Какие резцы применяют для вытачивания фасонных поверхностей: “1. Как вытачивают конические и фасонные поверхности? 2. Какие резцы применяют для вытачивания фасонных поверхностей? 3. Чем контролируют профиль фасонных.”. Скачать бесплатно и б
alexxlab | 02.04.2023 | 0 | Разное
Фасонные резцы. Основные понятия
- Главная /
- Механическая обработка /
- Фасонные резцы
Фасонные резцы относятся к нестандартным резцам.
Фасонные резцы применяют для обработки деталей со сложной формой образующей. По сравнению с обычными резцами они обеспечивают идентичность формы, точность размеров детали, которая зависит в основном от точности изготовления резца, высокую производительность благодаря одновременной обработке всех участков фасонного профиля детали и большую экономию машинного времени. Резцы проектируют для обработки конкретной детали, и их применение экономически оправдано в крупносерийном и массовом производстве.
Рис. 1. Формы фасонных резцов.
а) | б) |
в) |
Фасонные резцы классифицируют по следующим признакам:
1. По форме – стержневые (рис. 1, а), призматические (рис. 1, б) и круглые (рис. 1, в).
- Стержневые резцы применяют для обработки коротких фасонных поверхностей. Их недостатком является малое число переточек – из-за малой высоты рабочей части.
- Призматические фасонные резцы имеют большее число переточек и могут обрабатывать более длинные фасонные поверхности. Крепление и базирование резца в специальном резцедержателе осуществляется с помощью крепления типа “ласточкин хвост”. Недостаток призматических резцов – невозможность обработки внутренних фасонных поверхностей.
- Круглые фасонные резцы применяют для обработки как наружных, так и внутренних фасонных поверхностей. Они более технологичны, чем призматические и допускают большее число переточек. Устанавливают резцы в специальном резцедержателе и базируют по отверстию и торцу.
2. По направлению подачи: радиальные (рис. 2,а) и тангенциальные (Рис.
Рис. 2. Радиальный и тангенциальный фасонные резцы. Sr — радиальная подача резца, St — тангенциальная подача.
3. По расположению оси отверстия или установочной базы резца по отношению к оси вращения заготовки: с параллельным или наклонным расположением.
4. По конструкции: цельные и составные, например, с припаянными пластинами из твёрдого сплава.
Таблица 1
Геометрические элементы лезвия рабочей части фасонных резцов
Материал заготовки | Передний угол g, град. | |
БРС | ТС | |
Алюминий, медь | 20 – 25 | 10 – 15 |
0 – 10 | 0 – 5 | |
Сталь с sв, МПа: | – | – |
до 500 | 25 | 20 |
500 – 800 | 20 – 25 | 15 – 20 |
800 – 1000 | 10 – 15 | 5 – 10 |
Чугун с НВ: | – | – |
до 200 | 12 – 15 | 8 – 10 |
свыше 200 | 8 | 8 |
Задний угол, a | 8 – 15 | 8 – 12 |
Примечание: БРС – быстрорежущая сталь, ТС – твёрдый сплав |
Таблица 2
Размеры фасонных дисковых резцов с отверстиями под штифт, мм.
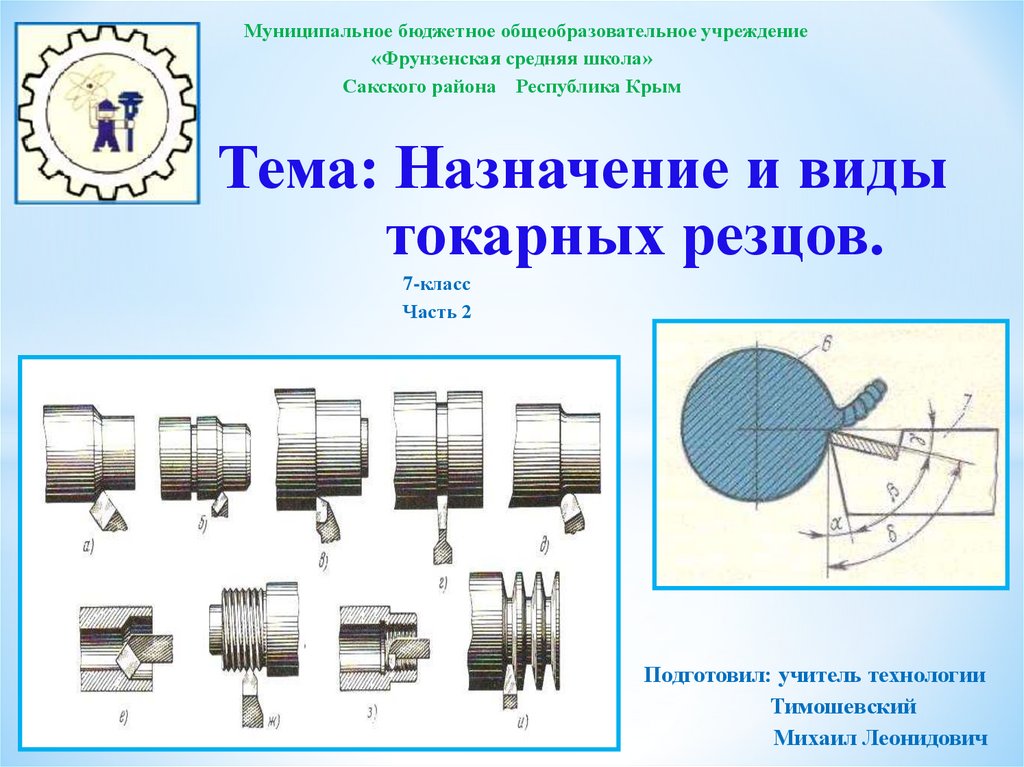
Глубина профиля заготовки, tmax, мм, не более | D | D | d1 | bmax | K | r | D1 | d2 |
6 | 50 | 13 | 20 | 9 | 3 | 1 | 28 | |
8 | 60 | 16 | 25 | 11 | 3 | 2 | 34 | 5 |
11 | 75 | 22 | 34 | 15 | 4 | 2 | 42 | 5 |
14 | 90 | 22 | 34 | 18 | 4 | 2 | 45 | 6 |
18 | 100 | 27 | 40 | 23 | 5 | 2 | 52 | 8 |
25 | 125 | 27 | 40 | 30 | 5 | 3 | 55 | 8 |
Таблица 3
Размеры фасонных дисковых резцов с торцовыми рифлениями, мм.
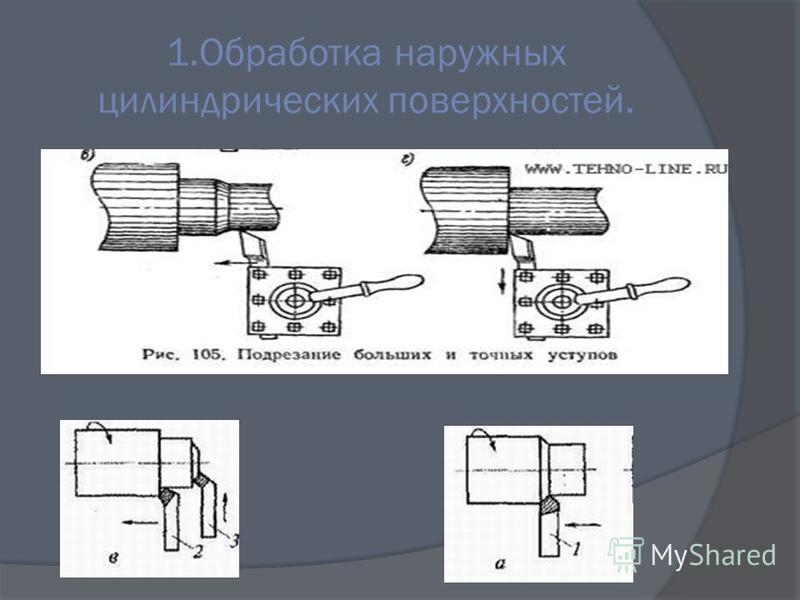
Глубина профиля заготовки, tmax, мм, не более | D | D | d1 | bmax | K | r | D1 |
|
4 | 30 | 10 | 16 | 7 | 3 | 1 | – | – |
6 | 40 | 13 | 20 | 10 | 3 | 1 | 20 | 3 |
8 | 50 | 16 | 25 | 12 | 4 | 2 | 26 | 3 |
10 | 60 | 16 | 25 | 14 | 4 | 2 | 32 | 3 |
12 | 70 | 22 | 34 | 17 | 5 | 2 | 35 | 4 |
15 | 80 | 22 | 34 | 20 | 5 | 2 | 40 | 4 |
18 | 90 | 22 | 34 | 23 | 5 | 2 | 45 | 5 |
21 | 100 | 27 | 25 | 5 | 2 | 50 | 5 |
Примечания:
- Для заданной глубины профиля tmax допускается применять резцы больших габаритных размеров, например, для заготовки с глубиной профиля 7 мм можно принять резцы с габаритными размерами для tmax< 14 мм .
- Передний угол g выбирают по табл. 1
- Размер Lp зависит от длины обрабатываемой поверхности.
- Размеры
Рис. 3. Резцедержатель круглого фасонного резца | Рис. 4. Резцедержатель призматического фасонного резца |
- Токарные резцы
- Осевой инструмент
технология, контроль, инструмент, методы и способы изготовления
Формирование фасонных поверхностей при токарной обработке происходит путем вращения криволинейных образующих вокруг оси изделий. Образующие могут представлять собой также сочетания линий различного профиля, создающих при вращении определенную конфигурацию детали. Существует несколько способов изготовления и контроля формы изделий с фасонными поверхностями, в том числе с использованием:
- шаблона;
- фасонного инструмента;
- копира;
- сочетанием указанных способов.
При использовании шаблонов подача резца осуществляется как в продольном, так и в поперечном направлении. После срезания определенной толщины слоя к детали прикладывается шаблон для определения размера следующего срезаемого слоя.
Наиболее простым способом получения фасонной поверхности детали является использование резца с режущей кромкой, повторяющей заданную криволинейную образующую.
Применение копира дает возможность получения наиболее точную конфигурацию детали. Иногда на практике приходится использовать комбинацию всех перечисленных способов – чаще всего это касается вытачивания удлиненных изделий с использованием твердосплавного и быстрорежущего инструмента.
Современное станочное оборудование обеспечивает высокую точность обработки заготовок, при этом деталь должна быть надежно закреплена в шпинделе или центрах станка. В случаях, если длина заготовки значительно превышает ее диаметр, применяются добавочные опоры – люнеты. Таким образом, можно значительно увеличить жесткость установки детали, что способствует точности обработки.
Применение на практике резцов с криволинейной конфигурацией ограничивается шириной их режущей части, которая не должна превышать 60 мм. Радиус чугунных и стальных заготовок из чугуна или стали ограничивают 20-ю миллиметрами. В таких случаях важно учитывать, что действующие усилия в зоне резания должны соответствовать общей жесткости всех составляющих системы СИД.
Если необходимо получить радиус обрабатываемой детали, превышающий 20 мм, используют проходные резцы, радиус закругления которых меньше, чем радиус закругления сопрягаемой детали, к примеру, подшипника.
Фасонные резцы:
а – цельный; б – с механическим креплением режущей части; в – дисковый
Обработка проходными резцами
В единичном производстве требования к точности изготовления невелики, поэтому вытачивание на станках фасонных поверхностей выполняется в ручном режиме, а качество исполнения обеспечивается за счет высокой квалификации рабочих. Это объясняется отсутствием автоматических настроек: процесса резания и точность выполнения работы обеспечивает исполнитель, сочетая продольное и поперечное перемещение резца. Для получения практических навыков обработки готовую деталь заданного фасонного профиля устанавливают в шпинделе станка, вдоль которой токарь вручную, используя рукоятки суппорта станка, перемещает резец таким образом, чтобы его режущая часть повторяла контур изделия.
Процесс токарной обработки происходит в двух позициях. Сначала заготовка рукоятки крепится в шпинделе станка за цилиндрическую часть А, выполняется обработка ступенчатой фасонной поверхностью (B, C, D, E) хвостовика. Перед этим на заготовку наносится разметка по длине. Затем деталь переворачивают, закрепляют за обработанный ступенчатый хвостовик и ведут обработку части G детали. Сначала выполняют снятие чернового припуска в несколько проходов, далее – обеспечивают доводку до требуемого размера. Останавливая вращение шпинделя, к неподвижной заготовке несколько раз прикладывают шаблон, измеряют максимальный и минимальный диаметры рукоятки, чтобы за несколько проходов довести ее форму до заданных размеров. В целях ускорения процесса резания продольное перемещение устанавливают в автоматический режим, оставляя ручное управление для поперечного суппорта.
Последовательность обработки фасонной поверхности рукоятки прохладным резцом с применением продольной и поперечной подач:
а – готовая деталь; б, в и г – полуфабрикаты для получения детали; A, B, C, D, E и G – обрабатываемые поверхности
При работе с копиром используют специальное приспособление, в комплекте из копира 5, тяги 3 с пальцем 4. Палец 4, проскальзывая вдоль копира, обеспечивает перемещение тяги, соединенной с суппортом, передвигая его и установленный на нем режущий инструмент в соответствии с контуром копира. Ход суппорта в продольном направлении рекомендуется выполнять в автоматическом режиме, поперечную подачу отключить. Инструмент, повторяя движение тяги, формирует рельеф вращающейся заготовки.
Обработка фасонных поверхностей по копиру:
1 – резец, 2- рукоятка, 3 – тяга, 4 – палец, 5 – копир
Использование фасонных резцов
Детали небольшой длины целесообразно изготавливать при помощи резцов рабочей кромкой, в точности совпадающий с заданным контуром. Обязательное условие точного выполнения технических параметров резания – передняя поверхность режущего инструмента должна располагаться на уровне линии центров токарного станка. Для затачивания резцов для фасонной обработки ведется используется передняя поверхность, что важно учитывать, если возникнет необходимость их неоднократной установки. Следует проверить, чтобы резец был установлен перпендикулярно по отношению к линии центров станка – это условие существенно влияет на качество и чистоту реза. Проверяется перпендикулярность при помощи угольника, одно ребро которого располагается по направлению оси детали, другое – вдоль одной из боковых сторон резца. Тело резца в сечении может быть круглым и прямоугольным – это облегчает обработку поверхностей со сложным рельефом.
Местом установки призматических радиальных фасонных резцов являются горизонтальная револьверная головка либо поперечный суппорт. Линия режущей кромки фасонного резца должна быть на уровне центра закрепленной в шпинделе или в центрах детали. Размеры задних углов α можно выставить, регулируя положение резца в державке, что достаточно удобно на этапе подготовительных работ.
На металлообрабатывающих производствах предпочтение отдается, как правило, резцам с винтовыми образующими режущих кромок по сравнению с резцами, в которых режущие кромки выполнены в виде кольцевых образующих. Это объясняется тем, что поверхность, обработанная резцами с винтовой образующей, менее шероховатая, в то же время процесс резания происходит гораздо быстрее.
Высокая производительность резцов с винтовой образующей режущей кромки в полной мере используется при их установке в револьверной головке. Для улучшения качества резания используется равномерная подача не более 0,05 мм/об при ширине резца 10…20 мм. Более широкие фасонные резцы (шириной больше 20 мм) рассчитаны на подачу до 0,03 мм/об.
Способы контроля фасонных поверхностей
Основным способом контроля фасонных поверхностей деталей является шаблон, с которым сверяют профиль полученной в результате обработки детали. Если размеры детали имеют отклонения от чертежа, причинами могли стать такие факторы как погрешности при обработке, неточности режущих параметров резца, ошибки в его установке. Возможно также, что отклонения произошли из-за деформаций изделия в процессе обработки – в таком случае следует уменьшить подачу режущего инструмента.
Что такое режущая кромка в режущем инструменте? Его функция, резкость и номера
Режущая кромка — это пересечение двух поверхностей режущей кромки. Режущий инструмент представляет собой клиновидное устройство, которое фактически удаляет (срезает) лишний материал с предварительно отформованной заготовки, чтобы получить желаемую форму, размер и точность. Во время механической обработки или резки металла режущий инструмент с силой сжимает тонкий слой материала заготовки и срезает его.
Каждый режущий инструмент состоит как минимум из двух поверхностей, а именно передней поверхности и боковой поверхности. Передняя поверхность — это поверхность схода стружки; тогда как боковая поверхность скользит по обработанной поверхности заготовки. Пересечение этих поверхностей образует режущую кромку.
Как следует из названия, основной функцией режущей кромки является отрезание или срезание материала для достижения конечной цели обработки. Однако не все режущие кромки могут в равной степени участвовать в режущем действии. Например, в токарном инструменте основная режущая кромка обычно удаляет материал, тогда как вспомогательная режущая кромка частично удаляет материал только в некоторых определенных операциях. Фактически токарный инструмент имеет две разные режущие кромки, как показано ниже.
- Основная режущая кромка — Пересечение между передней поверхностью и главной боковой поверхностью образует главную режущую кромку. Эта режущая кромка режет материал во время обработки.
- Вспомогательная режущая кромка — Встречается на пересечении передней поверхности и вспомогательной боковой поверхности. Он также может выполнять нарезку в некоторых операциях определенного типа, таких как нарезание резьбы.
Режущая кромка может быть или не быть прямой линией. Например, у одноточечного токарного инструмента (SPTT) режущие кромки прямые. Точно так же у фрезы и сверла она обычно прямая. Однако, если рассматривать абразивные фрезы, это может быть не обязательно прямо.
Можно ли напрямую измерить резкость? — Нет! Острота любого физического объекта определяется радиусом края, и они обратно пропорциональны. То есть чем меньше радиус края, тем он острее. Следовательно, теоретически максимальная острота или минимальный радиус кромки ограничены атомным радиусом материала. Вы не можете пойти ниже него.
Хотя радиус атома слишком мал (несколько нм), в высокоточных режущих инструментах режущие кромки в этом диапазоне острые. Радиус кромки прецизионной токарной алмазной фрезы составляет 10 – 100 нм, а у микроконцевых фрез – 1 – 5 мкм. Однако у обычных токарных, фрезерных, сверлильных и т. п. резцов радиус кромки обычно значительно больше, порядка десятков микрон. Стоит отметить, что более острым инструментам требуется меньшая мощность резания для удаления материала, но они очень подвержены катастрофическим поломкам.
Режущий инструмент может иметь одну или несколько режущих кромок, поэтому его можно разделить на три категории: однолезвийные, двухлезвийные и многолезвийные режущие инструменты.
Одноточечные режущие инструменты — Эти инструменты состоят только из одной режущей кромки, которая может одновременно снимать металл. Токарный инструмент является прекрасным примером одноточечного инструмента. Формообразующие, строгальные, прорезные, расточные инструменты также являются одноточечными инструментами.
Режущие инструменты с двумя концами — Эти инструменты имеют две режущие кромки, и обе кромки могут выполнять операцию удаления материала одновременно. Дрель — единственный пример для этой категории.
Многолезвийные режущие инструменты — Как следует из названия, эти инструменты имеют более двух режущих кромок. Количество режущих кромок, присутствующих в режущем инструменте, может варьироваться от четырех (у фрезы) до сотен (у шлифовального круга). Однако все режущие кромки не могут выполнять режущие функции одновременно; они могут последовательно включаться и отключаться. Примеры включают фрезы, червячные плиты, протяжные инструменты, шлифовальные круги и т. д. Читайте: Разница между одноточечным и многоточечным режущим инструментом.
- Книга: Принципы машиностроения С. Сингха (С. Шанд).
- Книга: Механическая обработка и станки А. Б. Чаттопадхьяя (Wiley).
- Книга: Резка металла: теория и практика А. Бхаттачарьи (Новое центральное книжное агентство).
- Книга: Производственные процессы Дж. П. Каушиша (PHI).
- Книга: Производственная наука М. И. Хака и С. Хана (PHI).
9 Типы процессов обработки
Что такое обработка? Механическая обработка — это процесс изготовления металла путем удаления из него ненужного материала. Этот процесс может быть выполнен многими различными способами. Существует много типов обработки. В данной статье рассматриваются станочные процессы токарной, сверлильной, фрезерной, шлифовальной, строгальной, пильной, протяжной, электроэрозионной и электрохимической обработки.
1. Токарная обработка
Токарная обработка — это метод механической обработки, при котором используется токарный станок для вращения металла, в то время как режущий инструмент перемещается линейно для удаления металла по диаметру, создавая цилиндрическую форму. Режущий инструмент можно наклонять под разными углами для создания различных форм. Токарную обработку можно выполнять вручную на традиционном токарном станке, который часто требует постоянного наблюдения со стороны оператора, или на автоматическом токарном станке, который этого не требует. На сегодняшний день наиболее распространенным типом такой автоматизации является числовое программное управление, называемое ЧПУ.
При токарной обработке используются токарные станки или токарные станки. Доступные типы токарных станков включают токарные станки с револьверной головкой, токарные станки с двигателями и токарные станки специального назначения. При токарной обработке производятся вращающиеся, как правило, осесимметричные детали со многими элементами, такими как отверстия, канавки, резьба, конусность, ступени диаметра и даже контурные поверхности. Детали, полностью изготовленные путем токарной обработки, часто включают компоненты, используемые в ограниченных количествах, возможно, для прототипов, такие как изготовленные по индивидуальному заказу валы и крепежные детали.
Токарная обработка применяется, в частности, для изготовления бейсбольных бит, распределительных валов, чаш, коленчатых валов, киев, вывесок, музыкальных инструментов, ножек столов и стульев.
2. Сверление
Сверление — это процесс механической обработки, при котором используются многогранные сверла для получения цилиндрических отверстий в заготовке. При сверлении станок подает вращающееся сверло перпендикулярно плоскости поверхности заготовки, делая вертикально ориентированные отверстия диаметром, равным диаметру сверла, используемого для операции сверления. Тем не менее, специальные конфигурации станков и заготовок также могут выполнять операции углового сверления.
При сверлении используются вращающиеся сверла для создания цилиндрических отверстий в заготовке. Конструкция сверла позволяет металлическим отходам, т. е. стружке, отходить от заготовки. Существует несколько типов сверл, каждый из которых используется для определенного применения. Типы сверл включают центрирующие сверла (для получения неглубоких или пилотных отверстий), сверла с вертикальным сверлением (для уменьшения количества стружки на заготовке), сверла для винтовых станков (для создания отверстий без пилотного отверстия) и патронные развертки (для расширения). уже сделанные отверстия).
Бурение применяется в строительстве, производстве медицинского оборудования, транспорта и электронного оборудования.
3. Фрезерование
Фрезерование — это метод обработки, при котором для удаления материала с заготовки используются вращающиеся многогранные режущие инструменты. При фрезеровании с ЧПУ станок с ЧПУ обычно подает заготовку к режущему инструменту в том же направлении, что и вращение режущего инструмента. Напротив, при ручном фрезеровании станок подает заготовку в направлении, противоположном вращению режущего инструмента.
При фрезеровании используются вращающиеся многогранные режущие инструменты для придания формы заготовке. Фрезерные инструменты ориентированы либо горизонтально, либо вертикально, включая концевые фрезы, винтовые фрезы и фрезы для снятия фаски.
В процессе фрезерования с ЧПУ также используются фрезерные станки с ЧПУ, называемые фрезерными станками или мельницами, которые могут быть ориентированы горизонтально или вертикально. Базовые мельницы могут иметь трехосное перемещение, а более продвинутые модели могут иметь дополнительные оси. Доступные типы фрезерных станков включают ручные, простые, универсальные и универсальные фрезерные станки. Некоторые из наиболее распространенных типов фрезерных станков включают коленный, плунжерный, станковый (или производственный) и строгальный станки.
Фрезерование включает в себя изготовление различных зубчатых колес, изготовление пазов или канавок в заготовках, обработку плоских и неровных поверхностей, а также обработку сложных форм.
4. Шлифование
Шлифование — это метод механической обработки, при котором небольшое количество материала удаляется как с плоских поверхностей, так и с цилиндрических поверхностей. Плоские шлифовальные машины совершают возвратно-поступательную работу на столе, подавая его на шлифовальный круг. Глубина, на которую врезается круг, обычно составляет от 0,00025 до 0,001 дюйма.
Круглошлифовальные станки устанавливают заготовку на центры и вращают ее, одновременно прикладывая к ней периферию вращающегося абразивного круга. Бесцентровое шлифование позволяет производить мелкие детали в больших объемах, где шлифованная поверхность не имеет отношения к какой-либо другой поверхности, кроме как в целом.
Грунтовые поверхности 200-500 мин. Среднеквадратичные значения обычно считаются приемлемыми для многих применений и являются отправной точкой для дальнейших чистовых операций, включая притирку, хонингование и суперфинишную обработку. Двойное шлифование дисков — это еще один машинный процесс, при котором детали проходят один или несколько раз между двумя шлифовальными кругами, вращающимися в противоположных направлениях.
5. Строгание
Строгание используется для обработки больших плоских поверхностей, особенно таких, которые будут обработаны шабрением, например, направляющие станка. Для достижения экономичного планирования мелкие детали собираются вместе в приспособлении.
Применения планирования включают линейные траектории, такие как создание точных плоских поверхностей и вырезание пазов, таких как шпоночные канавки.
6. Распиловка
Распиловка осуществляется с помощью отрезных станков и делается для создания более коротких отрезков из прутков, экструдированных профилей и т. д. Стандартными являются вертикальные и горизонтальные ленточные пилы, в которых используются непрерывные петли зубчатых лент для долбления материала. . Скорость ленты варьируется в зависимости от того, какой металлический материал распиливается, при этом для некоторых жаропрочных сплавов требуется низкая скорость 30 футов в минуту. Более мягкие материалы, такие как алюминий, можно обрабатывать со скоростью 1000 футов в минуту и выше. К другим отрезным машинам относятся механические пилы, абразивные круги и циркулярные пилы.
7. Протяжка
Протяжка — это процесс механической обработки, в котором используется протяжка, состоящая из множества зубьев, расположенных последовательно почти как напильник, но каждый последующий зуб немного больше предыдущего. Протяжка делает серию все более глубоких надрезов, когда ее протягивают или проталкивают через подготовленное отверстие лидера (или мимо поверхности).
Толчковая протяжка часто выполняется с помощью вертикальных прессов. Протяжное протягивание часто выполняется с помощью вертикальных или горизонтальных станков, которые во многих случаях имеют гидравлический привод. Скорость резки варьируется от 5 футов в минуту для высокопрочных металлов до 50 футов в минуту для более мягких металлов. Применение протягивания включает квадратные отверстия, шпоночные пазы, шлицевые отверстия и т. д.
8. Электроэрозионная обработка
Электроэрозионная обработка, или сокращенно EDM, использует электрические дуговые разряды для создания микрократеров, которые быстро приводят к полному резу. Электроэрозионная обработка, также известная как искровая обработка, используется в приложениях, требующих сложных геометрических форм из твердых материалов и с жесткими допусками. Однако для этого необходимо, чтобы основной материал был электропроводным, что ограничивает его использование сплавами железа.
Производители используют EDM для широкого спектра применений. Поскольку этот процесс позволяет резать крошечные детали, он часто является идеальным выбором для производства небольших деталей с высокой детализацией, которые обычно слишком деликатны для других типов обработки. Кроме того, электроэрозионная обработка экономически эффективна для небольших проектов и может быть полезна при изготовлении прототипов, даже если фактический проект выполняется другими средствами.
9. Электрохимическая обработка
Электрохимическая обработка — это процесс обратного гальванопокрытия, при котором получаются отверстия без заусенцев с высоким качеством поверхности. Электрохимический процесс удаляет материал. Обычно он используется для массового производства и для работы с чрезвычайно твердыми материалами или материалами, которые трудно обрабатывать. Основной материал должен быть электропроводным.
ECM может вырезать маленькие или необычные углы, полости или сложные контуры в твердых и экзотических металлах, таких как алюминиды титана, сплавы с высоким содержанием никеля, кобальта и рения. Кроме того, это холодный процесс обработки, который не создает термических напряжений в заготовке.
Что такое обработка?
Метод изготовления металла, называемый механической обработкой, относится к процессу формирования металла путем удаления из него ненужного материала. Этот процесс может выполняться различными способами. Существует множество процессов механической обработки, включая сверление, точение и фрезерование.
Какова цель механической обработки?
Целью механической обработки является создание чего-либо путем удаления металла с объекта для придания ему формы во что-то новое. Механическая обработка удаляет ненужный материал из детали для получения определенной формы или поверхности. Промышленный сектор, несомненно, использует наиболее обработанные детали, особенно в производстве и механическом оборудовании.
Какие существуют типы инструментов для обработки?
Типы инструментов для обработки зависят от процесса обработки. При токарной обработке режущий инструмент с одной режущей кромкой удаляет материал с вращающейся заготовки, придавая ей цилиндрическую форму.
При сверлении используется вращающийся инструмент, который обычно имеет две или четыре спиральные режущие кромки для создания круглого отверстия.
При растачивании используется инструмент с одним изогнутым заостренным наконечником. Режущий инструмент проникает в грубо сделанное отверстие во вращающейся заготовке, чтобы увеличить отверстие и немного повысить его точность.
При фрезеровании используется вращающийся инструмент с несколькими режущими кромками, который медленно перемещается относительно материала для получения прямой поверхности. Направление движения подачи перпендикулярно оси вращения инструмента. Вращающаяся фреза обеспечивает скоростное движение.
Режущий инструмент, используемый для механической обработки, имеет одну или несколько острых режущих кромок и изготовлен из более твердого материала, чем рабочий материал. Режущая кромка служит для отделения стружки от основного рабочего материала.
Резюме
В этой статье представлены девять различных типов процессов механической обработки, объяснено, что они из себя представляют, и обсуждено, когда использовать каждый из них в производстве. Чтобы узнать больше о типах процессов обработки, свяжитесь с представителем Xometry.
Xometry предоставляет широкий спектр производственных возможностей, включая обработку с ЧПУ и другие дополнительные услуги для всех ваших потребностей в прототипировании и производстве.