Клинский станкостроительный завод: Главная / ОАО “Клинский станкостроительный завод”
alexxlab | 09.08.1988 | 0 | Разное
Клинский станкостроительный завод КСЗ
Клинский станкостроительный завод, Московская область, г. Клин
Основание завода
Клинский станкостроительный завод основан в 1897 году австрийским предпринимателем Чепелем, как чугунолитейное и механическое предприятие.
В 1941 году дано было указание эвакуировать Клинский станкостроительный завод в город Белорецк на Южный Урал в Башкирию. Первые эшелоны с людьми и оборудованием прибыли в ноябре.
Под завод было отдано здание Дворца культуры. Несколько месяцев устанавливалось оборудование, а в марте 1942 он начал выпускать продукцию.
Сборочный цех размещался в вестибюле, механический цех – в большом зале. Сцена была убрана. Инструментальный цех занимал помещение буфета, в спортивном зале располагались ремонтные службы главного механика и главного энергетика. Для термического цеха был сооружен пристрой между спортзалом и фойе большого зала. Для «литейки» построили отдельное помещение, где сейчас расположен гараж.
Первыми станками, которые выпустил завод, были фасонно-токарные, предназначенные для обработки снарядных головок. Станок был несовершенным, и вскоре отдел главного конструктора выдал техническую документацию на более совершенные станки. В дальнейшем и эта модель была модернизирована. В месяц сборочный цех собирал и сдавал на склад в готовом виде до 35 таких станков.
В 1943 году завод получил заказ на выпуск еще двух видов станков. Один из них был универсальным, на нем можно было соединять снаряды с гильзами для пушек калибром от 37 до 45 мм. Одновременно был налажен выпуск станков для запрессовки пыжей в снарядные гильзы. Станок тоже был универсальным и предназначался для широкого диапазона гильз.
Официально на заводе был установлен одиннадцатичасовой рабочий день, но работать приходилось больше: из-за недостатка людей и большого плана выпуска станков он обычно продолжался по 16 часов. В конце месяца, бывало, и не выходили из цеха до тех пор, пока не справлялись с поставленной задачей.
В конце 1944 года пришел приказ завод демонтировать и вывезти его в Витебск, где на его базе был создан завод по производству шлифовальных станков.
Сборочный цех продолжал работать до января 1945 года, а затем и его оборудование было отправлено обратно в Клин.
В 1963 году завод вошёл в состав Министерства станкоинструментальной промышленности СССР и определился приоритетный профиль деятельности – производство вертикальных зубодолбёжных полуавтоматов с максимальным диаметром от 800 до 1000 мм., включая станки, оснащённые системой УЦИ.
Первые долбежные станки 5Б150, 5В150, 5В161, 5В161 завод производил по документации Егорьевского станкостроительного завода “Комсомолец”.
До распада СССР распределение производственных предприятий по номенклатуре выпускаемого зубообрабатывающего оборудования было следующим:
- Витебский станкозавод им. Коминтерна, с 2002 года ВИСТАН
- Егорьевский станкозавод «Комсомолец – производил зубофрезерные и зубодолбежные станки в диапазоне от Ø 250 до 1250 мм;
- Клинский станкозавод изготавливал зубодолбежные станки в диапазоне от Ø 800 до 2240 мм;
- Коломенский завод тяжелого станкостроения — зубофрезерные станки в диапазоне от Ø 2000 до 12500 мм.
- Саратовский завод тяжелых зуборезных станков — станки для производства конических зубчатых колес в диапазоне от Ø 320 до 1600 мм;
- Саратовский завод зубострогальных станков, СЗЗС — зубофрезерные и зубострогальные станки в диапазоне до Ø 125 мм.
- Корсунь-Шевченковский станкозавод им. Б. Хмельницкого – зубодолбежные станки с размером обрабатываемых деталей до Ø 250 мм;
- Московский станкостроительный завод – зубошлифовальные, шлицешлифовальные, рейкошлифовальные;
- Вильнюсский станкостроительный завод им. 40-летия Октября – зубофрезерные станки повышенной точности.
Наши дни
Завод имеет высокоточный станочный парк, включая уникальный зубофрезерный Мастер-Станок модели 543 ЭНИМС для делительных червяных колёс.
с 11.07.1996 ОАО Клинский станкостроительный завод, присвоен ИНН 5020006465, КПП 502001001, ОГРН 1025002589908, ОКПО 00221474.
В 1990-е годы было ликвидировано Министерство инструментальной и станкостроительной промышленности, не стало госзаказов и завод оказался на грани закрытия.
Завод удалось сохранить, но требовалась модернизация оборудования и новые заказы. Большая часть станков оказалась на консервации.
с 11 ноября 2002 АО Клинский станкостроительный завод.
Ещё в 2013 году были заказы от БелАЗ на станки и детали, на насосы для буровой скважины.
Сейчас большая часть площадей завода сдаётся под производства, а заводоуправление – под офисы.
Краткая справка
Клинский станкостроительный завод, г. Клин, Волоколамское ш., д. 25
Клинский станкостроительный завод, Московская область, г. Клин
Станки, выпускаемые Клинским станкостроительным заводом, КСЗ
- 5В150 – станок зубодолбежный вертикальный полуавтомат Ø 800
- 5М150 – станок зубодолбежный вертикальный полуавтомат Ø 800
- 5М161 – станок зубодолбежный вертикальный полуавтомат Ø 1250
- 5М161 – Станок зубодолбежный – наибольший диаметр изделия: 1250 мм, Наибольший модуль 12 мм
- 5М161П – Станок зубодолбежный – наибольший диаметр изделия: 1250 мм, Наибольший модуль 12 мм
- 5М150ПФ3 – Станок зубодолбежный с ЧПУ
- 5М150ПМФ4 – Станок зубодолбежный с ЧПУ
- 5М161ПМФ4 – Станок зубодолбежный с ЧПУ
- КСЗ-52М – Станок зубодолбежный – с увеличенной высотой обработки
Клинский станкостроительный завод.
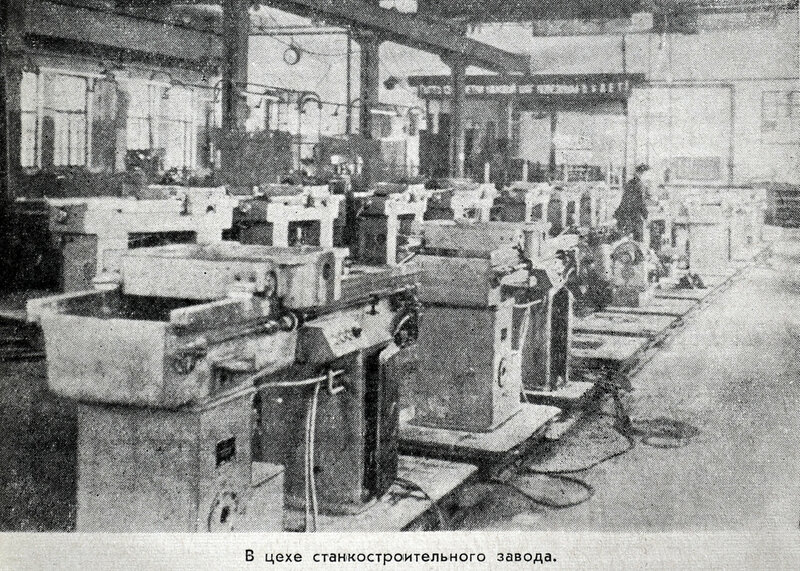
Полезные ссылки по теме
ООО “КЛИНСКИЙ СТАНКОСТРОИТЕЛЬНЫЙ ЗАВОД” ИНН 5020082635 в г Клин – выписка из ЕГРЮЛ и проверка ОГРН 1175007007230, отзывы и контакты на Выписка-Налог
ООО “КЛИНСКИЙ СТАНКОСТРОИТЕЛЬНЫЙ ЗАВОД” ИНН 5020082635 в г Клин – выписка из ЕГРЮЛ и проверка ОГРН 1175007007230, отзывы и контакты на Выписка-НалогГлавная
>
Юридические лица
>
Московская область
>
г Клин
>
68. 20
>
ООО “КЛИНСКИЙ СТАНКОСТРОИТЕЛЬНЫЙ ЗАВОД” ИНН 5020082635
ИНН: 5020082635, Адрес: Московская обл, г Клин, Волоколамское шоссе, д 25 к 1, оф 301
Сводка Надежность Выручка Проверки Контакты Генеральный директор Суды Отзывы Реквизиты
Сводка
Организация ОБЩЕСТВО С ОГРАНИЧЕННОЙ ОТВЕТСТВЕННОСТЬЮ “КЛИНСКИЙ СТАНКОСТРОИТЕЛЬНЫЙ ЗАВОД” из г Клин по которой в сервисе Выписка Налог можно получить выписку с эцп или проверить организацию на надежность и платежеспособность, имеет реквизиты для проверки в нашей базе фирм ИНН 5020082635, ОГРН 1175007007230 и официальный офис компании находится по адресу Московская обл, г Клин, Волоколамское шоссе, д 25 к 1, оф 301. Так же можно узнать данные о регистрации в налоговой инспекции и дату создания компании, сведения о постановке в ПФР и ФСС, прибыль организации и бухгалтерский баланс
Данные юридического лица ИНН 5020082635 ОГРН 1175007007230
Общие сведения | |
---|---|
Наименование компании | ООО “КЛИНСКИЙ СТАНКОСТРОИТЕЛЬНЫЙ ЗАВОД” |
Адрес одной строкой (может отличаться от записанного в ЕГРЮЛ) | Московская обл, г Клин, Волоколамское шоссе, д 25 к 1, оф 301 |
Адрес одной строкой как в ЕГРЮЛ | 141607, ОБЛАСТЬ МОСКОВСКАЯ, ГОРОД КЛИН, ШОССЕ ВОЛОКОЛАМСКОЕ, ДОМ 25, КОРПУС 1, ОФИС 301 |
Количество филиалов | 0 |
Тип подразделения | Головная организация |
Тип организации | Юридическое лицо |
ИНН Что это? | 5020082635 |
КПП Что это? | 502001001 |
ОГРН Что это? | 1175007007230 |
Код ОКВЭД Что это? | 68.![]() |
Версия справочника ОКВЭД | 2014 |
Дата выдачи ОГРН | 2013-08-08 |
Руководитель | |
ФИО руководителя | Матвеев Михаил Викторович |
Должность руководителя | ГЕНЕРАЛЬНЫЙ ДИРЕКТОР |
Наименование | |
Полное наименование с ОПФ | ОБЩЕСТВО С ОГРАНИЧЕННОЙ ОТВЕТСТВЕННОСТЬЮ “КЛИНСКИЙ СТАНКОСТРОИТЕЛЬНЫЙ ЗАВОД” |
Краткое наименование с ОПФ | ООО “КЛИНСКИЙ СТАНКОСТРОИТЕЛЬНЫЙ ЗАВОД” |
Полное наименование | КЛИНСКИЙ СТАНКОСТРОИТЕЛЬНЫЙ ЗАВОД |
Краткое наименование | КЛИНСКИЙ СТАНКОСТРОИТЕЛЬНЫЙ ЗАВОД |
Организационно-правовая форма | |
Код ОКОПФ Что это? | 12300 |
Полное название ОПФ | Общество с ограниченной ответственностью |
Краткое название ОПФ | ООО |
Версия справочника ОКОПФ | 2014 |
Состояние | |
Дата актуальности сведений | 2020-03-24 |
Дата регистрации | 2017-05-29 |
Статус организации | Действующая |
Коды ОКВЭД | |
68.![]() | Аренда и управление собственным или арендованным недвижимым имуществом |
16.23 (доп) | Производство прочих деревянных строительных конструкций и столярных изделий |
25.99 (доп) | Производство прочих готовых металлических изделий, не включенных в другие группировки |
28.41 (доп) | Производство металлообрабатывающего оборудования |
41.20 (доп) | Строительство жилых и нежилых зданий |
47.99 (доп) | Торговля розничная прочая вне магазинов, палаток, рынков |
ИФНС регистрации | |
Код отделения | 5081 |
Наименование отделения | Межрайонная инспекция Федеральной налоговой службы №23 по Московской области |
Адрес отделения | 144000,РОССИЯ,МОСКОВСКАЯ ОБЛ,,ЭЛЕКТРОСТАЛЬ Г,,СОВЕТСКАЯ УЛ,26А,, |
ИФНС отчётности | |
Код отделения | 5020 |
Наименование отделения | Инспекция Федеральной налоговой службы по г.![]() |
Отделение Пенсионного фонда | |
Код отделения | 060020 |
Наименование отделения | Государственное учреждение – Управление Пенсионного фонда РФ №23 Клинский район Московской области |
Отделение Фонда соц. страхования | |
Код отделения | 5037 |
Наименование отделения | Филиал №37 Государственного учреждения – Московского областного регионального отделения Фонда социального страхования Российской Федерации |
ООО “КЛИНСКИЙ СТАНКОСТРОИТЕЛЬНЫЙ ЗАВОД” на Карте России
Получить полный отчет
по компании
ООО “КЛИНСКИЙ СТАНКОСТРОИТЕЛЬНЫЙ ЗАВОД”
Получено %
- Численность сотрудников
- Руководители
- Бух отчетность
- Возраст на рынке
- Положение на рынке
- Финансовое положение
- Связанные компании
- Участие в торгах
- Штрафы
Теперь акт о приемке выполненных работ можно подписывать и представлят.
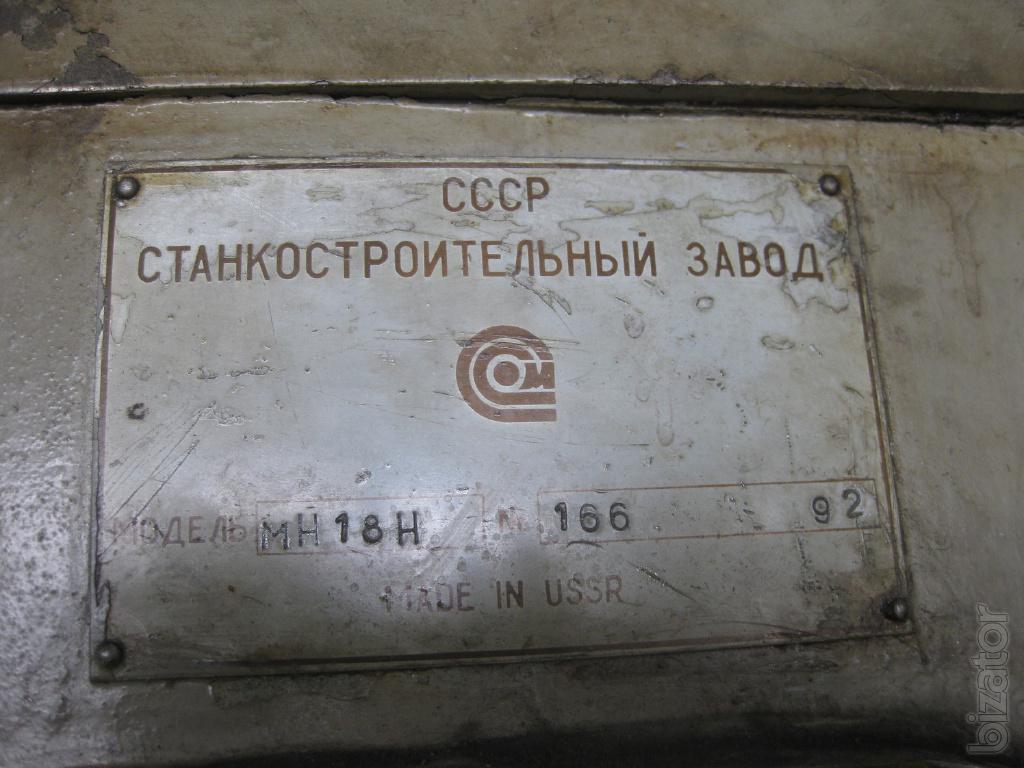
ФНС России утвердила формат акта о приемке выполненных работ. Он формируется по результата…
2022-09-26 08:48:43
Какие изменения учтены при расчете земельного налога для физических ли…
При расчете земельного налога за 2021 год в отношении земельных участков, находящихся в со…
2022-09-20 09:17:34
На сайте ФНС России актуализированы адреса проведения ВКС с налоговыми…
В разделе «Досудебное урегулирование споров» актуализирован перечень налоговых орга…
2022-09-21 08:36:53
Смотреть все новости
Источники информации для сбора данных
Образец полного отчета по компании
Банковские операции
Информация об оборотных суммах, количеству и дате прихода-ухода денежных средств. Оценка рискованности.
Бухгалтерская отчетность
Сведения о лицензиях, виды деятельности. Сводные планы проверок Генпрокуратуры.
Наличие гос.контрактов
Номера контрактов, суммы и сроки исполнения. Информация об участии в гос.закупках, реестр опубликованых заказов
Информация об учредителях
Адреса, телефоны, наименования держателей реестра акционеров. Информация об учрежденных организациях и руководстве.
Вносимые изменения в реестре
Список арбитражных управляющих и арбиртажная практика
Наличие задолженностей
Информация о задолженностях по заработной плате, задолженностях по платежам в бюджет, черный список работодателей
ООО “КЛИНСКИЙ СТАНКОСТРОИТЕЛЬНЫЙ ЗАВОД”
5020082635, Московская обл, г Клин, Волоколамское шоссе, д 25 к 1, оф 301
+ Выписка из ЕГРЮЛ/ЕГРИП c ЭЦП
Телефон
Я прочитал и согласен с пользовательским соглашением
Оплата при помощи удобного сервиса
Похожие на ООО “КЛИНСКИЙ СТАНКОСТРОИТЕЛЬНЫЙ ЗАВОД” компании
ООО “ЮПБ ДОВЕРИТЕЛЬНОЕ УПРАВЛЕНИЕ”
5020082547
ИП Головлев Светозар Владимирович
502009195873
ИП Юлдашева Лиана Петровна
502009070458
ИП Колесников Руслан Николаевич
502008491534
ИП Демкин Сергей Николаевич
502008104915
ИП Пырчев Сергей Владимирович
132707218550
ИП Гаджиев Валерий Валерьевич
502000090026
ИП Камышов Дмитрий Иванович
502000006419
ИП Ильин Владимир Валентинович
502000049740
Другие компании в г Клин
ИП Гусейнов Рауф Гусейн Оглы
502008344530
ИП Бедина Елена Анатольевна
502009090101
ИП Норец Алексей Станиславович
502008629013
ООО “МАКСИМУС”
5020085185
ИП Дыжин Артём Викторович
502009264252
ООО “ТИДЖИСЕРВИС”
5020083011
Московская область популярные компании с выпиской ЕГРЮЛ
ИП Гусейнов Рауф Гусейн Оглы
502008344530
ИП Бедина Елена Анатольевна
502009090101
ИП Норец Алексей Станиславович
502008629013
ООО “МАКСИМУС”
5020085185
ИП Дыжин Артём Викторович
502009264252
ООО “ТИДЖИСЕРВИС”
5020083011
Все данные о интересующей вас компании вы можете получить в полном отчете ФНС у нас на странице
ООО КЛИНСКИЙ СТАНКОСТРОИТЕЛЬНЫЙ ЗАВОД, Клин (ИНН 5020082635), реквизиты, выписка из ЕГРЮЛ, адрес, почта, сайт, телефон, финансовые показатели
Обновить браузер
Обновить браузер
Возможности
Интеграция
О системе
Статистика
Контакты
CfDJ8No4r7_PxytLmCxRl2AprPrFwfNGJIAIUKtxC-5pg-oIoErlX9rEnCEu6GiUCgjJr_UNIZ5b-6TrqrWMbtgajJJ8dcWW_rDiqiODJGWwaH57WU1c6QEJJRMn9xh2xNNyXnluAp9BIyvRzkV4vOz6oaY
Описание поисковой системы
энциклопедия поиска
ИНН
ОГРН
Санкционные списки
Поиск компаний
Руководитель организации
Судебные дела
Проверка аффилированности
Исполнительные производства
Реквизиты организации
Сведения о бенефициарах
Расчетный счет организации
Оценка кредитных рисков
Проверка блокировки расчетного счета
Численность сотрудников
Уставной капитал организации
Проверка на банкротство
Дата регистрации
Проверка контрагента по ИНН
КПП
ОКПО
Тендеры и госзакупки
Юридический адрес
Анализ финансового состояния
Учредители организации
Бухгалтерская отчетность
ОКТМО
ОКВЭД
Сравнение компаний
Проверка лицензии
Выписка из ЕГРЮЛ
Анализ конкурентов
Сайт организации
ОКОПФ
Сведения о регистрации
ОКФС
Филиалы и представительства
ОКОГУ
ОКАТО
Реестр недобросовестных поставщиков
Рейтинг компании
Проверь себя и контрагента
Должная осмотрительность
Банковские лицензии
Скоринг контрагентов
Лицензии на алкоголь
Мониторинг СМИ
Признаки хозяйственной деятельности
Репутационные риски
Комплаенс
Компания ООО КЛИНСКИЙ СТАНКОСТРОИТЕЛЬНЫЙ ЗАВОД, адрес: Московская обл. , г. Клин, шоссе Волоколамское, д. 25 к. 1 офис 301 зарегистрирована 29.05.2017. Организации присвоены ИНН 5020082635, ОГРН 1175007007230, КПП 502001001. Основным видом деятельности является аренда и управление собственным или арендованным недвижимым имуществом, всего зарегистрировано 11 видов деятельности по ОКВЭД. Связи с другими компаниями отсутствуют.
Количество совладельцев (по данным ЕГРЮЛ): 1, генеральный директор – Матвеев Михаил Викторович. Размер уставного капитала 10 000₽.
Компания ООО КЛИНСКИЙ СТАНКОСТРОИТЕЛЬНЫЙ ЗАВОД не принимала участие в тендерах. В отношении компании нет исполнительных производств. ООО КЛИНСКИЙ СТАНКОСТРОИТЕЛЬНЫЙ ЗАВОД не участвовало в арбитражных делах.
Реквизиты ООО КЛИНСКИЙ СТАНКОСТРОИТЕЛЬНЫЙ ЗАВОД, юридический адрес, официальный сайт и выписка ЕГРЮЛ доступны в системе СПАРК (демо-доступ бесплатно).
Полная проверка контрагентов в СПАРКе
- Неоплаченные долги
- Арбитражные дела
- Связи
- Реорганизации и банкротства
- Прочие факторы риска
Полная информация о компании ООО КЛИНСКИЙ СТАНКОСТРОИТЕЛЬНЫЙ ЗАВОД
299₽
- Регистрационные данные компании
- Руководитель и основные владельцы
- Контактная информация
- Факторы риска
- Признаки хозяйственной деятельности
- Ключевые финансовые показатели в динамике
- Проверка по реестрам ФНС
Купить Пример
999₽
Включен мониторинг изменений на год
- Регистрационные данные компании
- История изменения руководителей, наименования, адреса
- Полный список адресов, телефонов, сайтов
- Данные о совладельцах из различных источников
- Связанные компании
- Сведения о деятельности
- Финансовая отчетность за несколько лет
- Оценка финансового состояния
Купить Пример
Бесплатно
- Отчет с полной информацией — СПАРК-ПРОФИЛЬ
- Добавление контактных данных: телефон, сайт, почта
- Добавление описания деятельности компании
- Загрузка логотипа
- Загрузка документов
Редактировать данные
СПАРК-Риски для 1С
Оценка надежности и мониторинг контрагентов
Узнать подробности
Заявка на демо-доступ
Заявки с указанием корпоративных email рассматриваются быстрее.
Вход в систему будет возможен только с IP-адреса, с которого подали заявку.
Компания
Телефон
Вышлем код подтверждения
Эл. почта
Вышлем ссылку для входа
Нажимая кнопку, вы соглашаетесь с правилами использования и обработкой персональных данных
Американское производство | Klein Tools
С 1857 года Klein Tools производит инструменты в Америке, и для семьи Кляйн так же важно сохранить эту традицию сейчас, как и более 150 лет назад. Видите ли, Кляйн — это не просто название нашей компании; это также наша фамилия, поэтому мы должны гордиться всем, что делаем.
Члены семьи Кляйн в пятом и шестом поколении продолжают наследие Klein Tools.
В наши дни трудно найти компании, производящие продукцию, на которую можно положиться. Но это именно то, что вы получите от Klein Tools.
Мы не просто делаем отличные продукты; мы производим отличные продукты, отвечающие требованиям профессионалов, использующих их каждый день. Поскольку наши стандарты так же высоки, как и ваши, мы требуем, чтобы каждый из наших ручных инструментов обладал всеми характеристиками, надежностью и точностью, необходимыми для качественного выполнения работы.
И, используя только материалы высочайшего качества, превосходное качество изготовления и размещая наше производство как можно ближе к дому, мы можем поддерживать эти строгие стандарты.
Klein Tools продолжает инвестировать в производство в США и стремится сохранить свое место в качестве фаворита среди электриков. Klein — единственный в мире крупный производитель инструментов, ориентированный на применение в электротехнике и коммунальном хозяйстве. Ни один другой производитель ручных инструментов и сопутствующих товаров, используемых в электротехнике, не производит в Америке больше изделий, чем Klein Tools. Мы ценим ваш бизнес и интерес к Klein Tools и надеемся, что информация на этой странице ответит на ваши вопросы о нашей приверженности производству в США.
Сотрудники Klein Tools перерезали ленточку на новом предприятии по термообработке в Мэнсфилде, штат Техас, апрель 2014 г.
Часто задаваемые вопросы
В: Какие обязательства Klein Tools взяла на себя перед американским производством?
О: Компания Klein Tools была основана в США в 1857 году. Мы постоянно инвестируем в наши производственные мощности в США по мере расширения наших производственных линий. За последние 10 лет подавляющее большинство наших инвестиций было направлено на увеличение наших производственных мощностей в США. Кроме того, хотя мы недавно построили несколько новых объектов, мы также продолжаем инвестировать в наши существующие заводы, чтобы поддерживать инициативы по улучшению качества продукции и производительности. Будущие запланированные инвестиции в размере более 100 миллионов долларов США позволят нам производить в США некоторые продукты, которые мы в настоящее время поставляем, а также производить новые продукты американского производства, которые в противном случае были бы импортированы без этих инвестиций.
В: Что означает «Сделано в США»?
A: Когда на наших продуктах написано «Сделано в США», они на самом деле сделаны в США. Неправильное указание страны происхождения продукта является незаконным. Согласно FTC, «для того, чтобы продукт мог называться «Сделано в США» или быть заявленным как отечественное происхождение без каких-либо оговорок или ограничений в заявлении, продукт должен быть «полностью или практически полностью» произведен в США. ‘, как указано в Заявлении о правоприменительной политике, включает 50 штатов, округ Колумбия, а также территории и владения США». Вы можете узнать больше здесь.
В: Сколько ваших инструментов произведено в США?
О: Подавляющее большинство продаваемой нами продукции производится в США. Точный процент часто меняется, поскольку мы поставляем некоторые продукты на наши заводы в США и добавляем новые продукты в нашу линейку. В последние годы компания Klein представила много новых товаров, произведенных в США (отверстия, отвертки, рыболовные ленты, универсальные гаечные ключи, ведра, сумки и т. д.). За последнее десятилетие мы вложили средства в четыре новых производственных предприятия в США, а также вложили значительные средства в новое оборудование и инструменты на наших заводах, чтобы увеличить наши мощности и качество.
В: Почему некоторые из ваших инструментов производятся за границей?
О: Как и большинство мировых компаний, мы закупаем некоторые продукты за границей, но Klein Tools производит в США в 14 раз больше продукции, чем в любой другой стране. Для любого из наших аутсорсинговых продуктов мы вкладываем наше время и деньги в дизайн и качество этих продуктов, поэтому, когда вы покупаете инструмент Кляйна, вы знаете то, что знают все профессионалы… когда вы берете в руки инструмент Кляйна, он никогда не подведи тебя.
Мы живем в международной бизнес-среде, и Klein расширяет свою деятельность по всему миру, продавая продукцию, произведенную в США. Хотя мы хотели бы производить каждый продукт, который мы продаем, в США, это просто невозможно. Тем не менее, Klein Tools производит больше наименований инструментов, используемых в электротехнике здесь, в Соединенных Штатах, чем любой из наших конкурентов.
За некоторыми исключениями, если таковые имеются, продукты, которые мы поставляем, являются новыми дополнениями к нашей линейке или инструментами, которые у нас могут не быть возможности производить самостоятельно немедленно. Наша работа состоит в том, чтобы снабжать американских торговцев лучшими инструментами, доступными в любой точке мира, и мы сами производим эти инструменты в США, когда это возможно.
В: Klein Tools отправляет заказы за границу?
О: Klein Tools никогда не закрывала производственные предприятия в Соединенных Штатах и не отправляла рабочие места за границу, и мы не собираемся делать это в будущем.
Вы можете узнать больше о Klein Tools и ее приверженности производству в США в Интернете на сайте ProTools Review или щелкнув значок справа.
Klein Tools управляет следующими заводами в США:
-
Линкольншир, Иллинойс • СШАПродажи, маркетинг, обслуживание клиентов, разработка продуктов, ИТ и администрирование
-
Мэнсфилд, Техас • СШАРазработка продуктов, ИТ и администрирование
-
Мэнсфилд, Техас • СШАПроизводит отвертки, гаечные ключи и ленты; Всемирный дистрибьюторский центр.
-
Элк-Гроув-Виллидж, Иллинойс • СШАПроизводство инструментальных поковок из высококачественной запатентованной инструментальной стали
-
Форт-Смит, Арканзас • СШАПроизводство изделий из кожи и холста
-
Боливар, Нью-Йорк • СШАПроизводство высококачественных ножниц и других столовых приборов
Klein Tools de Mexico управляет заводом в Мехико с 1970 года. Этот завод производит продукцию для рынков Мексики и Центральной Америки. Несколько инструментов, которые производятся здесь, продаются в США, например, наши нокаутирующие удары, но по большей части продукты мексиканского производства потребляются в Мексике.
Установка гранулирования с колосниковой печью – Metso Outotec
Дом Полное портфолио Завод гранулирования с колосниковой печью
Поставщик оригинальных технологий для систем колосниковой печи
Metso Outotec является первоначальным поставщиком технологий для систем колосниковой печи, приобретя технологию у Allis-Chalmers.
Особенности
Преимущества
Системы Grate Kiln состоят из трех основных частей оборудования.
Обзор процесса
Колосниковая печь состоит из трех основных частей оборудования. Решетка, печь и охладитель. Целью процесса является преобразование гранулированного концентрата в твердые окатыши, которые можно использовать в качестве сырья для доменной печи или для печи прямого восстановления.
Передвижная решетка — это место, где пеллеты сушатся, а затем нагреваются до температуры около 800-900°C. Тепло, используемое для сушки и предварительного нагрева пеллет, обычно поступает из печи и охладителя. Рециркуляция горячего воздуха из разных зон повышает энергоэффективность.
В печи окатыши доводятся до температуры окончательной закалки. При вращении печи весь слой окатышей подвергается теплу, излучаемому горелкой, что обеспечивает однородное качество окатышей. Горелка печи использует более холодный отходящий газ для нагрева слоя материала до номинальной температуры 1200-1340 °C, завершая связывание шлака и связывание минералов с образованием окатышей.
В охладителе гранулы доводятся до температуры, подходящей для последующего оборудования для обработки материалов. Газы из охладителя рециркулируются в печь и колосниковую решетку, в результате чего печь с колосниковой решеткой является наиболее энергоэффективной системой для производства твердых гранул.
- Окомкование железной руды
- Подача в доменную печь или установку прямого восстановления
Описание процесса
Передвижная решетка
Подвижная решетка состоит из полотна пластин, соединенных в цепь, по которой гранулы перемещаются подобно конвейеру. Разница в том, что в пластинах цепи решетки есть отверстия, через которые проходит воздух. Цепь решетки движется ровно и прямо. Колосник проходит через печь с несколькими зонами, в которых пеллеты подвергаются разным температурам. Как только пеллеты выгружаются в печь, цепь колосников возвращается вниз. Решетка приводится в движение двигателем с редуктором или гидравлическим приводом. Решетка поддерживается роликами.
Вращающаяся печь
Окончательное отверждение окатышей осуществляется во вращающейся печи, в которой основным механизмом передачи тепла является излучение от основной горелки системы.
Технологическая система спроектирована таким образом, что перемещение материала с колосниковой решетки в печь происходит, когда материал на колосниковой решетке достаточно предварительно нагрет, чтобы иметь необходимую прочность для последующей обработки во вращающейся печи.
Вращающаяся печь представляет собой вращающуюся стальную круглую оболочку с огнеупорной футеровкой. Эта оболочка вращается с помощью приводной шестерни и системы электрического или гидравлического привода. Корпус опирается на большие подшипники. Есть одна большая горелка, которая нагревает пеллеты, когда они проходят через печь.
Кольцевой охладитель
Кольцевой охладитель представляет собой поворотный стол, на котором хранятся горячие гранулы. Окружающий воздух продувается через горячие гранулы. Поворотный стол изготовлен из клиновидных кастрюль. Гранулы падают из печи прямо на противни. Гранулы перемещаются по всему поворотному столу, пока поддон не опрокинется и гранулы не упадут под него. Затем чаша выпрямляется, чтобы принять больше материала. Кулеры поддерживаются роликами.
Сопутствующие товары и услуги
EDITUBE Мокрый электростатический осадитель
EDITUBE WESP — это решение для влажной очистки газов, предназначенное для удаления мельчайших фракций частиц пыли и аэрозолей тумана.
Техническое обслуживание и ремонт
Для оборудования, используемого в горнодобывающей и металлургической промышленности.
Услуги жизненного цикла для майнинга
Для компаний, работающих в горнодобывающей промышленности.
Свяжитесь с местными экспертами по продажам
Ваша информация в безопасности. Ознакомьтесь с нашим уведомлением о конфиденциальности для получения более подробной информации.
Спасибо!
Мы свяжемся с вами в ближайшее время. Вы можете снова отправить новый запрос через 15 минут.
Контакты
RIEDHAMMER – ВЕДУЩИЙ В МИРЕ ПРОИЗВОДИТЕЛЬ ПЕЧЕЙ
С 1924 года ….
RIEDHAMMER’S “GREEN”
Сила сокращения потребления и затрат
Литий-ионные аккумуляторы
>300 печей с роликовым подом для производства литий-ионных аккумуляторов CAM и AAM успешно поставлены в промышленность
Продукты для литий-ионных аккумуляторов
>60 вращающихся печей для производства порошка литий-ионных аккумуляторов успешно поставляются в промышленность
УГЛЕРОД
Наиболее эффективные и надежные решения для выпекания углерода
Современные материалы и техническая керамика
Выдающаяся технология для максимальной производительности
САНТЕХНИКА
Энергоэффективный обжиг керамической сантехники
ОГНЕУПОРНЫЕ ИЗДЕЛИЯ
Высокая температура соответствует высокой эффективности
ПОСУДА
Современные решения для традиционных продуктов
Riedhammer — ведущий мировой производитель печей
Благодаря более чем 95-летнему опыту, инновационным технологиям и передовому опыту в области углерода, керамики и сантехники мы являемся идеальным партнером для клиентов, которым нужны передовые и надежные технологические решения для всех видов обжига. процессы. Мы поставляем и устанавливаем комплексные заводские решения, которые простираются как до, так и после печи по всему миру.
РИДХАММЕР ИЗОБРАЖЕНИЕ ВИДЕО
Брошюра Riedhammer Image
Загрузить брошюру
НОВИНКА: ПРОДАЕТСЯ
RIEDHAMMER ПЕЧЬ НА ЛИТИЙ-ИОННЫХ АККУМУЛЯТОРАХ
Новая/неиспользованная печь с роликовым подом с электрическим подогревом, модель TR36/4X33/2X12-GE110 с газонепроницаемым кожухом печи для обжига ионно-литиевых аккумуляторов Материал CAM, изготовленный в качестве пилотной печи, с возможностью модификации, установки и обслуживания печи Riedhammer по запросу клиента.
Контактное лицо по продажам: HILCO, см. ниже.
Подробнее
Товары и услуги
Литий-ионный аккумулятор
Передовые материалы
Техническая керамика
Углерод
Сантехника
Огнеупорные изделия
Посуда
Реконструкция – модернизация
Услуги и техническая помощь
Литий-ионный аккумулятор
Проектирование, разработка и изготовление машин и оборудования для производства порошковых материалов для литий-ионного аккумулятора.
Подробнее
ПЕРЕДОВЫЕ МАТЕРИАЛЫ
Проектирование, проектирование и строительство машин и комплексных установок для производства передовых материалов.
Подробнее
ТЕХНИЧЕСКАЯ КЕРАМИКА
Проектирование, проектирование и строительство машин и комплексных установок для производства технической керамики и современных материалов.
Подробнее
УГЛЕРОД
Проектирование, проектирование и строительство обжиговых печей для производства анодов и катодов для алюминиевой промышленности и электродов для сталелитейной промышленности.
Подробнее
САНТЕХНИКА
Проектирование, проектирование и изготовление машин и комплексных установок для производства сантехники.
Подробнее
ОГНЕУПОРНЫЕ ИЗДЕЛИЯ
Проектирование, разработка и изготовление машин и комплексных установок для производства огнеупоров.
Подробнее
СТОЛОВАЯ ПОСУДА
Проектирование, проектирование и изготовление машин и комплексных установок для производства посуды.
Подробнее
МОДЕРНИЗАЦИЯ
Реконструкция и модернизация с целью экономии энергии, доочистки отработанных газов, безопасности установки и т. д. как экономичная альтернатива новой установке.
Подробнее
ПОСТАВЩИК РЕШЕНИЙ К ВАШИМ УСЛУГАМ
Компания Riedhammer является партнером по комплексным решениям, предоставляющим вам комплексные услуги по технической поддержке, обучению и запасным частям для вашего конкретного ассортимента продукции.
ТЕХНИЧЕСКАЯ ПОМОЩЬ
Осмотр, техническое обслуживание, инструкции и обучение, совершенствование процессов, консультации, дистанционное управление, управление запасными частями.
Читать далее
ОБУЧЕНИЕ
Инструкции, обучение и консультации.
ЗАПАСНЫЕ ЧАСТИ И ЭЛЕКТРОННЫЕ УСЛУГИ
Поставка запасных частей с онлайн-формой запроса.