Классификация сталей по назначению: Классификация сталей: по назначению, составу, применению
alexxlab | 07.06.2023 | 0 | Разное
Классификацию сталей по назначению. Статья
В Вашем браузере отключена функция javascript. Информация может отображаться некорректно!
Включите функцию javascript в Вашем браузере и обновите страницу
По назначению стали и сплавы классифицируются на следующие группы:
- конструкционные стали;
- инструментальные стали;
- стали с особыми физическими и химическими свойствами.
Конструкционные стали
Классификация конструкционных сталей может быть представлена следующими пунктами.
Строительные стали
К строительным сталям относятся углеродистые стали обыкновенного качества, а также низколегированные стали. Основное требование к строительным сталям – их хорошая свариваемость.
Пример строительных сталей: С255, С345Т, С390К, С440Д.
Стали для холодной штамповки
Для холодной штамповки применяют листовой прокат из низкоуглеродистых качественных марок и марок нормального качества стали.
Пример сталей для холодной штамповки: 08Ю, 08пс и 08кп.
Цементируемые стали
Цементируемые стали применяют для изготовления деталей, работающих в условиях поверхностного износа и испытывающих при этом динамические нагрузки. К цементируемым относятся малоуглеродистые стали, содержащие 0,1-0,3% углерода (такие, как 15, 20, 25), а также некоторые легированные стали (15Х, 20Х, 15ХФ, 20ХН 12ХНЗА, 18Х2Н4ВА, 18Х2Н4МА, 18ХГТ, ЗОХГТ, 20ХГР).
Пример цементируемых сталей: 15, 20, 25, 15Х, 20Х, 15ХФ, 20ХН 12ХНЗА, 18Х2Н4ВА, 18Х2Н4МА, 18ХГТ, ЗОХГТ, 20ХГР.
Улучшаемые стали
К улучшаемым сталям относят стали, которые подвергают улучшению – термообработке, заключающейся в закалке и высоком отпуске. К ним относятся среднеуглеродистые стали (35, 40, 45, 50), хромистые стали (40Х, 45Х, 50Х), хромистые стали с бором (ЗОХРА, 40ХР), хромоникелевые, хромокремниемарганцевые, хромоникельмолибденовые стали.
Пример улучшаемых сталей: 35, 40, 45, 50, 40Х, 45Х, 50Х, 3ОХРА, 40ХР.
Высокопрочные стали
Высокопрочные стали – это стали, у которых подбором химического состава и термической обработкой достигается предел прочности примерно вдвое больший, чем у обычных конструкционных сталей. Такой уровень прочности можно получить в среднеуглеродистых легированных сталях.
Пример высокопрочных сталей: 30ХГСН2А, 40ХН2МА, ЗОХГСА, 38ХНЗМА, 03Н18К9М5Т, 04Х11Н9М2Д2ТЮ.
Рессорно-пружинные стали
Рессорно-пружинные стали сохраняют в течение длительного времени упругие свойства, поскольку имеют высокий предел упругости, высокое сопротивление разрушению и усталости. К пружинным относятся углеродистые стали (65, 70) и стали, легированные элементами, которые повышают предел упругости – кремний, марганец, хром, вольфрам, ванадий, бор (60С2, 50ХГС, 60С2ХФА, 55ХГР).
Пример рессорно-пружинных сталей: 65, 70, 60С2, 50ХГС, 60С2ХФА, 55ХГР.
Подшипниковые стали
Подшипниковые (шарикоподшипниковые) стали имеют высокую прочность, износоустойчивость, выносливость. К подшипниковым предъявляют повышенные требования на отсутствие различных включений, макро- и микропористости. Обычно шарикоподшипниковые стали характеризуются высоким содержанием углерода (около 1%) и наличием хрома (ШХ9, ШХ15).
Пример подшипниковых сталей: ШХ9, ШХ15
Автоматные стали
Автоматные стали используют для изготовления неответственных деталей массового производства (винты, болты, гайки и др.), обрабатываемых на станках-автоматах. Для повышения обрабатываемости резанием в такие стали дополнительно вводится сера, селен, теллур, а также свинец, что способствует образованию короткой и ломкой стружки, а также уменьшает трение между резцом и стружкой. Недостаток автоматных сталей – пониженная пластичность.
Пример автоматных сталей: А12, А20, АЗО, А40Г, АС11, АС40, АЦ45Г2, АСЦЗОХМ, АС20ХГНМ.
Износостойкие стали
Износостойкие стали применяют для деталей, работающих в условиях абразивного трения, высокого давления и ударов (крестовины железнодорожных путей, траки гусеничных машин, щеки дробилок, черпаки землеройных машин, ковши экскаваторов и др. ). В качестве износостойкой стали применяют высокомарганцовистую сталь.
Пример износостойких сталей: 110Г13Л.
Инструментальные стали
Классификация сталей инструментального назначения может быть представлена следующими пунктами.
Стали для режущих инструментов
Стали для режущих инструментов должны быть способными сохранять высокую твердость и режущую способность продолжительное время, том числе и при нагреве. В качестве сталей для режущих инструментов применяют углеродистые, легированные инструментальные, быстрорежущие стали.
Углеродистые инструментальные стали
Углеродистые инструментальные стали содержат 0,65-1,32% углерода. К данной группе, помимо нелегированных углеродистых инструментальных сталей, условно относят также стали с небольшим содержанием легирующих элементов, которые не сильно отличаются от углеродистых.
Пример углеродистых инструментальных сталей: У7, У7А, У13, У13А.
Легированные инструментальные стали
В данную группу сталей входят стали, содержащие легирующие элементы в количестве 1-3%. Легированные инструментальные стали имеют повышенную теплостойкость – до +300 °С. Легированные инструментальные стали широко используют для производства сверл малых и больших диаметров, фрез, зенкеров, протяжек, разверток и пр.
Пример легированных инструментальных сталей: 9ХС, ХВГ, ХВГС.
Быстрорежущие стали
Быстрорежущие стали применяют для изготовления различного режущего инструмента, работающего на высоких скоростях резания, так как они обладают высокой теплостойкостью – до +650вС. Наибольшее распространение получили быстрорежущие стали марок
Пример быстрорежущих сталей: Р9, Р18, Р6М5, Р9Ф5, Р10К5Ф5.
Стали для измерительных инструментов
Инструментальные стали для измерительных инструментов помимо твердости и износостойкости должны сохранять постоянство размеров и хорошо шлифоваться.
Сталь для измерительных инструментов применяют в производстве плиток, калибров, шаблонов, измерительных скоб, шкал, линеек и других плоских и длинных инструментов. Для получения рабочей поверхности с высокой твердостью и износостойкостью инструменты подвергают цементации и закалке.
Пример сталей для измерительных инструментов: У8…У12, X, 12X1, ХВГ, Х12Ф1, 15, 15Х.
Штамповые стали
Штамповые стали обладают высокой твердостью и износостойкостью, прокаливаемостью и теплостойкостью.
Стали для штампов холодного деформирования
Эти стали должны обладать высокой твердостью, износостойкостью и прочностью, сочетающейся с достаточной вязкостью, также должны быть теплостойкими. Во многих случаях для изготовления штампов для холодного деформирования используют быстрорежущие стали.
Пример сталей для штампов холодного деформирования: Х12Ф1, Х12М, Х6ВФ, 6Х5ВЗМФС, 7ХГ2ВМ.
Стали для штампов горячего деформирования
Эти стали должны иметь высокие механические свойства (прочность и вязкость) при повышенных температурах и обладать износостойкостью, окалиностойкостью, разгаростойкостью и высокой теплопроводностью.
Пример сталей для штампов горячего деформирования: 5ХНМ, 5ХНВ, 4ХЗВМФ, 4Х5В2ФС, ЗХ2В8Ф, 4Х2В5МФ.
Валковые стали
Данные стали применяют для рабочих, опорных и прочих валков прокатных станов, бандажей составных опорных валков, ножей для холодной резки металла, обрезных матриц и пуансонов.
Пример валковых сталей: 9X1, 55Х, 60ХН, 7Х2СМФ.
Стали с особенными химическими и физическими свойствами
Кроме всех вышеперечисленных, существуют также марки сталей с особыми свойствами.
Электротехническая сталь
Электротехническая сталь – это сплав железа и кремния, иногда легированный алюминием. Применяется данная сталь при производстве магнитопроводов разнообразного электротехнического оборудования.
Суперинвар
Суперинвар – это сплав железа, никеля и кобальта, применяемый при изготовлении высокоточного оборудования.
Жаростойкая сталь
Жаростойкая сталь обладает повышенной стойкостью против разрушения при температурах от 900 °C. Данная сталь легируется алюминием, кремнием, никелем.
Жаропрочная сталь
Жаропрочная сталь применяется для изготовления деталей газотурбинных установок. Такие стали призваны работать в нагруженном состоянии при высокой температуре в течение некоторого времени.
Классификация сталей
Аустенитные стали используются как кислотостойкие для изготовления химической аппаратуры, а также для деталей машин и криогенного оборудования, работающего при температурах до -253 С. Стали этого класса могут использоваться и как жаростойкие, жаропрочные материалы.
Наиболее
известными сталями ферритного класса
являются высокохромистые стали, содержащие
17…30 % хрома и не более 0,2 % углерода. Они
хорошо сопротивляются как электрохимической
так и газовой коррозии при высоких температурах,
т.е. являются кислотостойкими и жаростойкими
(окалиностойкими). Недостатком этих сталей
является низкая прочность и возникающая
при перегреве (например, при сварке) крупнозернистость,
которая не устраняется термической обработкой,
Крупнозернистость придаёт сталям повышенную
хрупкость.
Рассмотренные стали мартенситного, аустенитного и ферритного класса относятся с особыми свойствами.
Стали карбидного класса по назначению являются инструментальными. Они отличаются повышенной износостойкостью и теплостойкость (красностойкостью). Благодаря этому их используют для изготовления режущего инструмента, работающего при высоких скоростях резания. Наилучшие режущие свойства стали приобретают после сложной термической обработки. Отожженные заготовки имеют структуру сорбитообразного перлита и карбидов. После механической обработки заготовок и придания инструменту необходимой формы он подвергается закалке и трёхкратному отпуску. Схема режимов термической обработки приведена.
С целью
выравнивания температуры по всему сечению
инструмента и в избежании его деформации
производится подогрев до температуры
около 800°С, а затем окончательный нагрев
в расплавах солей до температур 1260.. . 1290
°С (для стали Р18). Высокие температуры
закалки необходимы для более полного
растворения карбидов и получения при
нагреве высоколегированного аустенита.
Это обеспечивает получение после закалки
в масле (или на воздухе) высоколегированного
мартенсита, обладающего высокой устойчивостью
против отпуска, т.е. теплостойкостью.
Часть карбидов, не растворившихся при
нагреве, препятствуют росту зерна аустенита.
В процессе охлаждения часть аустенита превращается в мартенсит. Кроме того в структуре сохраняются не растворенные карбиды и некоторое количество остаточного аустенита, т.к. точка Мк лежит ниже нуля градусов и мартенситное превращение не заканчивается. Остаточный аустенит понижает твёрдость и режущие свойства, поэтому его присутствие в структуре недопустимо.
После закалки
следует отпуск при температуре около
560 °С, при котором происходит превращение
остаточного аустенита в мартенсит с выделением
дополнительного количества дисперсных
карбидов. Это сопровождается увеличением
твёрдости. Чтобы весь остаточный аустенит
превратился в мартенсит, отпуск проводят
3 раза подряд с выдержкой по одному часу.
Для инструмента простой формы можно делать
после закалки обработку холодом и однократный
отпуск при 560°С.
Твёрдость стали после закалки составляет HRC 62…63, а после трёхкратного отпуска HRC 64…65. Высокая твёрдость сохраняется при последующих нагревах в процессе работы до температур до 600 “С, что обеспечивает теплостойкость инструмента.
1.1.2. Углеродистые стали
Углеродистые стали — это сплавы в основном железа с углеродом, содержащие до 2% углерода. Кроме углерода, эти стали содержат до 0,8% марганца и до 0,4% кремния, остающихся после раскисления, а также вредные примеси — до 0,055% серы и до 0,045% фосфора.
Углеродистая
сталь является основным материалом для
изготовления деталей машин и аппаратов.
Для котельных агрегатов, турбин, вспомогательного
оборудования широко применяют низкруглеродистые
стали, содержащие до 0,25% углерода. Они
очень пластичны и поэтому хорошо поддаются
обработке давлением, гибке и правке в
горячем и холодном состоянии, хорошо
свариваются. Эти стали можно использовать
также в виде стального фасонного литья.
Кроме того, они обладают вполне удовлетворительными
механическими свойствами: достаточно
прочны при температурах до 450° С, хорошо
воспринимают динамические нагрузки.
Низкоуглеродистые стали удовлетворительно сопротивляются коррозии в условиях работы ряда деталей тепломеханического оборудования электростанций. Эти стали самые дешевые и наименее дефицитные.
Особенности производства стали и стальных полуфабрикатов оказывают существенное влияние на механические свойства и качество готовых изделий. Большинство деталей котлов и турбин изготавливают из углеродистой стали, выплавленной в основных мартеновских печах.
Продувкой
в бессемеровском конвертере получают
углеродистую сталь с содержанием углерода
до 0,5%. Эту сталь применяют для производства
сварных труб неответственного назначения,
болтов, профилей, тонкой жести.
Кроме способа выплавки, на свойства стали и готовых изделий большое влияние оказывает способ раскисления, по которому стали делятся на спокойные (сп), полуспокойные (пс) и кипящие (кп).
По назначению
углеродистые стали делят на конструкционные
и инструментальные. Конструкционные
стали в свою очередь разделяют на строительные
и машиностроительные. В строительных
сталях содержание углерода обычно не
превышает 0,25%, т.
Машиностроительные малоуглеродистые стали часто применяют в качестве цементуемых, т. е. для деталей, подвергаемых поверхностному науглероживанию и закалке для повышения износостойкости, а также для изготовления крепежных деталей.
Среднеуглеродистые машиностроительные стали (0,3—0,7% углерода) прочнее строительных и могут подвергаться закалке с высоким отпуском. В результате такой термической обработки улучшаются их механические свойства. Однако эти стали хуже свариваются и плохо поддаются деформации в холодном состоянии, v Инструментальные стали содержат от 0,7 до 1,4% углерода.
Углеродистые
стали классифицируют также по качеству,
которое определяется содержанием серы
и фосфора, способом производства и постоянством
механических свойств и химического состава.
Чем меньше содержание вредных примесей,
колебание механических свойств и химического
состава, тем выше качество стали.
Углеродистые стали бывают обыкновенного качества, качественные и высококачественные. Углерод — элемент, в основном определяющий свойства углеродистых сталей. С увеличением содержания углерода возрастают предел прочности и твердость стали, снижаются показатели пластичности (относительное удлинение и относительное сужение), а также ударная вязкость. При 0,8% углерода прочность стали достигает максимального значения, после чего она начинает снижаться.
Изменение прочности стали в зависимости от содержания углерода легко объяснить характером изменения микроструктуры. Незакаленная углеродистая сталь при содержании углерода менее 0,8% состоит из кристаллитов свободного феррита и перлита, при 0,8% — только из перлита и при содержании углерода более 0,8% — из перлита и свободного цементита.
Феррит
(твердый раствор углерода в а-железе)
— очень пластичен и вязок, но непрочен.
Перлит, механическая смесь тонкодисперсных
пластинок феррита и цементита, придает
прочность. Цементит очень тверд, хрупок
и статически прочен. При повышении в стали
содержания углерода (в пределах до 0,8%)
увеличивается содержание перлита и повышается
прочность стали. Однако вместе с этим
снижаются ее пластичность и ударная вязкость.
При содержании 0,8% С (100% перлита) прочность
стали достигает максимума. При дальнейшем
увеличении содержания углерода избыточный
свободный цементит образует оторочку
вокруг перлитных зерен, что приводит
к хрупкому разрушению и неко-торому снижению
прочности стали.
Марганец вводят в любую сталь для раскисления (т. е. для устранения вредных включений закиси железа). Марганец растворяется в феррите и цементите, поэтому его обнаружение металлографическими методами невозможно. Он повышает прочность стали и сильно увеличивает прокаливаемость. Содержание марганца в углеродистой стали отдельных марок может достигать 0,8%.
Кремний,
подобно марганцу, является раскислителем,
но действует более эффективно. В кипящей
стали содержание кремния не должно превышать
0,07%. Если кремния будет больше, то раскисление
кремнием произойдет настолько полно,
что не получится «кипения» жидкого металла
за счет раскисления углеродом. В спокойной
углеродистой стали содержится от 0,12 до
0,37% кремния. Весь кремний растворяется
в феррите. Он сильно повышает прочность
и твердость стали.
Сера —
вредная примесь. В процессе выплавки
стали содержание серы снижают, но полностью
ее удалить не удается. В мартеновской
стали обыкновенного качества содержание
серы допускается до 0,055%. Присутствие
серы в большом количестве приводит к
образованию трещин при ковке, штамповке
и прокатке в горячем состоянии, ото явление
называется красноломкостью. В углеродистой
стали сера взаимодействует с железом,
в результате чего получается сернистое
железо FeS. Сернистое железо образует с
железом относительно легкоплавкую эвтектику,
которая располагается по границам зерен.
При температурах ковки, штамповки, прокатки
в горячем состоянии эвтектика FeS—Fe находится
в жидком состоянии. В процессе горячей
пластической деформации по границам
зерен, где располагается жидкая эвтектика,
образуются горячие трещины. Если в сталь
ввести достаточное количество марганца,
то вредное влияние серы будет устранено,
так как она будет связана в тугоплавкий
сульфид марганца MnS. Включения MnS располагаются
в середине зерен, а не по их границам.
При горячей обработке давлением включения
MnS легко деформируются без обра-зования
трещин.
Фосфор,
подобно сере, является вредной примесью.
Растворяясь в феррите, фосфор резко снижает
его пластичность, повышает температуру
перехода в хрупкое состояние, или иначе
— вызывает хладноломкость стали. Это
явление наблюдается при содержании фосфора
свыше 0,1 %. Однако допустить содержание
даже 0,05% Р для стали ответственного назначения
уже рискованно, так как фосфор очень склонен
к ликвации. Области слитка с повышенным
содержанием фосфора становятся хладноломкими.
В мартеновской стали обыкновенного качества
допускается не более 0,045% Р.
Сера и фосфор, вызывая ломкость стали и одновременно понижая механические свойства, улучшают обрабатываемость резанием: повышается чистота обрабатываемой поверхности, увеличивается время между переточками резцов, фрез и т. д. Поэтому для ряда неответственных деталей, подвергаемых механической обработке, применяют так называемые автоматные стали с повы-шенным содержанием серы (до 0,30%) и фосфора (до 0,15%).
Кислород — вредная примесь. Закись железа, подобно сере, вызывает красноломкость стали. Очень твердые окислы алюминия, кремния и марганца резко ухудшают обрабатываемость стали резанием, быстро затупляя режущий инструмент.
В процессе выплавки углеродистой стали из металлического лома в нее могут попасть никель, хром, медь и другие элементы. Эти примеси ухудшают технологические свойства углеродистой стали (в частности, свариваемость), поэтому их содержание стараются свести к минимуму.
1.2. Классификация сталей по качеству
По качеству
стали подразделяются на стали обыкновенного
качества и качественные углеродистые
стали.
1.2.1.Стали обыкновенного качества
В зависимости от назначения различают три группы сталей обыкновенного качества: А, Б и В.
Группа А поставляется только по механическим свойствам, химический состав сталей этой группы не регламентируется, он только указывается в сертификатах завода-изготовителя. Стали этой группы обычно используются в изделиях в состоянии поставки без обработки давлением и сварки.
Группа Б поставляется только с гарантируемым химическим составом. Чем больше цифра условного номера стали, тем выше содержание углерода. Эти стали в дальнейшем могут подвергаться деформации (ковке, штамповке и др.), а в отдельных случаях и термической обработке. При этом их первоначальная структура и механические свойства не сохраняются.
Стали группы
В могут подвергаться сварке. Их поставляют
с гарантированным химическим составом
и гарантированными свойствами. Эта сталь
имеет механические свойства, соответствующие
ее номеру по группе А, а химический состав
– номеру по группе Б с коррекцией по способу
раскисления.
1.2.2. Качественные углеродистые стали
Качественные углеродистые стали – этот класс углеродистых сталей изготавливается по ГОСТ 1050-74. Качественные стали поставляют и по химическому составу, и по механическим свойствам.. К ним предъявляются более жесткие требования по содержанию вредных примесей (серы не более 0,04 %, фосфора не более 0,035 %), неметаллических включений и газов, макро- и микроструктуры.
Качественные стали делят на две группы: с обычным содержанием марганца (до 0,8 %) и с повышенным содержанием (до 1,2 %). Марганец повышает прокаливаемость и прочностные свойства, но несколько снижает пластичность и вязкость стали.
По содержанию углерода качественные углеродистые стали подразделяются на низкоуглеродистые (до 0,25 % С), среднеуглеродистые (0,3-0,55 % С) и высокоуглеродистые (0,6-0,85 % С).
Для изделий
ответственного назначения применяют
высококачественные стали с еще более
низким содержанием серы и фосфора. Низкое
содержание вредных примесей в высококачественных
сталях дополнительно удорожает и усложняет
их производство. Поэтому обычно высококачественными
сталями бывают не углеродистые, а легированные
стали. Углеродистые стали, содержащие
0,7-1,3 % С, используют для изготовления ударного
и режущего инструмента.
Четыре типа стали и их применение
Сталь — невероятно полезный материал, который бывает всех форм, размеров и типов. Он повсюду: от столовых приборов, которыми мы пользуемся, от кухонь, которые нас кормят, больниц, которые заботятся о нашем здоровье, до домов, в которых мы живем. Это удивительно гибкий материал, который можно использовать буквально тысячами раз.
Но что вы знаете о стали?
Сегодня мы собираемся обсудить четыре основных типа стали, их относительные свойства и популярные области применения каждого из них. К концу вы будете знать столько, сколько вам нужно знать об этом удивительном материале!
Фото Кристофа Диона на Unsplash Четыре основных типа стали Существует четыре основных типа стали. Они есть; углеродистая сталь, легированная сталь, инструментальная сталь и нержавеющая сталь. Тот, о котором мы все, вероятно, слышали. Остальные три могут быть загадкой.
Из этих четырех типов стали существует более 3500 различных марок, охватывающих практически все мыслимые сочетания стали и сплава.
Хотя сама сталь всегда представляет собой смесь железа и углерода, другие элементы и их количества в стали определяют ее сорт.
Пока остановимся на этих четырех основных типах.
К ним относятся:
Углеродистая стальУглеродистая сталь содержит следовые количества сплавов и составляет около 90% от общего объема производства стали. Материал подразделяется на три различных типа: низкоуглеродистая сталь, среднеуглеродистая сталь и высокоуглеродистая сталь. Каждый из них отличается количеством углерода в стали.
- Низкоуглеродистая сталь содержит до 0,3% углерода
- Среднеуглеродистая сталь содержит 0,3-0,6% углерода
- Высокоуглеродистая сталь содержит более 0,6% углерода
Низкоуглеродистая сталь часто используется для изготовления заклепок, проволоки, штампованных стальных изделий, труб, машин, хирургических инструментов, конструктивных элементов и приспособлений.
Низкоуглеродистая сталь дешева в производстве, прочна и легкодоступна. Это самый распространенный тип стали в производстве. Его можно дополнительно усилить науглероживанием.
Углеродистая сталь известна своей низкой стоимостью, низкой твердостью, умеренной прочностью, высокой ударной вязкостью, пластичностью и свариваемостью. Он также может быть легко обработан.
Photo by Ibrahim Boran on Unsplash Легированная стальЛегированная сталь изготавливается из стали и ряда сплавов, включая алюминий, хром-кобальт, молибден, никель, вольфрам и ванадий. Каждый компонент сплава придает стали различные свойства, предлагая почти безграничные варианты.
Легированную сталь трудно классифицировать из-за огромного диапазона и разнообразия возможных смесей сплавов.
Этот материал имеет тенденцию быть дорогим из-за более интенсивного производственного процесса, поэтому он не так популярен, как углеродистая сталь. Вы часто найдете легированную сталь в автомобильных деталях, электрическом оборудовании, генераторах, электродвигателях, трубопроводах, корпусах кораблей и ряде других применений.
Легированная сталь может быть науглероженной, т.е. имеет закаленную поверхность, или полностью закаленной насквозь.
Инструментальная стальИнструментальные стали содержат в различных количествах такие сплавы, как вольфрам, молибден, кобальт и ванадий. Как следует из названия, этот тип стали часто используется в инструментах и инструментах благодаря своим износостойким свойствам и ударопрочности.
В инструментальной стали используются различные количества этих сплавов для создания очень прочных и относительно дешевых материалов.
Вы найдете инструментальные стали в инструментах, промышленных инструментах, сверлах и буровом оборудовании, режущем оборудовании, стержнях, рельсах, проволоке, трубах, листах, полосах, клапанах, фитингах, фланцах и во многих коммерческих или промышленных целях.
Нержавеющая сталь, пожалуй, самая известная сталь. Нержавеющая сталь состоит из железа, хрома, никеля, марганца и меди. Он содержит от 10 до 30% хрома, что придает ему тот блеск и устойчивость к коррозии, которыми он так хорошо известен.
Существует три основных типа нержавеющей стали:
- Аустенитная сталь – Немагнитная и не поддается термической обработке. Аустенитная сталь является наиболее распространенной, и ее можно найти в посуде, оборудовании для приготовления пищи, оборудовании для пищевой промышленности, трубопроводах и во многих промышленных целях.
- Ферритная сталь – Тип нержавеющей стали с никелевыми, хромовыми, углеродными и другими сплавами. Его нельзя подвергать термической обработке, но можно подвергать холодной обработке.
- Мартенситный – Мартенситная сталь содержит от 11 до 17 % хрома, менее 0,4 % никеля и до 1,2 % углерода.
Эта сталь поддается термообработке и является магнитной. Вы часто найдете его в кухонной утвари, ножах, хирургическом оборудовании, режущих инструментах и продуктах, где требуется твердость по сравнению с другими характеристиками.
Нержавеющая сталь представлена более чем сотней различных марок, охватывающих все области производства и продукции. Система классификации стали одновременно проста и сложна и включает системы Британских стандартов, Международной организации по стандартизации (ISO), Европейского стандарта (EN) и других организаций.
Обычно мы используем систему оценок AISI/SAE, в которой используются три числа. Например, нержавеющая сталь 316. Само по себе оценивание заняло бы более одного поста в блоге, поэтому мы оставим его там!
Типы стали и их использование [Полное руководство]
СтальТипы стали и их использование:- В основном существует четыре типа стали: ( Типы металлов )
- Нержавеющая сталь
- Углеродистая сталь
- Легированная сталь
- Инструментальная сталь
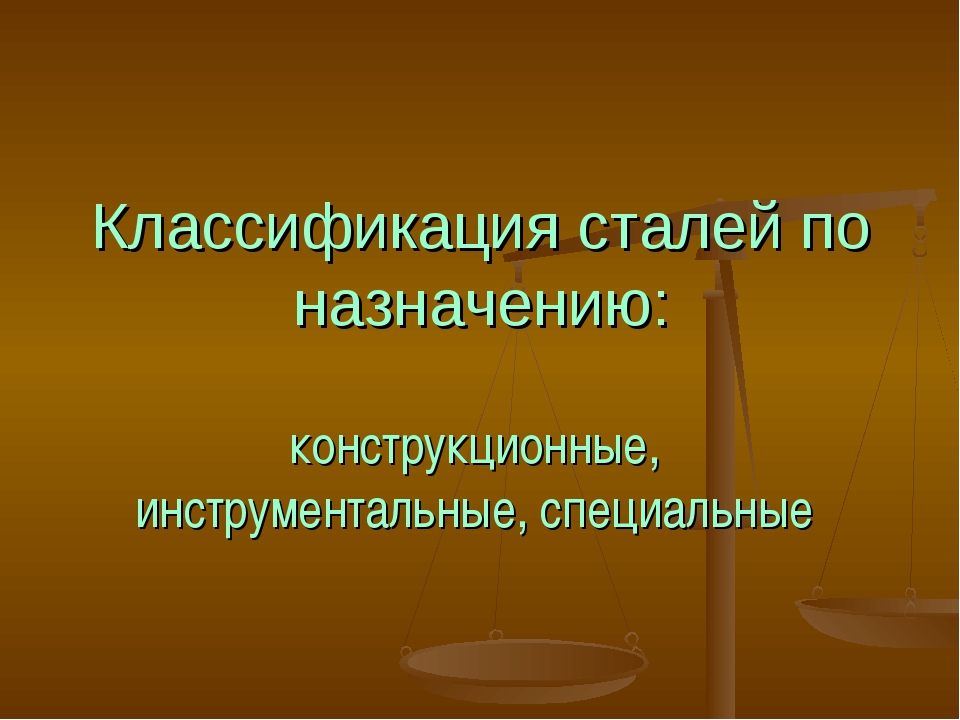
Нержавеющая сталь очень популярна среди всех типов сталей. Он блестящий на вид и содержит от 10 до 20 процентов хрома в качестве сплава. Использование хрома в качестве сплава предотвращает коррозию стали и позволяет легко придавать ей различные формы. Благодаря своей пластичности и гибкости нержавеющая сталь лучше всего подходит для изготовления столового серебра, бытового применения, хирургического оборудования и т. д.
Нержавеющая сталь бывает четырех различных типов:
a) Ферритная стальФерритная нержавеющая сталь, в которой процентное содержание хрома составляет от 10,5 до 30 процентов. Этот тип стали не имеет содержания углерода более 0,1%. Он имеет магнитную природу и обладает высокой устойчивостью к температурному окислению, а также к коррозионному растрескиванию под напряжением.
b) Аустенитная сталь Аустенитная сталь – очень распространенный тип нержавеющей стали с высоким содержанием никеля, молибдена и хрома. Аустенитный используется там, где требуется высокая ковкость и прочность.
Эта сталь имеет высокое содержание углерода, составляющее около 1,2 процента, но структурно она подобна ферритной стали. Благодаря высокому содержанию углерода они могут быть сильно закалены. Они хорошо подходят для хирургических инструментов и медицинских инструментов.
d) ДуплексВ этом типе нержавеющей стали аустенитная нержавеющая сталь сочетается с ферритной нержавеющей сталью, в результате чего получается металл, более прочный, чем мягкая сталь, а также углеродистая сталь. Благодаря своей коррозионной стойкости они хорошо подходят для морских применений.
2. Углеродистая сталь: (Типы стали) Углеродистая сталь имеет матовый вид и матовую текстуру. Углеродистая сталь очень подвержена коррозии. Углеродистая сталь состоит из меньшего количества легирующих элементов и очень прочна, поэтому углеродистые стали используются для изготовления автомобильных деталей, проволоки высокого напряжения, ножей и различных изделий. Углеродистые стали делятся на три категории в зависимости от содержания углерода.
Три различных типа углеродистой стали:
a) Низкоуглеродистая стальНизкоуглеродистая сталь также известна как мягкая сталь. Как правило, в низкоуглеродистой стали содержание углерода составляет от 0,04 до 0,30 процента. Эта сталь встречается в нескольких формах, от конструкционных балок до плоских листов. Для получения желаемых свойств стали в конструкционной стали повышают уровень углерода. Уровень углерода обычно поддерживается низким, когда требуется более пластичная сталь или когда вводится алюминий.
б) Среднеуглеродистая сталь Среднеуглеродистая сталь содержит углерод в диапазоне от 0,31% до 0,60%. Оно имеет содержание марганца между 0. 06 процентами к 1. 65 процентам. Среднеуглеродистая сталь обладает большей прочностью, чем низкоуглеродистая сталь, благодаря более высокому процентному содержанию углерода. Такие операции, как формовка, резка и сварка, для среднеуглеродистой стали затруднены, поскольку с увеличением содержания углерода снижается пластичность. Поскольку среднеуглеродистая сталь обычно тверже, ее закаляют путем термической обработки.
Высокоуглеродистая сталь также известна как углеродистая инструментальная сталь, и содержание углерода в этой стали варьируется от 0,61 процента до 1,50 процента. Эту сталь трудно сгибать, резать и сваривать из-за высокого содержания углерода. После нагрева высокоуглеродистая сталь становится как хрупкой, так и твердой.
3. Легированная сталь: (Типы стали)Легированная сталь представляет собой смесь различных металлов, таких как медь, никель и алюминий. Он дешевле и устойчив к коррозии, поэтому используется в трубопроводах, автомобильных деталях, механических конструкциях и корпусах кораблей. Их прочность определяется процентным содержанием различных металлов, содержащихся в легированной стали.
Легированная сталь различных типов:
- Низколегированная сталь
- Высокопрочная низколегированная сталь
- Высоколегированная сталь
- Нержавеющая сталь
- Микролегированная сталь
- Усовершенствованная высокопрочная сталь
- Стареющая сталь
- Инструментальная сталь
Низколегированная сталь имеет содержание легирующих элементов (нежелезных элементов) менее 8 процентов, а высоколегированная сталь имеет содержание легирующих элементов более 8 процентов. Эта сталь имеет лучшие механические свойства по сравнению с углеродистой сталью. Низколегированная сталь обладает высокой прочностью, экономичностью и обрабатываемостью. Низколегированная сталь используется в производстве строительного оборудования, трубопроводов, военной техники, кораблей, конструкционных элементов и т. д.
Высоколегированная сталь очень дорогая в производстве и сложна в обработке, но она обладает высокой ударной вязкостью, твердостью и коррозионной стойкостью, поэтому она лучше всего подходит для химической обработки, конструкционных компонентов, энергетического оборудования и автомобилей.
Единственным недостатком легированной стали является низкая формуемость, обрабатываемость и свариваемость.
4. Инструментальная сталь: ( Типы стали ) Эта сталь твердая. Он устойчив к истиранию и нагреванию. Он обычно используется для изготовления металлических инструментов, таких как молотки. Инструментальная сталь состоит из вольфрама, кобальта и молибдена, поэтому обладает высокой термостойкостью и долговечностью.
Инструментальная сталь бывает следующих типов:
a) Ударопрочная инструментальная стальЭти инструментальные стали обладают очень высокой ударной вязкостью и ударопрочностью, но умеренной износостойкостью. Поэтому содержание углерода поддерживается в диапазоне от 0,45 до 0,60 процента. Основными сплавами, используемыми в ударопрочной инструментальной стали, являются вольфрам, кремний и хром. Кремний полезен для придания прочности ферриту, но его большее количество может привести к сильному обезуглероживанию. Хром обеспечивает твердость, а также износостойкость.
Эта сталь обычно закаливается в масле, но иногда для полного достижения твердости требуется закалка в воде. Они используются для изготовления ударных молотков и даже для таких приложений, как ножницы, а также штампы для посуды.
b) Инструментальная сталь с закалкой в воде Инструментальная сталь с закалкой в воде имеет содержание углерода от 0,60 до 1,40% и в основном представляет собой простую углеродистую инструментальную сталь, поэтому она дешевле. Как правило, они обладают меньшей твердостью, но при увеличении содержания марганца с ванадием и хромом твердость и износостойкость значительно увеличиваются. Инструментальные стали, закаливаемые в воде, имеют низкое содержание углерода, что обеспечивает ударопрочность и ударную вязкость. Они используются для резки низкоуглеродистых сталей, дерева, алюминия и латуни.
Инструментальная сталь для холодной обработки обычно используется для изготовления инструментов, используемых для холодной обработки. Они имеют широкий спектр составов для удовлетворения огромных потребностей. Сплавы, которые в основном используются, это ванадий, хром, хром-ванадий или хром-вольфрам и т. Д. Инструментальная сталь для холодной обработки обладает износостойкостью, ударопрочностью, высокой ударной вязкостью и высокой абразивностью.
Они бывают следующих трех типов:
- Стали воздушной закалки
- Стали, закаливаемые в масле
- Высокоуглеродистые высокохромистые стали
Инструментальная сталь для горячей обработки используется в операциях обработки металлов давлением, таких как прошивка, горячая штамповка, горячее волочение, горячая ковка, штамповка, горячая экструзия и т. д., и рабочая температура составляет более 200 ̊ C до 800 ̊ C. Они обладают различными желательными свойствами, такими как хорошая теплопроводность, коррозионная стойкость; износостойкость, ударная вязкость, потому что они обладают низким содержанием углерода, которое составляет от 0,3 процента до 0,5 процента. Легирующий элемент также присутствует в небольшом количестве.
Сплавы, используемые в инструментальной стали для горячей обработки, включают ванадий, вольфрам, кобальт, хром и т. д. С увеличением содержания вольфрама также увеличивается стойкость к абразивному износу. Это, в свою очередь, снижает устойчивость к тепловому удару. Кобальт повышает устойчивость к эрозии и термическим ударам.
Они подразделяются на три типа:
- Инструментальная хромистая сталь для горячей обработки
- Вольфрамовая инструментальная сталь для горячей обработки
- Инструментальная молибденовая сталь для горячей обработки
В быстрорежущей стали используется высокое содержание легирующих элементов, так как эта сталь используется для высокоскоростной резки металлов. Сплавы, используемые в быстрорежущих сталях, включают в себя кобальт, вольфрам, молибден, хром и т. д. Содержание углерода в быстрорежущих сталях превышает 0,60%. Они обладают высокой твердостью, ударной вязкостью и износостойкостью.
Далее они подразделяются на два типа в зависимости от используемого сплава:
- Вольфрамовая быстрорежущая сталь: Имеют высокое содержание вольфрама с ванадием, хромом.
- Молибденовая быстрорежущая сталь: Имеют в составе молибден, хром, вольфрам, ванадий.
Сталь для форм используется для изготовления форм для пластмасс. Эта сталь подвергается высокому давлению, а также истиранию из-за формовочных порошков. Поэтому поверхность формы должна быть устойчивой к истиранию, а сердцевина формы должна быть ударопрочной. Сталь для пресс-форм представляет собой сталь с низким содержанием углерода, потому что ей требуется высокая ударная вязкость и обрабатываемость.