Классификация по назначению стали – Классификация сталей: по назначению, составу, применению
alexxlab | 19.11.2019 | 0 | Разное
Лекция 25
34
Классификация сталей
Стали и чугуны являются сплавами на основе железа. Технически чистое железо содержит углерода не более 0,04 %. Углеродистые стали относятся к сплавам системы Fe–Fe3C. По составу стали располагаются на диаграмме до точки Е, с концентрацией 2,14 % С. Промышленные углеродистые стали относятся к многокомпонентным системам, т.к. кроме углерода они содержат примеси других элементов. Содержание отдельных примесей может быть соизмеримо с содержанием углерода, однако углерод оказывает основное влияние на формирование структуры и на свойства сталей, поэтому анализ структуры промышленных углеродистых сталей можно проводить по диаграмме состояния Fe–Fe3C.
Промышленные нелегированные чугуны (серые, высокопрочные, ковкие, с вермикулярным графитом) относятся к высокоуглеродистым сплавам на основе системы Fe–C–Si, в которых углерода содержится более 2,14 %.
Кристаллизация таких чугунов реализуется по стабильной Fe–C–Si или метастабильной Fe–Fe3C–Si диаграмме, в зависимости от состава и условий охлаждения. Белые чугуны кристаллизуются в условиях ускоренного охлаждения, для формирования их структуры можно использовать метастабильную диаграмму Fe–Fe3C, они являются исходным материалом для получения ковкого чугуна.
Стали относятся к сплавам на основе железа с углеродом (углеродистые стали). Стали, дополнительно содержащие хром, марганец, кремний, никель, молибден, и другие элементы, называют легированными сталями.
Стали являются основными и наиболее распространенными сплавами для изготовления деталей конструкций, инструмента и изделий специального назначения. Сплавы на основе железа имеют хорошее сочетание высокой прочности, твердости, пластичности, вязкости и технологичности.
По химическому составу стали классифицируются на углеродистые и легированные.
По назначению стали подразделяются на конструкционные, инструментальные и стали специального назначения.
По способу производства изделий стали классифицируются на деформируемые и литейные.
По металлургическому качеству в зависимости от содержания вредных примесей стали подразделяются на категории: стали обыкновенного качества, (ГОСТ 380-94), качественные (ГОСТ 1050-88 и др.), высококачественные, особо высококачественные.
К наиболее вредным примесям сталей (табл. 4.10) относятся сера и фосфор. Сера приводит к красноломкости стали, т.е. к хрупкости при горячей обработке давлением. Марганец, который вводят в сталь при раскислении, устраняет вредное влияние серы. Фосфор вызывает хладноломкость, т.е. охрупчивания при низких температурах.
По способу раскисления при выплавке стали классифицируются на кипящие, спокойные и полуспокойные.
Раскислением называется процесс восстановления железа из FeO, который протекает по следующим химическим реакциям:
FeO + Mn = Fe + MnO
2FeO + Si = 2Fe + SiO2
3FeO + 2Al = 3Fe + Al2O3
Кремний и марганец вводят в виде ферросплавов, алюминий – в чистом виде. Кипящие стали раскисляют только ферромарганцем. В таких сталях остается растворенный FeO, и при кристаллизации продолжается процесс кипения по реакции
FeO + C = Fe + CO
Газовые пузыри остаются в теле слитка и завариваются при последующей прокатке. Кипящая сталь дает наиболее высокий выход годного металла.
Таблица 4.10Массовая доля серы и фосфора в углеродистых и легированных сталях
Спокойную сталь раскисляют марганцем, кремнием, алюминием; при этом в металле достаточно полно удаляется растворенный кислород. При кристаллизации процесс кипения прекращается, сталь успокаивается.
Углеродистые стали относятся к железоуглеродистым сплавам с содержанием углерода от 0,05 до 1,35 % С. Углеродистые конструкционные стали содержат до 0,65 % С, инструментальные – более 0,65 % С.
Кроме вышеуказанной классификации, углеродистые стали подразделяются по содержанию углерода, по структуре, по назначению.
По содержанию углерода углеродистые стали делятся на низкоуглеродистые до 0,25%С, среднеуглеродистые – 0,3–0,5%С, высокоуглеродистые – > 0,50 % С.
По структуре стали подразделяются на доэвтектоидные – до 0,8 % С, эвтектоидные – 0,8 % С, заэвтектоидные – более 0,8 % С.
Углеродистые стали, как наиболее дешевые, технологичные и имеющие достаточно высокий комплекс механических свойств, применяются для металлоконструкций общего назначения, используются в строительных конструкциях, для изготовления деталей в машиностроении и т.д.
Углеродистые стали по назначению подразделяются на стали общего и специального применения. К сталям специального назначения относятся автоматные, котельные, строительные, стали для глубокой вытяжки.
Влияние углерода, легирующих элементов, примесей на свойства сталей
Углерод является важнейшим элементом, определяющим структуру и свойства углеродистой стали. Даже при малом изменении содержания углерод оказывает заметное влияние на свойства стали. С увеличением содержания углерода в структуре стали увеличивается количество цементита. При содержании до 0,8 % С сталь состоит из феррита и перлита, при содержании более 0,8 % С в структуре стали кроме перлита появляется структурно свободный вторичный цементит. Феррит имеет низкую прочность, но сравнительно пластичен. Цементит характеризуется высокой твердостью, но хрупок. Поэтому с ростом содержания углерода увеличивается твердость и прочность, однако уменьшается вязкость и пластичность стали. Рост прочности происходит при содержании углерода в стали до 0,8–1,0 %. При увеличении содержании углерода в стали более 0,8 % уменьшается не только пластичность, но и прочность стали. Это связано с образованием сетки хрупкого цементита вокруг перлитных колоний, легко разрушающейся при нагружении. По этой причине заэвтектоидные стали подвергают специальному отжигу, в результате которого получают структуру зернистого перлита.
Углерод оказывает также существенное влияние на технологические свойства стали – свариваемость, обрабатываемость резанием и давлением.
Низкоуглеродистые стали хорошо свариваются и имеют высокую обрабатываемость давлением.
Постоянными примесями в углеродистых сталях являются марганец, кремний, сера, фосфор, а также скрытые примеси – газы: кислород, азот, водород. Примесями могут считаться и такие элементы, как медь, никель, хром (если они не предусматриваются марочным составом стали и их содержание ограничивается по верхнему пределу с указанием «не более»). К полезным примесям (технологическим добавкам) в углеродистых сталях относятся марганец, кремний, хром; их содержание обычно не превышает одного процента.
Марганец и кремний вводят в сталь при раскислении, они упрочняют железо. Марганец увеличивает прокаливаемость (возможную глубину закаленного слоя) сталей, а также уменьшает вредное влияние серы. Содержание вредных примесей – серы и фосфора регламентируется стандартами. Основным источником серы и фосфора в стали является исходное сырье – чугун. Сера снижает пластичность и вязкость стали, а также приводит к красноломкости стали при прокатке и ковке. Она образует с железом соединение FeS – сульфид железа. При нагреве стальных заготовок до температуры горячей деформации включения FeS вызывают в стали хрупкость, а в результате оплавления при деформации образуют надрывы и трещины. Фосфор, растворяясь в железе, уменьшает его пластичность. Кислород и азот мало растворимы в феррите. Они загрязняют сталь хрупкими неметаллическими включениями, снижают вязкость и пластичность стали. Повышенное содержание водорода охрупчивает сталь и приводит к образованию внутренних трещин – флокенов.
Углеродистые стали
Классификация углеродистых сталей. Углеродистыми сталями называют железоуглеродистые сплавы с содержанием углерода от 0,05 до 1,35 % углерода. Углеродистые стали подразделяются на конструкционные и инструментальные. Конструкционные стали содержат до 0,65%С, инструментальные – более 0,65 % С.
Кроме вышеуказанной классификации, углеродистые стали подразделяются по содержанию углерода, по структуре, по назначению, качеству, способу производства.
По содержанию углерода углеродистые стали делятся на низкоуглеродистые (до 0,25 % С), среднеуглеродистые (от 0,3 до 0,5 % С), высокоуглеродистые (более 0,50 % С).
По структуре стали подразделяются на доэвтектоидные при содержании углерода до 0,8 % С, эвтектоидные – 0,8 % С и заэвтектоидные – более 0,8 % С.
Углеродистые стали, как наиболее дешевые, технологичные и имеющие достаточно высокий комплекс механических свойств, применяются для металлоконструкций общего назначения, используются в строительных конструкциях, для изготовления деталей в машиностроении и т.д. Стали углеродистые поставляются по ГОСТ 380-94 (стали обыкновенного качества), ГОСТ 1050-88 (прокат из углеродистой качественной конструкционной стали).
По назначению стали подразделяются на стали общего и специального применения. К сталям специального назначения относятся автоматные, котельные, строительные, стали для глубокой вытяжки.
По качеству стали подразделяют на стали обыкновенного качества, качественные и высококачественные.
По способу производства стали подразделяют на деформируемые стали и на литейные.
Согласно диаграмме железо–углерод, к сталям относят сплавы железа с содержанием углерода, менее 2,14 % (все сплавы левее точки Е). Углерод является важнейшим элементом, определяющим структуру и свойства углеродистой стали. Даже при малом изменении содержания углерод оказывает заметное влияние на свойства стали. С ростом содержания углерода увеличивается твердость и прочность, однако уменьшается вязкость и пластичность стали.
Рост прочности происходит при содержании углерода в стали до 0,8 –1,0 %. При увеличении содержании углерода в стали более 0,8 % уменьшается не только пластичность, но и прочность стали. Это связано с образованием сетки хрупкого цементита вокруг перлитных колоний, легко разрушающейся при нагружении.
Углерод оказывает также существенное влияние на технологические свойства стали – свариваемость, обрабатываемость резанием и давлением.
Низкоуглеродистые стали хорошо свариваются и имеют высокую обрабатываемость давлением.
Кроме железа и углерода (основных компонентов), в сталях содержатся технологические добавки (марганец, кремний) и примеси, главными из которых, наиболее вредными, являются сера и фосфор.
Сера и фосфор – основные вредные примеси в сталях. Массовая доля серы в стали всех марок по ГОСТ 380-94, кроме Ст0, должна быть не более 0,050 %, фосфора – не более 0,040 %, в стали марки Ст0: серы – не более 0,060 %, фосфора – не более 0,070 %. Кроме того, вредными примесями в сталях являются кислород, водород и азот. Их присутствие вызывает понижение пластичности.
Кислород и азот мало растворимы в феррите. Они загрязняют сталь хрупкими неметаллическими включениями, снижают вязкость и пластичность стали. Повышенное содержание водорода охрупчивает сталь и приводит к образованию внутренних трещин – флокенов.
Деформируемые углеродистые стали. Деформируемые углеродистые стали поставляются металлургическими заводами в горячекатаном состоянии без дополнительной термической обработки, или после термического упрочнения. Из таких сталей производят листы, полосы, прутки, швеллерные и двутавровые прокатанные профили, то есть деформируемые полуфабрикаты.
Маркировка и технические условия деформируемых углеродистых конструкционных и инструментальных сталей обыкновенного качества, а также качественных и высококачественных определены, соответственно, в ГОСТ 380-94, ГОСТ 1050-88, ГОСТ 1435-90.
Углеродистые стали обыкновенного качества. Конструкционные стали обыкновенного качества, благодаря их технологическим свойствам, доступности и возможности получения необходимого комплекса свойств, используются при изготовлении металлоконструкций массового производства, а также слабонагруженных деталей машин и приборов.
Углеродистые стали по ГОСТ 380-94 применяют для изготовления проката горячекатаного: сортового, фасонного, толстолистового, тонколистового, широкополосного и холоднокатаного тонколистового, а также слитков, блюмсов, слябов, сутунки, заготовок катаной и непрерывнолитой, труб, поковок и штамповок, ленты, проволоки, метизов и др.
Углеродистые горячекатаные стали, обыкновенного качества по ГОСТ 380-94 «Сталь углеродистая обыкновенного качества» изготовляют следующих марок: Ст0, Ст1кп, Ст1пс, Ст2кп, Ст2пс, Ст3кп, Ст3пс, Ст3сп, Ст3Гпс, Ст3Гсп, Ст4кп, Ст4пс, Ст4сп, Ст5пс, Ст5сп, Ст5Гпс, Ст6пс, Ст6сп (табл. 4.14).
Таблица 4.14
Марки и химический состав сталей углеродистых обыкновенного качества по ГОСТ 380-94
Буквы Ст обозначают «Сталь», цифры – условный номер марки в зависимости от химического состав стали, буквы «кп» – кипящая, «пс» – полуспокойная, «сп» – спокойная – способ раскисления стали. Массовая доля вредных примесей в стали всех марок, кроме Ст0, должна быть не более 0,050 %, фосфора – не более 0,040 %, в стали марки Ст0 серы – не более 0,060 %, фосфора – не более 0,070 %. Массовая доля углерода в сталях колеблется от 0,06 до 0,49 %, массовая доля марганца – от 0,25 до 0,80 %. Полуспокойные и спокойные стали могут содержать повышенное количество марганца (до 1,20 %), тогда в обозначении марок добавляют букву «Г», например, Ст5Гпс. В кипящих сталях массовая доля кремния составляет не более 0,05 %, в полуспокойных – от 0,05 до 0,15 %, в спокойных – от 0,15 до 0,3 %.
В сталях допускается повышенное содержание вредных примесей, газонасыщенность и загрязненность неметаллическими включениями, поэтому они относятся к наиболее дешевым сталям.
Кипящие стали отличаются от спокойных и полуспокойных более низкой ударной вязкостью. Порог хладноломкости (температура перехода стали из вязкого состояния в хрупкое) у кипящей стали на 30–40 градусов выше, чем у спокойной. Для ответственных конструкций лучше всего использовать спокойные стали. Однако кипящие стали вследствие низкого содержания кремния имеют невысокий уровень предела текучести и упругости. Этим объясняется высокая способность кипящей стали к вытяжке при деформации.
Недостатком при использовании сталей обыкновенного качества является малая прочность и малая хладностойкость.
Стали обыкновенного качества Ст2пс, Ст2кп, Ст3кп применяются для неответственных, малонагруженных элементов сварных конструкций. Стали Ст4пс, Ст5сп используются для изготовления деталей клепаных конструкций, болтов, гаек, звездочек, рычагов и других изделий.
Углеродистые качественные конструкционные стали. Стандарт ГОСТ 1050-88 «Прокат сортовой, калиброванный, со специальной отделкой поверхности из углеродистой качественной конструкционной стали» устанавливает технические условия для горячекатаного и кованого сортового проката из сталей марок 05кп, 08кп, 08пс, 08, 10кп, 10пс, 10, 11кп, 15кп, 15пс, 15, 18кп, 20кп, 20пс, 20, 25, 30, 35, 40, 45, 50, 55, 58 (55пп), 60 диаметром или толщиной до 250 мм. Качественные углеродистые стали, по ГОСТ 1050-88 маркируются буквами и цифрами. Двузначные числа показывают содержание углерода в сотых долях процента. Последующее буквенное обозначение указывает на степень раскисления: с – спокойная сталь, пс – полуспокойная сталь, кп – кипящая сталь. При отсутствии буквенного обозначения сталь относят к спокойной стали. Содержание углерода в конструкционных углеродистых сталях составляет от 0,05 до 0,65 %, марганца – от 0,25 до 0,80 %, кремния – от 0,03 до 0,37 % в зависимости от степени раскисления и содержания углерода. По содержанию углерода стали 05кп, 08, 08кп, 10, 15, 20, 25 относятся к низкоуглеродистым сталям, 30, 35, 40, 45, 50 – к среднеуглеродистым, 55, 60 – к высокоуглеродистым.
Главное преимущество сталей качественных по ГОСТ 1050-88 – более низкое содержание серы (не более 0,035 %) и фосфора (не более 0,040 %).
Содержание примесей в этих сталях меньше, чем в сталях обыкновенного качества. Массовая доля серы в сталях должна быть не более 0,040 %, фосфора – не более 0,035 %, исключая марки 11кп и 18кп.
Механические свойства проката из углеродистой качественной конструкционной стали по ГОСТ 1050-88 приведены в табл. 4.15. В соответствии с маркой стали увеличение содержания углерода приводит к росту прочности (σв и σт) и уменьшению пластичности (δ и Ψ).
Таблица 4.15
Механические свойства проката из сталей по ГОСТ 1050-88
Кроме содержания углерода, на уровень механических свойств оказывает большое влияние термическая обработка. Прокат поставляется в отожженном, высокоотпущенном, нормализованном, улучшенном состояниях.
Низкоуглеродистые кипящие стали характеризуются низким пределом текучести, т.к. практически не содержат кремния. Низкоуглеродистые стали типа 05кп, 08, 08кп, 10кп, 10 используются без термической обработки, они хорошо штампуются в отожженном состоянии и применяются в автомобилестроении для изготовления изделий сложной формы: крылья, двери, капот, не несущих деталей кузова.
Стали качественные по ГОСТ 1050-88 предназначены для изготовления широкой номенклатуры изделий, полуфабрикатов, металлоконструкций в строительстве, машиностроении и других отраслях промышленности.
Стали 15, 20, 25 – цементуемые. Данные стали применяют для изделий, работающих в условиях повышенного износа и динамических нагрузок, но не испытывающих значительных напряжений. Из цементуемых сталей 15кп, 20, 25, 20кп изготавливают болты, винты, фланцы, рычаги, шпиндели, клапаны холодильных аппаратов, змеевики и другие детали, работающие при температурах от –40 до +125 °С.
Стали от 30 до 60 – улучшаемые. Детали из них подвергаются закалке с высоким отпуском, что обеспечивает им высокий комплекс механических свойств. Они не склонны к отпускной хрупкости, дешевы, однако обладают низкой прокаливаемостью. Критический диаметр, при котором обеспечивается сквозная прокаливаемость, не более 12 мм. Улучшаемые стали 30, 35, 40, 45 используются для изготовления деталей средних размеров несложной конфигурации, к которым предъявляются требования повышенной прочности: ролики, валики, втулки, коленчатые валы, звездочки, оси, шайбы, шатуны, зубчатые колеса, болты и др.
Стали с содержанием углерода более 0,6 % (60, 65, 70, 75, 80), а также стали такого же класса, но дополнительно содержащие повышенное количество кремния или марганца (65Г, 60С2, 70С3), применяются для изготовления рессор и пружин. При этом такие стали подвергаются термической обработке, заключающейся в закалке и среднетемпературном отпуске, после которой пружины и рессоры приобретают высокие упругие характеристики механических свойств и большой предел выносливости. Высокоуглеродистые стали применяют после нормализации, закалки, отпуска или поверхностного упрочнения. Они обладают высокой прочностью и износостойкостью, а также высоким пределом упругости.
studfiles.net
Классификация сталей по назначению и применению
По назначению и применению сталь подразделяют на:
конструкционные (общего и специального назначения и с особыми свойствами) и
инструментальные.
Конструкционные стали
В конструкционных сталях выделяют строительные и машиностроительные низколегированные стали, а также улучшаемые, цементируемые стали и стали повышенной обрабатываемости резанием (автоматные стали). К конструкционным сталям специального назначения и сталям с особыми свойствами относятся шарикоподшипниковые, рессорно-пружинные, высокопрочные, коррозионно-стойкие, жаростойкие и жаропрочные, сварочные и наплавочные стали, стали с особыми магнитными, электрическими и тепловыми свойствами, котельные, корпусные стали для судостроения и прочие.
Инструментальные стали
Инструментальные стали предназначены для изготовления инструментов, применяемых в процессе металлообработки, а также для измерений. Эти материалы подразделяются на инструментальные стали, твердые сплавы и особо твердые материалы. По назначению инструментальные материалы классифицируются на материалы для режущего, штампового и измерительного инструментов.
Эти стали используются для изготовления инструментов, подвергаемых поверхностной (местной) закалке: пилы, зубила, штемпели, ножи для холодной и горячей резки, обрезные матрицы и пуансоны и т. п. Некоторые стали имеют специальное применение: сталь 13Х предназначена главным образом для бритвенных ножей и лезвий, хирургического и гравировального инструмента; сталь В2Ф предназначена для ленточных пил и ножовочных полотен для резки сталей средней твердости, по работоспособности превосходящая стали типа 9ХФ в 1,5–2 раза. Сталь ХВ4Ф отличается особо высокой твердостью и износостойкостью благодаря присутствию W6C, который не растворяется при температуре закалки. Эту сталь называют алмазной и из неё изготовляют резцы и фрезы для обработки с небольшими скоростями материалов с высокой поверхностной твердостью.
Список используемой литературы:
Арзамасов Б.Н. Материаловедение. М.: Изд-во МГТУ им. Н. Э. Баумана, 2003
Байер B.E., Архитектурное материаловедение. Архитектура-С, 2005
Колесов С.Н. Материаловедение и технология конструкционных материалов. М. Высш шк., 2004
Кузьмин Б. А. и др. Металлургия. Металловедение и конструкционные материалы. М.: Высшая школа, 1977
Лахтин Ю.М., Леонтьева В.П. Материаловедение. М.: Машиностроение, 1990.
Мезенин Н.А. Занимательно о железе. М. «Металлургия», 1972.
Ройтман И.А., Кузьменко В.И. Основы машиностроения в черчении. М.: Гуманит. изд. центр ВЛАДОС, 2000
Приложения приложение 1. Устройство доменной печи
Приложение 2. Схемы устройства сталеплавильных печей
Схема устройства мартеновской печи
Схема устройства конвертора
Схема устройства электропечи
Приложение 3. Схема организации производства стали
26
studfiles.net
Классификация конструкционных сталей
Стали классифицируют по химическому составу, качеству, степени раскисления, структуре и прочности.
По химическому составу стали классифицируют на углеродистые и легированные. По концентрации углерода те и другие подразделяют на низкоуглеродистые (< 0,3 % С), среднеуглеродистые (0,3-0,7% С) и высокоуглеродистые (> 0,7% С). Легированные стали в зависимости от введенных элементов подразделяют на хромистые, марганцовистые, хромоникелевые, хромокремнемарганцевые и многие другие. По количеству введенных элементов их разделяют на низко-, средне- и высоколегированные. В низколегированных сталях количество легирующих элементов не превышает 5%, в среднелегированных содержится от 5 до 10%, в высоколегированных – более 10%.
По качеству стали классифицируют на стали обыкновенного качества, качественные, высококачественные и особовысококачественные.
Под качеством стали понимают совокупность свойств, определяемых металлургическим процессом ее производства. Однородность химического состава, строения и свойств стали, а также ее технологичность во многом зависят от содержания газов (кислорода, водорода, азота) и вредных примесей – серы и фосфора. Газы являются скрытыми, количественно трудно определяемыми примесями, поэтому нормы содержания вредных примесей служат основными показателями для разделения сталей по качеству. Стали обыкновенного качества содержат до 0,055% S и 0,045% Р, качественные – не более 0,04% S и 0,035% Р, высококачественные – не более 0,025% S и 0,025% Р, особовысококачественные – не более 0,015% S и 0,025% Р.
По степени раскисления и характеру затвердевания стали классифицируют на спокойные, полуспокойные и кипящие. Раскисление – процесс удаления из жидкого металла кислорода, проводимый для предотвращения хрупкого разрушения стали при горячей деформации.
Спокойные стали раскисляют марганцем, кремнием и алюминием. Они содержат мало кислорода и затвердевают спокойно без газовыделения. Кипящие стали раскисляют только марганцем. Перед разливкой в них содержится повышенное количество кислорода, который при затвердевании, частично взаимодействуя с углеродом, удаляется в виде СО. Выделение пузырей СО создает впечатление кипения стали, с чем и связано ее название. Кипящие слали дешевы, их производят низкоуглеродистыми и практически без кремния (Si < 0,07%), но с повышенным количеством газообразных примесей.
Полуспокойные стали по степени раскисления занимают промежуточное положение между спокойными и кипящими.
При классификации стали по структуре учитывают особенности ее строения в отожженном и нормализованном состояниях. По структуре в отожженном (равновесном) состоянии конструкционные стали разделяют на четыре класса: 1) доэвтектоидные, имеющие в структуре избыточный феррит; 2) эвтектоидные, структура которых состоит из перлита; 3) аустенитные; 4) ферритные. Углеродистые стали могут быть первых двух классов, легированные – всех классов.
Влияние углерода и постоянных примесей на свойства стали
Сталь — сложный по составу железоуглеродистый сплав. Кроме железа и углерода – основных компонентов, а также возможных легирующих элементов, сталь содержит некоторое количество постоянных и случайных примесей, влияющих на ее свойства.
Углерод, концентрация которого в конструкционных сталях достигает 0,8%, оказывает определяющее влияние на их свойства. Степень его влияния зависит от структурного состояния стали, ее термической обработки.
После отжига углеродистые конструкционные стали имеют ферритно-перлитную структуру, состоящую из двух фаз – феррита и цементита. Количество цементита, который отличается высокой твердостью и хрупкостью, увеличивается пропорционально концентрации углерода. В связи с этим, по мере повышения содержания углерода, увеличиваются прочность и твердость, но снижаются пластичность и вязкость стали.
Влияние углерода еще более значительно при неравновесной структуре стали. После закалки на мартенсит временное сопротивление легированных сталей интенсивно растет по мере увеличения содержания углерода и достигает максимума при 0,4%С. При большей концентрации углерода становится нестабильным из-за хрупкого разрушения стали, о чем свидетельствуют низкие значения ударной вязкости. При низком отпуске механические свойства полностью определяются концентрацией углерода в твердом растворе.
Углерод изменяет и технологические свойства стали. При увеличении его содержания снижается способность сталей деформироваться в горячем и особенно в холодном состояниях, затрудняется свариваемость.
Постоянные примеси в стали: марганец, кремний, сера, фосфор, а также газы: кислород, азот, водород.
Марганец – полезная примесь; вводится в сталь для раскисления и остается в ней в количестве 0,3-0,8%. Марганец уменьшает вредное влияние кислорода и серы.
Кремний – полезная примесь; вводится в сталь в качестве активного раскислителя и остается в ней в количестве до 0,4%, оказывая упрочняющее действие.
Сера – вредная примесь, вызывающая красноломкость стали – хрупкость при горячей обработке давлением. В стали она находится в виде сульфидов. Красноломкость связана с наличием сульфидов, которые образуют с железом эвтектику, отличающуюся низкой температурой плавления (988 °С) и располагающуюся по границам зерен. При горячей деформации границы зерен оплавляются, и сталь хрупко разрушается. От красноломкости сталь предохраняет марганец, который связывает серу в сульфиды, исключающие образование легкоплавкой эвтектики. Устраняя красноломкость, сульфиды, так же как и другие неметаллические включения (оксиды, нитриды и т. п.), служат концентраторами напряжений, снижают пластичность и вязкость стали. Содержание серы в стали строго ограничивают. Положительное влияние серы проявляется лишь в улучшении обрабатываемости резанием.
Фосфор – вредная примесь. Он растворяется в феррите, упрочняет его, но вызывает хладноломкость – снижение вязкости по мере понижения температуры. Сильное охрупчивающее действие фосфора выражается в повышении порога хладноломкости. Каждая 0,01 % Р повышает порог хладноломкости на 25 °С. Хрупкость стали, вызываемая фосфором, тем выше, чем больше в ней углерода.
Фосфор – крайне нежелательная примесь в конструкционных сталях. Однако современные методы выплавки и переплавки не обеспечивают его полного удаления. Основной путь его снижения – повышение качества шихты.
Кислород, азот и водород – вредные скрытые примеси. Их влияние наиболее сильно проявляется в снижении пластичности и повышении склонности стали к хрупкому разрушению. Кислород и азот растворяются в феррите в ничтожно малом количестве и загрязняют сталь неметаллическими включениями (оксидами, нитридами). Кислородные включения вызывают красно- и хладноломкость, снижают прочность. Повышенное содержание азота вызывает деформационное старение.
Водород находится в твердом растворе или скапливается в порах и на дислокациях. Хрупкость, обусловленная водородом, проявляется тем резче, чем выше прочность материала и меньше его растворимость в кристаллической решетке.
Случайные примеси – элементы, попадающие в сталь из вторичного сырья или руд отдельных месторождений. Из скрапа в сталь попадает сурьма, олово и ряд других цветных металлов. Сталь, выплавленная из уральских руд, содержит медь, из керченских – мышьяк. Случайные примеси в большинстве случаев оказывают отрицательное влияние на вязкость и пластичность стали.
studfiles.net
Классификация сталей
СОДЕРЖАНИЕ
1. Общая характеристика сталей
2. Маркировка, расшифровка, свойства, термическая обработка и область применения
2.1 Углеродистых конструкционных сталей
2.2 Автоматных сталей
2.3 Конструкционных низколегированных сталей
2.4 Конструкционных цементуемых сталей
2.5 Конструкционных улучшаемых сталей
2.6 Рессорно-пружинных сталей
2.7 Шарикоподшипниковых сталей
2.8 Износостойких сталей
2.9 Корозионностойких сталей
2.10 Жаропрочных сталей и сплавов
1. Общая характеристика сталей
Ж/у сплавы с содержанием углерода до 2,14% называются сталями. Кроме железа и углерода в сталях содержатся полезные и вредные примеси.
Сталь – основной металлический материал, широко применяемый для изготовления деталей машин, летательных аппаратов, приборов, различных инструментов и строительных конструкций. Широкое использование сталей обусловлено комплексом механических, физико-химических и технологических свойств. Методы широкого производства стали были открыты в середине Х IX в. В это же время были уже проведены и первые металлографические исследования железа и его сплавов.
Стали сочетают высокую жесткость с достаточной стати-ческой и циклической прочностью. Эти параметры можно менять в широком диапазоне за счет изменения концентрации углерода, легирующих элементов и технологий термической и химико-термической обработки. Изменив химический состав, можно получить, стали с различными свойствами, и использовать их во многих отраслях техники и народного хозяйства.
Углеродистые стали, классифицируют по содержанию углерода, назначению, качеству, степени раскисления и структуре в равновесном состоянии.
По содержанию углерода стали, подразделяются на низкоугле-родистые (< 0,3 % С), среднеуглеродистые (0,3-0,7 % С) и высокоугле-родистые (> 0,7 % С).
По назначению стали классифицируют на конструкционные и инструментальные. Конструкционные стали, представляют наиболее обширную группу, предназначенную для изготовления строительных сооружений, деталей машин и приборов. К этим сталям относят цементуемые, улучшаемые, высокопрочные и рессорно-пружинные. Инструментальные стали, подразделяют на стали для режущего, измерительного инструмента, штампов холодного и горячего (до 200 0 С) деформирования.
По качеству стали, классифицируют на обыкновенного качества, качественные, высококачественные. Под качеством стали понимается совокупность свойств, определяемых металлургическим процессом ее производства. Стали обыкновенного качества бывают только углеродистыми (до 0,5 % С), качественные и высококачественные – углеродистыми и легированными.
По степени раскисления и характеру затвердевания стали классифицируют на спокойные, полуспокойные и кипящие. Раскисление – процесс удаления из жидкого металла кислорода, проводимый с целью предотвращения хрупкого разрушения стали при горячей деформации.
Полуспокойные стали по степени раскисления занимают промежуточное положение между спокойными и кипящими.
По структуре в равновесном состоянии стали, делятся на: 1) доэвтектоидные, имеющие в структуре феррит и перлит; 2) эвтектоидные, структура которых состоит из перлита; 3) заэвтектоидные, имеющие в структуре перлит и цементит вторичный.
2. Маркировка, расшифровка, свойства, термическая обработка и область применения.
2.1 Углеродистые конструкционные стали
Стали обыкновенного качества выпускают в виде проката (прутки, балки, листы, уголки, трубы, швеллеры и т.п.) в нормализованном состоянии и в зависимости от назначения и комплекса свойств подразделяют на группы: А, Б, В.
Стали маркируются сочетанием букв Ст и цифрой (от 0 до 6), показывающей номер марки, а не среднее содержание углерода в ней, хотя с повышением номера содержание углерода в стали увеличивается. Стали групп Б и В имеют перед маркой буквы Б и В, указывающие на их принадлежность к этим группам. Группа А в обозначении марки стали не указывается. Степень раскисления обозначается добавлением индексов: в спокойных сталях – «сп», полуспокойных – «пс», кипящих – «кп», а категория нормируемых свойств (кроме категории 1) указывается последующей цифрой. Спокойными и полуспокойными производят стали Ст1 – Ст6, кипящими – Ст1 – Ст4 всех трех групп. Сталь Ст0 по степени раскисления не разделяют.
Стали группы А используют в состоянии поставки для изделий, изготовление которых не сопровождается горячей обработкой. В этом случае они сохраняют структуру нормализации и механические свойства, гарантируемые стандартом.
Сталь марки Ст3 используется в состоянии поставки без обработки давлением и сваркой. Ее широко применяют в строительстве для изготовления металлоконструкций.
Стали группы Б применяют для изделий, изготавливаемых с применением горячей обработки (ковка, сварка и в отдельных случаях термическая обработка), при которой исходная структура и механические свойства не сохраняются. Для таких деталей важны сведения о химическом составе, необходимые для определения режима горячей обработки.
Стали группы В дороже, чем стали групп А и Б, их применяют для ответственных деталей (для производства сварных конструкций).
Углеродистые стали обыкновенного качества (всех трех групп) предназначены для изготовления различных металлоконструкций, а также слабонагруженных деталей машин и приборов. Эти стали, используются, когда работоспособность деталей и конструкций обеспечивается жесткостью. Углеродистые стали обыкновенного качества широко используются в строительстве при изготовлении железобетонных конструкций. Способностью к свариванию и к холодной обработке давлением отвечают стали групп Б и В номеров 1-4, поэтому из них изготавливают сварные фермы, различные рамы и строительные металлоконструкции, кроме того, крепежные изделия, часть из которых подвергается цементации.
Среднеуглеродистые стали номеров 5 и 6, обладающие большой прочностью, предназначаются для рельсов, железнодорожных колес, а также валов, шкивов, шестерен и других деталей грузоподъемных и сельскохозяйственных машин. Некоторые детали из этих сталей групп Б и В подвергаются термической обработке – закалке с последующим высоким отпуском.
В машиностроении углеродистые качественные стали, используются для изготовления деталей разного, чаще всего неответственного назначения и являются достаточно дешевым материалом. В промышленность эти стали поставляются в виде проката, поковок, профилей различного назначения с гарантированным химическим составом и механическим свойствами.
В машиностроении применяют углеродистые качественные стали, поставляемые по ГОСТ 1050-74. Маркируются эти стали двузначными цифрами 05, 08, 10, 15, 20, …, 75, 80, 85, обозначающими среднее содержание углерода в сотых долях процента.
К углеродистым сталям относят также стали с повышенным содержанием марганца (0,7-1,0 %) марок 15Г, 20Г, 25Г, …, 70Г, имеющих повышенную прокаливаемость.
Спокойные стали маркируют без индекса, полуспокойные и кипящие – с индексом соответственно «пс» и «кп». Кипящие стали производят марок 05кп, 08кп, 10кп, 15кп, 20кп, полуспокойные – 08пс, 10пс, 15пс, 20пс.
Качественные стали широко применяются в машиностроении и приборостроении, так как за счет разного содержания углерода в них, а соответственно и термической обработки можно получить широкий диапазон механических и технологических свойств.
Низкоуглеродистые стали 05кп, 08кп, 10кп, 15кп, 20кп отличаются малой прочностью и высокой пластичностью в холодном состоянии. Эти стали в основном производят в виде тонкого листа и используют после отжига или нормализации для холодной штамповки с глубокой вытяжкой. Они легко штампуются из-за малого содержания углерода и незначительного количества кремния, что и делает их очень мягкими. Их можно использовать в автомобилестроении для изготовления деталей сложной формы. Глубокая вытяжка из листа этих сталей применяется при изготовлении консервных банок, эмалированной посуды и других промышленных изделий.
Спокойные стали 08, 10 применяют в отожженном состоянии для конструкций невысокой прочности – емкости, трубы и т. д.
Стали 10, 15, 20 и 25 также относятся к низкоуглеродистым сталям, они пластичны, хорошо свариваются и штампуются. В нормализованном состоянии в основном их используют для крепежных деталей – валики, оси и т. д.
Для увеличения поверхностной прочности этих сталей их цементуют (насыщают поверхность углеродом) и применяют для деталей небольшого размера, например слабонагруженных зубчатых колес, кулачков и т. д.
Среднеуглеродистые стали 30, 35, 40, 45, 50 и аналогичные стали с повышенным содержанием марганца 30Г, 40Г и 50Г в нор
mirznanii.com
ТОП 10: |
⇐ ПредыдущаяСтр 5 из 10Следующая ⇒
Углеродистые стали – это сплавы железа с углеродом, содержащие до 2,14 % углерода (С) при малом содержании других элементов. Они обладают высокой пластичностью и хорошо деформируются. Углерод сильно влияет на свойства стали даже при незначительном изменении его содержания. Углеродистые стали можно классифицировать по нескольким параметрам: · По способу раскисления Легированные стали. Это стали в состав которых помимо углерода и примесей целенаправленно вводят один или несколько легирующих элементов для обеспечения требуемой прочности, пластичности, вязкости и др. технологических и эксплутационных свойств. Легирование производится с целью изменения механических свойств (прочности, пластичности, вязкости), физических свойств (электропроводности, магнитных характеристик, радиационной стойкости) и химических свойств (коррозионной стойкости). Чугун — сплав железа с углеродом (обычно более 2%) содержащий также постоянные примеси (Si, Mn, Р и S), а иногда и легирующие элементы, затвердевает с образованием эвтектики. Чугун — важнейший первичный продукт чёрной металлургии, используемый для передела при производстве стали и во вторичной плавке в чугунолитейном производстве. Виды чугунов Белый чугун В белом чугуне весь углерод находится в виде цементита. Структура такого чугуна – перлит, ледебурит и цементит. Такое название этот чугун получил из-за светлого цвета излома. В промышленности разновидности чугуна маркируются следующим образом: |
infopedia.su
Основная классификация сталей и ее виды
Сплав железа с углеродом с содержанием последнего не более 2,14% называют сталью. Главные качества стали: прочность, пластичность, вязкость, упругость, износоустойчивость и прочие. Основная классификация сталей определяется:
Химическим составом.
- Структурным составом.
- Качеством стали или сплава (зависит от количества вредных примесей и способа производства).
- Степенью раскисления.
- Назначением.
Химический состав
В зависимости от количества содержания углерода в составе сплава различают углеродистые и легированные марки стали. Содержание углерода в обоих видах стали также определяет их маркировку и ГОСТ знак. Классификация углеродистых сталей подразделяется на:
- Малоуглеродистые (содержание C (углерод) менее 0,3%).
- Среднеуглеродистые (содержание C – от 0,3 до 0,7%).
- Высокоуглеродистые (содержание C – выше 0,7%).
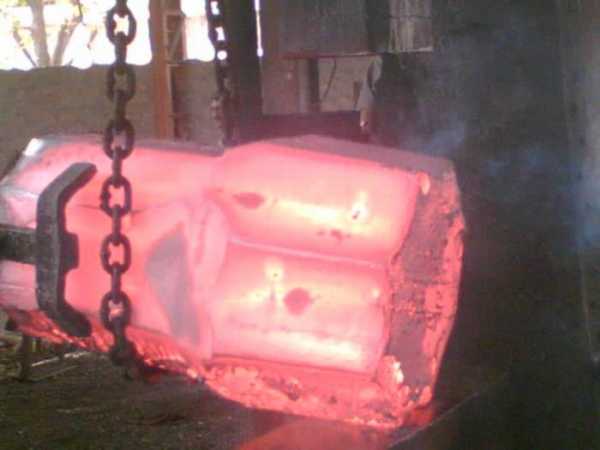
Для того чтобы улучшить технологические характеристики сплава, сталь легируют. В сплав вводят, кроме основных компонентов и примесей, специальные химические элементы (никель, хром, молибден, аллюминий, бор, ванадий, таллий и др), которые обеспечивают комплексное легирование. В свою очередь классификация легированных сталей выделяет:
- Низколегированные (содержат менее 2,5% компонентов, легирующих сталь).
- Среднелегированные (содержат от 2,5 до 10% компонентов, легирующих сталь).
- Высоколегированные (содержат выше 10% компонентов, легирующих сталь).
Классификация сталей по структурному составу
Сталь, прошедшая процесс легирования, подразделяется на классы по структурному составу. Структура полученного сплава зависит от содержания в нем углерода, легирующих компонентов и скорости охлаждения после нагрева до 900 ⁰С. Выделяют пять типов структурного состава:
- Перлитный сплав.
- Мартенситный сплав.
- Аустенитный сплав.
- Ферритный сплав.
- Карбидный сплав.
Классификация сталей по качеству
По условиям производства (способ выплавки, содержание примесей) стали и сплавы можно подразделить на несколько категорий:
- Обыкновенного качества (содержание S (сера) > 0,06%, P (фосфор) < 0,07%).
- Качественные (содержание S (сера) > 0,04%, P (фосфор) < 0,35%).
- Высококачественные (содержание S (сера) > 0,025%, P (фосфор) < 0,025%).
- Особо высококачественные (содержание S (сера) > 0,015%, P (фосфор) < 0,025%).
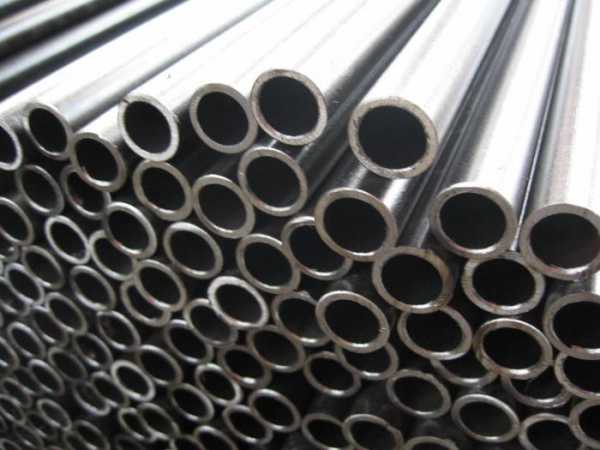
К сталям обыкновенного качества относятся углеродистые, стоимость и технологические характеристики которых значительно уступают сталям других классов.
По химическому составу к качественным видам могут относиться как легированные, так и углеродистые стали. При производстве качественных сталей соблюдают более строгие требования к изготовлению.
Углеродистые типы сталей обыкновенного качества и качественные определяются по степени раскисления и характеру затвердевания как спокойные, полуспокойные и кипящие.
Высококачественные и особо высококачественные стали имеют высокие технологические характеристики, повышенную степень очистки от вредных примесей.
Классификация сталей по назначению
По назначению сталь классифицируется на:
- Инструментальную.
- Конструкционную.
- Сталь с особыми свойствами.
fb.ru
Классификация и свойства сталей — Материалы и свойства
Автор Admin На чтение 3 мин. Просмотров 70 Опубликовано
Сталь – ковкий сплав железа с углеродом (до 2 %), содержащий те же примеси, что и чугун, но в меньших количествах (от сотых долей до 1 %).
Стали классифицируют по способу получения, назначению, химическому составу, характеру застывания металла в изложнице, качеству, а также методу прокатки.
По способу получения различают стали конверторные (прежнее название бессемеровские), мартеновские и электростали, которые получают в соответствующих печах — кислородных конверторах, мартенах, электрических печах.
По назначению
По назначению стали делят на конструкционные, инструментальные и специальные.
Конструкционные стали содержат от 0,08 до 0,85 % углерода. Они хорошо обрабатываются давлением и резанием, выпускаются углеродистыми и легированными. Из таких сталей изготавливают детали машин и механизмов, строительные конструкции, корпуса вагонов и судов и т. д.
Инструментальные стали
Инструментальные стали характеризуются повышенным содержанием углерода (0,7—1,35%), обладают высокой твердостью, жаропрочностью и износостойкостью. В соответствии со своим названием служат для изготовления различного инструмента: режущего, ударно-штампового, мерительного (резцов, фрез, штампов, калибров и др.).
Специальные стали
Специальные стали характеризуются особыми свойствами (нержавеющие, немагнитные, кислотостойкие, износостойкие, жаропрочные и др.), как правило, они высоколегированные. Из таких сталей изготавливают ответственные детали машин и приборов.
По химическому составу
По химическому составу различают углеродистые и легированные стали. Обычными углеродистыми сталями называются стали без легирующих добавок. В состав легированных сталей вводятся специальные добавки, улучшающие качество стали и придающие ей особые свойства.
Углеродистые стали подразделяются на низкоуглеродистые (до 0,25% углерода), среднеуглеродистые (от 0,25 до 0,6%) и высокоуглеродистые (свыше 0,65 %). С увеличением содержания углерода уменьшается пластичность и возрастает твердость стали. Прочность ее также повышается, но при содержании углерода более 1 % вновь снижается.
Легированные стали
Легированные стали в зависимости от степени легирования делятся на низколегированные (менее 2,5 % легирующих элементов), среднелегированные (2,5—10%) и высоколегированные (более 10%). Название им часто дается по преобладающим элементам, например, вольфрамовая сталь, хромоникелевая сталь и т. д.
По характеру застывания металла в изложнице сталь подразделяют на спокойную, полуспокойную и кипящую. Процесс застывания происходит тем спокойнее, чем полнее удален из стали кислород. При разливе малораскисленной стали в излож-нице происходит бурное выделение пузырьков оксидов углерода – сталь как бы кипит. Для удаления кислорода (раскисление стали) в расплав в конце варки вводят раскислители (ферросилиций, ферромарганец, алюминий), способные соединяться с кислородом. Сталь, в которую введены все три раскислителя, называют спокойной, два – полуспокойной, один – кипящей.
По качеству
По качеству стали делят на обыкновенные, качественные, высококачественные и особокачественные. Различие между ними состоит в количестве содержания вредных примесей (серы и фосфора) и неметаллических включений. Допустимые содержания элементов, %: в особо высококачественных сталях – каждого элемента до 0,015; в высококачественных – серы не более 0,02 и фосфора – 0,025; в качественных – каждого элемента не болеее 0,035; в обыкновенных – серы до 0,08 и фосфора – 0,09.
По методу прокатки
По методу прокатки различают стали горячекатаные и холоднокатаные. Последние имеют более ровную и гладкую поверхность и наиболее равномерную толщину.
arxipedia.ru