Класс чистоты обработки поверхности металла: Классы чистоты обработки металла – Особенности и виды
alexxlab | 24.08.2021 | 0 | Разное
Качество обработки поверхностей | МеханикИнфо
Качество сборки отдельных соединений изделия зависит не только от точности изготовления деталей, но и от качества поверхности деталей.
Все изготовляемые детали на своей поверхности имеют следы обработки режущего инструмента в виде «гребешков» — шероховатости. Шероховатости бывают по своей величине и характеру различны. В процессе эксплуатации детали машины, изготовленные с поверхностью, имеющей большую шероховатость, подвергаются большему износу, чем детали, имеющие ровную поверхность. Это объясняется тем, что площадь опоры шероховатой поверхности меньше, чем ровной, так как поверхности соприкасаются между собой только гребешками.
Из-за шероховатости зависит характер посадок. У шероховатой поверхности больший износ, чем у ровной при подвижных посадках, в следствии чего увеличивается посадочный зазор из-за быстрого стирания гребешков. Шероховатость также влияет на прочность соединяемых деталей Гребешки при соединении двух деталей с шероховатой поверхностью неподвижной посадкой срезаются при посадке, и натяг уменьшается.
Из этого следует, что при различных видах неподвижных посадок чистота поверхности должна иметь шероховатость в определенных пределах. Поэтому для различных посадок поверхности обрабатываются различными способами, а именно, опиловкой, шабровкой, притиркой, доводкой.
ГОСТ качество поверхности.
Степень чистоты зависит от величины гребешков, оставшихся от механической обработки, которая измеряется особым прибором, называемым профилографом. ГОСТ 2789 — 45 делит поверхности на разряды и классы в зависимости от средней высоты гребешков. Имеется четыре разряда чистоты поверхностей, которые в свою очередь разделяются на четырнадцать классов (см. табл. 1). Первые три разряда имеют по три класса — с 1 по 9-й, а четвертый — пять классов — с 10 по 14-й.
Классификация чистоты поверхности.

Таблица 1. Классификация чистоты поверхности.
Обозначение класса | Средняя высота микронеровностей Нср в мк | Примерное назначение |
Без знака ~ | Поверхности отливок поковок, штамповок, отрезки и пр. Черные, но ровные поверхности отливок, штамповок, проката, зачищенные поверхности отливок, поковок, отрезки и пр. | |
▽1 | св. 125 до 200 | Поверхности разъемов, отверстий из-под сверла фасок и пр. |
▽2 | св. 63 до 125 | Нерабочие поверхности детали |
▽3 | св. 40 до 63 | Нерабочие поверхности деталей. Посадочные нетрущиеся поверхности изделий поточностью не свыше 5 класса (А5, С5, Х5 |
▽▽4 | св. 20 до 40 | Точно прилегающие поверхности. Поверхности под шабровку.![]() |
▽▽5 | св. 10 до 20 | Отверстия в неподвижных соединениях всех классов точности. Отверстия в нетрущихся соединениях 4 и 5 классов точности. Боковые поверхности зубьев зубчатых колес 3 и 4 классов точности |
▽▽6 | св. 3 до 10 | Отверстия в трущихся соединениях 2 и 3 класса точности. Валы в неподвижных соединениях всех классов точности. Поверхности валов в трущихся поверхностях 4 и 5 классов точности. Боковые поверхности зубьев зубчатых колес 2 класса точности |
▽▽▽7 | св. 3,2 до 6,3 | Поверхности валов в трущихся соединениях 2 и 3 классов точности. Поверхности валов под подшипники качения |
▽▽▽8 | св. 1,6 до 3,2 | То же для более ответственных поверхностей |
▽▽▽9 | св.![]() | Весьма ответственные и трущиеся поверхности валов либо других охватываемых деталей |
▽▽▽▽10 | св. 0,5 до 0,8 | Применяются только в случае особой необходимости |
▽▽▽▽11 | „ 0,25 „ 0,5 | |
▽▽▽▽12 | „ 0,12 „ 0,25 | |
▽▽▽▽13 | » 0,06 „ 0,12 | |
▽▽▽▽14 | до 0,06 |
Обозначение чистоты обработки поверхности.
На чертежах чистота обработки поверхности обозначается треугольниками: первый разряд — одним треугольником, второй — двумя треугольниками, третий — тремя треугольниками и четвертый — четырьмя треугольниками. Необработанная поверхность никакого знака не имеет, а зачищенная поверхность обозначается знаком ~.
Классы обозначаются проставлением арабской цифры около треугольников (например, ▽▽ 4). К первому разряду относятся грубо обрабатываемые поверхности, которые получаются путем обдирки. Ко второму разряду относятся получистые поверхности, полученные путем грубой обработки. К третьему разряду относятся чистые поверхности, гладкие, матовые, полученные в результате чистовой обработки металла — шлифованием, развертыванием и т. д. К качественному четвертому разряду относятся весьма чистые поверхности — зеркального блеска, которые получаются после отделочных операций — притирки, доводки и т. д.
Для определения чистоты поверхности пользуются эталонами чистоты.
Классы чистоты поверхности — шероховатость
Вернуться к Литература
Класс чистоты поверхности ГОСТ 2789-59 | Параметры шероховатости ГОСТ 2789-73 | Обозначение шероховатости по ГОСТ 2,309-73 с 01.![]() | ||
Ra, мкм | Rz, мкм | |||
1 | 2 | 3 | 4 | 5 |
ᐁ1 | 80; 63; 50; 40 | 320; 250; 200; 160 | ||
ᐁ2 | 40; 32; 25; 20 | 160; 125; 100; 80 | ||
ᐁ3 | 20; 160; 12,5; 10 | 80; 63; 52; 40 | ||
ᐁ4 | 10; 8,0; 6,3; 5,0 | 40; 32; 25; 20 | ||
ᐁ5 | 5,0; 4,0; 3,2; 2,5 | 20; 16; 12,5; 10 | ||
ᐁ6 | 2,5; 2,0; 1,6; 1,25 | 10; 8,0; 6,3 | ||
ᐁ7 | 1,25; 1,0; 0,8; 0,63 | 6,3; 5,0; 4,0; 3,2 | ||
ᐁ8 | 0,63; 0,5; 0,40; 0,32 | 3,2; 2,5; 2,0; 1,5 | ||
ᐁ9 | 0,32; 0,25; 0,20; 0,16 | 1,6; 1,25; 1,0; 0,8 | ||
ᐁ10 | 0,16; 0,125; 0,10; 0,8 | 0,8; 0,63; 0,5; 0,4 | ||
ᐁ11 | 0,08; 0,063; 0,05; 0,04 | 0,4; 0,32; 0,25; 0,2 | ||
ᐁ12 | 0,04; 0,032; 0,025; 0,02 | 0,2; 0,16; 0,125; 0,1 | ||
ᐁ13 | 0,02; 0,016; 0,012; 0,01 | 0,1; 0,08; 0,063; 0,05 | ||
ᐁ14 | 0,01; 0,008 | 0,05; 0,04; 0,032; 0,025 |
- В обозначении шероховатости поверхности пользоваться предпочтительными параметрами, выделенными в графе 4 и 5.
- В обозначении шероховатости поверхности, способ которой не устанавливается, применяют знак .
Например: ; . - В обозначении шероховатости поверхности, которая должна быть образована удалением слоя материала, применяют знак .
Например: ; . - В обозначении шероховатости поверхности, которая должна быть образована без удаления слоя металла применяют знак .
Например: ; .
Чистота поверхностей (по ГОСТ 2789-45)
КЛАССИФИКАЦИЯ И ОБОЗНАЧЕНИЯ
Любая машина или механизм состоит из целого ряда взаимно связанных деталей, из которых одни соединены неподвижно, другие катятся или скользят одна по другой. В зависимости от условий работы и характера соединений деталей те или иные поверхности их должны быть обработаны с различной степенью чистоты. При изготовлении деталей на их поверхности получаются следы от обработки режущим инструментом, которые являются следствием различных условий обработки. Следы от обработки создают на обрабатываемой поверхности различные по величине и форме поверхностные неровности.
1. ГОСТ 2789-45 устанавливает классификацию и обозначения чистоты поверхностей в зависимости от среднего квадратичного отклонения Hск их неровностей.
П p и м e ч а н и я.
1. Среднеквадратичное отклонение неровностей поверхности есть корень квадратный из среднего квадрата расстояний точек профиля неровностей до его средней линии.
2. В случаях, когда необходимо измерение максимальной высоты неровностей (Hмакс), определение классов чистоты может быть произведено пут?м пересч?тов на Нск.
Средняя линия профиля неровностей делит профиль таким образом, что площади по обеим сторонам от этой линии до профиля равны между собой.
2. Чистота поверхностей классифицируется по группам, классам и разрядам, согласно шкалам таблиц настоящего стандарта.
3. Назначение чистоты поверхностей производится по шкале групп или классов чистоты. Шкала разрядов чистоты применяется при необходимости в особой дифференциации чистоты. В этом случае наркоматами устанавливаются соответствующие нормали.
П p и м e ч а н и я.
1. Поверхности ч?рные, но ровные, обозначаются знаком . . . .
2. Поверхности, обработанные со значе-
нием Нск больше 100 микронов, обозначаются
(если это необходимо) знаком . . . .
В табл. 24 приведены краткие сведения из области применения классов чистоты для деталей.
Классы чистоты обработки поверхностей – Энциклопедия по машиностроению XXL
Конструкция узла уплотнения поршня показана на рис.
Классы чистоты обработки поверхностей 648 [c.678]
В учебном пособии приведены необходимые при проектировании деталей машин таблицы и стандарты на различные материалы и полуфабрикаты. Кроме того, в приложении даны краткие сведения о взаимозаменяемости в машиностроении, допусках и посадках, стандарты на классы чистоты обработки поверхностей. [c.10]
Затем образцы шлифуют до размеров, предусмотренных ГОСТом 9454—60 и ГОСТом 6996—54 (образец типа VI). Класс чистоты обработки поверхности должен соответствовать указанному на фиг. 128.
[c.208]
Классы чистоты обработки поверхности. Классы точности [c.315]
Коэффициент сложности конструкции ксл определяют путем сравнения деталей, входящих в типовой представитель, с деталями приводимого изделия по точности и классу чистоты обработки поверхностей деталей и другим факторам, характеризующим трудоемкость обработки. Кроме того, коэффициент сложности конструкции учитывает число наименований деталей, входящих в сравниваемые объекты производства. [c.333]
В промышленности широко распространен гальванопластический метод получения деталей и узлов сложного профиля повышенной точности и высокого класса чистоты обработки поверхности. Этим методом возможно изготовлять детали с толщиной стенки от нескольких микрометров до десятков миллиметров. [c.113]
Назначать класс чистоты обработки поверхностей нужно с учетом их назначения (см. рис. 1.1). [c.12]
Ориентировочное сопоставление классов точности и классов чистоты обработки поверхности деталей при различной механической обработке сталей средней твердости
[c. 211]
Распределение высоты неровностей по классам чистоты приведено в табл. 6, составленной согласно ГОСТ 2789—59. В этой таблице указаны наибольшие величины шероховатости по Нг и Яа. средние, экономически достижимые классы чистоты обработки поверхностей в зависимости от видов обработки представлены в табл. 7. [c.12]
Условные обозначения классов чистоты обработки поверхностей [c.68]
Несмотря на высокий класс чистоты обработки поверхности этих деталей, соблюдение установленной температуры и чистоты воздуха при сборке — все же не удавалось полностью предотвратить возникновение коррозии на этих деталях. [c.181]
Гидроабразивная обработка. В течение последних лет разработан и внедрен в промышленность новый эффективный процесс гидроабразивной обработки металлов. Данный процесс заключается в обработке поверхности изделий струей жидкости определенного давления, содержащей во взвешенном состоянии абразивный материал, которым могут служить наждачные порошки различной зернистости и другие порошковые-абразивные материалы. В соответствии с размерами зерен абразива получается различная чистота обработки поверхности изделий. Например, применяя в качестве абразива наждачную пыль,, удается получить 7—10-й класс чистоты обработки поверхности.
[c.31]
Высокий класс чистоты обработки поверхности цилиндрических отверстий с данной конструкцией протяжки обеспечивается наличием на них выглаживающих зубьев, которые располагаются на оправке после режущих зубьев на расстоянии, равном длине протягивания. Обычно берется 4—6 выглаживающих зубьев. [c.147]
Согласно данным табл. 131 для класса чистоты обработки поверхности V V 5, при радиусе закругления вершины резца в 1 мм и скорости резания 130 м мин величина подачи изменяется от 0,46 до 0,42 мм о6. [c.272]
Выражение для тепловой проводимости контакта при повторных приложениях нагруз ки для всех классов чистоты обработки поверхностей, а также при первоначальных нагружениях для поверхностей с чистотой обработки выше 11-го класса получим путем подстановки (3-9) и (3-236) в (1-1)
[c. 87]
Повышение класса чистоты обработки поверхностей по существу ведет к вырождению зависимости Як=1 х). [c.128]
Приведенный в настоящей главе анализ структурных схем металлорежущих станков позволяет сделать следующие выводы. Кинематическая структура металлорежущих станков зависит от геометрической формы, размеров обрабатываемой поверхности и метода обработки. Чем меньше необходимое число исполнительных формообразующих движений, тем из меньшего количества кинематических цепей состоит кинематическая структура станка, тем более простыми могут быть кинематика и конструкция станка. Существенное значение имеют и другие факторы, например, точность и класс чистоты обработки поверхности, вопросы динамики резания, условия обслуживания станка и экономические факторы. [c.15]
Однако современная техника предъявляет все большие требования к точности и чистоте обработки деталей машин, механизмов и приборов. Удовлетворить эти требования могут лишь наиболее точные методы обработки, к которым относится обработка металлов резанием — точение, сверление, фрезерование, строгание, шлифование, доводка и пр. , обеспечивающая размерную точность деталей порядка сотых и даже тысячных долей миллиметра (а в некоторых случаях и микронную точность) и высокий класс чистоты обработки поверхностей.
[c.61]
Модели плоскошлифовальных станков. Неизменный рост выпуска машин высокой точности и высокого класса чистоты обработки поверхностей привели к необходимости выпуска значительного количества различных моделей плоскошлифовальных станков. [c.226]
По шероховатости поверхности реза кислородная резка может обеспечить требования ГОСТ 2789—73 к 2—4 классу чистоты обработки поверхности. [c.197]
Зная hep, выбирают необходимый класс чистоты обработки поверхности цапфы и подшипника. При этом необходимо, чтобы Ях + Яа [c.152]
Болты по рис. 412 изготовляют но змальной точности (ГОСТ 7798—62) и повышенной точности (ГОСТ 7805—62), отличие состоит в классах чистоты обработки поверхностей. Такие же болты выпускают с шестигранными уменьшенными головка. ми (ГОСТ
[c.409]
Зиая h, выбирают необходимый класс чистоты обработки поверхности. [c.133]
Все большее распространение получают металлорежущие станки с числовым программным управлением для автоматизации мелкосерийного и опытного производства. Обладая производительностью станка-авюмата, с одной стороны, и легкостью переналадки универсального станка, с другой стороны, станки с ЧПУ незаменимы в условиях частой смены изделий. Применение металлорежущих станков с ЧПУ дает значительный экономический эффект, сокращает до 50% ручные, доводочные и разметочные работы, дает высокое качество изготавливаемых деталей (точность 3—4 классов), чистоту обработки поверхности 5—6 классов, идентичность размеров (в пределах 0,05—0,1 мм). [c.50]
МИНИН и шпинель (MgAl204). Заготовки образцов прессовались из порошков зернистостью 1—3 мк в специальных пресс-формах, по-зволяюш их получить торцы заданной формы. Спекание полученных заготовок производилось в вакууме при температуре 1900— 1950° С Образцы из керамик на основе окиси алюминия после обжига имели плотность 3,93—3,97 г см , из шпинели 3,2—3,3 г см . Доводка поверхностей трения и их совместная притирка производились с алмазными пастами. Класс чистоты обработки поверхностей составлял V10—VII. После притирки образцы тш ательно промывались и для удаления внедрившихся частиц алмаза прокаливались на воздухе при 1200 С.
[c.50]
Отверстия для неподвижных соединений цилиндрические поверхности подвижных и неподвижных соединений, выполняемых по 3-му классу точности канавки под уплоч-нители и детали с фасонной расточкой цекованныс и зенкованные рабочие поверл-иости. а также рабочие поверхности зубьев и зубчатых колес и шлицы, выполняемые фрезерованием нарезанные прямоугольные и трапецеидальные резьбы. Класс чистота обработки поверхности метрических резьб в чертежах не указывается [c.190]
По формуле (V, 6) проведем оценку минимального и максимального значений приведенного радиуса кривизны. Минимальное значение приведенного радиуса кривизны получим из условий, что г,ф = Гаоп и а = 3 А. Максимальное значение приведенного радиуса кривизны будет иметь место вдоль основания выступа шероховатой поверхности при Гкр = Гпр. Расчетные значения минимальных и максимальных радиусов кривизны в зависимости от классов чистоты обработки поверхностей будут следующие 152]
[c.150]
Универсальность элементов УСП состоит в том, что они имеют такую конструкцию и изготовляются таким методом, которые позволяют многократно использовать их в различных сочетаниях, для разных целей в конструкции приспособления. Например, плоский прихват, который в обычных специальных приспособлениях используется как прижимная планка для крепления обрабатываемого изделия, в системе УСП (УСП-400) в одном случае служит как прижим, в другом — как упор для установки обрабатываемой детали, в третьем — как планка, через которую проходит резьбовая шпилька УСП-410 или пазовый болт УСП-420 для поджима или крепления обрабатываемой детали. Прихваты УСП изготовляют из цементуемой стали 20, закаливают на твердость HiR 55—60, шлифуют и доводят до 3-го класса точности и 6-го класса чистоты обработки поверхностей.
[c.81]
Работы Миллера включают постановку опытов на образцах из бронзы, дюраля, меди, стали 45, 1X13 в широком диапазоне классов чистоты обработки поверхностей (У2—У8) при усилиях сжатия до 4 900-10 н м . В зоне контакта использовались различные газовые среды воздух, углекислый газ, водород. Часть опытов проводилась в условиях глубокого вакуума. Для постановки опытов применялась обычная установка стержневого типа. Экспериментальные данные в основном подтверждают ранее выявленные положения по контактному теплообмену металлических поверхностей. [c.19]
Термическое сапротивленпе контакта уменьшается с повышением теплопроводности контактирующих металлов, увеличением усилия сжатия образцов и повышением класса чистоты обработки поверхностей. Подтверждается также значительное увеличение термического сопротивления контакта в среде глубокого вакуума. [c.19]
Изменение микрогеометрии контактируемых поверхностей может вызывать засасывание смазки, ее распыление и бо яее равномерное распределение по контактной поверхности. Р личные смазки эффективны только для определенного класса чистоты обработки поверхности инструмента (табл. 1). При режимах жидкостного трения, когда эффективность смазки обусловлена ее адгезионными и прочностными свойствами, ульт /азвуковые колебания могут повысить эффективность смазки благодаря снижению сопротивления сдвигу.
[c.112]
Поверхности Обработка механическая — Способы — Классы чистоты
Величины припусков на обработку и допуски на размеры заготовок зависят от ряда факторов, степень влияния которых различна. К числу основных факторов относятся следующие материал заготовки, конфигурация и размеры заготовки, вид заготовки и способ ее изготовления, требования в отношении механической обработки, технические условия в отношении качества и класса чистоты поверхности и точности размеров детали. [c.47]На прочность сцепления влияют способ механической обработки и шероховатость исходной поверхности.
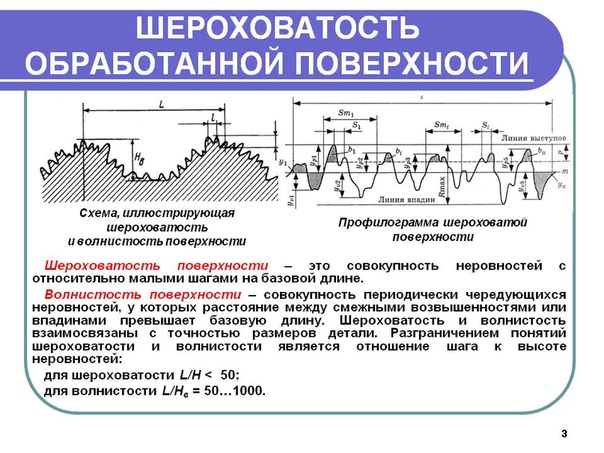
В табл. 18 приведены краткие сведения о шероховатости поверхностей деталей, которая достигается различными способами механической обработки, а в табл. 19 приведены сведения о применении классов чистоты для некоторых наиболее распространенных деталей машин. [c.65]
Выбор классов чистоты поверхности для участков вала под посадки 2 и 3-го классов точности по нормали станкостроения указаны в табл. 5, а в табл. 6 даны сведения о связи чистоты поверхности со способами механической обработки. [c.308]
Способ ротационной обработки впервые был применен в промышленном масштабе на Московском электромеханическом заводе имени Владимира Ильича при изготовлении статоров и роторов электрических машин. Производственники вскоре же убедились в необычайно высокой эффективности нового метода. Вот конкретные цифры производительность труда возросла в четыре раза чистота обработанной поверхности улучшилась в среднем на два класса улучшилось качество поверхностного слоя вследствие полной или частичной ликвидации отрицательных факторов механической обработки — ликвидированы мостики сварки, наволакивание алюминия из пазов на железо ротора, уменьшилась степень и глубина наклепа. В результате коэффициент полезного действия
[c.138]
Основная обработка деталей этого класса происходит при вращении детали. В неподвижном положении детали обрабатывают обычно второстепенные поверхности (сверлят и протягивают отверстия, фрезеруют фасонные поверхности и др.). Все детали этого класса имеют одинаковую схему процесса механической обработки. Однако количество отделочных операций различных деталей и способы их выполнения значительно отличаются и зависят от требуемой точности и чистоты обрабатываемой поверхности, а также от вида заготовки детали.
[c.216]
Обычно литьем под давлением изготовляются тонкостенные детали типа корпусов, коробок, крыльчаток, обработка которых очень сложна, а отливка их другим способом почти невозможна из-за высокой точности размеров, высокого класса чистоты поверхностей и тонкостенности детали типа крышек с большим количеством отверстий, выполняемых отливкой, что значительно снижает трудоемкость механической обработки пустотелые детали, при изготовлении которых из проката большое количество металла уходит в стружку. [c.398]
Чем чище требуется обработка, тем ниже должны быть гребешки. Высота гребешков и глубина впадин (микрогеометрия) колеблются в значительных пределах — от десятых долей миллиметра до сотых долей микрона. Высота и глубина микронеровностей зависит от способа обработки, степени вязкости металла обрабатываемой детали, конструкции режущего инструмента, режима механической обработки (скорости резания, подачи и др.

Электролитическое полирование. Сущность этого способа заключается в анодной обработке поверхности металла в специальных электролитах. Поверхность металла сглаживается в результате растворения выступающих участков. Прн электролитическом полировании удаляются лишь мелкие шероховатости (второго порядка). Поэтому изделия после грубой обработки резцом или изделия, имеющие глубокие впадины на поверхности (шероховатости первого порядка), перед электрополированием должны предварительно подвергаться механической обработке и иметь поверхность, соответствующую 7—8-му классу чистоты обработки. [c.119]
Механическая отделочная обработка применяется в тех случаях когда необходимо повысить класс чистоты поверхности перед нанесением покрытия, удалить следы формообразующего инструмента в виде царапин, вмятин, заусениц или придать поверхности металла определенную фактуру. Кроме того, она используется как промежуточная и окончательная операция в процессе и после нанесения покрытий (особенно многослойных), если они должны обладать высокой степенью блеска. Несмотря на значительное усовершенствование способов механической подготовки, они все еще, особенно для деталей сложной конфигурации, являются весьма трудоемкими, нередко составляя главную статью расходов в производстве покрытий. В зависимости от природы конструкционного материала, назначения, размеров и формы деталей, наконец, от особенностей выбранного покрытия механическая подготовка осуществляется различными способами [143].
[c.84]
Припуски на механическую обработку назначают с целью достижения заданных чертежом конечного или промежуточного размера, обеспечения требуемых шероховатостей поверхности детали и чистоты поверхностного сюя металла отливки. Минимальные припуски определяют в зависимости от класса точности отливки, ее номинального и габаритного размеров, положения данной поверхности при заливке, способа литья и вида сплава.
[c.129]
Этот способ механической обработки позволяет получать в сплошном металле глухие и сквозные цилиндрические отверстия с точностью 4—5-го классов и с чистотой поверхности 2—3-го классов. [c.42]
Развертывание — это способ чистовой механической обработки отверстий. Окончательное развертывание обеспечивает более правильную, чем зенкерование, геометрическую форму отверстия, точность обработки в пределах 2—3 -го классов и чистоту поверхности в пределах [c.59]
Точное литье по выплавляемым моделям позволяет получать сложные тонкостенные отливки 3—5-го класса точности, с чистотой поверхности 4— 5 уменьшается объем механической обработки до 80—90%, сокращается расход жидкого металла в 1,5—2 раза, удешевляется изготовление деталей в 2—3 раза по сравнению с обычными способами производства деталей из проката, поковок и т. п. Этим способом литья получают отливки из. любых сплавов, в том числе плохо поддающихся обработке резанием и давлением.
[c.24]
Основное назначение обработки материалов резанием — получение деталей необходимых геометрических форм, размеров, класса точности и чистоты обработанных поверхностей, что достигается в результате удаления с заготовок слоя металла (припуска). Припуски с заготовок удаляют при помощи металлорежущих станков (механическая обработка) и ручным или механизированным способом (слесарные работы). Заготовки для изготовления деталей получают способами отливки, ковки, штамповки и из прокатанного сортового материала. [c.333]
Литье по выплавляемым моделям позволяет получить заготовки сложной формы, настолько близкой к готовой детали, что в отдельных случаях частично или полностью исключается механическая обработка. По выплавляемым моделям обычно изготовляют отливки небольшого веса (до 3 кг), хотя в отдельных случаях они могут выполняться и значительно большего веса.
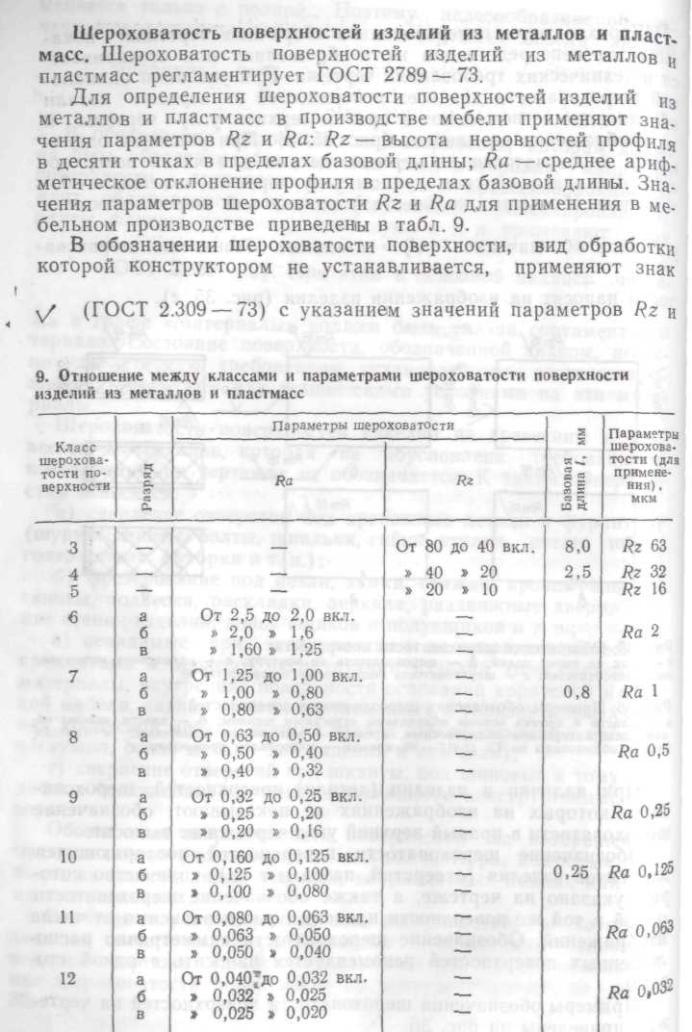
В настоящее время в (Советском Союзе обработке давлением подвергаются 90 о выплавляемой стали, 55″о цветных металлов и их сплавов, различные виды пластмасс и другие неметаллические материалы. Получают заготовки для дальнейшей механической обработки н готовые детали. Так, например детали, полученные листовой штамповкой, поступают непосредственно на сборку прокаткой получают готовые профили, листы, фольгу толщиной 2 -н 2,5 мк волочением изготавливают проволоку с диаметром в несколько микрон и т. д. Способом холодного выдавливания можно получить детали с высоким классом точности и с чистотой поверхности до 10-го класса и выше.
[c.201]
Сущность тонкого точения заключается в срезании с поверхности заготовки тончайших стружек, что обеспечивает высокую точность (2а, 2 и 1 классы) и высокую чистоту поверхности (до V 11). Припуск под тонкое точение составляет 0,1—0,2 мм. Тонкое точение иногда называют алмазным, потому что наибольший эффект по производительности, стойкости инструмента и качеству обработки дают резцы, оснащенные кристаллами естественного алмаза (рис. 229, а). Для этой цели используют кристаллы массой до 0,6 карата (1 карат= 0,2 г), которые крепят в державке механическим способом (прижим планкой) (рис. 229, б) или впаивают в державку. Кристалл алмаза проходит ог- [c.163]
В тех случаях, когда требуется получить высокую чистоту поверхности (8-й класс и выше), обычно сочетают электроискровую обработку с механической доводкой. Необходимо отметить, что поверхности, обработанные электроискровым способом, даже при очень высокой степени чистоты имеют матовый вид.
[c.48]
Для нужд газотурбостроения, когда детали работают при температурах выше 1 100° К, были поставлены опыты Л. 23—25] по определению термического сопротивления контакта стали с металлокерамическими сплавами в зависимости от нагрузки при различной чистоте обработки поверХ)Ностей (рис. 1-9). Примененные в опытах образцы из металлокерамики имели два вида контактных поверхностей. Контактные поверхности одной части образцов были обработаны анодно-механическим способом по 4—5-му классу чистоты, а контактные поверхности другой части образцов не лод-вергались специальиой обработке и имели 2-й класс чистоты. Сила сжатия изменялась в диапазоне (5-Т-392) 10 /л тепловые потоки достигали величины (25,6- -29,1) -10 при средней температуре [c.19]
Основные способы механической обработки и соответствующие им предельно достижимые классы чистоты и параметры шероховатости поверхности приведены в табл. 12. Данные этой таблицы являются укрупненными и позволяют судить о перечисленных способах обработки с точки зрения возможности технологического обеспечения заданного класса чистоты. Наивысший класс чистоты поверхности, относящийся к тому или иному способу обработки, может быть получен путем выполнения чисювой или отделочной операции при хорошем состоянии оборудования, инструмента, приспособления, при правильном назначении режимов резания и других параметров, связанных с выполнением операции
[c.127]
Абразивно-жидкостной обработкой или иначе жидкостным хонингованием называется полирование с помощью смеси жидкости и абразива, подаваемой на деталь из сопла со скоростью свыше 50 м сек. Применяется этот способ для получения чистоты поверхности 7—9-го классов в местах, труднодоступных для механической обработки, например, для отделки форм для литья под давлением, прессформ для пластмасс, профильных отверстий и т. д. [c.63]
Для большинства видов механической обработки, например точения, поперечная шероховатость примерно в 2—3 раза больше продольной и оценку шероховатости в этом случае производят в поперечнбм направлении. Для многих видов чистовых способов обработки шероховатость как в продольном, так и в поперечном направлении может быть одинаковой. Например, при чистовом шлифовании продольная и поперечная шероховатости примерно равны. Измерение класса чистоты поверхности в таких случаях производят в двух направлениях, по наибольшему значению неровностей определяют класс чистоты поверхности.
[c.39]
Следует отметить противоречие между смыслом, заложенным в обозначениях чистоты, и смыслом, вкладываемым в обозначения при простановке на чертежах. По ГОСТу 2789—59 класс чистоты указывает лишь степень шероховатости поверхности, независимо от того, каким способом получена эта поверхность — механической обработкой или в результате заготовительных операций (штампование, литье и т. д.). Между тем, для производства необходимо определенное и не допускающее разнотолкований выделение поверхностей, подлежащих механической обработке. [c.390]
Основным способом механической обработки осталеиных цилиндров поверхностей является шлифование. Чтобы не допу- TPiTb снижения микротвердости поверхностного слоя и получить чистоту поверхности 7—8-го классов, рекомендуется при шлифовании электролитического железа с микротвердостью 500 ед, применять круги Э40СМ2К5. Глубина шлифования 0,06— 0,10 мм/дв. ход, окружная скорость круга 25—40 м/с. Смазочноохлаждающая жидкость должна подаваться в количестве не менее 10 л/мин и не должна вызывать коррозии покрытия.
[c.333]
На станках любой конструкции можно производить наружное обтачивание резцами в концевых оправках. Недостаток этого способа обточки состоит в том, что с ростом длины обтачивания увеличивается вылет резца или оправки и поэтому чистота поверхности получается неудовлетворитель юй. При таком способе обработки установка на глубину резания производится подкола-чиванием резца. Следовательно, обработка деталей с наружным диаметром 2 и 3 класса точности требует участия расточников высокой квалификации.

Заготовками для волочения служит прокат в виде проволоки, прутков н труб, а такж е прессованные профили. Волочением изготовляют проволоку диаметром от 0,002 мм и более, калибруют трубы, прутки различных размеров при этом получают изделия высокого класса точности и с высокой чистотой поверхности. Чтобы уменьшить износ инструмента, предотвратить обрывы изделия и снизить усилие протягивания, заготовку перед волочением обрабатывают одним из термических способов, очищают от окалины и смазывают либо сухим мыльным порошком, либо минеральным маслом, либо покрывают тонким слоем меди. В процессе получения готового изделия может прменяться термическая обработка (отжиг) для восстановления пластических свойств металла. Готовый продукт также может проходить термообработку для приобретения необходимых механических свойств и структуры.
[c.371]
При современном состоянии технологии электрополирования этот процесс не может служить полной заменой механическому полированию, но во многих случаях либо заменяет его, либо сопутствует ему, существенно снижая трудоемкость полирования. Электрополирование, как способ чистовой обработки металлов, наиболее целесообразно применять для деталей и изделий, предварительная механическая обработка которых производилась по 8-му и 10-му классам в соответствии с ГОСТ 2789—51. В этом случае чистота обработки электрополированием может быть повышена на 2—3 класса. При более грубой обработке металла, в пределах 4 —7-го класса, электрополируемая поверхность приобретает блеск, чистота поверхности при этом повышается только на один класс. [c.38]
Шероховатость (чистота) поверхности – Разметка
Шероховатость (чистота) поверхности
Категория:
Разметка
Шероховатость (чистота) поверхности
Поверхности деталей после обработки получаются не гладкими, а состоящими из чередующихся впадин и выступов, т. е. с образованием определенной шероховатости (микрогеометрии).
Шероховатость поверхности оказывает влияние:
а) на величину силы трения, а следовательно, и на величину потери энергии при трении в машинах;
б) на сохранение характера посадок, необходимого для обеспечения требуемой прочности соединения в неподвижных посадках и расчетного зазора в посадках подвижных и других.
Очевидно, что обеспечение взаимозаменяемости деталей требует их идентичности не только в размерах и геометрической форме, но и в шероховатости поверхностей.
В СССР введена и в настоящее время действует стандартная оценка шероховатости поверхности (ГОСТ 2789-59). В основу оценки микрогеометрии ГОСТ 2789-59 включает две вполне определенные численные величины, поддающиеся измерению с помощью специальных приборов, а именно: среднее арифметическое отклонение профиля Ra — среднее значение расстояний (у1, у2 … уN) точек измеренного профиля до его средней линии (т), которая служит базой для определения числовых значений шероховатости (рис. 1), и высоту неровностей Rz — среднее расстояние между находящимися в пределах базовой длины I пятью высшими и пятью низшими точками впадин, измеренное от линии, параллельной средней линии (tn).
Рис. 1. Микропрофиль обработанной поверхности
Контроль шероховатости поверхности производится с помощью специальных приборов. В цеховых условиях пользуются также эталонами шероховатости поверхности, с помощью которых путем сравнения можно определить шероховатости обработанной поверхности с 1-го до 10-го класса.
Обозначение классов чистоты поверхностей на чертежах производится по ГОСТу 2309-68 ЕСКД; шероховатость поверхностей детали обозначается знаком V, рядом с которым указывается класс или класс и разряд чистоты поверхности по ГОСТу 2789-59. Например: V6; V7б. Для ограничения наибольшей и наименьшей величин шероховатости указывают наибольший и наименьший классы или разряды чистоты. Например: V9 … 10; V9б …9в.
Способы обработки поверхностей на чертеже не указывают, за исключением случаев, когда способ обработки является единственным, гарантирующим требуемую шероховатость, например: упол“ровать
Поверхности, не подвергающиеся дополнительной обработке (например, поверхности после прокатки, отливки, штамповки), обозначают знаком со.
Обозначение преобладающей (по количеству поверхностей) шероховатости наносят в правом верхнем углу чертежа. Знак V, взятый в скобки (V), означает, что все остальные поверхности детали, кроме обозначенных знаками шероховатости, имеют шероховатость, указанную перед скобкой, например: V 6 (V). Если шероховатость контурной поверхности должна быть одинаковой, то соответствующее обозначение наносят один раз с надписью «По контуру».
Реклама:
Читать далее:
Основные сведения о допусках и отклонениях
Статьи по теме:
Чистота обработки поверхности металла на токарных станках. Чистовое точение. Причины появления неровностей
Поверхность детали из древесины всегда имеет неровности различной формы и высоты, образующиеся в процессе обработки.
На полученной в результате обработки поверхности древесины различают следующие неровности различного происхождения (рис. 7): риски, неровности разрушения, неровности упругого восстановления по годовым слоям древесины, структурные неровности, ворсистость и мшистость.
Риски представляют собой следы, оставленные на обработанной поверхности рабочими органами режущих инструментов (зубьями пил, ножами фрез и пр.). Риски имеют форму гребешков и канавок (рис. 7,а), обусловленных геометрической формой зубьев пил, или периодически повторяющихся возвышений и впадин (рис. 7, б), являющихся следствием кинематического процесса резания при цилиндрическом фрезеровании (кинематическая волнистость).
Неровности разрушения (рис. 7, в) – это выколы и вырывы целых участков поверхности древесины и образовавшиеся в результате этого углубления с неровным дном. Выколы и вырывы всегда ориентированы вдоль волокон и сопутствуют сучкам, наклону волокон, свилеватости и завиткам.
Неровности упругого восстановления (рис. 7, г) образуются в результате неодинаковой величины упругого смятия режущим инструментом поверхностного слоя древесины на участках различной плотности и твердости. Различные по плотности и твердости годичные слои древесины восстанавливаются после прохода резца неодинаково, в результате чего поверхность обработки получается неровной.
Структурные неровности (рис. 7, д) представляют собой различные по форме, размерам и расположению впадины, полученные на поверхностях изделий, спрессованных из древесных частиц, и обусловленные способом изготовления этих изделий и расположением частиц.
Ворсистость – это присутствие на поверхности обработки часто расположенных не полностью отделенных волокон (ворсинок) древесины, мшистость – не полностью отделенных пучков волокон и мелких частиц древесины.
Шероховатость поверхности обработки характеризуется размерными показателями неровностей и наличием или отсутствием ворсистости или мшистости. Требования к шероховатости поверхности установлены (ГОСТ 7016-75) без учета неровностей, обусловленных анатомическим строением древесины (впадины, образованные полостями перерезанных сосудов), а также без учета случайных дефектов поверхности (скол, вырыв, выщербина).
Шероховатость поверхности определяется среднеарифметической величиной Rz max максимальных высот неровностей и рассчитывается по формуле: (2)
где H max 1 H max 2 ,. ., H max n – расстояния от вершины гребня до дна впадины; n – количество замеров (для изделий мебели устанавливается пять на деталях площадью до 0,5 м 2 и десять на деталях площадью более 0,5 м 2).
В зависимости от числового значения Rz max установлены классы шероховатости:
Классы……..1-й 2-й 3-й 4-й 5-й 6-й 7-й 8-й 9-й 10-й 11-й 12-й Rz max , мкм не более…1600 1200 800 500 320 200 100 60 32 16 8 4
Значение Rz max характеризует только высоту неровностей и не отражает наличие или отсутствие ворсистости и мшистости на обработанной поверхности. Ворсистость и мшистость нормируются указанием на допустимость или недопустимость их на обработанных поверхностях. Ворсистость на поверхности древесины и древесных материалов не допускается, если параметр шероховатости Rz max: имеет значение менее 8 мкм. Мшистость на поверхности древесины и древесных материалов не допускается, если параметр шероховатости Rz max имеет значение менее 100 мкм. Наличие ворсистости и мшистости определяется визуально.
Для контроля шероховатости поверхности в лабораторных условиях применяют микроскопы МИС-11 и ТСП-4 и индикаторный глубиномер. Метод определения шероховатости поверхности устанавливает ГОСТ 15612-70.
В цеховых условиях для сравнительной визуальной оценки шероховатости поверхности пользуются специально изготовленными эталонами. Каждый эталон делают из той же породы древесины и обрабатывают тем же видом резания, что и контролируемые детали. Эталоны должны арестовываться заводской лабораторией и заменяться новыми при их старении.
Влияние различных факторов на шероховатость поверхности обработки . Высота и форма, а также характер расположения неровностей на поверхностях обработанных заготовок зависят от ряда причин: состояния станков и инструмента, остроты и геометрии резца, направления резания относительно направлений волокон древесины, угла установки резца, толщины стружки, скорости резания. Кроме того, шероховатость поверхности зависит от анатомического строения древесины.
На шероховатость поверхности оказывает влияние вибрация в системе станок – инструмент – деталь, возникающая из-за недостаточной жесткости станка. По мере износа станка и особенно вследствие неравномерности его износа вибрация возрастает, увеличивая размеры неровностей.
Влияние вибрации может быть частично снижено профилактическим ремонтом станка с целью увеличения его жесткости, если она ниже установленной нормы.
При строгании ручным инструментом может вибрировать нож рубанка, если он закреплен ненадежно. В этом случае нож будет оставлять неровности на поверхности обработки. Вибрацию ножа в рубанке устраняют ремонтом рубанка, а также надежным закреплением ножа.
Большое влияние на качество резания оказывает острота резца, т. е. его способность образовывать в древесине при резании новые поверхности с заданной шероховатостью.
Чем острее лезвие, тем выше качество резания, т. е. тем меньше шероховатость обрабатываемой поверхности.
Реальный резец не может быть абсолютно острым (рис. 8, а). При заточке резца по мере приближения абразива к лезвию кончик лезвия выкрашивается. Причем чем меньше угол заострения резца, тем на большей длине происходит выкрашивание. Выкрашивание лезвия уменьшают правкой режущих граней оселком. После правки лезвие имеет скругленную форму (рис. 8, б).
Полученные при заточке лезвие и геометрическая форма резца в процессе работы изменяются. Происходит затупление резца (рис. 8, в), в результате чего уменьшается его режущая способность.
Различают две стадии затупления. Первая стадия – разрушение и закругление кончика лезвия, так как прочность резца в области, соприкасающейся с древесиной, небольшая.
Радиус закругления кончика лезвия в процессе работы резца возрастает. Причем у резцов с одним и тем же углом резания, но с разными углами заострения рβ за одно и то же время работы радиус затупления будет больше у резца с большим углом заострения (рис. 9).
Следующая стадия затупления – износ поверхностей резца в результате трения этих поверхностей о древесину. Изнашиваются больше всего передняя и задняя грани резца.
Режущую способность резцов увеличивают, используя для их изготовления высокопрочные и износостойкие материалы и выбирая оптимальные углы заострения.
Направление резания относительно направлений волокон древесины, угол установки резца и толщина стружки – взаимосвязанные факторы, определяющие качество поверхности обработки. При резании древесины вдоль волокон возможны два случая стружкообразования: с опережающей трещиной и без нее.
Опережающая трещина (рис. 10) образуется уже в начальный период работы резца. При внедрении резца в древесину после некоторого уплотнения стружки передней гранью резца начинается оттягивание стружки резцом от остальной массы древесины. Одновременно стружка изгибается. Когда связь между волокнами древесины достигнет предела прочности древесины на разрыв поперек волокон, начинается отслоение стружки и образование опережающей трещины. Длина опережающей трещины возрастает с увеличением толщины стружки.
Скорость распространения опережающей трещины всегда выше скорости резания. Поэтому после образования опережающей трещины режущая кромка не работает. В этот период поверхность резания образуется передней гранью резца путем отрыва стружки от обрабатываемой детали; режущая кромка только сглаживает образованную гранью поверхность. Поскольку стружка образуется отрывом, а не срезается непосредственно лезвием, качество поверхности обработки получается невысоким. Кроме того, при резании против волокон опережающая трещина, расположенная в плоскости волокон, может стать причиной вырыва волокон древесины, приводящего к браку.
Чтобы уменьшить вредное влияние опережающей трещины на качество поверхности обработки, необходимо создать подпор волокон древесины вблизи лезвия (рис. 11). В результате подпора волокон древесины стружка надламывается по мере продвижения резца. Надлом стружки происходит вблизи ребра подпорного элемента, поэтому чем меньше щель между ребром и лезвием резца, тем меньше граница развития опережающей трещины. Такой способ применяют, например, при строгании ручными рубанками.
Наиболее высокое качество поверхности обработки получается при тонкой стружке, когда длина элемента стружки l э мала. Чтобы получить стружку с небольшой длиной элемента, применяют ручные рубанки с двойным ножом, имеющие специальные стружколомы.
При резании древесины вдоль волокон без образования опережающей трещины качество поверхности обработки получается высоким, так как поверхность резания образуется режущей кромкой. Если режут по волокнам и параллельно им (угол встречи равен нулю), то при срезании тонкой стружки и малом угле резания опережающая трещина не появляется, так как резцу легче отогнуть стружку, чем разорвать древесину. В этом случае качество поверхности обработки повышается с уменьшением угла резания.
Однако обрабатываемые заготовки имеют неоднородное строение текстуры древесины, поэтому при больших значениях угла встречи, особенно на участках, имеющих пороки строения древесины, будут появляться вырывы волокон, приводящие к браку. Кроме того, уменьшение угла резания связано с уменьшением угла заточки, что снижает прочность резца.
Резание без образования опережающей трещины возможно также смещением слоев стружки относительно слоев древесины под поверхностью резания, т. е. при продольной усадке стружки.
Продольная усадка стружки возникает, когда передняя грань резца, двигая перед собой стружку, сжимает ее вдоль волокон и превращает в изолированный от обрабатываемой заготовки уплотненный слой. Режущая способность резца используется в полной мере, когда угол резания составляет 70°, а толщина стружки невелика. В этих условиях обеспечивается высокое качество поверхности резания при различных значениях угла встречи резца с волокнами. Резание с продольной усадкой стружки применяют, например, при строгании ручным рубанком-шлифтиком.
При резании древесины в торец качество поверхности обработки получается невысоким. Под поверхностью обработки волокна древесины изогнуты и растянуты, в направлении волокон образуются трещины (рис. 12). Качество обработки при прочих равных условиях выше, когда толщина стружки и угол резания малы.
При резании древесины поперек волокон по мере продвижения резца образуются стружка скалывания (рис. 13, а) или стружка отрыва (рис. 13, б) с короткой опережающей трещиной. Качество поверхности обработки при образовании стружки скалывания достаточно высокое. При стружке отрыва поверхность получается очень шероховатой, с образованием неровностей разрушения.
Качество обработки на больших скоростях резания всегда выше, чем обработка тем же видом резания, но с малыми скоростями. Поэтому для повышения класса шероховатости обрабатываемой поверхности следует повышать в пределах технической возможности станка скорость резания, что одновременно ведет к увеличению производительности станка.
Классы шероховатости поверхности при различных видах обработки и нормы шероховатости. При обработке древесины резанием на станках и ручным инструментом можно получить поверхности различных классов шероховатости в зависимости от режимов обработки, состояния инструмента и обрабатываемой древесины.
Классы шероховатости поверхности при различных видах обработки:
Продольное черновое пиление: на ленточнопильных станках……………………5-2 на круглопильных станках……………………..4-2 ручными пилами………………………………3-2 Продольное чистовое пиление: на круглопильных станках……………………..8-4 ручными пилами………………………………6-4 Поперечное черновое пиление: на круглопильных станках……………………..4-3 ручными пилами………………………………3-2 Поперечное чистовое пиление: на круглопильных станках……………………..7-4 ручными пилами………………………………5-3 Фрезерование черновое………………………..7-5 Фрезерование чистовое………………………..9-6 Сверление отверстий, долбление гнезд на станках…8-6 Сверление отверстий вручную…………………..7-5 Долбление гнезд вручную долотами………………4-2 Точение: черновое……………………………………7-4 чистовое……………………………………10-7 Строгание вручную шерхебелем………………….6-5 Строгание вручную рубанками, фуганком………….8-5 Циклевание ручными циклями: черновое……………………………………9-8 чистовое……………………………………11-10 Шлифование на станках: черновое……………………………………8-6 чистовое……………………………………10-9 Шлифование вручную…………………………..12-8
Приведенные классы шероховатости можно получить при средних режимах работы на станках, нормальном состоянии инструмента и древесины. Класс шероховатости при обработке шерхебелем приведен без учета волнистости, обусловленной формой ножа шерхебеля.
Требования к шероховатости поверхностей при изготовлении мебели диктуются назначением деталей, характером последующей обработки.
Шероховатость не отделываемых поверхностей мебели, видимых при эксплуатации и невидимых, но соприкасающихся с предметами в процессе эксплуатации, должна быть не ниже 8-го класса, остальных невидимых – не ниже 6-го.
Чтобы достичь заданной точности размеров детали и установить при контроле, действительно ли получен заданный размер, необходимо обеспечить при обработке надлежащий класс шероховатости поверхности.
Необходимая точность обработки, отвечающая требованиям заданного класса точности, достигается на различных станках разными способами.
Точность выполнения размеров определяется квалитетами (в системе ОСТ – классы точности). Квалитет (по стандартам СЭВ – Совет Экономической Взаимопомощи) показывает относительную точность изготовления детали.
В зависимости от величины допуска на размер установлено 19 квалитетов точности (IT01, IT0, IT1, IT2,…IT17; IT – Intеrnational Tolerance – международный допуск). IT8 – допуск системы по 8 квалитету ISO (ISO – международная организация по стандартизации).
Практикой определены взаимосвязи между видами обработки и шероховатостью поверхности. Так, например, установлено, что средняя высота неровностей не должна превышать 10-25% от допуска на обработку. Это позволило установить достижимую шероховатость поверхности для различных видов обработки, а с учётом затрат при любом другом способе обработки – и экономически достижимую шероховатость поверхности.
Различные методы обработки по-разному влияют на качество поверхности.
Таблица 1. Характеристики точности и качества, характерные для различных способов обработки резанием
№ п/п | Вид обработки | Точность размеров формы | Качество поверхности | |
квалитет | степень точности | R а мкм | ||
Доводка | 3-4 | 0,08-0,01 | ||
Суперфиниширование | 3-4 | 0,16-0,01 | ||
Хонингование | 3-4 | 0,63-0,01 | ||
Полирование | Предшествующ. | Пр.обработка | 0,63-0,02 | |
Тонкое точение – строгание – шлифование – фрезерование – растачивание | 5-6 | 5-6 6-7 3-4 6-7 5-6 | 1,25-0,32 6,3-1,2 0,63-0,16 1,6 1,25-0,32 | |
Чистовое шлифование – фрезерование – точение -растачивание – строгание -развертывание – зенкерование | 5-6 6-7 5-6 5-7 6-7 | 6-7 8-9 8-9 6-7 9-10 | 1,25-0,63 6,3-3,2 10-1,25 5-2,5 6,3-3,2 1,25-0,32 6,3-3,2 | |
Черновое точение – шлифование – растачивание – сверление – зенкерование – развертывание – фрезерование – строгание – долбление | 9-10 7-9 7-9 11-13 10-11 7-9 | 6-7 9-10 13-15 8-10 7-9 9-10 9-10 9-10 | 40-20 2,5-1,25 80-50 25-5 25-12,5 2,5-1,25 50-25 25-12,5 25-12,5 | |
Сверление по кондуктору | 11-12 | 8-9 | 25-6,3 | |
Координатное растачивание | 4-5 | 1,25-0,32 | ||
Нарезание резьбы: метчиком (плашкой) резцом фрезой | 10-5 5-1,25 5-1,6 |
Для достижения заданного взаимного расположения поверхностей, формы и размеров деталей, их шероховатости и физико-механических свойств при производстве машиностроительной продукции применяют различные методы обработки: резание лезвийным и абразивным инструментами; поверхностное пластическое деформирование; электрофизические, электрохимические и другие методы. По мере приближения размера обрабатываемой поверхности к заданному размеру по чертежу обработка заготовки может быть нескольких видов: обдирочная, черновая, получистовая, чистовая, тонкая, отделочная.
Обдирочная обработка применяется для крупных поковок и отливок 16-18-го квалитетов точности. Она уменьшает погрешности формы и пространственных отклонений грубых заготовок, обеспечивая 15-16-й квалитеты точности, шероховатость поверхности Ra больше 100 мкм.
Черновая обработка выполняется в большом диапазоне точности (12-16-й квалитеты). Шероховатость поверхности Ra = 100-25 мкм.
Получистовая обработка применяется для заготовок, к точности которых предъявляются повышенные требования. Этот вид обработки обеспечивает 11-й, 12-й квалитеты точности. Шероховатость поверхности
Ra = 50,0-12,5 мкм.
Чистовая обработка применяется как окончательный вид обработки для тех заготовок, заданная точность которых укладывается в точность, достигаемую чистовой обработкой (8-11-й квалитеты). Шероховатость поверхности обеспечивается в пределах Ra = 12,5-2,5 мкм.
Тонкая обработка применяется для окончательного формирования поверхностей детали и при малых операционных припусках. Шероховатость поверхности находится в пределах значений Ra = 2,5-0,63 мкм.
Отделочная (финишная) обработка используется для получения требуемой шероховатости поверхности детали на точность обработки влияния почти не оказывает. Выполняется, как правило, в пределах допуска предшествующей обработки. Отделочная обработка обеспечивает получение шероховатости поверхности Ra = 0,63-0,16 мкм.
В современном машиностроении наиболее распространены обработка заготовок лезвийным и абразивным инструментами, которые формируют точность и качество поверхностей деталей. Лезвийным инструментом из сверхтвердых материалов можно обрабатывать заготовки с твердостью до 45 HRC, а абразивным инструментом целесообразно выполнять обработку металлов с более высокой твердостью.
Обработка лезвийным инструментом используется как процесс чистовой и тонкой обработки: тонкое точение, тонкое фрезерование, тонкое развертывание, протягивание, прошивание.
Сущность тонкого точения заключается в снятии стружки малого по толщине сечения при больших скоростях резания (100-1000 м/мин): для чугунных заготовок скорость резания составляет 100-150 м/мин; для стальных – 150-250 м/мин; для цветных сплавов – до 1000 м/мин. Подача устанавливается для предварительного хода – 0,15 мм/об, а для окончательного – 0,01 мм/об. Глубину резания принимают 0,2-0,3 и 0,05-0,01 мм соответственно.
Малые по толщине сечения стружки не вызывают больших усилий резания и значительных деформаций технологической системы СПИД, что обеспечивает 6-8-й квалитеты точности (при обработке цветных металлов и сплавов – 5-6-й квалитеты). Шероховатость поверхности у заготовок из черных металлов Ra = 2,50-0,63 мкм; цветных металлов – Ra = 0,32-0,16 мкм.
Тонкое точение применяется перед хонингованием, суперфинишированием, полированием и выполняется на высокооборотных станках (10-15 тыс. мин -1). Радиальное биение шпинделя не должно превышать 0,005 мм. Все вращающиеся детали должны быть точно отбалансированы.
Резцы оснащаются твердыми сплавами, алмазом, эльбором и другими режущими материалами с высокой износостойкостью. Тонкое обтачивание обеспечивает допуск размеров 5-80 мкм, овальность и конусообразность не более 3 мкм.
Тонкое фрезерование осуществляется преимущественно торцовыми фрезами при обработке плоских поверхностей. Фрезу устанавливают с уклоном 0,0001, чтобы исключить контакт с поверхностью зубьев, не участвующих в резании. При тонком фрезеровании снимается припуск 0,2-0,5 мм, а отклонение от плоскостности на 1 м длины составляет 0,02-0,04 мм. Шероховатость поверхности Ra= 2,5-0,63 мкм.
Тонкое развертывание обеспечивает высокую точность и малую шероховатость, однако не исправляет положения оси обрабатываемого отверстия, поскольку снимает равномерный припуск по всей поверхности. Тонкое развертывание обеспечивает точность, соответствующую 5-7-му квалитетам, Ra = 1,25-0,63 мкм, и чаще всего выполняется после сверления и зенкерования или чернового и чистового растачивания отверстий.
Протягивание применяется для обработки внутренних и наружных поверхностей. При чистовом протягивании цилиндрических отверстий обеспечивается точность 6-9-го квалитетов (шероховатость поверхности
Ra = 2,50-0,63 мкм), протягивание наружных поверхностей обеспечивает точность 11-го квалитета. Протягивание выполняется на горизонтальных и вертикальных станках, универсальных и специальных полуавтоматах и автоматах.
Прошивание осуществляется специальным инструментом (прошивкой), который проталкивают через обрабатываемое отверстие в заготовке с помощью пресса.
Тема 4. Качество поверхности деталей
Эксплуатационные свойства деталей машин, их долговечность в значительной степени зависят от состояния их поверхностей.
Качество поверхности детали определяется геометрическими характеристиками и физико-механическими свойствами поверхностного слоя.
Поверхность, ограничивающую деталь и отделяющую ее от окружающей среды, называют реальной поверхностью.
Номинальная поверхность – это идеальная поверхность, форма которой задана чертежом или другой технической документацией.
Геометрические характеристики качества обработанной поверхности определяются отклонениями реальной поверхности от номинальной, т.е. неровностями различной формы и высоты. Эти отклонения условно можно разделить на разновидности: отклонения от правильной геометрической формы; волнистость; шероховатость.
Критерием этого деления может служить отношение протяженности отклонения L к величине отклонения h (рис. 4.1).
Отклонение формы – геометрические отклонения, у которых отношение L/h более 1000.
Волнистость – совокупность периодически чередующихся возвышенностей и впадин с отношением L/h=50…1000.
Шероховатость – микроскопические отклонения с отношением L/h
При механической обработке качество поверхности оценивается преимущественно шероховатостью.
Шероховатостью поверхности называют совокупность микро неровностей поверхности с относительно малыми шагами, выделенную с помощью базовой длинны.
Термины и определения шероховатости поверхности установлены ГОСТом 25142-82.
Высота, форма, характер расположения и направление неровностей поверхности обрабатываемых заготовок зависят от следующих причин:
Режима обработки;
Условий охлаждения и смазывания обрабатываемого материала;
Геометрии и режущей способности режущего инструмента;
Типа и состояния оборудования и приспособлений и ряда других причин.
Шероховатость может быть:
Продольная образующая в параллельном направлении режущего инструмента;
Поперечная образующая в направлении перпендикулярном направлению движения режущего инструмента.
Параметры шероховатости
Шероховатость поверхности определяют по ее профилю, который образуется в сечении этой поверхности с плоскостью, перпендикулярной к нормальной поверхности. На рис.4.2. показаны основные параметры шероховатости поверхности.
Базовая линия или поверхность – это линия или поверхность заданной геометрической формы, проведенная относительно профиля поверхности и служащая для оценки геометрических параметров шероховатости поверхности.
Базовая длина l –длина базовой линии, используемая для определения параметров шероховатости поверхности. Значение базовых длин могут быть равны 0.01; 0.03; 0.08; 2.5; 8 и 25мм. Шероховатость поверхности определяется на длине L, которая может содержать одну или несколько базовых длин l.
Значение параметров шероховатости поверхности определяется от единой базы, за которую принята средняя линия.
Cредняя линия – m – базовая линия, проведенная так, что в пределах базовой длины среднеквадратичное отклонение профиля от этой линии минимально.
I–e отклонение выступа от средней линии.
I-е отклонение впадин от средней линии.
По ГОСТ 2789-82 установлено шесть параметров шероховатости поверхности:
1. – среднее арифметическое отклонение профиля в пределах базовой длины
или приближенно
где – базовая длина;
n – число измерений на базовой длине.
2. – высота поверхностей профиля по десяти точкам – сумма средних абсолютных значений пяти наибольших выступов и пяти наименьших впадин в пределах базовой длины.
где – высота i-ого наибольшего выступа;
Глубина i –ой наибольшей впадины.
3. – наибольшая высота неровностей профиля – это расстояние между линией выступов и линией впадин в пределах базовой длины.
4. – средний шаг неровностей профиля в пределах базовой длины
где n – число шагов неровностей по вершинам в пределах базовой длины;
Шаг неровностей i-го профиля, равный длине отрезка средней линии, ограничивающей неровность профиля.
5. – средний шаг местных выступов профиля в пределах базовой длины
где n – число шагов неровностей профиля по вершинам в пределах базовой длины;
Шаг неровностей профиля по вершинам, равный отрезку средней линии между проекциями двух наивысших точек соседних выступов профиля.
6. – относительная опорная длина профиля.
где – опорная длина профиля, равная сумме отрезков , отсекаемых на уровне ;
Длина опорной длины выступа на расстоянии Р от средней линии.
ГОСТом 2789-73 установлены 14 классов чистоты поверхности.
Максимальные значения шероховатости и на базовой длине l должны соответствовать данным табл.4.1.
Таблица 4.1
Таблица 4.2
Качество обработки | R a , мкм | R z , мкм | шероховатости |
черновая обработка | 12,5 | ||
чистовая обработка | 6,3 3,2 1,6 0,8 0,4 | 12,5 6,3 1,6 | |
доводочная обработка | 0,2 0,1 0,05 0,025 0,012 | 0,8 0,4 0,2 0,1 0,05 |
Классы точности с 6 по 14 дополнительно подразделяются еще на разряды (табл. 4.3).
Таблица 4.3
ГОСТ 2.309-73 устанавливает обозначение шероховатости и правила нанесения ее на чертежах:
Обозначение шероховатости поверхности, вид обработки которой конструктор не устанавливает.
Шероховатость поверхности, полученной с удалением слоя материала (точение, сверление, фрезерование, шлифование и т.д.).
Шероховатость поверхности, полученная без удаления слоя материала (литье, ковка, штамповка, волочение и др.).
Требования к шероховатости поверхности по одному или нескольким параметрам с указанием их численных значений или диапазона значений, указываются на значке шероховатости.
На рис.4.3 показано, какие параметры указываются на значке шероховатости.
Рис. 4.3.
Факторы, влияющие на шероховатость поверхности при обработке
Шероховатость поверхности в процессе обработки зависит от следующих факторов: метода обработки, режима обработки, геометрических параметров и качества режущей части инструмента, пластической и упругой деформации материала заготовки или детали, жесткости системы СПИД, смазочно-охлаждающей жидкости и т.д.
Каждый метод обработки позволяет получить поверхность детали с определенным диапазоном величины шероховатости (см. табл.4.4).
Так обдирочное точение – 1…4 класс чистоты; чистовое точение – 4…7 класс, тонкое точение – 7…9 класс.
Грубое шлифование – 6…7 класс, чистовое шлифование – 8…9 класс, тонкое шлифование – 9…11 класс и т.д. В зависимости от класса чистоты, указанной на чертеже для поверхности детали, конструктор и технолог выбирают соответствующий метод ее обработки.
Шероховатость обработанной поверхности – это, прежде всего след рабочего движения режущей кромки инструмента, контактируемой с обрабатываемой поверхностью. Высоту этой шероховатости можно определить расчетным путем, в зависимости от геометрических параметров режущей части инструмента и режима обработки.
Сильное влияние на искажение расчетной высоты неровностей поверхности оказывают пластическая деформация материала заготовки при обработке материалов, которые не дают наростов на режущем инструменте, влияние деформации на величину R z объясняется распространением волны деформации в сторону соседнего слоя, а при обработке
материалов, дающих нарост, добавляется еще действие вершины нароста, в результате чего на поверхности детали образуются зазоры.
Влияние упругих деформаций материала детали на R z является следствием наличия на лезвии любого режущего инструмента притупления, что вызывает упругие деформации материала около режущей кромки. Минуя ее, материал заготовки приподнимается и занимает прежнее положение.
Все неровности лезвия режущего инструмента копируются на обрабатываемой поверхности.
Из параметров режима обработки на величину шероховатости наибольшее влияние оказывает скорость резания и подача.
При обработке материалов, не образующих нарост, шероховатость поверхности практически не зависит от скорости резания, а при обработке материалов, образующих нарост, зависит. Так зависимость изменения Rz от скорости резания V p можно разбить на четыре зоны, показанных на рис.4.4.
Рис.4.4. Изменение шероховатости от скорости резания
Таблица 4.4
Обрабатывамые поверхности | Методы обработки | Классы частоты | |||||||||||||||
Наружные цилиндрические | Точение | Х | Х | Х | Х Х | Х | Х | Х Х | Х | Х | |||||||
Шлифование | грубое чистовое тонкое | Х | Х | Х | Х Х | Х | Х | ||||||||||
Притирка | средняя тонкая | Х | Х | Х | Х | Х | Х | ||||||||||
Обкатывание роликом | Х | Х | Х | ||||||||||||||
Суперфини ширование | чистовое тонкое | Х | Х | Х | Х | ||||||||||||
Внутренние цилиндрические | Растачивание | обдирочное чистовое тонкое | Х | Х | Х | Х | Х | Х | Х | Х | Х | Х | |||||
Сверление | Х | Х | Х | ||||||||||||||
Зенкерование | черновое чистое | Х | Х | Х Х | Х | Х | |||||||||||
Развертывание | чистое отделочное | Х | Х Х | Х | Х | ||||||||||||
Протягивание | чистое отделочное | Х | Х | Х | Х | Х | |||||||||||
Внутреннее Шлифование | чистое тонкое | Х | Х Х | Х | Х | ||||||||||||
Калибровка шариком | Х | Х | Х | ||||||||||||||
Притирка | средняя тонкая | Х | Х | Х | Х | Х | Х | ||||||||||
Хонингование | предварител. окончательн. | Х | Х | Х Х | Х | ||||||||||||
Плоские | Строгание | обдирочное чистое тонкое | Х | Х | Х Х | Х | Х | Х | Х Х | Х | Х | ||||||
Цилиндрическое фрезерование | обдирочное чистовое | Х | Х | Х Х | Х Х | Х | |||||||||||
Торцевое фрезерование | обдирочное чистовое | Х | Х | Х Х | Х Х | Х | |||||||||||
Плоское шлифование | грубое чистовое тонкое | Х | Х | Х | Х Х | Х | |||||||||||
Притирка | средняя тонкая | Х | Х | Х | Х | Х | Х | Х | |||||||||
Первая зона соответствует малым скоростям резания (до 1м/мин) и характеризуется тем, что нарост в ней отсутствует, и шероховатость не зависит от Vp
Вторая зона характеризуется увеличением нароста и при Vp = 25…30м/мин нарост наибольший, а поверхность имеет наибольшую шероховатость. С ростом Vp от 30 до 80 м/мин нарост постепенно уменьшается и шероховатость также уменьшается.
При Vp > 80 м/мин нарост вновь исчезает и шероховатость поверхности близка к расчетной.
С увеличением подачи шероховатость при любом способе обработки возрастает, поэтому для снижения значений показателей шероховатости необходимо максимально уменьшить подачу (шаг резания).
Глубина резания незначительно влияет на шероховатость поверхности, однако изменение глубины резания сказывается на упругой и пластической деформации заготовки и инструмента, что отражается на шероховатости поверхности.
Применение смазочно-охлаждающих жидкостей способствует уменьшению параметров шероховатости. При холодной штамповке пуансон и матрицу смазывают, а при обработке резанием применяют водоэмульсионное охлаждение.
Чистовое точение в условиях заводов тяжелого машиностроения часто выполняется теми же проходными и подрезными резцами, что и обдирка. Примерные подачи резца, в зависимости от требуемой шероховатости обрабатываемой поверхности, указаны в табл. 26.Таблица 26 Примерные подачи в зависимости от требуемой шероховатостиОднако при обработке больших поверхностей такой метод обработки часто не может обеспечить получение 6—7 классов чистоты и одновременно 2—3 классов точности. Дело в том, что под влиянием износа резца шероховатость и диаметр обрабатываемой детали увеличиваются и при длительной работе резца выходят за пределы допуска. Для замедления износа резца нужно уменьшить его путь по обрабатываемой поверхности, что возможно достигнуть только за счет увеличения подачи.Поэтому в подобных случаях часто оказывается выгодным работать широкими чистовыми резцами из быстрорежущей стали (фиг. 42,а, б). Они применяются для обработки шеек прокатных, шестеренных валов и т. п., и при этом достигается шероховатость v6—v7 классов чистоты. Режимы резания при работе этими резцами и возможный класс точности обработки указаны в табл. 27.Таблица 27 Режимы резания и точность обработки при работе широкими чистовыми резцами
В некоторых случаях удается работать при подаче 30—40 мм/об. Глубина резания должна быть не менее 0,02 мм при последнем проходе и не более 0,15 мм при первом проходе.
Фиг. 42. Широкий чистовой резец (а) и схема установки его на станке (б). Длина режущей кромки резца принимается равной 80 – 100 мм. С обеих сторон ее на длине примерно 10 мм при помощи оселка заправляются заборный и обратный конусы (фиг. 42, а). Геометрия резца выбирается в зависимости от свойств обрабатываемой стали (табл. 28).Таблица 28 Геометрия широкого чистового резца в зависимости от предела прочности стали
Резцы вставляются с плотной посадкой в гнездо пружинной державки (фиг. 42, б). Желаемая степень упругости державки достигается с помощью деревянной планки, забиваемой в паз державки.Режущая кромка резца устанавливается ниже оси обрабатываемого изделия. Это устраняет вибрации и гарантирует от подхватывания резца. Кроме того, как показывает долголетний; опыт, более высокое качество обработки обеспечивается при работе на обратном вращении шпинделя (фиг. 42, б). В качестве смазки рекомендуется применять жидкость следующего состава: олифа 60%, скипидар 30% и керосин 10%.Наиболее часто чистовое точение производится твердосплавными резцами. Обычные проходные резцы со вспомогательным углом в планеприменяются на токарных, карусельных, расточных и других станках. Они изготовляются с пластинками твердого сплава Т15К6. Этот твердый сплав позволяет работать при скорости резания v = 100 – 250 м/мин, в зависимости от свойств обрабатываемой стали и некоторых других факторов. При такой скорости резания нарост на резце, как известно, не образуется, и поэтому, выбирая соответствующую подачу, удается уверенно получать поверхность, соответствующую 6 классу по ГОСТ 2789—59, а в некоторых случаях и по 7 классу чистоты. Применение сплава Т30К4 позволяет повысить скорость резания примерно на 30—40% и более. Некоторые токари-скоростники повышают скорость резания до 400—500 м/мин. Твердый сплав Т30К4 обладает значительно большей износостойкостью, чем твердый сплав Т15К6. Поэтому наибольший эффект от его применения наблюдается при чистовом точении стали повышенной твердости, особенно при высоких требованиях к чистоте или точности обработки и когда приходится точить большие поверхности с малой подачей, не снимая резца до конца прохода.Резцы с минералокерамическими пластинками находят пока ограниченное применение. Как и твердый сплав Т30К4, керамику целесообразно применять в тех случаях, когда на значительной длине необходимо получить высокую точность и чистоту поверхности, особенно при обработке чугуна.Несмотря на высокую скорость резания, допускаемую твердыми сплавами Т15К6 и Т30К4, обычные проходные резцы со вспомогательным углом в планене могут обеспечить высокую производительность чистовой обработки под v 6—v 7, так как приходится работать при подачах в несколько десятых долей миллиметра. Поэтому, как и во всей машиностроительной промышленности, на заводах тяжелого машиностроения широким распространением пользуются твердосплавные чистовые резцы с дополнительной режущей кромкой, параллельной образующей-детали (фиг. 43,в). Для получения 6—7 класса чистоты такими резцами работают при t 150 м/мин. Наилучшие результаты достигаются при v=250 – 300 м/мин. Однако практически осуществимые скорости резания обычно не превышают 100 м/мин, и поэтому шероховатость поверхности получается не выше 6 класса чистоты. Но после непродолжительной зачистки наждачным полотном сравнительно нетрудно получить и седьмой класс. Большое влияние на шероховатость обработанной поверхности оказывают: отношение длины прямолинейного участка режущей кромки l к подаче s (фиг. 43,а), глубина резания t, правильность установки резца, качество и геометрия его заточки. Чем больше отношение t/s, тем меньше шероховатость обработанной поверхности. При t/s = > 3 достигается 7—8 класс, при t/s = 2 – 1,5—6 класс . Глубину резания t следует принимать, исходя из условий жесткости системы станок — деталь—резец. Обычно t 300 =-5°, а для стали с твердостью Hb
На шероховатость поверхности, обработанной резанием, оказывает влияние большое число факторов, связанных с условиями изготовления заготовки. В частности, высота и форма неровностей, а также характер расположения и направление обработочных рисок зависят от принятого вида и режима обработки; условий охлаждения и смазки инструмента; химического состава и микроструктуры обрабатываемого материала; конструкции, геометрии и стойкости режущего инструмента; типа и состояния используемого оборудования, вспомогательного инструмента и приспособлений.
Все многообразные факторы, обусловливающие шероховатость обработанной поверхности, можно объединить в три основные группы: причины, связанные с геометрией процесса резания; пластической и упругой деформациями обрабатываемого материала и возникновением вибраций режущего инструмента относительно обрабатываемой поверхности.
Процесс возникновения неровностей вследствие геометрических причин принято трактовать как копирование на обрабатываемой поверхности траектории движения и формы режущих лезвий. С геометрической точки зрения величина, форма и взаимное расположение неровностей (направление обработочных рисок) определяются формой и состоянием режущих лезвий и теми элементами режима резания, которые влияют на изменение траектории движения режущих лезвий относительно обрабатываемой поверхности. В различных условиях обработки пластические и упругие деформации обрабатываемого материала и вибрация искажают геометрически правильную форму неровностей, нарушают их закономерное распределение на поверхности и в значительной степени увеличивают их высоту. В ряде случаев пластические деформаций и вибрации вызывают появление продольной шероховатости, достигающей значительных размеров, и увеличение поперечной шероховатости.
Преобладающее влияние на формирование шероховатости поверхности оказывает (как правило) одна из трех указанных групп причин, которая и определяет характер и величину шероховатости. Однако в отдельных случаях шероховатость возникает в результате одновременного и почти равнозначного воздействия всех указанных причин и вследствие этого не имеет четко выраженных закономерностей.
Геометрические причины образования шероховатости
За один оборот заготовки резец перемещается на величину подачи S1 (мм/об) и переходит из положения 2 в положение 1 (рис. 1, а). При этом на обработанной поверхности остается некоторая часть металла, не снятая резцом и образующая остаточный гребешок m. Совершенно очевидно, что величина и форма неровностей поверхности, состоящих из остаточных гребешков, определяются подачей S1 и формой режущего инструмента.
Например, при уменьшении подачи до значения S2 высота Rz неровностей снижается до Rz (рис. 1, б). Изменение углов φ и φ1 в плане оказывает влияние не только на высоту, но и на форму неровностей поверхности (рис. 1, в).
При использовании резцов с закругленной вершиной достаточно большого радиуса r1 форма неровностей становится соответственно также закругленной (рис. 1, г). При этом увеличение радиуса закругления вершины резца до r2 приводит к уменьшению высоты Rz шероховатости (рис. 1, д).
Рис. 1. Геометрическике причины образования шероховатости при точении
Формула расчета подачи учитывающая геометрические причины образования шероховатости:
S o =0,14 x √(Ra x r) ,
Где S o – подача на оборот; Ra – шероховатость, мкм; r – радиус при вершине инструмента, мм.
При изготовлении режущего инструмента и при его затуплении на режущем лезвии инструмента образуются неровности и зазубрины, определенным образом увеличивающие шероховатость обрабатываемой поверхности. Влияние неровностей лезвия инструмента на шероховатость обработанной поверхности особенно существенно при тонком точении с малыми подачами, когда неровности лезвия соизмеримы с величиной Rz. В отдельных случаях полного копирования профиля зазубрин лезвия на обрабатываемую поверхность может и не произойти, так как пластически деформированный металл стружки и обрабатываемой поверхности иногда затекает в зазубрины режущей кромки, частично затормаживаясь в их плоскости, и делает их как бы более мелкими. В результате этого рост высоты шероховатости обработанной поверхности в некоторых случаях отстает от увеличения глубины зазубрин режущего лезвия. Однако и в этих случаях влияние зазубрин лезвия на шероховатость обрабатываемой поверхности может быть значительным.
По имеющимся практическим данным при затуплении режущего инструмента и появлении на нем зазубрин шероховатость обработанной поверхности возрастает при точении – на 50-60%, фрезеровании цилиндрическими фрезами – на 100-115 %, фрезеровании торцовыми фрезами – на 35-45%, сверлении – на 30-40% и развертывании – на 20-30%. Указанное увеличение шероховатости обрабатываемой поверхности при затуплении режущего инструмента связано не только с геометрическим влиянием зазубрин, возникающих на режущем лезвии, но и с возрастанием радиуса округления лезвия. Увеличение радиуса округления лезвия повышает степень пластической деформации металла поверхностного слоя, что приводит к росту шероховатости поверхности. Для устранения влияния зазубрин и притупления режущего лезвия рекомендуются тщательная (желательно алмазная) доводка инструментов и своевременная их переточка.
Приведенные выше сведения о геометрических причинах возникновения неровностей при точении
дают основание сделать следующие выводы.
1. Увеличение главного φ
и вспомогательного φ
1 углов резца в плане приводит к росту
высоты неровностей. При чистовой обточке целесообразно пользоваться проходными резцами с малыми
значениями углов φ
и φ
1, не следует без особой необходимости применять подрезные резцы.
2. Возрастание радиуса закругления вершины резца снижает высоту шероховатости поверхности.
3. Понижение шероховатости режущих поверхностей инструмента посредством тщательной (желательно
алмазной) доводки устраняет влияние неровностей режущего лезвия на обрабатываемую поверхность.
Наряду с уменьшением шероховатости обрабатываемой поверхности доводка заметно повышает стойкость
режущего инструмента, а следовательно, и экономичность его использования.
Пластические и упругие деформации металла поверхностного слоя
При обработке резанием пластичных материалов металл поверхностного слоя претерпевает пластическую деформацию, в результате которой значительно изменяются размеры и форма неровностей обработанной поверхности (обычно шероховатость при этом увеличивается).
При обработке хрупких металлов наблюдается вырывание отдельных частиц металла, что также ведет к увеличению высоты и изменению формы неровностей.
Скорость резания является одним из наиболее существенных факторов, влияющих на развитие пластических деформаций при точении.
Шероховатость обработанной поверхности в значительной степени связана с процессами образования стружки и в первую очередь с явлениями нароста . В зоне малых скоростей (v = 2÷5 м/мин), при которых нарост не образуется, размеры неровностей обработанной поверхности незначительны.
С увеличением скорости размеры неровностей поверхности возрастают, достигая при 20-40 м/мин своего наивысшего значения, многократно превосходящего расчетную величину.
Дальнейшее повышение скорости резания уменьшает нарост и понижает высоту шероховатости обработанной поверхности.
В зоне скоростей (v > 70 м/мин), при которых нарост не образуется, шероховатость поверхности оказывается минимальной. В этом случае дальнейшее увеличение скорости резания лишь незначительно снижает высоту шероховатости поверхности.
При высокой скорости резания глубина пластически деформированного поверхностного слоя незначительна и размеры шероховатости приближаются к расчетным.
В случае обработки хрупких материалов (например, чугуна) наряду со срезом отдельных частиц металла происходят их сдвиг и беспорядочное хрупкое откалывание от основной массы металла, увеличивающее шероховатость поверхности. Повышение скорости резания уменьшает откалывание частиц, и обрабатываемая поверхность становится более гладкой.
При чистовой обработке металлов, когда состояние и точность обработанной поверхности имеют решающее значение, совершенно естественно стремление вести обработку в зоне скоростей, при которых нароста на инструменты не образуется, а шероховатость поверхности получается наименьшей.
Подача – второй элемент режима резания, оказывающий большое влияние на шероховатость, что связано не только с указанными выше геометрическими причинами, но и в значительной степени обусловлено пластическими и упругими деформациями в поверхностном слое.
Резание металлов осуществляется инструментом, лезвие которого всегда имеет некоторый радиус округления ρ. При внедрении резца в обрабатываемый материал происходит отделение стружки по плоскости скалывания А-А (рис. 2). При этом часть металла, лежащего ниже точки В, не срезается, а подминается округленной частью резца, подвергаясь упругой и пластической деформации.
Рис. 2. Схема отделения стружки резцом
После прохождения резца несрезанный слой металла частично упруго восстанавливается, вызывая трение по задней поверхности резца. Разница степени упругого восстановления металла выступов и впадин неровностей обычно увеличивает высоту шероховатости.
Наименьшая толщина t min срезаемого слоя (при превышении t min происходит резание, а при снижении – только пластическое и упругое смятие металла округленной поверхностью лезвия инструмента) зависит от радиуса округления режущего лезвия, свойств обрабатываемого материала и скорости резания (при сокращении радиуса округления р и увеличении скорости резания t min уменьшается).
Неровности поверхности в этом случае образуются не столько под влиянием геометрических причин, сколько в результате упругих и пластических деформаций, скорости резания и радиуса округления режущего лезвия резца. В связи с этим для обеспечения наименьшей шероховатости обработанной поверхности и высокой производительности чистовое точение углеродистых конструкционных сталей следует проводить при s = 0,05÷0,12 мм/об.
При точении цветных сплавов хорошо доведенными или алмазными резцами t min уменьшается, поэтому для снижения высоты шероховатости может оказаться полезным уменьшение подачи до 0,01-0,02 мм/об.
Наблюдениями многочисленных исследователей установлено, что при обычном точении влияние глубины резания на шероховатость ничтожно и практически может не приниматься во внимание. При уменьшении глубины резания до 0,02 мм (вследствие наличия на режущей кромке резца округления) нормальное резание прекращается и резец, отжимаясь от изделия, начинает скользить по обрабатываемой поверхности, периодически врезаясь в нее и вырывая отдельные участки. Поэтому глубину резания при работе обычными резцами не следует брать слишком малой.
При глубине резания меньше подачи глубина оказывает геометрическое влияние на высоту шероховатости. В этом случае уменьшение глубины резания снижает высоту шероховатости.
Обрабатываемый материал и его структура оказывает существенное влияние на характер и высоту неровностей обработанной поверхности. Более вязкие и пластичные материалы (например, малоуглеродистая сталь), склонные к пластическим деформациям* дают при их обработке резанием грубые и шероховатые поверхности.
Применение смазочно-охлаждающих жидкостей, предотвращающих схватывание, уменьшающих трение и облегчающих процесс стружкообразования, способствует снижению высоты неровностей поверхности.
Вибрации режущего инструмента, станка и заготовки
В процессе резания возникают вынужденные колебания системы станок-заготовка-инструмент, вызываемые действием внешних сил, и автоколебания системы, появление которых связано с периодическим упрочнением (наклепом) срезаемого слоя металла и изменением условий трения или резания. Вынужденные колебания системы обусловливаются дефектами отдельных механизмов станка (неточностью зубчатых передач, плохой балансировкой вращающихся частей, неудовлетворительной сшивкой ремня, чрезмерными зазорами в подшипниках и др.), являющимися причиной неравномерности его движения.
Вибрация лезвия режущего инструмента относительно обрабатываемой поверхности являются дополнительным источником увеличения шероховатости обработанной поверхности. Очевидно, что высота шероховатости поверхности будет тем значительнее, чем больше удвоенная амплитуда колебания лезвия инструмента относительно обрабатываемой поверхности.
Большое влияние на шероховатость обработанной поверхности оказывает состояние станка. Новые и хорошо отрегулированные станки, установленные на массивных фундаментах или на виброопорах, хорошо изолированные от вибраций другого оборудования, обеспечивает минимальную шероховатость.
Очень важным является создание достаточно высокой жесткости приспособлений для крепления заготовок и вспомогательных инструментов для установки режущего инструмента. Например, в случае обработки заготовок на револьверном станке из прутка с закреплением последнего в трехкулачковом самоцентрирующем патроне высота шероховатости обработанной поверхности на 30-40 % выше, чем при зажатии прутка в нормальном цанговом патроне, имеющем большую поверхность соприкосновения с заготовкой и создающем поэтому большую ее устойчивость.
Особенно сказываются вибрации технологической системы на шероховатость обработанной поверхности при тонком растачивании на алмазно-расточных станках. Неравномерность припуска, снимаемого при тонком растачивании, обусловливающая колебание сил резания, также может являться причиной вибрации технологической системы, увеличивающих шероховатость обработанной поверхности.
Формирование шероховатости поверхности при различных видах механической обработки (фрезеровании, сверлении, шлифовании, доводке и др.) подчиняется в общем тем же закономерностям, что и при точении. Характер этих закономерностей видоизменяется в зависимости от изменения соотношения влияния геометрических причин, пластических деформаций и вибраций, связанных с особенностями отдельных видов механической обработки.
Сравнение стандартов подготовки поверхности – SSPC / NACE и ISO 8501
Два основных стандарта абразивно-струйной очистки, ISO 8501 и совместные стандарты SSPC / NACE, трудно сравнивать. Хотя они признают примерно одинаковые уровни чистоты, они классифицируют их по-разному, мутя воду.
Это было достаточно просто, пока промышленность не потребовала новой спецификации для степени чистоты, которая могла бы сократить расходы за счет замены белого металла в ситуациях, когда почти белый был достаточно хорош.ISO адаптировала его к установленному порядку как Sa 2 1/2, Very Thorough Blast Cleaning , но SSPC вышла за рамки этого заказа, добавив его в хронологическом порядке как SP 10 Near White . Эти две версии не были равны: Sa 2.5 допускал, чтобы пятна, полосы и тени от ржавчины, прокатной окалины и покрытий оставались на поверхности до 15% *, тогда как SP 10 допускал только 5% .
В 2000 году SSPC и NACE выпустили совместные стандарты в ожидании слияния организаций, членство которых в значительной степени пересекалось.Слияние провалилось, но новый приказ КДЕС, в соответствии с которым КДЕС № 1, 2, 3, 4 отображался на SSPC SP 5, 6, 10, 7, остался в силе.
Это проясняло ситуацию вплоть до 2006 года, когда SSPC / NACE представила промышленную абразивоструйную очистку, новую спецификацию между Brush Off и Commercial, и классифицировала ее в хронологическом порядке как SSPC SP 14 / NACE № 8. ISO отказалась включить новую спецификацию в свою систему как Sa 1.5.
Несмотря на различия, обычно считается, что степени чистоты совместимы.Они отражают аналогичные допустимые уровни пятен и плотно приставшей ржавчины, прокатной окалины и покрытий и могут быть сведены в таблицу:
* Расчетная площадь. ISO 8501-1 является визуальным справочником и не указывает явным образом проценты.
В спецификациях конкретно упоминаются пятна, полосы и тени, но они практически одинаковы: разница в цвете, но не заметной толщины. Плотно приклеенный материал относится ко всему, что нельзя снять тупым шпателем.
Существуют стандарты подготовки поверхности для максимального увеличения срока службы покрытия и для минимизации затрат .
Поскольку подготовка поверхности составляет до 40% стоимости проекта перекраски, владельцы предприятий стремятся ограничить количество материалов и часов, затрачиваемых на взрывные работы. Достижение белого металла обходится дорого, особенно при техническом обслуживании, и, как правило, оно предназначено для критически важных приложений, где стоимость отказа катастрофична. Почти белый цвет достаточно хорош для работы в самых суровых условиях.Коммерческое использование дешевле и подходит для неагрессивной атмосферы и условий эксплуатации. Brush Off сэкономит владельцу большую часть денег в краткосрочной перспективе, если ему это сойдет с рук.
При выборе покрытия владелец взвешивает затраты на пескоструйную очистку и окраску с риском преждевременного разрушения покрытия. Если в худшем случае ему придется перекрашивать через 5 лет вместо 7, он может сэкономить деньги, сократив расходы с коммерческих до чистки. Когда преждевременное повреждение покрытия может привести к утечке пяти миллионов галлонов коррозионных, опасных и дорогостоящих химикатов, он склоняется к White Metal и высокопроизводительному покрытию.
Подготовка поверхности – SteelConstruction.info
Подготовка поверхности – это важнейший первый этап обработки стальной основы перед нанесением любого покрытия, который, по общему мнению, является наиболее важным фактором, влияющим на общий успех системы защиты от коррозии.
На характеристики покрытия в значительной степени влияет его способность должным образом прилипать к материалу основы. Остаточная окалина на стальных поверхностях является неудовлетворительной основой для нанесения современных высокоэффективных защитных покрытий и поэтому удаляется абразивно-струйной очисткой.Другие поверхностные загрязнения на поверхности стального проката, такие как масло и жир, также нежелательны и должны быть удалены перед процессом струйной очистки.
В процессе подготовки поверхности не только очищается сталь, но и создается подходящий профиль для нанесения защитного покрытия.
[вверху] Исходное состояние поверхности
Конструкционные стальные элементы в новых конструкциях обычно представляют собой горячекатаные профили или сборные листовые балки.Исходные стальные поверхности обычно соответствуют степени ржавчины A или B согласно BS EN ISO 8501-1 [1] . По возможности следует избегать использования материала с ямками, то есть степени ржавчины C или D, поскольку во время подготовки поверхности трудно удалить все продукты коррозии с ямок. Ниже приведены описания степеней ржавчины от A до D.
A – Стальная поверхность в значительной степени покрыта приставшей прокатной окалиной, но практически отсутствует ржавчина
B – Стальная поверхность, которая начала ржаветь и с которой прокатная окалина начала отслаиваться
C – Стальная поверхность, на которой прокатная окалина заржавела или с которой ее можно поцарапать, но с небольшими изъязвлениями при нормальном зрении
D – Стальная поверхность, на которой прокатная окалина проржавела и на которой при нормальном зрении видна общая коррозия
Прокат горячекатаный с окалиной (марка Б)
[наверх] Методы подготовки и степени чистоты
Различные методы и степени чистоты представлены в BS EN ISO 8501-1 [1] .Этот стандарт в основном относится к внешнему виду поверхности стали после ручной очистки, очистки механическим инструментом, абразивоструйной очистки или очистки пламенем и дает описания с графическими ссылками на степени чистоты.
[вверх] Очистка ручного и электроинструмента
Очистка поверхности ручными инструментами, такими как скребки и проволочные щетки, относительно неэффективна для удаления прокатной окалины или приставшей ржавчины. Электроинструменты предлагают небольшое улучшение по сравнению с ручными методами, и эти методы могут быть эффективны примерно от 30% до 50%, но обычно не используются для изготовления новых стальных конструкций.Там, где очистка с помощью абразивно-струйной очистки невозможна, методы ручного или механического инструмента могут быть единственно приемлемыми альтернативными методами.
Современный электроинструмент был разработан не только для достижения высоких стандартов чистоты поверхности и профиля, но и для обеспечения почти полного удержания всей образующейся пыли и мусора. Теперь доступно новое оборудование для использования ударных игл с возвратно-поступательным движением, вращающихся заслонок с абразивным покрытием и угловых шлифовальных машин, все в вакуумном кожухе, что делает подготовку поверхности на месте экологически приемлемой.
Подготовка поверхности вручную и с помощью электроинструмента регулируется BS EN ISO 8504-3 [2] , а стандартные степени чистоты в соответствии с BS EN ISO 8501-1 [1] :
- Стр. 2: Тщательная очистка ручных и механических инструментов
- St. 3: Очень тщательная очистка ручных и механических инструментов
Ручная проволочная щетка
(Изображение любезно предоставлено Corrodere / MPI)Rotary wire_brush
(Изображение любезно предоставлено Corrodere / MPI)Ротационная шлифовальная машина
(Изображение любезно предоставлено Corrodere / MPI)Игольчатый пистолет
(Изображение любезно предоставлено Corrodere / MPI)
[вверх] Абразивоструйная очистка
Стальная поверхность, очищенная струйной очисткой до стандарта Sa 2½
Безусловно, наиболее важным и важным методом, используемым для тщательной очистки покрытых окалиной и ржавых поверхностей, является абразивоструйная очистка.Этот метод включает механическую очистку путем непрерывного воздействия абразивных частиц с высокой скоростью на стальную поверхность либо в струе сжатого воздуха, либо с помощью центробежных крыльчаток. Последний метод требует большого стационарного оборудования, оснащенного радиальными лопатками, на которые подается абразив. Когда колеса вращаются с высокой скоростью, абразив отбрасывается на стальную поверхность, причем сила удара определяется размером колес и их радиальной скоростью. В современных установках этого типа используется несколько колес, обычно от 4 до 8, сконфигурированных для обработки всех поверхностей очищаемой стали.Абразивные материалы рециркулируют с помощью сит-сепараторов для удаления мелких частиц. Этот процесс может быть на 100% эффективным при удалении прокатной окалины и ржавчины.
Стандартные степени чистоты для абразивно-струйной очистки в соответствии с BS EN ISO 8501-1 [1] :
- Sa 1 – Легкая струйная очистка
- Sa 2 – Тщательная струйная очистка
- Sa 2½ – Очень тщательная струйная очистка
- Sa 3 – Пескоструйная очистка до визуально чистой стали
Согласно спецификациям для стальных конструкций мостов обычно требуется класс Sa 2½ или Sa 3.
Очищенные поверхности следует сравнить с соответствующей эталонной фотографией в стандарте согласно спецификации.
Доступен очень широкий ассортимент абразивов. Они могут быть неметаллическими (металлические шлаки, оксид алюминия и т. Д.) И металлическими (стальная дробь или крошка и т. Д.).
Размер частиц абразива также является важным фактором, влияющим на скорость и эффективность очистки. В общем, мелкие сорта эффективны для очистки относительно новых стальных конструкций, тогда как грубые сорта могут потребоваться для сильно корродированных поверхностей.Удаление ржавчины со стали с изъянами легче осуществить с помощью мелких сортов стали, и, в зависимости от состояния стальной поверхности, сначала может потребоваться смесь сортов для разрушения и удаления прокатной окалины и очистки участков с изъязвлениями.
Ручная струйная очистка
(Видео любезно предоставлено Corrodere / MPI)
[вверх] Очистка пламенем
В этом методе используется кислородно-газовое пламя, которое проходит по стальной поверхности.Внезапный нагрев приводит к отслаиванию чешуек ржавчины в результате разного расширения чешуек и стальной поверхности. Затем всю рыхлую ржавчину можно удалить соскабливанием и очисткой проволочной щеткой с последующим удалением пыли. Очистка пламенем не является экономичным методом и может повредить покрытие на обратной стороне обрабатываемой поверхности. Также этот метод не очень эффективен для удаления всей ржавчины со стали, поэтому он используется редко.
[наверх] Кислотное травление
Этот процесс включает погружение стали в ванну с подходящими ингибированными кислотами, которые растворяют или удаляют окалину и ржавчину, но не оказывают заметного воздействия на открытую стальную поверхность.Очистка может быть 100% эффективной. Кислотный захват обычно используется только для конструкционной стали, предназначенной для горячего цинкования.
[вверх] Удаление растворимых продуктов коррозии железа
В зависимости от состояния стальных конструкций перед струйной очисткой на поверхности могут присутствовать другие загрязнения, кроме прокатной окалины и ржавчины. Маловероятно, что начальное состояние стальной поверхности марок от A до C будет затронуто, однако состояние класса D (стальные конструкции с ямками) может содержать загрязняющие вещества внутри ям, которые не могут быть удалены с помощью процесса сухой струйной очистки.Испытания на наличие растворимых продуктов коррозии железа обычно не требуются для новых стальных конструкций, но иногда проводятся на стальных конструкциях, которые хранились во внешней среде в течение длительных периодов времени, и на существующих конструкциях, подвергающихся ремонту.
[вверху] Мокрая абразивно-струйная очистка
Мокрая абразивно-струйная очистка
Введение воды в струю абразивной струи способствует снижению опасности пыли, особенно при удалении старых красок на основе свинца и водорастворимых загрязнений.Было разработано несколько методов использования воды с абразивами. При обычной мокрой абразивно-струйной очистке используется такое же давление, что и для обычной сухой струйной очистки и аналогичного оборудования. Вода обычно вводится сразу за форсункой, так что она распыляется и ускоряется через отверстие форсунки вместе с воздухом и абразивом. Вода также может подаваться в контролируемых количествах в основании струйной камеры, а затем смешиваться с воздухом и абразивом, когда она проходит по струйному шлангу.
Существует система низкого давления, в которой вода впрыскивается в воздушный поток, который затем покрывает воздушно-абразивную смесь и предотвращает выход пыли во время взрывных работ. Давление воздуха / воды в сопле относительно низкое; до 7,0 кгс / см 2 (100 фунтов / дюйм 2 ). Из-за низкого отношения воды к воздуху в системе мелкие частицы абразива могут оставаться на стальной поверхности, и их необходимо удалить путем промывки водой. Этот метод обеспечивает высокий визуальный стандарт очистки и эффективен при удалении большого количества растворимых солей.
В некоторых процессах мокрой абразивной обработки в воде используются ингибиторы, предотвращающие ржавление очищенной поверхности. Важно установить, будут ли какие-либо оставшиеся следы таких ингибиторов совместимы с лакокрасочным покрытием, которое будет нанесено впоследствии. Обычно, если ингибиторы не используются, любая ржавчина на поверхности после влажной абразивно-струйной очистки обычно удаляется заключительной легкой сухой струйной очисткой.
[вверху] Водоструйная очистка сверхвысокого давления
Очистка под сверхвысоким давлением воды
Струя воды под сверхвысоким давлением более 1700 бар (25000 фунтов на квадратный дюйм) становится все более популярной, отчасти из-за ее способности удалять высокий процент растворимых солей со стальной поверхности.Его преимущество заключается в том, что он не производит отработанного абразива и не требует затрат на его утилизацию. Кроме того, при более высоком давлении используются меньшие объемы воды, что снижает затраты на утилизацию по сравнению с традиционными методами водоструйной очистки. Водоструйная очистка сверхвысокого давления оставляет теплую поверхность, с которой быстро высыхают следы остаточной воды, но при этом не выделяется достаточно тепла, чтобы вызвать термическое напряжение на стальной поверхности.
Удаление высокой доли растворимых солей со стальной поверхности считается основным преимуществом водоструйной очистки сверхвысокого давления.Ржавчина и покрытия срезаются и снимаются с поверхности относительно легко по сравнению с другими методами струйной очистки. Растворимые соли удаляются более эффективно, поскольку стальной профиль обычно остается неизменным.
Введение небольшого количества абразива в поток воды может привести к более шероховатому профилю поверхности, но также может увеличить эксплуатационные расходы. Подготовка поверхности водоструйной очисткой сверхвысокого давления соответствует требованиям стандарта BS EN ISO 8501-4 [3] .
Водоструйная очистка сверхвысокого давления – чрезвычайно универсальный и эффективный метод удаления краски и металлических покрытий, растворимых солей и других загрязнений со стальных поверхностей.Это безвредно для окружающей среды, и, хотя в настоящее время оно обходится дороже по сравнению с традиционными методами струйной очистки, считается, что это новая технология, которая в ближайшем будущем будет конкурировать и, возможно, заменять традиционные методы открытой абразивоструйной очистки.
Водоструйная очистка UHP
(видео любезно предоставлено Corrodere / MPI)
[вверху] Профиль и амплитуда поверхности
Тип и размер абразива, используемого при струйной очистке, оказывают значительное влияние на получаемый профиль и амплитуду.Помимо степени чистоты, в спецификациях по подготовке поверхности следует также учитывать «шероховатость» по отношению к наносимому покрытию. Для высокоструктурированных лакокрасочных покрытий и термически напыленных металлических покрытий требуется грубый угловой профиль поверхности, чтобы обеспечить механический ключ. Это достигается за счет использования абразивных материалов. Дробеструйные абразивы используются для тонкопленочных лакокрасочных покрытий, таких как заводские грунтовки.
Разница между дробеструйными и зернистыми абразивами и соответствующими профилями поверхности проиллюстрирована ниже на трехмерных диаграммах, полученных с помощью оборудования для бесконтактного определения характеристик поверхности.
Спецификация обработки поверхности должна описывать требуемую шероховатость поверхности, обычно как показатель средней амплитуды, достигаемой в процессе струйной очистки. Было разработано несколько методов для измерения или оценки расстояния между выступами и впадинами поверхностей, очищенных струйной очисткой. К ним относятся панели компаратора, специальные индикаторы часового типа, реплики лент и измерительный щуп. Обычно используются компараторы или копии лент, и соответствующими стандартами являются BS EN ISO 8503-1 [4] и BS EN ISO 8503-5 [5] соответственно.
Компараторы профиля поверхности
[вверху] Поверхностная пыль
При струйной очистке образуется большое количество пыли и мусора, которые необходимо удалить с истираемой поверхности. Автоматические установки обычно оснащаются механическими щетками и воздуходувками. Другие методы могут использовать подметание и чистку пылесосом. Однако эффективность этих операций по очистке может быть нелегко заметна, и наличие мелких остаточных частиц пыли, которые могут мешать адгезии покрытия, можно проверить с помощью чувствительной к давлению ленты, прижатой к поверхности, очищенной струйной очисткой.Затем лента вместе с приставшей к ней пылью помещается на белый фон и сравнивается с графической оценкой. Этот метод описан в BS EN ISO 8502-3 [6] . Хотя в стандарте предусмотрен метод проверки на пыль, нет никаких рекомендаций по приемлемым уровням.
[вверх] Состояние поверхности непосредственно перед нанесением покрытия
После подготовки поверхности до приемлемого стандарта чистоты и профиля важно, чтобы стальные конструкции не вышли из строя.Повторное ржавление может произойти очень быстро во влажной среде, и если сталь не поддерживается в сухом состоянии, нанесение покрытия на поверхность должно быть выполнено как можно скорее. Любое повторное появление ржавчины на поверхности следует рассматривать как загрязнение и удалять с помощью струйной очистки.
[вверх] Дополнительная обработка поверхности
После абразивно-струйной очистки можно проверить наличие дефектов поверхности и изменений поверхности, вызванных производственными процессами, например: сварка. Определенные дефекты поверхности, появившиеся во время первоначальной обработки стали, не могут отрицательно повлиять на эксплуатационные характеристики покрытия, особенно для конструкций, относящихся к категориям окружающей среды с относительно низким уровнем риска.Однако, в зависимости от конкретных требований к конструкции, может потребоваться удалить общие дефекты поверхности сварных швов и обрезных кромок, чтобы обеспечить приемлемое состояние поверхности для окраски.
Сварные швы на сборных стальных конструкциях представляют собой относительно небольшую, но важную часть конструкции и могут создавать переменный профиль поверхности и неровные поверхности или острые выступы, которые могут вызвать преждевременное разрушение покрытия. Хотя сварные участки проверяются, требования к качеству сварного шва обычно не учитывают требования к покрытию.Сварные швы должны быть сплошными, без проколов, острых выступов и чрезмерных подрезов. Также следует удалить сварочные брызги и остаточные шлаки.
- Примеры дефектов поверхности, возникающих во время сварки (изображения любезно предоставлены Corrodere / MPI)
BS EN ISO 8501-3: 2006 [7] описывает степени подготовки сварных швов, обрезанных кромок и других участков на стальных поверхностях с дефектами, чтобы сделать стальные поверхности пригодными для нанесения покрытий.Описаны три степени подготовки с проиллюстрированными примерами соответствующих недостатков, а именно:
- P1- Легкая подготовка
- P2 – тщательная подготовка
- P3 – Очень тщательная подготовка
Выбранная степень подготовки коррелирует с категорией коррозионной активности окружающей среды (от C1 до C5, как описано в BS EN ISO 12944 Часть 2 [8] ) в зависимости от конструкции.
Торцы и кромки пиленых и обрезанных пламенем необходимо обработать, чтобы обеспечить прилипание покрытия и достаточную толщину.
Поперечный разрез с уменьшением толщины покрытия в углу
При внешних выступах (т. Е. Встреча между двумя поверхностями) существует потенциальная проблема, когда есть острый (то есть 90 °) край, потому что жидкое покрытие не будет покрывать его должным образом (см. Справа). Следовательно, их следует сгладить шлифованием или опиливанием. Обычно считается достаточным сгладить угол до радиуса около 2 мм; снятие фаски до 45 ° также эффективно, но трудно избежать появления острых краев при попытке сделать это с помощью ручных инструментов.Можно утверждать, что с современными толстослойными покрытиями и использованием полосовых покрытий (дополнительное покрытие, наносимое только на месте) достаточно сглаживания до радиуса 1 мм. Компания Network Rail устанавливает минимальный радиус в 3 мм, и это считается некоторыми подрядчиками по производству стальных конструкций обременительным требованием.
В дополнение к требованию сглаживания выступов, Спецификация Highways England для дорожных работ [9] определяет нанесение одного или нескольких полосовых покрытий на все внешние углы (а также на сварные швы и крепежные детали по той же причине).
Углы прокатных профилей, как правило, не требуют шлифовки, так как в результате прокатки они обычно получаются гладкими.
Для обработки поверхностей, обработанных пламенем, которые тверже прокатанной поверхности, см. Руководящую записку компании Steel Bridge Group GN 5.06.
[вверх] Рекомендации по покраске строительной площадки
[наверх] Соединения и стыки на объекте
Соединения балок и детали соединений часто не получают полной защиты в магазине, поэтому зоны соединения необходимо ремонтировать на месте.Частым следствием является то, что эти зоны наименее подготовлены и защищены и первыми обнаруживают признаки выхода из строя. Следовательно, важно уделять особое внимание защите этих участков от коррозии.
[вверху] Сварные соединения
В сварных соединениях ключевыми факторами обеспечения эффективности системы покрытия является эффективность защиты перед окончательным покрытием. Места, прилегающие к сварным швам, обычно замаскированы, чтобы предотвратить их покрытие.Маскировка остается на месте до тех пор, пока стык не будет сварен; это не идеальная форма защиты при длительном воздействии перед сваркой.
После сварки важно, чтобы поверхности стыка, включая сам сварной шов, были подготовлены в соответствии с установленными стандартами чистоты и профиля. Из-за загрязнения сварочного флюса необходимо уделять особое внимание удалению всех остатков.
Поверхности сварных швов не должны нуждаться в шлифовке, если они соответствуют требованиям стандарта BS EN 1011: Часть 2 [10] по гладкости и плавности прилегания к основному металлу.Однако шероховатые профили, плохо сформированные старт-стопы, острые подрезы и другие дефекты, такие как прилипшие сварочные брызги, следует удалять путем тщательной шлифовки. Особое внимание необходимо уделять профилю, очищенному струйной очисткой, поскольку металл шва более твердый, а струйная очистка участка сложнее, чем заводская струйная очистка.
[вверху] Болтовые соединения
Болтовые соединения с предварительным натягом заслуживают особого внимания, как поверхности, которые будут оставаться открытыми, так и те, которые не будут (например.грамм. прилегающие поверхности). Поверхности трения обычно либо неокрашенные, либо металлическое напыление без герметика. Следовательно, их необходимо защитить (обычно малярной лентой) до тех пор, пока детали не будут окончательно скреплены болтами.
Следует обратить внимание на удаление любого клея, используемого на защитных пленках для прилегающих поверхностей, и на удаление любых смазочных материалов, нанесенных на резьбу болтов. Также следует проявлять осторожность, чтобы избежать загрязнения поверхностей во время установки болтов. Например, старые пневматические гайковерты имеют тенденцию производить мелкий маслянистый или туманный выхлоп, который может оседать на поверхности.
[вверху] Поверхности, контактирующие с бетоном
Поверхности, контактирующие с бетоном, обычно, за исключением краевой полосы на краях границы раздела, подвергаются пескоструйной очистке из чистой стали. Краевую полосу следует рассматривать как внешнюю поверхность, за исключением того, что необходимо наносить только межоперационные покрытия. Ширина краевой полосы в идеале должна быть не меньше ширины необходимого покрытия арматуры при тех же условиях воздействия. Обычно ширина 50 мм. Любой алюминиевый металлический спрей на поверхностях, контактирующих с бетоном, должен нанести по крайней мере один слой краски, чтобы предотвратить реакцию, которая может возникнуть между бетоном и алюминием.Рекомендуется размещать любые соединители, работающие на сдвиг, на композитных балках так, чтобы они (и их сварные швы) не лежали в пределах краевой полосы; они также должны быть защищены от чрезмерного распыления покрытия.
[вверх] Повреждения при обращении
Во время обработки, поворота и сборки следует избегать повреждения кромок и поверхностей из-за использования зажимов с острыми зубьями, принимая меры предосторожности, такие как использование подъемных устройств с мягкими возобновляемыми контактными поверхностями или правильно сконструированных подъемных скоб.Если повреждение все же произошло, его необходимо тщательно растереть путем шлифовки (и восстановить полную защитную обработку с указанными перекрытиями между слоями).
[наверх] Чистота на участке
Так же, как чистота поверхности перед нанесением первого покрытия является основополагающим для характеристик системы, так и чистота окрашенных поверхностей перед нанесением последующих слоев. На месте незадолго до покраски всегда необходима тщательная очистка, чтобы удалить загрязнения, накопившиеся с течением времени и от строительных работ, включая пыль, утечки цементного раствора при бетонировании, а также продукты струйной очистки, болтовых соединений и сварки.
[вверх] Список литературы
- ↑ 1,0 1,1 1,2 1,3 BS EN ISO 8501-1: 2007, Подготовка стальной поверхности перед нанесением красок и сопутствующих материалов. Визуальная оценка чистоты поверхности. Степени ржавления и степени подготовки стальных поверхностей без покрытия и поверхностей после полного удаления предыдущих покрытий, ISO
- ↑ BS EN ISO 8504-3: 2018, Подготовка стальной поверхности перед нанесением красок и сопутствующих материалов.Методы подготовки поверхности. Очистка ручных и механических инструментов, BSI
- ↑ BS EN ISO 8501-4: 2006, Подготовка стальной поверхности перед нанесением красок и сопутствующих материалов. Визуальная оценка чистоты поверхности. Начальное состояние поверхности, степени подготовки и степень ржавчины в связи с водоструйной очисткой под высоким давлением, ISO
- ↑ BS EN ISO 8503-1: 2012, Подготовка стальной поверхности перед нанесением красок и сопутствующих материалов. Характеристики шероховатости стальных поверхностей, очищенных струйной очисткой.Спецификации и определения для компараторов профиля поверхности ISO для оценки поверхностей, очищенных абразивно-струйной очисткой, BSI
- ↑ BS EN ISO 8503-5: 2017, Подготовка стальной поверхности перед нанесением красок и сопутствующих материалов. Характеристики шероховатости стальных поверхностей, очищенных струйной очисткой. Реплика ленточного метода определения профиля поверхности, BSI
- ↑ BS EN ISO 8502-3: 2017, Подготовка стальной поверхности перед нанесением красок и сопутствующих материалов.Тесты для оценки чистоты поверхности. Оценка запыленности стальных поверхностей, подготовленных к покраске (метод самоклеящейся ленты), BSI
- ↑ BS EN ISO 8501-3: 2007 Подготовка стальной поверхности перед нанесением красок и сопутствующих материалов – Визуальная оценка чистоты поверхности – Часть 3: Степени подготовки сварных швов, кромок и других участков с поверхностными дефектами. BSI
- ↑ BS EN ISO 12944-2: 2017, Краски и лаки. Антикоррозионная защита стальных конструкций защитными лакокрасочными системами.Классификация сред, BSI
- ↑ Руководство по контрактной документации на дорожные работы: Том 1 – Технические условия на дорожные работы, серия 1900 «Защита стальных конструкций от коррозии», август 2014 г., The Stationery Office
- ↑ BS EN 1011-2, 2001, Сварка. Рекомендации по сварке металлических материалов. Дуговая сварка ферритных сталей. BSI
[вверх] Ресурсы
[наверх] Дополнительная литература
- Д. Дикон и Р. Хадсон (2012 г.), Руководство по проектированию стальных конструкций (7-е издание), глава 36 – Коррозия и предотвращение коррозии, Институт стальных конструкций.
- Д.А. Бейлисс и Д. Х. Дикон (2002), Контроль коррозии стальных конструкций (2-е издание), Spon Press.
[вверху] См. Также
Разъяснение различных стандартов чистоты поверхности
Различные стандарты подготовки стальной поверхности используются во всем мире, поэтому может быть непонятно, как каждый стандарт соотносится с другим, а также о практических последствиях для чистоты поверхности. В KUE Group мы работаем в соответствии со стандартами ISO 8501-1: 2007, которые обеспечивают международно признанный набор из четырех классов визуальной чистоты в зависимости от уровня абразивоструйной очистки, необходимого для достижения этого стандарта.
Однако существует несколько других стандартов чистоты, которые широко используются и соблюдаются предприятиями во всем мире – и различаются в зависимости от того, в какой части мира вы работаете, и от профессиональной организации, к которой вы относитесь.Три основных альтернативы ISO 8501-1: 2007:
1. Национальная ассоциация инженеров-коррозионистов / NACE International (NACE), США: Национальная ассоциация инженеров-коррозионистов начала свою жизнь как региональная профессиональная ассоциация в Техасе, но с тех пор расширила свою деятельность до поистине международной ассоциации с аккредитованными членами. по всему миру (включая KUE Group здесь, в Великобритании).NACE выпускает четко определенный набор категорий чистоты поверхности, которые действуют вместе с их эквивалентами ISO.
2. Общество защитных покрытий (SSPC), США: SSPC – это профессиональная ассоциация предприятий, занимающихся обработкой поверхностей, специализирующаяся на промышленном и морском оборудовании. Стандарты чистоты поверхности SP SSPC во многом пересекаются со стандартами NACE, с которыми они тесно связаны, и прямые эквиваленты могут быть составлены со стандартами ISO.В отличие от стандартов NACE, которые широко используются во всем мире, стандарты SSPC в основном используются предприятиями в Северной Америке.
3. Шведский институт стандартов, Швеция: Шведский институт стандартов является автором влиятельных стандартов чистоты поверхности Sa, которые были разработаны, чтобы прояснить небольшие различия между стандартами ISO и США в отношении сухой абразивоструйной очистки, создавая мост между два. Марки Sa широко используются в Европе, и часто отдают предпочтение или используются взаимозаменяемо с эквивалентной маркой ISO.Хотя марки Sa хорошо известны на рынке США, предпочтительными стандартами в Северной и Южной Америке являются ISO, NACE и SSPC.
Что значит чистота?
Чистота поверхности углеродистой стали перед обработкой определяется видимым уровнем ржавчины и прокатной окалины. Как мы обсуждали в предыдущей статье от июля 2019 года, чистоту поверхности можно условно разделить на четыре степени ржавчины, от наименее загрязненной до самой высокой.
A – Обширное покрытие прокатной окалины, но небольшое количество ржавчины или ее отсутствие.
B – Фрезерная окалина начала отслаиваться, и на ней стали заметны зародыши ржавчины.
C – Мельничная окалина в значительной степени заржавела, открыв невооруженным глазом слегка изъеденную поверхность.
D – Мельничная окалина полностью заржавела, оставив общую ямку, которая видна при нормальных условиях.
Стандарты подготовки поверхности описывают визуальное состояние поверхности углеродистой стали после струйной очистки определенной интенсивности. В соответствии со стандартами ISO 8501-1: 2007;
Легкая струйная очистка – в результате получается поверхность, которая заметно свободна от грязи, жира и масла, а также от плохо приставшей ржавчины, краски, прокатной окалины и загрязнений.
Тщательная струйная очистка – в результате получается поверхность, с которой были удалены все видимые жир, масло и грязь, а также большая часть прокатной окалины и ржавчины. Вросшая и прочно приставшая ржавчина и загрязнения все еще могут быть видны.
Очень тщательная струйная очистка – в результате поверхность полностью очищена от жира, грязи, прокатной окалины, ржавчины и краски. Загрязнение может остаться в виде видимых пятен, полос и пятен.
Пескоструйная очистка до визуально чистой стали – обработанная поверхность не имеет видимых загрязнений, прокатной окалины, ржавчины или пятен и имеет однородный металлический вид.
В таблице ниже показано, как стандарты ISO 8501-1: 2007 соотносятся со своими шведскими и американскими аналогами.
ISO 8501-1 | Сб | SSPC | КДЕС | Альтернативное обозначение NACE / SSPC |
Легкая струйная очистка | Sa1 | SP7 | 4 | Пескоструйная очистка |
Тщательная струйная очистка | Sa2 | SP6 | 3 | Коммерческий взрыв |
Очень тщательная струйная очистка | Sa 2½ | SP10 | 2 | Ближний белый взрыв |
Струйная очистка до визуально чистой стали | Sa3 | СП5 | 1 | Белый взрыв |
Подробнее
Чтобы узнать больше о стандартах чистоты стальных поверхностей и о том, как различные стандарты связаны с нашей работой здесь, в KUE Group, или обсудить требования вашего проекта, позвоните по телефону 01274 721188 сегодня.
Источники изображений: NACE, SSPC, SISОсмотр после подготовки поверхности
Внешний вид поверхности стали после струйной очистки указан в графических стандартах. Стандарт ISO 8501-1 (Шведский стандарт ржавчины) определяет внешний вид с использованием классов чистоты вместе со справочными изображениями.
Как и в случае с классами ржавчины, обсуждавшимися ранее, существует четыре степени чистоты для абразивно-струйной очистки новой стали, это следующие для стали класса A:
В спецификации покрытия указывается, какая степень чистоты требуется.Для оценки очищенной поверхности ее следует сравнить с соответствующими фотографиями в стандарте. Остерегайтесь, эти стандарты часто называют стандартами профиля, это не так, это стандарты чистоты поверхности – их часто путают.
Примечание. Для различных марок стали (стали B, C и D) существуют разные классы чистоты (SB, SC и SD). Они также упоминаются в стандарте ISO 8501-1 с соответствующими фотографиями. Существуют также различные степени чистоты для поверхностей, очищенных пламенем и очищенных водой.
Очистка пламенем – это процесс очистки поверхности конструкционной стали путем пропускания через нее очень горячего кислородно-ацетиленового пламени. Горелка, работающая на кислородном топливе, используется параллельно поверхности, чтобы расплавить и сдуть любые пятна, которые хочет оператор, в том числе некоторые из самых трудных для очистки веществ, таких как смазочные материалы и консистентная смазка. Существуют также стандарты визуальной чистоты для других типов оснований, таких как бетон.
Обратите внимание, что существует несколько версий графических стандартов , и выбор используемой стандартизации указан в спецификации задания.Ниже приведен список наиболее часто используемых.
- ISO 8501-1 (Шведский стандарт по ржавчине)
- SSPC VIS 1-01 (SSPC эквивалент шведского стандарта Rust)
- SSPC VIS-2 (Степень коррозии окрашенных поверхностей)
- SSPC VIS-3 (Ручные и электрические инструменты)
- SSPC VIS-4 (водоструйная очистка)
- SSPC VIS-5 (Мокрый абразив)
- BS EN ISO 8501-4 (водоструйная очистка под высоким давлением)
- ASTM D 2200-08 Стандартная практика по использованию графических стандартов подготовки поверхности и руководств для окраски стальных поверхностей
- IMO MSC 215 (82)
- IMO MSC 244 (83)
- ВМС США NSI 009-32
- ВМС США ИПП 63101-000
Наряду с визуальным осмотром для оценки чистоты поверхности (с использованием графических стандартов), можно измерить / оценить профиль поверхности, достигнутый во время пескоструйной обработки, и проверить поверхность основания на наличие невидимых загрязнений, таких как ионы хлорида, сульфата или нитрата.Эти методы обсуждаются в следующих разделах.
Уровень «приемлемости» обычно определяется в спецификациях контракта, а также может быть определен в паспорте материала покрытия.
Измерение профиля или шероховатости поверхности
Пока остается спорным вопрос о том, проверять ли поверхность на наличие невидимых загрязнений до или после измерения профиля поверхности, для этого раздела в первую очередь будет обсуждаться профиль поверхности.Если профиль неправильный и требуется дополнительная струйная очистка, то чистоту поверхности необходимо будет проверить после завершения всех струйных работ.
В то время как «профиль» и «шероховатость» часто являются взаимозаменяемыми терминами, используемыми при описании поверхности подложки, в индустрии покрытий термин «профиль поверхности» обычно используется для описания анкерного рисунка подложки, обработанной струйной обработкой. В то время как «шероховатость поверхности» чаще всего используется для описания обработки поверхности обработанной подложки.SSPC: Общество защитных покрытий определяет профиль поверхности как «текстурированную поверхность, полученную в результате абразивно-струйной очистки или механической очистки металла до голого металла».
Для стали под профилем поверхности понимается высота от пика до впадины. Это часто выражается как среднее значение нескольких отдельных показаний прибора и обычно находится в диапазоне от менее 25 мкм до 127 мкм (от 1 мил до 5 мил).
SSPC определяет шероховатость поверхности как «комбинированные характеристики профиля поверхности (высоты) и количества пиков или плотности для поверхности».Степень профиля на поверхности влияет на общие характеристики покрытия. Высота профиля от пика до впадины (измеренная от пиков до впадин) определяет такие аспекты, как адгезия, покрытие покрытия и общий объем используемого покрытия.
За счет создания профиля на подложке общая площадь поверхности значительно увеличивается. Чем больше увеличивается профиль, тем больше увеличивается площадь поверхности.
Лучше всего это продемонстрировать, сложив лист бумаги.Лист бумаги для копировального аппарата в плоском виде имеет длину примерно 300 мм (11,5 дюйма). Если вы сложите его вперед и назад полосами по 25 мм (1 дюйм), создав эффект гармошки, и положите его на стол, общая длина значительно уменьшится (примерно на 30%).
Рис. 1а. Плоский лист бумаги
Рис. 1б. Тот же лист бумаги сложенный
На самом деле длина подложки не была укорачена, но добавление профиля позволило оригинальной длине 300 мм уместиться в поперечную длину 210 мм.Следовательно, добавление профиля к поверхности увеличивает площадь поверхности на метр длины.
Таким образом, профиль обеспечивает покрытие с большей площадью поверхности, что приводит к повышенной адгезии покрытия.
Однако неверно утверждать, что если вы удвоите профиль, вы также удвоите адгезию.
Если профиль слишком большой, количество покрытия, необходимое для обеспечения адекватного покрытия выступов, увеличивается, в противном случае существует опасность, что выступы останутся без покрытия или будут покрыты слишком тонким слоем, что приведет к появлению пятен ржавчины или точечной ржавчины.
Кроме того, слишком большой профиль может привести к захвату растворителя. Это когда покрытие на дне впадин профиля остается неотвержденным, что уменьшает площадь поверхности для адгезии.
Рис. 2. Пики могут оставаться без покрытия –
допускает появление пятен ржавчины
Мокрая пленка: верхняя поверхность краски высыхает быстрее, чем нижняя, так как летучие компоненты легче испаряются с поверхности.
При разрыве кожуры неотвержденная краска смывается, «растрескивается грязь» и покрытие преждевременно разрушается, что приводит к коррозии.Более того, если профиль поверхности слишком гладкий, может быть недостаточно ключа для обеспечения адекватной адгезии, что приведет к преждевременному разрушению покрытия.
Существует 4 различных метода проверки профиля поверхности и / или шероховатости поверхности:
1. Поверхностные компараторы
2. Реплика ленты
3. Калибры профиля поверхности
4. Приборы для измерения шероховатости поверхности
Поверхностные компараторы Справочная информация
Компараторы поверхностей используются для сравнения свежеобработанных профилей с предварительно заданными профилями.Стандартные компараторы доступны в виде песка, дроби или песка. Выбор компаратора зависит от среды, используемой при взрывных работах.
Рис. 3. Поверхностные компараторы бывают
различных стилей
Отверстие в середине некоторых компараторов позволяет разместить компаратор на поверхности для оценки так, чтобы компаратор и поверхность были видны вместе, что обеспечивает четкое визуальное сравнение с эталонными профилями.С некоторыми продуктами для визуального сравнения можно использовать лупу с подсветкой .
В некоторых случаях используется тактильное сравнение с использованием пальца, ногтя или булавки. Однако следует соблюдать осторожность, чтобы не загрязнить субстрат солями с кожи пальца. Эти компараторы и способ использования подробно описаны в ISO 8503-1.
Рис. 4. Elcometer 125 Grit
Comparator
Важно помнить, что сварные швы – это часть поверхности, подлежащей оценке.Существуют компараторы (такие как Elcometer Surface Weld Comparator ), которые доступны для измерения качества сварных швов.
Компараторы предоставляют значения профиля в
Реплика ленты
Рис. 5. Elcometer 122 Testex ®
Replica Tape
Хотя компараторы поверхностей обеспечивают полезную индикацию профиля поверхности, интерпретация профиля зависит от опыта пользователя.Следовательно, использование компараторов поверхностей для определения профиля поверхности является субъективной оценкой, часто с переменными результатами повторяемости и воспроизводимости.
Реплика ленты , однако, дает числовое значение для профиля поверхности пика и имеет часто заявляемое преимущество обеспечения «доказательства испытания», поскольку использованную ленту можно сохранить и включить в отчеты о проверке (при правильном хранении).
Лента, состоящая из прокладки из пеноматериала, прикрепленной к несжимаемой несжимаемой полосе, укладывается на измеряемую поверхность, при этом прокладка из пеноматериала контактирует с профилем.Затем пену вдавливают в профиль, протирая подложку пластиковой палочкой. Пена повторяет профиль основания. Профиль пенопласта, созданный профилем в подложке, затем может быть измерен с помощью толщиномера микрометра .
Лента доступна в четырех диапазонах для разных диапазонов профилей;
- Грубый минус (C-) (не используется в профилях взрыва)
- Крупный (C) для 20-64 мкм (0,8-2.5 мил) профилей
- X-Coarse (XC) 38-115 мкм (1,5-4,5 мил) и
- X-Coarse Plus (XC +) для профилей 115-127 мкм (4,5-5,0 мил)
Некоторые инспекторы упустили эту информацию из виду. Для тех инспекторов, у которых есть запасы старых версий магнитной ленты, следует позаботиться о том, чтобы тип ленты был четко указан в протоколе.
Как обсуждалось выше, измерение реплики ленты проводится с помощью толщиномера микрометра .Также следует позаботиться о том, чтобы вычесть исходную толщину несжимаемого окна из несжимаемой полосы из общей толщины несущей полосы и пенопласта.
При выборе подходящего микрометра следует учитывать дополнительные факторы – не только для обеспечения соответствующей шкалы на циферблате, но и для того, чтобы к пене прилагалось соответствующее усилие и площадь наковальни (следовательно, давление).
Рис. 6. Elcometer 124
Толщиномер
Толщиномер Elcometer 124 был специально разработан для обеспечения правильной площади опоры и измерительного усилия, чтобы не влиять на показания профиля.Калибр также можно обнулить, чтобы компенсировать исходную толщину окна ленты (обычно 50 мкм (2 мил).
Имейте в виду, что реплика ленты не может использоваться дважды и что «повторное измерение» с использованием одного и того же куска ленты неизбежно приведет к раздавливанию материала, что сделает второй тест недействительным. Также обратите внимание, что если требуется постоянная запись чтения, то необходимо очень осторожное хранение ленты.
Определение и использование ленты-реплики правильного качества для измерения профиля требует, чтобы инспектор имел некоторое представление / знание того, каким должен быть профиль.
Рис. 7. Лента Elcometer 122 Testex Replica может использоваться для измерения профилей до 127 мкм (4,5-5,0 мил)
Чтобы обеспечить разумную повторяемость от пользователя к пользователю, метод C ASTM 4417 рекомендует снимать как минимум 2 показания в каждом месте.
Обратите внимание, что диапазон профиля, который может измерять каждая марка реплики ленты , перекрывается.
При использовании ленты класса X-Coarse измеренное значение находится в диапазоне 38-64 мкм (1.5 – 2,5 мил), измерение также необходимо проводить с лентой грубого помола. Если это показание также находится в диапазоне 38–64 мкм (1,5–2,5 мил), тогда профиль принимается как среднее значение этих двух измерений.
Если используется лента с грубым пометом и показание профиля находится в диапазоне 38–64 мкм (1,5–2,5 мил), то второе показание должно быть снято с лентой с грубым пометом X. Если значение показания грубого помола X больше 64 мкм (2.5 мил), то это показание, которое нужно записать.
Исходное показание с грубой оценкой следует отбросить. Если значение показания грубого помола по X составляет 38–64 мкм (1,5–2,5 мил), тогда профиль принимается как среднее из двух измерений.
Важно отметить, что оба сорта ленты должны быть в наборе инструментов инспектора, поскольку простого измерения одного сорта недостаточно для записи точного измерения профиля.
Как видите, этот на первый взгляд простой и быстрый тест может привести к потенциальным ошибкам у неподготовленных инспекторов. Это еще больше усложняется тем фактом, что более ранние версии реплики ленты не требовали этой процедуры усреднения, и многие пользователи ленты не знают об изменении.
Однако с помощью измерителя профиля мы можем измерить практически любой профиль, который используется на рынке защитных покрытий (0–125 мкм).
Калибры профиля поверхности
Рис 8.Измеритель профиля поверхности Elcometer 224
Измеритель профиля поверхности является альтернативой использованию дублирующих лент с различными диапазонами измерения. Эти датчики доступны с диапазонами измерения 0-500 мкм (0-20 мил), 0-1000 мкм (0-40 мил) и т. Д.
Ключевым преимуществом прибора является то, что он доступен с памятью для хранения пакетных данных. Эти партии могут быть загружены на ПК, смартфон или планшет, чтобы производить постоянную запись измерений.
Состоящий из иглы с коническим наконечником, работающей на плоской ножке диаметром 25 мм, измеритель профиля поверхности Elcometer 224 измеряет высоту от пика до впадины, исходя из расстояния между кончиком иглы и верхушкой иглы. профиль (вершины) и расстояние между кончиком иглы и низом профиля (впадины).
Этот метод позволяет точно определить значение среднего профиля от пика до впадины.
Рис. 9. Измерители профиля поверхности снимают
точных показаний профиля в определенной точке
. Чтобы установить точный профиль, необходимо выполнить
в среднем от 5 до 10
измерений
В соответствии с NACE SP0287, среднее значение для местоположения должно состоять из серии от 5 до 10 показаний прибора в пределах области 150 x 150 мм (6 x 6 дюймов). Среднее значение этих отдельных точечных измерений предоставляет пользователю высоту от пика до впадины в этой точке измерения.Метод ASTM гласит, что калибр следует обнулять с помощью листового стекла.
При снятии показаний плотно прижмите датчик к тестовой подложке, не тяните датчик, так как это ускорит износ наконечника. Измерьте «профиль» в точках, достаточных для характеристики поверхности, либо по соглашению между сторонами, либо по согласованной спецификации.
В каждом месте снимите 10 показаний и определите среднее значение. Затем определите среднее значение по всем точкам и укажите это значение как профиль поверхности (недавний обзор ASTM теперь позволяет регистрировать либо среднее, либо максимальное значение).
Использование цифрового измерителя профиля поверхности Elcometer 224 предоставляет инспектору самый быстрый, точный, воспроизводимый и воспроизводимый метод оценки профиля поверхности на плоских поверхностях.
Для каждого места измерения пользователь может выбрать количество измерений, которые будут сняты и «усреднены» для получения значения. Компания Elcometer рекомендует проводить как минимум 2 измерения для каждого местоположения.
Использование режима подсчета среднего значения позволяет автоматически записывать в память среднее значение точечных показаний.Затем эти показания можно отправить на устройство с ОС Android или iOS или напрямую на ПК – через Bluetooth или USB.
Рис. 11. Программное обеспечение ElcoMaster
для Android может
автоматически наносить считанные значения
на карту
Используя режим чтения в реальном времени, в сочетании с устройством Android и iOS с GPS, пользователи могут записывать не только профиль поверхности, но и координаты GPS. Затем программа ElcoMaster нанесет значения на карту, которая может быть отображена на экране.
Верхние и нижние пределы значений также могут быть установлены на цифровом измерителе профиля поверхности Elcometer 224 , что позволяет предупреждать пользователей, когда профиль поверхности слишком высокий или слишком низкий, чтобы соответствовать спецификации.
Наконечник является контактным элементом и будет изнашиваться. Инспектор может увидеть это как сплющивание (или закругление) кончика булавки.
Наконечник заменяется пользователем.
Рис 12.Калибровку можно проверить
с помощью специальной поверочной фольги, помещенной
на стеклянную нулевую плитку
Калибровку измерителя профиля поверхности Elcometer 224 можно проверить (вместе с износом наконечника) с помощью проверочной фольги Elcometer и стеклянной нулевой плитки.
Компания Elcometer разработала датчик для измерения профиля цилиндрических поверхностей, таких как трубы. Этот датчик может учитывать кривизну и вносить необходимые поправки для получения точных и повторяемых показаний глубины профиля.
Рис. 13. Датчик профиля поверхности
Convex Elcometer 224
В определенных условиях может существовать риск взрыва электронного оборудования, например, в нефтегазовой промышленности.
Для этого приложения существуют аналоговые датчики, такие как Elcometer 123 Surface Profile Gauge , который измеряет профиль с помощью иглы аналогично датчику Elcometer 224 Surface Profile Gauge .
Поскольку эти датчики не имеют пакетной памяти, пользователям необходимо вручную записывать все измерения и вычислять среднее значение этих измерений для определения профилей поверхности.
Измеритель шероховатости поверхности
Рис. 14. Тестеры шероховатости
, такие как Elcometer 7062, используют иглу
на моторизованной руке
Измеритель шероховатости поверхности состоит из иглы (наконечника), прикрепленной к рычагу, который будет тянуть наконечник с постоянной скоростью по заранее определенной линейной длине.Измеритель позволяет отслеживать поверхность, а также глубину профиля.
Датчик обеспечит очень подробный анализ профиля поверхности.
Измерение шероховатости поверхности важно для производителей обрабатываемых деталей, поэтому датчики очень чувствительны для измерения почти «гладких» поверхностей.
Чувствительный (и деликатный) характер этого манометра не делает его идеальным устройством для использования в полевых условиях.
Измеритель шероховатости также может использоваться для измерения профиля взрыва. Некоторые стандарты испытаний требуют измерения Rmax, Ra, Rt и Rz, что требует измерения профиля по линейному пути.
Рис. 15. Тестеры шероховатости могут использоваться для определения профиля и расстояния
между самой нижней впадиной и самым высоким пиком (Rt) для каждой трассы. Среднее значение числа Rt по нескольким трассам известно как Rz
- Rmax: Наибольшее расстояние между самым высоким пиком и самой низкой впадиной на длине выборки.
- Ra: Средняя шероховатость по длине выборки.
- Rt: Расстояние между самым высоким пиком и самой низкой впадиной в пределах любой заданной длины выборки
- Rz: Среднее расстояние между наивысшим пиком и самой низкой впадиной на нескольких участках выборки
Отделка металла – какие виды отделки бывают?
Изображение предоставлено: Вадим Ратников / Shutterstock.ком
Обработка металла – это заключительный этап производственного процесса, обеспечивающий эстетичный вид и защиту окружающей среды. Он также используется для уменьшения шероховатости поверхности за пределами возможностей операций механической обработки деталей, которые должны сопрягаться или уплотняться. Он также включает методы очистки металла, удаления окалины, снятия заусенцев и т. Д. Короче говоря, для различных целей используются многочисленные типы процессов отделки металла. В этом руководстве рассматриваются некоторые основные методы отделки, а также их применение и рекомендации по выбору процесса отделки металла.Некоторые из общих преимуществ обработки металлов включают:
- Повышенная прочность
- Улучшенная декоративная привлекательность
- Повышенная электропроводность
- Более высокое электрическое сопротивление
- Повышенная химическая стойкость
- Повышенная стойкость к потускнению
Виды обработки металлов
Ниже приведены некоторые из доступных способов отделки:
Покрытие
Для нанесения металлического покрытия используются химические ванны для покрытия или изменения поверхности подложек тонкими слоями металла, такого как цинк, никель, кадмий или хром.При нанесении гальванического покрытия на подложку генерируется электрический ток, а при нанесении покрытия химическим способом используется автокаталитический процесс, при котором подложка катализирует реакцию. Поскольку гальваника – это химически интенсивный крупномасштабный процесс, он почти всегда выполняется поставщиками услуг по гальванике, которые специализируются в этой области.
Металлическое покрытие может улучшить долговечность продукта, устойчивость к коррозии, поверхностное трение и внешний вид. В случае оцинкованного металла цинковое покрытие служит жертвенным анодом, который сам корродирует, защищая целостность лежащей под ним подложки.Однако гальванические машины обычно не подходят для сглаживания дефектов поверхности.
Шерардизация – это процесс, используемый для покрытия небольших стальных деталей, таких как болты и шайбы, коррозионно-стойким сплавом цинка и железа. Детали помещаются в нагретый барабан, содержащий цинковую пыль, что обеспечивает высокую коррозионную стойкость. При крупносерийном производстве машина для чистовой обработки стволов является быстрым и эффективным решением для нанесения покрытий.
Более подробную информацию о гальванических покрытиях можно найти в этой статье, посвященной антикоррозийным покрытиям.
Чистка / Очистка
В отличие от металлизации, обработка металла щетками является эффективным методом устранения дефектов поверхности. Эти отделочные машины создают однородную текстуру поверхности с параллельными зернами, чтобы сгладить внешний вид продукта. Для достижения этого эффекта обычно используется абразивная лента или проволочная щетка. Кроме того, особое направление ленты или кисти может создать слегка закругленные края, перпендикулярные волокну.
Кроме того, очистка проволочной щеткой используется для удаления шлака, образующегося при некоторых сварочных операциях, а также для удаления окалины и песка с металлических поверхностей перед очисткой.
Химические ванны и кислотные ванны используются для очистки остатков масла, оставшихся от механической обработки, формовки и других процессов перед нанесением гальванического покрытия или покрытия.
Полировка / полировка / хонингование / притирка
Эти абразивные методы используются для уменьшения шероховатости поверхности металлов после механической обработки. Шероховатость измеряется в микродюймах при самых сложных процессах обработки (развертывание, протяжка), обеспечивающих чистоту поверхности 16–125 мкм. Прецизионное или тонкое шлифование (см. Ниже) может снизить шероховатость поверхности до 8–16 мкм.с помощью абразивных кругов или насадок. Кроме того, абразивные порошки используются в сочетании с кожаными или войлочными кругами для полировки (1-32 мкм) и полировки (0,5-16 мкм) по мере необходимости. При хонинговании и притирке используются абразивные составы для улучшения шероховатости поверхности сопрягаемых деталей путем их трения друг о друга (например, притертых клапанов двигателя) или пропуска сопрягаемой формы через полость (например, отточенный цилиндр).
Процесс, который уменьшает шероховатость поверхности, также увеличивает блеск металла, поскольку отраженный свет меньше рассеивается от более гладких поверхностей.Таким образом, эти же методы часто используются просто для улучшения внешнего вида.
Шлифовальный
В шлифовальных станках используются абразивные круги для сглаживания поверхностей. Существует несколько типов шлифовальных станков, предназначенных для обеспечения конечной гладкости разного уровня. Как отмечалось выше, шлифование используется для уменьшения шероховатости поверхности, оставшейся после обработки, и в качестве последнего шага в процессе обработки, чтобы приблизиться к допуску. Плоскошлифовальный станок является наиболее распространенной формой шлифовального станка, но существует множество специализированных шлифовальных машин, таких как бесцентровые шлифовальные машины и шлифовальные машины Blanchard, которые также используются в повседневной жизни.
Многочисленные разновидности ручных шлифовальных машин используются для удаления металла, очистки шлака и т. Д. Шлифовальные машины для штампов используются для детальной обработки проходов впускных коллекторов, штампов и т. Д. Они обычно оснащены абразивными кругами специальной формы, известными как установочные наконечники.
Вибрационная чистовая
Вибрационные отделочные машины используются для снятия заусенцев с продуктов и удаления острых кромок, литников и т. Д. Они размещают детали внутри барабана, заполненного абразивными гранулами, и применяют опрокидывающую вибрацию для создания однородной произвольной текстуры.Скорость цикла машины и величина вибрации, как правило, варьируются, что позволяет эффективно обрабатывать различные детали от мелких до крупных.
Взрывной
Пескоструйное оборудование, такое как пескоструйные машины, обычно используется в проектах, требующих однородной матовой текстуры. В процессе пескоструйной обработки (также известной как дробеструйная обработка) песок, стальные дроби, металлические гранулы или другие абразивные материалы наносятся на основу с высокой скоростью. В результате получается гладкая, чистая текстура продукта, особенно при работе с мягкими металлами.
Дробеструйная обработка – это метод дробеструйной обработки, используемый для создания сжимающего напряжения на поверхности металлов с целью повышения сопротивления усталости, сопротивления коррозионному растрескиванию под напряжением, сопротивления истиранию и т.д. стресс, вызванный во время производства. Полировка – это еще один метод модификации поверхности холодной обработки, используемый для создания сжимающего напряжения для сопротивления усталости.
Термическая обработка
Важным этапом во многих операциях по производству металла является термообработка, которая используется для обеспечения желаемых характеристик материала после того, как ему будет придана окончательная форма.Например, после нарезания шестерен их обычно закаляют с помощью индукционного или пламенного нагрева для повышения износостойкости поверхностей зубьев при одновременном повышении прочности нижележащих зубьев. При закалке обычно применяется операция закалки, которая является критическим этапом преобразования зернистой структуры металла. Упрочнение используется на скобах замков, например, для изготовления оболочки, стойкой к механическим воздействиям. Также применяется термическая обработка для снятия любых остаточных напряжений, оставшихся при производстве.Азотирование – это еще один процесс поверхностного упрочнения, который можно проводить при температуре ниже температуры превращения стали, что устраняет необходимость в закалке и любой деформации детали, которая может возникнуть.
Покрытие
Краски на водной и масляной основе используются для недорогой защиты металлов от коррозии. Доступны специальные краски для суровых условий окружающей среды, например, противообрастающие краски для морских применений.
Порошковое покрытие – это декоративная отделка, аналогичная краске, но более прочная.Процесс включает УФ или тепловое отверждение сухого термопластичного или термореактивного полимерного порошка на металле для получения текстурированного, матового или глянцевого покрытия. Это электростатический процесс, при котором заряд, помещенный на подложку, притягивает к ней частицы порошка. Текстурированное порошковое покрытие очень эффективно скрывает дефекты поверхности.
Алюминий часто анодируют, это химическая обработка поверхности для обеспечения коррозионной стойкости, эстетических эффектов или, в случае анодирования с твердым покрытием, большей устойчивости к износу.
Горячее чернение
Машины для горячего чернения наносят тонкий слой черной окиси на поверхность продукта, создавая матово-черный цвет с высокой стойкостью к истиранию. Это высокотемпературный процесс горячей отделки, при котором продукт помещается в серию резервуаров, содержащих очистители, щелочи и охлаждающие жидкости. Горячее чернение чаще всего используется при производстве автомобильных деталей, инструментов и огнестрельного оружия. Воронение – это разновидность черного оксидного покрытия, которое используется для защиты стали от коррозии.
Выбор процесса обработки металла
При выборе техники отделки металла необходимо учитывать несколько факторов. Вот несколько полезных вещей, о которых следует помнить:
- Скорость производства : Как быстро технология позволяет нанести отделку на продукт?
- Экономическая эффективность : Некоторые отделочные машины (например, вибропогружатели) могут быть дорогими, но могут компенсировать свою цену за счет более высокой частоты цикла.
- Твердость металла : более твердые металлы обычно требуют более интенсивных методов отделки, таких как шлифование, или могут потребоваться более жесткие абразивные материалы, чем те, которые используются для более мягких материалов
Сводка
В этой статье представлено краткое обсуждение различных видов обработки металлов.Для получения дополнительной информации о других продуктах обратитесь к другим нашим руководствам или посетите платформу Thomas Supplier Discovery Platform, чтобы найти потенциальные источники поставок или просмотреть подробную информацию о конкретных продуктах.
Прочие изделия из металла
Прочие “виды” изделий
Больше от Custom Manufacturing & Fabricating
Стандарты подготовки поверхности
«Никогда не красить грязную поверхность» – это что-то вроде мантры в промышленных малярных кругах. Без надлежащей подготовки поверхности покрытие не будет правильно прилипать к основанию, и система выйдет из строя.Существующие стандарты, публикуемые и постоянно пересматриваемые независимыми отраслевыми надзорными агентствами, хорошо справляются со стандартизацией результатов подготовки поверхности, но соглашения об именах между агентствами могут сбивать стандарты с толку. Именно это побудило Thomas Industrial Coatings создать исчерпывающее наглядное руководство: упростить понимание стандартов подготовки поверхности.
СтандартыНаиболее общепринятыми стандартами для подрядчиков и организаций являются стандарты подготовки совместных поверхностей NACE International / Общества защитных покрытий (SSPC).Эти стандарты отлично справляются со стандартизацией результатов подготовки поверхности и предоставляют шаблон для соответствия рабочим спецификациям. Тем не менее, эти стандарты могут сбивать с толку, потому что числа, указанные для каждого уровня подготовки поверхности, не всегда коррелируют; более высокие числа не обязательно означают более высокую степень подготовки поверхности, как можно было бы ожидать.
Для большей ясности ниже приводится список кратких объяснений каждого стандарта вместе с наглядной иллюстрацией.
- SSPC-Подготовка поверхности (SP) -1: Очистка растворителем. Этот метод подготовки поверхности предназначен для удаления со стали растворимых веществ. Перед нанесением краски или другого защитного покрытия растворитель используется для удаления всех видимых масел, жиров, грязи, составов для рисования или резки или других растворимых загрязнений. Растворители могут включать пар, эмульгаторы или другие чистящие соединения.
- SSPC-SP-2: Очистка ручным инструментом. Очистка ручным инструментом означает подготовку поверхности, при которой для очистки стальной поверхности используются ручные инструменты без привода.Очистка ручного инструмента предназначена для удаления всей рыхлой прокатной окалины, ржавчины, краски и других загрязнений, которые могут нанести вред нанесению покрытия. Согласно SSPC, «незакрепленные» загрязнения – это те загрязнения, которые нельзя удалить, сняв их тупым шпателем.
- SSPC-SP-3: Очистка электроинструментом. Как и при очистке ручного инструмента, SP-3 – это метод подготовки стальной поверхности, предназначенный для удаления всей рыхлой прокатной окалины, ржавчины, краски и других загрязнений, которые могут нанести вред нанесению покрытия.Как следует из названия Power Tool, SP-3 означает использование электроинструментов для очистки поверхности. Опять же, согласно SSPC, незакрепленные загрязнения – это те загрязнения, которые нельзя удалить, подняв их тупым шпателем.
- NACE № 1 / SSPC-SP-5: Струйная очистка белого металла. Этот стандарт соединений SSPC / NACE описывает очистку стальной поверхности, ранее окрашенной или неокрашенной, до состояния белого металла с помощью абразивно-струйной обработки. Белый металл – это термин, используемый для описания поверхности, которая равномерно свободна от всех посторонних веществ и имеет белый или серый цвет.Согласно SSPC, поверхность, подвергнутая пескоструйной очистке до белого металла, должна, без увеличения, быть свободна от всех видимых масел, смазки, пыли, грязи, прокатной окалины, ржавчины, покрытия, оксидов, продуктов коррозии и других посторонних веществ.
- NACE № 3 / SSPC-SP-6: Промышленная пескоструйная очистка. № 3 / SP-6 – еще один совместный стандарт, описывающий очистку стальной поверхности с помощью абразивно-струйной обработки. Он включает инструкции по применению перед абразивоструйной очисткой, а также по проверке очистки после ее проведения.Как и при струйной очистке белого металла, поверхности, подготовленные в соответствии со стандартом № 3 / SP-6, должны быть, без увеличения, свободными от всех видимых масел, жира, пыли, грязи, прокатной окалины, ржавчины, покрытия, оксидов, продуктов коррозии, и другие посторонние предметы. Допускается случайное окрашивание от предыдущего контакта с этими загрязнителями; однако это только до тех пор, пока загрязнение не составляет более 33 процентов каждой «единицы» площади, как описано в стандарте. Такое окрашивание может принимать форму светлых теней, небольших полос или незначительного изменения цвета, вызванного пятнами ржавчины, прокатной окалины или ранее нанесенным покрытием, согласно SSPC.
- NACE № 4 / SSPC-SP-7: Абразивоструйная очистка щеткой. Этот стандарт устанавливает требования к очистке стальной поверхности, окрашенной или неокрашенной, с использованием абразивно-струйной обработки. Он содержит описания необходимого конечного состояния поверхности, которая подверглась очистке щеткой, а также необходимые методы для проверки конечного состояния актива. При просмотре без увеличения все масло, жир, грязь и пыль должны быть удалены с поверхности. Слабая прокатная окалина, ржавчина и покрытия также должны быть удалены в соответствии с настоящим стандартом, но плотно прилегающая прокатная окалина, ржавчина и покрытия могут остаться.Они считаются плотно прилегающими, если их нельзя удалить, приподняв тупым шпателем.
- NACE No. 2 / SSPC-SP-10: Практически белая пескоструйная очистка. Этот стандарт устанавливает требования к очистке стальной поверхности, окрашенной или неокрашенной, с использованием абразивоструйных средств. Он также включает инструкции по достижению и проверке требуемых по стандарту конечных условий. Как и при промышленной пескоструйной очистке, подготовленная поверхность должна быть очищена, если смотреть без увеличения, от видимых масел, пыли, грязи, жира, прокатной окалины, ржавчины, налета, оксидов, коррозии и других посторонних веществ, за исключением ограниченного количества приемлемое окрашивание.В отличие от промышленной пескоструйной очистки, только пять процентов каждой единицы площади, как определено стандартом, могут иметь окрашивание. Эти пять процентов могут состоять из светлых теней, небольших полос и небольших изменений цвета, которые могут быть результатом воздействия ржавчины, прокатной окалины или предыдущего покрытия.
- SSPC-SP-11: Очистка электроинструментом до чистого металла. Этот стандарт описывает требования к поверхности до голого металла, обеспечивая минимальный профиль поверхности 1 мил (25,4 микрона). Он используется в ситуациях, когда абразивоструйная очистка невозможна или нецелесообразна.В отличие от SP-3, этот стандарт требует создания или сохранения профиля поверхности. В отличие от SP-15, этот стандарт не допускает появления пятен прокатной окалины, ржавчины или краски на поверхности.
- NACE № 8 / SSPC-SP-14: Промышленная пескоструйная очистка. Этот стандарт устанавливает требования к очистке стальной поверхности, окрашенной или неокрашенной, с использованием абразивоструйных средств. Он также включает инструкции по достижению и проверке требуемых по стандарту конечных условий. Как и в случае промышленных абразивоструйных аппаратов и почти белых промышленных абразивов, подготовленная поверхность должна быть очищена при просмотре без увеличения от видимых масел, пыли, грязи, жира, прокатной окалины, ржавчины, налета, окислов, коррозии и других посторонних предметов. имеет значение, за исключением ограниченного количества приемлемого окрашивания.№ 8 / SP-14 отличается от промышленной струйной очистки и почти белой коммерческой струйной очистки в отношении приемлемой площади для остатков остатков и поверхностных пятен. Этот стандарт позволяет плотно прилегающей прокатной окалине, ржавчине и покрытиям, а также поверхностным пятнам оставаться на 10 процентах каждой единицы площади, как описано в стандарте. Пятна на поверхности могут состоять из светлых теней, небольших полос и незначительных изменений цвета, которые могут быть результатом воздействия ржавчины, прокатной окалины или предыдущего покрытия.
- SSPC-SP-15: Очистка электроинструмента промышленного уровня.Как и в SP-11, этот стандарт описывает требования к поверхности до чистого металла, обеспечивая при этом минимальный профиль поверхности 1 мил (25,4 микрона). В отличие от SP-11, SP-15 позволяет случайному окрашиванию оставаться на субстрате.
- SSPC-SP-16: Абразивно-струйная очистка цветных металлов. Этот стандарт регулирует подготовку поверхности цветных металлов перед нанесением защитного покрытия. Он используется при добавлении профиля поверхности к нержавеющей стали, оцинкованной стали, меди и другим металлам, не относящимся к углеродистой стали.Он требует минимального профиля поверхности 0,75 мил (19,0 микрон) и отсутствия на поверхности неплотного покрытия и других загрязнений, что подтверждается визуальным осмотром.
Каждый подрядчик по нанесению покрытий должен соответствующим образом подготовить основание, будь то работа по нанесению покрытия на автомобильный мост, облицовке стального резервуара или защите пола пивоварни. Поэтому полезно знать, как правильно использовать эти стандарты. Надеемся, что с небольшой визуальной помощью другие подрядчики смогут успешно выполнить свои следующие работы по нанесению покрытий.
Об авторе
Джош Томас начал свою карьеру в Thomas Industrial Coatings в 1998 году, взяв перерыв в семейном бизнесе, чтобы получить степень магистра делового администрирования в Белларминском университете. Он вернулся на полную ставку в 2011 году, чтобы завершить проект моста Хьюи П. Лонг в Новом Орлеане, штат Луизиана. Томас в настоящее время является операционным директором, где ему поручено завершить проекты безопасно, вовремя и в рамках бюджета, поддерживая команду проекта. менеджеры в их повседневной управленческой деятельности.За дополнительной информацией обращайтесь: Thomas Industrial Coatings, www.thomasindcoatings.com
Эта статья переиздана с разрешения CoatingsPro. Журнал .
Системы очистки | Продукция Отделочные
Когда думаешь об уборке, в первую очередь на ум приходят мыло и вода. На протяжении всего детства вы видели, как одежду и посуду мыли водой с мылом. Это было нормально. Вода была чудодейственным эликсиром, растворяющим все, или так? Не все отходы или загрязнения можно удалить простой водой.
Вы узнали, что небольшая очистка (механическая энергия) вместе с мылом и водой улучшают ваши шансы на очистку. Использование устройства передачи энергии, такого как ткань, щетка или проволочная сетка, было особенно полезно для удаления пятен от грязи и травы, которые вы заработали в этом сенсорном футбольном матче.
Однако, если вы говорите об отходах или загрязняющих веществах в порах материала, было мало надежды на удаление материала, если только поверхность материала не была также слегка удалена или модифицирована.Жидкая обработка поверхности может лишь на многое; тогда как механические передаточные устройства, оборудование или системы имеют дело в первую очередь с профилями поверхности сырья.
Большинство технологий очистки используют энергию и молекулы разной плотности, характеристик и поведения, чтобы воздействовать на поверхность с другой плотностью. Оба влияют на общую чистоту поверхности обоих элементов, хотя желательным результатом является изменение только одного элемента. Результатом всех технологий, использующих этот принцип, является процесс очистки, который часто называют механической обработкой поверхности при использовании твердых частиц.
Из-за массы среды и способа использования энергетических сил механический процесс обычно удаляет больше материала быстрее и оказывает большее физическое влияние на размеры детали, чем жидкие химические процессы, даже с использованием электрического тока. Эти системы настолько агрессивны, что их обычно считают системами удаления заусенцев или полировки, а не системами очистки.
Сегодня проблемы и методы промышленной очистки более сложны, чем когда-либо. Сначала нужно разобраться во всех вариантах очистки и отделки поверхности.Обработка поверхности – это результат рабочих процессов и / или окончательный внешний вид детали. Подготовка поверхности – это окончательный внешний вид детали перед нанесением окончательного покрытия.
Несмотря на то, что между этими двумя словами существует различие, обычное использование этих слов и фактические методы обработки сбивают их с толку. Каким бы ни был внешний вид, покрытия необходимы для защиты отделки от окисления. Подготовка поверхности – это окончательный внешний вид детали перед другим процессом герметизации поверхности материалов.Подготовка поверхности – это намного более грубая обработка, чем обработка поверхности.
Чтобы определить, какой тип отделки поверхности требуется, инженеры должны спланировать, какой тип обработки материала необходим для того, чтобы продукт работал и соответствовал определенным условиям. Инженер не только должен указать материал, размер и размеры детали, он также должен указать подгонку, форму и функцию. Инженер должен понимать, что размеры обрабатываемой детали могут отличаться от окончательных размеров из-за обработки поверхности, необходимой для очистки и защиты детали.
По мере того, как детали становятся меньше или когда производительность и надежность становятся более важными, необходимо все больше и больше думать о подготовке или модификации поверхности с учетом возможных допусков на размеры. Существует три основных варианта отделки деталей: 1) Подготовка поверхности для нанесения тяжелых или толстых защитных покрытий, таких как краска или пленка на пластиковой основе; 2) Подготовка поверхности для тонкопленочных химических покрытий или обработок; и 3) изменение пористости поверхности для эстетического внешнего вида или полировки.
Варианты отделки поверхности
Тип I: Подготовка поверхности для толстых защитных покрытий
- Обработка поверхности будет самой грубой из всех возможных, а готовая деталь будет превышать окончательные размеры детали из-за покрытия.
- Поверхность должна быть как можно более шероховатой, чтобы увеличить площадь поверхности для обеспечения хороших адгезионных свойств и / или характеристик износостойкости покрытия. RMS 35 или выше.
- Профиль шероховатости отделки поверхности не должен превышать высоту конечной пленки или толщину покрытия.
- Поверхность должна быть как можно более чистой от мусора, масел и окисления. Поэтому чистку следует проводить непосредственно перед нанесением покрытия, но детали должны быть сухими.
Тип II: Подготовка поверхности для тонкопленочных покрытий
- Обработка поверхности обычно требует вторичной модификации, и это будут окончательные размеры детали. Это может быть положительной стороной допуска в зависимости от пленки или покрытия.
- Обработка поверхности требует сглаживания или модификации детали для улучшения однородности профиля поверхности окончательно обработанной детали.Нормальный диапазон RMS составляет от 12 до 20.
- Профиль шероховатости поверхности не так важен для большинства химических обработок; однако чем ровнее поверхность, тем равномернее обработка.
Тип III: полированная поверхность
- Обработка поверхности будет самой гладкой из всех возможных и близкой к окончательным размерам детали, но с отрицательной стороной допуска. Если все же требуется тонкопленочное покрытие, размеры могут превышать конечный размер детали.
- Иногда этот процесс считается не подготовкой поверхности, а процедурой модификации или процессом удаления материала. Готовая деталь будет иметь текстурированный узор или зеркальную отделку в диапазоне RMS от 2 до 18.
- Обработка поверхности – это в основном вопрос пористости; тем не менее, покрытия все же можно наносить из соображений защиты.
Все механические абразивные системы представляют собой процессы удаления материала, даже системы полировки или полировки. Единственное различие между ними заключается в использовании размера абразива, формы и характеристик частиц, а также в том, как к ним прикладывается энергия.При съеме тяжелых материалов общее практическое правило: чем крупнее и тверже абразив, тем больше материала удаляется за кратчайшее время. Однако он также оставляет самую грубую поверхность. Естественно, чем мельче абразив, тем мягче и ровнее поверхность.
Абразивные материалы, используемые для модификации поверхности, обычно выбираются по твердости и / или экономичности; поэтому практический опыт – лучший судья для определения использования медиа.
Чем тверже абразивная частица, тем больше материала удаляется.Кроме того, большинство твердых материалов больше царапают, чем сглаживают или полируют. По мере разрушения твердых материалов их края скругляются, и они становятся более подвижными и лучше подходят для полировки в свободном подвижном состоянии. Следовательно, для целей очистки необходимо определить требования к подготовке поверхности перед выбором системы удаления механических абразивных частиц.
Минеральная твердость – важный фактор, влияющий на скорость съема материала и время обработки. Однако это не единственный фактор. Также важны размер и рыхлость.Чем больше размер абразивных частиц, тем больше выделяется кинетическая энергия. Помимо фактического высвобождения энергии в виде тепла, существует еще и движение. Смещение и сила усиливаются при быстром движении оставшегося материала, создавая огромное давление на все, с чем они контактируют.
Из-за различного качества материалов и сред абразивные системы отделки иногда кажутся ненаучными, но между ними существует взаимосвязь. Большинство знаний об абразивных материалах, удалении заусенцев и финишной обработке не преподаются, а развиваются на основе опыта.
Чем тверже минеральный элемент, тем сильнее молекулярная связь. Однако связь или кристаллическая структура не связаны с силами кинетической энергии. Обычно это означает, что по мере разрушения абразивных частиц им требуется большая внешняя энергия или сила для выполнения требуемого уровня очистки. Это как истинное, так и ложное утверждение.
Поскольку частицы становятся меньше, их объем и вес на одну частицу меньше, но, следовательно, больше поверхностный контакт и трение. Это снижает количество энергии и размер удаляемого материала.Сложности заключаются в нагрузочных характеристиках процесса удаления материала.
Из-за удельного веса, сопротивления, плотности и молекулярной структуры деталь обычно больше, чем абразивная среда, и, следовательно, более устойчива к изменениям. Большая масса всегда сначала влияет на меньшую массу. Сначала во время очистки, удаления заусенцев или модификации поверхности удаляются более крупные, меньшие и более тяжелые неровности. Затем, когда поверхность детали становится более гладкой, размер снимаемого материала становится все меньше и меньше.Это создает впечатление незначительной модификации поверхности или ее отсутствия. На самом деле скорость съема материала остается довольно постоянной, но физическое восприятие обманчиво. Если исходить строго по весу снятого материала, это ложное утверждение.
Все абразивные среды будут работать до определенного момента, а затем их эффективность будет постепенно снижаться в зависимости от веса, массы и кинетической энергии. Пока существует передаточный механизм для приложения давления как к детали, так и к абразиву, удаление материала будет происходить.Однако, поскольку мы говорим о нормальных условиях работы и времени обработки, точка эффективности достигается задолго до того, как истечет срок службы носителя. В какой-то момент для выполнения более тонкой или гладкой модификации поверхности требуются большая энергия силы или давления и меньшего размера.
Когда характеристики абразивных частиц быстро снижаются, следует добавлять новые или другие абразивные частицы или абразивные среды. Больше энергии или давления можно приложить к среде или абразиву только до той точки, где эта энергия может быть передана по отношению к детали.
За исключением плоской гладкой поверхности, неровности всегда будут в некоторой степени из-за пористости. Однако размер и / или количество неровностей можно уменьшить, и они будут постоянно уменьшаться до точки, при которой размер абразивной среды не будет работать эффективно.
Вес и масса являются наиболее важными факторами для удаления большого количества неровностей поверхности. Однако наступает момент, когда вес и масса становятся помехой. В какой-то момент, который зависит от характеристик используемой абразивной среды, скорость разрушения или рыхлость среды становится более важным фактором, чем вес и масса.Технически вы не можете получить более гладкую поверхность, чем используемая вами абразивная частица, потому что частица фактически будет давать неровности, соответствующие физическому размеру используемых абразивных частиц.
Единственный способ обойти это правило размера – разрешить абразивному материалу плавать или поддаваться в зависимости от давления, прилагаемого как к абразиву, так и к обрабатываемому материалу. Однако, поскольку большинство абразивов закреплены или связаны с жесткой поверхностью, их способность плавать не будет, если вы не добавите в процесс воздух или воду.С другой стороны, если абразивы могут свободно плавать, это может не дать однородной поверхности. Из-за этого контактное давление важно для скорости съема материала и обработки поверхности, где важно время. То, как энергия применяется и передается абразивным частицам, также важно для процессов удаления материала.
Для получения более тонкого материала или обработки кромок требуются меньшие размеры зерна, более длительные циклы и более агрессивные методы обработки. Самый быстрый способ получить гладкую полированную поверхность – сначала подготовить или усовершенствовать края или элементы поверхности с помощью крупнозернистого или более крупного материала, а затем обработать эту же область с последовательно меньшим размером зерна, используя несколько этапов.Эта пошаговая процедура – медленный процесс, но он также быстрее, чем использование небольшого абразивного материала только одного размера для выполнения той же задачи чистовой обработки. Опять же, необходимо учитывать время и эффективность.
Абразивные частицы должны измениться или разрушиться при удалении заусенцев, мусора или неровностей поверхности. Не разрушаясь, избыточная энергия не передается в среду, что может вызвать состояние, напоминающее апельсиновую корку. Это также означает, что поверхность материала может стать более плотной в месте удара, что приведет к возникновению состояния, называемого деформационным упрочнением, которое является аналогичным эффектом, возникающим при термообработке материалов.В абразивных процессах частица может деформировать поверхность материала, создавая визуальные или микроскопические вмятины, которые делают поверхность более шероховатой, чем она была вначале. Это обычное состояние возникает при использовании систем абразивоструйной обработки.
Существует пять основных систем оборудования, обеспечивающих чистовую обработку поверхности или удаление материала, шесть, если считать ручные операции. Из первых пяти три являются механическими системами, в которых используются абразивные материалы, а в двух используются жидкости и температура для очистки деталей.
Используемое оборудование во многом зависит от того, какое оборудование уже имеется в доме.Однако есть не только варианты отделки поверхности, но и варианты оснащения. После определения требований к чистоте поверхности необходимо выбрать оборудование и метод очистки или подготовки поверхности. То, как оборудование использует энергию, имеет решающее значение для времени, качества и экономии в любом процессе. До сих пор выбор системы обычно зависел от внутреннего оборудования и / или знаний систем самоучки.
Ниже приводится система классификации, разработанная для всех систем удаления заусенцев или материала.
Классификация оборудования
Тип 0: Эта система предназначена только для ручной обработки деталей. Энергия направлена вниз взад-вперед или по кругу с абразивной средой. Чем больше направленная вниз сила, тем больше истирание.
Тип 1: Эта система используется на относительно плоских материалах, где энергетические силы направлены вниз и параллельно обрабатываемому материалу посредством колеса, диска или ремня. Результатом действия является горизонтальное вытирание и сглаживание поверхностных элементов.
Тип 2: Эта система используется в основном для подготовки поверхности под толстые покрытия. При этом используется метод абразивно-струйной обработки, при котором сила энергии передается твердой частице, которая направлена перпендикулярно или вниз под небольшим углом к заготовке. Результатом действия является шероховатая текстурированная поверхность.
Тип 3: Данная система используется в оборудовании массового отделочного типа. При этом используются абразивные частицы или формы преформ в произвольной комбинации или смешанные силы энергии или рисунки, которые возникают во всех направлениях относительно детали.Результатом являются модифицированные смешанные поверхности и равномерно обработанные детали.
Тип 4: Эта система электрополировки используется в гальванической промышленности. Это в первую очередь электрический ток, проходящий через жидкую среду. В результате получаются как поверхностные, так и подповерхностные молекулярные изменения деталей.
Тип 5: В данной системе используется метод высокотемпературного нагрева на воздушной основе. Это система избирательного удаления материала, которая работает в первую очередь с неровностями поверхности или заусенцами.В результате этого процесса тонкие выступы на поверхности испаряются и плавятся.
Классификация заусенцев
Класс 0: Заусенцев или неровностей материала не существует, но требуется модификация поверхности.
Класс 1: Заусенцы – это острые края, которые со временем и / или вибрацией могут порезать пальцы, порезать проволоку или трубку.
Класс 2: Заусенцы – это тонкие неровности, которые можно частично удалить ногтем. Толщина материала примерно 0-0.01 дюйм.
Класс 3: Заусенцы или неровности материала требуют большего давления для удаления, чем при использовании одной рукой. Толщина материала составляет приблизительно 0,01 – 0,02 дюйма.
Класс 4: Заусенцы или неровности материала требуют большого давления и силы на материал и деталь. Толщина материала больше 0,02 дюйма.
Расположение заусенцев
0 Расположение: Только для модификации поверхности.
1 Расположение: Для легкого доступа к внешним размерам.
2 Расположение: Для труднодоступных внутренних или внутренних размеров.
3 Расположение: Для всех заусенцев, внутренних и внешних, а также поверхностных.
Размер детали также является важным фактором для определения оборудования, процессов, темпов производства и контроля отчетности деталей. Почти каждая классифицированная до сих пор система удаления материала имеет альтернативную меньшую систему. Один размер не подходит для всех. Отделочное оборудование построено так, чтобы отражать детали разного размера и объема; поэтому выбор машины обычно определяется диапазоном или сочетанием размеров деталей.В большинстве систем обработки есть четыре размера или диапазона деталей, которые мы можем классифицировать и соотнести с системой классификации оборудования.