Литье по газифицированным моделям: Литье по газифицируемым моделям (ЛГМ)
alexxlab | 21.03.1993 | 0 | Разное
Литье по газифицируемым моделям в Свердловске
Впервые о литье по газифицируемым моделям (ЛГМ) узнали в 1958 году, когда потребовалось быстро и экономично изготовить художественные отливки. Результатом нового запатентованного метода стала150-килограммовая бронзовая скульптура Пегаса. В дальнейшем таким же способом произвели отливку мачты для колокола, украшенную художественным орнаментом и весящую 3,5 т, и другие предметы из алюминиевого сплава.
Сегодня ЛГМ — одна из наиболее перспективных технологий. От литья по выплавляемым моделям она отличается тем, что удаляется из формы в процессе заливки, а не до него. Поступающий металл вытесняет своим объемом модель, которая постепенно «испаряется», и в результате занимает все пространство формы.
На изготовление моделей идет полистирол разных марок, представленный в виде гранул, плит или блоков. Когда расплавленный металл начинает поступать в литейную форму с пенополистироловой моделью, она преобразуется в газ и уступает ему место. Поэтому модели и называются газифицированными.
ЛГМ используют в массовом и серийном производстве. Процесс литья происходит в следующем порядке. Сначала в поддон помещают гранулированный полистирол и, чтобы он набух, нагревают его до 80°С. Гранулы увеличиваются до 1-15 мм. Их сортируют, задувают в пресс-формы из алюминия, затем помещают в автоклав, где выдерживают при температуре, превышающей 100°С, и под давление 0,2 МПа. В таких условиях полистирол вспенивается и приобретает контуры пресс-формы. Готовую модель детали с элементами литниковой системы извлекают, сушат, затем собирают и склеивают в блоки, сверху покрывают огнеупорным составом, который состоит из кварцевого песка и этилсиликата. Перед формовкой наносят слой противопригарной краски толщиной 0,2 мм и помещают в двустенные опоки, во внутренних стенках которых есть отверстия для выхода газа.
Полистироловые блоки или плиты обычно используют для моделей, идущих на изготовление крупных отливок. Их сваривают или склеивают, а вместо формовочной обмазки могут применять чугунную дробь или ферромагнитный порошок. Благодаря этому происходит дополнительное уплотнение электромагнитным полем, а сам состав остается на месте во время заливки металла.
Производство литниковой системы для крупных форм происходит из смеси полистирола и керамических трубок. Металл подводится сифонным способом, обеспечивая постепенное поступление расплава по направлению снизу вверх и газификацию модели. Скорость подъема металла зависит от материала и поперечного сечения и укладывается в следующие рамки: для чугуна — 3-5 см/с, для стали — 5-7 см/с.
Преимущества
- даже сложные модели получаются без разъемов;
- отсутствуют стержни;
- нет необходимости в извлечении модели;
- не требуется связующее при использовании огнеупорного материала.
Для разовых моделей из пенополистирола применяют другие способы. Для крупносерийного производства используют подвспененные гранулы суспензионного полистирола, для единичного изготовления — механическую обработку плит.
Сложные модели изготавливают по частям, затем соединяют сваркой или склеиванием в литниковую систему, покрывают огнеупорной краской и просушивают на открытом воздухе. В результате пенополистирольная модель заключается в газонепроницаемую огнеупорную оболочку. Контейнер, в который подают опорный материал, закрывают полиэтиленовой пленкой и, чтобы форма не разрушилась, устанавливают разрежение 0,04-0,05 МПа. Жидкий металл заливают в форму, и при температуре 560°С пенополистирол газифицируется и покидает ее. Для крупных отливок применяют холоднотвердеющие смеси, сыпучие или жидкоподвижные.
Как только отливка охладится и станет твердой, опоку переворачивают. Наполнитель отделяется, а готовая отливка отправляется на обработку. Если используют обычные формовочные смеси, то применяют выбивные решетки.
О применении неразъемной формы
Главное достоинство способа заключается в качестве готовых отливок. Количество частей формы и стержней сокращается, вследствие этого отливки становятся более точными по размерам, без искажения конфигурации. Точность отливок ЛГМ регламентируется ГОСТ 26645-85 (с изменениями № 1, 1989) и полностью соответствует точности аналогов, полученных в кокиле.
Достоинства метода
- обработка пенопласта легче, чем древесины;
- пенопласт не деформируется при обработке и подходит для создания сложных форм;
- на производстве не требуется высшая квалификация персонала;
- процесс упрощается благодаря отсутствию этапа извлечения модели;
- трудоемкость уменьшается в несколько раз;
- исключено повреждение формы, не нужна доработка.
Этот метод используют для отливки форм из чугуна, стали, латуни, бронзы. Отливки, даже самые сложные по конфигурации, получаются очень точными — 7-12 класс по регламенту ГОСТ 26645-85. Благодаря частичному вакуумированию они становятся плотными, с высоким качеством поверхности (RZ 40-80). Механическая обработка после литья или не требуется совсем, или необходима в минимальном количестве, и тогда сохраняются минимальные припуски. В результате серийного производства отливки получаются идентичными.
Особенности применения пенополистирола
Изготавливают газифицируемые модели из вспенивающегося полистирола, имеющего синтетическое происхождение. Его получают путем суспензионной полимеризации стирола в сочетании со стабилизатором, эмульгатором и парообразователем, в качестве которого применяют изопетан. Гранулы вспенивающегося полистирола — это белые или прозрачные шарики величиной 3,2 мм. Под твердой оболочкой каждого элемента находится жидкий изопетан.
Процесс вспенивания происходит следующим образом. Когда температура нагрева достигает 27,9°С, начинается кипение изопетана и переход его в газообразную фазу. При дальнейшем повышении температуры до 80-90°С оболочка становится мягкой и деформируется, а сами гранулы увеличиваются в 10-40 раз. В замкнутом пространстве они спекаются и образуют монолитную массу, повторяющую конфигурацию формы, в которую они помещены.
В мелкосерийном производстве или для изготовления единичных моделей гранулы сразу засыпают в пресс-форму, которую устанавливают в автоклав и нагревают 10-12 минут. Гранулы разбухают, вспениваются и образуют единую массу, по конфигурации повторяющую очертания формы. Форму помещают в проточную воду, охлаждают, модель извлекают. К ней с помощью клея БФ-4, декстринового или столярного клея присоединяют пенополистироловую литниковую систему. Так создают сложные и крупные модели. Их также можно склеивать из отдельных деталей, заранее вырезанных из блоков или листов пенополистирола нагретой до 300°С нихромовой проволокой.
Свойства пенополистирола, используемого для отливок
- плотность 20-30 кг/м³ и прочность 0,1-0,2 МПа для сохранения конфигурации при производстве, хранении, перевозке и формовке;
- высокая скорость газификации, способствующая быстрой заливке металла в форму;
- стабильная минимальная усадка 0,15-0,2% на всех этапах производственного процесса;
- разложение с небольшим содержанием коксообразующих элементов в процессе газификации для предотвращения засоров.
К особенностям ЛГМ относят использование моделей без формовочных уклонов и стержневых знаков, с минимизированными припусками на финишную обработку. Процесс формовки заметно упрощается: сначала в опоку насыпают слой формовочной смеси, затем помещают модель с литниковой системой, сверху снова засыпают формовочной смесью. Процесс уплотнения при этом производится или при помощи вибрационного стола, или вручную. Предпочтение все больше отдают способу формовки с использованием жидких самотвердеющих составов.
ЛГМ сегодня и в перспективе
Технология ЛГМ признана эффективной и экономичной, поэтому становится все более востребованной на отечественных предприятиях. Благодаря ей появилась возможность выпуска заготовок из разнообразных сортов металла и сплавов, включая драгоценные. В серийном производстве можно изготавливать огромное количество высококачественных деталей, не требующих дальнейшей финишной обработки.
Целесообразно применять ЛГМ в 2-х случаях:
- Для производства отливок среднего и крупного размера при изготовлении небольших серий или опытных образцов.
- Для производства более сложных отливок, если используются цветные и черные сплавы не тяжелее 50 кг — например, отливок «блок цилиндров» для двигателей автомобилей.
При серийном изготовлении важна высокая точность размеров.
При использовании технологии ЛГМ значительно уменьшаются расходы на производство и ускоряется процесс заливки, особенно при объединении нескольких форм в одну модель. В дальнейшем не требуется трудоемкая механическая доработка. Ресурс алюминиевых форм увеличен за счет того, что вспененный полистирол не оказывает агрессивного действия. Значительно экономятся расходные материалы — предположим, кварцевый песок можно использовать многократно.
Отработанный газ полностью сжигается, поэтому производство признано экологически чистым. Из-за отсутствия вредных выбросов условия труда для сотрудников гораздо лучше, чем для их коллег из цехов с традиционным литейным производством. Благодаря перечисленным преимуществам технология ЛГМ становится все более популярной и на крупных металлургических предприятиях, и в мастерских, занимающихся художественным литьем.
Литье по газифицируемым моделям, услуги «Камский Металлург» Москва
Виталий Камоцкий
Специалист отдела продаж
8 8552 25 30 68 доб. 317
Ахметзянова Лилия
Специалист отдела продаж
8 8552 25 30 68 доб. 304
Все контакты
Главная страница
Литье по газифицируемым моделям
Почему это выгодно
Для изготовления моделей используется литейный полистирол мелких фракций01
Полистирол предварительно подвспенивается на паровой ванне и просушивается02
Алюминиевая пресс-форма03
В пресс-формы задувается подвспененный полистирол04
Затем достают готовые модели05
Модели собираются в блоки (кусты) путем склеивания.
40-60 С в течение 2-3 часов.
06
Окраска блоков моделей производится в 1 слой специальным противопригарным покрытием путём окунания в ванну. Сушка окрашенных блоков производится в камере при температуре 40-60 С в течение 2-3 часов.07
Заформованные опоки подаются на заливочный участок. Опоки подсоединяются к вакуумной системе. Наверх формы укладывается полиэтиленовая пленка. После включения вакуумного насоса и системы очистки газов, формовочный песок приобретает необходимую прочность.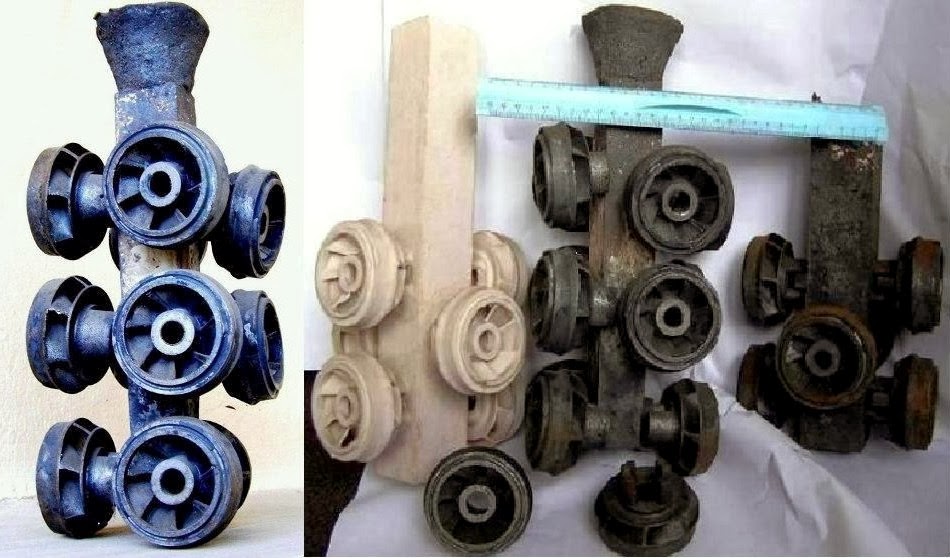
09
Залитые блоки моделей остывают в песке от 5 минут до нескольких часов в зависимости от толщины отливки, массы детали и технических условий, оговоренных технологическим процессом. 10После извлечения блоков из опоки и отрезки отливок от литниковой системы, они проходят очистку от остатков антипригарного покрытия.11
Смотреть всё
Вы оставляете заявку на сайте. Вот тут
Вас консультирует наш специалист-технолог
и составляет техническое задание на изготовление
изделия
Мы формируем цену, согласуем её, составляем
и заключаем договор
Согласуем чертежи и проектируем оснастку
Изготавливаем пробную партию и доставляем
по указанному в заявке адресу
Заказать консультацию
Ситдиков РусланИльдусович Главный технолог Импорт
смт :.
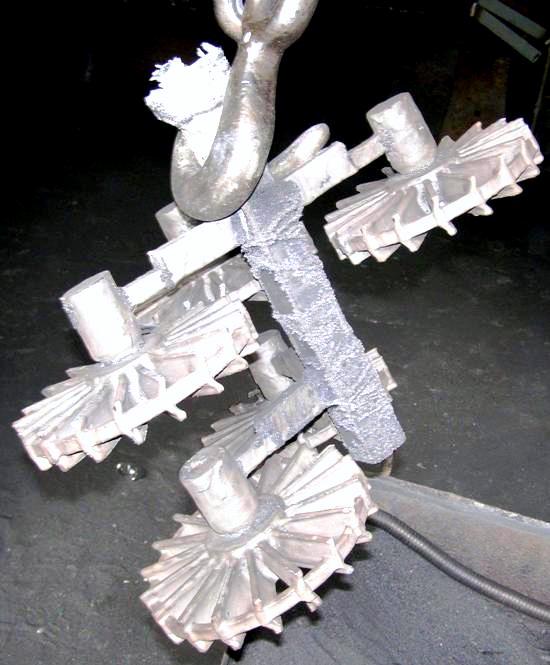
Распространенные дефекты литья
Дефект | Описание | Изображение |
ПОРИСТОСТЬ – ГАЗОВЫЕ ОТВЕРСТИЯ | Пустоты, вызванные захваченным газом, растворенным в расплавленном металле, или воздухом и влагой в самой литейной форме. Газовые отверстия имеют круглую или каплевидную форму. | |
ПОРИСТОСТЬ – УСАДКА | Пустоты, возникающие в результате замерзания металла и блокирующие поступление металла в последние участки отливки перед затвердеванием. Причиной обычно является недостаточный рост. Усадка также может происходить из-за проблем с направленным затвердеванием, потенциально из-за геометрической формы и расположения входных литников и подаваемого металла. | |
ПОРИСТОСТЬ – ИНОСТРАННЫЙ МАТЕРИАЛ | Форма пор обычно неправильная. Причиной является песок или керамика, которые откололись от формы. Это также могут быть примеси в расплаве, известные как окалина или шлак. | |
ХОЛОДНОЕ ЗАКРЫТИЕ | Это происходит, когда металл, поступающий в форму с разных направлений, не сплавляется должным образом. Обычно это выглядит как трещина в отливке. Холодный металл приводит к отсутствию текучести. | |
MISRUN / КОРОТКАЯ ЗАЛИВКА | Когда расплавленный металл не полностью заполняет литейную форму, возникают пропуски хода. Причиной может быть сломанная форма (кончилась) или недостаточное количество металла в процессе заливки или недостаточная текучесть металла. | |
СМЕНЫ – ФОРМЫ ИЛИ СЕРДЕЧНИКА | Это распространенный дефект при литье в песчаные формы, который можно исправить с помощью установочных штифтов. | |
ТЕПЛОВЫЕ ПРОВЕРКИ / ГОРЯЧИЙ РАЗРЫВ | Положительный металл на поверхности отливки из-за трещин в формах. Тепловая проверка — это термин литья под давлением, возникающий в результате трещин в стальных штампах из-за термоциклирования. Hot Tear — это термин, используемый при литье в песчаные формы для описания шероховатых линий позитивного металла на поверхности. Оба являются косметическими и легко удаляются. | |
ШЕРОХОВАЯ ПОВЕРХНОСТЬ | Обычно вызывается слабым формовочным песком, который вымывается во время заливки. Песок также может отколоться от формы и прилипнуть к рисунку из-за чрезмерной влажности или шероховатости узора. | |
ЧРЕЗМЕРНОЕ ВСПЫШИВАНИЕ | Состояние возникает, когда две половины литейной формы расходятся, позволяя расплавленному металлу вытекать. |
5 типов дефектов литья в песчаные формы и способы их предотвращения для улучшения качества литья
Здесь мы представляем 5 основных типов дефектов литья в песчаные формы, часто встречающихся в металлообработке. Вы найдете причину каждого дефекта литья, а также меры, которые можно предотвратить для улучшения качества литья.
Литье в песчаные формы – это популярный процесс литья в литейном производстве , при котором отливки создаются путем формирования полости формы в контейнере для песка, заливки расплавленного металла и разрушения песочницы для сбора отливки.
Этот традиционный и популярный метод литья выгоден из-за возможности отливки больших объемов, высокой детализации и низкой стоимости литья.
Подобно другим процессам литья (отливка не идеальна, даже самый инновационный метод), литье в песчаные формы сохраняет несовершенство.
Участие в многосложном процессе литья в песчаные формы вызывает некоторые опасения по поводу различных типов дефектов, которые снижают качество продукции.
Дефекты литья металла – это несовершенные состояния литья по сравнению с требованием, которые должны быть исправлены, устранены или отклонены. Некоторые дефекты литья в песчаные формы небольшие, что может быть приемлемым допуском, некоторые можно легко отремонтировать и обработать. Некоторые суровые, у которых нет другого выхода, кроме как отказаться и начать новую партию литья.
Ключом к предотвращению и минимизации дефектов металлического литья, а также установлению ожиданий и допусков является знание того, откуда берутся неровности, и поиск решений для их предотвращения.
Удовлетворив эти потребности, здесь мы перечисляем 5 основных групп наиболее популярных дефектов литья в песчаные формы , наблюдаемых в металлообработке, и устраняем причины дефектов литья, а также предлагаем меры по улучшению качества литья и поставке лучших литых деталей вашим клиентам.
Добавьте заголовок, чтобы начать создание оглавления
Усадочные дефекты литья
Металлические сплавы усаживаются по мере затвердевания в полости литейной формы на этапе заливки. Это нормальное явление при литье, потому что расплавленный металл менее плотный, чем твердый.
В литейном производстве усадка требует точного расчета модели и конструкции формовки.
Дефект усадки является одним из наиболее серьезных дефектов литья в песчаные формы, снижающим качество литья. Здесь возникают усадочные дефекты отливок, так как процесс усадки происходит неравномерно, что приводит к образованию усадочных раковин в деталях отливки. Два типа усадочных дефектов литья — это закрытые усадочные дефекты и открытые усадочные дефекты.
Открытые усадочные дефекты можно обнаружить на поверхности отливки на глаз, а закрытые усадочные дефекты (усадочная пористость) находятся внутри отливки.
Открытые усадочные дефекты
Открытые усадочные дефекты образуются, когда происходит явление неравномерной усадки и вовлекает воздух внутрь формы. Они делятся на два типа: труба и поверхность с выемками на поверхности отливки, которую можно наблюдать невооруженным глазом.
Открытые дефекты усадки при литье в песчаные формы снижают эстетический вид поверхности, вызывают появление трещин и ослабляют прочность литья.
Закрыть дефекты усадки
Близкие усадочные дефекты, также известные как усадочная пористость, представляют собой полости (отверстия), обнаруженные в отливке, которые образуются там, где часть расплавленного металла горячее, чем другая жидкость материала. Они бывают с микропористой фазой или макропористой фазой , которые могут ослабить отливку, а также ухудшить коррозионно-стойкие свойства.
Макроусадочная пористость представляет собой большую полость с шероховатой и губчатой поверхностью, тогда как микроусадочная пористость выглядит как зубчатые метки или линии. Макроусадочную пористость можно увидеть невооруженным глазом, а микроусадочные дефекты обнаруживаются под микроскопом.
Что вызывает дефекты усадки при литье в песчаные формы?
Усадочные дефекты возникают в основном из-за неравномерного или неконтролируемого затвердевания расплавленной жидкости.
Возникает в основном из-за неправильной заливки конструкций и технических работ, таких как:
- Неисправность литниковой системы и стояка (питателя)
- Слишком высокая температура заливки
- Из-за высокого давления стенки формы
- Охладители размещены неправильно
- Внезапное изменение толщины срезов
Как лечить дефекты усадки отливок?
Явление усадки отливки неизбежно, однако мы можем уменьшить дефекты этого металлического литья за счет геометрических и технологических модификаций.
Ниже перечислены факторы, которые можно использовать для повышения качества конечного литья:
- Разработайте соответствующую литниковую систему для обеспечения непрерывного потока расплавленного металла
Конструкция литниковой системы должна обеспечивать критерии (1) Контролировать скорость потока металла, не подвергаться ударам, не закручиваться, не разбрызгиваться, должна быть плавной и постоянной; (2) быстро заполняет полость формы без потери разбавления металла; (3) Контроль температуры в полости формы для стабильного охлаждения металла.
- Разработайте надлежащую систему подачи (также известную как стояк), чтобы компенсировать усадку при затвердевании и свести к минимуму образование усадочной полости
Подъемник представляет собой полость для хранения расплавленного металла, используемую для подачи жидкого расплава в полость литейной формы для компенсации усадки при затвердевании металла.
Два критерия проектирования стояка включают:
(1): должен содержать достаточный объем расплавленной жидкости, чтобы компенсировать усадку при затвердевании.
(2): должен находиться в позиции окончательного затвердевания отливки, затвердевает позже, чем отливка, и дольше всего находится в жидком состоянии
Объем стояка рассчитывается по следующей формуле:
V F ≈ αV C
, в котором:
V F – это громкий объем
α – объем усадка
V C α – это объем V C . Охладитель, охлаждающие ребра или охлаждающий змеевик используются для улучшения процесса затвердевания в литейной части формы. Это должно быть место, где тепло имеет тенденцию накапливаться, например, кирка и тяжелые секции. Газовая пористость — еще один распространенный дефект литья в песчаные формы, чаще всего встречающийся в процессе литья металлов. Газовая пористость — это пузырьки, образующиеся внутри отливки после этапа охлаждения. Проблемы литья с газовой пористостью связаны с тремя типами пузырьков: точечными отверстиями, газовыми отверстиями и открытыми отверстиями. Эти проблемы с литьем возникают из-за того, что некоторое количество газа (азот, кислород или водород) содержится в жидком металле, но не содержится в твердом металле. Эти пузырьки присутствуют в виде пор или пор на поверхности или внутри отливки. Поры могут варьироваться от 0,01 до 0,05 мм для нескольких кг отливки, тогда как поры отливки большего веса могут иметь диаметр 0,04 мм. Проколы, также называемые пористостью, представляют собой крошечных пузырьков, в основном собранных на верхней поверхности отливок. Обычно он имеет размер около 2 мм и может быть обнаружен невооруженным глазом без профессионального контрольного оборудования. Газовая пористость
Следовательно, когда жидкость охлаждается, это количество растворенного газа образует пузырьки, которые снижают прочность, пластичность и эстетику отливок.
Отверстия
Дыхательное отверстие
Дыхания, также известные как удары, представляют собой более крупные полости, чем точечные отверстия, которые обычно появляются внутри литых деталей. Он невидим невооруженным глазом.
Для определения качества внутренней отливки применяется рентгеновский, гармонический, ультразвуковой или магнитный анализ для сканирования дыр. Отверстия также могут быть обнаружены на этапах механической обработки.
Открытое отверстие
Открытое отверстие похоже на большие полости типа дыхала, но появляется на видимой невооруженным глазом поверхности деталей литья.
Что вызывает газовую пористость при литье в песчаные формы?
Чрезмерное поглощение газа в основном происходит из-за чрезмерной влажности и плохой настройки вентиляции. В частности, причины могут быть перечислены следующим образом:
- Слишком высокая влажность в песчаной формовочной смеси
- Инструменты для транспортировки расплавленного металла (ковши) влажные
- Газифицированный песок недостаточен
- По сравнению с высокой температурой расплавленного металла
- .
- Песчаная форма перегружена
- Турбулентность металла во время заливки
Как лечить дефекты газовой пористости?
Надлежащая практика литейного производства может свести к минимуму газовую пористость и обеспечить качество отливки. С помощью следующих действий можно уменьшить количество газа, захваченного в металле, и избежать образования полостей:
- Контролируйте достаточное содержание влаги в песчаной форме и следите за тем, чтобы формовочная смесь была сухой и проницаемой.
Обратите внимание, что слишком мелкий песок может ослабить газопроницаемость песчаной формы. Рекомендуется использовать более крупный песок для лучшей газопроницаемости.
Кроме того, не утрамбовывайте чрезмерно песчаную форму, так как это также может снизить проницаемость песчаной формы. Создайте больше вентиляционных отверстий в песчаной форме с помощью вентиляционных стержней для лучшей проницаемости. Кроме того, форму необходимо высушить стандартным способом сушки.
- Формы и стержни должны быть высушены и храниться в стандартных условиях сушки.
- Обеспечьте достаточное количество вентиляционных отверстий для песчаных форм и стержней, чтобы газы могли выходить.
- Используйте нержавейку, чистые охлаждающие и сухие инструменты
- Применяйте правильно процессы плавки и заливки
среде малорастворимых газов или под флюсом, исключающим контакт воздуха с расплавленным металлом. Кроме того, заливка расплавленной жидкости при более низкой температуре для увеличения скорости затвердевания и уменьшения поглощения газа.
Кроме того, турбулентность при заливке металла может привести к попаданию газов, поэтому требуется надлежащая конструкция литниковой системы для предотвращения турбулентности металла во время заливки.
Дефекты заливки металла
Дефекты заливки металла образуются в результате неправильного процесса заливки расплава в полость формы.
Эта категория проблем литья делится на четыре типа: холодное запирание, пропуски и шлаковые включения.
Холодное запирание в отливке
Холодные затворы в отливке — это линии или трещины, образованные в средней части поверхности отливки на шероховатой кромке, образующие слабое место. Холодные затворы видны невооруженным глазом, а отливки часто бракуются, если в них есть дефекты холодных затворов.
Эти дефекты литья в песчаные формы ослабляют прочность литья, что может привести к его разрушению.
Эти дефекты литья в песчаные формы возникают, когда расплавленный металл заливается в полость формы из двух точек заливки, но два потока расплавленной жидкости не сливаются должным образом.
Что вызывает дефекты холодного закрытия?
Дефекты холодного закрытия возникают из-за:
- Недостаточная текучесть расплавленного металла
- Неправильная конструкция литниковой системы
Как лечить дефекты холодного закрытия?
Основной причиной, вызывающей дефект холодного литья, является недостаточная текучесть расплавленного металла. Вот решения для повышения текучести металлической жидкости:
- Правильно спроектируйте литниковую систему
- Ограничьте процесс преждевременного затвердевания за счет повышения температуры заливки
- Используйте более крупный песок для улучшения проницаемости песчаной формы
Ошибки
Пропуски – это дефекты литья, при которых полость литейной формы не полностью заполнена расплавленным металлом, что приводит к незаполненным частям или отсутствующим частям.
Это происходит из-за того, что металлическая жидкость замерзает до того, как заполнит всю полость формы.
Что вызывает пропуск дефектов?
Причина, приводящая к пропуску литья, дефекты литья аналогичны холодному замыканию, т.е. недостатку текучести расплавленного металла.
Как лечить дефекты пропусков?
Подобно средствам защиты от холодного закрытия, если ваша отливка сталкивается с явлением неправильного хода, проверьте
- Конструкция литника
- Конструкция формовки из песка
- Температура заливки
Включение шлака
Шлаковые включения представляют собой темно-серые скопления или единичные распределения на поверхности или внутри отливки.
Обычно обнаруживается в процессах пескоструйной обработки и механической обработки.
Что вызывает шлаковые включения?
Причины образования дефектов шлаковых включений в том числе:
- Сырье и сырье для плавки содержат примеси (оксиды, нитриды, карбиды, сульфиды и т.
д.)
- Неправильная конструкция системы разливки приводит к затягиванию шлаков в полость формы в процессе плавильная печь, разливочный стакан.
- Загрязнения , содержащие песчаную форму
- Шлак не удаляется и не очищается после этапа рафинирования, плюс жидкость сплава чрезмерно перемешивается при высокой температуре, вызывая повторное окисление
Как обрабатывать шлаковые включения?
Существует несколько способов минимизировать концентрацию шлаковых включений. Чтобы предотвратить образование шлаковых включений в отливке, вы можете проверить следующие средства:
- Контроль подачи сырья и плавки
Предлагается поместить сырье в анализатор состава SpetroMax для проверки качества поступающего материала . Кроме того, очищайте и удаляйте примеси из плавильного материала и храните их надлежащим образом.
- Квалифицировать процесс плавки металла для обеспечения получения чистой жидкости сплава
Для предотвращения образования оксидов в металле рекомендуется плавить металл в вакууме, флюсе, инертной атмосфере.
Если вы плавите металл в обычной печи, убедитесь, что она хорошо контролирует входной материал, добавки и температуру плавления. Удалите все шлаковые образования в печи во время плавки.
- Оптимизация системы заливки
Установка фильтрующего слоя, скимминга, элементов сбора шлака в конструкцию системы заливки, чтобы свести к минимуму попадание шлака в полость кристаллизатора.
- Правильная техника заливки
Используйте разливочный стакан с секцией блокировки шлака. Наливайте медленно, непрерывно и равномерно, чтобы поток жидкости не прерывался. Помните, что нельзя использовать малый ковш (разливочный стакан) для заполнения большей полости формы.
Дефекты материала литейной формы
В процессе литья в песчаные формы используется естественное связывание песчаной формы, что приводит к возникновению дефектов литья, связанных с формой. Дефекты материала пресс-формы — это проблемы, связанные с материалом формования и конструкцией пресс-формы.
Существуют различные дефекты материала формы, здесь мы перечисляем основные дефекты, часто встречающиеся в процессе литья.
Стрижка и стирка
Порезы и промывки являются распространенными дефектами литья в песчаные формы, которые возникают из-за того, что расплавленный металл разрушает песчаную форму, вызывая чрезмерное количество металлических отливок. Дефекты порезов и промывок представлены в виде низких выпуклостей , расположенных вдоль поверхности отливки и наклоненных к тому концу, на который оказывается большее давление заливки.
Что вызывает дефекты порезов и промывок?
Дефекты порезов и промывок возникают из-за:
- Слишком высокой скорости расплава в процессе разливки
- Неправильной конструкции литниковой системы
- Низкой прочности песчаной формы и стержня и стержневая подставка
Как предотвратить дефекты порезов и промывок?
Чтобы предотвратить дефекты обрезки и промывки, вы можете попробовать отрегулировать следующие вещи:
- Спроектировать правильную литниковую систему
- Повышение прочности песчаной формы и стержня путем подбора песчаной формовочной смеси (размер зерен песка, глины, содержание влаги) и контроля технологии формования
- Добавление связующих в облицовочную и стержневую стойки
Проникновение металла
Проникновение металла – это дефект литья, при котором металл проникает в зазоры песчинок, что приводит к шероховатой и неровной поверхности литья.
Эти дефекты литья в песчаные формы видны невооруженным глазом и снижают эстетику литья.
Что вызывает дефекты проплавления металла?
Явление проникновения металла возникает из-за:
- Использование слишком большого количества крупнозернистого песка
Слишком большое количество более крупного песка (крупного размера) с большей вероятностью вызовет сильное проникновение металла, чем мелкий песок.
- Песчаная форма слишком мягкая
- Песчаная форма и стержень имеют низкую прочность
- Нет промывки формы
Как предотвратить дефекты проплавления металла?
Чтобы предотвратить эти дефекты литья в песчаные формы, устраните вышеуказанные причины путем:
- Использовать мелкий песок
- Увеличить прочность песчаной формы и сердцевины
- Обеспечить достаточное уплотнение песчаной формы
Фьюжн
Плавление – это дефекты литья в песчаные формы, при которых песчинки сплавляются с течением металла, в результате чего на отливке образуется тонкая корка стеклообразного и хрупкого вида.
Что вызывает дефекты сплавления?
Дефекты плавления возникают в основном из-за:
- Песчаная форма имеет низкую огнеупорность
- Высокая температура заливки
- Неправильная конструкция литниковой системы
Как предотвратить дефекты сплавления?
Предотвращение дефектов литья в песчаные формы путем:
- Правильное проектирование литниковой системы
- Снижение температуры заливки
- Повышение огнеупорности песчаной формы за счет добавления кварцевого песка
4out
Биение – это дефекты литья в песчаные формы, при которых расплавленный металл вытекает из формы, в результате чего полость формы не заполняется полностью и образуются недостающие/незавершенные детали.
Что вызывает дефекты
Runout ?Дефекты биения возникают по 2 основным причинам:
- Низкоточная конструкция пресс-формы
- Неподходящая опока (набор инструментов для содержания песчаной формы)
Как предотвратить дефекты
Биение ?Решения для предотвращения дефектов биения:
- Спроектируйте точную песчаную форму.
Отбраковка неподходящих песчаных форм перед заливкой
- Выберите высокотемпературный материал для песчаной формы, чтобы предотвратить износ
Набухание
Вздутия вызывают увеличение отливки по сравнению с желаемым объемом, что требует последующей механической обработки и потерь металла.
Что вызывает дефекты вздутия?
Вздутие отливки причина дефектов от:
- Низкая прочность песчаной формы
- Песочная форма плохо утрамбована
Как предотвратить вздутие?
Предотвратить вздутие литья с помощью:
- Жестко утрамбованной песчаной формы
- Повышение прочности песчаной формы, чтобы выдерживать давление потока расплава
Металлургические дефекты
Металлургические дефекты возникают, когда возникают проблемы с отливкой металла. Двумя металлургическими дефектами литья являются горячие разрывы и горячие точки.
Горячие разрывы/трещины
Горячие разрывы, известные как горячие трещины, представляют собой дефекты литья в песчаные формы, которые проявляются в виде трещин неправильной формы в отливке. Некоторые трещины видны невооруженным глазом, для обнаружения некоторых требуется увеличение.
Эти трещины образуются из-за того, что металл слаб в горячем состоянии, а остаточные напряжения (растягивающие) в металле могут вызвать проблемы при его затвердевании. Если застывший металл не обладает достаточной прочностью, чтобы противостоять остаточным напряжениям, появляются горячие трещины.
Что вызывает дефекты горячего разрыва?
- Неправильная конструкция пресс-формы
- Песчаная форма не складывается
- Песчаная форма слишком сильно утрамбована
Как предотвратить дефекты горячего разрыва?
- Надлежащая конструкция пресс-формы для улучшения разборности
- Форма из мягкого утрамбованного песка
Горячие точки/твердые точки
Горячие точки, также называемые твердыми точками, возникают, когда область литья остывает быстрее, чем другие окружающие области, что приводит к более твердым точкам, чем другие.
Что вызывает дефекты горячих точек?
- Неправильная практика охлаждения
Как предотвратить дефекты в местах перегрева?
- Обеспечение надлежащего охлаждения
- Отрегулировать состав металла
Как наш литейный цех обрабатывает дефекты литья в песчаные формы?
Как упоминалось в начале, ни один процесс литья не совершенен на 100%. Несмотря на отличные литейные свойства, существуют дефекты литья, о которых следует беспокоиться.
Специально для одного из самых любимых и популярных видов литейного производства – литья в песчаные формы. Нельзя отрицать, что литье в песчаные формы является исключительным благодаря своей способности отливать большие объемы, высокую детализацию и низкую стоимость литья отливок. Тем не менее, очень важно рассмотреть возможные дефекты литья в песчаные формы, чтобы оценить допуск и ожидания клиента.
На литейном заводе VIC мы прозрачно обсуждаем с нашими клиентами возможные дефекты литья, которые могут возникнуть в процессе работы.
Мы всегда стараемся максимально ограничить дефекты литья в песчаные формы и поставлять литейные детали самого высокого качества.
Наш подход к дефектам литья в песчаные формы зависит от различных дефектов. Тем не менее, наш рабочий девиз: всегда лучше профилактика, чем лечение . Поэтому мы применяем строгие процессы контроля для всех производственных процессов, от ввода сырья, плавки металла, системы заливки, охлаждения до механической обработки.
На литейном заводе VIC мы оборудовали машинами SpetroMax для анализа состава исходного материала. Перед каждым этапом плавки качество сырья тщательно контролируется, чтобы уменьшить металлургические дефекты. Таким образом, мы можем в первую очередь ограничить дефекты литья.
В то же время мы постоянно контролируем литниковую систему и процесс заливки, чтобы обеспечить их эффективность и правильность в соответствии с каждым требованием отливки. Все механические процессы находятся под наблюдением менеджера для обеспечения надлежащей техники.