Как загнуть арматуру стеклопластиковую: Как гнуть стеклопластиковую арматуру, чтобы она не ломалась и держала форму?
alexxlab | 31.01.2020 | 0 | Разное
Как гнуть стеклопластиковую арматуру, чтобы она не ломалась и держала форму?
4 2 01 Апреля 2019Стеклопластиковая арматура – легкий и надежный композитный материал, который успешно используется при возведении мостовых опор, тоннелей, бассейнов и даже огородных теплиц. Жгуты из стеклянных волокон очень прочные, но проблемные в использовании – их сложно согнуть. Как сделать это правильно?
Особенности и виды композитной арматуры
Стеклопластиковая арматура вошла в активное употребление в 70-х годах ХХ века. На момент изобретения она стоила в разы дороже металлической арматура, поэтому на постсоветском пространстве почти не применялся, зато был очень популярен в США и Европе.
- конструкций, контактирующих с водой и агрессивными веществами;
- сейсмоустойчивых сооружений и зданий для химпромышленности;
- промышленных и частных зданий любого назначения;
- армирования бетонных конструкций сеткой;
- создания канализации и бассейнов;
- опор для виноградников, теплиц;
- укрепления опор ЛЭП;
- дорожных покрытий;
- навесов и тентов.
Композитный стройматериал изготавливается из наполнителя (стеклянных, базальтовых или углепластиковых волокон, скрученных в жгут), и связующей синтетической смолы. Он легче металлических аналогов в 10 раз и прочнее в 4 раза, не боится влаги и химикатов, хорошо удерживает тепло, является диэлектриком и не требует сварочных работ.
Как работать со стеклопластиковой арматурой
Использование готовой композитной арматуры из стеклопластика может показаться затруднительным – ее (как и любую полимерную арматуру) практически невозможно согнуть в домашних условиях – готовый охлажденный стержень сломается или снова распрямится. Нагреть стеклопластиковую арматуру можно до +200°С, но она не размягчится. Температурного пика вещество достигает примерно при +550-600°С, и арматура просто оплавится. Поэтому гнуть стержни с помощью инструментов или строительного фена, как иногда советуют в сети, бесполезно и даже опасно.
Как же согнуть стеклопластиковый пруток?
Есть три варианта:
- Заказать у производителя готовую. В заводских условиях изготовить гнутый элемент из композита по чертежу заказчика «с нуля» не составит труда.
- Использовать стальные наконечники для композитных стержней. Наконечники крепятся к концам прутков цанговыми зажимами или химическими анкерами. Если нужно зафиксировать арматуру в согнутом состоянии, наконечники привариваются, и вы получаете нужную конструкцию.
- Сгибать одновременно соединенные металлические и стеклопластиковые прутья. Такая «связка» обеспечит нужный радиус и надежность.
Важно: сгибать стеклопластиковый стержень можно максимум полудугой – такие формы используют для создания навесов и теплиц. Кроме того, не любая арматура поддается сгибанию. Например, в бухтах поставляется арматура диаметром до 12 мм, а все, что толще, уже нарезается отрезками, необходимыми заказчику. Интересно: американский производитель композитной продукции MFX-BAR сообщает, что арматура его производства гнется намного свободнее, чем аналоги. Такой материал станет прорывом и практически заменит металл в строительстве.
Интернет-магазин Триколор предоставит консультацию по любому вопросу о стеклопластиковой арматуре. У нас вы купите продукцию для любых строительно-ремонтных потребностей по самой приятной цене в Украине.
Можно ли согнуть стеклопластиковую арматуру?
Можно ли согнуть композитную арматуру?
Готовая к использованию стеклопластиковая арматура, как и все армирующие элементы из композитных материалов, не подвергается сгибу в условиях строительной площадки. Гнутая стеклопластиковая арматура после снятия напряжения с композитного прутка не сохраняет требуемую форму и выпрямляется до исходного состояния. После отвердевания композита, который является связующим для волокон стеклопластика арматурного стержня, невозможно размягчить с последующим затвердеванием и сохранением всех свойств. Можно только полностью разрушить структуру материала, который становится непригодным к использованию.
Сформированный в заводских условиях арматурный стержень из композитных материалов может быть согнут на время. Но после снятия нагрузки гнутые элементы из стеклопластиковой арматуры самостоятельно выпрямляются и ведут себя как пружина. Сварка композитных армирующих материалов также исключается. Для соединения отдельных элементов можно использовать специальные клеевые составы.
На практике сгибание и соединение арматуры решается значительно проще. При необходимости использования гнутых элементов можно оформить их изготовление у производителя. По предварительной договоренности и при наличии чертежей гнутая композитная арматура любого размера и формы выполняется непосредственно на этапах производства армирующих элементов.
Помимо этого возможно использование гибридных каркасов, которые выполнены из стальных и композитных прутков. Применение такого каркаса не является редкостью в малоэтажном строительстве и при армировании бетонных изделий.
Очень часто на разных этапах строительства и производства стоит цель приварить гнутые элементы из стеклопластиковой арматуры к конструкции или выполнить преднапряжение композитных прутков. В этом случае единственным вариантом является использование композитной арматуры с предварительно установленными стальными наконечниками.
Стальной наконечник крепится к концам прутков двумя основными способами:
- При помощи специальных цанговых зажимов;
- С использованием химических анкеров.
Наконечники устанавливаются на композитные стержни необходимой длины в заводских условиях, после договоренности с производителями композитной арматуры.
Как гнуть композитную арматуру
Главная › Новости
Опубликовано: 01.09.2018
стеклопластиковая арматура смертельная особенностьСтатьи
Технология производства стеклопластиковой арматуры разработана ещё в 60-е годы XX века, но лишь в начале нового тысячелетия появилась возможность сделать её действительно доступной, недорогой. В году принят ГОСТ 31938- для композитной полимерной арматуры бетонных сооружений. В соответствии со стандартами ГОСТа номинальный диаметр композитных материалов от 4 до 32 мм. Наиболее востребованной считается арматура с сечением 6, 8 и 10 мм. Особенно удобно приобретение композитных материалов армирования большой длины в компактных и нетяжёлых бухтах.
В соответствии с ГОСТом недопустимы дефекты внешнего вида арматуры. Сколы, вмятины и расслоившиеся участки – признак недоброкачественной продукции.
Имеются ли недостатки у стеклопластиковой арматуры
Ждать абсолютного совершенства какого-либо строительного материала неразумно. Совершенства в мире нет и быть не может. Многочисленные достоинства АСП имеют оборотную сторону, с которой необходимо считаться.
как согнуть стеклопластиковую арматуру видео
Утверждение о дороговизне АСП верно только в том случае, если сравнивать стеклопластиковую и стальную арматуру одинакового диаметра.
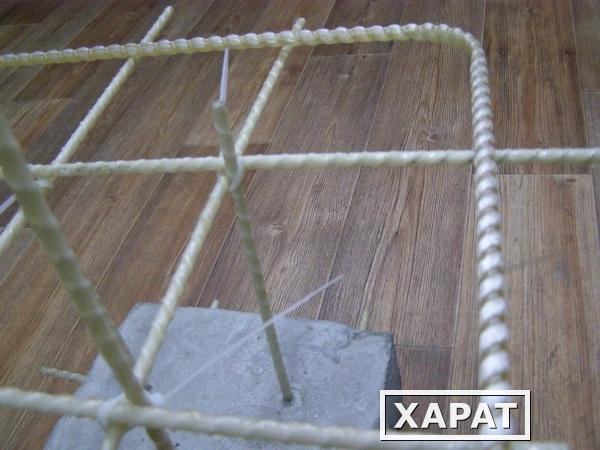

Чётко уяснив для себя «слабые» и «сильные» места стеклопластиковой арматуры можно выбрать области строительства, где её применение оправдано, целесообразно и очень выгодно.
При сооружении плитных и ленточно-заглублённых ниже уровня промерзания фундаментов на крепких грунтах. Плывучие слабые грунты вызывают повышение нагрузки на излом, которые стеклопластиковая арматура переносит хуже стальной. Востребована АСП в армировании кирпичных и блоковых конструкций. Стеклопластиком армируют не только стены, но используют для создания гибкой связи облицовочной стены с несущей. Для обустройства гибких связей в многослойных панелях. Идеально использование стеклопластиковой арматуры в несущих частях сооружений подверженных повышенной коррозийной опасности от воды или химически агрессивных реагентов. При укреплении береговых сооружений, для строительства бассейнов, водоотводов, дорожного полотна использование стеклопластика чрезвычайно эффективно.
Разумное и продуманное использование композитной арматуры позволяет увеличить эффективность строительства и значительно снизить расходы.
– СТЕКЛОПЛАСТИКОВАЯ АРМАТУРА
Можно ли согнуть композитную арматуру?
Готовая к использованию стеклопластиковая арматура, как и все армирующие элементы из композитных материалов, не подвергается сгибу в условиях строительной площадки. Гнутая стеклопластиковая арматура после снятия напряжения с композитного прутка не сохраняет требуемую форму и выпрямляется до исходного состояния. После отвердевания композита, который является связующим для волокон стеклопластика арматурного стержня, невозможно размягчить с последующим затвердеванием и сохранением всех свойств. Можно только полностью разрушить структуру материала, который становится непригодным к использованию.
Сформированный в заводских условиях арматурный стержень из композитных материалов может быть согнут на время. Но после снятия нагрузки гнутые элементы из стеклопластиковой арматуры самостоятельно выпрямляются и ведут себя как пружина. Сварка композитных армирующих материалов также исключается. Для соединения отдельных элементов можно использовать специальные клеевые составы.
На практике сгибание и соединение арматуры решается значительно проще. При необходимости использования гнутых элементов можно оформить их изготовление у производителя. По предварительной договоренности и при наличии чертежей гнутая композитная арматура любого размера и формы выполняется непосредственно на этапах производства армирующих элементов.
Помимо этого возможно использование гибридных каркасов, которые выполнены из стальных и композитных прутков. Применение такого каркаса не является редкостью в малоэтажном строительстве и при армировании бетонных изделий.
Очень часто на разных этапах строительства и производства стоит цель приварить гнутые элементы из стеклопластиковой арматуры к конструкции или выполнить преднапряжение композитных прутков. В этом случае единственным вариантом является использование композитной арматуры с предварительно установленными стальными наконечниками.
Стальной наконечник крепится к концам прутков двумя основными способами:
Наконечники устанавливаются на композитные стержни необходимой длины в заводских условиях, после договоренности с производителями композитной арматуры.
Как согнуть композитную арматуру
В строительстве и на производстве по достоинству оценили преимущества стеклопластиковой и другой композитной арматуры. малый вес, высокая прочность на разрыв, невосприимчивость к коррозии и агрессивной среде. Благодаря вышеперечисленным характеристикам данный материал активно применяется и позволяет сэкономить на устройстве арматурного каркаса по сравнению с использованием стальных стержней.
Несмотря на очевидные преимущества, известен и ряд некоторых недостатков, из-за которых зачастую применение данного материала не представляется возможным.
Изгиб композитной арматуры
Изготовленные композитные стержни невозможно согнуть непосредственно на строительной площадке — после снятия нагрузки арматура вернется в свое исходное состояние. Композит, который связывает волокна стержня не поддается повторному отверждению, поэтому арматура либо сохранит свою первоначальную форму, либо разрушится под действием нагрузки.
Существует два варианта решения данной проблемы:
заказ на изготовление стеклопластиковой арматуры у производителя по чертежам заказчика. На стадии производства композитным стержням можно придать абсолютно любую форму, которая будет сохраняться; использование гибридного каркаса с сочетанием композитных и металлических стержней. Данный вариант связанных каркасов довольно часто встречается в реальности и полностью себя оправдывает.Сварка композитных стержней
Стеклопластиковые стержни не поддаются электросварке. В полевых условиях данная проблема решается только с помощью склеивания изделий или применении других способов соединения элементов — хомутов или пластиковых зажимов.
Но электрическая сварка стеклопластиковой арматуры все же возможна. Данная задача решается путем установки специальных стальных наконечников, которые и выполняют роль свариваемого элемента. Наконечники устанавливаются в заводских условиях и крепятся к стержню с помощью специальных зажимов-цангов. Данный способ позволяет выполнить сварку или преднапряжение стеклопластикового элемента.
Таким образом, существует реальное решение проблем, которые могут возникнуть при эксплуатации композитной арматуры. Несмотря на возникающие неудобства, стеклопластиковая арматура является оптимальным решением для малоэтажного строительства, при котором ни одна из конструкций не подвержена ощутимо высоким нагрузкам. Армирование фундаментов стеклопластиковыми стержнями значительно снижает трудозатраты на монтаж и возведение конструкции, позволяет сэкономить на стоимости строительных материалов.
Источники: http://armatura-super.ru/articles/21-chego-boitsya-stekloplastikovaya-armatura, http://plast-komposit. ru/faq/gnutaya_stekloplastikovaya_armatura, http://alyans-stroy.perm.ru/poleznye-statyi/kak-sognut-kompozitnyu-armatyru/
Как согнуть композитную арматуру – Альянс-Строй
В строительстве и на производстве по достоинству оценили преимущества стеклопластиковой и другой композитной арматуры: малый вес, высокая прочность на разрыв, невосприимчивость к коррозии и агрессивной среде. Благодаря вышеперечисленным характеристикам данный материал активно применяется и позволяет сэкономить на устройстве арматурного каркаса по сравнению с использованием стальных стержней.
Несмотря на очевидные преимущества, известен и ряд некоторых недостатков, из-за которых зачастую применение данного материала не представляется возможным.
Изгиб композитной арматуры
Изготовленные композитные стержни невозможно согнуть непосредственно на строительной площадке — после снятия нагрузки арматура вернется в свое исходное состояние. Композит, который связывает волокна стержня не поддается повторному отверждению, поэтому арматура либо сохранит свою первоначальную форму, либо разрушится под действием нагрузки.
Существует два варианта решения данной проблемы:
- заказ на изготовление стеклопластиковой арматуры у производителя по чертежам заказчика. На стадии производства композитным стержням можно придать абсолютно любую форму, которая будет сохраняться;
- использование гибридного каркаса с сочетанием композитных и металлических стержней. Данный вариант связанных каркасов довольно часто встречается в реальности и полностью себя оправдывает.
Сварка композитных стержней
Стеклопластиковые стержни не поддаются электросварке. В полевых условиях данная проблема решается только с помощью склеивания изделий или применении других способов соединения элементов — хомутов или пластиковых зажимов.
Но электрическая сварка стеклопластиковой арматуры все же возможна. Данная задача решается путем установки специальных стальных наконечников, которые и выполняют роль свариваемого элемента. Наконечники устанавливаются в заводских условиях и крепятся к стержню с помощью специальных зажимов-цангов. Данный способ позволяет выполнить сварку или преднапряжение стеклопластикового элемента.
Таким образом, существует реальное решение проблем, которые могут возникнуть при эксплуатации композитной арматуры. Несмотря на возникающие неудобства, стеклопластиковая арматура является оптимальным решением для малоэтажного строительства, при котором ни одна из конструкций не подвержена ощутимо высоким нагрузкам. Армирование фундаментов стеклопластиковыми стержнями значительно снижает трудозатраты на монтаж и возведение конструкции, позволяет сэкономить на стоимости строительных материалов.
Часто задаваемые вопросы – ТатАрма
Как вязать стеклопластиковую арматуру?Нейлоновыми стяжками или отожженной проволокой диаметром 0,8—1,2 мм вручную, при помощи вязального крючка или пистолета. Для соединения арматуры также могут быть использованы специальные пластиковые клипсы.Какая арматура лучше металлическая или стеклопластиковая?
Стеклопластиковая арматура превосходит металлическую при армировании конструкций, подвергающихся растягивающим усилиям, а уступает ей при преобладающих сдвиговых нагрузках.Как согнуть (гнуть) стеклопластиковую арматуру?![]()
Сгибать стеклопластиковую арматуру с превышением минимально допустимого радиуса нельзя. Гнутые элементы могут быть изготовлены по чертежам на заводе. Формирование углов при армировании следует выполнять вязкой отдельных прямых прутов или с помощью готовых элементов.Как армировать стеклопластиковой арматурой?
Невысокий слой бетона армируется одной сеткой из связанных прутов, уложенной на специальные пластиковые фиксаторы требуемой высоты. Для объемных конструкций с помощью перемычек формируют каркас из нескольких сеток, установленных на ребро или расположенных одна над другой.Как размотать стеклопластиковую арматуру?
Как делают стеклопластиковую арматуру?Следует надежно зафиксировать один из концов стержня и, удерживая бухту в вертикальном положении, раскатать смотанный отрезок в прямую линию на ровной поверхности
Как соединить стеклопластиковую арматуру?Пропитывают отдельные жгуты стеклоровинга термореактивными связующими веществами и формируют из них цилиндрический прут. После чего обматывают его еще одним перекрученным жгутом и протягивают через туннельную печь, в которой смола полимеризируется
Как сделать теплицу из стеклопластиковой арматуры?Стеклопластиковая арматура позволяет формировать каркас цельными прутами, без составных частей. Пересекающиеся стержни соединяются между собой пластиковыми стяжками, отожженной вязальной проволокой или специальными клипсами. Если без составных частей обойтись не удается, они соединяются внахлест, с перекрытием порядка 100 диаметров используемой арматуры
Как сделать парник из стеклопластиковой арматуры?Высота теплицы должна позволять стоять в ней в полный рост. Из стеклопластиковой арматуры практичнее делать арочные или пристенные полуарочные конструкции. Для капитальных теплиц обустраивается армированный композитом ленточный фундамент, в котором до заливки бетона закрепляются концы дуг из арматуры. Для разборных конструкций используют отрезки пластиковых или стальных труб в виде закладных деталей. Крепление к стене осуществляют при помощи деревянного бруса с отверстиями под концы дуг
Как правильно монтировать стеклопластиковую арматуру?Высота парника обычно лежит в пределах от 0,5 до 1,5 метра. Концы дуг могут быть воткнуты непосредственно в землю. Практичнее всего для их закрепления изготовить из деревянного бруса прямоугольную раму необходимого размера со сквозными отверстиями
Отрезаются пруты необходимой длины, маркером намечаются места крепления, раскладываются на ровной поверхности и соединяются перемычками в сетку с помощью хомутов или проволоки. Для объемных каркасов готовые сетки связываются между собой
Как правильно вязать стеклопластиковую композитную арматуру
Как правильно вязать стеклопластиковую композитную арматуру – описание
Бетон является очень качественным и надежным материалом, однако если он используется для фундамента при его заливке необходимо задействовать дополнительный каркас, усиливающий прочность. Самым современным и качественным материалом для вязки армирующего каркаса фундамента является композитная стеклопластиковая арматура производства ООО “ОБНИНСКИЙ ЗАВОД КОМПОЗИТНЫХ МАТЕРИАЛОВ”. Вязка арматуры для фундамента должна проводиться в соответствии с установленными требованиями. Ниже подробно описан метод осуществления данного процесса.
Стеклопластиковая арматура состоит из крепкого стекловолокна и связующей термопрочной смолы. Арматуру легко транспортировать и соединять между собой, стоит она на порядок дешевле металлической. Выпускается она двух видов: гладкая и ребристая. Обладает антикоррозийными свойствами, очень прочная и способна выдержать большие нагрузки.
Арматурный каркас представляет собой прямоугольную ячеистую конструкцию, попадая в которую бетон не растекается, не образует пустот и пузырей. Для того, чтобы правильно собрать его, следует знать, как правильно вязать стеклопластиковую арматуру.
Пошаговые действия для вязания стеклопластиковой композитной арматуры
Вам потребуется обыкновенная вязальная проволока, которую можно приобрести на любом строительном рынке или пластиковые хомуты. Вот несколько простых рекомендаций, с помощью которых вы сможете легко осуществить данный процесс самостоятельно:
- Для поперечных прутьев нижнего слоя из стеклопластиковой арматуры используются специальные арматурные фиксаторы. Их можно установить уже в начале работы, предварительно вымерив размер ячеек, или после того, как каркас будет собран.
- Расстояние между горизонтальными и вертикальными линиями сетки зависит от типа основания постройки. Как правило, оно колеблется в пределах от 15 до 35 см. Эти размеры предполагает схема вязки арматуры для ленточного фундамента. В редких случаях расстояние доходит до 60 см.
- Долевые прутья разложите на необходимом расстоянии друг от друга и нанесите на них метки при помощи маркера. К ним хомутами или проволокой прикрепите под прямым углом перемычки.
- Перемычки крепите к каркасу не сверху, а снизу. Хомуты или проволоку затягивайте потуже, чтобы они не разошлись в процессе заливки цементно-песчаной смеси. Помните о том, что это напрямую влияет на конечную прочность фундамента.
- После того, как первый ряд сетки будет готов, можно приступать к остальным составляющим каркаса. Перпендикулярные перемычки необходимо крепить таким же образом с внутренней стороны ячеек. Так вы получите надежную конструкцию, которая не разъедется во все стороны во время заливки бетона.
- Особое внимание уделяется углам. У многих возникает вопрос – как правильно вязать стеклопластиковую арматуру в этих местах, если гнуть ее не рекомендуется? В специализированных магазинах сегодня можно приобрести готовые элементы, которые легко устанавливаются перед началом работ или во время сборки каркаса. Если такой возможности нет, то помните о том, что в углах допускается только вязка своими руками арматуры и без какого-либо теплового воздействия.
Процесс вязания стеклопластиковой арматуры прост и не займет много времени даже у неподготовленного человека.
Удачи в строительстве!
Стеклопластиковая арматура – применение, достоинства и недостатки
Давайте попробуем в этом разобраться и определиться, где применение стеклопластиковой арматуры оправдано, а где нет.
Связывается такая арматура практически также, как и обычная – с помощью крючка для вязки арматуры.
Теперь давайте разберемся во всем по порядку – сначала рассмотрим достоинства и недостатки стеклопластиковой арматуры, а затем, основываясь на них, определим, где ее применение будет целесообразным. В конце статьи я расскажу о своем личном мнении по поводу применения стеклопластиковой арматуры.
Как и у любого строительного материала, у стеклопластиковой арматуры есть свои как достоинства, так и недостатки по сравнению с аналогичной металлической, которые могут стать серьезным подспорьем или помехой в применении ее в различных областях строоительства.
Давайте, наверное, начнем с достоинств:
Достоинства стеклопластиковой арматуры
1. Небольшой удельный вес. Это достоинство позволяет применять ее в легких конструкциях, таких, например, как ячеистый бетон и т.п. Это свойство стеклопластиковой арматуры позволяет снизить массу всей конструкции.
Стоит отметить, что применение стеклопластиковой арматуры в обычном бетоне не будет так же значительно влиять на массу конструкции, учитывая то, что основной вес будет давать сам бетон.
2. Низкая теплопроводность. Как известно, стеклопластик проводит через себя тепло значительно хуже, чем металл.
Это достоинство стеклопластиковой арматуры позволяет применять ее там, где необходимо сократить мостики холода, которые так замечательно создает стальная арматура.
3. Упаковка в бухтах. Для строительства частных домов это очень весомое достоинство стеклопластиковой арматуры, потому что на ее доставку к участку можно не тратиться, а, как известно, при постройке дома, особенно если строите своими руками, каждая копейка на счету.
В добавок к вышесказанному можно добавить, что применение стеклопластиковой арматуры в бухтах уменьшает ее расход, так как в арматурном каркасе нахлестов практически не будет, а это так же позволит немного снизить финансовые расходы.
4. Долговечность. Производители основываются на том факте, что стеклопластик, по сравнению с металлом, гораздо долговечнее.
Это немного сомнительное достоинство стеклопластиковой арматуры, учитывая то, что металл внутри бетона практически не подвержен коррозии и внутри железобетонной конструкции также прослужит очень долго.
5. Диэлектрическая. Это свойство, скорее всего, в частном строительстве не дает никаких достоинств стеклопластиковой арматуры над металлической, но о нем тоже не стоит забывать.
6. Устойчивость к химическим воздействиям. Это означает, что в кислых и других агрессивных химических средах стеклопластиковой арматуре намного комфортнее чем стальной.
В малоэтажном частном строительстве это достоинство стеклопластика, так же, как и предыдущее, практически не играет никакой роли, за исключением строительства зимой, когда в раствор или бетон добавляют различные соли, пагубно воздействующие на металл.
7. Радиопрозрачность. Это означает, что стеклопластиковая арматура не создает никаких радиопомех, в отличие от металлических контуров, создаваемых стальной арматурой.
Такое достоинство стеклопластиковой арматуры как радиопрозрачность, будет играть значительную роль только в том случае, если в стенах вашего дома много арматуры. Тогда применение стеклопластиковой арматуры уменьшит радиопомехи внутри дома.
В достоинствах разобрались, теперь давайте рассмотрим недостатки стеклопластиковой арматуры, применяемой в строительстве.
Недостатки стеклопластиковой арматуры
У любого материала есть недостатки и стеклопластиковая арматура – не исключение.
1. Стеклопластиковая арматура дороже обычной стальной если сравнивать арматуру одинакового диаметра.
2. Термически не устойчива. Стеклопластиковая арматура не выдерживает высоких температур.
Так же сомнительный недостаток, потому как в малоэтажном частном строительстве я даже не могу представить ситуацию, где будет необходимо нагреть арматуру до 200 градусов.
3. Не гнется. Таким образом, если нам понадобится, например, согнуть арматуру под углом 90 градусов, мы этого сделать не сможем. Хотя с другой стороны – мы можем все изгибы сделать из обычной стальной и нарастить их со стеклопластиковой.
4. Низкий модуль упругости на излом. Это означает, что стеклопластиковая арматура не выдерживает на излом таких же нагрузок, как металлическая.
Многие производители утверждают обратное – что модуль упругости у стеклопластиковой арматуры больше, но это, скорее всего, они имеют ввиду растяжение, а бетон, как правило подвержен больше нагрузкам именно на излом. Это основной недостаток, из-за которого ограничивается применение стеклопластиковой арматуры в строительстве.
5. Трудность в сооружении жесткого арматурного каркаса. Другими словами, каркас из стеклопластиковой арматуры не такой жесткий как из металлической, и, соответственно, менее устойчив к вибрации и нагрузкам, которые будут присутствовать при заливке бетона с автомобильного миксера.
Вот мы и рассмотрели практически все основные достоинства и недостатки стеклопластиковой арматуры. Судя по ним, невозможно с большой уверенностью сказать, что она значительно лучше или хуже металлической арматуры, поэтому давайте рассмотрим в каких строительных конструкциях и сооружениях применение стеклопластиковой арматуры будет оправдано и целесообразно.
Применение стеклопластиковой арматуры оправдано в некоторых случаях как в промышленном строительстве, так и в частном малоэтажном.
По поводу промышленного строительства, я думаю, говорить много не стоит, все же сайт посвящен строительству домов своими руками, поэтому давайте разберем область применения стеклопластиковой арматуры в частном малоэтажном строительстве.
1. Стеклопластиковая арматура применяется в некоторых типах фундаментов, таких как ленточный – заглубленный ниже глубины промерзания, плитный фундамент.
Стоит отметить, что это касается только малоэтажного частного строения, на хорошем грунте. На плывучих грунтах будут повышенные нагрузки на излом, которые стеклопластиковая арматура может не выдержать.
2. Целесообразно применение стеклопластиковой арматуры в армировании кирпичных стен, стен из блоков, очень часто можно встретить армирование стен из газосиликатных блоков стеклопластиковой арматурой.
Применение стеклопластиковой арматуры в армировании стен очень популярно среди застройщиков. Причем применяется такая арматура как элемент армирования самих стен, так и в качестве связки облицовочной стены с несущей.
3. В многослойных панелях в качестве связей. Так как внутри панелей, как правило присутствует плотный утеплитель, для связки между собой бетонных частей и используется стеклопластиковая арматура.
4. Оправдано применение стеклопластиковой арматуры в несущих частях элементов, подверженных повышенной коррозии, бассейнов, например.
5. Также стеклопластиковая арматура широко применяется в армировании клееных деревянных балок, увеличивая их жесткость.
6. Армирование асфальта, в местах повышенных нагрузок, хотя я такого еще ни разу не видел.
Как видите, область применения стеклопластиковой арматуры в строительстве довольно широка, хотя и присутствуют кое-какие ограничения.
Мнение автора о применении стеклопластиковой арматуры в строительстве
Я считаю, что стеклопластиковая арматура пока не способна полностью заменить металлическую, но это не значит, что ею можно совсем пренебречь.
Я широко применяю ее в строительстве стен из блока и кирпича, также в качестве связей облицовочной стены с несущей, так как при применении металла в качестве связей, во-первых, он будет подвержен коррозии, ну а во-вторых, металл создает мостики холода, которые в современном строительстве крайне нежелательны.
Применение стеклопластиковой арматуры в фундаменте так же оправдано, если у вас нетяжелая постройка, например, каркасный дом или гараж.
Если же на участке слабый грунт и предвидятся огромные нагрузки на фундамент, я бы не стал рисковать с применением арматуры, у которой упругость на излом меньше чем у металлической.
Как согнуть бетон, армированный стекловолокном
Эрик Шеффер из Majestic Concrete Design и Билл Шитц из Polytek Development Corp. снимают решетчатую панель с цилиндрической формы. Фото Денни Бойера, Polytek Development Corp.Большинство людей не думают о бетоне как о гибком, но это так, даже в его затвердевшем состоянии. Тем не менее, сгибание и деформация бетона более управляема, пока он еще находится в пластичном состоянии. Одна часть привлекательности деформируемого бетона – это крутой фактор, а другая часть – это экономия времени и труда.В случае деформации бетона по сравнению с отливкой в трехмерных формах преимущество заключается в значительной экономии средств.
Формы
Формы из полиуретановой резины настолько полезны, что их можно было изобрести для деформации бетона. Резиновые формы просты в изготовлении, очень гибкие (в зависимости от твердости используемой резины) и очень прочные. Мне нравится резина Poly 74-45 от Polytek Development Corp. для резиновых форм с плавными изгибами и без поднутрений, и Poly 74-20 (который немного мягче) для форм с очень крутыми изгибами и множеством деталей, таких как элементы решетки. показано на фотографиях.
Я делаю мастеров по отливке резиновых форм из фанеры ДВП средней плотности. МДФ не имеет какой-либо зернистой структуры, поэтому его легко обрабатывать или шлифовать. Покройте необработанный МДФ лаком, чтобы закрепить его. Затем, перед заливкой резины, нанесите пару слоев воска Johnson’s paste и отполируйте. Дайте каучуку день, чтобы застыть, и вы готовы к отливке. Если вы внимательно к ним относитесь, ваших форм хватит на сотни отливок.
Смесь
Давайте посмотрим на отливку GFRC без лицевого покрытия и без видимых волокон.Большинство мелких производителей и все большее число крупных производителей GFRC используют методы премикса GFRC. При использовании технологии предварительного смешивания лицевое покрытие без волокон распыляется или распыляется на форму, а заднее покрытие с волокнами наносится вручную или распыляется на форму. В методах распыления на форму распыляется лицевое покрытие без волокон, а стекловолокно разрезается с помощью рубильного пистолета с ровницей и смешивается с струей раствора для образования заднего покрытия.
В обоих методах используется лицевое покрытие без волокон, но мы пошли еще дальше и отказались от лицевого покрытия.Вот объяснение того, почему и как это работает:
У всего есть удельный вес. Это измерение показывает, сколько весит данный объем чего-либо по сравнению с данным объемом воды. Вода имеет удельный вес 1, а сталь, например, имеет удельный вес около 7,8 (в зависимости от марки). Это означает, что данный объем стали весит в 7,8 раз больше, чем тот же объем воды. Когда вы бросаете кусок стали в воду, сталь тонет.
Когда вы смешиваете предметы с разной удельной массой, они будут разделяться (расслаиваться) на разные слои, если смешивающая среда позволяет это происходить.Сделайте смесь слишком жидкой, добавив слишком много воды или слишком много пластификатора, и вы получите отдельные слои. Вы можете воспользоваться этим, позволяя этому происходить очень незначительно и в контролируемых условиях.
Материалы в вашей смеси имеют разную плотность. Цемент – 3,15, песок – обычно около 2,62, вода – стандарт 1, а большинство пуццоланов – около 2,5. Хорошая новость заключается в том, что стекловолокно имеет удельный вес 2,5. Это означает, что при правильных условиях стекловолокно не останется на поверхности вашей отливки.
В очень текучей смеси цемент оседает на дно, песок оседает поверх цемента, затем идут стекловолокно и пуццоланы (примерно такой же удельный вес), а слой воды находится сверху. Очевидно, что мы не хотим, чтобы смесь полностью расслаивалась, иначе полученный бетон будет очень непрочным.
Ваша задача – позволить стекловолокну хоть немного отойти от лица, не расслаивая смесь. Вы можете сделать это, добавив триновый пластификатор, чтобы сделать смесь более жидкой, слегка взбалтывая смесь или используя их комбинацию.Стекловолокно все равно будет видно, если вы отшлифуете кусок, но вам будет трудно увидеть какое-либо волокно, если вы пропустите полировку.
Это также отличный метод для использования при заливке бетонной плитки или стеновых панелей. Я называю это «свалил и готово». Значительная экономия времени по сравнению с нанесенным распылением и отложенным вручную пальто.
Когда Trinic провела независимые испытания нашей добавки, мы изготовили образцы купонов, используя эту технику. Результаты показали, что самоуплотняющаяся смесь GFRC в пропорции с добавкой GFRC и пластификатором Trinic имеет прочность, равную прочности предварительно смешанной смеси GFRC, которая укладывается вручную и раскатывается для уплотнения.Это открывает целый новый мир возможностей для производителей GFRC.
Когда сгибать
Когда вы изгибаете бетон в пластичном состоянии, вы разрываете связи первоначального набора, пока не стало слишком поздно для их заживления. Слишком рано изгибайтесь, и бетон оседает. Слишком поздно гнуться, и он треснет. Согните в нужное время, и он будет сгибаться без каких-либо негативных последствий.
По мере того, как бетон достигает своего первоначального состояния, он начинает переходить из пластичного состояния в затвердевшее.Окно для изгиба обычного неускоренного бетона на основе портландцемента прослужит около 15 минут при температуре 90 градусов по Фаренгейту и дольше при температуре 60 градусов. Проблема в том, что «сгибаемое окно» может появиться в течение часа или более при 90-градусном дне, и, возможно, до трех часов при 60-градусном дне.
Чтобы ускорить процесс, мы заменяем часть портландцемента на цемент CSA. Цемент CSA, или цемент на основе сульфоалюмината кальция, схватывается намного быстрее, чем обычный портландцемент.Сколько вы замените, зависит от партии и температуры окружающей среды. Замена 20% в мастерской с углом наклона 80 градусов приведет к деформации примерно через 15 минут после литья. Замена 40 процентов может потребоваться для той же производительности в 50-градусной мастерской. Сделайте небольшие образцы, чтобы оценить время схватывания, иначе вы можете обнаружить, что партия нагревается и начинает схватываться, пока вы ее перемешиваете.
Чтобы увидеть, готов ли ваш бетон изгибаться, слегка приподнимите край формы и следите за проседанием.Я предпочитаю гнуть бетон, чтобы не растрескаться. Покройте бетон пластиком, как только он будет деформирован, чтобы предотвратить потерю влаги во время отверждения. При использовании смеси портланд-CSA вы сможете снять кусок в тот же день, когда оно было отлито.
Mix Design для гибкого бетона
Следующая смесь составляет около 1 кубического фута – этого достаточно, чтобы отлить 16 квадратных футов при толщине 3/4 дюйма.
62 фунта вяжущих ингредиентов
Портландцемент можно смешивать с цементом CSA.
Начните с 80-процентного портала, 20-процентного CSA и при необходимости работайте с дополнительным CSA.
62 фунта песка
Мне нравится песок размером от 30 до 50 меш. Смесь
40-50 работает очень хорошо.
18 фунтов воды
Это даст вам соотношение воды и цемента 0,29.
Не переживайте, если вы используете немного больше или немного меньше.
1,86 фунта Trinic GFRC Admix (3 процента цементной массы)
62 фунта цемента, умноженные на 3 процента = 1.86 фунтов
От 0,31 до 0,62 фунтов тринового пластификатора (от 0,5 до 1,0 процента цементирующей массы)
Начните с 0,5 процента.
Чем мельче песок, тем больше требуется для поддержания текучести. 3,72 фунта стекловолокна A R (общий сухой вес партии [124 фунта], умноженный на 3 процента)
200 пучков 1/2 дюйма или 3/4 дюйма подойдет.
Приобрести готовые формы для деформации бетона:
www.ej3inc.com
сооружений – Школа аэронавтики и астронавтики
Пропустить навигациюБыстрые ссылки
- Найти информацию для
- Текущие студенты
- Абитуриенты
- Выпускники и друзья
- Взаимодействуйте с Purdue
- Карьера
- Исследования и инновации
Быстрые ссылки
- Применить
- Новости
- Президент
- Магазин
- Посетите
- Дайте
- Скорая помощь
Меню
- Школы
- Инженерный колледж
- Аэронавтика и космонавтика
- Сельскохозяйственная и биологическая инженерия
- Биомедицинская инженерия
- Химическая промышленность
- Гражданское строительство
- Строительное проектирование и менеджмент
- Электротехника и вычислительная техника
- Инженерное образование
- Purdue Интернет
- Экологическая и экологическая инженерия
- Промышленное проектирование
- Материаловедение
- Машиностроение
- Ядерная инженерия
- Программ
- Инженерная программа с отличием
Замена стальной арматуры на арматуру из стеклопластика в бетонных конструкциях
Реферат
Полимер, армированный стекловолокном (GFRP), был подтвержден как решение, являющееся основным шагом вперед в технологии усиленного бетона .Синтез арматуры GFRP с использованием продольных стекловолокон (армирующий материал) и ненасыщенной полиэфирной смолы с 1% МЕКП (матричный материал) посредством ручного процесса. Арматура из стеклопластика имеет диаметр 12,5 мм (это значение эквивалентно 0,5 дюйма; это наиболее распространено при применении для фундаментов). Поверхности из стеклопластика модифицированы добавлением крупного песка для увеличения прочности сцепления арматуры с бетоном. Затем выполняются механические характеристики железобетона с арматурой из стеклопластика и сравниваются с характеристиками стальной арматуры.Приготовление образцов бетона (неармированный бетон, гладкий армированный стеклопластик, железобетон из стеклопластика с песчаным покрытием и железобетон) с фиксированным соотношением ингредиентов (1: 1,5: 3) и соотношением Вт / Цельсия 0,5 проводили при двух периодах выдержки (7 и 28) дней при температуре окружающей среды. Величина объемной доли стеклопластика и стальной арматуры в железобетоне была (5 об.%) Равномерно распределена с заданными расстояниями в кристаллизаторе. Результаты показывают, что прочность на разрыв арматуры из стеклопластика составляет 593 МПа, а прочность на изгиб – 760 МПа.Прочность на сжатие бетона находилась в разумных пределах – 25,67 МПа. Прочность на изгиб неармированного бетона составляет 3 МПа, а армированного бетона с арматурой GFRP, особенно GFRP RC с песчаным покрытием, прочность на изгиб составляет 13,5 МПа, в результате чего увеличивается сцепление с бетоном и более высокая деформация составляет 10,5 МПа за 28 дней, чем у железобетона. за счет модуля упругости при изгибе.
Ключевые слова
Арматура из стеклопластика
Стальная арматура
Железобетон
Механические свойства
Рекомендуемые статьиЦитирующие статьи (0)
Просмотреть аннотацию© 2018 Авторы.Производство и хостинг выполняются Elsevier B.V. от имени Университета Кербалы.
Рекомендуемые статьи
Ссылки на статьи
Основы стекловолокна | Фибер Гласт
Хотите проверить свои знания стекловолокна?
Примите наши основы викторины из стекловолокна!
Введение
- Фото предоставлено IStock Photo.
Композиты – это материалы, состоящие из отдельных компонентов, общая физическая прочность которых превышает свойства каждого из них по отдельности.В случае композитных ламинатов используются два основных элемента: волокнистое армирование (например, стекловолокно или углеродное волокно) и смола. Эти два элемента не предназначены для использования исключительно – они предназначены для объединения. При этом они соединяются механически и химически, образуя твердую ламинатную деталь, которую невозможно реформировать.
Представьте себе лодку. Многие лодки сделаны из стекловолокна, которое начинается с ткани – как длинный кусок ткани, который сворачивается в рулон. Стекловолокно закладывается в форму, из которой создается корпус лодки.Смола в жидкой форме катализируется и наносится на стекловолокно в форме. Он отверждается и химически связывается со стекловолокном, выделяя большое количество тепла (так называемое термоотверждение). Здесь задействовано несколько слоев и различные техники, но конечный результат – лодка.
Композиты, как и лодка, популярны по ряду причин, но в основном из-за их высокой прочности и небольшого веса. Как правило, их можно адаптировать для различных областей применения и придать им уникальные и сложные формы.Они также популярны благодаря своей превосходной стойкости к большинству сред и могут использоваться большинством производителей без значительных вложений.
Мы рассмотрим ряд арматур и смол, из которых можно выбрать. Во-первых, давайте взглянем на реальные примеры продуктов из волокон и смол, чтобы вы лучше познакомились с отраслью композитов. После этого мы рассмотрим некоторые основные термины, которые вы услышите при работе с композитами.
Глоссарий составных терминов
Формование: Формование – это процесс создания детали внутри формы.Обычно предварительно вырезанную арматуру помещают в форму по одному слою и пропитывают смолой. Когда деталь достигнет желаемой толщины и ориентации, ее оставляют для отверждения. После извлечения из формы он будет иметь точную форму поверхности формы.
Ламинирование: Ламинирование первоначально относилось к нанесению тонкого защитного покрытия из смолы и армирования на такую поверхность, как дерево. Использование этого термина расширилось и теперь включает практически любую готовую композитную деталь, формованную или иную.Текущий пример: «Тестируемая деталь представляла собой 10-слойный ламинат, упакованный в вакуумный мешок».
График ламинирования: Это список отдельных слоев и ориентации слоев, используемых для создания составной детали, и обычно указывает вес армирования в унциях и стиль переплетения.
Отливка: Отливка означает заливку большой массы смолы в полость. Полость может быть формой при отливке деталей или может быть задним наполнителем для инструмента при изготовлении самой формы.Необходимо использовать специализированные литейные смолы, которые при отверждении выделяют меньше тепла и, таким образом, создают меньшую деформацию конечной детали. При необходимости можно добавлять волокнистые наполнители для усиления отливки.
Лепка: Лепка обычно выполняется путем вырезания формы из пенополиуретана и последующего ламинирования поверхности. Это может быть сделано для создания заглушки для процесса формования или для придания формы готовой детали в случае конструкции без формы.
Типы, свойства и стили армирования
Физические свойства композитов являются определяющими.Это означает, что при объединении смолы и волокна их характеристики больше всего соответствуют свойствам отдельных волокон. Например, недостаточно просто усреднить прочность на разрыв ткани и смолы для определения прочности панели. Данные испытаний показывают, что волокнистая арматура является компонентом, несущим большую часть нагрузки. По этой причине выбор ткани имеет решающее значение при проектировании композитных конструкций. Сегодня производители выбирают из трех распространенных армирующих материалов, включая стекловолокно, углеродное волокно и кевлар.Каждый из них имеет различные формы и стили, а также имеет свои преимущества и недостатки, которые следует проанализировать перед тем, как начинать какой-либо проект.
Выше у нас были примеры каждого из наиболее распространенных применений и характеристик. Теперь давайте подробнее рассмотрим их физические свойства.
Ниже приводится таблица, в которой сравниваются относительные свойства армирующих тканей. Легенда гласит: P = плохо, F = удовлетворительно, G = хорошо, E = отлично.
Технические характеристики | Стекловолокно | Углерод | Кевлар® |
---|---|---|---|
Плотность | P | E | E |
Прочность на разрыв | F | E | G |
Прочность на сжатие | G | E | P |
Жесткость | F | E | G |
Сопротивление усталости | G-E | G | E |
Сопротивление истиранию | F | F | E |
Шлифование / обработка | E | E | P |
Электропроводность | P | E | P |
Термостойкость | E | E | F |
Влагостойкость | G | G | F |
Совместимость смол | E | E | F |
Стоимость | E | P | F |
Формы армирования
Эти три усиления можно купить во многих формах и стилях плетения.Все три, как правило, доступны в виде жгутов (чисто однонаправленных волокон), вуалей и тканых материалов. Стекловолокно также предлагается в виде матов из прессованных рубленых прядей.
Буксировка и ровинг
Материал в этой форме демонстрирует наивысшие свойства, достижимые для данного семейства волокон. Как правило, они поставляются на катушках, чтобы их можно было подавать в намотчики волокон или разматывать и резать, если они необходимы для избирательного повышения жесткости. Волокна должны оставаться в натянутом состоянии по мере отверждения смолы, иначе механическое преимущество будет потеряно.После эксплуатации изгибы жгута должны быть сначала вытянуты прямо, прежде чем волокно сможет выдержать нагрузку. Очевидно, что чем ровнее будет исходное расположение ткани, тем лучше. Используя этот материал, можно наматывать чрезвычайно прочные трубы.
Примеры продукции
Товар | Описание | |
---|---|---|
Карбоновая буксировка 24k | Carbon Tow (или пряжа) идеально подходит для добавления направленного армирования к вашему композитному ламинату.Буксировка используется для создания галтели на деталях, для усиления лонжерона или в сочетании с измельчителем для создания рубленых графитовых волокон. | |
Ровинг для пистолета | Этот универсальный ровинг можно либо измельчить, либо быстро смачивать и сушить для получения высокопрочных и легких композитов. В сочетании с пистолетом-измельчителем воздуха его можно использовать в системе распыления, как заполненной, так и незаполненной. |
Покровные коврики
Покровные маты представляют собой тонкие слои непрерывных прядей волокон, которые случайным образом наматываются петлями на рулон материала.Они имеют консистенцию папиросной бумаги. Легкий связующий материал скрепляет вуаль. Хотя они не предназначены для использования в конструкции, у них есть две очень важные функции. Во-первых, вуаль можно поместить в форму непосредственно за поверхностным слоем, чтобы свести к минимуму печать через более тяжелые армирующие ткани, применяемые позже. Это тонкое внешнее покрытие также позволяет шлифовать поверхность готовых деталей без врезания в армирующую ткань внизу. Вторая по величине область применения – сэндвич-сердечники.Мат-вуаль может быть помещен непосредственно поверх сердцевины для поддержания оптимальной толщины линии склеивания. Вуаль также эффективна для предотвращения стекания излишков смолы в ячейки сотовых заполнителей, когда вакуум не используется.
Примеры продукции
Товар | Описание | |
---|---|---|
Мат для наплавки сплошной вуалью | Поверхностный матможет быть добавлен в качестве поверхностного покрытия, чтобы минимизировать просвечивание и минимизировать повреждение структурной ткани при шлифовании, или оптимизировать толщину связующего слоя при использовании материала сэндвич-сердечника. | |
Вуаль из углеродного волокна | Использование вуали из углеродного волокна поверх стекловолокна будет лучше работать как проводник электричества, а не как инсоляция. Точно так же использование углеродного волокна поможет распространять радиочастотные сигналы. |
Мат из рубленого волокна
Этот материал соответствует названию.Волокна обычно имеют длину от трех до четырех дюймов и ориентированы произвольно. Мат из рубленых прядей – не очень прочный материал из-за небольшой длины волокон. Однако он изотропен. Это означает, что он одинаково прочен во всех направлениях (мат и наполнители – единственные композитные армирующие элементы, демонстрирующие это свойство). Мат – это наименее дорогая форма армирования и, следовательно, наиболее широко используемая. Подходит для изготовления форм и деталей. Произвольная ориентация эффективно скрывает отпечаток ткани через гелькоут и делает формы одинаково жесткими во всех направлениях.Следует отметить, что мат из рубленых прядей совместим только с полиэфирной смолой.
Примеры продукции
Товар | Описание | |
---|---|---|
Мат из рубленого волокна | Коврик из рубленых прядейчаще всего используется для придания толщины деталям между слоями ткани. Обычно производители рвут мат из рубленых прядей, а не разрезают его.Это сохраняет длину волокон вдоль разорванного края, создавая более прочное соединение. |
Ткани
Ткани являются сильным армирующим материалом, потому что волокна скручиваются в пряжу, ориентированную всего в двух направлениях. Нити основы и наполнителя проходят под углом 0 и 90 градусов соответственно. Таким образом, ткани анизотропны или прочны только в двух направлениях. Ткани должны быть ориентированы таким образом, чтобы волокна пряжи проходили параллельно с ожидаемыми нагрузками.Если требуется дополнительная прочность в другом направлении, необходимо добавить еще один слой под углом к первому. Наиболее распространенные углы составляют +/- 45 градусов.
Примеры продукции
Товар | Описание | |
---|---|---|
Стекловолокно | Стекловолокно – основа композитной промышленности. Он использовался во многих приложениях для композитов с 1950-х годов, и его физические свойства довольно хорошо изучены.Он легкий, имеет умеренную прочность на разрыв и прост в обращении. Стекловолокно используется в широком спектре проектов в отрасли. | |
Углеродное волокно | Углеродное волокно встречается повсюду, от автогонок до авиакосмической отрасли. Хотя он дороже, чем стекловолокно и кевлар, он может похвастаться самой высокой прочностью на растяжение, сжатие, изгиб и изгиб в отрасли. Углеродное волокно обычно используется для проектов, требующих более высокого уровня прочности, таких как несущие детали. | |
Кевлар | Кевлар – одно из первых высокопрочных синтетических волокон, получивших признание в промышленности армированных волокнами пластмасс. Кевлар сияет в его стойкости к ударам и истиранию. Кевлар идеально подходит для таких деталей, как каноэ и байдарки, панели фюзеляжа самолетов и сосуды под давлением, где ожидается сильное воздействие и истирание. |
Стили тканых материалов
Есть много стилей тканых тканей, из которых можно выбирать.Наиболее распространены ткани с полотняным переплетением, в которых попеременно пересекаются нити основы и наполнителя. Обычные тканые ткани, как правило, наименее податливы, но их легко разрезать и обрабатывать, потому что они нелегко распутываются. Однако их прочность снижается из-за сильного «предварительного прихвата», уже присутствующего в ткани. Как указано в разделе «жгуты», волокна обладают наибольшей прочностью только тогда, когда они идеально прямые. Частое пересечение нитей снизу и вверх снижает прочность полотняного переплетения, хотя они по-прежнему подходят для всех областей применения, кроме наиболее эффективных.
Саржевое переплетение и атласные ткани очень пластичны и прочнее, чем полотняное переплетение. При атласном переплетении одна пряжа с наполнителем плавает над тремя-семью другими нитями основы, прежде чем прошиваться под другой нитью основы. Нити этого типа с неплотным плетением идут ровнее и дольше, сохраняя теоретическую прочность волокна. Очевидно, что податливость выше, и эти ткани легко принимают сложные формы. Однако после обрезки они легче распутываются, потому что каждая нить удерживается не так плотно.Саржевое переплетение – это компромисс между атласным и полотняным переплетением, а также часто желаемый косметический эффект «елочка».
Практическое руководство по выбору подкрепления
Прежде чем начинать какой-либо проект, подумайте о потребностях готовой детали. Насколько жесткой, легкой, износостойкой или устойчивой к повреждениям должна быть деталь или конструкция? Обязательно учитывайте стоимость. Сравните свой список с описанием материалов и таблицей, на которую ранее ссылались, чтобы выбрать лучшую ткань с точки зрения производительности и стоимости.Стекловолокно неизменно приносит пользу почти для каждого проекта.
Как правило, для нанесения защитного слоя на дерево можно использовать любую ткань с полотняным переплетением. Если ламинат предназначен для использования в морских условиях, следует рассмотреть не менее двух слоев. Легкие ткани хороши, если защитный слой должен быть прозрачным, например, на каноэ, построенных из полос. Обычное плетение средней плотности, от шести до десяти унций на квадратный ярд, возможно, является наиболее универсальным. Обычно их называют лодочными тканями, они недорогие, прочные и легко формируются.Они часто сочетаются со слоями мата при изготовлении форм или используются для защиты сердцевины при строительстве без форм.
Атласное и саржевое переплетение для авиакосмической промышленности следует использовать везде, где требуются высочайшие физические свойства.
Выбор смолы
Фото предоставлено IStock Photo. Выбор смолы зависит от совместимости ткани, условий эксплуатации и желаемых характеристик готовой детали. Существует два распространенных типа термореактивной смолы: эпоксидная и полиэфирная.Операции по формованию, формованию, ламинированию и литью могут выполняться с помощью любой системы. Эпоксидная смола – это система с более высокими характеристиками и более высокой ценой. Он используется в приложениях с критическим весом, высокой прочностью и точными размерами. Полиэфирные смолы менее дороги, более устойчивы к коррозии и более щадящие, чем эпоксидные. По этой причине они наиболее широко используются.
Сложный виниловый эфир – это третий вариант смолы, часто описываемый как нечто среднее между эпоксидной и полиэфирной смолами, поскольку он находится между ними по цене и характеристикам обработки.Он обладает отличной стойкостью к коррозии и истиранию, поэтому хорошо подходит для таких применений, как резервуары для хранения химикатов.
Некоторые смолы совместимы не со всеми тканями. Например, у Kevlar® часто возникают проблемы с адгезией, поэтому следует использовать эпоксидную смолу или полиэстер высшего качества. Кроме того, маты из стекловолокна имеют связующее, растворимое в полиэфирной основе. Эпоксидные смолы могут растворить это, и их никогда не следует использовать с матом. При разработке проекта тщательно проверяйте совместимость материалов.
Примеры продукции
Товар | Описание | |
---|---|---|
Полиэфирная смола | Полиэфирные смолы являются наиболее широко используемыми смолами в композитной промышленности.Полиэфирные смолы менее дороги, обладают некоторой коррозионной стойкостью и более щадящие, чем эпоксидные смолы. Полиэфирные смолы просты в использовании, быстро затвердевают и устойчивы к экстремальным температурам и катализаторам. | |
Винилэфирная смола | Смолана основе сложного винилового эфира считается гибридом полиэфира и эпоксидной смолы, что означает, что ее эксплуатационные характеристики, свойства и цена обычно ниже двух других.Виниловый эфир отличается высокой стойкостью к коррозии, температуре и растяжению. | |
Эпоксидная смола | Для композитных деталей, требующих максимальной прочности, производители будут использовать эпоксидную смолу. Помимо улучшенных прочностных свойств, эпоксидные смолы также обычно превосходят полиэфир и сложный виниловый эфир по стабильности размеров и улучшенному сцеплению с другими материалами. |
Ниже приведены некоторые общие рекомендации по выбору смолы:
Применение клея: Если приложение требует адгезионных свойств, настоятельно рекомендуется использовать эпоксидные смолы. Выбирайте эпоксидную смолу со сроком жизнеспособности, максимально близким к требуемому времени работы. При необходимости измельченное стекловолокно можно смешивать для создания структурной пасты-наполнителя.
Примеры продукции
Товар | Описание | |
---|---|---|
Система 1000 | System 1000 Epoxy – это смола с низкой смешанной вязкостью, которая быстро смачивает армирующие волокна в процессе укладки.Это позволяет ускорить процесс изготовления. | |
Винилэфирная смола | Смолана основе сложного винилового эфира считается гибридом полиэфира и эпоксидной смолы, что означает, что ее эксплуатационные характеристики, свойства и цена обычно ниже двух других. Виниловый эфир отличается высокой стойкостью к коррозии, температуре и растяжению. |
Применение в пресс-формах: Лучше всего их выполнять с использованием полиэфирной формовочной смолы №77 или любой эпоксидной смолы со средним и длительным сроком службы.Предварительно нарежьте тканевую арматуру и держите ее под рукой. Используйте кисти, ракели и валики для пропитки, чтобы смочить ткань. Для деталей, которые будут использоваться в высококоррозионных средах, выберите нашу изофталевую полиэфирную смолу № 90 или Винилэфирную смолу № 1110.
Примеры продукции
Товар | Описание | |
---|---|---|
Полиэфирная формовочная смола | Полиэфирная формовочная смола – одна из самых распространенных и популярных смол в промышленности.Он отлично подходит для изготовления деталей общего назначения и для недорогих пресс-форм. Со смолой легко работать, она дешевле по сравнению с другими причинами и не содержит воска, поэтому шлифование между слоями не требуется. | |
Изофталевая полиэфирная смола | Изофталевая полиэфирная смола имеет гораздо лучшую прочность по сравнению с полиэфирными смолами общего назначения, отлично подходит для создания полиэфирных форм со стабильными размерами, изготовления деталей, которые должны выдерживать сильную коррозию, и прочных материалов для ремонта футеровки резервуаров. | |
Винилэфирная смола | Винилэфирная смоласчитается гибридом полиэстера и более прочной эпоксидной смолы, а это означает, что ее эксплуатационные характеристики, свойства и цена обычно находятся между двумя другими. Винилэфир отличается коррозионной стойкостью, термостойкостью и вязкостью при удлинении. |
Ремонт общего назначения и тонкое ламинирование: Для этих целей лучше всего использовать смолу общего назначения, смешанную со стирольным воском.Если выбрана эпоксидная смола, используйте версию с коротким жизнеспособностью, которая затвердеет быстрее при нанесении на тонкие участки.
Примеры продукции
Товар | Описание | |
---|---|---|
Полиэфирная формовочная смола | Полиэфирная формовочная смола – одна из самых распространенных и популярных смол в промышленности. Он отлично подходит для изготовления деталей общего назначения и для недорогих пресс-форм.Со смолой легко работать, она дешевле по сравнению с другими причинами и не содержит воска, поэтому шлифование между слоями не требуется. | |
Стироловый воск | Добавление стирольного воска к невощеной полиэфирной смоле предотвратит длительную липкость, связанную с тонкими срезами полиэфиров в композитном материале. Этот воск поднимается на поверхность во время отверждения, после чего его необходимо отшлифовать. | |
Система 1000 | System 1000 Epoxy – это смола с низкой смешанной вязкостью, которая быстро смачивает армирующие волокна в процессе укладки.Это позволяет ускорить процесс изготовления. |
Минимальная деформация: Эпоксидные смолы всегда обеспечивают наиболее стабильные размеры деталей и форм, но можно успешно использовать полиэфирную смолу премиум-класса, такую как изофталевая полиэфирная смола № 90.
Примеры продукции
Товар | Описание | |
---|---|---|
Изофталевая полиэфирная смола | Изофталевая полиэфирная смола имеет гораздо лучшую прочность по сравнению с полиэфирными смолами общего назначения, отлично подходит для создания полиэфирных форм со стабильными размерами, изготовления деталей, которые должны выдерживать сильную коррозию, и прочных материалов для ремонта футеровки резервуаров. | Система 1000 | System 1000 Epoxy – это смола с низкой смешанной вязкостью, которая быстро смачивает армирующие волокна в процессе укладки. Это позволяет ускорить процесс изготовления. |
Система 2000 | System 2000 Epoxy – это смола для ламинирования светло-янтарного цвета, обеспечивающая максимальную прочность эпоксидной смолы при комнатной температуре.Он часто используется для изготовления высокопрочных деталей, требующихся в конструкционных конструкциях. | |
Отливка: Толстые секции можно отливать с помощью эпоксидной системы медленного отверждения # 2000/2120 или любой из наших уретановых смол для литья. Стандартные смолы не рекомендуется заливать в массу, достаточно большую для литья.
Примеры продукции
Товар | Описание | |
---|---|---|
Система 2000 | System 2000 Epoxy – это смола для ламинирования светло-янтарного цвета, обеспечивающая максимальную прочность эпоксидной смолы при комнатной температуре.Он часто используется для изготовления высокопрочных деталей, требующихся в конструкционных конструкциях. | |
Эуретановая литьевая смола – Shore A | Смолы для литья под давлением уретановые идеально подходят для изготовления четырех деталей и оснастки. Уретановая смола для литья под давлением – Shore A используется для создания жестких, гибких деталей и форм. | |
Смола для литья под давлением – 75 Shore D | Уретановая литьевая смола – 75 Shore D отлично подходит для изготовления готовых деталей и мелкосерийных оболочек. Она отлично подходит для создания твердых деталей с улучшенными деталями и превосходными косметическими качествами. |
Выбор инструментов
По сравнению с классической обработкой и изготовлением инструментов, для работы с композитами требуется несколько специальных инструментов. Однако есть ряд элементов, облегчающих работу и повышающих качество продукции.
Предметы повседневного спроса, такие как чистые емкости для смешивания, весы и другое измерительное оборудование, качественные ножницы и множество перчаток, – простые предметы, о которых часто забывают.Ракель, щетки и валики – рекомендуемые аппликаторы для пропитывания арматуры смолой. Ракели и валики для пропитки также могут использоваться для обработки воздуха из ламината и сжатия слоев ткани. Бритвенные ножи и лобзики нужны для обрезки готовых деталей и форм. Для ускорения резки используйте качественные композитные диски со средним числом зубьев. Механические шлифовальные машины, шлифовальные машины и буферы полезны при выполнении более крупных работ, но эту работу можно выполнить вручную, если у вас будет достаточно времени и усилий. Последняя рекомендация по оборудованию – это стеллаж для резки ткани для хранения и хранения материала.Стойка поддерживает ткань горизонтально на трубе и может быть изготовлена из простых строительных материалов.
Примеры продукции
Товар | Описание | |
---|---|---|
Принадлежности для смешивания | Mixing Supplies следует использовать для смешивания смолы с добавками смолы при подготовке к процессу укладки.Для правильного действия смол необходимы такие добавки, как катализатор и отвердитель. Другие добавки, такие как наполнители, пигмент и воск, не являются обязательными и выбираются с учетом желаемых характеристик, которые они придают смоле. | |
Режущее оборудование | Почти каждый композитный проект потребует некоторой резки, особенно на стадии подготовки. Обязательно выберите ножницы, резаки и вспомогательные приспособления для ткани, которые будут соответствовать качеству композитной детали, которую вы планируете производить. | |
Средства защиты и чистки | Безопасная и чистая рабочая среда – первый шаг к созданию успешного композитного ламината. Обязательно планируйте свой проект или ремонт соответствующим образом и принимайте простые меры безопасности для каждого проекта. | |
Щетки | Простой выбор, который, тем не менее, окажет большое влияние на ваш проект.Кисти помогут пропитать ткань выбранной смолой. Убедитесь, что используемая кисть соответствует качеству вашего проекта. | |
Ракели и ролики | Ракели и валикипозволяют равномерно распределять смолу по ткани и легко удаляют излишки смолы с детали. Неровное покрытие может повредить вашу композитную деталь, но этого легко избежать при работе с соответствующими инструментами. |
Оценка веса материалов и затрат
Точная оценка материала необходима по двум причинам. Во-первых, очевидно, что они нужны для правильного заказа, хранения материалов и проведения торгов по проектам. Что еще более важно, оценки дают возможность рассчитать вес или стоимость детали, используя различные графики ламинирования, прежде чем приступить к сборке.
В отличие от оценки покрытия при покраске, использование смолы будет зависеть от типа используемого армирования.Чем тяжелее ткань, тем больше смолы потребуется для ее смачивания. Хороший ламинат для рук состоит примерно из 50% ткани и 50% смолы по весу. Например, если для приложения требуется 3 квадратных ярда ткани плотностью 4 унции на квадратный ярд (общий вес ткани составляет 12 унций), потребуется 12 унций смолы. Однако, если выбрано 3 ярда ткани по 10 унций на квадратный ярд (общий вес ткани составляет 30 унций), потребуется 30 унций смолы.
Стекломат требует минимум 2 унции смолы на каждую унцию мата.Следовательно, если приложение требует 20 квадратных футов мата толщиной 1,5 унции на квадратный фут, потребуется минимум 60 унций смолы. Помните, что мат указывается в унциях на квадратный фут, а ткани – в унциях на квадратный ярд. Рубленый коврик плотностью 1,5 унции на квадратный фут на самом деле весит 13,5 унций на квадратный ярд!
Поскольку существует множество возможных комбинаций материалов, следует рассчитать вес и стоимость одного слоя с использованием различных армирований.Затем они могут быть добавлены или вычтены из теоретического слоистого материала, пока не будут достигнуты проектные свойства.
Рабочий лист оценки материалов
1) Начните с расчета площади проекта.
Оцените неправильные формы, измерив прямоугольники приблизительного размера, необходимые для определения конических участков. Умножьте длину на ширину для каждого прямоугольника, а затем сложите все отдельные прямоугольники вместе, чтобы получить общую площадь поверхности детали.Если расчет ведется в квадратных футах, разделите на 9, чтобы получить квадратные ярды.
2) Составьте список каждого типа армирования, рассматриваемого для ламинирования.
Умножьте вычисленные квадратные ярды на вес ткани в унциях. Это общий вес одного слоя этого материала. Это также количество смолы, необходимое для его насыщения. Если это известно для 2 или 3 различных типов материалов, можно рассчитать вес и стоимость ламината, изготовленного из любой комбинации этих тканей.Чтобы преобразовать вес унции в фунты, разделите на 16. Те, у кого нет опыта в пропитывании стекловолокна, обычно используют слишком много смолы. Хорошо пропитанный ламинат является однородно полупрозрачным, без «молочных» сухих пятен, но из-за веса и стоимости в нем немного лишней смолы.
3) Рассчитайте использование гелькоута, грунтовки и поверхностной грунтовки.
Все формованные ламинаты, кроме самых легких, требуют гелевого покрытия. Толщина этого гелевого покрытия должна составлять 15-20 мил.
Для гелевого покрытия толщиной 20 мил потребуется один галлон смеси для гелькоута на каждые 80 квадратных футов поверхности формы. Если требуется более светлый поверхностный слой, распылите деталь № 1041-B Duratec Surfacing Primer в форму вместо гелевого покрытия. Его можно наносить более тонким (10-12 мил) и, следовательно, более легким слоем. Duratec также является идеальным финишным слоем для покрытия ламинатов из вспененной фанеры или фанеры.
При покрытии фанеры стекловолокном потребуется дополнительная смола для грунтования древесины.Для большинства видов древесины для этого покрытия потребуется около 3 унций смолы на каждый квадратный фут поверхности. Это в дополнение к смоле, необходимой для пропитывания стекловолокна. Чтобы обеспечить достаточное насыщение, добавьте на 20% больше смолы к первоначальной оценке.
Пример:
Следующий пример поможет прояснить оценку материала, а также охватит некоторые аспекты дизайна.
Начато строительство фанерного катера. Лодка 12 футов в длину, 4 фута в ширину внизу, по 2 борта с каждой стороны.5 футов высотой, транец – 2 на 5 футов. Фанера толщиной три четверти дюйма выдерживает нагрузки, но стекловолокно должно герметизировать и защищать как внутреннюю, так и внешнюю часть лодки. Стекловолокно было выбрано вместо KEVLAR®, чтобы снизить затраты. Сколько материала потребуется, и какой вес будет добавлен?
1) Начните с расчета площади поверхности каждой детали.
Этаж
12 футов x 4 фута = 48 кв. Футов
Стороны
12 футов x 2,5 фута = 30 кв.фут x 2 = 60 кв. футов
Транец
2 фута x 5 футов = 10 кв. Футов
Всего
118 кв. Футов
На каждый слой приходится 118 квадратных футов, и слои будут добавлены как внутри, так и снаружи лодки. Затем разделите 118 квадратных футов на 9 квадратных футов, чтобы найти общую площадь в квадратных ярдах на слой. Это преобразование необходимо, чтобы площадь можно было сравнить с весом ткани, указанным в квадратных ярдах.
118 кв. Футов / 9 кв.ft. = 13,5 кв. ярдов
Рассматриваемые ткани имеют полотняное переплетение 10 унций и 7,5 унций. Вес ткани умножается на площадь поверхности, чтобы определить общий вес одного слоя ткани.
10 унций / кв. ярд х 13,5 кв. ярд. = 135 унций. / 16 = 8,5 фунтов / слой
7,5 унций / кв. ярд х 13,5 кв. ярд. = 101,25 унций / 16 = 6,5 фунтов / слой
При соотношении ткань-смола 50/50 смола также будет весить столько же, сколько и ткань.
Поскольку лодка будет использоваться только у песчаных берегов, была выбрана ткань весом 7,5 унций, что позволяет сэкономить 4 фунта на каждом слое. Если бы берег был каменистым, ткань на 10 унций могла бы быть лучшим выбором для долговечности, несмотря на дополнительный вес.
2) Рассчитайте весь дополнительный расход смолы и грунтовки, как указано выше.
На фанеру потребуется грунтовка из полиэфирной смолы. Для достаточного покрытия поверхности потребуется 3 унции на квадратный фут площади поверхности.
3 унции. x 118 кв. футов = 354 унции. / 16 = 22 фунта смолы.
Поверхностное покрытие будет создано путем распыления на деталь № 1041-B Duratec Surfacing Primer. Один галлон легко покроет 118 квадратных футов слоем материала толщиной 12 мил.
Заключение
Это руководство предназначено, чтобы помочь новичку осмыслить процесс создания композитного стекловолокна. В связи с недавними достижениями и доступностью других высокоэффективных композитных материалов, некоторые из них также были включены в этот документ.Подчеркивается важность выбора волокна, и в качестве удобного справочного материала приводится таблица, в которой сравниваются сильные и слабые стороны трех доступных армирующих элементов. Разработайте проекты с учетом этих свойств ткани, а затем выберите систему смол, совместимую с тканью и конечными условиями эксплуатации, которые будет видна деталь. Смета материалов также важна в процессе проектирования. Варианты графика ламинирования можно сравнить на этапе проектирования, а ламинат можно адаптировать к условиям эксплуатации и бюджету проекта.Пример трехэтапного процесса оценки материала должен сделать эти оценки безболезненными. Очевидно, что по этим вопросам доступно больше информации, но эти основы демонстрируют легкость, с которой могут быть достигнуты преимущества композитов.
Markforged
Ключ к раскрытию прочности в 3D-печати из непрерывного волокна заключается в понимании того, где вы можете использовать нити или панели, чтобы они распределяли нагрузочные силы при растяжении или изгибе, как мы рассмотрели в Физике 3D-печати.Ниже мы расскажем о нескольких различных методах определения и размещения волокна в вашей детали, чтобы обеспечить прочность там, где она вам нужна.
Как думать об армировании непрерывными волокнами
Проектирование армирования волокнами аналогично проектированию для базовой 3D-печати, но с дополнительным вниманием к потребностям в прочности. 1. Определите условия нагрузки Взгляните на свою конструкцию. Где он будет испытывать изгибающие силы? Растягивающие силы? Сжимающие силы? Если вы не уверены, подумайте о том, как силы будут передаваться через другие части – при необходимости нарисуйте диаграмму! Это поможет вам принять обоснованное решение о своей стратегии волоконно-оптической маршрутизации.
В каком направлении с вашей стороны перемещаются самые большие грузы? Вы хотите, чтобы ваша деталь была ориентирована таким образом, чтобы эти силы в основном перемещались в плоскости с печатным столом, нагружая волокна при изгибе или растяжении. Если у вас много больших сил, охватывающих несколько осей, вы можете рассмотреть возможность изменения конструкции или разделения ее на несколько частей.
Какие поверхности или сегменты необходимо усилить в зависимости от условий нагрузки? Имея это в виду, подумайте, какие типы подкрепления вам нужно будет применить в этих областях.
Если армирована только одна сторона детали, она может деформироваться из-за неровной сэндвич-панели, что происходит, когда одна сторона укрепляется, а другая – нет. t, или если одна грань имеет совершенно другое поперечное сечение, чем другая. Если одна группа слоев вашей детали армирована, сбалансируйте сэндвич-панель, усилив эквивалентную группу слоев на самом дальнем Z-слое с аналогичным поперечным сечением.
Подходит ли волокно и проходит ли оно в нужных вам областях? Можете ли вы проследить непрерывные нити волокна, которые проходят по путям нагрузки и «подпирать» силу? В противном случае вам может потребоваться отрегулировать настройки волокна или изменить характеристики так, чтобы волокно проходило в нужных вам местах. Помните, что для печати групп волокон требуется как минимум четыре пластиковых слоя крыши и пола, поэтому любые грани, которые нуждаются в армировании, должны начинаться со смещения четырех слоев от ближайшей крыши или пола.
Базовая стратегия армирования: шелушение
Ниже описана базовая стратегия армирования печатной детали. Эта стратегия гарантирует, что ваша деталь в целом будет прочной и устойчивой к изгибающим и ударным нагрузкам по любой оси. Как описано ранее, более важно усилить крайние стороны вашей части, чем стержень, поэтому мы расскажем вам, как «обшить» часть для обеспечения эффективной силы со всех сторон.
Shelling – верный способ укрепить любую деталь, напечатанную на 3D-принтере, непрерывным волокном, потому что он защищает от большинства условий нагрузки. 1. Изотропные панели на самых дальних Z-слоях Чтобы максимизировать прочность на изгиб, создайте сэндвич-панель с 2-4 слоями изотропного волокна на верхней и нижней плоскостях детали, исключая любые небольшие выступы на поверхности. Слои волокна должны начинаться выше четырех слоев «пола» или заканчиваться ниже четырех слоев «крыши» данной горизонтальной поверхности.
Добавьте 2-4 слоя изотропного волокна под или над любыми поверхностями, которые требуют больших изменений в геометрии детали, снова учитывая четыре «крыша» и «пол». »Слои.
Усиление отверстий под болты по оси Z двумя кольцами из концентрических волокон. Используйте «только внутренние отверстия», если вам не требуется усиление боковой нагрузки, или используйте «все стены» для охвата шага 4. Это распределяет сжимающую силу, прилагаемую болтом, и создает композитную «втулку», чтобы противостоять любому смещению оси. скручивающие нагрузки, которые испытывает болт.
Чтобы максимизировать прочность на изгиб по оси Z и усилить против боковых нагрузок, укрепите внешние стенки детали двумя кольцами из концентрических волокон.Используйте «только внешнюю оболочку», если у вас нет отверстий для болтов по оси Z, или используйте «все стены» для охвата шага 3. Это также усилит любые отверстия с осями на плоскости XY.
Специализированные стратегии армирования
Если вам нужно решить более конкретные условия нагрузки, вы можете использовать другую тактику для усиления определенных областей, усиления определенных секций детали или управления размещением волокон. Ниже приведены некоторые уникальные дополнительные стратегии, которые вы можете реализовать внутри своей части.
Для повышения прочности на изгиб в плоскости XY вы можете добавить «полосы» ИЗОТРОПНОГО ВОЛОКНА через несколько Z-слоев. Это наиболее эффективно с более толстыми деталями, которые имеют довольно постоянное или симметричное поперечное сечение, потому что полосы из волокон создают несколько наложенных друг на друга многослойных панелей для дальнейшего усиления изгибаемой детали.
Волокно можно направлять в определенных направлениях с помощью армированных ребер или вырезов, которые следуют по путям нагрузки от сил, приложенных к вашей детали. Вы можете заставить волокно следовать этим путям нагрузки, применив концентрическое волокно для усиления вокруг вырезов или стен.
Вы можете использовать инструмент «Углы волокон», чтобы направить «зигзаг» изотропных волокон в определенном направлении, чтобы лучше согласоваться с силами, прилагаемыми к вашей детали.При настройке по умолчанию узор заливки поворачивается на 45 градусов для каждого слоя, но вы можете изменить это, поместив определенный угол или узор углов в диалоговом окне «Углы волокон» для любого слоя, любой группы слоев или по всей части.
Достижение прочности по оси Z Вы можете обойти проблемы с прочностью по оси Z при 3D-печати, добавив болты в вашу деталь.Умный дизайн и стратегии усиления позволяют добиться большей прочности по нескольким осям.Пропускание болта через вашу деталь с изотропным волокном, усиливающим сжатые поверхности, может усилить деталь и предотвратить срезание или растяжение от разделения детали по линиям слоев. Вы можете усилить область вокруг болта с помощью концентрического волокна «только внутренние отверстия», чтобы любая из этих сил распределялась по волокну в виде изгибающих сил.
CE Center – Пластик, армированный стекловолокном: высокие характеристики потолочных и стеновых панелей
Свойства FRP
Прочность
Композитные панелиFRP имеют высокое отношение прочности к весу и не подвержены царапинам и вмятинам.Они невосприимчивы к большинству слабых кислот и не гниют, не разъедают, не пачкают, не отслаивают и не раскалывают. Как правило, прочность панели FRP не зависит от широкого диапазона температур (от -65 ° F до 135 ° F).
ПанелиFRP используются в конструкциях, где требуется определенная мера прочности или модуля упругости, с которой неармированные пластмассы или альтернативные материалы не могут соответствовать ни механически, ни экономически. Как уже упоминалось, изделия из стеклопластика чрезвычайно долговечны по сравнению со многими традиционными изделиями, поскольку свойства термореактивной смолы обеспечивают химическую, влагостойкость и термостойкость, в то время как армирование из стекловолокна увеличивает прочность и обеспечивает хорошие характеристики в широком диапазоне температур по сравнению с термопластами, на которые сильно влияет по температуре.
Свойства композитов FRP измеряются так же, как измеряются традиционные материалы, поэтому можно проводить сравнения для оценки. Типичные размеры включают:
- Прочность на сжатие. Описывает, какую нагрузку может выдержать материал, прежде чем он будет раздавлен или сломан.
- Модуль упругости при изгибе. Число, связанное с гибкостью или жесткостью материала. Он указывает, насколько сильно материал будет изгибаться при приложении к нему определенной нагрузки.Чем ниже модуль, тем более гибкий материал. ASTM D790
- Прочность на изгиб. Измеряет, какую нагрузку может выдержать материал до того, как он сломается или сломается, когда он находится в процессе изгиба. Более высокие числа указывают на более прочные материалы, которые могут выдержать более тяжелую нагрузку перед разрушением. ASTM D790
- Ударная вязкость . Есть два основных испытания на удар; один называется ударом ИЗОД, а другой – ударом Гарднера. Удар IZOD измеряет энергию, необходимую для разрушения материала при ударе о его край.Удар по Гарднеру измеряет энергию, необходимую для повреждения или прокола материала при ударе по передней поверхности.
- Твердость по Роквеллу или Барколу. Измеряет твердость поверхности материала. Стальной наконечник вдавливается в материал и измеряется его сопротивление проникновению. Чем выше значение твердости, тем более устойчивый материал к царапинам, истиранию и вмятинам. ASTM D785
- Модуль упругости. Число, связанное с вытягиванием или растяжением материала (натяжение), а также степень его удлинения при приложении к нему определенной нагрузки.Чем ниже модуль, тем больше материал будет вытягиваться или растягиваться. ASTM D790
- Прочность на разрыв. Измеряет, какую нагрузку может выдержать материал до того, как он сломается или сломается, когда он находится в процессе растяжения. Более высокие числа указывают на материалы, которые могут выдержать более сильное растяжение перед разрушением. ASTM D790
Устойчивость к плесени, плесени, пятнам и бактериям
P или ASTM D373 или D3274, панели FRP не поддерживают плесень или плесень, как дерево и гипсокартон с бумажной облицовкой.Панели влагостойкие, их легко чистить, они выдерживают многократные чистки без повреждения поверхности.
Фото: Crane Composites, Inc. |
Отделка FRP может быть гладкой или рельефной. Тестирование показало, что любая поверхность очищает нержавеющую сталь, а также является финишем №3. Тесты на рост бактерий и плесени, в том числе проведенные по ASTM D3273 и D274, показывают, что композиты FRP не поддерживают рост ни того, ни другого.
Некоторые специалисты утверждают, что тисненая отделка имеет дополнительное преимущество, так как обеспечивает более устойчивую к истиранию поверхность, чем гладкая панель. Независимое тестирование тисненой отделки из стеклопластика в сравнении с гладкой отделкой на мясоперерабатывающем предприятии, проведенное в Новой Зеландии Mirinz Laboratories, показало, что за четырехнедельный период «количество бактерий на всех уровнях (глаза, талия и колени) в целом соответствовало рекомендациям Mirinz. и обнаружено, что в нем не больше бактерий, чем в существующих панелях из нержавеющей стали и гладких пластиковых панелях.«Рельефные панели также применимы в агрессивных средах, поскольку они имеют хороший послужной список в плане очищаемости и стойкости к истиранию. Каждая неровность на поверхности представляет собой смесь твердой смолы. Любое устойчивое истирание концентрируется на« неровностях », защищая саму панель от истирание и воздействие бактерий или пятен.
Низкие эксплуатационные расходы
Композитные панелиFRP не требуют покраски и не требуют особого ухода. Рекомендуется регулярно очищать стеновые или потолочные панели из стеклопластика мягким неабразивным очистителем, чтобы на них не скапливались почва и грязь.Можно использовать 5–10-процентный водный раствор тринатрийфосфата при температуре не выше 130 ° F (55 ° C). Если тринатрийфосфат недоступен, следует использовать 5-10-процентный раствор бытового моющего средства для автоматических посудомоечных машин. Если требуется очиститель, одобренный USDA или FDA, предпочтительнее нейтральный очиститель (диапазон pH 6,5–7,5). Во всех случаях следует соблюдать инструкции производителя.
Панели из стеклопластикалучше всего чистить губкой или мягкой щеткой. Проволочные щетки или другие абразивные инструменты или подушки могут поцарапать поверхность.Нанесите очиститель, нанося его на поверхность чистящими или круговыми движениями. Тщательно промойте, чтобы удалить все следы очистителя; в противном случае образуется пленка, из-за которой панель приобретет тусклый и грязный вид. При использовании специального чистящего средства следуйте инструкциям производителя. Перед нанесением на всю поверхность проверьте небольшой участок.
Для удаления отложений из жесткой воды следует использовать 10-процентный раствор уксусной кислоты в холодной воде в соответствии с описанными выше процедурами очистки.Если поверхность панели станет матовой или истерзанной, полная очистка может оказаться невозможной. Панели FRP могут выдерживать многократные чистки без отрицательного воздействия.
Простота установки
ПанелиFRP отличаются относительно простой установкой. Они прикрепляются с помощью клея или механических креплений с помощью обычных столярных инструментов, достаточных для большинства установок. FRP также легко режется в полевых условиях и может быть установлен поверх гипсокартона или других плоских сухих поверхностей как при ремонте, так и в новых строительных проектах.Настенные и потолочные панели можно устанавливать прямо на керамическую плитку. Непористые поверхности требуют использования заклепок, если поверхность плитки не вскрывается шлифованием или использованием химического абразива. Клей следует использовать только на пористых поверхностях. При установке поверх бетонного блока неровные поверхности необходимо выровнять штукатуркой или бетонными составами. Бетонные стены должны быть хорошо затвердевшими и полностью сухими. Если бетонные или блочные стены находятся ниже уровня земли, где влага может проникать и мешать хорошему адгезионному соединению, следует использовать планки для обшивки и установить предварительно ламинированные панели с механическими креплениями.Панели устойчивы к усадке и расширению под воздействием влаги.
Для использования с гипсокартонными плитами и фанерными основаниями, VOC-совместимые клеи были специально разработаны для монтажа панелей из стеклопластика с «быстрым захватом» и способностью склеивания, что значительно снижает потребность в расширенных связях. Многие из этих клеев не содержат химикатов, разрушающих озоновый слой. В отличие от клеев на основе растворителей, они негорючие, не выделяют вредных паров и моются водой. Некоторые из этих клеев превосходят спецификацию ASTM C557 и обеспечивают водостойкость, оставаясь при этом постоянно гибкими.Их легко затирать затиркой, а рабочее время составляет 30 минут, что позволяет точно укладывать рабочие материалы.
Декоративное обращение
Традиционно стеновые панели из стеклопластика использовались в подсобных помещениях, таких как кухни, складские помещения и закрытые помещения в коммерческих помещениях. Теперь они доступны в различных узорах, фактурах и цветах, которые подходят для столовых, вестибюлей и других частей фасада дома. Палитры производителей включают панели FRP, имитирующие внешний вид плитки, а также поверхности с тиснением из песчаника, льна, кедра, бисера и гальки.
Фото: Crane Composites, Inc. Панели из стеклопластикаимеют привлекательную санитарную поверхность. |
Расчетный жизненный цикл составляет 100 лет
Арматура из стекловолокна по сравнению со стальной арматурой
Является ли арматура из стекловолокна конкурентоспособной по сравнению со сталью?
Арматура из стекловолокна является более дешевым материалом по сравнению со сталью с покрытием. Если коррозия не является проблемой или неметаллическое армирование не требуется, то подходящим вариантом может быть сталь.Основываясь на анализе затрат жизненного цикла, использование Mateenbar ™ обеспечивает конкурентоспособные цены, отсутствие необходимости в обслуживании, превосходную долговечность и длительный расчетный срок службы. Использование Mateenbar позволяет сэкономить в следующих областях:
- Уменьшение покрытия бетона – дополнительная толщина бетона не требуется для защиты арматуры
- Не требуются припуски на уменьшение диаметра из-за коррозии
- Не требуются дорогостоящие гидроизоляционные добавки для бетона
- Катодная защита не требуется
- Значительно дешевле нержавеющей стали
- Не требует защиты поверхности, как эпоксидная арматура, поэтому не требует подкраски после размещения
- Отсутствие затрат на обслуживание Арматура из стеклопластика
- на 75% легче стали – это экономит груз, ускоряет монтаж и снижает трудозатраты.
Каков модуль упругости Mateenbar ™ по сравнению со стальной арматурой?
Mateenbar ™ имеет два диапазона модуля: 46 ГПа и 60 ГПа. Диапазон 60 ГПа обычно предлагает проектировщику более экономичное решение. Сталь имеет модуль упругости при растяжении 200 ГПа.
Какова прочность на разрыв арматуры из стекловолокна по сравнению со стальной арматурой?
Mateenbar ™ – одна из самых прочных композитных арматурных стержней с пределом прочности на разрыв более 1000 МПа. Это более чем в два раза превышает предел прочности стальной арматуры, который обычно составляет от 400 до 500 МПа.
Характеристики арматуры из стекловолокна
Как можно учесть более низкий модуль упругости в конструкции?
Более низкий модуль упругости можно преодолеть, поскольку Mateenbar ™ устойчив к коррозии. Для защиты не требуется большого бетонного покрытия, поэтому арматуру из стекловолокна можно разместить ближе к поверхности. Увеличенное расстояние от нейтральной оси увеличивает модуль упругости.
Из-за того, что Mateenbar ™ не вызывает коррозии, допуск на ширину трещины, определенный ACI, увеличивается с 0.От 3 мм до 0,7 мм.
Можно ли изготовить арматуру из стекловолокна с более высоким модулем упругости?
Модуль Mateenbar ™ превышает 60 ГПа, что является теоретическим пределом для арматуры, армированной стекловолокном ECR. Могут быть использованы другие армирующие элементы, такие как углеродное волокно, арамидное волокно или S-стекло. Однако все эти варианты армирования дороги.
Имеет ли арматура из стекловолокна пластичное разрушение?
Арматура из стекловолокна является линейно эластичной до точки разрушения, правильная методология проектирования гарантирует, что конструкция демонстрирует желаемый механизм пластического разрушения.Это достигается за счет сбалансированной конструкции армирования. Более высокая прочность на разрыв арматуры затем приводит к возникновению механизма прогрессирующего разрушения связи, что приводит к режиму пластического разрушения конструкции. Документ ACI 440 Американского института бетона содержит дополнительную информацию.
Влияет ли Mateenbar ™ на щелочные условия?
Mateenbar ™ изготовлен из высококачественного стекловолокна, называемого ECR-стеклом. Он невосприимчив к щелочной атаке.
Можно ли согнуть mateenbar ™ на месте?
Отводы Mateenbar ™ должны изготавливаться по форме на заводе.Однако доступны стандартные формы сгиба.
Изгибы такие же прочные, как прямые?
Как и в случае гибов стальных и других арматурных стержней, изогнутый участок арматурного стержня из стеклопластика не такой прочный, как прямые.
Работа с арматурой из стекловолокна
Существуют ли какие-либо особые требования при обращении с арматурой из стекловолокна?
Обработка стеклопластиковой арматуры на месте аналогична обработке стали. Посетите наши Инструкции по безопасности и обращению для получения дополнительной информации.
Нужно ли устранять повреждения на месте?
Любая арматура может привести к значительным повреждениям.Незначительные повреждения не повлияют на характеристики mateenbar ™, так как он не имеет никакого покрытия для защиты от коррозионных элементов.
Нужно ли проектировать специально для арматуры из стеклопластика?
При проектировании необходимо учитывать свойства арматуры из стеклопластика. Комитет ACI 440 Американского института бетона является отличным источником информации, и проектировщики должны ознакомиться с ACI 440.1R-06 или аналогичными руководствами. Узнайте о последних нормах и стандартах для арматуры из стеклопластика здесь.
Команда Mateenbar ™ всегда готова работать с инженерами-проектировщиками, если им нужна помощь в переходе от стали к Mateenbar ™.
Когда мне следует использовать mateenbar ™?
Mateenbar ™ представляет собой не подверженную коррозии альтернативу арматурным стержням с увеличенным сроком службы в самых сложных и агрессивных средах. Если проблема коррозии присутствует в каком-либо проекте, Mateenbar ™ следует рассматривать как превосходную альтернативу стали – исключающую риск коррозии и связанные с этим расходы на техническое обслуживание.Не требует защитного покрытия или катодной защиты.
Mateenbar ™ неметаллический, что делает его идеальным для сред, где проводимость создает угрозу безопасности или создает помехи для чувствительного оборудования. Mateenbar можно безопасно использовать рядом с МРТ-сканером в больницах, на проектах скоростного трамвая, на площадках для калибровки компаса в аэропортах и на электрических подстанциях.
В чем разница между арматурой из стеклопластика и стеклопластиком?
GFRP означает полимер, армированный стекловолокном (обычно называемый стекловолокном).