Кокиль литье: Литье в кокиль. Технология литья в кокиль.
alexxlab | 27.06.1987 | 0 | Разное
Алюминиевое литье в кокиль под заказ — литейный завод «РОСАЛ»
Технологический процесс
Кокиль представляет собой форму многоразового использования (до 10 000 заливок) и идеально подходит для организации серийного и крупносерийного производства. Основные операции и процессы: очистка кокиля от старой облицовки, прогрев его до 200—300°С, покрытие рабочей полости новым слоем облицовки, установка стержней, закрывание частей кокиля, заливка металла, охлаждение и удаление готовой отливки.
Общие требования к отливкам, получаемых в кокилях, — это обтекаемая конфигурация без острых углов, резких переходов от одной поверхности к другой, без высоких ребер и выступов, глубоких отверстий и карманов. Наши конструктора помогут Вам разработать технологичную отливку, правильно выбрать толщину и уклоны ее стенок, чтобы обеспечить заливку, усадку и легкую разборку формы.
Наше производство оснащено стационарными кокильными машинами с горизонтальными и вертикальными плоскостями разъема. Все машины имеют гидравлический привод, обеспечивающий автоматизацию и значительное усилие при запирании и открытии кокиля, извлечении стержней и выталкивании отливок.
Качество
Литье в кокиль позволяет получать прочные и износостойкие отливки с гладкой поверхностью при уменьшении припусков и сокращении потерь от брака. Благодаря ускоренной кристаллизации алюминия в кокиле, изделия получаются плотные и обладают хорошими показателями герметичности.
В кокиле создаются особые условия формирования отливок различных конструкций. Это могут быть как простые по форме отливки типа болванки, колосники, втулки, так и сложные — картеры, головки блока цилиндров, ребристые корпуса электродвигателей и стоек плугов.
Литье алюминиевой посуды
Литье алюминия в кокиль позволяет нам изготавливать основу для качественной алюминиевой посуды (сковородок, жаровен, казанов, кастрюль) на которые в последующем наносится высокопрочное покрытие. Мы создаем литой толстостенный алюминиевый корпус, где толщина дна составляет от 6 мм, а стенок от 3.8 мм. На такой посуде исключена деформация в процессе эксплуатации, а толстое дно обеспечивает равномерное распределение нагрева по всей поверхности. Узнать больше можно на сайте литой алюминиевой посуды: www.hot-kitchen.ru
Литье запасных частей
Сегодня большую часть алюминиевого литья мы изготавливаем для отечественного машиностроения. В нашем арсенале более 300 наименований отливок из алюминия развесом от 0,1 до 40 кг., среди них корпуса и крышки ТНВД, головки блока цилиндров, корпуса масляных и водяных насосов, ТННД, гидромуфты и другие комплектующие и запчасти.
Литье деталей из алюминия
Наша компания занимается производством алюминиевого литья деталей для различных сфер применения. Литье деталей из алюминия может быть произведено по Вашему заказу, как с термической обработкой, так и без нее.
Возможности
Мы соблюдаем все необходимые для кокильного производства условия, такие как режим плавки, температуру заливаемого металла, график заливки, начальную температуру кокиля, состав и толщину его теплозащитного покрытия и д.р. — все это позволяет нам получать отливки с заданной структурой отвечающей целям и задачам наших клиентов.
Удобство работы с нами — это широкие возможности по организации производства изделий из алюминия. Мы работаем по Вашим чертежам, эскизам или предоставленному образцу. Сами выполняем проектирование и создание оснастки для кокильного литья.
Согласно ГОСТ
Алюминиевое литьё изготавливается из любых марок и сплавов алюминия согласно ГОСТ 1583-93, однако основными марками используемого алюминия являются сплавы АК7 и АК12. Плавка чушкового алюминия, производится в газовых тигельных печах.
Наименьшие толщины стенок отливок, включая припуск на механическую обработку в зависимости от протяженности стенки отливки, составляют от 3 до 25 мм. Минимальный диаметр литых отверстий составляет 15 мм., а максимальное отношение глубины отверстия к диаметру составляет 2/3.
Полный цикл
Мы представляем собой производство полного цикла: от проектирования и создания кокильной оснастки до серийного изготовления детали.
Высокое качество
Мы обеспечиваем высокое качество литья, соответствующее требованиям ГОСТ. Наши отливки обладают высокими физико-механическими характеристиками.
Производительность
Нас отличает высокая автоматизация процесса и производительность в условиях крупносерийного и массового производства.
Сервис
Мы являемся сервисной компанией. Для наших клиентов мы готовы обеспечить упаковку, доставку отливок. В отдельных случаях предоставить отсрочку платежа.
выгодные цены
Схема сотрудничества
1
Звоните нам
2
Получаете коммерческое предложение
3
Заключаем договор
4
Изготавливаем оснастку
5
Запускаем производство
Контакты
Ярославль, ул.
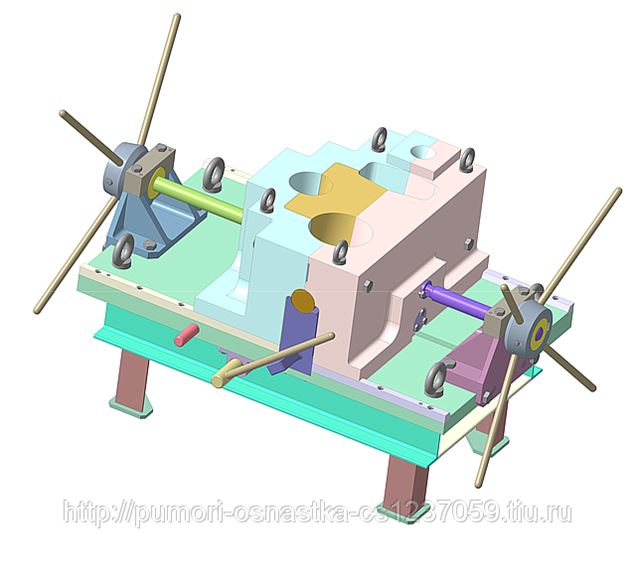
+7 (4852) 59-97-37
+7 (4852) 59-97-39
[email protected]
По будням с 09:00 до 17:00
Литье в кокиль: технология, преимущества, недостатки, изготовление
Литье в кокиль – это технологический процесс изготовления отливок путем заливания металлического расплава в многооборотные формы, выполненные из металла (сталь, чугун и пр.). Эту форму называют кокиль.
Грибовидный кокиль
Содержание
Процесс литья в кокиль
Перед началом литья в кокиль металлического расплава необходимо выполнить операции технологического процесса по подготовке его к работе. Эта работа выполняется в несколько этапов.
- Поверхности кокиля и место стыков полуформ необходимо очистить от загрязнений, коррозии, масел.
- Выполняют проверку подвижности перемещающихся деталей, точность их установки и надежность крепления на местах для этого предназначенных.
- На этом этапе поверхности формы смазывают огнестойкими материалами.
В этом качестве применяют специальные краски и смазки.
Технологический процесс литья в кокиль
Веществ, которые применяют при облицовке кокиля, зависят от марки заливаемого состава. Толщина покрытия зависит от необходимой скорости охлаждения отлитой заготовки. То есть, чем больше слой наносимой облицовки, тем заготовка будет медленнее охлаждаться. Огнестойкий слой призван решить еще одну задачу в процессе этого литья – обеспечить сохранность формы от скачка температуры во время заливки металла, а также оплавления ее частей и их схватывания с расплавом. В состав огнеупорной облицовки могут входить следующие материалы – кварц, глина, жидкое стекло, графит.
Процесс отлива в кокиль
Перед началом заливки металла форму прогревают до температуры порядка 200 градусов. Эта температура определяется маркой заливаемого металла и габаритов отливки.
Конструктивные особенности кокиля
Кокиль для литья – это многооборотная форма, изготавливаемая из металла. Несмотря на то что в такие формы могут использовать для получения отливок разных форм, их принципиальная конструкция одинакова. В состав кокиля для литья входят полуформы, плита, различные вставки и литейные стержни. С помощью последних, происходит формирование отливки. Для его центрирования и соединения применяют штыри. Непосредственно перед началом заливки полуформы фиксируют с помощью специальных замков. Металлический расплав подают в форму через систему литников.
Литье в металлические формы (кокиль)
По мере заполнения кокиля излишки воздуха выводятся через воздуховодные каналы.
В литейном производстве применяют и другой вид форм – их называют вытряхными. Эти формы отличаются тем, что они неразъемные и применяются для отливок простой формы.
Процесс изготовление кокиля и используемые материалы
При изготовлении кокилей проектировщик должен руководствоваться марками сплава, которые будут заливаться в изготавливаемую форму. Разумеется, он должен учитывать и размер деталей, получаемых в результате литья в эту оснастку.
Так, при изготовлении деталей с небольшими габаритами из цветных металлов, чугуна и некоторых других материалов рекомендуется использовать для производства литейных форм серые чугуны 20 или 25. Для производства кокилей применяют и другие виды материалов. Надо отметить, что чем прочнее материал, например, сталь 15Л, тем выше стойкость формы. Для определенных марок металла формы производят из алюминия, но перед эксплуатацией этих кокилей рабочие поверхности анодируют.
Производство кокилей выполняют на оборудовании объемной штамповки. Но современное оборудование, работающее под управлением компьютера, например, токарно-фрезерный центр позволяет производить особо точные формы.
Преимущества и недостатки литья в кокиль
Литье этого типа, как и многие технологические процессы, обладают и преимуществами, и недостатками. Можно сравнить литье в кокильную оснастку с литьем в песчаные формы.
К основным преимуществам можно отнести то, что литье в металлические формы отличается от всех остальных качеством получаемых деталей, в частности, точностью. Применение песочных стержней позволяет выполнять отливки сложной формы.
Использование металлических кокилей позволяет повысить производительность труда на литейном производстве. Это обусловлено тем, что из производства исключены такие операции, как приготовление литьевой смеси, и чистки отливок.
Использование такого типа литья позволяет уменьшить припуски на дальнейшую механическую обработку. Такой подход позволяет снизить себестоимость готового изделия.
Такое свойство кокилей, как оборачиваемость позволяет механизировать процессы литья и последующей обработки отливок. Например, операция сборки этой оснастки может быть легко автоматизирована. Кроме того из процессов исключены факторы, которые могут отрицательно сказаться на качестве отливок, например, газопроницаемость смеси. Автоматизация литейных процессов регулировать технологические режимы литейных процессов, что приводит к изменению характера труда оператора литейного комплекса и повышению его безопасности.
Между тем при множестве достоинств литье этого класса имеет и ряд недостатков.
Кокиль обладает высокой стоимостью, это является следствием его конструктивной сложности и и высокой трудоемкости производства. Особенно это относится к оснастке, в которые отливают детали сложной геометрической конфигурации.
Литейная оснастка такого типа имеет ограниченную стойкость. Стойкость оснастки определяется количеством качественных отливок. При снижении качества, его просто направляют в утилизацию. Стойкость – это ключевой экономический показатель литья. Над повышением стойкости форм этого класса работают производители и проектировщики оборудования для литья в формы этого типа по всему миру.
Литье сплава в кокиль
Интенсивность охлаждения отливок в кокиле существенно выше, чем в песчаных или земляных оснастках. Это приводит к тому, что ограничена возможность изготовления отливок с тонкими стенками.
Поскольку эти оснастки не обладает достаточной податливостью – это может привести к появлению в отлитых деталях внутренних напряжений. Которые потом устраняют с помощью термообработки.
Область применения
Кокильное литье широко используют для производства отливок из черных и цветных металлов. На автоматизированном оборудовании, предназначенном для этой обработки металлов допустимо литье алюминия в кокиль, но при этом вес отливки не должен превышать 30 кг.
На неавтоматизированном оборудовании допустимо литье чугуна в кокиль, при этом масса отливки не должна превышать 12 тонн.
Этапы литья в кокиль
Сложно найти промышленную отрасль, в которой не применяют литье в кокиль. Эта технология позволяет изготавливать широкий круг деталей из различных металлов. Например, на электротехнических заводах их применяют для отливки деталей электрических машин, на предприятиях, которые выпускают силовые установки для автомобилей, эту технологию применяют для производства головок блока цилиндров или картеров защиты.
Кокильная литейная машина
Практика показывает, что чаще всего литье этого типа применяют в отношении алюминия и его сплавов. На втором месте стоит чугун и на третьем сталь.
Литье в кокиль. Технология, преимущества, недостатки литья в кокиль
- льтье
- жидкая штамповка
- литье под давлением
Кокиль для литья представляет собой разборную форму, которая используется для изготовления различных отливок из расплавленного металла.
Кокильное литье – один из способов литья, представляющий собой процесс заливки в формы расплавленного металла и получение в результате готовой отливки. Формы для изготовления отливки в кокиле предназначены для многократного использования, что очень удобно и часто используется в литейном производстве для выпуска серийных отливок.
Кокиль для литья состоит из полуформы, платформа, стержни, закрепляющие замки и фиксаторы.
Кокили могут содержать один, несколько или ни одного разъёма.
Давайте более детально рассмотрим виды кокиля:
- неразъемные (вытряхной кокиль) которые используются для отливки простых форм и конфигураций
- кокиль с вертикальным разъемом, используемый для получения форм с выступами на наружной поверхности
- кокиль с комбинированным разъемом, используемый для изготовления сложных отливок.
Процесс отливки в кокиль происходит в несколько этапов.
Первое что нужно сделать это подготовить кокиль к заливке металла, для этого его тщательно очищают от следов ржавчины, масла и прочих загрязнений. После чего наносится слой кокильной краски и огнеупорного покрытия на рабочую поверхность и металлические стержни. Этот процесс необходим для контроля резкого повышения температуры на рабочей поверхности и регулировки скорости охлаждения отливки. Состав краски и покрытия зависит от того какой сплав металла будет использоваться, а толщина слоя напрямую зависит от того как быстро необходимо охладить деталь. Чем толще нанесен слой огнеупорного покрытия, тем медленнее происходит процесс охлаждения отливки. Кокиль нагревают до температуры 250-300 °С.
Далее устанавливаются стержни (песчаные или керамические), если таковые необходимы для получения необходимой отливки, соединяются полуформы и сжимаются специальными замками, после чего приступают к процессу заливки расплавленного метала в форму. Последним этапом идет извлечение отливки из кокиля, для этого охлаждают деталь до необходимой температуры, открывают кокиль, извлекают металлический стержень. Если для отливки необходимо было использование песчаного стержня, его выбивают из формы и проводят контроль качества полученной отливки.
К основным особенностям литья в кокиль относятся:
- возможность многократно использовать металлическую форму кокиля
- снижение себестоимости готового изделия, за счет уменьшения трудовых ресурсов на изготовление смеси и дальнейшую механическую обработку
- автоматизация процессов литья
- высокая теплопроводность, теплоемкость и прочность формы, что способствует быстрому затвердеванию изделий
- газонепроницаемость и минимальная газотворность кокиля
- минимальные погрешности размеров отливок
- получение мелкозернистой структуры деталей за счет ускоренной кристаллизации, герметичности отливок и высоким физико-механическим свойствам
К преимуществам также можно отнести факт того что литье в кокиль относится к малооперационному процессу. Практически все этапы проводятся автоматически. Данная технология позволяет изготовить разнообразный ассортимент деталей и удобна в применении серийного производства изделий из различных видов металла (стали, чугуна, сплавов из алюминия и магния) масса которых может достигать несколько сотен килограммов.
Помимо множества достоинств в данном способе литья выделяют следующие недостатки:
- дороговизна кокиля и сложность в изготовлении различных геометрических конфигураций (наличие дополнительных разъемов, вставок, стержней)
- ограниченная стойкость кокиля. Этот показатель показывает, какое количество годных отливок можно получить. Процесс литья в кокиль с точки зрения экономической эффективности напрямую зависит от стойкости кокиля.
- опасность образования трещин на отливках из-за неподатливости кокиля.
На сегодняшний день можно смело сказать, что одним из наиболее распространённых видов литья является литье в кокиль, так как оно уменьшает вредное воздействие на окружающую среду, а также относится к малооперационному, малоотходному и материалосберегающему процессу, улучшающему условия труда в цехах, за счет автоматизации процесса литья.
Кокильное литьё на заказ, доставка по РФ, низкие цены АО ОЗЦЛ
Email-адрес
Сообщение (не менее 20 символов)
При необходимости прикрепите к сообщению изображения (максимум 5):
Выберите файл…
Обновить
Код, показанный на изображении
Нажимая кнопку, я принимаю условия Пользовательского соглашения и даю своё согласие на обработку моих персональных данных, в соответствии с Федеральным законом от 27.07.2006 года №152-ФЗ «О персональных данных».
Исправьте данные и отправьте форму ещё раз.
Форма успешно отправлена. Нажмите на
ссылку, чтобы отправить ещё одно сообщение.
+7(383)353-02-82, +7(383)361-19-47
Наши преимущества
Низкие цены за высокое качество
Наше предприятие является ведущим в Сибири производителем продукции методом центробежного литья
Подробнее
Контроль качества
Продукция в соответствии с ГОСТам
Продукция нашего завода соответствует высочайшим стандартам качества предъявляемых к изделиям из металла
Подробнее
Наши награды
Участник и победитель выставок
Новосибирский завод опытного литья неоднократно удостаивался самых высоких наград
Подробнее
Главная » Литьё » Кокильное литьё
Поскольку центробежным литьем достигается самое лучшее качество отливки, на производстве АО ОЗЦЛ делается упор именно на этот метод. Но существуют виды продукции, которые имеют форму, отличную от пустотелых цилиндрических отливок. Это квадраты, пластины, цилиндры и круги без внутреннего отверстия и др.
Кокильное литье – литье металла, осуществляемое свободной заливкой кокилей.
Литье в кокили – один из древнейших способов литья. Кокилем является металлическая форма с естественным или принудительным охлаждением, заполняемая расплавленным металлом под действием гравитационных сил.
Металлическая форма обладает по сравнению с песчаной значительно большей теплопроводностью, теплоемкостью, прочностью, практически нулевыми газопроницаемостью и газотворностью. Эти свойства материала кокиля обусловливают рассмотренные ниже преимущества по сравнению с песчаной формой:
- возможность многократного использования форм;
- возможность автоматизации труда;
- хорошие механические свойства отливок, обусловленные их мелкозернистой структурой;
- снижение припусков на механическую обработку;
- снижение расходов на возврат литья за счет уменьшение количества металла на литниковую систему или ее отсутствие.
- Сегментов направляющих буровых установок
- Сегментов прокатных станов
- Сегментов шпонок
- Сегментов клиньев
- Сегментов ползунов
- Контактных пластин и т.д.
Высокая скорость охлаждения и затвердевания при литье в кокиль благоприятно влияет на качество отливок: повышаются их механические свойства, герметичность, плотность, улучшается структура. Повышение скорости охлаждения способствует приближению характера затвердевания широкоинтервальных сплавов к последовательному. Поэтому, например, отливки из оловянных бронз в кокиль имеют большую плотность, чем при литье в песчаные формы. Отливки из кремнистых латуней и бронз меньше поражены газовой пористостью, так как высокая скорость охлаждения расплава препятствует выделению газов из раствора. Повышенная скорость затвердевания отливок из свинцовых бронз уменьшает ликвацию, способствует измельчению включений свинца, что повышает антифрикционные свойства отливок.
Наша продукция
ДЕТАЛИ ВРАЩЕНИЯ – БРОНЗОВЫЕ, ЛАТУННЫЕ, МЕДНО-НИКЕЛЕВЫЕ, ЦИНКОВЫЕ
Бронзовые втулки, венцы, вкладыши, гайки, шайбы, кольца, цилиндры изготавливаются методом центробежного литья. Применяются во всех отраслях промышленности и в строительстве.
Необходимость использования бронзовых втулок в работе оборудования обусловлена природой силы трения, которая оказывает негативное воздействие на целостность механизмов.
БРОНЗОВЫЕ КОЛЬЦА
Производим детали механизмов вращения по технологии центробежного литья с последующей механической обработкой. Нашими заказчиками являются тракторные, судоремонтные, машиностроительные, агрегатные, вагоноремонтные, авиационные, металлургические и другие заводы.
БРОНЗОВЫЕ ПЛАСТИНЫ, КРУГИ
Преимущества заказа пластин из бронзы у нас высокое качество; недорогая цена; минимальные сроки выполнения заказа. Планки (пластины) из бронзы и латуни производятся методом литья в кокиль и применяются для изготовления: сегментов направляющих буровых установок направляющих для прокатных станов шпонок, клиньев, ползунов
ЛИТЬЁ КОЛОКОЛОВ
Литье колоколов – на основе традиций старинных российских мастеров, с учетом церковных канонов. Колокола производятся индивидуально, с рельефным изображением икон, орнаментов и молитвенных надписей с благословения РПЦ. Колокола, вышедшие из рук наших мастеров, звонят на многих церквях и приходах Новосибирской, Томской, Кемеровской областей, Алтайского и Красноярского края, в Казахстане и Воронеже.
Previous Next
МЫ на карте
Основные виды литья для изготовления отливок armtorg.ru
Основные виды литья для изготовления отливок
Литьё в песчаные формы
Литьё в песчаные формы — дешёвый, самый грубый, но самый массовый (до 75-80 % по массе получаемых в мире отливок) вид литья. Вначале изготовляется литейная модель (ранее — деревянная, в настоящее время часто используются пластиковые модели, полученные методами быстрого прототипирования), копирующая будущую деталь. Модель засыпается песком или формовочной смесью (обычно песок и связующее), заполняющей пространство между ею и двумя открытыми ящиками (опоками). Отверстия в детали образуются с помощью размещённых в форме литейных песчаных стержней, копирующих форму будущего отверстия. Насыпанная в опоки смесь уплотняется встряхиванием, прессованием или же затвердевает в термическом шкафу (сушильной печи). Образовавшиеся полости заливаются расплавом металла через специальные отверстия — литники. После остывания форму разбивают и извлекают отливку. После чего отделяют литниковую систему (обычно это обрубка), удаляют облой и проводят термообработку.
Новым направлением технологии литья в песчаные формы является применение вакуумируемых форм из сухого песка без связующего. Для получения отливки данным методом могут применяться различные формовочные материалы, например песчано-глинистая смесь или песок в смеси со смолой и т.д. Для формирования формы используют опоку (металлический короб без дна и крышки). Опока имеет две полуформы, то есть состоит из двух коробов. Плоскость соприкосновения двух полуформ — поверхность разъёма. В полуформу засыпают формовочную смесь и утрамбовывают её. На поверхности разъёма делают отпечаток промодели (промодель соответствует форме отливки). Также выполняют вторую полуформу. Соединяют две полуформы по поверхности разъёма и производят заливку металла.
Литьё в кокиль
Литьё металлов в кокиль — более качественный способ. Изготавливается кокиль — разборная форма (чаще всего металлическая), в которую производится литьё. После застывания и охлаждения, кокиль раскрывается и из него извлекается изделие. Затем кокиль можно повторно использовать для отливки такой же детали.
Литьё в кокиль, кокильное литьё, способ получения фасонных отливок в металлических формах — кокилях. В отличие от других способов литья в металлические формы (литьё под давлением, центробежное литьё и др.), при литьё в кокиль заполнение формы жидким сплавом и его затвердевание происходят без какого-либо внешнего воздействия на жидкий металл, а лишь под действием силы тяжести. Основные операции и процессы: очистка кокиля от старой облицовки, прогрев его до 200—300°С, покрытие рабочей полости новым слоем облицовки, простановка стержней, закрывание частей кокиля, заливка металла, охлаждение и удаление полученной отливки. Процесс кристаллизации сплава при литье в кокиль ускоряется, что способствует получению отливок с плотным и мелкозернистым строением, а следовательно, с хорошей герметичностью и высокими физико-механическими свойствами. Однако отливки из чугуна из-за образующихся на поверхности карбидов требуют последующего отжига. При многократном использовании кокиль коробится и размеры отливок в направлениях, перпендикулярных плоскости разъёма, увеличиваются.
В кокилях получают отливки из чугуна, стали, алюминиевых, магниевых и др. сплавов. Особенно эффективно применение кокильного литья при изготовлении отливок из алюминиевых и магниевых сплавов. Эти сплавы имеют относительно невысокую температуру плавления, поэтому один кокиль можно использовать до 10000 раз (с простановкой металлических стержней). До 45 % всех отливок из этих сплавов получают в кокилях. При литье в кокиль расширяется диапазон скоростей охлаждения сплавов и образования различных структур. Сталь имеет относительно высокую температуру плавления, стойкость кокилей при получении стальных отливок резко снижается, большинство поверхностей образуют стержни, поэтому метод кокильного литья для стали находит меньшее применение, чем для цветных сплавов. Данный метод широко применяется при серийном и крупносерийном производстве.
Литьё под давлением
ЛПД занимает одно из ведущих мест в литейном производстве. Производство отливок из алюминиевых сплавов в различных странах составляет 30—50 % общего выпуска (по массе) продукции ЛПД. Следующую по количеству и разнообразию номенклатуры группу отливок представляют отливки из цинковых сплавов. Магниевые сплавы для литья под давлением применяют реже, что объясняется их склонностью к образованию горячих трещин и более сложными технологическими условиями изготовления отливок. Получение отливок из медных сплавов ограничено низкой стойкостью пресс-форм.
Номенклатура выпускаемых отечественной промышленностью отливок очень разнообразна. Этим способом изготовляют литые заготовки самой различной конфигурации массой от нескольких граммов до нескольких десятков килограммов. Выделяются следующие положительные стороны процесса ЛПД:
- Высокая производительность и автоматизация производства, наряду с низкой трудоёмкостью на изготовление одной отливки, делает процесс ЛПД наиболее оптимальным в условия массового и крупносерийного производств.
- Минимальные припуски на мехобработку или не требующие оной, минимальная шероховатость необрабатываемых поверхностей и точность размеров, позволяющая добиваться допусков до ±0,075 мм на сторону.
- Чёткость получаемого рельефа, позволяющая получать отливки с минимальной толщиной стенки до 0,6 мм, а также литые резьбовые профили.
- Чистота поверхности на необрабатываемых поверхностях, позволяет придать отливке товарный эстетический вид.
Также выделяют следующие негативное влияние особенностей ЛПД, приводящие к потере герметичности отливок и невозможности их дальнейшей термообработки:
- Воздушная пористость, причиной образования которой являются воздух и газы от выгорающей смазки, захваченные потоком металла при заполнении формы. Что вызвано неоптимальными режимами заполнения, а также низкой газопроницаемостью формы.
- Усадочные пороки, проявляющиеся из-за высокой теплопроводности форм наряду с затрудненными условиями питания в процессе затвердевания.
- Неметаллические и газовые включения, появляющиеся из-за нетщательной очистки сплава в раздаточной печи, а также выделяющиеся из твёрдого раствора.
Задавшись целью получения отливки заданной конфигурации, необходимо чётко определить её назначение: будут ли к ней предъявляться высокие требования по прочности, герметичности или же её использование ограничится декоративной областью. От правильного сочетания технологических режимов ЛПД, зависит качество изделий, а также затраты на их производство. Соблюдение условий технологичности литых деталей, подразумевает такое их конструктивное оформление, которое, не снижая основных требований к конструкции, способствует получению заданных физико-механических свойств, размерной точности и шероховатости поверхности при минимальной трудоёмкости изготовления и ограниченном использовании дефицитных материалов. Всегда необходимо учитывать, что качество отливок, получаемых ЛПД, зависит от большого числа переменных технологических факторов, связь между которыми установить чрезвычайно сложно из-за быстроты заполнения формы.
Основные параметры, влияющие на процесс заполнения и формирования отливки, следующие:
- давление на металл во время заполнения и подпрессовки;
- скорость прессования;
- конструкция литниково-вентиляционной системы;
- температура заливаемого сплава и формы;
- режимы смазки и вакуумирования.
Сочетанием и варьированием этих основных параметров, добиваются снижения негативных влияний особенностей процесса ЛПД. Исторически выделяются следующие традиционные конструкторско-технологические решения по снижению брака:
- регулирование температуры заливаемого сплава и формы;
- повышение давление на металл во время заполнения и подпрессовки;
- рафинирование и очистка сплава;
- вакуумирование;
- конструирование литниково-вентиляционной системы;
Также, существует ряд нетрадиционных решений, направленных на устранение негативного влияние особенностей ЛПД:
- заполнение формы и камеры активными газами;
- использование двойного хода запирающего механизма;
- использование двойного поршня особой конструкции;
- установка заменяемой диафрагмы;
- проточка для отвода воздуха в камере прессования;
Литьё по выплавляемой модели
Ещё один способ литья металлов — по выплавляемой модели — применяется в случаях изготовления деталей высокой точности (например лопатки турбин и т. п.) Из легкоплавкого материала: парафин, стеарин и др., (в простейшем случае — из воска) изготавливается точная модель изделия и литниковая система. Наиболее широкое применение нашёл модельный состав П50С50 состоящий из 50 % стеарина и 50 % парафина, для крупногобаритных изделий применяются солевые составы менее склонные к короблению. Затем модель окунается в жидкую суспензию на основе связующего и огнеупорного наполнителя. В качестве связующего применяют гидролизованный этилсиликат марок ЭТС 32 и ЭТС 40, гидролиз ведут в растворе кислоты, воды и растворителя (спирт, ацетон). В настоящее время в ЛВМ нашли применения кремнезоли не нуждающиеся в гидролизе в цеховых условиях и являющиеся экологически безопасными. В качестве огнеупорного наполнителя применяют: электрокорунд, дистенсилиманит, кварц и т. д. На модельный блок (модель и ЛПС) наносят суспензию и производят обсыпку, так наносят от 6 до 10 слоёв. С каждым последующим слоем фракция зерна обсыпки меняются для формирования плотной поверхности оболочковой формы.
Сушка каждого слоя занимает не менее получаса, для ускорения процесса используют специальные сушильные шкафы, в которые закачивается аммиачный газ. Из сформировавшейся оболочки выплавляют модельный состав: в воде, в модельном составе, выжиганием, паром высокого давления. После сушки и вытопки блок прокаливают при температуре примерно 1000 для удаления из оболочковой формы веществ способных к газообразованию. После чего оболочки поступают на заливку. Перед заливкой блоки нагревают в печах до 1000. Нагретый блок устанавливают в печь и разогретый металл заливают в оболочку. Залитый блок охлаждают в термостате или на воздухе. Когда блок полностью охладится его отправляют на выбивку. Ударами молота по литниковой чаше производится отбивка керамики, далее отрезка ЛПС.Таким образом получаем отливку.
В силу большого расхода металла и дороговизны процесса ЛВМ применяют только для ответственных деталей.
Процесс литья по выплавляемым моделям базируется на следующем основном принципе:
• Копия или модель конечного изделия изготавливаются из легкоплавкого материала.
• Эта модель окружается керамической массой, которая затвердевает и образует форму.
• При последующем нагревании (прокалке) формы модель отливки расплавляется и удаляется.
• Затем в оставшуюся на месте удалённого воска полость заливается металл, который точно воспроизводит исходную модель отливки.
Литьё по газифицируемым (выжигаемым) моделям
Литьё по газифицируемым моделям (ЛГМ) из пенопласта по качеству фасонных отливок, экономичности, экологичности и высокой культуре производства наиболее выгодно. Мировая практика свидетельствует о постоянном росте производства отливок этим способом, которое в 2007 году превысило 1,5 млн т/год, особенно популярна она в США и Китае (в одной КНР работает более 1,5 тыс. таких участков), где всё больше льют отливок без ограничений по форме и размерам. В песчаной форме модель из пенопласта при заливке замещается расплавленным металлом, так получается высокоточная отливка. Чаще всего форма из сухого песка вакуумируется на уровне 50 кПа, но также применяют формовку в наливные и легкоуплотняемые песчаные смеси со связующим. Область применения ЛГМ — отливки массой 0,1—2000 кг и более, тенденция расширения применения в серийном и массовом производстве отливок с габаритными размерами 40—1000 мм, в частности, в двигателестроении для литья блоков и головок блоков цилиндров и др.
На 1 тонну годного литья расходуется 4 вида модельно-формовочных (неметаллических) материалов:
- кварцевого песка — 50 кг,
- противопригарного покрытия — 25 кг,
- пенополистирола — 6 кг,
- плёнки полиэтиленовой — 10 кв.м.
Отсутствие традиционных форм и стержней исключает применение формовочных и стержневых смесей, формовка состоит из засыпки модели песком с повторным его использованием на 95-97 %.
Центробежное литье и центробежный метод литья
Центробежный метод литья (центробежное литьё) используется при получении отливок, имеющих форму тел вращения. Подобные отливки отливаются из чугуна, стали, бронзы и алюминия. При этом расплав заливают в металлическую форму, вращающуюся со скоростью 3000 об/мин.
Под действием центробежной силы расплав распределяется по внутренней поверхности формы и, кристаллизуясь, образует отливку. Центробежным способом можно получить двухслойные заготовки, что достигается поочерёдной заливкой в форму различных сплавов. Кристаллизация расплава в металлической форме под действием центробежной силы обеспечивает получение плотных отливок.
При этом, как правило, в отливках не бывает газовых раковин и шлаковых включений. Особыми преимуществами центробежного литья является получение внутренних полостей без применения стержней и большая экономия сплава в виду отсутствия литниковой системы. Выход годных отливок повышается до 95 %.
В нашем производстве используют машины с горизонтальными осями вращения. Широким спросом пользуются отливки втулок, гильз и других заготовок, имеющих форму тела вращения, произведенные с помощью метода центробежного литья. Что такое центробежное литьё?
Центробежное литье — это способ получения отливок в металлических формах. При центробежном литье расплавленный металл, подвергаясь действию центробежных сил, отбрасывается к стенкам формы и затвердевает. Таким образом получается отливка. Этот способ литья широко используется в промышленности, особенно для получения пустотелых отливок (со свободной поверхностью).
Технология центробежного литья обеспечивает целый ряд преимуществ, зачастую недостижимых при других способах, к примеру:
- Высокая износостойкость.
- Высокая плотность металла.
- Отсутствие раковин.
- В продукции центробежного литья отсутствуют неметаллические включения и шлак.
Центробежным литьём получают литые заготовки, имеющие форму тел вращения:
- втулки;
- венцы червячных колёс;
- барабаны для бумагоделательных машин;
- роторы электродвигателей.
Наибольшее применение центробежное литьё находит при изготовлении втулок из медных сплавов, преимущественно оловянных бронз.
По сравнению с литьём в неподвижные формы центробежное литьё имеет ряд преимуществ: повышаются заполняемость форм, плотность и механические свойства отливок, выход годного. Однако для его организации необходимо специальное оборудование; недостатки, присущие этому способу литья: неточность размеров свободных поверхностей отливок, повышенная склонность к ликвации компонентов сплава, повышенные требования к прочности литейных форм.
Литьё в оболочковые формы
Литьё в оболочковые формы — способ получения фасонных отливок из металлических сплавов в формах, состоящих из смеси песчаных зёрен (обычно кварцевых) и синтетического порошка (обычно фенолоформальдегидной смолы и пульвер-бакелита). Предпочтительно применение плакированных песчаных зёрен (покрытых слоем синтетической смолы).
Оболочковую форму получают одним из двух методов. Смесь насыпают на металлическую модель, нагретую до 300°С, выдерживают в течение нескольких десятков секунд до образования тонкого упрочнённого слоя, избыток смеси удаляют. При использовании плакированной смеси её вдувают в зазор между нагретой моделью и наружной контурной плитой. В обоих случаях необходимо доупрочнение оболочки в печи (при температуре до 400°С) на модели. Полученные оболочковые полуформы скрепляют, и в них заливают жидкий сплав. Во избежание деформации форм под действием заливаемого сплава перед заливкой их помещают в металлический кожух, а пространство между его стенками и формой заполняют металлической дробью, наличие которой воздействует также на температурный режим охлаждающейся отливки.
Этим способом изготавливают различные отливки массой до 25 кг. Преимуществами способа являются значительные повышение производительности по сравнению с изготовлением отливок литьём в песчаные формы, управление тепловым режимом охлаждения отливки и возможность механизировать процесс.
Поделиться
Опыт работы более 10 лет. Обучение. Проектирование цехов. Модернизация заводов
Широкий модельный ряд наклоняющихся литейных машин позволит выбрать оптимальное решение для получения высокоточных отливок из цветных сплавов. Контроль скорости заполнения вкупе с системой охлаждения кокиля позволяет получить контролируемую кристаллизацию отливки и добиться максимально качественного результата.
Для заказа оборудования направьте, пожалуйста, заявку.
Наши специалисты свяжутся с Вами в ближайшее время.
В наши цели входит не просто поставить Вам оборудование, но и подобрать наиболее подходящее для Вашего производства.
Оборудование для литейного и металлургического производства возможно приобрести в Лизинг.
Заказ на оборудование высылайте на почту [email protected].
Наклоняемый автомат для литья в кокиль предназначен для приготовления отливок из черных и цветных сплавов.
Оборудование для непрерывного литья в кокиль произведено из:
- стационарной и подвижной части,
- гидроцилиндров наклона,
- систем нагрева и охлаждения кокиля,
- системы управления на основе PLC(Omron).
На поворотной части машины поставлены стационарные и подвижные плиты для крепления кокиля. В зависимости от вида кокиля машины оснащаются боковыми, нижними или же верхними подвижными плитами для подрыва стержней. или же для трудного разъема установленного кокиля. Подвижные плиты имеют привод от гидроцилиндров. Для равномерности хода и точности сборки кокиля любая плита оснащается направляющими колоннами. Кроме того для подрыва отливки учтены гидравлические и стационарные выталкиватели. Цикл машины для литья в кокиль наступает с начального положения 90º, когда кокиль открыт. По команде контроллера запускается обогрев кокиля до поставленной температуры, на трудящиеся плоскости наносится противопригарное покрытие, которое мгновенно сохнет, впоследствии чего в кокиль проставляются песчаные стержни и кокиль запирается в поставленной очередности. Порция металла из раздаточной печи влечет за собой в приемный ковш машины, подвижная доля машины наклоняется на поставленный угол. Из приемного ковша начинается самозаполнение металлом рабочего размера кокиля. Впоследствии заливки вероятна подача охлаждающей воды в рубаху. Дальше автомат переходит в начальное состояние, кокиль ориентируется и отливка выталкивается.
Опционально кокильная машина может быть оснащена манипулятором для окраски кокиля, а также манипулятором для извлечения готовой отливки.
Параметры | J430 | J650 | J750 | J850 | J1060 | J1380 |
---|---|---|---|---|---|---|
Размеры основных плит машины, мм | 400х300 | 600х500 | 700х500 | 800х500 | 1000х600 | 1300х800 |
Минимальное расстояние между плитами, мм | 300 | 300 | 495 | 495 | 500 | 600 |
Максимальное расстояние между плитами, мм | 600 | 650 | 1000 | 1000 | 1000 | 1200 |
Усилие закрытия кокиля, кН | 25 | 90 | 90 | 90 | 120 | 120 |
Усилие открытия кокиля, кН | 20 | 65 | 65 | 65 | 100 | 100 |
Усилие гидроцилиндра наклона, кН | 15 | 90 | 90 | 90 | 120 | 160 |
Угол наклона машины при заполнении, º | 0~90 | 0~90 | 0~90 | 0~90 | 0~90 | 0~90 |
Рабочее давление гидравлики, МПа | 5 | 12 | 12 | 12 | 12 | 12 |
Мощность гидростанции, кВт | 3,75 | 7,5 | 7,5 | 11 | 15 | 22 |
Мощность нагрева кокиля, кВт | 30 | 40 | 40 | 40 | 60 | 60 |
Машины для литья в кокиль
Преимущества непрерывного литья в кокильные формы
Литье металлов является важнейшим компонентом экономики Соединенных Штатов. Более 90% всех деталей, производимых в США, имеют одну или несколько деталей, изготовленных методом литья металла. Ожидается, что в 2019 году индустрия литья металлов принесет более 33,7 миллиардов долларов. В Соединенных Штатах так много операций по литью металлов, что большинство людей в настоящее время находятся в пределах 10 футов от продукта литья металла.
Существует множество различных методов литья металлов, используемых для создания всех деталей, необходимых для снабжения глобальной цепочки поставок промышленного литья. Одним из таких методов является литье в кокильные формы с постоянными формами, которое позволяет производить высококачественную продукцию с низкими затратами в больших масштабах.
Что такое литье в кокильные формы? Литье в постоянные формы (часто называемое «литьем в кокиль») — это процесс металлообработки, в котором используются постоянные многоразовые формы для создания прочных деталей. Форма (или штамп) создается с использованием сверхпрочных материалов — инструментальной стали или экзотических медных сплавов. Эти материалы могут выдерживать множество термических циклов.
Затем расплавленные материалы заливаются в форму под действием силы тяжести, а не впрыском. Это делает постоянное литье в форму идеальным для проектов, требующих больших объемов или сверхвысокой долговечности. Литье в постоянные формы позволяет производить детали с более жесткими допусками и превосходной отделкой по сравнению с другими традиционными процессами литья , такими как литье в песчаные формы.
Как работает литье в кокильные формы?Процесс литья в кокиль с постоянной формой можно разделить на четыре основных компонента. Каждый из этих компонентов может отличаться в зависимости от бизнеса по литью металлов, с которым вы работаете. Некоторые литейщики используют новейшие технологии для достижения превосходных результатов, в то время как другие по-прежнему полагаются на традиционные методы из-за наличия оборудования или обучения.
Шаг 1. Создание формы Первым шагом является создание формы. Этот процесс требует тщательного внимания к деталям и невероятной изобретательности. В Burnstein Von Seelen мы гарантируем, что пресс-форма точно соответствует качеству и спецификациям каждого проекта.
Сама форма состоит из двух или более секций и стержней, которые вставляются для образования множества сложных деталей. Важно отметить, что во время этого процесса не используется песок и что вся форма представляет собой постоянную, твердую часть.
Поверхность формы покрыта термостойким материалом, что позволяет ей выдерживать циклы нагрева и охлаждения. Покрытие также влияет на теплопроводность и смазку матрицы, поэтому в зависимости от потребностей и сложности проекта можно использовать уникальное покрытие.
Этап 2. Заливка расплавленного металла После того, как форма собрана, высококачественный расплав металла аккуратно заливается в форму через ковш, расположенный в верхней части формы. Затем расплавленный металл стекает по желобу в форму для затвердевания.
Этот процесс прост. Металлу дают остыть внутри отливки в течение установленного периода времени. Это время зависит от используемого материала.
Это некоторые из наиболее распространенных материалов, используемых при литье в постоянные формы.
- Pure Mapper
- Алюминиевые сплавы
- магниевые сплавы
- Медные сплавы
- TIN -сплавы
- 9007 9000 9000 9000 9000 9000 9000 9000 9000 9000 9000 9000 9000 9000 9000 9000 9000 9000 9000 9000 9000 9000 9000 9000 9000 9000 9000 9000 9000 9000 9000 9000 9000 9000 9000 9000 9000 9000 9000 9000 9000 9000 9000 9000 9000 9000 9000 9000 9000 9000 9000 9000 9000 9000 9000 9000 9000 9000 9000 9000 9000 9000 9000 9000 9000 9000 9000 9000 9000 9000 9000 9000 9000 9000 9000 9000 9000 9000 9000 9000 9000 9000 9000 9000 9000 9000
20202020202 слепок открывается, и часть удаляется. На этом этапе, в зависимости от этапа цикла, форма будет снова установлена и использована на более поздних операциях.
Любой лишний материал, прикрепленный к детали, также обрезается и используется для повторного плавления.
Чтобы узнать больше о сложностях, связанных с литьем в постоянные формы, включая математические свойства, см. здесь.
Преимущества литья в кокильные формыКокильное литье в постоянные формы имеет множество преимуществ.
- Хорошо подходит для крупносерийного производства : Основные затраты, связанные с литьем в постоянные формы, составляют само литье. Применительно к высокопроизводительным циклам литье в кокиль обеспечивает лучшую себестоимость детали, чем другие методы литья. Экономия затрат на постоянное литье в формы является предметом исследований в течение многих лет. Кроме того, во множестве тематических исследований литье в постоянные формы оказалось наиболее рентабельным методом крупносерийного литья.
- Более плотная граница зерна : Компания Burnstein Von Seelen гарантирует проводимость на уровне 98 % по IACS.
- Однородные свойства : Однородные свойства кокильного литья в постоянные формы гарантируют, что все части невероятно однородны.
- Невероятная чистота поверхности : Литье в постоянные формы обеспечивает превосходную чистоту поверхности по сравнению с другими методами литья (например, литье в песчаные формы, формование в оболочку и т. д.)
- Меньшие литые отверстия чем другие методы, что помогает поддерживать жесткие допуски.
- Минимальная вариация деталей : Поскольку вы не создаете новые отливки для каждого цикла, отливки в постоянные формы предлагают вариации всего +/-0,010.
- Более тонкие стенки : Литье в кокильные формы с постоянными формами позволяет получить более тонкие стенки, чем другие методы литья.
- Превосходные механические свойства : Механические свойства (например, прочность, текучесть, пластичность и т. д.) выше при литье в постоянные формы из-за характера процесса.
- Защита окружающей среды : Литье в кокильные формы с постоянными формами потребляет гораздо меньше энергии и производит меньше отходов, чем другие методы литья, такие как литье в песчаные формы.
Несмотря на то, что литье в постоянные формы имеет много общего с литьем в песчаные формы и литьем по выплавляемым моделям, оно имеет несколько ключевых отличий. Во-первых, он не использует одноразовую форму. Как для литья в песчаные формы, так и для литья по выплавляемым моделям используются одноразовые формы, годные только для одного цикла. Постоянные пресс-формы сохраняют точность и долговечность в течение многих циклов , что делает их рентабельными для проектов с большим объемом и временем выполнения.
Другое ключевое отличие заключается в том, как обращаться с расплавленным металлом. Литье в постоянную форму использует гравитацию вместо впрыска, чтобы ввести расплавленные металлы в форму.
И эти различия гарантируют, что литье в постоянные формы обеспечивает превосходную чистоту поверхности и точность размеров по сравнению с литьем в песчаные формы.
Основными различиями между ними являются качество конечного продукта и цена за единицу.
Другим важным моментом является то, что литье в постоянные формы не выделяет столько отходов, сколько литье в песчаные формы , что создает чрезмерное количество побочного продукта в виде песка.
- Кокильное литье в постоянную форму лучше подходит для крупносерийного производства.
- Литье в песчаные формы дешевле при небольших партиях.
- Кокильное литье в постоянную форму позволяет получить деталь более высокого качества.
- При литье в песчаные формы используются одноразовые формы, что может увеличить количество отходов.
- Кокильное литье в постоянные формы требует более высоких первоначальных затрат на оснастку.
- Отливки в постоянные формы отливаются почти до чистой формы с минимальными припусками, необходимыми для механической обработки.
Как и при литье в песчаные формы, при литье по выплавляемым моделям для производственных циклов используются одноразовые формы. Однако для создания формы вместо песка используется воск, что приводит к несколько более высоким затратам на единицу продукции, чем литье в песчаные формы. Восковая форма обеспечивает хорошую точность размеров, но она намного дороже, чем литье в кокиль с постоянной формой.
Основными различиями между этими двумя процессами вне процесса литья в формы являются стоимость единицы продукции, качество и скорость доставки деталей. Литье по выплавляемым моделям часто имеет более высокие затраты, когда производство ограничивается небольшими и средними тиражами.
Благодаря этому литье в постоянные формы превосходно подходит для средних и больших производственных циклов.
- Кокильное литье в постоянную форму более рентабельно для крупносерийного производства.
- Литье по выплавляемым моделям часто обходится дороже, чем литье в постоянные формы.
- Кокильное литье в постоянную форму обеспечивает более конкурентоспособную цену, чем литье по выплавляемым моделям.
- Для литья по выплавляемым моделям используются одноразовые формы.
- Литье в кокильные формы с постоянными формами имеет более низкие производственные и трудовые затраты, но более высокие первоначальные затраты на оснастку, чем другие методы литья.
Burnstein Von Seelen — единственное предприятие в Северной Америке, сертифицированное по стандарту и имеющее сертификат ISO. Мы покупаем только самые качественные первичные металлы у надежных поставщиков. И запуском каждого из наших проектов занимаются менеджеры, сертифицированные в области контроля качества, которые используют новейшие технологии и графики, чтобы помочь сократить расходы и повысить производительность по каждому проекту, используя наше современное оборудование с ЧПУ.
В настоящее время мы сертифицированы по ISO 9001:2015 и военному стандарту 105 D. Мы также обеспечиваем точность размеров и целостность сплава, используя нашу ультрасовременную лабораторию контроля качества с передовыми технологиями тестирования и контроля. Мы не просто создаем невероятные детали, используя кокильное литье в постоянные формы; мы создаем счастливых клиентов.
Щелкните здесь, чтобы просмотреть некоторые из наших прошлых тематических исследований.
Вы ищете решение для литья в постоянные формы, которое снижает затраты, повышает производительность и базируется в США?
Свяжитесь с нами. Мы являемся универсальным магазином и предоставляем широкий спектр услуг по литью металлов, включая сплавы, оснастку, гальваническое покрытие и механическую обработку.
В чем разница между прямым охлаждением и непрерывным литьем алюминия?
Машины непрерывного литья заготовок являются одними из самых популярных машин на производственной линии, когда речь идет об алюминии.
Непрерывное литье позволяет растягивать, формовать и затвердевать такие металлы, как алюминий, без каких-либо пауз или перерывов. Преимущества очевидны: более высокая производительность и экономия средств. Для некоторых продуктов, таких как батареи, теперь это стандарт.
Но существует два основных типа методов непрерывного литья: прямое охлаждение и непрерывное охлаждение (иногда также называемое полунепрерывным). Оба метода используют один и тот же принцип затвердевания алюминиевого сплава в открытой форме в контролируемых условиях, но конечные результаты совершенно разные!
Загрузить нашу спецификацию на алюминий сейчас
Kloeckner Metals — поставщик полного ассортимента алюминия и сервисный центр. Загрузите нашу спецификацию алюминия и узнайте, что Kloeckner Metals регулярно поставляет на склад.
Спецификация алюминия
Читайте дальше, чтобы узнать, чем отличается прямое охлаждение от непрерывнолитого алюминия, и на что следует обратить внимание, прежде чем выбрать один из них по сравнению с другим.
Сколько существует видов алюминиевого литья?
Существует два основных типа алюминиевого литья — непрерывное литье (CC) и полунепрерывное литье (SCC). Эти термины относятся к тому, как быстро расплавленный алюминий затвердевает после того, как он покидает промежуточный ковш (резервуар в верхней части формы).
- Литье CC включает заливку жидкого металла в формы, содержащие воду или другую охлаждающую жидкость , так что, как только все части каждой полости будут заполнены, немедленно начнется затвердевание.
- Литье алюминия SCC включает заливку жидкости в формы без промежуточного охлаждения . При полном заполнении вливают дополнительное количество металла до тех пор, пока все пространство не будет занято металлом. После заполнения каждая последующая заливка способствует затвердеванию. Литье с прямым охлаждением является одним из старейших и наиболее распространенных подтипов литья SCC.
Обзор алюминиевого литья с прямым и непрерывным литьем
Хотя алюминиевое литье с прямым и непрерывным литьем является разновидностями алюминиевого литья, между ними есть некоторые различия.
Что такое прямое охлаждение?
Во-первых, давайте начнем с прямого охлаждения. Прямое литье в кокиль обычно описывает изготовление прямоугольных или цилиндрических слитков. Далее они обрабатываются прокаткой, ковкой или другими способами для создания листов, плит или других изделий.
В случае экструзионно-литого алюминия прямое охлаждение включает в себя нагнетание расплавленного металла через сопло для формирования длинных тонких трубок, которым можно придать форму листов или других изделий путем их прокатки или плющения. Полученный продукт известен как алюминий, отлитый из фольги, потому что он часто бывает настолько тонким, что по внешнему виду напоминает фольгу.
Если бы вы приложили к своей коже кусок алюминия, отлитого из фольги, это было бы похоже на шелковое нижнее белье — настолько оно легкое! И если вы согните или согнете его даже слегка (он не порвется), он почти сразу вернется на место, потому что его состав допускает гибкость.
Литье с прямым охлаждением – это процесс, который позволяет производителям отливать алюминий непосредственно из жидкого металла в форму .
Поскольку его не нужно формовать в прокатном стане, прямое охлаждение более рентабельно, чем традиционные методы, но все же дороже, чем непрерывное литье. Это также создает меньше затрат на энергию и выбрасывает меньше углекислого газа в атмосферу.
В качестве альтернативы алюминиевой заготовке прямое охлаждение часто используется для фитингов нефте- или газопроводов и декоративных элементов, таких как колеса для тракторов или вагонов. Однако его использование не ограничивается коммерческими приложениями. Прямое охлаждение также можно использовать для бытовых товаров, таких как садовые ножницы и шланги.
Что такое непрерывное литье?
Непрерывное литье алюминия — это производственный процесс, в результате которого получают алюминиевые слитки одинакового размера, формы и веса. Что еще более важно, он может производить сплавы в больших количествах, но предпочтительнее, когда качество не так важно, как характеристика конечного продукта. К сожалению, несмотря на то, что это более экономичный вариант из двух методов, он имеет более ограниченные возможности для конечного использования.
При непрерывной разливке расплавленный металл заливают в водоохлаждаемую форму, установленную под углом, чтобы сила тяжести вытягивала затвердевающий слиток . Затем его разрезают на стержни или экструдируют через головку, чтобы сформировать ленты. Этот тип литья использует только одну печь и производит сплав, который не требует дополнительной обработки для использования в повседневных продуктах, таких как автомобильные детали, бытовая техника или компоненты электроники.
Преимущества прямого охлаждения по сравнению с непрерывным литьем алюминия
Основным преимуществом прямого охлаждения является качество. Процесс прямого охлаждения позволяет лучше контролировать каждый этап производства, гарантируя, что полученная алюминиевая деталь будет иметь превосходное качество и внешний вид поверхности . Кроме того, если вы выберете компанию, имеющую сертификаты, такие как UL или ISO 9001, вы сможете рассчитывать на то, что они будут производить высококачественные детали каждый раз.
Основным преимуществом непрерывнолитого алюминия является экономия затрат.
Недостатки прямого охлаждения алюминия по сравнению с алюминием непрерывного литья
Одним из основных недостатков алюминия прямого охлаждения по сравнению с алюминием непрерывного литья является то, что, поскольку прямое охлаждение требует быстрой заморозки, более вероятно образование воздушных карманов или застойной воды. Это может привести к более слабым и менее прочным деталям.
Другим недостатком прямого литья в кокиль является то, что оно имеет меньшую производительность, чем непрерывное литье алюминия, и стоит больше, чем другие типы процессов литья. Кроме того, продукты могут иметь непостоянные допуски на размеры, поскольку при прямом охлаждении требуется меньше проверок качества, чем при непрерывном литье.
Основным недостатком непрерывнолитого алюминия является низкое качество и ограничения в области конечного применения. Если качество и внешний вид поверхности являются менее важными компонентами вашего проекта, может быть целесообразно рассмотреть возможность непрерывного литья для экономии средств, если он подходит для вашего конечного использования.
Как работает каждый процесс?
В методе литья с прямым охлаждением используются три основных элемента оборудования: ковш, печь и разливочная машина. Он отличается от непрерывного литья тем, что в нем используется заливка металла в охлажденные контейнеры для затвердевания, а не формование его как одной непрерывной детали.
Одной из проблем прямого кокильного литья является необходимость охлаждения каждой отдельной отливки, прежде чем ее можно будет извлечь из формы. Это приводит к более длительному времени оборота, чем при непрерывном литье, что позволяет отливать больше деталей одновременно, охлаждая их одновременно струями воды или масла.
Непрерывное литье работает аналогично тому, как изготавливаются литые алюминиевые изделия, такие как банки для напитков. Расплавленный алюминий непрерывно заливают во вращающуюся форму с открытым концом, в которую впрыскивается углекислый газ. Когда весь алюминий добавлен, вокруг его поверхности начинает образовываться жидкий шлак, а поверх него начинает образовываться корка (так называемая синяк).
Затем через ролики, прикрепленные к каждому концу конвейерной ленты, подается электрический ток, чтобы они могли прижиматься друг к другу и создавать достаточную силу для идеального затвердевания продукта!
Области применения для каждого типа алюминия
Существует много различий между алюминием прямого охлаждения и алюминием непрерывного литья в отношении применения. Наиболее заметное отличие заключается в прочности и функциональности . Детали из непрерывнолитого алюминия, как правило, гораздо более функциональны, чем их аналоги с прямым охлаждением, в основном потому, что они подвергаются термообработке после затвердевания. Хорошим примером применения непрерывного литья могут быть водосточные желоба, где цена имеет более высокий приоритет, чем качество или внешний вид поверхности. В целом, однако, конечное применение процесса непрерывной разливки более ограничено.
В зависимости от того, насколько плотно должна прилегать деталь, любой тип может быть подходящим для применения, но в зависимости от того, насколько сложной или сложной должна быть деталь с точки зрения функциональности или эстетики, алюминиевые детали непрерывного литья могут лучше подходить для ваших нужд.
Если деталь не требует большой прочности или какой-либо сложной геометрии или изготовления, то алюминий с прямым охлаждением, вероятно, подойдет вам.
Свяжитесь с нашей квалифицированной командой сейчас
Kloeckner Metals — поставщик полного ассортимента алюминия и сервисный центр. Kloeckner Metals сочетает в себе национальное присутствие с новейшими технологиями производства и обработки и самыми инновационными решениями для обслуживания клиентов. Свяжитесь с нами в Kloeckner Metals, чтобы определить, какой алюминий подходит для вашего проекта.
Свяжитесь с нами сейчас
Особенности литья магниевых сплавов в кокиль
[1] С.Л. Бураков, А.И. Вейник, Н.П. Дубинин, Литье в кокиль, Машиностроение, Москва (1980).
[2] К.
Н. Гавариева, Л.А. Симонова, Д.Л. Панкратов, Р.В. Гавариев, Разработка экспертных систем моделирования технологического процесса литья под давлением на основе искусственного интеллекта, Конф. Серия: Материаловедение и инженерия. 240 (2017) 012019.
DOI: 10.1088/1757-899x/240/1/012019
[3] С. Хуан, Г. Фэн, Г. Сяобо, Ф. Хайцюань, Исследование взаимодействия твердого раствора и существующих форм легирующих элементов в сплаве Mg-Al-Zn-Gd, Journal of Alloys and Compounds. 854 (2021) 156209.
DOI: 10.1016/j.jallcom.2020.156209
[4] Л.
Д.К. Екатерина, Д.А. Хамид, Механические свойства и обрабатываемость магниевого сплава AZ31 и AZ91 – сравнительный обзор, IOP Conf. Серия: Материаловедение и инженерия. 1062 (2021) 012054.
DOI: 10.1088/1757-899x/1062/1/012054
[5] О. Трудоносын, П. Рандельжофер, К. Кёрнер, Термическая обработка литья под высоким давлением сплавов Al-Mg-Si-Mn-Zn, Journal of Alloys and Compounds. 872 (2021) 159692.
DOI: 10.1016/j.jallcom.2021.159692
[6] В.Н. Гилман, А.И. Фасхутдинов, И.П. Балабанов, Повышение эффективности бритья за счет использования износостойких покрытий и предварительного моделирования резки, Явления твердого тела.
299 (2020) 839-844.
DOI: 10.4028/www.scientific.net/ssp.299.839
[7] К.Н. Гавариева, Л.А. Симонова, Д.Л. Панкратов, В.Г. Шибаков, Р.В. Гавариев, Применение многоагентной системы для управления параметрами процесса прецизионной штамповки конических зубчатых колес, Серия конференций ИОП: Материаловедение и инженерия. 412 (2018) 012020.
DOI: 10.1088/1757-899x/412/1/012020
[8] Р.В. Гаварьев, И.А. Савин, И.О. Леушин, К вопросу о литье сплавов цветных металлов в кокиль, Материаловедческий форум. 946 (2019) 631-635.
DOI: 10.
4028/www.scientific.net/msf.946.631
[9] Д.Л. Панкратов, Р.В. Гавариев, Повышение качества отливок из сплавов цветных металлов при литье в металлические формы, Конф. Серия: Материаловедение и инженерия. 570 (2019) 012072.
DOI: 10.1088/1757-899x/570/1/012072
[10] Р.В. Гаварьев, И.А. Савин, Е.Н. Солдаткина, Выбор защитного покрытия металлических форм для литья цветных сплавов, Явления твердого тела. 299 (2020) 867-871.
[11] Н.
Н. Сафронов, Л.Б. Мингалеева, И.А. Савин А. В. Оптимизация состава шихты в процессе СШ с получением ферросилида из газообразных отходов металлургического производства // Черные металлы. 2 (2018) 53-59.
[12] СРЕДНИЙ. Шапарев, И.А. Савин, Влияние состояния контактных поверхностей на формирование соединения стали и латуни при холодной наплавке, Явления твердого тела. 284 (2018) 319-325.
DOI: 10.4028/www.scientific.net/ssp.284.319
[13] Я. Савин, М. Ахмедеев, Соединение стальных труб, имеющих полимерное покрытие на внутренней и внешней поверхностях, Явления твердого тела.
299 (2020) 766-771.
DOI: 10.4028/www.scientific.net/ssp.299.766
[14] И.П. Балабанов, В.Н. Гилман, Т.С. Тимофеева, А.И. Фасхутдинов, Моделирование влияния скругления режущей кромки на стойкость инструмента при обработке зубчатого колеса методом Power Skiving, International Journal of Engineering and Technology (ОАЭ). 7(4) (2018) 71-73.
DOI: 10.14419/ijet.v7i4.7.20386
[15] В.Н. Гилман, И.П. Балабанов, А.И. Фасхутдинов, Повышение эффективности бритья за счет использования износостойких покрытий, Серия конференций IOP: Материаловедение и инженерия.
570 (2019) 012024.
DOI: 10.1088/1757-899x/570/1/012024
[16] СРЕДНИЙ. Шапарев, И.А. Савин, Расчет пластической деформации соединения с образованием соединения металла в холодном состоянии, Явления твердого тела. 265 (2017) 313-318.
DOI: 10.4028/www.scientific.net/ssp.265.313
[17] И.Дж. Polmear, Магниевые сплавы и их применение, Материаловедение и технология (Великобритания). 10(1) (1994) 1-16.
[18] Х.
К. Ли, З.М. Чжан, Ю.Л. Чжао, Успехи исследований и перспективы деформированных магниевых сплавов, Технология термической обработки. 24 (2011) 54.
[19] Р.В. Гавариев, К.Н. Гавариева, к вопросу о тепловом балансе пресс-форм для литья под давлением сплавов цветных металлов, Серия конференций ИОП: Материаловедение и инженерия. 969(1) (2020) 012069.
DOI: 10.1088/1757-899x/969/1/012069
[20] Р.В. Гавариев, К.Н. Гавариева, Е.Н. Солдаткина, Особенности конструкции кокилей для литья цветных металлов, Серия конференций ИОП: Материаловедение и инженерия.
969(1) (2020) 012068.
DOI: 10.1088/1757-899x/969/1/012068
[21] Д.Л. Панкратов, Р.В. Гавариев, К вопросу об автоматизации процесса литья под давлением, Серия конференций ИОП: Материаловедение и инженерия. 915(1) (2020) 012043.
DOI: 10.1088/1757-899x/915/1/012043
[22] СРЕДНИЙ. Шапарев, И.А. Савин, С.Н. Птичкин, Применение полимерного материала РИМАМИД для изготовления деталей машин, Конф. Серия: Материаловедение и инженерия. 969 (2020) 012021.
DOI: 10.
1088/1757-899x/969/1/012021
[23] СРЕДНИЙ. Шапарев, И.А. Савин, Расчет величины обжатия, необходимого для образования составных слоев при холодной прокатке биметаллов, Материаловедческий форум. 870 (2016) 328-333.
DOI: 10.4028/www.scientific.net/msf.870.328
[24] СРЕДНИЙ. Шапарев, Исследование влияния содержания кислорода во вспомогательном технологическом газе на качество и скорость лазерной резки стальных листов, Явления твердого тела. 299 (2020) 457-461.
DOI: 10.4028/www.scientific.net/ssp.299.457
[25] Ю.
Влияние процесса кокильного литья на структуру и свойства алюминиевых сплавов с эвтектическими составляющими // Цветные металлы. 5 (2018) 77-81.
DOI: 10.17580/tsm.2018.05.11
[26] И.П. Клейнбуг, Л.М. Железняк, С.И. Паршаков, Е.Н. Белоносова, Кокиль оригинальной конструкции для непрерывного литья сложнолегированных латуней и бронз, Металлург. 59 (2015) 431-434.
DOI: 10.1007/s11015-015-0122-5
Что такое литье в кокиль?
Вопрос задан: проф. Освальдо Линдгрен
Оценка: 4,9/5 (32 голоса)
Отбел — это предмет, используемый для ускорения затвердевания в определенной части металлической литейной формы.
Обычно металл в литейной форме охлаждается с определенной скоростью относительно толщины отливки.
Что означает литье в кокиль?
Способ производства фасонных отливок в металлических постоянных (или кокилях) формах . Кокильное литье применяют для получения отливок из железа, стали, алюминия, магния и других сплавов. …
Какая польза от холода и венков при литье?
Охладители и прокладки используются для обеспечения однонаправленного затвердевания . Кокили представляют собой металлические предметы, которые помещают в форму для увеличения скорости охлаждения отливок.
Какие бывают 4 типа литья?
10 Различные типы литья
- (1)Литье в песчаные формы.
- (2) Литье по выплавляемым моделям.
- (3) Литье под давлением.
- (4) Литье под низким давлением.
- (5) Центробежное литье.
- (6) Гравитационное литье под давлением.
- (7)Вакуумное литье под давлением.
- (8) Литье под давлением.
Что такое процесс прямого охлаждения?
Прямое литье в кокиль – это метод изготовления цилиндрических или прямоугольных твердых слитков из цветных металлов , особенно из алюминия, меди, магния и их сплавов. … Литье с прямым охлаждением осуществляется путем непрерывной заливки жидкого металла в короткую форму (глубиной 7,5–15 см), открытую снизу.
Что такое ПРЯМОЕ КОЛОДИЛЬНОЕ ЛИТЬЕ? Что означает ПРЯМОЕ ОХЛАЖДЕНИЕ? ПРЯМОЕ КОЛОДИЛЬНОЕ ЛИТЬЕ значение
Найдено 36 связанных вопросов
Что такое слиток постоянного тока?
Литье с прямым охлаждением (DC) представляет собой процесс вертикального полунепрерывного литья, используемый для изготовления цилиндрических заготовок или прямоугольных слитков/блюмов из цветных металлов, таких как алюминиевые сплавы, медные сплавы, магниевые сплавы.
… Более половины алюминия в мире отливается методом прямого охлаждения (DC).
Что такое Chaplet в процессе литья?
Венчик Небольшая металлическая вставка или распорка, используемая в литейных формах для поддержки стержня в процессе литья . … Охлаждение Металлическая вставка в песчаной форме, используемая для локального охлаждения и выравнивания скорости затвердевания по всей отливке.
Что такое кастинг Python?
Преобразование типов — это метод, используемый для изменения переменных/значений, объявленных в определенном типе данных, в другой тип данных , чтобы соответствовать операции, которую должен выполнить фрагмент кода. В Python эту функцию можно реализовать с помощью функций-конструкторов, таких как int(), string(), float() и т. д.
Как узнать свой тип заклинания?
Обычно брифинги для кастинга определяют, какой тип актера им нужен, поэтому вам нужно подумать, подходите ли вы под эти скобки. Тип обычно состоит из возраста, внешности (включая пол, рост, цвет волос и т.
д.), личных качеств, навыков и, иногда, вашего голоса.
Какие бывают два типа литья?
Существует два основных типа слепков: гипсовые и стекловолоконные .
Какова функция охлаждения?
Отбел — это объект , используемый для ускорения затвердевания в определенной части металлической литейной формы . Обычно металл в литейной форме охлаждается с определенной скоростью относительно толщины отливки.
Что такое озноб и венки?
Венчики представляют собой анкеры стержней , т. е. венчики поддерживают сердечник
2. Направленное затвердевание в отливках можно улучшить с помощью. а) озноб и мурашки. (b) озноб и отек.
Что такое закаленная сталь?
Холоднодеформированная сталь (CFS), общий термин для изделий , изготовленных путем прокатки или прессования тонких листов листовой стали в изделия . «Холодная сталь», современная альтернатива фразе «холодное железо», означающее любое оружие, предназначенное для кровопролития, см.
Железо в фольклоре.
Как производится отбеленный чугун?
Отливка из закаленного чугуна может быть получена путем регулирования состава углерода в белом чугуне таким образом, чтобы нормальная скорость охлаждения на поверхности была достаточно высокой для получения белого чугуна, в то время как более низкая скорость охлаждения под поверхностью приводит к получению серого утюг.
Какие меры предосторожности следует соблюдать при выборе холодца?
Следует произвести дробеструйную обработку охладителей перед размещением , чтобы удалить любые загрязнения. Затем убедитесь, что ваш охладитель был разработан для конкретной формы/отливки. Если это не так, холод не останется на месте, когда литейная форма или стержень будут удалены. Поэтому убедитесь, что ваш холод правильно уплотнен.
Внешнее охлаждение так же эффективно, как внутреннее?
То есть, если поверхность необходимо охладить (например, для направленного затвердевания отливки), то внешнее охлаждение столь же эффективно, как и внутреннее охлаждение .
Однако часто требуется охлаждение на некоторой глубине под поверхностью отливки. В этом случае внутренний озноб был бы более эффективным.
Какие существуют типы прослушиваний?
Но есть четыре категории прослушиваний, такие как Открытое прослушивание, Частное прослушивание, Повторный просмотр и Экранный тест .
Тебе как актеру приходится красить волосы?
Изменение цвета волос — это ~большое дело~ и серьезное обязательство. Однако актеры делают это все время, часто ради роли, которую играют. … Когда его спросили, красил ли он волосы для прослушивания, Апа рассмеялся и сказал: « Нет, определенно не . Процесс окрашивания волос занимает более двух часов, и Апа должен делать это каждые две недели.
Как называется, когда актер играет несколько ролей?
Двойная роль (также известная как двойная роль) относится к одному актеру, играющему две роли в одной постановке. … В театральной постановке, где несколько персонажей играют более одного актера, его иногда называют актерским составом «Железный человек».
Что такое нарезка в Python?
Нарезка в Python — это функция, которая позволяет получить доступ к частям последовательностей, таким как строки, кортежи и списки . Вы также можете использовать их для изменения или удаления элементов изменяемых последовательностей, таких как списки. Срезы также можно применять к сторонним объектам, таким как массивы NumPy, а также серии Pandas и фреймы данных.
Является ли Python языком с учетом регистра?
Python — это язык с учетом регистра , потому что он различает такие идентификаторы, как переменная и переменная. Проще говоря, мы можем сказать, что он заботится о верхнем и нижнем регистре.
Зачем нам нужно использовать Python?
Python позволяет избежать потери данных при неявном преобразовании типов. Явное преобразование типов также называется преобразованием типов, типы данных объектов преобразуются с использованием предопределенных функций пользователем. При приведении типов может произойти потеря данных, поскольку мы применяем к объекту определенный тип данных .
Может ли венчик также действовать как охлаждающее объяснение?
Объяснить. В то время как теоретически венки могут служить охлаждающими , на практике венки редко делают это. Венчики предназначены для поддержки стержня или части формы. Если они размещены в положении, поддерживающем ядро, они могут оказаться не в том месте, где требуется охлаждение.
Что такое слякоть?
Отливка из шлама – это вариант непрерывного литья под давлением для создания полой отливки или полой отливки . При этом материал заливается в форму и охлаждается до тех пор, пока в форме не образуется оболочка из материала. Затем оставшуюся жидкость выливают, оставляя полую оболочку.
Что такое литейное производство?
Стержень представляет собой предварительно отформованную, связанную песчаную вставку, помещенную в форму для формирования внутренней части отливки или части отливки, которой нельзя придать форму по шаблону. Стержни часто используются для создания полых секций или полостей в отливке.
Похожие вопросы
- 29Могут ли персонажи нулевого холода кататься на коньках?
Реклама
Популярные вопросы
- 23Почему дезинтермедиация важна?
- 36Можно ли положить песок в теневой ящик?
- 37Где означает «не занят»?
- 36Почему интерфейс или абстрактный класс?
- 39Объясните, подходит ли секуляризм для Индии?
- 19Что означает парсек?
- 22Где снимали удар в спину для новичков?
- 37Когда использовать краситель нигрозин?
- 34Как нейроны хранят память?
- 32Должно ли поле выщелачивания пахнуть?
10 различных типов процесса литья (определение, этапы производства, литье металлов и загрузка в формате PDF)
Содержание
Что такое литье процесс?Литье относится к методу обработки плавления твердого металла в жидкое состояние и заливки его в форму определенной формы для затвердевания.
Затвердевшая деталь, также известная как отливка, выталкивается или выламывается из формы для завершения процесса.
Литье – это процесс, при котором металл плавится в жидкость, отвечающую определенным требованиям, и заливается в форму.
После охлаждения, затвердевания и очистки получается отливка заданной формы, размера и характеристик.
Поскольку литейная заготовка почти сформирована, ее можно достичь без механической обработки или с небольшой обработкой, что в определенной степени снижает стоимость и сокращает время изготовления.
Литье является одним из основных процессов современной обрабатывающей промышленности.
Большинство отливаемых материалов представляют собой металлы (такие как медь, железо, алюминий, олово, свинец и т. д.), которые изначально находятся в твердом состоянии, но нагреваются до жидкого состояния, в то время как материалы литейной формы могут быть песком, металлом или даже керамика.
Используемые методы различаются в зависимости от различных требований.
Литье является одним из первых процессов горячей обработки металлов, освоенных человеком, история которого насчитывает около 6000 лет.
Отливаемые металлы: медь, железо, алюминий, олово, свинец и т. д. Материалами обычной литейной формы являются необработанный песок, глина, жидкое стекло, смола и другие вспомогательные материалы.
Форма специального литья включает литье по выплавляемым моделям, литье по выплавляемым моделям, литье по металлу, литье по керамическим формам и т. д. (песок-сырец включает: кварцевый песок, магнезиальный песок, циркониевый песок, хромитовый песок, форстеритовый песок, кианитовый песок, графит песок, железный песок и др.)
Технологический процесс: жидкий металл → заливка → затвердевание → литье
Технологические характеристики:
Возможно изготовление деталей любой сложной формы, особенно со сложной формой внутренней полости.
Высокая адаптивность, неограниченные типы сплавов и почти неограниченный размер отливки.
Широкий источник материалов, отходы можно переплавлять, а инвестиции в оборудование невелики.
Высокий процент брака, низкое качество поверхности и плохие условия труда.
10 типов процесса литьяКлассификацию процесса литья можно разделить на следующие 10 типов, включая литье в песчаные формы, литье по выплавляемым моделям, литье под давлением, литье под низким давлением, центробежное литье, литье под давлением , вакуумное литье, литье под давлением, литье по выплавляемым моделям, непрерывное литье.
Далее мы представим определения, характеристики, преимущества и недостатки этих 10 различных процессов литья.
Думаю, после прочтения у вас появится новое понимание технологии литья.
1. Литье в песчаные формыЧто такое литье в песчаные формы ?
Способ литья для получения отливок в песчаную форму.
Отливки из стали, чугуна и большинства цветных сплавов могут быть получены литьем в песчаные формы.
Технологический процесс:
Процесс литья в песчаные формы
Технические характеристики:
Подходит для изготовления заготовок сложной формы, особенно со сложной внутренней полостью;
Широкие возможности адаптации и низкая стоимость;
Для некоторых материалов с плохой пластичностью, таких как чугун, литье в песчаные формы является единственным формовочным процессом для изготовления его деталей или заготовок.
Application s : Автомобильный блок двигателя, головка блока цилиндров, коленчатый вал и другие отливки.
2. Литье по выплавляемым моделямЧто такое литье по выплавляемым моделям ?
Вид метода литья, который обычно относится к изготовлению моделей из легкоплавких материалов, покрытию поверхности модели несколькими слоями огнеупорных материалов, а затем выплавлению модели из оболочки формы для получения формы без разделительной поверхности, который можно заполнить после выпечки при высокой температуре.
Технологический процесс:
Процесс литья по выплавляемым моделям
Advantage s :
3 90 высокая точность размеров и геометрическая точность;
- Высокая шероховатость поверхности;
- Может отливать сложные отливки, а литейные сплавы не ограничены.
Недостатки: сложность процедур и высокая стоимость
Применение s :
Он подходит для производства мелких деталей сложной формы, требующих высокой точности, или другой обработки, которую трудно выполнить, например лопаток турбины.
Что такое литье под давлением ?
Металлическая жидкость под высоким давлением вдавливается в прецизионную полость металлической формы на высокой скорости, металлическая жидкость охлаждается и затвердевает под давлением для формирования отливки.
Технологический процесс:
Advantage S :
- Жидкость металла подвергается высоким давлению, а скорость потока быстрое во время ликвидации вымира.
- Хорошее качество продукции, стабильный размер и хорошая взаимозаменяемость.
- Высокая эффективность производства и возможность многократного использования форм для литья под давлением.
- Подходит для массового производства с хорошей экономической выгодой.
Недостатки:
- Отливка склонна к образованию мелких пор и усадке.
- Литые детали обладают низкой пластичностью и не должны работать при ударных нагрузках и вибрации.
- При литье под давлением сплава с высокой температурой плавления срок службы формы низкий, что влияет на расширение производства литья под давлением.
Области применения:
Литье под давлением сначала применялось в автомобильной и приборостроительной промышленности, а затем постепенно распространилось на различные отрасли, такие как сельскохозяйственное машиностроение, станкостроение, электронная промышленность, национальная оборонная промышленность, компьютеры , медицинское оборудование, часы, фотоаппараты и бытовые приборы.
Что такое литье под низким давлением ?
Относится к методу заполнения формы жидким металлом под низким давлением (0,02–0,06 МПа) и кристаллизации под давлением с образованием отливки.
Технологический процесс:
Технические характеристики:
Давление и скорость при заливке можно регулировать, поэтому его можно применять для различных литейных форм (таких как металлические формы и песчаные формы), литья различные сплавы и отливки различных размеров.
Применяется заливка снизу, заливка металлической жидкостью стабильна, нет явления разбрызгивания, что позволяет избежать вовлечения газа и эрозии стенки и сердечника формования, что повышает квалификацию отливок.
Отливка кристаллизуется под давлением.
Отливка имеет плотную структуру, четкий контур, гладкую поверхность, высокие механические свойства.
Особенно подходит для литья крупных тонкостенных деталей.
Устранение необходимости засыпки стояка и увеличение коэффициента использования металла до 90-98%.
Низкая трудоемкость, хорошие условия труда, простое оборудование, легко реализуемая механизация и автоматизация.
Применение:
В основном используется в традиционных продуктах (головка цилиндра, ступица, рама цилиндра и т. д.).
Что такое центробежное литье ?
Это метод литья, при котором расплавленный металл заливают во вращающуюся форму, которая заполняется и затвердевает под действием центробежной силы.
Технологический процесс:
Advantage S :
- . Практически не наблюдается потребления металла в системе заливочной системы и в системе RISER, что обрабатывает достопримечательности.
- При производстве полых отливок стержень может отсутствовать, что позволяет значительно улучшить заполняемость металлом при производстве длинных трубчатых отливок.
- Отливка имеет высокую плотность, мало дефектов, таких как поры и шлаковые включения, и высокие механические свойства.
- Легко изготавливаемые композитные металлические отливки стволов и гильз.
Недостатки:
- Существуют определенные ограничения при использовании в производстве отливок специальной формы.
- Диаметр внутреннего отверстия отливки неточный, поверхность внутреннего отверстия шероховатая, качество низкое, припуск на обработку большой.
- Отливка склонна к ликвации по удельному весу.
Применение s :
Центробежное литье впервые было использовано для производства литых труб.
В стране и за рубежом металлургия, горнодобывающая промышленность, транспорт, ирригационное и дренажное оборудование, авиация, национальная оборона, автомобилестроение и другие отрасли промышленности использовали процессы центробежного литья для производства отливок из стали, железа и цветных углеродных сплавов.
Среди них наиболее распространено производство центробежных чугунных труб, гильз цилиндров двигателей внутреннего сгорания и втулок валов.
Что такое литье под давлением ?
Относится к методу литья, при котором жидкий металл заливается в металлическую форму под действием силы тяжести, охлаждается и затвердевает в форме для получения отливки.
Технологический процесс:
Advantage s :
- .
- Позволяет получать отливки с более высокой точностью размеров и меньшей шероховатостью поверхности, а также имеет хорошую стабильность качества.
- Поскольку песчаный сердечник не используется и используется редко, окружающая среда улучшается, уменьшается количество пыли и вредных газов, а также снижается трудоемкость.
Недостатки:
- Сама металлическая форма не является воздухопроницаемой, поэтому необходимо принять определенные меры для удаления воздуха и воздуха, создаваемого песчаной сердцевиной в полости.
- Металлическая форма не имеет уступов, и при затвердевании отливки легко возникают трещины.
- Металлические формы имеют более длительный производственный цикл и более высокую стоимость. Следовательно, хорошие экономические эффекты могут быть продемонстрированы только при массовом производстве.
Применение s :
Металлическое литье подходит для крупносерийного производства отливок из цветных сплавов, таких как алюминиевые и магниевые сплавы сложной формы, а также из чугуна и стали. отливки и слитки.
Что такое вакуумное литье под давлением ?
Усовершенствованный процесс литья под давлением, который улучшает механические свойства и качество поверхности деталей для литья под давлением путем удаления или значительного уменьшения количества пор и растворенных газов в детали для литья под давлением путем извлечения газа из полости формы для литья под давлением во время процесс литья под давлением.
Технологический процесс:
Advantage S :
- он может устранить или уменьшить воздушные пары внутри кастинга. литье, а также производительность покрытия.
- Для уменьшения противодавления полости можно использовать более низкое удельное давление и сплав с плохими литейными характеристиками. Большие отливки можно отливать под давлением с помощью небольших машин.
- Улучшает условия заполнения, позволяет отливать более тонкие отливки.
Недостатки:
- Уплотнительная конструкция пресс-формы сложна, изготовление и установка сложны, поэтому стоимость высока.
- Если метод вакуумного литья под давлением не контролируется должным образом, эффект не будет очень значительным.
Что такое литье под давлением ?
Это метод затвердевания жидкого или полутвердого металла под высоким давлением и проточной формовки для непосредственного получения продукта или заготовки.
Обладает такими преимуществами, как высокая степень использования жидкого металла, упрощенный процесс и стабильное качество.
Энергосберегающая технология обработки металлов давлением с потенциальными перспективами применения.
Технологический процесс:
Литье под давлением прямым прессованием:
Аэрозольная краска, литейный сплав, зажим формы, герметизация, удержание давления, сброс давления, разделение формы, извлечение заготовки и повторная установка.
Литье под давлением с непрямым выдавливанием:
Нанесение покрытия распылением, зажим формы, подача, заполнение, повышение давления, удержание давления, сброс давления, разделение, извлечение заготовки из формы, возврат в исходное положение.
Технические характеристики:
- Устраняет внутренние поры, усадку и другие дефекты.
- Низкая шероховатость поверхности и высокая точность размеров.
- Предотвращает появление трещин в литье.
- Легко реализуемая механизация и автоматизация.
Применение:
Может использоваться для производства различных типов сплавов, таких как алюминиевый сплав, цинковый сплав, медный сплав, чугун с шаровидным графитом и т.д.
Что такое литье по выплавляемым моделям (также известное как монолитное литье) ?
Это новый метод литья, при котором сочетание парафиновых или пенопластовых моделей, сходных по размеру и форме с литьем, образует модельный кластер.
После чистки и сушки огнеупорного покрытия его закапывают в сухой кварцевый песок для вибрации.
Заливка под отрицательным давлением для испарения модели, жидкий металл занимает положение модели и образуется после затвердевания и охлаждения.
Технологический процесс:
Предварительное вспенивание → Пеноформование → Покрытие погружением → Сушка → Моделирование → Заливка → Падающий песок → Очистка

Применение s :
Подходит для производства прецизионных отливок различных размеров со сложной структурой.
Ограничений по видам сплавов и партиям выпуска нет.
Например, коробка двигателя из серого чугуна, колено из высокомарганцовистой стали и так далее.
Что такое непрерывное литье ?
Это усовершенствованный метод литья. Его принцип заключается в непрерывной заливке расплавленного металла в специальную металлическую форму, называемую кристаллизатором.
Затвердевшая (покрытая коркой) отливка непрерывно вытягивается с другого конца формы, и может быть получена отливка любой длины или определенной длины.
Технологический процесс:
Технические характеристики:
Поскольку металл быстро охлаждается, кристаллы плотные, структура однородная, механические свойства хорошие.
Экономьте металл и повышайте производительность.
Упрощенные процедуры, исключающие моделирование и другие процедуры, что снижает трудоемкость и значительно сокращает требуемую производственную площадь.
Производство непрерывного литья заготовок легко осуществить механизацией и автоматизацией и повысить эффективность производства.
Применение s :
Непрерывное литье может использоваться для литья стали, железа, медных сплавов, таких профилей постоянного сечения, алюминиевых сплавов, магниевых сплавов с в виде слитков, слябов, стержневой заготовки, труб и т. д.
- Скачать PDF 10 типов процесса литья
Слишком высокая температура заливки вызовет набухание песчаной формы, особенно для отливок из серого чугуна со сложными песчаными сердечниками
При повышении температуры заливки ≥ 1420 ℃, количество отходов увеличивается, а при температуре заливки 1460 ℃ количество отходов достигает 50%.
В производстве температуру расплавленного чугуна можно хорошо контролировать с помощью плавки в индукционной печи.
2. Возможные дефекты при слишком низкой температуре заливки(1) Марганцово-сульфидная пористость Этот вид пористости расположен ниже поверхности отливок из серого чугуна и в основном на поверхности.
Часто обнажается после обработки.
Диаметр пористости составляет около 2 ~ 6 мм.
Иногда в скважине имеется небольшое количество шлака.
Металлографические исследования показывают, что этот дефект вызван сегрегацией MnS и смешиванием шлака, поскольку температура разливки низкая, а количество Mn и s в расплавленном чугуне высокое.
Такое содержание S и подходящее содержание Mn (0,5% ~ 0,65%) могут значительно улучшить чистоту расплавленного железа и эффективно предотвратить такие дефекты.
(2) Пористость и пористость, вызванные газом песчаного керна, часто возникают из-за плохого отвода песчаного керна.
Поскольку песчаный стержень в основном затвердевает в стержневом ящике во время изготовления стержня, количество выпускных отверстий песчаного стержня часто бывает недостаточным.
Для формирования вентиляционных отверстий после затвердевания керна может быть проведено дополнительное сверление.
(3) После обработки жидкими шлаковыми включениями под поверхностью отливок из серого чугуна будут обнаружены одиночные небольшие отверстия.
Диаметр отверстий обычно составляет 1 ~ 3 мм.
В некоторых случаях имеются только 1-2 небольших отверстия.
Металлографическое исследование показывает, что эти небольшие отверстия появляются вместе с небольшим количеством жидкого шлака, но выделения серы там не обнаружено.
Исследования показывают, что дефект связан с температурой заливки.
При температуре заливки выше 1380 ℃ такой дефект в отливке не обнаруживается, поэтому температуру заливки следует контролировать на уровне 1380-1420 ℃.
Следует отметить, что изменение конструкции системы заливки не устранило этот недостаток.
Таким образом, этот дефект можно считать вызванным низкой температурой заливки и заливкой расплавленного чугуна в микровосстановительной атмосфере.
Наиболее распространенная причина низкой температуры разливки заключается в том, что расплавленный чугун перед разливкой долгое время находился в открытом ковше для отвода тепла.
Потери тепла можно значительно уменьшить, если использовать крышку ковша с изоляционным материалом.
Процесс производства отливок
Отливка производится путем плавления металла или сплава и заливки его в форму для охлаждения и затвердевания.
Процесс производства литья представляет собой сложную совокупность комплексных процессов, включающую в себя множество производственных процессов и звеньев, от подготовки металлических и неметаллических материалов до плавки сплава, формовки, изготовления стержней, литья в формы, очистки, устранения дефектов, плавки обработка отливок до получения качественных отливок.
Процесс производства отливок включает следующие основные процессы: подготовка формовочных и стержневых смесей, лепка, плавка, сушка песчаных форм, заливка, очистка, термообработка отливок.
Процесс подготовки формовочной смеси напрямую влияет на качество формовочной смеси.
Подготовка формовочной смеси обычно делится на подготовку и проверку сырья и подготовку и контроль качества формовочной смеси.
2. ЛепкаСпособ и процесс изготовления песчаной формы с помощью формовочной смеси, модели и другого технологического оборудования называется формованием.
Существует множество методов формования, которые зависят от формы, размера и технических требований к отливке.
3. ПлавкаПроцесс и операция перевода металла из твердого состояния в жидкое путем нагревания и удаления примесей в расплавленном металле посредством металлургической реакции для приведения его температуры и состава в соответствие с заданными требованиями становятся плавкой.
Существует множество видов оборудования для плавки металлов. Мы производим платформы из чугуна и обычно используем вагранку для литья станков.
Сухое литье обычно используется для некоторых крупных или высококачественных отливок.
Например, большая чугунная платформа, отливка станины станка, верстак станка, отливка станка и т.д. .
6. ОчисткаПроцесс удаления поверхностного налипания песка, формовочного песка и излишков металла с отливки после отсыпки песка называется очисткой
7. Термическая обработка отливкиПроцесс нагрева отливки до определенного диапазона температур, выдерживая его в течение определенного периода времени, а затем охлаждая до соответствующей температуры с заданной скоростью для получения ожидаемой структуры и свойств, называется термообработкой литья.
Целью термической обработки отливки является устранение литейного напряжения отливки.
Например, чугунная платформа, станочное литье и станочный верстак могут обрабатываться только после термической обработки .
Какие литейные металлы обычно используются?
Обычные литые металлы включают серый чугун, ковкий чугун, ковкий чугун и литейную сталь.
Обычно отливаемые цветные металлы включают латунь, оловянную бронзу, бронзу без олова, алюминиевый сплав и т. д.
Сколько существует видов литейных материалов ?Существует 8 типов обычно используемых литейных материалов, в том числе: серый чугун, ковкий чугун, ковкий чугун, вермикулярный чугун, литая сталь, литой алюминиевый сплав, литая бронза, литая латунь и т. д.
Их характеристики и области применения описывается следующим образом:
Серый чугунХорошая текучесть, малая усадка при охлаждении, низкая прочность, пластичность и ударная вязкость.
Модуль упругости варьируется от 80000 до 140000 МПа в зависимости от микроструктуры.
Прочность на сжатие в 3-4 раза выше, чем на растяжение.
Хорошая износостойкость и поглощение вибрации.
Нечувствителен к зазубринам и обладает хорошей режущей способностью. Плохая производительность сварки.
Его нельзя использовать в течение длительного времени при температуре выше 300 ~ 400 ℃, что составляет 85% ~ 90% чугуна
M Легкий чугунЛитейные свойства хуже, чем у серого чугуна, и лучше, чем у стального литья.
Применяется для изготовления мелких тонкостенных отливок с определенными требованиями к прочности и ударной вязкости.
Хорошая коррозионная стойкость и хорошая технологичность.
Ударная вязкость в 3-4 раза выше, чем у серого чугуна
Ковкий чугунЛитейные характеристики хуже, чем у серого чугуна, легко возникают дефекты.
Хорошая режущая способность, термическая обработка может привести к изменению производительности в большом диапазоне.
Прочность на растяжение выше, чем у чугуна и стальной отливки, а отношение предела текучести к пределу прочности выше, чем у ковкого чугуна и стали.
Пластичность наилучшая у чугуна, а ударная вязкость ниже, чем у стали, но намного выше, чем у серого чугуна.
Обладает хорошими низкотемпературными характеристиками.
Усталостная прочность высокая, близкая к стали №45, но чувствительность к концентрации напряжений ниже, чем у стали.
Хорошая износостойкость, термостойкость и коррозионная стойкость.
Коэффициент гашения вибрации стали, ковкого чугуна и серого чугуна составляет 1:1,8:4,3.
Все чаще используется в качестве важных деталей
Чугун с вермикулярным графитомМеханические свойства чугуна с вермикулярным графитом находятся между серым чугуном и ковким чугуном, и он имеет хорошую плотность, теплостойкость и износостойкость.
Его литейные свойства лучше, чем у чугуна с шаровидным графитом, и близки к свойствам серого чугуна.
Его прочность аналогична прочности чугуна с шаровидным графитом, а антивибрационные, теплопроводные и литейные свойства аналогичны серому чугуну, но он имеет лучшую пластичность и сопротивление усталости, чем у серого чугуна.
Чугун с вермикулярным графитом неизбежно содержит определенное количество сфероидального графита.
Увеличение сфероидального графита повысит его прочность и жесткость, но за счет снижения литейных свойств расплавленного чугуна и ухудшения технологичности и теплопроводности отливок.
C ast steelХарактеристики литья плохие, текучесть плохая, усадка большая, но он обладает высокими комплексными механическими свойствами, т.е. высокой прочностью, ударной вязкостью и пластичностью.
Прочность на растяжение почти равна прочности на сжатие.
Некоторые специальные литые стали обладают особыми свойствами, такими как жаростойкость и коррозионная стойкость
Литой алюминиевый сплавПлотность алюминиевого сплава составляет всего 1/3 плотности железа, и из него изготавливают различные легкие конструкции.
Некоторые алюминиевые сплавы можно упрочнить термической обработкой, чтобы они имели лучшие комплексные свойства
Литая бронза Делится на оловянную бронзу и безоловянную бронзу.
Оловянная бронза обладает хорошей износостойкостью и коррозионной стойкостью, высокой прочностью и твердостью, плохими литейными характеристиками и легко образующейся сегрегационной и усадочной пористостью.
Закалка не оказывает укрепляющего действия.
Алюминиевая бронза или свинцовая бронза обычно используется в бронзе, не содержащей олова, с плохими характеристиками литья.
Алюминиевая бронза обладает высокой прочностью, высокой износостойкостью и коррозионной стойкостью.
Свинцовая бронза обладает высокой усталостной прочностью, хорошей теплопроводностью и кислотостойкостью
Литая латуньБольшая усадка, высокая общая прочность, хорошая пластичность, хорошая коррозионная стойкость и износостойкость.
Good cutting performance
Comparison of common cast iron materialsGray cast iron | Malleable iron | Ductile iron | Vermicular graphite cast iron | |
Graphite morphology | Flaky | Флокулянт | Шаровидный | Вермикулярный |
Резюме | Чугун, полученный путем полного проведения первой стадии процесса графитизации | Белый чугун представляет собой разновидность чугуна с высокой прочностью и ударной вязкостью, полученный графитизирующим отжигом | Сфероидальный графит получен сфероидизацией и модификацией | Вермикулярный графит получен вермикуляцией и модификацией |
Литейные свойства | 9 | чем у серого чугуна | хуже, чем у серого чугуна | хорошо |
режущая способность | хорошо | good | good | very good |
Wear resistance | good | good | good | good |
Strength / hardness | Ferrite: low Pearlite: high | Higher than gray cast iron | Очень высокая | Выше серого чугуна |
Пластичность/вязкость | Очень низкая | Близка к стальному литью | Очень высокая | Выше серого чугуна |
Применение | Цилиндр, маховик, поршень, тормозное колесо, нагнетательный клапан и т.![]() | Мелкие и средние детали сложной формы и воздействия на подшипники, такие как гаечные ключи, сельскохозяйственные инструменты и шестерни | Детали, требующие высокой прочности и ударная вязкость, такие как коленчатый вал и клапан двигателя внутреннего сгорания | Детали, которые могут работать в условиях термического удара, такие как головка блока цилиндров дизельного двигателя |
Примечания | Низкая чувствительность к меткам | Ковка и штамповка не допускаются | Высокая жаростойкость, коррозионная стойкость и усталостная прочность (в 2 раза выше серого чугуна) | Теплопроводность, сопротивление термоусталости, сопротивление росту и окислению |
Как отлить запчасти дома?
Во-первых, должно быть устройство, способное плавить железо или алюминий.
Если суточная выработка не большая, то рекомендуется купить электрическую печь небольшой мощности, а можно использовать и старую.
Керосиновые печи также можно использовать для плавки алюминия.
Помните, железо и алюминий нельзя использовать в одной печи, иначе материал трудно контролировать.
Конечно, если нет потребности в материале, другое дело.
Далее нам понадобится пресс-форма, которая подгоняется под детали.
Кроме того, необходим еще и песок. В это время необходима мешалка для песка. Если вы не покупаете его, вы можете использовать ручное смешивание.
С помощью некоторых простых инструментов моделирования, описанных выше, вы можете лепить, плавить и заливать.
В это время изготавливается литейная заготовка.
Наконец, чистящие инструменты необходимы для снятия сливного стояка и удаления заусенцев.
Добавление дробеструйного ролика сделает отливку более красивой.
Литье – Энциклопедия Нового Света
Эта статья о производственном процессе. Чтобы узнать о других значениях этого термина, см. Кастинг (значения) .
Чугун в песчаной форме.
Литье — это производственный процесс, при котором расплавленный материал, такой как металл или пластик, помещают в форму, дают ему затвердеть в форме, а затем выталкивают или выламывают для изготовления готовой детали. Литье применяется для изготовления деталей сложной формы, которые было бы трудно или неэкономично изготовить другими способами (например, вырубкой из твердого материала).
Он использовался более 5000 лет для создания предметов искусства и инструментов. Самым ранним отливом была медная лягушка, датируемая 3200 91 719 гг. до н. э. , отлит в Месопотамии. Сегодня он используется во всем мире для всего: от изготовления огромных инструментов до небольших произведений искусства, таких как украшения. В будущем литье можно будет использовать даже для неметаллических вещей. Одной из целей, которая сейчас проходит испытания, является использование пресс-формы для создания искусственного сердечного клапана. Однако вместо пластика они используют живые человеческие клетки в смеси смолы, чтобы сделать живой клапан.
Литье может использоваться для формования горячих жидких металлов или плавких пластиков (называемых термопластами) или различных материалов, которые отверждаются в холодном состоянии после смешивания компонентов, таких как некоторые пластмассовые смолы ( например, эпоксидные смолы), водоотверждаемые материалы, такие как бетон или гипс, а также материалы, которые становятся жидкими или пастообразными во влажном состоянии, такие как глина, которую, когда она достаточно высохнет, чтобы стать твердой, извлекают из формы, дополнительно сушат и обжигают в печи.
Содержание
- 1 История
- 1.1 Раннее металлическое литье
- 1.2 Металлическое литье от Средневековья до индустриализации
- 1.3 Раннее чугунное литье в Китае
- 1.4 Чугунное литье в период индустриализации
- 1.5 Литье и художественные работы
- 2 Литье в одноразовые формы
- 2.1 Литье в песчаные формы
- 2.
2 Литье гипсовое (из металлов)
- 2.3 Литье из гипса, бетона или пластмассы
- 2.4 Обшивка корпуса
- 2.5 Литье по выплавляемым моделям
- 3 Многоразовое литье в формы
- 3.1 Литье в постоянную форму
- 3.1.1 Литье под давлением
- 3.2 Центробежное литье
- 3.3 Непрерывное литье
- 3.1 Литье в постоянную форму
- 4 Скорость охлаждения
- 5 Усадка
- 5.1 Объемная усадка
- 5.2 Линейная усадка
- 6 Каталожные номера
- 7 кредитов
Замена всегда является фактором при принятии решения о том, следует ли использовать другие методы вместо литья. Альтернативы включают детали, которые можно штамповать на штамповочном прессе или глубокой вытяжке, штамповать, детали, которые можно изготавливать методом экструзии или холодной гибки, а также детали, которые можно изготавливать из высокоактивных металлов.
Процесс литья подразделяется на две отдельные подгруппы: литье в формы одноразового и многоразового использования:
История
Раннее металлическое литье
Древнейшие сохранившиеся литые детали – оружие и предметы культа из меди – происходят из Ближнего Востока и Индии. Они датируются периодом около 3000 лет г. до н.э. Возможно, технология литья металлов с использованием форм зародилась на Ближнем Востоке. Однако есть предположения, что этот процесс мог быть разработан в Индии и Китае.
Плавильные печи раннего железного века частично восходят к керамическим печам для обжига. Создание модели и пресс-формы было освоено с самого начала очень хорошо. Уже использовались утраченные формы из суглинка и глины, восковые модели, штучные, а также постоянные формы из камня и металла для серийного производства отливок. Создание полых пространств с помощью стержней уже доказано самыми древними обнаруженными отливками.
Металлическое литье от средневековья до индустриализации
После великих достижений в области литья металлов в древности потребовалось много времени, чтобы достичь прежнего уровня в западном средневековье. Однако, в то время как практически нет непрерывной документации о технологии литья в древности, немецкий монах Тофилус уже очень интенсивно исследовал формование и литье около 1140 года в своем трактате «О различных искусствах». «Книги о фейерверках», особенно книга итальянца Бирингуччо, были написаны после 1500 г. г. н.э. г. также следует упомянуть в этом контексте. Суглинок, гипс и воск были наиболее важными рабочими материалами. Для плавки медных, оловянных и свинцовых сплавов были доступны тигли, а позже и пламенные печи. Литье с помощью формовочного песка было обычным делом для мелких деталей; постоянные формы имели большое значение для серийного литья свинцовых и оловянных материалов. Вначале основное внимание уделялось литью колоколов и другого канцелярского оборудования. Рельефное литье соответствовало художественному качеству античного металлического литья начала нового времени.
Раннее чугунное литье в Китае
Китайцы научились плавить железо с 500 г. г. до н.э. , за 2000 лет до европейцев. Новые раскопки доказали, что массовое производство литых орудий и сельскохозяйственного инвентаря удалось после развития чугунного литья. Европейское чугунное литье до индустриализации
Около 1400 г. пушечные стволы и пули были первыми изделиями, отлитыми из чугуна в Европе. Технология формования бочек соответствовала формованию глины с помощью шаблонов, разработанных уже в средние века для литья бронзы. После технологии формования суглинка, использовавшейся вначале для серийного производства пуль, появилось использование неразъемных форм из чугуна. В середине пятнадцатого века из чугуна изготавливали такие предметы, как водопроводные трубы и колокола. Первый период художественного применения чугунного литья начался в 1500 году с производства плит для печей, духовок, памятников и фонтанов.
Чугунное литье в период индустриализации
Развитие новых технологий и повышенный спрос на литые детали дали огромный импульс развитию литейной промышленности во второй половине восемнадцатого века.
Художественное оформление чугунных отливок не только ограничивалось созданием декоративных предметов, но также использовалось для изготовления деталей машин и предметов повседневного обихода.
Литье и художественные изделия
С давних времен и до наших дней литье металлов использовалось для создания произведений искусства.
Одноразовое литье в формы
Одноразовое литье в формы — это общая классификация, включающая литье из песка, пластмассы, ракушек и инвестиционных форм (метод выплавляемых моделей). Этот метод литья в формы предполагает использование временных, одноразовых форм.
Литье в песчаные формы
Литье в песчаные формы требует много дней для производства с высокой производительностью (1-20 шт./час-форма) и не имеет себе равных при производстве крупных деталей. Зеленый (влажный) песок практически не имеет ограничения по массе, в то время как сухой песок имеет практический предел массы 2300-2700 кг. Песок связывают вместе с помощью глин (как в зеленом песке), химических связующих или полимеризованных масел. Песок в большинстве операций может многократно перерабатываться и требует незначительных дополнительных затрат.
Подготовка песчаной формы выполняется быстро и требует шаблона, который может «штамповать» шаблон для литья. Как правило, литье в песчаные формы используется для обработки низкотемпературных металлов, таких как сплавы железа, меди, алюминия, магния и никеля. Литье в песчаные формы также можно использовать для высокотемпературных металлов, где другие методы были бы нецелесообразны. Это, безусловно, самая старая и наиболее понятная из всех техник. Следовательно, автоматизация может быть легко адаптирована к производственному процессу, несколько труднее к проектированию и изготовлению форм. Эти формы должны соответствовать строгим стандартам, поскольку они являются сердцем процесса литья в песчаные формы, что создает наиболее очевидную потребность в человеческом контроле.
Литье из гипса (из металлов)
Литье из гипса аналогично литью в песчаные формы, за исключением того, что песок заменяется гипсом. Штукатурная смесь фактически состоит из 70-80% гипса и 20-30% усилителя и воды. Как правило, изготовление формы занимает менее недели, после чего достигается производительность 1-10 единиц формы в час для изделий массой от 45 кг и до 30 г с очень высоким разрешением поверхности и точными допусками.
После использования и растрескивания обычный гипс не может быть легко переработан. Гипсовое литье обычно используется для цветных металлов, таких как сплавы на основе алюминия, цинка или меди. Его нельзя использовать для литья черных металлов, потому что сера в гипсе медленно реагирует с железом. Перед подготовкой формы на шаблон наносится тонкий слой разделительного состава, чтобы предотвратить прилипание формы к шаблону. Устройство встряхивают, чтобы гипс заполнил небольшие полости вокруг рисунка. Форму снимают после того, как гипс схватится.
Литье из гипса представляет собой шаг вперед в сложности и требует навыков. Автоматические функции легко передаются роботам, но для более точного проектирования моделей требуется еще более высокий уровень непосредственной помощи человека.
Литье из гипса, бетона или пластиковой смолы
Сам гипс может быть отлит, как и другие химические твердеющие материалы, такие как бетон или пластиковая смола, с использованием одноразовых отходов Формы многократного использования шт.1708 формы или формы из гибкого материала, такого как латексная резина (который, в свою очередь, поддерживается внешней формой). При отливке гипса или бетона готовое изделие, в отличие от мрамора, относительно непривлекательно, лишено прозрачности, поэтому его обычно окрашивают, часто таким образом, чтобы он выглядел как металл или камень. В качестве альтернативы отлитые первые слои могут содержать цветной песок, чтобы придать вид камня. Отливая бетон, а не гипс, можно создавать скульптуры, фонтаны или сиденья для использования на открытом воздухе. Имитация высококачественного мрамора может быть сделана с использованием определенных химически отвержденных пластиковых смол (например, эпоксидной или полиэфирной) с добавлением порошкообразного камня для окраски, часто с использованием нескольких цветов. Последнее является распространенным средством изготовления привлекательных умывальников, столешниц для умывальников и т.д. душевые кабины с умелой работой с несколькими цветами, что приводит к имитации узоров окрашивания, которые часто встречаются в натуральном мраморе или травертине.
Формование в оболочке
Формование в оболочке также похоже на литье в песчаную форму, за исключением того, что смесь песка и 3-6 процентов смолы удерживает зерна вместе. Наладка и изготовление шаблонов оболочковых форм занимает недели, после чего достигается производительность 5-50 штук пресс-форм в час. Изделия из алюминия и магния в среднем весят около 13,5 кг в качестве нормального предела, но возможно литье изделий весом от 45 до 90 кг. Толщина стенок оболочковой формы варьируется от 3 до 10 мм в зависимости от времени формирования смолы.
Существует дюжина различных этапов обработки оболочковых форм, включая:
- первоначальная подготовка металлической пластины
- смешивание смолы и песка
- режим нагрева, обычно до 505-550 K
- переворачивание шаблона (песок находится на одном конце ящика, а узор на другом, и ящик переворачивается на время, определяемое желаемой толщиной фрезы)
- засолка и запекание
- удаление вклада
- вставка сердечников
- повторение для другой половины
- сборочная форма
- форма для заливки
- снятие литья
- чистка и обрезка.
Смесь песка и смолы может быть переработана путем сжигания смолы при высоких температурах.
Литье по выплавляемым моделям
Литье по выплавляемым моделям (процесс по выплавляемым моделям) дает детализированный и точный продукт, но механические свойства не являются хорошими, поскольку процесс включает медленное охлаждение.
Пенополистирол также используется в литье по выплавляемым моделям — см. литье по выплавляемым моделям.
По прошествии определенного периода времени, обычно недель, можно производить 1–1000 шт./час форм массой 2,3–2,7 кг. Изделия весом до 45 кг и весом до 30 г возможны для штучного производства.
Процесс начинается с создания пресс-формы для литья под давлением с заданными характеристиками. Эта форма будет использоваться для впрыска воска для создания моделей, необходимых для литья по выплавляемым моделям. Шаблоны прикрепляются к центральному восковому литнику, создавая сборку или форму. Литник содержит заливную чашу, через которую расплавленный металл будет заливаться в сборку.
Теперь восковую сборку несколько раз погружают в керамический раствор, в зависимости от желаемой толщины оболочки. Поверх каждого керамического слоя добавляется слой мелкого песка (обычно циркона). Этот процесс будет повторяться до тех пор, пока не будет создана нужная оболочка.
После изготовления скорлупы в соответствии с требуемыми параметрами воск необходимо удалить; обычно это достигается с помощью автоклава. Отсюда и пошло название «процесс выплавляемого воска». Это оставляет отпечаток нужной отливки, которая будет залита металлом. Однако перед литьем снаряды необходимо нагреть в печи, чтобы они не сломались в процессе литья.
Далее в горячую керамическую оболочку заливается нужный металл. Металл заполняет каждую часть сборки, полость центрального литника и заливной стакан. Отдельные части будут удалены после того, как форма остынет и оболочка будет удалена. Оболочку обычно удаляют струей воды, хотя можно использовать и другие методы. Остались литые металлические детали, но они все еще прикреплены к литнику в сборе. Отдельные части удаляются методом холодного разрушения (погружение в жидкий азот и отламывание частей молотком и зубилом) или большими отрезными пилами.
Большинство отливок по выплавляемым моделям требуют некоторой степени механической обработки после отливки, чтобы удалить литник и направляющие, а также улучшить качество поверхности. Выполняются шлифовальные операции по снятию ворот. Детали также проверяются, чтобы убедиться, что они были отлиты правильно, а если нет, то их исправляют или утилизируют. В зависимости от оборудования для литья по выплавляемым моделям и спецификаций дополнительные отделочные работы могут выполняться на месте, с привлечением субподрядчика или вообще не выполняться.
Литье по выплавляемым моделям позволяет получать изделия исключительно высокого качества из всех типов металлов. Он имеет особое применение при изготовлении очень жаропрочных металлов, таких как легированные стали или нержавеющие стали, особенно таких, которые нельзя отливать в металлических или гипсовых формах, а также тех, которые трудно обрабатывать или обрабатывать.
Литье по выплавляемым моделям часто используется в аэрокосмической и энергетической промышленности для производства монокристаллических турбинных лопаток, которые обладают превосходным сопротивлением ползучести по сравнению с равноосными отливками. Комбинация медленных скоростей охлаждения, затравочных кристаллов и сложной системы литника и литника, называемой «косичкой», используется для производства монокристаллических отливок.
Многоразовое литье в формы
Многоразовое литье в формы отличается от одноразовых процессов тем, что форму не нужно переделывать после каждого производственного цикла. Этот метод включает в себя как минимум четыре различных метода: постоянное литье, кокиль, центробежное литье и непрерывное литье.
Литье в постоянную форму
Литье в постоянную форму (обычно для цветных металлов) требует времени наладки порядка недель для подготовки стального инструмента, после чего достигается производительность 5-50 штук/час-форма с верхним пределом массы 9 кг на изделие из сплава железа (ср. до 135 кг для многих деталей из цветных металлов) и нижним пределом около 0,1 кг. Стальные полости перед обработкой покрывают огнеупорной пропиткой из ацетиленовой сажи, что позволяет легко снимать заготовку и увеличивает срок службы инструмента. Постоянные формы имеют срок службы, который варьируется в зависимости от технического обслуживания, после чего они требуют повторной отделки или замены. Литые детали из постоянной формы обычно показывают увеличение прочности на растяжение на 20% и увеличение удлинения на 30% по сравнению с продуктами литья в песчаные формы.
Единственная необходимая информация — регулярное нанесение покрытия. Как правило, литье в постоянные формы используется при формовании сплавов на основе железа, алюминия, магния и меди. Процесс высоко автоматизирован.
Литье под давлением
Литье под давлением — это процесс подачи расплавленного металла под высоким давлением в полости стальных форм. Формы называются штампами. Штампы различаются по сложности для производства любых деталей из цветных металлов (которые не обязательно должны быть такими же прочными, твердыми или жаростойкими, как сталь) от смесителей для раковины до блоков цилиндров (включая скобяные изделия, составные части машин, игрушечные автомобили и т. д.). Фактически, этот процесс подходит для изготовления любой металлической детали, которая:
- должен быть точным (размеры плюс-минус всего 50 мкм — на коротких расстояниях),
- должен иметь очень гладкую поверхность, на которую можно наносить блестящее покрытие без предварительной полировки и полировки,
- имеют очень тонкие секции (например, листовой металл – всего 1,2 мм),
- должны производиться намного экономичнее, чем детали, которые в основном подвергаются механической обработке (многогнездные формы для литья под давлением, работающие на высокой скорости, намного производительнее, чем станки или даже штамповочные прессы)9.0046
- должен иметь очень гибкий дизайн; одно литье под давлением может иметь все характеристики сложной сборки.
Если потребуется несколько операций механической обработки или потребуется сборка нескольких деталей (для изготовления готовой детали), литье под давлением, вероятно, будет гораздо более экономичным. Этот уровень универсальности поместил литье под давлением в число самых массовых продуктов, производимых в металлообрабатывающей промышленности.
Обычно используемые в литье под давлением металлы включают цинк и алюминий. Обычно это не чистые металлы; скорее сплавы, которые имеют лучшие физические характеристики.
В последние годы пластиковые детали, изготовленные методом литья под давлением, заменили некоторые детали, изготовленные методом литья под давлением, поскольку они, как правило, дешевле (и легче, что особенно важно для автомобильных деталей с учетом стандартов экономии топлива). Пластмассовые детали практичны (особенно теперь, когда стало возможным покрытие пластмассы), если не требуется твердость и если детали можно изменить, чтобы они приобрели необходимую прочность.
Процесс литья под давлением состоит из четырех основных этапов. Сначала форму обрызгивают смазкой и закрывают. Смазка помогает контролировать температуру штампа, а также помогает при удалении отливки. Затем расплавленный металл впрыскивается в пресс-форму под высоким давлением. Высокое давление обеспечивает отливку такой же точной и ровной, как форма. Как только полость заполнена, давление поддерживается до тех пор, пока отливка не станет твердой (хотя этот период обычно максимально сокращается за счет водяного охлаждения формы). Наконец, пресс-форма открывается, и отливка выбрасывается.
Не менее важным, чем впрыск под высоким давлением, является высокоскоростной впрыск, необходимый для заполнения всей полости до того, как какая-либо часть отливки затвердеет. Таким образом, можно избежать разрывов (испорченных отделкой и даже ослабления отливки), даже если конструкция требует очень тонких участков, которые трудно заполнить.
Перед запуском цикла матрица должна быть установлена в машину для литья под давлением (настроена) и доведена до рабочей температуры. Для этой настройки требуется 1-2 часа, после чего цикл может занять от нескольких секунд до нескольких минут в зависимости от размера отливки. Максимальные пределы массы для деталей из магния, цинка и алюминия составляют примерно 4,5 кг, 18 кг и 45 кг соответственно. Типичный набор штампов выдерживает 500 000 выстрелов в течение всего срока службы, при этом срок службы сильно зависит от температуры плавления используемого металла или сплава. Алюминий и его сплавы обычно сокращают срок службы матрицы из-за высокой температуры жидкого металла, что приводит к износу полостей стальной формы. Формы для литья цинка под давлением служат почти бесконечно долго из-за более низкой температуры цинка. Формы для литья под давлением из латуни являются самыми недолговечными из всех. И это несмотря на то, что во всех случаях полости литейной формы изготавливаются из самой лучшей доступной легированной стали для «горячей обработки».
Выстрел происходит каждый раз, когда штамп заполняется металлом. Выстрелы отличаются от отливок тем, что в матрице может быть несколько полостей, что дает несколько отливок за выстрел. Также дробь состоит не только из отдельных отливок, но и из «лома» (который, в отличие от лома от механической обработки, не продается дешево, а переплавляется), состоящего из металла, затвердевшего в каналах, ведущих в и из полостей. Сюда входят, например, литник, бегунки и переливы. Кроме того, обычно есть некоторый незапланированный тонкий лом, называемый заусенцем, в результате того, что формы не плотно прилегают друг к другу.
Кубик должен выполнять четыре основные функции. Во-первых, он должен удерживать расплавленный металл в форме окончательной отливки. Пресс-форма также должна обеспечивать путь для попадания расплавленного металла в литейную полость. В-третьих, матрица предназначена для отвода тепла от отливки. Наконец, матрица должна иметь возможность выбрасывать затвердевшую отливку.
Поскольку наборы штампов открываются и закрываются вдоль линии разъема отливки, конструктивные элементы, такие как поднутрения, не могут быть отлиты без добавления подвижных направляющих в набор штампов. В противном случае эти функции должны быть добавлены (более дорого) за счет операций вторичной обработки.
Машины для литья под давлением оцениваются по силе зажима, которую они могут приложить. Стандартные размеры варьируются от 100 до 4000 тонн. Наряду с размером есть две основные категории, на которые попадают машины для литья под давлением. Это машины с горячей камерой для цинка и металлов с более низкой температурой плавления или машины с холодной камерой для алюминия и металлов с более высокой температурой плавления. Машина для литья под давлением автоматически открывает и закрывает форму и впрыскивает жидкий металл под высоким давлением и как можно быстрее, в случае цинка до нескольких сотен раз в час. (Однако самые маленькие цинковые машины могут выполнять тысячи циклов в час.) Иногда предусмотрены средства для автоматического удаления дроби и повторного цикла машины. Самые большие машины размером с автомобиль.
Часто проводится вторичная операция по отделению отливок от металлолома; это часто делается с помощью обрезной матрицы в силовом прессе или гидравлическом прессе. Более старый метод – это разделение вручную или распиливанием, и в этом случае может потребоваться шлифовка, чтобы сгладить метку литника, где расплавленный металл входит или выходит из полости. Наконец, менее трудоемкий метод — кувыркаться, если ворота тонкие и легко ломаются. Разделение должно последовать.
Большинство машин для литья под давлением выполняют другие вторичные операции для получения элементов, которые трудно отлить. Наиболее распространенным является нарезание резьбы (чтобы получить винт).
Или поверхность можно улучшить; например, полировка и полировка. Или гальваника или покраска.
В машине с горячей камерой металл закачивается в пресс-форму непосредственно из печи с расплавленным металлом. Системы с холодной камерой переносят расплавленный металл из печи в барабан дроби. Затем металл проталкивается из цилиндра в матрицу.
Центробежное литье
Центробежное литье не зависит ни от гравитации, ни от давления, поскольку оно создает собственную принудительную подачу с использованием временной песчаной формы, удерживаемой в прядильной камере. Время выполнения варьируется в зависимости от приложения. Полу- и настоящая центробежная обработка позволяют производить 30-50 штук пресс-форм в час, с практическим ограничением для периодической обработки примерно 9 штук. 000 кг общей массы с типичным лимитом на единицу 2,3-4,5 кг.
В промышленном отношении центробежное литье железнодорожных колес было ранним применением метода, разработанного немецкой промышленной компанией Krupp, и эта возможность способствовала быстрому росту предприятия.
Небольшие художественные изделия, такие как ювелирные изделия, часто отливают этим методом по выплавляемым моделям, так как силы позволяют довольно вязким жидким металлам течь через очень маленькие каналы и проникать в мелкие детали, такие как листья и лепестки. Этот эффект аналогичен преимуществам вакуумного литья, также применимого к литью ювелирных изделий.
Непрерывное литье
Непрерывное литье — это усовершенствование процесса литья для непрерывного крупносерийного производства металлических профилей с постоянным поперечным сечением. Расплавленный металл заливают в медную форму с открытым концом, охлаждаемую водой, что позволяет сформировать «кожу» из твердого металла поверх все еще жидкого центра. Прядь, как ее теперь называют, извлекается из формы и подается в камеру с валками и водяными форсунками; ролики поддерживают тонкую оболочку пряди, в то время как спреи отводят тепло от пряди, постепенно затвердевая прядь снаружи внутрь. формирования процессов, или на склад. Размеры отливок могут варьироваться от полосы (толщиной несколько миллиметров и шириной около пяти метров) до заготовок (9от 0 до 160 мм) в плиты (шириной 1,25 м и толщиной 230 мм). Иногда прядь может подвергаться начальному процессу горячей прокатки перед резкой.
Непрерывное литье обеспечивает более высокое качество продукции, поскольку позволяет лучше контролировать процесс литья, наряду с очевидными преимуществами, присущими процессу непрерывного формования. Такие металлы, как сталь, медь и алюминий, разливаются непрерывно, причем наибольший объем разливки приходится на сталь.
Скорость охлаждения
Скорость охлаждения отливки влияет на ее микроструктуру, качество и свойства.
Скорость охлаждения в значительной степени зависит от формовочной среды, используемой для изготовления формы. Когда расплавленный металл заливается в форму, начинается охлаждение. Это происходит потому, что тепло внутри расплавленного металла переходит в относительно более холодные части формы. Формовочные материалы передают тепло от отливки в форму с разной скоростью. Например, некоторые формы из гипса могут передавать тепло очень медленно, в то время как форма, полностью сделанная из стали, передает тепло очень быстро. Это охлаждение заканчивается (затвердеванием), когда жидкий металл превращается в твердый металл.
На базовом уровне литейный цех может разливать отливку, не обращая внимания на то, как отливка охлаждается и металл застывает внутри формы. Однако, если надлежащее планирование не выполнено, результатом может стать газопористость и усадочная пористость внутри отливки. Чтобы улучшить качество отливки и разработать способ ее изготовления, инженер-литейщик изучает геометрию детали и планирует, как следует контролировать отвод тепла.
Там, где требуется быстрый отвод тепла, инженер планирует оснастить литейную форму специальными теплоотводами, называемыми охладителями. Ребра также могут быть спроектированы на отливке для отвода тепла, которое позже удаляется в процессе очистки (также называемой зачисткой). Оба метода можно использовать в отдельных местах формы, где тепло будет быстро отводиться.
Там, где тепло должно отводиться медленно, к отливке можно добавить стояк или некоторую прокладку. Подступенок представляет собой дополнительную отливку большего размера, которая будет остывать медленнее, чем место ее крепления к отливке.
Вообще говоря, область отливки, которая быстро охлаждается, будет иметь мелкозернистую структуру, а область, которая охлаждается медленно, будет иметь крупнозернистую структуру.
Усадка
Как почти все материалы, металл менее плотный в жидком состоянии, чем в твердом, поэтому отливка сжимается при охлаждении — в основном при затвердевании, но также и при понижении температуры твердого материала. Компенсацию за это природное явление необходимо рассматривать двояко.
Объемная усадка
Усадка, вызванная затвердеванием, может привести к образованию полостей в отливке, ослабляя ее. Подступенки обеспечивают дополнительный материал для отливки по мере ее затвердевания. Подступенок (иногда его называют «фидером») предназначен для затвердевания позже, чем та часть отливки, к которой он прикреплен. Таким образом, жидкий металл в стояке будет поступать в затвердевающую отливку и питать ее до тех пор, пока отливка не станет полностью твердой. В самом стояке будет полость, показывающая, куда подавался металл. Подступенки увеличивают стоимость, потому что часть их материала необходимо удалить путем вырезания из отливки, которая будет отправлена покупателю. Они часто необходимы для изготовления деталей без внутренних усадочных пустот.
Иногда, чтобы способствовать направленной усадке, в форме необходимо использовать охладители. Отбел – это любой материал, который отводит тепло от отливки быстрее, чем материал, используемый для формования. Таким образом, если для формования используется кварцевый песок, кокиль может быть изготовлен из меди, железа, алюминия, графита, цирконового песка, хромита или любого другого материала, способного быстрее локально отводить тепло от отливки. Все отливки затвердевают постепенно, но в некоторых конструкциях для контроля скорости и последовательности затвердевания отливки используется охлаждение.
Линейная усадка
С усадкой после затвердевания можно справиться, используя шаблон увеличенного размера, предназначенный для соответствующего сплава. Изготовители моделей используют специальные «усадочные линейки» для изготовления моделей, используемых в литейном цехе для изготовления отливок требуемого размера. Эти линейки увеличены на 1-6% в зависимости от отливаемого материала. Эти линейки в основном упоминаются по их фактическим изменениям размера. Например, линейка 1/100 добавит 1 мм к 100 мм, если измерить ее «стандартной линейкой» (поэтому она называется линейкой сжатия 1/100). Использование такой линейки при изготовлении выкройки обеспечит получение выкройки большего размера. Таким образом, форма также больше, и когда расплавленный металл затвердеет, он сожмется, и отливка будет иметь размер, требуемый конструкцией, если ее измерить стандартной линейкой. Выкройка, соответствующая существующей детали, будет сделана следующим образом: сначала существующая деталь будет измерена с помощью стандартной линейки, затем при построении выкройки изготовитель выкройки будет использовать усадочную линейку, гарантируя, что отливка сожмется до правильный размер.
Ссылки
Ссылки ISBN поддерживают NWE за счет реферальных сборов
- Барри, Брунер Ф. (1992). Изготовление форм, литье и патина. Декстер, Мичиган: A.B.F.S. Издательский. ISBN 0963186701
- Кэмпбелл, Джон (2003). Отливки, второе издание . Берлингтон, Массачусетс: Баттерворт-Хайнеманн. ISBN 0750647906
- Хоторн, Джон Г. и Сирил Стэнли Смит. О РАЗНЫХ ИСКУССТВАХ: ТРАКТАТ ТОФИЛА. Чикаго: University of Chicago Press, 19.63. ASIN: B000W9KGQC .
- МакКрайт, Тим (1986). Практический кастинг: студийный справочник. Портленд, Мэн: Brynmorgen Press. ISBN 0961598409
- МК Технологии. 2007. «История металлического литья».
Файнгусс / История литья металлов. Проверено 10 февраля 2007 г.
Кредиты
Энциклопедия Нового Света писатели и редакторы переписали и дополнили статью Википедии в соответствии со стандартами энциклопедии Нового Света. Эта статья соответствует условиям лицензии Creative Commons CC-by-sa 3.0 (CC-by-sa), которая может использоваться и распространяться с надлежащим указанием авторства. Кредит должен соответствовать условиям этой лицензии, которая может ссылаться как на г. Энциклопедия Нового Света участников и самоотверженных добровольных участников Фонда Викимедиа. Чтобы процитировать эту статью, щелкните здесь, чтобы просмотреть список допустимых форматов цитирования. История более ранних вкладов википедистов доступна исследователям здесь:
- Литье история
История этой статьи с момента ее импорта в New World Encyclopedia :
- История «Кастинг»
Примечание.