этой статье подробно описаны шаги, которые мы предприняли на протяжении всего процесса изготовления и литья форм:
Шаг 1: Выбор метода изготовления формы и формы
Резина
Шаг 2: Сборка формы и подготовка
Скульптура
Шаг 3: Измерить, смешать и залить силиконовую форму
Резина
Шаг 4: Извлечение формы
Шаг 5: Вырезать форму
Шаг
6: Вращательное литье
Шаг 1. Выберите метод изготовления формы и резиновую форму
Метод изготовления формы
Для этой скульптуры мы выбрали метод «литой блочной формы».
Вот причины, по которым мы отказываемся от других методов:
Нанесение кистью: Мы обеспокоены тем, что в сложных деталях на основе
скульптура. Кроме того, формы, наносимые кистью, как правило, имеют толстые и тонкие места — тонкие места в конечном итоге становятся слабыми местами.
плесень.
Форма для литого одеяла: Одним из этапов процесса изготовления литого одеяла является формирование слоя глины сверху. оригинальной модели ( ознакомьтесь с учебным пособием по литой форме для одеяла здесь ). Этот шаг, скорее всего, деформирует глиняный оригинал.
Основываясь на форме скульптуры, мы также знаем, что форму потребуется разрезать, чтобы удалить оригинальная скульптура и последующие отливки.
Формовочная резина
Для этого конкретного проекта мы также знаем, что хотим использовать силиконовую формовочную резину, поскольку она не требует
разделительный состав при заливке полиуретановой смолы. Разделительный состав может быть трудно наносить на сложные участки.
и его может быть трудно удалить из литья. Остаточный разделительный состав может предотвратить прилипание краски к
отливки.
Силиконовые каучуки, отвержденные платиной, и силиконовые каучуки, отвержденные оловом
Силиконы Polytek делятся на две основные категории: отвержденные платиной и отвержденные оловом. Основные сравнения между двумя варианты указаны в таблице ниже:
Тип резины | Преимущества | Недостатки | Литейные материалы | Методы |
Силиконовые формовочные каучуки, отвержденные платиной | Отсутствие усадки при отверждении, отвержденная резина имеет длительный срок хранения | Жидкая резина может страдать от ингибирования отверждения некоторыми материалами (например, серой
глина, оловянные силиконы, бондо, некоторые виды пластика, напечатанные на 3D-принтере, латексная резина).![]() | Большинство материалов, особенно смолы, пены и некоторые легкоплавкие металлы. | Заливка, кисть, распыление. |
Силиконовые формовочные каучуки, отвержденные оловом | Не ингибирует отверждение, немного дешевле, чем системы с платиновым отверждением | Усадка при отверждении (~1%), более короткий срок службы библиотеки (2-5 лет), чем у систем с платиновым отверждением. | Большинство материалов, особенно смолы, пены и некоторые легкоплавкие металлы. Может ингибировать полиуретан резина, отвержденный платиной силикон и отливки из полиоптической смолы серии 14. | Заливка, кисть, распыление. |
Силиконовые каучуки, отвержденные платиной, имеют преимущества по сравнению с силиконовыми каучуками, отвержденными оловом (например, отсутствие усадки при отверждении,
более длительный срок службы библиотеки), но может страдать от ингибирования отверждения при воздействии определенных материалов. Сера, для
например, является известным ингибитором и присутствует в некоторых глинах для лепки.
Мы не уверены, содержит ли скульптура Джона серу, поэтому проводим небольшое тестовое лечение.
Для теста мы смешиваем и выливаем в глину быстротвердеющий платиновый силиконовый каучук (PlatSil ® 71-10). Зона сдерживания против небольшой секции на задней стороне скульптуры.
Через 30 минут мы удаляем силиконовый каучук, чтобы определить, правильно ли он затвердел. Мы находим, что резина, которая касалась скульптуры, оставалась липкой, в то время как стороны резины подвергались воздействию воздуха и глина застыла правильно. Это указывает на наличие загрязнения внутри или на глине, которое может предотвратить любой силиконовый каучук, отвержденный платиной, отвержден должным образом.
Основываясь на этих выводах, мы выбрали силиконовый каучук, отвержденный оловом, в качестве материала формы: TinSil ® 80-15 Силикон. Резина. Мы выбираем мягкий силикон (Шор A15) из-за глубоких подрезов на
скульптура. Более твердую резину может быть труднее снять без повреждений.
TinSil 80-15 Силикон Резина: Технические характеристики Твердость: по Шору A15 Смесь Соотношение: 1A:10B Время заливки: 30 минут Смешанная вязкость: 12 000 сП Время извлечения из формы: 24 часа Затвердевший цвет: Персиковый Удельный объем: 25,3 дюйм³/фунт
Шаг 2: Изготовление формы и подготовка скульптуры во всех направлениях), а затем загерметизировали вазелином.

ПРИМЕЧАНИЕ. Рекомендуется сузить внутреннюю часть коробки формы, чтобы форму можно было легче удалить, если перевернуть коробку пресс-формы вверх дном.
Затем на глиняную скульптуру наносится антиадгезив
Pol-Ease ® 2500.
ПРИМЕЧАНИЕ: Используйте Pol-Ease ® 2300 при изготовлении формы из полиуретановой резины.
Коробка для формы помещается вокруг подготовленной скульптуры, чтобы убедиться, что размеры подходят.
Количество каучука, необходимого для пресс-формы, оценивается следующим образом:
Объем коробки для пресс -формы = ~ 1716 в 3
Объем скульптуры = ~ 84,78 в 3
Том коробки для плесени – объем скульптуры: 1 716in 3 – 84,78 в 3 = 1,63131131 – 84,78 в 3 = 1,63131 – 84,78 в 3 = 1,6131 3131 – 84,78 в 3 = 1,63131 – 84,78 в 3 = 1,63131 – 84,78 в 3 = 1,6130 3 – 84,78 в . в 3
1 631,22 в 3 ÷ 23,7 в 3 /фунт (удельный объем TinSil 80-15) = 68,8 фунта силиконовой резины TinSil 80-15
68,8 фунта — это большое количество каучука, и мы понимаем, что есть возможность уменьшить
это количество, добавив угловые вставки и другие блоки.
Мы добавляем несколько блок-аутов, но сохраняем расстояние не менее 1 дюйма между скульптурой и формой.
стены коробки/блокауты.
После закрепления всех блоков форму снимают, чтобы запечатать новую фанеру.
дополнить вазелином и зачеканить все края подогретым пластилином
глина. Заделка краев помогает предотвратить утечку, когда жидкий силикон заливают в форму.
коробка позже.
Скульптура помещается обратно в форму, а затем форма закрепляется
винты.
Шаг 3. Отмерьте, перемешайте и залейте силиконовую резину для формования Резина нужна для изготовления формы.
Как упоминалось ранее, TinSil 80-15 имеет соотношение компонентов 1A:10B. Компоненты измеряются по весу, а затем тщательно перемешивается.
ПРИМЕЧАНИЕ: Не пытайтесь измерять продукты с соотношением компонентов 1A:10B по объему – всегда измеряйте масса.
Из-за большого количества каучука, необходимого для этого проекта, мы смешиваем две отдельные партии с помощью турбонагнетателя.
Смеситель.
Каучук перемешивают до достижения однородного цвета.
ПРИМЕЧАНИЕ: Старайтесь не ударять турбомиксером стенки емкости для смешивания, так как это может привести к попаданию воздуха в смесь.
Затем партии перемешиваются вручную с помощью поли-лопасти.
ПРИМЕЧАНИЕ. Это
важно несколько раз соскрести стенки и дно емкости для смешивания, так как именно там
материал имеет свойство цепляться.
Силикон заливают в самую нижнюю точку формы и дают ему подняться.
Резина заливается до тех пор, пока она не достигнет высоты не менее 1,0 дюйма над самой высокой точкой скульптуры.
Мы оставляем резину сохнуть при комнатной температуре на ~24 часа. Тепловые лампы могут помочь ускорить
излечивать.
ПРИМЕЧАНИЕ. Время извлечения из формы зависит от продукта. Ознакомьтесь с техническими бюллетенями продукта для
эта информация.
Шаг 4. Извлечение формы
Перед извлечением из формы места расположения стенок и заглушек опоки отмечают ручкой. Это сделано для того, чтобы
Коробка формы может быть правильно собрана для последующего литья.
Все края формы отделяют от плинтуса шпателем до
плесень удаляется.
После снятия формы с плинтуса скульптура разделяется пополам, оставляя верх
половина в форме.
Шаг 5: Разрежьте форму
Чтобы удалить остатки скульптуры и последующие отливки, мы готовимся сделать разрез на одной стороне формы. Фотографии скульптуры распечатываются, чтобы определить хорошее место для разреза.
ПРИМЕЧАНИЕ: Если возможно, лучше всего резать по линии, которая уже существует на скульптуре или в незаметное место (т.е. избегать лица).
Для разреза используется скальпель.
ПРИМЕЧАНИЕ. Важно
для создания неправильной формы разреза (т. е. шпунт-паз или зигзагообразный разрез), чтобы две стороны совпадали
лунка для литья ( для получения общей информации о резке резиновых форм см. статью ).
Остаток скульптуры удаляется из формы, а глина остается в форме.
очищается.
Шаг 6. Вращательное литье
Форма помещается обратно в коробку формы и затем закрепляется.
Поскольку мы планируем использовать машину ротационного литья, мы делаем крышку опоки с заливным отверстием.
В это отверстие заливают быстротвердеющую смолу, когда опока находится на машине ротационного литья.
По бокам коробки добавлены деревянные бруски, чтобы установить и прикрепить ее к вращающемуся
литейная машина.
Силиконовая заглушка позже будет использоваться для закрытия отверстия при заливке.
Короб формы загружается на машину ротационного литья и закрепляется С-образными зажимами.
EasyFlo 120 Liquid Plastic — это продукт, который мы
чаще всего рекомендуют для вращательного или слаш-заброса. Он предназначен для постепенного затвердевания.
рабочего времени, в отличие от «защелкивания» (подобно характеристикам отверждения EasyFlo 60, еще одного продукта с
серии ИзиФло). Это постепенное сгущение в течение последних 30-45 секунд рабочего времени помогает обеспечить
ровное пальто.
EasyFlo 120 Жидкость Пластик: Технические характеристики
Твердость: Shore D65
Смесь Соотношение: 1A:1B по объем, 100A:90B по весу
Время застывания: 2-2,5 минуты
Смешанный Вязкость: 120 сП
Время извлечения из формы: 15-30 минут
Цвет отверждения: Белый
Удельный объем: 26,9 дюйм³/фунт
Приблизительно 2 фунта EasyFlo 120 тщательно перемешивают и заливают в форму.
ПРИМЕЧАНИЕ: В идеале эту смолу следует смешивать и заливать менее чем за минуту.
Отверстие для заливки закрывается силиконовой заглушкой, после чего машина включается.
Через ~30 минут форму извлекают из машины для ротационного литья, а затем заливку
удаляется из формы.
Для следующего цикла мы смешиваем EasyFlo 120 + коричневый краситель PolyColor + бронзовый порошок для получения холодного литья.
бронзовая копия.
Вот несколько фотографий детали из бронзы холодного литья перед полировкой стальной ватой (стальная шерсть
используется для воздействия бронзового порошка на поверхность отливки). Изначально на отливках появится шоколад
коричневый; вы заметите маленькое пятно на его щеке, которое было отполировано.
Как сделать силиконовые формы для смолы – пошаговое руководство
Этот пост может содержать партнерские ссылки. Мы можем получать небольшую комиссию от покупок, сделанных через них, без каких-либо дополнительных затрат для вас.
Для изготовления красивых отливок или украшений из эпоксидной смолы необходимо использовать хорошую негативную форму. Они доступны в многочисленных проектах, чтобы купить. Если же вы хотите отважиться на особенные, индивидуальные формы или просто хотите что-то построить сами, то силиконовую форму можно сделать без особых усилий. В этой статье мы покажем вам, как сделать силиконовые формы для смолы своими руками.
Содержание
- 1 Работа с эпоксидной смолой
- 2 Какая эпоксидная смола лучше всего подходит для силиконовых форм?
- 3 Почему силиконовые формы являются лучшим выбором для литья смолы?
- 4 Наиболее важный фактор для форм из смолы: степень твердости
- 5 Как сделать силиконовые формы с помощью шаблона
- 6 Как сделать силиконовые формы без шаблона
- 7 Как сделать формы из смолы – некоторые соображения перед началом работы
- 8 Материалы, необходимые для изготовления силиконовых форм для смолы
- 8.
1 Лучшие наборы для изготовления силиконовых форм Рекомендации
- 8.2 Другие материалы, необходимые для изготовления собственных форм для смолы
- 8.
- 9 Как сделать силиконовые формы для смолы – шаг by Step Tutorial
- 9.1 Изготовление рамки
- 9.2 Смешивание силикона
- 9.3 Заливка силикона
- 9.4 Извлечение готовой формы для литья силикона
- 10 Изготовление двухкомпонентных форм из смолы и силикона
- 11 Силиконовые формы с выемками
- 12 Силиконовые формы для смолы – ценные советы и рекомендации
- 13 Как чистить формы – Учебное пособие
- 14 Как предотвратить проблемы с силиконовыми формами 906 903 906 903 15 Рекомендации по изготовлению силиконовых форм для самостоятельного изготовления
Работа с эпоксидной смолой
Для работы с эпоксидной смолой основными требованиями являются смола и соответствующий отвердитель . В зависимости от того, какому проекту вы хотите посвятить себя, будут добавлены другие материалы, такие как различные цветовые пигменты. Часто также необходимы полированные силиконовые формы. Практически нет ограничений для творчества, когда дело доходит до формовки: кубики, шары, пирамиды, звезды, сердца, цветы, подставки и всевозможные фигуры. Все возможно и может быть заполнено эпоксидной смолой для создания красивых произведений искусства или подарков.
В выбранной вами форме вы даете готовую смесь эпоксидной смолы . Либо мы используем смесь кристально чистой, либо окрашиваем жидкими красками или пигментами. Затем вы можете добавить различные элементы, такие как блестки, камни, ракушки, цветы и т. д., если хотите. После затвердевания осторожно извлеките готовую работу из формы.
Какая эпоксидная смола лучше всего подходит для силиконовых форм?
При работе с эпоксидной смолой основными требованиями являются смола и соответствующий отвердитель. В зависимости от того, какому проекту вы хотите посвятить себя, могут быть добавлены другие материалы, такие как различные цветовые пигменты. Полированные силиконовые формы также часто необходимы, чтобы придать готовому изделию более глянцевый вид.
Креативность практически безгранична, когда дело доходит до формовки: кубиков, шаров, пирамид, звезд, сердечек, цветов, подставок и всевозможных фигурок. Все возможно и может быть заполнено эпоксидной смолой для создания красивых произведений искусства или подарков.
Вам потребуется литьевая смола с более низкой вязкостью, так как эта смола имеет жидкую консистенцию, что позволяет ей с большим эффектом заполнять все виды форм. Эта смола была разработана специально для заливки в гипс и может быть залита слоями толщиной до 2 дюймов.
Эта смола станет кристально чистой, если не будет добавлен краситель. Эта конкретная смола особенно совместима с пигментированными порошками слюды. Вы можете смешать жидкую смолу и отвердитель в соотношении 2:1.
INCREDIBLE SOLUTIONS Deep Pour Clear Casting Resin
- Индивидуальная формула создает минимальное количество пузырьков и предотвращает появление кратеров
- Эпоксидная смола при правильном использовании и отверждении безопасна со слабым запахом
- Хорошо смешивается со слюдяными пигментными порошками и обеспечивает кристальную чистоту
Посмотреть на Amazon
В то время как большинство смол предлагают только короткий период времени, в течение которого с ними можно работать, у вас будет значительно больше рабочего времени, прежде чем эта смола начнет затвердевать. Это связано с его низкой экзотермической скоростью, что означает, что он выделяет меньше тепла при отверждении. Однако качество густой заливки этой смолы означает, что для отверждения может потребоваться от 36 до 48 часов.
Эпоксидная смола имеет тенденцию становиться желтой при воздействии солнечного света в результате вредных ультрафиолетовых лучей солнца. Эта смола была изготовлена с дополнительными ингибиторами УФ-излучения, чтобы противостоять воздействию УФ-излучения и предотвратить пожелтение. Этот продукт также водостойкий, почти не имеет запаха и не выделяет летучих органических соединений.
Pros
- Blemish- and water-resistant
- UV-resistant
- Low odor and zero VOCs
- Longer working time
- Very little shrinkage
Минусы
- Медленное отверждение
Благодаря тому, что он действует как антиадгезив, силикон идеально подходит в качестве материала для литейных форм . Готовые изделия из смолы можно легко извлечь из формы после отверждения благодаря гибкости силикона.
Еще одним преимуществом является то, что силикон считается нетоксичным. Тот факт, что он используется в качестве обычного материала при производстве форм для выпечки или даже пустышек, доказывает, что этот материал совершенно безвреден. Кроме того, на сегодняшний день практически не известно об аллергии на силикон.
На рынке уже представлен очень большой выбор готовых силиконовых форм. Особенно новички в этой технике могут прибегнуть к формам для выпечки из силикона или полированным силиконовым формам, сделанным специально для работы со смолой.
Если вас интересуют готовые силиконовые формы для литья эпоксидной смолы, вот наши рекомендации:
Форма для подставок LET’S RESIN Coaster для смолы
- Включает формы сердца, круглые, эллиптические, прямоугольные и квадратные формы
- Мягкий и гибкий силикон высшего качества с высокой прочностью на разрыв
- Очень гладкая внутренняя поверхность с антипригарным покрытием для получения стеклоподобного покрытия и легкого извлечения из формы
Посмотреть на Amazon
Формы для литья силиконовой смолы EU TENG HAO, 18 шт.
- Всего в упаковке 18 предметов
- Включает 1 сферу, 1 куб, 1 ромб, 1 треугольную пирамиду, 2 мерных стакана, 2 разные формы для хрусталя, 10 деревянных палочек
- Очень гибкий, легко чистится и может использоваться повторно, не легко повреждается
Посмотреть на Amazon
Литейные формы для ювелирных изделий из смолы LET’S RESIN
- Стартовый набор высококачественных силиконовых форм для ювелирных изделий
- Формы для браслетов, ожерелий, сережек, подвесок и колец
- Подходит для литья и УФ-смолы, но не для покрытия смола
Посмотреть на Amazon
Однако недостатком многих из этих силиконовых форм (особенно форм для выпечки) является то, что нагрузка на материал чрезвычайно велика при работе с эпоксидной смолой . Первые признаки износа, т.е. матовая поверхность, быстро видны. В результате становится все труднее удалять смолу из формы. Кроме того, как уже упоминалось, доступно множество пресс-форм. Тем не менее, они, конечно, предопределены и могут ограничивать ваше собственное творчество. Решение: Вы можете легко сделать свою собственную силиконовую форму!
Наиболее важный фактор для форм из смолы: степень твердости
Основным материалом для производства силиконовых форм является силиконовый каучук. Вы можете получить его у местного дилера. Силиконовый каучук представляет собой мягкую массу, которая очень быстро затвердевает и становится чрезвычайно эластичной. Тем не менее, силикон не является бесконечно гибким: I Если материал чрезмерно растянут, он может легко сломаться или треснуть . Степень твердости определяет хрупкость материала.
Силиконовый каучук доступен с различной степенью твердости. Степень твердости силикона указывается в единицах Шора. Эмпирическое правило здесь таково: чем ниже значение Шора, тем выше эластичность.
- Шор от 0 до 20 : Мягкий материал с очень высокой гибкостью.
Однако этот материал также относительно нестабилен.
- Твердость по Шору от 20 до 40 : Довольно стабильный материал со средней эластичностью.
- Твердость по Шору от 40 до 80 : Материал достаточно твердый и малоэластичный. Он очень стабилен в размерах, но также слегка хрупок.
Степень твердости, которую вы должны выбрать для своего проекта, зависит от того, для чего вы хотите использовать силикон. Вам также может быть легче работать с одной степенью твердости, чем с другой. Вы можете только попробовать это.
Преимущество мягкого силикона в том, что готовую работу можно легко извлечь из формы после того, как он затвердеет . Однако форма также очень неустойчива при низкой степени твердости и относительно быстро деформируется. В этом отношении с силиконовыми формами с более высоким значением Шора, конечно, сложнее обращаться, так как отливку не так просто удалить. Кроме того, необходимо следить за тем, чтобы они не сломались и не порвались во время выпуска. Однако при осторожном обращении их можно использовать очень часто из-за их высокой размерной стабильности. Потому что они практически совсем не деформируются.
Помимо степени твердости, при выборе также играет роль вязкость силикона. В зависимости от проекта вы можете выбрать толстый или тонкий силиконовый каучук.
Если вы хотите изготовить формы для шоколада или выпечки из силикона, вы должны убедиться, что используемый материал является безопасным для пищевых продуктов и термостойким. Должна быть указана термостойкость до 200°С.
Если вы хотите работать с эпоксидной смолой, бетоном или другими химическими литейными материалами, вы должны сначала убедиться, что используемый вами силикон устойчив к химическим веществам.
Если вы не уверены, соответствует ли ваш силикон вашим требованиям, прочтите спецификацию производителя или обратитесь за консультацией к своему дилеру.
Если вы хотите сделать свои собственные силиконовые формы, вы можете выбрать один из двух вариантов: негативная форма с оригинальной формой или негативная форма без оригинальной формы. Мы хотели бы объяснить различия между этими двумя вариантами более подробно ниже.
Как сделать силиконовые формы
с ШаблонНегативная форма с оригинальной формой идеально подходит для изготовления копии . Для такого проекта вам понадобится рамка. Это гарантирует, что силикон не растечется бесконтрольно после заливки. Если вы хотите построить каркас самостоятельно, ориентируйтесь на размеры объекта, который хотите воспроизвести. Так как силикон довольно дорог, эта процедура имеет смысл, чтобы не расходовать излишне много материала. Ваша самодельная рама должна быть абсолютно герметичной. Это единственный способ гарантировать, что силикон не вытечет в возможные трещины или под края во время заливки. Вместо рамки вы также можете использовать пустую пластиковую упаковку для заливки смолы .
Теперь можно поместить заготовку в рамку и подготовить силикон. Как всегда, вы должны тщательно следовать инструкциям производителя. Затем равномерно распределите смесь по раме и дайте ей затвердеть. После этого форму можно просто снять с рамы.
Как сделать силиконовые формы
без шаблонаЧтобы сделать силикон пригодным для этого типа обработки, вылейте смесь в миску, содержащую смесь воды и моющего средства. Затем обложите подготовленную заготовку уже гибким силиконом. Убедитесь, что вы используете достаточную массу. Если вы слишком экономите на силиконе на этом этапе, ваша форма позже станет хрупкой и нестабильной.
Если вы хотите сделать силиконовую форму таким образом, не забывайте, что форма должна иметь отверстие на конце, через которое можно будет извлечь объект. В качестве альтернативы форму можно разрезать в какой-то момент после затвердевания.
Bilder: Van Rossen / Jlortiz / shutterstock.com
9000 2Как сделать решающие плесени – некоторые созерцания.
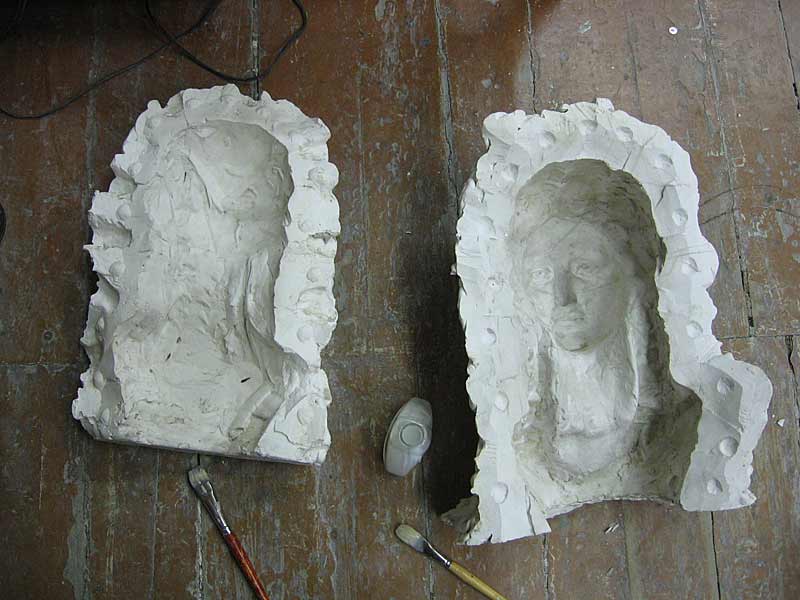
- На что похожа поверхность заготовки? Он очень гладкий или имеет канавки, края или орнамент? Это важно для выбора оптимальной твердости силикона. Если поверхность заготовки неровная, следует использовать мягкий силикон, чтобы позже отливку из смолы можно было извлечь из формы. С более простой заготовкой также работает силикон с более высокой степенью твердости.
- Насколько велика и тяжела заготовка? Каким материалом потом залить форму? Эти соображения также важны при выборе правильной степени твердости. Если вы преждевременно определились с мягким материалом, вполне возможны проблемы с устойчивостью при последующей заливке формы.
Для того, чтобы сделать силиконовые формы самостоятельно, это не обязательно должен быть дорогой специальный силикон.
Также можно использовать силикон для ванной, купить который намного дешевле. Специально для новичков он предлагает добраться до этой экономичной альтернативы. Так вы не будете раздражаться из-за неудачных, дорогих попыток. Однако при использовании силикона для ванной вы должны знать, что вы можете использовать его только для изготовления простых силиконовых форм. Филигранные, подробные иллюстрации не подойдут.
Материалы, необходимые для производства силиконовых форм для смолы
Если вы хотите изготовить силиконовую форму самостоятельно, тип вашего проекта определяет точные требования к материалам. Следующий список основан на негативной форме с оригинальной формой:
Лучшие наборы для изготовления силиконовых форм Рекомендации
Ваш творческий потенциал является вашим единственным ограничением, когда дело доходит до создания собственных силиконовых форм. Если вы хотите сделать силиконовую форму самостоятельно, характер вашего проекта будет определять точные требования к материалам. Следующий список основан на создании негативной формы с помощью оригинальной формы или шаблона:
Лучшее соотношение цены и качества: НЕВЕРОЯТНЫЕ РЕШЕНИЯ Набор для изготовления силиконовых форм
Этот набор для изготовления силиконовых форм содержит два компонента, которые при объединении образуют желтый нетоксичный резиновый силиконовый материал. Продукт не имеет запаха и очень удобен в использовании. При простом соотношении смешивания 1:1 две части этого набора легко комбинируются. Вы должны тщательно перемешать компоненты вместе в течение 5 минут, после чего у вас будет еще 5 минут, чтобы отлить и придать форму силикону.
НЕВЕРОЯТНЫЕ РЕШЕНИЯ Силиконовая замазка для форм
- Изготовление собственных силиконовых форм, легкое соотношение смешивания 1:1 Нет необходимости в чашках для смешивания, палочках для перемешивания и т. д.
Посмотреть на Amazon
Этот силикон не образует пузырьков, так как любые пузырьки исчезают менее чем за два часа без необходимости дегазации или нагревания. Смесь затвердеет через 5 минут, и ее необходимо выдерживать в течение 20 минут при комнатной температуре, хотя это может варьироваться в зависимости от размера и толщины формы. Людям, которые не умеют самостоятельно делать силиконовые формы, следует остановить свой выбор на этом продукте, так как он прост в использовании и легко моется. Вы можете создавать формы для любого количества применений.
Pros
- Non-toxic
- Odorless
- Food Safe
- Easy to use
Cons
- Short working time
Выбор премиум-класса: Набор для изготовления силиконовых форм BECKLY
Этот набор силиконовых форм премиум-класса прост в использовании и дает результаты высочайшего качества. При простом соотношении смешивания 1:1 эту жидкость с низкой вязкостью можно смешивать и наливать с максимальной легкостью. Тонкая консистенция жидкости делает ее идеальной для захвата деталей в ваших формах.
Набор для изготовления силиконовых форм BECKLY Diamond Driven
- Очень легко смешивается: пропорция смешивания 1:1
- Жизнеспособность: ~30 минут
- Отверждение через 6 часов, идеально подходит для смолы
Силиконовая смесь начнет затвердевать после 30 минут жизнеспособности при комнатной температуре и потребует шести часов отверждения. Продукт следует хранить при комнатной температуре для достижения наилучших результатов.
Силикон отвердевает до фиолетовый цвет , что означает, что это не лучший выбор для добавления собственных цветов. Несмотря на высокую цену, этот продукт предлагает отличное соотношение цены и качества.
Pros
- Выпуски пузырьки автоматически
- Простой коэффициент смешивания
- Отлично для сложных форм с множеством деталей
- 03 Отлично для сложных форм с множеством деталей
- 03 .
0007 Cons
- Containers are difficult to reseal
- Can be messy to work with
- Cannot add color
Other Materials you need for making your own Resin Mold
Цифровые весы в граммах и унциях
- Профессиональные цифровые весы с ЖК-дисплеем и функцией TARE
- Высокая точность с точностью до 1 г (максимальный вес 5 кг)
- Идеальны для взвешивания смолы для литья и ламинирования
Посмотреть на Amazon
CCBETTER Мини-пистолет для горячего клея с 30 клеевыми стержнями
- Пистолет для горячего клея с временем прогрева от 3 до 5 минут
- Идеально склеивает металл, картон, пластик, дерево, электронику и т. д.
- 30 клеевых стержней в комплекте
Посмотреть на Amazon
BRIGHT CREATIONS Листы МДФ 1/4 дюйма
- МДФ изготовлен из древесных волокон и является прочным и простым в использовании и резке
- Эти плиты МДФ очень хороши вырезаны без острых краев, готовы к использованию и склеиванию
- Размер каждой доски 11 x 14 дюймов
Посмотреть на Amazon
Глина для лепки Sargent Art Plastilina
- Масса для лепки EFA plast classic, белая, 3 кг
- Воздушная сушка и глина, как
- отвержденный
Посмотреть на Amazon
- чашка для смешивания
- деревянные палочки для смешивания
- силиконовый спрей
- тальк
- ватный тампон
- 3
- 3
- 3
- ватный тампон
- 3
- 0603
- изделие для воспроизведения
Чрезвычайно важно, чтобы в процессе заливки из рамы вытекало очень мало силикона или совсем не вытекало .
Поэтому с помощью зубочистки или ватной палочки все стыки закрываются моделирующим составом и каркас максимально герметизируется.
Как сделать силиконовые формы для смолы – пошаговое руководство
На первый взгляд может показаться, что сделать силиконовые формы очень сложно. С нашим пошаговым руководством даже для вас, как новичка, не составит труда сделать успешный негативный слепок.
Конструкция каркаса
- Каркас, в который будет заливаться силикон, должен быть как можно лучше герметизирован, чтобы в дальнейшем материал не вытекал из-за возможных трещин. Кроме того, рамка должна полностью закрывать заготовку.
- Опорная плита прототипа должна быть гладкой. Для этой цели подходят все гладкие материалы, кроме стекла. Это не будет отталкивать силикон, и поэтому последующее высвобождение без повреждения силикона будет практически невозможно. Лучше всего использовать гладкую плиту МДФ .
Гладко выструганная древесина также очень подходит для четырех боковых стенок, окружающих опорную плиту. Теперь приклейте боковые стороны к основанию с помощью пистолета для горячего клея. Эти боковые стенки должны выступать за вашу заготовку примерно на десять миллиметров. Стыки формы должны быть тщательно герметизированы модельным составом. Для разглаживания состава подойдут ватные палочки или зубочистки.
- Когда рамка будет готова, поместите в нее заготовку. Изображаемая сторона должна быть направлена вверх. Объект можно прикрепить к опорной пластине с помощью двустороннего скотча или капли горячего клея. Закрепите заготовку достаточно хорошо, чтобы она не могла соскользнуть, когда будете заливать силиконовую массу.
Смешивание силикона
- После взвешивания необходимого количества силикона смешивают два компонента в соотношении 1:1 . Для смешивания используйте чашу для смешивания и деревянную лопаточку. Будьте осторожны, чтобы не потратить слишком много силикона.
Для этого вы можете рассчитать объем или приблизительную потребность с помощью мерной палочки.
- Рекомендуется смешивать несколько небольших порций вместо одной большой порции силикона . Их легче смешивать без образования комков. Так как силикон очень жесткий, размешать его очень большое количество практически невозможно. Так что лучше разделить силикон, используя несколько маленьких чашек.
- Для разрыхления пузырьков в массе можно несколько раз постучать чашками дном о столешницу после перемешивания . Перед заливкой силикона в рамку следует подождать несколько минут. Это единственный способ, которым любой воздух действительно может выйти из массы.
Силиконовая заливка
- Если в качестве материала для изготовления каркаса выбрано дерево, перед заливкой силикона его необходимо тщательно обрызгать разделительной смазкой . Кроме того, вы также можете покрыть раму маслом. Но будьте осторожны: не все масла совместимы с силиконом и могут воздействовать на поверхность материала.
- Поэтому y следует заранее соблюдать инструкции производителя.
- Теперь можно заливать силиконовой массой заготовку в рамку.
- Залить силиконом большой предмет с гладкой поверхностью очень просто . Здесь жидкий силикон медленно выливается с относительно большой высоты на заготовку. Убедитесь, что он полностью закрыт массой.
- Если заготовка имеет множество кромок, углов, углов или трещин , то они должны быть вылиты в первую очередь. Лучше всего это работает с очень тонкой силиконовой струей. Затем можно обрамлять остатки силикона. Эта процедура гарантирует, что все детали будут видны на следующей иллюстрации.
- Затем рама заполняется оставшейся массой, пока она не будет выступать над объектом примерно на пять миллиметров.
- Наконец, из формованного силикона следует удалить пузырьки воздуха . Для этого осторожно постучите по всем четырем сторонам рамы, чтобы вышел воздух.
Затем вы можете позволить вашей форме затвердеть.
Извлечение готовой силиконовой литейной формы
- Время отверждения силиконовой формы зависит от используемого силикона и его размера . Он может варьироваться от одного до 24 часов. Если вы хотите проверить, полностью ли затвердел силикон, вы можете аккуратно вдавить его в форму пальцем. Если вы заметили, что масса затвердела, силиконовая форма теперь освобождается от рамки. Если он был тщательно обработан смазка для форм или масло, обычно это не проблема. Для окончательного выпрямления края лучше всего использовать ножницы, ковровый нож или скальпель. №
- Чтобы сохранить эластичность силикона и сохранить его, вы можете натирать его тальком после снятия с оправы и после каждого использования.
Изготовление двухкомпонентных форм из смолы и силикона
Для литья из смолы, конечно, очень подходят двухслойные формы.
При работе с эпоксидной смолой можно создавать впечатляющие трехмерные объекты, в которые можно отливать различные материалы, такие как камни, цветы или другие объекты.
Но также и для строителей моделей формы из двух частей, конечно, очень интересны, потому что они могут создавать разные объекты . С двухкомпонентными силиконовыми формами можно без проблем комбинировать детали разных размеров и из разных материалов. Из таких материалов, как бетон или гипс, можно создать фасады домов, ворота или опоры мостов, которые после затвердевания можно красиво покрасить и декорировать.
В дополнение к материалам, уже перечисленным выше для простой формы, вам также понадобится глина для лепки двухкомпонентных форм . При этом вы заполняете рамку наполовину. Затем поверхность необходимо выровнять, а углы хорошо выровнять.
Теперь вдавите половину заготовки в глину и залейте силиконом рамку. После застывания тесто и силиконовую форму снимают.
Готовая силиконовая форма помещается обратно в раму. Затем заготовка помещается в ранее сделанное углубление. Чтобы впоследствии можно было хорошо отделить половинки формы друг от друга, теперь вы должны смазать форму вазелином, прежде чем снова заливать жидкий силикон в раму. Этот силиконовый состав также должен хорошо затвердевать.
Силиконовые формы с поднутрениями
Силиконовые формы с так называемыми поднутрениями могут представлять особую сложность . Заготовки с поднутрениями имеют хорошо видимые выступающие углы и края, которые могут мешать при извлечении из формы. Если эти поднутрения относительно небольшие и вы используете мягкий силикон (от 0 до 20 по Шору), эти кромки не должны вызывать серьезных проблем.
Немного сложнее будет в случае с большими подрезами. В этом случае целесообразно изготовить форму из двух частей или даже из нескольких частей. В любом случае вам следует выбрать гибкую мягкую силиконовую резину и обращать особое внимание при извлечении объекта, чтобы он не растягивался.
Если нет возможности снять заготовку обычным способом, можно обрезать силиконовую форму с одного края и затем снять заготовку. Полученный разрез затем можно закрыть, прикрепив к форме несколько очень тугих резинок. Это позволяет очень легко впоследствии извлечь отлитую деталь из негативной формы.
Силиконовые формы для смолы – ценные советы и рекомендации0008 .
Возьмите опорную плиту из гладкого строганного дерева, а затем поместите рамку из кирпичиков Lego, которую приклейте к плите. С этим вы абсолютно гибки в размере и форме. При герметизации и последующем заливании силикона вы действуете так же, как и в случае деревянной рамы.
- Оптимальная комнатная температура для сушки силикона составляет от 18° до 22° C . Если температура выше, материал может слипаться, потому что сохнет слишком быстро. Если температура в помещении ниже 18°C, процесс сушки излишне затягивается.
- Еще один маленький трюк, если вы не уверены, сколько силикона вам действительно нужно: соберите деревянную раму, как описано, и прикрепите заготовку к опорной плите. Теперь заполните форму рисом так, чтобы он был примерно на один сантиметр выше объекта. Так как вес риса примерно соответствует необходимому количеству силикона, вам остается только его взвесить.
- Важный совет в конце: Чтобы не потерять радость от вашего проекта в начале, сначала запланируйте относительно простую форму и не торопитесь с реализацией .
Постепенно можно повышать уровень сложности.
- 03 Отлично для сложных форм с множеством деталей
Как очистить формы – Учебное пособие
С нашими советами вы вернете силиконовую форму в идеальное состояние.
- Просто поместите нетвердую эпоксидную смолу в морозильную камеру . Холод заставляет жидкую смолу кристаллизоваться, и устраняются самые большие повреждения. Этот трюк также работает с УФ-смолой, но здесь вы должны сначала попробовать его с более длительным временем отверждения. Пожалуйста, помещайте силиконовые формы в морозильную камеру только упакованными и промаркированными. Желательно в пустой отсек. В любом случае следует избегать контакта с пищевыми продуктами.
- Теперь большую часть смолы можно легко удалить, оставив только остатки. № Их лучше всего удалять большим количеством жидкости для мытья посуды № , которую втирают в форму в перчатках и промывают водой. Поместите форму на безворсовую ткань для просушки.
- При этом форма выглядит лучше и теоретически может быть использована снова.
Но остатки прилипнут к новой смоле. Для всех перфекционистов, которые хотят потратить еще 5-10 минут работы, теперь они прибегают к клейкой ленте. Просто используйте клейкую сторону, чтобы удалить оставшуюся смолу, пигменты и остатки блесток из формы, и она должна выглядеть как новая и готова к следующему литью смолы
Как предотвратить проблемы с силиконовыми формами
- Запрещено использовать открытый огонь в форме. Выжигание пузырьков — популярный способ избавиться от надоедливых пузырьков воздуха в смоле. Но будьте осторожны: избегайте любого контакта с силиконом. Силиконовые формы можно кратковременно нагревать до 180°С. Зажигалка достигает температуры от 800° до 1300° по Цельсию — это слишком много.
- Смешайте смолу в соответствии с инструкциями на упаковке. Даже минимальные отклонения могут привести к тому, что смола станет излишне теплой, что приведет к более быстрому старению формы.
- Используйте только цвета, подходящие для смолы.
Акриловые краски могут вызвать кипение смолы и повредить форму.
- Никогда не чистите силиконовые формы губками или другими кислотосодержащими предметами.
- Можно использовать разделительные составы. Разделительные составы ухудшат отделку вашей работы из смолы, но помогут вашей силиконовой форме прослужить дольше. Наше предложение: используйте разделительные составы только для сложных форм, которые трудно формовать, или если вы уже заметили, что качество вашей силиконовой формы ухудшается.
Силиконовые формы «Сделай сам»
Даже если у вас пока нет большого опыта в изготовлении силиконовых форм, вы все равно можете сделать небольшие украшения . Нет предела вашему творчеству. Подвески различной формы из эпоксидной смолы и встроенных материалов привлекают внимание.
Если ваш ребенок очарован вашим любимым украшением, вы можете создать красивую копию с блестящими дополнительными элементами, такими как блестящие частицы.
Если вы уже немного разбираетесь в литейных формах, примите участие в изготовлении шахматной партии из эпоксидной смолы . Уникальная идея подарка для любителей шахмат, когда большие усилия в конце концов окупаются.
Нет предела возможностям — вы даже можете собрать гитару с помощью собственной силиконовой формы.
Обычные силиконовые формы легко доступны на рынке . Однако, если вы хотите выпустить пар и создать действительно уникальную вещь, вам не обойтись без изготовления силиконовой формы своими руками. Просто попробуйте — с нашим руководством все может пойти не так 🙂
Руководство для начинающих по изготовлению пресс-форм и литью
Мы можем напечатать на 3D-принтере много разных вещей, и не все из них должны быть конечными продуктами. Вместо этого мы могли бы сделать различные инструменты, шаблоны, контейнеры… или литейные формы . Именно этот вариант и является темой нашей текущей статьи. Мы покажем вам, как отливать такие материалы, как воск или мыло, в домашних условиях с помощью легкодоступных инструментов.
Наша цель – доказать, что литье из силиконовых форм намного проще, чем может показаться на первый взгляд. Мои собственные попытки включали некоторые пробы и ошибки, прежде чем я научился правильным методам. Поэтому я надеюсь, что теперь смогу помочь другим сэкономить материал, время и силы.
Примечание: На приведенных ниже рисунках показано, что я использовал старый печатный лист PEI в качестве рабочей площадки. У этого нет специальной цели, вместо этого используйте что угодно другое — не рискуйте повредить свой идеальный лист для печати 🙂
Материал для изготовления формы
Для создания формы мы будем использовать двухкомпонентный силиконовый каучук конденсационного отверждения. В нашем случае это продукт местного чешского производства под названием Lukopren N Super, но есть много аналогичных продуктов, которые вы, вероятно, можете найти по всему миру, например, Smooth-on, силиконы ACC, RTV и т. д.
Lukopren состоит из части A (сам силикон) и части B (отвердитель/активатор) и отверждается при комнатной температуре примерно через 24 часа . Время отверждения зависит от количества отвердителя и температуры окружающей среды.
Полученная форма имеет стабильную форму и устойчива как к химическому, так и к термическому воздействию. Вы можете использовать его для литья многих материалов, включая полиуретан , эпоксид, полиэстер, гипс, бетон, цемент, воск, низкоплавкие сплавы или мыло . Этот формовочный материал подходит как для небольших, детализированных слепков, так и для крупных объектов (например, статуй). Вакуумный насос не требуется из-за отличной текучести и низкой вязкости. Силиконовый каучук можно как наливать, так и наносить кистью (с добавлением в смесь загустителя), хотя есть и лучшие варианты нанесения кистью, например, Smooth-on, упомянутый выше.
Металлическое литье будет подробно описано в нашей следующей статье, посвященной ювелирному делу и применению в стоматологии.
Модель
Для получения качественной отливки в первую очередь нужна качественная мастер-модель для создания формы.
Разработка такой модели может быть утомительной и требует некоторого терпения и внимания к деталям, особенно если вы новичок в приложениях для 3D-моделирования. Вы можете вообще пропустить эту часть, просто загрузив готовую модель из базы данных в Интернете, например, с www.prusaprinters.org.
Будьте осторожны с так называемыми выступами – контурами модели, имеющими более острый угол (90°) по отношению к плоскости разъема пресс-формы. Другими словами, если вы посмотрите на пресс-форму прямо сверху, вы должны увидеть всю внутреннюю поверхность , ничего не спрятанного «за углом». Эти выступы могут позже привести к застреванию мастер-модели или окончательной отливки в форме. К счастью, одним из больших преимуществ силиконовой резины является ее эластичность — она немного деформируется, когда мы сгибаем и скручиваем ее, чтобы вынуть готовый слепок. Это означает, что мы могли позволить себе определенный уровень выступов. Правильно отлитая модель должна выскочить почти самопроизвольно после легкого нажатия на форму.
Если мы используем метод так называемого литья по выплавляемым моделям, нам, конечно, вообще не нужно беспокоиться о выступах, потому что мы не вынимаем модель, она разрушается внутри формы. .
Для изготовления форм из силиконовой резины в качестве эталонной модели подходит любой непористый материал. Это означает, что вы можете использовать 3D-печать из нити или смолы. Напечатать слои не проблема (с точки зрения извлечения из формы), но они, конечно, будут видны на готовой отливке. значит печать из смолы больше подходит — я использовал принтер Original Prusa SL1.
Для литья по выплавляемым моделям доступны специальные литейные смолы, которые можно полностью расплавить или выжечь из формы. Более подробная информация об этом методе также будет в следующей статье.
Мастер, напечатанный на 3D-принтере, гораздо более расходный материал, чем изготовленный вручную. В худшем случае, если мы каким-то образом повредим его во время нашей первой попытки изготовления пресс-формы, мы всегда сможем напечатать его заново.
Тщательно осмотрите поверхность мастер-модели, прежде чем использовать ее для изготовления пресс-форм. Справьтесь с любыми небольшими дефектами, потертостями, заглушками поддержки или даже отпечатками пальцев! В противном случае все эти поверхностные дефекты будут скопированы в конечную отливку!
Окончательная подготовка к изготовлению пресс-формы
Перед изготовлением собственно пресс-формы, состоящей из двух частей, нам необходимо разметить ее разделяющую плоскость . Заливочный канал и вентиляционные отверстия в форме мы прорежем позже, перед самой отливкой.
Разделяющая плоскость будет создана следующим образом: втолкните мастер-модель в пластилин до предполагаемого уровня разделительной плоскости (конечно, она не обязательно должна быть строго горизонтальной).
Чтобы позже можно было правильно выровнять обе половины пресс-формы, создайте так называемые регистрационные ключи .
Это могут быть простые отверстия, сделанные ручкой щетки, прорезанные канавки – все, что может нарушить гладкую поверхность, что может привести к скольжению половинок формы.
Также нам предстоит создать внешнюю оболочку, которая будет удерживать жидкий силикон внутри и не даст ему разлиться по всему столу. Изучив несколько тупиков с использованием кубиков Lego или различных блоков, соединенных клеевым пистолетом, мы нашли простое, чистое, но не столь очевидное (хм…) решение — мы напечатали его на 3D-принтере Original Prusa i3 MK3S: ). 4 стенки по периметру сделали корпус достаточно прочным.
Все внутреннее пространство, т.е. внутренние стенки корпуса, поверхность пластилина и мастер-модели, должны быть покрыты разделительной смазкой , в противном случае позже мы не сможем извлечь мастер модель из формы.
Теперь давайте создадим нижнюю половину пресс-формы. Залейте силиконовую смесь с добавлением отвердителя/активатора (согласно инструкции) в угол раковины с достаточной высоты (не менее 10 см / 4 дюйма). Пусть силикон растечется и заполнит все закоулки самостоятельно.
Дайте силикону как следует высохнуть, затем снимите нижнюю часть формы с корпуса и осторожно очистите всю модельную глину.
Когда форма и мастер-модель полностью очистятся, снова покройте их разделительным составом, чтобы верхняя половина формы не прилипла к нижней. Еще раз влейте силиконовую смесь и создайте остальную часть формы.
Теперь форма готова, и мы можем снять мастер-модель и отложить ее в сторону.
Литейный материал заливают в форму через разливочный желоб . Его размер имеет решающее значение для качества литья (если мы не используем метод центробежного литья). Для большинства материалов, кроме металла, длина должна быть не менее 3–5 см (2 дюйма). Для материалов с худшей текучестью, таких как гипс, бетон или воск, ширина канала должна быть не менее 3 см (1,2 дюйма), в противном случае ширины 1 см (0,5 дюйма) должно быть достаточно.
Вы также должны вырезать хотя бы один воздухоотводчик , чтобы воздух быстрее вышел из формы. Такие вентиляционные отверстия всегда должны располагаться над точкой, где сливной канал встречается с полостью модели, а также во всех местах, где могут образоваться воздушные карманы. Для правильной процедуры литья характерно, что все вентиляционные отверстия также полностью отлиты (заполнены литым материалом).
Процесс литья
У нас есть готовая форма, включая разливочный канал и вентиляционные отверстия. Обратите внимание, что пресс-форму можно использовать несколько раз , вы можете получить до 30-50 слепков, в зависимости от того, насколько детализированы контуры.
Теперь самое время кастинга. Опять же, мы используем антиадгезив для покрытия внутренних поверхностей формы – убедитесь, что вы действительно тщательно, иначе отливка может прилипнуть к форме.
Будем отливать мыло и воск .
Для литья мыла нам нужно сначала разжижить материал, нагрев его . Вы можете использовать обычную микроволновую печь с максимальными настройками примерно на одну минуту (зависит от мощности микроволн и того, какой именно мыльный материал вы используете). Чтобы быть в безопасности, мы рекомендуем проверять ситуацию каждые 30 секунд.
Плотно скрепите обе половины формы скотчем. Медленно залейте горячий материал в форму.
Он затвердеет примерно через 1-3 часа, в зависимости от температуры окружающей среды (вы можете поставить его в холодильник, чтобы ускорить процесс).
Тот же процесс можно использовать для отливки воска для свечей, единственный дополнительный шаг — вырезание канавки для фитиля свечи на противоположном конце от заливочного канала.
Вставьте фитиль и залейте воск (опять же, расплавленный в микроволновой печи) в форму.
Воск затвердевает быстрее, чем мыло, и готов к извлечению из формы примерно через 30-60 минут (опять же, в зависимости от температуры окружающей среды).