Каленый металл: Каленый металл: технологии получения
alexxlab | 23.06.2023 | 0 | Разное
Каленый металл: технологии получения
Вопросы, рассмотренные в материале:
- Необходимость закалки металла
- Виды закалки, используемые технологии и охлаждающие среды
- Особенности закалки металла
- Температурный режим при закалке металла
- Технологии отпуска каленого металла
- Технологии старения металла
- Специфика закалки цветных металлов
Необходимость закалки металла
Для того чтобы получить каленый металл, существует методика, которая в общих чертах включает ряд последовательных операций. На первом этапе следует тщательно очистить поверхность заготовок, удалив пятна ржавчины, масло и грязь. Далее металл необходимо нагреть до требуемой температуры. Заканчивается процесс охлаждением и отпуском.
При соблюдении нужных параметров закалка изменяет структуру материала, улучшая его эксплуатационные характеристики, что позволяет увеличить прибыльность производства за счет снижения себестоимости продукции.
Металл подвергают закаливанию с целью:
- увеличения твердости внешних слоев заготовки;
- повышения прочности материала;
- снижения пластичности до требуемых значений, что повышает стойкость металла к изгибающим нагрузкам;
- облегчения готовых изделий за счет дополнительной прочности и твердости.
Как правило, закалке подлежат детали из углеродистой и легированной стали, однако в отдельных случаях могут закаливаться заготовки из меди, латуни, бронзы, алюминиевых сплавов, титановые изделия.
Работа с цветными сплавами имеет специфику, так как после закаливания они могут не стать более прочными, но приобрести большую пластичность. В таких случаях металл отпускают в специальном режиме. После этой процедуры снимается напряжение, оставшееся после отливки, волочения, прокатки и других видов пластического деформирования.
Виды закалки, используемые технологии и охлаждающие среды
Существует несколько видов закалки, позволяющей улучшить характеристики металла:
- Первый включает полиморфное вращение.
Эта технология разработана для железных сплавов. Чтобы привести к нормальным показателям пластичность, вязкость и хрупкость, металл подвергают отпуску, после которого слегка снижаются прочностные показатели.
- Второй не предусматривает полиморфного вращения и предназначен для цветных металлов и их сплавов. Чтобы привести свойства материала к требуемым показателям, его подвергают так называемому старению.
При закалке могут использоваться различные режимы и среды для охлаждения. Для каждого случая существуют отдельные технологии. Разберемся с тем, как сделать металл каленым посредством каждой из них:
- Закаливание с применением одного охладителя, в ходе которого нагретые заготовки погружаются в жидкий охладитель до полного остывания.
- Изотермическое закаливание подразумевает выдерживание изделий в охладителе до наступления аустенитного превращения в структуре металла.
- Прерывистое закаливание проводится с использованием двух охладителей.
На первом этапе заготовки проходят быстрое охлаждение в воде. Далее они медленно остывают во втором охладителе, которым чаще всего служит масло. Этот метод закалки используется для улучшения характеристик углеродистой стали.
- Ступенчатое закаливание проводится в охладителе, температура которого превышает точку мартенситного превращения. В ходе охлаждения температура металла и среды выравнивается по всему объему заготовки. Далее детали постепенно охлаждают окончательно.
- Струйчатое закаливание производится при помощи струи воды. Такой метод позволяет улучшать характеристики отдельных частей изделия и обеспечивает более высокое прокаливание.
- Закаливание с самоотпуском. Если уменьшить время воздействия охладителя на заготовку, в толще металла сохраняется относительно высокая температура, которая, постепенно снижаясь и выходя наружу, снимает напряжение с металла, отпуская его. Такой метод требует от специалиста определенного навыка, так как требуется безошибочно определить момент, когда изделие нужно извлечь из ванны с охладителем.
Широко распространены технологии закалки с применением в качестве среды охлаждения воды, соляных и щелочных растворов, расплава свинца и различных технических масел.
Одним из самых востребованных является закаливание в растворах NaCl или едкого натра.
Особенности закалки металла
Важно учитывать, что скорость закаливания напрямую сказывается на его экономической эффективности, ведь от того, как быстро идет процесс, зависит расход энергии. Однако при слишком быстром нагреве заготовок увеличивается риск появления трещин и деформаций, вызванных резким перепадом температуры между внешними и глубокими слоями металла.
Поэтому очень важно постепенное и равномерное нагревание деталей. Ход процесса обязательно должны контролировать опытные специалисты, ориентируясь на специальные таблицы и значения, полученные опытным путем.
Не менее важным моментом является прямое влияние скорости охлаждения металла на структурные и химические преобразования в ходе термической обработки. Так, при быстром охлаждении с помощью воды комнатной температуры происходит мартенситное превращение в структуре углеродистой стали, а использование в качестве охлаждающей среды горячего масла или других горячих жидкостей ведет к образованию трооститов.
Для каждого типоразмера и конфигурации изделий должен подбираться отдельный режим термообработки. Именно этим вызвана необходимость разработки операционных карт и маршрутизации технологического процесса для производства новой продукции.
К примеру, для тонкостенных изделий и деталей, выполненных из углеродистой или легированной стали, в качестве охладителя используют минеральные масла, температура которых должна быть постоянной вне зависимости от окружающих условий. Охлаждающая среда при этом не должна содержать воды.
Углеродистую сталь сложного химического состава охлаждают поэтапно и с быстрой сменой охладителя. На первом этапе заготовки остывают в воде, а далее их погружают в техническое масло.
Для изделий и заготовок сложной геометрии применяют 50%-ный охлаждающий раствор едкого натра, нагретый до +60 °С. Для такой закалки характерно осветление поверхностных слоев металла.
Простые металлические изделия, как правило, закаливают, охлаждая их в простой воде без соли и других примесей при температуре около +30 °С.
Для визуального определения температуры металла при его закаливании используют таблицу цветов побежалости:
Ярко-белый
>1300 °C
Желто-белый
+1250…+1300 °C
Светло-желтый
+1150…+1250 °C
Темно-желтый
+1050…+1150 °C
Оранжевый
+900…+1050 °C
Красный
+870…+900 °C
Ярко-красный
+830…+870 °C
Вишнево-алый со светлым оттенком
+800.
Вишнево-алый
+770…+800 °C
Вишнево-красный
+730…+770 °C
Вишневый
+650…+730 °C
Красно-коричневый
+580…+650 °C
Темно-коричневый
+530…+580 °C
Рассмотрим возможные изъяны, которые характерны для закаливаемых изделий. Такого рода дефекты могут быть исправимыми и неисправимыми. Первая разновидность, как правило, связана с неравномерностью закалки или с несоответствием полученной твердости металла требуемым значениям. Формирование таких изъянов обычно связано с нарушениями режима термической обработки и/или охлаждения заготовок.
Ко второй категории, помимо полного разрушения изделия, относится появление сколов и растрескивание. Причиной таких проблем чаще всего становится низкое качество металла.
Температурный режим при закалке металла
Нормативные значения температуры при закаливании металлических деталей находятся в прямой зависимости от углеродистости стали и процентного содержания легирующих компонентов. Как правило, эту зависимость можно определить так: понижение содержания углерода требует повышения температуры закаливания.
Недостаточный нагрев изделий не обеспечивает формирования нужной структуры, а избыточный ведет к разуглероживанию, окислению верхних слоев, деформациям и образованию зон внутренней напряженности.
Сложная геометрия изделий требует их предварительного подогрева, для чего заготовки несколько раз погружают в ванну с соляным раствором или недолго выдерживают в печи при температуре в диапазоне от +400 до +500 °С. Время, требуемое на прогрев, зависит от размеров деталей и их количества в загрузке. Важно следить, чтобы произошло полное и равномерное нагревание.
Для измерения температуры металла при промышленном производстве используют как контактные, так и бесконтактные пирометры. В последнее время широко распространено дистанционное определение температуры при помощи специальных инфракрасных приборов, которые дают возможность измерить ее значение на любом участке поверхности обрабатываемых заготовок. И, как уже говорилось, приблизительно оценить нагрев стали позволяют таблицы цветов побежалости.
Технологии отпуска каленого металла
Закаливание металла ведет к повышению хрупкости и формированию зон внутреннего напряжения, что может привести к разрушению стали под действием ударных нагрузок или иных повреждающих воздействиях. Для того чтобы снять напряжение и повысить пластичность материала, разработаны технологии отпуска.
Отпуск завершает процесс закалки и представляет собой нагрев заготовок до определенной температуры и их постепенное охлаждение, которое происходит на воздухе при комнатной температуре либо в специальных средах. Для отпуска используют ванны с маслом или расплавленным металлом.
Изменения, происходящие в структуре металла, и фазовые переходы находятся в прямой зависимости от температуры. С ее повышением происходит постепенное снижение твердости и хрупкости, сопровождаемое увеличением вязкости и пластичности. Различают три режима нагрева при отпуске закаленной стали, которые отличаются предельной температурой:
- При низком отпуске максимальная температура равна +300 °С. Такой метод позволяет получить особо твердую сталь. Отпуск сопровождается постепенным снятием внутреннего напряжения и повышением вязкости.
- Для среднего отпуска изделия нагревают до +450 °C. Такая технология применяется для производства прочной стали с повышенной упругостью. Этот метод позволяет сохранить неизменными показатели вязкости. Детали охлаждаются на открытом воздухе. Такой отпуск применяют для рессорной и пружинной стали.
- Высокий отпуск, который позволяет повысить пластичность каленого металла, производят при температуре +450…+650 °С. Обработка уменьшает внутреннее напряжение на 95 %.
Технологии старения металла
Обработка каленого металла, которую принято называть старением, производится для повышения показателей твердости стали и делится на три основных способа:
- Естественное старение представляет собой выдерживание изделий на открытом воздухе.
Процесс сопровождается самопроизвольным увеличением прочности стали и снижением ее пластичности.
- Для термического старения заготовки подвергают воздействию высокой температуры. Такой метод несет в себе риск так называемого перестаривания, когда после достижения максимальных значений может начаться процесс постепенного понижения твердости, плотности и текучести материала.
- При деформационном старении каленый металл, имеющий структуру твердого раствора, подвергают пластическому деформированию.
Специфика закалки цветных металлов
Для каждого цветного металла или его сплава процесс закаливания имеет свою специфику.
Здесь мы не станем рассматривать термообработку всех цветных металлов, ограничившись примером стальных и медных сплавов:
Алюминий
Изделия из этого металла и сплавов на его основе нечасто подвергают закалке из-за того, что они уже прошли термообработку в ходе литья и обработку с использованием холодного или горячего пластического деформирования, что повысило твердость и прочность материала.
Закаливание в домашней мастерской может понадобиться, например, для сварных деталей из алюминиевого сплава, у которых при сварке произошло снижение жесткости материала в прилегающих к швам областях. Самостоятельная закалка связана с целым рядом проблем.
Для того чтобы алюминиевую деталь не повело при термической обработке, необходимо учитывать особенности конкретного сплава и точно соблюдать рекомендованную температуру. Допустимая погрешность при этом не должна превышать пяти градусов Цельсия. Не менее важно соблюдение технологических требований при охлаждении изделия, так как в противном случае также возможны деформации.
Данный вид термообработки следует производить в специальной печи для закаливания с точной регулировкой температуры. Для индивидуального подбора правильных параметров, скорее всего, придется закаливать каждую деталь по отдельности.
Медь
Параметры термообработки медных сплавов коренным образом отличаются от тех, что допустимы для стальных заготовок. При быстром охлаждении в водной среде детали из меди, предварительно разогретой докрасна (около +600 °С), металл отпускается, что ведет к его размягчению.
Самостоятельная закалка медных сплавов без отпуска возможна, но достаточно сложна, так как при нагревании нельзя допустить красного каления, то есть температура не должна быть больше +400 °С. После охлаждения на открытом воздухе сплав приобретет твердость, сравнимую с получаемой при нагартовке. Помимо специальной печи, если вы собираетесь производить закаливание в условиях домашней мастерской, следует обзавестись пирометром, который позволит контролировать температурный режим.
Рекомендуем статьи
- Неподвижные опоры трубопроводов: типы, расчет, установка
- Правильная сварка труб: пошаговый алгоритм и техника безопасности
- Обработка нержавеющей стали: основные методы и секреты мастерства
Закаливание металлических заготовок требует тщательного соблюдения целого ряда параметров, ведь неправильно подобранный режим термической обработки может привести как к размягчению поверхностных слоев металла, так и к избыточной хрупкости. Нужно разобраться в методах закаливания, чтобы избежать возможных ошибок и получить хороший результат.
Сварка высокопрочных и закаленных сталей
- Свариваемость высокопрочных сплавов
- Технология сварки высокопрочных сплавов
- Ручная дуговая сварка покрытыми электродами
- Сварочные работы в защитных газах
- Сварочные работы под флюсом
- Электрошлаковая сварка
Состав и свойства высокопрочных сталей
Стали с пределом прочности свыше 1500 МПа называются высокопрочными. Такой предел достигается подбором химического состава и наиболее подходящей термической обработкой. Данный уровень прочности может образовываться в среднеуглеродистых легированных сталях (40ХН2МА, 30ХГСН2А) путем использования закалки с низким отпуском (при 200…250оС). Легирование таких сталей W, Mo, V затрудняет разупрочняющие процессы, что снижает порог хладоломкости и повышает сопротивление хрупкому разрушению. Как варить металл, если перед вами высокопрочная сталь? Сварка высокопрочных сталей отличается использованием некоторых дополнительных технологических приемов (сварка каскадом, горкой, секциями, предварительный подогрев, применение мягкой прослойки и других).
Изотермическая закалка среднеуглеродистых легированных сталей придает им немного меньшую прочность, но большую вязкость и пластичность. Поэтому они более надежны в эксплуатации, чем низкоотпущенные и закаленные. Низкоотпущенные и закаленные среднеуглеродистые стали с высоким уровнем прочности обладают повышенной восприимчивостью к концентраторам напряжения, склонностью к хрупкому разрушению. Из-за этого их рекомендуют использовать для работы, связанной с плавным нагружением.
К высокопрочным сталям можно отнести так называемые рессорные (пружинные) стали. Они содержат 0,5…0,75% С и дополнительно легируются другими элементами. Термообработка легированных рессорных сталей (закалка 850…880оС, отпуск 380…550оС) обеспечивает получение высокой прочности и текучести. Может применяться изотермическая закалка. Сварка рессорной стали выполняется с обязательной предварительной термообработкой, с подогревом в процессе сварочных работ и дальнейшей термической обработкой.
Мартенситно-стареющие стали (04Х11Н9М2Д2ТЮ, 03Н18К9М5Т) также относятся к высокопрочным сталям. Они превосходят среднеуглеродистые легированные стали по конструкционной прочности и технологичности. Для таких сталей характерны высокое сопротивление хрупкому разрушению, низкий порог хладоломкости и малая чувствительность к надрезам при прочности около 2000 МПа. Мартенситно-стареющие стали являются безуглеродистыми сплавами железа с никелем и дополнительно легированы молибденом, кобальтом, алюминием, хромом, титаном и другими элементами. Эти стали имеют высокую конструкционную прочность в диапазоне температур от криогенных до 500оС и применяются в изготовлении стволов артиллерийского и стрелкового оружия, корпусов ракетных двигателей, зубчатых колес, шпинделей и так далее.
Свариваемость высокопрочных сплавов
Для изготовления тяжело нагруженных машиностроительных изделий,сосудов высокого давления и других ответственных конструкций используют среднеуглеродистые высокопрочные стали, которые после соответствующей термообработки обладают прочностью 1000…2000 МПа при достаточно высоком уровне пластичности. Необходимый уровень прочности при сохранении высокой пластичности достигается комплексным легированием стали различными элементами, главные из которых никель, хром, молибден и другие. Эти элементы упрочняют феррит и повышают прокаливаемость стали. Подогрев изделия при сварочных работах не снижает скорости охлаждения металла до значений, меньших критических, и способствует росту зерна, что приводит к возникновению холодных трещин и вызывает уменьшение деформационной способности.
Поэтому такие металлы сваривают без предварительного подогрева, но с применением специальных приемов сварочных работ (блоками, каскадом, короткими или средней длины участками). Также применяют специальные устройства, которые подогревают выполненный шов и тем самым увеличивающие время пребывания его в определенном температурном интервале. Для увеличения времени нахождения металла околошовной зоны при температуре выше точки образования мартенситной структуры накладывают так называемый отжигающий валик, границы которого находятся в пределах металла шва.
Во избежание трещин при охлаждении сварного соединения, необходимо использовать такие сварочные материалы, которые обеспечили бы получение металла шва, обладающего большой деформационной способностью. Это достигается, когда наплавленный металл и металл шва будут менее легированы, чем свариваемая сталь. При этом шов будет представлять как бы мягкую прослойку с временным сопротивлением, но с повышенной деформационной способностью. Чтобы обеспечивалась технологическая прочность сварных швов, выполненных низколегированными сварочными материалами, углерод в шве должен содержаться в количестве не более 0,15%.
Когда производится сварка закаленной стали, то после прохождения сварочной дуги на зону сварного соединения рекомендуется подавать охладитель. Это делается для уменьшения степени разупрочнения околошовной зоны. В качестве охладителя может служить душевая вода, сжатый воздух или паровоздушная смесь — в зависимости от состава свариваемого материала. Такое охлаждение снижает время нахождения металла в зоне высоких температур.
Технология сварочных работ по соединению высокопрочных сталей
При сварке среднелегированных глубокопрокаливающихся высокопрочных сталей нужно подбирать такие сварочные материалы, которые обеспечат получение швов с высокой деформационной способностью при минимальном количестве водорода в сварочной ванне. Это достигается применением низколегированных сварочных электродов, которые не содержат в покрытии органические вещества и подвергнутых высокотемпературной прокалке (низководородистые электроды). При этом нужно исключить другие источники насыщения сварочной ванны водородом в ходе сварки (ржавчина, влага и другие). Высокая технологическая прочность получается при следующем содержании легирующих элементов в металле шва: С — не более 0,15%; Si — не более 0,5%; Ni — не более 2,5%; Mn — не более 1,5%; Cr — не более 1,5%; V — не более 0,5%; Mo — не более 1,0%.
Повышение свойств шва до нужного уровня возможно путем легирования металла шва за счет основного металла. Необходимые прочностные характеристики металла шва достигаются легированием его элементами, которые повышают прочность, но не снижают его ударную вязкость и деформационную способность. Для сварки среднеуглеродистых высокопрочных сталей нужно выбирать сварочные материалы, содержащие легирующих элементов меньше, чем основной металл.
Ручная дуговая сварка покрытыми электродами
Для сварки среднелегированных высокопрочных сталей используют электроды типов Э-13Х25Н18, Э-08Х21Н10Г6 и других по ГОСТ 10052-75 и ГОСТ 9467-75. Если сталь перед сваркой подвергалась термической обработке на высокую прочность (закалка с отпуском или нормализация), а после сварки — отпуску для снятия напряжений и выравнивания механических свойств сварного соединения, то критерием определения температуры предварительного подогрева будет такая скорость охлаждения, при которой происходила бы частичная закалка околошовной зоны. При этом гарантируется отсутствие трещин в процессе сварки и до проведения дальнейшей термообработки.
В том случае когда термообработка сварного изделия не может быть сделана, например, из-за крупных габаритов, на кромки детали, подлежащие сварке, наплавляют незакаливающийся слой металла аустенитными или низкоуглеродистыми электродами. Толщина этого слоя должна быть такой, чтобы температура стали под слоем в процессе сварки не превышала бы температуру отпуска при термообработке деталей с наплавленными кромками. Такие детали сваривают аустенитными или низкоуглеродистыми и низководородистыми электродами без подогрева и дальнейшей термообработки. Режим сварки принимают согласно рекомендациям для аустенитных электродов.
Сварочные работы в защитных газах
Высокое качество сварных соединений из среднеуглеродистых высокопрочных сталей толщиной 3…5 мм достигается при аргонодуговой сварке неплавящимся электродом. Присадочный материал для дуговой сварки в защитных газах следует выбирать в зависимости от газа, в среде которого происходит сварка. Первый слой выполняют без присадки с полным проваром кромок стыка, второй — с поперечными низкочастотными колебаниями электрода и механической подачи присадочной проволоки. Возможно и выполнение третьего слоя с поперечными колебаниями электрода без присадочной проволоки на небольшом режиме для обеспечения постепенного перехода от шва к основному металлу.
Для повышения проплавляющей способности дуги при аргонодуговой сварке применяют активирующие флюсы, которые позволяют исключить разделку кромок при толщинах 8…10 мм. Также используется флюс, представляющий собой смесь компонентов (TiO2, SiO2, NaF, Cr2O3). Такой метод с активирующим флюсом эффективен при механизированных способах для получения равномерной глубины проплавления. Неплавящийся электрод при таком способе сварки выбирают из наиболее стойких в эксплуатации марок вольфрама.
Современная аргоновая горелкаПри выполнении сварки среднелегированных высокопрочных сталей в защитных газах (в основном инертных или их смесях с активными) применяют низкоуглеродистые легированные и аустенитные высоколегированные проволоки, например, Св-08Х20Н9Г7ТТ, Св-03ХГН3МД, Св-10ХГСН2МТ, Св-10Х16Н25-АМ6, Св-08Х21Н10Г6. Однако равнопрочности металла шва и свариваемой стали получить не удается. В данном случае можно обеспечить равнопрочность за счет эффекта контактного упрочнения мягкого металла шва. Этот эффект может быть реализован при использовании так называемой щелевой разделки, которая представляет собой стыковые соединения с узким зазором.
Сварка под флюсом
Конструктивные элементы подготовки кромок для автоматической и полуавтоматической сварки под флюсом выполняют в соответствии с ГОСТ 8713-79. Однако в диапазоне толщин, для которого возможна сварка без разделки и со скосом кромок, последней следует отдать предпочтение. При механизированной сварке под флюсом необходимы подготовка кромок, техника и режимы сварки, при которых доля основного металла в шве была бы минимальной. Но такая методика повышает вероятность образования в сварочных швах горячих трещин.
Выбор флюса осуществляется в зависимости от марки электродной проволоки. При использовании низкоуглеродистой проволоки сварку выполняют под кислыми высоко- и среднемарганцовистыми флюсами. При использовании низколегированных проволок лучшие результаты обеспечивает применение низкокремнистых и низкомарганцовистых флюсов. Сварку среднелегированных высокопрочных сталей аустенитной проволокой марок Св-08Х21Н10Г6 или Св-08Х20Н9Г7Т производят только под безокислительными или слабо окислительными основными флюсами.
Электрошлаковая сварка
Схема процесса сварочных работДанный вид сварочных работ рационально применять для соединения толстолистовых конструкций из среднелегированных высокопрочных сталей. Основные типы и конструктивные элементы сварных соединений и швов при этом должны соответствовать требованиям ГОСТ 15164-78. Электродные проволоки при сварке плавящимся мундштуком и проволочными электродами выбирают из числа групп легированных или высоколегированных проволок по ГОСТ 2246-70. Для предупреждения трещин в околошовной зоне при сварке жестко закрепленных элементов необходимо применять предварительный подогрев до 150…200оС.
Низкая скорость охлаждения околошовной зоны при электрошлаковой сварке приводит к длительному пребыванию ее в зоне высоких температур, вызывающих рост зерна и охрупчивание металла. В связи с этим после электрошлаковой сварки среднелегированных высокопрочных сталей необходимо выполнить высокотемпературную термообработку сварных изделий для восстановления механических свойств до нужного уровня. Время с момента окончания сварки до проведения термообработки должно регламентироваться.
Закаленная сталь и нержавеющая сталь
Блог ThePipingMart Металлы Закаленная сталь и нержавеющая сталь – в чем разница
20 января 2023 г. 20 января 2023 г. | 10:53
Вы пытаетесь выяснить, какой тип стали лучше всего подходит для конкретной работы? Если это так, понимание разницы между закаленной сталью и нержавеющей сталью может помочь вам принять обоснованное решение. Оба типа стали имеют свои преимущества, поэтому давайте рассмотрим их подробнее, чтобы определить, какой из них лучше всего подходит для вашего проекта.
Закаленная сталь
Закаленная сталь — это разновидность легированной углеродистой стали, которая подвергается тепловой или химической обработке, чтобы сделать ее более прочной и долговечной. Обладает высокой прочностью на растяжение и износостойкостью, что делает его подходящим для тяжелых условий эксплуатации. Он также обладает отличными амортизирующими свойствами, что делает его идеальным для промышленного использования в тяжелых условиях. Однако, поскольку закаленная сталь в некоторых случаях может быть хрупкой, она может не подходить для определенных проектов, требующих гибкости или пластичности.
Нержавеющая сталь
Нержавеющая сталь — это еще один тип легированной углеродистой стали, который содержит хром и другие элементы, такие как никель или молибден. Эта комбинация придает нержавеющей стали ее коррозионную стойкость и делает ее намного более долговечной, чем обычная углеродистая сталь. Он также обладает хорошей прочностью на растяжение и износостойкостью, хотя и не такой прочной, как закаленная сталь. Кроме того, с нержавеющей сталью намного легче работать из-за ее податливой природы, что делает ее лучшим выбором для проектов, требующих сгибания или придания материалу определенной формы.
Разница между закаленной сталью и нержавеющей сталью
- Закаленная сталь — это тип стали, который подвергается термической или химической обработке, чтобы сделать ее более твердой и устойчивой к износу.
- Нержавеющая сталь — это тип стали, содержащий не менее 10% хрома, что делает ее устойчивой к коррозии. Закаленная сталь
- обычно используется для инструментов и механизмов, подверженных высокому износу, таких как топоры, ножи и пилы.
- Нержавеющая сталь часто используется для производства оборудования для пищевой промышленности, хирургических инструментов и кухонной утвари, поскольку ее легко чистить и она не ржавеет.
- С закаленной сталью может быть труднее работать, чем с нержавеющей сталью, поскольку ее труднее резать и формировать.
Заключение:
Как закаленная сталь, так и нержавеющая сталь являются отличными вариантами при поиске материалов, которые являются прочными, но при этом достаточно гибкими для работы. В зависимости от ваших конкретных требований к проекту один может подойти лучше, чем другой. Закаленная сталь обеспечивает превосходную прочность на растяжение и способность поглощать удары, тогда как нержавеющая сталь обеспечивает лучшую коррозионную стойкость и пластичность. Понимание различий между этими двумя типами металлов поможет вам принять обоснованное решение о том, какой из них подходит для нужд вашего проекта.
Абхишек Модак
Абхишек — опытный блоггер и отраслевой эксперт, который делится своими взглядами и знаниями по различным темам. Своими исследованиями Абхишек предлагает ценные идеи и советы профессионалам и энтузиастам. Подпишитесь на него, чтобы получить экспертные советы о последних тенденциях и разработках в металлургической промышленности.
Металлические пластины из предварительно закаленной стали, конфигурируемые | МИСУМИ
- org/ListItem”> МИСУМИ Главная>
- Материалы>
- Металлические материалы>
- Металлические пластины и блоки>
- Металлические пластины из предварительно закаленной стали, конфигурируемые
Щелкните это изображение, чтобы увеличить его.
Наведите указатель мыши на изображение для увеличения
MISUMI
MISUMI
Размеры, допуски и метод отделки можно выбирать свободно!
- Быстрое проектирование
(i)Внимание
- Пожалуйста, проверьте содержание на нашем веб-сайте, так как PDF-файл не содержит самой последней информации.
・Materials
PG-STARF | G-STAR | 33~37HRC |
PPX5F | PXA30 | 30~33HRC |
PNAK55F | NAK55 (JIS) | 37 ~43HRC |
Технические характеристики
Номер детали | – | A | 8 –
PG-STARF PPX5F | P Q N M | P Q N M | 50 ~ 500 | 20 ~ 200 | 5 ~ 40 |
PNAK55F | 50 ~ 300 |
① Плал. 0,2
+0.1~+0.3 | 0~+0.2 | ±0.1 | -0.2~0 | +0.1~+0.3 | 0~+0.2 | ±0.1 | -0.2~0 |
+0.1~+0.6 | 0~+0,5 | ±0,25 | -0,5~0 |
Изменения
Номер детали Предварительно просмотр:
Загрузка . ..
Плагин требуется для 3D Предварительный просмотр
CAD Download
Номер детали 9079 |
---|
Номер. [50-500/1]-[20-200/1]-[5-40/1] |
PG-STARFMN-[50-500/1]-[20-200/1]-[5- 40/1] |
PG-STARFMP-[50-500/1]-[20-200/1]-[5-40/1] |
PG-STARFFMQ-[50-500/1] -[20-200/1]-[5-40/1] |
PG-STARFNM-[50-500/1]-[20-200/1]-[5-40/1] |
PG-STARFNN-[50-500/1]-[20- 200/1]-[5-40/1] |
PG-STARFNP-[50-500/1]-[20-200/1]-[5-40/1] |
PG-STARFNQ -[50-500/1]-[20-200/1]-[5-40/1] |
PG-STARFPM-[50-500/1]-[20-200/1]-[5 -40/1] |
PG-STARFPN-[50-500/1]-[20-200/1]-[5-40/1] |
PG-STARFPP-[50-500/1 ]-[20-200/1]-[5-40/1] |
PG-STARFQM-[50-500/1]-[20-200/1]-[5-40/1] |
PG-STARFQM-[50-500/1]-[20-200/1 ]-[5-40/1] |
PG-STARFQN-[50-500/1]-[20-200/1]-[5-40/1] |
PG-STARFQP-[50 -500/1]-[20-200/1]-[5-40/1] |
PG-STARFQQ-[50-500/1]-[20-200/1]-[5-40/ 1] |
ПНАК55ФММ-[50-300/1]-[20-200/1]-[5-40/1] |
ПНАК55ФМН-[50-300/1]-[20-200/ 1]-[5-40/1] |
ПНАК55ФМП-[50-300/1]-[20-200/1]-[5-40/1] |
ПНАК55ФМQ-[50-300/1]-[20-200/1]-[5-40/1] |
ПНАК55ФНМ-[50-300/1]-[20-200/1] -[5-40/1] |
ПНАК55ФНН-[50-300/1]-[20-200/1]-[5-40/1] |
ПНАК55ФНП-[50-300/1] -[20-200/1]-[5-40/1] |
PNAK55FNQ-[50-300/1]-[20-200/1]-[5-40/1] |
PNAK55FPM -[50-300/1]-[20-200/1]-[5-40/1] |
ПНАК55ФПН-[50-300/1]-[20-200/1]-[5-40 /1] |
ПНАК55ФПП-[50-300/1]-[20-200/1]-[5-40/1] |
PNAK55FPQ-[50-300/1]-[20-200/1]-[5-40/1] |
PNAK55FQM-[50-300/1]-[20-200/1] -[5-40/1] |
PNAK55FQN-[50-300/1]-[20-200/1]-[5-40/1] |
PNAK55FQP-[50-300/1] -[20-200/1]-[5-40/1] |
PNAK55FQQ-[50-300/1]-[20-200/1]-[5-40/1] |
PPX5FMM -[50-500/1]-[20-200/1]-[5-40/1] |
PPX5FMN-[50-500/1]-[20-200/1]-[5-40 /1] |
PPX5FMP-[50-500/1]-[20-200/1]-[5-40/1] |
PPX5FMQ-[50-500/1]-[20-200/1]-[5-40/1] |
PPX5FNM-[50-500/1]-[20-200/1] -[5-40/1] |
PPX5FNN-[50-500/1]-[20-200/1]-[5-40/1] |
PPX5FNP-[50-500/1] -[20-200/1]-[5-40/1] |
PPX5FNQ-[50-500/1]-[20-200/1]-[5-40/1] |
PPX5FPM -[50-500/1]-[20-200/1]-[5-40/1] |
PPX5FPN-[50-500/1]-[20-200/1]-[5-40 /1] |
PPX5FPP-[50-500/1]-[20-200/1]-[5-40/1] |
PPX5FPQ-[50-500/1]-[20-200/1]-[5-40/1] |
PPX5FQM-[50-500/1]-[20-200/1] -[5-40/1] |
PPX5FQN-[50-500/1]-[20-200/1]-[5-40/1] |
PPX5FQP-[50-500/1] -[20-200/1]-[5-40/1] |
PPX5FQQ-[50-500/1]-[20-200/1]-[5-40/1] |
Номер детали | Скидка за объем | Количество дней до отгрузки | RoHS | Материал | Толщина T (мм) | Ширина B (мм) | Длина a (мм) | Толерантность к ширине (мм) | Длина.![]() | |||||||||||||||||||||||||||||||||||||||||||
---|---|---|---|---|---|---|---|---|---|---|---|---|---|---|---|---|---|---|---|---|---|---|---|---|---|---|---|---|---|---|---|---|---|---|---|---|---|---|---|---|---|---|---|---|---|---|---|---|---|---|---|---|
5 дней | 10 | [Предварительно закрепленная сталь] G -Star | 5 ~ 40 | 20 ~ 200 | 50 ~ 500 | -0,5 до 0 | -0,5 до 0 | 4444444 -0,2 до 00085 | -0,5 до 0 | 44444444444444 -0,2 до 00085 | -0,5 до 0 | 4444444 -0,2 до 0 | .||||||||||||||||||||||||||||||||||||||||
5 дней | 10 | [Предварительно запорная сталь] G-Star | 5 ~ 40 | 20 ~ 200 | 50 ~ 500 | ± 0,1 | ± 0.1 | ± 0,1 | ± 0.1 | ± 0,1± 0,1 | ± 0,1 | ± 0,1 | от -0,2 до 0 | |||||||||||||||||||||||||||||||||||||||
5 дней | 10 | [Предварительно закрепленная сталь] G-Star | 5 ~ 40 | 20 ~ 200 | 50 ~ 500 | +0,1 до +0,6 | +0,11.![]() | –084 –084 –084 –084 –084-0,084-0,085 | –085 | -0,084-0,084 –084-0,0.1-0,0,6 | . до 0 | |||||||||||||||||||||||||||||||||||||||||
5 дней | 10 | [Предварительно закрепленная сталь] G-Star | 5 ~ 40 | 20 ~ 200 | 50 ~ 500 | 0 до +0,5 | 0 до +0,5 | 4444444444444.2 до 0.0085 | 0 до +0,5 | 44444444444444444 4.2 до 0.0085 | . | |||||||||||||||||||||||||||||||||||||||||
5 дней | 10 | [Предварительно закаленная сталь] G-STAR | 5 ~ 40 | 20 ~ 200 | 50 ~ 500 | –±0,1 | ||||||||||||||||||||||||||||||||||||||||||||||
5 Days | 10 | [Pre-hardened Steel] G-STAR | 5 ~ 40 | 20 ~ 200 | 50 ~ 500 | ±0.![]() | ±0.1 | ±0.1 | ||||||||||||||||||||||||||||||||||||||||||||
5 дней | 10 | [Pre-hardened Steel] G-STAR | 5 ~ 40 | 20 ~ 200 | 50 ~ 500 | +0.1 to +0.6 | +0.1 to +0.6 | ±0.1 | ||||||||||||||||||||||||||||||||||||||||||||
5 дней | 10 | [Предварительно закаленная сталь] G-STAR | 5 ~ 40 | 20 ~ 200 | 50 ~ 5 9 | + 9008,80084 от 0 до +0,5 | ±0,1 | |||||||||||||||||||||||||||||||||||||||||||||
5 дней | 10 | [Предварительно закрепленная сталь] G -Star | 5 ~ 40 | 20 ~ 200 | 50 ~ 500 | -0,5 до 0 | -0,5 до 0 | +084 +084 +084 +084 +084 +084 +084 +084 +084 +0844 +084 +084 +084 +084.![]() | ||||||||||||||||||||||||||||||||||||||||||||
5 дней | 10 | [Pre-hardened Steel] G-STAR | 5 ~ 40 | 20 ~ 200 | 50 ~ 500 | ±0.1 | ±0.1 | +0.1 to +0.3 | ||||||||||||||||||||||||||||||||||||||||||||
5 дней | 10 | [Предварительно закрепленная сталь] G-Star | 5 ~ 40 | 20 ~ 200 | 50 ~ 500 | +0.1 до +0,6 | +0,1 до +0.6 9.1.0085 | от +0,1 до +0,3 | ||||||||||||||||||||||||||||||||||||||||||||
5 дней | 10 | [Предварительно запорная сталь] G-Star | 5 ~ 40 | 20 ~ 200 | 50 ~ 500 | 0 до +0,5 | 0 до +0,5 | ++084 ++084 ++084 ++084 ++084 ++084 ++084 ++084 ++084 ++084 ++084 ++084 ++084 ++084 +.![]() | ||||||||||||||||||||||||||||||||||||||||||||
5 дней | 10 | [Предварительно закрепленная сталь] G -Star | 5 ~ 40 | 20 ~ 200 | 50 ~ 500 | -0,5 до 0 | -0,5 до 0 | 444444444408555555955 | -0,5 до 0 | 444444444408555955955 | -0,5 до 0 | 444440855085 | -0,5 до 0 | 08555 | .||||||||||||||||||||||||||||||||||||||
5 дней | 10 | [Предварительно запорная сталь] G-Star | 5 ~ 40 | 20 ~ 200 | 50 ~ 500 | ± 0,1 | ± 0.1 | ± 0,1 | ± 0.1 | ± 0,1± 0,1 | ± 0,1 | ± 0,1 | от 0 до +0,2 | |||||||||||||||||||||||||||||||||||||||
5 Days | 10 | [Pre-hardened Steel] G-STAR | 5 ~ 40 | 20 ~ 200 | 50 ~ 500 | +0.![]() | +0.1 to +0.6 | 0 to +0,2 | ||||||||||||||||||||||||||||||||||||||||||||
5 дней | 10 | [Предварительно закрепленная сталь] G-Star | 5 ~ 40 | 20 ~ 200 | 50 ~ 500 | от 0 до +0,5 | 0 до +0,5 | 44440.5 | .||||||||||||||||||||||||||||||||||||||||||||
6 дней | 10 | [Предварительно закаленная сталь] NAK55 | 5 ~ 40 | 20 ~ 200 | 50 ~ 300 | 92084 -09.0085от -0,2 до 0 | от -0,2 до 0 | |||||||||||||||||||||||||||||||||||||||||||||
6 дней | 10 | [Pre-hardened Steel] NAK55 | 5 ~ 40 | 20 ~ 200 | 50 ~ 300 | ±0.1 | ±0.1 | -0.![]() | ||||||||||||||||||||||||||||||||||||||||||||
6 дней | 10 | [Pre-hardened Steel] NAK55 | 5 ~ 40 | 20 ~ 200 | 50 ~ 300 | +0.1 to +0.3 | +0.1 to +0.3 | -0.2 to 0 | ||||||||||||||||||||||||||||||||||||||||||||
6 дней | 10 | [Предварительно закаленная сталь] NAK55 | 5 ~ 40 | 20 ~ 200 | 50 ~ 300 | от 0 до +0,2 | от 0 до +0,2 | от -0,2 до 0 | ||||||||||||||||||||||||||||||||||||||||||||
6 дней | 10 | [Предварительно закрепленная сталь] NAK55 | 5 ~ 40 | 20 ~ 200 | 50 ~ 300 | -0,2 до 0 | -0,2 до 0 | 4444444444444444444444444444444444444444444444444444444444444444444444444444444444444444444444444444444444444444444444444444444н.![]() | 6 дней | 10 | [Pre-hardened Steel] NAK55 | 5 ~ 40 | 20 ~ 200 | 50 ~ 300 | ±0.1 | ±0.1 | ±0.1 | |||||||||||||||||||||||||||||||||||
6 дней | 10 | [Предварительно закаленная сталь] NAK55 | 5 ~ 40 | 20 ~ 200 | 50 ~ 300 | +3,9 до +0, | от +0,1 до +0,3 | ±0,1 | ||||||||||||||||||||||||||||||||||||||||||||
6 дней | 10 | [Pre-hardened Steel] NAK55 | 5 ~ 40 | 20 ~ 200 | 50 ~ 300 | 0 to +0.2 | 0 to +0.2 | ±0.1 | ||||||||||||||||||||||||||||||||||||||||||||
6 дней | 10 | [Предварительно закрепленная сталь] NAK55 | 5 ~ 40 | 20 ~ 200 | 50 ~ 300 | -0,2 до 0 | -0,2 до 0 | 4444444444 +084444444444 +0844444444444 +084444444444 +084444444444 +084444444444 +084444444444 +084444444444 +084444444444 +08444444440,1.![]() | 6 дней | 10 | [Предварительно закаленная сталь] NAK55 | 5 ~ 40 | 20 ~ 200 | 50 ~ 300 | ±0,1 | ±0,1 | от +0,1 до +0,3 | |||||||||||||||||||||||||||||||||||
6 дней | 10 | [Предварительно закрепленная сталь] NAK55 | 5 ~ 40 | 20 ~ 200 | 50 ~ 300 | +0,1 до +0,3 | +0,1 до | . | ||||||||||||||||||||||||||||||||||||||||||||
6 дней | 10 | [Pre-hardened Steel] NAK55 | 5 ~ 40 | 20 ~ 200 | 50 ~ 300 | 0 to +0.![]() | 0 to +0.2 | +0.1 to +0.3 | ||||||||||||||||||||||||||||||||||||||||||||
6 дней | 10 | [Предварительно закаленная сталь] NAK55 | 5 ~ 40 | 20 ~ 200 | 50 ~ 300 | от -0,2 до 0 | от -0,2 до 0 | от 0 до +0,2 | ||||||||||||||||||||||||||||||||||||||||||||
6 дней | 10 | [Pre-hardened Steel] NAK55 | 5 ~ 40 | 20 ~ 200 | 50 ~ 300 | ±0.1 | ±0.1 | 0 to +0.2 | ||||||||||||||||||||||||||||||||||||||||||||
6 дней | 10 | [Предварительно закрепленная сталь] NAK55 | 5 ~ 40 | 20 ~ 200 | 50 ~ 300 | +0,1 до +0,3 | +0,15 + | .![]() | ||||||||||||||||||||||||||||||||||||||||||||
6 дней | 10 | [Предварительно закаленная сталь] NAK55 | 5 ~ 40 | 20 ~ 200 | 50 ~ 300 | от 0 до +0,2 | от 0 до +0,2 | от 0 до +0,2 | ||||||||||||||||||||||||||||||||||||||||||||
6 дней | 10 | [Предварительно закрепленная сталь] Pxa30 | 5 ~ 40 | 20 ~ 200 | 50 ~ 500 | -0,5 до 0 | -0,5 до 0 | 444444.5.085 | -085 до 0.0085-085.900.18 40085 4008 4.085 до 0.085 9008.98.6 дней | 10 | [Pre-hardened Steel] PXA30 | 5 ~ 40 | 20 ~ 200 | 50 ~ 500 | ±0.![]() | ±0.1 | -0.2 to 0 | |||||||||||||||||||||||||||||||||||
6 дней | 10 | [Предварительно закаленная сталь] PXA30 | 5 ~ 40 | 20 ~ 200 | 50 ~ 500 |
6 дней
6 дней

6 дней
6 дней
6 дней
6 дней
6 дней
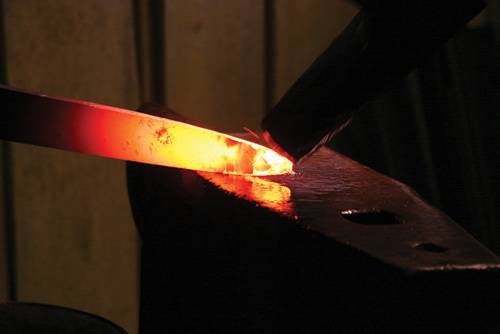
6 дней
6 дней
6 дней

6 дней
6 дней
6 дней
