Как согнуть полосу металла в круг – Гибка металлической полосы по радиусу плашмей и на ребро
alexxlab | 06.03.2020 | 0 | Разное
Гибка металлической полосы по радиусу плашмей и на ребро
Гибка полосы из металла используется при изготовлении различных приспособлений: скоб, кронштейнов, хомутов и других элементов. Основными критериями качества гибки заготовок является точность параметров внешней конфигурации, сохранение равномерной толщины профиля обрабатываемого изделия и его прочности в процессе эксплуатации.
Гибку полосы делают на специальном оборудовании как из сырьевой массы (алюминиевой, стальной или из нержавейки), так и из других металлических предметов (труб, продукции сортового или фасонного проката). Делая гибку из готовых деталей, в качестве сырья применяют изделия сортового проката с характером профиля в форме круга или квадрата, а из фасонного используется швеллер или уголок. Гибка полосы имеет особенности:
Гибка полосы по радиусу производится для создания сферической поверхности. Гибку делают поперек волокон материала, образовавшихся в процессе проката. В месте сгиба металл утончается и деформируется в поперечном сечении. Гибка может производиться с разными радиусами. Чем меньше радиус, тем на большую площадь заготовки распространяется деформация. При ошибке в расчетах радиуса сгиба на поверхности полосы или трубы могут появиться разрывы от излишнего сжатия или растяжения основы. Гибку производят по технологии, обеспечивающей сохранение формы после воздействия на изделие.
Гибка в кольцо также требует проведения точных расчетов соотношения между толщиной металла и диаметром. Гибку в кольцо выполняют в нескольких вариантах: полосы или трубы сгибают с постоянным или переменным радиусом, плашмя (ширина материала до 240 мм ) или на ребро (ширина материала до 150 мм ). Гибку в кольцо применяют в тех случаях, когда необходимо сохранить одинаковую деформацию структуры по всей протяженности профильных элементов.
Гибка полосы волной. Толщина профилей должна соответствовать радиусу изгиба. Во избежание сложных расчетов применяют станки с ЧПУ;
Гибка полосы в спираль бывает разных видов:
- гибка по дуге применяется для декоративных деталей разной толщины профиля;
- гибка скручиванием: одна или две полосы одинаковых профилей, зажатые с одного конца, поворачиваются относительно своей оси. Скручивание производят также из прутков круглого профиля;
Гибка под прямым углом позволяет делать металлоконструкции в виде квадрата. В изготовлении используется лист стали или нержавейки. Не исключено применение алюминиевой полосы;
Гибка полосы под острым углом. Полоса может располагаться как плашмя, так и на ребро.
Гибку металлических заготовок облегчает аппаратура ЧПУ. Высокотехнологическое оборудование значительно повышает точность расчетов напряжения металла, исключает воздействие на гибку трубы или металлопроката случайных факторов. Гибка обрабатываемого предмета становится качественней, значительно повышаются его эксплуатационные качества. Особое значение программное управление приобретает при создании декоративных элементов, позволяя выпускать предметы сложной конфигурации с высокими эстетическими свойствами.
Параметры гибки и требования к профилям
Тип | Размер мм | Толщина стенки, мм | Минимал. радиус, мм |
1. Полоса – гиб на ребро | |||
![]() | 30 | 10 | 125 |
45 | 20 | 150 | |
50 | 20 | 250 | |
60 | 20 | 250 | |
70 | 15 | 350 | |
120 | 15 | 600 | |
2. Полоса – гиб плашмя | |||
30 | 10 | 125 | |
45 | 20 | 125 | |
60 | 30 | 150 | |
100 | 10 | 200 | |
150 | 15 | 350 | |
260 | 20 | 400 |
Примечание:
Данные параметры предоставлены для ориентира и всегда зависят от толщины и типа материала.
Виды металлов
Компания принимает заявки на обработку проката из разнообразного сырья: алюминия, стали и нержавейки. Правильная гибка металлической полосы позволяет сохранить ее свойства с минимально возможным смещением слоев. В отдельных случаях такой способ формовки способен заменить сваривание, обеспечивая большую скорость готовности, эстетичность, устойчивость к эксплуатационному изменению формы, возникновению очагов коррозии при отсутствии защитного покрытия.
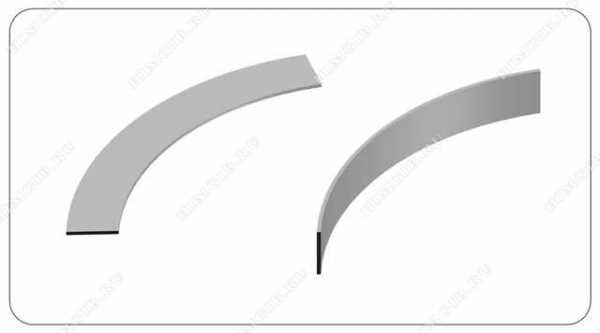
Гибка алюминиевой полосы
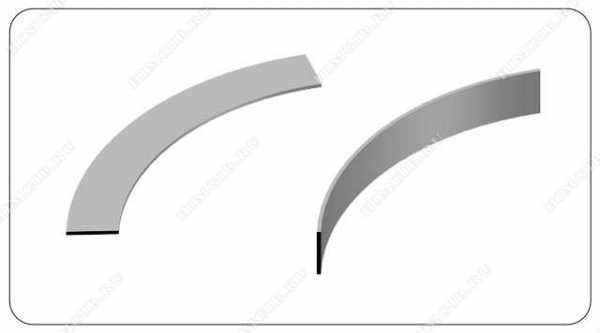
Гибка полосы из нержавейки

Гибка стальной полосы
Смотрите также: гибка профильной трубы по радиусу
himgib.ru
Согнуть стальную полосу 60*6 в полукольцо в тисках, усилие – Общий
-=Красный механиК=-,
Если зажимать в тисках полосу, она может согнуться в одной точке и получится не то что хочется.
Спасибо.
По моему опыту, чаще сгибается в одной точке при изгибании вбок, когда один конец полосы зажат а второй гнется. Поэтому и отказался от мысли постепенных гибов на оправке. Мне казалось, при продольном сжатии деформация должна быть более кругообразной.
Полукольца надо будет вставлять в кольцевые канавки во фрезерованном основании.
городить простой “полосогиб” со сменными оправками.
Конструкция? Мне пока в голову приходит только две трубы, на которых лежат концы полосы, и еще одна сверху по центру. Ударами по центральной трубе полоса гнется. Но удастся ли так получить кольцо?
Из полученного меньшего диаметра сделать больший проще чем наоборот и сначала делаем то что должно получиться и только потом отрезаем от куска, с кусочками впритык работают только на крупносерийном производстве
Идея понятна, из кольца действительно проще получить сектор окружности нужного диаметра. С перерасходом материала готов смириться.
А как без вальцов слесарными методами получить достаточно точное кольцо? Возможно ли это вообще, на холодную и на стали такой размерности?
Изменено пользователем IvanIvanov76www.chipmaker.ru
Ответы@Mail.Ru: Как согнуть металлическую полосу
вот такая хрень была у петрвича с пятнадцатого <img src=”//otvet.imgsmail.ru/download/u_bc4eae1c3ba98398ad1452a7e6261f45_800.jpg” alt=”” data-lsrc=”//otvet.imgsmail.ru/download/u_bc4eae1c3ba98398ad1452a7e6261f45_120x120.jpg” data-big=”1″>
Трубу соответствующего диаметра и рихтуй потЯхонку молотком
Идешь в скупку металлолома, находишь подходящую по диаметру трубу и зажимаешь ее с полосой в тисках и гнешьБерете трубу 76 (на скрине №4) привариваете к ней приток диаметром 12-14 мм (№3),таким образом, чтобы ваша полоса входила между трубой и прутком. Крепите трубу с приваренным прутком (это уже будет называться “оправка”) можно в тески (чтобы в тисках не проворачивалась оправка к трубе доварить пару прутиков в месте крепления оправки в тисках) или приварить к чему то массивному, вставляете полосу между трубой и прутком и гнете полосу вокруг трубы. После гибки полоса за счет пружинения получит больший диаметр, и отрезаете загнутую часть полосы, начало гиба и конец будут иметь прямолинейности. Вставляете следующую и гнете и гнете и гнете))) позиции 1 и 2 по скрину не нужны. Можно также развести тиски положить сверху полосу и простукивать ее молотком, тоже согнется, это дольше первого способа и для разовой гибки. <img data-hsrc=”//otvet.imgsmail.ru/download/18489081_086edf8a2321d968b38524dbecbcbc12_800.jpg” src=”//otvet.imgsmail.ru/download/18489081_086edf8a2321d968b38524dbecbcbc12_120x120.jpg”><img data-hsrc=”//otvet.imgsmail.ru/download/18489081_2c6a566663036c0f2dbb123a6a4ccce7_800.jpg” src=”//otvet.imgsmail.ru/download/18489081_2c6a566663036c0f2dbb123a6a4ccce7_120x120.jpg”>
touch.otvet.mail.ru
Гибка уголка с использованием подручных инструментов
Гибка уголка — это технологический процесс получения различных изделий заданных параметров и необходимых форм путем механического воздействия, в том числе на специальном профилегибочном оборудовании.
Получаемые при сгибании металлического уголка изделия находят широкое применение в различных сферах строительства. Они позволяют создавать надежные каркасы и различные металлоконструкции, которые способны при своей внешней легкости выдерживать значительные нагрузки.
Способы гибки уголка
Применяют несколько основных способов получения из металлического уголка конструкций заданной формы и профиля, а именно различают:
- холодное сгибание,
- горячее сгибание,
- придание формы с помощью разрезания, сгибания и сварки готового изделия.
Холодное сгибание металлического уголка, в свою очередь, разделяется на:
- свободную гибку — это когда уголок сгибают без применения специального оборудования;
- сгибание с помощью вальцовочного механизма на специализированном профилегибочном станке.
Применение холодной гибки металлического уголка, в отличие от других способов, имеет определенные преимущества, а именно:
- это наименее затратный метод придания металлу заданной формы, при этом не требуется использования дополнительного оборудования для разогрева, резки, сварки и последующей обработки металла;
- получаемый в итоге каркас имеет большую прочность, так как при этом исключаются возможные дефекты, характерные при применении разогрева, резки и сварки;
- готовые конструкции гарантированно служат больший срок из-за того, что при обработке сохраняется целостность структуры металлического профиля;
- снижается вероятность возникновения очагов коррозии металла со временем.
Сгибание уголка по радиусу
Гибка металлического уголка по радиусу достаточно сложная технологическая операция, так как любое сгибание — это одновременное сжимание внутреннего и растягивание внешнего слоя металла, а, в случае с профилем в виде уголка, такие процессы никак не могут протекать равномерно, что будет сопровождаться попыткой продольного смещения одного из этих слоев.
Непосредственно для металлического уголка применяют два основных способа сгибания в плоскости профиля — это когда одна из полок лежит в вертикальной плоскости, а другая в горизонтальной и ее сгибание будет:
- вовнутрь радиуса кривизны деформации, при этом она будет сильно сжиматься ,
- наружу радиуса кривизны деформации, соответственно, она будет растягиваться .
Холодное сгибание металлического уголка методом вальцовки на специальном профилегибочном оборудовании позволяет согнуть как стальной уголок, так и профиль из алюминия, получая при этом изделия практически любого радиуса с идеальной формой.
Как согнуть уголок по радиусу своими руками можно посмотреть на этом видео.
Стоит иметь в виду, что как для горячего, так и холодного способа сгибания существуют предельные величины радиусов, которые напрямую зависят от размера полок уголка и его толщины. Так, можно упрощенно рассчитать радиус, на который допустимо загибать уголок, согласно следующим значениям:
- допустимый радиус для равнополочного уголка должен составлять минимальные 45 размеров ширины полки;
- для неравнобокового профиля допустимый радиус не может быть меньше 45 размеров ширины полки для большей полки и 50 — для меньшей.
Но лучше и проще руководствоваться значениями, которые приведены в таблицах.
Таблицы минимально допустимых радиусов сгибания стальных уголков в зависимости от типа, размеров и отношения величин полок
Как согнуть уголок в кольцо своими руками
Для этого лучше всего воспользоваться горячим способом обработки металла. А вот добиться заданного радиуса можно только с помощью заранее приготовленного шаблона. Предварительно нагреваем металл и начинаем равномерно огибать шаблон, при этом горизонтальную полку необходимо править во время всего процесса сгибания с помощью кувалды или молота, в противном случае полки не сохранят изначальный угол в 90 градусов между собой.
Нагревать металл необходимо до половины значения температуры его плавления, так, к примеру, алюминиевый уголок придется нагреть как минимум до 250⁰ С, а стальной профиль — до 600⁰ С. Для этого вам понадобится горелка на природном газе или бензиновая паяльная лампа, а лучше всего воспользоваться сварочным ацетиленовым резаком, если уголок большого размера.
С помощью болгарки и сварочного аппарата тоже можно согнуть стальной уголок в кольцо, но для этого необходимо произвести достаточно точные расчеты, разметить и расчертить удаляемые сектора, согнуть и заварить швы. К сожалению, как бы вы ни старались, в этом случае получиться круг в виде округлого многогранника.
Под 90 градусов
Практически все постройки имеют прямоугольную форму, поэтому самое частое действие с уголками — это необходимость их загнуть под 90 градусов.
Согнуть уголки под 90 градусов для будущего каркаса достаточно просто. Сначала надо сделать в месте будущего сгиба развертку. Для этого на одной из полок отмечаем два угла в разные стороны от нормали по 45 градусов каждый и вырезаем их болгаркой. Аккуратно и медленно гнем уголок и свариваем место реза электросваркой, при этом рекомендуется предварительно нагреть место сгиба, чтобы вторая полка во время сгибания не треснула и не сломалась.
Допустимые расчетные размеры для того, чтобы правильно разметить и согнуть металлические уголки под 90 градусов, приведены в таблице:
wikimetall.ru
Гибка полосовой стали – Гибка и правка металла
Гибка полосовой стали
Категория:
Гибка и правка металла
Гибка полосовой стали
Полосовую сталь удобнее всего гнуть в слесарных тисках. Для этого нужно установить заготовку таким образом, чтобы сторона с нанесенной на нее риской места загиба была обращена к неподвижной губке тисков. Риска должна выступать над губкой примерно на 0,5 мм. Удары наносить следует тоже в направлении неподвижной губки тисков (рис. 1).
Для того чтобы загнуть полосу под острым углом, необходимо воспользоваться оправкой, которая соответствует требуемому углу загиба. Ее нужно зажать в тисках вместе с заготовкой, расположив высокой стороной к заготовке, и загнуть ударами молотка (рис. 1).
Для изготовления из полосовой стали скобы применяется брусок-оправка, равный по толщине проему скобы. Его нужно зажать в тисках вместе с полосой стали и легкими ударами молотка загнуть одну сторону скобы. Затем вложить брусок внутрь скобы и, снова зажав в тисках, отогнуть другую сторону.
Для крепления труб и металлических стержней различного назначения часто используется хомут из полосовой стали. Он также изготавливается на тисках. Для этого нужно взять круглую оправку нужного диаметра, зажать ее в тисках и двумя плоскогубцами загнуть на ней полоску стали необходимой ширины и длины.
Затем оправку нужно освободить из губок тисков и, зажав в них отогнутые концы хомутика, придать ему окончательную форму.’ Лучше наносить удары молотком не по самому хомутику (чтобы не оставить на нем забоев, вмятин и царапин), а через медную пластинку небольшой толщины, которая хорошо перераспределяет усилие удара. Если нужен хомутик полуоткрытый, то его доводку удобно производить на плите.
Полосовая гибка часто применяется при соединении деталей — в так называемых гибочных соединениях. Они носят самый различный характер и применяются достаточно широко. Соединение может быть целиком гибочным — крепежное усилие может создаваться изгибом одной или обеих деталей, а может играть вспомогательную роль и усиливать, например, резьбовое соединение, как стопорная шайба или шплинт в соединении гайка-болт (рис. 2).
Если ваша домашняя мастерская оборудована настольным ручным прессом, имеющим усилие 5-10 килоньютонов, то их можно оснастить очень производительными штампами, с помощью которых можно придавать металлическим листам изгиб нужного профиля. На основание пресса установите матрицу с заранее выбранным профилем, а верхнюю, силовую часть пресса, оборудуйте пуансоном, соответствующей матрице формы (рис. 16). При изготовлении штампов следует помнить, что ширина пуансона должна быть меньше ширины «ручья» матрицы на удвоенную толщину металлической заготовки.
Рис. 1. Приемы гибки полос: а — порядок гибки; б — гибка острого угла
Рис. 2. Примеры гибочных соединений при сборке: примеры гибочных соединений при сборке
В тех случаях, когда требуется изогнуть стальную полосу на ребро, используется роликовое приспособление. При работе с ним следует учесть, что верхняя прорезь бруска основания должна точно соответствовать размерам полосы. Кроме того, верхнюю часть полосы, которая будет испытывать деформацию растяжения , а также рабочий ролик нужно смазать маслом.
Заготовки из стальных прутков удобно гнуть на простейшем приспособлении, которое представляет собой два штифта различного диаметра, ввернутых в металлическую плиту-основание. Пруток нужно вставить в промежуток между штифтами и оборачивать его вокруг штифта большего диаметра. При необходимости можно использовать молоток (если пруток слишком толстый или короткий). Недостаток этого приспособления в том, что оно позволяет получать изгибы только одного диаметра (соответствующего диаметру большого штифта). Впрочем, при желании его можно усовершенствовать, сделав штифты сменными.
Рис. 3. Гибка заготовок с помощью гибочного штампа
Рис. 4. Гибка стальной полосы на ребро
Реклама:
Читать далее:
Рубка металла
Статьи по теме:
pereosnastka.ru
Коршевер Наталья. Работы по металлу
Гибка
Если поковке придается изогнутая форма по заданному контуру, то такая кузнечная операция называется гибкой. При гибке происходит неравномерное деформирование различных частей заготовки. Те слои, которые расположены у внешнего края угла, растягиваются, внутренние, наоборот, сжимаются. За счет этого толщина изделия уменьшается на величину, называемую утяжиной.В процессе такой деформации главное – избежать появления трещин на внешней части. Она подвергается наиболее сильному воздействию, которое зависит от величины угла сгиба, пластичности металла, толщины заготовки и направления волокон.
Чаще всего гнется горячий металл, но тонкие полосы поделочной стали гнутся и в холодном виде. Деформация такой полосы более упругая, поэтому ее лучше делать на угол, на несколько градусов больше, чем требуется.
Приемы гибки
Они зависят от формы поперечного сечения заготовки. Перед началом операции ее разогревают до температуры ковки, желательно только в том месте, в котором осуществляется сгиб.Следующий этап – высадка внешней части сгиба, которая будет компенсировать утяжину (рис. 151).

Размеры ее определяются с учетом толщины и угла сгиба. Можно оставить утолщение на месте сгиба во время выполнения протяжки. Заготовку кладут на угол наковальни, прижимают сверху кувалдой или струбциной и ручником изгибают на нужный угол (рис. 151, а).
У более коротких заготовок металл наращивают уже после того, как произведена гибка. Сделать это можно прямыми ударами по торцу или же гладящими ударами по внешним сторонам (рис. 152, б). Когда требуется сделать угол меньше 90°, проводят высадку внешней части, затем сгибают деталь необходимым образом. Далее проводится протяжка угла, то есть запас металла перемещается в сторону утяжины. Удар ручником делается с небольшим наклоном, как показано на рис. 151, в.
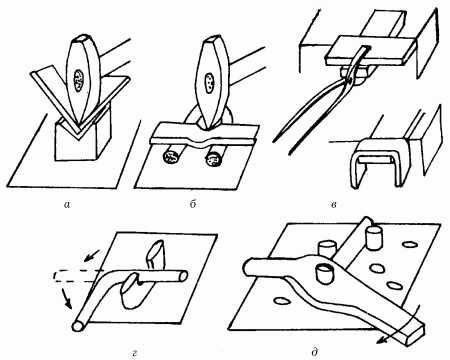
Сгибание полосы
Очень просто согнуть полосу металла, поскольку толщина ее обычно небольшая. Сделать это можно с помощью различных подкладок (рис. 152), например углового нижника (рис. 152, а).Нижник устанавливают в квадратное отверстие наковальни, заготовку кладут на ребра и деформируют заостренной кувалдой.
Используя другие подкладки, можно получить различные формы сгиба, как это показано на рис. 152, б, в.
Сгибание круглой заготовки
Для сгибания круглой заготовки высадку проводить неудобно, поэтому его осуществляют в специальной вилке (рис. 152, г). Пруток удерживают в ней клещами, а свободную сторону загибают на нужный угол ударами молота. Более усовершенствованную модель представляет собой гибочная плита с перемещаемыми держателями. На металлической плите делается несколько отверстий, в которые вставляются штырьки, фиксирующие стержень под нужным углом по отношению к вилке. Для сгибания применяется рычаг, который равномерно деформирует деталь.Гибка по дуге
Эта разновидность гибки очень часто используется художниками для создания красивых завитков, спиралей и прочих украшений. Производится она на роге наковальни, шпераках и сложных оправах, которые служат для серийной гибки одинаковых орнаментов.Гнуть завитки и спирали можно на специальной подкладке в форме перевернутого сапожка. На конусообразной подставке делают конусные спирали, плотно наматывая на нее раскаленную проволоку или загибая ее с помощью ручника.
Скручивание
Эта операция заключается в том, что одна часть заготовки поворачивается относительно другой. Во многих случаях она является вспомогательной: отдельные детали поковки выполняются в одной плоскости, а затем поворачиваются под разными углами.Для расположения в пространстве отдельных элементов орнамента часть заготовки поворачивается на угол до 180°, обычно с одновременным изгибом по дуге или под углом. Многократное скручивание на 360° граненого стержня делает его витым. Несколько тонких прутков или проволок можно скрутить (свить) в шнур. Наиболее красивый шнур образуют два туго свитых круглых прутка.
Скручивание или свивание производят при ярко-красном или желтом калении, иначе на изделии из-за недостаточной пластичности металла могут возникнуть трещины (рис. 153).
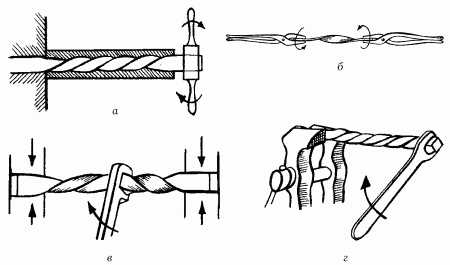
Толстые поковки скручивают с помошью воротка, стальной полосы с отверстием, соответствующим сечению скручиваемой поковки, ключа или вилки (рис. 153, в), второй конец заготовки при этом зажимают в тиски.
Для того чтобы заготовка не изгибалась при скручивании, на нее надевают отрезок трубы. Тонкие заготовки быстрее остывают, поэтому их либо больше нагревают перед зажатием в тиски и вороток, либо (что лучше) скручивают вдвоем. При этом необходимо клещами захватить концы заготовки и одновременно начать вращать в противоположных направлениях (рис. 153, б).
Широкие полосы закручивают с помошью специальной вилки, зажав оба конца заготовки (рис. 153, г).
Сварка
Это одна из самых сложных операций ручной ковки. Для овладения ею требуется большой опыт работы с металлами и знание технологического процесса.Кузнечная (горновая сварка) позволяет соединять отдельные детали изделия. Откованные по отдельности детали можно более тщательно оформить, соединить в большое и сложное изделие и т. д. В последнее время все чаще используется электрическая или газовая сварка, однако зачастую только горновая сварка может обеспечить высокие художественные достоинства изделия, так как кузнечные швы легче обрабатываются и отделываются.
При кузнечной сварке различают 4 основных операции: подготовка концов, нагрев, сварка, проковка шва.
Кузнечная сварка отличается от аналогичной слесарной операции. Когда при деформировании на малое расстояние происходит сближение поверхностей, между атомами кристаллической решетки возникают мощные силы притяжения. Если металл имеет высокую пластичность, то на такое расстояние его можно свести нагреванием в кузнечном горне.
Выбор материала
Хорошее качество сварки можно получить у низкоуглеродистой конструкционной стали. Кузнечной сваркой лучше всего сваривать сталь с содержанием углерода 0,15–0,25 %.Некоторые примеси, например сера и фосфор, сильно ухудшают свариваемость, поэтому содержание этих веществ не должно превышать 0,05 %. Легированные стали брать не рекомендуется, сварка их в условиях обычной кузницы почти невозможна. Положительно на качество сварки влияет добавление марганца. Также к сварочному флюсу рекомендуется добавлять опилки низкоуглеродистой стали. При горении они будут поглощать углерод, и сварка получится более прочной.
Нагрев под сварку
Перед началом сварки заготовкам необходимо придать определенную форму, которая зависит от сечения поковки. Поверхности очищают от окалины. Горн следует прочистить тщательнее, чем обычно, удалить всю старую золу. Нагрев должен быть равномерным и сильным.Температура, при которой можно проводить сварку, зависит от содержания углерода: чем оно выше, тем ниже температура. Низкоуглеродистую сталь можно варить при 1350–1370° С, когда заготовка становится ослепительно белой. Лучшим топливом является древесный уголь, так как содержание серы в нем невелико. При работе с кузнечным углем надо использовать те сорта, в которых содержится минимальное количество серы.
Флюсы
Даже при незначительном повышении температуры ковки (а она гораздо ниже сварочной) происходит интенсивное образование окалины и возможен пережог металла. Чтобы избежать нежелательного нагара при горновой сварке, раскаленные части заготовок посыпают специальным составом – флюсом. Используются и сварочные порошки, состоящие из кварца, поваренной соли и буры (Na2B4O7).Для сварки низкоуглеродистой стали в качестве флюса берут просеянный речной песок с добавлением буры. Если сталь конструкционная, в состав включают металлические и марганцевые опилки. Его насыпают на заготовку при температуре 950–1050 °C, что соответствует оранжевому или светло-желтому цвету металла. Делать это лучше до того, как металл начнет искриться. Попадая на разогретые концы, флюс плавится, вследствие чего предотвращается окисление и растворяется окалина.
Проверить готовность поковки можно тонким металлическим стержнем: если он вязнет в металле, то нагрев достаточный. Однако сразу после этого вынимать ее не рекомендуется, лучше подсыпать еще флюса и немного погреть заготовку.
После окончательного нагрева и непосредственно перед сваркой флюс удаляют с заготовки ударом о наковальню или счищают металлической щеткой.
Способы сварки
Вынув металл из горна и счистив шлак, концы заготовок складывают вместе и сваривают быстрыми ударами молота. Первые удары делают легкими, чтобы лучше пригнать поверхности и выбить шлак, последующими проводят окончательную сварку. В это время зернистость металла уменьшается, он становится более прочным.Заключительными ударами заготовке придают требуемую форму.
Всю сварку надо проводить быстро, чтобы металл не успел остыть. Повторное нагревание уже закаленного металла нежелательно. Часто для большей скорости сварку делают одновременно несколько человек.
Для окончательной отделки используют гладилки, обжимки и другие кузнечные инструменты.
Подготовка свариваемых концов зависит прежде всего от их толщины (рис. 154).
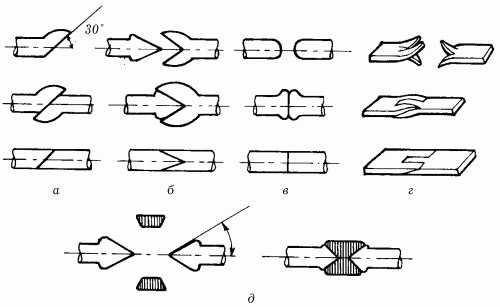
Поковки толщиной до 100 мм можно сварить внахлестку. Этот способ позволяет создать высокопрочный стык за счет большой площади совместной деформации.
Перед сваркой концы заготовок высаживают и делают плоскость контакта под углом 30–45° (рис. 154, а). Их накладывают друг на друга, совмещают несильными ударами, а затем проводят окончательную проковку с одновременной осадкой до нужной формы.
Толстые изделия сваривают вразруб, этот метод требует более сложной подготовки концов деталей. Один из них высаживается и надрубается зубилом по продольной оси, полученные части разгибаются под углом 30–40°. Другой конец после высадки заостряют с двух сторон так, чтобы он заполнял разруб первого (рис. 154, б).
Пустоты, образующиеся при вставке, ликвидируют холодной ковкой. Для учета раздачи металла при нагревании в промежуток между ними вставляют тонкие пластины. Нагретые и очищенные от флюса концы совмещают и сваривают сильными ударами. Затем, когда металл немного остынет, проводят окончательную отделку. Этот способ применяется при сварке сталей разных марок, причем металл меньшей пластичности вставляется в металл большей.
Тонкие полосовые заготовки сваривают врасщеп. Концы заготовок дважды разрубают вдоль продольной оси, после чего загибают в разные стороны, как показано на рис. 154, г. После доведения металла до нужной температуры детали соединяют, кладут на наковальню и сильными ударами сверху накрепко сваривают концы. Преимущество этого способа сварки в том, что соединение получается очень прочным.
Встык варят заготовки в том случае, если нет возможности подготовить концы указанными выше способами, а также тогда, когда стержень приваривается к продольной поверхности другой детали.
При подготовке осаживать концы деталей не надо, это происходит уже в процессе сварки. Заготовки соединяют встык и сильными ударами вдоль продольной оси доводят до образования прочного спая (рис. 154, в). Для этого другой конец обязательно должен быть холодным. После окончания работы проводят вытяжку.
По прочности сварки этот способ уступает всем остальным, его рекомендуется применять в тех случаях, когда не требуется создания прочных конструкций. Но для изготовления декоративных деталей он подойдет.
Для ремонта поврежденных деталей или частей металлических колец, которые теряют нужную форму из-за наложения, применяют способ сварки, выполняемый с помощью шашек. Так называются металлические вспомогательные части сварного узла, которые вставляют между концами заготовок. Вместе с последними они образуют участок полосы, по форме не отличающийся от целого (рис. 154, д).
Обычно шашки делаются из низкоуглеродистой стали, что повышает качество сварки. Удары делают сильными, по плоской поверхности спая. Можно разбить процесс на несколько этапов: сначала приварить шашки к концам заготовок, а потом проводить сварку так, как это делается способом внахлестку.
Сварка колец
Чтобы сварить кольцо из прутка круглого или прямоугольного сечения, необходимо предварительно согнуть его на роге наковальни (рис. 155).Рис. 155. Сварка колец: а – на роге; б – на наличнике.
Концы протягивают или отрубают под одинаковым углом и немного разводят в стороны. Сварку проводят при обычной температуре, на наковальне. Если срез делался в плоскости кольца, то оно отковывается на роге (рис. 155, а), а если в плоскости ребра – на плоской поверхности (рис. 155, б).
Пайка латунью
Она не относится к кузнечным операциям, но часто применяется для соединения небольших деталей художественных композиций из металла. Паять можно только изделия из поделочной стали, имеющие плоскую или квадратную форму. Круглые прутки соединяются плохо, так как имеют маленькую плоскость соприкосновения.Перед началом пайки изделие собирают, скрепляя его отдельные части металлической проволокой (биндрой). Затем его помещают в горн и нагревают до красного каления. Закладка должна производиться очень осторожно, место для изделия в углях расчищают кочергой. На решетке оставляют достаточно большой и ровный слой топлива. Подгребать уголь следует так, чтобы его кусочки не попадали на поковку. Дутье горна для равномерного прокаливания должно быть слабым.
В качестве флюса обычно используется бура, которую перед нанесением немного смачивают водой. Когда она растекается по всей поверхности, можно начинать пайку. Для этого прутком латуни, не снимая флюса, касаются тех мест, которые требуется соединить. При этом цвет пламени в горне меняется на зеленый. Передвигать изделие во время пайки нельзя, чтобы не сместить со своих мест отдельные детали.
Композиции, состоящие из многих элементов, сваривают иным образом. В местах пайки заранее раскладывают кусочки латуни с таким расчетом, чтобы при нагревании они растеклись и скрепили детали.
Наряду с кусочками латуни, можно использовать стружку или опилки, которые насыпают на места сварки. Они должны быть чистыми, от примесей железа их очищают с помощью магнита. Более мелкие изделия паяют, применяя в качестве скрепляющего материала глину с добавлением соли. Их собирают, соединяя отдельные части латунной, а не железной проволокой. Затем посыпают бурой, обмазывают глиной и осторожно кладут на металлический лист, который помещают в горн.
Дутье должно быть слабым, чтобы глина успела равномерно прогреться, после ее засыхания воздуха можно подавать больше. Когда она начинает трескаться, детали уже надежно скреплены. Латунная проволока начинает плавиться и спаивает отдельные части изделия.
После окончания процесса горн выключают, а готовой поковке дают остыть. Далее с нее аккуратно удаляют глину и флюс, лишний припой снимают напильником.
Правка
Заключительным элементом ковки изделия является правка. С ее помощью устраняют неровности, кривизну и пр.Изгиб заготовки
Он может проходить по плоскости заготовки или по ребру. В первом случае заготовку укладывают на наковальню выпуклой частью вверх, одной рукой поддерживают с противоположной стороны клещами, а с другой наносят молотом удары по прилегающей к наличнику части выступа. По мере выравнивания молот перемещают в сторону середины.Сила удара зависит от толщины заготовки. По мере выпрямления все большая его часть переходит в пластическую деформацию металла, что ведет к нежелательной протяжке. Поэтому к концу обработки размах молота постепенно уменьшают.
Изгиб по ребру исправляют растяжением выпуклой части металла. Заготовку ставят так, чтобы горб оказался сверху, и по нему наносят сильные удары кувалдой, которые при перемещении молота к одному из краев делают слабее. Нижнее ребро постепенно удлиняется, а верхнее, наоборот, уменьшается. Окончательную правку делают, переворачивая заготовку с одной стороны на другую. Если в поковке присутствуют сразу оба этих дефекта, то сначала устраняют неровность по плоскости, а затем по ребру.
В том случае, когда образуются дополнительные боковые деформации, заготовку переворачивают на другую сторону и выправляют.
Выглаживание
После того как все основные операции выполнены и форма изделия откована, приступают к отделке, или выглаживанию. Цель этой операции – устранить следы молотка, шероховатости и другие неровности кованой поверхности.Выравнивание поверхности производится с помошью гладилок с прямой или изогнутой рабочей частью. Для цилиндрических и граненых участков используют обжимки, для внутренних и вогнутых участков – специальные гладилки.
При операции выглаживания (рис. 156) постепенно перемещают гладилку по поверхности изделия, ударяя по ней кувалдой или ручником.
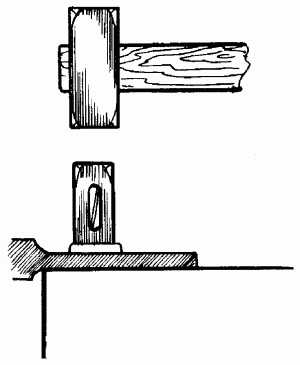
Поковку при этом размещают на наковальне так, чтобы отделываемый участок был над ней. В некоторых случаях для большей художественной выразительности нужно выглаживать только отдельные участки изделия (например, выпуклые участки). Прутки круглого сечения, выглаженные плоской гладилкой, будут казаться слегка граненными и лучше смотреться в ограде или орнаменте.
Термическая обработка готовых изделий
Термическая обработка проводится с готовой уже поковкой и служит для того, чтобы изменить структуру металла. От правильного ее выполнения зависит качество изделия и его долговечность.Закалка
Она предназначена для придания изделиям из металла большей прочности и твердости. Но следует помнить, что при этом они становятся хрупкими. Обычно закаливаются рабочие части инструментов и детали механизмов, подвергающиеся тяжелым нагрузкам. Изделия из низкоуглеродистой стали практически не меняют своих свойств после закалки, поэтому подвергают их термической обработке крайне редко.Нагрев
Деталь нагревают до температуры, превышающей на 30–70 °C температуру установления правильной кристаллической структуры. Время нагрева должно быть достаточным для установления равномерного строения во всем объеме металла. Оно зависит от размеров детали и ее формы, а также от сорта стали.Слишком длительная выдержка приводит к тому, что зерна металла увеличиваются, и он теряет прочность. Поэтому продолжительность выдержки ориентировочно берется равной 0,2 от времени нагрева. В горне деталь следует расположить так, чтобы холодный воздух из фурмы не попадал на ее поверхность. Для этого заготовку кладут на слой смешанного с золой угля.
Охлаждение
Очень важной частью закалки является охлаждение. От него зависит установление необходимой структуры металла.Скорость охлаждения не должна быть меньше 150 °C в секунду. Так как температуру заготовки целесообразнее всего доводить до 400–450 °C, то продолжительность процесса составляет лишь 2–3 секунды.
В качестве жидкостей для охлаждения используются вода и трансформаторное масло. В последнем скорость понижения температуры меньше, при нормальных условиях она не превышает 180 °C в секунду. В холодной воде охлаждение идет быстрее – примерно 600 °C в секунду.
При погружении раскаленной детали в жидкость очень важно, чтобы температура последней повышалась очень незначительно. Если объем ее небольшой, то увеличить конвекцию можно помешиванием.
Хороший результат дает закалка в проточной воде, так как при этом образующийся между заготовкой и жидкостью слой пара быстро рассеивается. Улучшить качество закалки можно добавлением в емкость поваренной соли, соды (до 10 %) или серной кислоты (до 12 %).
Когда требуется закалить только часть изделия, например рабочую часть инструмента, после опускания на необходимую глубину его несколько раз перемещают в вертикальном направлении, чтобы не образовалось трещин в промежуточной части.
При неправильном погружении в воду изделие может покоробиться от неравномерного охлаждения. Чтобы этого избежать, надо опускать детали в воду так, как это показано на рис. 157.
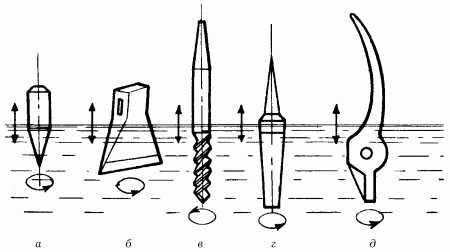
Скорость охлаждения так же, как и скорость нагрева, зависит от размеров заготовки и материала, из которого она сделана. Изделия из малоуглеродистых сталей охлаждают в воде, но если они имеют сложную форму, то лучше проводить процесс в масле, иначе на поверхности могут появиться трещины.
У заготовок большой площади сечения верхние слои охлаждаются быстрее нижних, поэтому закалка внешней части гораздо более сильная. Если сталь содержит легирующие элементы – такие, как марганец, хром и другие – то глубина закалки увеличивается.
Часто кузнецы выполняют закалку изделий сразу после ковки, что позволяет значительно экономить топливо. Для этого ковка выполняется с таким расчетом, чтобы после ее окончания металл имел температуру, при которой можно проводить закаливание.
Способы закалки
С понижением накала изделия скорость охлаждения тоже должна меняться. В интервале 650–450 °C она должна быть не больше 30 °C в секунду. Чтобы достичь такого режима, пользуются способом, который называется «через воду в масло».Заготовку опускают сначала на несколько секунд в воду, а затем быстро переносят в масло. Время выдержки составляет 1–1,5 секунды на каждые 5 мм сечения детали. Такой способ применяется для закалки инструментов, сделанных из низкоуглеродистой стали.
Часто у различных режущих инструментов требуется закалить только верхнюю поверхность, а середину оставить мягкой. В этом случае пользуются поверхностным способом закалки.
Изделие на короткий срок помещают в горн или раскаленную до 1000 °C печь, а затем подвергают быстрому охлаждению под проточной водой. При этом надо тщательно соблюдать температурный режим закалки, в противном случае не исключено образование трещин.
Закалка различается по интенсивности. Получить сильную степень можно с использованием охлажденной до 15–18 °C воды и добавками соли и соды.
Среднюю закалку дает погружение поковки в горячую воду, а также добавление нефти, мазута, жидкого минерального масла и пр. Эти материалы образуют на поверхности пленку толщиной до 3 мм, которая более плавно охлаждает деталь.
Закалка с использованием в качестве охлаждающего материала струи воздуха или расплавленного свинца получается самой слабой.
Таким способом закаливают художественные изделия и части несущих конструкций, требующих большой точности расположения частей.
Отпуск
После закалки изделия приобретают не только прочность, но и излишнюю твердость. За счет сохраняющихся в поковке закалочных напряжений появляются трещины. Если начать работу закаленным молотком, то от него будут откалываться маленькие кусочки металла, другие детали от ударов крошатся.Для устранения этих дефектов изделие необходимо подвергнуть отпуску. Эта операция после закалки обязательна и состоит в нагревании предмета до определенной температуры, выдерживании при ней в течение 10 минут и последующем медленном охлаждении. Она служит для придания металлу большей пластичности.
Перед началом отпуска поверхность зачищают. При нагревании она начинает покрываться тонкой оксидной пленкой, которая с увеличением температуры меняет свой цвет. По ней можно следить за сроком окончания отпуска.
При естественном освещении температуры соответствуют следующим цветам побежалости:
– 220 °C – светло-желтый;
– 230 °C – желтый;
– 240 °C – золотисто-желтый;
– 255 °C – коричнево-желтый;
– 265 °C – красно-коричневый;
– 275 °C – ярко-красный;
– 285 °C – фиолетовый;
– 305 °C – темно-синий;
– 325 °C – светло-синий;
– 345 °C – серый.
При высоких температурах поверхность металла покрывается темным налетом, который пропадает только после достижения отметки 600 °C, то есть с появлением цветов каления.
В зависимости от требуемых свойств и материала, из которого изготовляется деталь, используются разные виды отпусков.
Высокий отпуск
Так сокращенно называется высокотемпературный отпуск, при котором сильно увеличивается пластичность и почти полностью ликвидируются закалочные напряжения.Детали нагревают до 450–650 °C, выдерживают в зависимости от площади поперечного сечения 5–10 минут (полное прогревание) и охлаждают.
Углеродистую сталь можно охлаждать на открытом воздухе, а легированную – в воде, так как иначе металл не приобретет пластичности.
Следует отметить, что прочность стали при высоком отпуске значительно снижается. Поэтому данный способ не используют при изготовлении инструментов.
thelib.ru
Как согнуть полосу шестерку П-образно?
StepnoyA 01-09-2011 08:13Приветствую всех участников форума.
Нужна помощь мастеров и знающих металл специалистов.
Мне необходимо в условиях небольшой гаражной мастерской изготовит П-образный кронштейн из стандартной полосы 6х80 (ГОСТ 103-76, 3СП/ПС)
В дальнейшем два таких изделия закрепленных на вертикальной плоскости должны выдерживать периодическую нагрузку примерно до 400 кг.
1. Чем можно согнуть такую полосу? Что можно соорудить для гибки?
2. Возможен ли в местах гибки разрыв металла и какими способами можно это минимизировать?
Заранее спасибо!
P.S. Размеры: 400мм*70мм(полка)*200мм
ВАС-ВАС 01-09-2011 08:29паяльная лампа, газовая горелка + тиски + молоток кувалда ,газовая горелка может быть маленькой http://mirpiknika.ru/gazovaya_gorelka_portati
Viziter 01-09-2011 08:41Легче не гнуть а варить из отдельных деталей нарезанных болгаркой в условиях гаражной мастерской.
Garun 01-09-2011 08:47Вообще такую скобу можно загнуть что называется на “коленке”. Ну а если серьезно, то первый гиб делается в тисках, это просто. А для второго прийдется ченить приспособить. Как я понял один “хвост” скобы должен быть 400мм, а другой 200мм, если так то нужно заготовить металический или на крвйняк деревянный (дубовый) брусок соотвественных размеров. Вкладываете его в первый гиб, фиксируете в тисках и гнете второй гиб.
ВАС-ВАС 01-09-2011 08:50quote:
Легче не гнуть а варить из отдельных деталей нарезанных болгаркой в условиях гаражной мастерской.
всё зависит от нагрузки 6-ку лутше гнуть 10-ку варитьАлексей С 01-09-2011 09:54
Я бы по горячему стал такую полосу гнуть. Локальный нагрев места сгиба ацетиленовой горелкой – и вперед.
nailski 01-09-2011 10:00у нас когда на заводе мы вили пружины амортизаторные из 12мм прутка 65г
– то вили ни токарном станке но потом что бы убрать напряжение отдавали в термичку – ну там отпуск, закалка.
так что вариант с грелкой думаю что предпочтительнее.
Как вариант-надрезать болгаркой с внутренней стороны по линиям сгиба,согнуть и проварить.
StepnoyA 02-09-2011 07:14Спасибо всем за ваше участие в моей проблеме.
Кстати, может есть участники форума из Новосибирска, кто сможет непосредственно помочь данному процессу гибки?
Или может кто продаст/предоставит комплект газовой горелки?
quote:
Легче не гнуть а варить из отдельных деталей нарезанных болгаркой в условиях гаражной мастерской.
Согласен, сварить было бы проще, но нужна именно гибка.
Так задумано в проекте, менять решение нельзя.
Примерное решение уже вырисовывается
Зажать в тиски – греть – гнуть – мастерить приспособу – греть – гнуть
Осталось определиться чем греть.
Не очень хочется покупать оборудование для пропановой/ацетиленовой горелки
Дорого, да и в последствии может и не пригодиться.
Есть ли бюджетные варианты решения?
Паяльная лампа?
Маленькая горелка с одноразовыми баллончиками? (прогреет ли шестерку?)
Газовый паяльник?
Например: http://www.220-volt.ru/catalog-18607/
Такие газовые паяльники вам не помогут – мощность ничтожна, горелка понадобится довольно крупная. Посмотрите на горелки которыми крыши проваривают при укладке рубероида.
Например: http://www.pulscen.ru/predl/equipment/machcommon/weld/svarochnye_gorelki/46731
guns.allzip.org