Кокиль это литье в: Литье в кокиль | ООО «УПРЗ»
alexxlab | 07.02.2023 | 0 | Разное
41.Литье в кокиль
К о к и л е м называют металлическую форму, заполняемую расплавом под действием гравитационных сил. Сущность способа заключается в применении многократно используемой литейной формы, которая формируют конфигурацию и свойства отливки.
По конструкции кокили бывают: вытряхные (рис.102,а), с вертикальным разъемом (рис.102,б), с горизонтальным разъемом (рис.102,в), створчатые, с комбинированным разъемом, стопочные.
Кокиль изготавливают из серого чугуна, стали, алюминиевого сплава с анодированной рабочей поверхностью (табл.29). Для повышения стойкости кокили изготавливают из нормализованных элементов (пластин), игольчатыми, методами порошковой металлургии.
Толщина стенок кокиля от 10 до 100мм и зависит от толщины стенок отливки. Толщина кокиля должна быть по возможности равномерной. Для повышения стойкости кокиля, а также производительности

При литье в металлические формы применяют как металлические (для простых полостей), так и песчаные литейные стержни (для сложных полостей). Для выталкивания отливки из кокиля используют толкатели диаметром 10-20 мм,
Рис.102. Конструктивные виды кокилей:
а) вытряхной (1-кокиль, 2-стержень песчаный, 3-толкатель), б) с вертикальным разъемом (1-кокиль, 2-стержень песчаный, 3-толкатель, 4-контртолкатель, 5-литниковая система), в) с горизонтальным разъемом (1-кокиль, 2-стержень песчаный, 3-толкатель, 4-контртолкатель, 5-стержень с литниковой системой)
а) б) в)
г) д) е)
Рис. 103
. Последовательность операций изготовления
отливок в кокиль:
а)нанесение на нагретую до 150-180°С рабочую поверхность кокиля с помощью пульверизатора защитной краски; б – установление с помощью манипулятора песчаного стержня; в – заливка расплава в кокиль, половины которого соединены и скреплены специальными зажимами; г – затвердевание до температуры выбивки; д – раскрытие кокиля и протягивание вниз металлического стержня; е – удаление отливки манипулятором. 1 – поддон; 2, 3 – симметричные полуформы; 4 – металлический стержень; 5 – пульверизатор; 6 – песчаный стержень; 7 – отливка
Детали кокиля | Назначение, условия работы | Материал |
Рабочие стенки | Кокили для мелких и средних отливок из алюминиевых сплавов, чугуна, с воздушным и водовоздушным охлаждением Кокили для мелких,
средних, крупных отливок из чугунов
с воздушным и водовоздушным охлаждением. Кокили для мелких, средних, крупных и особо крупных отливок из чугуна, стали, алюминиевых, магниевых, медных сплавов Вставка для интенсивного охлаждения отдельных частей отливок, тонкостенные водоохлаждаемые кокили, массивные металлические стержни. Водоохлаждаемые кокили с анодированной поверхностью для мелких отливок из алюминиевых, медных сплавов, чугунов. | СЧ20, СЧ25 ВЧ40, ВЧ45 Стали 10, 20, 15Л-11, 15ХМЛ, Ст3 Медь и ее сплавы, легированные стали, специальные сплавы АК7 (АЛ9), АК7Ц9 (АЛ11) |
Стержни, штыри, толкатели, тяги | Соприкасаются с жидким металлом, работают на истирание | Сталь 45 |
Стержни, вставки, выталкиватели с резкими переходами в сечениях | Оформляют глубокие
полости и находятся под действием
высоких температур. | 30ХГС, 35ХГСА, 35ХНМ |
Выталкиватели | Испытывают ударные нагрузки | Стали У8А, У10А |
Оси, валы, эксцентрики | Работают на истирание | Сталь 25 (подвергают цементации) |
Рис 104. Стержни:
1 – кокиль; 2 – отливка; 3 – песчаный стержень; 4 – вкладыш; 5 металлический стержень; 6 – плита; 7,8,9- части металлического стержня
которые
изготавливают из углеродистой
стали. Большую
роль при формировании отливки в
металлической форме играет покрытие
рабочей поверхности кокиля огнеупорным
материалом (мел, графит, тальк, глина
огнеупорная, жидкое
стекло и др.
Литье в облицованный кокиль – это отдельный технологический процесс литья в кокиль с толстостенными разовыми покрытиями (облицовками) из термореактивных смесей толщиной 3-10мм.
Литьем в кокиль получают фасонные заготовки из серого, ковкого и высокопрочного чугунов, сталей, алюминиевых, магниевых и медных сплавов.
Литье в кокиль
Оглавление
Введение…………………………………………………………

Сущность способа литья в кокиль………………………………………………………….5
Основные операции технологического процесса литья в кокиль………………………..7
Особенности формирования и качество отливок в кокиле………………………………..9
Эффективность производства и область применения отливок в кокиль…………………11
Классификация конструкций кокилей………………………………………………….….
Отливки в кокиль из алюминиевых сплавов…………………………………………..…..15
Заключение……………………………………………………
Список использованной литературы……………………………………………………
Введение
Литье в кокиль относится к прогрессивным специальным способам литья с большим будущим. Между тем, это один из древних способов изготовления отливок, появившийся чуть ли не на заре возникновения литейного ремесла.

Литейное ремесло в Скифии было высоко развито, об искусстве литья замечательных скифских котлов с восторгом писал Геродот; свидетельством тому служат также многие дошедшие до нашего времени литые изделия.

Что касается археологических находок скифского периода, то они, как и находки периода Борющихся царств (403—221 гг. до н. э.), свидетельствуют об умелом использовании кокилей древними литейщиками.
Пробелы в истории литья в кокиль объясняются не утерей древних секретов, а тем, что в разные периоды отсутствовали благоприятные условия эффективного использования кокилей. Такие условия появились в России в XVI в., когда потребовалось массовое изготовление чугунных пушечных ядер с достаточным воспроизводством размеров и масс.
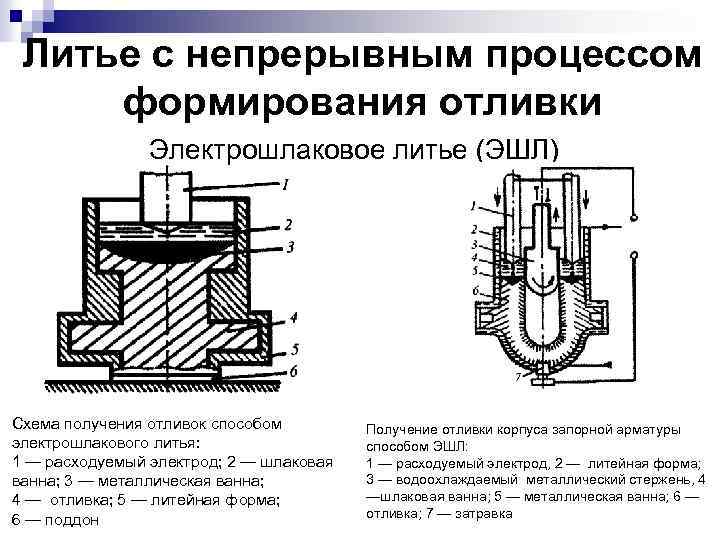
В дальнейшем кокили нашли еще более широкое применение для литья самой разнообразной продукции: вагонных колес, буферов электровозов, тяжелых корпусов редукторов, различной аппаратуры, хозяйственных изделий, тонкостенной посуды и т.

Сущность способа литья в кокиль
Кокиль – металлическая форма, которая заполняется расплавом под действием гравитационных сил. Они являются закрытыми металлическими литейными формами с внутренней полостью, соответствующей форме изделия, и литниковой (заливочной) системой, которые выполняются путем механической обработки в чугунном, бронзовом, алюминиевом или стальном блоке. Кокиль состоит из двух или большего числа деталей, после соединения которых остается лишь небольшое отверстие сверху для заливки расплавленного металла. Для формования внутренних полостей в кокиль закладываются гипсовые, песочные, стеклянные, металлические или керамические «стержни». Методом литья в кокиль получают отливки из сплавов на основе алюминия, меди, цинка, магния, олова и свинца.

Кокили изготавливают из серого (СЧ15, СЧ18, СЧ20, СЧ25) и высокопрочного чугуна (ВЧ 42-12, ВЧ 45-5), конструкционных углеродистых (10, 20, 15Л, 25Л) и легированных (15ХМЛ) сталей, медных (латуни) и алюминиевых (АЛ2, АЛ4, АЛ9, АЛИ, АЛ 12) сплавов. Для изготовления стержней и вставок многократного действия, работающих в условиях воздействия больших тепловых и механических нагрузок, используют легированные стали (ЗОХГС, 35ХГСА, 4Х5МФС и др.). Выталкиватели выполняют из инструментальных сталей (У8А, У10А), поскольку они должны обладать большой твердостью и износостойкостью. Многократность использования формы обусловлена, главным образом, материалом отливки. С помощью одной формы (или большей части ее элементов) кокильным литьем получают до 500 мелких стальных, 5000 чугунных или десятки тысяч алюминиевых отливок. Отдельные элементы кокиля (в первую очередь – стержни, оформляющие внутренние полости отливки) могут изготавливаться как из металла, так и из стержневой смеси; в последнем случае они предназначаются лишь для разового использования.

В отличие от разовой песчаной формы кокиль может быть использован многократно. Таким образом, сущность литья в кокили состоит в применении
Кокиль (рис.1) обычно состоит из двух полуформ (1), плиты (2), вставок (10). Полуформы взаимно центрируются штырями (8), и перед заливкой их соединяют замками (9). Размеры рабочей полости (13) кокиля больше размеров отливки на величину усадки сплава. Полости и отверстия в отливке могут быть выполнены металлическими (11) или песчаными (6) стержнями, извлекаемыми из отливки после ее затвердевания и охлаждения до заданной температуры. Расплав заливают в кокиль через литниковую систему (7), выполненную в его стенках, а питание массивных узлов отливки осуществляется из прибылей (питающих выпоров) (3).

Основные операции технологического процесса литья в кокиль
Перед заливкой расплава новый кокиль подготовляют к работе: поверхность рабочей полости и разъем тщательно очищают от следов загрязнений, ржавчины, масла; проверяют легкость
Затем на поверхность рабочей полости и

После нанесения огнеупорного покрытия кокиль нагревают до рабочей температуры, зависящий в основном от состава заливаемого сплава, толщины стенки отливки, ее размеров, требуемых свойств.
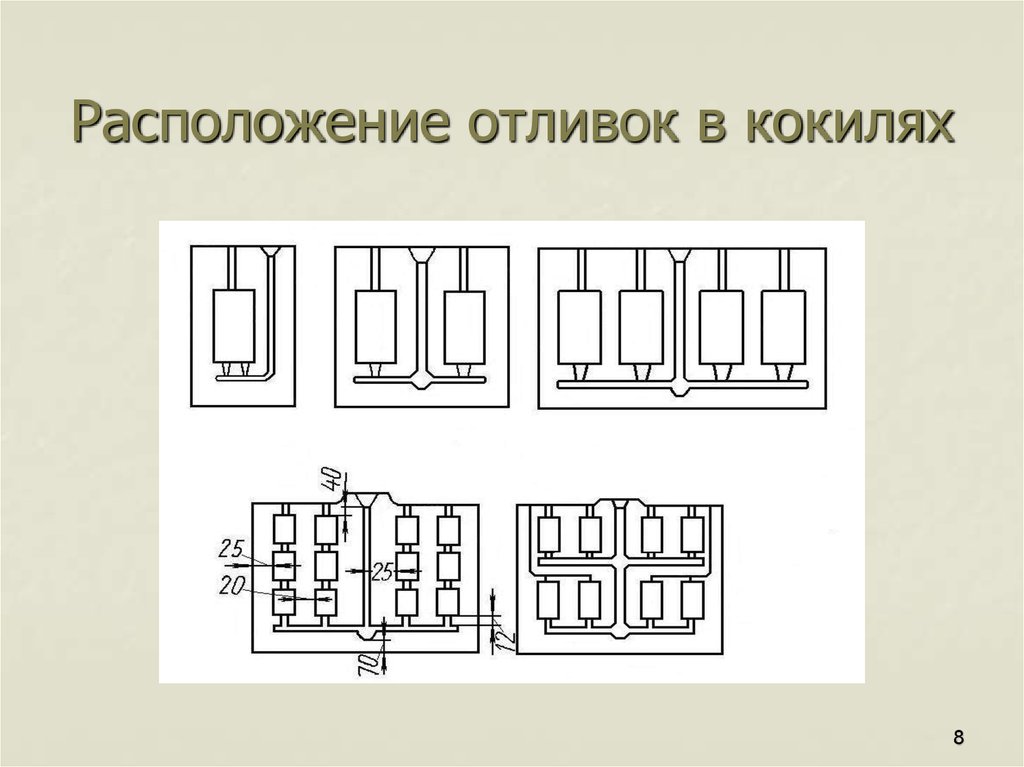
а – очистка полуформ;
б – установка стержней;
в – заливка расплава;
г – частичное удаление металлического стержня;
д – извлечение отливки.
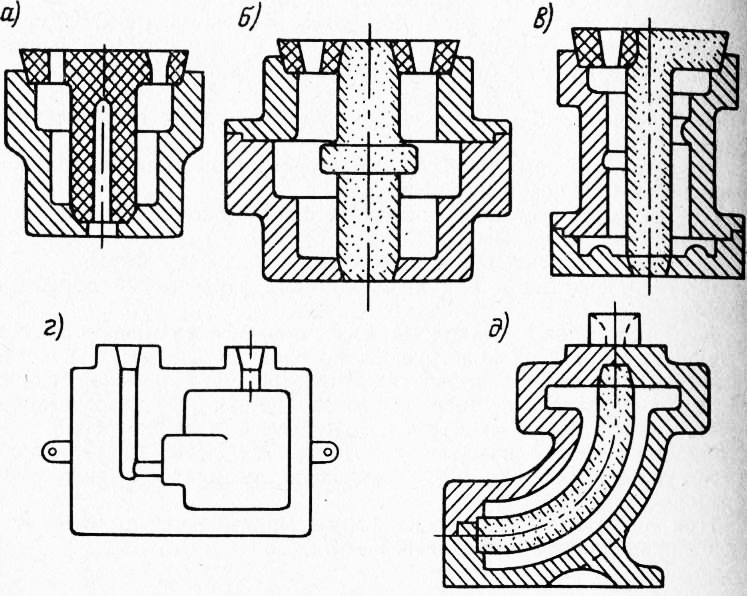
Перед повторением цикла осматривают рабочую поверхность кокиля, плоскость разъема. Обычно огнеупорную краску наносят на рабочую поверхность кокиля 1 – 2 раза в смену, изредка восстанавливая ее в местах, где она отслоилась от рабочей поверхности. После этого при необходимости, что чаще бывает при литье тонкостенных отливок или сплавов с низкой жидкотекучестью, кокиль подогревают до рабочей температуры, так как за время извлечения отливки и окраски рабочей поверхности он охлаждается. Если же отливка достаточно массивная, то, наоборот, кокиль может нагреваться ее теплотой до температуры большей, чем требуемая рабочая, и перед следующей заливкой его охлаждают. Для этого в кокиле предусматривают специальные системы охлаждения.
Как видно, процесс литья в кокиль – малооперационный. Манипуляторные операции достаточно просты и кратковременны, а лимитирующей по продолжительности операцией является охлаждение отливки в форме до заданной температуры. Практически все операции могут быть выполнены механизмами машины или автоматической установки, что является существенным преимуществом способа, и, конечно, самое главное – исключается трудоемкий и материалоемкий процесс изготовления формы: кокиль используется многократно.
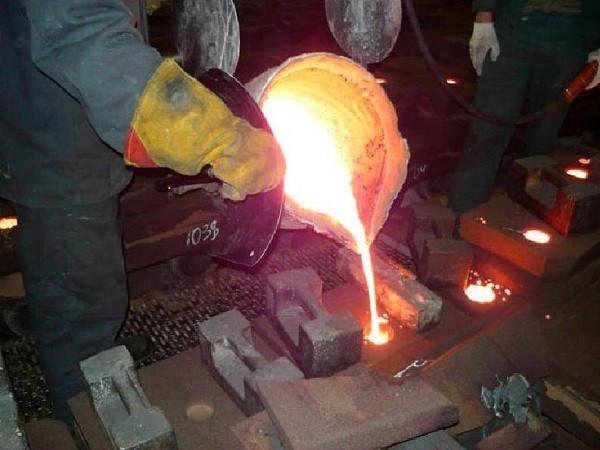
Особенности формирования и качество отливок в кокиле
Кокиль – металлическая форма, обладающая по сравнению с песчаной значительно
1. Высокая эффективность теплового взаимодействия
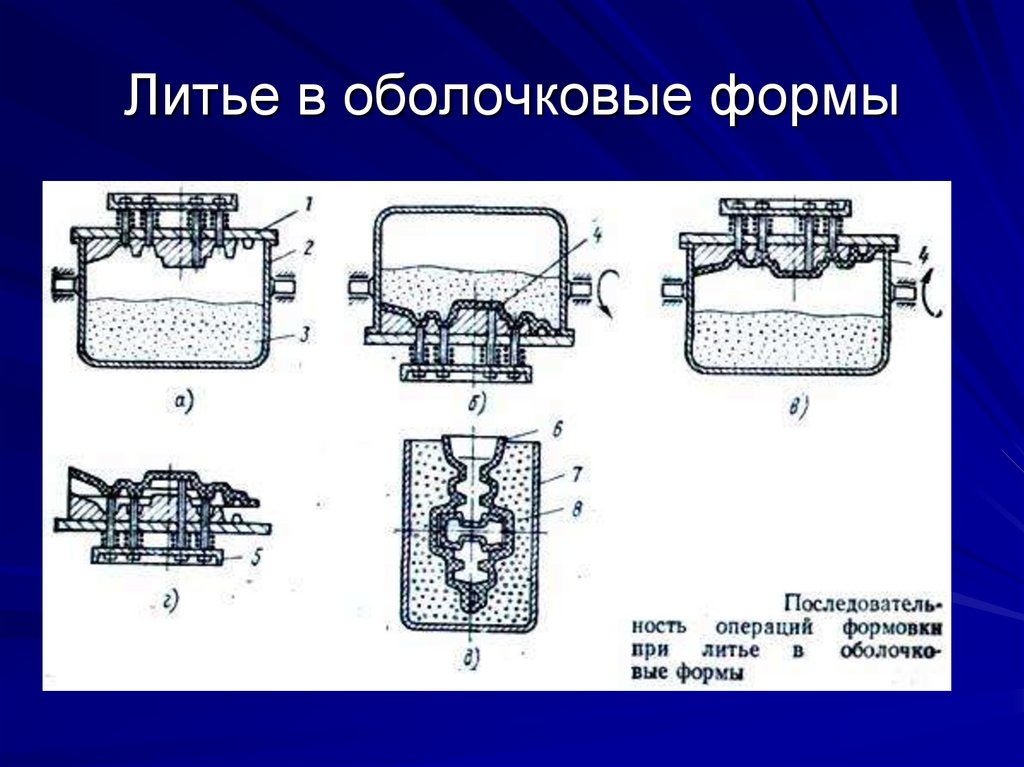
2. Кокиль практически неподатлив и более интенсивно препятствует усадке отливки, что затрудняет извлечение ее из формы, может вызвать появление внутренних напряжений, коробление и трещины в отливке.
Однако размеры рабочей полости кокиля могут быть выполнены значительно точнее, чем песчаной формы. При литье в кокиль отсутствуют погрешности, вызываемые расталкиванием модели, упругими и остаточными деформациями песчаной формы, снижающими точность ее рабочей полости и соответственно отливки.

3. Физико-химическое
4. Кокиль практически газонепроницаем, но и газотворность его минимальна и определяется в основном составами

Металлолитье Термины | Американское литейное общество
Настоящий Глоссарий терминов в области литья металлов предоставляет проектировщикам и покупателям отливок практические определения общих фраз и терминов в области литья металлов.
AQL Приемлемый уровень качества. Уровень качества, установленный в заранее организованной системе контроля с использованием образцов, отобранных случайным образом.
В литом состоянии Отливка без последующей термической обработки.
Песок для подложки Основная масса песка в опоке. Песок, уплотненный поверх облицовочного песка, который покрывает узор.
Связующее Связующее вещество, используемое в качестве добавки к формовочному или стержневому песку для придания прочности или пластичности в «сыром» или сухом состоянии.
Пригарный песок Песок, прилипший к поверхности отливки, который очень трудно удалить.
Венчик Небольшая металлическая вставка или прокладка, используемая в формах для поддержки стержня в процессе литья.
Загрузка Заданный вес металла, введенного в печь.
Охладитель Металлическая вставка в песчаной форме, используемая для локального охлаждения и выравнивания скорости затвердевания по всей отливке.
Очистка Удаление желобов, стояков, заусенцев, излишков металла и песка из отливки.
Холодное запирание Дефект поверхности из-за неудовлетворительного плавления металла.
Коуп Верхняя половина пресс-формы с горизонтальным разъемом.
Сердечник Песчаная или металлическая вставка в форму для придания формы внутренней части отливки или той части отливки, которой нельзя придать форму по шаблону.
Стержень в сборе Сборник, состоящий из нескольких стержней.
Стержневой ящик Деревянный, металлический или пластиковый инструмент, используемый для изготовления стержней.
Coreprint Выступ на шаблоне, который оставляет отпечаток в форме для поддержки сердечника.
Промывка стержней Жидкая суспензия огнеупорного материала, нанесенная на стержни и высушенная (предназначена для улучшения поверхности отливки).
Раздавливание Смещение песка на стыках формы.
Вагранка Цилиндрическая печь с прямым валом (обычно футерованная огнеупором) для плавки металла в непосредственном контакте с коксом путем нагнетания воздуха под давлением через отверстия у ее основания.
Лечить Укреплять.
Штамп Металлическая форма, используемая в качестве постоянной формы для литья под давлением или восковой модели при литье по выплавляемым моделям.
Штифт Штифт различных типов, используемый на поверхности разъема шаблонов или штампов с разъемами для обеспечения правильной приводки.
Осадка Сужение на вертикальных сторонах шаблона или стержневого ящика, позволяющее удалить стержень или песчаную форму без деформации или разрыва песка.
Перетаскивание Нижняя половина формы с горизонтальным разделением.
Выталкивающие штифты Подвижные штифты в шаблонных штампах, которые помогают удалять шаблоны из штампа.
Облицовочный песок Песок, используемый для покрытия рисунка, образующего поверхность, контактирующую с расплавленным металлом.
Питатель Иногда его называют «стояком», он является частью литниковой системы, образующей резервуар расплавленного металла, необходимый для компенсации потерь из-за усадки при затвердевании металла.
Припуск на чистовую обработку Количество припуска, остающегося на поверхности отливки для механической обработки.
Маркировка отделки Символ (f, fl, f2 и т. д.), появляющийся на линии чертежа и обозначающий край поверхности отливки, подлежащей механической обработке или другой отделке.
Фляга Жесткая металлическая или деревянная рама, используемая для удерживания песка, из которой формируется форма и обычно состоящая из двух частей: верхней и нижней.
Возврат литейного производства Металл (известного состава) в виде литников, литников, желобов, стояков и бракованной отливки, возвращаемый в печь для переплавки.
Газовая пористость Состояние, существующее в отливке, вызванное захватом газа расплавленным металлом или формовочными газами, выделяющимися во время заливки отливки.
Шибер (затвор) Часть желоба, через которую расплавленный металл попадает в полость формы.
Зеленый песок Влажный формовочный песок на глинистой связке.
Плавка Одна загрузка металла в печь.
Термическая обработка Комбинация операций нагрева и охлаждения, рассчитанных по времени и применяемых к металлу или сплаву в твердом состоянии таким образом, чтобы получить желаемые механические свойства.
Горячий ящик Процесс на основе смолы, в котором используются нагретые металлические стержневые ящики для производства стержней.
Горячий разрыв Разрушение неправильной формы в отливке, возникающее в результате напряжений, возникающих из-за крутых температурных градиентов внутри отливки во время затвердевания.
Включения Частицы шлака, огнеупорных материалов, песка или продуктов раскисления, попавшие в отливку при затвердевании заливки.
Литье по выплавляемым моделям Процесс литья по образцу, в котором используется воск или модель из термопласта. Модель обкладывается (окружается) огнеупорным раствором. После высыхания формы выплавляют или выжигают модель из полости формы, а в образовавшуюся полость заливают расплавленный металл.
Ковш Контейнер, используемый для перемещения расплавленного металла из печи в форму.
Фиксирующая подушка Выступ на отливке, помогающий поддерживать выравнивание отливки при операциях механической обработки.
Опорная поверхность Поверхность отливки, используемая в качестве основы для измерения при выполнении операций вторичной обработки.
Мастер-шаблон Объект, из которого можно изготовить штамп; как правило, металлическая модель отливаемой детали с добавлением технологической усадки.
Механические свойства Свойства материала, проявляющие упругие и неупругие свойства при приложении силы. Этот термин не следует использовать взаимозаменяемо с «физическими свойствами».
Партия металла Основная плавка, одобренная для отливки и получившая порядковый номер от литейного завода.
Форма Обычно состоит из верхней и нижней форм, изготовленных из песка, металла или любого другого паковочного материала. Он содержит полость, в которую заливают расплавленный металл для получения отливки определенной формы.
Полость формы Отпечаток в форме, полученный удалением шаблона. Он заполняется расплавленным металлом для формирования отливки.
Покрытие формы (См. промывку стержней.)
Процесс Nobake Формы/стержни, изготовленные из связанного смолой песка для отверждения на воздухе. Также известен как процесс воздушной отверждения, потому что пресс-формы оставляют затвердевать в нормальных атмосферных условиях.
Линия разъема Линия, показывающая разделение двух половин формы.
Узор Деревянная, металлическая, пенопластовая или пластиковая форма, используемая для формирования углубления в песке. Шаблон может состоять из одного или нескольких оттисков и обычно монтируется на доску или пластину вместе с системой направляющих.
Уклон шаблона Сужение, разрешенное на вертикальных поверхностях шаблона, позволяет легко извлечь шаблон из формы или штампа. (См. черновик.)
Макет узора Чертеж узора в натуральную величину, показывающий его расположение и структурные особенности.
Усадка моделиста Допуск на усадку, сделанный на всех моделях для компенсации изменения размеров при охлаждении затвердевшей отливки в форме от температуры замерзания металла до комнатной температуры. Узор увеличивается за счет величины усадки, характерной для конкретного металла в отливке, и величины результирующей усадки, с которой приходится сталкиваться.
Проницаемость Свойство материала литейной формы пропускать литейные/стержневые газы во время заливки расплавленного металла.
Физические свойства Свойства вещества, такие как плотность, электрическая и теплопроводность, расширение и удельная теплоемкость. Этот термин не следует использовать взаимозаменяемо с «механическими свойствами».
Чугун Чугун Чугунные блоки с известным химическим анализом металла, используемые для плавки (с соответствующими добавками лома и т. п.) для производства черных отливок.
Пилотная или пробная отливка Отливка, изготовленная по образцу, изготовленному в производственной форме, для проверки точности размеров и качества отливок, которые будут изготовлены.
Пористость Отверстия в отливке из-за: газов, попавших в форму, реакции расплавленного металла с влагой в формовочной смеси или неполного сплавления венков с расплавленным металлом.
Уровень восстановления Отношение количества продаваемых деталей к общему количеству изготовленных деталей, выраженное в процентах.
Огнеупорный Жаростойкий керамический материал.
Уровень брака Отношение количества бракованных деталей к общему количеству изготовленных деталей, выраженное в процентах.
Подъемник (См. питатель.)
Система желобов или литниковая система Набор каналов в форме, через которые заливают расплавленный металл для заполнения полости формы. Система обычно состоит из вертикальной секции (нижней заслонки или литника) до точки, где она соединяется с полостью литейной формы (литниковой) и выходит из полости литейной формы через вертикальные каналы (стояки или питатели) (рис. 3).
Включения песка Полости или дефекты поверхности отливки, вызванные вымыванием песка в полость формы.
Лом (a) Любой металлический лом, расплавленный (обычно с подходящими добавками чугуна или слитков) для производства отливок; (b) браковать отливки.
Встряска Процесс отделения затвердевшей отливки от материала формы.
Усадка Усадка металла в форме во время затвердевания. Этот термин также используется для описания дефекта литья, такого как усадочная полость, которая возникает из-за плохой конструкции, недостаточной подачи металла или неадекватной подачи.
Шлак Плавленый неметаллический материал, который защищает расплавленный металл от воздуха и извлекает из расплава определенные примеси.
Шлаковые включения Дефекты поверхности отливок, похожие на включения песка, но содержащие примеси из шихтовых материалов, кремнезема и глины, выветрившихся из огнеупорной футеровки, и золы из топлива в процессе плавки. Также может возникать из-за реакций металл-огнеупор, протекающих в ковше при заливке отливки.
Шлам Текучая смесь огнеупорных частиц, взвешенных в жидкости.
Процесс с силикатом натрия/CO2 Формовочная смесь смешивается с силикатом натрия, а форма насыщается газом CO2 для получения твердой формы или стержня.
Литник (нижний литник) Канал, обычно вертикальный, в который поступает расплавленный металл (рис. 3).
Испытательный стержень Стандартный образец, предназначенный для определения механических свойств металла, из которого он был отлит.
Проушина для испытаний Проушина, отлитая как часть отливки и впоследствии удаленная для целей тестирования.
Вентиляционное отверстие Отверстие или проход в форме или стержне для облегчения выхода газов при заливке формы.
A Грунтовка для литья в несъемные формы
MCDP Персонал
Процесс литья в неразъемные формы позволяет производить инженерные компоненты с жесткими допусками, хорошим качеством поверхности и высокими механическими свойствами. Его способность достигать этих деталей основана на фундаментальном принципе этого процесса — заливке расплавленного металла в многоразовые металлические формы. Эта металлическая форма придает металлу характеристики охлаждения во время затвердевания для получения более мелкозернистой структуры, снижения пористости и повышения механических свойств затвердевшего литого компонента.
При крупносерийном производстве отливки в постоянные формы обычно имеют вес от 1 унции до 1 унции. до более чем 100 фунтов; однако отливки весом до 400 фунтов. производятся на коммерческой основе. Если для отливки требуется стержень для формирования внутренней полости, можно использовать постоянный металлический стержень многократного использования или складной стержень из песка. Этот выбор основан на дизайне и сложности отливки.
К преимуществам постоянной пресс-формы относятся:
• Превосходная точность размеров.
• Возможность достижения высокого качества чистоты поверхности после литья со среднеквадратичным значением 100 (RMS).
• Постоянство размеров от детали к детали с пуансоновыми отверстиями, выступами, прокладками и другими точками.
• Возможность литья вставок из черных и цветных металлов, чтобы сочетать свойства для повышения прочности, износостойкости или усталостной долговечности.
• Более мелкозернистая структура, меньшая пористость и лучшие механические свойства из-за повышенного охлаждения металлической формы.
Литье в несъемные формы использует нулевой или минимальный уровень давления или вакуума для заливки металла в форму, в то время как в других процессах используется давление, превышающее 15 000 фунтов на квадратный дюйм. Как правило, подходящий для производства компонентов на основе алюминия и меди, выбранный тип процесса литья в постоянную форму зависит от типа производимого литого компонента.
Четыре основных типа литья в постоянные формы:
• Гравитация.
• Наклонная заливка.
• Низкое давление.
• Вакуум.
Выбор надлежащего процесса непрерывной пресс-формы для конкретных компонентов зависит от нескольких факторов, включая количество, размер, ограничения по стоимости и требования к механическим свойствам. В общем, чем больше в постоянном формовочном процессе используется давление и/или вакуум, тем лучших механических свойств можно достичь, а также тем выше производственные затраты. Кроме того, по мере усложнения процесса литья возрастают сложность и стоимость оснастки.
Гравитационное литье – старейшая, простейшая и наиболее традиционная форма литья в несъемные формы. При этом две половинки металлической формы соединяются вместе, образуя полость формы.
Расплавленный металл выливается в разливочную ванну (под действием силы тяжести) и проходит через литниковую систему в полость литейной формы, где он затвердевает и превращается в отлитую деталь.
Литье с наклонной заливкой в постоянную форму берет традиционную заливку под действием силы тяжести и поднимает ее на ступеньку выше, поворачивая/вращая металлическую форму во время или после заливки металла в ванну для заливки для заполнения полости формы. Формы поворачиваются до 90 градусов во время процесса наклона с целью уменьшения турбулентности, с которой сталкивается металл, когда он движется из разливочной ванны через систему литников в полость формы. За счет снижения турбулентности повышаются механические свойства отливок в постоянных формах.
Литье в постоянные формы под низким давлением переворачивает форму вверх дном и помещает ее в литейное устройство над герметичной герметичной камерой, содержащей тигель с расплавленным металлом. Заливная трубка проходит от формы вниз в расплавленный металл. Отливка производится путем повышения давления в камере, содержащей расплавленный металл, и принудительного помещения металла в форму. Металл в наливной трубе действует как стояк, питая отливку во время затвердевания, что позволяет достичь хорошего выхода в этом процессе. Кроме того, контролируя скорость заполнения формы давлением, литейщик обеспечивает плавное заполнение формы, без захвата воздуха и других включений в отливке, что повышает качество отливки и механические свойства. Этот метод также поддается автоматизации и обычно работает при более низких температурах пресс-формы с более коротким временем цикла, чем обычная стационарная пресс-форма. Форма с более низкой температурой сокращает время затвердевания отливки, что повышает механические свойства отливки.
Вакуумное литье аналогично литью под низким давлением, за исключением того, что в полости литейной формы создается вакуум, и металл вытягивается, а не проталкивается в литейную форму. Подобно низкому давлению, отличные механические свойства и высокая производительность являются нормой для этого процесса из-за низкой температуры пресс-формы. Кроме того, этот процесс обеспечивает такие же результаты литья, как и при низком давлении. Однако этот процесс обычно связан с отливками меньшего размера и требует специальной сложной конструкции пресс-формы для надлежащего создания вакуума.
Что касается вакуума и низкого давления, многие инновации в процессах позволили литейщикам сочетать вакуум и давление во время литья, чтобы лучше контролировать заполнение формы. Это ключ к более продвинутому производству литья в постоянные формы – контроль потока металла в форму, чтобы обеспечить как можно более спокойное заполнение формы за как можно более короткий цикл литья. Чем быстрее и менее турбулентно, тем качественнее литье при меньших затратах.
Варианты металла
Основными металлами, отливаемыми в постоянные формы, являются сплавы на основе алюминия и меди, но также могут отливаться серый и ковкий чугун, магний и цинк. Хотя основной процесс литья при литье на алюминиевой и медной основе не меняется, каждый металл, благодаря своим индивидуальным физическим и металлургическим свойствам, имеет уникальные проблемы, которые необходимо решать во время литья.
Алюминиевые сплавы
Выбор алюминиевых сплавов основан на текучести и характеристиках заполнения формы металлом. Из-за склонности алюминиевых сплавов к горячему растрескиванию эти сплавы обычно содержат 5% и более кремния. Некоторые алюминиевые сплавы, которые традиционно отливают с использованием процесса постоянного литья:
319 — Этот сплав и его варианты используются, когда умеренные механические свойства без термической обработки являются удовлетворительными.
333 и A333 — эти сплавы обладают необычайно хорошими литейными характеристиками в постоянной форме и обладают лучшими механическими свойствами в литом состоянии, чем сплавы типа 319.
355 и 356 — эти термообрабатываемые сплавы обладают хорошей литейной способностью и используются, когда требуются хорошие свойства при растяжении. 356 также обладает отличной коррозионной стойкостью. Уменьшая количество примесей в этих сплавах до С355 и А356, механические свойства сплавов значительно улучшаются.
443 — Этот сплав и его варианты применяются, когда требуется высокая пластичность и коррозионная стойкость, но не важна высокая прочность.
513 — как чистый алюминиево-магниевый сплав с добавлением 2% цинка, сплав 513 может использоваться для простых отливок, в которых требуется исключительная коррозионная стойкость и хорошее качество поверхности.
Литейная промышленность занимается исследованиями, испытаниями и испытаниями литья в несъемные формы различных новых сплавов, таких как A206. Всегда уточняйте у поставщика литья другие возможные варианты сплавов, которые могут быть хорошим выбором.
Сплавы на основе меди
Как и алюминиевые сплавы, некоторые сплавы на основе меди легче отливаются в постоянные формы. Из-за ограничений некоторых семейств сплавов важно проконсультироваться с литейщиком, чтобы определить возможность литья сплава для определенного применения. Следующие сплавы распределены по семействам с использованием пятизначного кода единой системы нумерации, разработанного Ассоциацией развития меди:
Желтая латунь (C8330-C89990) — это медные сплавы, в которых цинк является легирующим элементом. Хотя коррозионная стойкость этих сплавов ниже, чем у аналогов, высокопрочные желтые латуни (С86200 и С86500) используются для механических изделий, требующих хорошего износа.
Кремниевые бронзы/латуни (C87300-C87900) — это сплавы средней прочности. Они обладают хорошей коррозионной стойкостью в воде, хорошими литейными характеристиками и приемлемой обрабатываемостью. Кремний дает возможность отливать мелкие детали и улучшает качество поверхности отливки.
Алюминиевые бронзы (C95200-C95900) — содержат 3–12 % алюминия, а железо, кремний, никель и марганец добавляются по отдельности или в комбинации для повышения прочности и коррозионной стойкости. Эти сплавы образуют защитные, богатые оксидом алюминия пленки продуктов коррозии, которые обеспечивают исключительную стойкость к окислению и коррозии. Кроме того, они обладают прочностью от умеренной до высокой и могут подвергаться термической обработке до прочности на растяжение более 100 тысяч фунтов на квадратный дюйм.
SeBiLoy III (C89550) — этот сплав представляет собой селено-висмутсодержащую желтую латунь, специально разработанную для литья в постоянные формы. Это бессвинцовая латунь для питьевой воды, не требующая механической обработки, которая обладает улучшенными механическими свойствами, стойкостью к горячему разрыву и текучестью. По прочности сплав также превосходит желтую латунь.
Конструктивные соображения
Чтобы достичь требуемого уровня качества при наименьших затратах, конструкторы должны учитывать множество соображений применительно к любому методу литья. Например, срезы должны быть максимально однородными, без резких перепадов толщины. Тяжелые секции не должны быть изолированы, а допуски должны быть не более жесткими, чем это необходимо.
В дополнение к общим правилам, ниже приведены некоторые особенности, применимые к низкозатратному производству компонентов, отлитых в постоянные формы. Каждое предприятие по литью в постоянные формы может соответствовать различным стандартам проектирования, поэтому всегда лучше проконсультироваться с поставщиком литья об ограничениях.
• По возможности все установочные точки должны находиться в одной половине полости пресс-формы. Кроме того, точки крепления должны находиться вдали от ворот, стояков, линий разъема и выталкивающих штифтов.
• Следует избегать использования отверстий диаметром менее 0,25 дюйма, даже если отверстия диаметром 0,125 дюйма возможны.
• Углы уклона в направлении течения металла на наружных поверхностях могут варьироваться от 1 до более 10 градусов, а внутренний уклон от чуть менее 2 до 20 градусов. Однако использование минимальной осадки увеличивает сложность и стоимость заброса. Внутренние стены можно отливать без осадки, если использовать сборно-разборные металлические стержни, но такая практика увеличивает стоимость.
• Гайки, втулки, шпильки и другие вставки часто можно отливать на место. Связь между отливкой и вставкой может быть механической и/или металлургической.
• В условиях наилучшего контроля в небольших формах допуск на припуск может быть менее 0,03 дюйма (0,8 мм). Однако поддержание такого низкого припуска на механическую обработку обычно увеличивает затраты на единицу продукции. Более практично допускать 0,03–0,06 дюйма (0,8–1,6 мм) припуска для механической обработки для отливок до 10 дюймов (250 мм) в основных размерах и допускать до 0,125 дюйма для более крупных отливок.
• Конструктор не должен ожидать, что чистота поверхности отливок будет лучше 100 микродюймов (2,5 микрометра) при оптимальных условиях. Обычно чистота литья колеблется от 125 до 300 микродюймов. в зависимости от отливаемого металла.
Производство отливки часто можно улучшить, избегая резких изменений толщины сечения. Тяжелые фланцы, примыкающие к тонкой стенке, особенно часто вызывают неравномерное промерзание и горячие разрывы. В таких случаях может потребоваться перепроектирование отливки. Минимальная толщина сечения, которую можно получить по разумной цене, значительно зависит от размера отливки и однородности толщины стенок отливки.
Как и в случае всех конструкций литых компонентов, а также выбора производственного процесса, лучше проконсультироваться с поставщиками отливок и предоставить им возможность помочь в выборе процесса, а также в проектировании для производства.