Как загнуть арматуру стеклопластиковую: Как гнуть стеклопластиковую арматуру, чтобы она не ломалась и держала форму?
alexxlab | 26.06.2019 | 0 | Разное
Как гнуть стеклопластиковую арматуру. Стеклопластиковая арматура. ArmaturaSila.ru
Как работать с арматурой?
Находясь внутри строительных материалов, арматура значительно увеличивает их прочность. Она представляет собой совокупность металлических элементов, которые соединены друг с другом. Одним словом, арматура – это прочный каркас внутри стройматериала. Длительное время арматурные пруты использовались только для изготовления железобетона. Внушительная прочность на растяжение – это главное достоинство железобетонных конструкций. Этим качеством бетон в одиночку похвастаться не мог, поэтому Жозеф Монье в 1867 году придумал вшивать в него арматуру.
После этого бетон и арматурные прутья стали друзьями на века. Из железобетона начали делать готовые конструкции: лестницы, блоки, перемычки и т.д. Их использование очень удобно при строительстве коттеджей из кирпича или крупных блоков. Также применяется арматура и для фундамента. Его кладка должна быть максимально прочной, ведь это основа конструкции! С этим заданием отлично справляется железобетон уже долгие годы.
Для изготовления арматуры в основном используется сталь, ввиду высокой прочности и стойкости к коррозии.
Плюс ко всему стальные прутья гарантируют отличное сцепление с бетоном. Не так давно начали использовать стеклопластик в качестве сырья для арматуры. Этот материал ничем не отличается от стали по своим техническим характеристикам, даже в чем-то превосходит его. Стальные прутья арматуры бывают разными по сечению (от 6 до 40 мм). Также встречается профилированная арматура: в виде уголков, швеллеров, двутавра и др.
В частном строительстве используются арматурные стержни диаметром от 8 до 16 мм.
Для возведения дачного домика или небольшого коттеджа лучше всего купить арматуру из стеклопластика, ведь она намного легче, является диэлектриком (не проводит ток), стоит дешевле металлической и не заслоняет радиоволны. Выбором диаметра стержня можно не дурить себе голову – надо брать арматуру А5-го класса 10 или 12 мм в диаметре, хоть она и дорогая, но прослужит долгие-долгие годы. Всего бывает 6 классов качества арматуры: от А1 до А6. С увеличением класса увеличивается прочность и стоимость.
Самостоятельное строительство для некоторых – это не только возведение зданий собственными руками, но и самостоятельная подготовка материалов! У таких товарищей всегда возникает вопрос: Как гнуть арматуру? . Этот вопрос нельзя оставить без внимания, поэтому расскажем, как это делать.
Существует 2 основных способа:
Рычаг. Берется две крепкие, длинные трубы. Одна прочно крепится в землю, а другая должна оставаться свободной. В закрепленную трубу сажается арматурный прут, а другой трубой, наподобие рычага, происходит его сгибание.
Паяльная лампа и молоток. Для начала арматурный стержень можно напрочь закрепить. Потом с помощью паяльной лампы место сгиба раскаляется, а молотком гнется в нужном направлении.
Следует учесть, что процесс сгибания арматуры весьма трудоемкий: совершенная рутина и отсутствие динамики. Поэтому подойти к это работе нужно серьезно и добросовестно.
Фото: hiwtc.com, dukesinvestmentsinternational.com
Как в ванной установить раковину?
Помещение ванной комнаты невозможно себе представить без раковины для комфортного умывания. Однажды может наступить такой момент, когда такой конструктивный элемент необходимо будет обновлять. Именно в тот момент и возникает в голове.
Чем хороша стеклопластиковая арматура?
Арматура – это сырье для армирования конструкций из железобетона. Ее основная функция – придание прочности строительному материалу. По некоторым критериям различают несколько видов арматуры: По материалу изготовления: стальная.
Обзор арматуры из стеклопластика (композитной)
До недавних пор единственным строительным элементом, используемым для укрепления фундамента, являлась стальная армированная сетка. Сегодня на смену ей пришел композитный материал, который является легким и прочным. Речь идет о стеклопластиковой арматуре для фундамента. Популярность ее обусловлена рядом преимуществ и широкой сферой применения.
Основные виды и характеристики
Этот композит включает в себя стеклянные волокна, имеющие форму жгута или нитей, и синтетическую смолу. Первый компонент служит наполнителем, а второй #8212; связующим. О том, что арматура из стеклопластика полностью вытеснила свой стальной аналог, говорить пока не приходится, но популярность ее растет с каждым годом. Все это благодаря целому ряду отменных характеристик:
- Антикоррозийна.
- Стойкости к воздействию различных химических веществ.
Кроме того, арматура композитная стеклопластиковая обладает и таким свойством, как магнитоинертность. Она может поставляться в продажу в виде:
- Хлыстов – диаметр их от 4 до 16 мм, при этом длина может быть разной.
- Бухт такого же диаметра, но со строго нормированной длиной от 12 до 500 м.
- Нарезаться по индивидуальным размерам заказчика.
Стеклопластик может быть гладкий, не используется для фундаментного каркаса, или рифленый, он стоит дороже и обеспечивает лучшую сцепку с бетоном.
Применение композитной арматуры
Она используется для зданий и сооружений, к которым предъявляются особые требования. Речь идет об опорах мостов, тоннелях, а также морских сооружениях. Это относится и к постройкам, сталкивающимся с частой переменой уровня воды. Армирование фундамента стеклопластиком производится при строительстве сейсмоустойчивых сооружений и возведении зданий для химического производства. В частном строительстве ее применяют при заливке основания.
Плюсы и минусы арматуры
К достоинствам можно отнести:
- Повышенную прочность на разрыв.
- Не требуется использовать сварку при монтаже.
- Высокую степень упругости при условии, что стекловолокно не гнется.
- Возможность использования при любой температуре воздуха.
- Неспособность проводить тепло.
- Диэлектричность.
- Легкий вес, обеспечивающий простоту и удобство монтажа.
- Отсутствие коррозии.
- Простоту и удобство транспортировки.
- Сравнительно низкую стоимость #8212; цена за метр композитной пластиковой арматуры для фундамента в 1,5-2 раза меньше стального аналога.
К недостаткам можно отнести низкую прочность на излом, которая начинает проявляться с годами после длительного воздействия химических веществ.
Технология укладки своими руками
Композитная арматура не требует стыковки при помощи специального оборудования.
Стекловолоконные прутья связывают между собой обычными хомутами из пластика, которые обладают повышенной прочностью и не деформируются во время полного высыхания фундамента.
Начинают данный процесс со сборки опалубки. Стеклопластиковая арматура должна находиться от ее стенок на расстоянии не менее 5-8 см. Сначала монтируются долевые, затем поперечные балки, так делают 2 или 3 пояса. Для углов желательно приобрести готовые элементы, поскольку гнуть ее, применяя специальные инструменты, не рекомендуется.
Средняя стоимость по Москве и области
Купить для фундамента стеклопластиковую рифлёную арматуру можно по следующей цене:
Отзывы и мнения
«О стеклопластиковой арматуре услышал в одной передаче. Доверия этот композитный материал у меня не вызвал. На деле выяснилось, что он прочнее стальной армированной сетки. Сначала попробовал его для фундамента забора. Стоит уже лет 6 и все в порядке. Теперь планирую и для бани».
«Отзывы о стеклопластиковой арматуре, прочитанные мною на одном из сайтов, подкупали #8212; отрицательных не увидел. Узнал, что такой компонент обходится практически в 2 раза дешевле стального. После покупки провел свой эксперимент, так называемую проверку на прочность. Эта стеклопластиковая арматура действительно не гнется и обладает высокой упругостью. Теперь я уверен, что фундамент прослужит долго».
«Мы живем в сейсмоопасной зоне, поэтому выбора между стальной и стеклопластиковой арматурой даже не стояло. Купил второй вариант и не пожалел. Прочная, упругая, надежная и главное недорогая. А еще очень легко монтируется и не требует использования сварки. Привез ее из магазина на легковушке, не пришлось тратиться на грузовую машину. В общем, сплошная экономия при предельно высоком качестве».
«Транспортировать композитную арматуру действительно удобно. Подкупает также возможность приобретения нужных диаметра и длины. Заливку бетона с таким каркасом произвели совсем недавно, поэтому о других качествах говорить не берусь. Но вяжется она быстро. Это влияет на экономию времени при подготовке к укладке фундамента».
Хитрый счетчик, сберегающий электроэнергию. Окупается за 2 месяца!
Это нужно знать каждому, чтобы сэкономить!
как гнуть арматуру на гибочном станке
Но согнуть арматуру 012 мм в дугу радиусом от 600 мм и менее очень трудно. Перемещая захват, продолжайте гнуть до тех пор, пока не получите круглое кольцо
Как согнуть стеклопластиковую арматуру
Готовую стеклопластиковую арматуру, как и любую другую полимерную арматуру, согнуть прямо на строительной площадке невозможно (так чтобы после снятия нагрузки она осталась согнутой). После процесса затвердевания, композит, связывающий волокна, из которых состоит арматурный стержень, можно только разрушить. Как-либо размягчить его и потом снова вернуть твердость первоначального уровня — невозможно.
На рис. 30 показаны элементы гнутой арматуры: для вязаных арматурных сеток и каркасов плит, колонн, балок — отгибы, крюки (рис. 30, а)
На практике, обе эти задачи решаются проще. Касательно гнутых элементов — можно заказать их изготовление у производителя композитной арматуры. В заводских условиях всегда можно изготовить гнутые композитные элементы по чертежу заказчика ещё на этапе производства композитной арматуры.
Блондинка, видимо, – давно пора знать, если строишь там чего-то, – гнуть арматуру по оправке можно по радиусу 5d, где d – диаметр арматуры.
Кроме того можно просто использовать композитную арматуру вместе с металлической. Так называемые гибридные каркасы, связанные из стальной и стеклопластиковой арматуры — не редкость.
Когда стоит задача, во что бы это ни стало, приварить композитный арматурный стержень к чему-либо или выполнить преднапряжение композитной арматуры, есть единственное решение — использовать стержни композитной арматуры с установленными стальными наконечниками. Эти стальные наконечники могут крепиться к концам композитных арматурных стержней с помощью цанговых зажимов либо с помощью химических анкеров. Такие наконечники могут устанавливаться на концы композитных арматурных стержней прямо на заводе-производителе стеклопластиковой арматуры.Как гнуть и как вязать арматуру – варианты и приёмы работы. Чем больше длина трубы, тем легче будет согнуть арматуру.
Когда необходимо согнуть металлическую трубу или прут, часто используют то что под рукой: тиски 22 марта . Приспособление для гибки труб, арматуры, проволоки.
Чем согнуть арматуру? Обычно этим вопросом начинаю задаваться в тот момент, когда дело доходит до заливки фундамента. А как гнуть-то её?
Как согнуть арматуру? Здравствуйте, многоуважаемые товарищи! Как гнуть арматуру?
Как гнуть арматуру. как согнуть арматуру. вязка арматуры. Просто о стеклопластиковой арматуре.
Гнули 10 и 12 арматуру: на арматуре отмеряли, сколько нужно загнуть, продевали арматуру до метки в трубу железную диам.
Если вы решите создать что-либо своими руками, у вас непременно возникнет вопрос: «Как гнуть арматуру?».
Вот такое простейшее приспособление для гнутья арматуры я изготовил себе, начиная свою стройку: С ним гнуть арматуру можно очень быстро.26 апреля 2007
Для армирования ленточного фундамента используют арматуру различных Гнутые элементы применяются для поперечных связей и анкеров в арматурных каркасах.21 мая
Как согнуть арматуру. Строительство дома всегда начинается с возведения фундамента. Для строительства основания дома придётся гнуть прутья.
И так теперь вы знаете, как гнуть арматуру самостоятельно, и можете браться за стройку, не боясь встречи с данной проблемой.
Сварить композитную арматуру с чем-либо тоже не получится. На практике, обе эти задачи решаются проще. Касательно гнутых элементов — можно заказать их
Такой станок позволяет гнуть арматуру более качественно Как согнуть нержавейку Среди технологий обработки металла гибка занимает одно из ведущих мест.
Источники: http://www.ktovdome.ru/likbezzz/15099.html, http://stoneguru.ru/obzor-armatury-iz-stekloplastika-kompozitnoj.html, http://gidserials.ru/kak_gnut_armaturu.html
Комментариев пока нет!
КАК СОГНУТЬ КОМПОЗИТНУЮ АРМАТУРУ ИЛИ ПРИВАРИТЬ ЕЁ К ЧЕМУ-ЛИБО?
Уже изготовленную стеклопластиковую арматуру, как и любую другую композитную арматуру, согнуть на строительной площадке невозможно (так чтобы после снятия нагрузки она оставалась согнутой). После отверждения, композит, связывающий волокна, из которых состоит арматурный стержень, можно только разрушить. Размягчить его с последующим повторным отверждением — не получится.
Сформированный композитный арматурный стержень можно согнуть на время, но он будет вести себя как пружина и после снятия нагрузки снова выпрямится самостоятельно.
Сварить композитную арматуру с чем-либо тоже не получится. В крайнем случае можно приклеить…
На практике, обе эти задачи решаются проще. Касательно гнутых элементов — можно заказать их изготовление у производителя композитной арматуры. В заводских условиях можно изготовить гнутые композитные элементы по чертежу заказчика ещё на этапе производства композитной арматуры. Кроме того, Вы можете просто использовать композитную арматуру вместе с металлической. Так называемые гибридные каркасы, связанные из стальной и композитной арматуры — не редкость.
Когда стоит задача, во что бы это ни стало, приварить композитный арматурный стержень к чему-либо или выполнить преднапряжение композитной арматуры, есть единственное решение — использовать стержни композитной арматуры с установленными стальными наконечниками. Эти стальные наконечники могут крепиться к концам композитных арматурных стержней с помощью цанговых зажимов либо с помощью химических анкеров. Такие наконечники могут устанавливаться на концы композитных арматурных стержней прямо на заводе-производителе композитной арматуры.
Как согнуть композитную арматуру – Альянс-Строй
В строительстве и на производстве по достоинству оценили преимущества стеклопластиковой и другой композитной арматуры: малый вес, высокая прочность на разрыв, невосприимчивость к коррозии и агрессивной среде. Благодаря вышеперечисленным характеристикам данный материал активно применяется и позволяет сэкономить на устройстве арматурного каркаса по сравнению с использованием стальных стержней.
Несмотря на очевидные преимущества, известен и ряд некоторых недостатков, из-за которых зачастую применение данного материала не представляется возможным.
Изгиб композитной арматуры
Изготовленные композитные стержни невозможно согнуть непосредственно на строительной площадке — после снятия нагрузки арматура вернется в свое исходное состояние. Композит, который связывает волокна стержня не поддается повторному отверждению, поэтому арматура либо сохранит свою первоначальную форму, либо разрушится под действием нагрузки.
Существует два варианта решения данной проблемы:
- заказ на изготовление стеклопластиковой арматуры у производителя по чертежам заказчика. На стадии производства композитным стержням можно придать абсолютно любую форму, которая будет сохраняться;
- использование гибридного каркаса с сочетанием композитных и металлических стержней. Данный вариант связанных каркасов довольно часто встречается в реальности и полностью себя оправдывает.
Сварка композитных стержней
Стеклопластиковые стержни не поддаются электросварке. В полевых условиях данная проблема решается только с помощью склеивания изделий или применении других способов соединения элементов — хомутов или пластиковых зажимов.
Но электрическая сварка стеклопластиковой арматуры все же возможна. Данная задача решается путем установки специальных стальных наконечников, которые и выполняют роль свариваемого элемента. Наконечники устанавливаются в заводских условиях и крепятся к стержню с помощью специальных зажимов-цангов. Данный способ позволяет выполнить сварку или преднапряжение стеклопластикового элемента.
Таким образом, существует реальное решение проблем, которые могут возникнуть при эксплуатации композитной арматуры. Несмотря на возникающие неудобства, стеклопластиковая арматура является оптимальным решением для малоэтажного строительства, при котором ни одна из конструкций не подвержена ощутимо высоким нагрузкам. Армирование фундаментов стеклопластиковыми стержнями значительно снижает трудозатраты на монтаж и возведение конструкции, позволяет сэкономить на стоимости строительных материалов.
Вязка стеклопластиковой (композитной) арматуры фундамента своими руками
Композитная арматура относится к современным материалам, призванным заменить дорогой металлопрокат и обеспечить большую устойчивость к негативному влиянию внешних факторов. После того, как с 2012 года этот вид полимерного прута стал производиться в России, интерес к нему со стороны строителей стал возрастать с каждым годом.

Пластиковые пруты применяют на объектах индивидуальной застройки, при возведении крупных зданий и сооружений, для береговых укреплений и автомобильных дорог. В частном строительстве из нее изготавливают армирующие каркасы для ленточных и плитных фундаментов, а также армируют кладку из пенобетонных блоков.
Материал, из которого изготовлена пластиковая арматура, представляет собой полимерную смесь из продольного стекловолокна повышенной прочности и термически стойкой смолы. Стандартные диаметры выпускаемых прутов находятся в диапазоне от 4 до 32 мм. Максимальная температура эксплуатации 60˚C. Предел прочности 150 МПа.
Подготовка материалов для сборки армирующего каркаса
Для повышения общей прочности бетонного монолита, его усиливают конструкцией из стеклопластиковой арматуры в виде плоской сетки или пространственного каркаса, которые собирают из круглых прутов переменного или постоянного сечения. Отдельные элементы таких конструкций соединяют между собой с помощью вязальной проволоки, фиксирующих хомутов или специального пистолета.
Поэтому для вязки армирующего каркаса необходимо приобрести:
- пластиковую арматуру проектных диаметров;
- вязальную проволоку или затяжные хомуты.

Поэтому перед началом сборки каркаса ее необходимо размотать и нарезать на куски необходимой длины. Резка производится ножовкой или другим инструментом, не допускающим нагрева материала. Разметку мест реза на поверхности легко сделать с помощью обыкновенного маркера.
Вязальная проволока должна быть круглого сечения и диаметром не менее 1 мм, чтобы обеспечить необходимую прочность соединения и не лопнуть при скручивании. Для быстрого получения отрезков проволоки нужной для вязки длины, всю свернутую бухту необходимо разрезать болгаркой на 3 или 4 части.
Чтобы сделать вязальную проволоку более мягкой, ее можно обжечь в пламени с помощью паяльной лампы или в костре. Необожженная проволока гнется хуже и не всегда обеспечивает плотный охват соединения. Кроме этого, неподготовленный металл обладает меньшей тягучестью и чаще рвется во время работы.


Инструмент для проволочного связывания арматуры
Использовать для вязки плоскогубцы не очень удобно. Они не обеспечивают необходимой плотности охвата соединения и требуют приложения больших усилий. Поэтому стальную проволоку скручивают на арматурных прутах при помощи специальных крючков или вязального пистолета. Магазины инструмента предлагают к продаже два вида крючков, предназначенных, чтобы вязать арматуру:
- простые ручные, которые необходимо все время вращать во время работы;
- полуавтоматические винтовые, с вращающимся при нажатии на ручку крючком;
- пластиковые фиксаторы в виде одеваемых на арматуру колец и вертикальных стоек.
Простой крючок можно не покупать, а сделать самостоятельно (подробнее о том, как это сделать — тут), согнув его из толстой стальной проволоки и заточив острие. В этом случае вам будет чем вязать проектную конструкцию из прутов и без покупки инструмента.
Способ применения вязального пистолета ускоряет и упрощает процесс, но этот достаточно крупный инструмент может не обеспечить доступ в отдельные места. Кроме этого, такой инструмент приводит к перерасходу проволоки.
Пластиковые фиксаторы нужны для того, чтобы зафиксировать собранный арматурный каркас в необходимом пространственном положении внутри опалубки перед подачей бетона.
Технология ручной проволочной вязки стеклопластиковой арматуры
Для того, чтобы арматурный каркас или сетка приняли необходимую пространственную форму и не изменили ее при заливке бетона, все отдельные элементы необходимо надежно соединить между собой. Наиболее часто для этого используют вязальную проволоку. Вязка — это простой и быстрый способ соединения, для которого не требуется высоких квалификационных навыков. Кроме того, стеклопластиковую арматуру просто невозможно соединить при помощи сварки, а поэтому такой тип крепления наиболее приемлем в данном случае.
Весь процесс того, как вязать стеклопластиковую арматуру для фундамента, можно разделить на следующие пошаговые этапы:
- свернутая в бухту арматура разматывается и нарезается на отрезки проектной длины;
- на поперечные прутья нижнего арматурного слоя надеваются пластиковые фиксаторы;
- на расставленные поперечные элементы на заданном друг от друга расстоянии укладываются продольные пруты;
- во всех местах пересечений арматуры выполняются соединения путем скручивания петель из сложенной вдвое вязальной проволоки;
- после сборки нижнего ряда к пересечениям наружных ячеек вяжутся вертикальные арматурные элементы;
- к верхним концам или к середине вертикальных стоек, в зависимости от проектного количества рядов, привязываются поперечные отрезки;
- укладывается и вяжется следующий ряд продольной арматуры;
- собранный каркас переносится и устанавливается внутрь опалубки для ленточного фундамента.
Работу можно значительно упростить, если совмещать стеклопластиковую арматуру с металлической. Из стальных прутов можно заранее заготовит прямоугольные рамки и тогда не потребуется выполнять отдельную вязку вертикальных отрезков.
Нюансы вязки конструкций под заливку плитного фундамента
Армирование монолитных опорных оснований плитного типа выполняется в виде одного или двух рядов сеток в зависимости от проектного решения. Поэтому в такой конструкции арматурные пруты не рассматриваются как продольные и поперечные. Для поднятия нижней сетки над гидроизоляционным слоем на арматуру через каждые полтора-два метра одевают вертикальные стойки фиксаторы из пластика. Это позволяет установить арматурный каркас строго в горизонтальной плоскости на заданной высоте.
Важная особенность сборки арматуры для плитного фундамента заключается в том, что она производится по месту. Это необходимо из-за больших размеров конструкции и невозможности последующего перемещения. Поэтому во время вязки необходимо быть предельно осторожным, чтобы не наступить на уложенные арматурные прутья и не повредить конструкцию.
В шведской и финской утепленной плите (подробнее о ней в этой статье) необходимо предусмотреть пересечение прутов плиты с арматурным каркасом боковой опорной ленты. Для этого пруты нарезают длиннее, напускают их на вертикальные боковые арматурные каркасы и связывают проволокой.
Нюансы вязки стеклопластиковых каркасов для ленточных фундаментов
Особенности сборки арматуры для ленточного фундамента заключается в наличии боковых примыканий, пересечений и углов.


Изгибать арматуру из стекловолокна следует очень осторожно, не применяя термической обработки. Упругие свойства пластика делают процедуру сгибания довольно трудной. Поэтому для сборки углов и примыканий рекомендуется покупать согнутые элементы заводского изготовления.
Места пересечений стеклопластиковой арматуры под ленточный фундамент можно соединять прямыми отрезками или собирать одну из пересекающихся конструкций по месту установки.
Сборка арматурных каркасов может выполняться на открытом месте, в стороне от выкопанной траншеи. Правильная укладка уже собранной конструкции предусматривает расстояние от стенок опалубки и дна не менее 25 мм.
В заключение
Вязка стеклопластиковой арматуры для фундамента — это технологически простой процесс, не требующий особых профессиональных навыков. Быстро научиться ему сможет даже неподготовленный человек. Нужно просто немного потренироваться.
Небольшой вес материала значительно упрощает работу, а большая длина арматурного прута в бухте позволяет нарезать стержни любой необходимой длины. Это уменьшает количество стыков в отличие от стальных материалов.
Более подробно о том, как правильно вязать стеклопластиковую арматуру, вы можете посмотреть на следующих видео.
Видео по теме
Стеклопластиковая арматура – Про ремонт
Композитная арматура

Одним из таких материалов является арматура.

Наиболее часто встречается и используется ее металлическая разновидность, но, существует и целый ряд пластиковых аналогов.
Ничем не уступающих и во многом даже превосходящих металлическую «классику».
В частном строительстве использование пластиковых арматур наиболее оправдано.

Так как на крупных промышленных объектах недостатка в разнообразной технике и приспособлениях нет, то использование металлической арматуры не тянет за собой никаких дополнительных расходов.
А вот на «домашней» стройке для работ с металлической арматурой понадобится аренда специнструмента, что естественно повлечет увеличение итоговой стоимости объекта.
Да и сами работы по монтажу металлической арматуры требуют навыков, и начинающему мастеру не всегда удастся все сделать правильно.
А вот композитная арматура, хотя и несколько дороже, но гораздо менее «проблемна в обращении».
Ее проще и доставить и хранить и монтировать.
Пластиковую арматуру сможет собрать качественно даже новичок.

В итоге, сравнивая общие затраты на арматуру из металла и пластиковую, мы видим, что использовать пластик нисколько не дороже, а порой, даже и выгоднее металла.
Арматура строительная
Пластиковая, она же, полимерная или композитная, строительная арматура, появилась в строительной индустрии не так уж и недавно — ее использование началось примерно в семидесятых годах предыдущего столетия.

На территории бывшего союза она особо «не прижилась», так как с металлом у нас в то время было гораздо «попроще» чем с пластмассами.
А вот в Европе и Америках композитная арматура получила широкое применение.
И, по прошествии стольких лет, «вернулась» к нам уже в усовершенствованном и доработанном виде.
Собственно, разновидности пластиковой арматуры:

- АСП — арматура из стеклопластика, на основе стекловолокна и термоактивных смол, основное достоинство — очень малый вес
- АБП — арматура из базальтопластика, состоит из базальтовых волокон и органических смол, достоинство — устойчивость к агрессивным средам — щелочи, кислоты, соли
- АУП — арматура из углепластика, произведена из углеводородного волокна — самый дорогой вид композитных арматур
- АКК — арматура комбинированная, из смеси стекловолокон с базальтовыми
Отличить основной материал легко по цвету готовой арматуры — стеклопластик дает светлый, желтоватый или почти белый цвет, базальтопластик и углепластик — темные, черные и почти черные оттенки.
Стеклопластиковая арматура – фотогалерея
Окрашенная же композитная арматура может быть совершенно любого цвета и оттенка.
И, что бы не говорили некоторые производители, к прочности, диаметру или иным характеристикам цвет не имеет никакого отношения.
Достоинства композитных арматур:
- не подвержена коррозии
- прекрасно переносит повышенную влажность
- устойчива к воздействию агрессивных сред
- имеет высокую удельную прочность (выше, чем у металлической А-3 в десять — пятнадцать раз)
- обладает низкой теплопроводностью
- диэлектрична (не создаст помех при прохождении волновых сигналов)
- мало весит (легче металлического аналога более чем в пять раз)
- удобна в транспортировке и хранении (можно легко свернуть в бухту)
- экономична и практически безотходна
- устойчива к перепадам температур (рабочие пределы от минус семьдесят до плюс сто 0С)
- долговечна (прослужит втрое дольше металлической)
- экологична (не выделяет никаких вредных испарений)
- стоимость вполне сопоставима с достоинствами
Как и любой материал, арматура из композитов имеет ряд недостатков, о которых следует знать, выбирая именно ее для строительства.
Недостатки пластиковых арматур:
- малоупругий материал — показатели растяжимости в четыре раза ниже, чем у металлической
- хрупкость — без предварительного нагрева в нужном отрезке деформировать композит не получится — попросту треснет
- не переносит высокой температуры — при нагреве свыше ста пятидесяти 0С теряет прочность (базальтопластик — при температуре более трехсот 0С)
Применение
Несмотря на некоторые особенности, спектр применения стеклопластиковых арматур достаточно широк.
Так как их положительные качества с лихвой покрывают немногочисленные недостатки.


Композитная арматура используется для:
- конструкций, регулярно контактирующих с агрессивными средами
- армирования сооружений из бетона и железобетона
- любых объектов частного и промышленного строительства
- создания дорожных покрытий
- армирования опор линий ЛЭП
- исправления дефектов железобетонных сооружений
- строительства бассейнов
- устройства канализации
- строительства зданий из комбинированных материалов
- конструкций, в которых высок риск возникновения электрохимических коррозий
- строительства складов на химическом производстве
- предотвращения осыпания грунта в тоннелях и на откосах котлованов
- сооружения теплиц, опор в виноградниках, тентов и навесов




Стеклопластиковая арматура – фотогалерея

Для того чтобы вы могли получить представление о рабочих параметрах арматур из композитных материалов, представляем вам сравнительную таблицу:
Параметры |
Металл А-3 |
Композит |
Плотность | 7850 кг/м3 | 1900 кг/м3 |
Растяжимость | 14 % | 2,2 % |
Предельная прочность при растяжении | 390 МПа | 1100 МПа |
Модуль упругости на деформацию | 200000 МПа | 41000 МПа |
Предельная прочность при растяжении | 390 МПа | 1100 МПа |
Диаметр | от 6 до 80 мм |
от 4 до 24 мм (СНГ) от 6 до 40 мм (Европа/США) |
Заменимость конструкции
(нагрузки 25000 кг/м2) |
Диаметр 8 А-3 ячейка 140 на 140 мм вес 5,5 кг/м2 |
Диаметр 8 мм ячейка 230 на 230 мм вес 0,61 кг/м2 |
Заменимость диаметров
без потерь показаний по прочности |
8 мм 10 мм 12 мм 14 мм 16 мм 18 мм 20 мм |
4 мм 6 мм 8 мм 10 мм 12 мм 14 мм 16 мм |
Длина | от 6 до 12м |
от 6 до 12м и под заказ> |
Возможно, вам будет интересна технология производства композитной арматуры.
Процесс этот максимально автоматизирован и происходит при минимальном участии рабочих, что в свою очередь, сводит практически «к нулю» так называемый «человеческий фактор».

Этапы производства:
- силикатное стекло плавится в специальной печи
- полученная масса вытягивается в нити толщиной до двадцати микрон
- нити обрабатываются масляным составом и собираются в ровинг (пучок)
- ровинги (до шестидесяти штук) в свою очередь собираются в канаты
- канаты поступают на линию натяжения для выравнивания
- подготовленные выровненные заготовки раскладываются в нужном порядке и обрабатываются струей горячего воздуха для удаления масел и влаги
- полученный жгут пропускается через емкость с разогретым смоляным составом
- далее на специальном станке жгут формуют для получения нужного диаметра
- сформованная заготовка проводится через тоннельную печь, где происходит полимеризация связующих смол
- готовая арматура охлаждается с помощью проточной воды
- далее ее или мотают в бухты или нарезают на отрезки нужной длины (в зависимости от диаметра)


Специфика работы с композитной арматурой
Расчеты композитной арматуры производятся по тем же принципам, что и металлической, разница лишь в замене диаметров на равнопрочностные.
При работах со стеклопластиковой арматурой нужно учесть две специфические особенности этого материала:
- его практически невозможно согнуть в готовом виде — то есть, если вам нужны изогнутые участки, заказывать их нужно непосредственно у производителя, так как гнуть композитную арматуру можно только в горячем состоянии, готовый же, охлажденный стержень, либо треснет, либо распрямится обратно при попытках придать ему нужный угол изгиба
- нельзя соединять с помощью сварки — крепят пластиковую арматуру вязальной проволокой (как и металлическую), специальными клипсами или обычными пластиковыми хомутами (стяжками)
Хотя, нужно отметить, находятся умельцы у которых получается изогнуть стеклоарматуру применив строительный фен.

Стяжки — самый простой, удобный и экономичный способ крепления композитной арматуры, так как для него не понадобится ни вязальная машина, ни дополнительные расходы на приобретение специальных клипс.
Для выравнивания высоты арматурных сеток из композита выпускаются специальные пластиковые фиксаторы (крепежи).


Одним из достоинств пластиковых арматур является их безотходность при нарезке.
Но вот чем и как резать композит, чтоб расход был действительно без обрезков?
Есть несколько способов «расчленения»:
- болгарка или ножовка по металлу
- топор или болторез
Наиболее предпочтительной будет нарезка с помощью болгарки с диском алмазным или абразивным покрытием.

Ножовка тоже неплохо, но при больших объемах работы резчик явно устанет и качество нарезки заметно снизится.
Рубка топором и перекусывание болторезом способы хотя и быстрые, но не очень хорошие.
Недостаток их в трещинах, которые неизбежно образуются в арматуре.
Они могут быть совершенно невидны невооруженным взглядом, но, постепенно проникнут вглубь стержня, что повысит его уязвимость и снизит прочность.
Особенно быстро процесс пойдет после промерзания конструкции зимой и оттаивания летом.

Работая со стеклопластиком, не забывайте о защитной одежде.
Попадание мельчайших частиц базальта или стекловолокна в глаза, дыхательные пути, да и просто на кожу ведет к достаточно неприятным последствиям в виде сильного раздражения, слезотечения, зуда и кашля.
Поэтому обязательно используйте:
- защитную маску или респиратор
- защитные строительные очки
- перчатки с латексным или силиконовым покрытием — через обычное х/б волокно мелкие частицы стекловолокна с легкостью «проходят»

Поделиться статьей:
Статьи по теме Стеклопластиковая арматура
Комментарии
Добавить комментарий
Чем резать композитную стеклопластиковую арматуру для фундамента?
Чем можно разрезать композитную арматуру
Одним из основных достоинств композитной арматуры считается простота ее нарезки. Резка стеклопластиковой арматуры осуществляется непосредственно на месте производства работ, что значительно сокращает сроки строительства. Чтобы нарезать пруты по размеру, используют следующие инструменты:
- топор;
- болторез;
- ножовку по металлу;
- углошлифовальную машинку.
Рассмотрим преимущества и недостатки каждого инструмента.
Углошлифовальная машинка
Когда возникает вопрос, чем резать стеклопластиковую арматуру для фундамента (подробнее про сам материал мы уже писали здесь), строители в первую очередь вспоминают о болгарке. Этот инструмент позволяет качественно, быстро и с минимальным усилием нарезать большое количество материала.
К плюсам использования углошлифовальной машинки относят:
- высокую скорость работы;
- с помощью болгарки можно нарезать сразу пучок прутков;
- механизированная резка не требует большой мышечной силы;
- возможность применения дисков с любой режущей кромкой (для металла или камня).
Перед тем, как резать стеклопластиковую арматуру болгаркой, нужно учесть и минусы работы этим инструментом:
- порезать стеклопластик болгаркой без пыли не получится. Высокая скорость вращения диска приводит к распылению в воздухе мелких частиц стеклопластика. Нагнетатель воздуха для охлаждения двигателя инструмента способствует еще большему распространению композитной пыли. Поэтому при работе с углошлифовальной машинкой нужно использовать средства защиты глаз и органов дыхания, особенно, если предстоит пилить арматуру в помещении;
- для работы болгаркой необходимо иметь точку подключения к электричеству.
В общем, минусы довольно тривиальные.
Ножовка по металлу
Если предстоит выполнить всего несколько разрезов, можно использовать обычную ножовку по металлу.
Применение ручного инструмента дает следующие плюсы:
- ножовка по металлу найдется у каждого хозяина. Это самый простой и дешевый способ нарезать небольшое количество прутков для связки арматурного каркаса;
- отсутствие распыления мелких частиц, как в случае с УШМ.
Отрицательные моменты применения ножовки по металлу для резки композитной арматуры:
- низкая скорость работы;
- высокая нагрузка на работника, если необходимо выполнить большой объем работы;
- возможность использования только в индивидуальном строительстве при малых объемах работ.
Болторез
Перед тем, как резать композитную арматуру с помощью болтореза, также следует изучить плюсы и минусы работы с этим инструментом. Нужно понимать, что болторез выполняет не резку композитного прутка, а скорее его перекусывание, что сказывается на технических характеристиках материала.
Преимущества использования болтореза:
- не требуется подключение к электросети;
- при работе болторезом не образуется большого количества мелких частиц, поэтому готовить прутки по размеру можно внутри помещения;
- с болторезом в руках можно перемещаться и работать в любом месте (нет проводов).
Недостатки применения болтореза:
- с помощью болтореза нельзя разрезать одновременно более 3 прутков;
- при работе с этим инструментом необходимо задействовать значительные мышечные усилия;
- болторез редко находится в списке домашних инструментов. Для работы его придется брать в аренду или покупать, что экономически нецелесообразно;
- применение болтореза вызывает деформацию материала в месте разреза (на конце прута появляются крошки материала и продольные трещинки). Такая деформация снижает несущую способность арматуры, и сокращает срок ее службы.
Топор
При ограниченности в средствах, для подготовки арматуры может использоваться и топор. Он, как и болторез, перерубает пруток, что сказывается на состоянии арматуры в месте переруба.
Положительные моменты:
- топор есть у любого хозяина. Не требуется отдельно приобретать инструмент;
- скорость. При подготовке основания для рубки арматуры, выполнить работы можно довольно быстро.
Отрицательные моменты:
- неточность разреза. Не каждый мастер может точно и сильно попасть топором в нужное место, чтобы разрубить композитный пруток;
- деформация кончика прута. При эксплуатации в продольные трещины может попасть вода, цемент, щелочь, что приведет к нарушению технических характеристик стеклопластика и ослаблению всей конструкции. При изменениях температуры, расщепленная арматура внутри изделия будет изменяться в объеме, что приведет к разрушению бетона.
Рекомендации по резке композитной арматуры
Прежде, чем резать пластиковую арматуру своими руками, следует ознакомиться с мерами безопасности при выполнении работ.
При работе с электромеханическими инструментами необходимо использовать следующие средства защиты:
- респиратор. Мелкие композитные частицы быстро распространяются в воздухе, особенно если работы ведутся в помещении. Для защиты органов дыхания необходимо надевать респиратор и тщательно подгонять его по размеру лица;
- защитные очки. При резке стеклопластика углошлифовальной машинкой часто отлетают мелкие фракции. Попадание таких частиц в глаза чревато нарушением целостности роговицы и воспалительными процессами. Поэтому глаза защищают маской или специальными очками;
- перчатки с латексным слоем позволят защитить кожу рук от мелких частиц стеклопластика.
Как вязать стеклопластиковую арматуру для фундамента: видео, фото
Популярность вопроса о том, как наиболее правильно вязать стеклопластиковую арматуру для укрепления фундамента и других конструкций из бетона, обусловлена тем, что этот материал все активнее начинает использоваться как в капитальном, так и в частном строительстве. Многих из тех, кто собирается применять этот инновационный материал, также интересует вопрос и о том, насколько эффективно его использование для армирования стен строений, возводимых из блочных строительных элементов.
Армирующий каркас плитного фундамента – одна из сфер использования стеклопластиковой арматуры
История появления стеклопластиковой арматуры в строительстве
Стеклопластиковая арматура на самом деле не является новинкой на строительном рынке, она была разработана и начала производиться еще в 60-е годы прошлого столетия. Однако ее высокая стоимость на момент начала производства способствовала тому, что ее использовали для армирования только тех конструкций, в которых стальные укрепляющие элементы подвергались активной коррозии: бетонных конструкций, эксплуатирующихся в суровых климатических условиях, опор мостов и др.
Стеклопластиковая арматура будет лучшим решением при строительстве бетонных сооружений, контактирующих с морской водой
Активное развитие химической промышленности привело к тому, что со временем себестоимость производства стеклопластиковой арматуры значительно снизилась, что и позволило начать применять ее более активно. Широкому использованию данного материала способствовал и тот факт, что в 2012 году был утвержден государственный стандарт (31938-2012), согласно которому определяются требования не только к производству, но также к методам испытаний стеклопластиковой арматуры.
Согласно требованиям вышеуказанного нормативного документа, арматура из стеклопластиковых материалов может выпускаться в интервале диаметров от 4 до 32 мм. Но наибольшее применение, особенно в малоэтажном строительстве, приобрели изделия, диаметр которых составляет 6, 8 и 10 мм. В отличие от аналогичных изделий из стали, стеклопластиковая арматура отпускается заказчику не в виде отдельных прутков, а намотанной в бухты.
Арматура СП: удобная, лёгкая, устойчивая и упругая
В нормативном документе кроме технических характеристик стеклопластиковой арматуры оговорены требования к состоянию ее внешней поверхности. Согласно этим требованиям, на поверхности таких изделий не допускается наличие сколов, расслаиваний, вмятин и других дефектов.
Характеристики материала
Арматура, изготавливаемая из композитных материалов, в зависимости от используемого для ее изготовления непрерывного армирующего наполнителя, подразделяется на несколько категорий:
- стеклокомпозитная, которая обозначается аббревиатурой АСК;
- углекомпозитная, обозначаемая АУК;
- комбинированная или АКК;
- и ряд других категорий.
Физико-механические параметры полимерной арматуры различных видов
Выбирая композитную арматуру для укрепления фундамента или стен возводимых строительных конструкций, следует учитывать ее основные характеристики:
- предельная температура, при которой эта арматура может эффективно эксплуатироваться;
- предел прочности изделия, измеряемый при растяжении; данный параметр рассчитывается как отношение прилагаемой силы к площади поперечного сечения арматурного прутка, для изделий категории АСК он должен быть не меньше 800 МПа, а для арматуры АУК — не менее 1400 МПа;
- модуль упругости при растяжении; у углекомпозитной арматуры данный показатель превышает аналогичную характеристику стеклопластиковых изделий более чем в 2,5 раза;
- предел прочности изделия, измеряемый при его сжатии; для всех типов композитной арматуры данный показатель должен составлять не менее 300 МПа;
- предел прочности арматуры, измеряемый при поперечном срезе; для различных типов композитной арматуры данный показатель должен составлять: для арматуры АСК — 150 МПа и более; для АУК — более 350 МПа.
Арматура из металла или композитных материалов?
Принимая решение, какую арматуру использовать для укрепления фундамента или стен здания, следует сравнить характеристики традиционных изделий из металла и стеклопластика. По сравнению с металлическими, стеклопластиковая арматура обладает следующими преимуществами:
- исключительная устойчивость к коррозии: фундаменту, для укрепления которого использована композитная арматура, не страшно взаимодействие с кислотными, солеными и щелочными средами;
- обладая низкой теплопроводностью, стеклопластиковая арматура не создает мостиков холода, что является особенно актуальным качеством для эксплуатации зданий в климатических условиях нашей страны;
- материалы, применяемые для изготовления стеклопластиковой арматуры, являются диэлектриками, поэтому фундаменты и стены, для укрепления которых она использована, обладают абсолютной прозрачностью для радио и электромагнитных волн;
- вес композитной арматуры значительно ниже, чем масса изделий, изготовленных из металла;
прочность армирующих прутков из стеклопластика практически в 2–3 раза выше, чем у арматуры, изготовленной из металла; - по причине того, что композитная арматура поставляется заказчику в бухтах по 100–150 метров, при укреплении фундамента с ее использованием можно минимизировать количество стыковочных соединений, которые, как известно, являются наиболее слабыми местами в любой бетонной конструкции;
- приобретение композитной арматуры более экономически выгодно за счет того, что вы можете купить ровно такой объем, который вам необходим для укрепления фундамента или стен своего строения, не ориентируясь на фиксированную длину прутков, как в случае с изделиями из металла;
- коэффициент теплового расширения композитных материалов почти идентичен с аналогичным параметром бетона, поэтому в конструкциях, для армирования которых они используются, практически не возникает трещин.
Если сравнивать по стоимости, то затраты на использование металлических и стеклопластиковых изделий практически одинаковые.
Сравнение металлической и стеклопластиковой арматуры (нажмите для увеличения)
Самым значимым недостатком арматуры, изготовленной из стеклопластика, является достаточно низкий показатель ее прочности на излом, что ограничивает ее применение для укрепления сильно нагруженных бетонных конструкций.
Особенности использования композитной арматуры
Арматуру, которая изготовлена из композитных материалов, преимущественно используют для укрепления ленточных или плитных фундаментов в малоэтажном строительстве. Объясняется это тем, что данная арматура по причине своего относительно недавнего появления на отечественном строительном рынке еще мало изучена и не протестирована длительной практикой своего использования.
Прежде чем приступить к монтажу арматурного каркаса, необходимо подготовить опалубку для заливки будущего фундамента. Такая процедура выполняется по стандартной схеме, как и в случае использования металлической арматуры. Для армирования ленточных фундаментов небольших строений преимущественно используют композитные прутки диаметром 8 мм, что соответствует 12-ти миллиметровым изделиям из металла. В первую очередь из таких прутков вяжут сетки, из которых затем монтируют армирующий каркас.
Скрепление арматурной сетки с помощью вязальной проволоки
При использовании прутков из композитных материалов важно знать, как вязать стеклопластиковую арматуру так, чтобы из нее получился надежный каркас, который эффективно укрепит бетонную конструкцию. Элементами, которые позволят надежно и правильно связать такую конструкцию, могут быть пластиковые хомуты или обычная вязальная проволока. Выбор того или иного варианта зависит только от личных предпочтений и наличия под рукой тех или иных приспособлений.
Как изготовить надежный каркас для фундамента
Для того чтобы правильно изготовить основу для ленточного фундамента, для которого будет использоваться стеклопластиковая арматура, можно просмотреть обучающее видео и воспользоваться несложными рекомендациями. Итак, алгоритм изготовления такого каркаса выглядит следующим образом.
- Прежде чем вязать арматуру, необходимо составить чертеж своего будущего каркаса и нарезать все элементы для его изготовления по точным размерам.
- Поперечные прутья нижнего слоя арматурного каркаса позиционируют при помощи специальных фиксаторов. Устанавливать такие элементы можно как до начала сборки арматурного каркаса, предварительно вымерив размер его ячеек, так и после его готовности.
- Размер ячеек зависит в первую очередь от размеров ленточного фундамента, который вы собираетесь укреплять. Такой размер может варьироваться в достаточно широких пределах: 15–30 см.
- Продольные прутья арматурного скелета перед тем, как вязать, лучше предварительно разложить на земле и сделать на них отметки маркером в тех местах, где к ним будут фиксироваться поперечные элементы. Начав вязать арматуру, следует следить за тем, чтобы элементы фиксировались друг с другом строго под прямым углом.
- Поперечные перемычки нужно вязать с продольными элементами каркаса с их нижней стороны. Чтобы армирующий скелет и, соответственно, будущий фундамент получился надежным и устойчивым, пластиковые хомуты или вязальную проволоку в местах соединений следует вязать потуже.
- Изначально изготавливаются горизонтальные слои армирующего каркаса, только потом следует вязать их между собой вертикальными перемычками. Фиксировать вертикальные перемычки также необходимо с внутренней стороны ячеек каркаса, это позволит вам получить в итоге надежную и устойчивую конструкцию, которая не разъедется в процессе заливки бетона и будет отлично выполнять свои армирующие функции.
- Углы — это особое место армирующей конструкции, и им необходимо уделить отдельное внимание. Стеклопластиковую арматуру не рекомендуется самостоятельно гнуть под воздействием нагрева, что может самым негативным образом сказаться на ее прочностных характеристиках. Поэтому угловые элементы арматурного скелета лучше вязать из уже гнутых прутков, которые сегодня можно приобрести, либо аккуратно выполнять изгиб без теплового воздействия.
- После того, как арматурная конструкция будет полностью готова, ее необходимо аккуратно поместить во внутреннюю часть уже подготовленной опалубки.
Схема армирования углов ленточного фундамента
Схема армирования примыканий ленточного фундамента
Если вязать элементы арматурного каркаса при помощи проволоки, то для облегчения своего труда можно изготовить вязальный крючок, для чего удобно использовать старую отвертку. Как сделать такой крючок и вязать с его помощью арматурный каркас, так же можно ознакомиться по соответствующему видео.
Изготовление армирующего каркаса из прутков, которые сделаны из стеклопластика, — несложный процесс, о чем можно судить даже по обучающему видео, где подробно показано, как его вязать. Для работы с таким материалом, как стеклопластик, вам не потребуются специальные инструменты и сложное оборудование, его легко резать и вязать, он обладает более легким весом, чем арматура, изготовленная из металла.
В любом случае, выбирая такой материал для укрепления фундамента или стен своего дома или строения любого другого назначения, следует иметь в виду, что вы поступаете на свой страх и риск, так как стеклопластиковая арматура появилась недавно на отечественном строительном рынке, и ее характеристики еще не до конца подтверждены длительностью применения на практике.
Оценка статьи:
Загрузка…Поделиться с друзьями:
The Ultimate Fiberglass Repair Guide
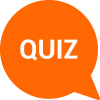
Хотите проверить свои знания в области ремонта стекловолокна? Пройдите нашу викторину по ремонту стекловолокна!
Обзор стекловолокна и композитов
Композитыобладают многочисленными преимуществами по сравнению с обычными строительными материалами. Одно из преимуществ, которое может быть неочевидным, – это простота и долговечность ремонта. Поскольку многим не хватает знаний для ремонта композитных деталей и форм, поврежденные детали часто заменяют; тем, у кого есть понимание новичка, процесс может сначала показаться пугающим.Не бойтесь, композитные детали часто легче ремонтировать, чем детали, сделанные из традиционных материалов. В этой статье мы дадим общее представление о ремонте композитных материалов, а также подробные инструкции и рекомендации, которым необходимо следовать при структурном и косметическом ремонте.
Если вы прочитали эту статью и не имели ранее представления о композитных материалах или типичных процессах производства композитов, вы можете прочитать некоторые дополнительные статьи в нашем учебном центре.У нас есть другие статьи, которые могут помочь в получении некоторых базовых знаний, в том числе о том, как начать работу с композитами, об основах стекловолокна, о смолах, об армировании и формовании стекловолокна. Более широкое понимание композитных материалов и методов производства, а также небольшая практика могут иметь большое значение для более успешного ремонта.
Перед тем, как перейти к сути статьи, мы будем использовать термины композитный ремонт и ремонт стекловолокна как синонимы.Это связано с тем, что описанные методы работают с любой структурой из стекловолокна, а также со многими «продвинутыми» композитами, изготовленными из углеродного волокна и KEVLAR®. Общие концепции применимы к большинству композитных материалов. Это означает, что мы предоставим вам основы для самых разных видов ремонта – от ремонта косметического гелькоута до промежуточного ремонта лодок и кузовов автомобилей – вплоть до ремонта структурных композитов. Однако есть одно предостережение: для некоторых частей могут потребоваться специальные процедуры, помимо описанных в этой статье.Производители высокотехнологичных или конструкционных деталей часто публикуют подробную информацию о ремонте, относящуюся к их деталям. Наша позиция заключается в том, что инструкции производителя заменяют всю другую информацию, которую мы предоставляем, и должны полностью выполняться. Как правило, инструкции производителя более конкретны и не противоречат стандартным процедурам ремонта, описанным здесь. Если не брать в расчет, если инструкции по ремонту стекловолокна, приведенные в этой статье, будут хорошо выполнены, в результате получится серьезный ремонт, независимо от того, делаете ли вы профессиональный ремонт композитов или ремонт стекловолокна своими руками.
Что нужно знать о ремонте стекловолокна?
Есть несколько фундаментальных принципов, понимание которых позволяет успешно завершить большинство ремонтов композитных материалов. Успешный ремонт позволяет продлить срок службы детали или формы и сэкономить на замене композитной детали. Начнем с рассмотрения трех основных принципов ремонта композитных материалов:
- Ремонт отличается от оригинальной детали. – Первый принцип, который вы должны понять, заключается в том, что структурный ремонт производится другим способом, нежели оригинальная деталь.При первоначальном изготовлении композитной детали ее смола затвердевает, соединяясь как химически, так и физически с армирующей тканью, в результате чего получается единый блок, независимо от количества или ориентации слоев ткани. Это называется первичной структурой или связью, и это самый прочный тип связи, который может существовать в составной части.
После повреждения детали все ремонты становятся вторичными связями, прикрепленными к исходной первичной структуре. Это означает, что весь ремонт зависит от физического соединения с поверхностью исходной первичной конструкции (подробнее об этом позже).По этой причине ремонт стекловолокна зависит от адгезионных качеств смолы для их прочности – прочности физического сцепления с первичной структурой. Из-за этого смола, используемая для ремонта, должна быть такой же прочной, как смола, использованная для изготовления детали. На самом деле, для ремонта иногда используются смолы с сильными адгезионными свойствами.
- Увеличенная площадь поверхности увеличит прочность ремонта композитных материалов. – Поскольку ремонт стекловолокна зависит от поверхностной адгезии (физического соединения) ремонта с первичной структурой, увеличение площади поверхности линии соединения повысит прочность и долговечность соединения – и по расширению запчасти или ремонт.
Как правило, для увеличения площади поверхности используется шлифование конуса или скоса. Этот тип шлифования означает, что область рядом с повреждением постепенно шлифуется, в результате чего обычно получается примерно ½-дюйма площади на слой композитного ламината. Шлифовка шарфов обычно выполняется с помощью высокоскоростной шлифовальной машинки со сжатым воздухом. Поскольку большинство композитных конструкций довольно тонкие, это щадящий процесс. Размер конуса относительно толщины ламината выражается в виде отношения.Как правило, чем сильнее или серьезнее должен быть ремонт, тем выше соотношение. Структурный ремонт обычно требует более мягкого конуса с соотношением от 20: 1 до 100: 1.
Альтернативный метод увеличения площади поверхности – ступенчатое шлифование. Эта процедура определяет размер внутреннего ремонта, затем удаляет окружающие материалы шириной ½ дюйма на слой детали, работая по направлению к поверхности детали. Это приводит к значительному увеличению ремонтной поверхности и позволяет четко определить ориентацию волокон. на каждом этапе.
Оба метода приемлемы для большинства ремонтных работ из композитных материалов, хотя большинство считает, что удаление зазоров проще, и в целом считается лучшим. Ступеньки приводят к резким краям и стыкам в каждом ремонтируемом слое. Трудно также шлифовать песок без разреза, что может привести к повреждению нижележащих слоев.
- По возможности, вы должны сопоставить свой ремонт с оригинальной деталью. – Хотя ваш композитный ремонт отличается от оригинальной детали, при ремонте рекомендуется продублировать толщину, плотность и ориентацию слоев оригинального ламината.Это поможет сохранить работоспособность детали. Больше не всегда лучше – в этом случае, если ваш ремонтный материал толще оригинальной детали, он почти наверняка будет жестче, независимо от используемого материала. Введение в деталь различной прочности может вызвать непреднамеренные точки напряжения, что в конечном итоге приведет к усталости материала или разрушению. Лучше аккуратно заменить каждый слой, который был удален в поврежденном месте, на идентичный материал, размещенный по возможности в той же ориентации.Такой подход с заменой слоя на слой гарантирует, что отремонтированная конструкция может выдерживать те же нагрузки, что и исходная, и что она будет распределять нагрузки, как задумано.
С учетом этих трех основных принципов: ремонт отличается от оригинальной детали, увеличенная площадь поверхности увеличивает прочность, а ремонт должен соответствовать исходной детали; у вас есть основа для понимания последовательности ремонта. Как было сказано ранее, мы собираемся предоставить подробные этапы как структурного ремонта стекловолокна, так и общего косметического ремонта композитного материала.Имейте в виду, что это общие шаги, и для некоторых приложений могут потребоваться дополнительные шаги или небольшие изменения в подходе.
Этапы ремонта из композитных материалов
- Проверить и измерить, идентифицировать и определить
- Удаление поврежденного материала и подготовка поверхности
- Ламинат ремонтная нашивка
- Осмотреть ремонт
Поскольку после ремонта структурного композитного материала обычно следует косметический ремонт, мы начнем с инструкций для более серьезных повреждений. В этом разделе мы ответим на часто задаваемые вопросы «Как ремонтировать стеклопластик?» и «Что нужно для ремонта стеклопластика».Это будет разбито на 4 этапа:
Осмотреть и измерить, идентифицировать и определить:
Как проверить поврежденные композиты
Существует четыре основных категории сложных повреждений. Ваш ремонт может включать одну или все эти категории в зависимости от серьезности удара или отказа.Категории следующие:
- Разрыв – Это повреждение возникает, когда предел прочности композитной детали был превышен и ламинат разрушился. Обычно это приводит к разрыву, который полностью проходит через подложку.
- Отверстие или прокол – Обычно это повреждение в результате удара или порезов. Отверстия и проколы иногда ограничиваются поверхностными слоями или оболочками.
- Crushed Core – Это повреждение относится только к композитным деталям, содержащим материалы многослойного сердечника. Обычно это результат удара, который заставляет композитную обшивку ламината прогибаться, но не разрушаться, в результате чего материал сердцевины сэндвича разрушается.
- Отслоение – Это повреждение приводит к тому, что слои материала отделяются друг от друга. Обычно это вызвано ударами или напряжением между слоями или между ними.
Как измерить объем вашего композитного ремонта
Как только вы поймете, какой тип повреждений у вас есть, мы рекомендуем вам использовать контрастный маркер, чтобы очертить границу повреждения. Это поможет вам понять масштаб и размер повреждений, а также даст вам возможность полностью осмотреть свою деталь. Однако обратите внимание, что вам следует внимательно осмотреть повреждения, поскольку проблемная зона часто выходит за пределы, которые можно легко обнаружить визуально.Один совет, который мы можем предложить, – это проверка монетоприемником. Постучав монетой по окружающему пространству, вы можете быстро и легко создать слышимую разницу между сплошным ламинатом, раздробленным материалом и потенциально расслоенным участком.
Стоит ли этот ремонт затраченных усилий?
После того, как станет известна степень повреждения и тип материала, вы должны определить, следует ли отремонтировать данную деталь или вам лучше заменить ее.Если вы обнаружили спецификации производителя при поиске необходимых материалов, проверьте, не слишком ли велика поврежденная область для ремонта. Если невозможно просмотреть информацию, мы рекомендуем вам быстро оценить материалы и рабочее время, необходимые для ремонта. Сравните эту цифру со стоимостью новой детали. Как правило, если вы можете добиться экономии не менее 50 процентов, значит, вы выполнили норматив, гарантирующий продолжение ремонта.
Удаление поврежденного материала и подготовка поверхности
Удаление поврежденного материала
Предполагая, что вы уже осмотрели поврежденный участок и отметили его контрастным маркером, можно приступить к удалению поврежденного материала.Когда деталь сломана или раздавлена, может быть трудно выровнять детали, потому что изношенные волокна имеют тенденцию «зависать» друг от друга. Чтобы сделать ремонт максимально надежным, вам нужно определить последовательность и ориентацию материала по мере его удаления слой за слоем. Чтобы помочь с этим, используйте лезвие пилы, чтобы разрезать по длине трещины или разрывы. Это снимет нагрузку с твердых ламинатов, часто позволяя им возвращаться к своей первоначальной форме с небольшим усилием или без него. Детали, изготовленные из материала сэндвич-сердечника, имеют тенденцию к блинчикам и грибовидным образованиям, что еще больше затрудняет переналадку.Фрезерный станок отлично подходит для удаления поврежденного материала сердечника без нарушения целостности кожи лица.
При удалении поврежденного материала старайтесь удалить как можно меньше материала, чтобы объем ремонта не увеличился больше, чем необходимо. Однако не забудьте удалить достаточно материала, чтобы остался прочный ламинат, необходимый для хорошего ремонта. По мере удаления поврежденного материала периодически останавливайтесь и проводите еще одну проверку монетоприемником. Это позволит вам убедиться, что вы удалили весь поврежденный материал, и вам следует продолжать шлифование или резку, пока не будет удален весь поврежденный материал.
Поддержите деталь и подготовьте поверхность
После удаления поврежденного материала поддержите деталь, чтобы ничего не деформировалось во время ремонта. Иногда это так же просто, как приклеивание нескольких полосок малярной ленты шириной 2 дюйма, в других случаях это так же сложно, как изготовленная на заказ зажимная конструкция. Вообще говоря, высокопроизводительные детали имеют более жесткие допуски и требуют более точной системы поддержки. После того, как деталь будет закреплена, приступайте к подготовке склеиваемой поверхности.Как упоминалось выше, это обычно включает шлифование или шлифование конуса или ступенек в материале вокруг повреждения. Это критический шаг для функционального ремонта, но его часто упускают из виду или злоупотребляют. Не торопитесь и убедитесь, что ваш ремонт выполнен правильно.
Если необходимо использовать конус, измерьте глубину впадины и вычислите, насколько далеко должно пройти шлифование, чтобы достичь желаемого соотношения. С помощью контрастного маркера отметьте внешний край конуса и начните шлифование внутрь по направлению к впадине.Обязательно снимайте материал медленно, чтобы конус проходил равномерно. Открывая каждый слой, записывайте тип и ориентацию ткани, чтобы вы могли заменить ее таким же образом.
При ступенчатом шлифовании первоначальный расчет еще точнее. Например, предполагая, что повреждение является круглым, диаметром два дюйма и в ламинате пять слоев, отметьте концентрические круги, расширяющиеся на полдюйма на один слой от края самого внутреннего круга. Окончательный диаметр подготовленного участка составит семь дюймов.Начните шлифование в центре, пока не обнажится самый глубокий слой. Сделайте шаг на полдюйма и зашлифуйте до второго самого глубокого слоя и так далее, пока не будут готовы все пять шагов. Угловая шлифовальная машина обеспечивает наилучшее ощущение и контроль при выполнении этой деликатной процедуры.
При использовании любого метода для обеспечения личной безопасности и чистоты мы рекомендуем прикрепить к рабочей поверхности липкой лентой шланг промышленного пылесоса, чтобы пыль могла быть удалена во время шлифования. Кроме того, убедитесь, что вы носите респиратор и, если возможно, защитную одежду, так как это очень грязный процесс, и вы хотите быть максимально защищены.По окончании шлифования всю поверхность необходимо тщательно очистить. Пропылесосьте оставшуюся пыль, а затем тщательно протрите поверхность тряпкой для растворителя. Ацетона обычно достаточно для удаления масла, жира, пыли, воска или других поверхностных загрязнений, которые потенциально могут повлиять на адгезию вашего ремонта.
Полезные продукты
Ламинат ремонтный пластырь из стекловолокна
Подготовьте композитные заплаточные материалы
Первый шаг к ламинированию ремонтной заплатки – это предварительная обрезка материала заплатки для соответствия ремонту.Это включает в себя предварительную обрезку материала сердечника и всех слоев усиления, чтобы они соответствовали конусу, который вы подготовили, когда вы подготовили поверхность. Если ваша деталь состоит из многослойного материала сердцевины, сначала вырежьте сердцевину, чтобы заполнить самое глубокое отверстие. Обратите внимание, что некоторые основные материалы, такие как Nomex® Honeycomb, имеют свою собственную ориентацию, которую необходимо выровнять в детали. Обязательно проверьте это как для сэндвич-сердцевины, так и для армирующей ткани, сверяясь со списком, который был составлен в процессе подготовки, чтобы каждый слой армирования был обрезан для правильной ориентации.Обрежьте каждый слой так, чтобы он точно входил в область конуса или ступеньку, которая была подготовлена для него. Современный ремонт проводится послойно, поэтому самая маленькая деталь должна сначала попасть на дно впадины. Укладывайте арматуру рядом с тем местом, где она будет использоваться, при этом первый слой должен быть размещен в области склеивания поверх стопки.
Отмерьте, перемешайте и нанесите смолу
Как только ваши заплаточные материалы будут подготовлены, предварительно взвесьте график армирования.При ремонте вы должны ориентироваться на соотношение волокна и смолы 50:50, поэтому, взвесив арматуру, отмерьте такой же вес смолы. Добавьте катализатор или отвердитель и перемешайте смолу в соответствии с инструкциями.
После того, как вы отмерили и смешали смолу, начните с предварительного смачивания смолой всей области склеивания. Это позволит вам создать пленку из смолы по всей площади склеивания, увеличивая физическое скрепление. Затем вы можете начать пропитывать каждый слой арматуры перед его укладкой на деталь.Работайте с пластиковым листом, чтобы ткань можно было легко снять со стола, когда она будет готова. Гибкий резиновый ракель – лучший инструмент для равномерного распределения смолы по ткани и удаления излишков смолы, которая может присутствовать. Поместите каждый слой арматуры на место ремонта, соблюдая правильную ориентацию. Фото предоставлено IStock Photo.
Останавливайте слой через каждые несколько слоев, чтобы максимально уплотнить и уменьшить плотность заплатки. Количество слоев, которые вы можете нанести между удалением налетов, зависит от веса ткани и используемого переплетения, но обычно вам следует удалять массу через каждые 3–5 слоев.Для этого хорошо подойдет ракель или валик из стекловолокна. Продолжайте складывать ремонтные слои, пока вся удаленная ткань не будет заменена. Затем можно добавить последний поверхностный слой, чтобы покрыть всю площадь. Планируйте уплотнение окончательной ремонтной заплаты как можно плотнее, пока смола застывает. Метод вакуумной упаковки в мешки – наиболее универсальный метод, но ракели, ролики или другое прижимное давление будут работать адекватно. Следуйте рекомендациям производителя по отверждению смолы. Если был запланирован двусторонний ремонт, подготовка к противоположной стороне может начаться после полного отверждения первого пластыря, обычно через 48 часов.
Полезные продукты
Осмотр ремонта
- Осмотреть, измерить и идентифицировать.
- Удаление поврежденного материала и подготовка поверхности
- Смешать и нанести наполнитель
- Отполировать ремонтную площадь
Как проверить композитный ремонт
Перед тем, как вернуть отремонтированную деталь в эксплуатацию, необходимо осмотреть ремонт. Используйте метод монетоприемника, чтобы проверить ремонт после того, как он полностью затвердел. Вся конструкция должна резонировать с таким же твердым звуком. Для большего спокойствия или большего количества критических деталей на этом этапе также может быть реализовано неразрушающее нагрузочное тестирование.Это состоит в том, чтобы нагружать деталь до ожидаемого предела обслуживания, но не выше. Если деталь выйдет из строя преждевременно, даже если неисправность возникла вне вашего ремонта, ее следует выбросить. Для более ответственных структур может потребоваться испытательная лаборатория или специализированное оборудование до утверждения.
Если ваша деталь прошла техосмотр, можно приступать к косметическому ремонту.
Этапы косметического ремонта
Внешняя косметическая отделка детали спроектирована так, чтобы скрыть и защитить структурное усиление, расположенное ниже, а также при этом быть эстетически приятной.Именно на эту поверхность большинство людей будет смотреть и оценивать всю структуру. Даже небольшие повреждения, такие как царапины и вмятины, испортят внешний вид. Хуже того, они часто создают прямой путь к структурным слоям, вызывая еще большие проблемы. Косметические пузыри – это проблема, которая, если ее не лечить, может превратить весь корпус лодки в губки.
Последовательность ремонта косметического композита аналогична последовательности структурных изменений, но армирующий материал заменяет обтекатель, заполняющий состав и / или гелькоут.Подготовка поверхности по-прежнему остается самым важным аспектом длительного ремонта. Финишное шлифование и полировка представляют собой дополнительный этап, но время, потраченное на этот этап, может привести к действительно профессиональному ремонту композитного материала. Многие люди опасаются заниматься косметической работой, поскольку считают, что для получения удовлетворительных результатов требуется дорогостоящее оборудование для распыления. Несмотря на то, что оборудование имеет важное значение, правильный выбор материалов является ключом к положительным результатам.
В этом разделе мы дадим рекомендации по косметическому ремонту композитов, включая ремонт трещин стекловолокна, ремонт стекловолоконного гелевого покрытия и отделку композитного ремонта.Он будет разбит на 5 шагов, которые аналогичны тем, которые требуются для ремонта конструкции:
Теперь давайте рассмотрим каждый из них более подробно.
Осмотреть, измерить и идентифицировать
Как проверить косметические повреждения
Обследование косметических повреждений так же важно, как и структурных повреждений.Существует четыре основных категории косметических композитных повреждений, и вы можете найти один или все эти типы повреждений в зависимости от того, через что прошла ваша часть. Категории следующие:
• Gouge Канавка – это длинная глубокая выемка на поверхности, достаточно серьезная, чтобы потребовать наполнителя и покрытия для ремонта поверхности. Порезы обычно возникают из-за грубого обращения, скользящих ударов или неправильной прокладки.
• Волдыри Волдыри – это выпуклости, появляющиеся на поверхности детали.Обычно это вызвано попаданием жидкости или газа в подложку, отталкивающей кожу от стекла.
• Царапины Царапины похожи на выбоины, но недостаточно глубокие, чтобы их можно было заполнить. Царапины, как правило, можно исправить без использования шпатлевки.
• Трещины Трещины с трещинами – это микротрещины, которые не проходят через толщину детали, а иногда даже не проходят через толщину поверхностного покрытия.Растрескивание обычно вызывается чрезмерным напряжением детали, тепловыми проблемами или напряжением между слоями или между ними.
Как измерить объем вашего композитного ремонта
Как только вы поймете, какой тип повреждений у вас есть, мы рекомендуем вам использовать контрастный маркер , чтобы очертить границу повреждения. Обратите внимание, что зазубрины часто оставляют поднутрения на неподдерживаемом гелевом покрытии, что на первый взгляд кажется нормальным.Однако если надавить на них тупым инструментом, они легко треснут. Очень важно, чтобы все поврежденные участки были полностью идентифицированы, чтобы их можно было правильно подготовить в следующей процедуре. После того, как вы определили и отметили свои участки, определите приблизительную площадь поверхности, требующую ремонта.
Как определить композитные ремонтные материалы
После того, как вы успешно определили размер и масштаб косметического повреждения, вы сможете приблизительно оценить, сколько требуется ремонтного материала.Порезы и волдыри потребуют как наполнителя, так и гелевого покрытия, а царапины и трещины обычно можно исправить с помощью одного гелькоута. Если ваша деталь изначально была сделана из полиэфирной смолы, для ремонта подойдут полиэфирные шпатлевки и гелькоут. Если вы не уверены, мы также предлагаем эпоксидные наполнители, а также грунтовку Duratec® Surfacing Primer, которая обеспечит поверхность, с которой может связываться эпоксидная или полиэфирная смола.
Полезные продукты
Товар | .Описание | |
---|---|---|
Обтекатель и заправка | Они используются для заполнения более глубоких царапин и повреждений.Убедитесь, что ваш состав соответствует смоле, которую вы использовали для ремонта | |
Гель-коут | Гелевые покрытиябывают разных цветов, чтобы соответствовать исходному цвету детали, которую вы ремонтируете. | |
Duratec Surfacing Primer | Duratec Surfacing Primer позволяет создать на вашей детали поверхность, на которую эпоксидная смола или полиэстер могут лучше держаться. |
Удаление поврежденного материала и подготовка поверхности
Удаление поврежденного материала
Как для выбоин, так и для пузырей необходимо убедиться, что неподдерживаемый поверхностный материал удален.Как упоминалось ранее, это можно сделать, нажав на них тупым инструментом. После удаления неподдерживаемого материала протрите поверхность ацетоном и тряпкой, чтобы удалить воск, масло или жир, которые могут загрязнить ремонт.
Когда поверхность высохнет, заклейте область вокруг повреждения. Это сведет к минимуму шлифовку царапин на неповрежденных участках. Затем удалите весь отслоившийся материал канцелярским ножом, а затем используйте наждачную бумагу с зернистостью 40, чтобы скосить края до конуса.Даже тонкие трещины необходимо «вскрыть», прежде чем можно будет добавить материал для их заполнения. На этом этапе необходимо полностью обнажить волдыри. Пока вы расширяете поврежденную область, убедитесь, что оставшийся ламинат твердый и сухой. Если ламинат не твердый и сухой, возможно, вам придется выполнить дополнительный структурный ремонт перед завершением косметического ремонта.
Подготовить поверхность
После того, как вы удалили поврежденный материал и раскрыли трещины, используйте наждачную бумагу средней зернистости, чтобы слегка отшлифовать окружающую область.Это даст вам возможность перенести ремонт на неповрежденную поверхность. После шлифования поверхности протрите поверхность ацетоном в последний раз, чтобы удалить пыль и все остальное, что может нарушить адгезию.
Полезные продукты
Товар | .Описание | |
---|---|---|
Наполнители | При заделке более глубоких бороздок в детали фрезерованные волокна смешивают со смолой, чтобы получить структурную замазку для ремонта. | |
Ацетон | Ацетон – популярный растворитель, который используется для удаления загрязнений из зоны ремонта, предотвращая возможные осложнения | |
ПВС | PVA или поливиниловый спирт можно распылить на поверхность ремонтируемого участка, чтобы получить отверждение без липкости и шлифования. | |
Наждачная бумага | Шлифовка зоны ремонта позволяет скосить края зоны ремонта до конуса, что упрощает процесс ремонта |
Смешать и нанести наполнитель
Заполнение неглубоких царапин и трещин гелевым покрытием
Мелкие царапины можно напрямую заполнить гелевым покрытием соответствующего цвета, а не шпатлевкой.Убедитесь, что вы подбираете гелькоут к отшлифованной и полированной части оригинала, а не к общему выцветшему цвету. Ваш ремонт может поначалу выделяться, но примерно через месяц все поблекнет до такого же цвета. При использовании гелькоута для заполнения царапины используйте небольшую кисть, чтобы нанести гелькоут. Убедитесь, что она выше окружающей поверхности, чтобы ее можно было отшлифовать заподлицо. Нанесите тонкий слой ПВА на ремонт, чтобы отвердить, не оставляя следов.
Заполнитель для глубоких царапин, выбоин и пузырей
Глубокие канавки потребуют структурной ремонтной шпатлевки для замены отсутствующего материала перед нанесением финишного слоя гелевого покрытия.Смола, смешанная с измельченным стекловолокном толщиной 1/32 дюйма, является отличной структурной замазкой. Мы также предлагаем широкий выбор обтекателей и наполнителей на основе как полиэфира, так и эпоксидной смолы. С помощью ракеля нанесите выбранный наполнитель на дно канавки. Если гелевое покрытие является предполагаемым верхним слоем, держите этот наполнитель немного ниже окружающей поверхности. При окраске шпатлевка может быть на одном уровне с поверхностью, так как краска добавляет немного густоты. При заполнении пузырей, например, при ремонте корпуса лодки из стекловолокна, обязательно используйте винилэфирную смолу с фрезерованными стекловолокнами для замазки.Это добавит дополнительную защиту от коррозии этим ослабленным участкам.
Если ваш косметический ремонт следует за структурным ремонтом, может потребоваться выровнять структурную заплату с помощью сплошного ламината. Для этого может потребоваться как измельчение, так и заполнение. Отшлифуйте все выступы до тех пор, пока они не будут на одном уровне с остальной поверхностью, если это не ухудшит структурную прочность заплатки. Используйте наполнитель, чтобы выровнять все углубления. Если шлифование невозможно по структурным причинам, можно слегка добавить наполнители для сглаживания неровностей и отшлифовать до гладкого пера, но при этом пятно всегда будет видно.Для ремонта судов используйте шпатлевку для фрезерованного стекла толщиной 1/32 дюйма, как описано ранее. Другие структуры обычно можно заполнить стандартными наполнителями или смешиванием талька и смолы, если не указано иное. Продолжайте добавлять шпатлевку и шлифовать, пока поверхность не станет идеально ровной.
Ремонтные работы на эпоксидной смоле после затвердевания довольно стабильны, но ремонтные работы на основе полиэстера перед окончательной отделкой следует слегка нагреть. Полиэфирная смола в ремонтной заплате и в стандартном наполнителе кузова часто продолжает некоторое время давать усадку под воздействием тепла.Этого можно избежать, если вы используете один из наших безусадочных полиэфирных наполнителей, а в противном случае просто поместите проект на несколько дней на солнце или установите нагревательную лампу. Однако, если используется лампа, не помещайте деталь слишком близко и не оставляйте ее слишком долго. Вы пытаетесь «заставить» наполнитель дать усадку перед окончательной шлифовкой, и не хотите деформировать деталь. Как только вы отшлифуйте идеальный контур, ваша деталь будет стабилизирована от будущих тепловых проблем.
Смешайте и нанесите верхнее покрытие соответствующего цвета
Для отделки гелькоутом
Если гелькоут является предполагаемым верхним слоем, мы всегда рекомендуем его нанесение распылением.Мы продаем различные пистолеты-распылители различных размеров, с которыми вы можете столкнуться при ремонте, от полноразмерного пистолета для чашек с гелевым покрытием до нашего распылителя Preval, который можно использовать для самого небольшого ремонта. Все гелькоуты, которые мы продаем, разработаны для нанесения с помощью пистолета-распылителя, и этот метод нанесения обеспечивает наилучшую отделку поверхности. Специально для ремонта мы рекомендуем смешать гелькоут с добавкой Duratec® Hi-Gloss. Эта добавка позволит отверждать на открытом воздухе, разбавить гелькоут и уменьшить апельсиновую корку.Это означает, что вам не нужно добавлять воск, который потребует дополнительных усилий, гелькоут будет легче распылять, и вам придется меньше шлифовать и полировать, чтобы закончить ремонт. Для нижеследующего ремонта ватерлинии на морских проектах рекомендуется использовать поверхностный агент, такой как ПВА или стирольный воск, чтобы гарантировать полное отверждение. Воск отлично подходит для больших, труднодоступных участков, но он может помутнить прозрачные гелькоуты. ПВА лучше всего использовать для точечного ремонта или там, где легко получить доступ, пока гелькоут еще влажный.
Гель-покрытие необходимо отшлифовать перед окончательной полировкой. Используйте шлифовальный блок из твердой резины и начните с влажной / сухой бумаги зернистостью 400, чтобы выровнять гелькоут. Сосредоточьте усилия на шлифовании только на выступах, пока все не станет на одном уровне. Затем используйте пенопласт и более мелкую наждачную бумагу для идеальной отделки. Обязательно меняйте воду каждый раз, когда вы переходите на более мелкую наждачную бумагу, чтобы частицы пыли от более грубой бумаги не продолжали резать поверхность.
Для лакокрасочного покрытия
Если краска является вашим верхним слоем, под нее стоит нанести грунтовку.Грунтовка скроет мелкие неровности, которые могут еще существовать, а также герметизирует заплату. Для большинства ремонтных работ Duratec® Surfacing Primer – лучший материал для этой задачи. Он имеет высокую температуру тепловой деформации, что дополнительно защищает уже стабилизированные участки от усадки. Большинство лакокрасочных систем придерживаются затвердевшей эпоксидной смолы, поэтому перед использованием обязательно проверьте свою краску на предмет рекомендаций по грунтовке.
Полезные продукты
Отполировать ремонтную площадь
Как закончить композитный ремонт
Последний этап профессионального ремонта композитных материалов – шлифовка и полировка.Наши полироли для форм №1102 и №1103 идеально подходят для использования с полиэфирными и эпоксидными заплатами или гелевыми покрытиями. Для полировки лакокрасочного покрытия вам понадобится только № 1103, наш состав для Шага 2. Эти составы быстро удалят мелкие царапины, оставленные бумагой с зернистостью 600-1000, а также удаляют излишки распыления и некоторые эффекты ореола, которые обычно возникают при точечном ремонте. Полироль Step 2 придаст вашему ремонту желаемый блеск для окончательного сияния.
А как насчет SMC? Как мне восстановить SMC?
Листовой композит (SMC) – это композитный материал, который часто используется на рынке автомобильных, промышленных и персональных гидроциклов.SMC создает уникальные проблемы с ремонтом, поэтому мы кратко их обсудим.
Во-первых, важно отличить SMC от других типов композитов FRP, чтобы можно было выполнить надлежащий ремонт. Детали, изготовленные с использованием SMC, обычно производятся в пресс-формах, что делает их гладкими как внутри, так и снаружи – обычно это первая подсказка для их идентификации. Далее, детали из SMC не имеют внешнего гелевого покрытия, а обычно окрашиваются в цвет и иногда окрашиваются.Наконец, когда краска отшлифована из SMC, короткие грубые волокна обнажаются, и образующаяся пыль более сухая и более порошкообразная, чем другие композиты. Эти подсказки облегчат идентификацию SMC.
Далее необходимо выбрать подходящую смолу. Хотя SMC является материалом на основе полиэстера, его нельзя отремонтировать полиэфирной смолой. Это связано с тем, что смазка для пресс-формы присутствует по всей части SMC. В отличие от обычных формованных деталей, где на поверхность формы наносятся разделительные агенты, SMC смешивают с разделительным агентом, диспергированным в смеси смол для более быстрой обработки.Это означает, что по мере шлифовки повреждений для подготовки хорошей склеиваемой поверхности свежий разделительный состав становится открытым. Продукты из полиэфирной смолы не обладают достаточно прочной физической связью для прилипания к этой поверхности. Из-за этого SMC следует ремонтировать только с использованием эпоксидных смол, наполнителей и клеев.
Как завершить ремонт SMC? Большинство ремонтов SMC будет окрашиваться, и следует использовать только системы окраски каталитического типа.
Сводка
- Start Smart : тщательно осмотрите повреждения, четко отметьте их, определите, из какого материала изготовлена оригинальная деталь, и решите, имеет ли смысл ремонт.
- Подготовка – ключ к успеху : Сфера номер один, определяющая успех ремонта стекловолокном, – это удаление поврежденных материалов и надлежащая подготовка склеиваемой поверхности.
- Планирование ремонта : Сделайте ремонт конструкции послойно, послойно, предварительно нарежьте материалы и используйте соответствующую смолу. Для косметического ремонта имейте под рукой соответствующие материалы и не делайте для себя больше работы, чем необходимо.
- Осмотр и завершение : После ремонта конструкции обязательно осмотрите деталь перед тем, как снова ввести ее в эксплуатацию. После того, как вы сделали косметический финиш, потратьте дополнительное время, чтобы убедиться, что он сияет.
Композиты – это растущая категория, которая получает все большее распространение во всех типах современных транспортных средств, конструкций и оборудования для отдыха.Чем больше их используют, тем больше они начнут утомляться и ломаться; когда детали ломаются, их все не нужно заменять. Следуя этим процедурам, вы можете быть достаточно уверенными, чтобы приступить к выполнению простых ремонтных работ. Немного попрактиковавшись, вы сможете перейти к более сложным задачам. Эта статья предназначена для того, чтобы помочь любому начать работу. Собираетесь ли вы набраться смелости, чтобы заняться ремонтом ванны из стекловолокна, ремонтом бассейна или ремонтом кузова автомобиля, в этой статье мы можем дать вам советы по ремонту стекловолокна, необходимые для начала работы.Практика отточит и улучшит ваше мастерство, но следование этим простым рекомендациям позволит вам добиться положительного результата с первого раза.
В заключение обязательно запомните эти несколько ключей к успешному ремонту.
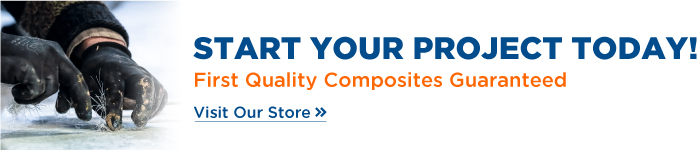
Детализация железобетонной балки в соответствии с ACI Code
Ясно, что детализация железобетонных элементов является ключом к хорошему проектированию и выполнению работ на объекте. Поэтому плохая детализация арматуры приводит к растрескиванию конструкции, чрезмерному прогибу, или даже коллапс.
Арматура выдерживает силу растяжения. Они также могут потребоваться в зонах сжатия для увеличения способности к сжатию, увеличения пластичности, уменьшения длительных прогибов или увеличения способности балок к изгибу.
Кроме того, они предотвращают растрескивание бетона из-за усадки и температурных напряжений.
Наконец, в следующих разделах объясняются различные аспекты детализации железобетонных балок на основе Кодекса ACI.
Виды армирования в балке
- Основные стержни (нижние стали) – выдерживают силу растяжения
- Верхние стержни (анкерные стержни) – удерживайте хомуты в их положении
- Отрезные стержни – выдерживают усилия натяжения
- Стремена с разной шириной захвата – ножницы вертикальные и диагональные.
Анкер с крючком
Функция крючковых анкеров заключается в обеспечении дополнительной анкеровки, когда прямой длины недостаточно для создания стержня.
Обычно стандартные хуки, описанные в разделе 7.1 Кодекса ACI, используются, за исключением случаев, когда это специально указано.
Стандартные крючки ACI следующие:
Стандартные крючки ACI для первичного армирования
- Изгиб на 180 градусов плюс удлинение на 4 дБ, но не менее 65 мм на свободном конце стержня.
- Изгиб на 90 градусов плюс удлинение на 12 дБ на свободном конце стержня.

Рис.1: Стандартный крюк, 180 градусов

Рис.2: Стандартный крюк, 90 градусов
Крючки стандартные ACI для хомутов
- 16 бар и меньше, изгиб на 90 градусов плюс удлинение на 6 дБ на свободном конце стержня.
- 19, № 22 и № 25 бар, изгиб на 90 градусов плюс удлинение на 12 дБ на свободном конце стержня
- 25 бар и меньше, изгиб на 135 градусов плюс удлинение на 6 дБ на свободном конце стержня.

Рис.3: Крюки со скобами

Рис.4: сейсмический хомут, 135 °
Минимальный диаметр изгиба
Стандартные изгибы в арматурных стержнях описываются с точки зрения внутреннего диаметра изгиба, потому что его легче измерить, чем радиус изгиба.
Основными факторами, определяющими минимальный диаметр изгиба, являются возможность изгиба без разрушения и предотвращение раздавливания бетона внутри изгиба.
- Диаметр изгиба, измеренный на внутренней стороне стержня, кроме хомутов типоразмера No.С 10 по 16, не должно быть меньше значений, указанных в таблице 1.
- Внутренний диаметр изгиба для хомутов должен быть не менее 4 дБ для бар № 16 и менее. Для прутков больше № 16 диаметр изгиба должен соответствовать таблице 1.
- Внутренний диаметр изгиба в арматуре сварной проволоки для хомутов должен быть не менее 4 дБ для деформированной проволоки крупнее MD40 и 2 дБ для всех остальных проволок. Отводы с внутренним диаметром менее 8 дБ должны находиться на расстоянии не менее 4 дБ от ближайшего сварного пересечения.
Таблица 1 минимальный внутренний диаметр крюков в зависимости от размера стержней
Размер стержня | Минимальный диаметр |
№ 10 по № 25 | 6 дБ |
№ 29, № 32 и № 36 | 8 дБ |
№ 43 и № 57 | 10 дБ |
дБ – диаметр стержня |

Рис.5: Внутренний диаметр стержня с крюком
Стремена
При детализации балки специалист по деталям или проектировщик должен указать размеры, расстояние, расположение и типы всех хомутов, включая открытые и закрытые хомуты.хомуты могут быть вертикальными или наклонными.

Рис.5: Различные конфигурации хомутов
Кроме того, если конструкция требует закрытых хомутов для сдвига, укупорочное средство может состоять из перекрывающихся, стандартных 90 o концевых крюков одно- или двухкомпонентных хомутов или правильно соединенных пар U-образных хомутов.
Кроме того, когда конструкция требует закрытых стяжек для скручивания, укупорочное средство может состоять из стандартных 135 o крючков с одной или двумя стяжками внахлест, охватывающих продольный стержень.
Наконец, существуют различные методы крепления хомутов, но наиболее распространенным является использование одного из стандартных крючков, как показано на рисунках 3 и 4.
Длина развертки (ld)
Длина проявления (ld) – это самая короткая длина стержня, на которой напряжение стержня может увеличиваться от нуля до предела текучести (fy). Он отличается по растяжению и сжатию, и основное уравнение для каждого случая выглядит следующим образом:
Длина развертки при растяжении
Используйте следующее выражение для расчета длины развертки при растяжении, но не менее 30.48см.
Где:
cb: коэффициент наименьшего размера боковой крышки. покрытие на стержне или проволоке (в обоих случаях измеряется до центра стержня или проволоки)
Ktr: коэффициент, который обозначает вклад ограничивающего армирования через потенциальные плоскости разделения.
: традиционный коэффициент расположения арматуры для отражения неблагоприятных воздействий положения заливки верхней арматуры.
: коэффициент покрытия, отражающий эффект эпоксидного покрытия.Произведение
не должно превышать 1,7.
: коэффициент размера арматуры, который отражает более благоприятные характеристики арматуры меньшего диаметра.
: коэффициент, отражающий более низкую прочность на разрыв легкого бетона и, как следствие, уменьшение сопротивления раскалыванию, что увеличивает длину разработки в легком бетоне.
(cb + Ktr) / db равно 2,5, если результат (cb + Ktr) / db меньше 2,5.
дБ: диаметр стержня
Atr: общая площадь поперечного сечения всей поперечной арматуры в пределах расстояния s.
n: количество стержней или проволок, разворачиваемых вдоль плоскости разделения
Длина развертки при сжатии
Длина разверткиможет быть рассчитана по наибольшей из следующей формулы, но она не должна быть меньше 20,32 см.
ldc = (0,02fy /) db Уравнение 3
ldc = ((0,0003fy) db Уравнение 4
где
ldc : длина развертки в стержнях сжатия
fy : предел текучести прутков
db : диаметр стержня
Разработка комплектных стержней
Индивидуальная длина развертки стержня в связке при растяжении или сжатии должна быть такой же, как у отдельного стержня, увеличенной на 20 процентов для связки из трех стержней и на 33 процента для связки из четырех стержней.
Длина развертки ldh для стандартных крюков в натяжении
Длина развертки ldh для стандартных крюков в натянутом состоянии определяется как:
Где:
= 1,2 для арматуры с эпоксидным покрытием
= 1,3 для бетона на легких заполнителях.
Для остальных случаев и
равны 1,0.

Рис.5: развертка концевых крючков
Отрезок стержня в балках и длина развертки в изгибной арматуре
Пруток отрезанный в балке
Обычно арматура располагается рядом с нижней частью балок, чтобы противодействовать действию растягивающих усилий на балку.
Кроме того, это усиление рассчитано на основе максимальных моментов в средних пролетах и на поверхности опор. эти моменты уменьшаются в областях балки, кроме средних пролетов и опорных поверхностей.
Следовательно, можно отрезать стержни в зонах, где они больше не нужны. следовательно, отрезанные бруски обеспечивают экономические преимущества.
Тем не менее, обрезка стержней должна быть по возможности минимальной, чтобы уменьшить сложность проектирования и строительства.
Кроме того, важно, чтобы отрезанные стержни выходили за пределы точки отрезания на длину развертки (ld), чтобы обеспечить адекватное сцепление стержня с бетоном.Продолжительность разработки будет обсуждаться в следующем разделе.
Наконец, расположение точек, где стержни больше не нужны, зависит от напряжений при изгибе, возникающих в результате изгибающих моментов, и влияния сдвига на эти растягивающие силы.

Рис.6: Отрезные планки
Строительная длина при изгибном армировании балок
В балках длина развертки обеспечивается в точках критического напряжения. Точки критического напряжения в балках – это точки максимальных положительных и отрицательных моментов – это критические сечения, от которых должно быть обеспечено соответствующее крепление.
Кроме того, критические точки также находятся в точках внутри пролета, где происходит отсечение соседней арматуры; продолжающиеся стержни должны иметь адекватное крепление ld от теоретических точек отсечки ограниченных стержней.
Кроме того, отрезанные стержни должны выходить за теоретические точки отсечки, чтобы противостоять изгибу на расстояние, равное d или 12 дБ.
Разработка усиления положительного момента
Для простых элементов минимум одна треть усиления с положительным моментом и одна четверть от усиления с положительным моментом в неразрезных элементах должна проходить вдоль поверхности элемента в опору.
Эти усиления в балках должны доходить до опоры не менее 152,3 мм.
Разработка усиления отрицательного момента
Отрицательное подкрепление момент в непрерывном, сдерживается, или член кантилевера, или в любом члене жесткой рамы, должно быть закреплено в или через опорный элемент по длине заделки, крючков или механическим анкеру.
Кроме того, не менее одной трети общей растягивающей арматуры, предусмотренной для отрицательного момента на опоре, должна иметь длину заделки за точкой перегиба не менее d, 12 дБ или ширины пролета / 16, в зависимости от того, что больше.

Рис.6: Крепление арматуры с отрицательным моментом

Рис.7: Типовые детали армирования непериметрических балок с открытыми хомутами

Рис. 8: Типовые детали армирования непериметрических балок с закрытыми хомутами

Рис.9: Типовые детали армирования балок по периметру
,ОБРЕЗКИ И ТОЧКИ ИЗГИБА АРМАТИКИ
Отрезки и точки изгиба арматурных стержней
Обычная практика – резать или гнуть основную арматуру в балках и плитах там, где она больше не требуется. Но ни в коем случае нельзя прерывать производство прочной стали точно в теоретических точках отсечки или изгиба. Необходимо противодействовать растягивающим усилиям в арматуре за счет заделки за пределами этих точек.
Вся арматура должна выходить за пределы точки, в которой больше не требуется сопротивляться изгибу, на расстояние, равное эффективной глубине элемента или 12 диаметрам стержня, в зависимости от того, что больше, за исключением опор простых пролетов и свободного конца консоли. ,Меньшие удлинения можно использовать на опорах простого пролета и на свободном конце консоли.
Продолжающаяся арматура должна иметь длину заделки, превышающую точку, в которой изогнутая или оконцованная арматура больше не требуется для сопротивления изгибу. Длина заделки должна быть не меньше длины развертки l d .
Изгибная арматура не должна заканчиваться в зоне растяжения, если не выполняется одно из следующих условий:
1.Сдвиг составляет менее двух третей от обычно допустимого, включая поправку на срезную арматуру, если таковая имеется.
2. Непрерывные стержни обеспечивают вдвое большую площадь, необходимую для изгиба на отрезке, а срез не превышает трех четвертей допустимого значения (бар № 11 или меньше).
3. Стремена, превышающие обычно требуемые, предусмотрены в каждом направлении от среза на расстоянии, равном 75% эффективной глубины элемента. Площадь и шаг лишних хомутов должны быть такими, чтобы
Где, A v = площадь поперечного сечения хомута, дюйм 2
b w = ширина полотна, дюйм
S = шаг хомутов, дюйм
f y = предел текучести стали хомутов, фунт / кв. Дюйм
Расстояние между скобами не должно превышать , где
– это отношение площади отрезанных стержней к общей площади стержней растяжения в сечении, а d – эффективная глубина стержня.
Расположение теоретических срезов или точек изгиба обычно может быть определено по изгибающим моментам , поскольку напряжения в стали приблизительно им пропорциональны. Полосы обычно снимаются группами или парами. Так, например, если одна треть стержней должна быть изогнута вверх, теоретическая точка изгиба находится на участке, где изгибающий момент составляет две трети максимального момента. Точку можно найти аналитически или графически.
,Расчет прямоугольной железобетонной балки
Железобетонные балки – это конструктивные элементы, которые предназначены для восприятия поперечных внешних нагрузок. Нагрузки вызывают изгибающий момент, поперечные силы и в некоторых случаях скручивание по всей своей длине.
Кроме того, бетон прочен на сжатие и очень слаб при растяжении. Таким образом, стальная арматура используется для восприятия растягивающих напряжений в железобетонных балках.
Кроме того, балки выдерживают нагрузки от плит, других балок, стен и колонн.Они передают нагрузки на поддерживающие их колонны.
Кроме того, балки могут быть просто опорными, неразрезными или консольными. они могут быть выполнены в виде прямоугольного, квадратного, Т-образного и L-образного сечения.
Балки могут быть усилены отдельно или дважды. Последние используются, если глубина луча ограничена.
Наконец, в этой статье будет представлена конструкция прямоугольной железобетонной балки.
Рекомендации по проектированию
Прежде чем приступить к проектированию железобетонной балки, необходимо сделать определенные предположения.эти рекомендации предоставляются определенными кодексами и исследователями.
Следует знать, что опыт проектировщика играет важную роль в принятии этих предположений.
Глубина балки (h)
Не существует единой процедуры расчета общей глубины балки (h) для проектирования. Тем не менее, можно следовать определенным рекомендациям для расчета глубины балки, чтобы можно было удовлетворить требованиям отклонения.
- ACI 318-11 предоставляет рекомендуемую минимальную толщину для ненагруженных балок, если прогиб не рассчитан.т
- Канадская ассоциация стандартов (CSA) предоставляет аналогичную таблицу, за исключением одного непрерывного конца, который составляет 1/18.
Таблица 1 минимальная толщина не напряженных балок, если прогиб не рассчитан
Минимальная толщина, h | |||
Просто поддерживается | Один конец непрерывный | Оба конца непрерывные | Консоль |
Стержни, не поддерживающие перегородки или другие конструкции или не прикрепленные к ним, которые могут быть повреждены из-за больших прогибов | |||
л / 16 | л / 18.5 | л / 21 | л / 8 |
Примечания: Приведенные значения следует использовать непосредственно для элементов из бетона нормального веса и арматуры класса 420. Для других условий значения изменены следующим образом: a) Для легкого бетона, имеющего равновесную плотность ( wc) в диапазоне от 1440 до 1840 кг / м3, значения необходимо умножить на (1,65 – 0,0003 wc ) , но не менее 1,09. b) Для fy , кроме 420 МПа, значения следует умножить на (0.4 + fy /700) . |
- Глубину балки можно также оценить на основе отношения пролета к глубине. IS 456 2000 обеспечивает соотношение пролета к глубине для контроля прогиба балки, как указано в таблице 2.
Таблица 2 отношение пролета к глубине в зависимости от пролета и типа балок, IS 456 2000
Пролет балки | Тип балки | Отношение пролет / глубина |
до 10 м | Просто поддерживается | 20 |
Консоль | 7 | |
Непрерывный | 26 | |
Более 10 м | Просто поддерживается | 20 * 10 / пролет |
Консоль | – | |
Непрерывный | 26 * 10 / пролет |
Ширина балки (б)
Рекомендуется, чтобы отношение глубины балки к ее ширине составляло 1.От 5 до 2, причем наиболее часто используется верхняя граница 2. Расположение арматуры – один из основных факторов, определяющих ширину балки.
Таким образом, при оценке ширины балки необходимо учитывать минимальное расстояние между стержнями. Ширина балки должна быть равна или меньше размера колонны, поддерживающей балку.
Арматура
ACI 318-11 обеспечивает минимальный и максимальный коэффициент усиления. Коэффициент усиления – это показатель количества стали в поперечном сечении.
Таким образом, при расчете балки можно использовать любые значения в этом диапазоне. Тем не менее, на выбор влияют требования к пластичности, конструкция и экономические соображения.
, наконец, рекомендуется использовать максимальное усиление 0,6 *.
Размеры арматурного стержня
Обычно рекомендуется избегать использования стержней больших размеров для балок. Это связано с тем, что такие стержни вызывают растрескивание при изгибе и требуют большей длины для развития их прочности.
Однако стоимость установки стержней большого размера меньше, чем стоимость установки большого количества стержней малых размеров.
Кроме того, общие размеры стержней для балок варьируются от № 10 до № 36 (единица СИ) или от № 3 до № 10 (обычная единица США), а два стержня большего диаметра № 43 (№ 14) и № 57 (№ 18) используются для колонн.
Кроме того, можно комбинировать прутки разного диаметра для более точного соответствия требованиям к площади стали.
Наконец, максимальное количество стержней, которое может быть установлено в балке заданной ширины, зависит от диаметра стержня, минимального расстояния, максимального размера заполнителя, диаметра хомута и требований к бетонному покрытию.
Расстояние между стержнями
ACI 318-11 указывает минимальное расстояние между стержнями, равное диаметру стержня или 25 мм. Это минимальное расстояние должно соблюдаться, чтобы гарантировать правильное размещение бетона вокруг стальных стержней.
Кроме того, для предотвращения образования воздушных карманов под арматурой и обеспечения хорошего контакта между бетоном и стержнями для достижения удовлетворительного сцепления.
Если в балку уложены два слоя стальных стержней, то расстояние между ними должно быть не менее 25 мм.
Защита бетона для армирования
проектировщик должен поддерживать минимальную толщину бетонного покрытия за пределами самой внешней стали, чтобы обеспечить достаточную защиту бетона от огня и коррозии.
Согласно ACI Code 7.7, бетонное покрытие толщиной 40 мм для монолитных балок, не подвергающихся прямому воздействию земли или погодных условий.
Покрытие не менее 50 мм, если бетонная поверхность будет подвергаться воздействию погодных условий или контакту.
Чтобы упростить конструкцию и тем самым снизить затраты, габаритные размеры балок b и h почти округлены до ближайших 25 мм.
Расчет прямоугольной железобетонной балки технологией
Расчет бетонной балки включает оценку размеров поперечного сечения и площади арматуры, чтобы выдерживать приложенные нагрузки.
Существует два подхода к проектированию балок.
Сначала начните проектирование с выбора глубины и ширины балки, затем вычислите площадь армирования.
Во-вторых, предположите площадь армирования, а затем рассчитайте размеры поперечного сечения.
Первый подход будет представлен ниже
При проектировании прямоугольной железобетонной балки использовалась следующая процедура:
- Сначала выберите эффективную глубину (d) и ширину (b) балки. Эффективную глубину можно рассчитать, используя глубину луча (h).
- Затем рассчитайте требуемый коэффициент сопротивления изгибу, предположив, что? = 0.9
- После этого найдите коэффициент армирования, соответствующий вычисленному выше вычисленному сопротивлению изгибу,
- Коэффициент усиления должен быть меньше максимального коэффициента усиления и больше минимального коэффициента усиления.
- Минимальный коэффициент армирования,
- Максимальный коэффициент усиления
- Может использоваться любой коэффициент усиления, но последний будет гарантировать, что деформация в стали будет не менее 0.005.
- После этого вычислить площадь армирования,
- Затем найдите количество стержней, разделив площадь армирования на площадь одного стержня.
- Наконец, проверьте, можно ли разместить стержень в пределах выбранной ширины поперечного сечения,
- Значение S должно быть не менее 25 мм, что является минимальным требуемым расстоянием между соседними стержнями.
Где:
R: коэффициент сопротивления изгибу
p: коэффициент армирования
Mu: факторный момент нагрузки
: коэффициент снижения прочности
b: ширина поперечного сечения
d: эффективная глубина поперечного сечения балки от верха балки до центра арматурного слоя
fc ‘: прочность бетона на сжатие
fy: предел текучести стальных стержней
p_u: предельная деформация в бетоне, равная 0.003 согласно кодексу ACI и 0,0035 согласно EC
p_0.004: коэффициент армирования при деформации стали, равный 0,004
p_0.005: коэффициент армирования при деформации стали, равный 0,005
As: площадь армирования
S: расстояние между соседними стержнями
n : количество стержней в одном слое
Расчет на сдвиг прямоугольной балки
Расчет на сдвиг включает оценку расстояния между скобами для поддержки предельного усилия сдвига. Как правило, часть бетона будет противостоять силе сдвига, но часть, не поддерживаемая бетоном, будет нести сдвигающую арматуру.
- Во-первых, вычислите предельную силу сдвига на расстоянии d, которое является глубиной поперечного сечения. Существуют исключения, в которых при расчете на сдвиг должен использоваться сдвиг на поверхности опоры. Например, когда нагрузка прилагается к нижней части балки.
- Во-вторых, расчетная расчетная прочность бетона на сдвиг,
- Сдвиговое армирование не требуется, если Vu <0,5
Vc.
- Если 0,5
Vc> Vu <
Vc, тогда обеспечьте только минимальное усиление сдвига.
- Обеспечьте усиление сдвига, когда Vu>
Vc.
- В-третьих, выберите пробную область стальной перемычки на основе стандартных размеров хомутов от № 10 до № 16.
- Умножьте площадь поперечной арматуры на количество плеч хомутов, чтобы рассчитать площадь поперечной арматуры.
- Затем найдите расстояние между хомутами для вертикальных и наклонных хомутов, соответственно, используя уравнения 12 и 13.
- Не размещайте вертикальные хомуты ближе 100 мм. Поэтому размер хомутов следует выбирать так, чтобы расстояние между ними не уменьшалось.0,5bwd, то максимальное расстояние должно быть уменьшено вдвое.
- Наконец, нарисуйте расчетную балку с продольной арматурой и поперечной арматурой.