Лазер для резки: Лазерный станок для резки МЕТАЛЛА с ЧПУ — купить по цене от производителя
alexxlab | 03.11.1984 | 0 | Разное
Мощность лазера для резки металла
Мощность лазера для резки металла определяет его максимальные возможности. Одно из главных правил при покупке такого устройства — станок для резки металла лазером нужно покупать с запасом. Ведь наличие запаса силы гарантирует большую производительность и возможность дальнейшего развития организации.
- Что это за показатель — мощность лазера для резки?
- Для резки металла
Что это за показатель — мощность лазера для резки?
Мощность лазера для резки металла — золотая середина модельного ряда LaserFor BSR, которая находится в районе от 500 Вт до 3 кВт. Это оборудование — надежный инструмент, которому можно доверить большое количество работы и при этом не бояться подводных камней.
Лазерные установки включают в себя три главных параметра:
- рабочую среду;
- источник энергии;
- оптический резонатор.
По виду рабочей среды устройства для нарезания бывают следующих видов:
- Твердотельные .
Их основной узел заключается в осветительной камере. В ней расположен источник энергии, а также рабочее тело.
Справка. К твердотельному типу относятся также и волоконные устройства. В них излучение становится выше, а в качестве источника энергии выступает полупроводниковый лазер.
- Газовые. В них рабочим телом выступает углекислый газ, который прокачивается насосом сквозь газоразрядную трубку и заряжается электрическими разрядами. Чтобы усилить излучение, ставят прозрачное зеркало.
- Газодинамические. Они являются самыми мощными. Рабочее тело в них — углекислый газ, который нагрет до 3000 градусов. Он заряжается маломощным лучом. Газ с большой скоростью прокачивается через узкий канал, резко расширяется и охлаждается. В итоге его атомы переходят из заряженного в простое состояние, и газ становится источником излучения.
Для резки металла
Мощность нарезания материала лазером зависит от его теплопроводности: чем она выше, тем эффективнее будет процедура, в среднем это 0,15–12,5 м/с. Мощностная характеристика определяется плотностью потока и достигает 10 в 8 степени Ватт на один квадратный сантиметр. Также она определяется в зависимости от толщины заготовки и в среднем достигает 0,5–1,5 кВт.
В зависимости от типа используемых материалов
Справка. Чтобы нарезать металл с помощью специального оборудования, потребуется сила, которая в среднем составляет 450–500 Вт. Эффективным данный способ считается при толщине заготовок не выше 6 мм. При 20–40 мм подобное оборудование используется редко. Для материала большой толщины резка не осуществляется.
Резка лучом возможна, если материалом выступает:
- Сталь. Максимальная толщина листа не должна быть выше 20 мм, иначе необходимо использовать другой метод.
- Нержавеющая сталь. В этом случае ограничение составляет 16 мм. При таких показателях удастся избежать появления облоя и его можно легко удалить.
- Латунь. Для резки этого материала подойдут 12 мм листы, так как его сопротивление достаточно большое.
- Алюминиевый сплав. Можно резать металлические листы толщиной не выше 10 мм.
Каждому из этих видов материала соответствует свой вид оборудования.
Справка. Нарезание материала лучом не используется на вольфраме, титане, молибдене. Они обладают высокой прочностью, которая приведет к выходу устройства из строя.
В зависимости от толщины
Для качественной нарезки материала нужно учитывать несколько факторов. К примеру, для малоуглеродистых сталей параметры будут такими:
- При толщине в 1 мм мощность должна быть 100 Вт, а скорость резки заготовки 1,6 м в минуту.
- Для изделий плотностью в 1,2 мм — 400 Вт, а скорость резки — 4,6 м в минуту.
- Изделия в 2,2 мм и выше нуждаются в оборудовании силой 850 Вт и резке около 1,8 м в минуту.
Если обработке подвержена нержавеющая сталь, то параметры следующие:
- Для заготовки в 1 мм хватит мощности в 100 Вт.
- Если заготовка имеет толщину 1,3 мм, то сила вырастает до 400 Вт.
- Изделия толщиной в 2,5 мм обрабатывают лазером такой же силы, как и в предыдущем пункте, но в этот раз скорость падает до 1,3 м в минуту.
При резке титана параметры следующие:
- Материал толщиной 0,6 мм обрабатывают устройством, имеющим силу 250 Вт.
- Заготовки толщиной 1 мм обрабатывают с силой в 600 Вт.
В зависимости от производительности
Чем мощнее источник лазерного станка, тем толще может быть лист материала. У лампового устройства мощностью 500 Вт есть два достоинства, которых нет у оборудования меньшей силы. Им можно разрезать латунь и алюминий, что нельзя осуществить оборудованием меньшей мощности из-за большой отражательной способности этого материала.
Если потребности в производстве и производственные задачи высокие, то вы свободно достигнете их, используя силу 250 или 500 Вт. Если предполагается нарезка металла, то понадобится 500 Вт мощности, а если нужен просто станок для резки деталей, то хватит и 100 Вт.
Станки для лазерной резки металла — современное решение, которое нацелено на будущее. Их главные отличия состоят в качестве и сбалансированности всех элементов вместе с современными разработками в области ПО.
- 01 ноября 2020
- 5050
Получите консультацию специалиста
какая нужна головка (модуль) лазера
Лазерные технологии все активнее внедряются в производство и становятся доступными для домашнего использования. Популярное применение — обработка фанеры и дерева. При выборе такого оборудования важнейшим параметром становится мощность лазера для резки фанеры, и этот вопрос заслуживает особого внимания.
Какой лазер нужен для резки фанеры?
Лазерная резка работает по принципу выжигания материала направленным, концентрированным световым лучом повышенной мощности. Основные недостатки этого бесконтактного способа: ровные края, возможность получения сложных форм и заготовок разного размера, высокая точность раскроя, простота управления. Среди недостатков выделяется затемнение рабочего участка и высокая цена оборудования. На фото показана одна из моделей станка.
По функциональной способности различаются такие станки:
- Резательно-гравировальный станок. Он имеет небольшую мощность и предназначен для разрезания фанеры небольшой толщины и осуществления гравировки.
- Промышленный (профессиональный) лазерный станок. Он способен резать листы больших размеров любой толщины. Имеет рабочий стол увеличенного размера, усиленный корпус, большие размеры и повышенную мощность. Соответственно, выше и стоимость станка.
- Малогабаритные настольные лазерные резаки . Они могут использоваться в домашних условиях, имеют стол шириной не более 1 м, меньшую мощность и доступную цену.
- Универсальные фрезерные станки. Они способны не только резать материал, но и осуществлять фрезерные работы.
По типу управления выделяются такие варианты:
- Станки с ручным управлением. Это стандартное оборудование с электроприводом, управление которым осуществляется рабочим вручную.
- Станки с ЧПУ. Они имеют программное обеспечение, а управление осуществляется через компьютер. Достаточно ввести необходимую программу, и станок в автоматическом режиме обеспечит раскрой листа или гравировку точно по заданию.
Основные параметры, которые следует учитывать при выборе станка:
- Размеры рабочего стола. Они определяют габариты обрабатываемых фанерных листов. Для бытовых целей минимальное рабочее поле составляет 30 × 40 см, а для коммерческих целей следует выбирать не менее 60 × 90 см.
- Выходная мощность. От нее зависит глубина проникновения луча, а значит, и толщина разрезаемого листа. Для фанеры толщиной 1 мм нужно не менее 40 Вт.
- Ход рабочего стола. Важна высота его опускания для установки дополнительных приспособлений. Она рекомендуется не менее 15–20 см.
- Мощность лазерной трубки. От нее зависит скорость резки листа. Для производительного станка желательно иметь порядка 8–100 Вт.
Помимо указанных параметров следует принимать в расчет точность реза (отклонение), габариты и вес станка.
Лазерная головка для резки фанеры
Лазерная головка станка — это устройство, включающее сам источник лазерного излучения и оптическую систему для фокусировки луча. Выделяются такие ее разновидности:
- Газовый или СО2. Он работает на газовых смесях. Световой поток усиливается в результате вибрации при переходах в молекулах углекислого газа при прохождении света. Длина волны составляет 10,6 мкм. Головка с СО2-лазером наиболее часто используется в заводских станках для резки.
- Волоконный . В нем активная среда и резонатор составлены из оптических волокон. Такие лазеры обладают повышенной мощностью при небольших габаритах. Используются они для разрезания тугоплавких материалов и для фанеры экономически нецелесообразны, а потому используются редко.
- Твердотельный или полупроводниковый. В качестве активной среды применяется специальный полупроводниковый материал, находящийся в твердом состоянии. Лазеры имеют высокую цену и для резки дерева или фанерных листов не используются.
Они устанавливаются в универсальных станках, способных обрабатывать металлы.
- Диодный. Это полупроводниковый лазер, основанный на светодиоде. Лазерный луч формируется за счет инверсии в зоне p-n перехода при прохождении света. Такое устройство широко используется в различных электронных системах. Мощность у них невелика, но вполне достаточна для резки фанеры. Используется такой источник чаще всего в самодельных станках.
Таким образом, для резки фанеры оптимальным вариантом признаются головки на базе СО2-лазера. В самодельных головках применяются светодиоды от различных устройств (принтеры, плейеры, лазерные указки и т. п.).
Лазерный модуль для резки фанеры
Основным узлом станка для резки фанеры является лазерный модуль, включающий источник излучения, оптические элементы, блок питания, систему регулировки, управления и охлаждения. Модули различаются по типу лазерной головки. Кроме того, они классифицируются по виду излучения: коллимированные и сфокусированные. В последнем случае луч собирается в точку. В коллимированном исполнении можно получить линию, решетку, окружность. Для резки и гравировки более подходит сфокусированный вариант.
Модули различаются по длине волны. Она может варьироваться в широком диапазоне — от ультрафиолетовой до инфракрасной зоны. В устройствах важно обеспечить стабильность этого параметра. Для этого качественные аппараты имеют систему термостабилизации излучателя. Для подстройки в небольших пределах применяются специальные механизмы.
Мощность лазера для резки фанеры
Резка материала осуществляется за счет значительного разогрева при воздействии сконцентрированного светового луча. Температура должна быть достаточной для сгорания волокон. Она же в свою очередь зависит от энергии, которой обладает световой поток. Энергия, выделяемая источником за единицу времени, называется мощностью излучателя.
Мощность лазера считается его важнейшей характеристикой. От нее зависят его функциональные способности. Только при определенном значении волокна начинают выгорать. При этом с повышением увеличивается и глубина резки. Так, при небольшом ее значении обеспечивается только поверхностная обработка — гравировка. Для разрезания материала необходимо, чтобы температуры хватило для выжигания волокон на всю толщину листа.
Мощность зависит, прежде всего, от его типа, т. е. активной среды, накачки и наличия резонатора. Выходная мощность зависит еще и от оптической системы. Повышенная мощность обеспечивается волоконным и твердотельным лазером, но у них высока стоимость. Для фанеры вполне подходит менее мощный, но более дешевый СО2-лазер.
Какая мощность лазера нужна для резки фанеры?
В готовых станках чаще всего применяются СО2-лазеры. Для резки минимальная мощность составляет 20–25 Вт. Выбор станка производится с учетом толщины фанерного листа. Для СО2-лазера рекомендуются такие правила выбора:
- лист толщиной до 6 мм — 50 Вт;
- лист толщиной до 8 мм — 60 Вт;
- лист толщиной до 10 мм — 80 Вт.
При гравировке используются СО2-лазеры мощностью 20–50 Вт.
В зависимости от назначения станки имеют индивидуальные пределы регулировки мощности. Настольные, бытовые аппараты выпускаются до 80 Вт. В профессиональных станках она может достигать 200–250 Вт.
Естественно, возникает вопрос о возможности использования диодных лазеров от бытовых приборов, которые имеют значительно меньшие значения мощности излучения. В принципе возможно применение для резки лазеров такого типа на 2–15 Вт. Мощность указывается на корпусе модели и в инструкции.
Лазер 2,1 Вт
Диодный лазер (2,1 Вт) способен разрезать картон и фанеру толщиной до 1–1,2 мм. Обычно его используют для гравировки, но и для резки он пригоден. Наибольший эффект достигается при работе с бумагой и картоном, которые не обугливаются после воздействия луча.
На фото показан готовый лазерный модуль такой мощности — Endurance 2,1. Он обеспечивает гравировку на дереве и фанере со скоростью до 20 мм/с. Может резать лист толщиной 1–2 мм в 5–30 заходов.
Лазер 3,5 Вт
Диодный лазер мощностью 3,5 Вт может резать фанеру толщиной 2–3 мм. При резке многослойной фанеры такой толщины потребуется 20–25 заходов. Программа CNCC LaserAxe может обеспечить скорость порядка 50–150 мм/мин. На фото показана шкатулка, изготовленная на станке с лазером мощностью 3,5 Вт.
Лазер с короткофокусной линзой 5,6 Вт
Лазер мощностью 5,6 Вт гораздо быстрее справляется с резкой фанеры. Он способен раскраивать листы толщиной 3–5 мм. Станок Endurance 5,6 может работать в таком режиме:
- фанера толщиной 3 мм — до 4 заходов на скорости до 250 мм/мин;
- при толщине 4 мм — 8 заходов на скорости до 200 мм/мин;
- при толщине 5 мм — 9–10 заходов на скорости до 100 мм/мин.
При установке такого лазера рекомендуется использовать короткофокусную линзу G-2.
Ультрамощный 8 Вт
Возможности по резке фанеры значительно расширяются при использовании устройства мощностью 8 Вт. На таком станке можно разрезать листы толщиной 4 мм (при установке линзы G-2) в один заход. Чтобы раскроить фанеру толщиной 6–8 мм потребуется до 5 проходов, а толщиной 10 мм — до 10 проходов. При этом обеспечивается вполне подходящая скорость.
Лазер для резки 10 Вт
Модуль мощностью 10 Вт пригоден для разрезания фанеры до 10 мм. При этом листы толщиной 6–7 мм режутся в 1–2 захода. Листы толщиной 9–10 мм требует 3–5 проходов. Наибольшей популярностью пользуются устройства производства КНР, обеспечивающих длину волны 445–450 нм. Диаметр фокусируемого пятна изменяется от 0,1 до 10 мм. Высокой надежностью отличается лазерный модуль РРМ-010С компании MH GoPower для передачи мощности по оптоволокну.
Лазер 15 Вт
Станок с диодным лазером мощностью 15 Вт приближается к оптимальному режиму резки. Он обеспечивает раскраивание листов толщиной до 10 мм в один заход, а до 12–15 мм — в 3–5 заходов. Из КНР поставляется достаточно надежная модель 570073. Длина волны — 450 нм. Фокусное расстояние —18 мм.
Нюансы лазерной резки фанеры
Лазерная резка имеет ряд особенностей:
- При резке обеспечивается минимальная толщина прореза, что позволяет оптимально кроить лист с максимальной точностью.
- В зоне работ лучом появляется затемнение на фанере. С ростом мощности его интенсивность увеличивается. Небольшая обработка шлифовальной шкуркой устраняет дефект.
- При работе не требуется прикладывать никаких физических усилий. Процесс обеспечивается бесконтактно, что устраняет риск деформации тонких листов.
- На качество конечного результата влияет структура фанеры. Необходимо учитывать многослойность и наличие древесной смолы.
- При длительной работе рабочее место обязательно оборудуется вытяжной вентиляцией.
- Во время работы не образуется стружка и опилки.
- Перед началом работы с поверхности заготовки необходимо убрать пыль.
- Не рекомендуется использовать лазер при резке фанеры с лаковым покрытием.
При использовании лазерных модулей следует прислушаться к таким рекомендациям. Для гравировки вполне подходит лазер 2,1 Вт. Листы толщиной до 2 мм можно резать устройством 3,5 Вт, толщиной до 3 мм — 5,6 Вт, толщиной до 5 мм — 8 Вт. При необходимости раскраивать листы толщиной до 10–12 мм следует применять модули 10–15 Вт.
Лазеры для резки фанеры значительно облегчают труд и повышают точность раскроя. С помощью таких станков можно вырезать детали любой сложной формы. Важнейший критерий выбора оборудования — мощность излучения. Она определяет возможности станка, его производительность, толщину листов. С ее ростом повышается и стоимость устройства, а значит, требуется оптимальный подход к выбору с учетом назначения и конкретных условий.
- 21 сентября 2020
- 30819
Получите консультацию специалиста
Лазерная резка IPG Photonics Corporation
Лазерная резка IPG Photonics Corporation- Применения →
- Обработка материалов →
- Резка
Лазерная резка осуществляется за счет нагрева материала вследствие поглощения сфокусированного лазерного луча. При достижении материалом точки плавления, расплав следует удалять с помощью потока газа, соосно подающегося в зону реза. В результате формируется лазерный рез и происходит разделение материала.
- Резка
- Сверление
- Маркировка и гравировка
- Сварка металлов
- Сварка полимерных материалов
- Пайка
- Плакировка
- Аддитивное производство
- Удаление покрытий
- Термическая обработка
- Технологии лазерной резки
- Лазерная резка плавлением
- Лазерно-кислородная резка
Лазерная резка осуществляется за счет нагрева материала вследствие поглощения сфокусированного лазерного луча. При достижении материалом точки плавления, расплав следует удалять с помощью потока газа, соосно подающегося в зону реза. В результате формируется лазерный рез и происходит разделение материала.
Существует три базовых типа лазерной резки:
При резке плавлением продувка зоны реза осуществляется инертным газом, таким как азот или аргон. За счет энергии лазерного излучения происходит плавление материала. На фронте реза образуется пленка расплава, которая удаляется через канал реза потоком сжатого газа, подающегося через сопло. Такой способ можно использовать для резки практически любых металлов толщиной до 25 мм.
При лазерно-кислородной резке, в качестве вспомогательного газа, используется кислород. Данный процесс комбинированный: пока подводимая лазерным лучом энергия подогревает и плавит поверхность, газ вступает в экзотермическую реакцию с материалом с выделением большого количества тепла. Расплав и продукты горения удаляются потоком вспомогательного газа формируя канал реза. Лазерно-кислородная резка часто применяется при резке малоуглеродистой стали толщиной до 40 мм и позволяет достигать высоких скоростей обработки.
Сублимационная (или испарительная) резка происходит за счет испарения поверхностного слоя материала. Данный процесс требует высокого уровня плотности мощности, поэтому в испарительной резке используются одномодовые импульсные или непрерывные лазеры. Метод испарительной резки используется для материалов с низкой температурой испарения: полимеров, дерева, органических материалов и металлической фольги.
Волоконные лазеры позволяют легко управлять уровнем мощности излучения за счет динамической регулировки. Применяя различные оптические конфигурации можно обеспечить широкий диапазон размеров пятна. Эти возможности позволяют пользователю подобрать подходящую плотность мощности для резки разных материалов и толщин. Волоконные лазеры производства компании IPG представляют собой идеальное решение многих задач лазерной резки.
Типы металлов
Нержавеющие стали | Углеродистые стали | Золото и серебро | Алюминий |
Инструментальные стали | Никелевые сплавы | Латунь и медь | Титан |
Технология лазерной резки плавлением может быть использована при резке практических любых видов металлов и сплавов. Для тонколистовых материалов (толщиной менее 1 мм) лучше всего подходят одномодовые волоконные лазеры производства IPG благодаря возможности фокусировки в пятно минимальных размеров. Высокие плотности мощности, обеспечиваемые малыми размерами пятна и отличным качеством пучка, позволяют производить резку любой сложной формы на высокой скорости. Область применения одномодовых лазеров обширна — резка по трафаретам для нанесения припоя, резка тонкой меди, необходимая для производства аккумуляторов и, даже, сердечно-сосудистое стентирование. |
|
Квазинепрерывные волоконные лазеры позволяют обрабатывать как тонкие, так и толстые материалы. Резка в импульсном режиме обеспечивает минимальное количество шлака и минимальную зону термического влияния, что критично для многих процессов резки, например, при обработке миниатюрных и тонкостенных деталей.
Непрерывные и квазинепрерывные волоконные лазеры позволяют реализовать режим резки с малым коэффициентом заполнения. Высокая пиковая энергия в импульсе позволяет обрабатывать тонко- и толстолистовые материалы, а также материалы с высокой отражательной способностью. При этом средняя мощность излучения невелика. Резка в импульсном режиме используется и для обработки керамики. Высокомощные квазинепрерывные лазеры импульсной мощностью 20 кВт и средней мощностью 2 кВт используются при выполнении сверления в авиакосмической промышленности, где используются материалы толщиной >25 мм.
Производительность при обработке волоконными лазерами значительно выше, чем СО2-лазерами при одинаковой выходной мощности, на одном материале и толщине. Кроме того, потребление энергии значительно ниже, чем у СО2-лазера. Примерно 9 % преобразование электрической энергии в оптическую у СО2-лазера против >45 % у волоконного лазера (лазеры серии YLS-ECO имеют КПД преобразования электрической энергии в оптическую более 50 %).
Системы, оборудованные волоконными лазерами от 2 кВт до 6 кВт, позволяют резать тонколистовой и толстолистовой металл на одном станке. Из-за высокого поглощения излучения волоконные лазеры могут резать высокоотражающие материалы (бронзу, алюминий и медь) с высокой скоростью.
Уникальные возможности, простота применения и технического обслуживания волоконных лазеров компании IPG — делает их идеальным решением для резки металлов.
Лазерно-кислородная резка – гибридный процесс, поскольку помимо энергии лазерного излучения в резке участвует энергия экзотермической реакции окисления. При переходе к большим толщинам такой процесс дает возможность получить существенный прирост скорости обработки. Мощные непрерывные волоконные лазеры IPG серии YLS используются для резки тонких и толстых материалов в различных областях производства. Большая глубина фокусировки, в совокупности с продувкой кислородом, обеспечивают качественную резку даже на больших толщинах. Волоконные лазеры IPG используются в комплексах трехмерной резки, что снижает энергопотребление и время обработки. Такие системы обеспечивают надежный и эффективный метод резки тонких и толстых металлических листов. Головки IPG для резки, интегрированные в комплексы, оснащены системой удаленного управления и возможностью линейного перемещения. Основная область применения – трехмерная резка труб и элементов кузовов в автомобильной промышленности. Современные системы имеют возможность обработки плит, что делает их ещё более гибкими. |
Все непрерывные волоконные лазеры IPG, для обеспечения точной резки, имеют опцию модуляции выходного излучения на частотах до 5 кГц. Компания IPG создала ряд уникальных продуктов с высокой пиковой мощностью – квазинепрерывные волоконные лазеры (серия QCW). Эти лазеры характеризуется высокой пиковой и низкой средней мощностью. Область применения – сверление толстых материалов и материалов с высокими коэффициентами отражения.
Мощные непрерывные волоконные лазеры IPG широко используются в задачах плоского и объемного раскроя различных толщин и материалов. Большая энергоэффективность в сочетании с непревзойденными характеристиками выходного излучения обеспечивают высокую производительность и качество лазерной резки.
Как работает лазерная резка: разбираемся в технологии
Вопросы, рассмотренные в материале:
- Как работает лазерная резка
- Виды лазерной резки
- Плюсы и минусы лазерной резки металла
- Нюансы использования лазерной резки для некоторых металлов
- Параметры качества лазерной резки
- Как можно улучшить качество лазерной резки
Понимание того, как работает лазерная резка, необходимо для проведения работ этим способом или их оценки. Также необходимо знать предъявляемые требования качества к лазерному раскрою, допустимые отклонения по размерам и шероховатости.
Помимо вышеперечисленного, лазерная резка некоторых металлов имеет свои особенности, так же для проведения этих работ нужны определенные знания по настройке оборудования. Только все это вместе поможет получить качественные изделия.
Как работает лазерная резка
Само название «лазерная резка» раскрывает нам суть процесса, который заключается в резке металла лазерным лучом, испускаемым специальной установкой. Луч лазера имеет ряд свойств, позволяющих его сфокусировать на обрабатываемой поверхности, при этом пучок будет нести энергетический заряд высокой плотности. Под его воздействием практически любой материал активно сгорает, плавится, испаряется и пр. – в общем, разрушается.
Энергия луча с плотностью 108 Ватт на 1 см2, создаваемого станком для лазерной резки, концентрируется на поверхности металла. Для понимания сути процесса и, в частности, того, как получается данный эффект, надо узнать обо всех свойствах лазерного луча.
В отличие от волн света, лазерный луч имеет постоянные длину и частоту волны. Данное свойство называют монохроматичностью, а само излучение монохроматическим. Оно дает возможность, используя простые оптические линзы, легко сфокусировать луч на обрабатываемой поверхности.
Еще одним свойством лазерного луча является очень высокая его направленность, а также маленький угол расходимости. Это свойство помогает оборудованию создать фокусированный лазерный луч высокого уровня.
Следующее важное свойство лазерного луча – его когерентность. Суть его заключается в согласованности большого количества волновых процессов, происходящих в луче, а также в их резонансе по отношению друг к другу. Это позволяет значительно повысить суммарную мощность излучения.
Под влиянием луча поверхность металла очень быстро нагревается и затем плавится, оставляя ровный рез.
Благодаря ряду факторов, одним из которых является теплопроводность, зона плавления металла быстро распространяется вглубь заготовки. Лазерный луч работает, воздействуя на поверхность детали, и доводит температуру в точке резки до кипения, в этот момент металл начинает испаряться.
Существует два вида лазерной резки металла:
- Плавление.
- Испарение.
Испарение металла предполагает работу оборудования большой мощности, вследствие чего возникают большие затраты энергоресурсов. Это далеко не всегда экономически целесообразно. Кроме того, этот способ не подходит для обработки толстых заготовок, что отражено в достаточно строгих требованиях к резке. Поэтому его применение ограничивается резкой тонкостенных изделий.
Лазерная резка способом плавления металла используется значительно чаще. В последнее время ее усовершенствовали использованием различных газов, таких как воздух, кислород, азот или инертные газы. Специальные установки вдувают их в зону проведения лазерной резки. Ознакомиться с видеозаписью данного вида работ можно набрав соответствующий запрос в Интернете.
Новшество позволило снизить затраты энергии, увеличить скорость резки и применять оборудование малой мощности для обработки более толстого материала. Однако правильнее было бы изменить название данного способа с лазерного на газолазерный.
Рассмотрим ряд преимуществ, которые позволяют применять кислород как вспомогательный газа для проведения лазерной резки:
- окисление металла активизируется и дает возможность уменьшить его отражающую способность;
- увеличивается тепловая мощность зоны обработки из-за более активного процесса горения металла в кислородной среде;
- кислород, подаваемый под давлением, способствует выдуванию из зоны обработки продуктов сгорания и небольших частиц металла, что упрощает поступление новых волн газа в зону реза.
Виды лазерной резки
Интенсивность излучения, состав газа, используемого для проведения работ и давление при обработке различных металлов должны отличаться. Поэтому были разработаны несколько разновидностей резки.
1. Лазерно-кислородная резка.
Кислород, используемый в данном виде обработки, является режущим газом. В процессе его взаимодействия с горячим металлом возникает экзотермическая реакция окисления. А образующиеся в ходе того же процесса окислы мгновенно выдуваются кислородной струей.
Особенностями проведения работ с помощью данного вида лазерной резки являются скорость работы и диаметр сфокусированного луча, которые влияют на ширину разреза. Одновременно диаметр луча меньше, чем диаметр струи кислорода (как правило от 1 до 2 мм). Рез становится уже при возрастании скорости и снижении толщины заготовки. Разрез имеет минимальную ширину чуть менее 100 мкм. Существует обратная зависимость давления кислородного потока от толщины материала – с уменьшением толщины металла увеличивается давление.
VT-metall предлагает услуги:
Давление в процессе разрезания тонкого листа достигает 3-4 атм, а при увеличении толщины до 25 мм и более она становится около 0,3 мм. Струю формирует зазор между срезом сопла. Его размер зависит от толщины обрабатываемого металла. Колебания размера зазора могут быть от 0,5 мм для листов тонкого металла до 3 мм для металла толщиной 2,5–3 см. Максимальная толщина стального листа, разрезаемого лазером с мощностью 6 кВт, – 3 см. Скорость процесса при данной толщине – минимальная, около 0,5 м в минуту. Если скорость работы продолжает уменьшаться, то еще быстрее падает качество резки.
2. Кислородная резка с поддержкой лазерным лучом (LASOX).
Для работы с листами стали большой толщины имеет смысл использовать получившую в последние годы широкое распространение технологию, при которой луч лазера греет поверхность металла до достижения им температуры +1 000 °С, после чего в ход идет струя кислорода, которая со сверхзвуковой скоростью режет металл. Применение данного метода дает возможность существенно увеличить глубину разреза, если ее сравнивать с простой лазерно-кислородной резкой.
Сверхзвуковая кислородная струя формируется большим давлением, достигающим 6–10 атм. Рез имеет ширину, равную диаметру струи кислорода. Она имеет размер ≥ 3 мм. Расстояние от среза сопла до поверхности должно быть примерно 7 мм. Скорость реза при этом уменьшается до 0,2 м в минуту. Скорость работы при использовании представленной технологии значительно снижена по сравнению с лазерно-кислородной резкой. Но толщина обрабатываемого металла достигает 10 см.
Рекомендуем статьи по металлообработке
- Марки сталей: классификация и расшифровка
- Марки алюминия и области их применения
- Дефекты металлический изделий: причины и методика поиска
3. Лазерная резка в инертном газе.
Если нельзя допускать окисления краев обрабатываемого металла, то прекрасно работает технология лазерной резки в инертном газе. Она подходит для таких металлов, как титан, нержавейка, сплавы алюминия. Данная технология не предусматривает использования дополнительного источника нагрева, что, к сожалению, уменьшает эффективность раскроя металла.
Скорость проведения работ в среде инертного газа, а им может быть аргон, использующийся при резке титана, или азот, применяемый в иных случаях, достаточно низкая. Давление режущего газа должно быть более 10 атм. От ширины листа обрабатываемого металла зависит диаметр сопла. А он, соответственно, оказывает влияние на количество используемого газа, увеличивая его. Что сказывается на увеличении стоимости резки.
4. Лазерное термораскалывание стекла.
Данная технология хорошо работает для резки хрупких и ломких материалов, таких как стекло. Луч лазера нагревает материал неравномерно, а затем струя инертного газа работает на его охлаждение. В итоге образуется трещина. Направлением ее продвижения можно управлять, перемещая источник тепла вдоль поверхности материала. Результат работ – гладкая ровная грань.
5. Сублимационная резка (испарительная лазерная).
При необходимости минимизации теплового воздействия на подложку применяют технологию сублимационной резки. Основное ее приложение – микротехнологии. Интенсивность излучения лазера для такого вида резки должна быть очень высокой. Давайте рассмотрим, как работает станок лазерной резки. Если кратко, то оборудование действует на излучении пикосекундной и наносекундной длительности импульсов, то есть очень коротких. Волна излучения имеет длину меньше 1 мкм. Для такого излучения применяют эксимерные, твердотельные лазеры, а также те, что работают на парах металлов. Коэффициент полезного действия (КПД) таких процессов минимальный.
Следовательно, лазерно-кислородная технология является наиболее распространенным и стандартным видом резки материалов. Остальные виды носят специфический характер и решают отдельные задачи.
Плюсы и минусы лазерной резки металла
Использование технологии лазерной резки материалов происходит повсеместно в разных отраслях промышленного производства, таких как авиация, машиностроение, медицина и пр. Причина скрывается в ее преимуществах, таких как:
- высокоточная резка металлов;
- оборудование для лазерной резки работает над созданием криволинейных конструкций всех степеней сложности, а также объемных деталей и фасонных изделий;
- в процессе работы не происходит нагрев поверхности заготовки;
- образуется рез высокого качества;
- не происходит деформации материала в ходе работе;
- нет механического воздействия на заготовку;
- используется бесконтактный метод работы;
- технология справляется с созданием даже хрупких и сложных деталей;
- работа ведется без образования пыли;
- технология прекрасно зарекомендовала при работе с любыми металлами, в том числе имеющих высокий уровень теплопроводности, и их сплавов;
- возможно выполнение работы в автоматическом режиме;
- способ используется для резки не только металлов, но также пластика и дерева, картона, текстиля и кожи, иных материалов;
- продукция выходит качественной и не требующей дополнительной обработки;
- метод практически идеален для работы с легко деформирующимися в процессе механической работы заготовками;
- зона нагревания поверхности изделия минимальна;
- не происходит перегрева изделий во время работы;
- сроки производства очень короткие;
- оборудование чрезвычайно просто управляется.
Помимо достоинств, у технологии есть и недостатки. Ими являются высокая стоимость по сравнению с иными видами, неравномерная скорость изготовления и жесткие ограничения по размерам обрабатываемой заготовки. Лазерной резке можно подвергнуть листы с габаритами не более чем 15х30 м. Еще одним ограничением является толщина материала – заготовка не должна быть толстостенной. Также необходимо обязательно учитывать, что тип лазера сильно влияет на эффективность резки и иные параметры.
Для получения качественного изделия требуется доверить работу профессионалам. А неправильная работа оборудования может привести к пережогу металла.
Нюансы использования лазерной резки для некоторых металлов
- Алюминий.
Высокая теплопроводность алюминия и плохая способность поглощать луч лазера из-за оптических и теплофизических характеристик металла определяют особенности его обработки.
Все это приводит к сложностям в раскрое металла. Аппаратура работает на компьютерном управлении и легко настраивается.
При работе с алюминием мощность луча лазера должна быть больше, чем для иных материалов.
Впрочем, на показатели мощности и скорость работ большое влияние оказывают толщина металла, а также процент алюминия, содержащийся в обрабатываемом материале.
Давайте рассмотрим, как работает лазерная резка данного металла. Она происходит на различном по режимам работы и мощности оборудовании твердотельного типа, а также на газовых устройствах.
Последние являются более мощными, могут работать импульсно или в непрерывном режиме.
А твердотельное оборудование, как правило, работает в точечном (импульсном) режиме.
Технологический процесс имеет ряд особенностей. Алюминий лучше режет лазерный луч, чем обычное оборудование для резки металла. Причина в том, что при работе лазером оборудование не касается заготовки, в отличие от иной аппаратуры.
Лазерный луч представляет собой сфокусированный пучок света, с помощью которого происходит резка. Точная фокусировка позволяет провести обработку алюминия с высокой скоростью. К месту работы подводится газ и создается его приток. Струя газа сдувает кусочки расплавленного металла с места реза, не давая им осесть, и делает поверхность ровной и гладкой.
Качественного результата можно добиться, проводя работу с меньшей скоростью. Поскольку она исключает любые деформации, как большие, так и маленькие.
Для исключения каких-либо шероховатостей на кромках реза, даже незначительных, при работе оборудования используется азот.
На аппаратура установлено программное обеспечение, которое дает возможность проводить сверхточную работу высокого качества. Кроме того, заготовку не надо закреплять перед началом работ, поскольку физический контакт между оборудованием и изделием отсутствует. Деталь лежит на поверхности без движения.
Автоматическое оборудование работает следующим образом: в компьютер вносится чертеж, выставляются требуемые параметры, далее ожидается окончание резки.
- Латунь.
Латунь – это сплав красной меди и цинка. Хрупкость и твердость сплава определяются процентным содержанием цинка в нем – чем больше этого металла, тем выше данные показатели. Однако увеличение количества цинка ведет к непригодности использования латуни в технических целях, поскольку она практически не поддается резке. Установлено, что цинка в латуни может быть не более 42 %.
Латунь имеет высокую температуру плавления, поскольку сплав двухкомпонентный, то есть состоит из цинка и меди. Температура, необходимая для плавки латуни, как правило, имеет диапазон от +880 °С до +950 °С. Помимо этого, латунь обладает значительной теплопроводностью, устойчивостью к излучению лазера и повышенной твердостью.
Настройка промышленного лазерного станка зависит от толщины обрабатываемой латунной заготовки:
- для латуни толщиной менее 5 мм используют импульсный режим;
- если заготовка имеет толщину от 5 до 12 мм, то применяют плазменный режим резки.
Импульсный режим нагревает поверхность с короткими перерывами (импульсами), а не постоянно. Таким образом, уменьшается участок нагрева, что приводит к минимизации ширины реза и более высокому качеству краев. При резке латуни, которая имеет большую отражающую способность, оборудование работает в импульсном режиме, выдавая небольшую мощность лазерного луча при пороговой интенсивности.
Расплавный (плазменный) режим позволяет равномерно воздействовать теплом на зону разреза. Луч лазера раскаляет металл с помощью инертного газа. Плазма, которая образуется в ходе работы, сохраняет температуру по всей толщине заготовки.
Если торец изделия имеет шероховатость или пористость, это можно убрать с нижней стороны изделия. Лист меди очень плохо поглощает излучение. А оборудование для резки работает с малой скоростью. Помимо точного выбора режима работы, необходимо правильно выполнять условия лазерной резки листов металла различной толщины. Они различаются для алюминия, сталей, меди, а также сплавов ее с оловом, то есть бронзы, и с цинком, то есть латуни.
Качественный результат получается при использовании волоконных установок или Nd:YAG лазеров, имеющих длину волны 1,06 мкм. CO2-лазеры для резки латуни не годятся, поскольку ее поверхность их полностью отражает.
Параметры качества лазерной резки
Показателями качества резки металла являются шероховатость, ширина реза, глубина воздействия температуры, неперпендикулярность краев, точность выполнения деталей, грат на кромках. На них оказывают влияние толщина и вид обрабатываемого металла, скорость резки, вспомогательный газ, а также параметры излучения лазера. Для определенной толщины материала подбирают скорость обработки, которая должна приближаться к максимальной, но сохранять наилучшие показатели качества резки.
Качество резки значительно ухудшается с увеличением диаметра сфокусированного излучения, и, как следствие, увеличивается толщина расплава передней поверхности.
Положение фокальной плоскости резака относительно детали значительно влияет на качество обработки. Ее либо заглубляют на 1/3 толщины материала, либо располагают прямо на поверхности. Допустимые отклонения фокальной плоскости от установленного положения должны быть от 0,1 до 0,5 мм. Причем для тонких листов металла выбирают более жесткий показатель. В процессе работы допускается замена кислорода воздухом. Для заготовок толщиной более 3 мм это приводит к сужению ширины реза на 20–40 %. Но на нижнем краю заготовки возрастает количество грата. Это, а также уменьшение скорости работы приводят к углублению зоны термического воздействия.
Шероховатость поверхности реза имеет свою величину, которая характеризуется частотой повторений, наклоном бороздок, глубиной, и изменяется в зависимости от толщины заготовки. У верхнего края находится зона с минимальной глубиной бороздок. Они появляются на верхнем краю и распространяются вглубь материала из-за периодического разрушения. В зоне, которая располагается ниже, бороздки имеют большую глубину по причине одновременного влияния луча лазера и вспомогательного газа.
Непосредственно у нижнего края реза находится участок, где бороздки имеют максимальное отставание (наклон) в сторону, противоположную резке. Образуются они из-за воздействия вспомогательного газа и жидкого стекающего металла на кромку обрабатываемого материала. На поверхности реза глубина бороздок становится меньше при возрастании скорости резки и плотности мощности. Глубина, на которую заготовка прогревается, и ширина реза зависит от одних и тех же параметров. Это скорость резки и диаметр сфокусированного луча.
На качество резки неметаллических заготовок оказывают влияние все те же параметры, что и на металлические, с одним исключением – они значительно менее подвержены воздействию излучения. Например, над разлагающимися материалами лазерное оборудование работает с меньшей плотностью излучения. При одинаковой толщине со сталями ширина разреза больше в 1,5–2 раза, шероховатость меньше – имеет размер в 30–40 мкм. Кромки срезов стеклотекстолита, дерева, винипласта, кожи или резиностеклопластика (разлагающихся материалов) покрываются обугленным слоем толщиной от 0,5 до 1,0 мм. Если деталь является электроизолятором, то такой слой следует убрать.
Несмотря на то, что точность резки является комплексным параметром качества, она на 50–80 % определяется точностью работы оборудования, а также погрешностями в технологии обработки. Толщина заготовки, а также ее последующее предназначение определяют требования к точности резки. В большинстве случаев, допуск должен составить 0,1–0,5 мм.
Технологическая точность во многом зависит от следующих параметров качества: ширины разреза, неперпендикулярности краев, шероховатости среза. В ГОСТах 26940–86 и 5614–74 описывается необходимая для термической резки (которая включает и газолазерную) точность оборудования с числовым программным управлением (ЧПУ). Для окружностей с диаметром 50 см и квадратов, имеющих стороны 50 см, показатель максимальных отклонений от номинала должен быть 0,1–0,25 мм с обе стороны. На углах деталей максимальные отклонения размеров контуров увеличиваются вдвое.
Как можно улучшить качество лазерной резки
1. Необходимо очистить линзу или защитное стекло в соответствии со всеми правилами.
Каждому типу лазера соответствует своя процедура очистки. Работая с дисковым или волоконным лазером, специалистам следует очищать стекло, которое защищает линзы режущей головки.
Операторам, работающим с углекислотным лазером, необходимо чистить линзы. Профессионалы производственной сферы при очистке лазера отдают предпочтение полировке Topol polish от фирмы TRUMPF. Однако большое количество специалистов даже не знают, как с ней работать. Случается, что линзы серьезно поцарапаны. И вместо регулярной полировки работники покупают новую линзу. Но частая замена – очень дорогое удовольствие.
Как правильно работать с полировкой для линз? Нельзя сильно давить на линзу, поскольку могут появиться царапины. Но, одновременно с этим, полировка должна проходить под нажимом, достаточным для удаления грязи. Самое главное – научить соблюдать баланс.
Работать надо круговыми движениями, нанося полировку в умеренном количестве.
Для правильной полировки линзы специалист должен знать и видеть все ее недостатки. Рекомендуется дополнить оборудование углекислотного лазера дорогостоящим поляризатором, стоимость которого исчисляется сотнями долларов. Несмотря на высокую цену аппарата, его работа с лихвой окупит вложенные средства, причем очень быстро.
Специалисту, работающему с лазером, необходимо разместить линзу на устройстве, освещающем ее ярким светом снизу. Больше всего аппарат своей работой напоминает школьный проектор. При повороте линзы аппарата, он поляризует линзу лазера, размещенную наверху. Таким образом можно увидеть все ее недостатки: царапинки, внутренние трещины и пр.
2. Необходимо проверить фокусировку (центрацию) сопла.
Для проверки специалист должен пробить натянутую ленту. В течение секунды он направляет на нее луч лазера небольшой мощности, после чего осматривает отверстие и место его нахождения.
Работник освещает ленту, пытаясь понять, насколько точно в центре расположено отверстие. Его сдвиг не должен превышать 1 мм. Каким образом можно точно определить, что отверстие находится в центре сопла? Для этого надо воспользоваться 10-кратным увеличительным стеклом, оснащенным подсветкой.
Точная центрация сопла позволяет увеличить скорость на 20–80 % от начальной при правильности остальных настроек.
3. Необходимо регулярно проверять фокус.
Большая часть современного оборудования позволяет осуществлять автоматический тест фокуса. А на старых моделях станков производители рекомендовали делать тесты различными способами. На некоторых станках используется «световой тест».
Примером может служить старый аппарат Mazak. В процессе тестирования специалист включает луч лазера на малую мощность, затем, поворачивая ручку, ищет абсолютный фокус. Он наблюдает за светом луча, приобретающим синий цвет в процессе вращения ручки по кругу. После чего записывает номер. Возвращает режущую головку на прежнее место и повторяет процедуру три раза. В итоге специалист вычисляет среднее арифметическое полученных чисел, которое загружается в контроллер.
От работника требуется отыскать тончайшую полоску на тестовом образце, после чего удостовериться, что для этой полоски фокус контроллера равен 0. Если тончайшей полоске соответствует цифра 3, специалист перемещает точку фокуса на 3 мм и вновь возвращается к тесту. Операция проводится до тех пор, пока тончайшая полоска не будет соответствовать нулю.
При работе с лазером необходимо изучить такие факторы, как расход газа или применение в углекислотных системах дополнительной защиты оптики. Впрочем, рассмотренные нами принципы – всего лишь отправная точка, с которой можно начать настройку необходимых условий резки. В дальнейшем специалисты поймут, что обстоятельств, влияющих на работу лазера, много: от обрабатываемого материала и до местоположения предприятия.
Почему следует обращаться именно к нам
Мы с уважением относимся ко всем клиентам и одинаково скрупулезно выполняем задания любого объема.
Наши производственные мощности позволяют обрабатывать различные материалы:
- цветные металлы;
- чугун;
- нержавеющую сталь.
При выполнении заказа наши специалисты применяют все известные способы механической обработки металла. Современное оборудование последнего поколения дает возможность добиваться максимального соответствия изначальным чертежам.
Для того чтобы приблизить заготовку к предъявленному заказчиком эскизу, наши специалисты используют универсальное оборудование, предназначенное для ювелирной заточки инструмента для особо сложных операций. В наших производственных цехах металл становится пластичным материалом, из которого можно выполнить любую заготовку.
Преимуществом обращения к нашим специалистам является соблюдение ими ГОСТа и всех технологических нормативов. На каждом этапе работы ведется жесткий контроль качества, поэтому мы гарантируем клиентам добросовестно выполненный продукт.
Благодаря опыту наших мастеров на выходе получается образцовое изделие, отвечающее самым взыскательным требованиям. При этом мы отталкиваемся от мощной материальной базы и ориентируемся на инновационные технологические наработки.
Мы работаем с заказчиками со всех регионов России. Если вы хотите сделать заказ на металлообработку, наши менеджеры готовы выслушать все условия. В случае необходимости клиенту предоставляется бесплатная профильная консультация.
Станок лазерной резки XT Laser серии H ❇ Компания ТЕМИР
Экструдированная авиационная алюминиевая балка
Изготовлена в соответствии с аэрокосмическими стандартами и сформирована методом пресс-экструзии. После старения прочность и механические свойства металла достигают высоких показателей.
Авиационный алюминий имеет много преимуществ: высокую прочность, малый вес, коррозионную стойкость, антиокислительные свойства и значительное увеличение скорости обработки.
Автофокусная лазерная головка
Лазерная головка сама регулирует точку фокусировки в соответствии с толщиной материала и применяет различные фокусные расстояния, сокращая продолжительность перфорации и улучшая её качество. Кроме того, она следит за окружением и автоматически поднимается, чтобы избежать встречу с препятствием. Таким образом работает активное предотвращение столкновений.
Летающее режущее микро-соединение предотвращает деформацию листа и обеспечивает высокую скорость и стабильность при резке.
Интеллектуальная система ЧПУ
Подготовлена для эксплуатации даже неопытными пользователями. Поддерживает несколько графических файлов, включая DXF, PLT, DWG, AI, G-code, IGS (резка труб). Система также совместима с другим программным обеспечением для раскроя.
- Поддержка мультибрендового программного обеспечения для раскроя
- Поддержка нескольких языков
- Вспомогательный сигнал низкого давления газа и ошибки резки
- Предупреждающий индикатор безопасности.
Отличия моделей серии H
- XT-h2530
- XT-h2545
- XT-h3040
- XT-h3060
- XT-h3560
XT-A6060
# | Название | Параметры модели XT-h2530 |
---|---|---|
1
# |
Рабочая область
Название |
1530×3050 мм
Параметры модели |
2
# |
Мощность лазера
Название |
1000 Вт – 4000 Вт
Параметры модели |
3
# |
Скорость перемещения
Название |
140 м/мин
Параметры модели |
4
# |
Ускорение
Название |
1.![]() Параметры модели |
5
# |
Позиционная точность
Название |
± 0.03 мм
Параметры модели |
6
# |
Репозиционная точность
Название |
± 0.02 мм
Параметры модели |
XT-h2545
# | Название | Параметры модели XT-h2545 |
---|---|---|
1
# |
Рабочая область
Название |
1530×4550 мм
Параметры модели |
2
# |
Мощность лазера
Название |
1000 Вт – 4000 Вт
Параметры модели |
3
# |
Скорость перемещения
Название |
140 м/мин
Параметры модели |
4
# |
Ускорение
Название |
1.![]() Параметры модели |
5
# |
Позиционная точность
Название |
± 0.03 мм
Параметры модели |
6
# |
Репозиционная точность
Название |
± 0.02 мм
Параметры модели |
XT-h3040
# | Название | Параметры модели XT-h3040 |
---|---|---|
1
# |
Рабочая область
Название |
2030×4050 мм
Параметры модели |
2
# |
Мощность лазера
Название |
1000 Вт – 4000 Вт
Параметры модели |
3
# |
Скорость перемещения
Название |
140 м/мин
Параметры модели |
4
# |
Ускорение
Название |
1.![]() Параметры модели |
5
# |
Позиционная точность
Название |
± 0.03 мм
Параметры модели |
6
# |
Репозиционная точность
Название |
± 0.02 мм
Параметры модели |
XT-h3560
# | Название | Параметры модели XT-h3560 |
---|---|---|
1
# |
Рабочая область
Название |
2530×6050 мм
Параметры модели |
2
# |
Мощность лазера
Название |
1000 Вт – 4000 Вт
Параметры модели |
3
# |
Скорость перемещения
Название |
140 м/мин
Параметры модели |
4
# |
Ускорение
Название |
1.![]() Параметры модели |
5
# |
Позиционная точность
Название |
± 0.03 мм
Параметры модели |
6
# |
Репозиционная точность
Название |
± 0.02 мм
Параметры модели |
XT-h3060
# | Название | Параметры модели XT-h3060 |
---|---|---|
1
# |
Рабочая область
Название |
2030×6050 мм
Параметры модели |
2
# |
Мощность лазера
Название |
1000 Вт – 4000 Вт
Параметры модели |
3
# |
Скорость перемещения
Название |
140 м/мин
Параметры модели |
4
# |
Ускорение
Название |
1.![]() Параметры модели |
5
# |
Позиционная точность
Название |
± 0.03 мм
Параметры модели |
6
# |
Репозиционная точность
Название |
± 0.02 мм
Параметры модели |
как избежать неудачи при работе с резаком? / Хабр
Несколько советов для начинающих
Cтанки лазерной резки c ЧПУ нельзя назвать дешевыми, но средней руки предприниматель уже может себе позволить такую систему. Некоторые модели из Китая стоят около $4000. Лазером можно делать все — вырезать корпуса приборов, отдельные элементы конструкции, наносить изображения на металл, дерево, кожу и пластик.
Но наличие компьютерного управления вовсе не значит, что оператор может отдыхать на кушетке с любимой книжкой в одной руке и бутылкой пива — в другой. Для того, чтобы результат работы удовлетворял всем критериям успеха, оператору нужно приложить немалые усилия. На каких этапах резки сфокусировать внимание? Об этом рассказывает мастер, который довольно продолжительное время работал с системами лазерной резки разного типа.
Подготовка к работе
Даже на этом этапе многое может пойти не так. Ошибку можно допустить, подключая питание. Или вообще что-то можно собрать не так, и все пойдет прахом после подключения электричества. Сейчас многие системы содержат аварийную «защиту от дурака», но бывает всякое.
Вот так иногда приходится доставлять оборудование к месту установки
Проблемы могут быть не технического характера, например — плохо проверили габариты оборудования, и все — в двери оно не пролезает. Что делать? Разбирать станок? Не всегда возможно. Расширять дверной проем? Тоже сложно.
Подключение вытяжки и охлаждения (технический проект, бюджет). Для работы лазерного резака нужна не только энергия. Требуется также вытяжка и охлаждение. Вытяжка может быть любой, в зависимости от специфики аппарата. Чем короче трубы вытяжки, тем лучше (по возможности, конечно). Если же охлаждение водяное, требуется подвод дистиллированной/очищенной воды. Об установке вытяжки и охлаждения нужно подумать заранее, а не после того, как лазерный резак уже куплен.
Шум и запах. Работающий лазерный резак, его охлаждение и вытяжка производят много шума. Кроме того, будет и запах, какой хорошей вытяжка бы ни была. Работать система может часами, поэтому и место стоит выбрать соответствующее — такое, где резак мешать не будет. Обо всем этом лучше всего тоже позаботиться заранее. Вытяжка должна действительно выводить воздух с парами обработанного материала из помещения, а не гонять его по кругу.
Несмотря на советы в стиле КО, довольно много новичков о чем-то забывают, чем-то пренебрегают. И потом, уже после установки, может быть мучительно больно из-за нерешенной заранее проблемы.
Начало работы
Отсутствие системы подачи сжатого воздуха в место резки. Если такой системы нет или она отказала, то воспламеняющийся материал, с которым сейчас работает резак, вполне может загореться.
При подаче воздуха в место работы все пары отработанного материала уходят, а температура не успевает подниматься слишком быстро.
Использование проприетарного программного обеспечения. Недорогой лазерный резак из Китая, вероятно, будет работать с собственным закрытым программным обеспечением. Это, в большинстве случаев, проприетарное ПО, написанное производителем оборудования, и с этим программным обеспечением могут возникнуть неожиданные проблемы. Речь идет о CAD-программах, в которых готовятся модели для резака, несовместимых с ПО лазерной системы. Какие-то файлы могут не импортироваться, а какие-то — не экспортироваться. Это сильно замедляет работу, а сама проблема в некоторых случаях может испортить весь рабочий процесс. Если случилось нечто подобное, то можно подумать о смене CAD-программы (какой бы удобной она бы ни была) или замене контроллера.
Ошибка в характеристиках рабочего материала. В некоторых случаях характеристики купленного для работы материала (пластик, металл и т.п.) могут значительно отличаться от реальности. И тогда настроенный на один режим работы принтер может испортить весь проект из-за расхождения описанных производителем и реальных параметров материала.
Тестовый образец кожи после нанесения рисунка
Поэтому не стоит пускать в работу (например, начинать гравировку) рабочий образец — лучше проверить на тестовом образце, который не жалко испортить.
Рабочий процесс
Оставляем аппарат без присмотра. Как уже говорилось выше, оператор должен внимательно следить за системой все время. Если этого не сделать, то аппарат в силу каких-то сбоев (самых неожиданных) может полностью выйти из строя:
Каким бы ни был качественным и безопасным резак, какие бы технологии защиты в нем ни использовались, всегда есть вероятность возгорания отдельных элементов станка или рабочего материала. Это актуально даже для тех материалов, с которыми раньше владелец станка работал без проблем. Сбойнуть может программное обеспечение или электрическая сеть системы. Отказать может сервопривод, также может оборваться ремень. Если случилось что-то подобное, оператор может обесточить станок, и последствий проблема иметь не будет.
Неправильная фокусировка лазера. Для того, чтобы результат был идеальным, линзы должны быть настроены тоже идеально. Если что-то настроено хотя бы немного не так, работа может пойти прахом.
Защита поверхности. Нанесение узора на поверхности лучше производить с использованием защиты. Это может быть специальная пленка, которая не даст поверхности рядом с рабочей областью деформироваться или менять цвет. Многие типы пластика для резака уже продаются с такой защитой. Но здесь есть еще одна проблема.
Невозможность удаления защитной пленки по окончанию работы. Защитить поверхность просто, но нужно еще и снять защиту после работы. Под влиянием лазера пленка иногда может сплавиться с образцом, что приведет к неаккуратному внешнему виду. Такие случаи нужно предусматривать заранее, обдумывая ход работы.
Уникальные свойства материала. Характеристики некоторых типов материалов могут повлиять на процесс резки и отобразиться на конечном результате. К примеру, работа с зеркальной поверхностью — это проблема. Дело в том, что лазер, используемый для гравировки, отражается от зеркальной поверхности, и изображение получается двойным.
Очистка от мусора. Обычно лазерная резка не производит слишком уж много мусора. Но все же такой мусор есть, полностью от него избавиться нельзя. И если его не убрать вовремя, это может повредить поверхность материала — частички мусора могут загореться или сплавиться с изделием.
Выделение вредных веществ. В качестве примера стоит привести ПВХ. При резке поливинилхлорида лазером в воздух выделяется хлор. Как известно, это тяжелый газ, и он будет опускаться в недра машины. Хлор обладает коррозийными свойствами. Газ взаимодействует с большим количеством материалов, включая изоляцию, резиновые прокладки и т.п.
Если все идет хорошо – это не значит, что результат будет оптимальным
Допустим, все прошло хорошо, сбоев не было. Но прежде, чем радоваться хорошо выполненной работе, постарайтесь проверить, все ли действительно близко к идеалу.
Здесь все отлично благодаря проведенному ранее тесту с кожей
Дело в том, что у некоторых материалов во время нагревания лазером проявляются необычные свойства (деформация, изменение цвета и т.п.). Из-за этих свойств материал может менять свой внешний вид самым неожиданным образом. Проблемы могут быть и иного характера:
Деформация пластика. Например, очень тонкий пластик деформируется при воздействии высокой температуры. В этом случае помочь может относительно ровная нагретая до определенной температуры поверхность, где можно выправить пластик.
Острые края и заусенцы. Некоторые виды пластика могут оставлять и острые углы, и заусенцы. В этом случае для решения проблемы стоит использовать минеральные растворители.
Загрязнение текущего рабочего образца частицами, оставшимися на рабочем столе с предыдущего проекта. Нужно следить, чтобы рабочее пространство станка было чистым.
Скрытые расходы. Да, часто бывает так, что лазерный резак тянет за собой дополнительные расходы, и немалые. Все это пользователь начинает учитывать уже с опытом, в начале у большинства образуются лишние траты. Чрезмерный расход материала, значительное увеличение расхода электроэнергии и т.п. Все это нужно стараться просчитывать еще до покупки системы.
Нежелание что-либо менять
Это самая распространенная проблема. «И так сойдет», — эта поговорка становится призывом к действию для многих из нас. Она может привести к чрезмерным расходам, неудачному результату резки, недовольству клиентов. Если уж вы решили использовать лазерную резку, как профессионал, то и поступать должны, как настоящий мастер. За машиной нужно следить, ухаживать. Нужно выполнять многие правила эксплуатации лазерного резака и стараться эти правила не нарушать. И тогда все будет хорошо.
Что же, теперь осталось пожелать удачной работы!
Что такое лазерная резка? – Полное руководство по процессу
Лазерная резка — это процесс, в котором используется лазер для резки различных материалов как в промышленных, так и в более художественных целях, таких как травление.
Эта статья является одной из серии часто задаваемых вопросов (FAQ) TWI.
Нажмите здесь, чтобы посмотреть наши последние технические подкасты на YouTube .
Как работает лазерная резка?
Лазерная резка использует мощный лазер, который направляется через оптику и компьютерное числовое управление (ЧПУ) для направления луча или материала. Как правило, в процессе используется система управления движением, чтобы следовать ЧПУ или G-коду шаблона, который должен быть вырезан на материале. Сфокусированный лазерный луч горит, плавится, испаряется или сдувается струей газа, оставляя после себя высококачественную обработанную поверхность.
Лазерный луч создается путем стимуляции лазерных материалов с помощью электрических разрядов или ламп внутри закрытого контейнера. Лазерный материал усиливается за счет внутреннего отражения через частичное зеркало до тех пор, пока его энергии не станет достаточно для выхода в виде потока когерентного монохроматического света. Этот свет фокусируется на рабочей зоне с помощью зеркал или волоконной оптики, которые направляют луч через линзу, которая усиливает его.
В самом узком месте лазерный луч обычно имеет диаметр менее 0,0125 дюйма (0,32 мм), но в зависимости от толщины материала возможна ширина разреза до 0,004 дюйма (0,10 мм).
В тех случаях, когда процесс лазерной резки должен начинаться в любом месте, кроме края материала, используется процесс прокалывания, при котором импульсный лазер высокой мощности делает отверстие в материале, например, требуется 5-15 секунд, чтобы прожечь 0,5 лист из нержавеющей стали толщиной 13 мм.
Типы лазерной резки
Этот процесс можно разделить на три основных метода: CO 2 лазер (для резки, сверления и гравировки) и неодимовый (Nd) и неодимовый иттрий-алюминиевый гранат (Nd:YAG) , которые идентичны по стилю: Nd используется для высокоэнергетического растачивания с малым повторением, а Nd: YAG используется для очень мощного растачивания и гравировки.
Для сварки можно использовать все типы лазеров.
CO 2 В лазерах используется пропускание тока через газовую смесь (возбуждение постоянным током) или, что более популярно в наши дни, использование более новой технологии радиочастотной энергии (возбуждение радиочастотой). Радиочастотный метод имеет внешние электроды и, таким образом, позволяет избежать проблем, связанных с эрозией электродов и отложением материала электрода на стеклянной посуде и оптике, которые могут возникнуть при постоянном токе, в котором используется электрод внутри полости.
Другим фактором, влияющим на работу лазера, является тип газового потока. Общие варианты лазера CO 2 включают быстрый осевой поток, медленный осевой поток, поперечный поток и плиту. В быстром осевом потоке используется смесь двуокиси углерода, гелия и азота, циркулирующая с высокой скоростью с помощью турбины или воздуходувки. Лазеры с поперечным потоком используют простой нагнетатель для циркуляции газовой смеси с более низкой скоростью, в то время как пластинчатые или диффузионные резонаторы используют статическое газовое поле, которое не требует повышения давления или стеклянной посуды.
Различные методы также используются для охлаждения лазерного генератора и внешней оптики в зависимости от размера и конфигурации системы. Отработанное тепло может передаваться непосредственно в воздух, но обычно используется хладагент. Вода является часто используемым хладагентом, часто циркулирующим через систему теплопередачи или охладителя.
Одним из примеров лазерной обработки с водяным охлаждением является лазерная микроструйная система, которая соединяет импульсный лазерный луч со струей воды низкого давления для направления луча таким же образом, как оптическое волокно. Вода также дает преимущество в удалении мусора и охлаждении материала, в то время как другие преимущества по сравнению с «сухой» лазерной резкой включают высокую скорость нарезки, параллельный пропил и всенаправленную резку.
Волоконные лазеры также набирают популярность в металлообрабатывающей промышленности. В этой технологии используется твердая усиливающая среда, а не жидкость или газ. Лазер усиливается в стеклянном волокне, чтобы получить гораздо меньший размер пятна, чем достигается с помощью методов CO 2 , что делает его идеальным для резки отражающих металлов.
Услуги
TWI предлагает различные услуги, включая лазерную сварку, гибридную лазерно-дуговую сварку, лазерную обработку поверхности, вывод из эксплуатации лазера, лазерное напыление металла и селективное лазерное плавление.
Изобретая газовую лазерную резку в 1967 году, TWI продолжает играть активную роль в разработке процессов резки.
Лазерные технологии в TWI
TWI находится в авангарде развития лазерной обработки материалов и предлагает лазерную сварку, лазерную резку, гибридную лазерно-дуговую сварку и лазерную зачистку.
Лазерная резка
TWI обладает необходимым оборудованием, знаниями и опытом для проведения исследований и разработок в этой области.
Вывод из эксплуатации с использованием лазеров
TWI имеет опыт и постоянные исследования и разработки в области применения лазерных технологий для вывода из эксплуатации.
Лазерная чистка
Компания TWI разработала оборудование и методы для демонстрации использования высокомощного волоконного лазера для дистанционной очистки бетонных поверхностей.
Где используется?
Эта технология может использоваться для различных применений, включая резку и разметку таких металлов, как алюминий, нержавеющая сталь, низкоуглеродистая сталь и титан. Однако этот процесс также можно использовать для промышленной резки пластика, дерева, керамики, воска, тканей и бумаги.
Технологии лазерной резки используются в различных отраслях промышленности, в том числе в аэрокосмической и автомобильной, а также для резки в опасных средах, например, при выводе из эксплуатации атомных электростанций.
Металл
Резка металла является одним из наиболее распространенных применений лазерной резки и используется для таких материалов, как нержавеющая и мягкая сталь, вольфрам, никель, латунь и алюминий. Лазеры идеально подходят для резки металла, поскольку они обеспечивают чистый срез с гладкой поверхностью.
Металл, вырезанный лазером, широко используется для изготовления компонентов и структурных форм, включая кузова автомобилей, корпуса мобильных телефонов, рамы двигателей или балки панелей.
Древесина
Этот процесс резки можно использовать с древесиной, МДФ и березовой фанерой среди наиболее распространенных материалов, так как они могут быть изготовлены в виде больших листов. Чем тверже древесина, тем больше требуется мощность лазера, при этом для твердых пород дерева требуется больше мощности, чем для мягких пород, таких как бальза.
Древесина является предпочтительным материалом, поскольку она обеспечивает прочность без затрат на металлы, однако с другой стороны, древесина может деформироваться или гнуться со временем, особенно если она подвергается высоким нагрузкам или используется во влажной среде. Помимо резки, лазеры также часто используются для гравировки дерева, а программы САПР используются для создания точных, но сложных конструкций.
Преимущества
Лазерная резка имеет ряд преимуществ по сравнению с другими процессами, например, меньшее загрязнение и более легкая обработка . Точность также может быть улучшена с помощью лазеров, поскольку луч не изнашивается в процессе резки , а материалы также менее подвержены деформации при лазерной резке. Лазеры позволяют резать материалы, которые трудно разрезать другими методами.
Лазерные процессы также стабильно обеспечивают высокий уровень точности и аккуратности с небольшим допуском на человеческую ошибку, сокращение потерь, снижение энергопотребления и, как следствие, снижение затрат .
Лазерная резка может использоваться для травления сложных рисунков на небольших деталях, оставляя металл без заусенцев и с чистым срезом. Загрязнение заготовки при лазерной резке также меньше, чем при других процессах.
Недостатки
Несмотря на множество преимуществ, этот процесс также является синонимом высокое энергопотребление . Кроме того, лазерная резка пластика создает токсичные пары , которые необходимо выводить, что само по себе является дорогостоящей задачей.
Эффективность лазерной резки также зависит от толщины заготовки, разрезаемого материала и типа используемого лазера. Без надлежащего ухода материалы, подлежащие резке, могут сгореть, а некоторые металлы могут изменить цвет, если не будет использована правильная интенсивность лазера. Хотя плазменная резка по-прежнему позволяет резать более толстые листы, чем лазерная резка, достижения в лазерной технологии означают, что разрыв сокращается, хотя затраты на оборудование все еще могут быть непомерно высокими .
Наконец, будучи автоматизированным процессом, пробные прогоны и ремонт требуют участия человека, что приводит к риску серьезных ожогов в случае контакта оператора с лазером.
Связанные часто задаваемые вопросы (FAQ)
Какие проблемы возникают при лазерной резке алюминия и как их решить?
Объясняется отражение луча CO2-лазера и способы его преодоления.
В чем разница между станками с летающей оптикой и станками с фиксированной оптикой для лазерной резки CO2?
Эти два метода, используемые в лазерной резке, сравниваются, выделяя движение заготовки, лазерной головки или луча.
Компания лазерной резки | Изготовленные на заказ детали
Прототипы и производство по запросу, в тот же день от 50 долларов всего за 1. Скидка 93% за 10 000.
“Сегодня я получил свои изделия, и они выглядят великолепно! Они не только прибыли почти на две недели раньше запланированного, но и дерево было великолепным. Пожалуйста, передайте мою благодарность вашей производственной команде! :)”
«Мы рассматриваем это как начало чего-то грандиозного»
Оценщик цен
Узнайте, как ваши затраты могут колебаться в зависимости от материала, машинного времени и типа изготовления, с помощью нашего оценщика цен. Или получите индивидуальное предложение.
Независимо от того, является ли деталь прототипом или конечным продуктом, детали, вырезанные лазером Ponoko, всегда изготавливаются в соответствии с одними и теми же стандартами точности с размерной точностью ± 0,13 мм, сложными элементами 1×1 мм и лазерным разрезом 0 мм. до 0,2мм. Лазерная резка Ponoko всегда выполняется по самым высоким стандартам. Кроме того, все наши возможности применимы независимо от того, изготавливается ли деталь из стали, алюминия, дерева или войлока, и эти же возможности применимы к любому заказу любого размера.
Материал
Сложность детали
Размер детали
Маленькая деталь Большая деталь
Отделочные услуги
- В готовом виде
- Детали без заусенцев

QuantityEstimated Price
1
USD $6.59
5
USD $1.77
10
USD $1.14
50
USD $0.56
100
USD $0.47
1,000
0,28 долл. США
10 000
0,21 долл. США
Ведущий в отрасли сервис лазерной резки с программным управлением
Лазер Ponoko режет сотни материалов точно, точно и быстро. Воспользуйтесь нашей онлайн-системой расценок, чтобы легко получить цены на свои компоненты, даже если вам нужно отправить только одну деталь сегодня. Широкий ассортимент конструкционных материалов Ponoko доступен без минимального количества заказа, но его можно масштабировать, чтобы легко удовлетворить все ваши производственные потребности.
Ponoko предлагает услуги лазерной резки широкого спектра технических материалов с гарантией точности и качества. Хотя многие из наших клиентов являются лидерами в своих отраслях, наши услуги доступны даже для небольших стартапов и частных лиц. Наши клиенты варьируются от гигантов отрасли, таких как Apple, до студентов инженерных специальностей и любителей, которым нужны детали самого высокого качества, вырезанные лазером, по разумной цене.
Мы автоматически защищаем вашу интеллектуальную собственность с помощью наших стандартных условий обслуживания учетной записи, которые включают соглашение о неразглашении и условия конфиденциальности. Закажите детали, вырезанные лазером без риска, и если они не идеально подходят в соответствии с нашими гарантиями качества, мы бесплатно изготовим и повторно отправим их.
Нестандартные детали доставляются в тот же день.
Заказные лазерные детали с доставкой в тот же день (или возврат денег).
–+
Что такое лазерная резка?
Лазерная резка — это субтрактивный метод производства, в котором для резки заготовки используется сфокусированный лазерный луч.
Подавляющее большинство систем лазерной резки представляют собой двухосевые станки, которые перемещаются в направлениях X и Y и, как таковые, в основном предназначены для резки 2D-форм. Каждая ось приводится в движение с помощью шаговых двигателей, которые сами управляются компьютером. Таким образом, лазерные резаки подпадают под категорию станков с числовым программным управлением (ЧПУ).
Несмотря на то, что лазеры существуют с 1963 года, только в 1980-х годах лазерная резка как производство стала жизнеспособной. До этого лазеры в основном использовались для вырезания отверстий в алмазных штампах для аэрокосмической промышленности, но как только стало очевидно, что их скорость работы в сочетании с числовым управлением может создавать детали с невероятной степенью точности, их использование расширилось в геометрической прогрессии.
Ponoko — компания по лазерной резке, базирующаяся в районе залива Окленд, с более чем 15-летним опытом работы. Обслужив более 33 000 клиентов, изготовив более 2 миллионов деталей, мы участвовали в многочисленных проектах, охватывающих все отрасли. Поскольку самой большой проблемой, с которой сталкиваются инженеры, является время, мы сосредоточили свое внимание на развитии компании по лазерной резке, которая может рассчитать стоимость, произвести и поставить точные детали менее чем за 24 часа.
–+
Насколько быстро выполняется лазерная резка?
–+
В чем преимущество лазерной резки?
–+
Какие лазерные технологии существуют?
Заказные детали доставляются в тот же день.
Расценки на лазерную резку онлайн за считанные секунды, что сокращает время выхода на рынок.
–+
Какое программное обеспечение можно использовать для создания деталей лазерной резки?
Можно использовать любое программное обеспечение для проектирования, которое может выводить файлы, совместимые с нашей онлайн-службой программного обеспечения (мы принимаем файлы 3D STEP, 2D DXF, SVG, EPS и Ai). Как и в любом производственном процессе, программное обеспечение, используемое для разработки продукта, никогда не взаимодействует с оборудованием, и большинство производителей преобразуют представленные файлы в свои собственные форматы.
В случае лазерных резаков файлы дизайна преобразуются в G-код, который определяет положение лазерной головки, а также выходную энергию луча. Например, выгравированные области дают указание лазерной головке уменьшить мощность, а вырезанные области увеличивают эту мощность.
Для тех, кто ищет подходящий пакет программного обеспечения для проектирования, у инженеров есть множество вариантов, некоторые из которых платные, а другие бесплатные. FreeCAD — это один из вариантов, который могут использовать дизайнеры, и он идеально подходит для тех, кто ищет среду с открытым исходным кодом. Он может экспортировать распространенные форматы файлов, а его способность проектировать как 2D-, так и 3D-детали делает его идеальным для тех, кто хочет расширить свое использование САПР.
Для тех, кто ищет более ориентированный на инженеров пакет программного обеспечения для проектирования, Alibre станет хорошим выбором, поскольку он специально разработан с учетом инженерных проектов. Отдельные части могут быть спроектированы, объединены, а затем механически смоделированы. Оттуда детали могут быть обведены и экспортированы для использования с услугами лазерной резки Ponoko. Другие варианты программного обеспечения для проектирования, доступные инженерам, также включают AutoDesk, который пользуется огромной популярностью в сообществе САПР, и SolidWorks, способный создавать сложные инженерные проекты, такие как Alibre. Кроме того, у нас есть онлайн-инструменты САПР, такие как Autodesk Fusion 360 и PTC OnShape.
–+
Какие файлы читает лазерный резак?
–+
Должен ли я использовать векторную или растровую графику для лазерной резки?
Заказные детали доставляются в тот же день.
Производство с помощью программного обеспечения также означает снижение стоимости нестандартных деталей.
–+
Сколько стоит лазерная резка?
Лазерная резка предлагает инженерам одно из самых экономичных решений благодаря низким эксплуатационным расходам лазерной резки, скорости, с которой они могут резать, возможности легкого масштабирования и возможности резать любую 2D-форму без необходимость специфических для машины настроек.
Во-первых, лазерные резаки используют луч света для удаления материала, что означает отсутствие использования расходных инструментов (таких как сверла и лезвия). Хотя в лазерном резаке есть оптические компоненты, они редко требуют замены, особенно если лазерный резак находится в хорошем состоянии. Таким образом, единственным крупным расходом при эксплуатации лазерного резака является электроэнергия, необходимая для генерации лазерного луча.
Отсутствие пресс-форм, характерных для других методов производства, также устраняет необходимость в специальных инструментах или оборудовании для конкретных деталей. Лазерный резак может принять любой файл дизайна и начать резку без внесения каких-либо изменений в сам лазерный резак. Хотя литье пластмасс под давлением дешевле, чем лазерная резка, это касается только крупных заказов, превышающих десять тысяч. Даже в этом случае литье пластмасс под давлением не поддерживает внезапные изменения конструкции, поскольку требуются новые формы.
Как компания, занимающаяся лазерной резкой, мы стремимся предложить нашим клиентам отличный баланс между стоимостью, качеством и скоростью. Наш онлайн-сервис на основе программного обеспечения позволяет загружать проекты и цитировать их без какого-либо участия с нашей стороны, что позволяет инженерным группам уделять больше времени выбору материалов и проектированию деталей.
–+
Можно ли вырезать трехмерные фигуры с помощью лазерного резака?
Заказные детали доставляются в тот же день.
Мы обещаем вам точность ±0,13 мм (или повторим)
–+
Какую точность обеспечивает лазерная резка?
Постоянство лазерных лучей и использование шаговых двигателей позволяют использовать лазерные резаки для выполнения точных разрезов. В Ponoko наша точность находится в пределах допусков 0,13 мм.
Лазеры настолько точны, что их часто используют для активной подстройки прецизионных конденсаторов и резисторов, при этом материал удаляется до тех пор, пока не будут достигнуты желаемые электрические характеристики. По сравнению с другими производственными технологиями лазерная резка обеспечивает лучший компромисс между точностью и скоростью.
Например, 3D-печать печально известна низкой точностью размеров при печати пластиковыми материалами, такими как PLA и ABS, в то время как печать металлическими порошками вызывает проблемы с точностью, поскольку нагрев детали вызывает усадку. Фрезерование с ЧПУ — это производственный процесс, который может обеспечить более высокую точность, чем лазерная резка, но длительный период времени, необходимый для каждого прохода, означает, что он применим только в тех случаях, когда важна точность (например, установка поршней в блок цилиндров).
Мощные лазерные лучи могут с трудом формировать разрезы малого диаметра, в то время как маломощные лучи не могут резать прямо. Это означает, что, хотя лазерные резаки могут обеспечить превосходную точность размеров, они не идеальны для создания крошечных элементов с узкой шириной резки и сложными деталями, расположенными близко друг к другу.
Чтобы обеспечить единообразие для всех деталей и материалов, мы создали список возможностей, которые всегда гарантированы, независимо от того, какой материал вы выберете или размер детали. Например, точность размеров всех деталей составляет ±0,13 мм, что означает, что независимо от размера вашей детали ее размер всегда будет в пределах ±0,13 мм от указанного размера. Самые маленькие детали, которые мы можем вырезать, имеют размер 6×6 мм из-за использования решетчатых станин (это означает, что детали меньшего размера провалятся через отверстия в станине лазера). Сложные элементы на деталях имеют минимальный размер 1×1 мм, в противном случае сильный нагрев лазера может вызвать деформацию и обезображивание.
–+
Что такое лазерный пропил и стоит ли о нем беспокоиться?
–+
С какими проблемами сталкиваются станки для лазерной резки?
Заказные детали доставляются в тот же день.
Ponoko предлагает материалы инженерного качества, а также услуги по отделке.
Латунь PCM
5052-h42 Алюминий
Нержавеющая сталь 304
Красный акрил
Пенополиуретан
Прозрачный акрил
Черный силикон
Янтарная бамбуковая фанера
Белый делрин
Черный акрил
Неоновый оранжевый акрил
Серая поляризационная пленка
–+
Какие материалы можно резать лазером?
Лазером можно резать многие материалы, в том числе металл, пластик, дерево, органику и т. д., но, вопреки распространенному мнению, лазер не плавит разрезаемую деталь, а испаряет материал. Именно это испарение позволяет лазерным резчикам работать с горючими материалами, такими как дерево и бумага, не поджигая их.
Типы металлов, которые популярны для лазерной резки, включают алюминий, латунь и сталь, поскольку они хорошо работают с волоконными лазерами, но такие металлы, как медь, могут быть сложными, поскольку их отражающая природа может повредить оптические компоненты лазерной резки. Обычные пластмассы, используемые с лазерными резаками, включают акрил и делрин благодаря чистому краю, оставляемому лазерным резаком, простоте резки и их долговечности. Популярные органические материалы, используемые с лазерными резаками, включают бумагу, картон, дерево и войлок. Более толстые и тонкие материалы могут создавать уникальные проблемы.
Несмотря на то, что в лазерных резаках можно использовать различные материалы, не все можно использовать, поскольку некоторые из них могут быть токсичными, а другие могут повредить сам лазерный резак. Таким образом, перед инженерами часто ставится задача найти подходящий запас материалов, безопасных для лазера, и это может занять драгоценное время.
Чтобы помочь командам инженеров, Ponoko предлагает тщательно подобранный ассортимент безопасных для лазерного излучения материалов, доступных через наше онлайн-приложение для заказа деталей. Наш ассортимент материалов включает инженерный металл, дерево, пластик и многое другое. Наши материалы имеют тщательно контролируемые характеристики, такие как прочность на растяжение, плотность и электропроводность. Это особенно полезно для инженеров, разрабатывающих детали для приложений с жестким контролем, таких как медицина, автомобилестроение и аэрокосмическая промышленность.
Но если вам нужно разрезать очень специфический материал, мы можем это сделать! Просто отправьте нам запрос с указанием потребности в нестандартном материале, и наши инженеры помогут организовать проект, или выберите «Нестандартный материал» при выборе материала из нашего онлайн-каталога материалов.
–+
Существуют ли материалы, которые нельзя резать лазером?
–+
Подходит ли лазерная резка для массового производства?
–+
Что такое вырезанные лазером живые петли и как их можно использовать для создания трехмерных деталей?
Заказные детали доставляются в тот же день.
Ponoko быстро решает сложные задачи лазерной резки.
–+
Занимается ли Ponoko необычными и уникальными проектами лазерной резки?
Да. Если что-то и можно сказать о инженерных проектах, так это то, что всегда есть какая-то нестандартная проблема, которую необходимо решить, будь то потребность в нестандартном материале или разработка уникальной фурнитуры. Что еще хуже, может быть сложно найти производителей, готовых решить эти проблемы, не сталкиваясь с серьезными компромиссами в проекте.
Как компания, занимающаяся лазерной резкой, мы гордимся тем, что беремся за любой проект, который встречается на нашем пути. Независимо от того, являются ли наши клиенты стартапами, малыми предприятиями или крупными корпорациями, наша команда опытных инженеров и операторов машин может предоставить профессиональные консультации по процессам проектирования и производства. Обладая более чем 15-летним опытом работы в отрасли лазерной резки, мы реализовали множество уникальных проектов, начиная от наборов для экспресс-тестирования на COVID и заканчивая компонентами аэрокосмической отрасли, работающими в экстремальных условиях.
–+
Принимает ли Ponoko нестандартные материалы для лазерной резки?
Заказные детали доставляются в тот же день.
Нам доверяют более 35 000 основателей, генеральных директоров, инженеров, дизайнеров и ученых.
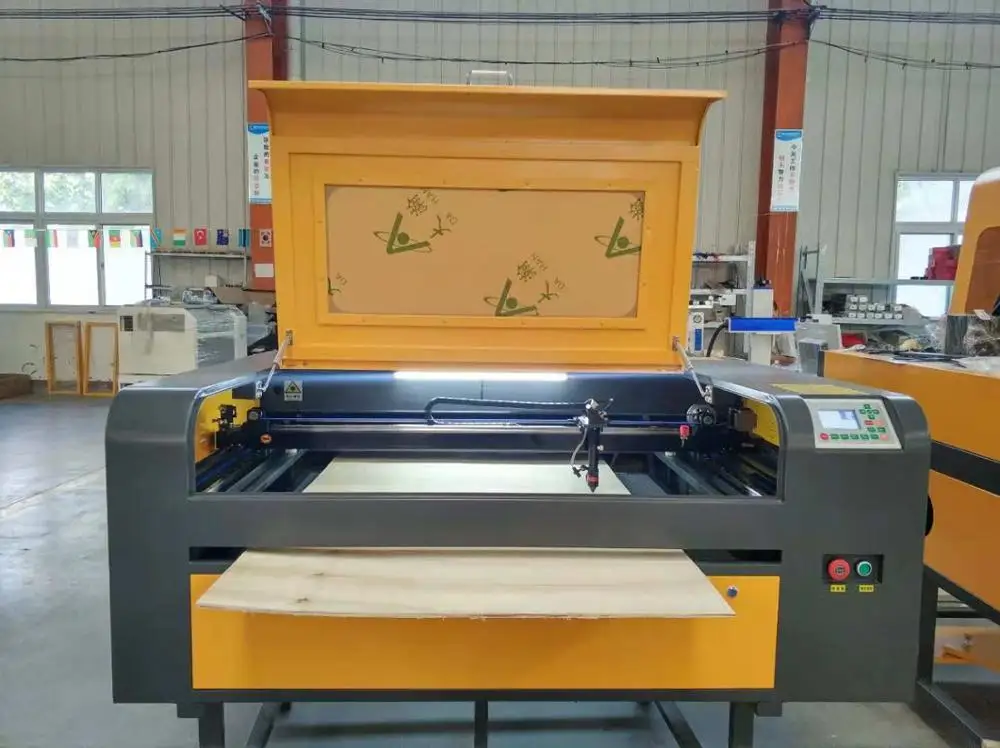
Закажите лазерную резку нестандартных деталей для своего ноутбука с доставкой в тот же день.
*От 50 долларов всего за 1. Скидка 93% на 10 000.
Нестандартные детали доставляются в тот же день.
* Доставка в тот же день (или возврат денег) доступна для заказов с использованием ограниченного набора материалов, размещенных до 11:00 по тихоокеанскому времени с понедельника по пятницу, от 1 до 100 деталей в офисы Bay Area USA. Доставка в тот же день (или возврат денег) доступна в США и по всему миру.
CO2-лазерные граверы, волоконные лазеры и многое другое
Ознакомьтесь с нашей широкой коллекцией лазерных станков! От лазерных резаков до волоконных лазерных граверов – здесь вы найдете свой новый лазерный гравировальный станок. Лазерные станки OMTech обеспечивают невероятное качество лазерной резки и гравировки.
Ознакомьтесь с нашими аксессуарами и деталями для лазерной гравировки, которые подходят к вашему станку лазерной резки!
25 товаров
Сортировать СортировкаЛучшиеЛучшие продажиПо алфавиту, от A до ZПо алфавиту, от Z до AЦена, от низкой к высокойЦена, от высокой к низкойДата, от старой к новойДата, от новой к старой
DF0812-40BG — CO2-лазерный гравер мощностью 40 Вт с рабочей зоной 8 x 12 дюймов, ЖК-дисплеем и указателем с красной точкой (синий) — бесплатный 4-дюймовый канальный вентилятор в комплекте
Цена продажи $499 99 499,99 долларов США Обычная цена $529 99 529,99 долларов США Сэкономьте $30
DF0812-40RW — Станок для лазерной гравировки на углекислом газе мощностью 40 Вт с рабочей зоной 8 x 12 дюймов, ЖК-дисплеем и указателем с красной точкой (красный) — бесплатный 4-дюймовый канальный вентилятор в комплекте
Цена продажи499$ 99 499,99 долларов США Обычная цена $529 99 529,99 долларов США Сэкономьте $30
MF1220-50 – Станок для лазерной резки CO2 мощностью 50 Вт с рабочей зоной 12 x 20 дюймов
Цена продажи 2199 долларов США 99 2199,99 долларов США Обычная цена 2399 долларов США 99 2399,99 долларов США Сэкономьте $200
MF1220-50R – Станок для лазерной гравировки CO2 мощностью 50 Вт 12 x 20 дюймов с поворотной осью
Цена продажи 2199 долларов США 99 2199,99 долларов США Обычная цена 2299 долларов США 99 2299,99 долларов США Сэкономьте $100
MF1624-55 – Станок для лазерной резки CO2 мощностью 55 Вт с рабочей зоной 16 x 24 дюйма
Цена продажи 2499 долларов США 99 2499,99 долларов США Обычная цена 2599 долларов США 99 2599,99 долларов США Сэкономьте $100
MF2028-60 – Станок для лазерной резки CO2 мощностью 60 Вт с рабочей зоной 20 x 28 дюймов
2999 долларов 99 2999,99 долларов
AF2028-60 — Станок для лазерной резки CO2 мощностью 60 Вт с рабочей зоной 20 x 28 дюймов (с автофокусом)
3199 долл. США 99 3199,99 долларов США
MF2028-80 — Станок для лазерной резки CO2 мощностью 80 Вт с рабочей зоной 20 x 28 дюймов
3 299 долл. США 99 $3299,99
AF2028-80 — Станок для лазерной резки CO2 мощностью 80 Вт с рабочей зоной 20 x 28 дюймов (с автофокусом)
3699 долларов 99 $3699,99
AF2435-80 — Станок для лазерной резки CO2 мощностью 80 Вт с рабочей зоной 24 x 35 дюймов (с автофокусом)
4 749 долл. США 99 4749,99 долларов
MF2028-100 – Станок для лазерной резки CO2 мощностью 100 Вт с рабочей зоной 20 x 28 дюймов
Цена продажи 3899 долларов США 99 3899,99 долларов США Обычная цена 3999 долларов США 99 3999,99 долларов США Сэкономьте $100
AF2440-100 — Станок для лазерной резки CO2 мощностью 100 Вт с рабочей зоной 24 x 40 дюймов (с автофокусом)
5 499 долл. США 99 5 499,99 долларов
ZF3551-100 – Станок для резки с двойным лазерным гравером CO2 мощностью 100 Вт с рабочей зоной 35 x 51 дюйм с двумя лазерными трубками и лазерными головками 6999,99 долларов США Обычная цена 7 299 долларов США 99 7 299,99 долларов США Сэкономьте $300
AF3555-130 – Станок для лазерной резки CO2 мощностью 130 Вт с рабочей зоной 35 x 55 дюймов (с автофокусом)
от 7 299 долларов США 99 от 7 299,99 долларов США Обычная цена 7 399 долларов США 99 7 399,99 долларов США Сэкономьте $100
ZF3551-130 – Станок для резки с двойным лазерным гравером CO2 мощностью 130 Вт с рабочей станиной 35 x 51 дюйм с охладителем воды 5202, двойными лазерными трубками и лазерными головками 7999,99 долларов США Обычная цена 8 299 долларов США 99 8 299,99 долларов США Сэкономьте $300
AF4063-150 — Станок для лазерной резки CO2 мощностью 150 Вт с рабочей зоной 40 x 63 дюйма (с автофокусом)
от 8 499 долларов США 99 от $8 499,99
AF5070-150 – СТАНОК ДЛЯ РЕЗКИ С СО2-ЛАЗЕРОМ, 150 Вт С РАБОЧЕЙ ЗОНОЙ 50 Х 70 ДЮЙМОВ (СО ВСТРОЕННЫМ ОХЛАДИТЕЛЕМ ВОДЫ)
Цена продажи 9 499 долларов США 99 9 499,99 долларов США Обычная цена 9 699 долларов США 99 9 699,99 долларов США Сэкономьте $200
FM4343-20S — 20-ваттный лазерный маркерный гравировальный станок с разъемным волокном и рабочей зоной 4,3 x 4,3 дюйма
Цена продажи 2799 долларов США 99 2799,99 долларов США Обычная цена 3199 долларов США 99 3199,99 долларов США Сэкономьте $400
FM6969-30S — Гравировальный станок с раздельным оптоволоконным лазером мощностью 30 Вт с рабочей зоной 6,9 x 6,9 дюймов
от 2 699 долл. США 99 от 2699,99 долларов США
Обычная цена
3999 долларов США 99 3999,99 долларов США
Сэкономьте 1300 долларов США
FM7979-50S – Гравировальный станок для лазерных маркеров с разъемным оптоволоконным разъемом мощностью 50 Вт с рабочей зоной 7,9 x 7,9 дюймов
5 799 долларов 99 $5799,99
Продано
MP6969-20 — МОПА ВОЛОКОННЫЙ ЛАЗЕРНЫЙ МАРКИРОВОЧНО-ГРАВИРОВАЛЬНЫЙ СТАНОК 20 Вт С РАБОЧЕЙ ЗОНОЙ 6,9 X 6,9 ДЮЙМА
5 599 долл. США 99 5 599,99 долларов США
MP6969-30 — МОРА ВОЛОКОННЫЙ ЛАЗЕРНЫЙ МАРКИРОВОЧНЫЙ СТАНОК 30 Вт С РАБОЧЕЙ ЗОНОЙ 6,9 X 6,9 ДЮЙМА
от 5 099 долл. США 99 от 5099,99 долларов США Обычная цена 5999 долларов США 99 5999,99 долларов США Сэкономьте $900
MP6969-60 — МОРА ВОЛОКОННЫЙ ЛАЗЕРНЫЙ МАРКИРОВОЧНЫЙ СТАНОК МОЩНОСТЬЮ 60 Вт С РАБОЧЕЙ ЗОНОЙ 6,9 X 6,9 ДЮЙМА
от 5 949 долл. США 99 от 5949,99 долларов США
Обычная цена
6 999 долларов США 99 6999,99 долларов США
Сэкономьте 1050 долларов США
MP6969-80 — 80-Вт ЛАЗЕРНЫЙ МАРКИРОВОЧНЫЙ СТАНОК MOPA С РАБОЧЕЙ ЗОНОЙ 6,9 X 6,9 ДЮЙМА
от 8 159 долл. США 99 от 8 159,99 долларов США Обычная цена 9 599 долларов США 99 $9,599,99 Сэкономьте $1440
MP6969-100 — МОПА ВОЛОКОННЫЙ ЛАЗЕРНО-ГРАВИРОВАЛЬНЫЙ СТАНОК 100 Вт С РАБОЧЕЙ ЗОНОЙ 6,9 X 6,9 ДЮЙМА
Цена продажи 12 499 долларов США 99 12 499,99 долларов США Обычная цена 12 999 долларов США 99 12 999,99 долларов США Сэкономьте $500
Индивидуальная онлайн-служба лазерной резки
Xometry предлагает высококачественные услуги лазерной резки металла. Наши услуги лазерной резки металла поддерживают различные металлические материалы, в том числе: сталь, нержавеющую сталь, инструментальную сталь, пружинную сталь, алюминий, латунь, бронзу, медь и титан. Наши станки для лазерной резки используют как волоконные лазеры, так и CO2-лазеры и могут резать до 4 дюймов металлического материала. Xometry предлагает мгновенные расценки на услуги лазерной резки металла и бесплатную доставку заказов в США.
Для получения дополнительной информации посетите нашу страницу услуг лазерной резки металла или просто начните расчет стоимости сейчас.
Список материалов для лазерной резки металла
Список металлических материалов, поддерживаемых службой лазерной резки металла Xometry, см. ниже. Другие материалы также могут быть доступны для цитаты.
- 1075 Пружинная сталь, отожженная
- 1075 Пружинная сталь, вороненая закалка
- 1095 Пружинная сталь, отожженная
- 1095 Пружинная сталь, вороненая закаленная
- 4130 chrome-moly steel, annealed
- Aluminum 2024-T3
- Aluminum 5052 h42
- Aluminum 6061 T6
- Aluminum 7075 T6
- Aluminum MIC6
- AR400 Steel, hardened
- AR500 Steel, hardened
- Bearing Bronze 932 M07
- Латунь 260
- Латунь 353 H02
- Латунь 464 H01
- Бронза 220 H02
- Bronze 510 H08 (Spring) 66666666666666666666666666666666666666666666666666666666666.
- Copper 110, Annealed
- Copper 110, H01
- Copper 110, H02
- Corten A588 (Weathered) Steel
- Hot Rolled Steel 1045
- Hot Rolled Steel A569/ASTM A1011
- Nickel 200, annealed
- Nickel 625, отожженная
- Предварительно анодированная 6061-T6, черная
- Кремниевая бронза 655
- Нержавеющая сталь 17-4 PH, отожженная
- Нержавеющая сталь 17-7 Подкладка, закаленная
- Нержавеющая сталь 300166
- нержавеющая сталь 304
- из нержавеющей стали 304 Shim, закаленная
- из нержавеющей стали 304, #4 с матовой сталью
- Stainless Steel 316
- NENSALENSALEDELED 316, ANEALED
-500x500-product_popup.jpg)
Услуги лазерной резки пластика
Xometry предлагает услуги лазерной резки пластика высокого качества. Наши услуги лазерной резки пластика поддерживают различные пластиковые материалы, в том числе: акрил, пену и эластомер. Наши станки для лазерной резки используют как волоконные лазеры, так и CO2-лазеры и могут резать до 4 дюймов пластикового материала.
Для получения дополнительной информации посетите нашу страницу «Услуги лазерной резки пластика» или просто начните мгновенное предложение сейчас.
Список материалов пластиковой лазерной режущей Черный
Услуги лазерной резки акрила
Xometry предлагает высококачественные услуги лазерной резки акрила. Мы предлагаем прозрачные (прозрачные) акриловые материалы, а также различные цвета. Преимущества лазерной резки акрилом включают в себя прочность, простоту использования, прозрачность и водонепроницаемость/влагостойкость.
Для получения дополнительной информации посетите нашу страницу услуг лазерной резки акрила или просто начните мгновенное предложение сейчас.
Услуги лазерной резки дерева
Xometry предлагает высококачественные услуги лазерной резки дерева. Мы предлагаем различные древесные материалы, включая лиственные породы вишни, ДВП, МДФ, лиственные породы тополя, лиственные породы красного дуба, ламинат без покрытия (фанеру) и березу.
Для получения дополнительной информации посетите нашу страницу услуг лазерной резки дерева или просто начните мгновенное предложение сейчас.
Альтернативы лазерной резке
Альтернативы лазерной резке для листовой резки включают услуги гидроабразивной резки и услуги плазменной резки. Лазерная резка имеет ограничения по толщине разрезаемого материала. Лазерная резка может резать до 4 дюймов материала. Для материалов толще 4 дюймов используйте услуги гидроабразивной или плазменной резки.
Станки для лазерной резки и сверления
Резка широкого спектра материалов от металлов, пластмасс и композитов до бумаги, керамики и дерева.
- Самый широкий ассортимент лазеров Не идите на компромисс. Получите лазерный источник, который идеально подходит для ваших нужд.
- Интуитивное управление программным обеспечением Получите единый графический интерфейс, объединяющий все аспекты настройки и выполнения процесса.
- Варианты автоматизации/интеграции Используйте как автономные машины или полностью интегрируйте их в свою производственную линию.
Упрощенная лазерная резка и сверление
Когерентные станки для лазерной резки предназначены для широкого спектра применений — от резки коронарных стентов до листовой стали для бытовой техники. Все они используют одно и то же объектно-ориентированное программное обеспечение Laser Framework, которое упрощает даже самую сложную последовательность операций.
Семейство продуктов для лазерной резки и сверления
Удаленная диагностика — быстрый возврат к работе (RTO). | Универсальность — большая рабочая камера. | Более точные результаты — разрешение позиционирования в микронах. | |
Сведение к минимуму термических эффектов — опциональный лазер USP обеспечивает холодную резку. | Гибкая резка — включает встроенную функцию влажной резки. | Стабильность и точность — прочная платформа для резки гранита. | |
Мощность до 1,5 кВт для высокой пропускной способности | Высококачественный (M2 ≤1,5) луч обеспечивает высокую точность | Оптимизированное программное управление для легкой интеграции | |
Долгий срок службы — проверенная технология Pure UV™.![]() | Гибкость — множество дополнительных функций. | Быстрая обработка — выбор мощности лазера 20 или 40 Вт. | |
Экономичность – CO₂-лазеры сочетают в себе низкую стоимость и высокую надежность. | Универсальность — луч среднего ИК-диапазона режет большинство неметаллов. | High Speed — до 450 Вт для высокой скорости обработки. | |
Маленькие и большие шатуны – 50 Вт, длительность импульса нс или 50 Вт, длительность импульса мс, волоконный лазер. | Комплексное решение — включает лазер, оптику, газовое сопло и контроллер. | Повышение производительности — 0,5 секунды на одну метку при скорости до 3 м/мин. | |
Power Up — доступны лазеры мощностью от 100 Вт до 600 Вт.![]() | Повышение качества — технологии SmartWeld™ и SmartWeld + для превосходных сварных швов. | Get a Head — интегрированное программное обеспечение и технологические головки для сварки или резки. | |
Гладкие отверстия — Один длинный лазерный импульс плавно просверливает каждое отверстие. | Высокая производительность — до 5 игл в секунду. | Широкий рабочий диапазон — сверление отверстий диаметром от 50 до 750 мкм. | |
Преимущества материалов — волоконные, твердотельные, CO₂, диодные и ультракороткие импульсные лазеры. | Just Your Size — четыре разных напольных шкафа. | Готов к использованию — предварительно загруженные технологические рецепты. | |
Оставайтесь сильными — поднимайте детали весом до 45 кг.![]() | Варианты лазера — наносекундный, USP или волоконный лазер. | Полная интеграция — закрытые (класс 1) или открытые (класс 4) корпуса. |
Избранный блог
Производство медицинского оборудования: спасение жизней, резка стентов с помощью лазеров
Узнайте, как лазерные установки Coherent широко используются производителями медицинских устройств, таких как коронарные стенты, которые обеспечивают минимально инвазивное лечение сердечных приступов.
Читать блог
Готов к
Начать?
Region *United StatesCanadaAfghanistanAland IslandsAlbaniaAlgeriaAmerican SamoaAndorraAngolaAnguillaAntarcticaAntigua and BarbudaArgentinaArmeniaArubaAustraliaAustriaAzerbaijanBahamasBahrainBangladeshBarbadosBelarusBelgiumBelizeBeninBermudaBhutanBoliviaBosnia and HerzegovinaBotswanaBouvet IslandBrazilBritish Indian Ocean TerritoryBritish Virgin IslandsBrunei DarussalamBulgariaBurkina FasoBurundiCambodiaCameroonCape VerdeCayman IslandsCentral African RepublicChadChileChinaChristmas IslandCocos (Keeling) IslandsColombiaComorosCongo (Brazzaville)Congo, (Kinshasa)Cook IslandsCosta RicaCroatiaCubaCuraçaoCyprusCzech RepublicCôte d’IvoireDenmarkDjiboutiDominicaDominican RepublicEcuadorEgyptEl SalvadorEquatorial GuineaEritreaEstoniaEthiopiaFalkland Islands (Malvinas)Faroe островаФиджиФинляндияФранцияФранцузская ГвианаФранцузская ПолинезияФранцузские южные территорииГабонГамбияГрузияГерманияГанаГибралтарГрецияГренландияГренадаГваделупаГуамГватемалаГернсиГвинеяГвинея-БисауГайанаГаитиХерд и Макдональдс Исла ndsHoly See (Vatican City State)HondurasHong Kong, SAR ChinaHungaryIcelandIndiaIndonesiaIran, Islamic Republic ofIraqIrelandIsle of ManIsraelItalyJamaicaJapanJerseyJordanKazakhstanKenyaKiribatiKoreaKuwaitKyrgyzstanLao PDRLatviaLebanonLesothoLiberiaLibyaLiechtensteinLithuaniaLuxembourgMacao, SAR ChinaMadagascarMalawiMalaysiaMaldivesMaliMaltaMarshall IslandsMartiniqueMauritaniaMauritiusMayotteMexicoMicronesia, Federated States ofMoldovaMonacoMongoliaMontenegroMontserratMoroccoMozambiqueMyanmarNamibiaNauruNepalNetherlandsNetherlands AntillesNew CaledoniaNew ZealandNicaraguaNigerNigeriaNiueNorfolk IslandNorth KoreaNorth MacedoniaNorthern Mariana IslandsNorwayOmanPakistanPalauPalestinian TerritoryPanamaPapua New GuineaParaguayPeruPhilippinesPitcairnPolandPortugalPuerto RicoQatarRomaniaRussian FederationRwandaRéunionSaint-BarthélemySaint HelenaSaint Kitts and NevisSaint LuciaSaint-MartinSaint Pierre и МикелонСент-Винсент и ГренадиныСамоаСан-МариноСан-Томе и ПринсипиСинт-Мартен (Dut ch part)Saudi ArabiaSenegalSerbiaSeychellesSierra LeoneSingaporeSlovakiaSloveniaSolomon IslandsSomaliaSouth AfricaSouth Georgia and the South Sandwich IslandsSouth KoreaSouth SudanSpainSri LankaSudanSurinameSvalbard and Jan Mayen IslandsSwazilandSwedenSwitzerlandSyrian Arab Republic (Syria)TaiwanTajikistanTanzania, United Republic ofThailandTimor-LesteTogoTokelauTongaTrinidad and TobagoTunisiaTurkeyTurkmenistanTurks and Caicos IslandsTuvaluU. S. Малые отдаленные острова США Виргинские островаУгандаУкраинаОбъединенные Арабские ЭмиратыВеликобританияУругвайУзбекистанВануатуВенесуэла (Боливарианская Республика)ВьетнамОстрова Уоллис и ФутунаЗападная СахараЙеменЗамбияЗимбабвеВиргинские острова (Британские) Виргинские острова (США)
StateALAKAZARCACOCTDEDCFLGAHIIDILINIAKSKYLAMMDMAMNMSMOMTNENVNHNJNMNYNCNDOHOKORPARISCSDTNTXUTVTVAWAWVWIWY
Выбрать в ДА! Я хочу получать новости и рекламные акции Coherent по электронной почте. Конфиденциальность
Обязательное поле
Введение в лазерную резку | Втулки
Ключевые выводы
- Лазерная резка отлично подходит как для единичных работ, так и для мелкосерийного производства
- Используйте лазерную резку для получения точных, простых и точно воспроизводимых деталей
- Лазерная резка идеально подходит для серийного производства различных деталей из одного и того же основного материала с минимальными изменениями в настройке
Что такое лазерная резка?
Лазерная резка — это высокоточный термический процесс с ЧПУ, в котором используется мощный лазерный луч для резки, плавления или сжигания листового материала. Он использует сфокусированный луч света для резки и травления листового материала в соответствии со спецификацией дизайна. Идеально подходит для различных типов материалов (включая металлы, дерево и полимеры) и позволяет изготавливать сложные детали без использования специального инструмента.
Этот процесс подходит как для разовых работ, так и для небольших и средних объемов производства благодаря высокой повторяемости. Лазерная резка особенно полезна для изготовления металлов (сталь, латунь, алюминий или никель). Он стал фаворитом в производстве медицинских изделий благодаря своей высокой точности, надежности и полученной гладкой поверхности.
В отличие от станков с ЧПУ лазерная резка работает с листовым материалом, изготавливая формы и формы глубиной не более 10 мм (в зависимости от типа материала).
Узнайте о различных типах изготовления листового металла →
В этой статье представлены основные различия между основными типами лазерной резки и обсуждены характеристики процесса. К концу у вас будет обзор основных принципов технологии и того, как они соотносятся с ее основными преимуществами и ограничениями.
Преимущества и недостатки лазерной резки
Преимущества
Почти непревзойденная гибкость при работе с листами материала
Лазерная резка обеспечивает почти непревзойденную гибкость при работе с листами материала. Он может резать, гравировать или надрезать различные формы из материала одинаковой толщины без изменения настроек — независимо от сложности или размера.
Узнайте о возможностях Hubs по изготовлению листового металла здесь →
Создает точные разрезы и метки
Лазерная резка позволяет создавать точные разрезы и метки, подходящие для чего угодно, от открывалок для бутылок до печатных плат. Это и быстрее, и эффективнее, чем ручные методы изготовления.
Недостатки
Сложно работать с более толстыми материалами
Работа с материалами толщиной более 100 мм может быть затруднена в зависимости от типа лазера.
Возможные более высокие затраты
Высокое потребление энергии может привести к относительно высоким эксплуатационным расходам. Перейдите к разделу расходов этой статьи для получения более подробной информации.
Основные типы лазерных резаков
При изготовлении деталей из листового металла производители используют три основных типа лазерных резаков: газовый, кристаллический и волоконный.
Газ CO2
Эти резаки с накачкой электрическим разрядом используют лазер, состоящий в основном из двуокиси углерода, гелия и азота. Излученный на длине волны 10,6 мм, CO2-лазер может прорезать материалы толще, чем резаки для волокон, с аналогичной выходной мощностью той же мощности. Эффективность и низкая стоимость – они широко используются в производстве.
Эффективный
Низкая стоимость
Широко используется и широко доступен
Кристаллические лазерные резаки
Лучи, генерируемые YVO или YAG, кристаллические лазерные резаки способны резать более прочные и толстые материалы, чем резаки CO2, из-за их меньших длин волн и более высокой интенсивности. Детали машины изнашиваются быстрее, чем бензорезы, из-за их более высокой концентрации и, следовательно, более дороги в эксплуатации.
Прочнее других типов фрез
Дороже, чем альтернативы
Детали машин быстро изнашиваются
Волоконные лазерные резаки
Принадлежащие к семейству твердотельных лазеров (лазер, использующий твердую усиливающую среду), эти инструменты используют стекловолокно для усиления базовых лазеров. Они в 3 раза более энергоэффективны, чем газовые резаки. Резаки по стекловолокну не имеют движущихся частей (таких как вентиляторы для циркуляции газа или зеркала в источнике света), что делает инструмент намного проще в обслуживании. В отличие от лазеров на основе углеродного газа, альтернативы из стекловолокна могут резать тонкие листы быстрее при той же мощности, а также могут без последствий резать материалы из отражающих материалов.
Энергоэффективнее газовых лазеров
Машина дешевле и проще в обслуживании
Можно резать светоотражающие материалы
Сравнение лазерных резаков
СО2-лазер | Кристаллический лазер | Волоконный лазер | |
---|---|---|---|
Государственный | На газовой основе | Твердотельный | Твердотельный |
Тип материала | Дерево, акрил, стекло, бумага, текстиль, пластик, фольга и пленки, кожа, камень | Металлы, металлы с покрытием, пластмассы, керамика | Металлы, металлы с покрытием, пластмассы |
Источник насоса | Газовый разряд | Лампа, диодный лазер | Диодный лазер |
Длина волны (мкм) | 10,6 | 1,06 | 1,07 |
Эффективность (%) | 10 | 2 – лампа, 6 – диод | <30 |
Диаметр пятна (мм) | 0,15 | 0,3 | 0,15 |
МВт/см2 Плотность мощности | 84,9 | 8,5 | 113,2 |
Как работает лазерный резак
При лазерной резке деталь помещается на станину, где материал затем травится или вырезается из листа с помощью лазера. Вот простой обзор процесса лазерной резки:
- Мощность регулируется в зависимости от разрезаемого материала и толщины листа. Типичный лазерный луч имеет диаметр 0,1 – 0,3 мм (мощность 2-3 кВт.)
- Чертеж САПР преобразуется в серию команд, которые могут быть интерпретированы станком лазерной резки. Обычно это делает оператор машины на основе стандартной рабочей процедуры.
- Затем лист материала режется по размеру, помещается на станину станка, заготовка закрепляется на станке, следя за тем, чтобы ориентация была прямой (не наклонной).
- Теперь материал разрезается или надрезается лазером. Свет излучается из резонатора; это герметичная стеклянная трубка, состоящая из двух обращенных друг к другу зеркал и заполненная диодно-активируемыми газами. Затем он излучается режущей головкой, где свет от резонатора фокусируется на изогнутой линзе, где он фокусируется в один пучок).
- Из одного листа можно вырезать несколько деталей, и они будут выполняться в одной и той же программе.
Лазерная резка — это универсальный метод производства, который можно использовать для резки различных материалов, включая металлы, пластмассы, дерево, бумагу и текстиль. Когда дело доходит до металлов, сталь режет лучше, чем алюминий и медь. Это связано с тем, что сталь, в отличие от алюминия и меди, отражает свет и тепловую энергию, что в противном случае может привести к деформации. Ниже вы можете найти краткую информацию о наиболее распространенных металлах, используемых для лазерной резки.
Материалы | Характеристики |
---|---|
Алюминий 5052 | + Исключительные отделочные качества (легко анодируется) + Прочность от средней до высокой – Низкая твердость |
Алюминий 5754 | + Прочность выше, чем у 5052 + Коррозионностойкий + Хорошая обрабатываемость |
Медь C110 | + Отличные тепловые и электрические свойства + Высокая пластичность – Высокая теплопроводность |
Нержавеющая сталь 304 | + Отличные механические свойства + Отличная коррозионная и кислотостойкость – Относительно трудно поддается механической обработке |
Нержавеющая сталь 316L | + Отличные механические свойства + Отличная коррозионная и кислотостойкость – Относительно трудно поддается механической обработке |
Мягкая сталь 1018 | + Полумагнитный + Относительно легко обрабатывается – Плохая коррозионная стойкость |
Стоимость лазерной резки
Стоимость лазерной резки может сильно различаться в зависимости от толщины материала, свойств материала и типа лазера.