Легирующие элементы что это: Что такое Легирующие элементы: виды, описание
alexxlab | 28.12.2022 | 0 | Разное
Легирующие элементы и примеси в сталях
1. ЛЕГИРОВАНИЕ СТАЛЕЙ
1.1. Легирующие элементы и примеси в сталях
1.1.1. Основные понятия и определения
Углеродистые стали часто не удовлетворяют повышенным требованиям, которые предъявляются развивающимися отраслями промышленности к материалам. Они имеют недостаточную прочность, вязкость, сопротивление хрупкому разрушению, низкую теплостойкость, прокаливаемость, коррозионную стойкость. Кроме того, углеродистые стали не обладают рядом физико-химических свойств: немагнитностью, жаростойкостью, особыми магнитными, электрическими и тепловыми свойствами и т.д.
Эти недостатки углеродистых сталей можно исправить легированием – введением в сталь легирующих элементов.
Легирующими элементами называют химические элементы, специально введенные в сталь для получения требуемых строения, структуры, физико-химических и механических свойств.
Основными легирующими элементами в сталях являются Мn, Si, Сг, Ni, Мо W, Со, Сu, Тi, V, Zr, Nb, Аl, В. В некоторых сталях легирующими элементами могут быть также Р, S, N, Se, Те, Рb, Се, Lа и др.
Легированные стали – это сплавы на основе железа, в химический состав которых специально введены легирующие элементы, обеспечивающие при определенных способах производства и обработки требуемую структуру и свойства.
Некоторые легирующие элементы (V, Nb, Тi, Zr, В) могут оказывать существенное влияние на структуру и свойства стали при содержании их в сотых долях процента (В – в тысячных долях процента). Такие стали иногда называют микролегированными.
1.1.2. Классификация легирующих элементов
Согласно общепринятой классификации железо и сплавы на его основе относятся к черным металлам, а все остальные металлы и сплавы на их основе – к цветным. Легирующие элементы – металлы можно условно разделить на следующие группы:
металлы железной группы – к ним относятся металлы кобальт, никель, а также близкий к ним по свойствам марганец;
тугоплавкие металлы – к ним относятся металлы, имеющие температуру плавления выше, чем у железа, т. е. выше 1539°С. Из тугоплавких металлов, наиболее часто используемых в качестве легирующих элементов в стали, можно отметить вольфрам, молибден, ниобий, а также ванадий и хром;
легкие металлы – из этой группы легирующих элементов наиболее часто применяют титан и алюминий;
редкоземельные металлы (РЗМ) – к этой группе относятся лантан, церий, неодим, а также близкие к ним по свойствам иттрий и скандий. Редкоземельные металлы часто используют в виде так называемого мишметалла, содержащего 40-45% церия и 45-50% всех других редкоземельных металлов.
В сплавах железо – углерод классификацию легирующих элементов можно проводить по степени сродства легирующих элементов к углероду по сравнению со сродством к нему железа. По этому признаку различают карбидообразующие и некарбидообразующие легирующие элементы. Карбидообразующие легирующие элементы (Тi, Zr, V, Nb, Та, Сr, Мо, W, Мn), а также железо могут образовывать в стали карбиды. Некарбидообразующие элементы (Сu, Ni, Со, Si, Аl) карбидов в стали не образуют. Склонность к карбидообразованию у легирующих элементов тем сильнее, чем менее достроена d-оболочка у металлического атома.
Ранее была принята буквенно-цифровая система обозначения марок сталей и сплавов.
Углеродистые конструкционные качественные стали обозначают двухзначным числом, указывающим среднее содержание углерода в сотых долях процента (например, 05; 08; 10; 15; 20; 25…80; 85).
Для сталей, полностью не раскисленных (при С<0,20 %), в обозначение добавляются индексы: кп – кипящая сталь (£0,07% Si) – 15кп, пс – полуспокойная сталь, например, 20пс (0,05- 0,17% Si). Для спокойных сталей индекс не указывается (0,12-0,30% Si). Углеродистые инструментальные стали обозначают буквой «У» и следующей за ней цифрой, указывающей среднее содержание углерода и десятых долях процента (например, У7; У8; У9; У10; У11; У12; У13).
В легированных сталях основные легирующие элементы обозначаются буквами: А (в середине марки) – N, К – Co, Т – Ti, Б – Nb, В – W, Г – Mn, Д – Cu, Е – Se, М – Mo, Н – Ni, П – P, Р – B, С – Si, Ф – V, Х – Cr, Ц – Zr, Ю – Al, Ч- РЗМ (La, Pr, Ce и др. ).
Цифры после буквы в обозначении марки стали показывают примерное количество того или иного элемента, округленное до целого числа. При среднем содержании легирующего элемента до 1,5 % цифру за буквенным индексом не приводят. Содержание углерода указывается в начале марки в сотых (конструкционные стали) или десятых (инструментальные стали) долях процента.
Так, конструкционная сталь, содержащая 0,42- 0,50% С; 0,5-0,8% Мn; 0,8-1,0% Сr; 1,3-1,8,% Ni; 0,2-0,3%Мо и 0,10-0,18%V, обозначается маркой 45ХН2МФ. Инструментальная сталь (штамповая) состава: 0,32-0,40% С; 0,80-1,20 % Si; 0,15-0,40 % Мn; 4,5- 5,5 % Сr; 1,20-1,50 % Мо и 0,3-0,5 % V обозначается 4Х5МФС.
Если содержание углерода в инструментальных легированных сталях 1 % и более, то цифру в начале марки иногда вообще не ставят (например, X, ХВГ).
Буква «А» в конце марки указывает, что сталь относится к категории высококачественной (ЗОХГСА), если та же буква в середине марки – то сталь легирована азотом (16Г2АФ), а в начале марки буква «А» указывает на то, что сталь автоматная повышенной обрабатываемости (А35Г2). Индекс «АС» в начале марки указывает, что сталь автоматная со свинцом (АС35Г2).
Особовысококачественная сталь обозначается добавлением через дефис в конце марки буквы «Ш» (ЗОХГС-Ш или ЗОХГСА-Ш).
Сталь, не содержащая в конце марки букв «А» или «Ш», относится к категории качественных (ЗОХГС).
В марках быстрорежущих сталей вначале приводят букву «Р», за ней следует цифра, указывающая содержание вольфрама. Во всех быстрорежущих сталях содержится около 4% Сг, поэтому в обозначении марки буквы «X» нет. Ванадий, содержание которого в различных марках колеблется в пределах от 1 до 5 %, указывается в марке, если его среднее содержание 2,0 % и более. Так как содержание углерода в быстрорежущих сталях пропорционально количеству ванадия, то содержание углерода в маркировке стали не указывается. Если в быстрорежущих сталях содержится молибден или кобальт, количество указывается в марке. Например, сталь состава: 0,7-0,8 % С; 3,8-4,4 % Сr; 17,0-18,5 % W; 1,0-1,4 % V обозначается маркой Р18, а сталь: 0,95-1,05% С; 3,8-4,4% Сr; 5,5-6% W; 4,6- 5,2 % Мо; 1,8-2,4 % V и 7,5-8,5 % Со обозначается Р6М5Ф2К8.
Высоколегированные стали сложного состава иногда обозначают упрощенно по порядковому номеру разработки и освоения стали на металлургическом заводе. Перед номером стали ставят индексы «ЭИ» (исследовательская), «ЭП» (пробная) – завод «Электросталь».
Например, упомянутая быстрорежущая сталь Р6М5Ф2К8 упрощенно обозначается ЭП658, а жаропрочная 37Х12Н8Г8МФБ – ЭИ481.
Маркировка марок жаропрочных и жаростойких сплавов на железоникелевой и никелевой основах состоит только из буквенных обозначений элементов, за исключением никеля, после которого указывается цифра, обозначающая его среднее содержание в процентах (ХН77ТЮР, ХН62ВМКЮ и др.).
Примесями называют химические элементы, перешедшие в состав стали в процеесе ее производства как технологические добавки или как составляющие шихтовых материалов.
Примеси в стали по классификации Н.Т. Гудцова подразделяют на постоянные (обыкновенные), случайные и скрытые (вредные).
Постоянными примесями являются элементы, которые вводятся в сталь по технологическим соображениям (технологические добавки).
Постоянными примесями в стали являются марганец и кремний, которые как примеси имеются практически во всех промышленных сталях. Содержание марганца в конструкционных сталях обычно находится в пределах 0,3-0,8 % (если марганец не является легирующим элементом), в инструментальных сталях его содержание несколько меньше (0,15-0,40 %). Введение марганца как технологической добавки в таких количествах необходимо для перевода серы из сульфида железа в сульфид марганца. Кремний в хорошо раскисленных (спокойных) сталях обычно содержится в пределах 0,17-0,37 %. В неполной мере раскисленных низкоуглеродистых (£0,2% С) сталях его содержится меньше: в полуспокойных 0,05-0,017 %, в кипящих <0,07 %. В нержавеющих и жаропрочных, нелегированных кремнием сталях его может содержаться до 0,8 %.
Случайными примесями в стали могут быть практически любые элементы, случайно попавшие в сталь из скрапа, природно-легированной руды или раскислителей. Чаще всего это Сr, Ni, Сu, Мо, W, А1, Т1 и др. в количествах, ограниченных для примесей.
Скрытыми примесями в стали являются сера, фосфор, мышьяк и газы: водород, азот и кислород. Однако в последнее время азот, серу, фосфор иногда используют в качестве легирующих добавок для обеспечения ряда особых свойств сталей.
По марочному химическому составу стали можно определить, какие элементы являются легирующими добавками, а какие – примесями. Если в марочном химическом составе стали устанавливают нижний (не менее) и верхний (не более) пределы содержания в стали данного элемента, то он будет легирующим. Как правило, для примесей устанавливается только верхний предел содержания. Исключение составляют лишь марганец и кремний, количество которых регламентируется нижним и верхним пределом, как для примесей, так и для легирующих добавок.
Содержание примесей в стали обычно ограничивается следующими пределами:
Mn £ 0,8%, Si £ 0,4%, Сr £ 0,3%, Ni £ 0,3%, Сu £ 0,3%, Мо £ 0,1%, W £ 0,2%, P £ 0,025%,
S £ 0,015-0,05%.
Вредные примеси сера, фосфор и газы присутствуют практически во всех сталях и в зависимости от типа стали они могут оказывать на свойства различное влияние.
В настоящее время в металлургии широко используют различные технологические процессы и способы производства стали, в результате которых достигается существенное уменьшение загрязненности металла неметаллическими включениями, и становится возможным регулирование их состава, размера и характера распределения. К таким процессам и способам относятся: рафинирующие переплавы (электрошлаковый, вакуумно-дуговой), вакуумная индукционная плавка, внепечная обработка стали синтетическими шлаками, вакуумирование в ковше и др.
Сера
При комнатной температуре растворимость серы в α-железе практически отсутствует. Поэтому вся сера в стали связана в сульфиды железа и марганца и частично в сульфиды легирующих элементов. С повышением температуры сера растворяется в α- и γ-железе, хотя и незначительно, но до вполне определенных концентраций (0,02 % в α-железе при 913 °С и 0,05 % S в γ-железе при 1365 °С). Поэтому сернистые включения могут видоизменяться при термической обработке стали.
Если сера связана в сульфид железа FeS, то при относительно низких температурах горячей деформации стали вследствие расплавления эвтектики сульфида железа (896 °С), с температурой плавления 988 °С, наблюдается красноломкость стали. При более высоких температурах горячей пластической деформации возможна горячеломкость стали, обусловленная расплавлением находящегося по границам первичных зерен аустенита, собственно сульфида железа (1188°С). Введение в сталь марганца в отношении Mn: S>8-10 приводит практически к полному связыванию серы в тугоплавкий сульфид марганца MnS (Тпл=1620 °С) и исключает образование легкоплавкой сульфидной эвтектики. Это позволяет избежать красноломкости и горячеломкости сталей при их горячей обработке давлением.
Увеличение содержания серы в стали мало влияет на прочностные свойства, но существенно изменяет вязкость стали и ее анизотропию в направлениях поперек и вдоль прокатки. Особенно сильно анизотропия выражена при высоких содержаниях серы.
В жаропрочных аустенитных сталях повышение содержания серы заметно уменьшает пределы ползучести и длительной прочности, т. е. сера снижает жаропрочные свойства.
Фосфор
Растворимость фосфора в α- и γ-железе значительно выше, чем содержание фосфора в стали как примеси. Поэтому фосфор в стали целиком находится в твердом растворе, и его влияние на свойства сказывается через изменения свойств феррита и аустенита. Вредное действие фосфора на свойства может усугубляться из-за сильной склонности его к ликвации (степень ликвации достигает 2-3).
Действие фосфора на свойства феррита проявляется в его упрочняющем влиянии и особенно в усилении хладноломкости стали, т.е. повышении температуры перехода из вязкого в хрупкое состояние.
Фосфор относится к сильным упрочнителям. Несмотря на то, что содержание его в стали обычно не превышает 0,030-0,040 %, он увеличивает предел текучести феррита на 20…30 МПа. В то же время увеличение содержания фосфора в пределах сотых долей процента может вызывать повышение порога хладноломкости на несколько десятков градусов (~20-25°С на 0,01 % Р) благодаря сильному уменьшению работы распространения трещины (рис. 1).
Рекомендуем посмотреть лекцию “Психопрофилактика”.
Рисунок 1 – Влияние фосфора на σв и σт и ударную вязкость KCU низкоуглеродистой феррито-перлитной стали (0,2 % С, 1 % Мn).
В конструкционных улучшаемых сталях содержание фосфора оказывает основное влияние на явление обратимой отпускной хрупкости. В этом случае влияние его на порог хладноломкости особенно сильно (0,010 % Р повышает температуру перехода на ~ 40 °С).
В сталях, выплавленных на базе керченских руд, содержится мышьяк. Его влияние на свойства стали аналогично фосфору, но вредное действие мышьяка значительно слабее, чем фосфора. Поэтому в качественной стали такого производства допускается до 0,08 % As.
Газы в стали
В сталях в определенных количествах обычно присутствуют водород, кислород, азот. Содержание их в сталях зависит прежде всего от способа выплавки. Водород может входить в состав твердого раствора стали и выделяться в газообразном состоянии, скапливаясь в порах металла, при этом в стали образуются флокены. Кислород обычно связан в неметаллические включения. Азот отрицательно влияет на свойства стали, если он находится в твердом растворе или образует нитриды железа, вызывая старение стали. Положительное влияние азота на свойства стали проявляется при связывании его в прочные нитриды A1N, VN, NbN или карбонириды V(C, N), Nb(C, N) и др., что используется в сталях с карбонитридным упрочнением. Кроме того, азот широко применяется в качестве аустенитообразующего элемента в коррозионностойких и жаропрочных сталях.
В заключение необходимо отметить, что борьбу с вредными примесями в стали в основном проводят при выплавке стали. Уменьшение содержания вредных примесей в стали требует немалых затрат для осуществления определенных технологических приемов и применения специальных методов выплавки.
Легирующие элементы в стали. Наиболее известные добавки.
|
|
|
Легирующие элементы | Как они влияют на свойства материала
Различают легирующие элементы, образуют ли они карбид, аустенит или феррит в стали и какой эффект достигается за счет добавления. Сила воздействия также может быть разной.
Примеры
Это становится очевидным, например, с легирующими элементами вольфрамом и кремнием и их влиянием на сталь:
Группа 5 CopyCreated with Sketch. Вольфрам
- Сильное улучшение износостойкости
- Не влияет на эластичность
Группа 5 CopyCreated with Sketch. Кремний
- Сильное снижение износостойкости
- Сильное увеличение эластичности
Этот пример впечатляющим образом показывает, насколько сложным может быть влияние легирующих элементов. Увеличение одного свойства может привести к уменьшению другого свойства.
В процессе производства стали добавляются элементы для улучшения свойств стали для ее последующего использования. Таким образом, существуют износостойкие, солеустойчивые и кислотостойкие стали, а также марки стали, способные противостоять ядерному излучению. Все зависит от различных элементов, добавленных в сплав.
Добавление легирующих элементов создает только предварительное условие для изменения свойства. Только дальнейшие этапы обработки, такие как термическая обработка, приводят к желаемым изменениям в структуре стали и, следовательно, к желаемому результату.
Наиболее важными легирующими элементами, помимо углерода, являются:
Твердая медь
Минерал вольфрама Шеелит
Минерал кобальта Эттрингит
См.
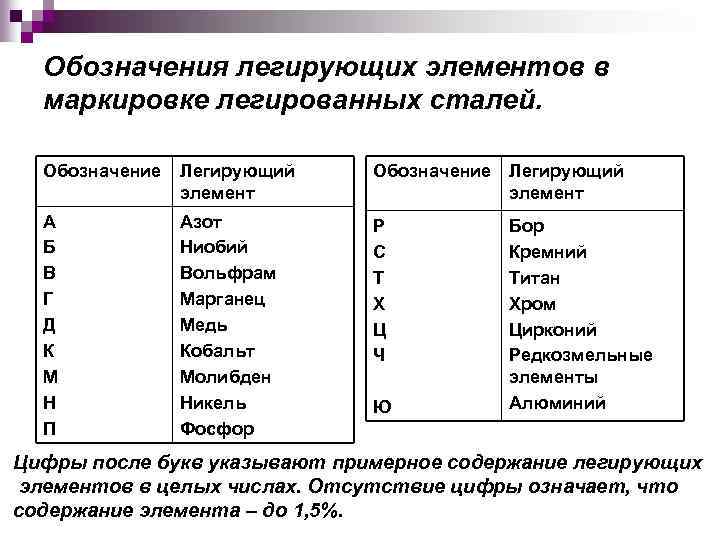
Сопутствующие элементы
Сталь состоит не только из железа и углерода. Другие элементы могут влиять на свойства стали.
Подробнее
Бокситы
Здесь вы можете узнать, почему алюминий был открыт так поздно и как его можно производить.
Подробнее
Углерод
Концентрация углерода влияет на твердость сталей. Таким образом, для каждого применения можно найти подходящую сталь.
Подробнее
Характеристики легирующих элементов
Присоединяйтесь к нам, поскольку наша техническая группа описывает основные элементы, используемые при пайке присадочных металлов, а также наиболее важные характеристики каждого элемента. Чем больше вы понимаете об этих элементах, тем лучше вы подготовлены к выбору и использованию правильных продуктов для вашей операции пайки.
Ниже приведены наиболее часто используемые легирующие металлы с их основными характеристиками:
Серебро (Ag) – температура плавления 1761°F/961°C
• Благородный металл
• Отличная электрическая и теплопроводность
• Отличное проникновение в швы
• Пластичность металл
Медь (Cu) – температура плавления 1981°F/1083°C
• Более низкая стоимость, чем Ag
• Отличная электро- и теплопроводность
• Отличное проникновение в швы
• Ковкий металл
• Сплавы/смачиваемость Fe
Медь образует сплавы с железом, кобальтом и никелем гораздо легче, чем серебро. Кроме того, медь удовлетворительно смачивает многие из этих металлов и их сплавов, а серебро — нет. Отсюда следует, что смачиваемость серебряно-медных присадочных металлов – по отношению к стали, нержавеющей стали, никель-хромовым сплавам – снижается по мере увеличения содержания серебра.
Цинк (Zn) – температура плавления 787°F/419°C
• Снижает температуру плавления сплавов меди и серебра
• Улучшает смачивание
• Высокое давление паров
• Хрупкий металл
Из элементов, обычно используемых для снижения температуры плавления и текучести медно-серебряных присадочных металлов, цинк является наиболее полезным смачивающим агентом при соединении сплавов, состоящих из железа, кобальта или никеля.
Кадмий (Cd) – температура плавления 610°F/321°C
• Понижает температуру плавления
• Улучшает смачивание
• Высокое давление паров
• Лучшая коррозионная стойкость, чем Zn
• Канцерогенный – вызывает рак
Примечание. Пары кадмия токсичны, поэтому эти материалы следует использовать только в хорошо проветриваемых помещениях.
Фосфор (P) – температура плавления 111°F/44°C
• Химически активен (предохраняет Cu от оксида)
• Понижает температуру плавления
• Хрупкий элемент
Этот присадочный металл широко используется для обработки меди и меди сплавов, а иногда и на молибденовых и высокомолибденовых сплавах. Мы не рекомендуем его для стали или никеля, так как образуются хрупкие фосфиды. Вы можете использовать Sil-Fos без флюса на меди даже без контролируемой атмосферы. Часть фосфора окисляет и восстанавливает оксиды меди, а образующийся P2O5 действует как флюс для растворения оксида меди, поэтому присадочный металл является самофлюсующимся.
Никель (Ni) – температура плавления 2651°F/1455°C
• Добавляет прочность и ударную вязкость сплавам серебра
• Улучшает смачивание
• Повышенная коррозионная стойкость
Никель, марганец и (нечасто) кобальт служат твердые припои для соединения стеллитов, цементированных карбидов и других тугоплавких сплавов с высоким содержанием молибдена или вольфрама. Мы особенно рекомендуем присадочные металлы, содержащие небольшое количество никеля, когда соединения из нержавеющей стали будут подвергаться коррозии в соленой воде.
Примечание: При пайке нержавеющих сталей и других сплавов, образующих тугоплавкие оксиды в восстановительной или инертной атмосфере без флюса, серебряные припои, содержащие литий в качестве смачивающего агента, весьма эффективны.
Марганец (Mn) – температура плавления 2273°F/1245°C
• Улучшает смачивание и сцепление с никель-хромовыми сплавами и карбидами
• Высокая прочность при повышенных температурах
Олово (Sn) – температура плавления 440°F/ 227°C
• Снижает температуру плавления
• Повышает текучесть
• Хорошее смачивание и проникновение в швы
• Повышает хрупкость
Используйте индий или олово в серебряных припоях вместо цинка или кадмия для атмосферных или вакуумных печей или когда вы впоследствии будете использовать сборки в высоком вакууме при промежуточные температуры. Добавление индия или олова оказывает практически такое же влияние на характеристики пайки припоев, хотя припои с индием обладают большей пластичностью. Обратите внимание, что присадочные металлы, содержащие цинк, смачивают черные металлы более эффективно, чем присадочные металлы, содержащие олово; там, где цинк допустим, предпочтительнее олово.
Пластичность присадочных металлов в зависимости от низких температур текучести
При увеличении общего содержания цинка и кадмия более чем на 40% пластичность снижается.